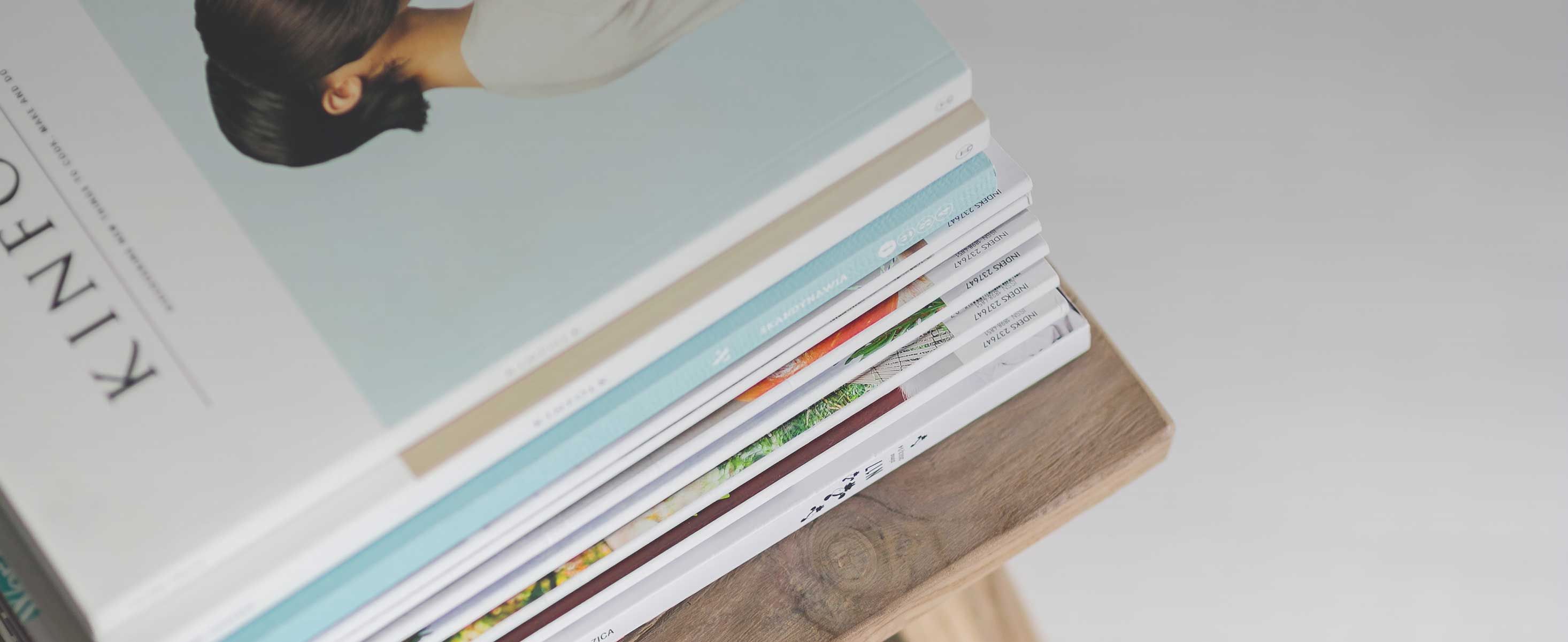
368 minute read
18EI3025 Entrepreneurship development for embedded system 3:0:0 3
50. 17EI3005 Intelligent Controllers 51. 17EI3006 Optimal Control Theory 52. 17EI3007 Advanced Industrial Instrumentation 3:0:0 3:0:0 3:0:0
53. 17EI3008 System Identification and Adaptive Control 54. 17EI3009 Industrial Instrumentation and Process Control Laboratory 55. 17EI3010 Virtual Instrumentation Laboratory 56. 17EI3011 Embedded Control Systems Laboratory
3:0:0 0:0:2 0:0:2 0:0:2 Karunya University 57. 17EI3012 Real Time and Embedded Control Automation 3:0:0 58. 17EI3013 Industrial Automation Systems 3:0:0 59. 17EI3014 Control System Design 3:0:0 60. 17EI3015 SCADA systems and Applications 3:0:0 61. 17EI3016 Design of Linear Multivariable control systems 3:0:0 62. 17EI3017 Embedded Instrumentation 3:0:0 63. 17EI3018 Networks and protocols for instrumentation and control 3:0:0 64. 17EI3019 Multi Sensor Data Fusion 3:0:0 65. 17EI3020 Non Linear Control Systems 3:0:0 66. 17EI3021 Robust Control 3:0:0 67. 17EI3022 Process Modelling and Control 3:0:0 68. 17EI3023 Advanced processor for control and automation 3:0:0 69. 17EI3024 Advanced Embedded Signal Processing 3:0:0 70. 17EI3025 Programmable Devices for industrial automation 3:0:0 71. 17EI3026 FPGA control design laboratory 0:0:2 72. 17EI3027 Embedded Virtual Instrumentation Laboratory 0:0:2 73. 17EI3028 Embedded Automotive Systems 3:0:0 74. 17EI3029 Embedded based Biomedical sensors and signal conditioning 3:0:0 75. 17EI3030 MEMS Technology for Embedded design 3:0:0 76. 17EI3031 Embedded Product Development 3:0:0 77. 17EI3032 Robotics and Factory Automation 3:0:0 78. 17EI3033 Linear Systems 3:0:0 16EI3001 ADVANCED VIRTUAL INSTRUMENTATION Credits: 3:0:0 Course Objectives: Learn the basics concepts of graphical programming. Acquire knowledge on Data Acquisition Systems and network interface concepts. To enable design and programming of Virtual Instruments for real time applications Course Outcomes: At the end of the course, the student will be able to Create a Virtual Instrument using graphical programming. Develop systems for real-time signal acquisition and analysis. Apply concepts of network interface for data communication. Implement and design data acquisition systems for practical applications. Suggest solutions for automation and control applications using virtual instrumentation.
Description:
Introduction – Virtual Instrumentation and its evolution, graphical programming, comparison with conventional programming, Development of virtual instrument, programming techniques,Instrument drivers.Data acquisition: Introduction to data acquisition on PC, Sampling fundamentals, Sensor and its characteristics, Signal Processing and manipulation, Calibration, Resolution, Data Acquisition Interface Requirements,Interface standards and PC buses, Advances in Sensing Technology, Applications: Instrument control, System Simulation, Development of data acquisition and control system, Image Acquisition and processing, motion control, remote data management
References:
1. Gray Johnson, LabVIEW Graphical Programming, Second edition, McGraw Hill, Newyork, 1997 2. Jovitha Jerome, “Virtual Instrumentation using LabVIEW”, PHI Learning Pvt. Ltd, New Delhi, 2010. 3. Sanjay Gupta and Joseph John, “Virtual Instrumentation using LabVIEW”, Tata McGraw Hill Inc., 2005 4. Kevin James, PC Interfacing and Data Acquisition: Techniques for Measurement, Instrumentation and Control, Newnes, 2000. Karunya University 5. Steve Mackay, Edwin Wright, John Park, and Deon Reynders, “Industrial Data Networks”, Elsevier, 2004. 6. P.Surekha, S.Sumathi, “LabVIEW based Advance Instrumentation”, Springer, 2007. 7. D Patranabis, ‘Sensors and Transducers’, PHI 2nd Edition, 2003. 8. Lisa K Wells and Geffrey Travis, “LabVIEW for Everyone: Graphical Programming Even Made Easier”, Prentice Hall Inc., 1996. 9. Clyde F Coombs, “Electronic Instruments Handbook”, McGraw Hill Inc., 1999. 17EI2001 SENSORS AND TRANSDUCERS Credits: 3:0:0 Course Objectives: To gain knowledge on methods of measurement, classification of transducers and measurement errors. Understand static and dynamic characteristics of transducers Get exposed to different types of resistive, inductive and capacitive transducers and their application. Course Outcomes: Describe the mathematics, science and engineering fundamentals involved in measurement applications. Examine the measuring problems related to sensors and transducers Select the suitable sensor/transducer for a given application. Determine the static and dynamic characteristics of transducers Formulate sensors using MEMS and Nano technology Design magnetic sensor and digital sensor based measuring circuits Unit I - Fundamental of Measurements and Classification of Transducers: Units and standards – generalized instrumentation system-Calibration techniques – Static calibration – errors in instrumentation system: Limiting error and probable error – Error analysis – Statistical methods – Odds and uncertainty – Classification of transducers –Selection of transducers. Unit II - Characteristics of Measuring Instruments: Static: Accuracy, precision, resolution, sensitivity, linearity, span and range - Dynamic characteristics: Mathematical model of transducer – Zero, I and II order transducers Response to impulse, step, ramp and sinusoidal inputs Unit III - Resistive Principle based Transducers: Principle of operation, construction details, characteristics and applications of potentiometer, strain gauge, resistance thermometer, Thermistor, hot-wire anemometer, piezoresistive sensor and humidity sensor. Unit IV - Inductive and Capacitive Principle based Transducers: Induction potentiometer – Variable reluctance transducers – EI pick up – Principle of operation, construction details, characteristics and applications of LVDT –Capacitive transducer and types – Capacitor microphone – Frequency response. Unit V - Other Sensors and Transducers: Force and torque transducers: proving ring-hydraulic and pneumatic load cell-dynamometer and gyroscope -Piezoelectric transducer - Hall Effect transducer – Magneto elastic sensorDigital transducers – Smart sensors – proximity devices, biosensors, Film sensors, MEMS – Nano sensors. Text Books 1. Doebelin E.O. and Manik D.N., “Measurement Systems”, 6 th Edition, Tata McGraw-Hill Education Pvt. Ltd., 2011. 2. Renganathan, S.,” Transducer Engineering”, Allied Publishers, New Delhi, 2003.
Reference Books
1. Neubert, H.K.P., “Instrument Transducers – An Introduction to their Performance and Design”, Oxford University Press, Cambridge, 2003. 2. Albert, D. Helfrick and Cooper, W. D., “Modern Electronic Instrumentation and 3. Measurement Techniques”, PHI Learning Pvt. Ltd., 2011.
4. Murthy, D.V.S., “Transducers and Instrumentation”, 2nd Edition, Prentice Hall of India Pvt. Ltd., New
Delhi, 2010. 5. John P. Bentley, “Principles of Measurement Systems”, 4th Edition, Pearson Education, 2004. Patranabis,
D., “Sensors and Transducers”, 2 nd Edition, Prentice Hall of India, 2010
Credits: 0:0:2 17EI2002 SENSORS AND TRANSDUCERS LABORATORY
Karunya University Course Objectives: To gain knowledge on classification of transducers and measurement errors. Understand static and dynamic characteristics of transducers Get exposed to different types of resistive, inductive and capacitive transducers and their application. Course Outcomes: Demonstrate the performance characteristics of various transducers Design a measurement system for an application Acquire Knowledge on testing the instruments Obtain idea about Calibration techniques Understanding of loading effect Trouble shooting of various sensors and transducers Description: This laboratory course enables the students to gain practical knowledge on sensors, their characteristics, design and applications The faculty conducting the laboratory will prepare a list of 12 experiments and get the approval of HOD/Director and notify it at the beginning of each semester. 17EI2003 VIRTUAL INSTRUMENTATION AND DATA ACQUISITION LABORATORY Credits: 0:0:1 Course Objective: To introduce the basics concepts of Virtual Instrumentation. To develop ability for programming in LabVIEW using structures, graphs and charts for system monitoring, processing and controlling To learn about the data acquisition and interfacing concepts using a state-of-the-art software platform such as National Instrument's LabVIEW. Course Outcomes: Create, Edit and Debug Virtual Instruments Develop Virtual instrumentation systems for practical applications Apply PC interfacing principles for data acquisition Understand the usage of Instrument Driver for Computer measurement and control. Formulate instrumentation and control applications using Lab VIEW Appraise the usefulness of LabVIEW for real time data acquisition and analysis Description: This course enables the students to gain practical knowledge in programming techniques, data acquisition and interfacing techniques of virtual instrumentation and apply it to real time environment. The faculty conducting the laboratory will prepare a list of 12 experiments and get the approval of HOD/Director and notify it at the beginning of each semester.
Credits: 3:0:0 17EI2004 ELECTRICAL AND ELECTRONIC MEASUREMENTS
Course Objectives:
To provide information on the basics of Electronic Measurements. To include specialized information needed for Analog and Digital Instrumentation.
To exploit an instrument’s potential, to be aware of its limitations.
Course Outcomes:
Investigate the Electromechanical and Electronic Equipment. Select the proper instrument for measurement. Develop instruments to measure Resistance, Impedance, Voltage and Current. Demonstrate different types of waveform generators and analyzers and their applications. Examine on virtual instrumentation, its applications, programming and DAQ cards and modules. Karunya University Create measurement method for the real time application using VI. Unit I - Measurement of Voltage and Current: Electrical Measurement: D’Arsonval galvanometer – Theory, calibration, application – Principle, construction, operation and comparison of moving coil, moving iron meters, Extension of range and calibration of voltmeter and ammeter – Errors and compensation. Electronic Voltmeter and their advantages – Types, Differential amplifier, source follower. Unit II - Measurement of Power, Energy, Resistance and Impedance: Electrodynamometer type wattmeter –Theory & its operation– Induction type energy meter – Calibration of wattmeter and Energy meter, D.C Bridges Wheatstone bridge– Kelvin double bridge A.C bridges – Measurement of inductance, capacitance – Q of coil –Maxwell Bridge – Wein’s bridge – Schering bridge ––Hay’s bridge- Q meter, ohmmeter Unit III - Signal Generator and Signal Analyzers: Wien Bridge, RC Phase Shift Oscillator, Pulse Generator & Function Generator– Harmonic distortion analyzer – Spectrum analyzer Unit IV - Digital Instrument and Displays: Electronic Counters, Digital Frequency Meter, Digital Voltmeter, Digital Multi-meter, LED & LCD. Unit V - CRO and Virtual Instrumentation: General purpose cathode ray oscilloscope – Dual trace, dual beam and sampling oscilloscopes– Analog and digital storage oscilloscope, Virtual instrumentation (VI) – Definition, flexibility – Block diagram and architecture of virtual instruments – Virtual instruments versus traditional instruments – Software in virtual instrumentation Text Books 1. David A Bell, “Electronic Instrumentation and Measurements”, Third Edition, Ox for University Press, 2013. Reference Books 1. A.D. Helfrick and W.D. Cooper, Modern Electronic Instrumentation and Measurement Techniques, Prentice Hall India Private Ltd., New Delhi, 2010. 2. H.S. Kalsi, Electronic Instrumentation, Tata McGraw-Hill, New Delhi, 2010. 3. J.J. Carr, Elements of Electronic Instrumentation and Measurement, Pearson Education India, New Delhi, 2011. 4. M.M.S. Anand, Electronics Instruments and Instrumentation Technology, Prentice Hall India, New Delhi, 2009. 5. Sanjay Gupta, Virtual Instrumentation using Lab view, Tata McGraw-Hill Education, 2010. 6. Sumathi S and P. Surekha , “LabVIEW based Advanced Instrumentation Systems” Springer, 2007. 7. Bouwens A.J., Digital Instrumentation, McGraw Hill Ltd., USA, 2002. 17EI2005 ELECTRICAL MEASUREMENTS AND MACHINES LABORATORY Credits: 0:0:2 Course Objectives: Understand characteristics of D.C machines and transformer. Apply the measurements techniques to bridge circuits. Develop platform independent applications in instrumentation system.
Course Outcomes:
Infer the basic concepts to obtain the no load and load characteristics of D.C machines and transformer. Show proficiency in testing and control. Identifying the type of special machines used for that particular application. Develop the measurement techniques for a given application while carrying out projects. Design the experiments using calibration for a measurement system. Create prototype for latest instrumentation for real time application.
The faculty conducting the laboratory will prepare a list of 12 experiments and get the approval of HOD/Director and notify it at the beginning of each semester.
Credits: 3:1:0 17EI2006 CONTROL SYSTEM
Karunya University Course Objectives: Understand about various representations of systems. To develop linear models mainly state variable model and Transfer function model from Non Linear systems. To make the students apply linear systems in time domain and frequency domain. Course Outcomes: Develop mathematical model of physical systems Analyze the various linear models in time domain and frequency domain. Outline the basics of state space representation of systems Examine the stability of systems Design appropriate controller for the given specifications. Acquire knowledge on compensator design. Unit I - Modeling of Linear Time Invariant System: Control system: Open loop and Closed loop – Feedback control system characteristics – First principle modelling: Mechanical, Electrical and Hydraulic systems – Transfer function representations: Block diagram and Signal flow graph. Unit II - State Space Model of LTI and LTV Systems: State variable formulation – Non uniqueness of state space model – State transition matrix –Free and forced responses for Time Invariant and Time Varying Systems –Controllability – Observability. Unit III - Time Domain and Stability Analysis :Standard test inputs – Time responses – Time domain specifications – Stability analysis: Concept of stability – Routh Hurwitz stability criterion – Root locus: Construction and Interpretation. Unit IV - Frequency Domain Analysis : Frequency response plots: Bode plot, Polar plot and Nyquist plot –Frequency domain specifications: Resonance peak, Resonant frequency and Bandwidth – Stability Analysis: Gain margin and Phase margin. Unit V - Compensator Design: Design specifications – Lead, Lag and Lag-lead compensators using Root locus and Bode plot techniques.
Text Books
1. Benjamin C. Kuo,
“Automatic Control Systems”, 7th Edition PHI Learning Private Ltd., 2010. 2. Nagarath, I.J. and Gopal, M., “Control Systems Engineering”, New Age International Publishers, 2010.
Reference Books
1. Richard C.Dorf and Bishop, R.H., “Modern Control Systems” , Education Pearson, 3rd Impression, 2009. 2. John J.D., Azzo Constantine, H. and Houpis Sttuart, N Sheldon, “Linear Control System Analysis and Design with MATLAB”, CRC Taylor& Francis Reprint 2009. 3. Katsuhiko Ogata, “Modern Control Engineering”, PHI Learning Private Ltd, 5th Edition, 2010.
17EI2007 CONTROL SYSTEMS LABORATORY Credits: 0:0:1
Course Objectives:
To strengthen the knowledge of Feedback control To inculcate the controller design concepts To introduce the concept of Mathematical Modeling
Course Outcomes:
Determine the mathematical model of physical systems. Design a suitable controller for a process. Analyze the time domain and frequency domain characteristics of systems. Apply the control system concepts to servomotor, synchro. Design and appraise the use of compensators in a control loop Evaluate the merits and demerits of feedback control systems.
The faculty conducting the laboratory will prepare a list of 12 experiments and get the approval of HOD/Director and notify it at the beginning of each semester. Karunya University 17EI2008 INDUSTRIAL INSTRUMENTATION Credit: 3: 0: 0 Course Objectives: To learn the principle of Pressure, Temperature, flow, level, density and viscosity measurements. To know about the selection, calibration and installation of different instruments To explore the application of measuring instruments in various industries Course Outcomes: Apply the knowledge of various Measuring Instruments to design a simple Instrumentation system. Calibrate the industrial instruments and use them in various fields. Select suitable instrument for a given application Analyzing the instrument in Industry Perform Calibration of Instruments Design Instrumentation Circuits for measurement systems. Unit I - Level Measurement :Float operated devices - Displacer devices - Pressure gauge method - Diaphragm boxAir purge system-Differential pressure method – Hydro-step for boiler drum level measurement - Electrical methods - Conductive sensors - capacitive sensors -Ultrasonic method -Solid level measurement Unit II - Flow Measurement: Positive displacement flowmeters - Inferential flowmeter-Turbine flowmeterVariable head flowmeters -Rotameter - Electromagnetic flowmeter - Ultrasonic flowmeter-Coriolis mass flowmeterCalibration of flowmeters application. Unit III - Temperature Measurement: Temperature standards - fixed points -filled-system thermometers Bimetallic thermometer Thermocouple - Laws of thermocouple - Cold junction compensation- Measuring circuits Speed of response -linearization - Resistance thermometer- 3 lead and 4 lead connections - thermistors - IC temperature sensors - Radiation pyrometer- Optical Pyrometer Unit IV - Pressure Measurement: Pressure standards - Dead weight tester - Different types of manometers Elastic elements, Electrical methods using strain gauge-High pressure measurement-Vacuum gauges - Mcleod gauge - Thermal conductivity gauges -Ionization gauge- Differential pressure transmitters Unit V - Density, Viscosity and Composition: Measurement of density – U-type densitometer, Buoyancy meter Measurement of composition – Viscosity measurement methods, Electrical conductivity cell, non-dispersive photometers, pH meter, Zirconia oxygen analyzer, dumbbell O2 analyzer, Gas chromatograph, Mass spectrometer Text Book 1. A.K. Sawhney, Puneet Sawhney , “A Course in Mechanical Measurements and Instrumentation & Control” Dhanpat Rai & Co. (P) Limited, 2017. Reference Books 1. Doebelin, E.O., “Measurement Systems Application and Design”, fourth edition McGraw Hill International, 1978. 2. Noltingk, B.E., “Instrumentation Reference Book”, II edition Butterworth Heinemann, 1996. 3. Flow measurement, “Practical Guides for Measurement and Control”, ISA publication, 1991. 4. Anderew, W.G., “Applied Instrumentation in Process Industries” - a survey Vol-I Gulf Publishing Company. 5. Liptak, B.G., “Process Measurement & Analysis”, IV Edition, Chilton Book Company 1995. 6. Considine, D.M., “Process Instruments and Control & Handbook", McGraw Hill 1985.
Credits: 3:0:0 17EI2009 PROCESS DYNAMICS AND CONTROL
Course Objectives:
To equip the students with the knowledge of modelling a physical process. To understand the design of various control schemes. To apply the control system in various processes. Karunya University Course Outcomes: Identify the fundamentals of system identification by deriving the models of physical systems. Describe the characteristics, selection and sizing of control valves. Apply various tuning techniques to attain the optimum gain in the composite controllers. Analyze and decide suitable control schemes for various industrial applications. Design the conventional controllers for regulating different parameters like pressure, temperature, level and flow in the process control industries. Interpret various processes with their P&ID diagrams and understand nomenclature associated with Process control domain. Unit I - Process dynamics: Process Control System: Terms and objectives - piping and Instrumentation diagram instrument terms and symbols- Process characteristics: Process equation- degrees of freedom- modeling of simple systems – thermal – gas – liquid systems- Self- regulating processes- interacting and non interacting processes Unit II - Basic control actions: Controller modes: Basic control action- two position- multi position- floating control modes Continuous controller modes: proportional, integral, derivative. PI – PD – PID – Integral wind-up and prevention- Auto/Manual transfer- Response of controllers for different test inputs- Selection of control modes for processes like level-pressure-temperature and flow Unit III - Optimum controller settings: Controller tuning Methods: Evaluation criteria - IAE, ISE, ITAE. Process reaction curve method,- Ziegler –Nichol’s tuning- damped oscillation method- Closed loop response of I & II order systems with and without valve -measuring element dynamics Unit IV - Final control elements: Pneumatic Actuators – Electric Actuators - Control valves- construction detailstypes- plug characteristics- Valve sizing- Selection of control valves- Inherent and installed valve characteristicsCavitation and flashing in control valves- Valve actuators and positioners Unit V - Advanced control system: Cascade control- ratio control- feed forward control- Split range and selective control- Multivariable process control- interaction of control loops - Case Studies: Distillation column- boiler drum level control- Heat Exchanger and chemical reactor control Text Books 1. Stephanopoulos, “Chemical Process Control”, Prentice Hall, New Delhi, 2003. 2. Coughanowr D.R., “Process Systems Analysis and Control”, McGraw Hill, Singapore, 2008. 3. Curtis D .Johnson,”Process control instrumentation technology,” Prentice Hall , New Jersey 2006. Reference Books 1. Smith C.L and Corripio. A..B, “Principles and Practice of Automatic Process Control”, John Wiley and Sons, New York, 2006. 2. Dale E. Seborg, Thomas F. Edgar, Duncan A. Mellichamp, “Process Dynamics and Control,” John Willey and Sons, Singapore, 2010. 3. B.Wayne Bequette, “Process control: modeling, design, and simulation” Prentice Hall, New Jersey-2003 4. Peter Harriott, “Process Control”, Tata McGraw Hill, New Delhi, 2008. 17EI2010 INDUSTRIAL INSTRUMENTATION LABORATORY Credits: 0:0:2
Course Objectives:
To gain the knowledge of the working of Industrial Instruments To learn the methods of Calibration for Instruments. To understand the operation of Instrumentation Circuits.
Course Outcomes:
Identify various process measurements using the appropriate instruments.
Design control algorithms for different control loops. Apply ladder logic in Programmable Logic Controller for Control purpose Select the type of transducer for the Industrial application. Develop Instrumentation Circuits for measurement systems. Suggest the instrument suitable for a specific application
The faculty conducting the laboratory will prepare a list of 12 experiments and get the approval of HOD/Director and notify it at the beginning of each semester. Karunya University 17EI2011 PROCESS CONTROL LABORATORY Credits: 0:0:2 Course Objectives: To introduce the practical concepts of digital controllers. To demonstrate Data Acquisition in VI To provide knowledge about controller design, simulation and implementation using Course Outcomes: Recall the concepts of process dynamics and control. Identify the fundamental methods to transmit the industrial parameters such as Pressure, Temperature, Level and Flow to the computer. Apply the control algorithms for the real time plants. Analyze the characteristics of the Actuating signal. Design conventional controllers to regulate the process stations present in the lab. Select suitable controller to the appropriate process stations. The faculty conducting the laboratory will prepare a list of 12 experiments and get the approval of HOD/Director and notify it at the beginning of each semester. 17EI2012 INDUSTRIAL DATA COMMUNICATION NETWORKS Credits: 3:0:0 Course Objectives: Understand the basics of networking Comprehend the significance of different Industrial Interface Standards Apply the appropriate interface for different applications Course Outcomes: Identify the conventional point to point and multipoint interface standards Classify the different channel access methods Choose the appropriate Industrial communication network Explain the various Industrial Communication Standards Justify the need of wireless network Describe the advanced wireless communication standards Unit I - Introduction And Basic Principles: Protocols – Physical standards – ISO/OSI reference –UART - Serial data communications interface standards –RS232,422,,423,449,485 interface standard – The 4 to 20mA current loop –Parallel Interface - IEEE 488 – USB. Unit II - Modbus And HART: Modbus protocol structure, Function codes. Evolution of signal standard: HART communication protocol – Communication modes – HART Networks – HART commands – HART applications –Troubleshooting Unit III - Profibus And Fieldbus: Fieldbus: Introduction – General Fieldbus architecture – Basic requirements of Fieldbus standard – Fieldbus topology – Interoperability and Interchangeability. Profibus: Introduction – Profibus protocol stack – Profibus communication model – Communication objects – Foundation field bus versus Profibus Unit IV - Actuator Sensor Interface (As-I), Devicenet And Industrial Ethernet: AS-i: Introduction –Physical layer – Data link layer – Operating characteristics. Device net: Introduction – Physical layer – Data link layer and Application layer. Industrial Ethernet: Introduction – 10Mbps Ethernet – 100Mbps Ethernet.
Unit V - Wireless Communication: Wireless sensor networks: Architecture – Sensor network scenario. Wireless HART – Existing Wireless Options: IEEE 802.15.4 - ISA 100 – Zigbee – Bluetooth – their relevance to industrial applications
Text Books
1. Mackay, S., Wright,E., Reynders,D., and Park,J., “Practical Industrial Data Networks: Design, Installation and Troubleshooting”, Newnes Publication, Elsevier, 2004. Karunya University 2. Buchanan,W., “Computer Busses: Design and Application”, CRC Press, 2000. Reference Books 1. Bowden,R., “HART Application Guide”, HART Communication Foundation, 1999. 2. Bela G.Liptak, “Instrument Engineers’ Handbook, Volume 3 : Process Software and Digital Networks”, 4th Edition, CRC Press, 2011. 3. Berge,J., “Field Buses for Process Control: Engineering, Operation, and Maintenance”, ISA Press, 2004. 4. Lawrence (Larry) M. Thompson and Tim Shaw, “Industrial Data Communications”, 5th Edition, ISA Press, 2015. 5. NPTEL Lecture notes on, ”Computer Networks” by Department of Electrical Engg., IIT Kharagpur. 17EI2013 DIGITAL CONTROL SYSTEMS Credits: 3:0:0 Course Objectives: To equip the students with the basic knowledge of A/D and D/A conversion. To study the stability analysis of digital control system. To equip the basic knowledge of digital process control design. Course Outcomes: Describe the operating principles of discrete-time systems and control capabilities. Determine the stability of discrete-time control systems. Estimate the steady state response of a discrete time system for any given input. Appreciate the issues associated with the implementation of digital controllers. Evaluate and solve system equations in state-variable form. Compose the digital control algorithm for real time applications. Unit I - Introduction to digital control: Need for digital control – Configuration of the basic digital control scheme - Principles of signal conversion - Basic discrete time signals – Time domain models for discrete time systems - Z transform - Transfer function models Unit II - Analysis of digital control: Frequency Response - Stability on the z-Plane and the Jury stability criterion Sample and hold systems - Sampled spectra and aliasing - Reconstruction of analog signals - Practical aspects of the choice of sampling rate - Principles of discretization Unit III - Models of digital control devices and systems: Introduction - Z domain description of sampled continuous time plants - Z domain description of systems with dead time - Implementation of digital controllers Tunable PID controllers - Digital temperature control systems - Digital position control system Unit IV - Design of digital control algorithms: Introduction - Z plane specifications of control system design Digital compensator design using frequency response plots – Digital compensator design using root locus plots - Z plane synthesis Unit V - State variable analysis of digital control systems: Introduction – State descriptions of digital processor State description of sampled continuous time plants – State description of systems with dead time - Solution of state difference equations – Controllability and observability - Multivariable systems
Text Books
1. Gopal M, “Digital Control and State variable Methods”, Tata McGrawHill, New Delhi, 2012. 2. Ogata, “Discrete Time Control Systems”, Prentice– hall Of India, New Delhi 2008.
Reference Books
1. Gene F. Franklin, J. David Powell, “Digital control of dynamic systems”, Pearson
Education Limited, New Delhi,2002. 2. Richard C. Dorf, Robert H. Bishop, “Modern control systems,” Pearson Educatio inc,
New Delhi, 2008.
Credits: 3:0:0 17EI2014 LOGIC AND DISTRIBUTED CONTROL SYSTEMS
Karunya University Course Objectives: To provide the fundamentals of Data Acquisition system. To introduce the concept of PLC and its Programming using Ladder Diagram. To cover the basics of Distributed Control Systems Course Outcomes: Identify and understand the real time inputs and outputs for the problem given. Select the appropriate PLC for the given problem. Develop real time application using PLC. Design distributed applications using computer controls. Create prototype for the real time application Using PLC,SCADA and DCS. Discriminates between user interface for DCS applications Unit I - Computer Controlled Systems: Data loggers – Data Acquisition Systems (DAS) – Direct Digital Control (DDC) – Supervisory Control and Data Acquisition Systems (SCADA) – sampling considerations – Functional block diagram of computer control systems Unit II - Programmable Logic Controller(PLC) Basics: Definition – Overview of PLC systems - Input/output modules - Power supplies and isolators - General PLC programming procedures - Programming on-off inputs/ outputs - Auxiliary commands and functions – PLC Basic Functions - Register basics - Timer functions - Counter functions. Unit III - PLC Intermediate Functions : PLC intermediate functions: Arithmetic functions, Comparison functions, Skip and MCR functions, Data move systems - PLC Advanced intermediate functions: Utilizing digital bits, Sequencer functions, Matrix functions – PLC Advanced functions: Alternate programming languages, Analog PLC operation, Networking of PLC - PID functions - PLC installation - Troubleshooting and maintenance - Design of interlocks and alarms using PLC. Unit IV - Distributed Control Systems (DCS): Introduction : DCS Evolution, DCS Architecture, Comparison –Local Control unit – Process Interfacing Issues – Redundancy concept - Communication facilities. Unit V - Interfaces in DCS: Operator interfaces: low level, high level – Operator Displays – Engineering Interfaces: Low level, high level – General purpose computers in DCS Text Books 1. John.W. Webb, Ronald A Reis, “Programmable Logic Controllers - Principles and Applications”, Prentice Hall Inc., New Jersey, 2015. 2. Michael P Lukas, “Distributed Control System”, Van Nostrand Reinhold Co., Canada, 1986. Reference Books 1. B.G. Liptak, “Instrument Engineers Hand, Process control and Optimization”, CRC press- Radnor, Pennsylvania, 2011. 2. M.Chidambaram, “Computer Control of Process,” Narosa Publishing, New Delhi, 2003 17EI2015 LOGIC AND DISTRIBUTED CONTROL SYSTEMS LABORATORY Credits: 0:0:2
Course Objectives:
To introduce the practical concepts of Industrial Automation using PLC and DCS To demonstrate Data Acquisition and control using PLC To provide knowledge on distributed control system
Course Outcomes:
Recall the concepts of PLC and Distributed control systems
Identify the fundamental methods to transmit the industrial parameters such as Pressure, Temperature,
Level and Flow to the computer. Apply the control algorithms for the real time plants. Analyze the characteristics of the Actuating signal. Design conventional controllers to regulate the process stations present in the lab. Select suitable controller to the appropriate process stations.
The faculty conducting the laboratory will prepare a list of 12 experiments and get the approval of HOD/Director and notify it at the beginning of each semester. Karunya University 17EI2016 SENSORS AND DATA ACQUISITION Credits: 3:0:0 Course Objectives: To deal with basics concepts for selection of sensors and the signal conditioning necessary to include these in a data acquisition system. To investigate the analogue to digital and digital to analogue conversion principles and their practical applications for data acquisition and control. To learn about the selection of output drivers and devices Course Outcomes: Understand the basics of measurement system and its characteristics Represent the equivalent circuit of sensors and describe their significant properties Choose the type of signal conditioning circuits to be used for a specific sensor Discuss the data conversion circuits and the constraints involved in their design Examine the requirements for interfacing circuit design Develop simple working model of a complete data acquisition system Unit I - Introduction: General Measurement System, Static and Dynamic characteristics of instruments –qualitative study, Loading effects, Signals and noise in Measurement Systems, Reliability, Choice and economics of Measurement systems. Unit II - Sensing Elements: Equivalent circuit of Resistive, capacitive, inductive, electromagnetic, thermoelectric, elastic, piezoelectric, piezoresistive, electrochemical sensing elements, Hall effect sensors, characteristics Unit III - Signal conditioning: Amplification, Impedance Matching, Instrumentation Amplifiers, Charge Amplifiers, Filtering, attenuation, Noise Reduction and Isolation – Grounding Conflict, Ground Loops, Cross Talk, Shielded Wiring, Isolation, Linearization, Circuit protection. Unit IV - Interfacing circuits: Digital I/O interfacing, Microprocessor interfacing, serial interfaces, multi-channel ADCs, internal microcontroller ADCs, ADC specifications, resolution, accuracy, linearity, offset and quantization errors, sample rate and aliasing, Codecs, line drivers and receivers, high power output drivers and devices, Unit V - Data Acquisition Systems: Parameters of Data Acquisition Systems such as dynamic range, calibration, bandwidth, processor throughput, time-based measurements and jitter-Transducer Electronic data sheet, Smart Sensors, System Architecture, Case Studies Text Book 1. Bentley, John P. Principles of Measurement Systems, 4:th edition, Pearson/Prentice Hall, 2005. References 1. Jacob Fraden, Handbook of Modern Sensors – Physics, Design and Applications, Fourth Edition, Springer, 2010. 2. Data Acquistion Handbook, A Reference for DAQ and analog and digital signal conditioning, 3rd Edition, 2012.
Credits: 3:0:0 17EI2017 BIOMEDICAL INSTRUMENTATION
Course Objectives:
To study the fundamentals of anatomy and human physiology system and its functions. To study the fundamental concepts of physiological parameters measurement. To study the concepts of various medical instruments for biomedical applications. Karunya University Course Outcomes: Identify the need of understanding human anatomy and physiology system Select the suitable acquisition method for analysing biomedical signal and vital parameters measurement. Apply the knowledge of biomedical instruments to practical applications Categorize the parameter monitoring techniques based on the application and relevance. Design the various structure for patient safety Develop systems for real time bio signal acquisition and processing. Unit I - Anatomy and Physiology of Human Body - The cell and its electrical activity– Principle physiological system: Cardiovascular System, Nervous system, Respiratory system, Muscular system – Origin of bioelectric signal – Bioelectric signals: ECG, EMG, EEG, EOG and their characteristics Unit II - Measurement of Physiological Parameters - Physiological transducers – Measurement of Blood pressure – Blood flow – Cardiac output measurement – Heart rate – Respiration rate – Measurement of lung volume – Oximeters – Audiometer Unit III - Therapeutic Equipments and Patient Safety - Electro Surgical unit: Short wave and microwave diathermy – Laser surgical unit – Defibrillators – Pacemaker – Heart Lung machine – Dialyser – Anesthesia machine – Ventilators – Nerve stimulators – Total artificial heart (TAH) – Patient Safety: Electric Shock Hazards, Leakage Current Unit IV - Clinical Laboratory Instruments Clinical Flame photometer – Spectrophotometer – Colorimeter –Chromatography–Blood Gas Analyzer – Blood pH Measurement– Measurement of Blood pCO2– Blood pO2 Measurement– Blood Cell Counters: Types and Methods of cell counting Unit V - Imaging Technique and Telemetry X– ray – C.T. scan – MRI instrumentation – Ultrasound scanner –Vector cardiograph – Echo cardiograph – Angiography – Telemetry: Wireless telemetry, Single channel and multichannel telemetry system– Multi patient Telemetry – Implantable Telemetry systems Text Books 1. Khandpur. R. S., “Handbook of Biomedical Instrumentation”, Prentice Hall of India, New Delhi, 2003. 2. Cromwell, “Biomedical Instrumentation and Measurements”, Prentice Hall of India, New Delhi, 2007. 17EI2018 AUTOMOTIVE INSTRUMENTATION Credits: 3:0:0 Course Objectives: To learn the fundamental principles of electronics and to introduce the application of electronics in the modern automobile. To develop ability to understand various latest Communication protocols used in automobile industries. To provide a thorough understanding of automotive systems and various electronic accessories used in automobile. Course Outcomes: Understand the basic electronics system of an automobile. Indicate the function of each system in automobile Analyze the characteristics of the sensors. Select suitable transducer for a specific system. Apply instrumentation techniques for security and safety of automobile. Develop automation for automobiles.
Unit I - Fundamentals of Automotive Electronics: Open loop and closed loop systems components for electronic engine management, vehicle motion control, Current trends in modern Automobiles
Unit II - Electronic Fuel Injection and Ignition systems: Introduction, Carburettor control system, throttle body ignition and multi port or point fuel injection, Advantages of electronic ignition system, Types of solid state ignition systems and their principle of operation, electronic spark timing control system. Unit III - Engine Control System: Engine cranking and warm up control, Acceleration enrichment –Deacceleration leaning and idle speed control, integrated engine control system, exhaust emission control system, Engine performance testing. Unit IV - Automobile Chassis Electronic Control System: Principle of electronic braking, automatic transmission Karunya University electronic control circuit, cruise control circuit, the electronic steering control theory, ABS, ASR, ESP, and other electronic control method. Unit V - Auto Body Electronic Control Technology: Automotive central locking and anti-theft system control technology, electronically controlled windows and doors and airbag technology, principle of control circuit components and characteristics. Text Books 1. Robert Bosch Gmbh ,“BOSCH– Automotive Handbook”, 7thEdition,John Wiley & Sons, ISBN: 0470519363, 2008. 2. Denton.T, “Automobile Electrical and Electronic System”, Elsevier Butterworth–HeinemannPublications,3rd Edition,2004. Reference Books 1. Knowles.D, “Automotive Electronic and Computer control Ignition Systems”, Prentice Hall,1988. 2. William.T.M, “Automotive Electronic System”,Elsevier Science,6th Edition,2003. 3. Kiencke,, Nielsen, “Automotive Control Systems” 2nd Edition.2005. 17EI2019 ANALYTICAL INSTRUMENTATION Credits: 3:0:0 Course Objectives: To equip the students with an adequate knowledge of analytical tools which are useful for clinical analysis, pharmaceutical laboratories, environmental pollution monitoring and control. To provide various techniques and methods of analysis which occur in the various regions of the spectrum. To give unique methods of separation of closely similar materials, using gas chromatography Course Outcomes: Develop instruments for clinical analysis. Apply the concepts of Analytical Instruments for Environmental Monitoring Analysis of industrial gases. Analyze and control pollution in the environment. Apply the latest ideas on ion-selective electrodes as well as biosensors which have potential applications in medical field, food and beverage industries. Analysis the important electromagnetic resonance and microscopic methods. Unit I - Colorimetry And Spectrophotometry: Special methods of analysis – Beer– Lambert law – Colorimeters –UV– Vis spectrophotometers – Single and double beam instruments – Sources and detectors – IR spectrophotometers – Types – Attenuated total reflectance flame photometers – Atomic absorption spectrophotometers – Sources and detectors – FTIR spectrophotometers – Flame emission photometers Unit II - Chromatography: Different techniques – Gas chromatography – Detectors – Liquid chromatographs –Applications – High– pressure liquid chromatographs – Applications Unit III - Industrial gas analyzers and pollution monitoring instruments: Types of gas analyzers: Oxygen, NO2 and H2S types, IR analyzers, Thermal conductivity analyzers, Analysis based on ionization of gases – Air pollution due to carbon monoxide, hydrocarbons, nitrogen oxides, sulphur dioxide estimation – Dust and smoke measurements Unit IV - Ph Meters And Dissolved Component Analyzers: Principle of pH measurement – Glass electrodes –Hydrogen electrodes – Reference electrodes – Selective ion electrodes – Ammonia electrodes – Biosensor –Dissolved oxygen analyzer – Sodium analyzer – Silicon analyzer
Unit V - Radio Chemical And Magnetic Resonance Techniques: Nuclear radiations – Detectors – GM counter –Proportional counter – Solid state detectors – Gamma cameras – X– ray spectroscopy – Detectors –Diffractometers– Absorption meters – Detectors – NMR – Basic principles – NMR spectrometer – Applications –Mass spectrometers – Different types – Applications
Text Books
1. Khandpur. R. S., ‘Handbook of Analytical Instruments’, Tata McGraw Hill Publishing Co. Ltd., 2006. Karunya University 2. Willard. H., Merritt, Dean. J. A., Settle. F. A., ‘Instrumental Methods of Analysis’, CBS publishing & distribution, 1995. Reference Books 1. Robert D. Braun, ‘Introduction to Instrumental Analysis’, McGraw Hill, Singapore, 1987. 2. Ewing. G. W., ‘Instrumental Methods of Chemical Analysis’, McGraw Hill, 1992. 3. Skoog. D. A. and West. D. M., ‘Principles of Instrumental Analysis’, Holt, Saunders Publishing, 1992. 17EI2020 INSTRUMENTATION AND CONTROL IN PETROCHEMICAL INDUSTRIES Credits: 3:0:0 Course Objective: To expose the students to the Instrumentation field and control applied in petrochemical industries. Course Outcomes: Illustrate the controls applied in various elements of Petrochemical industry Provide adequate knowledge about the measurement of various parameters in petrochemical industry. Apply the concepts to design instrumentation systems for a petrochemical industry Choose a suitable control schemes for a specific operation Explain the various measurement techniques in petrochemical industries Categorize the different types of evaporators and dryers involved in petrochemical industries. Unit I - Instrumentation and control in distillation columns: Distillation equipment, variables and degrees of freedom, measurement and control of column pressure, liquid distillate, vapour distillate and inserts, control of feed in reboiler and reflux, cascade and feed forward controls. Unit II - Instrumentation and control in chemical reactors & Dryers: Temperature and pressure control in batch reactors-Batch dryers and continuous dryers. Unit III - Instrumentation and control in heat exchangers: Variables and degrees of freedom, liquid to liquid heat exchangers, steam heaters, condensers, reboilers and vaporisers, use of cascade and feed forward control Unit IV - Instrumentation and control in evaporators: Types of evaporators, measurement and control of absolute pressure, density,conductivity, differential pressure and flow. Unit V - Instrumentation and control in effluent and water treatment: Chemical oxidation, chemical reduction, neutralization, precipitation and biological control. Text book 1. Liptak B. G, Process Control , Third edition , Chilton Book Company, Pennsylvania,1995. Reference Books 1. Liptak B. G, Process Measurement and Analysis, Third edition, Chilton Book Company, Pennsylvania, 1995. 2. Considine D.M., ‘Process / Industrial Instruments and Control Handbook’, Fourth edition, McGraw Hill, Singapore, 1993.
17EI2021 INSTRUMENTATION AND CONTROL IN PAPER INDUSTRIES
Credits: 3:0:0
Course Objectives:
Know the raw materials and the process in paper making Comprehend the significance of different sensors used in Paper Industries
Apply the appropriate computer interface for different applications
Course Outcomes:
Describe the basic processing in paper industry. Discuss the measurement of various parameters in paper industry Choose the appropriate sensor for different applications Explain the various control loops in Paper Industry. Analyze the computer applications in Paper Industry
Unit I - Process Description: Raw materials -pulping process – chemical recovery process – paper making process –converting.
Unit II - Instrumentation: Measurements of basic weight – density – specific gravity – flow – level of liquids and solids– pressure – temperature – consistency – moisture – pH – oxidation – reduction potential – graphic displays and alarms
Unit III - Controls: Blow tank controls – digester liquor feedpump controls – brown stock wacher level control –stock chest level control – basic weight control – dry temperature control
Unit IV - Dissolving tank density control – white liquor classifier density control – white liquor flow control –condensate conductivity control
Unit V - Computer applications in pulping process control, liquid level control and input stock control Karunya University Text Book 1. B.G Liptak, ‘Instrumentation in Process Industries’, Chilton Book Company, 1994. 17EI2022 INSTRUMENTATION AND CONTROL IN IRON AND STEEL INDUSTRIES Credits: 3:0:0 Course Objective To learn about the process of making steel from the raw materials. To know the role of instrumentation in a steel industry To deal with the control operations carries out at various stages Course Outcomes: Describe various process in Iron and Steel industry Indicate the use of instruments in steel making Suggest suitable sensor for a typical measurement Develop control systems for the various operations in Steel Industries Computers, Alarm and Graphical displays Evaluate the usefulness of Instrumentation in monitoring and control in the Steel industry Unit I - Introduction- Description of Process and Flow Diagram- Raw Material Preparation- Iron Making- Blast Furnace- Stoves- Raw Steel making- Oxygen Furnace- Electric Furnace. Unit II - Introduction to Steel Casting- Casting Process- Primary Rolling- Cold Rolling- Finishing- Molding Process- Melting-Pouring- Heat Treating- Cast Steels Compared to Other Processes- Application of Steel Casting in Industries. Unit III - Measurement of Level- Sensor Selection- Calibration- Electrical Methods- Measurement of PressureElectrical Methods- Dead Weight Tester- Measurement of Flow- Classification of Flow Meters- Flow Meter Selection- Calibration- Measurement of Density- Graphic Display- Alarm. Unit IV - Blast Furnace-Stove Combustion Control System- Gas and Water- Controls in BOF Furnace- Stand Casting Mould Level Control- Waste Water Treatment- Conventional Waste Water Treatment Process. Unit V - Model Calculation and Logging- Rolling Mill Control- Annealing Process Control- Center Utilities Dispatch Computer.
Text Book
1. Bela G.Liptak. “Instrumentation in the Processing Industries: Brewing, Food, Fossile Power, Glass, Iron and Steel, Mining and Minerals, Nuclear Power, Paper, Petrochemical, Pharmaceuticals” Chilton Book Co., Reprint 2003
Reference Books
1. Liptak B.G Instrument Engineers Handbook, Vol 2, Process Control, 1977 2. SK Singh, Industrial Instrumentation and Control, Tata McGraw Hill, 2003.
17EI2023 OPTOELECTRONICS AND LASER BASED INSTRUMENTATION Credits: 3:0:0
Karunya University Course Objectives: Acquire Knowledge about the basic concepts of Optical Fibers and LASERS Analyze the various applications of optical fibers in Industrial Measurements Understand the various applications of LASER Course Outcomes: Describe the principle of fiber optic communication Explain the various sources and detectors used for fiber optic communication Apply the principle of fiber optics in sensing various industrial applications Understand the principle of LASER Categorize the types of LASERS Describe the Medical application of LASER Unit I - Introduction: Principles of light propagation through a fiber-Different types of fibers and their properties Transmission characteristics of optical fiber-absorption losses-Scattering losses-Dispersion - Optical sources Optical detectors - LED -LD - PIN and APD Unit II - Optical Fibre Fundamentals: Modes– Types of Optical Fibres – Fibre coupling – Fibre optic sensors for Temperature, Pressure, Flow and Level measurement Unit III - Characteristics Of Lasers: Laser principle– Properties – Two, Three and Four level system – Resonator configuration – Q switching and Mode locking – Cavity dumping – Types of Lasers Unit IV - Industrial Applications Of Lasers: Lasers for measurement of distance and length, Velocity, Material processing: Laser heating, Melting, Scribing, Splicing, Welding and trimming of materials, Removal and Vapourization. Unit V - Hologram And Medical Application: Holography – Basic principle – Methods– Holographic Interferometry and applications – Holography for non – destructive testing – Medical applications of lasers :Laser interaction with biomolecules – Photothermal applications – Photochemical applications – Endoscopes Text Books 1. Arumugam.M. “Fiber Optics and Laser Instrumentation", Anuradha Agencies Publishers, Kumbakonam, 2006. 2. Optical Fiber Communications: Principles And Practice, John M. Senior, Pearson Education, 2006. Reference Books 1. G. Keiser, ‘Optical Fibre Communication’, McGraw Hill, 1995. 2. Ghatak A.K. and Thiagarajan K, Optical Electronics Foundation book , TMH, Cambridge University Press, 1989. 3. Wilson and Hawkes, “Opto Electronics –An Introduction”, 3rd Edition, Prentice Hall, New Delhi, 1998. 17EI2024 POWER PLANT INSTRUMENTATION Credits: 3:0:0 Course Objectives: To provide an overview of different methods of power generation with a particular stress on thermal power generation. To bring out the various measurements involved in power generation plants. To familiarize the students with the methods of monitoring different parameters like speed, vibration of turbines and their control.
Course Outcomes:
Identify the methods of power generation
Apply the concepts to design instrumentation systems for a power plant Choose a suitable control schemes for a specific operation Explain the various measurement techniques in power plant Categorize the different types of analyzers for safety purpose Illustrate the control of a variety of parameters in power plant
Unit I - Overview Of Power Generation : Brief survey of methods of power generation – Hydro, Thermal, Nuclear, Solar and Wind power– Importance of instrumentation in power generation – Thermal power plants –Building blocks – Details of boiler process – Piping and Instrumentation diagram of boiler – Cogeneration Unit II - Measurements In Power Plants: Electrical measurements: Current, Voltage, Power, Frequency, Power factor – Non– electrical parameters: Flow of feed water, Fuel, Air and steam with correction factor for temperature –Steam pressure and Steam temperature – Drum level measurement – Radiation detector – Smoke density measurement – Dust monitor Unit III - Analyzers In Power Plants: Flue gas oxygen analyzer – Analysis of impurities in feed water and steam –Dissolved oxygen analyzer – Chromatography – PH meter – Fuel analyzer – Pollution monitoring instruments Unit IV - Control Loops In Boiler: Steam pressure control – Combustion control – Air/Fuel ratio control –Furnace draft control – Drum level control – Main steam and reheat steam temperature control – Superheater control – Attemperator –Deaerator control – Distributed control system in power plants – Interlocks in boiler operation Unit V - Turbine Monitoring And Control: Speed, Vibration, Shell temperature monitoring and control –Lubricant oil temperature control Karunya University Text Book 1. K. Krishnaswamy, M. Ponnibala, “Power Plant Instrumentation”, PHI Learning Pvt Ltd.,2013. Reference Book 1. P.K Nag, “Power plant Engineering”, Tata McGraw Hill, 2002. 17EI2025 AIRCRAFT INSTRUMENTATION Credits: 3:0:0 Course Objectives: Understand the basics of Aircraft and the Instrumentation involved in Aircraft Systems. To learn the Instrumentation involved in Aircraft Systems Understand the performance of Aircraft and the Instrumentation Course Outcomes: Understand Aircraft and the Display Equipments. Apply the sensors to be used in the Flight. Analyze Power Plant Instruments. Appreciate the need for measurement in aircraft Design instrumentation systems for aircraft. Analyze gyroscopic instruments for attitude measurement Unit I - Introduction: Classification of Aircraft – Instrumentation – Instrument displays – Panels and Layouts Unit II - Flight Instrumentation: Static and Pitot Pressure Source – Altimeter – Airspeed indicator – Machmeter –Maximum Safespeed indicator – Accelerometer Unit III - Gyroscopic Instruments: Gyroscopic theory – Directional gyro indicator artificial horizon – Turn and slip indicator Unit IV - Aircraft Computer Systems: Terrestrial magnetism, Aircraft magnetism, Direct reading magnetic components – Compasses - gyro magnetic compass Unit V - Power Plant Instruments: Fuel flow – Fuel quantity measurement, Exhaust gas Temperature Measurement and Pressure Measurement
Text Books
1. Pallett, E.B.J ., : " Aircraft Instruments ", Pitman and sons, 2009.
Reference Books
1. Pallett, E.B.J,“ Aircraft Instrument Integrated Systems”, ISBN-10: 0582086272, Edition: 3rd 1992.
2. Nagabhushanam S. et.al, S. Nagabhushana, L. K. Sudha, “Aircraft Instrumentation and Systems”,
International Pvt Ltd,2010. 3. Federal Aviation Administration (FAA) “Instrument Flying Handbook”, 2013. 4. Doeblin.E.O, “Measurement Systems Application and Design”, McGraw-Hill, New York, 1999.
Credits : 3:0:0 17EI2026 TELEMETRY AND REMOTE CONTROL
Karunya University Course Objectives: To introduce the basics of telemetry and remote control To learn the principles of devices used for remote monitoring and control To explore the concepts of communication systems Course Outcomes: Understand the fundamentals of signal transmission Classify the types of modulation techniques. Analyze the errors in transmission Apply the concepts of telemetry and remote control to real life applications Illustrate the use of fiber optics for telemetry and control Develop simple models of remote telemetering systems Unit I - Introduction: Purpose of telemetry, basic scheme, voltage, current and frequency telemetry, line length limitations Concepts of Information transfer, bits, symbols, codes -source, line, channel, BCD, ASCII, BAUDOT, AMI, CMI, Manchester, HDBM, Block, Differential, Hamming, Conduction Unit II - Modulation codes: PAM, PFM, PTM, PCM 2 Bit error rate, Inter symbol, noise, parity checking 3 Review of modulation and multiplexing: FM-AM, FM-FM, PAM-AM, PAM-FM, PCM-AM, etc. Quantization and conversion methods, error in quantization, bandwidth consideration Unit III - FDM systems: IRIG standards in FDM systems in FDM telemetry, SCO’s, Mux and Demux circuits, Detectors and Demodulators, Pulse averaging, Quadrature FM and PLL, Mixers TDM systems (architecture)- TDMPAM, PAM- PM, TDM- PCM systems, synchronization, PCM generation, differential PCM, PCM reception and detection Unit IV - Modems: Digital modulation and Shift-keying, FSK, PSK, DPSK, QPSK, QAM, Modem Protocols Satellite telemetry, TT and C services, subsystems, The earth station Unit V - Fiber optic Telemetry: The Fibre as transmission medium, Interconnections, Repeaters, Sources, Detectors, WDM Remote control: concept and example from a typical industrial siteration Text Books: 1. D. Patranabis, Telemetry principles, TMH, 2007. 2. E. L. Gruenberg, Handbook of Telemetry and Remote control, Mc Graw Hill, 1967 Reference Book: 1. A.S. Tanenbaum, Computer Networks, Pearson, 2011. 17EI2027 ROBOTICS AND AUTOMATION Credits: 3:0:0 Course Objectives: To introduce the basics of robotics To study the various kinematics and inverse kinematics of robots To understand the principle of end effectors in robots applications.
Course Outcomes:
Explain the basic principle of working of a robot Understand the kinematics and dynamics in a robot Analyze the applications of sensors in robotics Suggest the suitable hardware requirements for a robot Develop a simple robot from basic understanding
Select the type of robot to be used for a specific application
Unit I - Introduction- Definition and origin of robotics – different types of robotics – various generations of robots – degrees of freedom – Asimov’s laws of robotics. Unit II - Power Sources And Sensors - Hydraulic, pneumatic and electric drives – determination of HP of motor and gearing ratio – variable speed arrangements – path determination – micro machines in robotics – machine vision – ranging – laser – acoustic – magnetic, fiber optic and tactile sensors. Karunya University Unit III - Manipulators, Actuators And Grippers - Construction of manipulators – manipulator dynamics and force control – electronic and pneumatic manipulator control circuits – end effectors –various types of grippers –design considerations. Unit IV - Kinematics And Path Planning -Solution of inverse kinematics problem – multiple solution jacobian work envelop – hill climbing techniques – robot programming languages Unit V - Case Studies - Mutiple robots – machine interface – robots in manufacturing and non- manufacturing applications – robot cell design – selection of robot. Text Book 1. Industrial Robotics – SIE, Nicholas Odray, Mitchell Weiss, McGraw-Hill, 2012 Reference Books 1. Industrial Robotics: Technology and applications, Mikell P. Groover, Nicholas Odray, Mitchell Weiss, Roger, 1987 2. Robotics for Engineers, Yoram Koren, Mc GrawHill, 2014 3. Robotics, Gonzalez, Fu, Lee, McGrawHill, 2008. 4. Issac Asimov I Robot, Ballantine Books, New York, 1986. 17EI2028 SCADA SYSTEMS DESIGN Credits: 3:0:0 Course Objective: To introduce the need for Data Acquisition. To understand the concept of Supervisory Control. To deal with the applications of SCADA Systems. Course Outcomes Appreciate the need of Data Acquisition. Apply the concept of Supervisory Control Perform simulation for various processes. Describe the programming logic involved in automation Analyze SCADA protocol for effective communication Apply the concept of optical and wireless techniques Unit I - Introduction to SCADA: Data acquisition systems, Evolution of SCADA, Communication technologies, Monitoring and supervisory functions, SCADA applications in Utility Automation, Industries Unit II - SCADA System Components: Schemes- Remote Terminal Unit (RTU), Intelligent Electronic Devices (IED), Communication Network, SCADA Server, SCADA/HMI Systems Unit III - SCADA Architecture: Various SCADA architectures, advantages and disadvantages of each system single unified standard architecture -IEC 61850 Unit IV - SCADA Communication: various industrial communication technologies -wired and wireless methods and fiber optics. Unit V - SCADA Applications: Utility applications- Transmission and Distribution sector -operations, monitoring, analysis and improvement. Simulation Exercises
Text Book:
1. Stuart A. Boyer: SCADA- Supervisory Control and Data Acquisition, Instrument Society of America Publications, USA, 1999
Reference Books:
1. Gordon Clarke, Deon Reynders: Practical Modern SCADA Protocols: DNP3, 60870.5 and Related Systems, Newness Publications, Oxford, UK, 2004
17EI2029 POWER ELECTRONICS AND DRIVES FOR INDUSTRIAL CONTROL Credits: 3:0:0
Karunya University Course Objectives: Understand the PWM converters and their analysis Understand the modeling on dc motor, drives and control techniques To educate on dynamic modeling of Induction motor drive Course Outcomes: Evaluate on the V/f and vector control of Induction motor Analize on generation of firing pulses and control algorithms in embedded platforms Identify the need and choice of various drives. Acquire knowledge on different speed control methods in D.C and A.C motors using thyristor based control schemes Acquire knowledge on different types of drives and applications in various industries. Analyze the characteristics of various motors and loads. Unit I - Power Electronic Converters For Drives: Power electronic switches-state space representation of switching converters-Fixed frequency PWM-variable frequency PWM- space vector PWM- Hysteresis current control-dynamic analysis of switching converters-PWM modulator model Unit II - Control of Dc Drives: Modelling of DC machines-block diagram/transfer function-phase control1phase/3phase converter fed DC drives- Chopper fed DC drives-four quadrant chopper circuit-closed loop control-speed control-current control-cascade control –constant torque/power operation-comparison of chopper/converter fed drives- techniques-merits/demits Unit III - Analysis And Modelling Of Induction Motor Drive: Basics of induction motor driveclassification – equivalent circuit- torque Vs slip characteristics-steady state performance- Dynamic modeling of induction motor, Three phase to two phase transformation-stator, rotor, synchronously rotating reference frame model Unit IV - Control Of Induction Motor Drive: VSI fed induction motor drives- waveforms for 1-phase, 3-phase Non-PWM and PWM VSI fed induction motor drives -principles of V/F control- principle of vector control-direct vector control- space vector modulation- indirect vector control . Unit V - Embedded Control of Drives:Generation of firing pulses- generation of PWM pulses using embedded processors-IC control of DC drives- fixed frequency/variable frequency/current control- V/F control using PIC microcontroller- vector control using embedded processors.
Text Books
1. R.Krishnan, “Electric Motor Drives, Modeling, Analysis and Control” Prentice Hall of India,
2002. 2. Ion Boldea, S.A.Nasar “Electric Drives” , CRC Press, 2006
Reference Books
1. Simon Ang, Alejandro Oliva “Power Switching Converters” , CRC Press, 2005 2. Thyristor control of Electric drives, Vedam Subrahmanyam, Tata McGraw Hill, 1988 3. Buxbaum, A. Schierau, and K.Staughen, “A design of control systems for DC drives” , Springer- Verlag, Berlin,1990.
17EI2030 SMART SENSOR TECHNOLOGY
Credits: 3:0:0
Course Objectives:
To teach basics of smart sensors and communication To inculcate the usage of smart sensors in real time applications
Course Outcomes:
Acquire the knowledge & concepts of smart sensors. Comprehend interfacing of sensor with processor . Applies the concepts of sensor communication protocol for real time applications. Analyze the importance of MEMs technology in smart sensor. Compare various standards of smart sensor Evaluate the implications of smart sensor in recent trends.
Unit I - Basics of smart sensors and micromachining: Introduction, Mechanical-Electronic transitions in sensing, nature of sensors, overview of smart sensing and control systems, integration of micromachining and microelectronics, introduction to micromachining, bulk micromachining, wafer bonding, surface micromachining, other micromachining techniques. Unit II - MCUs and DSPs for sensor: Introduction, MCU control, MCUs for sensor interface, DSP control, Software, tools and support, sensor integration. Unit III - Sensor Communication and MEMS: Wireless zone sensing, surface acoustical wave devices, intelligent transportation system, RF-ID, Microoptics, microgrippers, microprobes, micromirrors, FEDs, communications for smart sensors - sources and standards, automotive protocols, industrial networks, office and building automation, home automation, protocols in silicon, other aspects of networkcommunications. Unit IV - Packaging, Testing And Reliability of Smart Sensors: Introduction, Semiconductor packaging applied to sensors, hybrid packaging, packaging for monolithic sensors, reliability implications, testing smart sensors. Unit Standards for Smart Sensors: Introduction, setting the standards for smart sensors and systems, IEEE 1451.1, IEEE 1451.2, IEEE P1451.3, IEEE 1451.4, extending the systems to network. Unit V - Implications of Smart Sensor Standards And Recent Trends: Introduction, sensor plug-and-play, communicating sensor data via existing wiring, automated/remote sensing and web, process control over the internet, alternative standards, HVAC sensor chip, MCU with integrated pressure sensors, alternative views of smart sensing, smart loop.
Text Book
1. Understanding Smart Sensors- Randy Frank, 2nd Edition. Artech House Publications, 2013.
Reference Book
1. G. K. Ananthasuresh, K. J. Vinoy, S. Gopalakrishnan, K. N. Bhat, V. K. Aatre, Micro and Smart Systems: Technology and Modeling Wiley, 2012 Karunya University 17EI2031 PERVASIVE DEVICES AND TECHNOLOGY Credits: 3:0:0 Course Objectives: To expose the students to the fundamentals of wireless sensor technology To teach the infrastructure of WSN processor and its functions To study on challenges in Network communication Course Outcomes: Acquire the knowledge and concepts of wireless sensor technology. Comprehends the challenges in network communication. Applies the concepts of wireless technology for real time applications. Analyze the functions of WSN processor. Compare classification of commercial family of wireless technology Evaluate and discuss on interconnectivity of networks Unit I - Overview Of Wireless Sensor Networks: Challenges for Wireless Sensor Networks- Characteristic requirements for WSN - Challenges for WSNs – WSN vs Adhoc Networks - Sensor node architecture –Commercially available sensor nodes –Imote, IRIS, Mica Mote, TelosB,-Physical layer and transceiver design considerations in WSNs, introduction to fundamentals of MAC protocols - Low duty cycle protocols and wakeup concepts - Contention-based protocols - Schedule-based protocols -the IEEE 802.15.4 MAC protocol- Energy usage profile, Choice of modulation scheme, Dynamic modulation scaling, Antenna considerations-Applications of sensor networks
Unit II - Issues In Pervasive Sensor Network: Single-Node Architecture - Hardware Components, constraints & challenges in resourcesEnergy Consumption of Sensor Nodes, Operating Systems for Wireless Sensor Networks –Introduction - Operating System Design Issues - Examples of Operating Systems – TinyOS, Network Architecture Sensor Network Scenarios, Optimization Goals and Figures of Merit, Gateway Concepts. Data DisseminationFlooding and Gossiping-Data gathering Sensor Network Scenarios –Optimization, Goals and Figures of Merit –Design Principles for WSNs- Gateway Concepts – Need for gateway Unit III - Pervasive Networking and Computing - Introduction, Networking Infrastructure and Architecture of Karunya University PERV NET, Mobility management, service discovery, disconnected operation, Dynamic configuration, auto registration, content based routing, Backbone Technology: Electrical Backbone Networks – Optical Backbone Networks – Wireless Backbone Networks – Wireless Access Technology - Pervasive Web Application architectureAccess from PCs and PDAs - Access via WAP Unit IV - Pervasive Devices: Introduction with Case study of - PDA - Mobile Phone: Elements – Mobile Information Architecture - Mobile Phone Design - Android Overview – The Stack – Android User Interface –Preferences, the File System, the Options Menu and Intents. Unit V - Emerging Wireless Technologies: Evolution and Deployment of Cellular Telephone Systems – 1G, 2G, 2.5G, 3G, 4G. Introduction to wireless LAN, Wireless PAN, Wireless MAN, Broadband Satellite and Microware Systems – Emerging Wireless Technologies – IEEE 802.20 Mobile Broadband Wireless Access Text Book 1. Frank Adelstein, Sandeep K S Gupta, Golden G Richard III, Loren Schwiebert, “Fundamentals of mobile and pervasive computing, TMH, 2007. Reference Books 1. Debashis saha, Amitava mukherjee ,”Networking Infrastructure for Pervasive Computing, Springer International edition, 2011 2. Mullet,”Introduction to wireless telecommunications systems and networks", cengage learning, 2010 3. Brian Fling,”Mobile Design & Development,O’Reilly,2011 4. Marko Gargenta,”Learning Android”, O’Reilly,2011 17EI2032 THEORY AND DESIGN OF NEURO FUZZY CONTROLLERS Credits: 3:0:0 Course Objectives: To expose the students to the concepts of biological and artificial neural networks To teach the basics of fuzzy set theory and operations. To provide adequate knowledge applications of neural networks, fuzzy logic and genetic algorithm. Course Outcomes: Describe the evolution of soft computing techniques. Apply mathematical fundamentals to develop learning algorithms. Analyze problems to formulate models and develop control schemes using soft computing techniques for non-linear systems. Apply engineering fundamentals to use hybrid schemes and optimization Solve complex engineering problems using neurofuzzy controllers. Use modern tool boxes to simulate case studies. Unit I - Introduction – Biological neuron – Artificial neuron – Neuron modeling – Learning rules – Single layer –Multi layer feed forward network – Back propagation – Learning factors. Unit II - Neural Networks For Control - Feed back networks – Discrete time hop field networks – Transient response of continuous time networks – Applications of artificial neural network - Process identification – Neuro controller for inverted pendulum. Unit III - Fuzzy Systems - Classical sets – Fuzzy sets – Fuzzy relations – Fuzzification – Defuzzification – Fuzzy rules. Unit IV - Fuzzy Logic Control - Membership function – Knowledge base – Decision-making logic – Optimisation of membership function using neural networks – Adaptive fuzzy system – Introduction to genetic algorithm, Inverted pendulum – Image processing – Home heating system – Blood pressure during anesthesia
Unit V - Hybrid Control Schemes -Need for Hybrid control – Neuro-Fuzzy Control scheme – ANFIS – Case study – Familiarization with ANFIS toolbox – Introduction to Genetic Algorithm and Particle swarm optimization –Optimization of membership function and rule base using Genetic Algorithm – Introduction to Support vector machine.
Text Books
1. Jacek M. Zurada, ‘Introduction to Artificial Neural Systems’, Jaico Publishing home, 2002. Karunya University 2. Timothy J. Ross, ‘Fuzzy Logic with Engineering Applications’, Tata McGraw Hill, 1997. Reference Books 1. Laurene Fausett, Englewood cliffs, N.J., ‘Fundamentals of Neural Networks’, Pearson Education, 2008. 2. Simon Haykin, ‘Neural Networks’, Pearson Education, 2003. 17EI2033 MICRO CONTROLLER BASED SYSTEM DESIGN Credits: 3:0:0 Course Objectives: To impart knowledge on PIC microcontroller and ARM processor. To introduce the architecture, instruction set and peripheral devices of PIC To introduce the architecture and assembly language programming of ARM. Course Outcomes: Describe the architectural features of PIC and ARM processors Choose the processor relevant to a particular application. Apply the knowledge of PIC microcontroller and ARM processor to solve simple operations. Use the microcontroller programming skills to design and carry out projects Identify and formulate engineering problems and use the microcontrollers appropriately. Develop simple working models using the advanced processors. Unit I - Introduction to PIC Microcontroller – PIC 16F87x Architecture –Instruction Set – Simple Operations. Unit II - Ports, Counters, Timer, Ccp Module And Interrupts - PIC16F87I2C I/O Ports, Counters, Timers CCP Modules –Interrupts. Unit III - Peripherals And Interfacing 16F87xI2C Bus Peripherals Chip Access – Analog to Digital Converter – UART. Unit IV - Arm LPC2148 Introduction -ARM LPC2148 Architecture – ARM LPC2148 Development tools – ARM Assembly Languages Programming – Simple Examples. Unit V - Arm LPC2148 Organization -3-Stage Pipeline ARM Organization – 5-Stage Pipeline ARM Organization – ARM Implementation – ARM Instruction Set. Text Books 1. Peatman, J.B., “Design with PIC Micro Controllers”, Pearson Education, 3rd Edition, 2004. 2. Furber, S., “ARM System on Chip Architecture”, Addison Wesley trade Computer Publication,2000. Reference Books 1. Andrew N. Sloss, Dominic Symes and Chris Wright, “ARM System Developer’s Guide: Designing and Optimizing System Software”, Elsevier Inc., 2013. 2. Trevor Martin, “The insider’s guide to the Philips ARM 7 – based Microcontrollers: An Engineers Introduction to the LPC 2100 Series” Hitex (UK) Ltd., 2005. 3. Muhammed Ali Mazidi, RolinMckinlay and Danny Causey, “PIC Microcontroller and Embedded Systems using Assembly and C for PIC18”, Prentice Hall Publications, 2007. 4. Martin Bates, “Interfacing PIC Microcontrollers-Embedded Design by interactive simulation”,Newnes Publication, 2006. 5. Tim Wilmshurst, “Designing Embedded Systems with PIC Microcontrollers – Principles and Applications”, Newnes Publication, 2007.
Credit 3:0:0 17EI2034 INSTRUMENTATION AND CONTROL SYSTEMS
Course Objectives:
• Understand the fundamental concepts of Instrumentation System • To understand the importance of Instrumentation To provide sound knowledge in the basic concepts of control theory Karunya University Course Outcomes: Select suitable transducer for a specific instrumentation system Analyze the characteristics of transducers Apply controller principles to typical applications. Analyze the transient and frequency response of systems. Test the stability of a given system. Analyze instrumentation for real time applications Unit I - Generalized Measurement System: General concepts of Mechanical Instrumentation generalized measurement system - Classification of instruments as indicators, Recorders and integrators their working principles - Precision and accuracy: Measurement error and calibration Unit II - Pressure And Temperature Measurement: Pressure measurement: Gravitational, Bourdon, Elastic transducers, Strain gauge, Pressure cells – Temperature measurement: Bimetallic, Resistance thermometer, Thermocouples, Pyrometer. Unit III - Strain And Flow Measurement: Strain gauges types, Gauge rosettes.Force measurement: Scales and torque measurement: Mechanical torsion meter, Electrical torsion meter, Piezo Electric Transducer - Hot– Wire anemometer - Magnetic flowmeter- Ultrasonic flow meter Unit IV - Control Systems: Open and closed systems - Servo– mechanisms - Transfer functions, Signal flow graphs - Block diagram algebra - hydraulic and pneumatic control systems - Two –way control - Proportional control - Differential and Integral control Unit V - Stability analysis: Time response of First Order and Second Order Systems, Concept of Stability, Necessary condition for Stability, Routh stability criterion, Polar and Bode plots. Text Books 1. Jain R.K., “Mechanical and Industrial Measurements” Khanna Publishers, 2002. 2. Nagrath. M. and Gopal.I.J.Control systems Engineering, Wiley eastern Ltd.,.2001. Reference Books 1. Sawhny, A.K. “Electrical and Electronics Measurements & Instrumentation”, DhanpatRai& Co., 2000. 2. Collet. C. V. and Hope. A.D. ‘Engineering Measurements’ 2nd Edition ELBS. 3. Baskar S,’Instrumentation control system measurements and controls ‘anuradha agencies publishers,2004. 17EI2035 INSTRUMENTATION FOR AGRICULTURE Credits: 3:0:0 Course Objectives: To introduce the applications of instrumentation in agriculture To teach the principle of sensors used in agriculture, irrigation To gain knowledge on the automation in agriculture related applications Course Outcomes: Describe the need for sensors used in agricultural applications Select suitable sensors for various applications pertaining to agriculture Apply the concepts of automation to packing and storage systems Illustrate the application of sensors in metrological measurements Develop simple automation systems for agriculture Relate the sensor technology to real time applications in agriculture.
Unit I - Introduction: Engineering properties of soil, fundamental definitions and relationships, Need for measurement of soil parameters, Introduction to Sonic Anemometers, Hygrometers, Fine wire thermocouples, Open and Close Path Gas Analyzers, Brief introduction to various Bio-sensors, Soil moisture measurement methods: Resistance based method, Voltage based method, Thermal based method, Time-domain reflectometry(TDR) Unit II - Irrigation systems: Necessity for instrumentation, Irrigation methods: overhead, center pivot, lateral move, micro irrigation systems, Irrigation control management up- stream and down - stream control systems. Unit III - Green houses and instrumentation: ventilation, cooling and heating, wind speed, temperature and Karunya University humidity, rain gauge carbon dioxide enrichment measurement and control. Ground water occurrence, confined and unconfined aquifers, Aquifer properties, Ground water recharge measurement. Unit IV - Automation in earth moving equipment & farm equipment, application of SCADA & PLC in packing industry and cold storage systems, implementation of hydraulic, pneumatic & electronics control circuits in harvesters cotton pickers, tractor etc. Unit V - Leaf area length evapotranspiration, temperature, wetness & respiration measurement & data logging, electromagnetic radiations photosynthesis, agro metrological instrumentation weather stations, surface flux measurement. Text Book 1. Instrumentation handbook-process control, “B.G.Liptak”, Chilton 40 , 2013 Reference Books 1. Industrial instrumentation, “Patranabis”, Tata Mc GrawHill, 2010 2. Process control and instrumentation technology, “C.D. Johnson”, PHI, 2015 17EI2036 ENVIRONMENTAL INSTRUMENTATION Credits: 3:0:0 Course Objectives: Learn the terminology, nomenclature and classification systems used in environmental science Understand the methods of acquiring, interpreting and analysing environmental science information with a critical understanding of the appropriate contexts for their use Appreciate the contribution of environmental science to the development of knowledge of the world we live in Course Outcomes: Describe the methodology of measurement used for environment montoring Apply the knowledge of instruments to measure water and air quality Choose the type of measurement technique suitable for a particular application Evaluate the impact of measurement on environmental parameter monitoring Identify cases where monitoring is required and provide solutions Summarize the significance of instrumentation for environmental quality measurement and control Unit I - Instrumentation Methodologies -Influence of regulatory requirements on instrumentation design, In situ Vs extractive measurement, Online analysis of environmental samples, Ultra violet analysis of water and waste water Unit II - Water Quality parameters - Thermal conductivity detectors, Temperature Monitors, Ph analyzers, Turbidity monitoring, Watershed Scale, Water Quality Monitoring. Unit III - Groundwater monitoring – Level Measurements in ground water monitoring wells, techniques of ground water sampling, Soil permeability and dispersion analysis, instrumentation for assessment of soil and groundwater pollution. Unit IV - Waste water monitoring and air monitoring– Automatic waste water sampling systems, Waste water level measurement techniques, data acquisition systems for ambient air monitoring, air pollution control systems, measurement of ambient air quality. Unit V - Flow monitoring – Air flow measurement, Gas flow measurement, Non-open channel flow measurement, Open channel waste water flow measurement
Text Book
1. Environmental Instrumentation and Analysis Handbook, Randy D Down and Jay H Lehr, Wiley, 2004
Reference Books
1. Measuring the Natural Environment, Ian Strangeways, Cambridge Press, 2003 2. Food and agricultural waste water utilization and treatment, Sean X Liu, Blackwell Publishing, 2007 3. Environmental Instrumentation, Fritschen, Leo, Gay, Lloyd, Springer advanced text in life sciences, 1979.
17EI2037 VIRTUAL INSTRUMENTATION Karunya University Credits: 3:0:0 Course Objectives: Study about the virtual instrumentation system and LabVIEW based Virtual Instrumentation. Study about the hardware and software involved programming techniques in VI. Study about the basic of Programming Techniques and its applications. Course Outcomes: Understand the architecture of Virtual Instrumentation. Appreciate the advantages of Data flow programming Apply basic programming techniques of Virtual Instrumentation. Use Virtual Instrumentation for instrumentation and control Design a LabVIEW based instrumentation system. Identify a suitable interface for data acquisition Unit I - Review Of Virtual Instrumentation: Historical perspective, advantages, Block diagram and Architecture of a Virtual Instrument, Data Flow Techniques, Graphical programming in data flow, comparison with Conventional programming. Unit II - Introduction To LabVIEW: Advantages of LabVIEW Software Environment-Creating and Saving VIControls and Indicators- Data types. Sub VI: Creating- Opening-Editing-Placing a Sub VI in a block- Creating a Stand Alone Application Unit III - Programming Techniques: Loops and charts, arrays, clusters and graphs, case and sequence structures, formula nodes, local and global variables, string and file I/O Unit IV - Data Acquisition Basics: Signals Handling and Classification – Signal Conditioning Analog Interfacing (I/O) - Counters & Timers – Digital (I/O) - DAQ Hardware – DAQ Software Architecture - DAQ Assist Unit V - Common Instrument Interfaces: GPIB-RS232-Handshaking- RS232/RS485 interfacing, VISA – IVI PCMCIA – SCXI – VXI - Networking basics for office & Industrial applications Text Books 1. Jovitha Jerome, “Virtual Instrumentation Using LabVIEW” Prentice Hall India Learning Private Limited, New Delhi, 2010. 2. JohnEssick, “Hands-On Introduction to LabVIEW for Scientists and Engineers”, Oxford University Press,New York, 2nd Edition, 2010. Reference Books 1. NesimiErtugrul, “LabVIEW for Electric Circuits, Machines, Drives, and Laboratories”, Pearson Education, 2nd Edition, 2002. 2. LabVIEW: Basics I & II Manual, National Instruments, 2005. 3. Sanjay Gupta and Joseph John, “ Virtual Instrumentation using LabVIEW”, Tata McGraw – Hill Education India Private Limited, New Delhi, 2nd Edition, 2010. 4. Gary W. Johnson, Richard Jennings, “LabVIEW Graphical Programming”, McGraw-Hill Education, New York, 3rd Edition, 2001. 17EI2038 ULTRASONIC INSTRUMENTATION
Credits: 3:0:0
Course Objectives:
To introduce the fundamentals of ultrasonics To provide knowledge on the basics of Ultrasonic Instrumentation
To teach the applications of Ultrasonic Instruments
Course Outcomes:
Recall the principles of ultrasonic Instrumentation Discuss the various methods for the generation of ultrasonic waves Choose a suitable measurement technique for different parameters Analyze the different ultrasonic test methods Apply the concepts of ultrasonic instrumentation for practical applications Karunya University Illustrate the ultrasonic applications in the field of Medicine Unit I - Ultrasonic Waves: Principles and propagation of various waves – characterization of ultrasonic transmission, reflection and transmission coefficients – intensity and attenuation of sound beam. Power level –medium parameters Unit II - Generation/ Detection of Ultrasonic Waves: Magnetostrictive and piezoelectric effects – construction and characteristics – Detection of Ultrasonic Waves: Mechanical method- Optical Method-Electrical MethodPrecise Measurement: Pulse-echo Overlap- Cross correlation-Computer Based Automated methods: Pulse-echo Overlap- Cross correlation-search unit types Unit III - Classification of Ultrasonic Test Methods: Pulse echo- transit time-resonance- direct contact and immersion type and ultrasonic methods of flaw detection – Flow meters – Density measurement- Viscosity measurement, Level measurement – Sensor for Temperature and Pressure measurements Unit IV - Ultrasonic Application: Measuring thickness-depth-Rail Inspection using Ultrasonic- SONARInspection of Welds and defect detection in welds of anisotropic materials Unit V - Ultrasonic Applications in Medical Field: Medical Imaging- diagnosis and therapy- acoustical holography Text Books 1. Baldev Raj, V.Rajendran, P.Palanichamy, “Science and Technology of Ultrasonics”, Alpha Science International, UK, 2004. 2. J.David N.Cheeke,”Fundamentals and Applications of Ultrasonic Waves,” CRC Press, Florida, 2012. Reference Books 1. C.R. Hill,J.C. Bamber, G.R. ter Harr, “Physical Principles of Medical Ultrasonics,” John Wiley & sons, England, 2004. 2. Dale Ensminger, Foster B.Stulen, ”Ultrasonics Data,Equations and Their Practical Uses,” CRC Press, 2009. 3. Lawrence E.Kinsler, Austin R.Frey, Alan B.Coppens, James V. Sanders, “Fundamentals of Acoustics,” John Wiley and Sons Inc,USA,2000. 4. L.A. Bulavin, YU.F.Zabashta, “Ultrasonic Diagnostics in Medicine,” VSP, Koninklijke Brill,Boston, 2007. 17EI2039 FIBER OPTICS AND LASER INSTRUMENTATION Credits: 3:0:0 Course Objectives: Understand the basic concepts of Optical Fibers and Lasers and their applications in the field of Instrumentation. Understand the knowledge of Fiber optics and Laser Instrumentation and its Industrial Application. To introduce the techniques used by Fiber optics and Laser in the field of Medical Application. Course Outcomes: Understand measurement techniques in Optical fibers Apply LASER in Instrumentation and Biomedical applications. Understand the basic concepts of optical fibers and their properties. To provide adequate knowledge about the Industrial applications of optical fibers. Ability to understand Laser fundamentals. Aadequate knowledgpe about Industrial application of lasers.
Unit I - Optical Fibers And Their Properties: Principles of light propagation through a fiber – Different types of fibers and their properties – Optical sources: LED, Laser Diode – Optical detectors :PiN photodiode and Avalanche Photodetectors (APD) Unit II - Industrial Application Of Optical Fibers: Fiber optic sensors – Fiber optic Instrumentation system –Application in Instrumentation: Measurement of Pressure, Temperature, Liquid Level and strain. Unit III - Laser Fundamentals: Fundamental characteristics of Lasers – Three level and four level lasers –Properties of laser– Laser modes – Resonator configuration – Q switching and mode locking – Cavity dumping –Karunya University Types of lasers: Gas lasers, Solid lasers, Liquid lasers, Semi conductor lasers Unit IV - Industrial Application Of Lasers: Laser for measurement of distance, Length, Velocity, Acceleration, and atmospheric effect – Material processing: Laser heating, Welding, Melting and Trimming of materials –Removal and vaporization Unit V - Hologram And Medical Application: Holography – Basic principle – Methods– Holographic Interferometry and applications – Holography for non– destructive testing –Medical applications of lasers :Laser interaction with biomolecules – Photothermal applications – Photochemical applications – Endoscopes Text Books 1. Arumugam.M. “Fiber Optics and Laser Instrumentation", Anuradha Agencies Publishers, Kumbakonam, 2006. 2. Optical Fiber Communications: Principles And Practice, John M. Senior, Pearson Education, 2006 Reference Books 1. G. Keiser, ‘Optical Fibre Communication’, McGraw Hill, 1995. 2. Ghatak A.K. and Thiagarajan K, Optical Electronics Foundation book , TMH, Cambridge University Press, 1989. 17EI2040 BUILDING AUTOMATION Credits: 3:0:0 Course Objectives To gain knowledge on methods of automation techniques in building Understand Concept of CCTV Get exposed to different types of fire alarm systems standard Course Outcomes Describe the mathematics, science and engineering fundamentals involved in automation applications. Examine the measuring problems related building automation Select the suitable sensor/transducer for fire alarm system Determine the suitable networking and cable technology Formulate automation for safety purpose Design a CCTV based security system Unit I - Introduction to intelligent buildings and Building automation systems: -Intelligent architecture and structure-Facilities management vs. intelligent buildings- Lifecycle of building- Evolution of intelligent buildingsDifferent systems in BAS which includes HVAC, security, fire, lighting systems. Importance of each system in BAS- Process of BAS design, Role of different stakeholders (Architect, contractor, consultant, application engineer and engineer) in BAS system design- Comfort parameters for human being -temperature, humidity, flow, pressure, clean air, Co2%. Unit II - Introduction to Fire Alarm System: Fire alarm System-The History, Need for Fire alarm System, Basic Fire Alarm System, Classification of Fire Alarm System, Conventional Fire Alarm System, Addressable Fire Alarm System, Principles of Operations, Panel Components, Its Applications, FAS architecture: Types of
Architecture and Examples
Unit III - Fire Alarm Detection System Requirement: Stages of Fire Alarm System, Component within Fire
Alarm System, Specific Function within Component -Within Fire alarm System, Important Codes NFPA72 IS 2189 BS 5839,Critical Parameters in Facility Environment, FAS Loops-Classification of Loops and Examples,
Power Supply requirement and its designing parameters, Battery Calculations and Its Requirement and design
Unit IV - Fire Alarm System Details Standards: Network terminology, Classification of Cables, Class of
Cables-Types and distance Supported - Fire terminology -Types of Relay and its Working principle -Working
Principles of Fire Alarm devices and its working -Application in building safety - Components of fire alarm detection system - SLC wiring and its classification - Cause and effect Matrix-Fire alarm system - Concepts of
Water leak detection system - Concepts of VESDA (Very early smoke detection system)
Unit V - Introduction to CCTV, Intrusion and Guard Tour System: Basic of CCTV system, System
Architecture of CCTV System - Types of Camera –Fixed, PTZ, Analog, Digital - Terminology for Cameras CIF,
Mpeg, MP4, POE and Concepts- Camera Connectivity- Video Management System: DVR, DVM, NVR- Video
Analytics- Camera Calculations Parameters Resolution, Compression, Image Connectivity, Recording, Motion%, Karunya University FPS, Bandwidth-Concepts, Storage Tape, PPF (Pixel per foot), Levels of Resolutions, Distance and Width Approximate Compression techniques-Intrusion and Guard Tour System- Basics and Technology used in the Intrusion system.- Application of Intrusion System Text Book 1. Roger W. Haines “ HVAC Systems Design Handbook”, Fifth Edition 2010. 2. Building Control Systems, Applications Guide (CIBSE Guide) by The CIBSE (2000). Reference Books 1. Vlado Damjanovski, CCTV, Newnes, 1999. 2. Joel Konicek and Karen Little, “The Book on Electronic Access Control”, Newnes, 1997. 3. D. Helfrick and Cooper, W. D., “Modern Electronic Instrumentation and Measurement Techniques”, PHI Learning Pvt. Ltd., 2011. 4. Kruegle, Herman, “CCTV Surveillance: Analog and Digital Video Practices and Technology”, ButterworthHeinemann, 2006 14EI2041 MEASUREMENTS AND INSTRUMENTATION Credits: 3:0:0 Course Objectives: To introduce the fundamentals of measurement systems and errors. To provide adequate knowledge on the measurement of electrical and non-electrical quantities. To have an understanding of the concepts of signal generators, analyzers and recording instruments. Course Outcomes: Describe the principle of working of instruments and their characteristics Analyze the instrument characteristics and the errors in measurement. Choose the types of sensor to be used for a specific application. Apply the concepts of data acquisition for real time data processing Develop measurement systems for measuring electrical and non-electrical quantities. Suggest the types of analyzers, display devices and recording instruments for a specific application. Unit I - Measurement Standards: Measurements. Significance of measurements-methods of measurements –Standards and their classification. calibration- functional elements of a measurement system - errors in measurements and statistical analysis. Unit II - Indicating Instruments: D’Arsonval Galvanometer- PMMC Mechanism- DC Ammeters and voltmetersAC current and voltage measurements-RLC measurements-using ac and dc bridges-measurement of incremental inductance and low capacitances-AC voltmeters using rectifiers- digital voltmeters- Q meters-RF power and voltage measurement-high frequency measurement of inductances and capacitances. Unit III - Instruments For Signal Generation And Analysis: Introduction- Sine wave generator- frequency synthesized signal generator-pulse and square wave generator-Wave analyzers-harmonic distortion analyzerspectrum analyzer- heterodyne wave analyzer-frequency counter and time interval measurement- Block diagram of General Purpose Oscilloscope Measurement of voltage, current , phase and frequency using CRO. 7 17 Unit IV - Analog And Digital Data Acquisition Systems: Components of analog and digital data acquisition systems Instrumentation Systems-Interfacing transducers to Electronic control and measuring instrumentsMultiplexing-Types of multiplexing systems-Uses of data acquisition systems-Use of recorders in digital systemsDigital recording systems-Input conditioning systems-digital data acquisition systems digital display unitssegmental display-liquid crystal displays.
Unit V - Transducers: Classification of transducers-Selecting a transducer- strain gauges - Temperature Transducers – Linear Variable Differential Transformer(LVDT), Advantages and Disadvantages –Capacitive Transducers, – Piezo-electric Transducers and Optoelectronic Transducers.
Text books
1. Albert D Helfrich, Cooper. W.D.,” Electronic Instrumentation and Measurement Techniques” Prentice Hall of India, New Delhi, 2009. Karunya University 2. Sawhney A K,” A course in Electrical and Electronic Measurement and instrumentation”, Dhanpat Rai and Sons, New Delhi, 2000 References 1. Joseph J Carr,” Elements of Electronic Instrumentation and Measurement, Pearson Eduation, New Delhi, 2008. 2. Nakra B C and Choudhury K.k.,” Instrumentation Measurement and Analysis”, Tata McGraw Hill, New Delhi, 2004. 17EI2042 PROCESS CONTROL LABORATORY FOR FOOD ENGINEERS Credits: 3:0:0 Course Objectives: To introduce the basics of sensors and control To teach the signal conditioning circuits for data acquisition and control To study the characteristics of the control elements in a closed loop control loop. Course Outcomes: Analyze the characteristics of sensors and transducers. Determine the characteristics of instruments. Design controllers for a given system. Perform stability analysis of a system Understand the process system design Analyze various control valve characteristics The faculty conducting the laboratory will prepare a list of 12 experiments and get the approval of HOD/Director and notify it at the beginning of each semester. 17EI2043 PROCESS CONTROL FOR FOOD ENGINEERS Credits: 3:0:0 Course Objectives: To introduce the fundamentals of sensors and control concepts To teach the concepts of system analysis and control To gain knowledge about the working of various sensors Course Outcomes: • Represent the mathematical model of a system. • Determine the response of different order systems for various test inputs. • Analyze the stability of the system. Apply the knowledge of various Measuring Instruments to design a simple Instrumentation system. Derive the Mathematical Model of a physical system. • Analyse and decide suitable control schemes for a particular system. Unit I - Introduction to Process control: System – steady state design – process control – process control block diagram –definition of a process, measurement, controller, and control element, loop – damped and cyclic response- feedback control – transient responses – laplace transform – transforms of simple functions – step function, exponential function, ramp function and sine function. Unit II - Control systems: Open and closed loop systems, servo- mechanisms, hydraulic and pneumatic control systems, two-way control, proportional control, differential control and integral control. Control valve – Construction and working of pneumatically operated valve and spring – diaphragm
Actuator Unit III - Stability Analysis: Signal flow graph – Mason’s Gain formula, Block diagram algebra. Stability –concept of stability, definition of stability in a linear system, stability criterion, characteristic equation, Routh test for stability Unit IV - Pressure and Temperature sensors: Pressure measurement – Construction and working of capacitive pressure sensor, Inductive pressure sensor, strain gauge, pressure sensor, diaphragm, bourdon tube, differential pressure cell Temperature sensors –Construction and working of RTD, Thermistors, Thermocouples, bimetallic Karunya University strips Unit V - Level sensor: Simple float systems, capacitive sensing element, radioactive methods (nucleonic level sensing) – ultrasonic level sensor. Measurement of density – U-type densitometer, Buoyancy meter Measurement of composition – Electrical conductivity cell, non-dispersive photometers, pH meter, Gas chromatograph, Mass spectrometer. Text Books 1. J.F Richardson A D.G.Peacock, Coulson & Richardson’s “Chemical Engineering”, Volume3, Butherworth – Heinemann, an imprint of Elsevier, 2006. Reference Books 1. Donald R. Coughanowr., “Process System analysis and control” Mc- Graw Hill International Edition , Second Edition,singapore, S2008. 2. Nagoorkani.A “Control Systems”, RBA publications, 2nd edition, ninteenth reprint 2012 3. S.Baskar,”Instrumentation control system measurements and controls”Anuradha Agencies Publishers, 2004. 4. Nagrath, M and Gopal, I.J, “Control Systems Engineering”, Wiley Eastern Limited, Third Edition Reprint 2003. 5. Renganathan, “Transducer engineering, Allied publishers, New Delhi,2003. 6. Patranabis, “Principles of industrial instrumentation”, Printice Hall India, 2004. Patranabis, D., Second Edition Tata McGraw Hill Publishing Co. Ltd.. New Delhi. 1997, ISBN 0074623346. 7. Curtis D .Johnson, “Process Control Instrumentation Technology ”, Prentice Hall , New Jersey2006. 17EI2044 NANO SCALE SENSORS AND TRANSDUCERS Credits: 3:0:0 Course Objectives: To introduce the basics of Nano technology To teach the principles of nano sensors To explore the applications of nanosensor and transducers Course Outcomes: Describe the basics of development of Nano devices Indicate the use of nano technology in sensor development Identify the sensors that can be developed using nanotechnology Apply nano sensors to practical applications Evaluate the performance of nano sensors compared with conventional sensors Develop simple application models using nano sensors and transducers Unit I - Quantum Devices: Quantum Electronic devices – Electrons in mesocopic structures – Short channel, MOS Transistor – split Gate Transistor – Electron wave transistor – Electron spin transistor – Quantum Dot array –Quantum computer- Bit and Qubit. Carbon Nanotube based logic gates, optical devices. . Connection with quantum dots, quantum wires, and quantum wells Unit II - Tunneling Devices: Tunnelling element – Tunnel Effect and Tunneling Elements-Tunnelling Diode –Resonant Tunnelling Diode – Three -Terminal Resonate Tunnelling Devices-Technology of RTD-Digital circuits design based on RTDs - Basics Logic Circuits – Single Electron Transistor(SET) – Principle – Coulomb Blockade Performance – Technology- Circuit Design- Logic and Memory Circuits – SET adder as an Example of a Distributed Circuit.
Unit III - Nanosensors : Micro and nano-sensors, Fundamentals of sensors, biosensor, micro fluids, Packaging and characterization of sensors, Method of packaging at zero level, dye level and first level. Sensors for aerospace and defense: Accelerometer, Pressure Sensor, Night Vision System, Nano tweezers, nano-cutting tools, Integration of sensor with actuators and electronic circuitry, Unit IV - Applications: Sensor for bio-medical applications: Cardiology, Neurology and as diagnostic tool, For other civil applications: metrology, bridges etc. Biosensors. Clinical Diagnostics, generation of biosensors, immobilization, characteristics, applications, conducting Polymer based sensor, DNA Biosensors, optical sensors. Karunya University Biochips. Metal Insulator Semiconductor devices, molecular electronics, information storage, molecular switching, Schottky devices, Unit V - NEMS: Inertial sensors – accelerometer – gyroscope - micromechanical pressure sensors – pizoresistive –capacitive - microrobotics – micro channel heat sinks – optical MEMS – visual display – precision optical platform – optical data switching – RF MEMS – MEMS variable capacitors – MEMS switches – Resonators. Text Books 1. Sensors: Micro &Nanosensors, Sensor Market trends (Part 1&2) by H. Meixner., 2005 2. “Nanoelectronics and Nanosystems-From Transistors to Molecular Quantum Devices” , K. Goser, P. Glosekotter and J. Dienstuhl, Springer, 2004. 3. HerveRigneault, Jean-Michel Lourtioz, Claude Delalande, Ariel Levenson, “Nanophotonics”, ISTE. Reference Books 1. Nanoscience& Technology: Novel structure and phenomena by Ping Sheng (Editor) 2. Nano Engineering in Science &Technology : An introduction to the world of nano design 3. by Michael Rieth. 4. Tai –Ran Hsu, “MEMS & Microsystems Design and Manufacture”, Tata McGraw-Hill publication, 2001. 5. Rai-Choudhury, “MEMS and MOEMS technology and applications”, PHI learning private Ltd, 2009. 6. Mohamed Gad-el-Hak, “The MEMS Handbook”, CRC Press, 2002. 17EI3001 INSTRUMENTATION Credits: 3:0:0 Course Objective: To introduce the fundamental concepts of Instrumentation System To understand the importance of Instrumentation To learn about computer based instrumentation Course Outcomes: Identify the system with respect to the given inputs. Analyze the characteristics of transducers. Select suitable transducer for a specific instrumentation system. Develop digital measurement systems. Understand the use of virtual instrumentation. Apply computer based instrumentation for real time applications. Unit I - Instrumentation System: Introduction – Philosophy of Measurement – The general instrumentation system – Static and Dynamic Characteristics – The overall transfer function –Dynamic response of the sensor – The measurement system as a series of networks Unit II - Resistance and Inductance Transducer: Basic principle – Potentiometer –resistance strain gauge–Measurement of torque– Stress measurement on rotating members –Semi- conductor strain gauges – Contact pressure humidity measurement – Basic principle – Linear variable differential transformer – LVDT equations – RVDT – application of LVDT –LVDT pressure transducer – Synchros – Synchros as position transducer – Induction potentiometer – Variable reluctance accelerometer – Microsyn Unit III - Capacitance and Piezoelectric Transducers: Basic principle – Capacitance displacement transducer – Differential pressure transducer feedback type capacitance proximity pickup – Condenser microphone – Pulse width modulating circuit – Introduction – Material for
piezoelectric transducer – Equivalent circuit of a piezoelectric crystal – Piezoelectric coefficients – Mode of deformation – General form of piezoelectric transducers – Environmental effects Unit IV - Digital methods of Measurements: Digital voltmeters and multimeters – Digital frequency, period and time measurements – Digital tachometers – Digital phase meters – Automation in digital instruments – Digital data recording – Digital Transducers Unit V - Computer based Instrumentation: Evolution of Virtual Instrumentation – Architecture of Virtual Instrumentation – Virtual Instruments Versus Traditional Instruments – Advantages of VI – PC based Data Karunya University acquisition system – Interfacing techniques to the IBM PC –Plug– In data acquisition boards – Interface Buses: PCI, PXI, VXI Reference Books 1. Jackson R G, “Novel Sensors and Sensing”, Institute of Physics Publishing, Bristol and Philadelphia, 2004. 2. Doeblin E.O, “Measurement Systems– Applications and Design”, McGraw Hill,New York, 2008. 3. Kalsi H S, “Electronics Instrumentation, ”Second Edition, Tata McGrawhill, New Delhi, 2010 4. John Park ,Steve Mackay,” Practical Data Acquisition for Instrumentation and Control Systems” Elsevier 2003. 5. Mathivanan “PC– based instrumentation: concepts and practice” PHI, 2009 6. Dr.S.Renganathan, “Transducer Engineering”, Allied publishers, New Delhi, 2003. 7. D.Patranabis, “Principles of Electronic Instrumentation,” PHI, 2008 8. S. Sumathi and P. Surekha , “LabVIEW based Advanced Instrumentation Systems” Springer, 2007. 17EI3002 ADVANCED PROCESS CONTROL Credits: 3:0:0 Course Objectives: To equip the students with the basic knowledge of Process Modeling. To introduce the concept of Multivariable systems and decoupling. To analyze complex control schemes Course Outcomes: Develop mathematical model of a physical process. Analyze the various modes of controllers Categorize the different types of valves. Understand the knowledge of MIMO process and decoupling. Formulate the design of Model based and adaptive controllers Demonstrate various control algorithms in the real time complex process. Unit I - Process Control System: Terms and objectives, Piping and Instrumentation diagram, Instrument terms and symbols – Regulator and servo control – Classification of variables – Process characteristics: Process equation, Degrees of freedom, Modeling of simple systems – Thermal, Gas, Liquid systems, Process lag, Load disturbance and their effect on processes – Self – Regulating processes – Interacting and non –Interacting processes Unit II - Controller modes: Basic control action, Two position, Multi – Position, Floating control modes –Continuous controller modes: Proportional, Integral, Derivative – Composite controller modes: PI, PD, PID, Integral wind – Up and prevention. Auto/Manual transfer, Response of Controllers for different types of test inputs – Selection of control mode for different process with control scheme – Control Valve sizing – Control valve types: Linear, Equal percentage and quick opening valve Unit III - Optimum controller settings – Tuning of controllers by process reaction curve method – Damped oscillation method – Ziegler Nichol’s tuning – Pole placement method – Feed forward control –Ratio control –Cascade control – Split range control – Averaging control – Inferential control Unit IV - Introduction to multivariable system – Evolution of loop interaction – Evolution of relative gains –Single loop and overall stability – Model equations for a binary distillation column – Transfer function matrix –Method of inequalities – Decoupling control – Centralized controller
Unit V - Adaptive Controllers: Internal model control – Adaptive control – Model predictive control: dynamic matrix control – model – Generalized predictive control
Reference Books
1. Stephanopoulos G., “Chemical Process Control, Prentice Hall, New Delhi, 2003. 2. Coughanowr D.R., “Process Systems Analysis and Control”, McGraw – Hill Higher Education, Singapore,2008. Karunya University 3. Wayne BequetteB,’ Process control: modeling, design, and simulation’ Prentice Hall , New Jersey – 2003. 4. Smith C.L and Corripio.A..B, “Principles and Practice of Automatic Process Control”, John Wiley and Sons, New York, 2006. 5. Dale E. Seborg, Thomas F. Edgar, Duncan A. Mellichamp, “Process Dynamics and Control” ,Willey India, 2006. 6. Marlin. T.E., Process Control, Second Edition McGraw Hill NewYork, 2000. 17EI3003 ADVANCED CONTROL SYSTEMS Credits: 3:0:0 Course Objectives To understand the basics of mathematical modeling. To study the stability analysis of linear and non linear systems. To learn the characteristics of non linear systems Course Outcomes Describe the concept of Non-linear control systems. Identify the various techniques to design the controllers for the higher order systems Apply suitable mathematical method to solve the difference equation. Examine stability analysis of linear and non linear systems. Design the State Space model of various dynamic systems Interpret the concepts of subspace identification and design of advanced controllers for various real time dynamic systems in a better way by referring the examples. Unit I - Modeling of Dynamic Systems: Definition of System– Mathematical modeling – State space representation of system – Centrifugal Governor – Ground vehicle – Permanent Magnet stepper motor – Inverted Pendulum Unit II - Analysis of Mathematical Models: State space method– Phase plane – Isoclines – Numerical methods –Taylor Series – Euler’s method – Predictor Corrector method – RungeKutta method – Principle of Linearization of Differential Equation Unit III - State Space Analysis: Reachability and controllability – Observability and constructability –Companion forms – Controller / Observer form – State feed – back control – State estimator – Full order and reduced order Estimator – Combined controller estimator compensator Unit IV - Nonlinear Systems: Introduction to Non linear systems- Saturation–Relay–Dead zone – Backlash non linearities Unit V - Stability of Nonlinear System: Stability of Nonlinear system – Lyapunov stability theorems – Lyapunov function for nonlinear system – Krasovskii’s method – Variable gradient method – Phase plane analysis, Singular points, Constructing phase portraits – Limit cycle – Describing function analysis. Reference Books 1. Stanislaw Zak, ‘Systems and Control’, Oxford University Press, 2003. 2. Gopal M, Digital Control and State variable Methods, Tata McGrawHill, New Delhi, 2003. 3. Ogata K, “Modern Control Engineering”, Pearson Education, New Jersey 2009. 4. Vidyasagar .M, “Nonlinear system analysis”, Prentice Hall Inc., New Jersey 2002. 5. Singiresu S. Rao, “Applied Numerical Methods”, Prentice Hall, Upper Saddle River, New Jersey, 2001. 6. Jean – Jacques E. Slotine, Weiping Li, “Applied nonlinear control”, Prentice Hall Inc., New Jersey, 2004
Credits: 3:0:0 17EI3004 DISCRETE CONTROL SYSTEM
Course Objective
To learn the concepts of discrete time Control systems. To introduce polynomial equations approach to control system design. To deal with the different types of digital control algorithm. Karunya University Course Outcome Recognize the need for discrete time control systems Design control system using polynomial equations approach. Demonstrate the concept of pole placement and state observer techniques. Analyze the state space representation of discrete time system and infer whether all the variables are measurable or controllable. Identify different types of digital controllers for the real time systems. Evaluate the stability analysis of the discrete time system. Unit I - Introduction: Review of Z Transform – Impulse Sampling and data Hold – Reconstructing original signal from sampled signal – Pulse Transfer function – Mapping between the S plane and Z plane – Stability Analysis in Z domain – Transient and steady state response analysis – modified Z transform Unit II - State Space Analysis: State Space representation of discrete time Signals – Solving discrete time State Space Equations – Pulse Transfer Function Matrix – Discretization of continuous time State Space Equations Unit III - Pole Placement and Observer Design: Controllability – Observability – Useful Transformations in State Space Analysis and Design – Design Via Pole placement – State observer – Servo Systems Unit IV - Polynomial Equations approach to Control System Design: Diophantine Equations – Polynomial Equations Approach to Regulator system– Polynomial Equations Approach to Control system Design – Design of Model Matching Control Systems Unit V - Digital Control Algorithm: Implementation of different digital control algorithms: Digital PID, Deadbeat, Dahlin, Smith predictor and Internal Model Control algorithm with examples Reference Books: 1. Gopal M, “Digital Control and State variable Methods”, 4th Edition, Tata McGrawHill, New Delhi, 2012. 2. Ogata, “Discrete- Time Control Systems”, Pearson Education, Singapore,2002 3. Pradeep B Deshpande, “Computer Process Control with Advanced Control Applications”, Instrument Society of America,2000. 4. Gene F. Franklin,J. David Powell, “Digital control of dynamic systems”, Pearson Education Limited-2002. 17EI3005 INTELLIGENT CONTROLLERS Credit: 3:0:0 Course Objectives: To introduce the basic concepts of neural networks and its applications in Control. To introduce fuzzy logic concept and its applications in Control. To introduce genetic algorithm Course Outcomes: Identify and describe soft computing techniques Select suitable optimization algorithm for Industrial applications Apply Neural Network control techniques in real time systems Analyze Fuzzy Logic reasoning to handle uncertainity and solve engineering problems Develop soft computing algorithms to solve real world problems pertaining to control and embedded applications Predict the feasibility of applying a soft computing methodology for a particular problem Unit I - Introduction to Neural Networks : Introduction - biological neurons and their artificial models - learning, adaptation and neural network's learning rules - types of neural networks- single layer, multiple layer- feed forward, feedback networks; back propagation - learning and training - Hopfield network.
Unit II - Neural Network for Control Applications: Neural network for non-linear systems –schemes of neuro control- system identification forward model and inverse model- indirect learning neural network control applications – case studies- Inverted pendulum, cerebellar Model Articulation Control. Unit III - Introduction to Fuzzy Logic :Fuzzy sets- fuzzy operation -fuzzy arithmetic –fuzzy relations- fuzzy relational equations -approximate reasoning -fuzzy propositions - fuzzy quantifiers - if-then rules fuzzy for process automation- level, pressure, temperature process. Unit IV - Fuzzy Logic Control : Structure of fuzzy logic controller - fuzzification models- data base - rule base Karunya University inference engine defuzzification module - Non-linear fuzzy control - PID like FLC- sliding mode FLC - Sugeno FLC - adaptive fuzzy control -fuzzy control applications- case studies. Unit V - Genetic Algorithm and its Applications : Fundamentals of genetic algorithm: Evolutionary computation search space –encoding - reproduction-elements of genetic algorithm-genetic modeling-comparison of GA and traditional search methods - Applications of Genetic based machine learning-Genetic Algorithm and parallel processors - composite laminates - constraint optimization - multilevel optimization – case studies Reference Books 1. Jacek M Zurada, ‘Introduction to Artificial Neural Systems’, Jaico Publishing House, 1999 2. Rajasekaran.S and G.A Vijayalakshmi Pai, ‘Neural Networks, Fuzzy logic and Genetic Algorithms, Synthesis and Applications’, Prentice Hall of India, New Delhi – 2003. 3. Klir G.J. &Folger T.A. ‘Fuzzy sets, uncertainty and Information’, Prentice Hall of India Pvt. Ltd.,1993. 4. Zimmerman H.J. ‘Fuzzy set theory –and its Applications’ – Kluwer Academic Publishers,1994. 5. Melanie Mitchell, ‘An introduction to Genetic Algorithm’, Prentice – Hall of India, New Delhi, Edition: 2004. 6. Kosko, B. ‘Neural Networks and Fuzzy Systems’, Prentice – Hall of India Pvt. Ltd.,1994. 17EI3006 OPTIMAL CONTROL THEORY Credits: 3:0:0 Course Objectives: To provide an introductory account of the theory of optimal control and its applications To give students background in dynamic optimization To learn Calculus of Variations, Pontryagin's Minimum Principle, and Bellman's Dynamic Programming. Course Outcomes: Identify a linear or non -linear system Evaluate the performance of a given system Apply the concept of Dynamic Programming Solve the optimization problems using Calculus of variations Measure the performance of the system using Pontryagin’s Minimum Principle Devise Iterative Numerical Techniques for finding optimal controls and trajectories Unit I - Introduction: Problem formulation – Mathematical model – Physical constraints – Performance measure –Optimal control problem – Form of optimal control – Performance measures for optimal control problem –Selection of performance measure Unit II - Dynamic Programming: Optimal control law – Principle of optimality – An optimal control system – A recurrence relation of dynamic programming – Computational procedure –Characteristics of dynamic programming solution – Hamilton – Jacobi – Bellman equation –Continuous linear regulator problems Unit III - Calculus of Variations: Functions and Functional – Maxima and minima of function– Variation of functional – Extremal of functional – Euler Lagrange equation Unit IV - Variational Approach to Optimal Control Problems: Necessary conditions for optimal control –Linear regulator problems – Linear tracking problems –Pontryagin’s minimum principle and state inequality constraints Unit V - Iterative Numerical Techniques: Minimum control effort problems – Singular intervals in optimal control problems – Numerical determination of optimal trajectories – Two point boundary value problems –Methods of steepest descent – Variation of extremals – Quasilinearization – Gradient projection algorithm
Reference Books
1. Donald E. Kirk, Optimal Control Theory: An Introduction, Prentice – Hall networks series, New Jersey, 2004. 2. Singiresu S. Rao “Engineering Optimization: Theory and Practice” New Age International (P) Ltd., Publishers New Delhi – 2004. 3. Gopal. M, “Digital Control and State Variable Methods”, Tata McGraw – Hill Companies New Delhi, 2009. Karunya University 4. Dimitri P. Bertsekas.’Dynamic Programming and Optimal Control’ Vol –1 Athena Scientific, Bell mount MA, 2000. 17EI3007 ADVANCED INDUSTRIAL INSTRUMENTATION Credits: 3:0:0 Course Objectives: To understand the basic concepts of various process measurement. To provide sound knowledge about various techniques used for the measurement of industrial process parameters. To design measurement system for process variables. Course Outcomes: Recognize the Basic construction, principle and working of various type of transducers/sensor to measure physical quantities like pressure, flow, level. Analyze, formulate and select suitable sensor and how to calibrate also knows to apply for the given applications. Identify technical terms and nomenclature used in industrial measurement, industrial processes, process measurement and industrial process control Acquire knowledge of safety practices used in the measurement and control of industrial processes Demonstrate skills in trouble shooting problems with the measurement and control of industrial processes. Design an instrument for a specific application Unit I - Pressure: Manometers – Different types – Mechanical pressure measurements – Bourdon tube, bellows and Diaphragms – Electrical pressure elements – Piezo resistive sensor –Differential capacitance sensor- Resonator sensor – Force balance transmitter - Differential pressure transmitter and its applications – other methods – Dead weight tester. Design a pressure sensor to measure stream pressure measurement in a boiler. Unit II - Level:Level gauges – float gauges – Hydrostatic pressure – displacement –Echo –Ultrasonic level, radar level, laser, magnetostrictive level – Weight – Capacitive – Radiation – Measurement of level of solids – Other methods. Develop a procedure to measure liquid level in a boiler drum level measurement. Unit III - Flow: Pressure based flow meters – Venturi tubes and basic principles – Volumetric flow calculations –Mass flow calculations – Orifice plates – Pitot tube – proper installation – laminar flow meter – Other methods. Demonstrate the working of DPT for pressure based flow meters - Variable area flow meters – Rotameters, weirs and flumes – Velocity based flow meters – Positive displacement flow meters – True mass flow meters – coriolis mass flow meter-Principle and constructional details of electromagnetic flow meter – different types of excitation schemes used – different types of ultrasonic flow meters – laser doppler anemometer – vortex shedding flow meter – target flow meter Unit IV - Temperature: Bimetallic temperature sensors – filled bulb temperature sensor—Thermistor and RTD –Signal conditioning of industrial RTDs and their characteristics –Three lead and four lead RTD -Temperature sensor accessories - Thermometer - calibration of thermometer and their compensation - Thermocouples - Thermocouple types -Connections -Laws of thermocouple - Reference compensation - software compensation - Signal conditioning of thermocouple – Non contact temperature sensors. Design a signal conditioning circuit for thermocouple output range of 0v-10v. Unit V - Humidity, density and Viscosity: Humidity measurements – Density measurements – Viscosity terms –Definition of absolute and kinematic viscosity –continuous measurement of viscosity– Industrial viscosity meter. Construct a Humidity sensor for agriculture applications.
Reference Books
1. Doebelin, E.O., “Measurement Systems Application and Design”, fourth edition McGraw Hill International, 1978. 2. Noltingk, B.E., “Instrumentation Reference Book”, II edition Butterworth Heinemann, 1996. 3. Flow measurement, “Practical Guides for Measurement and Control”, ISA publication, 1991. 4. Anderew, W.G., “Applied Instrumentation in Process Industries” - a survey Vol-I Gulf Publishing Company. Karunya University 5. Liptak, B.G., “Process Measurement & Analysis”, IV Edition, Chilton Book Company 1995. 6. Considine, D.M., “Process Instruments and Control & Handbook", McGraw Hill 1985. 17EI3008 SYSTEM IDENTIFICATION AND ADAPTIVE CONTROL Credits: 3:0:0 Course Objectives: • To impart the concepts of process modeling • To recall the various system identification techniques • Apply adaptive control schemes in various processes Course Outcomes: • Classify the various models for identification • Identify the given process model • Validate the given model • Design adaptive control. • Apply the design of adaptive controllers for various industrial and real life applications Unit I - Models of LTI systems: Linear Models - State space Models - OE model - Model sets, Structures and Identifiability - Models for Time - varying and Non - linear systems: Models with Nonlinearities – Nonlinear state Space models - Black box models - Fuzzy models Unit II - Transient response and Correlation Analysis – Frequency response analysis – Spectral Analysis – Least Square – Recursive Least Square –Forgetting factor - Maximum Likelihood – Instrumental Variable methods Unit III - Open and closed loop identification: Approaches – Direct and indirect identification – Joint inputoutput identification – Non - linear system identification – Wiener models – Power series expansions – State estimation techniques – Non linear identification using Neural Network and Fuzzy Logic Unit IV - Adaptive Control: Introduction – Uses – Auto tuning – Self Tuning Regulators (STR) – Model Reference Adaptive Control (MRAC) – Types of STR and MRAC – Different approaches to self tuning regulators – Stochastic Adaptive control – Gain Scheduling Unit V - Case Studies: Inverted Pendulum - Robot arm - Process control application: heat exchanger, Distillation column - Application to power system - Ship steering control Reference Books 1. Lennart Ljung, “System Identification Theory for the User”, Prentice Hall, Inc., NJ, 1999. 2. Torsten Soderstrom, Petre Stoica, “System Identification”, prentice Hall ` International (UK) Ltd,2000. 3. Astrom and Wittenmark,” Adaptive Control Second Edition”, Addison - Wesley Publishing Company 2001. 4. William S. Levine, “ Control Hand Book” CRC Press, Jaico Publishing House, 2000 5. Narendra and Annasamy,” Stable Adaptive Control Systems, Prentice Hall, Inc., 2005 17EI3009 INDUSTRIAL INSTRUMENTATION AND PROCESS CONTROL LABORATORY
Credits:0:0:2
Course Objectives:
To demonstrate the various process Measurements. To inculcate the various controller design. To give an exposure about Programmable Logic Controller.
Course Outcomes:
Measure various process measurements using the appropriate instruments. Design control algorithms for different control loops. Write ladder logic program in Programmable Logic Controller for Control purpose. Perform simulation for complex control schemes Calibrate the process instruments Assess the performance of the system in real time applications
The faculty conducting the laboratory will prepare a list of 12 experiments and get the approval of HOD/Director and notify it at the beginning of each semester. Karunya University 17EI3010 VIRTUAL INSTRUMENTATION LABORATORY Credits:0:0 :2 Course Objectives: To strengthen the knowledge of Virtual Instrumentation. To understand the concept of signal processing using virtual instruments To introduce the concept of Data Acquisition using virtual instrumentation Course Outcomes: Understand the programming methodology. Will be able to use the appropriate function for the given problem. Develop simulations for real time process. Analyze real world signals. Interface real process with a virtual instrument. Perform signal processing operations using virtual instrumentation. The faculty conducting the laboratory will prepare a list of 12 experiments and get the approval of HOD/Director and notify it at the beginning of each semester. 17EI3011 EMBEDDED CONTROL SYSTEM LABORATORY Credits: 0:0:2 Course Objective: To impart the basic knowledge about Embedded hardware and its functions. To learn about the interfacing of embedded hardware with embedded software for Real World applications. To understand the concepts of embedded programming. Course Outcomes: List different software tools used for system design Review the structure of embedded software and download it to the embedded hardware. Demonstrate the necessary of embedded hardware and the interface issues related to it. Summarize the programming issues related to instrumentation system Identify the various procedures for designing real time control system Design a real time system for control applications The faculty conducting the laboratory will prepare a list of 12 experiments and get the approval of HOD/Director and notify it at the beginning of each semester.
17EI3012 REAL TIME AND EMBEDDED CONTROL AUTOMATION
Credits: 3:0:0
Course Objectives:
To study the fundamentals of embedded system and its architecture. To study the fundamental concepts of how process are created and controlled with OS To study the development activities of real time system for control and automation
Course outcomes:
Identify the basic need of embedded systems and their usage in Instrumentation systems Set up an interfacing circuit for real time processing and control. Select the suitable languages and techniques for embedded system application development Construct the real time models for control applications Schedule the structure of RTOS for multitasking execution for real time embedded applications Design real time system for control and automation applications using embedded processor
Unit I - Instrumentation System Design: Definitions-Characteristics -Architecture of an embedded systemOverview of micro-controllers and microprocessors- Classifications of an embedded system - Embedded processor architectural definitions-Typical application scenario of embedded systems- Design Process. Unit II - Methods for Interfacing and Control: Overview of analog and digital Interfacing- LED, Seven Segment Display, Switch Interface, Keypad Interface, Analog to Digital and Digital to analog converters, Timer operations. Pressure sensing, Temperature sensor interfacing and serial communications Unit III - Techniques for Embedded Instrumentation System Design: State Machine and state Tables in embedded design. High level language descriptions of S/W for embedded system, Getting embedded software into a target system, Simulation and Emulation of an embedded system, Software development tools. Unit IV - Real Time Models and Operating Systems: Real time languages , OS tasks, Task states, Real time kernel, Preemptive Kernel, Non preemptive kernel, Priority Inversion Problem, Task scheduling, Round robin scheduling, Cooperative scheduling, Preemptive Scheduling, Petrinet Model, Interrupt Service Routine in RTOS environment, Study of Micro C/OS-II RTOS Unit V - Control and Automation Applications: Fundamentals of real-time processing in automation and control, Liquid level control, Stepper Motor Control, Modern speed control- Hardware and software approach for PWM Signal Generation, Servo Motor Control, Square Wave generator, PID Controller, Control of Electro Pneumatic Mechanism, Elevator Control, Water Tank Control system, Embedded Implementation of temperature control system, Remote Control applications. Karunya University Reference Books 1. RajKamal, “Embedded Systems Architecture, Programming and Design”, Tata McGrawHill , Second Edition, 2008 2. Tim Wilhurst, “An Introduction to the Design of Small Scale Embedded Systems, Palgrave, 2004. 3. Tammy Noergaard, “Embedded Systems Architecture”, Elsevier, 2005. 4. Frank Vahid, Tony Givargis, “Embedded Systems Design”, Wiley India, 2006 17EI3013 INDUSTRIAL AUTOMATION SYSTEMS Credits: 3:0:0 Course Objectives: To introduce the process control philosophies To learn the Programmable Logic controller design To deal with computers based systems for control applications Course Outcomes: Explainarchitectureofindustrialautomationsystem Understandvariousautomationcomponentsand systems Measure industrial parameters like temperature, pressure, force, displacement, speed, flow, level, humidityand pH. Apply fundamentalsofprocesscontrol for automation. Develop Programs using programmablelogic controllers forindustrialautomation Use computers for industrial automation.
Unit I - Introduction to Industrial Automation: Defining Industrial Automation, Objectives and Requirements, Role of Automation in Industry, Types of Automation System, Architecture of Industrial Automation System Nature of Industrial Process: continuous & discrete state, sequential process, process variables and their classification.
Unit II - Process Control: Introduction to process control, Problems on Continuous, Discontinuous & Composite Controller, PID Control Tuning, Implementation of PID Controller, Control Structures of Feed Forward Feed, Backward & Inertial Controller, Process Variables & Classification Unit III - Automation components: Sensors for temperature, pressure, force, displacement, speed, flow, level, humidity and pH measurement. Actuators, process control valves, power electronics devices DIAC, TRIAC, power MOSFET and IGBT. Introduction of DC and AC servo drives for motion control. Unit IV - Programmable logic controllers: Programmable controllers, Programmable logic controllers, Analog Karunya University digital input and output modules, PLC programming, Ladder diagram, Sequential flow chart, PLC Communication and networking, PLC selection, PLC Installation, Advantage of using PLC for Industrial automation, Application of PLC to process control industries. Unit V - Computer aided measurement and control systems: Role of computers in measurement and control, Elements of computer aided measurement and control, man-machine interface, computer aided process control hardware, process related interfaces, Communication and networking, Industrial communication systems, Data transfer techniques, Computer aided process control software, Computer based data acquisition system, Internet of things (IoT) for plant automation Reference Books: 1. John webb, “Programmable logic controllers-Principles & applications”, Prentice Hall of India,2003. 2. C. D. Johnson, “Process control instrumentation Technology, 8th Edition, John Wiley & Sons, 2013. 3. S.K. Singh, “Industrial Instrumentation and Control” , 3rd Edition,The McGraw Hill,2009. 5.Andrew Parr, “Industrial control handbook” , 3rd Edition, Newnes,1998. 17EI3014 CONTROL SYSTEM DESIGN Credits: 3:0:0 Course Objectives Understand the performance specification, limitations and structure of controllers Design of controllers using root-locus and frequency domain techniques To introduce the techniques of extending the theory on continuous systems to discrete time systems Course Outcomes Ability to understand the specification, limitation and structure of controllers. Design controllers for process applications Design a controller using Root-locus and Frequency Domain technique. Design discrete state space systems Acquire knowledge on state space and ability to design a controller and observer. Design LQR and LQG for a system. Unit I - Basics And Root-Locus Design: Design specifications-sensitivity and stability- Limitations- Controller structure- one and two degrees of freedom- PID controllers and Lag-lead compensators- Root locus designDesign examples Unit II - Frequency Response Based Design: PID controllers and Lag-lead compensators – Design using Bode plots- use of Nyquist plots and Routh-Hurwitz Criterion-Design examples Unit III - Design In Discrete Domain: Sample and Hold devices -Discretisation - Effect of sampling on transfer function – Discrete root locus, Nyquist plots –Jury ’s stability test- Direct discrete design -Design examples Unit IV - Discrete State Variable Design: Effect of sampling on Controlability, observability- state and output feedback- observers - estimated state feedback –Design examples Unit V - LQR and LQG Design: Formulation of LQR problem- Pontryagin’s minimum principle and Hamiltonian solutions- Ricatti’s equation – Optimal estimation- Kalman filter –solution to continuous and discrete systems - Design examples.
Reference Books
1. M. Gopal “Modern control system Theory” New Age International, 2005. 2. Arthur G. O. Mutambara, “Design and Analysis of Control Systems” , CRC Press, 3. Indian reprint 2009.
Karunya University
4. G. F. Franklin, J. D. Powell and A. E. Naeini “Feedback Control of Dynamic Systems” , PHI (Pearson), 2002. 5. Graham C. Goodwin, Stefan F. Graebe and Mario E. Salgado “Control system Design” , PHI (Pearson), 2003. 6. G. F. Franklin, J. D. Powell and M Workman, “Digital Control of Dynamic Systems” , PHI (Pearson), 2002. 7. Loan D. Landau, Gianluca Zito, ” Digital Control Systems, Design, Identification and Implementation” ,
Springer, 2006. 8. Benjamin C. Kuo “Digital control systems” , Oxford University Press, 2004.
17EI3015 SCADA SYSTEMS AND APPLICATIONS
Credits: 3:0:0 Course Objectives:
To introduce the need for Data Acquisition. To understand the concept of Supervisory Control. To deal with the applications of SCADA Systems.
Course Outcomes:
Appreciate the need of Data Acquisition. Apply the concept of Supervisory Control Perform simulation for various processes. Describe the programming logic involved in automation Analyze SCADA protocol for effective communication Apply the concept of optical and wireless techniques Unit I - Introduction to SCADA: Data acquisition systems, Evolution of SCADA, Communication technologies, Monitoring and supervisory functions, SCADA applications in Utility Automation, Industries Unit II - SCADA System Components: Schemes- Remote Terminal Unit (RTU),Intelligent Electronic Devices (IED),Programmable Logic Controller (PLC), Communication Network, SCADA Server, SCADA/HMI Systems Unit III - SCADA Architecture: Various SCADA architectures, advantages and disadvantages of each system single unified standard architecture -IEC 61850 Unit IV - SCADA Communication: various industrial communication technologies -wired and wireless methods and fiber optics. Open standard communication protocols Unit V - SCADA Applications: Utility applications- Transmission and Distribution sector -operations, monitoring, analysis and improvement. Industries - oil, gas and water. Case studies, Implementation, Simulation Exercises
Reference Books:
1. Stuart A. Boyer: SCADA- Supervisory Control and Data Acquisition, Instrument Society of America Publications, USA, 1999 2. Gordon Clarke, Deon Reynders: Practical Modern SCADA Protocols: DNP3, 60870.5 and Related Systems, Newness Publications, Oxford, UK, 2004
17EI3016 DESIGN OF LINEAR MULTIVARIABLE CONTROL SYSTEMS Credits: 3:0:0 Course Objectives:
To inculcate the knowledge of Multivariable control systems. To design controller for multivariable control systems. To apply the design for various applications.
Course Outcomes:
Apply the concept of Multivariable control systems. Design controller for multivariable control systems. Use the corresponding controller synthesis techniques. To inculcate the knowledge of P&ID for multivariable processes. Testing the stability of multivariable control system
Derive the mathematical model of a system
Unit I - Analysis: System representations, return difference matrix, stability theory, multivariable poles and zeros.
Unit II - Design Methods: Design criteria, LQG design methods (including the optimal linear quadratic regulator and the Kalman filter), norm based methods, robust stability and performance.
Unit III - Advanced Design Methods: H-infinity design techniques, including the generalized regulator Karunya University problem. Unit IV - Reduction Techniques: Model reduction, including modal and balanced truncation. Unit V - Design examples: Use of software for the design of controllers for industrial processes such as distillation column, reactors. Reference Books: 1. Stanislaw Zak, ‘Systems and Control’, Oxford University Press, 2003. 2. Gopal M, “Digital Control and State variable Methods”, Tata McGraw Hill, New Delhi, 2003. 3. Charles R. Slivinsky, Donald G. Schultz, Lynn E. Weaver, “The design of linear multivariable control systems using modern control theory”, 1969. 4. Ying-Jyi Paul Wei, “Frequency-domain approaches to linear multivariable control system designs, 1979. 5. Ogata K, “Modern Control Engineering”, Pearson Education, New Jersey, 2009. 17EI3017 EMBEDDED INSTRUMENTATION Credits: 3:0:0 Course Objective: To introduce the fundamental concepts of Instrumentation System To understand the importance of Instrumentation To deal with the concepts of embedded instrumentation systems Course Outcomes: Infer the principle and characteristics of instrumentation system Select suitable transducer for a specific instrumentation system Analyze the characteristics of transducers Develop the Virtual Instrumentation in the Engineering Process Design the computer based instrumentation for real time applications Create a prototype using data acquisition board Unit I – Instrumentation: Introduction - Functional elements of an Instrumentation system. Classification of an instruments - Transducers- Static Characteristics - Dynamic Characteristics, Errors and error analysis UnitI I - Sensors And Transducers: Introduction Displacement, position and proximity sensors - PotentiometerCapacitive element -Differential transformers - Eddy current proximity sensors - Inductive proximity switch Optical encoders - Hall effect sensors Velocity and motion - Pyro electric sensors - Liquid flow - Liquid level Floats - Differential pressure - Temperature - Bimetallic strips - Light sensors Unit III - Virtual Instrumentation: Introduction - Evolution of Virtual Instrumentation - Architecture of Virtual Instrumentation - Virtual Instruments Vs traditional Instruments Creating Virtual Instruments Using LabVIEW Virtual Instrumentation in the Engineering Process Unit IV - Programming Techniques: LabVIEW Environment- Dataflow Programming - Programming Concepts of VI - Control Structures - Selection Structures – Arrays - Clusters - Inputs and Outputs Unit V - PC based data acquisition system - Interfacing techniques to IBM PC plug – In data acquisition boards Interface buses: PCI, PXI, VXI
Reference Books
1. Jackson R G, “Novel Sensors and Sensing”, Institute of Physics Publishing, Bristol and Philadelphia, 2004. 2. Doeblin E.O, “Measurement Systems– Applications and Design”, McGraw Hill,New York, 2011. 3. Kalsi H S, “Electronics Instrumentation” , Second Edition, Tata Mcgrawhill, New Delhi, 2010
4. John Park ,Steve Mackay,” Practical Data Acquisition for Instrumentation and Control Systems” Elsevier 2003. 5. Mathivanan “PC– based instrumentation: concepts and practice” PHI, 2008 6. Dr.S.Renganathan, “Transducer Engineering”, Allied publishers, New Delhi,2003. 7. D.Patranabis, “Principles of Electronic Instrumentation,” PHI, 2008 8. S. Sumathi and P. Surekha , “LabVIEW based Advanced Instrumentation Systems” Springer, 2007. 9. H K P Neubert, “Instrument Transducers”, Oxford University Press, Cambridge,2000. Karunya University 17EI3018 NETWORKS AND PROTOCOLS FOR INSTRUMENTATION AND CONTROL Credits: 3:0:0 Course Objectives: Understand the basics of networking Comprehend the significance of different Industrial Interface Standards Apply the appropriate interface for different applications Course Outcomes: Identify the conventional point to point and multipoint interface standards Classify the different channel access methods Choose the appropriate Industrial communication network Explain the concept of Distributed Control System Justify the need of wireless network Describe the advanced wireless communication standards Unit I - Introduction and basic principles: Protocols – Physical standards – ISO/OSI reference –UART - Serial data communications interface standards –RS232,422,,423,449,485 interface standard – The 4 to 20mA current loop –Parallel Interface - IEEE 488 – USB. Unit II - HART and Field Bus: Evolution of signal standards – HART communication protocol – Communication modes – HART networks – Control system interface – HART and OSI model – Filed bus introduction – General field bus architecture – Basic requirements of field bus standard – Field bus topology – Inter operability Unit III - Distributed Control System: Evolution – Architectures – Comparison – Local control unit – Process interfacing issues – Communication facilities. Unit IV - Interfaces in DCS: Operator interfaces - Low level and high level operator interfaces – Operator displays - Engineering interfaces – Low level and high level engineering interfaces – General purpose computers in DCS. Unit V - Wireless Communication: Wireless sensor networks: Architecture – Sensor network scenario. Wireless HART – Existing Wireless Options: IEEE 802.15.4 - ISA 100 – Zigbee – Bluetooth – their relevance to industrial applications Reference Books: 1. Mackay, S., Wright,E., Reynders,D., and Park,J., “Practical Industrial Data Networks: Design, Installation and Troubleshooting”, Newnes Publication, Elsevier, 2004. 2. Buchanan,W., “Computer Busses: Design and Application”, CRC Press, 2000. 3. Bowden,R., “HART Application Guide”, HART Communication Foundation, 1999. 4. Bela G.Liptak, “Instrument Engineers’ Handbook, Volume 3 : Process Software and Digital Networks”, 4th Edition, CRC Press, 2011. 5. Berge, J., “Field Buses for Process Control: Engineering, Operation, and Maintenance”, ISA Press, 2004. 6. Lawrence (Larry) M. Thompson and Tim Shaw, “Industrial Data Communications”, 5th Edition, ISA Press, 2015. 7. NPTEL Lecture notes on, ”Computer Networks” by Department of Electrical Engg., IIT Kharagpur.
Credits: 3:0:0 17EI3019 MULTI SENSOR DATA FUSION
Course Objectives:
To impart the concepts multi sensor data fusion technique. To give an exposure about the data fusion algorithm To introduce the concepts of filter design Karunya University Course Outcomes: Understand the concept of Multi sensor data fusion Develop algorithms for data fusion Analyse the practical issues in estimation Classify the different types of advanced filtering concepts Use multi sensor data fusion technique for practical applications Design a Kalman filter Unit I - Sensors and sensor data - Use of multiple sensors - Fusion applications - The inference hierarchy -Output data - Data fusion model - Architectural concepts and issues - Benefits of data fusion - Mathematical tools used –Algorithms - Co-ordinate transformations - Rigid body motion – Dependability and Markov chains - Metaheuristics Unit II - Taxonomy of algorithms for multisensor data fusion - Data association - Identity declaration Unit III - Kalman filtering - Practical aspects of Kalman filtering - Extended Kalman filters - Decision level identify fusion - Knowledge based approaches Unit IV - Data information filter - Extended information filter - Decentralized and scalable decentralized estimation - Sensor fusion and approximate agreement - Optimal sensor fusion using range trees recursivelyDistributed dynamic sensor fusion Unit V - Tessellated – Trees - Graphs and function - Representing ranges and uncertainty in data structures Designing optimal sensor systems with in dependability bounds - Implementing data fusion system Reference Books 1. David L. Hall and Sonya AH McMullen, Mathematical techniques in Multisensor data fusion 2nd Edition, Artech House, Inc., Norwood, MA, March,2004. 2. R.R. Brooks and S.S. Iyengar, Multisensor Fusion: Fundamentals and Applications with Software, Prentice Hall Inc., New Jersey, 1998. 3. Arthur Gelb, Applied Optimal Estimation, The Analytic Sciences Corporation, M.I.T. Press, 2001. 4. James V. Candy, Signal Processing: The Model Based Approach, McGraw –Hill Book Company, 1987. 17EI3020 NON LINEAR CONTROL SYSTEMS Credits: 3:0:0 Course Objectives: To describe the non-linear systems theory and its components To construct a general systems model using inputs, throughputs and a feedback loop To understand the concept of stability of control system and methods of stability analysis Course Outcomes: Assess the advantages and disadvantages of the different nonlinear methods, Choose methods for analysis and design of a dynamical system Apply the methods for analysis and design of nonlinear control systems Assess the advantages and limitations of the resulting nonlinear control system Analyze the stability of non linear systems Evaluate the importance of sliding mode control
Unit I - Introduction to Linearization Process: Behavior of non – Linear systems – Common non linearites in control system –Investigation of non-linear systems- Common physical non- linearities -Feed back linearization, Fourier series method. Unit II - Describing Function: Fundamentals -Describing function of dead zone non-Linearity saturation non-
linearity, relay with dead zone non-linearity, blacklash non-linearity - model reference adaptive control, stable and unstable limit cycles Unit III - Phase Plane Analysis: Concept of phase plane analysis, construction of phase portraits – Using analytical method – Isoclines, Singular points – Stable, Unstable complex roots – Real roots – Limit cycles. Unit IV - Stability analysis: Lyapunov stability definitions – lyapunov stability theorem – lyapunov function for non linear system – krasovski method – variable gradient method- Lyapunov stability non-autonomous system. Unit V - Sliding Mode Control: Variable structures systems – basic concepts – sliding mode control algorithm –Karunya University sliding mode controller for a two link robot – reinforcement learning control – Q-learning –neural Q learning –temporal difference learning Reference Books 1. M. Gopal, “Digital Control and State Variable Methods, Convention and Intelligent Control System”, Mc Graw Hill Inc., New Delhi, Third Edition, 2009. 2. Katsuhiko Ogata, “Modern Control Engineering”, Prentice Hall Inc., 2001 3. John K Khali, ”Non Linear Automatic Control”, Mc Graw Hill Inc., 2001 17EI3021 ROBUST CONTROL Credits: 3:0:0 Course Objectives To introduce norms, random spaces and robustness measures To understand H2 optimal control and estimation techniques To introduce Hinfinity optimal control techniques Course Outcomes Understand the structured and unstructured uncertainty of robustness. Design a H2 optimal controller and to implement kalman Bucy filter . Design a H-Infinity optimal control using Riccati and LMI Approach. Synthesis the Robust Controller and small gain theorem. Implement a robust Controller for CSTR and Distillation Column. Understand synthesis techniques for robust controllers and illustrate through case studies Unit I - Introduction: Norms of vectors and Matrices – Norms of Systems – Calculation of operator Norms – vector Random spaces- Specification for feedback systems – Co-prime factorization and Inner functions –structured and unstructured uncertainty- robustness Unit II - H2 Optimal Control: Linear Quadratic Controllers – Characterization of H2 optimal controllers – H2 optimal estimation-Kalman Bucy Filter – LQG controller Unit III - H-Infinity Optimal Control-Riccatti Approach: Formulation – Characterization of H-infinity suboptimal controllers by means of Riccati equations – H-infinity control with full information – Hinfinity estimation Unit IV - H-Infinity Optimal Control -LMI Approach: Formulation – Characterization of H-infinity suboptimal controllers by means of LMI Approach – Properties of H-infinity sub-optimal controllers – H-infinity synthesis with pole- placement constraints Unit V - Synthesis of Robust Controllers & Case Studies: Synthesis of Robust Controllers – Small Gain Theorem – D-K –iteration- Control of Inverted Pendulum- Control of CSTR – Control of Aircraft – Robust Control of Second-order Plant- Robust Control of Distillation Column
Reference Books
1. U. Mackenroth “Robust Control Systems: Theory and Case Studies” , Springer International Edition, 2010. 2. J. B. Burl, “ Linear optimal control H2 and H-infinity methods” , Addison W Wesley, 1998 3. D. Xue, Y.Q. Chen, D. P. Atherton, "Linear Feedback Control Analysis and Design
Credits: 3: 0: 0 17EI3022 PROCESS MODELLING AND SIMULATION
Course Objectives:
Understand the concepts of Process Modelling. Analyze lumped and distributed parameter models Introduce grey box models and Empirical models Karunya University Course Outcomes: Understand the need for Process Modelling. Classify the different types of Models Describe lumped and distributed parameter models Apply grey box models and Empirical Models Examine the solutions for lumped parameter models Comprehend finite element and finite volume methods Unit I - Introduction to Modelling : a systematic approach to model building- classification of models Conservation principles- thermodynamic principles of process systems. Unit II - Development of steady state models: lumped parameter systems- Dynamic models: lumped parameter systems- distributed parameter systems Unit III - Development of grey box models: Empirical model building- Statistical model calibration and validation- Population balance models. Unit IV - Solution strategies for lumped parameter models: Stiff differential equations- Solution methods for initial value and boundary value problems- Euler’s method- R-K method- finite difference methods-Solving the problems using MATLAB. Unit V - Solution strategies for distributed parameter models: Solving parabolic, elliptic and hyperbolic-partial differential equations-Finite element and finite volume methods. Reference Books: 1. K. M. Hangos and I. T. Cameron, “Process Modelling and Model Analysis”, Academic 2. Press, 2001. 3. B. Wayne Bequette, “Process control: modeling, design, and simulation”, Pearson 4. Education Inc., 2003. 5. Singiresu S. Rao, “Applied Numerical Methods for Engineers and Scientists” Prentice Hall, 6. Upper Saddle River, NJ, 2001 17EI3023 ADVANCED PROCESSOR FOR CONTROL AND AUTOMATION Credits : 3:0:0 Course Objectives: To Learn Recent Trends in Advanced Microcontroller Applications. To Learn Microcontroller Implementation for Control Applications To Understand Programming with 8 and 32 bit Microcontrollers. Course Outcomes: Identification of various Processors and Understanding of their On Chip Peripherals and Functions. Knowledge on Predict the Suitable Processor for the Required Applications for Control Automation. Solving problems using instruction set of various processor Design and Development of Interfacing Circuits for Microcontroller based Applications. Recognize suitable processors/controllers for real time applications Appraise the use of Advanced Processors by Interfacing Sensors and Actuators for real Time Automation.
Unit I - 8051 Microcontroller: Overview of 8 bit Microcontroller – General Architecture, Selection, On Chip resources, – Memory Organization–Addressing Modes – Instruction Set – I/O Ports-–Counters and Timers –
Interrupt – UART – Analog to Digital Converter – Relay Interfacing – Temperature Sensor Interfacing.
Unit II - AVR Microcontroller: Introduction - Architecture- Hardware Components- I/O Interfacing-Serial
Communication-Timer/Counter- Interrupt- Pulse Width Modulation-Drive speed control-Throttle Angle Control –
On Chip ADC-Air Flow Rate Sensor Interfacing
Unit III - Arm Processor: Arcon RISC Machine – Architectural Inheritance – Core & Architectures - ARM Karunya University Programmer’s Model – CPU Registers – Pipeline - Interrupts – Memory Organization - ARM processor family –Coprocessors - Instruction set – Thumb instruction set – Instruction cycle timings-Case Study: Digital Cruise Control Unit IV - Raspberry Pi Module: Onboard Processor – Linux OS - Integrated Development EnvironmentProgramming with Raspbian- Interfacing: I/O Devices – I2C Device – Sensors – Serial Communication-Case Study: Onboard Diagnostic System. Unit V - Blackfin Processor: Core Architecture- Memory Structure – Memory Port Flash Control– Addressing Unit – Sequencer - Event Handling- Data Files - Timer Operation - Interrupt Processing- Hardware Errors Exception Handling – JTAG Test and Emulation-Case Study: Onboard Diagnostic System. Reference Books 1. Rajkamal, “Microcontroller Architecture, Programming, Interfacing and Systems Design”, Pearson Education India, 2009. 2. Kenneth Ayala, “The 8051 Microcontroller – Architecture, Programming & Application”, 2nd Edition, Thomson Delmar Learning, 2004 3. Muhammad Ali Mazidi, “The 8051 Microcontroller and Embedded Systems using Assembly and C”, Prentice Hall, 2000. 4. Muhammad Ali Mazidi, “The AVR Microcontroller and Embedded Systems using Assembly and C”, Prentice Hall, 2011. 5. Steve Furber, “ARM System On-Chip Architecture”, 2nd Edition, Pearson Education, 2009. 6. Eben Upton, “Raspberry Pi User Guide”, 3rd Edition, Wiley, 2016 7. Woon Seng Gan, Sen M Kuo, “Embedded Signal Processing with Micro Signal Architecture” January 2007, Wiley-IEEE Press. 17EI3024 ADVANCED EMBEDDED SIGNAL PROCESSING Credits: 3:0:0 Course Objective: To develop skills for understanding the requirements of the Real Time Digital Signal Processing Algorithms. To develop skills to comprehend the Digital Signal Processor and FPGA Architectures. To develop skills to implement the signal processing algorithms using the Digital Signal Processors and FPGA. Course Outcome: Acquire the knowledge & concepts of basic digital signal processing techniques. Comprehends the Architectural features of Digital Signal Processors and FPGA . Applies the features of DSP and FPGA Program to achieve speed in Digital Signal Processing Algorithms. Analyze the Data path Architectures of DSP and FPGA. Design the program for Signal Processing Algorithms for both DSP and FPGA. Contrast the difference between Signal Processing Algorithm implementation in DSP and FPGA. Unit I - Overview Of Digital Signal Processing And Applications: Signals and their origin– Sampling theorem and discrete time system – Convolution – DSP in the sample and transform domain– Fast Fourier Transform –Digital Filters – Multi–rate Signal Processing Unit II - Introduction To Programmable DSP: Multiplier and Multiplier Accumulator –Modified Bus structures and Memory Access schemes in P – DSPs – Multiple Access Memory – Multi – ported Memory – VLIW Architecture–Pipelining –Special Addressing Modes in P –DSPs – On – Chip Peripherals
Unit III - Architecture Of TMS320C5x: Introduction – Bus Structure – Central Arithmetic Logic Unit – Auxiliary Register ALU – Parallel Logic Unit – Program controller – On Chip Peripherals –Assembly Language Syntax – Addressing Modes – Normal pipeline operation, Convolution using MAC, MACD instructions – FIR filter implementation Unit IV - Architecture of TMS320C54x And TMS320C6x: Architecture of TMS320C54X- Bus Structure – Data Path - Normal Pipe line operation – FIR filter implementation – VLIW Architecture of TMS320C6X- Bus Structure – Data path – Normal Pipe line operation – Serial/Partially Parallel/ Fully Parallel FIR filter Karunya University implementation. Unit V - DSP With FPGA: FPGA Technology pros and cons behind FPGA and programmable signal processors, FPGA structure, Implementation of basic MAC Unit, FIR filter, IIR filter in FPGA Reference Books 1. Venkataramani B & M.Bhaskar, “Digital Signal Processor”, TMH, New Delhi, 2003. 2. Meyer U – Baese “Digital Signal Processing with Field Programmable GateArrays”, Spinger, New York, 2003. 3. Michael John Sabastian Smith, “ Application Specific Integrated Circuits”,Pearson Education,USA,2005. 4. Stephen Brown, ZvonkoVranesic, “Fundamentals of Digital Logic with VHDLDesign”, McGraw – Hill Higher Education, New Delhi – 2005. 17EI3025 PROGRAMMABLE DEVICES FOR INDUSTRIAL AUTOMATION Credits: 3:0:0 Course Objectives To expose the students to the fundamentals of sequential system design, Asynchronous circuits, To teach Programmable Device architecuture and programming To introduce hardware descriptive lanugages for industrial automation Course outcome: Acquire the knowledge & concepts of basic Sequential circuit design. Comprehends the Architectural features of PLDs and FPGA. Applies the features of PLDs to design synchronous circuits. Analyze the FPGA Architectures for process automation. Develop program for real time applications using descriptive languages. Choose FPGA architectures for industrial automation applications. Unit I - Sequential Circuit Design: Analysis of Clocked Synchronous Sequential Networks (CSSN) Modelling of CSSN – State Stable Assignment and Reduction – Design of CSSN – ASM Chart – ASM Realization. Analysis of Asynchronous Sequential Circuit (ASC) – Flow Table Reduction – Races in ASC – State Assignment Problem and the Transition Table – Design of ASC – Static and Dynamic Hazards –Essential Hazards – Designing Vending Machine Controller. Unit II - Synchronous Design Using Programmable Devices: Programming Techniques - Re-Programmable Devices Architecture- Function blocks, I/O blocks, Interconnects, Realize combinational, Arithmetic, Sequential Circuit with Programmable Logic Devices. Unit III - Reconfigurable architecture and programming: PLDs – Xilinx FPGA – Xilinx 2000, Xilinx 3000, Xilinx 4000- Altera Max – ACT-implementation of combinational and sequential circuits with FPGA and PLDs. Process automation –flow, pressure and level control using FPGA Unit IV - High level descriptive languages and programming- VHDL and VERILOG: Design flow process –Software tools – Data objects – Data types – Data operators – Entities and Architectures – Component declaration and instantiation. Concurrent signal assignment – conditional signal assignment – selected signal assignment –concurrent and sequential statements – Data flow, Behavioral and Structural Modeling - Test bench –Verilog: Design methodology – Modules – Ports – Basic concepts – Operators – Nos. specification – Data types –Arrays – Parameters – Gate delays – Operator types – Conditional statements – Multiway branches - Loops Switch – Modeling elements.
Unit V - FPGA for industrial automation
Home automation-motor control- industrial networking with Xilinx devices- machine vision camera solutionsMonitoring processes and equipment- Automated system shut-down - Detecting dangerous situations.
Karunya University
Reference Books:
1. Charles H. Roth Jr., “Digital Systems design using VHDL”, Cengage Learning, 2010. 2. Samir Palnitkar, “Verilog HDL”, Pearson Publication, II Edition. 2003. 3. Muhammed Abdelati, “Modern Automation Systems”, University Science Press, 2009 4. Stephen Brown and Zvonk Vranesic, “Fundamentals of Digital Logic with VHDL Deisgn”, Tata McGraw Hill, 2002 5. Stephen Brown and Zvonk Vranesic, “Fundamentals of Digital Logic with verilog Deisgn”, Tata McGraw Hill, 2007 6. Donald G. Givone, “Digital principles and Design”, Tata McGraw Hill 2002.
17EI3026 FPGA CONTROL DESIGN LABORATORY
Credits: 0:0:2 Course Objective:
To illustrate theoretical concepts and to give the students the opportunity to build and test the digital systems. To learn the use of the Xilinx ISE tool for designing and implementing digital systems on FGPA. To implement circuits for control applications.
Course Outcome:
Compare different FPGA architectures. Write hardware descriptive language program to digital circuits Design combinational and sequential digital systems using FPGA Analyze various control process and implement the same in FPGA Identify tool for FPGA implementation Implement and test control applications using FPGA The faculty conducting the laboratory will prepare a list of 12 experiments and get the approval of HOD/Director and notify it at the beginning of each semester.
17EI3027 EMBEDDED VIRTUAL INSTRUMENTATION LABORATORY Credits: 0:0:2 Course Objective:
To strengthen the knowledge of Virtual Instrumentation. To understand the concept of signal processing To introduce the concept of Data Acquisition.
Course Outcomes:
Identify virtual instrumentation representation for simple circuits Choose VI to develop real time applications Apply block diagram concept for developing simple digital circuits Design embedded applications using VI Analyze various embedded algorithms and implement the same using VI Specify and develop control system methods using VI The faculty conducting the laboratory will prepare a list of 12 experiments and get the approval of HOD/Director and notify it at the beginning of each semester.
17EI3028 EMBEDDED AUTOMOTIVE SYSTEMS
Credits: 3:0:0
Course Objectives:
To Understand the Current Trends in Automobiles To Understand basic Sensor Arrangements and its Types To Understand the Embedded Processors
Course outcomes:
Summarize the Automobile systems and the Requirements of Electronic Sensors and Actuators. Identification of Suitable Sensors and Design the Automotive Electronics for Real Time Applications. Modeling of Automotive Systems and Diagnostic Tools to Test and Calibrate the System Parts. Interpretation of Automobile Concepts and Practice the Control Systems for Real Time Automotive Applications. Predict the Advance Control Systems in order to improve the Engine Performance and Control. Karunya University Evaluation of Automotive Systems by Implementing Advanced Communication Systems like GLS, GPSS, GMS Unit I - Trends in Automobile – Electronic Engine Management systems: Sensors – ECU – Actuators –Electronic Dashboard Instruments: Information gauges – Displays – Onboard Diagnostic Systems: Fault Code Display – DFI Oxygen sensor Test – Switch Test Series – Engine Data Display. Unit II - Security, Warning Systems – Vehicle Motion Control: Cruise Control – Antilock Breaking –Electronic Suspension Control – Electronic Steering Control – Sensor, Actuators Interfacing: Airflow rate Sensor – Crankshaft Angular position Sensor – Throttle Angle Sensor – Temperature Sensor – Exhaust Gas Recirculation Actuator – Electronic Motors. Unit III - Basic Sensor Arrangements – Sensor types – Electronic Ignition Systems: Constant Dwell – Constant Energy – Hall Effect Pulse Generator – Dwell Angle Control – Closed Loop Dwell – Capacitor Discharge Ignition. Unit IV - Solid State Ignition System: Triggering – Switching Devices – Digital Engine Control System –Distributor Less Ignition – Integrated Engine Control: Combined Ignition – Fuel management – Exhaust Emission Control. Unit V - Automotive Embedded Systems – PIC – Free Scale Microcontrollers – Recent Advance like GLS, GPSS, GMS. Reference Books 1. William B. Riddens, “Understanding Automotive Electronics” , 5th Edition, Butterworth Hennimann Woburn, 6th Edition, 2003 2. Tom Denton, Automobile Electrical and Electronic Systems, Third Edition, Taylor & Francis, 2012 3. Jack Erjavec, “Automotive technology: System Approach, 5th edition, Delmar Cengage Learning, 2009. 4. Tom Weather Jr. & Cland C. Ilunter, “Automotive Computers and Control System” Prentice Hall Inc., New Jersey., 2001 5. Robert Bosch, “Automotive Electrics and Automotive Electronics: Systems & Components Networking & Hybrid Drive”, 5th edition, Springer, 2007 17EI3029 EMBEDDED BASED BIOMEDICAL SENSORS AND SIGNAL CONDITIONING Credits: 3:0:0 Course Objectives: To understand bioelectric amplifiers To discuss filter and circuits To introduce application of signal conditioning in biomedical field Course Outcomes: Identify the method to apply various signal conditioning circuits Set up an Interface circuit for bioelectric signals with embedded systems Construct the application of signal condition circuits for biomedical field. Design a biomedical real time system based on various sensor with embedded system Select the suitable microcontroller for system development Apply embedded concepts for biomedical applications
Unit I - Measurement system: Measurement systems – Significance of Measurements, Methods of
Measurements – Direct and Indirect Methods, Classification of Instruments –Deflection and Null Type,
Generalised Measurement System, Characteristics of Instruments – Static and Dynamic, Types of errors, Error
analysis, Units and Standards. Study of biological sensors in the human body and their basic mechanism of action.
Unit II - BioElectric Amplifier: Bioelectric amplifiers- General-purpose linear and non-linear electronic circuits typically found in industrial applications- Instrumentation amplifiers, Transducer bridge Amplifier.
Unit III - Analysis of filtering circuit: Frequency and time domain analysis of low pass, high pass, band pass, and band stop filters. Filter class- Frequency discriminators, oscillators, multivibrators - Amplifier selection for a variety of biomedical sensors, Wheatstone bridge design, Active filter design using standard approaches Karunya University Unit IV - Study of various transducer for biomedical applications: Transducers - Definition, Classification of transducers, Characteristics of transducers, types of Transducers – Temperature transducers, Displacement transducers, potentiometric, resistive strain gauges, inductive displacement, capacitive displacement transducer. Pressure transducer, Blood pressure measurement, measurement of intracranial pressure, LVDT transducers, capacitive and piezo-electric type. Biosensors, Unit V - Microcontroller based biomedical system development: Front-end analogue circuit design for EMG, ECG, EEG ,Front-end analogue circuit design for limb movement sensing, Power supply topologies for biomedical instruments, Microcontroller based ECG-continuous monitoring systems for pulse rate, temperature, B.P, Respiration. Reference Books 1. R. B. Northrop, “Analysis and Application of Analog Electronic Circuits to Biomedical Instrumentation”, 2nd ed., CRC Press, 2012. 2. J. D. Bronzino, “Biomedical Engineering Handbook”, 3rd ed.,CRC Press & IEEE Press, 2006. 3. Ramón Pallás-Areny, John G. Webster,”Sensors and Signal Conditioning”, 2nd ed., Wiley publishers, 2000. 17EI3030 MEMS TECHNOLOGY FOR EMBEDDED DESIGN Credits: 3:0:0 Course Objectives: To teach the students properties of materials , microstructure and fabrication methods. To teach the design and modeling of Electrostatic sensors and actuators. To teach the characterizing thermal sensors and actuators through design and modeling Course outcomes: Familiar with micro fabrication and materials Compare various sensors and actuators Develop embedded application based on MEMS Explain the features of NEMS device in real time applications Describe various medical application based on MEMS Distinguish various sensors and actuators depending on the application Unit I - Micro-Fabrication, Materials And Electro-Mechanical Conepts : Overview of micro fabrication –Silicon and other material based fabrication processes – Concepts: Conductivity of semiconductors-Crystal planes and orientation-stress and strain-flexural beam bending analysis-torsional deflections-Intrinsic stress- resonant frequency and quality factor. Unit II - Electrostatic Sensors And Actuation : Principle, material, design and fabrication of parallel plate capacitors as electrostatic sensors and actuators-Applications Unit III - Thermal Sensing And Actuation : Principle, material, design and fabrication of thermal couples, thermal bimorph sensors, thermal resistor sensors-Applications.
Unit IV - Piezoelectric Sensing And Actuation :Piezoelectric effect-cantilever piezo electric actuator modelproperties of piezoelectric materials-Applications. Piezoresistive sensors, Magnetic actuation
Unit V - Case Studies : Micro fluidics applications, Medical applications, Optical MEMS.-NEMS Devicesmultisensor module for embedded design with IOT- web based system
Reference Books
1. Chang Liu, “Foundations of MEMS”, Pearson International Edition, 2006. 2. Marc Madou , “Fundamentals of microfabrication”,CRC Press, 1997. 3. Boston , “Micromachined Transducers Sourcebook”,WCB McGraw Hill, 1998. 4. M.H.Bao “Micromechanical transducers :Pressure sensors, accelerometers and gyroscopes”, Elsevier, Newyork, 2000.
Karunya University 17EI3031 EMBEDDED PRODUCT DEVELOPMENT Credits: 3:0:0 Course Objectives: To strengthen the knowledge of Virtual Instrumentation. To understand the concept of signal processing To introduce the concept of Data Acquisition. Course Outcomes: Describe the recent trends in embedded systems design with understand the integration of customer requirements in product design. Identify structural approach to concept generation, creativity, selection and testing Design of Consumer specific product, its Reverse Engineering manufacture , economic analysis and product architecture. Develop an improved Employability and entrepreneurship capacity due to knowledge up gradation on recent trends in embedded systems design. Analyze an embedded concept towards a product development Develop an embedded based product for multi real time applications. Unit I - Concepts Of Product Development: Need for Product Development- Generic product Development Process Phases- Product Development Process Flows, Product Development organization structures-Strategic importance of Product Planning process –Product Specifications-Target Specifications-Plan and establish product specifications - integration of customer, designer, material supplier and process planner, Competitor and customer -Understanding customer and behavior analysis. Concept Generation, Five Step Method-Basics of Concept selection- Creative thinking –creativity and problem solving- creative thinking methods generating design concepts-systematic methods for designing –functional decomposition – physical decomposition –Product Architecture--changes - variety – component Standardization –example case study on Conceptual Design of DeskJet Printer as a product. Unit II - Introduction To Approaches In Product Development : Product development management establishing the architecture - creation - clustering –geometric layout development - Fundamental and incidental interactions - related system level design issues - secondary systems -architecture of the chunks - creating detailed interface specifications-Portfolio Architecture- competitive benchmarking- Approach – Support tools for the benchmarking process, trend analysis- Setting product specifications- product performance analysis -Industrial Design, Robust Design – Testing Methodologies. Unit III - Industrial Design : Integrate process design - Managing costs - Robust design –need for Involving CAE, CAD, CAM, IDE tools –Simulating product performance and manufacturing processes electronically –Estimation of Manufacturing cost-reducing the component costs and assembly costs – Minimize system complexity - Prototype basics - Principles of prototyping - Planning for prototypes- Economic & Cost Analysis Understanding and representing tasks-baseline project planning -accelerating the project, project execution. Unit IV - Development Based On Reverse Engineering : Basics on Data reverse engineering – Three data Reverse engineering strategies – Finding reusable software components – Recycling real-time embedded software based approach and its logical basics-Cognitive approach to program understated – Integrating formal and structured methods in reverse engineering – Incorporating reverse engineering for consumer product development-ethical aspects in reverse engineering.
Unit V - Developing Embedded Product Design : Discussions on Creating Embedded System
Architecture(with at least one Case study example: Mobile Phone /Adaptive Cruise Controller/ Robonoid about ) -Architectural Structures- Criteria in selection of Hardware & Software Components, product design by
Performance Testing, Costing, Benchmarking ,Documentation
Reference Books
1. George E.Dieter, Linda C.Schmidt, “Engineering Design”, McGraw-Hill International Edition,4th Edition, 2009, ISBN 978-007-127189-9 2. Karl T. Ulrich, Steven D Eppinger, "Effective Product Design and Development", Tata Mc Graw Hill, New Delhi, 2003, 3. Kevin Otto, Kristin Wood, “Product Design”, Indian Reprint 2004, Pearson Education, ISBN 9788177588217 Karunya University 4. Yousef Haik, T. M. M. Shahin, “Engineering Design Process”, 2nd Edition Reprint, Cengage Learning, 2010, ISBN 0495668141 5. Clive L.Dym, Patrick Little, “Engineering Design: A Project-based Introduction”, 3rd Edition, John Wiley & Sons, 2009. 17EI3032 ROBOTICS AND FACTORY AUTOMATION Credits: 3:0:0 Course Objectives To educate the fundamental concepts or robotics To educate on the robot drives and power transmission systems To educate vision system for robotics Course Outcomes Recall the concept of robotics Summarize building blocks of automation Describe different sensors for robotic applications. Analyze vision system for robotics. Identify any intelligent automation system Design ladder diagram for automation system Unit I - Fundamental concepts of robotics: History, Present status and future trends in Robotics and automation Laws of Robotics - Robot definitions - Robotics systems and robot anatomy - Specification of Robots - resolution, repeatability and accuracy of a manipulator. Robotic applications. Robot drives and power transmission systems: Robot drive mechanisms, hydraulic – electric – servomotor stepper motor - pneumatic drives, Mechanical transmission method - Gear transmission, Belt drives, cables, Roller chains, Link - Rod systems - Rotary-to-Rotary motion conversion, Rotary-to-Linear motion conversion, Rack and Pinion drives, Lead screws, Ball Bearing screws, End effectors – Types. Unit II - Sensors: Principle of operation, types and selection of Position& velocity sensors, Potentiometers, Encoders, Resolvers, LVDT, Tacho generators, Proximity sensors. Limit switches – Tactile sensors - Touch sensors - Force and torque sensors. Unit III - Vision systems for robotics: Robot vision systems, Illumination techniques, Image capture- solid state cameras – Image representation - Gray scale and color images, image sampling and quantization - Image processing and analysis –, Image data reduction – Segmentation - Feature extraction - Object Recognition- Image capturing and communication - JPEG, MPEGs and H.26x standards, packet video, error concealment- Image texture analysis. Unit IV - Transformations and kinematics: Matrix representation- Homogeneous transformation matrices - The forward and inverse kinematics of robots - D-H representation of forward kinematic equations of robots. Unit V - PLC: Building blocks of automation, Controllers – PLC- Role of PLC in Robotics& FA - Architecture of PLC - Advantages - Types of PLC - Types of Programming - Simple process control programs using Relay Ladder Logic and Boolean logic methods - PLC arithmetic functions. Factory automation: Flexible Manufacturing Systems concept - Automatic feeding lines, ASRS, transfer lines, automatic inspection - Computer Integrated Manufacture - CNC, intelligent automation. Industrial networking, bus standards, HMI Systems, DCS and SCADA, Wireless controls.
Reference Books
1. Richard D Klafter, Thomas A Chmielewski, Michael Negin, "Robotics Engineering – An Integrated Approach", Eastern Economy, Prentice Hall of India P Ltd., 2006.
2. Mikell P Groover et. al., "Industrial Robots - Technology, Programming and Applications", McGraw Hill,
New York, 2008. 3. Saeed B Niku ,”Introduction to Robotics Analysis, Systems, Applications ”’PHI Pvt Ltd, New Delhi,2003.
17EI3033 LINEAR SYSTEMS
Credits: 3:0:0 Course Objectives:
Karunya University To understand the state model of LTI (Linear time invariant) system. To give basic knowledge in obtaining decomposition of transfer function from state model. To understand the concepts of Controllability, Observability and Lyapunov stability analysis. Course Outcomes: Determine the state space representation of any system Calculate the solution of state equation Design estimators for prediction of data for control system design. Analyse the system whether it is controllable and observable. Perform stability analysis of the systems. Summarise the concept of control theory for linear systems. Unit I - State model for linear time invariant systems: State space representation using physical - Phase and canonical variables – Diagonalization-Solution of state equation - State transition matrix Unit II - Analysis of linear time invariant systems: Transfer function from state model - Transfer matrix Decomposition Methods – State space representation of linear time invariant discrete time systems Unit III - Solution of discrete time state equation: Discretization of continuous time state equations - Eigen Values and Eigen Vectors – diagonalization Unit IV - State Variable Design: Concepts of Controllability and Observability – Pole Placement by State Feedback- Observer Systems. Unit V - Lyapunov’s Stability Analysis: Introduction-Lyapunov stability criterion-Direct Method- Methods of constructing Lyapunov functions for Nonlinear Systems Reference Books 1. Katsuhiko Ogata, “Modern Control Engineering”, Prentice Hall of India Private Limited, New Delhi, 4th Edition, 2002. 2. Nagrath I.J, & Gopal M, “Control System Engineering”, New Age International Publishers Limited, New Delhi, 5th Edition, 2007. 3. Nise S. Norman, “Control Systems Engineering”, John Wiley & Sons Inc, New Delhi, 3rd Edition, 2000. 4. John J. D'Azzo, Constantine H. Houpis, “Linear Control System Analysis and Design”, CRC Press, USA , 5 th Edition, 2003. 5. Shankar P. Bhattacharyya, Aniruddha Datta, Lee H. Keel, “Linear Control Theory: Structure, Robustness And Optimization” CRC Press, USA, 2009.
LIST OF COURSES
Course Code Nameof the Course Credits
16EI2001 Digital Control Systems 16EI2002 Sensors and Data Acquisition
3:1:0 3:0:0 Karunya University 16EI2003 Virtual Instrumentation and Data Acquisition Laboratory 0:0:1 16EI2004 Automotive Electronics 3:0:0 REVISED VERSION COURSES Course Code Version Nameof the Course Credits 14EI2001 1.1 Sensors and Transducers 3:0:0 14EI2002 1.1 Sensors and Transducers Laboratory 0:0:2 14EI2003 1.1 Electrical Measurements 3:0:0 14EI2004 1.1 Simulation Laboratory 0:0:2 14EI2005 1.1 Control System 3:1:0 14EI2006 1.1 Electrical Measurements and Machines Laboratory 0:0:2 14EI2007 1.1 Control Systems Laboratory 0:0:2 14EI2008 1.1 Industrial Instrumentation 3:0:0 14EI2009 1.1 Process Dynamics and Control 3:0:0 14EI2010 1.1 Industrial Instrumentation Laboratory 0:0:2 14EI2011 1.1 Electronic Instrumentation 3:0:0 14EI2012 1.1 Logic and Distributed Control Systems 3:0:0 14EI2013 1.1 Industrial Data Communication and Networks 3:0:0 14EI2014 1.1 Process Control Laboratory 0:0:2 14EI2015 1.1 Logic and Distribution Control Systems Laboratory 0:0:2 14EI2017 1.1 Biomedical Instrumentation 3:0:0 14EI2018 1.1 Automotive Instrumentation 3:0:0 14EI2019 1.1 Analytical Instrumentation 3:0:0 14EI2020 1.1 Instrumentation and Control in Petrochemical Industries 3:0:0 14EI2021 1.1 Instrumentation and Control in Paper Industries 3:0:0 14EI2022 1.1 Instrumentation and Control in Iron and Steel Industries 3:0:0 14EI2023 1.1 Opto-Electronics and Laser Based Instrumentation 3:0:0 14EI2024 1.1 Power Plant Instrumentation 3:0:0 14EI2025 1.1 Modern Control Techniques 3:0:0 14EI2026 1.1 Strength of Machine Elements 3:0:0 14EI2032 1.1 Flexible Manufacturing Systems 3:0:0 14EI2033 1.1 Vibration Analysis 3:0:0 14EI2035 1.1 Human-Robot Systems and Interaction 3:0:0 14EI2036 1.1 Environmental Instrumentation 3:0:0 14EI2038 1.1 Instrumentation for Agriculture 3:0:0 14EI2039 1.1 Instrumentation and Control for Avionics 3:0:0 14EI2040 1.1 Ultrasonic Instrumentation 3:0:0 14EI2041 1.1 Measurements and Instrumentation 3:0:0 14EI2042 1.1 Advanced Control Theory 3:0:0
14EI2043 1.1 Virtual Instrumentation 3:0:0
14EI2044 1.1 PLC and Automation 3:0:0
14EI2045 1.1 Artificial organs and Rehabilitation Engineering 3:0:0
14EI2046 1.1 Process Control for Food Engineers 14EI2047 1.1 Process Control Laboratory for Food Engineers 3:0:0 0:0:2
14EI2048 1.1 Instrumentation and Control Systems
3:0:0 Karunya University 14EI3002 1.1 Instrumentation 3:0:0 14EI3003 1.1 Advanced Process Control 3:0:0 14EI3004 1.1 Industrial Instrumentation and Process Control Laboratory 0:0:2 14EI3005 1.1 Advanced Control Systems 3:0:0 14EI3006 1.1 Discrete Control System 3:0:0 14EI3007 1.1 Intelligent Controllers 3:0:0 14EI3008 1.1 Optimal Control Theory 3:0:0 14EI3009 1.1 Industrial Instrumentation 3:0:0 14EI3010 1.1 Control System Design 3:0:0 14EI3011 1.1 Virtual Instrumentation laboratory 0:0:2 14EI3012 1.1 Embedded Control Systems Laboratory 0:0:2 14EI3014 1.1 Industrial Automation 3:0:0 14EI3015 1.1 System Identification and Adaptive Control 3:0:0 14EI3016 1.1 SCADA systems and Applications 3:0:0 14EI3017 1.1 Design of Linear Multivariable Control Systems 3:0:0 14EI3018 1.1 Piping and Instrumentation 3:0:0 14EI3019 1.1 Embedded Instrumentation 3:0:0 14EI3020 1.1 Networks and Protocols for instrumentation and control 3:0:0 14EI3022 1.1 Design of Embedded Control System 14EI3025 DESIGN OF EMBEDDED CONTROL SYSTEM 14EI3025 DESIGN OF EMBEDDED CONTROL SYSTEM
3:0:0 14EI3023 1.1 Advanced Processors for control and automation 3:0:0 14EI3028 1.1 Embedded Virtual Instrumentation Laboratory 0:0:2 14EI3029 1.1 Embedded Automotive Systems 3:0:0 14EI3030 1.1 Automotive Sensors and Intelligent Systems 3:0:0 14EI3031 1.1 Automotive Protocols and Telematics 3:0:0 14EI3033 1.1 Biomedical sensors and signal conditioning 3:0:0 14EI3038 1.1 Physiological Control Systems 3:0:0 14EI3039 1.1 Medical Instrumentation 3:0:0 14EI3040 1.1 Bio Virtual instrumentation 3:0:0 14EI3041 1.1 Hospital Management System 3:0:0 14EI3042 1.1 Cognitive technology for biomedical engineers 3:0:0 14EI3044 1.1 Embedded Based Medical Instrumentation Laboratory 0:0:2 14EI3045 1.1 Diagnostics and therapeutic Equipments Laboratory 0:0:2 14EI3046 1.1 Medical Imaging Techniques 3:0:0 14EI3048 1.1 Clinical Instrumentation 3:0:0 14EI3049 1.1 Medical Devices And Safety 3:0:0 14EI3051 1.1 Medical Sensors and wearable devices 3:0:0
14EI3052 1.1 Rehabilitation Engineering 14EI3054 1.1 Safe Biomechanics 3:0:0 3:0:0
14EI3055 1.1 Medical Diagnostics And Therapeutic Equipments 14EI3056 1.1 Limb prosthetics 14EI3057 1.1 Industrial electronics and instrumentation 14EI3058 1.1 Linear systems 14EI3059 1.1 Transducers and Actuators 3:0:0 3:0:0 3:0:0 3:0:0 3:0:0
14EI3060 1.1 Automated Test and Measurement
3:0:0 Karunya University 14EI3061 1.1 Remote Sensing and Control 3:0:0 14EI3063 1.1 Robot Programming 3:0:0 14EI3064 1.1 Kinematics and Dynamics of Robot 3:0:0 14EI3065 1.1 Advanced Instrumentation and Process Control for Food Engineers 3:0:0 14EI3066 1.1 Sensors and Data Acquisition Lab 0:0:2 14EI3067 1.1 Transducer Engineering 3:0:0 16EI2001 DIGITAL CONTROL SYSTEMS Credits: 3:1:0 Pre Requisite: 14EI2005 Control System Course Objective: • To introduce the concepts of system analysis using Z transforms. • To equip with the basic knowledge of digital process control design. • To study the stability analysis of digital control system Course Outcome: • Use Z transforms to analyse Discrete Systems. • Design controllers for a digital process. • Test the Stability of Discrete Systems. Need for digital control, Configuration of the basic digital control scheme, Principles of signal conversion, Basic discrete time signal, Z transform, Modified Z transform, Stability Analysis - Analysis Of Digital Control, Frequency Response, Stability on the z-Plane and the Jury stability criterion, Sample and hold systems , Digital Controller - Z domain description of sampled continuous time plants, Z domain description of systems with dead time, Implementation of digital controllers, Digital Algorithms - Design of Digital Control Algorithms, Z plane specifications of control system design, Digital compensator design using frequency response plots, State description of sampled continuous time plants, Structure realization of systems, State transition matrix, Controllability and Observability, Solution of state difference equations. References 1. Gopal M, “Digital Control and State variable Methods”, Tata McGrawHill, New Delhi, 2003. 2. Ogata, “Discrete Time Control Systems”, Prentice– hall Of India, New Delhi 2008. 3. Gene F. Franklin, J. David Powell, “Digital control of dynamic systems”, Pearson Education Limited, New Delhi,2002. 4. Richard C. Dorf, Robert H. Bishop, “Modern control systems,” Pearson Education inc, New Delhi, 2008. 5. Isermann R ‘Digital Control Systems’, Vol. I & II, Narosa Publishing, 2014.
Credits: 3:0:0 16EI2002 SENSORS AND DATA ACQUISITION
Course Objective:
To deal with basics concepts for selection of sensors and the signal conditioning necessary to include these in a data acquisition system. To investigate the analogue to digital and digital to analogue conversion principles and their Karunya University practical applications for data acquisition and control. To learn about the selection of output drivers and devices Course Outcome: Demonstrate a critical understanding of elements of signal conditioning necessary for different types of sensors. Describe and evaluate the operation of analogue to digital and digital to analogue converters. Critically evaluate and select appropriate techniques and devices for realizing a data acquisition system. Sensors and transducers, signal conditioning circuits, Parameters of Data Acquisition Systems such as dynamic range, calibration, bandwidth, processor throughput, sample rate and aliasing, types and principles of Analogue to Digital Converters (ADC) and Digital to Analogue Converters (DAC), ADC specifications, resolution, accuracy, linearity, offset and quantization errors, time-based measurements and jitter, microprocessor interfacing, serial interfaces, multi-channel ADCs, internal microcontroller ADCs, Codecs, line drivers and receivers, high power output drivers and devices. References 1. Bentley, John P. Principles of Measurement Systems, 4:th edition, Pearson/Prentice Hall, 2005. 2. Jacob Fraden, Handbook of Modern Sensors – Physics , Design and Applications, Fourth Edition, Springer, 2010. 3. Data Acquistion Handbook, A Reference for DAQ and analog and digital signal conditioning, 3rd Edition, 2012. 16EI2003 VIRTUAL INSTRUMENTATION AND DATA ACQUISITION LABORATORY Credit: 0:0:1 Course Objective: To introduce the basics concepts of Virtual Instrumentation. To develop ability for programming in LabVIEW using structures, graphs and charts for system monitoring, processing and controlling To learn about the data acquisition and interfacing concepts using a state-of-the-art software platform such as National Instrument's LABVIEW. Course Outcome: Create, Edit and Debug Virtual Instruments Design a complete Data Acquisition System, Accommodate PC interfacing principles and Instrument Driver for Computer measurement and control.
Description:
This course enables the students to gain practical knowledge in programming techniques, data acquisition and interfacing techniques of virtual instrumentation and apply it to real time environment.
Credit: 3:0:0 16EI2004 AUTOMOTIVE ELECTRONICS
Course Objectives:
To understand the various automotive sensors and actuators. To understand engine cranking system and control. Karunya University To understand various driver assistance and safety systems. Course Outcomes: Select sensors and actuators for an automotive applications. State various engine control techniques and its requirement. Explain the procedure of integration of various components to create an automotive system. Basic sensor arrangement- Various sensors in vehicle, Actuators for vehicle, Control modes, Engine cranking system, Ignition system, Block diagram of starting system, Condition at starting, Construction and working of starter motor, Advance driver navigation and information system, Collision avoidance radar warning system, ABS, Electronic steering control and electronic suspension, Low tire pressure warning system, Insulated and earth return systems, Head light and side light, Trafficator, Electric fuel pump, Horn, Wiper system, Introduction to CAN, FLEXRAY, LIN, MOST protocols. References: 1. William. B. Ribbens, “Understanding Automotive Electronics”, Butterworth Heinemann Woburn, Newyork, 6th Edition, 2003. 2. James. D. Haldeman and Chase. D. Mitchell, “Diagnosis and troubleshooting of Automotive electric, electronic and computer systems”, Prentice Hall, New Jersey, 4th Edition, 2006. 3. James. D. Haldeman and Chase. D. Mitchell, “Automotive Electricity and electronics”, Prentice Hall of India, New Delhi, 2004. 4. P.L. Kohli, “Automotive Electrical Equipment”, Tata Mc Graw hill Education India Pvt. Ltd., New Delhi, 2008. 5. Joseph Heitner, “Automotive Mechanics”, Affiliated East-West Pvt. Ltd., 2nd edition, 2012. 14EI2001 SENSORS AND TRANSDUCERS Credits: 3:0:0 (Version 1.1) Course Objective: To learn the characteristics of sensors To provide knowledge on the principle and operation of different transducers. To introduce the application of sensors and transducers in the measuring system. Course Outcome: Determine the characteristics of various sensors and analyze them Use the principle of transducers to design measuring systems Suggest suitable sensors for a particular application Transducers - Definition, Classification of transducers, Characteristics of transducers, types of Transducers – Resistive, Inductive, Capacitive, Piezoelectric, Magnetic transducers, principle of operation, working, characteristics and applications, Miscellaneous sensors – Elastic, digital, chemical, fiber optic, MEMS.
References
1. Doebelin. E.O., “Measurement Systems Application and Design”, McGraw Hill
International, New York, 2007. 2. Renganathan. S., “Transducer Engineering”, Allied publishers Limited, Chennai, 2003. 3. Cooper W.D., “Electronic Instrumentation and Measurement Techniques”, Prentice Hall of India, New Delhi, 2003. 4. Sawhney A.K., “A Course in Electrical and Electronics Measurements and Instrumentation”, Eighteenth Edition, Dhanpat Rai and Sons, New Delhi, 2007. 5. Ian R Sinclair, “Sensors and Transducers”, Third Edition, Newnes, New Delhi, 2011. Karunya University 14EI2002 SENSORS AND TRANSDUCERS LABORATORY Credits: 0:0:2 (Version 1.1) Co-Requisite: 14EI2001 Sensors and Transducers Course Objective: To introduce the practical aspects of transducers and their characteristics. To impart knowledge in the signal conditioning circuitry for a transducer. To improve the skills in designing a measurement system. Course Outcome: Analyze the performance characteristics of various transducers and infer the reasons for the behavior. Design the signal conditioning circuitry for a measurement system. Critically analyze a measurement application and suggest suitable measurement methods. Description: This laboratory introduces the different transducers, their working and determination of their characteristics. List of experiments The faculty conducting the laboratory will prepare a list of 12 experiments and get the approval of HoD/Director and notify it at the beginning of each semester. 14EI2003 ELECTRICAL MEASUREMENTS Credits: 3:0:0 (Version 1.1) Pre Requisite: 14EE2001 Electric Circuits and Networks Course Objective: To introduce the fundamentals of electrical measurements. To understand the principle of instruments used for measuring electrical quantities. To learn the working of bridges and recording instruments. Course Outcome: Use the basics of electrical measurement to analyze the characteristics of instruments. Apply the knowledge of electrical instruments to measure electrical quantities. Select and design the bridge circuits for a specific application. Fundamentals Of Electrical Measurements-Functional Elements of an Instrument, Input– Output Configuration of Measurement Systems, Performance Characteristics of Instruments, Electromechanical DC Instruments - Galvanometers, PMMC Instrument, DC Ammeter and Voltmeter, Calibration of DC instruments, Electromechanical AC Instruments-Moving Iron Instrument, Thermoinstruments, Electrodynamometers in Power Measurements, Watt– hour meter, Power– factor meters, Instrument
Transformers, A.C. and D.C. Bridge Circuits, Four probe method of measuring electrical properties, Recording Instruments.
References
1. Cooper W.D., “Electronic Instrumentation and measurement techniques”, Prentice Hall of India, New Delhi, 2004. 2. Tumanski. S., “Principles of Electrical Measurement”, Taylor and Francis Group, Ny, 2006. Karunya University 3. Kalsi.H.S, “Electronics Instrumentation”, Tata McGraw Hill, New Delhi, 2009. 4. Golding E.W. and Widdis F.E., “Electrical measurements and measuring instruments”, Sir Issac Pitman and Sons Pvt., Ltd., 2001. 5. Laughton. M. A. and Warne. D. J., “Electrical Engineer's Reference Book” Sixteenth Edition, Newnes, 2003. 6. Horst Czichos, Tetsuya Saito, Leslie E. Smith, “Springer Handbook of Materials Measurement Methods”, Springer Science & Business Media, 2007. 14EI2004 SIMULATION LABORATORY Credits: 0:0:2 (Version 1.1) Co-Requisite: 14EE2001 Circuit Analysis and Networks, 14EC2002 Electronic circuits Course Objective: To familiarize simulation software to analyze electronic circuits. To introduce simulation software to learn signal operations To design virtual instruments to analyze real time signals. Course Outcome: Simulate simple electronic circuits using simulation software. Simulate signals and analyze them using simulation software Acquire real time signals and perform simple operations on them using simulation software. Description: This laboratory aims to introduce simulation software that enables the student to understand the theoretical concepts by simulating them. List of experiments The faculty conducting the laboratory will prepare a list of 12 experiments and get the approval of HoD/Director and notify it at the beginning of each semester. 14EI2005 CONTROL SYSTEM Credits: 3:1:0 (Version 1.1) Pre Requisite: 14MA2003, 14MA2004 Course Objective: • To introduce the fundamentals of mathematical representation of a system. • To gain knowledge on the concepts of time response and frequency response. • To understand the concepts of stability analysis.
Course Outcome:
• Obtain the transfer function of a system. • Determine the response of different order systems for various test inputs. • Analyse the stability of the system.
Introduction to Control Systems, Types, Effect of Feedback, Differential equation of Physical Systems, Transfer functions, Block diagram algebra, Signal Flow graphs, Time Response of Feed Back Control Systems, Step response of First and Second order systems , Time response specifications of Second order Systems, Concepts of Stability, Routh stability criterion, Root Locus Techniques, stability analysis using Bode Plots, Polar plots, Introduction to lead, lag and lead–lag compensating networks, Nyquist criterion, Concepts of State, State variable and State models for electrical systems, Solution of State Equations, P, PI, PID Controllers. Karunya University References 1. Nagarath .J and Gopal M., “Control Systems Engineering”, New Age International (P) Limited, Publishers, Fourth edition – 2005 2. Ogata .K “Modern Control Engineering”, Pearson Education Asia/ PHI, 4th Edition, 2002. 3. Benjamin C. Kuo and Farid Golnaagi, Wiley “Automatic Control Systems”, 8th Edition, 2009. 4. Joseph J Distefano “Feedback and Control System”, III et al., Schaum’s Outlines, TMH, 2nd Edition 2007. 5. Norman. S. Nise, “Control Systems Engineering”, Wiley, 6th Edition, 2011. 14EI2006 ELECTRICAL MEASUREMENTS AND MACHINES LABORATORY Credits: 0:0:2 (Version 1.1) Co-Requisite: 14EI2003 Electrical Measurements Course Objective: To expose the students to the operation of DC and AC machines To learn about calibration of electrical instruments and bridge circuits To introduce the working of special electrical machines. Course Outcome: Analyze the characteristics of DC and AC Machines. Calibrate electrical instruments and bridge circuits Perform experiments on special electric machines. Description: This laboratory enables the student to understand the operation of electrical machines, bridges and the methods of calibrating electric instruments List of experiments The faculty conducting the laboratory will prepare a list of 12 experiments and get the approval of HoD/Director and notify it at the beginning of each semester. 14EI2007 CONTROL SYSTEMS LABORATORY Credits: 0:0:2 (Version 1.1) Co-Requisite: 14EI2005 Control System Course Objective: • To introduce the concept of Mathematical Modelling. • To explore the methods of controller design. • To understand the design of the compensating circuits.
Course Outcome:
• Derive the mathematical model of a system. • Design a controller for a real time system.
• Design lead and lag compensating circuits.
Description:
This laboratory demonstrates the methods to derive the mathematical model of a system and design a controller for a practical system.
List of experiments
The faculty conducting the laboratory will prepare a list of 12 experiments and get the approval of HoD/Director and notify it at the beginning of each semester. Karunya University 14EI2008 INDUSTRIAL INSTRUMENTATION Credits: 3:0:0 (Version 1.1) Course Objective: To learn the principle of measurement of various industrial parameters. To know about the selection, calibration and installation of different instruments To explore the application of measuring instruments in various industries Course Outcome: Apply the knowledge of Instruments to design a simple Instrumentation system. Select suitable instrument for a given application. Develop methods to perform measurement of physical parameters. Pressure Measurement-Standards, Dynamic testing, High and Low pressure measurement, Flow Measurement - Pitot static tube, Yaw tube, Pivoted vane, Anemometer, Obstruction meters, Rotameters, Turbine meters, Positive Displacement meters, Electromagnetic flow meter, Drag force flow meter , Ultrasonic flow meters, Vortex, Shedding flow meters, Temperature Measurement-Thermal Expansion Methods, Thermoelectric sensors, Electrical Resistance Sensors, Junction Semiconductor Sensors, Radiation methods, Level Measurement, Density And Viscosity Measurement, Selection, Range, Installation, Calibration and Protection of instruments, Industrial Safety Standards. References 1. Doebelin E.O, “Measurement Systems: Application and Design”, McGraw Hill, New York, 2003. 2. Singh S K, “Industrial Instrumentation and Control”, Tata McGraw– Hill, New Delhi, 2004. 3. William C. Dunn, “Fundamentals of Industrial Instrumentation and Process Control”, McGraw–Hill, New Delhi, 2005. 4. Liptak B.G, “Process Measurement and Analysis,” Chilton Book Company, Radnor, Pennsylvania, 2003. 5. Walt Boyes, “Instrumentation Reference Book,” Butterworth Heinemann, United States, 2003. 14EI2009 PROCESS DYNAMICS AND CONTROL Credits: 3:0:0 (Version 1.1) Pre Requisite: 14EI2005 Control System
Course Objective:
• To equip the students with the knowledge of modelling a physical process. • To understand the design of various control schemes. • To analyse the effect of controllers in a given process.
Course Outcome:
• Derive the Mathematical Model of a physical system.
• Tune controllers for Optimum gain using various techniques. • Selection of suitable control schemes for a particular process.
Process Control System -Terms and objectives, Piping and Instrumentation diagram, Degrees of freedom, Modelling of simple systems ,Basic Control Actions - Continuous Controller Modes, Response of controllers for different test inputs, Selection of control modes, Controller Tuning - Optimum controller settings, Controller tuning Methods, Final Control Elements – Characteristics, Selection of control valves, Advanced Control Schemes - Multivariable process control, Interaction of control loops, Case Studies: Distillation column, Boiler drum level control, Heat Exchanger and chemical reactor control Karunya University References 1. Stephanopoulos, “Chemical Process Control”, Prentice Hall, New Delhi, 2003. 2. Coughanowr D.R., “Process Systems Analysis and Control”, McGraw Hill, Singapore,2008. 3. Curtis D .Johnson, “Process Control Instrumentation Technology, ”Prentice Hall , New Jersey, 2006. 4. Dale E. Seborg, Thomas F. Edgar, Duncan A. Mellichamp, “Process Dynamics and Control,” John Willey and Sons, Singapore, 2006. 5. Wayne Bequette B., “Process control: modeling, design, and simulation” Prentice Hall , New Jersey– 2003 6. Peter Harriott, “Process Control”, Tata McGraw Hill, New Delhi, 2008. 14EI2010 INDUSTRIAL INSTRUMENTATION LABORATORY Credits: 0:0:2 (Version 1.1) Co-Requisite: 14EI2008 Industrial Instrumentation Course Objective: To gain the knowledge of the working of Industrial Instruments To learn the methods of Calibration for Instruments. To understand the operation of Instrumentation Circuits. Course Outcome: Use simple Industrial Instruments to measure physical quantities. Perform Calibration of Instruments. Design Instrumentation Circuits for measurement systems. Description: This laboratory introduces the operation of industrial instruments, their calibration and design of instrumentation circuits. List of experiments The faculty conducting the laboratory will prepare a list of 12 experiments and get the approval of HoD/Director and notify it at the beginning of each semester.
14EI2011 ELECTRONIC INSTRUMENTATION
Credits: 3:0:0
Pre Requisite: 14EC2008 Linear Integrated Circuits
(Version 1.1)
Course Objective:
• To introduce the principle of analog electronic measuring instruments.
• To deal with the basic principle of digital instrumentation. • To gain knowledge on the concept of virtual instruments.
Course Outcome:
• Apply the knowledge of electronic instruments to measure analog quantities. • Implement digital instrumentation techniques for measurement. • Develop virtual instruments using simulation software.
Electronic Analog Instruments – Introduction, Amplified DC meter, AC voltmeters using rectifiers, True RMS voltmeter, Q meter, Vector impedance meter. Oscilloscope, display devices and recorders, Signal generators and analyzers, Digital Instruments-Digital Voltmeters and Multimeters, Simple frequency counter, time interval, Digital Displacement transducer, Virtual Instrumentation – Evolution, Architecture, Presentation and Control, Functional Integration, Programming Requirements, Conventional and Distributed Virtual Instrumentation, Virtual Instruments and Traditional Instruments, Advantages, Study of evolution and procedures in simulation softwares. Karunya University References 1. Cooper W.D., “Electronic Instrumentation and measurement techniques”, Prentice Hall of India, New Delhi, 2009. 2. Kalsi.H.S, “Electronics Instrumentation”, Tata McGraw Hill, 2010. 3. Bouwens A.J., Digital Instrumentation, McGraw Hill Ltd., USA, 2002. 4. Sumathi S and P. Surekha , “LabVIEW based Advanced Instrumentation Systems” Springer, 2007. 5. Oliver B.H., and Cage J.M., “Electronics Measurements and Instrumentation”, McGraw Hill, 2009. 6. David A Bell, “Electronic Instrumentation and measurements”, Prentice Hall of India, New Delhi, 2006. 14EI2012 LOGIC AND DISTRIBUTED CONTROL SYSTEMS Credits: 3:0:0 (Version 1.1) Pre Requisite: 14EI2009 Process Dynamics and Control Course Objective: • To provide the fundamentals of Data Acquisition system. • To introduce the concept of PLC and its Programming using Ladder Diagram. • To cover the basics of Distributed Control Systems Course Outcome: • Appreciate the significance of SCADA and DCS. • Develop ladder logic programs for real time applications. • Apply the knowledge of DCS and communication standards. Review of Computers In Process Control - Data loggers, Data Acquisition Systems (DAS), Direct Digital Control (DDC), Supervisory Control and Data Acquisition Systems (SCADA), Overview of PLC systems, PLC programming procedures, PLC Basic Functions, PLC Intermediate Functions Sequencer functions, Matrix functions, Alternate programming languages, Analog PLC operation, Design of interlocks and alarms, Distributed Control Systems (DCS)-Evolution, Architecture, Comparison, Local Control unit, Process Interfacing Issues, Redundancy concept, Communication facilities, Interfaces In DCS, General purpose computers in DCS
References
1. John.W. Webb, Ronald A Reis, “Programmable Logic Controllers - Principles and Applications”, Prentice Hall Inc., New Jersey, 2003. 2. Michael P Lukas, “Distributed Control System”, Van Nostrand Reinhold Co., Canada, 1986. 3. B.G. Liptak, “Instrument Engineers Handbook, Process control and Optimization”, CRC pressRadnor, Pennsylvania, 2006. 4. B.G. Liptak, “Process software and digital networks,” CRC press,Florida-2003. Karunya University 5. Curtis D. “Johnson Process control instrumentation technology,” Prentice Hall , New Jersey 2006. 6. Krishna Kant, “Computer-Based Industrial Control,“ PHI, New Delhi, 2004 7. Frank D. Petruzella, “Programmable Logic Controllers”, McGraw Hill, New York, 2004. 14EI2013 INDUSTRIAL DATA COMMUNICATION AND NETWORKS Credits: 3:0:0 (Version 1.1) Pre Requisite: 14EC2080 Communication Engineering Course Objective: To introduce the basic principles of networking To learn the serial communication standards To equip the students with relevant knowledge about network protocols Course Outcome: Appreciate the need for network protocols during data transmission and reception. Analyze the methods of communication Compare the different protocols used as Universal standards. Introduction and Basic Principles – Protocols, Physical standards, Modern instrumentation, Bits, Bytes and characters, Communication principles, Communication modes, Synchronous and Asynchronous systems, Transmission Characteristics, Data Coding, UART, Serial data communications interface standards, Balanced and unbalanced transmission lines, RS232,422,,423,449,485 interface standard, Introduction To Protocols - Flow control Protocols, BSC Protocols, HDLC, SDLC, Data communication for Instrumentation and Control, Industrial protocols, Local Area Networks, Wireless Instrumentation. References 1. John Park, Steve Mackay, Edwin Wright, “Practical Data Communications for Instrumentation and Control”, Elsevier Publications, 2003. 2. Stallings W. “High speed Networks TCP/IP and ATM Design Principles “ PHI ,2002. 3. Behrouz A. Forouzan“ Data Communication and Networking” , TMH, 2006. 4. Lawrence. M. Thompson , “Industrial Data Communications”, 4th Edition , ISA- 2007. 5. Edwin Wright “Practical Industrial Data Networks: Design, Installation and Troubleshooting”, Newnes-2004. 6. Tony.R. Kuphaldt, “Lessons in Industrial Instrumentation”, Creative Commons Attribution, 2015.
14EI2014 PROCESS CONTROL LABORATORY
Credits: 0:0:2
Co-Requisite: 14EI2005 Control System
(Version 1.1)
Course Objective:
To introduce the practical concepts of digital controllers. To demonstrate Data Acquisition in VI Karunya University To provide knowledge about controller design, simulation and implementation Course Outcome: Design and compare Digital Control Algorithms. Analyze the performance of a Process Demonstrate Data Acquisition in VI Description: This laboratory introduces the design procedure for digital controllers and their implementation of real time process. List of experiments The faculty conducting the laboratory will prepare a list of 12 experiments and get the approval of HoD/Director and notify it at the beginning of each semester. 14EI2015 LOGIC AND DISTRIBUTED CONTROL SYSTEMS LABORATORY Credits: 0:0:2 (Version 1.1) Co-Requisite: 14EI2012 Logic and Distributed Control Systems Course Objective: • To strengthen the knowledge of Programmable Logic Controllers • To introduce the concepts of SCADA • To gain hands on experience on Distributed Control Systems Course Outcome: • Write simple programs in Programmable Logic Controllers • Design control system using Programmable Logic Controllers • Use SCADA for real time applications Description: This laboratory introduces the basic concepts of PLC programming and Distributed Control systems using simulation software. List of experiments The faculty conducting the laboratory will prepare a list of 12 experiments and get the approval of HoD/Director and notify it at the beginning of each semester. 14EI2017 BIOMEDICAL INSTRUMENTATION Credits: 3:0:0 (Version 1.1) Course Objective: • To introduce the human anatomy and physiology and the physiological parameters. • To learn about the generation of physiological signals and their measurement. • To understand the fundamentals of biomedical instruments used for diagnosis and therapy.
Course Outcome:
• Appreciate the need for measuring physiological parameters in the human body. • Develop measuring systems to measure the physiological parameters.
• Use the diagnostic and therapeutic instruments for specific application.
Cell and its Electrical activity, Physiological systems viz., cardiovascular system, Nervous system, Respiratory system, Visual system, Muscular system, Electrodes and bioelectric signals: Bio electrodes, ECG, EMG, EEG and EOG, Measurement of physiological parameters: Blood flow, Blood pressure, Cardiac output, and Bio-chemical measurement: Blood pH, Blood pO2, Blood pCO2, Photometers. Therapeutic equipments and imaging techniques. Karunya University References 1. Khandpur. R. S., “Handbook of Biomedical Instrumentation”, Prentice Hall of India, New Delhi, 2003. 2. Cromwell, “Biomedical Instrumentation and Measurements”, Prentice Hall of India, New Delhi, 2007. 3. Arumugam.M. “Biomedical Instrumentation", Anuradha Agencies Publishers, Kumbakonam, 2006. 4. Joseph J. Carr and John M. Brown, “Introduction to Biomedical Equipment Technology”, Pearson Education India, Delhi, 2004. 5. Webster, “Medical Instrumentation – Application & Design,” John Wiley and sons Inc, Netherlands, 2009. 14EI2018 AUTOMOTIVE INSTRUMENTATION Credits: 3:0:0 (Version 1.1) Course Objective: • To introduce the application of electronics in the modern automobile. • To understand the latest communication protocols used in automobile industries. • To provide information about the automotive systems and the electronic accessories used in automobile. Course Outcome: • Analyze the use of instruments in automotive industry • Design instruments for automotive applications. • Use Communication protocols to perform advanced monitoring and control. Automotive Electrical And Electronics - Basic Electronics components and their operation in an automobile, Starting Systems, Charging Systems, Ignition Systems, Electronic Fuel Control, Advanced vehicle control systems, Embedded System Communication Protocols - Vehicle Communication Protocols, Introduction to CAN, LIN, FLEXRAY, MOST, KWP2000, Details of CAN, Embedded System In Control Of Automotive Systems - Engine management systems, Vehicle Safety System, Electronic Control of braking and traction, Electronic transmission control, Environmental tests for electronic control units. References 1. RobertBoschGmbh ,“BOSCH– Automotive Handbook”, 7thEdition,John Wiley & Sons, ISBN: 0470519363, 2008. 2. Denton.T, “Automobile Electrical and Electronic System”, Elsevier Butterworth–HeinemannPublications,3rd Edition,2004. 3. Knowles.D, “Automotive Electronic and Computer control Ignition Systems”, Prentice Hall,1988. 4. William.T.M, “Automotive Electronic System”,Elsevier Science,6th Edition,2003. 5. Kiencke,, Nielsen, “Automotive Control Systems” 2nd Edition.2005
Credits: 3:0:0 14EI2019 ANALYTICAL INSTRUMENTATION
(Version 1.1)
Course Objective:
• To introduce the principle of analytic instruments • To learn the concept of chromatography • To know the applications of environment monitoring instruments Karunya University Course Outcome: • Analyze the different types of analytic instruments • Develop instruments for clinical analysis. • Apply the concepts of Analytical Instruments for Environmental Monitoring Colorimetry And Spectrophotometry-Special methods of analysis, Beer–Lambert law, Colorimeters, UV, Vis spectrophotometers, Single and double beam instruments, Sources and detectors, IR spectrophotometers, Types,Attenuated total reflectance flame photometers, Atomic absorption spectrophotometers, Sources and detectors, FTIR spectrophotometers, Flame emission photometers, Chromatography - Different techniques, Gas chromatography, Detectors, Liquid chromatographs, Applications, High– pressure liquid chromatographs, Applications, Industrial gas analyzers and pollution monitoring instruments, Ph meters and dissolved component analyzers, Radio chemical and magnetic resonance techniques References 1. Khandpur. R. S., ‘Handbook of Analytical Instruments’, Tata McGraw Hill Publishing Co. Ltd., 2006. 2. Willard. H., Merritt, Dean. J. A., Settle. F. A., ‘Instrumental Methods of Analysis’, CBS publishing & distribution, 1995. 3. Robert D. Braun, ‘Introduction to Instrumental Analysis’, McGraw Hill, Singapore, 1987. 4. Ewing. G. W., ‘Instrumental Methods of Chemical Analysis’, McGraw Hill, 1992. 5. Skoog. D. A. and West. D. M., ‘Principles of Instrumental Analysis’, Holt, Saunders Publishing, 1998. 14EI2020 INSTRUMENTATION AND CONTROL IN PETROCHEMICAL INDUSTRIES Credits: 3:0:0 (Version 1.1) Course Objective: • To introduce the basic concepts of piping and instrumentation diagrams. • To gain knowledge on the Instruments involved petrochemical industries. • To learn about the control system in the subsystems of a petrochemical plant. Course Outcome: • Develop and interpret the piping and instrumentation diagrams of a system. • Appreciate the significance of Measurement in Petrochemical Industry. • Use the knowledge of control system design to control the subsystems. Piping and Instrumentation diagrams, Instrumentation and control in distillation columns, chemical reactors- Temperature and pressure control in batch reactors – Instrumentation and control in dryers: Batch dryers and Continuous dryers, heat exchangers -, evaporators - Types of evaporators, Measurement and control of absolute pressure, Density, Conductivity, Differential pressure and Flow, Effluent and Water Treatment
References
1. Béla G. Lipták. ‘Instrumentation in the Processing Industries: Brewing, Food, Fossil Power, Glass, Iron and Steel, Mining and Minerals, Nuclear Power, Paper, Petrochemical, Pharmaceutical’, Chilton Book Co., Reprint 2003 2. Considine D.M., ‘Process / Industrial Instruments and Control Handbook’, Fourthedition, McGraw Hill, Singapore, 1999. 3. Curtis D .Johnson,”Process control instrumentation technology,”Prentice Hall , New Karunya University Jersey, 2006. 4. Singh S K, “Industrial Instrumentation and Control”, Tata McGraw– Hill, New Delhi, 2004. 5. William C. Dunn, “Fundamentals of Industrial Instrumentation and Process Control”, McGraw–Hill, New Delhi, 2005. 14EI2021 INSTRUMENTATION AND CONTROL IN PAPER INDUSTRIES Credits: 3:0:0 (Version 1.1) Course Objective: • To describe the paper making process and the need for measurement at various stages. • To gain knowledge about the Instruments used in paper industries. • To learn about the control operations in paper industries. Course Outcome: • Appreciate the need of instrumentation and control in paper making. • Select suitable sensors for a given process • Develop a control system for the various operations in the paper industry. Description Of The Process -Raw materials, Pulping process, Chemical Recovery Process, Paper making process, Converting, Instrumentation - Measurements of Basis Weight, Density, Specific gravity, Flow, Level of liquids and solids, Pressure, Temperature, Consistency, Moisture, PH, Oxidation-Reduction potential, Graphic displays and alarms, Control Operations - Blow tank controls, Digester liquor feed pump controls, Brown stock water level control, Stock chest level control, Basis weight control, Dry temperature control, density and flow control, computer applications. References 1. B.G Liptak, ‘Instrumentation in Process Industries’, Chilton Book Company, 2003 2. Renganathan. S., “Transducer Engineering”, Allied publishers Limited, Chennai, 2003. 3. Cooper W.D., “Electronic Instrumentation and Measurement Techniques”, Prentice Hall of India, New Delhi, 2003. 4. Singh S K, “Industrial Instrumentation and Control”, Tata McGraw– Hill, New Delhi, 2004. 5. William C. Dunn, “Fundamentals of Industrial Instrumentation and Process Control”, McGraw–Hill, New Delhi, 2005. 14EI2022 INSTRUMENTATION AND CONTROL IN IRON AND STEEL INDUSTRIES Credits: 3:0:0 (Version 1.1)
Course Objective:
• To learn about the process of making steel from the raw materials. • To know the role of instrumentation in a steel industry • To deal with the control operations carries out at various stages
Course Outcome:
• Appreciate the use of instruments in steel making. • Suggest suitable sensor for a typical measurement.
• Develop control systems for the various operations.
Description of Process -Flow diagram and description of the processes, Raw materials preparation, Iron making, Blast furnaces, Stoves, Raw steel making, Basic Oxygen Furnace, Electric Furnace, Casting of steel: Primary rolling, Cold rolling and Finishing, Measurement of level, Pressure, Density, Temperature, Flow, Weight, Thickness and shape, Graphic displays and alarms, Control Systems - Blast furnace, Stove combustion control system, Gas and water controls in BOF furnace, Strand Casting mould Level control, Mould Level sensors, Ingot weight measuring system, Waste water treatment, computer applications: Model calculation and logging, Rolling Mill Control, Annealing Process Control, Center Utilities Dispatch Computer. Karunya University References 1. Béla G. Lipták. ‘Instrumentation in the Processing Industries: Brewing, Food, Fossil Power, Glass, Iron and Steel, Mining and Minerals, Nuclear Power, Paper, Petrochemical, Pharmaceutical’, Chilton Book Co., Reprint 2003 Original from the University of California. 2. Liptak B. G, Instrument Engineers Handbook, volume 2, Process Control,Third edition, CRC press, London, 1995. 3. Considine D.M, Process / Industrial Instruments and Control Handbook, Fourth edition, McGraw Hill, Singapore, 1993. 4. Steel Designers Handbook 1)Branko 2)Ron Tinyou 3) ArunSyamGorenc Seventh Edition First Indian Reprint 2006. 5. Singh S K, “Industrial Instrumentation and Control”, Tata McGraw– Hill, 2004. 14EI2023 OPTO-ELECTRONICS AND LASER BASED INSTRUMENTATION Credits: 3:0:0 (Version 1.1) Course Objective: To introduce the basic concepts of opto-electronics and optical fibers. To learn about the principle of fiber optic sensors. To deal with the fundamentals of lasers and its application for measurement. Course Outcome: Apply the knowledge of optical fibers for measurement. Suggest the methods to use a fiber optic sensor for measurement. Use lasers for industrial measurement and biomedical applications. Basics of Opto-electronics - Characteristics of optical radiation, Optical Sources and Detectors, Charge Coupled devices, Opto –couplers and their applications, Optical Fibre - Principle, Types, Fibre coupling, Fibre optic sensors , Lasers and Applications - Principle, Laser Rate Equation, Properties, Two, Three and Four level system, Resonator configuration, Q switching and Mode locking, Cavity dumping, Types of Lasers, Industrial applications, Holography, Medical applications References 1. Arumugam. M. “Fiber Optics and Laser Instrumentation", Anuradha Agencies Publishers, Kumbakonam, 2006. 2. Optical Fiber Communications: Principles And Practice, John M. Senior, Pearson Education, 2006. 3. G. Keiser, ‘Optical Fibre Communication’, McGraw Hill, . 4. Ghatak A.K. and Thiagarajan K, Optical Electronics Foundation book , TMH, Cambridge University Press, 1989.
5. Wilson and Hawkes, “Opto Electronics – An Introduction”, 3rd Edition, Prentice Hall, New
Delhi, 1998.
Credits: 3:0:0 14EI2024 POWER PLANT INSTRUMENTATION
(Version 1.1)
Karunya University Course Objective: • To provide an overview of different methods of power generation with an emphasis on thermal power generation. • To bring out the various measurements involved in power generation plants. • To familiarize the students with the methods of monitoring different parameters in a power plant. Course Outcome: • Compare the different methods of power generation. • Apply the concepts to design instrumentation systems for a power plant. • Develop control algorithms for a particular operation in a power plant. Brief survey of methods of power generation, Hydro, Thermal, Nuclear, Solar and Wind power, Electrical measurements, Non– electrical parameters Measurements, Analytical instruments in Thermal power plants -Flue gas oxygen analyzer, Analysis of impurities in feed water and steam, Dissolved oxygen analyzer, Chromatography , PH meter , Fuel analyzer, Pollution monitoring instruments, Boiler control system in thermal power plant, Turbine Monitoring and Control References 1. K. Krishnaswamy, M. Ponnibala, “Power Plant Instrumentation”, PHI Learning Pvt Ltd.,2011. 2. P.K Nag, Power plant Engineering, Tata McGraw Hill, 2001. 3. Sam G Dukelow, The Control of Boilers, 2nd Edition, ISA Press, New York, 1991 4. Gill A B, Power Plant Performance, Butterworth, London, 1984. 5. P C Martin and I W Hannah, Modern Power Station Practice, British Electricity International, Vols. 1 & VI, Pergamon Press, London, 1992. 14EI2025 MODERN CONTROL TECHNIQUES Credits: 3:0:0 (Version 1.1) Pre Requisite: 14EI2005 Control System Course Objective: To enable the students to understand the advanced control systems like optimal control, Robust control, Adaptive control fuzzy and Neural control. To learn the methods to overcome the difficulties in implementing conventional control through advanced control. To analyze the modern control concepts Course Outcome: Design of conventional PID controller Perform stability analysis and optimal control Adaptive control and its implementation Modifications of PID control schemes, Two degrees of freedom control, Optimal Control – Formulation, Necessary conditions of optimality, state regulator problem, Output regulator tracking problems,
Pontryagin's minimum principle, infinite time optimal control , Problem, Advanced Control techniques Lyapunov Stability Analysis And Quadratic Optimal Control, Adaptive Control, Robust control
References
1. Katsuhiko Ogata, Morden Control Engineering,Third Edition, - Prentice Hall , India 2009. 2. Nagarath, I.J. and Gopal.M. Control Systems Engineering, Wiley & sons, 2008. 3. Astrom K.J. and Wittenmark.B, Adaptive Control, Addison Wesley Publishing, 1985. 4. Bernard friedlanced - Advanced Control System Design- Prentice Hall of India Pvt Ltd., New Delhi,1996. 5. Richard.C. Dorf and Robert.H.Bisho, Modern Control System, Addison Wesley & sons, 2008 Karunya University 14EI2026 STRENGTH OF MACHINE ELEMENTS Credits: 3:0:0 (Version 1.1) Course Objective: To introduce the basics of stress and strain on elements. To discuss the theory of failure in machines. To learn the concept of torsion on elements. Course Outcome: Appreciate the need for stress and strain analysis on elements. Determine the shear force and bending moment of elements. Analyze the effect of torsion on elements. Stress at a point, stress and strains in bars subjected to axial loading, Various strengths of material, Temperature stresses in simple & composite members. Strain energy due to axial load. Compound stress and strains, Mohr’s circle of stress; ellipse of stress and their applications, stresses in machine elements, Shear force and Bending moment – Definitions, Diagrams for cantilevers, simply supported beams with or without overhangs Uniform distributed load, Combination of Concentrated load & UDL, Uniformity varying load, Torsion equation, Applications to hollow and solid circular shafts, torsional rigidity, combined torsion and bending of circular shafts, analysis of close-coiled-helical springs, theories of failure, Buckling of columns. References 1. R. S. Khurmi, Strength of Materials, S. Chand, 2008 2. S. S. Ratan, Strength of Materials, Tata McGrawhill, 2011 3. Gere and Temoshenko, “Mechanics of Material”, CBS Publishers 4. S. Ramamrutham “Strength of Materials”, , Dhanpat Rai Publishing Company 5. Singer and Pytel “Strength of Materials”, , Harper and Row Publications 14EI2032 FLEXIBLE MANUFACTURING SYSTEMS Credits: 3:0:0 (Version 1.1) Course Objective: To deal with automation strategies used in assembly systems. To understand the concept of group technology. To learn the significance of Flexible Manufacturing systems.
Course Outcome:
Classify the automation strategies used in industries. Select the group technology to be adopted for specific applications. Appreciate the importance of Flexible manufacturing systems
Automation and Automated Assembly systems-Types, automation strategies, Detroit-type automation: Automated flow lines, methods of work part transport, Transfer mechanisms, design of automated assembly systems, Group Technology-Part families, parts classification and coding, Machine cell design, Flexible Manufacturing Systems - Components of an FMS, types of systems, FMS work stations, Material handling and storage system, Planning the FMS, analysis methods for FMS, applications and benefits.
References
1. Automation, Production Systems and Computer Integrated Manufacturing- Groover M.P, Prentice Hall of India, 2002 2. CAD/CAM – Groover M.P, Zimmers E.W, Prentice Hall of India, 2005 3. Approach to Computer Integrated Design and Manufacturing: Nanua Singh, John Wiley and Sons, 1998. 4. Production Management Systems: A CIM Perspective- Browne J, Harhen J, Shivnan J, Addison Wesley, 2nd Ed. 1996. Karunya University 14EI2033 VIBRATION ANALYSIS Credits: 3:0:0 (Version 1.1) Course Objective: To learn about the causes and effects of vibration and their characteristics. To understand the principle of vibration transducers. To learn the modern methods of vibration analysis. Course Outcome: Characterize the vibration and perform cause-effect analysis. Develop measurement systems to measure vibration. Apply the knowledge of vibration analysis to suggest solutions to overcome the effect fo vibration. Causes and effects of vibration- Vibrations of Single Degree, Two Degree and Multi Degree of freedom systems., Steady state and transient characteristics of vibration, Vibration measuring instrumentsVibration transducers, signal conditioning elements. Display-and recording elements. Vibration meters and analyzers, Special vibration measuring techniques - Change in sound method, Ultrasonic measurement method, Shock pulse measurement, Kurtosis, Acoustic emission monitoring, Cepstrum analysis, Modal analysis, critical speed analysis, Shaft –orbit & position analysis. References 1. Collacott, R.A., Mechanical Fault Diagnosis and Condition Monitoring, Chapman & Hall, London, 1982. 2. John S. Mitchell, Introduction to Machinery Analysis and Monitoring, Penn Well Books, Penn Well Publishing Company, Tulsa, Oklahoma, 1993. 3. Nakra, B.C. Yadava, G.S. and Thuested, L., Vibration Measurement and Analysis, National Productivity Council, New Delhi, 1989. 4. Pox and Jenkins, “Time Series Analysis: Forecasting and Control”, ISBN 978-0-470-27284-8, 2008.
Credits: 3:0:0 14EI2035 HUMAN - ROBOT SYSTEMS AND INTERACTION
(Version 1.1)
Course Objective:
To study multimodal interactions between a human and a robot To gain knowledge on surgical robotics. Karunya University To deal with rehabilitation and assistive robotics. Course Outcome: Perform motion analysis of human robots Develop robot supported surgical assistive devices. Design robots for rehabilitation. Definition of human-robot interaction problem, human factors: perception, motor skills, social aspect of interaction, safety, Haptic robots: kinematics, dynamics, collision detection, control, Teleoperation systems: architectures, control, virtual fixtures, micro/nano manipulation; Soft robots based on variable impedance actuators, Medical robotics: surgical robotics, robot-supported diagnostics, microrobots in the human body, nanorobots at the cell level, Rehabilitation and assistive robotics: motor rehabilitation, exoskeletons, robotic prosthetics References 1. M. Mihelj, J. Podobnik, Haptics for Virtual Reality and Teleoperation, Springer 2012. 2. J. Rosen, B. Hannaford, R.M. Satava, SurgicalRobotics: Systems Applications and Visions, Springer, 2011 3. M. Tavakoli, R.V. Patel, M. Moallem, A. Aziminejad, Haptics for Teleoperated Surgical Robotic Systems, World Scientific, 2008 4. Jose L. Pons, Wearable Robots:Biomechatronic Exoskeletons, John Wiley& Sons, 2008. 5. V. Dietz, T. Nef, W.Z. Rymer,Neurorehabilitation Technology, Springer, 2012 6. E. Burdet, D.W. Franklin, T.E. Milner, Human Robotics: Neuromechanics and Motor Control, The MIT Press, 2013 7. L. Sciavico, B. Siciliano: Modeling and Control of Robot Manipulators, The McGraw –Hill Companies, Inc., New York, 2000. 14EI2036 ENVIRONMENTAL INSTRUMENTATION Credits: 3:0:0 (Version 1.1) Course Objective: To introduce the instrumentation methodologies for environment monitoring. To deal with water quality monitoring and waste water treatment To discuss the instrumentation required for air pollution monitoring. Course Outcome: Design instrumentation systems for environment monitoring. Develop algorithms for waste water treatment Develop instruments to measure and analyze air quality Necessity of instrumentation & control for environment, Instrumentation methodologies, Quality of water: Standards, effects, Water quality parameters: Thermal conductivity, detectors, Opacity monitors, pH analyzers & their application, conductivity analyzers & their application, Water treatment: Requirement of water treatment facilities, process design, Sedimentation & flotation: sludge, storage & removal, design criteria of settling tank, effect of temperature on coagulation, Ground water monitoring: Level measurement in ground water monitoring wells, instrumentation in ground water monitoring,
assessment of soil & ground water pollution, Waste water monitoring: Waste water measurement techniques. Instrumentation set up for waste water treatment plant. Air pollution: Air monitoring, measurement of ambient air quality, Air flow measurement, Rain water harvesting: necessity, methods, rate of NGOs municipal corporation, Govt., limitations. Quality assurance of storage water.
References
1. Walter J. Weber, “Physiochemical processes for water quality control”. Karunya University 2. David Hendricks, “Fundamentals of Water Treatment Unit Processes”, CRC press, 2011. 3. M. N. Rao & H. V. N. Rao, Air pollution engineering, Mcgrawhill education, 2004. 4. Kenneth Wark, Cecil Warner, “Air pollution control technology”, IEP series in Mechanical Engineering, 2000. 5. Randy D. Down, Jey.H. Lehr, “Environmental Instrumentation & Analysis Handbook” Wiley International, 2004. 14EI2038 INSTRUMENTATION FOR AGRICULTURE Credits: 3:0:0 (Version 1.1) Course Objective: To introduce the fundamental principles of soil measurement systems. To deal with green house instrumentation. To discuss the working of automation equipment in agriculture Course Outcome: Design sensors for soil moisture measurement Develop green house instrumentation systems Apply the knowledge of instruments for automation in agriculture. Necessity of instrumentation & control for agriculture, engineering properties of soil: Sensors: introduction to sonic anemometers, hygrometers, fine wire thermocouples, open & close path gas analysers, brief introduction to various bio-sensors, soil moisture measurement methods: resistance based method, voltage based method, thermal based method, details of gypsum block soil moisture sensor, green houses & instrumentation: ventilation, cooling & heating, wind speed, temperature & humidity, rain gauge, carbon dioxide enrichment measurement & control. Automation in earth moving equipments & farm equipments, implementation of hydraulic, pneumatic & electronics control circuits in harvesters cotton pickers, tractor etc. Leaf area length evaportranspiration, temperature, wetness & respiration measurement , electromagnetic radiations photosynthesis, infrared & UV bio sensor methods in agriculture, agrometrological instrumentation weather stations, surface flux measurement, soil water content measurement using time-domain reflectometery(TDR) References 1. Industrial instrumentation, “Patranabis”, TMH, 2012. 2. Instrumentation handbook-process control, “B.G.Liptak”, Chilton 40 3. Process control and instrumentation technology, “C.D. Johnson”, PHI, 2005 4. Wills B.A., “ Mineral Processing Technology”, 4thEd.,Pergamon Press, 2000.
Credits: 3:0:0 14EI2039 INSTRUMENTATION AND CONTROL FOR AVIONICS
(Version 1.1)
Course Objective:
• To introduce the fundamentals of Aircraft systems. • To learn about the instrumentation involved in Aircrafts. • To provide knowledge on the working of aircraft instruments. Karunya University Course Outcome: • Appreciate the need for measurement in aircraft • Design instrumentation systems for aircraft. • Select suitable sensors to monitor the parameters in an aircraft. Flight Instrumentation – Pitot, Static Instruments and Systems, Altimeter, Airspeed indicator, Machmeter, Maximum Safe Speed indicator, Accelerometer, Gyroscope, Gyroscopic theory, Directional gyro indicator, Artificial horizon, Turn and slip indicator, Measurements in Aircraft - Measurement of Engine Speed, Measurement of Temperature, Pressure, Fuel Quantity and Fuel Flow, Engine Power And Control Instruments, Power Indicators, Pressure Indicators, Turbine Temperature Control, Engine Vibration Monitoring and Indicating Instruments. References 1. Pallett, E.B.J,“ Aircraft Instruments – Principles and applications", Pitman and sons, 1981. 2. Pallett, E.B.J,“ Aircraft Instrument Integrated Systems”, ISBN-10: 0582086272, Edition: 3rd 1992. 3. Nagabhushana S. Et.Al, S. Nagabhushana, L. K. Sudha, “ Aircraft Instrumentation and Systems”, International Pvt Ltd,2010. 4. Federal Aviation Administration (FAA) “Instrument Flying Handbook”, 2013. 5. Doeblin.E.O, “Measurement Systems Application and Design”, McGraw-Hill, New York, 1999. 14EI2040 ULTRASONIC INSTRUMENTATION Credits: 3:0:0 (Version 1.1) Course Objective: • To know about the generation and detection of ultrasonic waves • To provide knowledge on the concepts of Ultrasonic Instrumentation • To understand the applications of ultrasonic instruments Course Outcome: • Analyze the Characteristics of ultrasonic waves. • Develop sensors to measure physical quantities using ultrasonic methods. • Apply the concepts of ultrasonic instruments to make simple applications. Ultrasonic Waves -Principles and propagation of various waves, Characterization of ultrasonic transmission, Reflection and Transmission coefficients, Intensity and attenuation of sound beam. Generation/Detection Of Ultrasonic Waves - Magnetostrictive and piezoelectric effects, Detection of Ultrasonic Waves: Mechanical ,Optical and Electrical Method, Precise Measurement: Pulse– echo Overlap, Cross correlation, Ultrasonic Applications - Ultrasonic methods of flaw detection, Flow meters, Density measurement, Viscosity measurement, Level measurement, Sensor for Temperature and Pressure measurements, Measuring thickness, Depth, Rail Inspection, SONAR, Inspection of Welds and defect detection in welds of anisotropic materials, ultrasonic applications in medical field.
References
1. Baldev Raj, V.Rajendran, P.Palanichamy, “Science and Technology of Ultrasonics”,Alpha Science International, UK, 2004. 2. J.David N.Cheeke,”Fundamentals and Applications of Ultrasonic Waves,” CRC Press, Florida, 2002. 3. LawrenceE.Kinsler, Austin R.Frey, Alan B.Coppens, James V. Sanders, “Fundamentals of Acoustics,” John Wiley and Sons Inc,USA, 2000. Karunya University 4. L.A. Bulavin, YU.F.Zabashta, “Ultrasonic Diagnostics in Medicine,” VSP, Koninklijke, Brill,Boston, 2007. 5. Emmanuel P. Papadakis, “Ultrasonic Instruments and Devices”Academic Press,1999. 14EI2041 MEASUREMENTS AND INSTRUMENTATION Credits: 3:0:0 (Version 1.1) Course objective: To introduce the fundamentals of measurement systems and errors. To provide adequate knowledge on the measurement of electrical and non-electrical quantities. To have an understanding of the concepts of signal generators, analyzers and recording instruments. Course outcome: Analyze the instrument characteristics and the errors in measurement. Develop measurement systems for measuring electrical and non-electrical quantities. Suggest the types of analyzers, display devices and recording instruments for a specific application. Standards and Indicating Instruments-Errors in measurement- MC-MI-PMMC instrumentsMeasurement of electrical quantities- R,L,C,power,energy- Transducers used for sensing the measuring quantities - measurement of non-electrical quantities - temperature, pressure, speed - Signal Generators and analysers such as oscillators, spectrum and network analysers – various types of display indicators and different types of signal recorders as data acquisition systems References 1. Sawhney.A.K., “A Course in Electrical & Electronic Measurement and Instrumentation”, DhanpatRai& Company Private Limited, New Delhi, 18thEdition, 2007. 2. Helfrick A.D., “Modern Electronic Instrumentation & Measurements”, Prentice Hall India Private Limited, New Delhi, 2007. 3. Doeblin,E.O., “Measurement Systems : Application and Design”, 5th Edition, Tata Mc-Graw Hill Publishing Company Limited , New Delhi, 2004. 4. Golding,E.W., and Widdis,F.C., “Electrical Measurements and Measuring Instruments”, A H Wheeler & Company, Calcutta, 5th Edition, 2003. 5. Rangan,C.S., Sharma, G.R., Mani, V.S., “Instrumentation Devices and Systems”, Tata McGraw Hill, New Delhi, 1998. 6. John P Bentley, “Principles of measurement systems”, Pearson Prentice Hall, 4/e, 2005. 7. Alan S. Morris, “Measurement and Instrumentation Principles”, Elsevier, 2001.
14EI2042 ADVANCED CONTROL THEORY
Credits: 3:0:0
Pre Requisite: 14EI2005 Control System
(Version 1.1)
Course Objective:
• Provide adequate knowledge on the description and stability of non-linear system. • Understand the analysis of digital control system using state-space formulation. Karunya University • Look at the formulation and analysis of multi input multi output (MIMO) system. Course Outcome: • Gain knowledge in analysis of non-linear system and digital control of linear system. • Implement the concept of MIMO system. • Find non-linear system stability using the trajectory methods. State Space Analysis of Discrete Time Systems, Controllability, Observability, Pole placement design, Design of State observer, Response of sampled data system to step and ramp Inputs – Stability studies –Jury’s test and bilinear transformation, Types of nonlinearity, Construction of phase trajectories, Describing function method, Lyapunov stability analysis, Introduction to multivariable Nyquist plot and Singular values analysis, Advanced control techniques. References 1. Nagrath I.J., Gopal M., ‘Control Systems Engineering’, New Age International Publishers, 5th Edition, New Delhi 2003. 2. Raymond T. Stefani, Bahram Shahian, Clement J. Savant and Gene Hostetter , “Design of feedback Control systems”, Oxford University Press, New York,4th Edition, 2002. 3. Katsuhiko Ogata, “Discrete-Time Control Systems”, New Age International, New Delhi, 4th Edition, 2007. 4. Gopal M, “Digital Control and State Variable Methods”, Tata McGraw- Hill, New Delhi, 3rd Edition. 2008. 5. Richard C. Dorf and Robert H. Bishop, “Modern Control Systems”, Pearson Education, New Delhi, 8th Edition, 2004. 14EI2043 VIRTUAL INSTRUMENTATION Credits: 3:0:0 (Version 1.1) Course Objective: • To introduce the fundamentals of virtual instrumentation. • To provide knowledge about the programming techniques in virtual instrumentation. • To learn about the structures and special features of LabVIEW . Course Outcome: • Appreciate the advantages of Data flow programming • Use VI for instrumentation and control • Design a LabVIEW based instrumentation system. Historical perspective, advantages, Block diagram and Architecture of a Virtual Instrument, Data Flow Techniques, Graphical programming in data flow, comparison with Conventional programming Introduction and Advantages of LabVIEW, Software Environment, Creating and Saving VI- Front Panel Controls and Indicators – Block Diagram - Data types – Date flow program – LabVIEW documentation resources – Keyboard shortcuts – Modular Programming in LabVIEW – Icon and Connector Pane SubVI: Creating- Opening-Editing-Placing an SubVI - Creating a Stand Alone Application - Loops and charts, arrays, clusters and graphs, case and sequence structures, formula nodes, local and global variables, string and file I/O.
References
1. Jovitha Jerome, “Virtual Instrumentation Using LabVIEW” Prentice Hall India Learning Private Limited, New Delhi, 2010. 2. JohnEssick, “Hands-On Introduction to LabVIEW for Scientists and Engineers”, Oxford University Press,New York, 2nd Edition, 2010. 3. NesimiErtugrul, “LabVIEW for Electric Circuits, Machines, Drives, and Laboratories”, Pearson Karunya University Education, 2nd Edition, 2002. 4. LabVIEW: Basics I & II Manual, National Instruments, 2005. 5. Sanjay Gupta and Joseph John, “ Virtual Instrumentation using LabVIEW”, Tata McGraw – Hill Education India Private Limited, New Delhi, 2nd Edition, 2010. 6. Gary W. Johnson, Richard Jennings, “LabVIEW Graphical Programming”, McGraw-Hill Education, New York, 3rd Edition, 2001. 14EI2044 PLC AND AUTOMATION Credits: 3:0:0 (Version 1.1) Course Objectives: • To learn the basics and programming of PLC. • To examine the difference between SCADA and DCS. • To understand the basic concepts of Intelligent Automation. Course Outcome: • Identify, formulate, and solve problems related to PLC. • Design a system, component, or process to meet desired needs of the industrial requirement. • Implement a complete SCADA application relating to an industrial process or operation Description Basics of PLC – Architecture of PLC – Advantages – Types of PLC – Introduction to PLC Networking –Protocols – Field bus – Process bus and Ethernet. Types of Programming – Simple process control programs using Relay Ladder Logic and Boolean logic methods – PLC arithmetic functions – Process automation - Difference between SCADA system and DCS – Architecture – Local control Unit –Programming language – Operator interface – Engineering interfaces. Introduction to SCADA –Comparison between SCADA and DCS - Necessity and Role in Industrial Automation – Text display –Operator panels & Touch panels - Factory Automation - Computer Integrated Manufacture – CNC –Intelligent automation – Wireless controls. References 1. Webb, John W.Reis, Ronald A., “Programmable Logic Controllers Principles and Application”, PHI Learning, New Delhi, 5th Edition, 2002. 2. Dieter K. Hammer, Lonnie R. Welch, Dieter K. Hammer, “Engineering of Distributed Control Systems”, Nova Science Publishers, USA, 2001. 3. Gary Dunning, “Introduction to Programmable Logic Controllers”, Thomson Business Information, New Delhi, 2nd Edition, 2009. 4. Bolton. W, “Programmable Logic Controllers”, Elsevier India Private Limited, 5th Edition, New Delhi, 2010. 5. Mikell P. Groover, “Automation Produciton systems and Computer Integrated Manufacturing”, PHI Learning Ltd., 3rd Edition, New Delhi, 2009
14EI2045 ARTIFICIAL ORGANS AND REHABILITATION ENGINEERING Credits: 3:0:0 (Version 1.1)
Course Objective
To know about various types of assist devices. To give a basic idea of the artificial organs that can aid a human to live a normal life. Karunya University To provide the awareness on assistance that can be rendered to a differently abled person Course Outcome Design simple assist devices from basic principles. Choose suitable type of assist device for various disorders and legal aspects related to rehabilitation. Develop new devices based on the basic knowledge gained in different assisting devices. Description Biomaterials used in artificial organs andprostheses, Outlook for Organ replacement – Design considerations – Evaluation Process - Brief of kidney filtration, Haemodialysis: flat plate type, coil typeand hollow fiber. Haemodialysis Machine, Portable kidney machine - Brief of lungs gaseous exchange / transport,artificial heart-lung devices. Oxygenators: bubble, film oxygenators and membrane oxygenators. Gas flow rate and area for membrane oxygenators - Anatomy & Physiology of EAR-air conduction, bone conduction, masking, functional diagram of an audiometer. Hearing aids: different types, receiver amplifiers - Ultra sonic and laser canes, Intra ocular lens, Braille Reader, Tactile devices for visually challenged, Text voice converter. Reference Books 1. Joseph D. Bronzing, “The Biomedical Engineering Handbook”, CRC Press, Connecticut, 2nd Edition, 2000. 2. Leslie Cromwell, “Biomedical Instrumentation and measurement”, Prentice hall of India, New Delhi, 2007 3. Khandpur R.S, “Handbook of Biomedical Instrumentation”, Tata McGraw-Hill, New Delhi, 2007. 4. Laurence J. Street, “Introduction to Biomedical Engineering Technology”, CRC Press 2007. 5. Myer Kutz, “Standard Handbook of Biomedical Engineering & Design”, McGraw-Hill Professional. 1st Edition, 2002 6. D. Jennings, A. Flint, B.C.H. firton and L.D.M. Nokes, “Introduction to Medical Electronics Applications” Butterworth-Heinemann; 1995. 14EI2046 PROCESS CONTROL FOR FOOD ENGINEERS Credits: 3:0:0 (Version 1.1) Course Objective: To provide sound knowledge in the basic concepts of process control. To deal with the concepts of stability analysis of a system. To learn about the fundamentals of instruments used to measure physical parameters.
Course Outcome:
Derive the mathematical model of a system and analyze its characteristics. Determine the stability of a given system Apply the knowledge of industrial instruments to suggest sensors for a particular application.
Introduction to process control: Importance of Process control systems, steady state design, process control block diagram, types of responses, transforms of functions, Control systems, Open and closed loop systems, hydraulic and pneumatic systems, Control valves, Stability analysis, Stability criterion, Characteristic equation, Routh test for stability, signal flow graph, Masons’s Gain formula, block diagram, Industrial instrumentation, Measurement methods for sensing the pressure, temperature, level, density, composition.
Karunya University References 1. J.F Richardson A D. G. Peacock, Coulson & Richardson’s “Chemical Engineering” Volume3, (Chemical and Biochemical reactors and process control) Butherworth – Heinemann, an imprint of Elsevier, 2006. 2. Donald R. Coughanowr., “Process System analysis and control” McGraw Hill International Edition , Second Edition, Singapore, 2008 3. Nagoorkani. A “Control Systems”, RBA publications, 2nd edition, Nineteenth reprint 2012 4. S. Baskar, “Instrumentation control system measurements and controls”, Anuradha Agencies Publishers, 2004. 5. Nagrath. M and Gopal. I.J, “Control Systems Engineering”, Wiley Eastern Limited, Third Edition Reprint 2003. 14EI2047 PROCESS CONTROL LABORATORY FOR FOOD ENGINEERS Credits: 0:0:2 (Version 1.1) Co-Requisite: 14EI2046 Process Control for Food Engineers Course Objective: To provide adequate knowledge about the principle and characteristics of instruments. To learn about open loop and closed loop systems. To gain knowledge on stability analysis of a system Course Outcome: Determine the characteristics of instruments and analyze their performance. Analyze the performance of open loop and closed loop systems. Perform stability analysis of a given system. Description: This laboratory enables the student to analyze the performance of various measuring instruments and use them to control a system. List of experiments The faculty conducting the laboratory will prepare a list of 12 experiments and get the approval of HoD/Director and notify it at the beginning of each semester. 14EI2048 INSTRUMENTATION AND CONTROL SYSTEMS Credits: 3:0:0 (Version 1.1) Course Objective: • To provide adequate knowledge in the fundamental concepts of mechanical instrumentation • To introduce the basics of mathematical modelling and controller design. • To discuss about stability analysis of systems.
Course Outcome:
• Apply the knowledge of mechanical instruments to select suitable sensors for a particular application.
• Derive the mathematical model of a given system and develop control algorithms to improve its performance. • Determine the stability of a given system.
General concepts of Mechanical Instrumentation, generalized measurement system - Classification of instruments as indicators, Recorders and integrators Measurement error and calibration, Pressure And Temperature Measurement, Strain And Flow Measurement, Control Systems: Open and closed systems, Servo– mechanisms, Transfer functions,Signal flow graphs, Block diagram algebra, hydraulic and pneumatic control systems, Two way control , Proportional control - Differential and Integral control, Stability analysis, Concept of Stability, Necessary condition for Stability, Routh stability criterion, Polar and Bode plots, Nyquist plots Karunya University References 1. Jain R.K., “Mechanical and Industrial Measurements” Khanna Publishers, 2002. 2. Nagoorkani.A “Control Systems”, RBA publications, first edition ninth reprint 2002. 3. Sawhny, A.K. “Electrical and Electronics Measurements & Instrumentation”, DhanpatRai& Co., 2000. 4. Collet. C. V. and Hope. A.D. ‘Engineering Measurements’ 2nd Edition ELBS. 5. Nagrath. M. and Gopal.I.J.Control systems Engineering, Wiley eastern Ltd.,.2001. 6. Baskar S,’Instrumentation control system measurements and controls ‘anuradha agencies publishers,2004. 14EI3002 INSTRUMENTATION Credits: 3:0:0 (Version 1.1) Course Objective: To introduce the fundamental concepts of Instrumentation System To understand the importance of Instrumentation To learn about computer based instrumentation Course Outcome: Select suitable transducer for a specific instrumentation system Analyze the characteristics of transducers Apply computer based instrumentation for real time applications Instrumentation system – The general instrumentation system, Static and Dynamic Characteristics, Resistance and Inductance transducers, Capacitance and Piezoelectric transducers, Digital methods of measurements – Digital voltmeters and multimeters , Digital frequency, period and time measurements, Digital tachometers, Digital phase meters, Digital data recording, Digital Transducers, Computer based instrumentation – Evolution of Virtual Instrumentation, Architecture of Virtual Instrumentation, Virtual Instruments Versus Traditional Instruments, Advantages of VI, Interface Buses: PCI, PXI, and VXI. References 1. Jackson R G, “Novel Sensors and Sensing”, Institute of Physics Publishing, Bristol and Philadelphia, 2004. 2. Doeblin E.O, “Measurement Systems– Applications and Design”, McGraw Hill, New York, 2003. 3. Kalsi H S, “Electronic Instrumentation”, Second Edition, Tata McGraw Hill, New Delhi, 2009 4. John Park ,Steve Mackay,” Practical Data Acquisition for Instrumentation and Control Systems” Elsevier, 2003.
5. Mathivanan “PC based instrumentation: concepts and practice” PHI, 2008 6. Dr.S.Renganathan, “Transducer Engineering”, Allied publishers, New Delhi,2003. 7. D.Patranabis, “Principles of Electronic Instrumentation,” PHI, 2008 8. S. Sumathi and P. Surekha , “LabVIEW based Advanced Instrumentation Systems”
Springer, 2007. 9. H K P Neubert, “Instrument Transducers”, Oxford University Press, Cambridge,2000.
Karunya University 14EI3003 ADVANCED PROCESS CONTROL Credits: 3:0:0 (Version 1.1) Course Objective: • To equip the students with the basic knowledge of Process Modelling. • To understand various conventional and adaptive controllers. • To introduce the concept of Multivariable systems and decoupling. Course Outcome: • Develop mathematical model of a physical process. • Design various conventional and adaptive controllers. • Understand the knowledge of MIMO process and decoupling. Process control system – Terms and objectives, Piping and Instrumentation diagram, Instrument terms and symbols, Classification of variables, Modelling of simple systems Basic control action – Continuous controller modes- Selection of control mode for different process with control scheme, Control valve types and characteristics, Controller tuning – Optimum controller settings, Tuning of controllers, Advanced Control schemes, MIMO systems–Introduction, loop interaction , relative gains., Advanced control strategies – Internal model control, Adaptive control, Dynamic matrix control, Generalized predictive control References 1. Stephanopoulos G., “Chemical Process Control, Prentice Hall, New Delhi, 2003. 2. Coughanowr D.R., “Process Systems Analysis and Control”, McGraw – Hill Higher Education, Singapore, 2008. 3. Wayne BequetteB,’ Process control: modeling, design, and simulation’ Prentice Hall , New Jersey – 2003. 4. Smith C.L and Corripio.A..B, “Principles and Practice of Automatic Process Control”, John Wiley and Sons, New York, 2006. 5. Dale E. Seborg, Thomas F. Edgar, Duncan A. Mellichamp, “Process Dynamics and Control” ,Willey India, 2006. 6. Marlin. T.E., Process Control, Second Edition McGraw Hill NewYork, 2000 14EI3004 INDUSTRIAL INSTRUMENTATION AND PROCESS CONTROL LABORATORY Credits: 0:0:2 (Version 1.1) Co-Requisite: 14EI3003 – Advanced Process Control
Course Objective:
• To demonstrate the various process Measurements. • To inculcate the various controller design. • To implement Programmable Logic Control for real time applications.
Course Outcome:
• Measure various process measurements using the appropriate instruments. • Design control algorithms for different control loops. • Implement Programmable Logic Control for real time applications.
List of experiments
The faculty conducting the laboratory will prepare a list of 12 experiments and get the approval of HoD/Director and notify it at the beginning of each semester. Karunya University 14EI3005 ADVANCED CONTROL SYSTEMS Credits: 3:0:0 (Version 1.1) Course Objective: • To understand the basics of state space representation. • To study the controllers and the stability analysis of linear and non-linear systems. • To study the concepts of robustness Course Outcome: • Obtain the state space representation of a system. • Design controllers and analyse stability of a system • Design robust control systems Modelling of dynamic systems-Definition, Mathematical modelling, State space representation, Centrifugal Governor, Ground vehicle, Permanent Magnet stepper motor, Inverted Pendulum, Analysis of mathematical models – State space method, Phase plane, Isoclines, Numerical methods, State space analysis – Reachability and controllability , Observability and constructability, Companion forms, Controller / Observer form, State feedback control, State estimators, Stability of nonlinear system –Lyapunov stability theorems, Krasovskii’s method, Variable gradient method, Phase plane analysis, Singular points, Limit cycle, Describing function analysis. Robust PID control – Introduction to robust control- PID Tuning– Modifications of PID control scheme –Two Degrees of Freedom Control – Design consideration of Robust Control References 1. Stanislaw Zak, ‘Systems and Control’, Oxford University Press, 2003. 2. Gopal M, Digital Control and State variable Methods, Tata McGrawHill, New Delhi, 2003. 3. Ogata K, “Modern Control Engineering”, Pearson Education, New Jersey 2009. 4. Vidyasagar .M, “Nonlinear system analysis”, Prentice Hall Inc., New Jersey 2002. 5. Singaresu S. Rao, “Applied Numerical Methods” Prentice Hall, Upper Saddle River, New Jersey, 2001. 6. Jean – Jacques E. Slotine, Weiping Li, “Applied nonlinear control”, Prentice Hall Inc., New Jersey, 2004. 14EI3006 DISCRETE CONTROL SYSTEM Credits: 3:0:0 (Version 1.1)
Course Objective:
• To learn the concepts of discrete time Control systems. • To introduce polynomial equations approach to control system design. • To deal with the different types of digital control algorithm.
Course Outcome:
• Appreciate the need for discrete time control systems
• Design control system using polynomial equations approach. • Develop different types of digital control algorithm for a system.
Z transform – Review of Z Transform –Stability Analysis in Z domain State space analysis – State Space representation of discrete time Signals – Solving discrete time State Space Equations Pole placement and observer design – Controllability – Observability –Design via Pole Placement – State Observer Polynomial approach – Polynomial Equations Approach to Control System Design Digital algorithms – Implementation of different digital control algorithms Karunya University References 1. Ogata, “Discrete – Time Control Systems”, Pearson Education, Sigapore,2002. 2. Ky M. Vu, Optimal Discrete Control Theory The Rational Function Structure Model, Library and archives Canada cataloguing in publication, Canada,2007. 3. Gene F. Franklin,J. David Powell, “Digital control of dynamic systems”, Pearson Education Limited – 2002. 4. Gopal M, Digital Control and State variable Methods, Second Edition, Tata McGrawHill, New Delhi, 2003. 14EI3007 INTELLIGENT CONTROLLERS Credits: 3:0:0 (Version 1.1) Course Objective: To introduce the basic concepts of neural networks and its applications in Control. To introduce fuzzy logic concepts and its applications in Control. To introduce the fundamental concepts of genetic algorithm. Course Outcome: Develop and train a neural network. Develop a fuzzy system for a given application Use the neural network and fuzzy logic techniques to control a system. Neural Networks: Introduction – Biological Neurons and their artificial Models, Learning Rules, Types Of Neural Networks , Schemes Of Neuro Control, System Identification , Case studies, Fuzzy Logic: Fuzzy Sets, Fuzzy Operation, Fuzzy Arithmetic, Fuzzy Relations, Fuzzy Relational Equations, Approximate Reasoning, Fuzzy Propositions, Fuzzy Quantifiers Structure of Fuzzy Logic Controller, Fuzzy Control Applications Genetic Algorithm and its applications: Fundamentals, Comparison Of GA And Traditional Search Methods, Genetic Algorithm In Scientific Models And Theoretical Foundations, Case Studies References 1. Jacek M Zurada, ‘Introduction to Artificial Neural Systems’, Jaico Publishing House, 1999. 2. Rajasekaran.S and G.A Vijayalakshmi Pai, ‘Neural Networks, Fuzzy logic and Genetic Algorithms, Synthesis and Applications’, Prentice Hall of India, New Delhi – 2003. 3. Klir G.J. &Folger T.A. ‘Fuzzy sets, uncertainty and Information’, Prentice Hall of India Pvt. Ltd.,1993. 4. Zimmerman H.J. ‘Fuzzy set theory –and its Applications’ – Kluwer Academic Publishers,1994.
5. Melanie Mitchell, ‘An introduction to Genetic Algorithm’, Prentice – Hall of India, New Delhi,
Edition: 2004. 6. Kosko, B. ‘Neural Networks and Fuzzy Systems’, Prentice – Hall of India Pvt. Ltd.,1994.
Credits: 3:0:0 14EI3008 OPTIMAL CONTROL THEORY
(Version 1.1)
Karunya University Course Objective: • To introduce the theory of optimal control and its applications. • To provide knowledge of dynamic optimization • To deal with design of optimal control system Course Outcome: • Apply optimal control concepts to systems. • Use dynamic optimization techniques to controllers. • Design optimal control algorithms for real time systems. Introduction , Problem formulation , Optimal control problem, Performance measures for optimal control problem, Selection, Dynamic programming – Optimal control law, Principle of optimality, A recurrence relation of dynamic programming, Hamilton – Jacobi – Bellman equation, Calculus of variations –Functions and Functional , Maxima and minima of function, Variation of functional , Extremal of functional, Euler Lagrange equation Variational approach to optimal control problems, Necessary conditions for optimal control, Linear regulator problems, Linear tracking problems, Pontryagin’s minimum principle and state inequality constraints, Minimum time problems – Singular intervals in optimal control problems, Various optimization algorithms References 1. Donald E. Kirk, Optimal Control Theory: An Introduction, Prentice – Hall networks series, New Jersey, 2004. 2. Singiresu S. Rao “Engineering Optimization: Theory and Practice” New Age International (P) Ltd., Publishers New Delhi – 2004. 3. Gopal M, “Digital Control and State Variable Methods”, Tata McGraw – Hill Companies New Delhi, 2009. 4. Dimitri P. Bertsekas.’Dynamic Programming and Optimal Control’ Vol –1 Athena Scientific, Bell mount MA, 2000. 14EI3009 INDUSTRIAL INSTRUMENTATION Credits: 3:0:0 (Version 1.1) Course Objective: To provide the basic concepts of various industrial process measurements To give an exposure to smart instruments. To deal with the design and calibration of measuring Instruments Course Outcome: Design and calibrate the measuring instruments Analyze the characteristics of instruments Suggest suitable instruments for a particular application Design and Calibration of various types of measuring instruments for Pressure Measurement, Flow Measurement, Temperature Measurement and Level Measurement.
References
1. Doeblin E.O.I, Measurement Systems: Application and Design, Fifth Edition, McGraw –Hill Publishing Co. 5th edition, 2003. 2. Liptak B. ‘Process Measurement and Analysis’, 4th Edition,ISA, CRC Press, 2003. 3. Tatamangalam R., ‘Industrial Instrumentation Principles and Design’, Springer Verlag, 2000. 4. Singh. S.K, ‘Industrial Instrumentation and Control’, Tata McGraw Hill, Reprint 2004. Karunya University 14EI3010 CONTROL SYSTEM DESIGN Credits: 3:0:0 (Version 1.1) Course Objective: To impart the knowledge of compensators. To study the basic concepts of discrete domain representation of the system. To provide knowledge on the concepts of state estimation Course Outcome: Design compensators for process applications Represent systems in discrete domain Design state estimators. Conventional Design Methods: Design specifications, PID controllers and compensators, Root locus based design, Bode based design, Design examples, Design In Discrete Domain: Sample and Hold, Digital equivalents, Impulse and step invariant transformations , Methods of discretisation, Effect of sampling, Direct discrete design, Discrete root locus, Design examples, Optimal Control :Formation of optimal control problems, Calculus of variations, Hamiltonian formulation, Discrete State Variable Design: Discrete pole placement, State and output feedback, Estimated state feedback, Discrete optimal control , Dynamic programming - Design examples, State Estimation :State Estimation Problem, Luenberger’s observer - Noise characteristics, Kalman - Bucy filter, Separation Theorem, Controller Design, Wiener filter, Design examples. References 1. M. Gopal “Modern control system Theory” New Age International, 2005. 2. Benjamin C. Kuo “Digital control systems”, Oxford University Press, 2004. 3. G. F. Franklin, J. D. Powell and A. E. Naeini “Feedback Control of Dynamic Systems”, PHI (Pearson), 2002. 4. Graham C. Goodwin, Stefan F. Graebe and Mario E. Salgado “Control system Design”, PHI (Pearson), 2003. 5. G. F. Franklin, J. D. Powell and M Workman, “Digital Control of Dynamic Systems”, PHI (Pearson), 2002. 6. B.D.O. Anderson and J.B. Moore., ‘Optimal Filtering’, Prentice hall Inc., N.J., Second version published in 2005. 7. Loan D. Landau, Gianluca Zito,” Digital Control Systems, Design, Identification and Implementation”, Springer, 2006.
Credits: 0:0:2 14EI3011 VIRTUAL INSTRUMENTATION LABORATORY
(Version 1.1)
Course Objective:
• To strengthen the knowledge of Virtual Instrumentation. • To understand the concept of signal processing using virtual instruments • To introduce the concept of Data Acquisition using virtual instrumentation Karunya University Course Outcome: • Analyze real world signals • Interface real process with a virtual instrument. • Perform signal processing operations using virtual instrumentation. List of experiments The faculty conducting the laboratory will prepare a list of 12 experiments and get the approval of HoD/Director and notify it at the beginning of each semester. 14EI3012 EMBEDDED CONTROL SYSTEMS LABORATORY Credits: 0:0:2 (Version 1.1) Course Objective: To learn about the Embedded Processors with Real World applications. To introduce the concept of control applications in embedded systems. To enhance the knowledge in interfacing processes with embedded controllers. Course Outcome: Write programs in an IDE and download it to the Processor. Design and program Embedded circuits. Design control algorithms in an embedded processor. List of experiments The faculty conducting the laboratory will prepare a list of 12 experiments and get the approval of HoD/Director and notify it at the beginning of each semester. 14EI3014 INDUSTRIAL AUTOMATION Credits: 3:0:0 (Version 1.1) Course Objective: To introduce the process control philosophies To learn the Programmable Logic controller design To deal with PLC for control applications Course Outcome: Apply PLC programming for control purpose Apply ladder logic methodology in automation field Apply PLC in real time continuous process Nature of Industrial Process: continuous & discrete state , sequential process, process variables and their classification. Introduction to Process Control Philosophies: type of relays, ladder logic methodology, Introduction to Programmable Logic Controllers: PLC programming methodologies: ladder diagram,
STL, functional block diagram, creating ladder diagram from process control descriptions, introduction to IEC61131 international standard for PLC. PLC functions- PLC Timer & Counter functions - on-delay timer, off-delay, Timers- PLC Data Handling: - PLC arithmetic and logical functions- Analog value processing: types of analog modules, analog input and output examples, PID control of continuous process.
References
Karunya University 1. John webb, “Programmable logic controllers-Principles & applications”, Prentice Hall of India,2003. 2. T. A. Hughes, ”Programmable controllers, ISA, 2005. 3. 1.C. D. Johnson, “Process control instrumentation Technology, 3rd Edition, John Wiley & Sons, 1988. 14EI3015 SYSTEM IDENTIFICATION AND ADAPTIVE CONTROL Credits: 3:0:0 (Version 1.1) Course Objective: • To understand the concept of signal modelling • To impart the concepts of system identification • To introduce the concept of adaptive control Course Outcome: • Select a suitable model for a given system. • Perform system identification of a given process using different methods. • Design adaptive control strategies for real time applications. Signal modelling – Models of LTI systems- - Models for Time - varying and Non - linear systems, Models with Nonlinearities, Nonlinear state - space models, Black box models, Fuzzy models, Identification – Non - Parametric and Parametric identification, Transient response and Correlation Analysis, Frequency response analysis, Spectral Analysis, Least Square, Recursive Least Square, Validation – Non - Linear Identification and Model Validation, State estimation techniques, Non linear identification using Neural Network and Fuzzy Logic, Adaptive control – Self Tuning Regulators (STR), Model Reference Adaptive Control (MRAC) , Gain Scheduling, Applications – Inverted Pendulum, Robot arm, Process control application: heat exchanger, Distillation column - Application to power system, Ship steering control. References 1. Narendra and Annasamy,” Stable Adaptive Control Systems, Prentice Hall, Inc., 2005. 2. Astrom and Wittenmark,” Adaptive Control Second Edition”, Addison - Wesley Publishing Company 1995. 3. Monson H.Hayes,’ Statistical Digital Signal Processing and Modelling”, John Wiley and Sons,2002 4. Lennart Ljung, “System Identification Theory for the User”, Prentice Hall, Inc., NJ, 1999. 5. Torsten Soderstrom, Petre Stoica, “System Identification”, prentice Hall ` International (UK) Ltd,1994. 6. William S. Levine, “ Control Hand Book” CRC Press, Jaico Publishing House, 1999. 7. Narendra and Annasamy,” Stable Adaptive Control Systems, Prentice Hall, Inc., 2005.
Credits: 3:0:0 14EI3016 SCADA SYSTEMS AND APPLICATIONS
(Version 1.1)
Course Objective:
• To introduce the need for Data Acquisition. • To understand the concept of Supervisory Control. • To deal with the applications of SCADA Systems. Karunya University Course Outcome: • Appreciate the need of Data Acquisition. • Apply the concept of Supervisory Control • Perform simulation for various process. Introduction to SCADA and PLC:SCADA: Data acquisition system, PLC: Block diagram, programming languages, SCADA system components: Schemes, Remote Terminal Unit, Intelligent Electronic Devices, Communication Network, SCADA server, SCADA Architecture: Various SCADA Architectures, advantages and disadvantages, SCADA Communication and Operation and control of interconnected power system:SCADA applications References 1. Stuart A Boyer, “SCADA supervisory control and data acquisition”,ISA- The Instrumentation, Systems and Automation Society,2010. 2. Gordan Clark, Deem Reynders, “Practical Modem SCADA Protocols”, Elsevier Publications,2004. 3. Sunil S. Rao, “Switchgear and Protections”, Khanna Publication,1992. 4. John Park, Steve Mackay, “Practical Data Acquisition for Instrumentation and Control Systems”,.Elsevier Publications,2003. 14EI3017 DESIGN OF LINEAR MULTIVARIABLE CONTROL SYSTEMS Credits: 3:0:0 (Version 1.1) Course Objective: • To inculcate the knowledge of Multivariable control systems. • To design controller for multivariable control systems. • To apply the design for various applications. Course Outcome: • Apply the concept of Multivariable control systems. • Design controller for multivariable control systems. • Use the corresponding controller synthesis techniques. Analysis: system representations, return difference matrix, stability theory, multivariable poles and zeros. Design: design criteria, LQG design methods (including the optimal linear quadratic regulator and the Kalman filter), norm-based methods, robust stability and performance. H-infinity design techniques, including the generalised regulator problem. Model reduction, including modal and balanced truncation. Design examples: use of software for the design of controllers for industrial processes.
References
1. Stanislaw Zak, ‘Systems and Control’, Oxford University Press, 2003. 2. Gopal M, “Digital Control and State variable Methods”, Tata McGraw Hill, New Delhi, 2003. 3. Charles R. Slivinsky, Donald G. Schultz, Lynn E. Weaver, “The design of linear multivariable control systems using modern control theory”, 1969.
4. Ying-Jyi Paul Wei, “Frequency-domain approaches to linear multivariable control system designs, 1979. 5. Ogata K, “Modern Control Engineering”, Pearson Education, New Jersey, 2009.
14EI3018 PIPING AND INSTRUMENTATION
Credits: 3:0:0
(Version 1.1)
Karunya University Course Objective: • To provide knowledge on the symbols of Piping and Instrumentation diagram. • To deal with P&I flow diagram. • To learn the applications of Piping and Instrumentation diagrams in process plants. Course Outcome: • Identify the symbols used in Piping and Instrumentation diagrams. • Interpret the Piping and Instrumentation diagram of a process. • Analyze the condition of a process from the Piping and Instrumentation representation. Types of flow sheets, Flow sheet Presentation, Flow Sheet Symbols, Process flow diagram- Synthesis of steady state flow sheet - Flow sheeting software. P & I D objectives, guide rules, Symbols, Line numbering, Line schedule, P & I D development, typical stages of P & I D. P & I D for rotating equipment and static pressure vessels, Process vessels, absorber, Control System for Heater, Heat exchangers, reactors, dryers, Distillation column, Applications of P & I D in design stage - Construction stage - Commissioning stage - Operating stage Revamping stage - Applications of P & I D in Risk References 1. Ernest E. Ludwig, “Applied Process Design for Chemical and Petrochemical Plants”, Vol.-I Gulf Publishing Company, Houston, 1989. 2. Max. S. Peters and K.D.Timmerhaus, “Plant Design and Economics for Chemical Engineers”, McGraw Hill, Inc., New York, 1991. 3. 3.Bela G. Liptak, “ Process Measurement and Analysis”, ISA, CRC press,2003. 4. Anil Kumar,”Chemical Process Synthesis and Engineering Design”, Tata McGraw Hill publishing Company Limited, New Delhi - 1981. 5. A.N. Westerberg, et al., “Process Flowsheeting”, Cambridge University Press, 1979. 14EI3019 EMBEDDED INSTRUMENTATION Credits: 3:0:0 (Version 1.1) Course Objective: To introduce the fundamental concepts of Instrumentation System To understand the importance of Instrumentation To deal with the concepts of embedded instrumentation systems
Course Outcome:
Select suitable transducer for a specific instrumentation system Analyze the characteristics of transducers Develop computer based instrumentation for real time applications
Instrumentation system - resistance and inductance transducer-capacitance and piezoelectric transducers, digital methods of measurements: computer based instrumentation, evolution of virtual instrumentation, architecture of embedded virtual instrumentation, embedded virtual instruments versus traditional instruments , advantages of vi – pc based data acquisition system, interfacing techniques to the IBM PC –plug– in data acquisition boards – interface buses: PCI, PXI, VXI
References
Karunya University 1. S. Sumathi, P.Surekha, “LabVIEW based Advanced Instrumentation Systems “ springer 2007 2. N.Mathivanan, “ PC_Based Instrumentation- Concepts and Practice, PHI Learning Pvt. Ltd, 2007 3. Walt Boyes, “ Instrumentation Reference Books”, Third Edition, Butterworth Heinemann, 2003. 14EI3020 NETWORKS AND PROTOCOLS FOR INSTRUMENTATION AND CONTROL Credits: 3:0:0 (Version 1.1) Course Objective: To introduce the concept of communication protocols and give an overview of Data Communication Standards. To discuss the types of cables used for transmission. To discuss the operation and applications of the Protocols used in Industries . Course Outcome: At the end of the course, Students will be able to Identify the protocol. Choose the requires protocol and the communication modes for the given system. Select a suitable cable for the transmission . Open systems interconnection ( OSI ) model – protocols – physical standard – smart instrumentation systems – bits, bytes and characters – communication principles – communication modes –asynchronous systems – synchronous systems -data communication standards: standards organizations –serial data communications interface standards – balanced and unbalanced transmission lines – RS232 interface standard – troubleshooting serial data communication circuits – test equipment – ethernet –ethernet protocol operation – ethernet hardware requirements -cabling, electrical noise and error detection- modem and multiplexer- industrial protocol: profibus References 1. Steve Mackay, John Park and Edwin Wright, “Practical Data Communication for Instrumentation and Control”, Newnes Elsevier, USA, 2002. 2. TanenbaumA.S, “Computer Networks”, Fourth Edition, Prentice – Hall of India, Hyderabad, 2002. 3. William A Shay, “Understanding Data Communications and networks”, Pacific Grove, USA, 2003. 14EI3022 DESIGN OF EMBEDDED CONTROL SYSTEM
Credits: 3:0:0 (Version 1.1)
Course Objective:
To strengthen the knowledge of embedded design challenges To understand the concept of controller using embedded To deal with the concept of robot system
Course Outcome:
Design control application using embedded system To analyse the process using system identification technique Design control algorithms for robust control
Characteristics of embedded computing applications – Designing an Adaptive Cruise Control System, Embedded systems , basic concept, Introduction to embedded control system design, System identification and model-order reduction, Classical controller design, Classical controller design, Fundamentals of robust control, Robust controller design, Embedded safety loop development Karunya University References 1. Forrai, Alexandru Embedded Control System Design- “A Model Based Approach”, Springer publication, 2013. 2. Adamski, Marian Andrzej, Karatkevich, Andrei, Wegrzyn, Marek (Eds.), “Design of Embedded Control Systems”, Springer Publication, 2005. 14EI3023 ADVANCED PROCESSORS FOR CONTROL AND AUTOMATION Credits: 3:0:0 (Version 1.1) Course Objective: To learn recent trends in advanced microcontroller applications. To learn microcontroller implementation for control applications To understand programming with 8 and 32 bit microcontrollers. Course Outcome: Program microcontrollers for embedded applications. Illustrate architecture differences and to show common characteristics. Design the microcontroller for real time projects. 8 bit processor: 8051 architecture, Programming examples with stepper motor, dc motor, interfacing timer with control applications, CPU Architecture of PIC microcontroller –temperature, flow process interfacing , A/D converter, UART , 16 bit processor/32 bit processor: Introduction to 16/32 bit processor, ARM architecture, The ARM instruction set, The thumb instruction set , programming examples with control applications References 1. Raj Kamal – “Microcontrollers – Architecture, Programming, Interfacing and System Design”, Pearson Education, USA, 2005. 2. SteaveFurber,” ARM system–on–chip architecture” Addison Wesley, New Delhi, 2000. 3. John.B.Peatman, “Design with PIC Micro Controller”, Pearson Education, USA, 2003. 4. Mohammad Ali Mazide, Janice GillispicMazidi, RolinD.Mckinlay, “ The 8051 micro controller and embedded systems using assembly and C”, prentice Hall of India, Hyderabad, 2006. 5. Kenneth Ayala ,”The 8051 Microcontroller”, Thomson Delmar Learning , New Jersey, 2004.
14EI3028 EMBEDDED VIRTUAL INSTRUMENTATION LABORATORY Credits: 0:0:2 (Version 1.1)
Course Objective:
• To strengthen the knowledge of Virtual Instrumentation.. • To understand the concept of signal processing • To introduce the concept of Data Acquisition. Karunya University Course Outcome: • Build simple virtual instruments • Interface the embedded systems to real time signals • Design embedded applications. List of experiments The faculty conducting the laboratory will prepare a list of 12 experiments and get the approval of HoD/Director and notify it at the beginning of each semester. 14EI3029 EMBEDDED AUTOMOTIVE SYSTEMS Credits: 3:0:0 (Version 1.1) Course Objective: To understand the current trends in automobiles To understand basic sensor arrangement and its types To understand the embedded processor Course Outcome: Implement automotive embedded systems in real time applications Implement controllers design using recent advances like GLS, GPSS, GMS Design various sensors for real time applications. Current trends in Automobiles- components for electronic engine management system. Electronic dashboard instruments, onboard diagnostic system , security and warming system- Vehicle motio control. Sensors and actuators, and their interfacing. Basic sensor arrangement, types of sensors- Electronic ignition systems. Types of solid state ignition systems and their principleof operation. Digital engine control system. Distributor less ignition – Integrated engine control system, Exhaust emission control engineering. Automotive Embedded systems. PIC, Freescale microcontroller based system. Recent advances like GLS, GPSS, GMS References 1. William B. Riddens, “Understanding Automotive Electronics”, 5th Edition, Butterworth Hennimann Woburn, Sixth Edition, 2003 2. Tom Weather Jr. & Cland c. Ilunter, “ Automotive computers and control system” Prentice Hall Inc., New Jersey.,2001 3. Robert Bosch,” Automotive Hand Book”, SAE , (5th Edition),2000
14EI3030 AUTOMOTIVE SENSORS AND INTELLIGENT SYSTEMS Credits: 3:0:0 (Version 1.1)
Course Objective:
To introduce sensors in modern electronic system To introduce the concept of intelligent transport systems Karunya University To discuss various sensors and interfacing concept Course Outcome: To select sensor for automobile industry To gain in depth knowledge on the importance of various sensors in automative system Interface various sensors in automotive electronic systems Introduction to automotive sensors and instrumentation – sensor product selection guide- sensors and interfacing – principles of actuation and control- sensors and interfacing techniques for Engine control, adaptive cruise control, braking control, traction control, steering, stability, sensors for intelligent transport systems, sensors for occupant safety. References 1. Ronald K. Jurgeaon, “ Automotive ElectronicsHandbook, 2nd Edition, Mc Graw-Hill,2007 2. William B. Ribbens, “Understanding Automotive Electronics”, 5th Edition, Newnes, 2006 3. E.Q.Doeblin, “Measurement Systems, Application and Design”, 4th Edition, McGraw-Hill, 2002. 14EI3031 AUTOMOTIVE PROTOCOLS AND TELEMATICS Credits: 3:0:0 (Version 1.1) Course Objective: To prepare the students to analyse, simulate automotive communication protocols To introduce theoretical concepts of telematics technologies relevant to automotive applications To introduce automotive communication protocols and diagnostics protocols. Course Outcome: Gain in depth knowledge on data communication and networking and applied in real time applications. Implement automotive communication protocols and telematics technologies. Simulate and implement telematics in wireless technologies. Basics of Data Communication Networks and Automotive Communication Protocols - Controller Area Network (CAN) Protocol-CAN Higher Layer Protocols-Local Interconnect Network (LIN) ProtocolFlexRay Protocol-Media Oriented System Transport (MOST) Protocol - In Vehicle Network DiagnosticsTelematics basics, applications and technologies- Global Positioning Systems (GPS), Inertial Navigation Systems (INS), Vehicle Location and Navigation, Bluetooth, UWB, RFID, Satellite Radio(XM-Radio and SIRIUS), Fleet Management and Case Study References 1. Aswin Goel, “Fleet Management- Real-time management and planning of commercial vehicle operations Series”, Springer., 2008 2. Gilbert Held. “Inter- and Intra-Vehicle Communications”, CRC Press, 2007 3. Behrouz Forouzan., “Data Communications and Networking”, McGraw-Hill. 2003 4. Dennis Foy. Automotive Telematics, Red Hat., 2002
14EI3033 BIOMEDICAL SENSORS AND SIGNAL CONDITIONING
Credits: 3:0:0 (Version 1.1)
Course Objective:
To understand bioelectric amplifiers To discuss filter and circuits Karunya University To introduce application of signal conditioning in biomedical field Course Outcome: Identify the method to apply various signal conditioning circuits Interface bioelectric signals with embedded systems Identify the application of signal condition circuits for biomedical field. Bioelectric amplifiers- General-purpose linear and non-linear electronic circuits typically found in industrial applications- Instrumentation amplifiers, Transducer bridge Amplifier. Frequency and time domain analysis of low pass, high pass, band pass, and band stop filters. Filter class- Frequency discriminators, oscillators, multivibrators - Amplifier selection for a variety of biomedical sensors, Wheatstone bridge design, Active filter design using standard approaches, Front-end analogue circuit design for EMG, ECG, EEG ,Front-end analogue circuit design for limb movement sensing, Power supply topologies for biomedical instruments References 1. R. B. Northrop, “Analysis and Application of Analog Electronic Circuits to Biomedical Instrumentation”, 2nd ed., CRC Press, 2012. 2. J. D. Bronzino, “Biomedical Engineering Handbook”, 3rd ed.,CRC Press & IEEE Press, 2006. 3. Ramón Pallás-Areny, John G. Webster,”Sensors and Signal Conditioning”, 2nd ed., Wiley publishers, 2000. 14EI3038 PHYSIOLOGICAL CONTROL SYSTEMS Credits: 3:0:0 (Version 1.1) Prerequisite: 14BT3026 Human Anatomy and physiology Course Objective: To understand the basic ideas related to modeling of physiological systems To understand system identification techniques To analyse physiological system in time and frequency domain Course Outcome: Develop mathematical model of any physiological system. Apply system identification and optimization concepts in modeling. Simulate the physiological system and analyse in time and frequency domain. . Introduction to Physiological control systems, Illustration, modeling Elements, linear models, Distributed parameters versus lumped parameter models, principle of superposition, BioFeedback, Time and frequency domain analysis, stability analysis of linear system, model identification of physiological system, optimization technique, Simulation of biological systems, case studies.
References
1. Katz, A.M. “Physiology of the Heart”, Lippincott Williams & Wilkins, USA, 2006.
Ewart Carson, Claudio Cobelli, : “Introduction of Modeling in Physiology and Medicine”,Academic Press, Netherland, 2008. 2. Vasilis.Z.Mararelis, “ Nonlinear Dynamic Modeling of Physiological System”, John Wiley & Sons, New Jersey, 2004. 3. Daniel Weiner, Johan Gabrielsson, “Pharmacokinetic and Pharmacodynamic Data Analysis: Concepts and Applications, Sweden, 2000. 4. Milsum J H, “Biological control system analysis”, Mc GrawHill, Newyark, 1966. Karunya University 5. Michael.C.K.Khoo, “Physiological control systems: Analysis, Simulation and Estimation”, IEEE Press, Prentice Hall of India Pvt. Ltd. New Delhi. 2001. 14EI3039 MEDICAL INSTRUMENTATION Credits: 3:0:0 (Version 1.1) Course Objective: To introduce the basic principle of human physiological systems. To understand the measurement of various physiological parameters. To understand the design principle biomedical instruments. Course Outcome: Suggest suitable medical instrumentation for physiological measurements. Design instrumentation circuits for measuring new physiological parameters. Use the knowledge of biomedical instruments to solve clinical problems. Physiological measurements: Cell and its Electrical activity, Principle of Physiological systems: Cardiovascular, Nervous system, Respiratory system, Vision, Muscular system-Electrodes and bioelectric signals: Bio electrodes, ECG, EMG, EEG and EOG, Measurement of physiological parameters: Blood flow, Blood pressure, Cardiac output, Bio–chemical measurement, Photometer. References 1. Khandpur. R. S, “Handbook of Biomedical Instrumentation”, Tata McGraw Hill, 2/e, New Delhi, 2003. 2. Leslie Cromwell, Fred J Weibell, Erich A Pfeiffer, “Biomedical Instrumentation and Measurements”, Prentice Hall of India, New Delhi, 2007. 3. Joseph J. Carr and John M. Brown, “Introduction to Biomedical Equipment Technology”,Pearson Education India, Delhi, 2004. 4. Myer Kutz, “Standard Handbook of Biomedical Engineering & Design,” McGraw– Hill Publisher, New York, 2003. 5. Webster, “Medical Instrumentation – Application & Design,” John Wiley and sons Inc, Netherlands, 2004. 6. Arumugam, “Biomedical Instrumentation”, Anuradha Publisher, Chennai.2013. 14EI3040 BIO VIRTUAL INSTRUMENTATION Credits: 3:0:0 (Version 1.1)
Course Objectives:
To understand the salient features of virtual instruments. To know about how to acquire a data and control an external measuring device by interfacing to a computer. To become competent in bio-signal acquisition and medical image acquisition and processing.
Course Outcome:
Identify salient traits of a virtual instrument and incorporate these traits in projects. Experiment, analyze and document in the laboratory prototype measurement systems using a computer, plug-in DAQ interfaces and bench level instruments. Effectively use the virtual instrumentation in bio-signal processing and image processing.
Historical perspective, advantages, Architecture o f a Virtual Instrument-Graphical programming Development of Virtual Instrument-Software and hardware installation- Common Instrument InterfacesCurrent loop, interface buses- networking basics- Image and signal Acquisition and Processing- Motion control-Applications of virtual instruments in Biomedical engineering. Karunya University References 1. Jerome, Jovitha, “Virtual Instrumentation and LABVIEW”, PHI Learning, New Delhi, First Edition, 2010. 2. Sanjay Gupta and Joseph John, “ Virtual Instrumentation using LabVIEW”, Tata Mc Graw – Hill Publishing Company Limited, New Delhi, 1st Edition, 2005. 3. Ronald W. Larsen, “LabVIEW for Engineers”, Prentice Hall Ltd, USA Jan 2010. 4. LabVIEW: Basics I & II Manual, National Instruments, 2005. 5. Gupta, “Virtual Instrumentation Using Lab View”, Tata McGraw Hill, New Delhi,1st Edition, 2008. 14EI3041 HOSPITAL MANAGEMENT SYSTEM Credits: 3:0:0 (Version 1.1) Course Objective: To understand the need and significance of Clinical Engineering and Health Policies. To familiarize the training strategies, quality management policies and information technology used in health care. To know the needs of managerial training to hospital staffs Course Outcome: Appreciate the need for standard health policies and quality management in hospitals. Apply the knowledge of computer and information technology in health care. Relate the training needs at various level of organization Need and scopes of clinical engineering, Educational responsibilities-Design and layout of hospitalNational health policies, Health organization in state- Health education-Health insurance, Health legislation-Training -Employee appraisal method-Standards, codes and quality management in health care-regulation for mobile ICU-Maintenance of equipments-work planning-Medical records and information management-information technology in medicine and healthcare-operations research in hazard management. References 1. Webster J.C. and Albert M.Cook, “Clinical Engineering Principle and Practice”, Prentice Hall Inc., Englewood Cliffs, New Jersey, 1979. 2. Goyal R.C., “Handbook of hospital personal management”, Prentice Hall of India, 1996. 3. R. Panneerselvam, “Operations research”, PHI learning pvt. Ltd., Newdelhi.2006.
4. A.K.Malhotra,“Hospital management: An Evaluation”, Global India Publications,2009. 5. James R. Langabeer, “Health Care Operations Management: A Quantitative Approach to
Business and logistics”, Jones & Bartlett Learning, UK.2008.
14EI3042 COGNITIVE TECHNOLOGY FOR BIOMEDICAL ENGINEERS Credits: 3:0:0 (Version 1.1)
Karunya University Course Objective: To introduce the basic concepts of neural networks and its applications in biomedical field. To introduce fuzzy logic concept and its applications in medical diagnosis. To introduce the concepts of genetic algorithm and its application in biomedical field. Course Outcome: • Develop algorithms for medical applications using neural network. • Design suitable fuzzy logic controllers for various medical instrumentation. • Develop algorithms using genetic algorithm to solve real world problems pertaining to biomedical applications. Introduction to neural networks: Introduction – Biological neurons and their artificial models, Learning, Adaptation and neural network's learning rules, Types of neural networks, Special networks and applications: Associative memory, BAM, Hopfield network, ART Network, SOM, Case studies, Introduction to fuzzy logic: Fuzzy sets, Fuzzy logic control: Structure of fuzzy logic controller, Case studies, Genetic algorithm and its applications: Fundamentals of genetic algorithm, Case studies, Optimization techniques for medical applications, Artificial intelligence, software tools. References 1. Jacek M Zurada, ‘Introduction to Artificial Neural Systems’, Jaico Publishing House,1999. 2. Rajasekaran S. and G.A VijayalakshmiPai, ‘Neural Networks, Fuzzy logic and Genetic Algorithms, Synthesis and Applications’, Prentice Hall of India, New Delhi – 2003. 3. Klir G.J. &Folger T.A. ‘Fuzzy sets, uncertainty and Information’, Prentice –Hall of India Pvt. Ltd.,1993. 4. Zimmerman H.J. ‘Fuzzy set theory – and its Applications’ – Kluwer Academic Publishers,1994. 5. Kosko, B. ‘Neural Networks and Fuzzy Systems’, Prentice – Hall of India Pvt. Ltd.,1994. 14E3044 EMBEDDED BASED MEDICAL INSTRUMENTATION LABORATORY Credits: 0:0:2 (Version 1.1) Pre Requisite: 14EC3076 Embedded Systems for Biomedical Instrumentation Course Objective: To introduce the basic concepts of embedded systems and applications to biomedical instrument design To introduce various software tools for embedded Systems with real time examples. To deal with the concepts of interfacing issues with real time signals.
Course Outcome:
Design and Analyze the systems for disease diagnosis and treatment methods Apply real time models and languages in medical image processing applications Analyze interface issues related to embedded systems.
List of experiments
The faculty conducting the laboratory will prepare a list of 12 experiments and get the approval of HoD/Director and notify it at the beginning of each semester.
14EI3045 DIAGNOSTIC AND THERAPEUTIC EQUIPMENTS LABORATORY
Karunya University Credits: 0:0:2 (Version 1.1) Co-Requisite: 14BT3026 Human Anatomy and Physiology Course objectives: To know the various methods involved in biosignal recordings and operation of patient monitoring equipments. To understand the working of medical therapeutic equipments. To understand equipment used for rehabilitation. Course outcome: Develop measurement systems for biosignals and its signal conditioning circuits Devise monitoring instruments and brain-computer interfacing techniques Design and analyse assist devices for old age and gait analysis. List of experiments The faculty conducting the laboratory will prepare a list of 12 experiments and get the approval of HoD/Director and notify it at the beginning of each semester. 14EI3046 MEDICAL IMAGING TECHNIQUES Credits: 3:0:0 (Version 1.1) Course Objective: • To provide knowledge of the principle of operation of radiological equipment. • To know the working principles of radio diagnostic devices. • To know about the hazards and safety of radiation usage in hospitals Course Outcome: Analyse the working principle of various imaging techniques Compare the older technologies with newly developed techniques Be aware of standards and safe limits of radiation exposure and control of radiation. Generation of x – rays: principles and production of soft and hard x rays-radio diagnosis: radiography, angiography, fluoroscopy, special radiological equipments-application of radioisotopes: alpha, beta and gamma emission, principle of radiation detectors, nuclear angiogram- principles of radiation therapyRadiation safety: hazardous effect of radiation, radiation protection techniques-Safety limits, radiation monitoring-CT-MRI. References 1. Isaac Bankman, I. N. Bankman , Handbook of Medical Imaging: Processing and Analysis(Biomedical Engineering), Academic Press, 2000. 2. Jacob Beutel (Editor), M. Sonka (Editor), Handbook of Medical Imaging, Volume 2. Medical Image Processing and Analysis , SPIE Press 2000. 3. Khandpur R.S, “Handbook of Biomedical Instrumentation”, Tata McGraw Hill, New Delhi,2003.
Credits: 3:0:0 14EI3048 CLINICAL INSTRUMENTATION
(Version 1.1)
Course Objective:
To introduce various analytical instruments and methods of spectral analysis used in clinical laboratory. Karunya University To understand the unique methods of separation of closely similar materials with chromatography. To introduce the important radio chemical methods of analysis and techniques in clinical laboratory Course Outcome: Analyze the techniques used for characterization of materials, devices and biological molecules. Analyze the various methods used for separation of closely similar materials using chromatography. Compare the important radio chemical methods of analysis. Introduction to analytical instruments and Spectrophotometers, NMR and mass spectrometer, radiation techniques, Automated chemical analysis system, pH meters and Chromatography, Clinical instrumentation techniques, Electrophoresis and microscopy. References 1. Khandpur R.S,”Handbook of Analytical Instruments”, Tata McGraw – Hill Publishing company limited, 2006. 2. Mousumi Debnath, “Tools and techniques of Biotechnology”, Pointer publications, 2005. 3. John G Webster, “Medical instrumentation application and design”, John wiley & Sons (Asia) Pvt Ltd, 3rd edition, 2004 4. Willard, H.H., Merrit L.L., Dean J.A Seattle F.L., ‘Instrumental Methods of Analysis’,CBS Publishing and Distribution, 1995. 5. Robert D.Braun, Introduction to Instrumental Analysis, McGraw–Hill, Singapore, 1987. 14EI3049 MEDICAL DEVICES AND SAFETY Credits: 3:0:0 (Version 1.1) Course Objective: To provide in-depth knowledge in safety testing to reduce unacceptable errors in medical device performance. To understand the safe handling and operation of medical devices to avoid patient injury. To provide adequate information on medical device standards and various regulations. Course Outcome: Appreciate the need for prevention of medical errors. Analyze various case studies related to unsafe handling of medical devices which led to patient injury. Explore for reasonable, acceptable, and more effective remedies. Reliability, safety testing, Failure assessment, Safety and risk management, Tools for risk estimation, Safe medical devices, Handling and operation, Usability, Environmental safety , Interference with the environment, ecological safety, Mechanical safety, Electrical Safety, Biological aspect, Limitation-Protection, Leakage currents, Safety classe, Medical
Standards and Regulation, six sigma standard for medical device design.
References
1. Bertil Jacobson and alan Murray, “Medical Devices Use and Safety”, Elsvier Limited, 2007. 2. Richard Fries,“Reliable Design of Medical Devices – Second Edition”, CRC Press, Taylor & Francis Group, 2006. Karunya University 3. Norbert Leitgeb “SafetyofElectromedicalDevicesLaw – Risks – Opportunities”, Springer Verlog/Wein, 2010. 4. Gordon R Higson, “Medical Device Safety- The regulation of Medical Devices for Public Health and Safety”, IOP Publishing Limited, Bristol and Philadelphia, 2002. 5. Shayne Cox Gad, “Safety Evaluation of Medical Devices” Second Edition, Marcel Dekker Inc., 2002. 6. Basem El-Haik, Khalid S. Mekki, “Medical Device Design for Six Sigma: A Road Map for Safety and effectiveness” John Wiley & Sons, 2011. 14EI3051 MEDICAL SENSORS AND WEARABLE DEVICES Credits: 3:0:0 (Version 1.1) Course Objective: To provide introduction to the field of medical sensors and an indepth and quantitative view of device design and performance analysis. To gain overview of the current state of the art to enable continuation into advanced biosensor work and design. To study about the wearable sensors and smart sensors Course Outcome: Evaluate a sensor based on standard performance criteria and appropriateness for an application. Identify the key design criteria and suggest an appropriate wearable sensor approach which is most likely to meet a specific biosensor application Analyse the most relevant challenges facing the smart sensor research field and for a particular challenge suggest a reasonable approach to find a solution. Physiological Measurements: Sensors for Pressure Measurement- Sensors for Motion and Force Measurement- Sensors for Flow Measurement -Temperature Measurement- Sensors for speed, torque, vibration- Wearable Sensors-smart sensors. References 1. Tatsuo Togawa, Toshiyo Tamura, P. Ake Oberg, “Bio-Medical Transducers and Instruments”, CRC Press, USA, 2010. 2. Subhas Chandra Mukhopadhyay, Aime Lay Ekuakille, “Advances in biomedical sensing and measurements”, Lecture notes in electrical engineering, Springer Verlag, Berlin, Gábor Harsányi, “Sensors in biomedical applications: fundamentals, technology & applications”, CRC Press, USA, 2000. 3. Joseph D. Bronzino, “The biomedical engineering handbook”, Volume 2, CRC Press, USA, 2000.
Credits: 3:0:0 14EI3052 REHABILITATION ENGINEERING
(Version 1.1)
Course Objective:
To provide knowledge about various types of assist devices and its applications. To provide indepth understanding of the functions of assist devices Karunya University To develop new devices for rehabilitation Course Outcome: Appreciate and analyse the working of different assist devices. Choose the assist device suitable for specific disorder. Design and develop new products for rehabilitation Rehabilitation -Prosthetic And Orthotic Devices, Types, models- Feedback in orthotic system- Material Auditory and speech assist devices -visual aids-Tactile devices - Muscle and nerve stimulator-Robot as assist devices-Psychological aspects of Rehabilitation therapy- Legal aspect-case studies. References 1. Albert M.Cook and Webster J.G, “Therapeutic Medical devices”, Prentice Hall Inc., NewJersy, 1982. 2. Levine.S.N.Editor, Advances in Bio Medical Engineering and Medical Physics, Inter University Publication, New York 1968. 3. Kolff W.J., Artificial Organs, John Wiley and Sons, New York,1979. 4. Andreas.F.Von racum, Hand book of bio material evalution, Mc-Millan publishers, 1980. 5. Albert M.Cook and Webster J.G., “Therapeutic Medical Devices, Prentice Hall Inc., New Jersey, 1982 14EI3054 BIOMECHANICS Credits: 3:0:0 (Version 1.1) Course Objective: To introduce the fundamental terms and concepts of human system modelling. To understand the anthropometric, biomechanical and physiological principles and their use in human well-being and overall performance. To acquire knowledge in evaluation of physiological factors and fitness factors for vehicle drivers. Course Outcomes: Analyse the concepts of human system modelling. Analyse the biomechanical and physiological principles used in optimizing human well-being and overall performance. To Identify, analyze and implement solutions to a human factors problem. Human system modeling - human control of systems, biomechanics-stress and fatigue measurements of bones, muscles-cognitive stress-stress modeling- signal acquisition and processing-brain and computer interface-Effects of environmental conditions –heat, stress-Human Factors Applications in medical and industrial field-Human error- accidents analysis- human factors –case study on evaluation of the physiological factors and fitness factors for defence vehicle driver –safety Standards.
References
1. Subrata Pal,“Text book of Biomechanics”, Viva education Private limited,NewDelhi. 2009.
2. Karl Kroemer, Henrike Kroemer, Katrin Kroemer-Elbert, “Ergonomics” How to Design for Ease & Efficiency, Prentice Hall International Editions, 2001. 3. Mark S Sanders, “Human Factors in Engineering and Design”, McGraw Hill, New York, 1993. 4. Bridger R S, “Introduction to Ergonomics”, Taylor and Francis, London, 2003. 5. Martin Helander, “A Guide to Ergonomics of Manufacturing”, Tata Mc GrawHill, 1996. 6. Mccormic,E.J. and Sanders.M.S “Human factors in Engineering and Design”, McGraw Hill, 1992. Karunya University 7. Susan J.Hall,“Basics Bio Mechanics” 5th Edition, McGraw-Hill Publishing Co,Newyork, 2007. 14EI3055 MEDICAL DIAGNOSTICS AND THERAPEUTIC EQUIPMENTS Credits: 3:0:0 (Version 1.1) Course objectives: To know the various biopotential recordings and operating procedure of ICCU equipments. To develop an understanding of the medical therapeutic equipment. To learn the safety standards of the diagnostics and therapeutic equipment. Course outcome: Develop measurement systems for biosignals and its signal conditioning circuits Know the safe operating procedure of Cardiac care monitoring instruments. Get clear domain knowledge about various types of wearable and implantable devices. Pace makers - patient monitoring system-diathermy-heart lung machine-pumps-Principle of Hemodialysis-Wearable Artificial Kidney, Implanting Type- Respiratory aids-Breathing Apparatus Operating Sequence-thermography- Fiber optics -Endoscopy, Laparoscopy, principles of Lithotripsycommunication standards-wireless telemetry. References 1. Albert M Cook and Webster J G, “Therapeutic medical devices”, Prentice Hall NewYork , 1982. 2. Heinz Kresse, “ Handbook of Electro medicine”, John Wiely & Sons, Chrchester.1985 3. Webster J.G, “Medical Instrumentation application and design”, John Wiley and sons New York 3rd edition 1999 4. Jacobson B and Webster J G Medical and Clinical Engineering – Prentice Hall of India New Delhi 1999 5. Leslie Cromwell , Fred J.Weibell and Erich A.Pfeiffer, “Biomedical Instrumentation”, Prentice Hall New Delhi 2000 6. Joseph J Carr and John M Brown,“Introduction to Biomedical equipment Technology”, 7. Pearson Education 4th edition, New Delhi 2001. 8. Khandpur R.S “Hand Book of Biomedical Instrumentation”, Tata McGraw Hill publication , New Delhi 2nd edition 2003 9. John Denis Enderle, Joseph D. Bronzino, Susan M. Blanchard, “Introduction to Biomedical Engineering”, Academic Press, 2005
14EI3056 LIMB PROSTHETICS
Credits: 3:0:0 (Version 1.1)
Course Objective:
To introduce the Basic concepts of robots and its applications to artificial limbs To know the instrumentation involved in Robot Dynamics and Kinematics
To learn the applications of Robot controls
Course Outcome:
Design Robot Control System for positioning and movement Learn the basic sensor and actuators and applications of robots. Develop Robotic applications as assist devices for limbs.
Definition - Classification - History - Robots components - Degrees of freedom - Robot joints coordinates - Reference frames - Workspace - Robot languages - Actuators - Sensors - Sensor characteristics - and electric actuators - Trajectory planning- motion control - Non-linear control-Image Processing And Vision Systems- PROSTHESIS, Introduction to Prosthesis, -Gait Analysis in Transtibial Amputees, Prosthesis in Knee Disarticulation- Gait Analysis in Transfemoral Amputees, -Prosthesis for Hand Amputation and Wrist Disarticulation-Recent Advances in Prosthesis -Ambulatory Aids. Karunya University References 1. Saeed B. Niku , ''Introduction to Robotics'', Pearson Education, 2002 2. K.S.Fu, Ralph Gonzalez and C.S.G.Lee, ''Robotics", TATA McGraw Hill, Aug., 2008. 3. R.D. Klafter, TA Chmielewski and Michael Negin, "Robotic Engineering, An Integrated approach", Prentice Hall of India, 2003. 4. Millee Jorge, “Orthotics and Prosthetics in Rehabilitation”, third edition, Saunders Elsevier publishing, , Missouri, 2013 5. Chinnathurai R, Sekar P, Kumar M Ramaa, Manoj K Nithya, Kumar C Senthil, “Short Textbook of Prosthetics and Orthotics”, Jaypee Digital publishing, 2010. 6. Michelle Lusardi, Millee Jorge, Caroline Nielsen, “Orthotics and Prosthetics in Rehabilitation”, Third edition, Elsevier, Saunders publishing,2012. 14E3057 INDUSTRIAL ELECTRONICS AND INSTRUMENTATION Credits: 3:0:0 (Version 1.1) Course Objective • To understand the concepts of Conventional and Digital Transducers • To study the concepts of Industrial heating, Photoelectric devices and Smart Transducers • To study the Microprocessor based instrumentation Course Outcome • Select the type of transducer for the Industrial application. • Apply in case studies and mini projects in industries. • Design the Microprocessor based Controllers. Review of variable resistance, inductance capacitanceand piezoelectric transducers - Direct digital transducers, Absolute and incremental displacement transducers, Moiré Fringe transducers, Force and Pressure measurement, IC sensors - Dielectric heating, Photoelectric devices and PLC - Detection of zero crossing of an alternating waveform, Microprocessor based: triggering of a Thyristor, Voltmeter and Ammeter, Speed monitoring Unit, phase difference and power factor monitoring Unit, over and under voltage protection and over current protection - Smart transducer, Measurement of flow, pH with smart transducers.
References
1. Biswas S.N, “Industrial Electronics”, Dhanpat Rai & Company Private Ltd., New Delhi, 2
nd
Edition, 2008. 2. Murty.D.V.S., “Transducers and Instrumentation”, PHI Learning, New Delhi, 2nd Edition, 2009.
3. Paul Biswanath., “Industrial Electronics & Control: Including Programmable Logic Controller”, PHI Learning, New Delhi, 2nd Edition, 2009. 4. Doebelin E.O, “Measurement Systems, Application and Design”, Mc-Graw Hill Publishing Company Ltd., New Delhi, 5th Edition, 2002. 5. Webb, John W.Reis, Ronald A., “Programmable Logic Controllers Principles and Application”, PHI Learning, 5th Edition, 2009. 6. Ram. B., “Fundamentals of Microprocessors & Microcontrollers”, Dhanpat Rai (P) Ltd., New Karunya University Delhi 2008. 14EI3058 LINEAR SYSTEMS Credits: 3:0:0 (Version 1.1) Course Objective: To understand the state model of LTI (Linear time invariant) system. To understand the concepts of Controllability and Observability To provide adequate knowledge in the Lyapunov stability analysis. Course Outcome: Represent the given system in state space. Design a state estimator. Analyze the stability of a system. State model for linear time invariant systems: State space representation using physical - Phase and canonical variables - Solution of state equation - State transition matrix - Transfer function from state model - Transfer matrix - Decomposition Methods – State space representation of linear time invariant discrete time systems - Solution of discrete time state equation. - Discretization of continuous time state equations - Eigen Values and Eigen Vectors – diagonalization - Concepts of Controllability and Observability - State Estimators - Lyapunov Stability Analysis of linear time invariant system. References 1. Katsuhiko Ogata, “Modern Control Engineering”, Prentice Hall of India Private Limited, New Delhi, 4th Edition, 2002. 2. Nagrath I.J, & Gopal M, “Control System Engineering”, New Age International Publishers Limited, New Delhi, 5th Edition, 2007 3. Nise S. Norman, “Control Systems Engineering”, John Wiley & Sons Inc, New Delhi, 3rd Edition, 2000. 4. John J. D'Azzo, Constantine H. Houpis, “Linear Control System Analysis and Design”, CRC Press, USA , 5th Edition,2003 5. Shankar P. Bhattacharyya, Aniruddha Datta, Lee H. Keel, “Linear Control Theory: Structure, Robustness And Optimization” CRC Press, USA , 2009 14EI3059 TRANSDUCERS AND ACTUATORS Credits: 3:0:0 (Version 1.1) Course Objective • To understand different sensor systems used for process parameters. • To understand signal conversion and conditioning. • To understand sensor signal transmission.
Course Outcome
• Selection of sensor based on process parameter and application. • Interconnection of sensors with Controller.
• Prevent data loss or noise during sensor signal transmission.
Electrical Transducers: Variable resistance type – Potentiometers, strain gauges, RTD, thermistorsVariable inductance type – self and mutual inductance, pulse transducer-Variable capacitance transducers-Special Transducers: Semiconductor temperature sensors, thermo-electric sensors, piezoelectric sensors, smart sensors-Electromechanical Transducers: Electrodynamic, eddy current, force balance transducers. Basics of MEMS devices-Other Transducers: Limit Switches, Proximity Switches, Pressure, Temperature, Level, Flow, Speed-Power System Transducers: Analogue and digital transducers for measurement of voltage, current, power factor, frequency, power – active and reactive. RTU for tariff calculation-Analogue Signal Conditioning techniques: Bridge amplifier, carrier amplifiers, charge amplifiers and impedance converters, modulation - demodulation, dynamic compensation, linearization, multiplexing and demultiplexing-Signal Transmission: Transmitters, V-I, I-V and V-f converters. Single transmission. Cable transmission of analog and digital signal, fiber optic signal transmission, radio, telemetry, pneumatic transmission-Actuators: Solenoid Valves, Pneumatic Control Valves, PistonCylinder, Motors, Contactors.
Reference Books
1. Doeblin, E.O. – Measurement Systems: Application and Design, Mc Graw Hill International, 2002 2. Patranabis, D – Sensors and Transducers, Wheeler Pub., New Delhi, 2003. 3. Murthy, D.V.S., Transducers and Instrumentation, PHI, New Delhi, 2008. 4. Newbert, H. K. – Instrument Transducers, Oxford University Press, 1999. Karunya University 14EI3060 AUTOMATED TEST AND MEASUREMENT Credits: 3:0:0 (Version 1.1) Course Objective • To understand the difference between classical measurement and microprocessor based measurement. • To understand Real Time signals. • To understand standard IEEE buses used for smart measurement. Course Outcome • Differentiate industrial instrumentation buses. • Sensors and transducers with smart data transfer. • Process, analyze and log the sensor values Measurement automation, Comparison with classical measurement and microprocessor based measurement, Measured data base and data base management, Real time signals, Calculated signalsDigital signal processing, Processed signals, Data flow and graphical programming techniques, Virtual instrumentation (VI), Advantages, VIs and Sub Vis-Data acquisition methods, DAQ hardware, Instrumentation buses, IEEE 488.1 and IEEE 488.2, Serial interfacing-RS 232C, RS 422, RS 423, RS 485, CAMAC, VXI, SCXI, PXI -Industrial drives and interface, Sensors and transducers, Interfacing signal conditioning, Signal-analysis techniques, Networking methods and their applications in instrumentation.
References
1. N. Mathivanan, PC-based Instrumentation-Concepts and Practice, Prentice-Hall, 2007. 2. M, Chidambaram, Computer Control of Processes, CRC Press, 2002
3. B. G. Liptak, Instrumentation Engineers Handbook, Philadelphia: Chilton Book Company, 4th
Edition, 2003.
Credits: 3:0:0 14EI3061 REMOTE SENSING AND CONTROL
(Version 1.1)
Karunya University Course Objective • To understand methods for remote sensing. • To understand remote control techniques and its application in Industry Course Outcome • Classify characteristics of objects. • Ground data acquisition. • Importance of remote control in Industry. Electromagnetic radiation: Classification and nature, spectral, spatial and temporal characteristics of objects-Atmospheric interaction sensors: Photographic, thermal, multi-spectral, passive microwave and active microwave sensors- Ground data acquisition: Photo-interpretation, image processing techniques, remote sensing applications-Techniques of remote control: Remote control in industry including oil pipelines, rocket motion and satellite movements. References 1. Gupta - Remote Sensing Ecology, 2nd edition, Springer, 2005 2. Jensen - Remote Sensing of the Environment, Pearson, 2003 3. Barett, E.C. and Curtis, L.F. Introduction To Environmental Remote Sensing, 3/e, Chapman Hall, New York 1992. 4. Lo, C.P. Applied Remote Sensing, Wiley, New York 1986. 14EI3063 ROBOT PROGRAMMING Credits: 3:0:0 (Version 1.1) Course Objective • To understand the basics of Robot programming • To understand the VAL language applications • To understand the RAPID language applications • To understand the Practical study of virtual robot software • To understand the VAL-II and AML language Course Outcome Select proper safety interlock needed for robot action Program the robot for various application specific movements Developing robot programs in different software packages / languages Robot programming-Introduction-Types- Flex Pendant- Lead through programming, Coordinate systems of Robot, Robot controller- major components, functions-Wrist Mechanism-Interpolation-Interlock commands-Operating mode of robot, Jogging-Types, Robot specifications- Motion commands, end effectors and sensors commands-Robot Languages-Classifications, Structures- VAL language commands motion control, hand control, program control, pick and place applications, palletizing applications using VAL, Robot welding application using VAL program-WAIT, SIGNAL and DELAY command for communications using simple applications-RAPID language basic commands- Motion Instructions-Pick and place
operation using Industrial robot- manual mode, automatic mode, subroutine command based programming. Movemaster command language- Introduction, syntax, simple problems-Robot cycle time analysis-Multiple robot and machine Interference-Process chart-Simple problems-Virtual robotics, Robot studio online software-Introduction, Jogging, components, work planning, program modules, input 13 RB-2013 SRM and output signals-Singularities-Collision detection-Repeatability measurement of robotRobot economics-VAL-II programming-basic commands, applications- Simple problem using conditional statements-Simple pick and place applications-Production rate calculations using robot. AML LanguageKarunya University General description, elements and functions, Statements, constants and variables-Program control statements-Operating systems, Motion, Sensor commands-Data processing. References 1. Deb. S. R. “Robotics technology and flexible automation”, Tata McGraw Hill publishing company limited, 1994 2. Mikell. P. Groover, “Industrial Robotics Technology”, Programming and Applications, McGraw Hill Co, 1995. 3. Klafter. R.D, Chmielewski.T.A. and Noggin’s., “Robot Engineering : An Integrated Approach”, Prentice Hall of India Pvt. Ltd.,1994. 4. Fu. K. S., Gonzalez. R. C. & Lee C.S.G., “Robotics control, sensing, vision and intelligence”, McGraw Hill Book co, 1987 5. Craig. J. J. “Introduction to Robotics mechanics and control”, Addison-Wesley, 1999. 6. Robotcs Lab manual, 2007. 7. www.wpi.edu 14EI3064 KINEMATICS AND DYNAMICS OF ROBOT Credits: 3:0:0 (Version 1.1) Course Objective • To control both the position and orientation of the tool in the three dimensional space. • The relationship between the joint variables and the position and the orientation of the tool. • Planning trajectories for the tool to follow on order to perform meaningful tasks. • To precisely control the high speed motion of the system Course Outcome • To control both the position and orientation of the tool in the three dimensional space. • The relationship between the joint variables and the position and the orientation of the tool. • Planning trajectories for the tool to follow on order to perform meaningful tasks. • To precisely control the high speed motion of the system Introduction, position and orientation of objects, objects coordinate frame Rotation matrix, Euler angles Roll, pitch and yaw angles coordinate Transformations, Joint variables and position of end effector, Dot and cross products, coordinate frames, Rotations, Homogeneous coordinates. Direct Kinematics-Link coordinates D-H Representation, The ARM equation. Direct kinematic analysis for Four axis, SCARA Robot and three, five and six axis Articulated Robots- The inverse kinematics problem, General properties of solutions. Tool configuration, Inverse kinematics of four axis SCARA robot and three and five axis, Articulated robot-Workspace Analysis, work envelope of a Four axis SCARA robot and five axis articulated robot workspace fixtures, the pick and place operations, Joint 11 RB-2013 SRM space technique - continuous path motion, Interpolated motion, straight line motion and Cartesian space technique in trajectory planning-Manipulator Dynamics-Lagrange's equation kinetic and potential energy-Link inertia Tensor, link Jacobian Manipulator inertia tensor. Gravity, Generalized forces, Lagrange-Euler Dynamic model, Dynamic model of a Two-axis planar robot, Newton Euler formulation, Lagrange - Euler formulation, problems.
References
1. Robert J. Schilling, Fundamentals of Robotics Analysis and Control, PHI Learning., 2009. 2. Richard D. Klafter, Thomas .A, Chri Elewski, Michael Negin, Robotics Engineering an Integrated Approach, Phi Learning., 2009. 3. P.A. Janaki Raman, Robotics and Image Processing An Introduction, Tata Mc Graw Hill Publishing company Ltd., 1995. 4. Francis N-Nagy Andras Siegler, Engineering foundation of Robotics, Prentice Hall Inc., 1987. Karunya University 5. Bernard Hodges, Industrial Robotics, Second Edition, Jaico Publishing house, 1993. 6. Tsuneo Yohikwa, Foundations of Robotics Analysis and Control, MIT Press., 2003. 7. John J. Craig, Introduction to Robotics Mechanics and Control, Third Edition, Pearson, 2008. 8. Bijay K. Ghosh, Ning Xi, T.J. Tarn, Control in Robtics and Automation Sensor – Based integration, Academic Press, 1999. 14EI3065 ADVANCED INSTRUMENTATION AND PROCESS CONTROL FOR FOOD ENGINEERS Credits: 3:0:0 (Version 1.1) Course Objective: To introduce the concept of process instruments for various physical variables, system, automation. To gain knowledge of the different controllers To learn the complex control techniques used in process industries Course Outcome: Apply the knowledge of Measurement to various applications. Analyze the characteristics of Instrumentation systems. Design controllers for a typical application Functional Elements of an Instrument, Performance Characteristics, Static and Dynamics Characteristics, Open loop and closed loop systems, Response of First Order and Second order system for Unit Step input, Response of Second Order system for Unit Step Input. Pressure measurement: Manometers, Elastic elements, McLeod gauge, Ionization gauge, Thermal Conductivity Gauge:Pirani Gauge, Thermocouple Gauge, Temperature Measurement: Expansion Thermometer, Filled System Thermometer, Pyrometers,Thermocouple, RTD, Thermistor, Level Measurement: Direct methods, Radiation Level Detector, Ultrasonic Level Detector, Flow Measurement: Turbine flowmeter, Rotameter, Electromagnetic flowmeter, Ultrasonic flowmeter, Measurement of pH , Viscosity, Process Automation: Process Variables– Degrees of Freedom, Control Modes: P– PI–PID –Final Control element, Actuators, Control Valve characteristics, Control Valve types, Complex Control Techniques: Cascade control, Ratio control, Feed forward control, Split Range Control, Inferential Control, Case studies: Distillation column, Chemical reactor, Heat exchanger, Condenser, Evaporator References 1. Singh. S. K., “Industrial Instrumentation and Control”,2nd Edition, Tata McGraw– Hill,New Delhi, 2004. 2. Curtis Johnson, D., “Process Control Instrumentation Technology”, Prentice Hall of India,2006. 3. Coughanowr, and Koppel,“ Process systems analysis and control” , Tata McGraw– Hill,New Delhi,2004. 4. Seborg. D. E., Edger. T. F, and Millichamp. D. A, “Process Dynamics and Control”,JohnWiley and Sons, Newyork,2004.
5. Roffle. B., Betlem. B. H. L., “Advanced Practical Control”, Springer, Newyork,2004. 6. Stephanopoulos, “Chemical Process Control”, 2nd Edition, Prentice Hall, NewDelhi,
Credits: 0:0:2 14EI3066 SENSORS AND DATA ACQUISITION LAB
(Version 1.1)
Karunya University Course Objective: To learn the characteristics of sensors. To introduce the concept of data acquisition. To deal with experiments in data acquisition and analysis Course Outcome: Determine the characteristics of sensors. Acquire real time data for analysis Analyze acquired signals. List of experiments The faculty conducting the laboratory will prepare a list of 12 experiments and get the approval of HoD/Director and notify it at the beginning of each semester. 14EI3067 TRANSDUCER ENGINEERING Credits: 3:0:0 (Version 1.1) Objective: To elaborate on basic and advanced concepts of nanosensors and transducers for nanotechnology applications. To teach various transducers effects for the best understanding of various nanotransducers. To elaborate on the various types of nanosensors and actuators. Outcome: The students should be able to understand basic and advanced concepts of nanoelectronic devices The students should be able to understand basic and advanced concepts of sensors The students should be able to understand basic and advanced concepts of actuators Course Description: Transducers - capacitive transducers -Acoustic wave transducers -MOS capacitor based transducers –FET based transducers – Cantilever based transducers - Sensor Characteristics and Physical effects Static characteristics - Dynamic characteristic - Photoelectric effect – photodielectric effect –Photoluminescence effect – electroluminescence effect – chemiluminescence effect –Doppler effect –Barkhausen effect – Hal effect –Nano based Inorganic sensors - Organic /Biosensors - Signal conditioning and data acquisition - Phase locked loop. References 1. Nanoelectronics and Nanosystems: From transistors to Molecular and Quantum Devices by K. Goser (Edition, 2004), Springer. London. 2. Nanotechnology enabled sensors by Kouroush Kalantar – Zadeh, Benjamin Fry, Springer Verlag New York, (2007). 3. Sensors and signal conditioning, Ramon Pallas-Areny, John G. Webster John,2nd edition, Wiley & Sons (2001). 4. S.Renganathan “Transducer Engineering” – Allied publishers Limited, 1999.
5. Ernest O. Doeblin “Measurement Systems – Application & Design” McGraw – Hill Publishing company, 1990. 6. Biosensing: International Research and Development, Jerome Schultz, Milar Mrksich, Sangeeta
N. Bhatia, David J. Brady, Antionio J. Ricco, David R. Walt, Charles L. Wilkins, Springer 2006 7. H.Rosemary Taylor, Chapman and Hal, “Data acquisition for sensor systems”, London, 2007
Karunya University
LIST OF SUBJECTS
S.No. Sub. Code
Name of the Subject
1 15EI2001 Health and Hospital Management 2 15EI2002 Medical Electronics 3 15EI2003 Biomedical Sensors and Transducers 4 15EI2004 Biomedical Sensors and Transducers Laboratory 5 15EI2005 Biosignal Conditioning Circuits 6 15EI2006 Biocontrol systems 7 15EI2007 Medical Diagnostic Equipment 8 15EI2008 Biosignal Processing Laboratory 9 15EI2009 Intelligent Instrumentation Systems Laboratory 10 15EI2010 Fundamentals of Biomechanics 11 15EI2011 Telemedicine
Credits
3:0:0 3:0:0 3:0:0 0:0:2 3:0:0 3:1:0 3:0:0 0:0:2 0:0:2 3:0:0 3:0:0
12 15EI2012 Radiological Imaging Techniques 13 15EI2013 Medical Image Computing 14 15EI2014 Biosignal conditioning circuits Laboratory 15 15EI2015 Biomedical Instrumentation Laboratory 16 15EI2016 Medical Therapeutic Equipment 17 15EI2017 Modelling of Physiological systems
3:0:0 3:0:0 0:0:2 0:0:2 3:0:0 3:0:0 18 15EI2018 BioVirtual Instrumentation Laboratory 0:0:2 19 15EI2019 Finite Element Modelling in Biomedical Engineering 3:0:0 20 15EI2020 Ambulatory Services 3:0:0 21 15EI2021 Ergonomics in Hospitals 3:0:0 22 15EI2022 Surgical Assist Systems 3:0:0 23 15EI2023 Sensory and Motor Rehabilitation 3:0:0 24 15EI2024 Hospital Automation 3:0:0 25 15EI2025 Medical Equipment Troubleshooting and Maintenance 3:0:0 26 15EI2026 Bio Fluid and Solid Mechanics 3:0:0 27 15EI2027 Computer Application in Modelling of Physiological Systems 3:0:0 28 15EI2028 Biomedical Optics 3:0:0 29 15EI2029 Patient and Device Safety 3:0:0 30 15EI2030 ICU and Operation Theatre Equipment 3:0:0 31 15EI2031 Medical Ethics 3:0:0 32 15EI2032 Bioelectric Phenomena 3:0:0 33 15EI2033 MEMS Sensor Technology 3:0:0 34 15EI2034 Biometric systems 3:0:0 35 15EI2035 Ionizing and Non-Ionizing Radiation 3:0:0 36 15EI2036 Radiation and Nuclear Medicine 3:0:0 37 15EI2037 Intelligent Instrumentation Systems 3:0:0 38 15EI2038 Modern Automotive and Intelligent Systems 3:0:0 39 15EI2039 Automotive Control and HIL Simulation 3:0:0 40 15EI2040 Automobile Electric and Electronics Systems 3:0:0 41 15EI2041 Automotive In-Vehicle Communication System 3:0:0 42 15EI2042 Automotive Telematics and Infotainment 3:0:0 43 15EI2043 Automotive Fault Diagnostics 3:0:0
15EI2001 HEALTH AND HOSPITAL MANAGEMENT
Credits: 3:0:0
Course Objective:
To understand the need and significance of clinical engineering and health policies. To familiarize the training strategies, quality management policies and information technology used in health care. To know the needs of managerial training to hospital staffs.
Course Outcome:
Appreciate the need for standard health policies and quality management in hospitals. Apply the knowledge of computer and information technology in health care. Relate the training needs at various level of organization.
Health Organization of the country, National Health Policies, Health Financing System, Organization of Technical Section. Management of Hospital Organization, Nursing section Medical Sector, Central Services, Technical Department, Definition and Practice of Management by Objective, Transactional Analysis Human relation in Hospital, Importance to Team Work, Legal aspect in Hospital Management. FDA Regulation, Joint Commission Of Accreditation for Hospitals, National Fire Protection Association, Standard, IRPC. Organizing Maintenance Operations, Paper Work Control, Maintenance Job, Planning Maintenance Work. Measurement and Standards, Preventive Maintenance, Maintenance Budgeting and Forecasting, Maintenance, Training, Contract Mainframe, Function of Clinical Engineer, Role to be performed in Hospital, Man power Market, Professional Registration, Structure in hospital.
References:
1. R.C. Goyal, “Handbook of Hospital Personal Management”, Prentice Hall of India, 2008. 2. Joseph. F. Dyro, “ Clinical Engineering Management”, Academic Press Series in Biomedical Engineering, 2004 3. Antony Kelly, “Strategic Maintenance planning”, Butterworths London, 2006. 4. Cesar A. Caceres and Albert Zara, “The Practice of Clinical Engineering”, Academic Press, 1977. 5. Webster, J.G. and Albert M. Cook, “Clinical Engineering Principles and Practices”, Prentice HallInc.Englewood Cliffs, 1979.
15EI2002 MEDICAL ELECTRONICS
Credits: 3:0:0
Course Objective:
To furnish information on the mechanisms of current flow in semi-conductors. To yield understanding about the basic operations of diode, transistor and their medical applications. To provide knowledge about advanced semiconductor devices and their significant practical applications in medical field.
Course Outcome:
Apply the concepts of electronic circuits to biomedical applications. Design practical circuits for acquisition and analysis of biomedical signals. Build simple circuits for biomedical signal and analysis.
Overview of medical electronic equipments, transduction of bioelectric potentials, concepts of bio-impedence. PN junction diodes-VI characteristics, rectifiers, Zener diodes, Regulators, LED, LCD, Laser diodes, Special purpose diodes and their medical applications BJT and its medical applications: Construction, Characteristics, Hybrid model. Transistor as amplifier, Transistor as a switch, Opto-coupler & its medical application. Junction field effect transistor and its medical applications: JFET, MOSFET and its classification, Power MOSFET, MOS as a charge transferring Device – CCD, Uni-junction transistor. Medical application of MOSFET. Differential amplifiers: CM and DM, feedback amplifiers, Oscillators – LC, RC, crystal and their medical application, Pulse circuits for medical devices.
References:
1. Khandpur. R. S.,“Handbook of Biomedical Instrumentation”, Tata McGraw-Hill, Second edition, 2003. 2. Robert L. Boylestad, Louis Nashelsky, “Electronic Devices and Circuit Theory”, Prentice Hall, Sixth edition, 2009. 3. David A Bell, “Electron Devices and Circuits”, Prentice Hall Of India, Fifth edition, 2007. 4. Millman and Halkias, “Electronic devices and Circuits”, Tata McGraw Hill, First edition, 1994. 5. Thomas L. Floyd, “Electron Devices״, Charles & Messil Publications, Tenth edition 2009.
15EI2003 BIOMEDICAL SENSORS AND TRANSDUCERS
Credits: 3:0:0
Course Objective:
To provide introduction to the field of medical sensors and an in depth and quantitative view of device design and performance analysis. To provide knowledge on the principle and operation of different medical transducers. To introduce the application of sensors and transducers in the physiological parameter measuring system.
Course Outcome:
Identify the key design criteria and suggest an appropriate wearable sensor approach which is most likely to meet a specific biosensor application. Use the principle of transducers to design medical instrumentation systems. Suggest suitable sensors for a particular application.
Study of biological sensors in the human body and their basic mechanism of action, Study of various corpuscles like pacinian, functions and modeling, Chemoreceptor, hot and cold receptors, baro-receptors, sensors for smell, sound, vision, osmolality and taste. Temperature transducers, Displacement transducers, potentiometric, resistive strain gauges, inductive displacement, capacitive displacement transducer. Pressure transducer, Blood pressure measurement, measurement of intracranial pressure, LVDT transducers, capacitive and piezo-electric type. Biosensors, Biocatalysts based biosensors, bio-affinity based biosensors & microorganisms based biosensors, biologically active material and analyte. Types of membranes used in biosensor constructions. Ion exchange membrane, electrodes, Electrolytic sensors, optical sensor, fiber optic sensors. Biosensors in clinical chemistry, medicine and healthcare, Commercial prospects for biomolecular computingsystems.
References:
1. Michael. R. Newman, David. G. Flemming“Physical Sensors for Biomedical Applications”, CRC Press Inc., Florida. 2004. 2. Pearson, J.E. Gill, A., and Vadgama, P. “Analytical Aspects of Biosensors”. Ann Clin. Biochem,2002. 3. R.S.C. Cobbold, “Transducers for Biomedical Instruments”, Prentice Hall. 2003. 4. Joseph. J. Carr, John Michael Brown, “Introduction to Biomedical Equipment Technology”, Prentice Hall and Technology, 2008. 5. John. G. Webster. “Medical Instrumentation, Application and Design”.Fourth Edition. Wiley &sons, Inc., New York. 2009.
Credits: 0:0:2
Course Objective:
To introduce the practical aspects of various medical transducers and their characteristics. To impart knowledge in measurement of Resistance, Inductance and Capacitance using bridges. To improve the skills in calibrating analog meters.
Description:
This laboratory introduces the different biomedical transducers, their working and determination of their characteristics.
Course Outcome:
Analyze the performance characteristics of various transducers and infer the reasons for the behavior. Critically analyze any measurement application and suggest suitable measurement methods. Calibrate basic instruments.
The faculty conducting the laboratory will prepare a list of 12 experiments and get the approval of HOD/Director and notify it at the beginning of each semester.
15EI2005 BIOSIGNAL CONDITIONING CIRCUITS
Pre requisite: 15EI2002 Medical Electronics
Credits: 3:0:0
Course Objective:
To understand bioelectric amplifiers To discuss filters and circuits To introduce application of signal conditioning in biomedical field
Course Outcome:
Identify the method to apply various signal conditioning circuits Interface bioelectric signals with embedded systems. Identify the application of signal condition circuits for biomedical field.
Nature of Bio Electricity: Bioelectric Currents, Nernst Potential, Diffusion Potential, Action potential, Detection of Bio electric events, bio-electrode and electrode-skin interface. Operational Amplifiers and Comparators. Instrumentation and Medical Isolation Amplifiers: Instrumentation Amplifier, Medical Isolation amplifiers. Digital Interfaces: Analog to Digital , Digital to Analog conversion, Special analog circuits and systems used in biomedical Instrumentation, Phase Detectors-Analog and Digital, Voltage Controlled Oscillators, Phase locked loops.Electrical Interface problems and Safety Standards in Bio Potential Measurements.
References:
1. Robert B. Northrop, “ Analysis and Application of Analog Electronic Circuits to Biomedical Instrumentation”, CRC Press, II Edition, New York,2004 2. Myer Kutz, “Biomedical Engineering and Design Handbook”, II Edition, Volume 1, McGraw Hill Professional,2009 3. Robert F. Coughlin, Frederick F. Driscoll, “Operational Amplifiers & Linear Integrated Circuits”, Prentice-Hall, 6th Edition,2001. 4. Sergio Franco, “Design with Operational Amplifier and Analog Integrated Circuits”, TMH, 3rd Edition, 2002. 5. Milman & Hallkias, “Integrated Electronics-Analog and Digital Circuit”, McGraw Hill, II Edition,2011.
15EI2006 BIOCONTROL SYSTEMS
Pre requisite: 14MA2003 Mathematical Transforms
Credits: 3:1:0
Course Objective:
To study various Bio control systems modeling technique. Time response analysis and frequency response analysis. Analyze biological control systems.
Course Outcome:
Model any physiological systems. Perform the analysis of given system in time domain and frequency domain. Perform Stability analysis and to design any physiological control systems.
Basic structure of control system, Positive and Negative Feedback, transfer functions, modeling of electrical systems, block diagram and signal flow graph representation of systems, difference between engineering and physiological control systems, generalized system properties , models with combination of system elements.Physiological system modeling, Linear model of respiratory mechanics, model of chemical regulation of ventilation, linear model of muscle mechanics, model of regulation of cardiac output, model of Neuromuscular reflex motion, Introduction to simulation. Step response of first order and second order systems, determination of time domain specifications of first and second order systems. Definition of steady state error constants and its computation, definition of stability, Routh-Hurwitz criteria of stability, construction of root locus. Frequency response, Nyquist stability criterion, Nyquist plot and determination of closed loop stability, determination of gain margin and phase margin using Bode plot, use of Nichol’s chart to compute resonant frequency and band width.
References:
1. Michael. C. K. Khoo, “Physiological control systems”, IEEE press, Prentice –Hall of India, 2001. 2. M. Gopal “Control Systems Principles and design”, Tata McGraw Hill ,2002 3. Benjamin C. Kuo, ”Automatic control systems”, Prentice Hall of India,7th edition, 1995 4. John Enderle, Susan Blanchard, Joseph Bronzino “Introduction to Biomedical Engineering” second edition, Academic Press, 2005. 5. Richard C. Dorf, Robert H. Bishop,” Modern control systems”,Pearson, 2004
15EI2007 MEDICAL DIAGNOSTIC EQUIPMENT
Credits: 3:0:0
Course objective:
To know the various biopotential recordings and operating procedure of ICCU equipment. To develop an understanding of the physiotherapy and diathermy equipment. To learn the safety standards of the diagnostic equipment.
Course outcome:
Develop measurement systems for biosignals and its signal conditioning circuits Know the safe operating procedure of Cardiac care monitoring instruments. Get clear domain knowledge about various types of wearable and implantable devices.
ECG-continuous monitoring systems for pulse rate, temperature, B.P, Respiration, Arrhythmia monitor; B.P.monitor, Blood flow and cardiac output, Measurement, Plethysmography, Oximetry, Treadmill (StressECG). EMG, EEG, EOG, ERG. Audiometer, Different modes and assessments. UV, Visible and IR Spectrophotometers, Flame Photometers, Electrolyte analysis using sensitive electrodes, pHmeter, principle and applications. Densitometer and Electrophoresis apparatus. Principles and applications of oil, gas and liquid chromatographs, MassSpectrometry, Flow Cytometry, Radioimmunoassay and ELISA techniques, Blood gas analyzers, Blood cell counters. Various types of Endoscopes, Fiber optic, Fluid optic, Integral Camera Electron Microscope, Transmission and Reflection.
References:
1. Khandpur. R.S. “Handbook of Biomedical Instrumentation”. Second Edition, McGraw Hill 2003. 2. Geddas, L.A. & Baker, L.E. “Principles of Applied Biomedical Instrumentation”. Third Edition. John Wiley & Sons. 2008. 3. John. G. Webster. “Medical Instrumentation, Application and Design”.Fourth Edition. Wiley &sons, Inc.,New York.2009. 4. Leslie Cromwell, Fred. J. Weibell & Erich. A. Pfeiffer. “Biomedical Instrumentation and Measurements”. Second Edition. Prentice Hall Inc.2000. 5. Joseph. J. Carr, John Michael Brown, “Introduction to Biomedical Equipment Technology”, Prentice Hall and Technology, 2008.
15EI2008 BIOSIGNAL PROCESSING LABORATORY
Co-Requisite: 14EC2014 Digital Signal Processing
Credits: 0:0:2
Course Objective:
To record the biosignals and analyze it. To study the different preamplifiers used for amplifying the biosignals. To impart knowledge about the measurements and recordings of bioelectric and biochemical signals.
Description:
This laboratory introduces the different signal processing techniques used for analysing and recording biosignals.
Course Outcome:
Analyze the performance of various biomedical equipments and infer their safety aspects. Critically analyze any measurement application and suggest suitable measurement methods. Calibrate medical instruments.
Credits: 0:0:2
Course Objective:
To impart knowledge on the integration of hardware circuits with software. To introduce the concepts of programming in an IDE and download it into a processor. To learn about the practical aspects of data acquisition and analysis.
Description:
This laboratory introduces the basics of sensor data acquisition and interfacing issues related to it.
Course Outcome:
Design interfacing circuits to acquire real time data and process it using software. Develop intelligent instrumentation systems for biomedical applications. Use communication protocols for data transmission.
Course Objective:
To introduce the Fundamental terms and concepts of human factors. To discuss anthropometric, biomechanical and physiological principles and how they are used to optimize human well-being and overall performance. To Identify, Analyze, Setup and implement solutions to a human factors problem.
Course Outcomes:
Acquire biosignals and perform the quantification. Apply biomechanical and physiological principles to optimize human well-being and overall performance. Analyze and implement solutions to human factors problem.
Introduction: Newton’s laws, Stress, Strain, Non Viscous fluid, Newtonian Viscous fluid, Visco elasticity, Blood Characteristics, Mechanical Interaction of Red blood cells with solid wall, Thrombous formation and dissolution, Medical applications of blood rheology. Bone & its properties. Bone structure and Composition, Blood Circulation in Bone, Viscoelastic properties of Bone, Electrical Properties of Bone, Fracture Mechanism and Crack Propagation in bones, Kinetics and Kinematics of Joints .Cardio vascular system, Mechanical properties of blood vessels- Arteries, Arterioles, Capillaries, Veins, Blood flow- Laminar & turbulent , Prosthetic Heart Valves & replacement. Biomechanics of Spine- Structure, Movements, Loads on Spine, Exo-skeletal system for Paraplegics, Structure of Hip- Movements, Loads on Hip, Total Hip Prosthesis , Structure of Knee- Movements , loads on knee, Knee prosthesis , Powered wheel chair, Crutches and canes. Human Locomotion- Gait Analysis, Foot Pressure measurements- Pedo-barograph , Mechanics of Foot-Arthritis, Biomechanical treatment.
References:
1. Özkaya, N., Nordin, M., Goldsheyder, D., Leger, D., “Fundamentals of Biomechanics’’, Equilibrium, Motion, and Deformation 3rd ed., Springer Science plus Business Media, 2012. 2. Duane Knudson, “Fundamentals of Biomechanics”, Second Edition, Springer Science plus Business Media, 2007. 3. Iwan W. Griffiths, Lippincott Williams & Wilkins, “Principles of Biomechanics & Motion Analysis”, Medical publication, 2006. 4. Donald R. Peterson, Joseph D. Bronzino, “Biomechanics Principles and Applications”, CRC Press, 2008. 5. Dhanjoo N.Ghista, “Applied Biomedical Engineering Mechanics”, CRC Press, 2008. 6. Lucas, Cooke, “A Primer of Biomechanics”, Springer –Verlag, 1999.
15EI2011 TELEMEDICINE
Credits: 3:0:0
Course Objective:
To introduce the key principles of telemedicine and health. To understand telemedical technology. To learn telemedical standards, mobile telemedicine and its application.
Course Outcomes:
Apply multimedia technologies in telemedicine. Use protocols behind encryption techniques for secure transmission of data. Apply telehealth in healthcare.
Telemedicine and Health: History and Evolution of telemedicine, Functional diagram of telemedicine system, Ethical and legal aspects of Telemedicine – Telemedical technology: Principles of Multimedia - PSTN, POTS, ANT, ISDN, Internet, Air/ wireless communications: GSM satellite, and Micro wave, Modulation techniques, Types of Antenna, Satellite communication, mobile communication. Internet technology and telemedicine using world wide web (www). Video and audio conferencing. Clinical data – local and centralized. Telemedical standards: Data Security and Standards: Encryption, Cryptography. Protocols: TCP/IP, ISO-OSI, Standards to followed DICOM, HL7, H. 320 series (Video phone based ISBN) T. 120, H.324 (Video phone based PSTN), Video Conferencing, Real-time Telemedicine integrating doctors / Hospitals, Cyber laws related to telemedicine. Mobile telemedicine and telemedical applications.
References:
1. Norris, A.C. “Essentials of Telemedicine and Telecare”, Wiley, 2002 2. Wootton, R., Craig, J., Patterson, V., “Introduction to Telemedicine. Royal Society of Medicine” Press Ltd, Taylor & Francis 2006. 3. O'Carroll, P.W., Yasnoff, W.A., Ward, E., Ripp, L.H., Martin, E.L., “Public Health Informatics and Information Systems”, Springer, 2003. 4. Ferrer-Roca, O., Sosa - Iudicissa, M. , Handbook of Telemedicine. IOS Press (Studies in Health Technology and Informatics, Volume 54, 2002. 5. Simpson, W. Video over IP. A practical guide to technology and applications. Focal Press Elsevier, 2006.
Course Objective:
To provide knowledge of the principle of operation and design of radiological equipment. To learn the preferred medical imaging methods for routine clinical applications. To understand the engineering models used to describe and analyze medical image.
Course Outcomes:
Apply the tools for different problems in medical imaging. Implement various techniques to analyze the medical images. Suggest suitable imaging methodology for a specific ailment.
Ultrasonics- Principles of image formation, display, scanning modes, types of display. X-Rayprinciples and production of hard and soft x-rays, fluoroscopy-image intensifiers, Generations of X-ray imaging. CT-evolution, image formation, mathematical details of algorithms used, typesspiral, transverse. Angiography. MRI-image acquisition, density weighted images-T1 and T2, spin-echo and spin relaxation techniques, types of pulse sequences for fast acquisition, NMR spectroscopy. Other imaging techniques- PET,SPECT,DS Angiography, IR imaging, Thermography-clinical application, LCD, thermography.
References:
1. John Ball and Tony Price. Chesney’s, “Radiographic Imaging”. Blackwell Science Limited, U.K. 2006 2. Khandpur.R.S. “Handbook o f Biomedical Instrumentation”. Second edition Tata McGraw Hill Pub.Co.,Ltd. 2003. 3. Farr, “The Physics of Medical Imaging”.Adem Hilger, Bristol & Philadelphia, 2007. 4. Joseph Bronzino. “The Physics of Medical Imaging”.Secondedition.2005.
15EI2013 MEDICAL IMAGE COMPUTING
Credits: 3:0:0
Course Objective:
To understand digital image processing and reconstruction techniques. To introduce the basic concepts and methodologies for processing the CT, MRI and Ultrasound images. To acquire knowledge in the basic geometric transforms used in digital image processing.
Course Outcome:
Analyse the physiological events associated with the entire human system. Extraction of features that helps in easy diagnosis of various arrhythmias. Put forth new algorithms for processing the images for better results.
Elements of visual perception, Image sampling and quantization. Basic relationship between pixels, basic geometric transformations, Introduction to Fourier Transform and DFT, Properties of 2D Fourier Transform, FFT, Separable Image Transforms, Walsh, Hadamard, Discrete Cosine Transform, Haar, Slant, Karhunen, Loevetransforms. Spatial Domain methods: Basic grey level transformation, Histogram equalization, Image subtraction, Image averaging, Spatial filtering: Smoothing, Sharpening filters, Laplacian filters, Frequency domain filters: Smoothing, Sharpening filters, Homomorphic filtering. Model of Image Degradation/restoration process, Noise models, Inverse filtering, Least mean square filtering, Constrained least mean square filtering, Blind image restoration, Pseudo inverse, Singular value decomposition. Lossless compression: Variable length coding, LZW coding, Bit plane coding, predictive coding, DPCM. Lossy Compression: Transform coding, Wavelet coding, Basics of Image compression standards: JPEG, MPEG, Basics of vector quantization. Edge detection, Thresholding, Region based segmentation, Boundary representation: chair codes, Polygonal approximation, Boundary segments, Boundary descriptors: Simple descriptors, Fourier descriptors, Regional descriptors.
References:
1. Rafael C. Gonzalez, Richard E Woods, “Digital Image Processing” , Pearson Education 2010. 2. William. K. Pratt,“Digital Image Processing” ,John Wiley, 2001. 3. Jayaraman S, Veerakumar .T, Esakkirajan. S, “Digital Image Processing,” TataMc Graw Hill Pub.Co. Ltd.,2009 4. Najarain Splinter, “Biomedical Signal and Image Processing”, Taylor and Francis, 2012. 5. Chanda Dutta Magundar,“Digital Image Processing and Applications”, Prentice Hall of India,
Credits: 0:0:2
Course Objective:
To understand the design of filters and circuits for bioelectric amplifiers. To impart knowledge of the different preamplifiers used for amplifying the biosignals. To impart knowledge about the application of signal conditioning in biomedical field.
Description:
This laboratory introduces the filter design and circuit design for bioelectric amplifiers.
Course Outcome:
Apply and analyze the front end analogue circuit design for ECG, EMG, EEG, etc. Identify the method to apply various signal conditioning circuits. Identify the amplifiers for a variety of biomedical sensors.
Course Objective:
To record the biosignals and analyze it. To study the different preamplifiers used for amplifying the biosignals. To impart knowledge about the measurements and recordings of bioelectric and biochemical signals.
Description:
This laboratory introduces the different diagnostic and therapeutic equipment, their working and the methodologies used for analysing and recording biosignals.
Course Outcome:
Analyze the performance of various biomedical equipment and infer their safety aspects. Critically analyze any measurement application and suggest suitable measurement methods. Calibrate medical instruments.
Course Objective:
To learn the principles of cardiac assist devices. To understand the need and use of extracorporeal devices, and the use of lasers in medicine. To enable the students to gain knowledge on the working of therapeutic clinical equipment.
Course Outcomes:
Suggest suitable therapeutic devices for ailments related to cardiology, pulmonology, neurology, etc. Analyze the different types of therapies for suitable applications. Appreciate the application of lasers in biomedical applications.
External and implantable pacemakers, Programmable pacemakers, Cardiac Defibrillators, Energy requirements, Implantable Defibrillators, Defibrillator analyzers. Principles of constant pressure and constant volume ventilators, Basic principles of electromechanical, Pneumatic and electronic ventilators, Nebulizer, Ventilator testing. Electro diagnosis, Electrotherapy, Electrodes, Stimulators for Nerve and Muscle, Functional Electrical Stimulation. High frequency heat therapy, Principle, Shortwave diathermy, Microwave diathermy, Ultrasonic therapy, Lithotripsy, Therapeutic radiation, Therapeutic UV Lamps. Basic principles of Biomedical LASERS: Applications of lasers in medicine,CO2 laser, He-Ne laser, Nd-YAG and Ruby laser.
References:
1. Khandpur. R.S., “Handbook of Biomedical Instrumentation”. Second Edition. TataMc Graw Hill Pub. Co.,Ltd. 2003. 2. John. G. Webster. “Medical Instrumentation, Application and Design”.Fourth Edition. Wiley &sons, Inc.,New York.2009. 3. Leslie Cromwell, Fred. J. Weibell & Erich. A. Pfeiffer. “Biomedical Instrumentation and Measurements”. Second Edition. Prentice Hall Inc.2000. 4. JohnLow & AnnReed. “Electrotherapy Explained, Principles and Practice”. Second Edition. Butterworth Heinemann Ltd. 2000. 5. Joseph. J. Carr, John Michael Brown, “Introduction to Biomedical Equipment Technology”, Prentice Hall and Technology, 2008.
15EI2017 MODELLING OF PHYSIOLOGICAL SYSTEMS
Prerequisite: 15EI2006 Biocontrol Systems
Credits: 3:0:0
Course Objective:
To understand the basic ideas related to modeling and different modeling techniques of certain physiological systems. To analyze physiological system in time and frequency domain. To understand the physical and chemical properties of blood.
Course Outcomes:
Develop mathematical model of physiological system. Simulate the physiological system and analyze in time and frequency domain. Apply system identification and optimization concepts in modeling.
Systems, Analysis, examples of physiological control systems, differences between engineering and physiological control systems. Generalized system properties, mathematical approach, electrical analog, linear models, lung mechanics, muscle mechanics, distributed parameter versus lumped parameter models, static analysis, regulation of cardiac output, blood glucose regulation, chemical regulation of ventilation, electrical model of neural control mechanism Physical, chemical and rheological properties of blood, Dynamics of circulatory system. Biochemistry of digestion, types of heat loss from body, models of heat transfer between subsystem of human body like skin core, etc. and systems like within body, body environment, Transport through cells and tubules, diffusion, facilitated diffusion and active transport, methods of waste removal, counter current model of urine formation in nephron, Modeling Henle’sloop. Modeling oxygen uptake by RBC and pulmonary capillaries, Mass balancing by lungs, Gas transport mechanism of lungs, oxygen and carbondioxide transport in blood and tissues.
References:
1. David.O.Cooney,“Biomedical Engineering Principles”.Marcel Decker Pub.Co.2000 2. Michael C.K.Khoo.”Physiological Control Systems”.Prentice Hall of India. 2000 3. John Enderly, Susan Blanchard, Joseph Bronzino.“Introduction to Biomedical Engineering”, Second Edition, Academic Press Series in Biomedical E ngineering, 2005.
15EI2018 BIOVIRTUAL INSTRUMENTATION LABORATORY
Credit 0:0:2
Course Objective:
To provide knowledge about data acquisition and control an external measuring device by interfacing to a computer. To familiarize in signal conditioning and various processing tools. To become competent in designing virtual instruments for various biomedical measurements and applications.
Description:
This laboratory introduces the various applications of virtual instruments in biomedical engineering.
Course Outcome:
Identify salient traits of a virtual instrument and incorporate these traits in projects. Experiment, analyze and document in the laboratory prototype measurement systems using a computer, plug-in DAQ interfaces and bench level instruments. Recognize the application of Vis in medical instrumentation in developing medical instruments.
15EI2019 FINITE ELEMENT MODELLING IN BIOMEDICAL ENGINEERING Credit 3:0:0
Course Objectives:
To equip the students with the Finite Element Analysis fundamentals. To enable the students to formulate the design problems into FEA. To introduce basic aspects of finite element technology, including domain discretization, polynomial interpolation, application of boundary conditions, assembly of global arrays, and solution of the resulting algebraic systems.
Course Outcome: Identify mathematical model for solution of biomedical engineering problems. Formulate simple problems into finite elements and develop 3D models . Use professional-level finite element software to solve problems in dynamics of blood flow, cardiovascular system, etc.
Introduction: Basic concepts- Historical Background -finite element packages- Boundary Value and Initial Value Problem-Weighted Residual Methods-General Procedure of FEAElement Types and its Characteristics-Concept of Element Assembly-Bandwidth and its effectsBoundary conditions-Aspect Ratio- Pascal’s Triangle- Stiffness matrix -beam element-Shape Function for Spar element, Beam element-Convergence and Continuous criteria- Structural Problems: Equations of elasticity- plane elasticity problems - Bending of elastic plates .Heat Transfer Problems. One Dimensional Basic equation of heat transfer derivation of finite element equation- Fluid Mechanics Problems: incompressible fluid flow-Biomedical Applications: Case studies: FE modeling of blood flow channel, lungs, cardiovascular system, analysis using mechanical solver, electrical solver, electromechanical solver, Vibration analysis using software tools.
References:
1. David.V.Hutton, “ Fundamentals of Finite Element Analysis”, Tata McGraw Hill,2003. 2. Tirupathi.R.Chandrupatla, Ashok.D.Belegundu. ‘Introduction to Finite Elements in Engineering’, Prentice Hall of India, 2004. 3. Rao. S.S. “The Finite Element Method in Engineering”, Second Edition, PergamonPress,Oxford, 2001.
15EI2020 AMBULATORY SERVICES
Credits:3:0:0
Course objectives:
to understand the need for ambulance services to learn the wireless measuring instruments for vital parameter monitoring to understand computer based technology in ambulatory services
Course outcomes:
Appreciate the purpose of ambulatory services to save human life. Apply software and hardware required to develop wireless monitoring system Design the patient transport and networked services
Patient monitoring systems- artifacts- denoising techniques- Advancements in Wireless patient monitoring-design of ambulance- ambulance train- disaster relief squad- regulation for patient transportation-Lift mechanism- design of mobile services- diagnostic equipments with battery backup-mobile X-ray unit-nursing-medical gas handling-regulations-GPS in ambulancenetworked services-accident care- automated alert system- smart systems-fire protectionmaintenance and regulation- Arreditation for ambulatory services- Telehealth technology.
References:
1. David Tse and PramodViswanath, “Fundamentals of Wireless Communication”, Cambridge University Press, 2005. 2. Andreas F. Molisch, “Wireless Communications, 2nd Edition, John Wiley &sons,USA, 2010. 3. Jochen Schiller, “Mobile Communications”, Addison Wesley Publishers, 2000. 4. Yi-Bing Lin and ImrichChlamtac, “Wireless and Mobile Network Architecture”, John Wiley and Sons, New Delhi, 2nd Edition, 2001. 5. Feher K., “Wireless Digital Communications”, Prentice Hall of India, New Delhi, 1995.
15EI2021 ERGONOMICS IN HOSPITALS
Credit 3:0:0
Course Objective:
To introduce the Fundamental terms and concepts of human factors To discuss anthropometric, biomechanical and physiological principles and how they are used to optimize human well-being and overall performance. To learn signal acquisition, recording and processing of the physiological signals related to human stress problem
Course Outcomes: Quantify the anthropometric, biomechanical and physiological principles. Apply instrumentation techniques for the disability and Apply signal processing techniques for analysis and find solutions.
Definition, human technological system, human–machine system, manual, mechanical, automated system, human system reliability, human system modeling, Human Output And Control, material handling, motor skill, human control of systems, controls and data entry devices, hand tools and devices, Workplace Design: Applied anthropometry, workspace design and seating, design of computer worktable, case studies. Environmental Conditions Illumination, climate, noise, motion, sound, vibration. Musculoskeletal anatomy, Quantitative models, Measurement of muscle stress, fatigue using EMG, EEG, Modeling of pain. Human body kinematics and Instrumentation - Instrumentation for the Measurement human body kinematics. Case studies: computer based evaluation of recovery process caused due to limb fractures, cognitive stress to patients.
References:
1. Bridger R S, “Introduction to Ergonomics”, Taylor and Francis, London, 2003. 2. Karl Kroemer, Henrike Kroemer, Katrin Kroemer-Elbert, “Ergonomics” How to Design for Ease & Efficiency, Prentice Hall International Editions, 2001. 3. Mark S Sanders, “Human Factors in Engineering and Design”, McGraw Hill, NewYork, 1993. 4. Martin Helander, A Guide to Ergonomics of Manufacturing, Tata McGrawHill, 1996. 5. Mccormic.E.J., and Sanders.M.S, “Human factors in Engineering and Design”, McGraw Hill, 1992.
15EI2022 SURGICAL ASSIST SYSTEMS
Credits: 3:0:0
Course objectives:
To understand the need for assistive devices To understand robot kinematics To understand embedded system applications in controlling robot motion
Course Outcomes:
Write robotic equations of motion Design path planning algorithms Develop assist devices for surgery
Introduction to Robotics, degree of freedom, path planning, Lagrange equation of motion, kinetics, payload sensors, actuators, gripper- lift mechanism for surgery, special lighting controls, ventillator, heart lung machine, proximity switches, controllers, artificial intelligence, machine vision, design of controllers based on embedded system, human machine interface, case studies.
References:
1. Jacob Rosen, Blake Hannaford, Richard.M.Satava, “Surgical Robotics”, Systems Applications and Visions”, Springer, 2010. 2. Farid Gharagozloo, Farzad Najam,”Robotic surgery”, McGrawHill Publishers, US, 2009.First edition. 3. Bruno Siciliano and Lorenzo Sciavicco, “Robotics: Modelling, Planning and Control, Springer, 2010. 4. Bruno Siciliano, Oussama Khatib, “Springer Handbook of Robotics”, Springer, 2008. 5. Sebastian Thrun, Wolfram Burgard,” Probabilistic Robotics” ,Intelligent Robotics and Autonomous Agents series, 2005
15EI2023 SENSORY AND MOTOR REHABILITATION
Credit: 3:0:0
Course Objective:
To familiarize with the technology currently used to improve the quality of life of individuals with disabilities. Know new rehabilitation concepts for future development and applications. Understand orthopedic prosthetics and orthotics in rehabilitation.
Course Outcome:
Choose the appropriate assist device suitable for specific disorder. Develop new assist devices for the needy. Use limb and prosthetic devices.
Rehabilitation concepts, Engineering concepts in sensory rehabilitation, motor rehabilitation, communication disorders. Wheeled mobility, Categories of wheel chairs, wheel chair structure & component design, Ergonomics of wheel chair propulsion, Power wheel chair electrical system, Personal transportation. Sensory aids for the blind, Rehabilitation of auditory disorders, treatment of hearing impairment, Hearing aids and other assistive devices. Language disorders associated with Dementia, assessment and treatment of Apraxia and Dysarthia. Orthopedic prosthetics and orthotics in Rehabilitation: Fundamentals. Applications: Computer Aided Engineering in customized component design, intelligent prosthetic knee. A hierarchically controlled prosthetic hand, A self, aligning orthotic knee joint. Externally powered and controlled orthotics and prosthetics. Active Above Knee Prostheses, Myoelectric hand and arm prostheses. The MARCUS Intelligent Hand Prostheses.
Reference books:
1. Bronzino J.D., “The Biomedical Engineering handbook”. Second Edition. Vol. II, CRC press, Bocaraton, 2000 2. Cooper Douglas, A. Hobson.” An Introduction to Rehabilitation Engineering”, CRC Press, 2007 3. Horia, Hicholi, Teodorescu L., Lakme C Jain.”Intelligent Systems and 4. Technologies in Rehabilitation Engineering”. First Edition. CRC Press. 2000
15EI2024 HOSPITAL AUTOMATION
Credits: 3:0:0
Course Objectives
To know the need for acquisition and processing of multiple data types To learn about power generation, utility and protection system To know about distributed and central monitoring functions
Course outcomes:
Apply the data processing techniques and digital storage and transmit data Analyse the need of power generator, its maintenance and energy conservation, fire protection in hospitals Use digital computer for central monitoring of parameters
Medical data handling and automation-RFID in record retrival-surveillance system in hospitalbuilding automation-power generator, maintenance, battery-maintenance and troubleshooting, energy conservation-Medical gas production and automation-boiler, blower, compressor, air conditioning, lighting, heating systems, piping, leakage test- fire prevention and safety automation-control room, limit switches, sensors, controllers, alarm system –regulation and standards.
References:
1. Khandpur. R. S., “Handbook of Biomedical Instrumentation”, Prentice Hall of India, New Delhi, 2003. 2. Joseph J. Carr and John M. Brown, “Introduction to Biomedical Equipment Technology”, Pearson Education India, Delhi, 2008. 3. Curtis Johnson, D., “Process Control Instrumentation Technology”, Prentice Hall of India,2006. 4. John V. Grimaldi and Rollin H. Simonds., Safety Management, All India Travelers Book seller, New Delhi, 1989. 5. N.V. Krishnan, Safety in Industry, JaicoPublishery House, 1996.
Pre requisite: 15EI2002 Medical Electronics
Credits: 3:0:0
Course Objectives:
To know about power supply operation and troubleshooting To design electrical equipments with safety standards To know the principle of medical equipments.
Course Outcomes: Identify the reasons for equipment failure. Appreciate the need for grounding aspects , maintenance and troubleshooting. Design advanced equipments to solve critical problems.
AC, DC power supply, Grounding, shielding, Guarding, insulation testing, insulation resistance measurement, Testing of electronic components, Troubleshooting of PCB boards, Calibration of analog and digital sensor probe, Display interface, Safe electrical practice, Cables and standard, Fuse, Transformer testing, CT and PT, Panel wiring, Troubleshooting of X-ray machines, Troubleshooting of ECG recorders, ultrasound machine, patient monitor, ventilator, dialyser, heart lung machine, surgical lights, incubator, baby warmer, infusion pumps, annual maintenance, contract requirements, vendor services, quality and safety standards.
References: 1. Medical Equipment Maintenance Manuel, Ministry of Health and Family Welfare, New Delhi, 2010. 2. Shakti Chatterjee,Aubert Miller, “Biomedical Equipment Repair”, Cengage Learning Technology & Engineering, 2010. 3. David Herres, “Troubleshooting and Repairing Commercial Electrical Equipment”, McGrawHill, Professional edition, 2013. 4. L.Nokes.B.Turton, D.Jennings, T. Flint,”Introduction to Medical Electronics Applications”, A Butterworth Heinemann Title. 1995 5. Joseph F. Dyro, “Clinical engineering handbook, Elsevier Academic Press, 2004.
15EI2026 BIOFLUID AND SOLID MECHANICS
Credits: 3:0:0
Course Objective:
To learn the laws governing the mechanics & materials used in medicine. To introduce the mechanics involved in the blood flow to various vessels and valves. To study the breathing mechanism, airway resistance and lung diseases.
Course Outcome:
Analyze the problems in physiological systems and relate to its characteristic phenomenon Apply the mechanical principles in acquiring data, transduction and useful representation for clinical diagnosis. Identify the mechanical properties of the human body
Mechanical Properties of Materials used in Medicine, Newton’s laws, stress, strain, elasticity, viscoelasticity, Tissue Reactions and Blood Compatibility. Biofluid Mechanics:Hook’s law, Newtonian Fluid, Non Newtonian fluid , Biomechanics of Degenerative Disorders, Hematology & Blood Rheology, Relationship between diameter, Instrumentation for velocity & pressure of blood flow, Cardiac And Respiratory Mechanics: Mechanical properties of blood vessels, Instrumentation for respiratory mechanics. Soft Tissue Mechanics, Orthopedic mechanics, Mechanical properties of cartilages, Mechanical properties of bone, Bio mechanics in orthopedics: Prosthetic design, GAIT, goniometer, accelerometer, sensors and instrumentation techniques for orthopedic mechanics, evaluation and design of manual activities in various occupations.
References:
1. Fung .Y. C., “Biomechanics: Mechanical properties of living tissues”, Springer-Verlag, 2nd Edition,2004. 2. NihatOzkaya, Margareta Nordin, “Fundamentals of Biomechanics: Equilibrium, Motion, and Deformation”, Springer, 3rd Edition, Verlag, 2012. 3. Duane Knudson, “Fundamentals of Biomechanics”, Springer, 2nd Edition, US, 2007. 4. Sahay and Saxena, “Biomechanics", Tata McGraw Hill, New Delhi, 1998. 5. J.B.Park, “Bio-materials - Science and Engineering”, Plenum Press, New York, 1984.
15EI2027 COMPUTER APPLICATIONS IN MODELLING OF PHYSIOLOGICAL SYSTEM
Pre requisite: 15EI2017 Modeling of physiological systems
Credits: 3:0:0
Course Objectives:
To understand the modeling of physiological system To know the simulation tools and techniques To use software tools for simulation and analysis
Course Outcomes:
To learn the modeling tools in softwares To analyse the characteristics of physiological system To develop graphic user interface which helps as a tool for diagnosis.
Modeling of physiological system, electrical equivalent network-simulation, modeling of fluid flow characteristics of cardiovascular system – simulation, microsensor design and analysis, modeling and simulation of cardiac system, glucose regulation system, modeling and simulation of anesthesia, modeling of bones using finite element techniques and analysis.
References:
1. Myer Kutz, “Biomedical engineering and design Hand book”, CRC press, UK, 2004. 2. Sanjay Gupta, Joseph John, “Virtual Instrumentation using LabVIEW”, Tata McGraw Hill publishing, New Delhi, 2005. 3. MiChael.C.Khoo, “Physiological control systems -Analysis, simulation and estimation”,Prentice Hall of India Pvt Ltd, New Delhi, 2001. 4. Jovitha Jerome, “Virtual Instrumentation Using LabVIEW”, PHI Learning Pvt. Ltd., 2010.
15EI2028 BIOMEDICAL OPTICS
Credit 3:0:0
Course Objective:
To offer clear understanding of tissue characteristics when it is exposed to optical energy. To know about various optical sources and applications of lasers. To learn about Holography and its medical applications.
Course Outcome:
Analyze the optical properties of tissues and light interactions with tissues. Use optical sources for instrumentation and measurement. Apply photo dynamic therapy and optical holography for biomedical applications.
Optical properties of the tissues: Refraction, Scattering, absorption, light transport inside the tissue, tissue properties, Light interaction with tissues, optothermal interaction, fluorescence, speckles. Instrumentation for absorption, scattering and emission measurements, excitation light sources –high pressure arc lamp, solid state LEDs, LASERs, optical filters, polarisers, solid state detectors, time resolved and phase, resolved detectors, Laser in tissue welding, lasers in dermatology, lasers in ophthalmology, otolaryngology, urology. Wave fronts, Interference patterns, principle of hologram, optical hologram, applications, Near field imaging of biological structures, in vitro clinical diagnostic, fluorescent spectroscopy, photo dynamic therapy.
References:
1. Tuan Vo Dirh, Biomedical photonics – Handbook , CRC Press, Bocaraton, 2003. 2. Leon Goldman, M.D., &R.James Rockwell, Jr., Lasers in Medicine , Gordon and Breach, SciencePublishers Inc., New York, 1971.
15EI2029 PATIENT AND DEVICE SAFETY
Credits: 3:0:0
Course Objective:
To provide a source of useful ideas, concepts, and techniques that could be selectively applied to reduce an intolerable rate of unacceptable errors, mistakes, goofs, or shortcomings in expected Medical Device performance. To avoid patient injury, achieving efficacious treatment, and controlling health care costs. Medical error has proved to be a difficult and recalcitrant phenomenon.
Course Outcome:
Develop medical equipment that conforms to safety standards. Suggest reasonable, acceptable, and more effective remedies and countermeasures in medical device errors. Apply appropriate safety regulations to medical devices.
Reliability, Types of reliability, The concept of failure, Causes of failure, Types of Failures in Medical devices, Safety testing, Failure assessment and Documentation, Visual inspection: External & Internal visual inspection. Measurement, Safety parameters, Safety and risk management, Manufacturer’s and physician’s responsibilities. Safe medical devices, operation –Medical Application safety. Environmental safety, Interference with the environment, Ecological safety. Electrical Safety, Limitation of Voltages ,Macroshock and Microshock, Earth and Protection, Leakage currents, Magnetic fields and compatibility. Medical Standards and Regulations – Device classification – Registration and listing –Declaration of conformance to a recognized standard – Investigational Device Exemptions (IDEs) – Institutional Review Boards (IRBs) – IDE format – Good laboratory practices (GLPs) –Good manufacturing practices (GMPs) – Human factors – Design control – The Medical Devices Directives (MDD) – Definition, Process and choosing the appropriate directive –Active Implantable Medical Devices Directive (AIMDD) – In Vitro Diagnostic Medical Devices Directive (IVDMDD).
References:
1. Bertil Jacobson and Alan Murray, “Medical Devices Use and Safety”, Elsvier Limited,2007. 2. Richard Fries,“Reliable Design of Medical Devices – Second Edition”, CRC Press,Taylor& Francis Group, 2006. 3. Norbert Leitgeb “SafetyofElectromedicalDevicesLaw – Risks –Opportunities”,SpringerVerlog/Wein, 2010. 4. Gordon R Higson, “Medical Device Safety – The regulation of Medical Devices forPublic Health and Safety”, IOP Publishing Limited, Bristol and Philadelphia, 2002.
15EI2030 ICU AND OPERATION THEATRE EQUIPMENT
Credit: 3:0:0
Course Objective:
To offer clear understanding of various intensive care equipment and their working. To understand the necessity of different operation theatre equipment. To know about different dialyzers and ventilators.
Course Outcome:
Apply the knowledge acquired, in designing new monitoring devices for ICU. Suggest suitable surgical instruments and operational devices. Assist the medical personnel’s during emergency situations in the ICU.
Suction apparatus,Different types;Sterilizers,Chemical, Radiation, Steam for small and larger units. Automated drug delivery systems, Infusion pumps, closed loop control infusion system, implantable infusion system. Hemodialysis Machine, Differen ttypesof Dialyzers, Membranes, Machine controls and measurements. Heart Lung Machine, different types of oxygenators, peristaltic pumps, Incubators. OperationTheatreEquipment: Surgical diathermy, Instruments for operation. Anesthesia Equipment, Humidification, Sterilization aspects, Boyles apparatus. Centralized Oxygen, Nitrogen, Air supply & Suction. Centralized Air Conditioning, Operation Theatre table & Lighting. Patient electrical safety, Types of hazards,Natural protective mechanisms against electricity, Leakage current, Inspection of grounding and patient isolation, Hazards in operation rooms, ICCU and IMCUs, Optocouplers and Pulse transformers.
References:
1. Khandpur,R.S,”Handbook of Biomedical Instrumentation ”,Second Edition. Tata Mc Graw Hill Pub. Co., Ltd. 2003 2. John, G. Webster. Medical Instrumentation, Application and Design. Second Edition. John Wiley & sons, Inc., NewYork. 2008. 3. Joseph Dubovy, Introduction to Biomedical.Mc Graw Hill Co.1978 4. Terry Bahil.A, Biomedical and Clinical Engineering. Prentice Hall Inc.1981
15EI2031 MEDICAL ETHICS
Credit: 3:0:0
Course Objective:
Achieve familiarity with some basic ethical framework & understand how these ethical frame works can help us to think through contemporary questions in medical ethics. To know about the legal and ethical principles and application of these in medical field. Gain knowledge about the medical standards that to be followed in hospitals.
Course Outcome:
Apply the moral values and ethics in their work environment Maintain the confidentiality issues in medical practice. Suggest standards that are patient centered.
Introduction to medical ethics: Definition of Medical ethics, Scope of ethics in medicine, American medical Association code of ethics, CMA code of ethics- Fundamental Responsibilities, The Doctor and the Patient, The Doctor and the Profession, Professional Independence, The Doctor and Society. Ethical theories & moral principles: TheoriesDeontology& Utilitarianism, Casuist theory, Virtue theory, The Right Theory. Principles - NonMaleficence, Beneficence, Autonomy, Veracity, Justice. Autonomy & Confidentiality issues in medical practice, Ethical Issues in biomedical research, Bioethical issues in Human Genetics & Reproductive Medicine. Hospital accreditation standards, Accrediation- JCI Accreditation & its Policies. Patient centered standards, Healthcare Organization management standards. Hospital safety standards: Life Safety Standards- Protecting Occupants, Protecting the Hospital From Fire, Smoke, and Heat, Protecting Individuals From Fire and Smoke, Providing and Maintaining Fire Alarm Systems, Systems for Extinguishing Fires Environment of Care StandardsMinimizing EC Risks, Smoking Prohibitions, Managing Hazardous Material and Waste, Maintaining Fire Safety Equipment, Features, Testing, Maintaining, and Inspecting Medical Equipment.
References:
1. Domiel A Vallero “Biomedical Ethics for Engineers”, Elsevier Pub.1st edition, 2007 2. Biomedical Ethics: A Canadian Focus. Johnna Fisher (ed.), Oxford University Press Canada, 2009 3. Robert M Veatch” Basics of Bio Ethics”, Second Edition. Prentice- Hall,Inc. 2003
15EI2032 BIOELECTRIC PHENOMENA
Credits: 3:0:0
Course Objective:
To offer clear understanding of ionic activity in cells and generation of action potential. To know about generation and conduction of cardiac, nervous and muscular action potentials. To impart knowledge on the measurement and recording of the various biopotentials.
Course Outcome:
Analyze the ionic activity in cells and generation of action potential. Interpret the cardiac, nervous and muscular action potentials for diagnostic purpose. Measure and record the various bio potentials.
Cell membrane: Structure, Excitable cells, Nernst potential, Resting membrane potential, Polarized state, Goldman Hodgkin Katz equation, Action potential , Propagation of nerve impulses, Refractory period, Hodgkin Huxley model of squid gait axon membranes, Modes of transport of substances across the cell membranes. Electrical activity of the heart: Cardiac muscle, Action potentials in cardiac muscle, SA node, Origin and propagation of rhythmical excitation & contraction, refractoriness, regular and ectopic pace makers, Electrocardiogram, Arrhythmias, Electrical activity of brain – Sleep stages, Brain waves, waveforms & measurements, 10-20 electrode system , Evoked potentials , Magneto encephalogram, Electrogastrogram, Electroretinogram, Electroocculogram. Electrical activity of muscles –neuromuscular junction, synaptic potentials, motor unit, motor unit action potentials, Electromyogram ,Electrodes for measurement of biopotentials, electrode tissue interfaces , Polarizable and non polarizable electrodes , skin contact impedance. Electroneurogram – nerve conduction studies.
References: 1. Arthur C. Guyton : Textbook of Medical Physiology, Prism Books (Pvt) Ltd & W.B. Saunders Company, 12th edition, 2012 2. D.J. Aidley: The Physiology of Excitable cells, 3rd Ed., Cambridge University Press, 4th edition, 1998 3. John G. Webster: Medical Instrumentation - Application and Design; Houghton Mifflin Co., Boston, 3rd edition, 2009. 4. Richard Aston: Principles of Biomedical Instrumentation and Measurement, Merril Publishing Co., Columbus, 1st edition, 1990. 5. Khandpur R S: Handbook of Medical Instrumentation, Tata McGraw Hill, New Delhi.2004.
15EI2033 MEMS SENSOR TECHNOLOGY
Credits: 3:0:0
Course Objective:
To introduce the theories and concepts of microelectromechanical systems. To know about the materials used and the manufacture of MEMS To impart knowledge on the various types of Microsystems and their applications in medical field.
Course Outcome:
Analyze the theories and concepts of micro electro mechanical systems. Apply the fundamentals in the manufacture of MEMS Analyze the various types of Microsystems and their applications in medical field.
Introduction to MEMS: Historical Background, Smart Materials and Structures. Microsystems and their advantages. Materials used. Technology involved in MEMS. General applications in Aerospace, automotive industry and health care. Market size and world scenario. Micro machining technology: lithography, etching, ion implantation, wafer bonding, integrated processing, bulk micromachining, surface micro, machining, coating technology and CVD, LIGA process. Principles of Microsystems: general principles, micro sensors, pressure sensors, actuators, electrostatic forces, piezo-electric crystals, intelligent materials and structures. MEMS applications in medicine (BIOMEMS): special features/requirements for medical application. Current scenario of MEMS for health care. Drug delivery system and MEMS. Application models, blood pressure sensors, biochip, micro needles, microelectrodes, neural prosthesis, and catheter end sensors. Introduction to Nanotechnology: Nano materials, Nano materials fabrication by bottom, up and Top down approaches, Classification of Nano devices based on the characteristics, Medical use of Nano materials.
Reference books:
1. Sergey Edward Lysherski.Nano and Micro-electromechanical systems. Second Edition. CRC Press. 2005 2. WanjunWang, StevenA. Soper, Bio MEMS Technologies and Applications. CRC Press. 2006 3. N.P.Mahalik, Micro manufacturing & Nanotechnology. Springer. 2006
15EI2034 BIOMETRIC SYSTEMS
Credits: 3:0:0
Course Objective:
To introduce the basic concepts of fingerprint, iris, face and speech recognition. To impart knowledge on the general principles of design of biometric systems and the underlying trade-offs To render knowledge on personal privacy and security implications of biometrics based identification technology and the issues realized
Course Outcome:
Apply the technologies of fingerprint, iris, face and speech recognition. Analyze the general principles of design of biometric systems and the underlying tradeoffs. Inculcate knowledge on personal privacy and security implications of biometrics based identification technology and the issues involved.
Introduction and back ground, Biometric technologies, Biometric systems, Enrollment, templates, verification, Biometric applications, biometric characteristics, Authentication technologies -Need , Protecting privacy and biometrics and policy. Fingerprint pattern recognition, modeling of fingerprint images, fingerprint classification, fingerprint matching. Introduction to face recognition, Neural networks for face recognition, face recognition from correspondence maps, Hand geometry, scanning, Feature Extraction Adaptive Classifiers - Visual-Based Feature Extraction and Pattern Classification, Biometric fusion. Voice Scan, physiological biometrics, Behavioral Biometrics, Introduction to multimodal biometric system, Integration strategies, Architecture, level of fusion, combination strategy, training and adaptability, examples of multimodal biometric systems, Performance evaluationStatistical Measures of Biometrics ,Memory requirement and allocation. Introduction - Biometric Authentication Methods, Biometric Authentication Systems, Support Vector Machines. Securing and trusting a biometric transaction, matching location, local host authentication server, match on card (MOC), Multi biometrics and Two-Factor Authentication.
References:
1. James Wayman, Anil Jain, DavideMaltoni, Dario Maio, “Biometric Systems, Technology Design and Performance Evaluation”, Springer, 2005 2. S.Y. Kung, S.H. Lin, M.W.Mak, “Biometric Authentication: A Machine Learning Approach” Prentice Hall, 2005 3. Paul Reid, “Biometrics for Network Security”, Pearson Education, 2004. 4. Nalini K Ratha, Ruud Bolle, “Automatic fingerprint Recognition System”, Springer, 2003 5. L C Jain, I Hayashi, S B Lee, U Halici, “Intelligent Biometric Techniques in Fingerprint and Face Recognition” CRC Press, 1999.
15EI2035 IONIZING AND NON-IONIZING RADIATION
Credit 3:0:0
Course Objective:
To expose the student to the use of ionizing radition and its biological effects in the medical field. To know about the use of ionizing radiation in medical and industrial applications. To understand the biological effects of low and high doses of ionizing radiation.
Course Outcome:
Analyze the effect of radiation at cellular level. Analyze the effect of microwave on human organs and systems. Suggest suitable diagnostic and therapeutic devices to prevent unnecessary effects due to radiations.
Action of radiation in living cells: Various theories related to radiation at cellular level. Dna and chromosomal damages. Somatic application of radiation. Radio sensitivity protocols of different tissues of human. Ld50/30 effective radiation on skin, bone marrow, Eye, endocrine glands, and basis of radio therapy. Genetic effects of radiation: Threshold and linear dose, gene control hereditary diseases effect of dose. Effect of microwave: Effects on various human organs and systems. Wavelength in tissue, non thermal interaction. Standards of Protection, national and international standards and precautions. UV radiation, Classification of sources, measurement, photo medicine, uv radiation safety visible and infrared radiation.
References:
1. Mary Alice S, Paula J Visconti, E Russell Ritenour, Kelli Haynes,” Radiation Protection In medical Radiography,”Elsevier Health Sciences,2014 2. Glasser O.,”Medical Physics”, Volume I,II,III, The year book publishers inc, chicago 1980. 3. Moselly H., “Non ionizing radiation”, Adam-hilgar, Bristol 1988.
15EI2036 RADIATION AND NUCLEAR MEDICINE
Credits: 3:0:0
Course Objective:
To introduce the basic principles radiology, computer tomography and nuclear medicine. To impart knowledge on radioactivity, radiation measurement techniques and detectors To render knowledge on phototherapy, radioisotopes,application areas and hazards of radiation
Course Outcome:
Analyze the basic principles radiology, computer tomography and nuclear medicine. Apply the knowledge acquired on radioactivity, radiation measurement techniques and detectors. Inculcate knowledge on phototherapy, radioisotopes, application areas and hazards of radiation.
X-Ray spectrum, Production of X-rays, Modern X-ray tubes, Quality of X-rays, Photographic effects on X-ray films, Fluorescent and Intensifying screen, Scattered rays, Use of filters, HVL, Collimators, Cones, Bucky Grids, Fluoroscopy, Image intensifier, Digital Radiography, Computed Tomography(CT). Basic characteristics and units of radioactivity, Ionization chamber, GM tubes, Gas filled detectors, scintillation detectors, semiconductor detectors, Liquid scintillation counter, Statistical aspects of nuclear medicine. Rectilinear scanners, Scintillation Camera, principle of operation, collimator, photo multiplier tube, Pulse height Analyzer, computerized multi crystal Gamma camera, Principles of PET and SPECT. Principles of Radiation Therapy, Radio therapy treatment planning Dose in Radiotherapy, Mega voltage therapy, Intensity modulated Radiation therapy, Brachy-therapy, Radiotherapy using radio isotopes. Radiation sensitivity of biological materials, Evidence on radiobiological damage from cell survival curve, Radiation effects on humans, Maximum permissible dose equivalent limits, Hazard from ingested radioactivity, substances, ICRP regulations, Quality factor and sievert, Principles of radiological protection, personnel dosimetry.
References:
1. Dendy,P.P & Heaton. B, Physics for Radiologists. Third Edition. Charles C.Thomas Publisher S.A., 2000 2. .Khan,F.M, Physics for Radiation Therapy, Williams & Wilkins. 2009 3. Gopal B.Saha, Physics and Radiation biology of Nuclear Medicine. 2006 4. Penelope J. Allisy, Roberts Obefipsm. Farr’s Physics for Medical Imaging, Ferry Williams.2007
15EI2037 INTELLIGENT INSTRUMENTATION SYSTEMS
Credits: 3:0:0
Course Objective:
To introduce the basic principles of embedded systems. To impart knowledge on the design of embedded systems, memory requirements and interfacing. To render knowledge on real time operating systems and software development tools.
Course Outcome:
Design interfacing circuits to acquire real time data and process it using software. Develop intelligent instrumentation systems for biomedical applications. Use communication protocols for data transmission.
Concept of embedded systems design, Embedded microcontroller cores, embedded memories, Examples of embedded system, Design challenges in embedded system Design. Serial data communication, Microcomputer based control systems. Issues in sensor interfacing, Interfacing Keyboard displays, signal conditioning, interfacing with external systems, user interfacing, ADC, DAC, relay, optoisolator, LEDs. Process parameter measurement system. (DAQ), Digital Weighing machine, Embedded Implementation of temperature controller, Speed control of DC motor. Frequency counter. Stepper motor control. Introduction to real time operating systems: Tasks and task states, tasks and data, semaphores and shared data, message queues, mailboxes and pipes, timer functions, Events, memory management, Interrupt routines in an RTOS environment. Emulator, Simulators, Host and target machines, Linkers/locators for embedded software, getting embedded software into the target system and testing on host machine.
References:
1. A.Rajkamal, “Embedded systems, Architecture, Programming and design”, Tata McGraw Hill, New Delhi. 2008 2. David.E.Simon, An Embedded Software Primer. Addison Wesley, New Delhi. 2001 3. Micheal Predko, Myke Predko, PIC Microcontroller Pocket Reference. McGraw Hill, NewDelhi. 2000 4. WayneWolf. Computers as Components: Principles of Embedded Computer System Design. Morgan Kaufman. 2004 5. John.B. Peatman, Design with PIC Microcontrollers. Prentice Hall, NewDelhi.2006
Credits: 3:0:0
Course Objective:
To understand the basic knowledge about the Automotive Industry. To understand the fundamentals of Modern automotive systems. To understand the fundamentals of safety systems.
Course Outcome:
Identifying the challenges of electronics in modern automobile. Gaining fundamental knowledge about the physical system. Explore potential new functions and applications.
Description
Vehicle classifications, Modern automotive systems , need and application areas for electronics in automobiles, Sensors and actuators, Possibilities and challenges in automotive industry, Enabling technologies and industry trends-Ignition systems , Fuel delivery system and control, Engine control functions, modes and diagnostics. Transmission fundamentals, Types, Components, Electronic transmission control-Shift point control, Lockup control/torque converter clutch, Engine torque control during shifting, Safety and diagnostic functions, Improvement of shift quality Vehicle braking fundamentals and its dynamics during braking, Brake system components, Antilock braking systems, Components and control logic, Electronic stability, Steering system basics, Fundamentals of electronically controlled power steering: type, Electronically controlled hydraulic system, Electric power steering Active Passive and Functional Safety.
References:
1. William Ribbens, “Understanding Automotive Electronics: An Engineering erspective”, Butterworth-Heinemann, Elsevier Incorporation, Massachusetts, 7th Edition, 2012. 2. Tom Denton “Automotive Electrical and Electronic Systems”, Butterworth-Heinemann, Elsevier Incorporation,2009. 3. Jack Erjavec, “Automotive Technology- A System Approach”, Thomas Delmar Learning, New York, 3rd Edition, 2004. 4. Ronald K. Jurgrn, “Automotive Electronics Handbook”, McGraw Hill Incorporation, New York, 2nd Edition, 2007. 5. Robert Bosch, “Automotive Electrical and Electronics”, Robert Bosch, Germany, 3rd Edition, 1999.
15EI2039 AUTOMOTIVE CONTROL AND HIL SIMULATION
Credits: 3:0:0
Course Objective:
To understand need for simulation and co-simulation To understand the Real time prototyping To understand the concept of SIL, MIL and HIL
Course Outcome:
Ability to work with integrated platforms Ability to generate model based codes Skills to develop and validate the controller
Description:
Model Based system design, HIL simulation, need Basics of continuous and discrete simulation, modelling basics. Connection between Hardware and Simulation, Event Discrete simulation. xPc target, Real Time Workshops, state flow and Real Time Embedded coder. Using Simulink: for plant model, controller (PID) designs for an automotive application. Analog output, targeting a processor for plant. System modelling and validation using test setup. Interfacing of software models with hardware design. System programming and development of experimental setup for hardware in loop simulation. HIL: Separate and In the loop testing of plant and controller system verification and Validation: Comparing the HIL test results with real world result, Hardware inthe-loop testing.
References:
1. Christain Kohler, “Enhancing Embedded systems Simulation: A Chip-Hardware-in-theLoop Simulation Framework”, Viewe+Teubner Verlag/Springer, Germany, 1st edition, 2011. 2. Gaberial Nicolescu, Pieter J. Mosterman, “Model-Based Design For Embedded Systems”, CRC Press, Boca Raton,2010 3. Fabio Patern, “Model -based Design and Evaluation of Interaction Applications”, Springer-Verlag, Germany, 2000. 4. Mathworks Courseware, “InTroducing to Model-Based System Design” 5. Mathworks Courseware, “Advanced Model-Based System Design”
Credits: 3:0:0
Course Objective:
To understand the automotive electrical and electronics systems To understand the design aspect with respect to EMI/EMC To understand the safety constrains associated with electrical systems
Course Outcome:
Gain fundamental knowledge about the physical system Ability to develop integrated control system Explore potential new functions and applications
Description:
Electrical systems and circuits, EMI/EMC, Earthing , Positive and negative Relays, Charging systems, Starting systems, Ignition systems, Electronic Ignition system, Electronic fuel control, Interior and Exterior lighting Windscreen washers and wipers, Horns ,Chassis electrical systems comfort and safety ,Seats ,mirrors and sun-roofs, Central locking and electric windows, Cruise control, In-car multimedia, Security, Airbags and belt tensioners, Other safety and comfort systems, Diagnosing comfort and safety system faults, Active Passive and Functional Safety, Advanced comfort and safety systems technology, New developments in comfort and safety systems
References:
1. James D. Haldermen, ”Automotive Electricity and Electronics”, Prentice Hall, New Jersey,4th Edition,2013 2. Tom Denton, ”Automobile Electrical and Electronic Systems”, Elsevier ButterworthHeinemann, Oxford, 3rd Edition, 2004. 3. Robert Bosch GmBH , ”Bosch Automotive Hand Book”, Bentley publishers, 8th Edition, Cambridge, 2011
Credits: 3:0:0
Course Objective:
To understand the need for in vehicle communication. To analyze automotive communication protocols. To understand the automotive standards for communication.
Course Outcome:
Depth knowledge on data communication and networking. Ability to select the suitable protocol for an application. Ability to integrate different communication platforms.
Needs and benefits of IVN, Classes of IVN Protocols, Multiplexed electrical systems, Vehicle multiplexing, Bitwise contention, Network elasticity, Error processing and management. Overview of the automotive communication protocols: TCP/IP, CAN, LIN, Flexray, MOST: Features, Specifications, baud rate, timing, synchronizing, error detection and correction mechanisms, frames, standards, advantages and limitation. Cross protocol compatibility, gateway ECU, Comparison of different IVN protocols.
References:
1. Gilbert Held, “Inter and Intra Vehicle Communications”, Auerbach Publications, CRC Press, Boca Raton, 2007. 2. Behrouz Forouzan, “Data Communications and Networking”, McGraw-Hill Limited, NewYork, 4th Edition, 2006 3. Ronald K. Jurgen, “Automotive Electronics Handbook”, McGraw-Hill Incorporation, NewYork, 1999 4. Marc Emmelmman, Brend Bochow, Christopher Kellum, “Vehicular Networking : Automotive Applications and Beyond”, John Wley & Sons, 2010 5. Robert Bosch, “Bosch Automotive Networking: Expert know-how on Automotive Technology”, Bently Publishers, Cambridge, 2007
15EI2042 AUTOMOTIVE TELEMATICS AND INFOTAINMENT
Credits: 3:0:0
Course Objective:
• To understand the role of Telematics and Infotainment • To understand the role of electronics in driver assistant system • To understand the role of inter vehicle communication
Course Outcome:
• Depth knowledge about different assistive system • Ability to explore new infotainment system • Ability to develop fleet management system
Description:
Driver Assistance Systems: driver support systems, Vehicle support systems, Safety Systems: Anti - spin regulation, traction control systems Security Systems: Anti-theft technologies, smart card system, number plate coding. Comfort Systems Adaptive cruise control, adaptive noise control, active roll control system, cylinder cut- off technology. Telematics basics, applications and technologies: HUD, Global Positioning Systems (GPS), Inertial Navigation Systems (INS), Vehicle Location and Navigation, Bluetooth, UWB, RFID, Intelligent Transportation Systems (ITS) and Wireless Access in Vehicular Environments (WAVE), Communications, Air-interface, Long and Medium range (CALM), Real-time management and planning of commercial vehicle operation, Satellite Radio(XM-Radio and SIRIUS), Fleet Management
References:
1. William Ribbens, “Understanding Automotive Electronics: An Engineering Perspective”, Butterworth-Heinemann, Elsevier Incorporation, Massachusetts, 7th Edition, 2012. 2. Dennis Foy, “Automotive Telematics: The One-stop Guide to In-vehicle Telematics and Infotainment Technology and Applications, Red Hat Publishing Company Incorporation, Maryland, 2002. 3. Ljubo Vlacic, Michel Parent, Fumio Harashima, “Intelligent Vehicle Technologies”, Butterworth-Heinemann publications, Oxford, 2001. 4. Robert Bosch GmBH, “Bosch Automotive Hand Book”, Bentley Publishers, 8th Edition, Cambridge, 2011. 5. Ronald K Jurgen, “Navigation and Intelligent Transportation Systems – Progress in Technology”, Automotive Electronics Series, SAE, USA, 1998.
15EI2043 AUTOMOTIVE FAULT DIAGNOSTICS
Credits: 3:0:0
Course Objective:
To understand the importance about diagnostics To understand the methods of diagnostics To understand the tools available for fault diagnostics
Course Outcome:
Knowledge about different diagnostic tools Depth knowledge about the diagnostic process Ability to identify the faults on the vehicle
Description:
Need for diagnostics, Circuit testing, Vehicle specific details, The ’six-steps’ approach, Skills required for effective diagnosis, An approach to fault finding, Tools and equipment, Oscilloscope diagnostics, On-board diagnostics, Diagnostics of Engine system, chassis System, Electrical and Transmission system.
References:
1. Allan W. M. Bonnick, “Automotive Computer Controlled Systems Diagnostic tools and techniques”, Butterworth-Heinemann, Oxford, 1st Edition, 2001. 2. Tom Denton, “Advanced Automotive Fault Diagnosis”, Elsevier ButterworthHeinemann, Oxford, 2nd Edition, 2006. 3. Tracy Martin, “How to Diagnose and Repair Automotive Electrical Systems”, Motor Books/MBl Publishing Company, London, 1st Edition, 2005. 4. James D. Halderman Jim Linder Automotive Fuel And Emissions Control Systems third edition Pearson Education, 2012. 5. AlexanderA.Stotsky, “Automotive Engines Control, Estimation, Statistical Detection”Springer-Verlog, Berlin Heidelberg 2009.
LIST OF SUBJECTS
Sub.Code
14EI2001 Sensors and Transducers
Nameof the Subject
14EI2002 Sensors and Transducers Laboratory 14EI2003 Electrical Measurements 14EI2004 Simulation Laboratory 14EI2005 Control System 14EI2006 Electrical Measurements and Machines Laboratory 14EI2007 Control Systems Laboratory 14EI2008 Industrial Instrumentation 14EI2009 Process Dynamics and Control 14EI2010 Industrial Instrumentation Laboratory 14EI2011 Electronic Instrumentation 14EI2012 Logic and Distributed Control Systems 14EI2013 Industrial Data Communication and Networks 14EI2014 Process Control Laboratory 14EI2015 Logic and Distributed Control Systems Laboratory 14EI2016 Digital Control Systems 14EI2017 Biomedical Instrumentation 14EI2018 Automotive Instrumentation 14EI2019 Analytical Instrumentation 14EI2020 Instrumentation and Control in Petrochemical Industries 14EI2021 Instrumentation and Control in Paper Industries 14EI2022 Instrumentation and Control in Iron and Steel Industries 14EI2023 Opto-Electronics and Laser Based Instrumentation 14EI2024 Power Plant Instrumentation 14EI2025 Modern Control Techniques 14EI2026 Strength of Machine Elements 14EI2032 Flexible Manufacturing System 14EI2033 Vibration Analysis 14EI2035 Human- Robot Systems and Interaction 14EI2036 Environmental Instrumentation 14EI2038 Instrumentation for Agriculture 14EI2039 Instrumentation and Control for Avionics 14EI2040 Ultrasonic Instrumentation 14EI2041 Measurements and Instrumentation 14EI2042 Advanced Control Theory 14EI2043 Virtual Instrumentation 14EI2044 PLC and Automation 14EI2045 Artificial organs and Rehabilitation Engineering 14EI2046 Process Control for Food Engineers 14EI2047 Process Control Laboratory for Food Engineers 14EI2048 Instrumentation and Control Systems 14EI3002 Instrumentation
Credits
3:0:0 0:0:2 3:1:0 0:0:2 3:1:0 0:0:2 0:0:2 3:0:0 3:0:0 0:0:2 3:0:0 3:0:0 3:0:0 0:0:2 0:0:2 3:0:0 3:0:0 3:0:0 3:0:0 3:0:0 3:0:0 3:0:0 3:0:0 3:0:0 3:0:0 3:0:0 3:0:0 3:0:0 3:0:0 3:0:0 3:0:0 3:0:0 3:0:0 3:0:0 3:0:0 3:0:0 3:0:0 3:0:0 3:0:0 0:0:2 3:0:0 3:0:0
14EI3003 Advanced Process Control 14EI3004 Industrial Instrumentation and Process Control Laboratory 14EI3005 Advanced Control Systems 14EI3006 Discrete Control System 14EI3007 Intelligent Controllers 14EI3008 Optimal Control Theory 14EI3009 Industrial Instrumentation 14EI3010 Control System Design 14EI3011 Virtual Instrumentation Laboratory 14EI3012 Embedded Control Systems Laboratory 14EI3014 Industrial Automation 14EI3015 System Identification and Adaptive Control 14EI3016 SCADA systems and Applications 14EI3017 Design of Linear Multivariable control systems 14EI3018 Piping and Instrumentation 14EI3019 Embedded Instrumentation 14EI3020 Networks and Protocols for instrumentation and control 14EI3022 Design of Embedded Control System 14EI3023 Advanced Processors for control and automation 14EI3028 14EI3025 DESIGN OF EMBEDDED CONTROL SYSTEM Embedded Virtual Instrumentation Laboratory 14EI3029 14EI3025 DESIGN OF EMBEDDED CONTROL SYSTEM Embedded Automotive Systems 14EI3030 Automotive Sensors and Intelligent Systems 14EI3031 Automotive Protocols and Telematics 14EI3033 Biomedical sensors and signal conditioning 14EI3038 Physiological Control Systems 14EI3039 Medical Instrumentation 14EI3040 Bio Virtual instrumentation 14EI3041 Hospital Management System 14EI3042 Cognitive technology for biomedical engineers 14EI3044 Embedded Based Medical Instrumentation Laboratory 14EI3045 Diagnostics and therapeutic Equipments Laboratory 14EI3046 Medical Imaging Techniques 14EI3048 Clinical Instrumentation 14EI3049 Medical Devices And Safety 14EI3051 Medical Sensors and wearable devices 14EI3052 Safe Rehabilitation Engineering 14EI3054 Biomechanics 14EI3055 Medical Diagnostics And Therapeutic Equipments 14EI3056 Safe Limb prosthetics 14EI3057 Sasafety Saf Industrial electronics and instrumentation 14EI3058 Linear systems 14EI3059 Transducers and Actuators 14EI3060 Automated Test and Measurement 14EI3061 Remote sensing and control 3:0:0 0:0:2 3:0:0 3:0:0 3:0:0 3:0:0 3:0:0 3:0:0 0:0:2 0:0:2 3:0:0 3:0:0 3:0:0 3:0:0 3:0:0 3:0:0 3:0:0 3:0:0 3:0:0 0:0:2 3:0:0 3:0:0 3:0:0 3:0:0 3:0:0 3:0:0 3:0:0 3:0:0 3:0:0 0:0:2 0:0:2 3:0:0 3:0:0 3:0:0 3:0:0 3:0:0 3:0:0 3:0:0 3:0:0 3:0:0 3:0:0 3:0:0 3:0:0 3:0:0
14EI3063 Robot Programming 14EI3064 Kinematics and Dynamics of Robot 14EI3065 Advanced Instrumentation and Process Control for Food Engineers 14EI3066 Sensors and Data Acquisition Lab 14EI3067 Transducer Engineering 3:0:0 3:0:0 3:0:0 0:0:2 3:0:0
Credits: 3:0:0 14EI2001 SENSORS AND TRANSDUCERS
Course Objective:
To learn the characteristics of sensors To provide knowledge on the principle and operation of different transducers. To introduce the application of sensors and transducers in the measuring system.
Course Outcome:
Determine the characteristics of various sensors and analyze them Use the principle of transducers to design measuring systems Suggest suitable sensors for a particular application
Transducers - Definition, Classification of transducers, Characteristics of transducers, types of Transducers –Resistive, Inductive, Capacitive, Piezoelectric, Magnetic transducers, principle of operation, working, characteristics and applications, Miscellaneous sensors – Elastic, digital, chemical, fiber optic, MEMS.
References
1. Doebelin. E.O., “Measurement Systems Application and Design”, McGraw Hill International, New York, 2007. 2. Renganathan. S., “Transducer Engineering”, Allied publishers Limited, Chennai, 2003. 3. Cooper W.D., “Electronic Instrumentation and Measurement Techniques”, Prentice Hall of India, New Delhi, 2003. 4. Sawhney A.K., “A Course in Electrical and Electronics Measurements and Instrumentation”, Eighteenth Edition, Dhanpat Rai and Sons, New Delhi, 2007. 5. Ian R Sinclair, “Sensors and Transducers”, Third Edition, Newnes, New Delhi, 2011.
14EI2002 SENSORS AND TRANSDUCERS LABORATORY
Co-Requisite: 14EI2001 Sensors and Transducers
Credits: 0:0:2
Course Objective:
To introduce the practical aspects of various transducers and their characteristics. To impart knowledge in measurement of Resistance, Inductance and Capacitance using bridges. To improve the skills in calibrating analog meters.
Course Outcome:
Analyze the performance characteristics of various transducers and infer the reasons for the behavior. Critically analyze any measurement application and suggest suitable measurement methods. Calibrate basic instruments.
Description:
This laboratory introduces the different transducers, their working and determination of their characteristics.
Experiments:
The faculty conducting the laboratory will prepare a list of 12 experiments and get the approval of HOD/Director and notify it at the beginning of each semester.
14EI2003 ELECTRICAL MEASUREMENTS
Pre Requisite: 14EE2001 Electric Circuits and Networks
Credits: 3:1:0
Course Objective:
To introduce the principle of measurement of D.C. and A.C. voltages. To understand the use of instruments and techniques for practical measurements required in electrical measurements. To learn the working of D.C and A.C. Bridges
Course Outcome:
Apply the knowledge of electrical measurement techniques to design circuits. Solve problems through instrument illustrations. Use the concept of bridges in instrumentation application
Fundamentals Of Electrical Measurements-Functional Elements of an Instrument, Input– Output Configuration of Measurement Systems, Performance Characteristics of Instruments, Electromechanical DC Instruments Galvanometers, PMMC Instrument, DC Ammeter and Voltmeter, Calibration of DC instruments, Electromechanical AC Instruments-Moving Iron Instrument, Thermoinstruments, Electrodynamometers in Power Measurements, Watt– hour meter, Power– factor meters, Instrument Transformers, A.C. and D.C. Bridge Circuits and Recording Instruments.
References
1. Cooper W.D., “Electronic Instrumentation and measurement techniques”, Prentice Hall of India, New Delhi, 2004. 2. Tumanski. S., “Principles of Electrical Measurement”, Taylor and Francis Group, Ny, 2006. 3. Kalsi.H.S, “Electronics Instrumentation”, Tata McGraw Hill, New Delhi, 2009. 4. Golding E.W. and Widdis F.E., “Electrical measurements and measuring instruments”, Sir Issac Pitman and Sons Pvt., Ltd., 2001. 5. Laughton. M. A. and Warne. D. J., “Electrical Engineer's Reference Book” Sixteenth Edition, Newnes, 2003.
14EI2004 SIMULATION LABORATORY
Co-Requisite: 14EE2001 Electric Circuits and Networks 14EC2002 Electronic circuits
Credits: 0:0:2
Course Objective:
To familiarize simulation software to analyze electronic circuits. To introduce simulation software to learn signal operations To design virtual instruments to analyze real time signals.
Course Outcome:
Simulate simple electronic circuits using simulation software. Simulate signals and analyze them using simulation software
Acquire real time signals and perform simple operations on them using simulation software.
Description:
This laboratory aims to introduce simulation software that enables the student to understand the theoretical concepts by simulating them.
Experiments:
The faculty conducting the laboratory will prepare a list of 12 experiments and get the approval of HOD/Director and notify it at the beginning of each semester.
Credits: 3:1:0 14EI2005 CONTROL SYSTEM
Course Objective:
• To introduce the fundamentals of Feedback Control systems and mathematical modeling of the system. • To cover the concepts of time response and frequency response of the system. • To understand the basics of stability analysis of the system.
Course Outcome:
• Represent the mathematical model of a system. • Determine the response of different order systems for various test inputs. • Analyse the stability of the system.
Introduction to Control Systems, Types, Effect of Feedback, Differential equation of Physical Systems, Transfer functions, Block diagram algebra, Signal Flow graphs, Time Response of Feed Back Control Systems, Step response of First and Second order systems , Time response specifications of Second order Systems, Concepts of Stability, Routh stability criterion, Root Locus Techniques, stability analysis using Bode Plots, Polar plots, Introduction to lead, lag and lead–lag compensating networks, Nyquist criterion, Concepts of State, State variable and State models for electrical systems, Solution of State Equations, P, PI, PID Controllers.
References
1. Nagarath .J and Gopal M., “Control Systems Engineering”, New Age International (P) Limited, Publishers, Fourth edition – 2005 2. Ogata .K “Modern Control Engineering “, Pearson Education Asia/ PHI, 4th Edition, 2002. 3. Benjamin C. Kuo and Farid Golnaagi, Wiley “Automatic Control Systems”, 8th Edition, 2009. 4. Joseph J Distefano “Feedback and Control System”, III et al., Schaum’s Outlines, TMH, 2nd Edition 2007. 5. Norman. S. Nise, “Control Systems Engineering”, Wiley, 6th Edition, 2011.
14EI2006 ELECTRICAL MEASUREMENTS AND MACHINES LABORATORY
Co-Requisite: 14EI2003 Electrical Measurements
Credits: 0:0:2
Course Objective:
To expose the students to the operation of DC and AC machines To learn about calibration of electrical instruments and bridge circuits To introduce the working of special electrical machines.
Course Outcome:
Analyze the characteristics of DC and AC Machines. Calibrate electrical instruments and bridge circuits
Perform experiments on special electric machines.
Description:
This laboratory enables the student to understand the operation of electrical machines, bridges and the methods of calibrating electric instruments
Experiments:
The faculty conducting the laboratory will prepare a list of 12 experiments and get the approval of HOD/Director and notify it at the beginning of each semester.
14EI2007 CONTROL SYSTEMS LABORATORY
Co-Requisite: 14EI2005 Control System
Credits: 0:0:2
Course Objective:
• To explore the methods of controller design. • To introduce the concept of Mathematical Modelling. • To understand the design of the compensating circuits.
Course Outcome:
• Design a controller for a practical system. • Derive the mathematical model of a system. • Design lead and lag compensating circuits.
Description:
This laboratory demonstrates the methods to derive the mathematical model of a system and design a controller for a practical system.
Experiments:
The faculty conducting the laboratory will prepare a list of 12 experiments and get the approval of HOD/Director and notify it at the beginning of each semester.
Credits: 3:0:0 14EI2008 INDUSTRIAL INSTRUMENTATION
Course Objective:
To learn the principle of Pressure, Temperature, flow, level, density and viscosity measurements. To know about the selection, calibration and installation of different instruments To explore the application of measuring instruments in various industries
Course Outcome:
Apply the knowledge of various Measuring Instruments to design a simple Instrumentation system. Calibrate the various instruments and use them in various fields. Select suitable instrument for a given application
Pressure Measurement-Standards, Dynamic testing, High and Low pressure measurement, Flow Measurement Pitot static tube, Yaw tube, Pivoted vane, Anemometer, Obstruction meters, Rotameters, Turbine meters, Positive Displacement meters, Electromagnetic flow meter, Drag force flow meter , Ultrasonic flow meters, Vortex, Shedding flow meters, Temperature Measurement-Thermal Expansion Methods, Thermoelectric sensors, Electrical Resistance Sensors, Junction Semiconductor Sensors, Radiation methods, Level Measurement, Density And Viscosity Measurement, Selection, Range, Installation, Calibration and Protection of instruments
References
1. Doebelin E.O, “Measurement Systems: Application and Design”, McGraw Hill, New York, 2003. 2. Singh S K, “Industrial Instrumentation and Control”, Tata McGraw– Hill, New Delhi, 2004. 3. William C. Dunn, “Fundamentals of Industrial Instrumentation and Process Control”, McGraw– Hill, New Delhi, 2005. 4. Liptak B.G, “Process Measurement and Analysis,” Chilton Book Company, Radnor, Pennsylvania, 2003. 5. Walt Boyes, “Instrumentation Reference Book,” Butterworth Heinemann, United States, 2003.
14EI2009 PROCESS DYNAMICS AND CONTROL
Pre Requisite: 14EI2005 Control System
Credits: 3:0:0
Course Objective:
• To equip the students with the knowledge of modelling a physical process. • To understand the design of various control schemes. • To apply the control system in various processes.
Course Outcome:
• Derive the Mathematical Model of a physical system. • Tune controllers for Optimum gain using various techniques. • Analyse and decide suitable control schemes for a particular system.
Process Control System -Terms and objectives, Piping and Instrumentation diagram, Degrees of freedom, Modelling of simple systems ,Basic Control Actions - Continuous Controller Modes, Response of controllers for different test inputs, Selection of control modes, Controller Tuning - Optimum controller settings, Controller tuning Methods, Final Control Elements – Characteristics, Selection of control valves, Advanced Control Schemes Multivariable process control, Interaction of control loops, Case Studies: Distillation column, Boiler drum level control, Heat Exchanger and chemical reactor control
References
1. Stephanopoulos, “Chemical Process Control”, Prentice Hall, New Delhi, 2003. 2. Coughanowr D.R., “Process Systems Analysis and Control”, McGraw Hill, Singapore,2008. 3. Curtis D .Johnson, “Process Control Instrumentation Technology, ”Prentice Hall , New Jersey, 2006. 4. Dale E. Seborg, Thomas F. Edgar, Duncan A. Mellichamp, “Process Dynamics and Control,” John Willey and Sons, Singapore, 2006. 5. Wayne Bequette B., “Process control: modeling, design, and simulation” Prentice Hall , New Jersey– 2003 6. Peter Harriott, “Process Control”, Tata McGraw Hill, New Delhi, 2008.
14EI2010 INDUSTRIAL INSTRUMENTATION LABORATORY
Co-Requisite: 14EI2008 Industrial Instrumentation
Credits: 0:0:2
Course Objective:
To gain the knowledge of the working of Industrial Instruments To learn the methods of Calibration for Instruments. To understand the operation of Instrumentation Circuits.
Course Outcome:
Handle simple Industrial Instruments. Perform Calibration of Instruments.
Design Instrumentation Circuits for measurement systems.
Description:
This laboratory introduces the operation of industrial instruments, their calibration and design of instrumentation circuits.
Experiments:
The faculty conducting the laboratory will prepare a list of 12 experiments and get the approval of HOD/Director and notify it at the beginning of each semester.
14EI2011 ELECTRONIC INSTRUMENTATION
Pre Requisite: 14EC2008 Linear Integrated Circuits
Credits: 3:0:0
Course Objective:
• To provide information on the basics of Electronic Measurements. • To include specialized information needed for Analog and Digital Instrumentation. • To exploit an instrument’s potential, to be aware of its limitations.
Course Outcome:
• Correctly interpret the measurement results • Suggest the instrument suitable for a specific application • Discover applications and solve problems that arise in measurement applications
Electronic Analog Instruments – Introduction, Amplified DC meter, AC voltmeters using rectifiers, True RMS voltmeter, Q meter, Vector impedance meter. Oscilloscope, display devices and recorders, Signal generators and analyzers, Digital Instruments-Digital Voltmeters and Multimeters, Simple frequency counter, , time interval, Digital Displacement transducer, Virtual Instrumentation – Evolution, Architecture, Presentation and Control, Functional Integration, Programming Requirements, Conventional and Distributed Virtual Instrumentation, Virtual Instruments and Traditional Instruments, Advantages, Study of evolution and procedures in simulation softwares.
References
1. Cooper W.D., “Electronic Instrumentation and measurement techniques”, Prentice Hall of India, New Delhi, 2009. 2. Kalsi.H.S, “Electronics Instrumentation”, Tata McGraw Hill, 2010. 3. Bouwens A.J., Digital Instrumentation, McGraw Hill Ltd., USA, 2002. 4. Sumathi S and P. Surekha , “LabVIEW based Advanced Instrumentation Systems” Springer, 2007. 5. Oliver B.H., and Cage J.M., “Electronics Measurements and Instrumentation”, McGraw Hill, 2009. 6. David A Bell, “Electronic Instrumentation and measurements”, Prentice Hall of India, New Delhi, 2006.
14EI2012 LOGIC AND DISTRIBUTED CONTROL SYSTEMS
Pre Requisite: 14EI2009 Process Dynamics and Control
Credit: 3:0:0
Course Objective:
• To provide the fundamentals of Data Acquisition system. • To introduce the concept of PLC and its Programming using Ladder Diagram. • To cover the basics of Distributed Control Systems
Course Outcome:
• Acquire knowledge of data acquisition System
• Write simple Programs using ladder diagrams • Use the knowledge of DCS and communication standards in their Projects
Review of Computers In Process Control - Data loggers, Data Acquisition Systems (DAS), Direct Digital Control (DDC), Supervisory Control and Data Acquisition Systems (SCADA), Overview of PLC systems, PLC programming procedures, PLC Basic Functions, PLC Intermediate Functions Sequencer functions, Matrix functions, Alternate programming languages, Analog PLC operation, Design of interlocks and alarms, Distributed Control Systems (DCS)-Evolution, Architecture, Comparison, Local Control unit, Process Interfacing Issues, Redundancy concept, Communication facilities, Interfaces In DCS, General purpose computers in DCS
References
1. John.W. Webb, Ronald A Reis, “Programmable Logic Controllers - Principles and Applications”, Prentice Hall Inc., New Jersey, 2003. 2. Michael P Lukas, “Distributed Control System”, Van Nostrand Reinhold Co., Canada, 1986. 3. B.G. Liptak, “Instrument Engineers Handbook, Process control and Optimization”, CRC press- Radnor, Pennsylvania, 2006. 4. B.G. Liptak, “Process software and digital networks,” CRC press,Florida-2003. 5. Curtis D. “Johnson Process control instrumentation technology,” Prentice Hall , New Jersey 2006. 6. Krishna Kant, “Computer-Based Industrial Control,“ PHI, New Delhi, 2004 7. Frank D. Petruzella, “Programmable Logic Controllers”, McGraw Hill, New York, 2004.
14EI2013 INDUSTRIAL DATA COMMUNICATION AND NETWORKS
Pre Requisite: 14EC2080 Communication Engineering
Credits: 3:0:0
Course Objective:
To introduce the basic principles of networking To learn the serial communication standards To equip the students with relevant knowledge about network protocols
Course Outcome:
Appreciate the need for network protocols during data transmission and reception. Analyze the methods of communication Compare the different protocols used as Universal standards.
Introduction and Basic Principles – Protocols, Physical standards, Modern instrumentation, Bits, Bytes and characters, Communication principles, Communication modes, Synchronous and Asynchronous systems, Transmission Characteristics, Data Coding, UART, Serial data communications interface standards, Balanced and unbalanced transmission lines, RS232,422,,423,449,485 interface standard, Introduction To Protocols - Flow control Protocols, BSC Protocols, HDLC, SDLC, Data communication for Instrumentation and Control, Industrial protocols, Local Area Networks
References
1. John Park, Steve Mackay, Edwin Wright, “Practical Data Communications for Instrumentation and Control”, Elsevier Publications, 2003. 2. Stallings W. “High speed Networks TCP/IP and ATM Design Principles “ PHI ,2002. 3. Behrouz A. Forouzan“ Data Communication and Networking” , TMH, 2006. 4. Lawrence. M. Thompson , “Industrial Data Communications”, 4th Edition , ISA- 2007. 5. Edwin Wright “Practical Industrial Data Networks: Design, Installation and Troubleshooting”, Newnes2004.
14EI2014 PROCESS CONTROL LABORATORY
Co-Requisite: 14EI2005 Control System
Credits: 0:0:2
Course Objective:
To introduce the practical concepts of digital controllers. To demonstrate Data Acquisition in VI To provide knowledge about controller design, simulation and implementation
Course Outcome:
Design and compare Digital Control Algorithms. Analyze the performance of a Process Demonstrate Data Acquisition in VI
Description:
This laboratory introduces the design procedure for digital controllers and their implementation of real time process.
Experiments:
The faculty conducting the laboratory will prepare a list of 12 experiments and get the approval of HOD/Director and notify it at the beginning of each semester.
14EI2015 LOGIC AND DISTRIBUTED CONTROL SYSTEMS LABORATORY
Co-Requisite: 14EI2012 Logic and Distributed Control Systems
Credits: 0:0:2
Course Objective:
• To strengthen the knowledge of Programmable Logic Controllers • To introduce the concepts of SCADA • To gain hands on experience on Distributed Control Systems
Course Outcome:
• Write simple programs in Programmable Logic Controllers • Design control system using Programmable Logic Controllers • Use SCADA for real time applications
Description:
This laboratory introduces the basic concepts of PLC programming and Distributed Control systems using simulation software.
Experiments:
The faculty conducting the laboratory will prepare a list of 12 experiments and get the approval of HOD/Director and notify it at the beginning of each semester.
14EI2016 DIGITAL CONTROL SYSTEMS
Pre Requisite: 14EI2005 Control System
Credits: 3:0:0
Course Objective:
• To introduce the concepts of system analysis using Z transforms. • To equip with the basic knowledge of digital process control design. • To study the stability analysis of digital control system
Course Outcome:
• Use Z transforms to analyse Discrete Systems. • Design controllers for a digital process. • Test the Stability of Discrete Systems.
Need for digital control, Configuration of the basic digital control scheme, Principles of signal conversion, Basic discrete time signal, Z transform, Stability Analysis - Analysis Of Digital Control, Frequency Response, Stability on the z-Plane and the Jury stability criterion, Sample and hold systems , Digital Controller - Z domain description of sampled continuous time plants, Z domain description of systems with dead time, Implementation of digital controllers, Digital Algorithms - Design of Digital Control Algorithms, Z plane specifications of control system design, Digital compensator design using frequency response plots, State description of sampled continuous time plants, Solution of state difference equations
References
1. Gopal M, “Digital Control and State variable Methods”, Tata McGrawHill, New Delhi, 2003. 2. Ogata, “Discrete Time Control Systems”, Prentice– hall Of India, New Delhi 2008. 3. Gene F. Franklin, J. David Powell, “Digital control of dynamic systems”, Pearson Education Limited, New Delhi,2002. 4. Richard C. Dorf, Robert H. Bishop, “Modern control systems,” Pearson Education inc, New Delhi, 2008. 5. Isermann R ‘Digital Control Systems’, Vol. I & II, Narosa Publishing
Credits: 3: 0:0 14EI2017 BIOMEDICAL INSTRUMENTATION
Course Objective:
• To give knowledge of the principle of operation and design of Biomedical Instruments. • To render a broad and modern account of biomedical instruments. • To teach the application of biomedical instruments in real life applications
Course Outcome:
• Apply the concepts of Medical Instrumentation to physiological measurements • Design Instrumentation circuits for Biomedical Applications. • Use the knowledge of Biomedical Instruments to Practical Problems.
Cell and its Electrical activity, Physiological systems viz., cardiovascular system, Nervous system, Respiratory system, Visual system, Muscular system, Electrodes and bioelectric signals: Bio electrodes, ECG, EMG, EEG and EOG, Measurement of physiological parameters: Blood flow, Blood pressure, Cardiac output, and Bio-chemical measurement: Blood pH, Blood pO2, Blood pCO2, Photometers. Therapeutic equipments and imaging techniques.
References
1. Khandpur. R. S., “Handbook of Biomedical Instrumentation”, Prentice Hall of India, New Delhi, 2003. 2. Cromwell, “Biomedical Instrumentation and Measurements”, Prentice Hall of India, New Delhi, 2007. 3. Arumugam.M. “Biomedical Instrumentation", Anuradha Agencies Publishers, Kumbakonam, 2006.
4. Joseph J. Carr and John M. Brown, “Introduction to Biomedical Equipment Technology”, Pearson
Education India, Delhi, 2004. 5. Webster, “Medical Instrumentation – Application & Design,” John Wiley and sons Inc, Netherlands, 2009.
Credits: 3:0:0 14EI2018 AUTOMOTIVE INSTRUMENTATION
Course Objective:
• To learn the fundamental principles of electronics and to introduce the application of electronics in the modern automobile. • To develop ability to understand various latest Communication protocols used in automobile industries. • To provide a thorough understanding of automotive systems and various electronic accessories used in automobile.
Course Outcome:
• Analyze the use of instruments in automotive industry • Design instruments for automotive applications. • Use Communication protocols to perform advanced monitoring and control.
Automotive Electrical And Electronics - Basic Electronics components and their operation in an automobile, Starting Systems, Charging Systems, Ignition Systems, Electronic Fuel Control, Advanced vehicle control systems, Embedded System Communication Protocols - Vehicle Communication Protocols, Introduction to CAN, LIN, FLEXRAY, MOST, KWP2000, Details of CAN, Embedded System In Control Of Automotive Systems - Engine management systems, Vehicle Safety System, Electronic Control of braking and traction, Electronic transmission control, Environmental tests for electronic control units.
References
1. RobertBoschGmbh ,“BOSCH– Automotive Handbook”, 7thEdition,John Wiley & Sons, ISBN: 0470519363, 2008. 2. Denton.T, “Automobile Electrical and Electronic System”, Elsevier Butterworth–HeinemannPublications,3rd Edition,2004. 3. Knowles.D, “Automotive Electronic and Computer control Ignition Systems”, Prentice Hall,1988. 4. William.T.M, “Automotive Electronic System”,Elsevier Science,6th Edition,2003. 5. Kiencke,, Nielsen, “Automotive Control Systems” 2nd Edition.2005
Credits: 3:0:0 14EI2019 ANALYTICAL INSTRUMENTATION
Course Objective:
• To introduce the principle of analytic instruments • To learn the concept of chromatography • To know the applications of analytical instruments
Course Outcome:
• Analyze the different types of analytic instruments • Develop instruments for clinical analysis. • Apply the concepts of Analytical Instruments for Environmental Monitoring
Colorimetry And Spectrophotometry-Special methods of analysis, Beer–Lambert law, Colorimeters, UV, Vis spectrophotometers, Single and double beam instruments, Sources and detectors, IR spectrophotometers, Types,Attenuated total reflectance flame photometers, Atomic absorption spectrophotometers, Sources and detectors, FTIR spectrophotometers, Flame emission photometers, Chromatography - Different techniques, Gas chromatography, Detectors, Liquid chromatographs, Applications, High– pressure liquid chromatographs,
Applications, Industrial gas analyzers and pollution monitoring instruments, Ph meters and dissolved component analyzers, Radio chemical and magnetic resonance techniques
References
1. Khandpur. R. S., ‘Handbook of Analytical Instruments’, Tata McGraw Hill Publishing Co. Ltd., 2006. 2. Willard. H., Merritt, Dean. J. A., Settle. F. A., ‘Instrumental Methods of Analysis’, CBS publishing & distribution, 1995. 3. Robert D. Braun, ‘Introduction to Instrumental Analysis’, McGraw Hill, Singapore, 1987. 4. Ewing. G. W., ‘Instrumental Methods of Chemical Analysis’, McGraw Hill, 1992. 5. Skoog. D. A. and West. D. M., ‘Principles of Instrumental Analysis’, Holt, Saunders Publishing, 1998.
Credits: 3:0:0 14EI2020 INSTRUMENTATION AND CONTROL IN PETROCHEMICAL INDUSTRIES
Course Objective:
• To expose the students to the Instrumentation involved in petrochemical industries. • To learn the control applied in the subsystems of a petrochemical plant. • To introduce the instrumentation and control in Effluent And Water Treatment
Course Outcome:
• Appreciate the significance of Measurement in Petrochemical Industry. • Use the Knowledge of Control to design new Control Algorithms. • Design instruments and control algorithms for effluent and water treatment.
Piping and Instrumentation diagrams, Instrumentation and control in distillation columns, chemical reactorsTemperature and pressure control in batch reactors – Instrumentation and control in dryers: Batch dryers and Continuous dryers, heat exchangers -, evaporators - Types of evaporators, Measurement and control of absolute pressure, Density, Conductivity, Differential pressure and Flow, Effluent and Water Treatment
References
1. Béla G. Lipták. ‘Instrumentation in the Processing Industries: Brewing, Food, Fossil Power, Glass, Iron and Steel, Mining and Minerals, Nuclear Power, Paper, Petrochemical, Pharmaceutical’, Chilton Book Co., Reprint 2003 2. Considine D.M., ‘Process / Industrial Instruments and Control Handbook’, Fourthedition, McGraw Hill, Singapore, 1999. 3. Curtis D .Johnson,”Process control instrumentation technology,”Prentice Hall , New Jersey, 2006. 4. Singh S K, “Industrial Instrumentation and Control”, Tata McGraw– Hill, New Delhi, 2004. 5. William C. Dunn, “Fundamentals of Industrial Instrumentation and Process Control”, McGraw– Hill, New Delhi, 2005.
Credits: 3:0:0 14EI2021 INSTRUMENTATION AND CONTROL IN PAPER INDUSTRIES
Course Objective:
• To describe the paper making process and need for measurement • To expose the students to the Instrumentation applied in Paper industries. • To learn the control operations in paper industries.
Course Outcome:
• Appreciate the need of instrumentation and control in Paper making. • Select suitable sensors for a specific process • Design a Controller for paper industries.
Description Of The Process -Raw materials, Pulping process, Chemical Recovery Process, Paper making process, Converting, Instrumentation - Measurements of Basis Weight, Density, Specific gravity, Flow, Level of liquids and solids, Pressure, Temperature, Consistency, Moisture, PH, Oxidation-Reduction potential, Graphic displays and alarms, Control Operations - Blow tank controls, Digester liquor feed pump controls, Brown stock water level control, Stock chest level control, Basis weight control, Dry temperature control, density and flow control, computer applications.
References
1. B.G Liptak, ‘Instrumentation in Process Industries’, Chilton Book Company, 2003 2. Renganathan. S., “Transducer Engineering”, Allied publishers Limited, Chennai, 2003. 3. Cooper W.D., “Electronic Instrumentation and Measurement Techniques”, Prentice Hall of India, New Delhi, 2003. 4. Singh S K, “Industrial Instrumentation and Control”, Tata McGraw– Hill, New Delhi, 2004. 5. William C. Dunn, “Fundamentals of Industrial Instrumentation and Process Control”, McGraw– Hill, New Delhi, 2005.
14EI2022 INSTRUMENTATION AND CONTROL IN IRON AND STEEL INDUSTRIES
Credits: 3:0:0
Course Objective:
• To learn the steel making process and the need for measurement. • To know the role of instrumentation in a steel industry • To teach the control operations carried out at various stages
Course Outcome:
• Analyze the use of sensors in steel making • Suggest suitable sensor for a typical measurement • Develop control algorithms for any control operation
Description of Process -Flow diagram and description of the processes, Raw materials preparation, Iron making, Blast furnaces, Stoves, Raw steel making, Basic Oxygen Furnace, Electric Furnace, Casting of steel: Primary rolling, Cold rolling and Finishing, Measurement of level, Pressure, Density, Temperature, Flow, Weight, Thickness and shape, Graphic displays and alarms, Control Systems - Blast furnace, Stove combustion control system, Gas and water controls in BOF furnace, Strand Casting mould Level control, Mould Level sensors, Ingot weight measuring system, Waste water treatment, computer applications: Model calculation and logging, Rolling Mill Control, Annealing Process Control, Center Utilities Dispatch Computer.
References
1. Béla G. Lipták. ‘Instrumentation in the Processing Industries: Brewing, Food, Fossil Power, Glass, Iron and Steel, Mining and Minerals, Nuclear Power, Paper, Petrochemical, Pharmaceutical’, Chilton Book Co., Reprint 2003 Original from the University of California. 2. Liptak B. G, Instrument Engineers Handbook, volume 2, Process Control,Third edition, CRC press, London, 1995. 3. Considine D.M, Process / Industrial Instruments and Control Handbook, Fourth edition, McGraw Hill, Singapore, 1993. 4. Steel Designers Handbook 1)Branko 2)Ron Tinyou 3) ArunSyamGorenc Seventh Edition First Indian Reprint 2006. 5. Singh S K, “Industrial Instrumentation and Control”, Tata McGraw– Hill, 2004.
14EI2023 OPTO-ELECTRONICS AND LASER BASED INSTRUMENTATION
Credits: 3:0:0
Course Objective:
To introduce the basic concepts of Optical Fibers and Lasers To learn the measurements done using Optical fibers and Lasers To know the use of lasers in biomedical applications
Course Outcome:
Analyze the use of optical fibers and lasers in instrumentation Use Optical fibers for measurement Apply LASER in Instrumentation and Biomedical applications.
Basics of Opto-electronics - Characteristics of optical radiation, Optical Sources and Detectors, Charge Coupled devices, Opto –couplers and their applications, Optical Fibre - Principle, Types, Fibre coupling, Fibre optic sensors , Lasers and Applications - Principle, Laser Rate Equation, Properties, Two, Three and Four level system, Resonator configuration, Q switching and Mode locking, Cavity dumping, Types of Lasers, Industrial applications, Holography, Medical applications
References
1. Arumugam. M. “Fiber Optics and Laser Instrumentation", Anuradha Agencies Publishers, Kumbakonam, 2006. 2. Optical Fiber Communications: Principles And Practice, John M. Senior, Pearson Education, 2006. 3. G. Keiser, ‘Optical Fibre Communication’, McGraw Hill, . 4. Ghatak A.K. and Thiagarajan K, Optical Electronics Foundation book , TMH, Cambridge University Press, 1989. 5. Wilson and Hawkes, “Opto Electronics – An Introduction”, 3rd Edition, Prentice Hall, New Delhi, 1998.
Credit 3:0:0 14EI2024 POWER PLANT INSTRUMENTATION
Course Objective:
• To provide an overview of different methods of power generation with a particular stress on thermal power generation. • To bring out the various measurements involved in power generation plants. • To familiarize the students with the methods of monitoring different parameters like speed, vibration of turbines and their control.
Course Outcome:
• Survey of methods of power generation • Apply the concepts to design instrumentation systems for a power plant • Develop control algorithms for a particular operation
Brief survey of methods of power generation, Hydro, Thermal, Nuclear, Solar and Wind power, Electrical measurements, Non– electrical parameters Measurements, Analytical instruments in Thermal power plants -Flue gas oxygen analyzer, Analysis of impurities in feed water and steam, Dissolved oxygen analyzer, Chromatography , PH meter , Fuel analyzer, Pollution monitoring instruments, Boiler control system in thermal power plant, Turbine Monitoring and Control
References
1. K. Krishnaswamy, M. Ponnibala, “Power Plant Instrumentation”, PHI Learning Pvt Ltd.,2011. 2. P.K Nag, Power plant Engineering, Tata McGraw Hill, 2001. 3. Sam G Dukelow, The Control of Boilers, 2nd Edition, ISA Press, New York, 1991
4. Gill A B, Power Plant Performance, Butterworth, London, 1984. 5. P C Martin and I W Hannah, Modern Power Station Practice, British Electricity International, Vols.I & VI,
Pergamon Press, London, 1992.
14EI2025 MODERN CONTROL TECHNIQUES
Pre Requisite: 14EI2005 Control System
Credits: 3:0:0
Course Objective:
To enable the students to understand the advanced control systems like optimal control, Robust control, Adaptive control fuzzy and Neural control. To learn the methods to overcome the difficulties in implementing conventional control through advanced control. To analyze the modern control concepts
Course Outcome:
Design of conventional PID controller Perform stability analysis and optimal control Adaptive control and its implementation
Modifications of PID control schemes, Two degrees of freedom control, Optimal Control – Formulation, Necessary conditions of optimality, state regulator problem, Output regulator tracking problems, Pontryagin's minimum principle, infinite time optimal control , Problem, Advanced Control techniques - Lyapunov Stability Analysis And Quadratic Optimal Control, Adaptive Control, Robust control
References
1. Katsuhiko Ogata, Morden Control Engineering,Third Edition, - Prentice Hall , India 2009. 2. Nagarath, I.J. and Gopal.M. Control Systems Engineering, Wiley & sons, 2008. 3. Astrom K.J. and Wittenmark.B, Adaptive Control, Addison Wesley Publishing, 1985. 4. Bernard friedlanced - Advanced Control System Design- Prentice Hall of India Pvt Ltd., New Delhi,1996. 5. Richard.C. Dorf and Robert.H.Bisho, Modern Control System, Addison Wesley & sons, 2008
Credits: 3:0:0 14EI2026 STRENGTH OF MACHINE ELEMENTS
Course Objective:
To introduce the basics of stress and strain on elements To discuss the theory of failure To learn the concept of torsion
Course Outcome:
Appreciate the need for stress and strain analysis Determine the shear force and bending moment Analyze the effect of torsion on elements
Stress at a point, stress and strains in bars subjected to axial loading, Various strengths of material, Temperature stresses in simple & composite members. Strain energy due to axial load. Compound stress and strains, Mohr’s circle of stress; ellipse of stress and their applications, stresses in machine elements, Shear force and Bending moment – Definitions, Diagrams for cantilevers, simply supported beams with or without overhangs Uniform distributed load, Combination of Concentrated load & UDL, Uniformity varying load, Torsion equation,
Applications to hollow and solid circular shafts, torsional rigidity, combined torsion and bending of circular shafts, analysis of close-coiled-helical springs, theories of failure, Buckling of coloumns
References
1. R. S. Khurmi, Strength of Materials, S. Chand, 2008 2. S. S. Ratan, Strength of Materials, Tata McGrawhill, 2011 3. Gere and Temoshenko, “Mechanics of Material”, CBS Publishers 4. S. Ramamrutham “Strength of Materials”, Dhanpat Rai Publishing Company 5. Singer and Pytel “Strength of Materials”, Harper and Row Publications
Credits: 3:0:0 14EI2032 FLEXIBLE MANUFACTURING SYSTEMS
Course Objective:
To deal with Automation and Automated Assembly systems To understand the concept of Group Technology To learn the significance of Flexible Manufacturing systems
Course Outcome:
Classify the automation strategies being followed Decide the automation Appreciate the importance of Flexible manufacturing systems
Automation and Automated Assembly systems-Types, automation strategies, Detroit-type automation: Automated flow lines, methods of work part transport, Transfer mechanisms, design of automated assembly systems, Group Technology-Part families, parts classification and coding, Machine cell design, Flexible Manufacturing Systems Components of an FMS, types of systems, FMS work stations, Material handling and storage system, Planning the FMS, analysis methods for FMS, applications and benefits.
References
1. Automation, Production Systems and Computer Integrated Manufacturing- Groover M.P, Prentice Hall of India, 2002 2. CAD/CAM – Groover M.P, Zimmers E.W, Prentice Hall of India, 2005 3. Approach to Computer Integrated Design and Manufacturing: Nanua Singh, John Wiley and Sons, 1998. 4. Production Management Systems: A CIM Perspective- Browne J, Harhen J, Shivnan J, Addison Wesley, 2nd Ed. 1996.
Credits: 3:0:0
14EI2033 VIBRATION ANALYSIS
Course Objective:
To deal with Automation and Automated Assembly systems To understand the concept of Group Technology To learn the significance of Flexible Manufacturing systems
Course Outcome:
Classify the automation strategies being followed Decide the automation and group technology Appreciate the importance of Flexible manufacturing systems
Causes and effects of vibration- Vibrations of Single Degree, Two Degree and Multi Degree of freedom systems., Steady state and transient characteristics of vibration, Vibration measuring instruments-Vibration transducers, signal
conditioning elements. Display-and recording elements. Vibration meters and analyzers, Special vibration measuring techniques - Change in sound method, Ultrasonic measurement method, Shock pulse measurement, Kurtosis, Acoustic emission monitoring, Cepstrum analysis, Modal analysis, critical speed analysis, Shaft –orbit & position analysis.
References
1. Collacott, R.A., Mechanical Fault Diagnosis and Condition Monitoring, Chapman & Hall, London, 1982. 2. John S. Mitchell, Introduction to Machinery Analysis and Monitoring, Penn Well Books, Penn Well Publishing Company, Tulsa, Oklahoma, 1993. 3. Nakra, B.C. Yadava, G.S. and Thuested, L., Vibration Measurement and Analysis, National Productivity Council, New Delhi, 1989. 4. Pox and Jenkins, “Time Series Analysis: Forecasting and Control”, ISBN 978-0-470-27284-8, 2008.
Credits: 3:0:0 14EI2035 HUMAN - ROBOT SYSTEMS AND INTERACTION
Course Objective:
To study multimodal interactions between a human and a robot To introduce the concepts of neurorehabilitation To deal with surgical robotics
Course Outcome:
Model human robots for real applications Perform motion analysis of human robots Analyze the sensory feedback and use it to control robot movements
Course Content
Definition of human-robot interaction problem, human factors: perception, motor skills, social aspect of interaction, safety, Haptic robots: kinematics, dynamics, collision detection, control. Teleoperation systems: architectures, control, virtual fixtures, micro/nano manipulation; Soft robots based on variable impedance actuators, Medical robotics: surgical robotics, robot-supported diagnostics, micro-robots in the human body, nanorobots at the cell level, Rehabilitation and assistive robotics: motor rehabilitation, exoskeletons, robotic prosthetics
References
1. M. Mihelj, J. Podobnik, Haptics for Virtual Reality and Teleoperation, Springer 2012. 2. J. Rosen, B. Hannaford, R.M. Satava, SurgicalRobotics: Systems Applications and Visions, Springer, 2011 3. M. Tavakoli, R.V. Patel, M. Moallem, A. Aziminejad, Haptics for Teleoperated Surgical Robotic Systems, World Scientific, 2008 4. Jose L. Pons, Wearable Robots:Biomechatronic Exoskeletons, John Wiley& Sons, 2008. 5. V. Dietz, T. Nef, W.Z. Rymer,Neurorehabilitation Technology, Springer, 2012 6. E. Burdet, D.W. Franklin, T.E. Milner, Human Robotics: Neuromechanics and Motor Control, The MIT Press, 2013 7. L. Sciavico, B. Siciliano: Modeling and Control of Robot Manipulators, The McGraw –Hill Companies, Inc., New York, 2000.
Credits: 3:0:0
14EI2036 ENVIRONMENTAL INSTRUMENTATION
Course Objective:
To introduce the instrumentation methodologies for environment monitoring. To deal with water quality monitoring and waste water treatment
To discuss the instrumentation required for air pollution monitoring.
Course Outcome:
Design instrumentation systems for environment monitoring. Develop algorithms for waste water treatment Measure and analyze air quality
Necessity of instrumentation & control for environment, Instrumentation methodologies, Quality of water: Standards, effects, Water quality parameters: Thermal conductivity, detectors, Opacity monitors, pH analyzers & their application, conductivity analyzers & their application, Water treatment: Requirement of water treatment facilities, process design, Sedimentation & flotation: sludge, storage & removal, design criteria of settling tank, effect of temperature on coagulation, Ground water monitoring: Level measurement in ground water monitoring wells, instrumentation in ground water monitoring, assessment of soil & ground water pollution, Waste water monitoring: Waste water measurement techniques. Instrumentation set up for waste water treatment plant. Air pollution: Air monitoring, measurement of ambient air quality, Air flow measurement, Rain water harvesting: necessity, methods, rate of NGOs municipal corporation, Govt., limitations. Quality assurance of storage water.
References
1. Water treatment technology - Walter J. Weber 2. Air pollution engineering – M. N. Rao & H. V. N. Rao 3. Air pollution control technology – Wark & Warner 4. Environmental Instrumentation & Analysis Handbook- Randy D. Down.
Credits: 3:0:0 14EI2038 INSTRUMENTATION FOR AGRICULTURE
Course Objective:
To introduce the soil measurement systems. To deal with green house instrumentation To discuss the working of automation equipments in agriculture
Course Outcome:
Design sensors for soil moisture measurement Automate agricultural applications Measure characteristics of leaves
Necessity of instrumentation & control for agriculture, engineering properties of soil: Sensors: introduction to sonic anemometers, hygrometers, fine wire thermocouples, open & close path gas analysers, brief introduction to various bio-sensors, soil moisture measurement methods: resistance based method, voltage based method, thermal based method, details of gypsum block soil moisture sensor, green houses & instrumentation: ventilation, cooling & heating, wind speed, temperature & humidity, rain gauge, carbon dioxide enrichment measurement & control. Automation in earth moving equipments & farm equipments, implementation of hydraulic, pneumatic & electronics control circuits in harvesters cotton pickers, tractor etc. Leaf area length evaportranspiration, temperature, wetness & respiration measurement , electromagnetic radiations photosynthesis, infrared & UV bio sensor methods in agriculture, agrometrological instrumentation weather stations, surface flux measurement, soil water content measurement using time-domain reflectometery(TDR)
References
1. Industrial instrumentation, “Patranabis”, TMH. 2. Instrumentation handbook-process control, “B.G.Liptak”, Chilton 40 3. Process control and instrumentation technology, “C.D. Johnson”, PHI 4. Wills B.A., “ Mineral Processing Technology”, 4thEd.,Pergamon Press
Credits: 3:0:0 14EI2039 INSTRUMENTATION AND CONTROL FOR AVIONICS
Course Objective:
• To introduce the basics of Aircraft • To learn the Instrumentation involved in Aircraft Systems • To deal with gyroscopic instruments
Course Outcome:
• Appreciate the need for measurement in aircraft • Design instrumentation systems for aircraft. • Use gyroscopic instruments for attitude measurement
Flight Instrumentation – Pitot, Static Instruments and Systems, Altimeter, Airspeed indicator, Machmeter, Maximum Safe Speed indicator, Accelerometer, Gyroscope, Gyroscopic theory, Directional gyro indicator, Artificial horizon, Turn and slip indicator, Measurements in Aircraft - Measurement of Engine Speed, Measurement of Temperature, Pressure, Fuel Quantity and Fuel Flow, Engine Power And Control Instruments, Power Indicators, Pressure Indicators, Turbine Temperature Control, Engine Vibration Monitoring and Indicating Instruments.
References
1. Pallett, E.B.J,“ Aircraft Instruments – Principles and applications", Pitman and sons, 1981. 2. Pallett, E.B.J,“ Aircraft Instrument Integrated Systems”, ISBN-10: 0582086272, Edition: 3rd 1992. 3. Nagabhushana S. Et.Al, S. Nagabhushana, L. K. Sudha, “ Aircraft Instrumentation and Systems”, International Pvt Ltd,2010. 4. Federal Aviation Administration (FAA) “Instrument Flying Handbook”, 2013. 5. Doeblin.E.O, “Measurement Systems Application and Design”, McGraw-Hill, New York, 1999.
Credits: 3:0:0 14EI2040 ULTRASONIC INSTRUMENTATION
Course Objective:
• To know the generation and detection of ultrasonic waves • To provide knowledge on the concepts of Ultrasonic Instrumentation • To understand the applications of ultrasonic instrumentation
Course Outcome:
• Characterize the ultrasonic waves • Analyze the sensors used in ultrasonic application • Apply the concepts to make simple applications
Ultrasonic Waves -Principles and propagation of various waves, Characterization of ultrasonic transmission, Reflection and Transmission coefficients, Intensity and attenuation of sound beam. Generation/Detection Of Ultrasonic Waves - Magnetostrictive and piezoelectric effects, Detection of Ultrasonic Waves: Mechanical ,Optical and Electrical Method, Precise Measurement: Pulse– echo Overlap, Cross correlation, Ultrasonic Applications - Ultrasonic methods of flaw detection, Flow meters, Density measurement, Viscosity measurement, Level measurement, Sensor for Temperature and Pressure measurements, Measuring thickness, Depth, Rail Inspection, SONAR, Inspection of Welds and defect detection in welds of anisotropic materials, ultrasonic applications in medical field.
References
1. Baldev Raj, V.Rajendran, P.Palanichamy, “Science and Technology of Ultrasonics”,Alpha Science International, UK, 2004. 2. J.David N.Cheeke,”Fundamentals and Applications of Ultrasonic Waves,” CRC Press, Florida, 2002.
3. LawrenceE.Kinsler, Austin R.Frey, Alan B.Coppens, James V. Sanders, “Fundamentals of Acoustics,”
John Wiley and Sons Inc,USA, 2000. 4. L.A. Bulavin, YU.F.Zabashta, “Ultrasonic Diagnostics in Medicine,” VSP, Koninklijke, Brill,Boston, 2007. 5. Emmanuel P. Papadakis, “Ultrasonic Instruments and Devices”Academic Press,1999.
Credits: 3:0:0 14EI2041 MEASUREMENTS AND INSTRUMENTATION
Course objective:
To make student have a clear knowledge of the instruments, relevant circuits and their working To provide adequate knowledge in electrical instruments and measurements techniques. Emphasis is laid on analog and digital techniques used to measure voltage, current, power etc
Course outcome:
Good understanding of comparison methods of measurements. Exposure to various transducers, Signal Analyser and display devices.
Standards and Indicating Instruments-Errors in measurement- MC-MI-PMMC instruments-Measurement of electrical quantities- R,L,C,power,energy- Transducers used for sensing the measuring quantities - measurement of non-electrical quantities - temperature, pressure, speed - Signal Generators and analysers such as oscillators, spectrum and network analysers – various types of display indicators and different types of signal recorders as data acquisition systems
References
1. Sawhney.A.K., “A Course in Electrical & Electronic Measurement and Instrumentation”, DhanpatRai& Company Private Limited, New Delhi, 18thEdition, 2007. 2. Helfrick A.D., “Modern Electronic Instrumentation & Measurements”, Prentice Hall India Private Limited, New Delhi, 2007. 3. Doeblin,E.O., “Measurement Systems : Application and Design”, 5th Edition, Tata Mc-Graw Hill Publishing Company Limited , New Delhi, 2004. 4. Golding,E.W., and Widdis,F.C., “Electrical Measurements and Measuring Instruments”, A H Wheeler & Company, Calcutta, 5th Edition, 2003. 5. Rangan,C.S., Sharma, G.R., Mani, V.S., “Instrumentation Devices and Systems”, Tata McGraw Hill, New Delhi, 1998. 6. John P Bentley, “Principles of measurement systems”, , Pearson Prentice Hall, 4/e, 2005. 7. Alan S. Morris, “Measurement and Instrumentation Principles”, Elsevier, 2001.
14EI2042 ADVANCED CONTROL THEORY
Pre Requisite: 14EI2005 Control System
Credits: 3:0:0
Course Objective:
• Insight a wide knowledge on the description and stability of non-linear system. • Understand the analysis of digital control system using state-space formulation. • Look at the formulation and analysis of multi input multi output (MIMO) system.
Course Outcome:
• Gain knowledge in analysis of non-linear system and digital control of linear system. • Implement the concept of MIMO system. • Find non-linear system stability using the trajectory methods.
Pole placement design – Design of State observer - Response of sampled data system to step and ramp Inputs –Stability studies – Jury’s test and bilinear transformation - State Space Analysis of Discrete Time Systems - Types of nonlinearity Construction of phase trajectories, Describing function method, Lyapunov stability analysis - Models of MIMO system, Introduction to multivariable Nyquist plot and Singular values analysis, Advanced control techniques
References
1. Nagrath I.J., Gopal M., ‘Control Systems Engineering’, New Age International Publishers, 5th Edition, New
Delhi 2003. 2. Raymond T. Stefani, Bahram Shahian, Clement J. Savant and Gene Hostetter , “Design of feedback
Control systems”, Oxford University Press, New York,4th Edition, 2002. 3. Katsuhiko Ogata, “Discrete-Time Control Systems”, New Age International, New Delhi, 4th Edition, 2007. 4. Gopal M, “Digital Control and State Variable Methods”, Tata McGraw- Hill, New Delhi, 3rd Edition. 2008. 5. Richard C. Dorf and Robert H. Bishop, “Modern Control Systems”, Pearson Education, New Delhi, 8th
Edition, 2004.
Credits 3:0:0 14EI2043 VIRTUAL INSTRUMENTATION
Course Objective:
• Study about the Virtual instrumentation system and LabVIEW based Virtual Instrumentation. • Study about the hardware and software involved programming techniques in VI. • Study about the basic of Programming Techniques and its applications.
Course Outcome:
• Appreciate the advantages of Data flow programming • Use VI for instrumentation and control • Design a LabVIEW based instrumentation system.
Historical perspective, advantages, Block diagram and Architecture of a Virtual Instrument, Data Flow Techniques, Graphical programming in data flow, comparison with Conventional programming - Introduction and Advantages of LabVIEW, Software Environment, Creating and Saving VI- Front Panel Controls and Indicators – Block Diagram Data types – Date flow program – LabVIEW documentation resources – Keyboard shortcuts – Modular Programming in LabVIEW – Icon and Connector Pane -SubVI: Creating- Opening-Editing-Placing an SubVI Creating a Stand Alone Application - Loops and charts, arrays, clusters and graphs, case and sequence structures, formula nodes, local and global variables, string and file I/O.
References
1. Jovitha Jerome, “Virtual Instrumentation Using LabVIEW” Prentice Hall India Learning Private Limited, New Delhi, 2010. 2. JohnEssick, “Hands-On Introduction to LabVIEW for Scientists and Engineers”, Oxford University Press,New York, 2nd Edition, 2010. 3. NesimiErtugrul, “LabVIEW for Electric Circuits, Machines, Drives, and Laboratories”, Pearson Education, 2nd Edition, 2002. 4. LabVIEW: Basics I & II Manual, National Instruments, 2005. 5. Sanjay Gupta and Joseph John, “ Virtual Instrumentation using LabVIEW”, Tata McGraw – Hill Education India Private Limited, New Delhi, 2nd Edition, 2010. 6. Gary W. Johnson, Richard Jennings, “LabVIEW Graphical Programming”, McGraw-Hill Education, New York, 3rd Edition, 2001.
Credits: 3:0:0 14EI2044 PLC AND AUTOMATION
Course Objectives:
• To learn the basics and programming of PLC. • To examine the difference between SCADA and DCS.
• To understand the basic concepts of Intelligent Automation.
Course Outcome:
• Identify, formulate, and solve problems related to PLC. • Design a system, component, or process to meet desired needs of the industrial requirement. • Implement a complete SCADA project relating to an industrial process or operation
Description
Basics of PLC – Architecture of PLC – Advantages – Types of PLC – Introduction to PLC Networking – Protocols – Field bus – Process bus and Ethernet. Types of Programming – Simple process control programs using Relay Ladder Logic and Boolean logic methods – PLC arithmetic functions – Process automation - Difference between SCADA system and DCS – Architecture – Local control Unit – Programming language – Operator interface –Engineering interfaces. Introduction to SCADA – Comparison between SCADA and DCS - Necessity and Role in Industrial Automation – Text display – Operator panels & Touch panels - Factory Automation - Computer Integrated Manufacture – CNC – Intelligent automation – Wireless controls.
References
1. Webb, John W.Reis, Ronald A., “Programmable Logic Controllers Principles and Application”, PHI Learning, New Delhi, 5th Edition, 2002. 2. Dieter K. Hammer, Lonnie R. Welch, Dieter K. Hammer, “Engineering of Distributed Control Systems”, Nova Science Publishers, USA, 2001. 3. Gary Dunning, “Introduction to Programmable Logic Controllers”, Thomson Business Information, New Delhi, 2nd Edition, 2009. 4. Bolton. W, “Programmable Logic Controllers”, Elsevier India Private Limited, 5th Edition, New Delhi, 2010. 5. Mikell P. Groover, “Automation Produciton systems and Computer Integrated Manufacturing”, PHI Learning Ltd., 3rd Edition, New Delhi, 2009
Credits: 3:0:0 14EI2045 ARTIFICIAL ORGANS AND REHABILITATION ENGINEERING
Course Objective
• To know about various types of assist devices. • To give a basic idea of the artificial organs that can aid a human to live a normal life. • To provide the awareness of how a help can be rendered to a differently abled person
Course Outcome
• Have knowledge about various types of assist devices. • Students will have the ability to choose which type of assist device is suitable for various disorders and legal aspects related to rehabilitation. • Students will have the urge to develop new devices based on the basic knowledge gained in different assisting devices.
Description
Biomaterials used in artificial organs andprostheses, Outlook for Organ replacement – Design considerations –Evaluation Process - Brief of kidney filtration, Haemodialysis: flat plate type, coil typeand hollow fiber. Haemodialysis Machine, Portable kidney machine - Brief of lungs gaseous exchange / transport,artificial heart-lung devices. Oxygenators: bubble, film oxygenators and membrane oxygenators. Gas flow rate and area for membrane oxygenators - Anatomy & Physiology of EAR-air conduction, bone conduction, masking, functional diagram of an audiometer. Hearing aids: different types, receiver amplifiers - Ultra sonic and laser canes, Intra ocular lens, Braille Reader, Tactile devices for visually challenged, Text voice converter.
Reference Books
1. Joseph D. Bronzing, “The Biomedical Engineering Handbook”, CRC Press, Connecticut, 2nd Edition, 2000. 2. Leslie Cromwell, “Biomedical Instrumentation and measurement”, Prentice hall of India, New Delhi, 2007 3. Khandpur R.S, “Handbook of Biomedical Instrumentation”, Tata McGraw-Hill, New Delhi, 2007. 4. Laurence J. Street, “Introduction to Biomedical Engineering Technology”, CRC Press 2007.
5. Myer Kutz, “Standard Handbook of Biomedical Engineering & Design”, McGraw-Hill Professional. 1st
Edition, 2002 6. D. Jennings, A. Flint, B.C.H. firton and L.D.M. Nokes, “Introduction to Medical Electronics Applications”
Butterworth-Heinemann; 1995.
Credits: 3:0:0
14EI2046 PROCESS CONTROL FOR FOOD ENGINEERS
Course Objective:
To provide sound knowledge in the basic concepts of control theory To provide knowledge about the importance of control systems To provide knowledge on the basic concepts of instrumentation
Course Outcome:
Analyze the transient and frequency response of systems Test the stability of a given system Apply controller principles to typical applications
Introduction to process control: Importance of Process control systems, steady state design, process control block diagram, types of responses, transforms of functions, Control systems, Open and closed loop systems, hydraulic and pneumatic systems, Control valves, Stability analysis, Stability criterion, Characteristic equation, Routh test for stability, signal flow graph, Masons’s Gain formula, block diagram, Industrial instrumentation, Measurement methods for sensing the pressure, temperature, level, density, composition.
References
1. J.F Richardson A D. G. Peacock, Coulson & Richardson’s “Chemical Engineering” Volume3, (Chemical and Biochemical reactors and process control) Butherworth – Heinemann, an imprint of Elsevier, 2006. 2. Donald R. Coughanowr., “Process System analysis and control” McGraw Hill International Edition , Second Edition, Singapore, 2008 3. Nagoorkani. A “Control Systems”, RBA publications, 2nd edition, Nineteenth reprint 2012 4. S. Baskar, “Instrumentation control system measurements and controls”, Anuradha Agencies Publishers, 2004. 5. Nagrath. M and Gopal. I.J, “Control Systems Engineering”, Wiley Eastern Limited, Third Edition Reprint 2003.
14EI2047 PROCESS CONTROL LABORATORY FOR FOOD ENGINEERS
Co-Requisite: 14EI2046 Process Control for Food Engineers
Credits: 0:0:2
Course Objective:
To learn the characteristics of instruments. To introduce the concepts of control systems. To gain knowledge on stability analysis of a system
Course Outcome:
Determine the characteristics of instruments. Design controllers for a given system. Perform stability analysis of a system.
Description:
This laboratory enables the student to analyze the performance of various measuring instruments and use them to control a system.
Experiments:
The faculty conducting the laboratory will prepare a list of 12 experiments and get the approval of HOD/Director and notify it at the beginning of each semester.
Credits: 3:0:0
14EI2048 INSTRUMENTATION AND CONTROL SYSTEMS
Course Objective:
• To provide sound knowledge in the basic concepts of instrumentation • To introduce the basics of control systems • To discuss about stability analysis of systems
Course Outcome:
• Analyze the transient and frequency response of systems. • Test the stability of a given system. • Apply controller principles to typical applications.
General concepts of Mechanical Instrumentation, generalized measurement system - Classification of instruments as indicators,Recorders and integrators Measurement error and calibration, Pressure And Temperature Measurement, Strain And Flow Measurement, Control Systems: Open and closed systems, Servo– mechanisms, Transfer functions,Signal flow graphs, Block diagram algebra, hydraulic and pneumatic control systems, Two way control , Proportional control - Differential and Integral control, Stability analysis, Concept of Stability, Necessary condition for Stability, Routh stability criterion, Polar and Bode plots, Nyquist plots
References
1. Jain R.K., “Mechanical and Industrial Measurements” Khanna Publishers, 2002. 2. Nagoorkani.A “Control Systems”, RBA publications, first edition ninth reprint 2002. 3. Sawhny, A.K. “Electrical and Electronics Measurements & Instrumentation”, DhanpatRai& Co., 2000. 4. Collet. C. V. and Hope. A.D. ‘Engineering Measurements’ 2nd Edition ELBS. 5. Nagrath. M. and Gopal.I.J.Control systems Engineering, Wiley eastern Ltd.,.2001. 6. Baskar S,’Instrumentation control system measurements and controls ‘anuradha agencies publishers,2004.
Credits: 3:0:0 14EI3002 INSTRUMENTATION
Course Objective:
• To introduce the fundamental concepts of Instrumentation System • To understand the importance of Instrumentation • To learn about computer based instrumentation
Course Outcome:
• Select suitable transducer for a specific instrumentation system • Analyze the characteristics of transducers • Apply computer based instrumentation for real time applications
Instrumentation system – The general instrumentation system, Static and Dynamic Characteristics, Resistance and Inductance transducers, Capacitance and Piezoelectric transducers, Digital methods of measurements – Digital voltmeters and multimeters , Digital frequency, period and time measurements, Digital tachometers, Digital phase meters, Digital data recording, Digital Transducers, Computer based instrumentation – Evolution of Virtual Instrumentation, Architecture of Virtual
Instrumentation, Virtual Instruments Versus Traditional Instruments, Advantages of VI, Interface Buses: PCI, PXI, and VXI.
References
1. Jackson R G, “Novel Sensors and Sensing”, Institute of Physics Publishing, Bristol and Philadelphia, 2004. 2. Doeblin E.O, “Measurement Systems– Applications and Design”, McGraw Hill, New York, 2003. 3. Kalsi H S, “Electronic Instrumentation”, Second Edition, Tata McGraw Hill, New Delhi, 2009 4. John Park ,Steve Mackay,” Practical Data Acquisition for Instrumentation and Control Systems” Elsevier, 2003. 5. Mathivanan “PC based instrumentation: concepts and practice” PHI, 2008 6. Dr.S.Renganathan, “Transducer Engineering”, Allied publishers, New Delhi,2003. 7. D.Patranabis, “Principles of Electronic Instrumentation,” PHI, 2008 8. S. Sumathi and P. Surekha , “LabVIEW based Advanced Instrumentation Systems” Springer, 2007. 9. H K P Neubert, “Instrument Transducers”, Oxford University Press, Cambridge,2000.
Credits: 3:0:0 14EI3003 ADVANCED PROCESS CONTROL
Course Objective:
• To equip the students with the basic knowledge of Process Modelling. • To understand various controllers and control algorithms. • To introduce the concept of Multivariable systems and decoupling.
Course Outcome:
• Develop mathematical model of a physical process. • Design various controllers. • Understand the knowledge of MIMO process and decoupling.
Process control system – Terms and objectives, Piping and Instrumentation diagram, Instrument terms and symbols, Classification of variables, Modelling of simple systems Basic control action – Continuous controller modes- Selection of control mode for different process with control scheme, Control valve types and characteristics, Controller tuning – Optimum controller settings, Tuning of controllers, Advanced Control schemes, MIMO systems–Introduction, loop interaction , relative gains., Advanced control strategies – Internal model control, Adaptive control, Dynamic matrix control, Generalized predictive control
References
1. Stephanopoulos G., “Chemical Process Control, Prentice Hall, New Delhi, 2003. 2. Coughanowr D.R., “Process Systems Analysis and Control”, McGraw – Hill Higher Education, Singapore, 2008. 3. Wayne BequetteB,’ Process control: modeling, design, and simulation’ Prentice Hall , New Jersey – 2003. 4. Smith C.L and Corripio.A..B, “Principles and Practice of Automatic Process Control”, John Wiley and Sons, New York, 2006. 5. Dale E. Seborg, Thomas F. Edgar, Duncan A. Mellichamp, “Process Dynamics and Control” ,Willey India, 2006. 6. Marlin. T.E., Process Control, Second Edition McGraw Hill New York, 2000
14EI3004 INDUSTRIAL INSTRUMENTATION AND PROCESS CONTROL LABORATORY
Co-Requisite: 14EI3003 – Advanced Process Control
Credits: 0:0:2
Course Objective:
• To demonstrate the various process Measurements. • To inculcate the various controller design. • To give an exposure about Programmable Logic Controller.
Course Outcome:
• Measure various process measurements using the appropriate instruments. • Design control algorithms for different control loops. • Write ladder logic in Programmable Logic Controller for Control purpose.
Experiments:
The faculty conducting the laboratory will prepare a list of 12 experiments and get the approval of HOD/Director and notify it at the beginning of each semester.
Credits: 3:0:0 14EI3005 ADVANCED CONTROL SYSTEMS
Course Objective:
• To understand the basics of mathematical modeling. • To study the stability analysis of linear and non linear systems. • To study the concepts of robustness
Course Outcome:
• Apply the modelling concepts to systems • Analyse stability of a system • Perform robust control of systems
Modelling of dynamic systems-Definition, Mathematical modelling, State space representation, Centrifugal Governor, Ground vehicle, Permanent Magnet stepper motor, Inverted Pendulum, Analysis of mathematical models – State space method, Phase plane, Isoclines, Numerical methods, State space analysis – Reachability and controllability , Observability and constructability, Companion forms, Controller / Observer form, State feedback control, State estimators, Stability of nonlinear system – Lyapunov stability theorems, Krasovskii’s method, Variable gradient method, Phase plane analysis, Singular points, Limit cycle, Describing function analysis. Robust PID control – Introduction to robust control- PID Tuning– Modifications of PID control scheme – Two Degrees of Freedom Control – Design consideration of Robust Control
References
1. Stanislaw Zak, ‘Systems and Control’, Oxford University Press, 2003. 2. Gopal M, Digital Control and State variable Methods, Tata McGrawHill, New Delhi, 2003. 3. Ogata K, “Modern Control Engineering”, Pearson Education, New Jersey 2009. 4. Vidyasagar .M, “Nonlinear system analysis”, Prentice Hall Inc., New Jersey 2002. 5. Singaresu S. Rao, “Applied Numerical Methods” Prentice Hall, Upper Saddle River, New Jersey, 2001. 6. Jean – Jacques E. Slotine, Weiping Li, “Applied nonlinear control”, Prentice Hall Inc., New Jersey, 2004.
Credits: 3:0:0 14EI3006 DISCRETE CONTROL SYSTEM
Course Objective:
• To learn the concepts of discrete time Control systems. • To introduce polynomial equations approach to control system design. • To deal with the different types of digital control algorithm.
Course Outcome:
• Appreciate the need for discrete time control systems • Design control system using polynomial equations approach. • Develop different types of digital control algorithm for a system.
Z transform – Review of Z Transform –Stability Analysis in Z domain State space analysis – State Space representation of discrete time Signals – Solving discrete time State Space Equations Pole placement and observer design – Controllability – Observability –Design via Pole Placement – State Observer Polynomial approach – Polynomial Equations Approach to Control System Design Digital algorithms – Implementation of different digital control algorithms
References
1. Ogata, “Discrete – Time Control Systems”, Pearson Education, Sigapore,2002. 2. Ky M. Vu, Optimal Discrete Control Theory The Rational Function Structure Model, Library and archives Canada cataloguing in publication, Canada,2007. 3. Gene F. Franklin,J. David Powell, “Digital control of dynamic systems”, Pearson Education Limited –2002. 4. Gopal M, Digital Control and State variable Methods, Second Edition, Tata McGrawHill, New Delhi, 2003.
Credits: 3:0:0 14EI3007 INTELLIGENT CONTROLLERS
Course Objective:
To introduce the basic concepts of neural networks and its applications in Control. To introduce fuzzy logic concept and its applications in Control. To introduce genetic algorithm
Course Outcome:
Design Neural Network based application Use Soft Computing to solve real world problems mainly pertaining to Control system applications. Suggest an appropriate control approach for different applications.
Neural Networks: Introduction – Biological Neurons and their artificial Models, Learning Rules, Types Of Neural Networks , Schemes Of Neuro Control, System Identification , Case studies, Fuzzy Logic: Fuzzy Sets, Fuzzy Operation, Fuzzy Arithmetic, Fuzzy Relations, Fuzzy Relational Equations, Approximate Reasoning, Fuzzy Propositions, Fuzzy Quantifiers Structure of Fuzzy Logic Controller, Fuzzy Control Applications
Genetic Algorithm and its applications: Fundamentals, Comparison Of GA And Traditional Search Methods, Genetic Algorithm In Scientific Models And Theoretical Foundations, Case Studies
References
1. Jacek M Zurada, ‘Introduction to Artificial Neural Systems’, Jaico Publishing House, 1999.
2. Rajasekaran.S and G.A Vijayalakshmi Pai, ‘Neural Networks, Fuzzy logic and Genetic Algorithms,
Synthesis and Applications’, Prentice Hall of India, New Delhi – 2003. 3. Klir G.J. &Folger T.A. ‘Fuzzy sets, uncertainty and Information’, Prentice Hall of India Pvt. Ltd.,1993. 4. Zimmerman H.J. ‘Fuzzy set theory –and its Applications’ – Kluwer Academic
Publishers,1994. 5. Melanie Mitchell, ‘An introduction to Genetic Algorithm’, Prentice – Hall of India, New Delhi, Edition: 2004. 6. Kosko, B. ‘Neural Networks and Fuzzy Systems’, Prentice – Hall of India Pvt. Ltd.,1994.
Credits: 3:0:0 14EI3008 OPTIMAL CONTROL THEORY
Course Objective:
• To introduce the theory of optimal control and its applications. • To provide knowledge of dynamic optimization • To deal with design optimal control system
Course Outcome:
• Apply optimal control concepts to systems. • Use dynamic optimization techniques to controllers. • Design optimal control algorithms for real time systems.
Introduction , Problem formulation , Optimal control problem, Performance measures for optimal control problem, Selection, Dynamic programming – Optimal control law, Principle of optimality, A recurrence relation of dynamic programming, Hamilton – Jacobi – Bellman equation, Calculus of variations – Functions and Functional , Maxima and minima of function, Variation of functional , Extremal of functional, Euler Lagrange equation Variational approach to optimal control problems, Necessary conditions for optimal control, Linear regulator problems, Linear tracking problems, Pontryagin’s minimum principle and state inequality constraints, Minimum time problems – Singular intervals in optimal control problems, Various optimization algorithms
References
1. Donald E. Kirk, Optimal Control Theory: An Introduction, Prentice – Hall networks series, New Jersey, 2004. 2. Singiresu S. Rao “Engineering Optimization: Theory and Practice” New Age International (P) Ltd., Publishers New Delhi – 2004. 3. Gopal M, “Digital Control and State Variable Methods”, Tata McGraw – Hill Companies New Delhi, 2009. 4. Dimitri P. Bertsekas.’Dynamic Programming and Optimal Control’ Vol –1 Athena Scientific, Bell mount MA, 2000.
Credits: 3:0: 0 14EI3009 INDUSTRIAL INSTRUMENTATION
Course Objective:
• To provide the basic concepts of various industrial process measurements • To give an exposure about smart instruments. • To design and calibrate measuring Instruments
Course Outcome:
• Design and calibrate the measuring instruments • Analyze the characteristics of instruments • Suggest suitable instruments for a particular application
Design and Calibration of various types of measuring instruments for Pressure Measurement, Flow Measurement, Temperature Measurement and Level Measurement.
References
1. Doeblin E.O.I, Measurement Systems: Application and Design, Fifth Edition, McGraw –Hill Publishing Co. 5th edition, 2003. 2. Liptak B. ‘Process Measurement and Analysis’, 4th Edition,ISA, CRC Press, 2003. 3. Tatamangalam R., ‘Industrial Instrumentation Principles and Design’, Springer Verlag, 2000. 4. Singh. S.K, ‘Industrial Instrumentation and Control’, Tata McGraw Hill, Reprint 2004.
Credits: 3:0:0 14EI3010 CONTROL SYSTEM DESIGN
Course Objective:
To impart the knowledge of controllers and compensators. To make the students to study the basic concepts of discrete domain representation of the system. To guide the students to design filters, optimal discrete controllers.
Course Outcome:
Design controllers for process applications Represent systems in discrete domain Design filters for real time applications
Conventional Design Methods: Design specifications, PID controllers and compensators, Root locus based design, Bode based design, Design examples, Design In Discrete Domain: Sample and Hold, Digital equivalents, Impulse and step invariant transformations , Methods of discretisation, Effect of sampling, Direct discrete design, Discrete root locus, Design examples, Optimal Control :Formation of optimal control problems, Calculus of variations, Hamiltonian formulation, Discrete State Variable Design: Discrete pole placement, State and output feedback, Estimated state feedback, Discrete optimal control , Dynamic programming - Design examples, State Estimation :State Estimation Problem, Luenberger’s observer - Noise characteristics, Kalman - Bucy filter, Separation Theorem, Controller Design, Wiener filter, Design examples.
References
1. M. Gopal “Modern control system Theory” New Age International, 2005. 2. Benjamin C. Kuo “Digital control systems”, Oxford University Press, 2004. 3. G. F. Franklin, J. D. Powell and A. E. Naeini “Feedback Control of Dynamic Systems”, PHI (Pearson), 2002. 4. Graham C. Goodwin, Stefan F. Graebe and Mario E. Salgado “Control system Design”, PHI (Pearson), 2003. 5. G. F. Franklin, J. D. Powell and M Workman, “Digital Control of Dynamic Systems”, PHI (Pearson), 2002. 6. B.D.O. Anderson and J.B. Moore., ‘Optimal Filtering’, Prentice hall Inc., N.J., Second version published in 2005. 7. Loan D. Landau, Gianluca Zito,” Digital Control Systems, Design, Identification and Implementation”, Springer, 2006.
Credits: 0:0:2 14EI3011 VIRTUAL INSTRUMENTATION LABORATORY
Course Objective:
• To strengthen the knowledge of Virtual Instrumentation. • To understand the concept of signal processing using virtual instruments • To introduce the concept of Data Acquisition using virtual instrumentation
Course Outcome:
• Analyze real world signals • Interface real process with a virtual instrument. • Perform signal processing operations using virtual instrumentation.
Experiments:
The faculty conducting the laboratory will prepare a list of 12 experiments and get the approval of HOD/Director and notify it at the beginning of each semester.
Credits:0:0:2 14EI3012 EMBEDDED CONTROL SYSTEMS LABORATORY
Course Objective:
To learn about the Embedded Processors with Real World applications. To introduce the concept of control applications in embedded systems. To enhance the knowledge in interfacing processes with embedded controllers.
Course Outcome:
Write programs in an IDE and download it to the Processor. Design and program Embedded circuits. Design control algorithms in an embedded processor.
Credits: 3:0:0 14EI3014 INDUSTRIAL AUTOMATION
Course Objective:
To introduce the process control philosophies To learn the Programmable Logic controller design To deal with PLC for control applications
Course Outcome:
Apply PLC programming for control purpose Apply ladder logic methodology in automation field Apply PLC in real time continuous process
Nature of Industrial Process: continuous & discrete state ,sequential process, process variables and their classification. Introduction to Process Control Philosophies: type of relays, ladder logic methodology, Introduction to Programmable Logic Controllers: PLC programming methodologies: ladder diagram, STL, functional block diagram, creating ladder diagram from process control descriptions, introduction to IEC61131 international standard for PLC. PLC functions- PLC Timer & Counter functions - on-delay timer, off-delay Timers- PLC Data Handling: - PLC arithmetic and logical functions- Analog value processing: types of analog modules, analog input and output examples, PID control of continuous process.
References
1. John webb, “Programmable logic controllers-Principles & applications”, Prentice Hall of India,2003. 2. T. A. Hughes, ”Programmable controllers, ISA, 2005. 3. 1.C. D. Johnson, “Process control instrumentation Technology, 3rd Edition, John Wiley & Sons, 1988.
Credits: 3:0:0 14EI3015 SYSTEM IDENTIFICATION AND ADAPTIVE CONTROL
Course Objective:
• To impart the concepts of system identification • To introduce the concept of adaptive control
• To understand the concept of signal modelling
Course Outcome:
• Identify the given process • Validate the identified model • Design adaptive control for practical applications.
Signal modelling – Models of LTI systems- - Models for Time - varying and Non - linear systems, Models with Nonlinearities, Nonlinear state - space models, Black box models, Fuzzy models, Identification – Non - Parametric and Parametric identification, Transient response and Correlation Analysis, Frequency response analysis, Spectral Analysis, Least Square, Recursive Least Square, Validation – Non - Linear Identification and Model Validation, State estimation techniques, Non linear identification using Neural Network and Fuzzy Logic, Adaptive control –Self Tuning Regulators (STR), Model Reference Adaptive Control (MRAC) , Gain Scheduling, Applications –Inverted Pendulum, Robot arm, Process control application: heat exchanger, Distillation column - Application to power system, Ship steering control.
References
1. Narendra and Annasamy,” Stable Adaptive Control Systems, Prentice Hall, Inc., 2005. 2. Astrom and Wittenmark,” Adaptive Control Second Edition”, Addison - Wesley Publishing Company 1995. 3. Monson H.Hayes,’ Statistical Digital Signal Processing and Modelling”, John Wiley and Sons,2002 4. Lennart Ljung, “System Identification Theory for the User”, Prentice Hall, Inc., NJ, 1999. 5. Torsten Soderstrom, Petre Stoica, “System Identification”, prentice Hall ` International (UK) Ltd,1994. 6. William S. Levine, “ Control Hand Book” CRC Press, Jaico Publishing House, 1999. 7. Narendra and Annasamy,” Stable Adaptive Control Systems, Prentice Hall, Inc., 2005.
Credits: 3:0:0 14EI3016 SCADA SYSTEMS AND APPLICATIONS
Course Objective:
• To introduce the need for Data Acquisition. • To understand the concept of Supervisory Control. • To deal with the applications of SCADA Systems.
Course Outcome:
• Appreciate the need of Data Acquisition. • Apply the concept of Supervisory Control • Perform simulation for various process.
Introduction to SCADA and PLC:SCADA: Data acquisition system, PLC: Block diagram, programming languages, SCADA system components: Schemes, Remote Terminal Unit, Intelligent Electronic Devices, Communication Network, SCADA server, SCADA Architecture: Various SCADA Architectures, advantages and disadvantages, SCADA Communication and Operation and control of interconnected power system:SCADA applications
References
1. Stuart A Boyer, “SCADA supervisory control and data acquisition”,ISA- The Instrumentation, Systems and Automation Society,2010. 2. Gordan Clark, Deem Reynders, “Practical Modem SCADA Protocols”, Elsevier Publications,2004. 3. Sunil S. Rao, “Switchgear and Protections”, Khanna Publication,1992. 4. John Park, Steve Mackay, “Practical Data Acquisition for Instrumentation and Control Systems”,.Elsevier Publications,2003.
Credits: 3:0:0 14EI3017 DESIGN OF LINEAR MULTIVARIABLE CONTROL SYSTEMS
Course Objective:
• To inculcate the knowledge of Multivariable control systems. • To design controller for multivariable control systems. • To apply the design for various applications.
Course Outcome:
• Apply the concept of Multivariable control systems. • Design controller for multivariable control systems. • Use the corresponding controller synthesis techniques.
Analysis: system representations, return difference matrix, stability theory, multivariable poles and zeros. Design: design criteria, LQG design methods (including the optimal linear quadratic regulator and the Kalman filter), normbased methods, robust stability and performance. H-infinity design techniques, including the generalised regulator problem. Model reduction, including modal and balanced truncation. Design examples: use of software for the design of controllers for industrial processes.
References
1. Stanislaw Zak, ‘Systems and Control’, Oxford University Press, 2003. 2. Gopal M, “Digital Control and State variable Methods”, Tata McGraw Hill, New Delhi, 2003. 3. Charles R. Slivinsky, Donald G. Schultz, Lynn E. Weaver, “The design of linear multivariable control systems using modern control theory”, 1969. 4. Ying-Jyi Paul Wei, “Frequency-domain approaches to linear multivariable control system designs, 1979. 5. Ogata K, “Modern Control Engineering”, Pearson Education, New Jersey, 2009.
Credits: 3:0:0 14EI3018 PIPING AND INSTRUMENTATION
Course Objective:
• To inculcate the knowledge of Piping and Instrumentation diagram. • To learn the design of controller for multivariable control systems. • To apply the design for various applications.
Course Outcome:
• Apply the concepts of Multivariable control systems to real applications • Design controller for multivariable control systems. • Use the corresponding controller synthesis techniques.
Types of flow sheets, Flow sheet Presentation, Flow Sheet Symbols, Process flow diagram- Synthesis of steady state flow sheet - Flow sheeting software. P & I D objectives, guide rules, Symbols, Line numbering, Line schedule, P & I D development, typical stages of P & I D. P & I D for rotating equipment and static pressure vessels, Process vessels, absorber, Control System for Heater, Heat exchangers, reactors, dryers, Distillation column, Applications of P & I D in design stage - Construction stage - Commissioning stage - Operating stage - Revamping stage - Applications of P & I D in Risk
References
1. Ernest E. Ludwig, “Applied Process Design for Chemical and Petrochemical Plants”, Vol.-I Gulf Publishing Company, Houston, 1989. 2. Max. S. Peters and K.D.Timmerhaus, “Plant Design and Economics for Chemical Engineers”, McGraw Hill, Inc., New York, 1991.
3. 3.Bela G. Liptak, “ Process Measurement and Analysis”, ISA, CRC press,2003. 4. Anil Kumar,”Chemical Process Synthesis and Engineering Design”, Tata McGraw Hill publishing
Company Limited, New Delhi - 1981. 5. A.N. Westerberg, et al., “Process Flowsheeting”, Cambridge University Press, 1979.
Credits: 3:0:0 14EI3019 EMBEDDED INSTRUMENTATION
Course Objective:
• To introduce the fundamental concepts of Instrumentation System • To understand the importance of Instrumentation • To deal with the concepts of embedded instrumentation systems
Course Outcome:
• Select suitable transducer for a specific instrumentation system • Analyze the characteristics of transducers • Computer based instrumentation for real time applications
Instrumentation system - resistance and inductance transducer-capacitance and piezoelectric transducers, digital methods of measurements: computer based instrumentation, evolution of virtual instrumentation, architecture of embedded virtual instrumentation, embedded virtual instruments versus traditional instruments , advantages of vi –pc based data acquisition system, interfacing techniques to the IBM PC – plug– in data acquisition boards –interface buses: PCI, PXI, VXI
References
1. S. Sumathi, P.Surekha, “LabVIEW based Advanced Instrumentation Systems “ springer 2007 2. N.Mathivanan, “ PC_Based Instrumentation- Concepts and Practice, PHI Learning Pvt. Ltd, 2007 3. Walt Boyes, “ Instrumentation Reference Books”, Third Edition, Butterworth Heinemann, 2003.
14EI3020 NETWORKS AND PROTOCOLS FOR INSTRUMENTATION AND CONTROL Credits: 3:0:0
Course Objective:
To understand the System Interconnection and protocols. To introduce the concept of communication protocols and give an overview of Data Communication Standards. To discuss the types of cables used for transmission. To discuss the operation and applications of the Protocols used in Industries .
Course Outcome:
At the end of the course, Students will be able to Identify the protocol. Choose the require protocol and the communication modes for the given system. Select a suitable cable for the transmission .
open systems interconnection ( osi ) model – protocols – physical standard – smart instrumentation systems –bits, bytes and characters – communication principles – communication modes – asynchronous systems –synchronous systems -data communication standards: standards organizations – serial data communications interface standards – balanced and unbalanced transmission lines – RS232 interface standard – troubleshooting serial data communication circuits – test equipment – ethernet – ethernet protocol operation – ethernet hardware requirements -cabling, electrical noise and error detection- modem and multiplexer- industrial protocol: profibus
References
1. Steve Mackay, John Park and Edwin Wright, “Practical Data Communication for Instrumentation and Control”, Newnes Elsevier, USA, 2002. 2. TanenbaumA.S, “Computer Networks”, Fourth Edition, Prentice – Hall of India, Hyderabad, 2002. 3. William A Shay, “Understanding Data Communications and networks”, Pacific Grove, USA, 2003.
Credits: 3:0:0 14EI3022 DESIGN OF EMBEDDED CONTROL SYSTEM
Course Objective:
To strengthen the knowledge of embedded design challenges To understand the concept of controller using embedded To deal with the concept of robot system
Course Outcome:
Design control application using embedded system Meet the Demand for Embedded Controls Engineers Design robust controllers
Characteristics of embedded computing applications – Designing an Adaptive Cruise Control System, Embedded systems , basic concept, Introduction to embedded control system design, System identification and model-order reduction, Classical controller design, Classical controller design, Fundamentals of robust control, Robust controller design, Embedded safety loop development
References
1. Forrai, Alexandru Embedded Control System Design- “A Model Based Approach”, Springer publication, 2013. 2. Adamski, Marian Andrzej, Karatkevich, Andrei, Wegrzyn, Marek (Eds.), “Design of Embedded Control Systems”, Springer Publication, 2005.
Credit: 3:0:0 14EI3023 ADVANCED PROCESSORS FOR CONTROL AND AUTOMATION
Course Objective:
To learn recent trends in advanced microcontroller applications. To learn microcontroller implementation for control applications To understand programming with 8 and 32 bit microcontrollers.
Course Outcome: Program microcontrollers for embedded applications. Illustrate architecture differences and to show common characteristics. Design the microcontroller for real time projects.
8 bit processor: 8051 architecture, Programming examples with stepper motor, dc motor, interfacing timer with control applications, CPU Architecture of PIC microcontroller –temperature, flow process interfacing , A/D converter, UART , 16 bit processor/32 bit processor: Introduction to 16/32 bit processor, ARM architecture, The ARM instruction set, The thumb instruction set , programming examples with control applications
References
1. Raj Kamal – “Microcontrollers – Architecture, Programming, Interfacing and System Design”, Pearson Education, USA, 2005. 2. SteaveFurber,” ARM system–on–chip architecture” Addison Wesley, New Delhi, 2000. 3. John.B.Peatman, “Design with PIC Micro Controller”, Pearson Education, USA, 2003.
4. Mohammad Ali Mazide, Janice GillispicMazidi, RolinD.Mckinlay, “ The 8051 micro controller and embedded systems using assembly and C”, prentice Hall of India, Hyderabad, 2006. 5. Kenneth Ayala ,”The 8051 Microcontroller”, Thomson Delmar Learning , New Jersey, 2004.
Credits: 0:0:2 14EI3028 EMBEDDED VIRTUAL INSTRUMENTATION LABORATORY
Course Objective:
• To strengthen the knowledge of Virtual Instrumentation.. • To understand the concept of signal processing • To introduce the concept of Data Acquisition.
Course Outcome:
• Build simple virtual instruments • Interface the embedded systems to real time signals • Design embedded applications.
Experiments:
The faculty conducting the laboratory will prepare a list of 12 experiments and get the approval of HOD/Director and notify it at the beginning of each semester.
Credits: 3:0:0
14EI3029 EMBEDDED AUTOMOTIVE SYSTEMS
Course Objective:
To understand the current trends in automobiles To understand basic sensor arrangement and its types To understand the embedded processor
Course Outcome:
Implement automotive embedded systems in real time applications Implement controllers design using recent advances like GLS, GPSS, GMS Design various sensors for real time applications.
Current trends in Automobiles- components for electronic engine management system. Electronic dashboard instruments, onboard diagnostic system , security and warming system- Vehicle motion control. Sensors and actuators, and their interfacing. Basic sensor arrangement, types of sensors- Electronic ignition systems. Types of solid state ignition systems and their principleof operation. Digital engine control system. Distributor less ignition – Integrated engine control system, Exhaust emission control engineering. Automotive Embedded systems. PIC, Freescale microcontroller based system. Recent advances like GLS, GPSS, GMS
References
1. William B. Riddens, “Understanding Automotive Electronics”, 5th Edition, Butterworth Hennimann
Woburn, Sixth Edition, 2003 2. Tom Weather Jr. & Cland c. Ilunter, “ Automotive computers and control system” Prentice Hall Inc., New
Jersey.,2001 3. Robert Bosch,” Automotive Hand Book”, SAE , (5th Edition),2000
Credit: 3:0:0 14EI3030 AUTOMOTIVE SENSORS AND INTELLIGENT SYSTEMS
Course Objective:
To introduce sensors in modern electronic system To introduce the concept of intelligent transport systems To discuss various sensors and interfacing concept
Course Outcome:
Interface various sensors in automotive electronic systems Design, simulate and implement sensor interface Select sensors of different characteristics.
Introduction to automotive sensors and instrumentation – sensor product selection guide- sensors and interfacing –principles of actuation and control- sensors and interfacing techniques for Engine control, adaptive cruise control, braking control, traction control, steering, stability, sensors for intelligent transport systems, sensors for occupant safety.
References
1. Ronald K. Jurgeaon, “ Automotive ElectronicsHandbook, 2nd Edition, Mc Graw-Hill,2007 2. William B. Ribbens, “Understanding Automotive Electronics”, 5th Edition, Newnes, 2006 3. E.Q.Doeblin, “Measurement Systems, Application and Design”, 4th Edition, McGraw-Hill, 2002.
Credit: 3:0:0 14EI3031 AUTOMOTIVE PROTOCOLS AND TELEMATICS
Course Objective:
To prepare the students to analyse, simulate automotive communication protocols To introduce theoretical concepts of telematics technologies relevant to automotive applications To introduce automotive communication protocols and diagnostics protocols.
Course Outcome: Gain in depth knowledge on data communication and networking and applied in real time applications. Implement automotive communication protocols and telematics technologies. Simulate and implement telematics in wireless technologies.
Basics of Data Communication Networks and Automotive Communication Protocols - Controller Area Network (CAN) Protocol-CAN Higher Layer Protocols-Local Interconnect Network (LIN) ProtocolFlexRay Protocol-Media Oriented System Transport (MOST) Protocol - In Vehicle Network DiagnosticsTelematics basics, applications and technologies- Global Positioning Systems (GPS), Inertial Navigation Systems (INS), Vehicle Location and Navigation, Bluetooth, UWB, RFID, Satellite Radio(XM-Radio and SIRIUS), Fleet Management and Case Study
References
1. Aswin Goel, “Fleet Management- Real-time management and planning of commercial vehicle operations Series”, Springer., 2008 2. Gilbert Held. “Inter- and Intra-Vehicle Communications”, CRC Press, 2007 3. Behrouz Forouzan., “Data Communications and Networking”, McGraw-Hill. 2003 4. Dennis Foy. Automotive Telematics, Red Hat., 2002
Credits: 3:0:0 14EI3033 BIOMEDICAL SENSORS AND SIGNAL CONDITIONING
Course Objective:
To understand bioelectric amplifiers To discuss filter and circuits To introduce application of signal conditioning in biomedical field
Course Outcome:
Identify the method to apply various signal conditioning circuits Interface bioelectric signals with embedded systems Identify the application of signal condition circuits for biomedical field.
Bioelectric amplifiers- General-purpose linear and non-linear electronic circuits typically found in industrial applications- Instrumentation amplifiers, Transducer bridge Amplifier. Frequency and time domain analysis of low pass, high pass, band pass, and band stop filters. Filter class- Frequency discriminators, oscillators, multivibrators Amplifier selection for a variety of biomedical sensors, Wheatstone bridge design, Active filter design using standard approaches, Front-end analogue circuit design for EMG, ECG, EEG ,Front-end analogue circuit design for limb movement sensing, Power supply topologies for biomedical instruments
References
1. R. B. Northrop, “Analysis and Application of Analog Electronic Circuits to Biomedical Instrumentation”, 2nd ed., CRC Press, 2012. 2. J. D. Bronzino, “Biomedical Engineering Handbook”, 3rd ed.,CRC Press & IEEE Press, 2006. 3. Ramón Pallás-Areny, John G. Webster,”Sensors and Signal Conditioning”, 2nd ed., Wiley publishers, 2000.
14EI3038 PHYSIOLOGICAL CONTROL SYSTEMS
Prerequisite: 14BT3026 Human Anatomy and physiology
Credits: 3:0:0
Course Objective:
To understand basic ideas related to modeling and different modeling techniques of certain physiological systems To understand system identification techniques To analyse physiological system in time and frequency domain
Course Outcome:
Develop mathematical model of physiological system. Simulate the physiological system and analyse in time and frequency domain Apply system identification and optimization concepts in modeling . Introduction to Physiological control systems, Illustration, modeling Elements, linear models, Distributed parameters versus lumped parameter models, principle of superposition, BioFeedback, Time and frequency domain analysis, stability analysis of linear system, model identification of physiological system, optimization technique, Simulation of biological systems, case studies.
References
1. Katz, A.M. “Physiology of the Heart”, Lippincott Williams & Wilkins, USA, 2006. Ewart Carson, Claudio Cobelli, : “Introduction of Modeling in Physiology and Medicine”,Academic Press, Netherland, 2008. 2. Vasilis.Z.Mararelis, “ Nonlinear Dynamic Modeling of Physiological System”, John Wiley & Sons, New Jersey, 2004.
3. Daniel Weiner, Johan Gabrielsson, “Pharmacokinetic and Pharmacodynamic Data
Analysis: Concepts and Applications, Sweden, 2000. 4. Milsum J H, “Biological control system analysis”, Mc GrawHill, Newyark, 1966. 5. Michael.C.K.Khoo, “Physiological control systems: Analysis, Simulation and Estimation”, IEEE Press,
Prentice Hall of India Pvt. Ltd. New Delhi. 2001.
Credits: 3:0:0 14EI3039 MEDICAL INSTRUMENTATION
Course Objective:
To strengthen the knowledge of the principle of operation and design of biomedical instruments. An attempt to render a broad and modern account of biomedical instruments. The introductory idea about human physiology system which is very important with respect to design consideration.
Course Outcome:
Apply the concepts of Medical Instrumentation to physiological measurements Design Instrumentation circuits for Biomedical Applications. Use the knowledge of Biomedical Instruments to solve Practical Problems.
Physiological measurements: Cell and its Electrical activity, Principle of Physiological systems: Cardiovascular, Nervous system, Respiratory system, Vision, Muscular system-Electrodes and bioelectric signals: Bio electrodes, ECG, EMG, EEG and EOG, Measurement of physiological parameters: Blood flow, Blood pressure, Cardiac output, Bio–chemical measurement, Photometer.
References
1. Khandpur. R. S, “Handbook of Biomedical Instrumentation”, Tata McGraw Hill, 2/e, New Delhi, 2003. 2. Leslie Cromwell, Fred J Weibell, Erich A Pfeiffer, “Biomedical Instrumentation and Measurements”, Prentice Hall of India, New Delhi, 2007. 3. Joseph J. Carr and John M. Brown, “Introduction to Biomedical Equipment Technology”,Pearson Education India, Delhi, 2004. 4. Myer Kutz, “Standard Handbook of Biomedical Engineering & Design,” McGraw– Hill Publisher, New York, 2003. 5. Webster, “Medical Instrumentation – Application & Design,” John Wiley and sons Inc, Netherlands, 2004. 6. Arumugam, “Biomedical Instrumentation”, Anuradha Publisher, Chennai.2013.
Credits: 3:0:0 14EI3040 BIO VIRTUAL INSTRUMENTATION
Course Objectives:
To provide new concepts towards measurement and virtual instruments. To know about how to acquire a data and control an external measuring device by interfacing to a computer. To become competent in signal and image acquisition and processing tools
Course Outcome:
Identify salient traits of a virtual instrument and incorporate these traits in projects. Experiment, analyze and document in the laboratory prototype measurement systems using a computer, plug-in DAQ interfaces and bench level instruments. recognize the application of VIs in medical instrumentation in developing medical instruments
Historical perspective, advantages, Architecture o f a Virtual Instrument-Graphical programming -Development of Virtual Instrument-Software and hardware installation- Common Instrument Interfaces-Current loop, interface
buses- networking basics- Image and signal Acquisition and Processing- Motion control-Applications of virtual instruments in Biomedical engineering.
References
1. Jerome, Jovitha, “Virtual Instrumentation and LABVIEW”, PHI Learning, New Delhi, First Edition, 2010. 2. Sanjay Gupta and Joseph John, “ Virtual Instrumentation using LabVIEW”, Tata Mc Graw – Hill Publishing Company Limited, New Delhi, 1st Edition, 2005. 3. Ronald W. Larsen, “LabVIEW for Engineers”, Prentice Hall Ltd, USA Jan 2010. 4. LabVIEW: Basics I & II Manual, National Instruments, 2005. 5. Gupta, “Virtual Instrumentation Using Lab View”, Tata McGraw Hill, New Delhi,1st Edition, 2008.
Credits: 3:0:0 14EI3041 HOSPITAL MANAGEMENT SYSTEM
Course Objective:
To understand the need and significance of Clinical Engineering and Health Policies. To familiarize the training strategies, quality management policies and information technology used in health care. To know the needs of managerial training to hospital staffs
Course Outcome:
Appreciate the need for standard health policies and quality management in hospitals. Apply the knowledge of computer and information technology in health care. Relate the training needs at various level of organization
Need and scopes of clinical engineering, Educational responsibilities-Design and layout of hospital-National health policies, Health organization in state- Health education-Health insurance, Health legislation-Training -Employee appraisal method-Standards, codes and quality management in health care-regulation for mobile ICU-Maintenance of equipments-work planning-Medical records and information management-information technology in medicine and healthcare-operations research in hazard management.
References
1. Webster J.C. and Albert M.Cook, “Clinical Engineering Principle and Practice”, Prentice Hall Inc., Englewood Cliffs, New Jersey, 1979. 2. Goyal R.C., “Handbook of hospital personal management”, Prentice Hall of India, 1996. 3. R. Panneerselvam, “Operations research”, PHI learning pvt. Ltd., Newdelhi.2006. 4. A.K.Malhotra,“Hospital management: An Evaluation”, Global India Publications,2009. 5. James R. Langabeer, “Health Care Operations Management: A Quantitative Approach to Business and logistics”, Jones & Bartlett Learning, UK.2008.
Credits: 3:0:0 14EI3042 COGNITIVE TECHNOLOGY FOR BIOMEDICAL ENGINEERS
Course Objective:
To introduce the basic concepts of neural networks and its applications in biomedical applications. To introduce fuzzy logic concept and its applications in medical diagnosis. To introduce the concepts of genetic algorithm for artificial intelligence
Course Outcome:
• Apply the Basic Neural Network, Fuzzy Logic and Genetic algorithms in analysis. • Develop algorithms for medical signal and image processing to solve real world problems pertaining to Biomedical applications.
• Design develop intelligent methods based on human like thinking using computing techniques.
Introduction to neural networks: Introduction – Biological neurons and their artificial models, Learning, Adaptation and neural network's learning rules, Types of neural networks, Special networks and applications: Associative memory, BAM, Hopfield network, ART Network, SOM, Case studies, Introduction to fuzzy logic: Fuzzy sets, Fuzzy logic control: Structure of fuzzy logic controller, Case studies, Genetic algorithm and its applications: Fundamentals of genetic algorithm, Case studies, Optimization techniques for medical applications, Artificial intelligence, software tools.
References
1. Jacek M Zurada, ‘Introduction to Artificial Neural Systems’, Jaico Publishing House,1999. 2. Rajasekaran S. and G.A VijayalakshmiPai, ‘Neural Networks, Fuzzy logic and Genetic Algorithms, Synthesis and Applications’, Prentice Hall of India, New Delhi – 2003. 3. Klir G.J. &Folger T.A. ‘Fuzzy sets, uncertainty and Information’, Prentice –Hall of India Pvt. Ltd.,1993. 4. Zimmerman H.J. ‘Fuzzy set theory – and its Applications’ – Kluwer Academic Publishers,1994. 5. Kosko, B. ‘Neural Networks and Fuzzy Systems’, Prentice – Hall of India Pvt. Ltd.,1994.
14EI3044 EMBEDDED BASED MEDICAL INSTRUMENTATION LABORATORY
Corequisite: 14EC3076 Embedded Systems for Biomedical Instrumentation
Credits: 0:0:2
Course Objective:
To introduce the basic concepts of embedded systems and applications to biomedical instrument design To introduce various software tools for embedded Systems with real time examples. To deal with the concepts of interfacing issues with real time signals.
Course Outcome:
Design and Analyze the systems for disease diagnosis and treatment methods Apply real time models and languages in medical image processing applications Analyze interface issues related to embedded systems.
Experiments:
The faculty conducting the laboratory will prepare a list of 12 experiments and get the approval of HOD/Director and notify it at the beginning of each semester.
14EI3045 DIAGNOSTIC AND THERAPEUTIC EQUIPMENTS LABORATORY
Co-Requisite: 14BT3026 Human Anatomy and Physiology
Credits: 0:0:2
Course objectives:
To know the various methods involved in biosignal recordings and operation of patient monitoring equipments. To develop an understanding of the physiotherapy and diathermy equipment. To provide understanding of equipments for rehabilitation.
Course outcome:
Develop measurement systems for biosignals and its signal conditioning circuits
Devise monitoring instruments, brain computer interface techniques, Design and analyse assist devices for old age and gait analysis.
Experiments:
The faculty conducting the laboratory will prepare a list of 12 experiments and get the approval of HOD/Director and notify it at the beginning of each semester.
Credits: 3:0:0 14EI3046 MEDICAL IMAGING TECHNIQUES
Course Objective:
To provide knowledge of the principle of operation and design of Radiological equipments. To know the working principles of radio diagnostic devices To know about the hazards and safety of radiation usage in hospitals
Course Outcome:
Apply Radiological equipments and its imaging techniques Analyse the present technogies and will develop new techniques Be aware of standards and safe limits of radiation exposure and control of radiation
Generation of x – rays: principles and production of soft and hard x rays-radio diagnosis: radiography, angiography, fluoroscopy, special radiological equipments-application of radioisotopes: alpha, beta and gamma emission, principle of radiation detectors, nuclear angiogram- principles of radiation therapy-Radiation safety: hazardous effect of radiation, radiation protection techniques-Safety limits, radiation monitoring-CT-MRI.
References
1. Isaac Bankman, I. N. Bankman , Handbook of Medical Imaging: Processing and Analysis(Biomedical Engineering), Academic Press, 2000. 2. Jacob Beutel (Editor), M. Sonka (Editor), Handbook of Medical Imaging, Volume 2. Medical Image Processing and Analysis , SPIE Press 2000. 3. Khandpur R.S, “Handbook of Biomedical Instrumentation”, Tata McGraw Hill, New Delhi,2003.
Credits: 3:0:0 14EI3048 CLINICAL INSTRUMENTATION
Course Objective:
To provide various techniques and methods of spectral analysis used in clinical laboratory. To give unique methods of separation of closely similar materials with chromatography. To provide the important radio chemical methods of analysis and techniques in clinical laboratory
Course Outcome:
Analyze the techniques used for characterization of materials, devices and Biological molecules Compare the important radio chemical methods of analysis. Apply clinical laboratory instrumentation for real time applications
Introduction to analytical instruments and Spectrophotometers, NMR and mass spectrometer, radiation techniques, Automated chemical analysis system, pH meters and Chromatography, Clinical instrumentation techniques, Electrophoresis and microscopy.
References
1. Khandpur R.S,”Handbook of Analytical Instruments”, Tata McGraw – Hill Publishing company limited, 2006. 2. Mousumi Debnath, “Tools and techniques of Biotechnology”, Pointer publications, 2005.
3. John G Webster, “Medical instrumentation application and design”, John wiley & Sons (Asia) Pvt Ltd, 3rd edition, 2004 4. Willard, H.H., Merrit L.L., Dean J.A Seattle F.L., ‘Instrumental Methods of Analysis’,CBS Publishing and
Distribution, 1995. 5. Robert D.Braun, Introduction to Instrumental Analysis, McGraw–Hill, Singapore, 1987.
Credits: 3:0:0 14EI3049 MEDICAL DEVICES AND SAFETY
Course Objective:
To provide useful ideas, concepts, and techniques that could be applied to reduce unacceptable errors in expected Medical Device performance. To avoid patient injury, achieving efficacious treatment, and controlling health care costs. To understand Medical data error has to be a difficult and recalcitrant phenomenon.
Course Outcome:
Appreciate the need for prevention of medical errors Explore for reasonable, acceptable, and more effective remedies Will have better understanding, knowledge, and directed motivation, there should be rapid advancement in the medical device management discipline.
Reliability, safety testing, Failure assessment, Safety and risk management, Tools for risk estimation, Safe medical devices, Handling and operation, Usability, Environmental safety , Interference with the environment, ecological safety, Mechanical safety, Electrical Safety, Biological aspect, Limitation-Protection, Leakage currents, Safety classe, Medical Standards and Regulation, six sigma standard for medical device design.
References
1. Bertil Jacobson and alan Murray, “Medical Devices Use and Safety”, Elsvier Limited, 2007. 2. Richard Fries,“Reliable Design of Medical Devices – Second Edition”, CRC Press, Taylor & Francis Group, 2006. 3. Norbert Leitgeb “SafetyofElectromedicalDevicesLaw – Risks – Opportunities”, Springer Verlog/Wein, 2010. 4. Gordon R Higson, “Medical Device Safety- The regulation of Medical Devices for Public Health and Safety”, IOP Publishing Limited, Bristol and Philadelphia, 2002. 5. Shayne Cox Gad, “Safety Evaluation of Medical Devices” Second Edition, Marcel Dekker Inc., 2002. 6. Basem El-Haik Khalid S. Mekki, “Medical Device Design for Six Sigma: A Road Map for Safety and effectiveness” John Wiley & Sons, 2011.
Credits: 3:0:0 14EI3051 MEDICAL SENSORS AND WEARABLE DEVICES
Course Objective:
To provide introduction to the field of medical sensors and an indepth and quantitative view of device design and performance analysis. To gain overview of the current state of the art to enable continuation into advanced biosensor work and design. To study about the wearable sensors and smart sensors
Course Outcome:
Evaluate a sensor based on standard performance criteria and appropriateness for an application.
identify the key design criteria and suggest an appropriate wearable sensor approach which is most likely to meet a specific biosensor application Analyse the most relevant challenges facing the smart sensor research field and for a particular challenge suggest a reasonable approach to find a solution.
Physiological Measurements: Sensors for Pressure Measurement- Sensors for Motion and Force MeasurementSensors for Flow Measurement -Temperature Measurement- Sensors for speed, torque, vibration- Wearable Sensors-smart sensors.
References
1. Tatsuo Togawa, Toshiyo Tamura, P. Ake Oberg, “Bio-Medical Transducers and Instruments”, CRC Press, USA, 2010. 2. Subhas Chandra Mukhopadhyay, Aime Lay Ekuakille, “Advances in biomedical sensing and measurements”, Lecture notes in electrical engineering, Springer Verlag, Berlin, Gábor Harsányi, “Sensors in biomedical applications: fundamentals, technology & applications”, CRC Press, USA, 2000. 3. Joseph D. Bronzino, “The biomedical engineering handbook”, Volume 2, CRC Press, USA, 2000.
Credits: 3:0:0 14EI3052 REHABILITATION ENGINEERING
Course Objective:
To provide knowledge about various types of assist devices and its applications. To provide indepth understanding of the functions of assist devices To develop new devices for rehabilitation
Course Outcome:
Operate assist devices for real time applications Choose the assist device suitable for specific disorder. Design and develop new products for rehabilitation
Rehabilitation -Prosthetic And Orthotic Devices, Types, models- Feedback in orthotic system- Material -Auditory and speech assist devices -visual aids-Tactile devices - Muscle and nerve stimulator-Robot as assist devicesPsychological aspects of Rehabilitation therapy- Legal aspect-case studies.
References
1. Albert M.Cook and Webster J.G, “Therapeutic Medical devices”, Prentice Hall Inc., NewJersy, 1982. 2. Levine.S.N.Editor, Advances in Bio Medical Engineering and Medical Physics, Inter University Publication, New York 1968. 3. Kolff W.J., Artificial Organs, John Wiley and Sons, New York,1979. 4. Andreas.F.Von racum, Hand book of bio material evalution, Mc-Millan publishers, 1980. 5. Albert M.Cook and Webster J.G., “Therapeutic Medical Devices, Prentice Hall Inc., New Jersey, 1982
Credit 3:0:0 14EI3054 BIOMECHANICS
Course Objective:
To introduce the Fundamental terms and concepts of human factors To discuss anthropometric, biomechanical and physiological principles and how they are used to optimize human well-being and overall performance. To Identify, Analyze, Setup and implement solutions to a human factors problem
Course Outcome:
Acquire biosignals and perform the quantification
Understand biomechanical and physiological principles and how they are used to optimize human wellbeing and overall performance. Apply, Analyze, Setup and implement solutions to a human factors problem
Human system modeling - human control of systems, biomechanics-stress and fatigue measurements of bones, muscles-cognitive stress-stress modeling- signal acquisition and processing-brain and computer interface-Effects of environmental conditions –heat, stress-Human Factors Applications in medical and industrial field-Human erroraccidents analysis- human factors –case study on evaluation of the physiological factors and fitness factors for defence vehicle driver –safety Standards.
References
1. Subrata Pal,“Text book of Biomechanics”, Viva education Private limited,NewDelhi. 2009. 2. Karl Kroemer, Henrike Kroemer, Katrin Kroemer-Elbert, “Ergonomics” How to Design for Ease & Efficiency, Prentice Hall International Editions, 2001. 3. Mark S Sanders, “Human Factors in Engineering and Design”, McGraw Hill, New York, 1993. 4. Bridger R S, “Introduction to Ergonomics”, Taylor and Francis, London, 2003. 5. Martin Helander, “A Guide to Ergonomics of Manufacturing”, Tata Mc GrawHill, 1996. 6. Mccormic,E.J. and Sanders.M.S “Human factors in Engineering and Design”, McGraw Hill, 1992. 7. Susan J.Hall,“Basics Bio Mechanics” 5th Edition, McGraw-Hill Publishing Co,Newyork, 2007.
Credit 3:0:0 14EI3055 MEDICAL DIAGNOSTICS AND THERAPEUTIC EQUIPMENTS
Course objectives:
To know the various biopotential recordings and operating procedure of ICCU equipments. To develop an understanding of the physiotherapy and diathermy equipment. To learn the safety standards of the diagnostics and therapeutic equipments
Course outcome:
Develop measurement systems for biosignals and its signal conditioning circuits Know the safe operating procedure of Cardiac care monitoring instruments. Get clear domain knowledge about various types of wearable and implantable devices.
Pace makers - patient monitoring system-diathermy-heart lung machine-pumps-Principle of Hemodialysis-Wearable Artificial Kidney, Implanting Type- Respiratory aids-Breathing Apparatus Operating Sequence-thermography- Fiber optics -Endoscopy, Laparoscopy, principles of Lithotripsy-communication standards-wireless telemetry.
References
1. Albert M Cook and Webster J G, “Therapeutic medical devices”, Prentice Hall NewYork , 1982. 2. Heinz Kresse, “ Handbook of Electro medicine”, John Wiely & Sons, Chrchester.1985 3. Webster J.G, “Medical Instrumentation application and design”, John Wiley and sons New York 3rd edition
1999 4. Jacobson B and Webster J G Medical and Clinical Engineering – Prentice Hall of India New Delhi 1999 5. Leslie Cromwell , Fred J.Weibell and Erich A.Pfeiffer, “Biomedical Instrumentation”,
Prentice Hall New Delhi 2000 6. Joseph J Carr and John M Brown,“Introduction to Biomedical equipment Technology”, 7. Pearson Education 4th edition, New Delhi 2001. 8. Khandpur R.S “Hand Book of Biomedical Instrumentation”, Tata McGraw Hill publication , New
Delhi 2nd edition 2003 9. John Denis Enderle, Joseph D. Bronzino, Susan M. Blanchard, “Introduction to Biomedical Engineering”,
Academic Press, 2005
Credits: 3: 0: 0 14EI3056 LIMB PROSTHETICS
Course Objective:
To introduce the Basic concepts of robots and its applications to artificial limbs To know the instrumentation involved Robot Dynamics and Kinematics To learn the applications of Robot controls
Course Outcome:
Design Robot Control System for positioning and movement Learn the basic sensor and actuators and applications of robots. Develop Robotic applications as assist devices for limbs.
Definition - Classification - History - Robots components - Degrees of freedom - Robot joints coordinates Reference frames - Workspace - Robot languages - Actuators - Sensors - Sensor characteristics - and electric actuators - Trajectory planning- motion control - Non-linear control-Image Processing And Vision SystemsPROSTHESIS, Introduction to Prosthesis, -Gait Analysis in Transtibial Amputees, Prosthesis in Knee Disarticulation- Gait Analysis in Transfemoral Amputees, -Prosthesis for Hand Amputation and Wrist Disarticulation-Recent Advances in Prosthesis -Ambulatory Aids.
References
1. Saeed B. Niku , ''Introduction to Robotics'', Pearson Education, 2002 2. K.S.Fu, Ralph Gonzalez and C.S.G.Lee, ''Robotics", TATA McGraw Hill, Aug., 2008. 3. R.D. Klafter, TA Chmielewski and Michael Negin, "Robotic Engineering, An Integrated approach", Prentice Hall of India, 2003. 4. Millee Jorge, “Orthotics and Prosthetics in Rehabilitation”, third edition, Saunders Elsevier publishing, Missouri, 2013 5. Chinnathurai R, Sekar P, Kumar M Ramaa, Manoj K Nithya, Kumar C Senthil, “Short Textbook of Prosthetics and Orthotics”, Jaypee Digital publishing, 2010. 6. Michelle Lusardi, Millee Jorge, Caroline Nielsen, “Orthotics and Prosthetics in Rehabilitation”, Third edition, Elsevier, Saunders publishing,2012.
Credits: 3:0:0 14E3057 INDUSTRIAL ELECTRONICS AND INSTRUMENTATION
Course Objective
• To understand the concepts of Conventional and Digital Transducers • To study the concepts of Industrial heating, Photoelectric devices and Smart Transducers • To study the Microprocessor based instrumentation
Course Outcome
• Select the type of transducer for the Industrial application. • And apply in case studies and mini projects in industries. • Design the Microprocessor based Controllers.
Review of variable resistance, inductance capacitanceand piezoelectric transducers - Direct digital transducers, Absolute and incremental displacement transducers, Moiré Fringe transducers, Force and Pressure measurement, IC sensors - Dielectric heating, Photoelectric devices and PLC - Detection of zero crossing of an alternating waveform, Microprocessor based: triggering of a Thyristor, Voltmeter and Ammeter, Speed monitoring Unit, phase difference and power factor monitoring Unit, over and under voltage protection and over current protection - Smart transducer, Measurement of flow, pH with smart transducers.
References
1. Biswas S.N, “Industrial Electronics”, Dhanpat Rai & Company Private Ltd., New Delhi, 2nd Edition, 2008.
2. Murty.D.V.S., “Transducers and Instrumentation”, PHI Learning, New Delhi, 2nd Edition, 2009. 3. Paul Biswanath., “Industrial Electronics & Control: Including Programmable Logic Controller”, PHI
Learning, New Delhi, 2nd Edition, 2009. 4. Doebelin E.O, “Measurement Systems, Application and Design”, Mc-Graw Hill Publishing Company Ltd.,
New Delhi, 5th Edition, 2002. 5. Webb, John W.Reis, Ronald A., “Programmable Logic Controllers Principles and Application”, PHI
Learning, 5th Edition, 2009. 6. Ram. B., “Fundamentals of Microprocessors & Microcontrollers”, Dhanpat Rai (P) Ltd., New Delhi 2008.
Credits: 3:0:0 14EI3058 LINEAR SYSTEMS
Course Objective:
To understand the state model of LTI (Linear time invariant) system. To give basic knowledge in obtaining decomposition of transfer function from state model. To understand the concepts of Controllability and Observability To provide adequate knowledge in the Lyapunov stability analysis.
Course Outcome:
Very good knowledge in the basic concepts of linear control theory and design of control system. Gained the knowledge about the controllability & Observability. Solve the stability analysis problems.
State model for linear time invariant systems: State space representation using physical - Phase and canonical variables - Solution of state equation - State transition matrix - Transfer function from state model - Transfer matrix - Decomposition Methods – State space representation of linear time invariant discrete time systems - Solution of discrete time state equation. - Discretization of continuous time state equations - Eigen Values and Eigen Vectors –diagonalization - Concepts of Controllability and Observability - State Estimators - Lyapunov Stability Analysis of linear time invariant system.
References
1. Katsuhiko Ogata, “Modern Control Engineering”, Prentice Hall of India Private Limited, New Delhi, 4th Edition, 2002. 2. Nagrath I.J, & Gopal M, “Control System Engineering”, New Age International Publishers Limited, New Delhi, 5th Edition, 2007 3. Nise S. Norman, “Control Systems Engineering”, John Wiley & Sons Inc, New Delhi, 3rd Edition, 2000. 4. John J. D'Azzo, Constantine H. Houpis, “Linear Control System Analysis and Design”, CRC Press, USA , 5th Edition,2003 5. Shankar P. Bhattacharyya, Aniruddha Datta, Lee H. Keel, “Linear Control Theory: Structure, Robustness And Optimization” CRC Press, USA , 2009
Credits: 3:0:0 14EI3059 TRANSDUCERS AND ACTUATORS
Course Objective
• To understand different sensor systems used for process parameters. • To understand signal conversion and conditioning. • To understand sensor signal transmission.
Course Outcome
• Selection of sensor based on process parameter and application. • Interconnection of sensors with Controller. • Prevent data loss or noise during sensor signal transmission.
Electrical Transducers: Variable resistance type – Potentiometers, strain gauges, RTD, thermistors-Variable inductance type – self and mutual inductance, pulse transducer-Variable capacitance transducers-Special Transducers: Semiconductor temperature sensors, thermo-electric sensors, piezoelectric sensors, smart sensorsElectromechanical Transducers: Electrodynamic, eddy current, force balance transducers. Basics of MEMS devicesOther Transducers: Limit Switches, Proximity Switches, Pressure, Temperature, Level, Flow, Speed-Power System Transducers: Analogue and digital transducers for measurement of voltage, current, power factor, frequency, power – active and reactive. RTU for tariff calculation-Analogue Signal Conditioning techniques: Bridge amplifier, carrier amplifiers, charge amplifiers and impedance converters, modulation - demodulation, dynamic compensation, linearization, multiplexing and demultiplexing-Signal Transmission: Transmitters, V-I, I-V and V-f converters. Single transmission. Cable transmission of analog and digital signal, fiber optic signal transmission, radio, telemetry, pneumatic transmission-Actuators: Solenoid Valves, Pneumatic Control Valves, Piston-Cylinder, Motors, Contactors.
Reference Books
1. Doeblin, E.O. – Measurement Systems: Application and Design, Mc Graw Hill International, 2002 2. Patranabis, D – Sensors and Transducers, Wheeler Pub., New Delhi, 2003. 3. Murthy, D.V.S., Transducers and Instrumentation, PHI, New Delhi, 2008. 4. Newbert, H. K. – Instrument Transducers, Oxford University Press, 1999.
Credits: 3:0:0 14EI3060 AUTOMATED TEST AND MEASUREMENT
Course Objective
• To understand the difference between classical measurement and microprocessor based measurement. • To understand Real Time signals. • To understand standard IEEE buses used for smart measurement.
Course Outcome
• Differentiate industrial instrumentation buses. • Sensors and transducers with smart data transfer. • Process, analyze and log the sensor values
Measurement automation, Comparison with classical measurement and microprocessor based measurement, Measured data base and data base management, Real time signals, Calculated signals-Digital signal processing, Processed signals, Data flow and graphical programming techniques, Virtual instrumentation (VI), Advantages, VIs and Sub Vis-Data acquisition methods, DAQ hardware, Instrumentation buses, IEEE 488.1 and IEEE 488.2, Serial interfacing-RS 232C, RS 422, RS 423, RS 485, CAMAC, VXI, SCXI, PXI -Industrial drives and interface, Sensors and transducers, Interfacing signal conditioning, Signal-analysis techniques, Networking methods and their applications in instrumentation.
References
1. N. Mathivanan, PC-based Instrumentation-Concepts and Practice, Prentice-Hall, 2007. 2. M, Chidambaram, Computer Control of Processes, CRC Press, 2002 3. B. G. Liptak, Instrumentation Engineers Handbook, Philadelphia: Chilton Book Company, 4th Edition, 2003.
Credits: 3:0:0 14EI3061 REMOTE SENSING AND CONTROL
Course Objective
• To understand methods for remote sensing. • To understand remote control techniques and its application in Industry
Course Outcome
• Classify characteristics of objects. • Ground data acquisition. • Importance of remote control in Industry.
Electromagnetic radiation: Classification and nature, spectral, spatial and temporal characteristics of objectsAtmospheric interaction sensors: Photographic, thermal, multi-spectral, passive microwave and active microwave sensors- Ground data acquisition: Photo-interpretation, image processing techniques, remote sensing applicationsTechniques of remote control: Remote control in industry including oil pipelines, rocket motion and satellite movements.
References
1. Gupta - Remote Sensing Ecology, 2nd edition, Springer, 2005 2. Jensen - Remote Sensing of the Environment, Pearson, 2003 3. Barett, E.C. and Curtis, L.F. Introduction To Environmental Remote Sensing, 3/e, Chapman Hall, New York 1992. 4. Lo, C.P. Applied Remote Sensing, Wiley, New York 1986.
Credits: 3:0:0 14EI3063 ROBOT PROGRAMMING
Course Objective
• To understand the basics of Robot programming • To understand the VAL language applications • To understand the RAPID language applications • To understand the Practical study of virtual robot software • To understand the VAL-II and AML language
Course Outcome
Select proper safety interlock needed for robot action Program the robot for various application specific movements Developing robot programs in different software packages / languages
Robot programming-Introduction-Types- Flex Pendant- Lead through programming, Coordinate systems of Robot, Robot controller- major components, functions-Wrist Mechanism-Interpolation-Interlock commands-Operating mode of robot, Jogging-Types, Robot specifications- Motion commands, end effectors and sensors commandsRobot Languages-Classifications, Structures- VAL language commands motion control, hand control, program control, pick and place applications, palletizing applications using VAL, Robot welding application using VAL program-WAIT, SIGNAL and DELAY command for communications using simple applications-RAPID language basic commands- Motion Instructions-Pick and place operation using Industrial robot- manual mode, automatic mode, subroutine command based programming. Movemaster command language- Introduction, syntax, simple problems-Robot cycle time analysis-Multiple robot and machine Interference-Process chart-Simple problemsVirtual robotics, Robot studio online software-Introduction, Jogging, components, work planning, program modules, input 13 RB-2013 SRM and output signals-Singularities-Collision detection-Repeatability measurement of robotRobot economics-VAL-II programming-basic commands, applications- Simple problem using conditional statements-Simple pick and place applications-Production rate calculations using robot. AML Language-General description, elements and functions, Statements, constants and variables-Program control statements-Operating systems, Motion, Sensor commands-Data processing.
References
1. Deb. S. R. “Robotics technology and flexible automation”, Tata McGraw Hill publishing company limited, 1994 2. Mikell. P. Groover, “Industrial Robotics Technology”, Programming and Applications, McGraw Hill Co, 1995.
3. Klafter. R.D, Chmielewski.T.A. and Noggin’s., “Robot Engineering : An Integrated Approach”, Prentice
Hall of India Pvt. Ltd.,1994. 4. Fu. K. S., Gonzalez. R. C. & Lee C.S.G., “Robotics control, sensing, vision and intelligence”, McGraw Hill
Book co, 1987 5. Craig. J. J. “Introduction to Robotics mechanics and control”, Addison-Wesley, 1999. 6. Robotcs Lab manual, 2007. 7. www.wpi.edu
Credits: 3:0:0 14EI3064 KINEMATICS AND DYNAMICS OF ROBOT
Course Objective
• To control both the position and orientation of the tool in the three dimensional space. • The relationship between the joint variables and the position and the orientation of the tool. • Planning trajectories for the tool to follow on order to perform meaningful tasks. • To precisely control the high speed motion of the system
Course Outcome
• To control both the position and orientation of the tool in the three dimensional space. • The relationship between the joint variables and the position and the orientation of the tool. • Planning trajectories for the tool to follow on order to perform meaningful tasks. • To precisely control the high speed motion of the system
Introduction, position and orientation of objects, objects coordinate frame Rotation matrix, Euler angles Roll, pitch and yaw angles coordinate Transformations, Joint variables and position of end effector, Dot and cross products, coordinate frames, Rotations, Homogeneous coordinates. Direct Kinematics-Link coordinates D-H Representation, The ARM equation. Direct kinematic analysis for Four axis, SCARA Robot and three, five and six axis Articulated Robots- The inverse kinematics problem, General properties of solutions. Tool configuration, Inverse kinematics of four axis SCARA robot and three and five axis, Articulated robot-Workspace Analysis, work envelope of a Four axis SCARA robot and five axis articulated robot workspace fixtures, the pick and place operations, Joint 11 RB-2013 SRM space technique - continuous path motion, Interpolated motion, straight line motion and Cartesian space technique in trajectory planning-Manipulator Dynamics-Lagrange's equation kinetic and potential energy-Link inertia Tensor, link Jacobian Manipulator inertia tensor. Gravity, Generalized forces, Lagrange-Euler Dynamic model, Dynamic model of a Two-axis planar robot, Newton Euler formulation, Lagrange - Euler formulation, problems.
References
1. Robert J. Schilling, Fundamentals of Robotics Analysis and Control, PHI Learning., 2009. 2. Richard D. Klafter, Thomas .A, Chri Elewski, Michael Negin, Robotics Engineering an Integrated Approach, Phi Learning., 2009. 3. P.A. Janaki Raman, Robotics and Image Processing An Introduction, Tata Mc Graw Hill Publishing company Ltd., 1995. 4. Francis N-Nagy Andras Siegler, Engineering foundation of Robotics, Prentice Hall Inc., 1987. 5. Bernard Hodges, Industrial Robotics, Second Edition, Jaico Publishing house, 1993. 6. Tsuneo Yohikwa, Foundations of Robotics Analysis and Control, MIT Press., 2003. 7. John J. Craig, Introduction to Robotics Mechanics and Control, Third Edition, Pearson, 2008. 8. Bijay K. Ghosh, Ning Xi, T.J. Tarn, Control in Robtics and Automation Sensor – Based integration, Academic Press, 1999.
14EI3065 ADVANCED INSTRUMENTATION AND PROCESS CONTROL FOR FOOD ENGINEERS
Credits: 3:0:0
Course Objective:
To introduce the concept of process instruments for various physical variables, system, automation. To gain knowledge of the different controllers To learn the complex control techniques used in process industries
Course Outcome:
Apply the knowledge of Measurement to various applications. Analyze the characteristics of Instrumentation systems. Design controllers for a typical application
Functional Elements of an Instrument, Performance Characteristics, Static and Dynamics CharacteristicsOpen loop and closed loop systems, Response of First Order and Second order system for Unit Step input, Response of Second Order system for Unit Step Input. Pressure measurement: Manometers, Elastic elements, McLeod gauge, Ionization gauge, Thermal Conductivity Gauge:Pirani Gauge, Thermocouple Gauge, Temperature Measurement: Expansion Thermometer, Filled System Thermometer, Pyrometers,Thermocouple, RTD, Thermistor, Level Measurement: Direct methods, Radiation Level Detector, Ultrasonic Level Detector, Flow Measurement: Turbine flowmeter, Rotameter, Electromagnetic flowmeter, Ultrasonic flowmeter, Measurement of pH , Viscosity, Process Automation: Process Variables– Degrees of Freedom, Control Modes: P– PI–PID – Final Control element, Actuators, Control Valve characteristics, Control Valve types, Complex Control Techniques: Cascade control, Ratio control, Feed forward control, Split Range Control, Inferential Control, Case studies: Distillation column, Chemical reactor, Heat exchanger, Condenser, Evaporator
References
1. Singh. S. K., “Industrial Instrumentation and Control”,2nd Edition, Tata McGraw– Hill,New Delhi, 2004. 2. Curtis Johnson, D., “Process Control Instrumentation Technology”, Prentice Hall of India,2006. 3. Coughanowr, and Koppel,“ Process systems analysis and control” , Tata McGraw– Hill,New Delhi,2004. 4. Seborg. D. E., Edger. T. F, and Millichamp. D. A, “Process Dynamics and Control”,JohnWiley and Sons, Newyork,2004. 5. Roffle. B., Betlem. B. H. L., “Advanced Practical Control”, Springer, Newyork,2004. 6. Stephanopoulos, “Chemical Process Control”, 2nd Edition, Prentice Hall, NewDelhi,
Credits: 0:0:2 14EI3066 SENSORS AND DATA ACQUISITION LAB
Course Objective:
To learn the characteristics of sensors. To introduce the concept of data acquisition. To deal with experiments in data acquisition and analysis
Course Outcome:
Determine the characteristics of sensors. Acquire real time data for analysis Analyze acquired signals.
Credits: 3:0:0 14EI3067 TRANSDUCER ENGINEERING
Objective:
To elaborate on basic and advanced concepts of nanosensors and transducers for nanotechnology applications. To teach various transducers effects for the best understanding of various nanotransducers. To elaborate on the various types of nanosensors and actuators.
Outcome:
The students should be able to understand basic and advanced concepts of nanoelectronic devices The students should be able to understand basic and advanced concepts of sensors The students should be able to understand basic and advanced concepts of actuators
Course Description:
Transducers - capacitive transducers -Acoustic wave transducers -MOS capacitor based transducers – FET based transducers – Cantilever based transducers - Sensor Characteristics and Physical effects - Static characteristics Dynamic characteristic - Photoelectric effect – photodielectric effect – Photoluminescence effect –electroluminescence effect – chemiluminescence effect –Doppler effect – Barkhausen effect – Hal effect –Nano based Inorganic sensors - Organic /Biosensors - Signal conditioning and data acquisition - Phase locked loop.
References
1. Nanoelectronics and Nanosystems: From transistors to Molecular and Quantum Devices by K. Goser (Edition, 2004), Springer. London. 2. Nanotechnology enabled sensors by Kouroush Kalantar – Zadeh, Benjamin Fry, Springer Verlag New York, (2007). 3. Sensors and signal conditioning, Ramon Pallas-Areny, John G. Webster John,2nd edition, Wiley & Sons (2001). 4. S.Renganathan “Transducer Engineering” – Allied publishers Limited, 1999. 5. Ernest O. Doeblin “Measurement Systems – Application & Design” McGraw – Hill Publishing company, 1990. 6. Biosensing: International Research and Development, Jerome Schultz, Milar Mrksich, Sangeeta N. Bhatia, David J. Brady, Antionio J. Ricco, David R. Walt, Charles L. Wilkins, Springer 2006 7. H.Rosemary Taylor, Chapman and Hall, “Data acquisition for sensor systems”, London, 2007