
6 minute read
5 Industry 4.0
E mer gi ng Ma na ge rs
Mr. Indraneel Bapat Kirloskar Institute of Advanced Management Studies, Pune
Advertisement

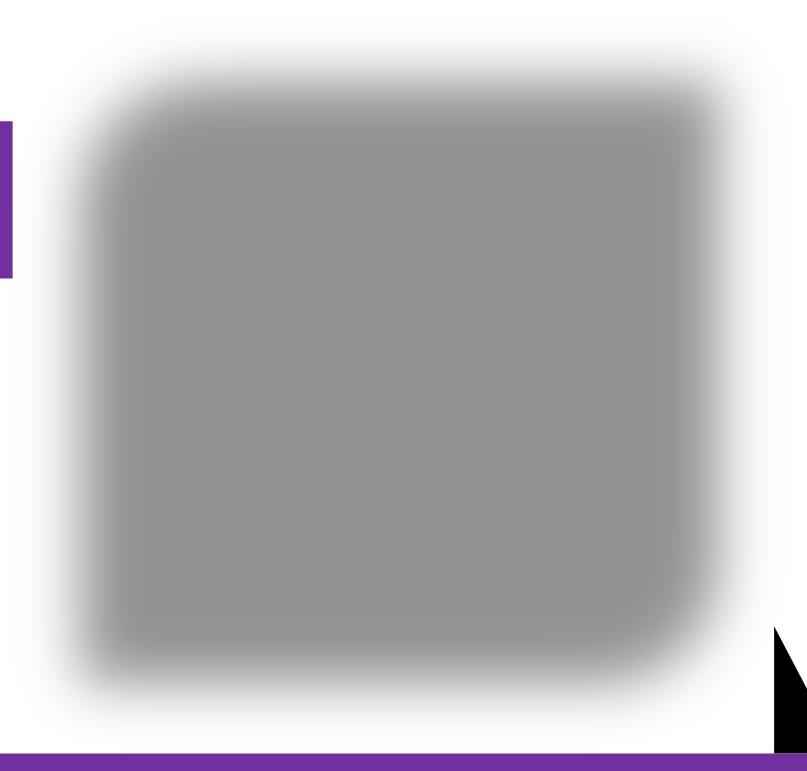
In d us tr y 4 . 0

People, machines, and products are directly workforce. What started as standardization of tasks networked with one another: the fourth industrial in simple processes, ultimately paved the way for revolution has begun. the beginning of automation and initiation of the The term "Industry 4.0", shortened to I4.0 or simply I4, originated in 2011 from a project in the hightech strategy of the German government, which promotes the computerization of manufacturing. The phrase Fourth Industrial Revolution was first introduced by Klaus Schwab, executive chairman of the World Economic Forum, in a 2015 article published by Foreign Affairs, "Mastering the Fourth Industrial Revolution”.

Before trying to understand the fourth industrial revolution and its real-world implementation, we must look at the beginning of the industrial revolution and its gradual advent towards today’s
second industrial revolution. technology-oriented industrial environment. The aftermath of the second world war was the massive industrial growth in the post-war western The beginning of the industrial revolution started in world. However, mechanization was a pestering Europe with the mechanization of simple jobs like issue in innovation and new product development weaving cloth, printing on paper, etc. However, as mechanical systems had their limitations. Thus, most of the mechanization was highly localized and the growth of electronics & electrical technology each process of manufacturing required a dedicated was going to be a breakthrough with the production
of programmable logic controllers (PLCs) ushering Inter-networking does not necessarily mean the world into the third industrial revolution. centralization. Rather, Industry 4.0 promotes the Automation became the standard with the speed of idea of each machine, and system is an autonomous production reaching the levels previously entity that shares and receives data from all the unimaginable with the mechanical systems. entities of the enterprise and takes its own With the arrival of the information age in the early ’70s mostly for defence in the western world, the 4. Technical assistance: world rushed into first commercially available internet in the ’90s and integration of information The ability to interconnect all systems breaks the systems in manufacturing in the 21st century. In silos within the supply chain and on the production this article, we will explore how the network- floor. Any problem encountered by any personnel connected smart devices will run our factories, can be solved more quickly and conveniently due improve our daily lives, and shape the future of to data and assistance pouring in from the entire highly innovative, customer-centric industry. The system. fourth industrial revolution or Industry 4.0 is at our doorstep. Challenges for adopting Industry 4.0
Industry 4.0 features
assurance, product management, IT, sales and levels of automated collaboration across the downstream chain that brings the finished products
3. Decentralized decision-making:
appropriate decisions.
• Risks to data security:
1. Horizontal & vertical integration: Putting your entire enterprise including company Horizontal integration across the enterprise will and especially your means of production/ service enable the systems, machines, and even on the internet comes with its own set of threats. manufacturing facilities spread across the globe to Tailored risk management strategies and data be interconnected and share performance data and security measures can mitigate the risk of cyberwoes continuously. Vertical integration aims to tie attacks with decentralized structures and limited together all logical layers within the organization access rights being cited as sensible security from the production floor through R&D, quality measures. marketing, and so on. • IT infrastructure:
2. Transparency of data: Industry 4.0 requires the existing installation to be Industry 4.0 proposes data transparency and high types of IT infrastructures. upstream supply and logistics chain that provisions For companies, especially manufacturing ones, the the production processes themselves as well as the cost implications are high. to market. • Dearth of talent:
information, financial details, your peoples’ data adapted and in some cases, needs entirely new
Connecting to an entirely virtual environment of networking and its digitization increases the
importance of new technical skills particularly in quality inspections, serialisation, data logging, and operating activities, warehousing and new more. mechanical working processes.
Also, new entrants in the job market might be are: With an increase in consumption from the newer millennial generation, the demands of customization are increasing. One of the best examples’ is the Nike online store where you can customize and design your shoes. The scope of networking offered by Industry 4.0 will enable manufacturing companies to make more extensive use of customization than they can now.
• Improved quality and efficiency:
pharmaceutical and medical device manufacturing
• Increased collaborative working:
required to be trained for the new technologies that Industry 4.0 technologies allow your production might add to the pre-existing costs of training and lines, business processes, and departments to development. communicate regardless of location, time zone, platform, or any other factor. Industry 4.0 can Advantages & new opportunities of Industry 4.0 achieve what may be considered as the pinnacle in Some various opportunities & advantages arise by manufacturing facility at one end of the world from to implementation of Industry 4.0. Some of them another end.
• Flexible customer integration: revolution:

international collaborative working ie. To operate a Contribution of India to the 4th industrial
The Indian government estimates India’s Analysis of big data captured by the devices and manufacturing sector would breach US$ 1 trillion machinery thorough sensors can enable the by 2025. However, manufacturers need to move companies to identify defects and shortcomings in beyond the current status, characterized by manual the manufacturing process at an early stage. This inputs, lack of ICT integration in manufacturing, will achieve the goal of improving the efficiency of and critical gaps in capability, to move to the next the process while maintaining the quality. stage and fill the critical technology gaps.
• Makes compliance easier: Apart from building long-term competitiveness on Complying with regulations in Industrys like from adopting Industry 4.0. the global stage, India stands to gain significantly does not have to be a manual process. Instead, First, it will allow manufacturers to improve Industry 4.0 technologies make it possible to productivity, efficiency, safety and performance automate compliance including track and trace, and help position India as a global manufacturing hub. Several Indian e-commerce companies are
using advanced data analytics to gain insights on new ones will be created in the new economy. customer behaviour and improve business Training in safety-related skills will also come into performance play with an increased level of human-machine cooperation. Second, Small and Medium Enterprises (SMEs), which form the backbone of Indian manufacturing, Finally, Industry 4.0 could provide a pathway for can leverage Industry 4.0 technologies to become Indian manufacturing to transform into an more agile, enhance productivity, streamline costs innovation-led and high-value manufacturing and reduce risks. The sooner they evolve to meet stage. Technology-intensive sectors such as the modern business needs, the more they will stay Aerospace & Defence (A&D), which is at the cusp relevant and secure new business on a global scale. of innovation and growth in India, are clear beneficiaries. Third, employers will be able to increase the skills of their workforce. While some jobs may be lost,