
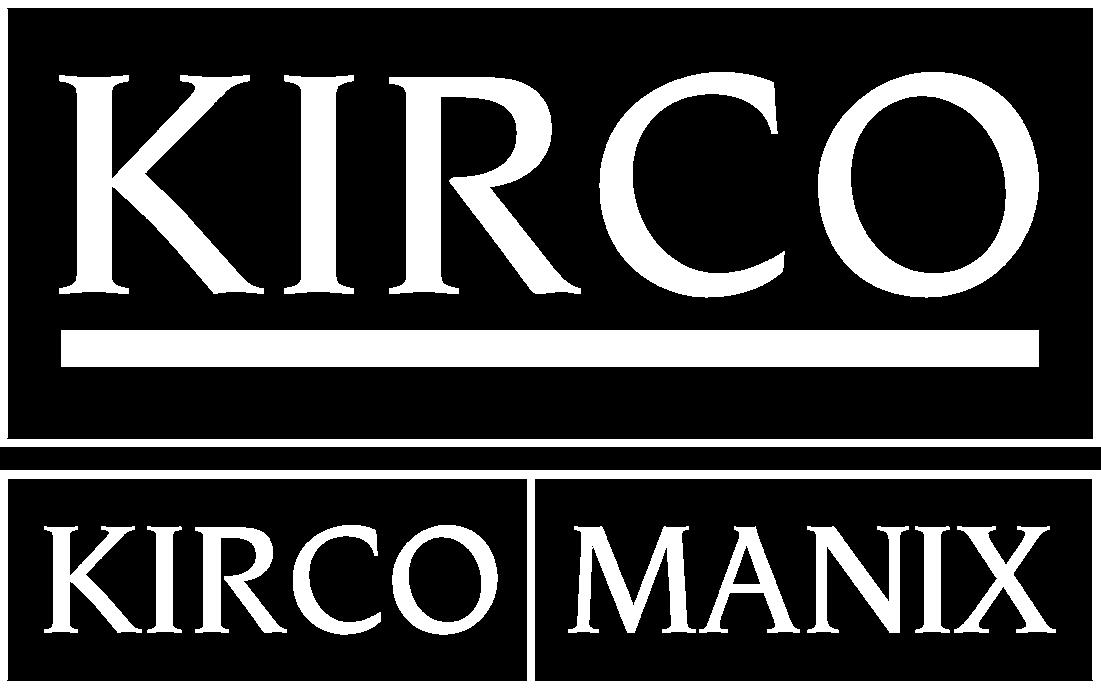
THANKS FOR VISITING US A.J. WASHELESKI CORPORATE REAL AJWasheleski@kircomanix.comESTATE HUNTER CONLEY BUSINESS HConley@kircomanix.comDEVELOPMENT ADAM MANIX DIR., CORPORATE REAL AManix@kircomanix.comESTATE QUINN KIRILUK EVP, CORPORATE REAL Quinn@kirco.comESTATE BRYAN MISCOVICH BUSINESS OPERATIONS BryanMiscovich@kirco.comANALYST JESSICA SKINNER TAX INCENTIVE JessicaSkinner@kirco.comSPECIALIST TELL US WHAT YOU’RE WORKING ON: 248.680.7180

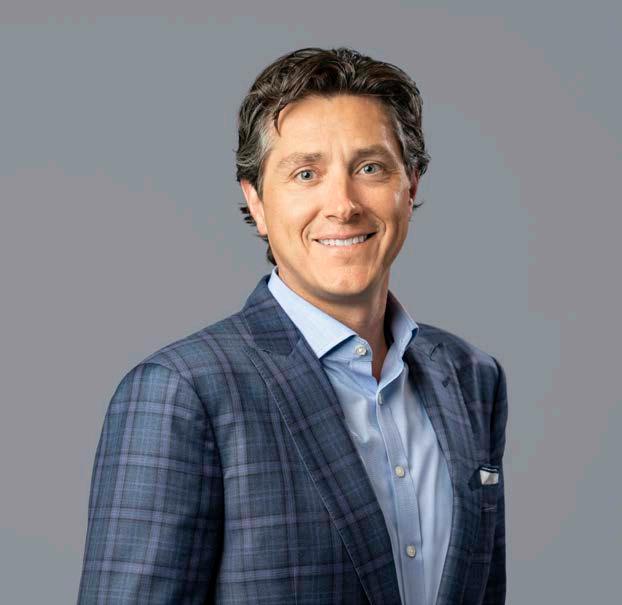

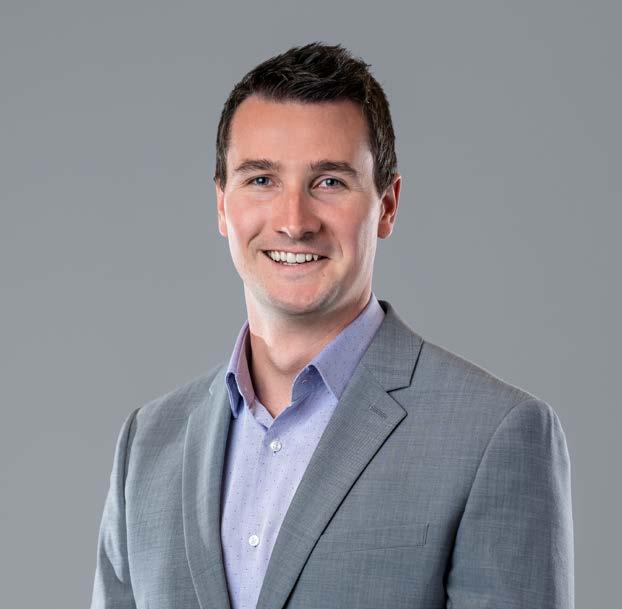
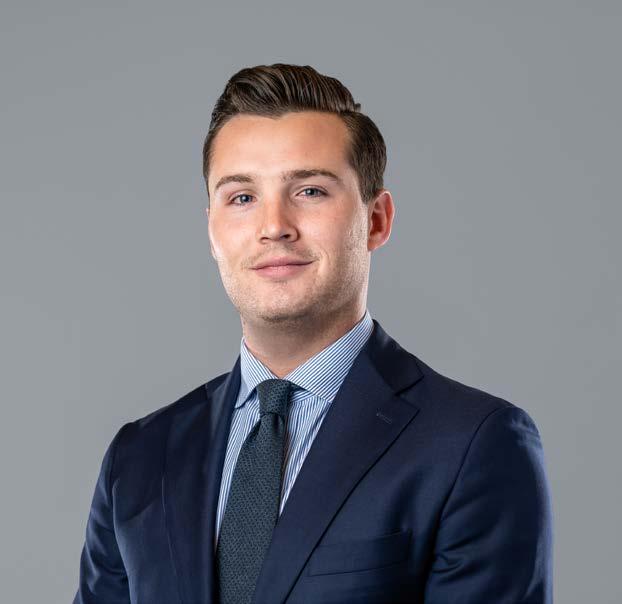
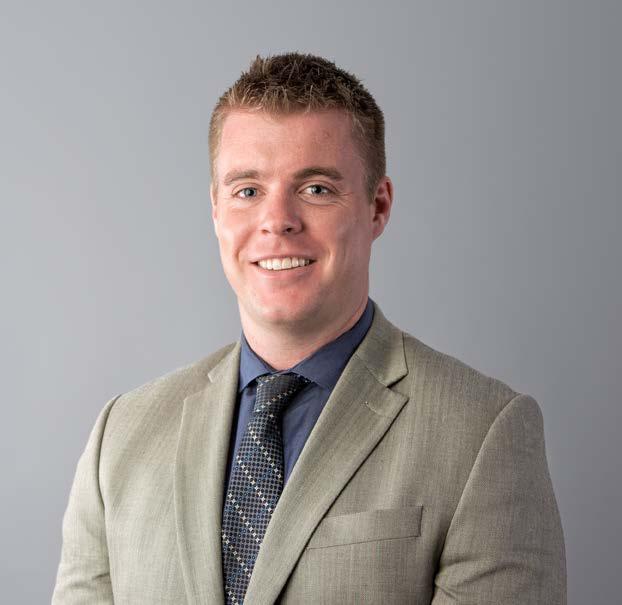
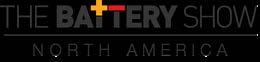
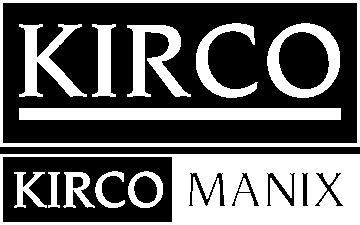
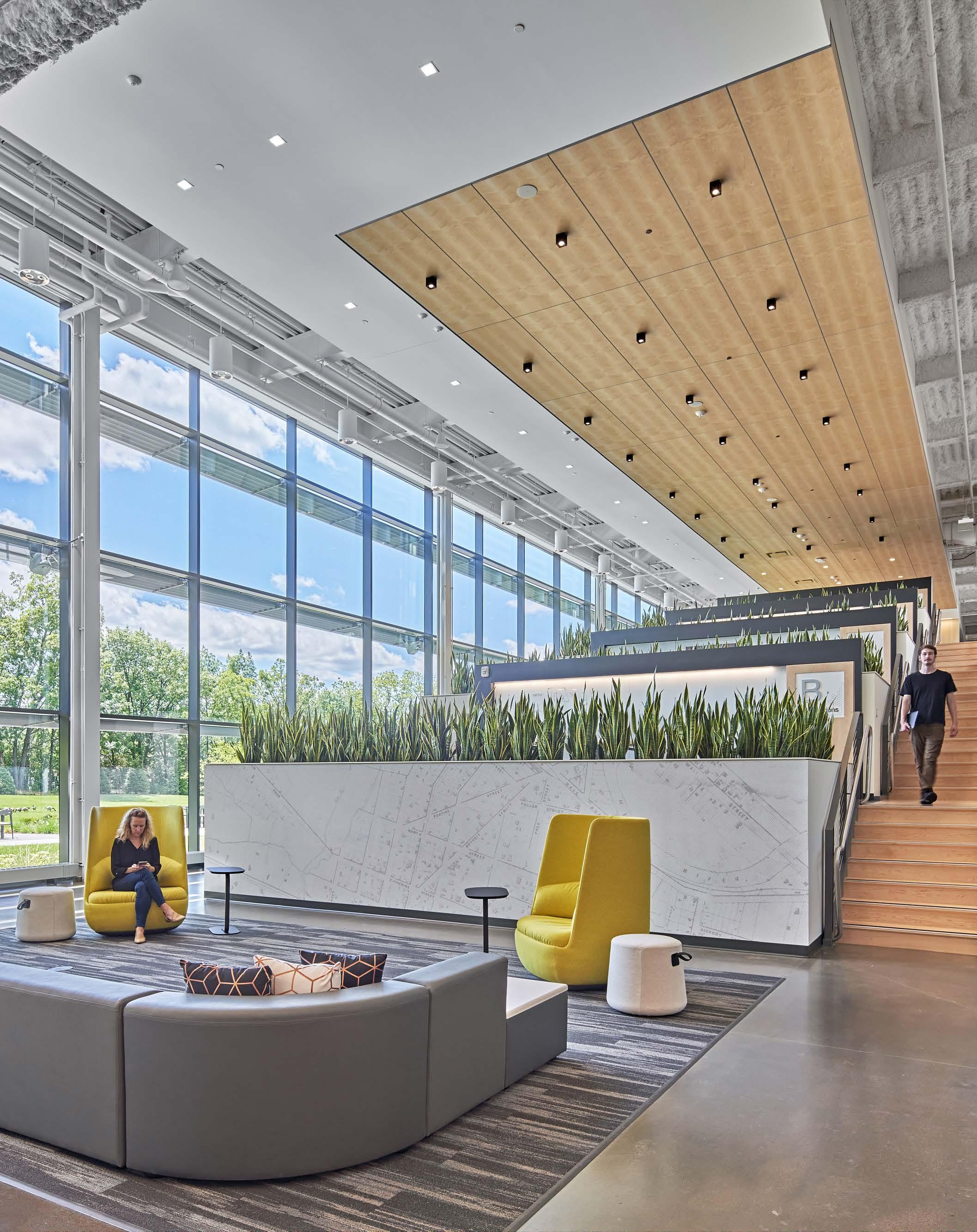
MARKETS SERVED Corporate Office & Headquarters • Advanced Manufacturing • Warehouse/Distribution Heavy Industrial • Healthcare & Senior Living • Retail • Lab/R&D NATIONAL REACH. WORLD-CLASS FACILITIES. We are experts in corporate real estate development, construction, and facility management. Privately held and well-capitalized, our award-winning approach focuses on Bringing Out The Best in every project. 47 MILLION SF DEVELOPED, BUILT & ACQUIRED FAMILYGENERATIONOWNED&OPERATED YEARS OF REALSUCCESSESTATE 36 Headquartered3rdin Detroit, MI Birmingham, AL • West Palm Beach, FL • Columbus, OH
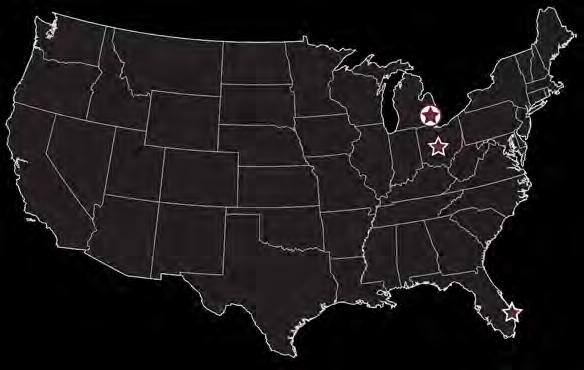
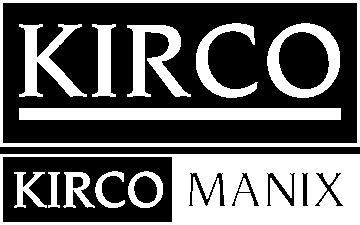
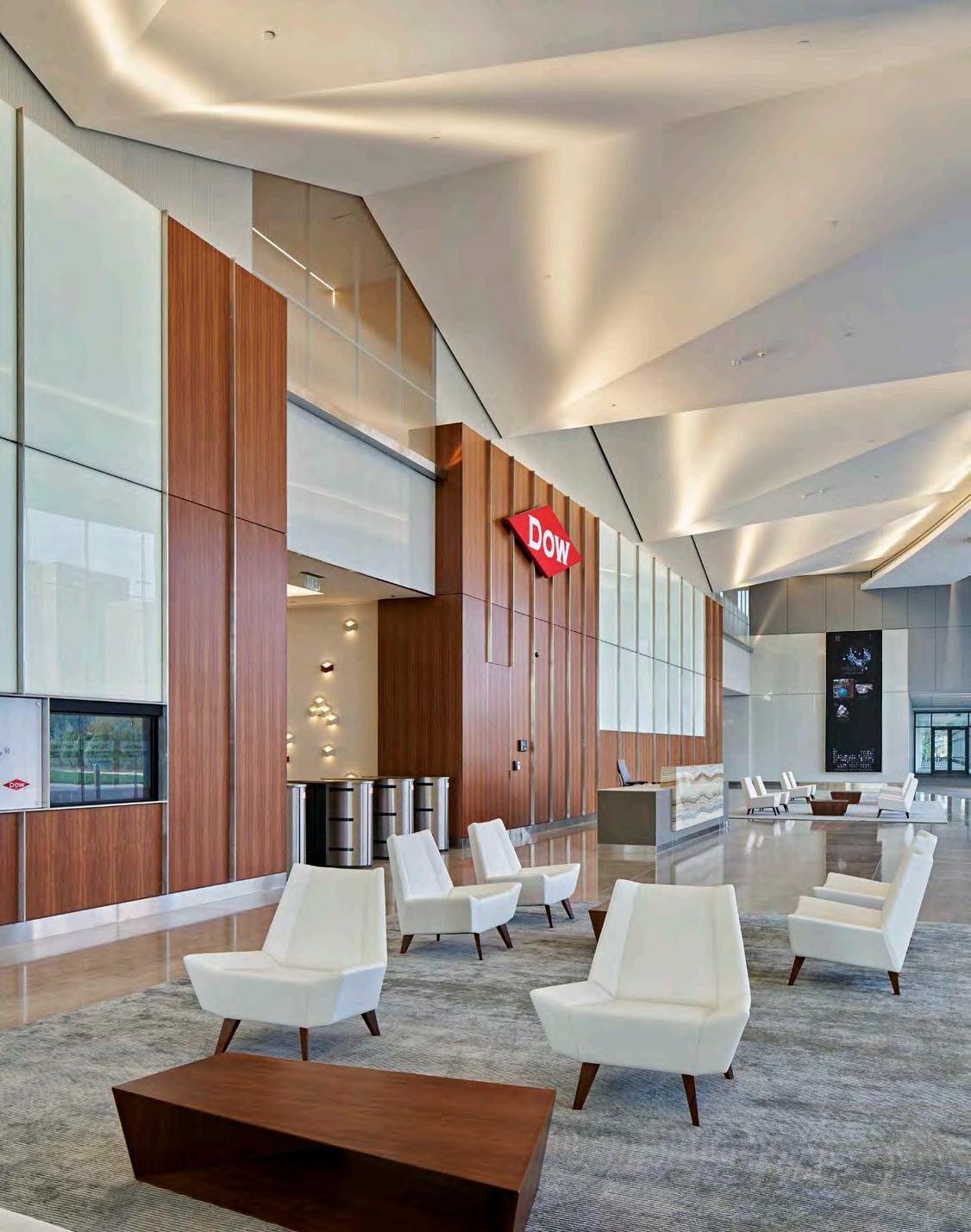
BUILD
KIRCO MANIX leverages over 100 years of experience and $4 billion of successfully delivered projects across the country to provide the highest level of pre-construction, design-build, and construction management expertise. We uphold an all-encompassing culture of safety, and are committed to delivering projects within budget and on schedule.
MANAGE
DEVELOP
Our comprehensive approach allows us to develop, build, and manage world-class facilities with the insight and mindset of a long-term owner. We are selective in the projects we choose, flexible to the delivery model, and focused on providing lasting value for our clients and their employees.
Our collaborative team of multi-disciplinary experts adds unmatched value to the project journey.
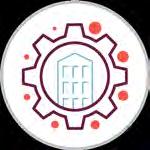
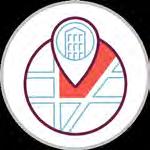
For nearly 50 years, we have planned and developed over 35 million square feet of real estate. From the simple to the complex, we utilize a transparent and detail-oriented discipline to exceed expectations and eliminate surprises. Every facility represents a business investing in its people, community, and future; that facility’s journey should be celebrated.
KIRCO Management is a nationally accredited industry leader in asset and facilities management. Having managed 25 million square feet over five decades, we ensure an outstanding environment for our occupiers and visitors. We provide a best-in-class experience with a strong reputation built on quality, integrity, service, and results.
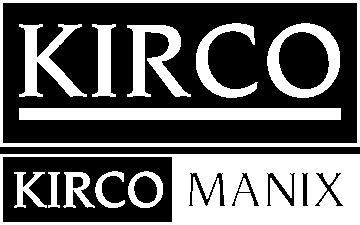
FUND
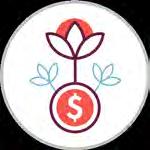
When desired, KIRCO offers extraordinary solutions to provide 100% of a project’s capital needs, including moving/relocation expenses, equipment and furniture, AV/IT/Security, cafeteria, fitness, and more.

INTEGRATEDFULL-SERVICE.APPROACH.
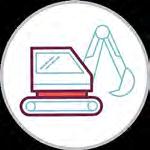
Jim Balzer, Cardinal Health
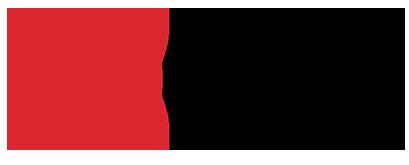
Peter Prychodko, Doeren Mayhew
Richard Plautz, Oerlikon
“KIRCO was at our side and partnered in the problem solving. Their insight in mitigating project impact was invaluable. With a project of this magnitude and complexity, they were instrumental in delivering against a very aggressive schedule, completed it on time, and under budget.”
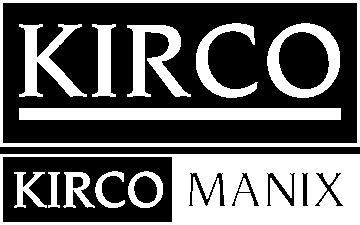
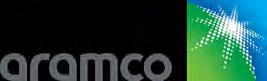
“KIRCO has worked very closely with us to value engineer any modifications that we made during the construction period and there have been several…they’ve done a great job of saying, ‘here’s an alternative. This is better than what you’ve got. This will provide a better cost benefit to you.”

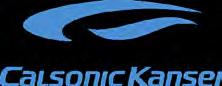
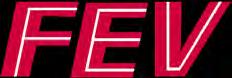
OUR CLIENTS

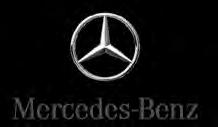
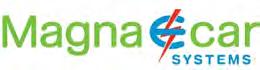
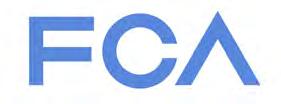


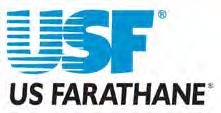

“KIRCO takes the attitude that this is their project that they are going to live with. They want it to come out perfect for you. You just don’t find that with everyone.”
“Part of the reason we selected KIRCO MANIX for this project was due to the fact each member of the management team is well qualified to cover their area of responsibility and each exhibited a high-level of confidence for managing cost, schedule, quality and safety on large, technically complicated projects.”
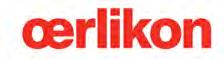
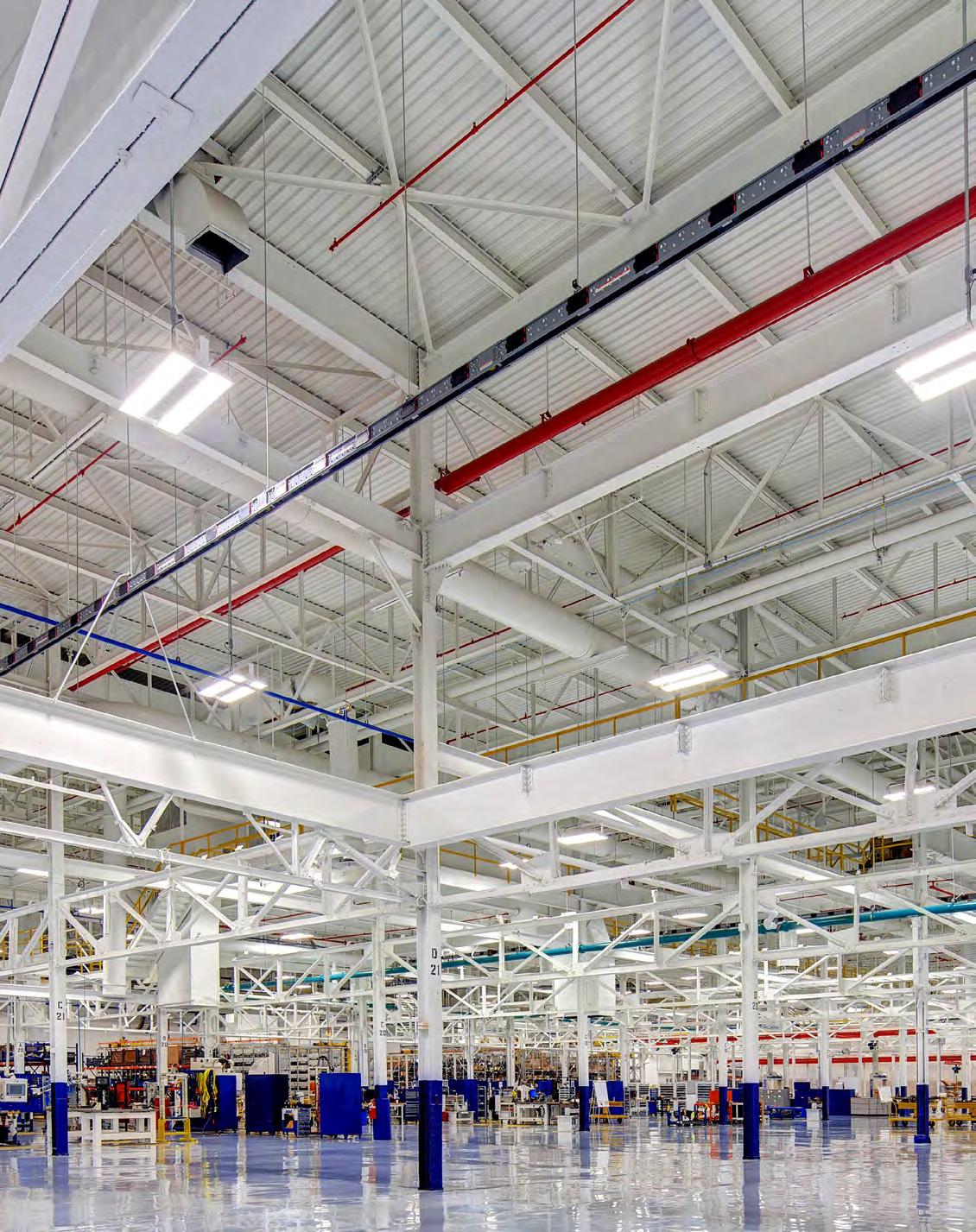
David T. Day, The Dow Chemical Company

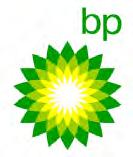

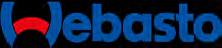

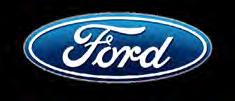
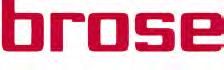
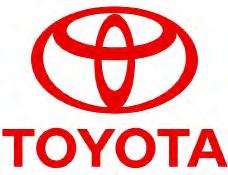

OERLIKON
KIRCO & KIRCO MANIX recently completed Oerlikon’s new state-of-the-art manufacturing facility dedicated to producing advanced materials for additive manufacturing and highend surface coatings. The new facility produces materials such as advanced titanium alloys and certain high-end thermal spray powders, which are packaged and shipped to automotive, aerospace, agricultural and medical customers worldwide. The site is fully equipped with next-generation Vacuum Induction melting with Gas Atomization (VIGA) technology, which is one of the most versatile methods for processing a variety of metals and alloys into powders. The facility also contains a high-tech research & development lab for further developments of titanium and other alloys (e.g. nickel, copper, iron and cobalt) and joint research & development projects with customers, and has the ability to produce customized powders in small batches. The facility houses approximately 70 employees and represents over $50 million of new investment into the community.
PROJECT TYPE
LOCATION PLYMOUTH TWP., MI
PROJECT SIZE 79,401 SF
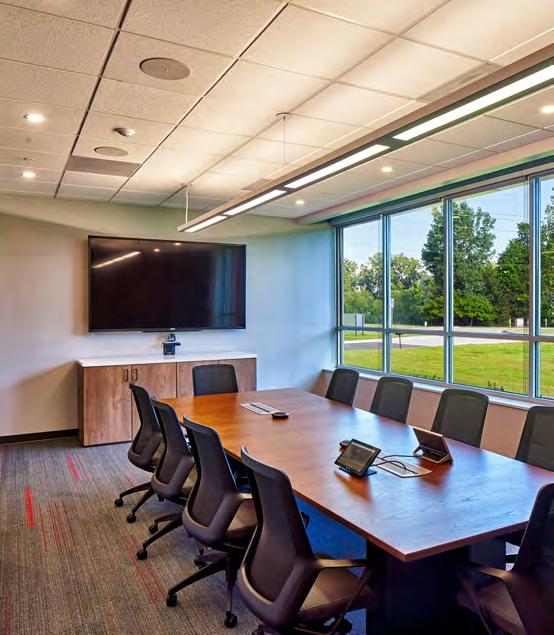
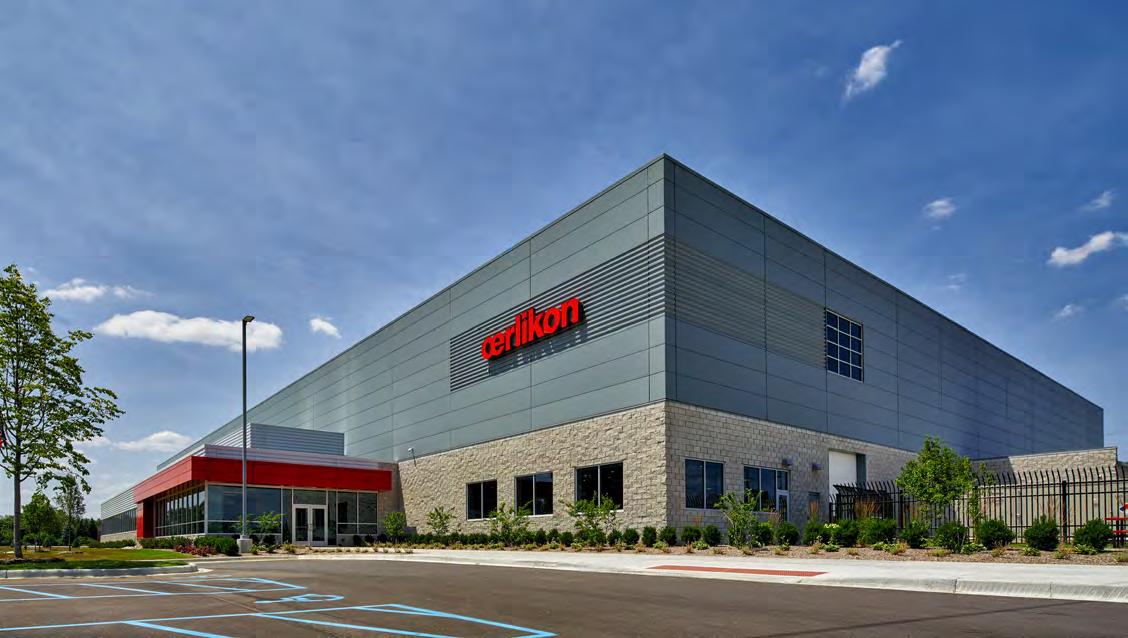
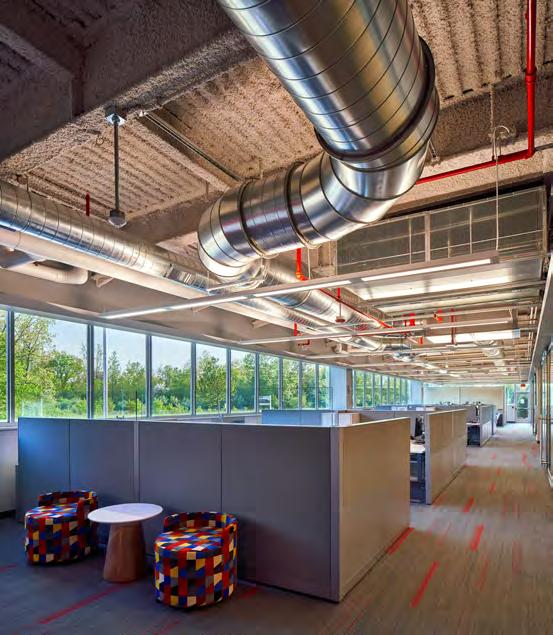


RESEARCHMANUFACTURING&DEVELOPMENT


“US Farathane selected KIRCO MANIX as the builder and partner for this extremely important expansion of our Westland operation based on their history of success in meeting critical timing deadlines, along with the impressive quality of work that has been displayed on prior completed building projects,” said Rodney Turton, Vice President of Purchasing, US Farathane.
US FARATHANE
LOCATION WESTLAND, MI
PROJECT TYPE MANUFACTURING
“We were pleased to partner with US Farathane for its Westland expansion project that was both complex and on a demanding timeline,” said Douglas W. Manix, president of KIRCO MANIX. “This expansion, as well as related site improvements, will help the company continue to meet the needs of its customers.”
KIRCO MANIX recently completed the construction of US Farathane’s 99,864 square foot manufacturing facility expansion in Westland, Michigan. The Auburn Hills, Michigan-based company is a leading manufacturer of plastics.
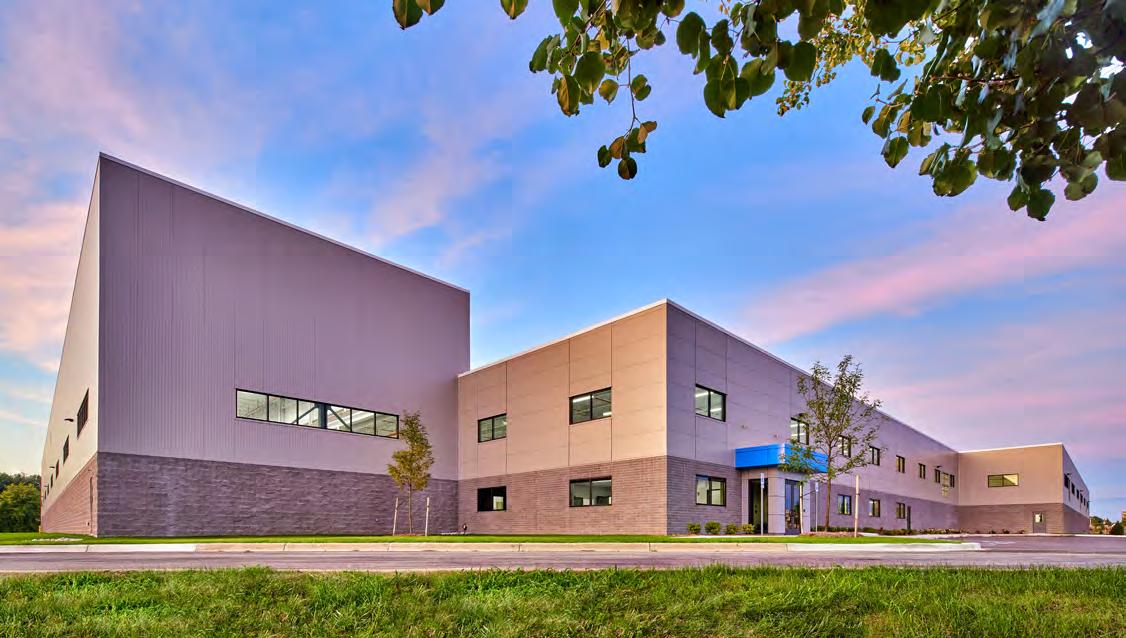

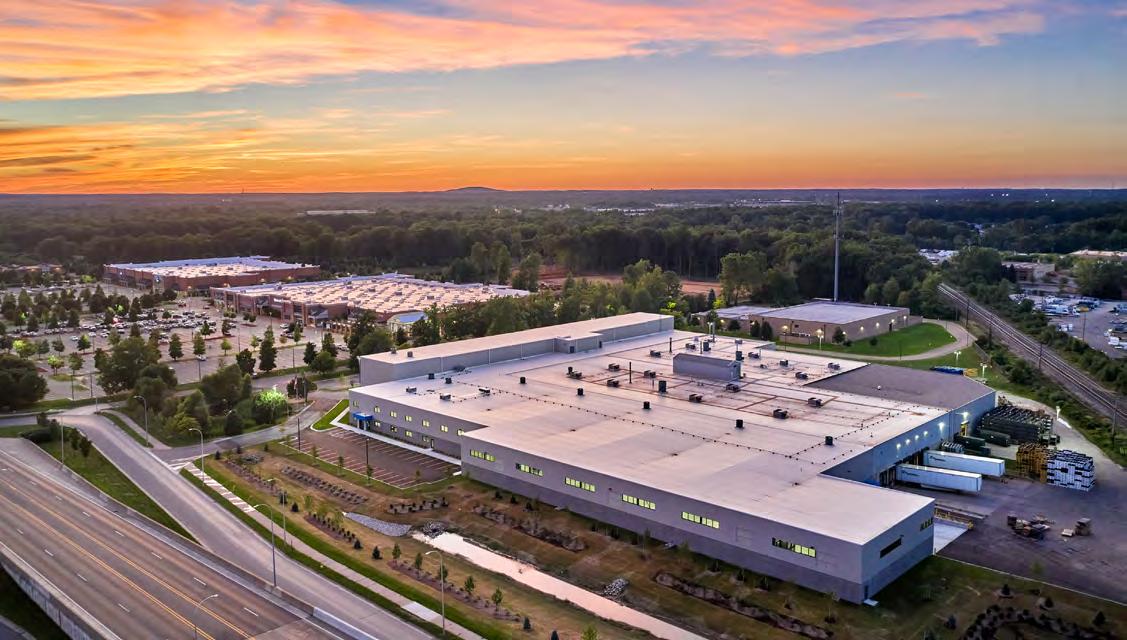
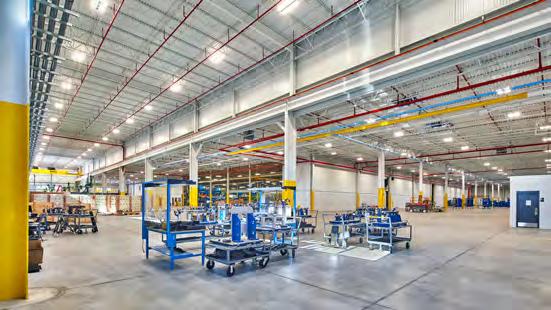
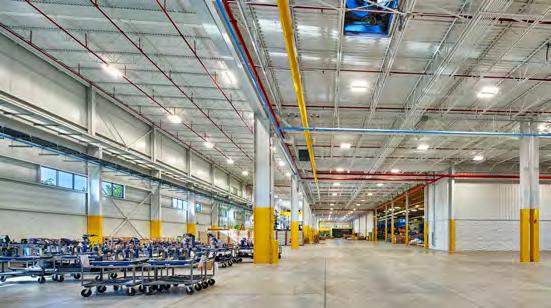
“KIRCO MANIX has done an excellent job on this project in every regard. They have been a great partner throughout and have put us in a position to execute successfully on our commitments to our customer by having this facility completed on time and on budget. We are extremely grateful to the KIRCO MANIX team.” Rodney Turton, Vice President of Purchasing, US Farathane.

PROJECT SIZE 99,864 SF
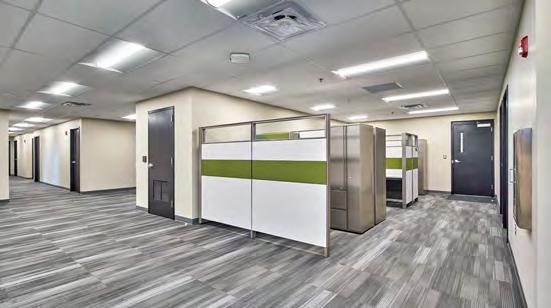

CHALLENGES:
AMERICAN AXLE MANUFACTURING
KIRCO MANIX will soon begin an additional project which will house American Axle’s recently purchased organization, formerly known as Metaldyne. The plant being renovated has been vacant for several years. The first phase of the project is 54,000 square feet of office renovation. Renovations will include complete removal and replacement of everything in the space; it will be a complete build-out with electrical, plumbing, mechanical, all-finishes and exterior improvements. Similar to Plant 3, the building was built in the 1920s so hazardous materials will have to be abated before demolition can commence.
The new office space offers an open work environment with designs to enhance natural light by using glass partitioned offices. One of the notable features of this facility includes the restoration of the original decorative pre-cast facade.
KIRCO MANIX provided assistance to the design team during this project in order to expedite design decisions and construction solutions.
The former manufacturing plant across from its global headquarters in Detroit houses several of American Axle’s departments: advanced manufacturing, advanced information technology, gear development, corporate manufacturing, next-generation prototype builds, warranty analysis and competitive assessment.
KIRCO MANIX completed 350,000 square feet of construction for American Axle Manufacturing at the company’s world headquarters in Detroit, Michigan. American Axle has converted one of its vacant former manufacturing facilities in Detroit into a $30 million Advanced Technology Development Center to help it design products for the
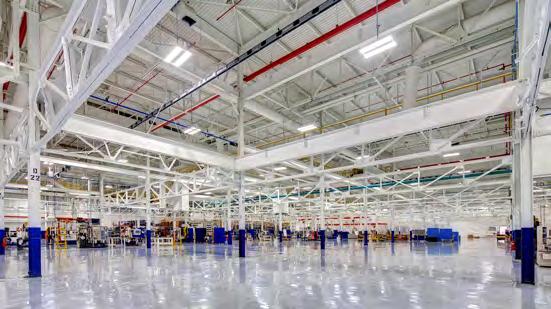
American Axle plans to move 300 administration employees into the new offices of “Plant 6” in 2018. DETROIT, MI
Another major challenge was coordination of construction phases while protecting AAM’s facility operations with phased area completion and occupancy.
Thefuture.scope
updated sat unused and unmaintained for nearly seven years prior to the start of this project.
This project presented many environmental challenges including asbestos and lead abatement.
TheManufacturing.spacebeing
LOCATION
PROJECT SIZE 350,000 SF PROJECT TYPE RESEARCHOFFICE & DEVELOPMENT

PLANT 6 PROJECT:
of this project was to convert 350,000 square feet of 80-year old finishes and furnishings to a state-of-the-art research and development facility for American Axle
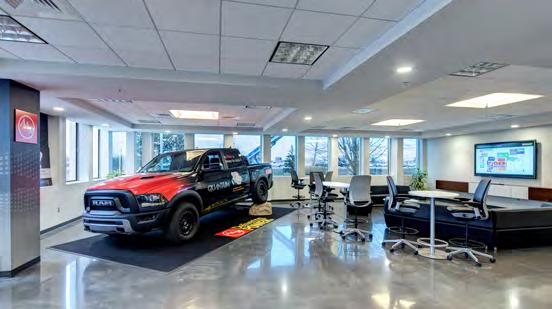
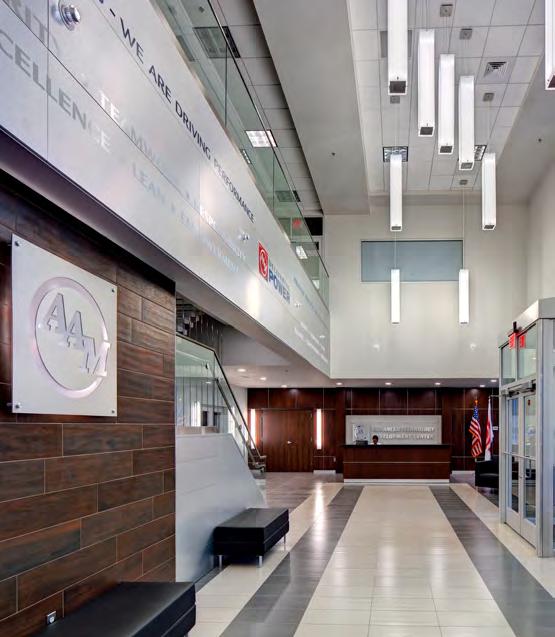

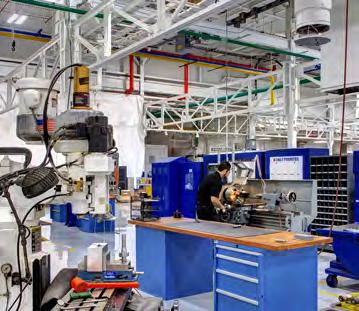
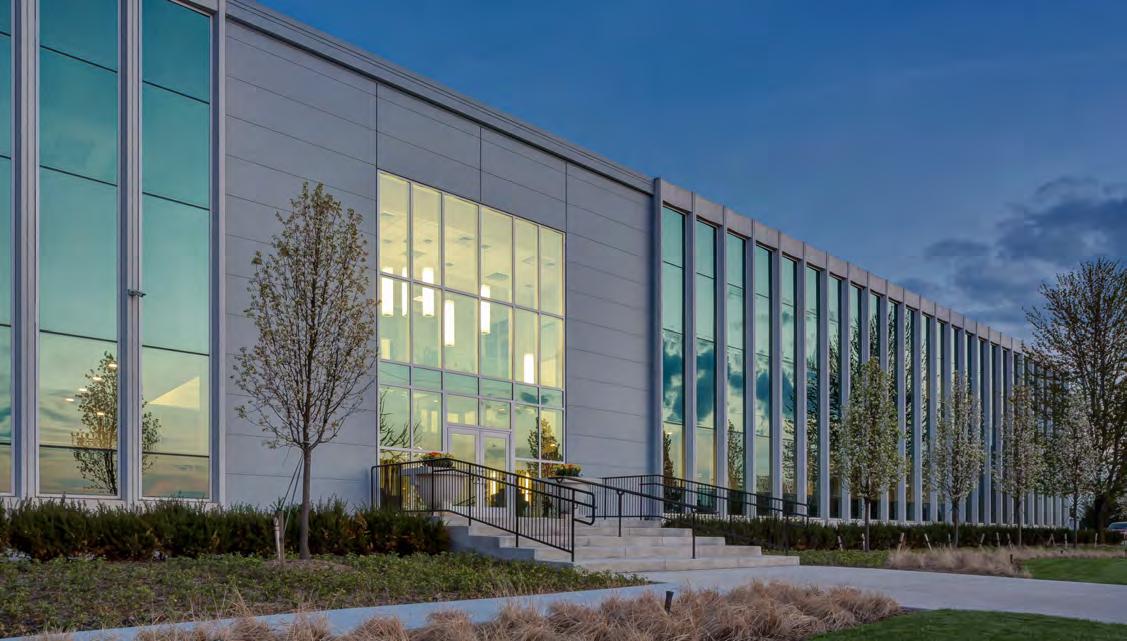
PROJECT SIZE 25,600 SF
RESEARCHINDUSTRIAL&
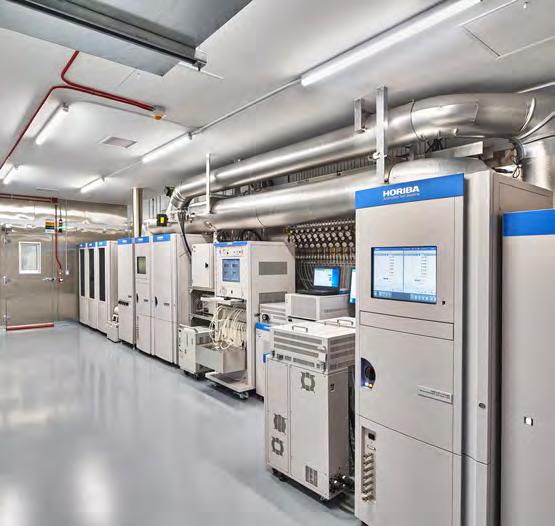

“Ascampus.aMichigan-based
FEV NORTH AMERICA
KIRCO MANIX has recently completed the construction of a new vehicle test center for FEV North America, expanding its campus in Auburn Hills, Mich. to three buildings. FEV is investing more than $27 million into the 25,600 square-foot facility, which FEV says will create approximately 250 additional jobs, for a total of 750 jobs at its Auburn Hills
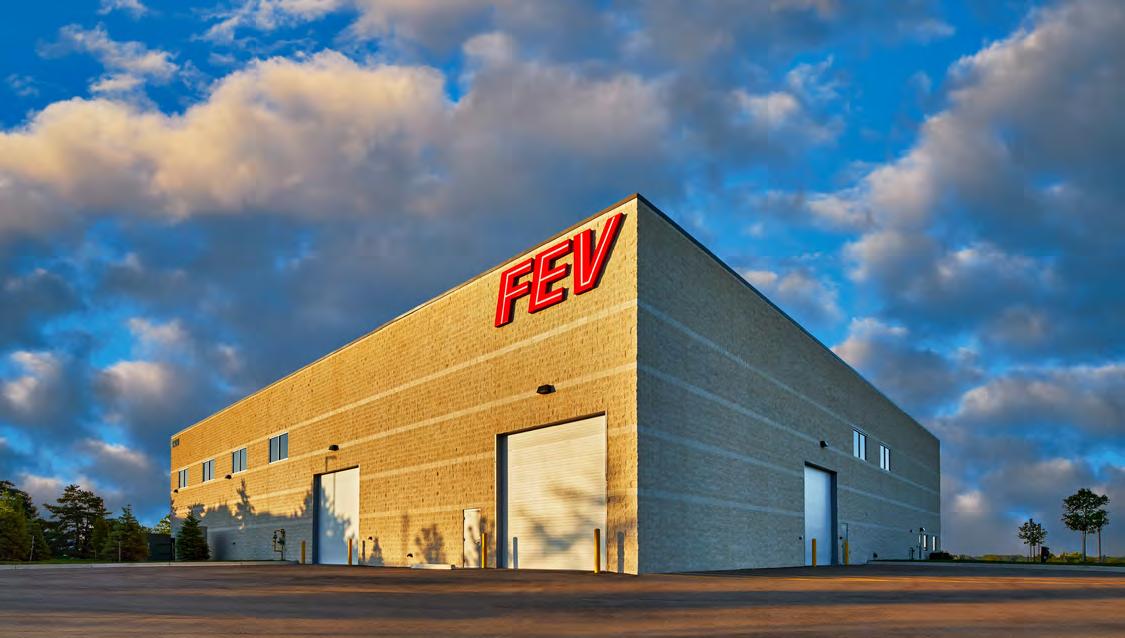
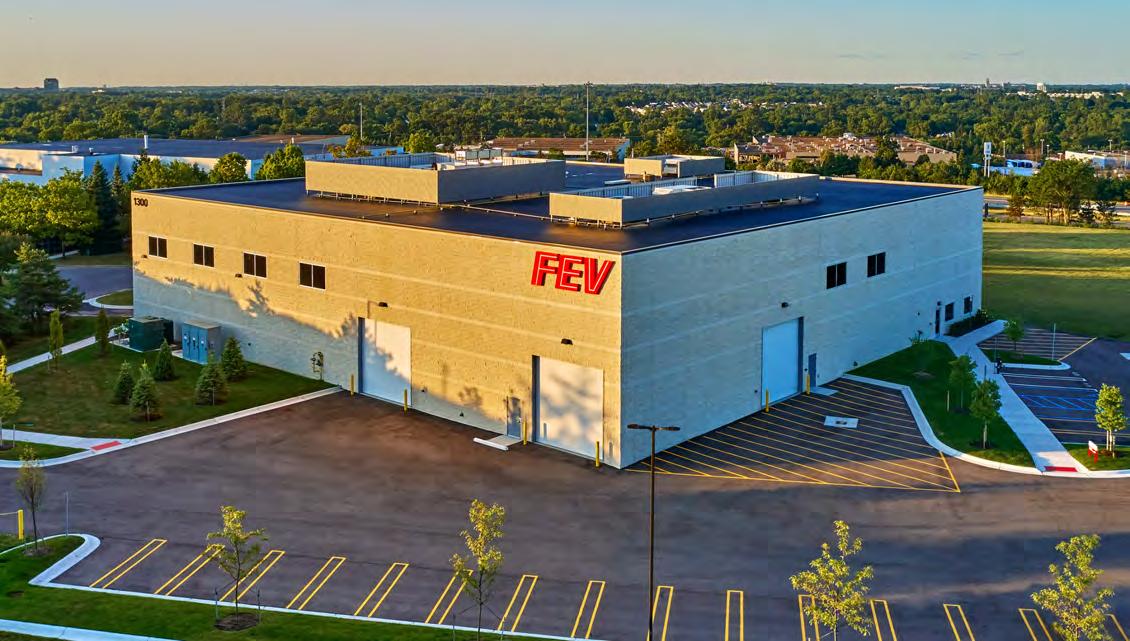
business, we are excited to team up with FEV on its new facility, as it expands its Auburn Hills campus and invests in the local community,” said Adam Manix, director – business development for KIRCO MANIX. “We pride ourselves on being a true partner with the ability to provide a unique, full-service approach through every phase of the project from design to construction.”
According to FEV, the new facility will strengthen FEV’s effort to provide a complete, onestop-shop for powertrain and vehicle development. The building houses a vehicle lab, state-of-the-art vehicle emissions dynamometer, office space and lab facilities.

PROJECT TYPE DEVELOPMENT
LOCATION AUBURN HILLS, MI
+ Closely coordinated and guided the design professionals to provide timely answers to questions and challenges
In addition to providing construction services, the R&D facility is also managed by KIRCO’s property management team.

“KIRCO MANIX successfully orchestrated the construction of the project, delivering the building temporary certificate of occupancy... almost 3 full months ahead of the industry norm.” Scott Ballew, Engineering Unit Supervisor, Aramco
CHALLENGES:
+ Constructing complex mechanical pipeline systems, electrical systems and state of the art automotive testing labs.



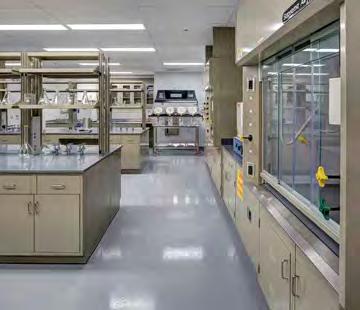
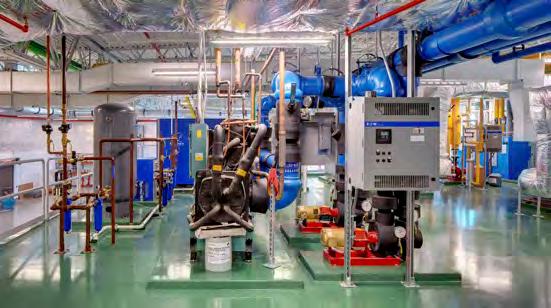
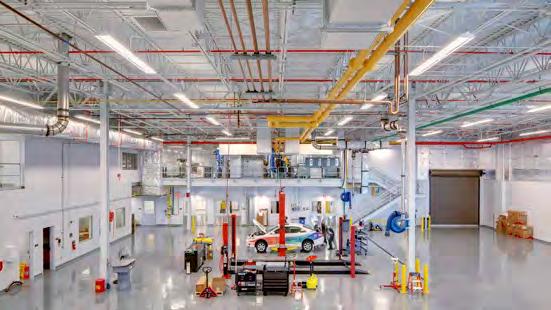
+ At the owner’s request, Phase 1 work had to be accomplished within a schedule reduced by a third.
+ Additionally, project phases could not impact daily operations at the facility.
+ Clearly communicated with the owner to manage expectations and plan ahead as necessary
+ Set up clear lines of responsibility among personnel to avoid confusion and frustration among various groups
+ Closely coordinated with sub contractors and suppliers to assure efficiency in installation without causing extra expense as best as possible due to overtime or weekend work
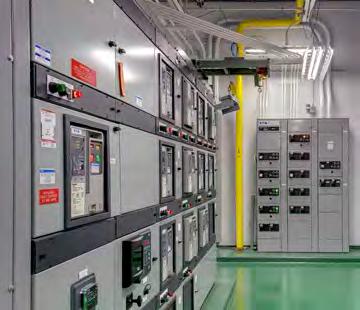
ARAMCO AMERICAS
+ Created and maintained a “can do, will do” attitude that permeated the project at all times
Aramco originally selected KIRCO MANIX to work with their program manager and architect to convert an existing industrial building shell into a state of the art research and development facility in Novi, Michigan. The facility is used to research the science required to lower carbon emissions of traditional fossil fuels.

PROJECT SOLUTIONS:
+ Utilizing Class A Architectural finishes in the office section while at the same time removing and replacing the exterior skin on approximately 33% of the building perimeter.
LOCATION NOVI, MI PROJECT SIZE 61,800 SF PROJECT TYPE RESEARCH & DEVELOPMENT OFFICE
Since the completion of the original project, KIRCO MANIX has managed the construction of numerous additional phases of work including tenant improvements, construction of advanced technical systems, and continuous updates of Aramco’s technical and dynamometer spaces.
+ Early onset expectations and communication lines with the city of Novi so as to keep them part of the process and avoid delays relating to inspections or code
KIRCO MANIX’s initial challenge was to value engineer in excess of $1 million from the project budget while not reducing the project quality. At the same time, they required completion of the work 90 days earlier than what was called for in the original project schedule. By creating a collaborative team approach amongst the owner, designers and subcontractors, KIRCO MANIX was able to achieve both goals and celebrated a successful completion of this $25 million project.
DSM
to allow for
The opening of the Troy Research & Technology Center strengthens DSM Engineering Plastics’ product development and application development capabilities in North America, and will enable it to collaborate more closely and efficiently with its customers.
part of the lab to application testing in partnership
addition,
been very responsive, friendly, helpful, and just great to work with... I

LOCATION TROY, MI PROJECT SIZE 31,550 SF PROJECT TYPE RESEARCH & DEVELOPMENT AWARDS Troy Chamber of Commerce’s Best of Troy Award VIDEO DSM Engineering Plastics Project Video

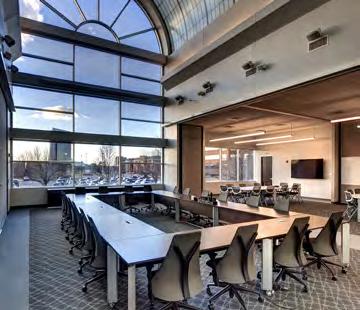
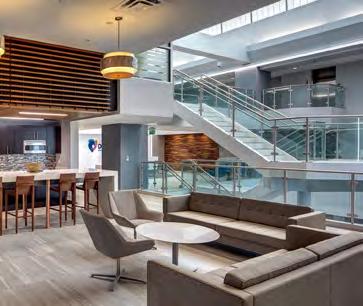
and
ENGINEERING PLASTICS
SOME OF THE NEW FACILITY’S FEATURES INCLUDE: + Broad range of mechanical testing capabilities + Analytical techniques including microscopy + Extensive testing capabilities on aging and chemical resistance of materials + Physical material testing, including rheology and thermal analysis + 3D printing capability to enable rapid prototyping
The has additional floor space available increasing capacity of its current testing activities, and for introducing further capabilities, including flammability testing secondary operations such as plastic welding.
DSM Engineering Plastics recently opened its expanded $5 million research and technology center in the Detroit suburb of Troy, Michigan.
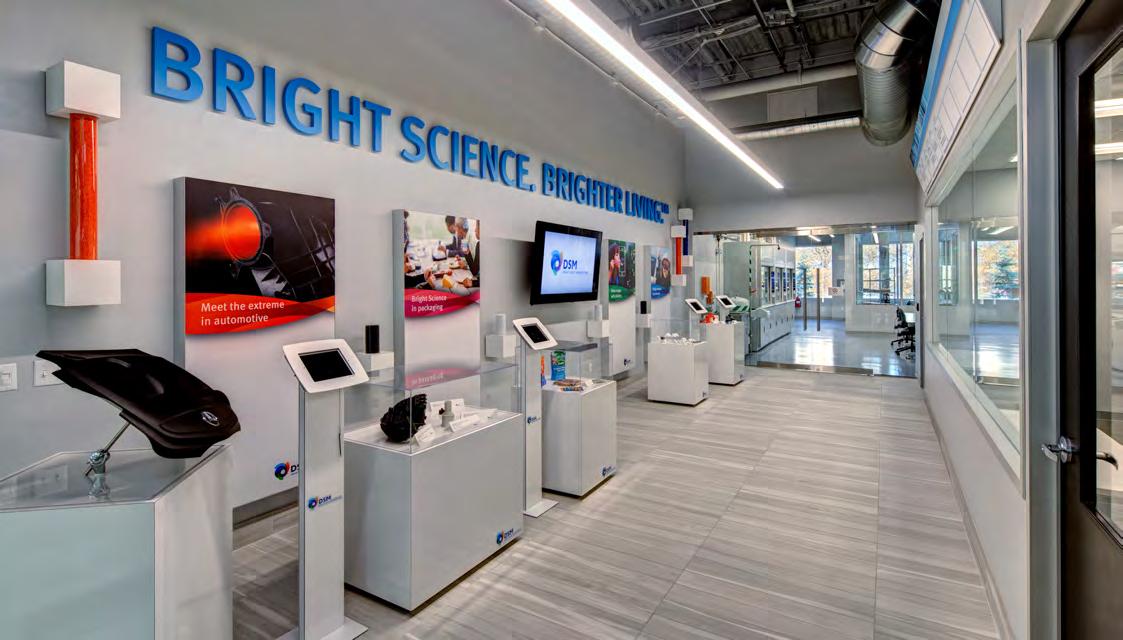
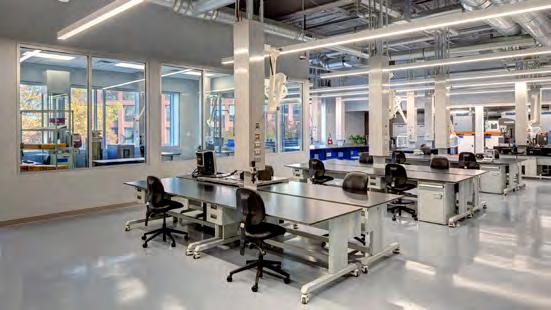
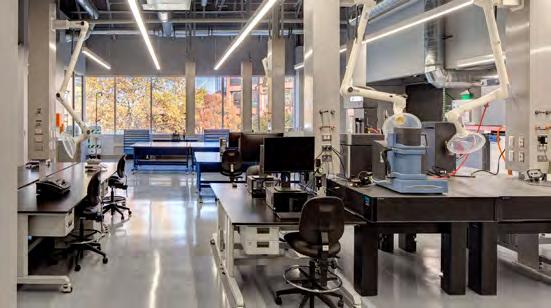

lab
team
will develop novel test set-ups to drive a better
customers. It
“The has would sum the relationship up as: open, transparent, cooperative.” - Scott Warren, DSM
In DSM is dedicating with its also understanding of the performance of DSM materials under field conditions.
Magna E-Car Systems’ 82,000 square foot facility was repurposed from an older facility into an extremely efficient battery testing lab as well as an electric hybrid vehicle and component research and development center.

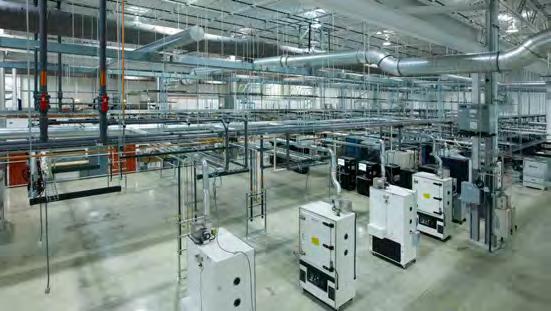
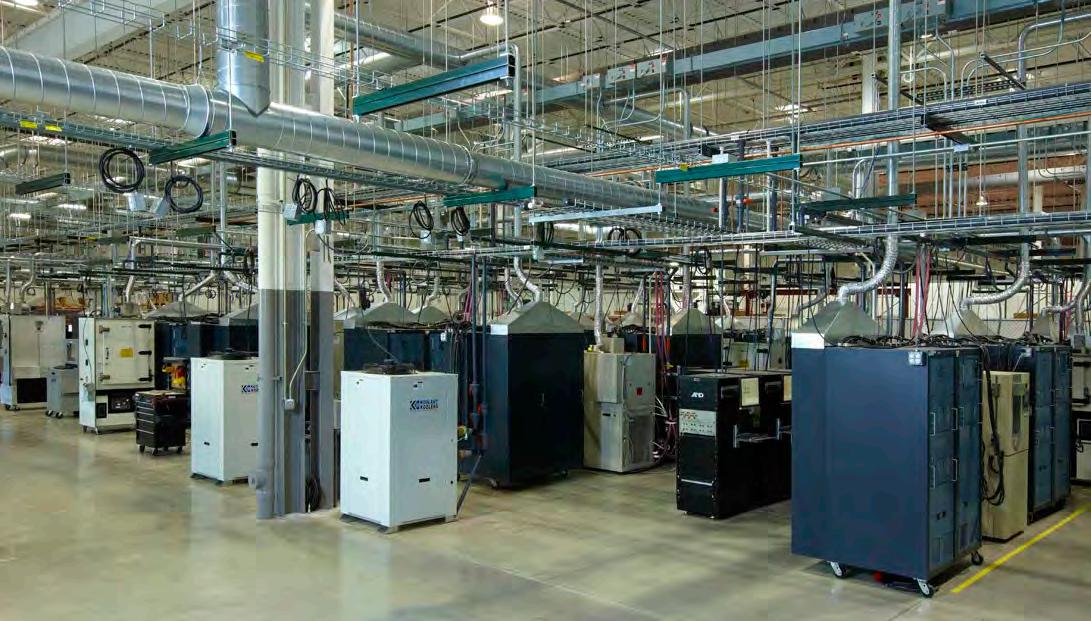
KIRCO MANIX was called upon to design and implement innovative solutions for the highly sophisticated infrastructure demands required for the state of the art equipment used in the facility.

MAGNA E-CAR
LOCATION AUBURN HILLS, MI PROJECT SIZE 82,000 SF PROJECT TYPE RESEARCH & DEVELOPMENT
+ Obtaining necessary permitting and city approvals in the city of Rochester Hills

+ Designing a shop layout for storage, material handling and chemical storage for plastic injection molding
+ A state-of-the-art conference room with web based audio/visual conference system
LOCATION ROCHESTER HILLS,
PROJECT SIZE 25,000 SF PROJECT TYPE MANUFACTURING ADDUXI
+ Receiving and installing imported plastic injection machines from France MI
+ Upgrading electrical services and installing new electrical feed to machinery including new lighting for manufacturing
+ Designing a compressed air system for molding machine operations
THE SCOPE OF THIS PROJECT INCLUDED:
+ Designing and installing IT systems
AdduXi occupied an existing industrial space where KIRCO MANIX completed 25,000 square feet of construction in only five months.
AdduXi, a French company, established a new facility in the United States used for plastic injection molding and manufacturing for the automotive industry.
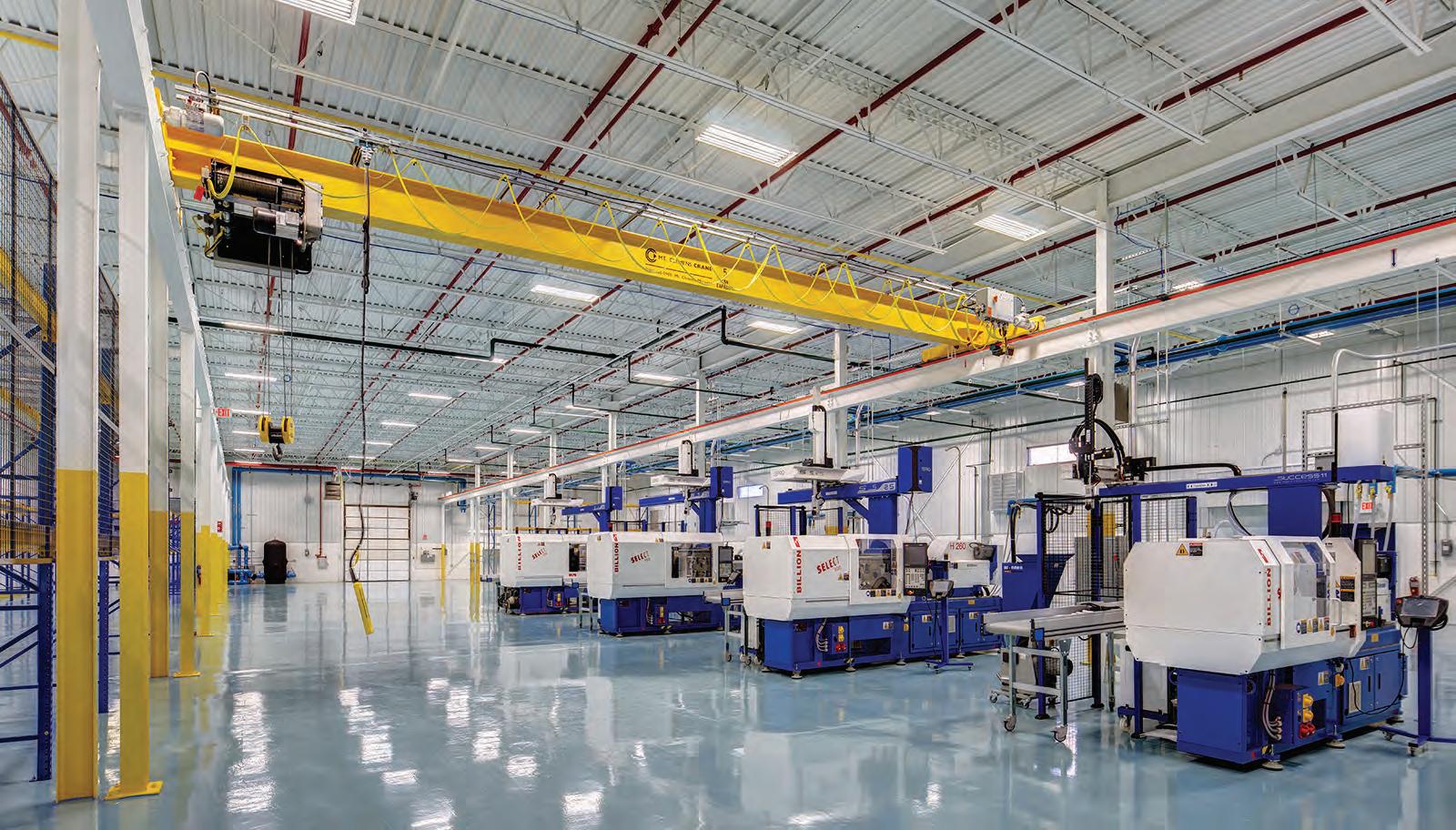
+ Coordinating with the existing landlord to renovate office space
+ Installing a split system chiller for process cooling
KIRCO MANIX was initially sought out to assess all of the equipment requirements for the new facility. Duane Allison, KIRCO MANIX Project Manager, traveled to Bellignat, France to visit AdduXi’s plants and study the setup of existing manufacturing machines to ensure proper installation and operation at the new Rochester Hills facility.
+ Designing and purchasing furniture systems
KIRCO MANIX was selected to construct Volvo Group’s new, state-of-the-art Vehicle Propulsion Lab (VPL), which represents a $33-million expansion of the company’s powertrain research and development site. Volvo’s VPL will be the first facility in North America to allow comprehensive testing of current and future products for Volvo Trucks, Mack Trucks, Prevost and Volvo Bus to meet evolving government regulations and ensure high performance on the diverse North American roadways. Housed under one roof, the lab will consist of two environmental chambers. One chamber will have a chassis dynamometer capable of emissions measurements and simulating extreme-weather and altitude conditions. The second will offer testing of fully operative vehicles, including highway and vocational trucks, as well as coach buses, for starting in a variety of weather conditions. The VPL will be two-stories tall and connected to the existing engine development lab on the Hagerstown campus and will add approximately 10 new jobs.
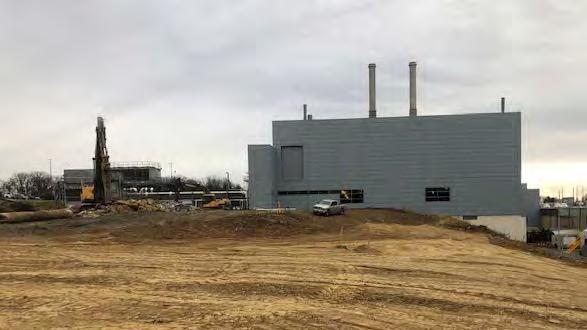
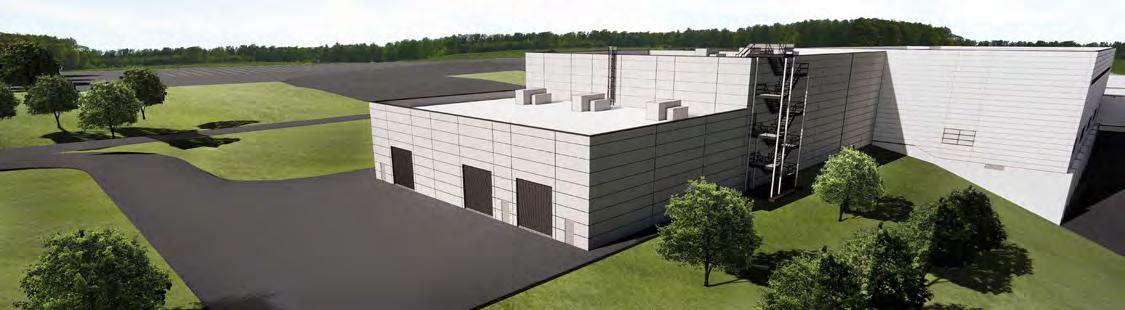
PROJECT TYPE INDUSTRIAL
VOLVO VEHICLE PROPULSION LAB
LOCATION HAGERSTOWN, MD
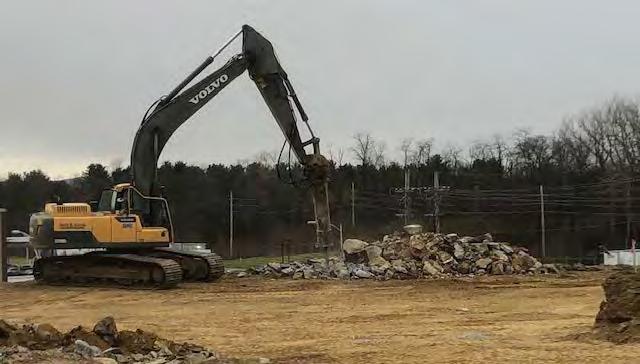
PROJECT SIZE 35,000 SF
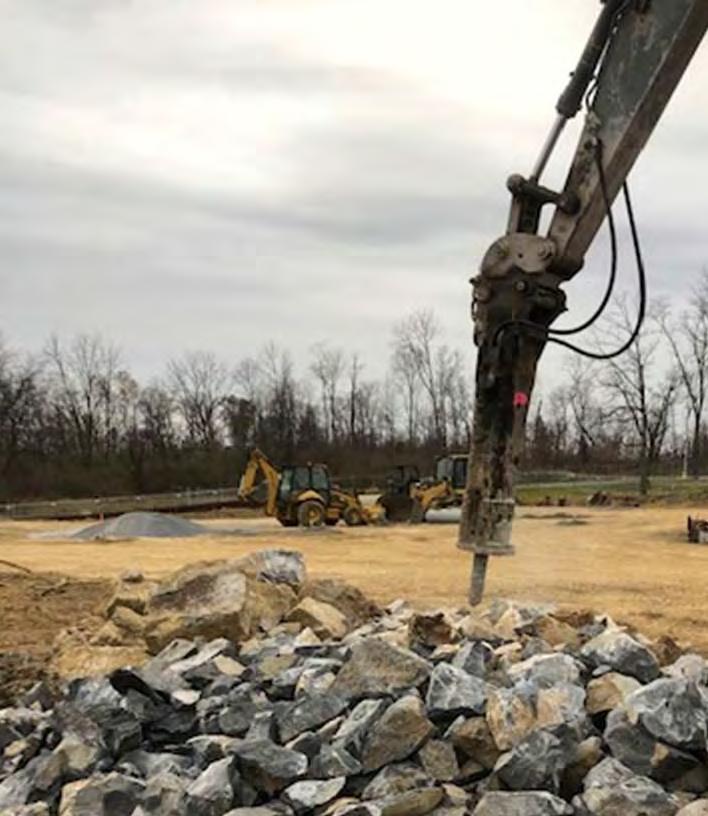
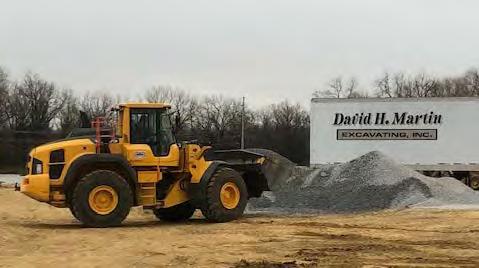
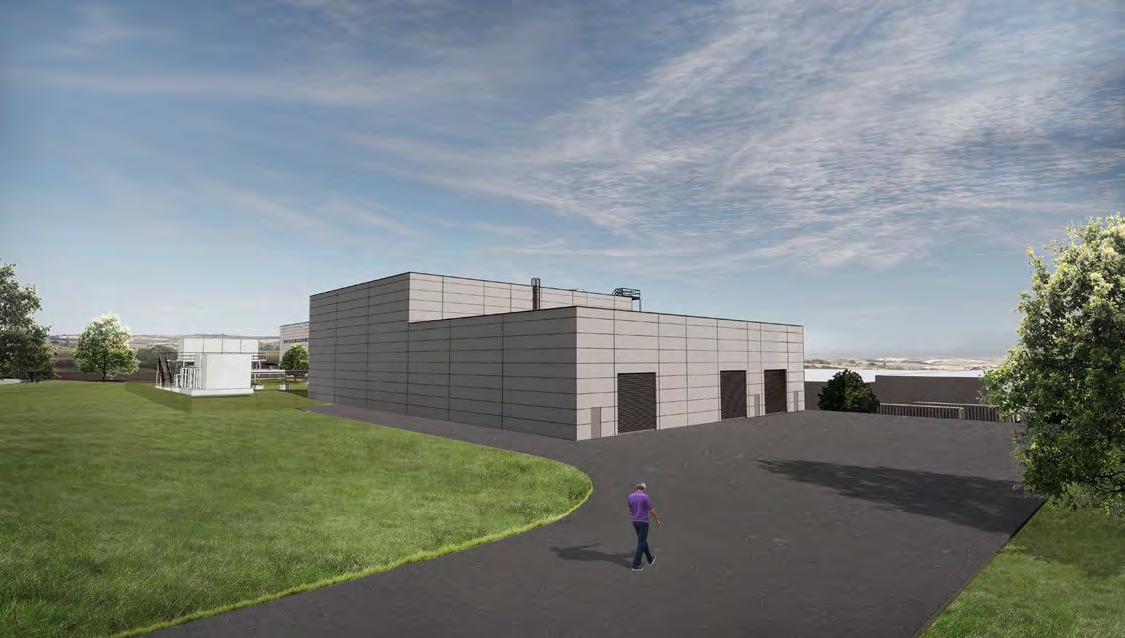

LOCATION FARMINGTON HILLS, MI
PROJECT SIZE 200,000 SF
Helena Giraldo, Corporate Real Estate, Daimler North America Corporation
The 200,000 square foot Mercedes-Benz Financial Services USA Headquarters sits attractively amongst the large swath of trees left untouched from the site’s original preconstruction landscape. A key areas of focus in creating this project was sustainability; the building is LEED certified and preserves many of its natural site features within its amenities, namely outdoor social areas, a pond and a walking path.
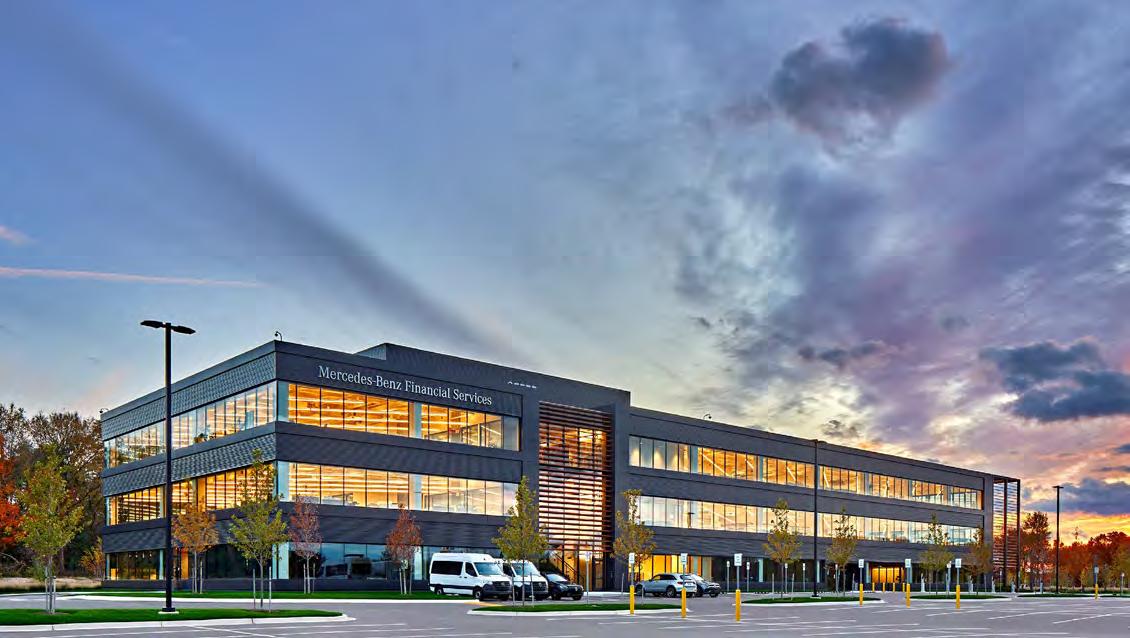
“I really appreciate the commitment of this team which has gone above and beyond expectations. It is very comforting to know people in this team care about this project as much as we in Mercedes-Benz Financial Services do.”
MERCEDES-BENZ FINANCIAL SERVICES USA

The building features open environments to encourage collaboration and the intentional use of windows provides an immense amount of natural light throughout. The building’s amenities include a full gym, showers, locker rooms, full kitchen, game room, and a large open gathering area with media walls. This headquarters was built with a focus on design, use of color, recycled materials, and high-quality finishes, and because of this, serves as a welcoming place for employees and a showcase for visitors.
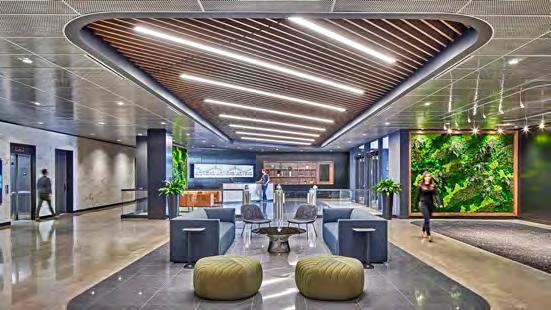
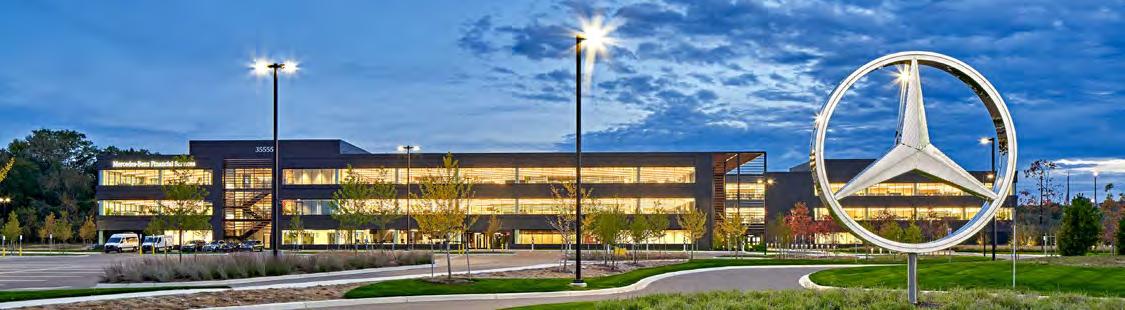
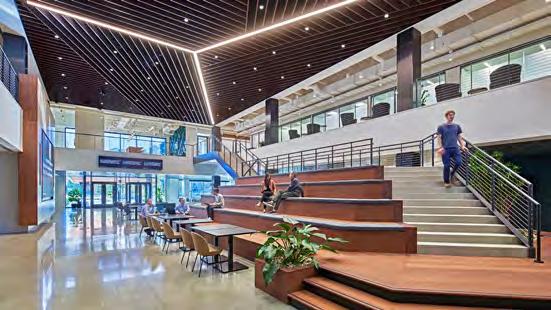
PROJECT TYPE CORPORATEOFFICE HEADQUARTERS
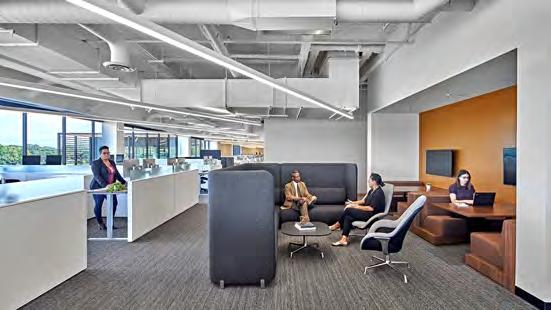


ANN ARBOR, MI
“KIRCO MANIX proved throughout the process to be a trusted and reliable partner. Even in the face of numerous challenges, including the pandemic and supply chain disruptions, we are able today to celebrate the journey and proudly open our building with excitement and positivity.” - Greg Brabec, director of Government Affairs and Special Projects for WACKER
PROJECT SIZE 140,000 SF
PROJECT TYPE
KIRCO and KIRCO MANIX were selected by Wacker Chemical Corporation to develop and construct its more than $70 million, 140,000 square foot North American Innovation Center & Regional Headquarters. Amenities in the new headquarters include world-class labs, a full-service cafeteria, a 24/7 fitness center and open collaborative workspaces.
The technology campus serves as the hub of leadership and innovation for WACKER’s North and Central Americas region; it houses over 200 team members, including the NCA senior leadership team, chemists, IT and other technical experts, support functions, and has capacity for over 300 employees. The investment allows WACKER team members who previously worked out of separate locations to collaborate and innovate in a single, dynamic environment. The new building will serve as a leading-edge location for advanced research and design activities, and enhanced employee collaboration.
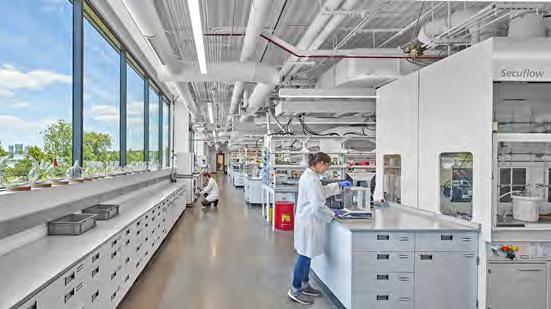


CORPORATEOFFICE HEADQUARTERS RESEARCH & DEVELOPMENT

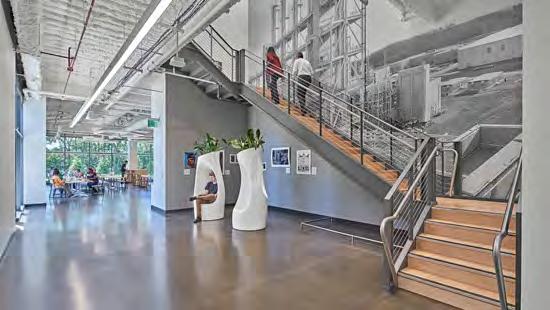
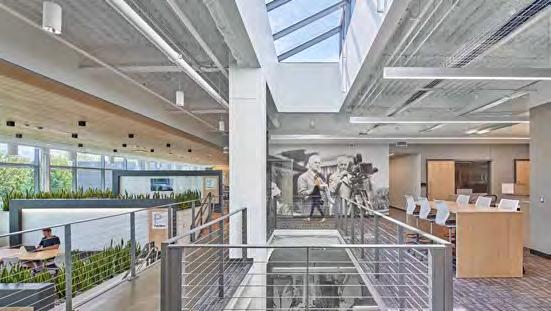
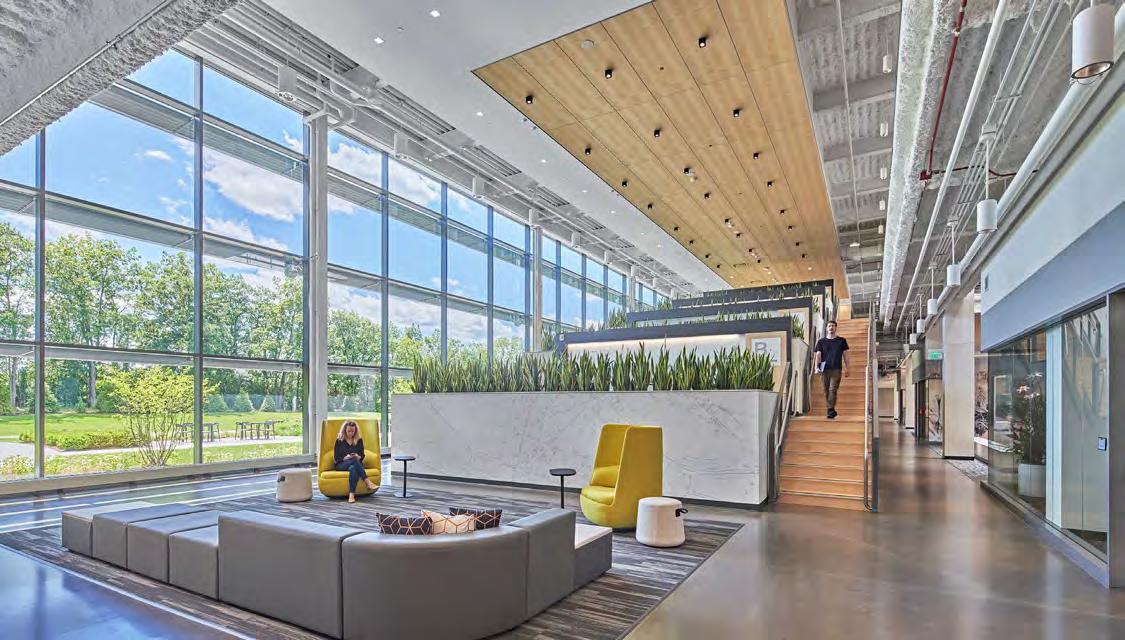

WACKER REGIONAL HEADQUARTERS
LOCATION
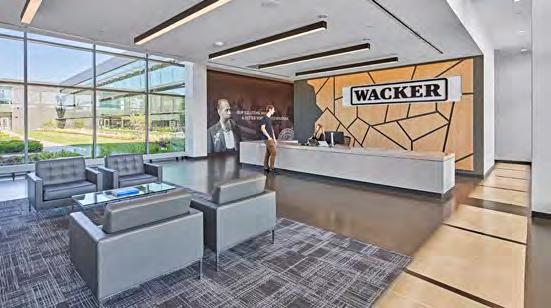
CORPORATE HEADQUARTERS
Elements of the Global Dow Center include: a six-story, 184,390 square foot, steel-frame and curtain wall structure; 21,000 square feet of vegetative rooftop and a nearly one-acre decorative pond wrapping a third of the building, helping to dramatically reduce heat islands and storm water runoff; and an enclosed employee walkway connecting occupants to parking and other campus facilities. The building’s two-story atrium lobby with floor-toceiling glass has technology features that will enrich customers’ and visitors’ appreciation of Dow’s distinguished history and innovative market solutions.
The open-plan design of the building and technology upgrades reflect Dow’s focus on engagement and streamlined communication to propel the company’s culture forward. The building’s sustainable and adaptable design is further expected to advance employee productivity that will benefit customers and the markets Dow serves.

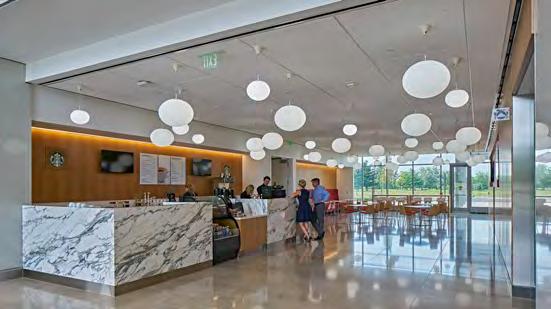
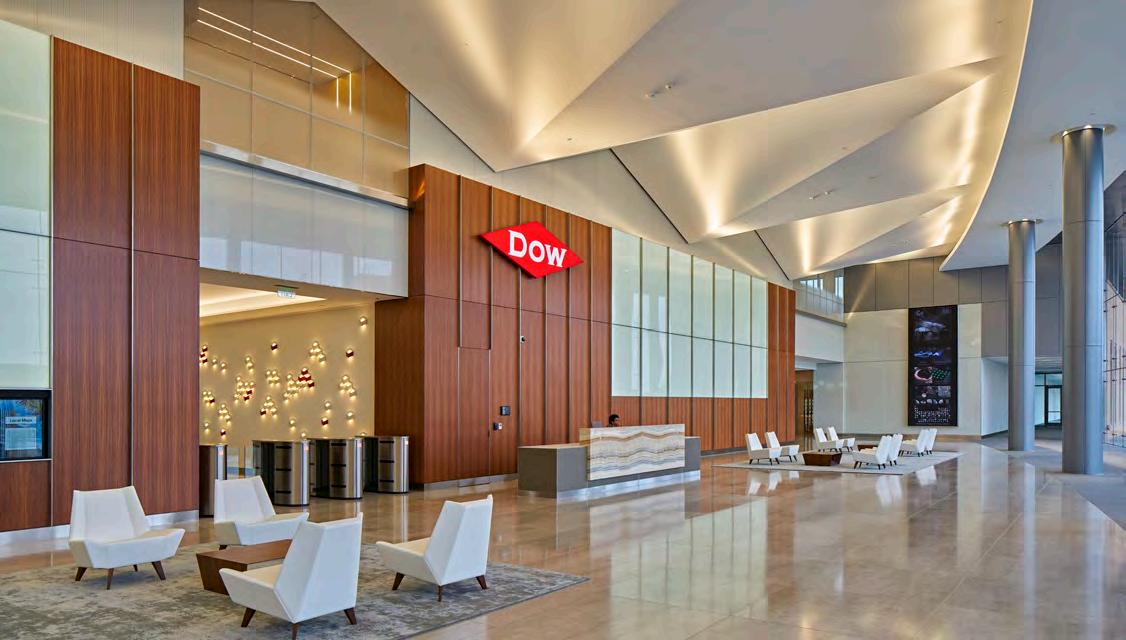
THE GLOBAL DOW CENTER
LOCATION MIDLAND, MI
PROJECT TYPE
“KIRCO was at our side and partnered in the problem solving. Their insight in mitigating project impact was invaluable. With a project of this magnitude and complexity, they were instrumental in delivering against a very aggressive schedule, completed it on time, and under budget.” David T. Day, Global Director, Information Technology and Facilities Services, Dow

KIRCO and KIRCO MANIX recently completed the development and construction of The Dow Chemical Company’s new global headquarters within their Midland, Michigan campus. The Global Dow Center is part of Dow’s ongoing initiative to support collaboration, company growth, and innovation. The new state-of-the-art building replaces the former Willard H. Dow Center (WHDC) 2020 Building.

OFFICE
Dow produces many products for the building and construction industry, many of which were utilized on this project. If laid sideby-side, more than 300 miles of Dow-manufactured products were utilized in the construction of the building.
AWARDS
Construction began in the third quarter of 2015 and was completed in summer of 2017.
The interior environment is open and collaborative, and the glass curtain wall exterior allows for extensive penetration of natural light into the workspaces. Features include a 4,000 square foot “town hall” flexible meeting space, a 17,000 square foot cafeteria, and a coffee kiosk and lounge adjacent to the lobby.

PROJECT SIZE 184,390 SF
LEED SILVER CERTIFIED
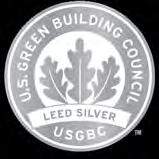
PROJECT SIZE 146,000 SF PROJECT TYPE CORPORATEOFFICE HEADQUARTERS
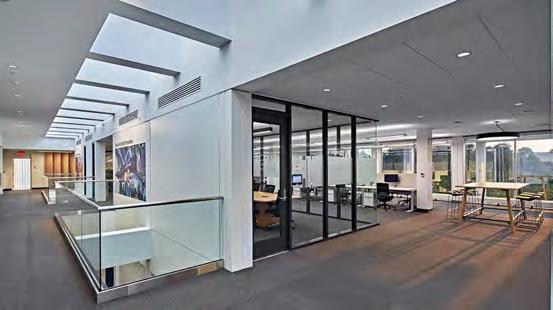
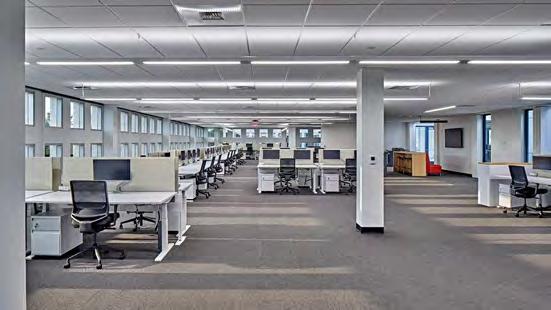
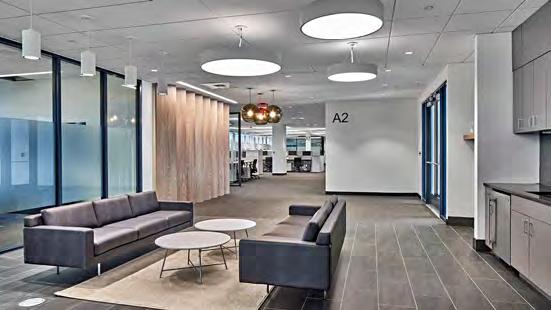

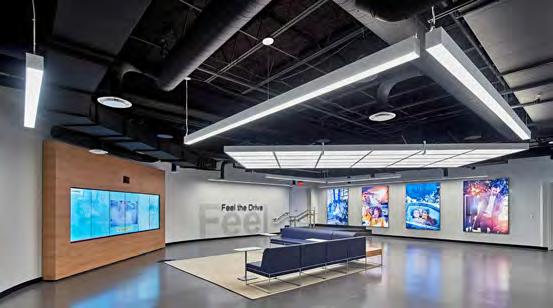
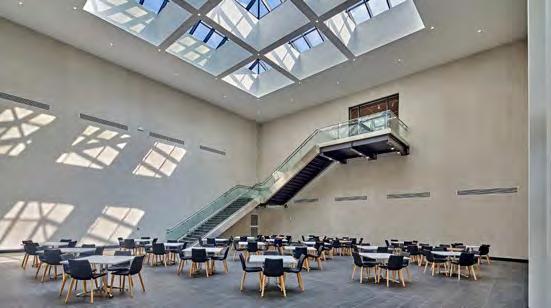

WEBASTO AMERICAS HEADQUARTERS

KIRCO MANIX was selected by Webasto – a global supplier of roof systems to automotive OEMs – to renovate and expand an existing building which became its new Americas headquarters. With an investment of $40 million, the expansion supported Webasto’s forecasted engineering and testing requirements, as well as consolidated existing staff from three locations. Webasto was dedicated to preserving the original characteristics and design intent, so KIRCO MANIX worked with attention to detail to match building styles and elements throughout the addition. For example, replacement and improvements to the building’s original skylights, and matching the 3,000 existing windows from the original design carried over to the new addition. Phase one of the began with demolition of the interior of the existing building. In phase two, KIRCO MANIX broke ground on a 40,000 square foot addition, which included adding a testing lab, office space and a dining area. Simultaneously, phase three began with interior renovations. HILLS, MI

LOCATION AUBURN
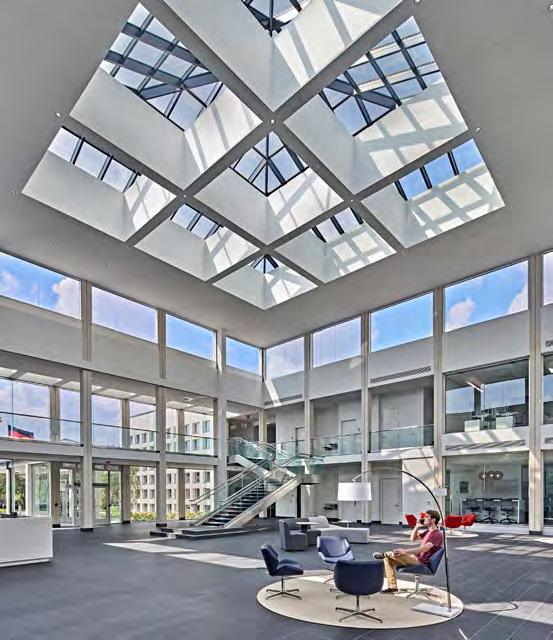
THE MORRELL GROUP
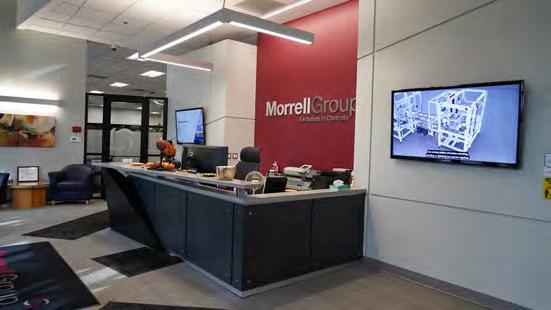
PROJECT TYPE CORPORATEOFFICE HEADQUARTERS
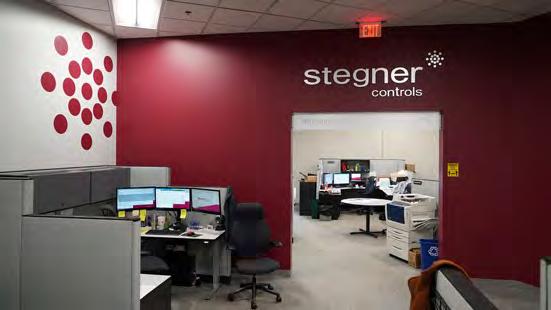

INDUSTRIAL
KIRCO recently acquired the Morrell Group’s 77,000 square foot headquarters in Auburn Hills, Michigan, and plans to lease the building back to the company. By doing so, the Morrell Group – a leading engineering partner, systems integrator and value-added distributor of advanced motion control solutions for industrial and mobile applications – will free up valuable capital that it can reinvest into its business.
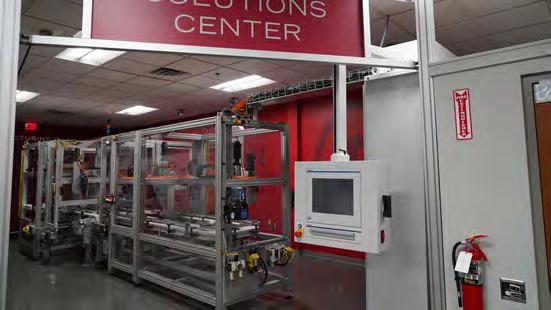
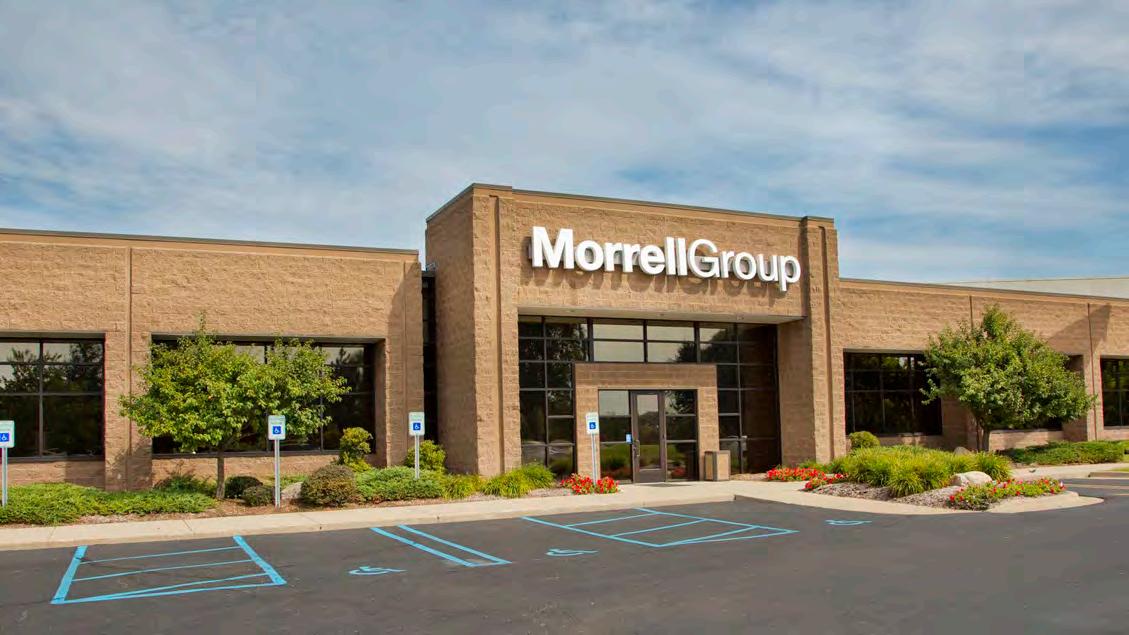
PROJECT SIZE 77,000 SF

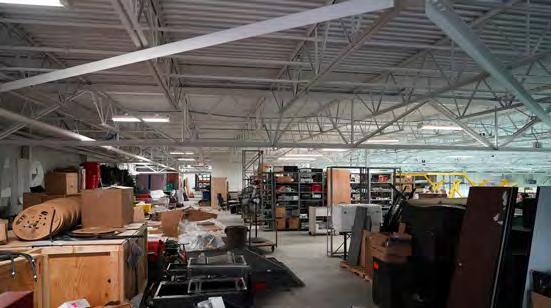
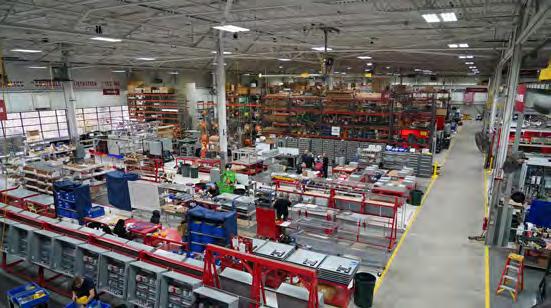
LOCATION AUBURN HILLS, MI
Companies like the Morrell Group are also looking to KIRCO as a trusted landlord partner who has a genuine pride in ownership and can better handle the complexities of facility ownership, management and maintenance, so that the tenant can focus more intensely on its core competencies. In fact, KIRCO’s pride in ownership dates back to when KIRCO MANIX (then Campbell Manix) originally built the Morrell Group headquarters.
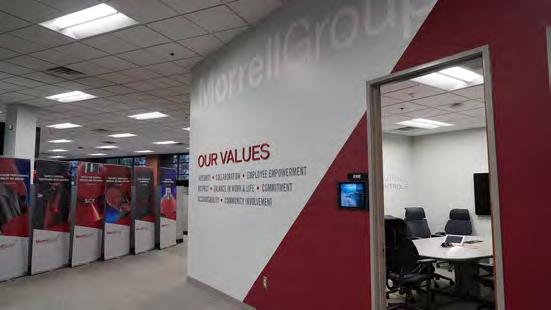
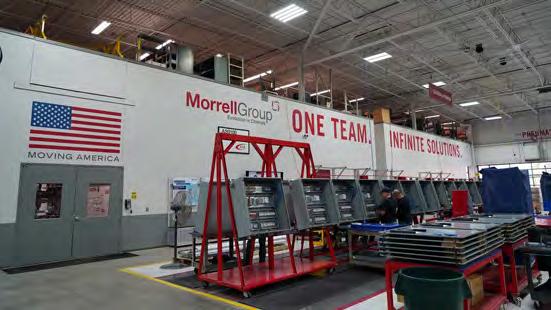
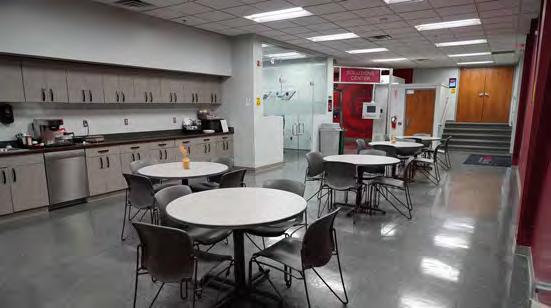

+ Expansion of high capacity mechanical and electrical systems from existing plant to expansion space
+ Expansion of three bays to the plant, totaling 238,000 square feet
MACI is one of the largest manufacturers of automotive air compressors in the world and produces mainly for General Motors and Chrysler. In total, KIRCO MANIX has constructed an additional 238,000 square feet of space for MACI’s needs in manufacturing, warehouse, distribution and lab space.
+ Phased expansion of fully operational, three shift production plant with zero tolerance for shut down of production
PROJECT SIZE 238,000 SF
+ Construction of a 16,200 square foot quality assurance lab
+ Earthwork and road/utility relocation
PHASE 2:
+ Construction of a 20,200 square foot “basement storage” facility
+ Construction of a 2.2 acre parking lot
PROJECT TYPE
MANUFACTURINGDISTRIBUTION
PHASE 1:
LOCATION
+ Due to owner purchasing constraints, KIRCO MANIX worked daily with owner buyout of various trade subcontractors and coordination of several phases of work

MACI
PARMA, MI
+ Addition of 28,800 square feet of warehouse, distribution, and manufacturing space
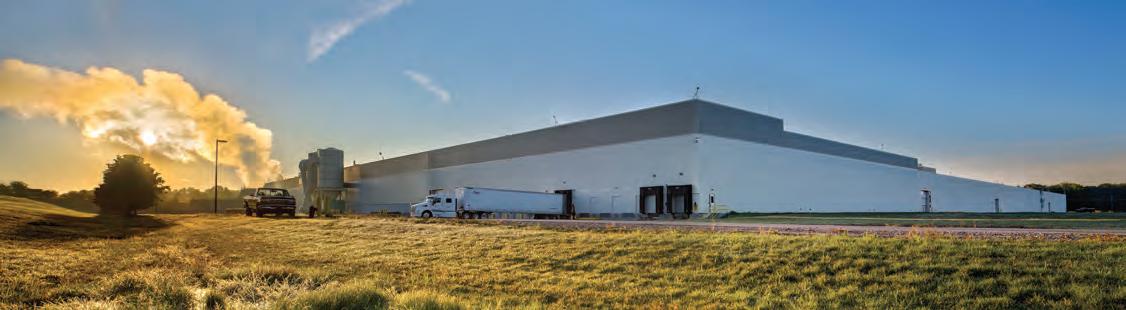
CHALLENGES:

LOCATION STERLING HEIGHTS, MI PROJECT SIZE 189,000 SF PROJECT TYPE MANUFACTURINGOFFICE
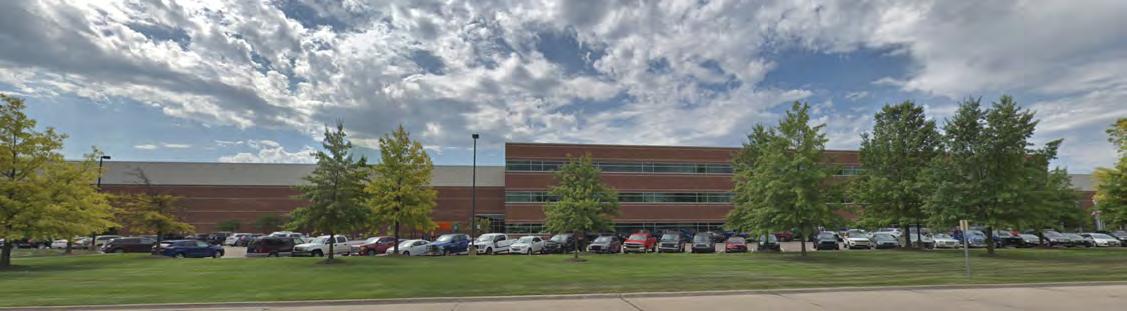

Kuka is a 189,000 square foot engineering, manufacturing, and office facility. The twostory, 40,000 square foot office and engineering space includes a high-end lobby and conference area. The plant includes heavy-duty floors, crane bays with 20-ton cranes, and upgraded electrical and mechanical systems.
KUKA
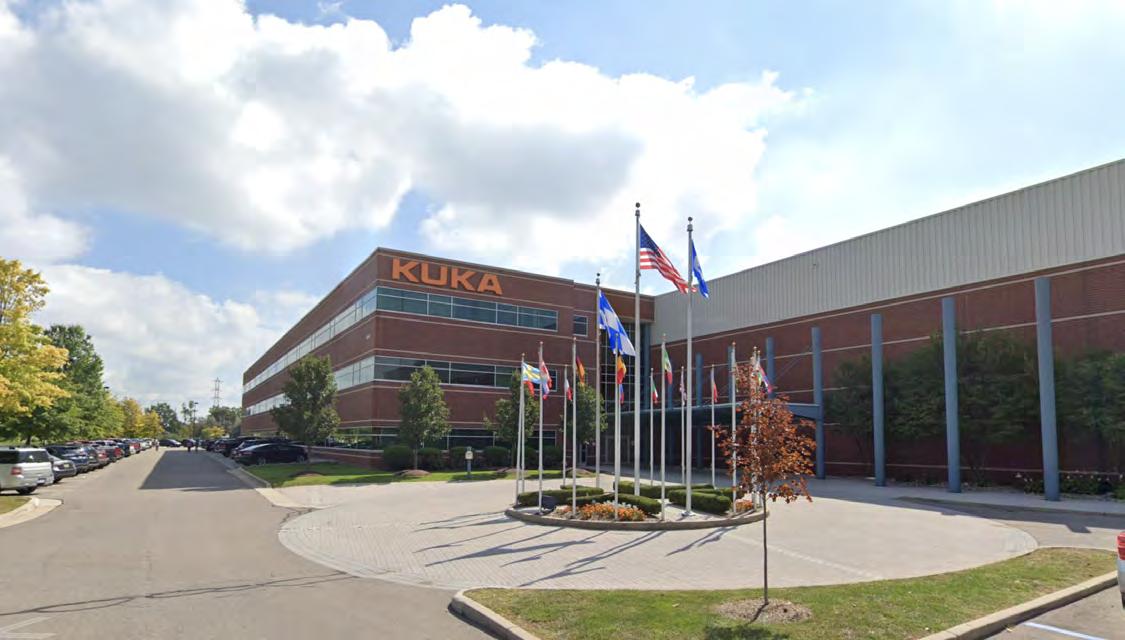
LOCATION OBETZ, OH
PROJECT SIZE 4,000,000 SF 239+ ACRES
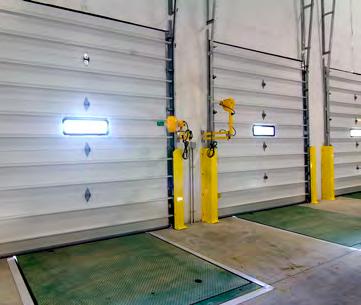
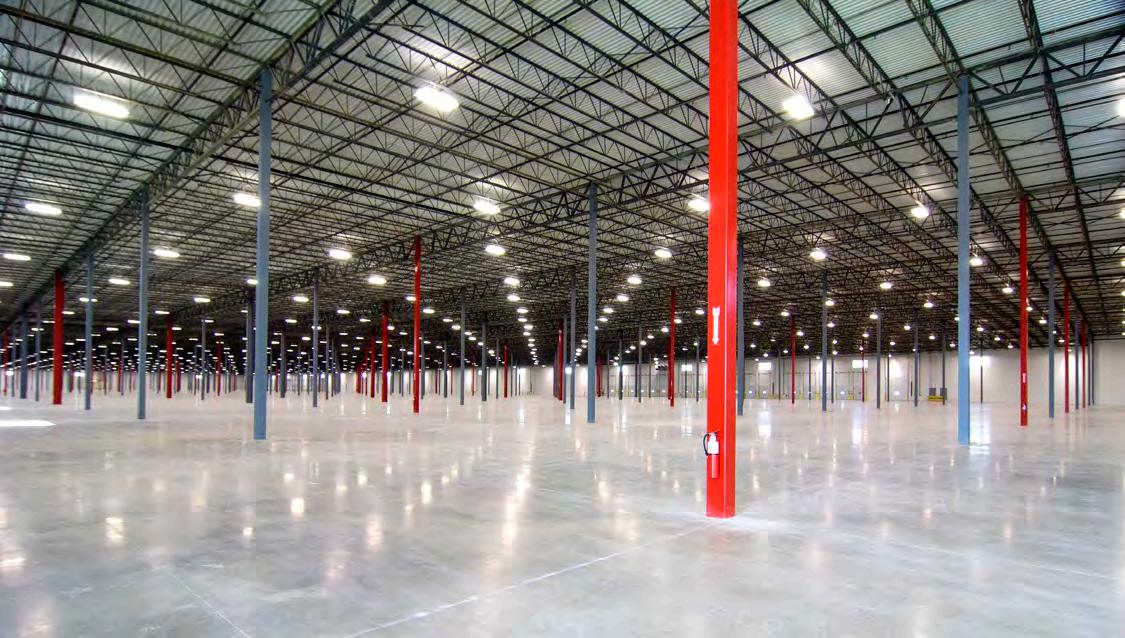


PROJECT TYPE DISTRIBUTIONINDUSTRIAL

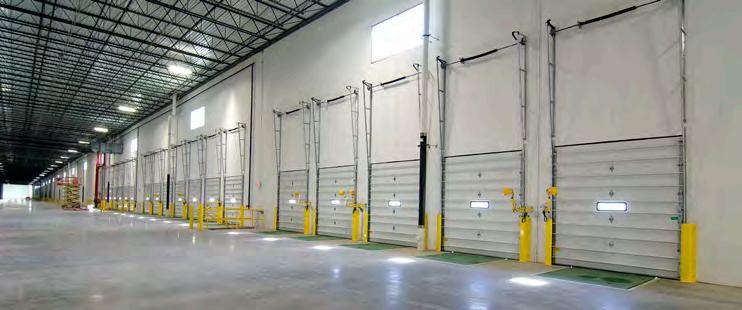
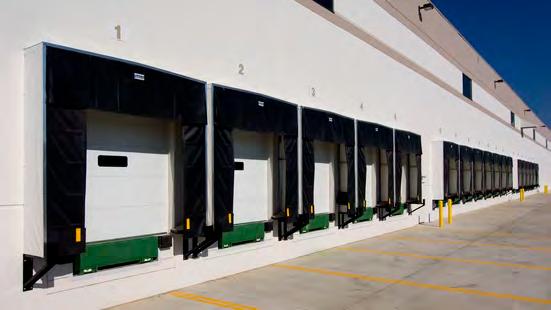
OBETZ BUSINESS
PARK
Obetz Business Park is a multi-phase industrial distribution development located in Obetz, Ohio. It offers distribution based companies and third-party logistics companies a unique choice to enhance efficiency of a distribution network with broad market reach in a high quality, institutional grade development park environment. When fully developed, it will total approximately four million square feet on 239 acres.
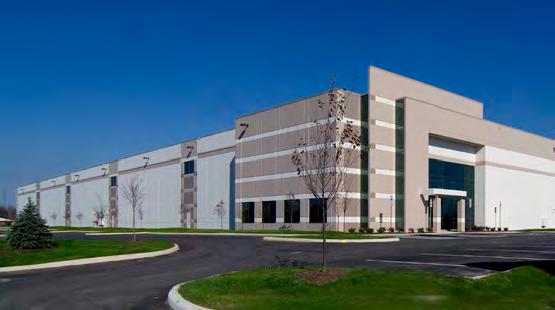

Systems, and Cardinal Health
LOCATION DETROIT, MI
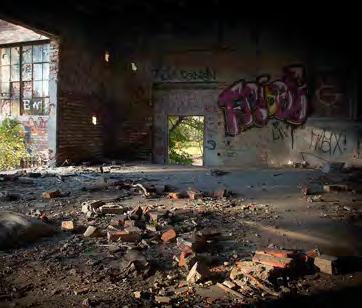
Henry Ford negotiated a new contract with Cardinal Health to help directly reduce supply chain related costs as a result of the changing healthcare reimbursement environment.
“KIRCO has worked very closely with us…they’ve done a great job of saying, ‘Here’s an alternative. This will provide a better cost benefit to you.” Jim Balzer, Senior Consultant, Operations, Cardinal Health

+ Urban redevelopment in one of the oldest neighborhoods in the City of
CREW Detroit Impact Award, Phoenix Award (Grand Prize & People’s Choice Award), CAM Magazine Award, Brownfield Redevelopment and Renewal Award
PROJECT CHALLENGES: Detroit Health
Cardinal Health and Henry Ford Health System selected KIRCO Development to act as their development partner for what was intended to be the first component of a $500750 million master planned community revitalization effort of 300 acres.
VIDEO Cardinal Health Project Video
AWARDS
PROJECT SIZE 275,000 SF
The project involved significant environmental site remediation and attainment of a $12 million brown-field tax increment financing package.
The Cardinal Health project brings a state of the art 275,000 square foot distribution and light assembly building to a blighted area in the City of Detroit.
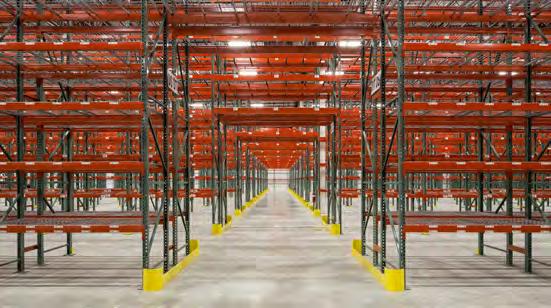
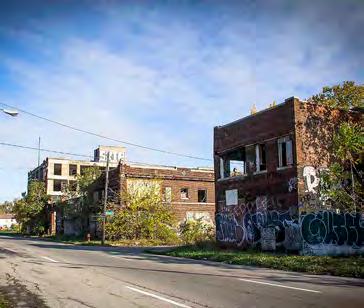

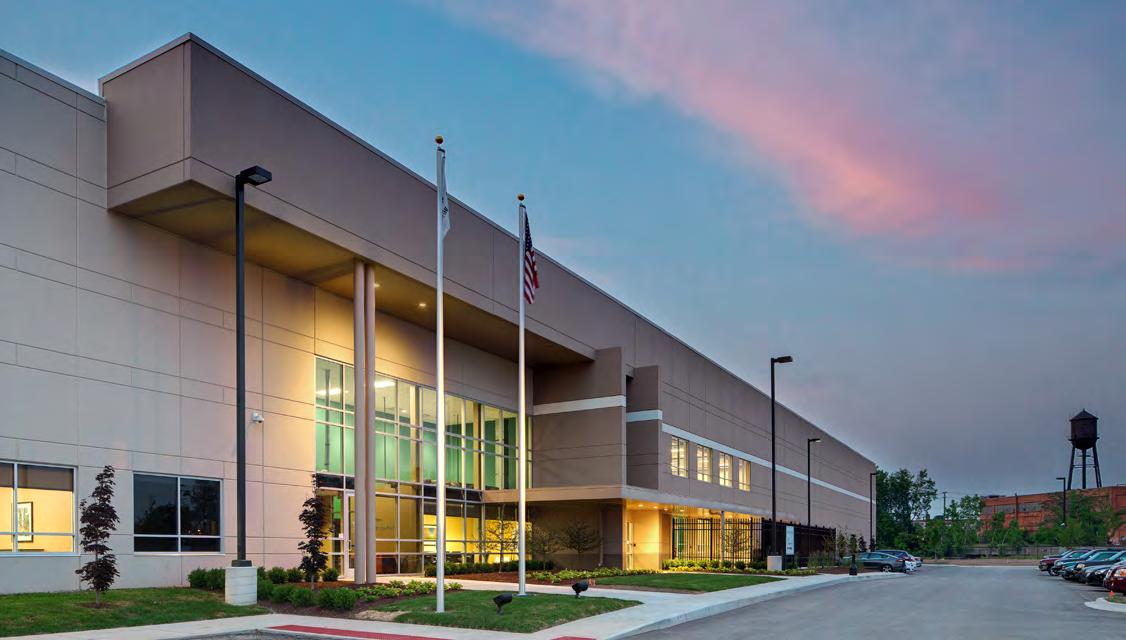


+ Pre-construction period of almost three years + Over 100 parcels of property required consolidation + Extreme environmental conditions of existing soils + Numerous abandoned structures ranging from single family homes to abandoned paint plants required intricate planning for remediation with numerous consultants and government agencies + Close coordination with stakeholders, Henry Ford
CARDINAL HEALTH DISTRIBUTION FACILITY, BEFORE
CARDINAL HEALTH DISTRIBUTION FACILITY, AFTER
PROJECT TYPE
DISTRIBUTIONINDUSTRIALHEALTHCARE
CARDINAL HEALTH DISTRIBUTION FACILITY
The land acquired by KIRCO will accommodate an expansion capability of an additional 135,000 square feet.
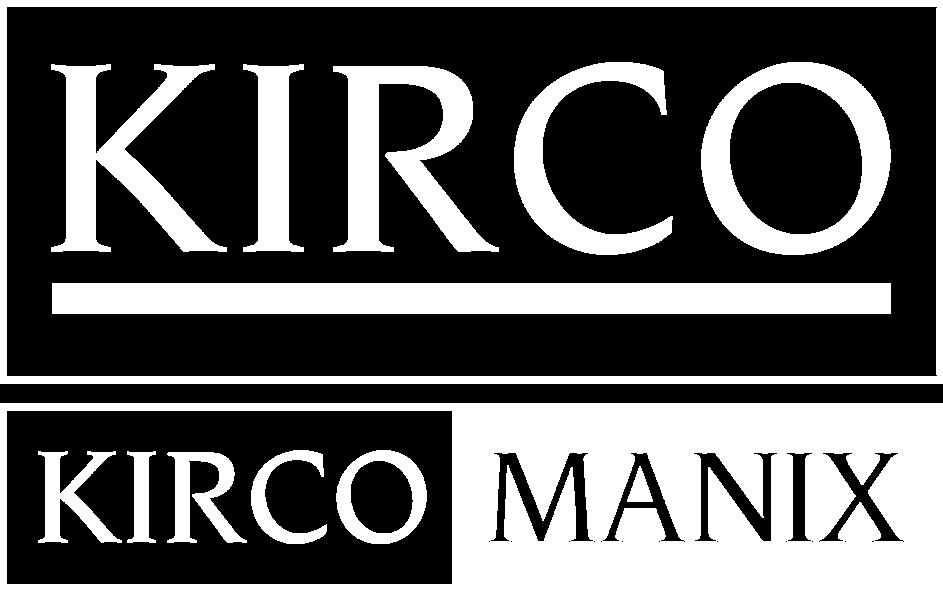