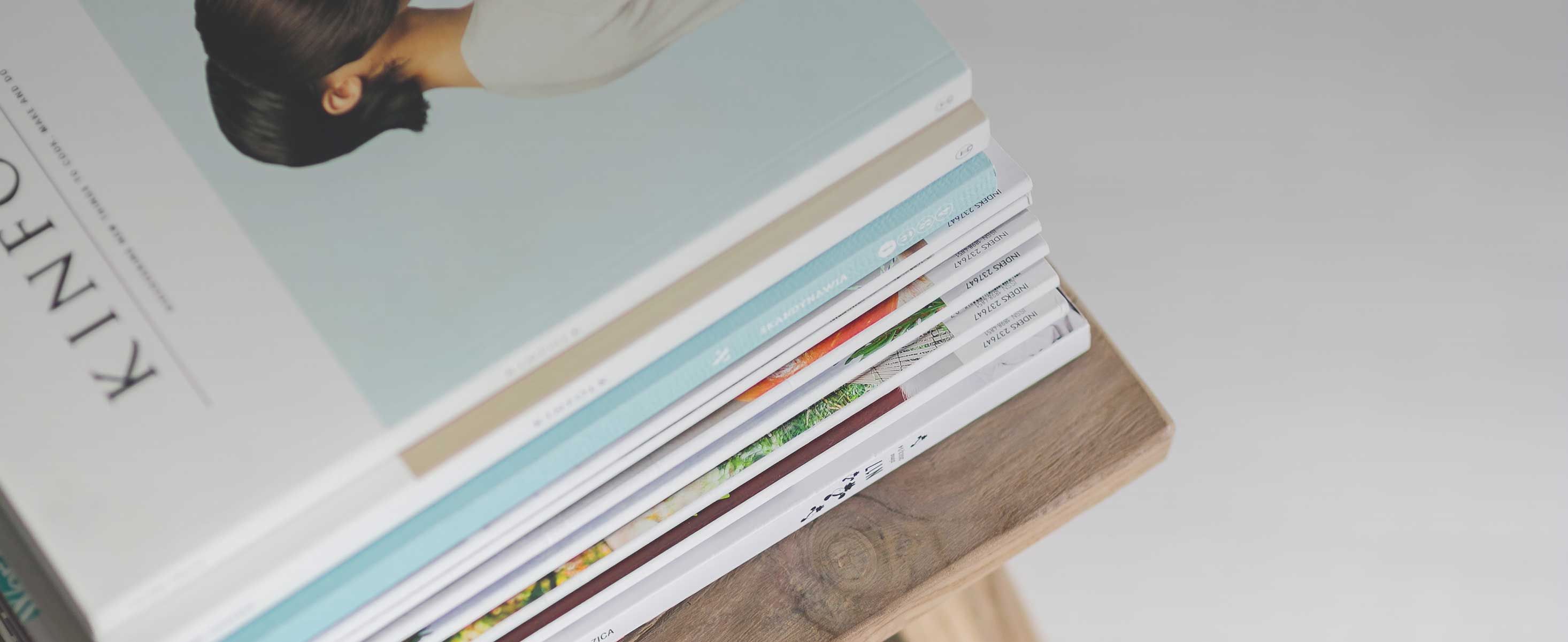
8 minute read
CORPORATE ANGLE
Mr. Akhil Sreenadhu
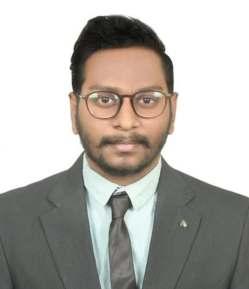
Advertisement
Technology Risk Analyst Ernst & Young Pvt Ltd.
The Role of Technology in Operations Management
Modern technology has completely changed how businesses run operations, resulting in higher productivity, lower costs, and better results. According to McKinsey, digitizing operations management systems is a crucial first step in building an organizational culture of ongoing innovation. The application of efficient digital business strategies is supported by using digital technology, such as the Internet, in managing activities in both the public and private sectors. Managers must define the tasks that technology should be able to complete, participate in the selection of that technology, oversee its installation, integrate it into the rest of the business, and maintain and replace it as needed. Business managers need to be at ease learning new technologies andadaptingtochangebecausebusinessesandemployeesrelyontechnology tohelpbuild efficient business practices. Business process automation (BPA), when utilized to supplement or replace human tasks and procedures, can also improve effectiveness, save time, and minimize errors in operations management.
Today's conception ofvaluecreation is primarily influenced by ecosystems interacting intelligently and autonomously. The pervasive experiment of digitizing every operational function recognizable in enterprises rings the death knell for conventional software and methods to manage manufacturing along whole supply chains. These sweeping business changes often result from the use of big data strategies, which are done "to generate value for the organization by optimizing, adapting, or drastically changing the operations model."Due to the digitization of digital products or (connected) services, or, at the very least, increased convenience and productivity due to the intelligent interpretation of gathered data linked to autonomous process flows, expectations of current and potential new customers across nearly all industries are rising. As a result, a request for papers for this PPC's special issue was put out in 2016. What it means for operations management
(OM) to digitize "everything" piqued our curiosity. We were interested in how businesses dealt with value-added services, internal digitization of processes, and value chains. We were interested in learning what factors affect how things, services, and their creation became digitized. Therefore, this special issue's emphasis is primarily on getting valuable insights. We will be able to gain knowledge from severalreal-worldexamplesandunderstandhowmanufacturersandbusinessesintheservicesector deal with the problem of digitizing processes, services, and exclusive products.
Over time, the focus of technology and operations management has shifted from product creation to the design, administration, and enhancement of operational systems and procedures.
The use of technology in operation management has ensured that firms can lower the cost, improve the delivery process, standardize and improve quality, and focus on
A few technological tools used in operations management -
a. Data analysis: Data analytics is choosing pertinent data for investigation and making choices based on the knowledge it offers. This study is carried out to support or refute existing business hypotheses, enhance business decision-making, and maintain business operations.
b. Satellite Workers: The number of workers using home offices has increased, making it more challenging to keep an eye on employees than just peering over the adjacent cubicle wall. Management can only aspire to have an accurate barometer to gauge the production from satellite offices or remote workers using technology.
c. Project Management: Project management covers various topics, such as keeping track of work, managing deadlines and budgets, and simplifying communication. Teams may collect and track the lifecycle of multiple projects using technology, regardless of where they are.
d. Communication Techniques: Global competition is a concern for today's enterprises. Competitors must feel comfortable using communication technology when a face-to-face meeting is impossible. A team of clients on the other side of the world can now be spoken to directly in real time.
To develop their future operating model, the firms that have adopted new technology carefully diagnosed their current situation. This is how they transformed their management systems.
The following are a few necessary actions to open the door for ongoing innovation: a. Explain the justification for the change and your team's objectives. Determining the desired goal is crucial, whether democratizing innovation or upskilling staff to develop the skill sets required for the future operating model. b. One can accurately determine its strengths and flaws by evaluating the management system's current state against time-tested management principles. c. Assemble the appropriate cross-functional team (including HR, IT, legal, and others) to create the initial minimum viable product. If an established management system exists, consider using process mining and value-stream mapping to advance current practices technologically. If there is no management system, begin small with an MVP toolkit and gradually expand.
About Author:
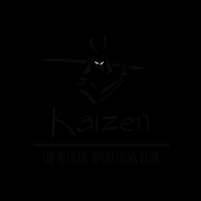
Akhil Sreenadhu has been working as an Analyst at EY for the past year. He has completed his MBA from the ICFAI Business School. He had served as an intern in the field of business at one of the firms in Delhi. He is interested in learning about various businesses and how they operate to maximize profits.
Mr. Karun Bansal Associate Consultant Tata Consultancy Services Ltd.
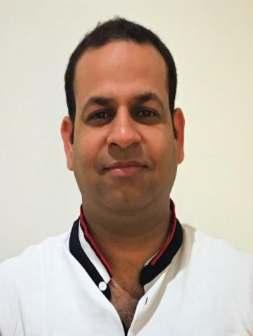
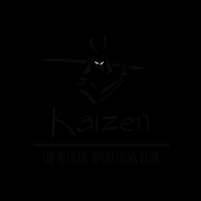
The European Foundation for Quality Management Model is not always a Silver Bullet to Success
The European Foundation for Quality Management (EFQM) model has been widely used by organizations across Europe to drive continuous improvement and achieve excellence in various areas of their operations. However, despite its popularity and widespread adoption, the EFQM model is not without its setbacks. Many organizations that have used the model have faced significant challenges and obstacles that have hindered their progress toward achieving their goals. In this article, we will look at some major setbacks associated with the EFQM model and explore ways organizations can overcome these challenges to maximize the benefits of using this popular quality management tool. So, if you're a business leader or quality management professional looking to improve your organization's performance, read on to discover the pitfalls to avoid when implementing the EFQM model.
Understanding the EFQM Model
Before we delve into the setbacks associated with the EFQM model, it's essential to understand the model and how it works. The EFQM model is a framework for quality management that the European Foundation for Quality Management developed. It is based on principles and concepts designed to help organizations achieve excellence in various areas of their operations, including leadership, strategy, people management, partnerships and resources, processes, products and services, and customer results.
The EFQM model is designed to be flexible and adaptable, allowing organizations to tailor it to their specific needs and requirements. It provides a structured approach to quality management that enables organizations to identify areas for improvement and implement changes that will drive continuous improvement and enhance overall performance.
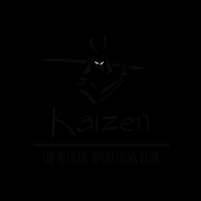
Criticisms of the EFQM Model
Despite its popularity and widespread adoption, the EFQM model has attracted its fair share of critics. Some of the most common criticisms of the model include its complexity, lack of clarity, and difficulty implementing it effectively. Another criticism of the EFQM model is that it tends to focus on the quantitative aspects of quality management, such as metrics and data analysis, while neglecting the softer, more qualitative aspects of quality management, such as culture, values, and employee engagement. This can lead to a narrow focus on performance metrics and a lack of attention to the human aspects of quality management, which can ultimately undermine the model's effectiveness.
Setbacks Associated with the EFQM Model
While the EFQM model has many benefits, it is not without its setbacks. Some of the most significant setbacks associated with the model include the lack of flexibility, limited applicability, failure to address organizational culture, and emphasis on quantitative data over qualitative data.
Lack of Flexibility in the EFQM Model
One of the major setbacks of the EFQM model is its lack of flexibility. While the model is designed to be adaptable and customizable, it can be difficult for organizations to modify the framework to suit their specific needs and requirements. This can make it challenging for organizations to implement the model effectively and achieve the desired outcomes.
Another issue with the lack of flexibility in the EFQM model is that it can lead to a one-size-fitsall approach to quality management. This can be problematic for organizations operating in diverse industries with unique requirements and challenges. It can also lead to a lack of innovation and creativity, as organizations may be reluctant to deviate from the prescribed approach.
Limited Applicability of the EFQM Model
Another major setback of the EFQM model is its limited applicability. While the model is wellsuited to certain types of organizations, such as manufacturing and service industries, it may not be suitable for organizations in other sectors, such as healthcare or education.
This can be particularly problematic for organizations looking to implement the EFQM model to drive continuous improvement and achieve excellence. If the model is not well-suited to the organization's specific needs and requirements, it may not be effective in achieving the desired outcomes.
EFQM Model's Failure to Address Organizational Culture
Another major setback of the EFQM model is its failure to address organizational culture. While the model provides a structured approach to quality management, it does not consider the cultural factors that can influence an organization’s performance.
Culture plays a critical role in determining the success or failure of quality management initiatives. If an organization’s culture is not aligned with the principles and values of the EFQM model, it may be challenging to implement the model effectively and achieve the desired outcomes.
The EFQM Model’s Emphasis on Quantitative Data Over Qualitative Data
Another major setback of the EFQM model is its emphasis on quantitative data over qualitative data. While the model provides a structured approach to data analysis and metrics, it can lead to a narrow focus on performance metrics and a need for more attention to the softer, more qualitative aspects of quality management. This can be particularly problematic for organizations that operate in industries where the human element is critical to success, such as healthcare or education. Organizations may struggle to achieve the desired outcomes and drive continuous improvement without focusing on the softer, more qualitative aspects of quality management.
Alternatives to the EFQM Model
Despite the setbacks associated with the EFQM model, organizations can use several alternative quality management frameworks to achieve excellence in various areas of their operations. Some of the most popular alternatives to the EFQM model include the ISO 9001 standard, Lean Six Sigma, and Total Quality Management (TQM).
Eachframeworkhasitsstrengthsandweaknesses,andorganizationsshouldcarefullyconsidertheir specific needs and requirements when selecting a quality management framework.
Conclusion
Weighing the Pros and Cons of the EFQM Model
In conclusion, the EFQM model is a popular and widely used framework for quality management that has helped many organizations achieve excellence in various operations. However, the model has its setbacks, including the need for more flexibility, limited applicability, failure to address organizational culture, and emphasis on quantitative data over qualitative data.
Organizations considering implementing the EFQM model should carefully weigh the pros and cons of the model and consider alternative quality management frameworks that may be better suited to their specific needs and requirements. By doing so, organizations can maximize the benefits of quality management and drive continuous improvement in their operations.
About Author
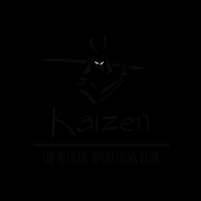
Mr. Karun Bansal is a professional with 15 years of in-hand experience at TATA Consultancy Services. He is currently working in London as an Associate Consultant. He is highly experienced as an Agile and Scrum Coach, Release Train Engineer, and Consultant with an outstanding track record of accelerating enterprise-wide performance and development quality. His expertise includes leveraging comprehensive knowledge of Product and Portfolio Management tools to navigate emerging obstacles. He is also skilled as a communicator and collaborator, able to forge strong working relationships with key stakeholders and internal team members to promote cohesion and enhance capacity.