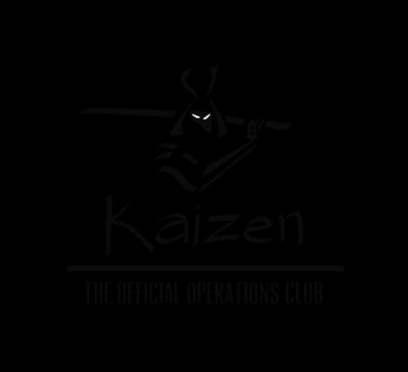
31 minute read
EMERGING MANAGERS
Mr. Priyam Sisodia MBA, 2022-2024 SIBM - Bengaluru
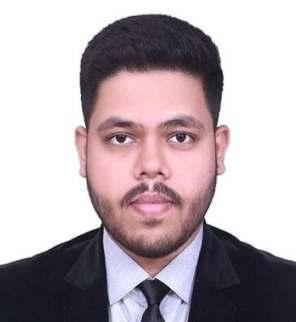
Advertisement
ERP programs to improve schools' and universities' operational effectiveness
We live in a space where technology is growing to leaps and bounds and demands human skills to adapt to new technological changes and advancements in technology boom in every industry and thus the educational sector. With the coronavirus, the academic calamity industry was affected abruptly. Those two years were a nightmare for educational institutions. Students faced many difficulties adapting to the online mode of learning. Online lectures and online exams have affected children's eyesight. There missed socialization, playing on the school grounds, learning together, group activities and many other opportunities were missed by them.
Covid put a complete stop to schooling and learning. This forced organizations and educational institutions to use e-education platforms to facilitate distance learning and boost operational effectiveness.Thismethodhasgainedpopularitybecauseiteffectivelyaddressestheproblemswith institutional amendment efficiency. This technology can improve operational efficiency by automating some processes due to corporate resource planning software, which makes processes run more smoothly.
Colleges and School ERP Solutions Improve Operational Efficiency
Like the business, various processes are synchronized while keeping the schools and colleges. Throughout the lockdown, the educational sector has seen a significant shift as a result of the adaptation and deployment of new technology. This prompts educational institutions to transform into online learning platforms to support distant learning. Using virtual means to change institutional activities, both academic and non-academic, is a difficulty that is well addressed by this strategy. ERP solutions assist organizations in ensuring the efficiency and effectiveness of all everyday operational tasks.
Work process automation
Digitally organizing tasks that are intellectual in nature is a little difficult. Universities should modify their everyday operational activities in order to get around this. The continuous flow of information and data increases the chance of errors and wastes time. These elements play a part in the unfinished chores that remain. Nonetheless, everything could result in operational effectiveness with ERP cooperation. ERP solutions can handle any excess information and data because they are technologically advanced. Theintegration ofnumerouscollegeorschool workprocesses simplifies things for the institutions. ERP software ensures seamless efficiency, transparency, and synchronization across all departments in addition to increasing operational efficiency, along with planning various operational operations for administrators, colleges, instructors, parents, students, and the school ERP help in analyzing and accessing data for enabling intelligent decisions. Mundane task automation decreases workforce expenditure and facilitates rapid decision-making.
Promoting data security
The most significant asset of every school or university is its data. The information may be academic or not. A data leak might raise privacy issues and harm the institution's reputation. Institutions are closed, making data security an even bigger issue for all parties. The impact of a data leak can be catastrophic for operational effectiveness.
Student data in academic processes, such as report cards and exam results, are more susceptible to manipulation. Also, it is possible for dues and fee-related information to be lost or stolen, which affects the organization's budget. Also, hackers have the option of interfering with emails for their convenience.
Yet thanks to the use of a robust ERP software solution, any size education institution may now guarantee data security & backup. These systems can protect all of the institutions' operations because they are combined with various cutting-edge security features. In turn, this will contribute to greater operational effectiveness and personnel productivity. The adoption of ERP solutions is rapidly increasing right now. These software solutions provide enormous convenience. The systems aid in streamlining repetitious tasks, saving a great deal of time and preserving operational effectiveness.
Streamline management of data
An institute has different departments, and each has its specific tasks that they carry out without fail. At the same time, they must manage a mountain of paperwork; for example, teachers must keep track of students' academic progress in various extracurricular and educational activities. The administrative division must simultaneously track the institute's monthly or yearly expenses. The administration department must record the cash transactions, the students who participated in the assignments, etc., as the institute runs several events and activities throughout the academic year. Thus, institutesrequiretechnologies liketheStudent management system toenablecentralized data management to record and retain such a dynamic data collection.
Cost efficiency
The institutions must ensure they implement a high education system that incorporates innovative techniques. They also need to ensure that inefficient procedures don't impair institutional performance, although higher workloads often hurt the administrative department the most. Yet, if the institutions incorporate the right technologies based on their requirements, it helps streamline most of the tiresome chores. Moreover, solutions like ERP software link several systems into a user-friendly platform, allowing the admin to share the data gathered with various departments. Also, it relieves stress on the institution's staff, saves labor hours, eliminates errors, quickens all procedures, and boosts workflow efficiency, all of which reduce operating costs.
Benefits of implementing education ERP
• Improves resource management.
• Paperless campus management.
• Efficient administration.
• Automates payment process.
• Secured student information system.
• Initiates online examination and results.
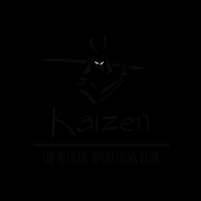
• Recording of attendance through a biometric system.
• Increases daily productivity.
• Quality education.
• Manages campus expenses, thus making it cost-effective.
• Potential for new opportunities
Boost effective communication
Each institution, whether a school, college, or university, must prioritize communication. During physical and social distancing, institutions' internal and external communication demands critical study. For a customized experience, the majority of institutions use bespoke ERP systems. This creates a productive contact line for parents, instructors, and students. Increasing communication by integrating several mobile applications tailored to each institution's stakeholder is best. The student's application provides updates and notifications on the timetable, exam schedule, assignment due date, events, etc. The teacher's app is similar in that it offers up-to-date attendance records, check answer sheets, projects, information about the syllabus, a timetable, etc. Parents and non-teaching personnel can quickly use this knowledge to improve the flow of communication between each stakeholder.
Specific modules significantly improve communication in schools, colleges, and universities. The primary module in ERP integration which sends updates to the stakeholders through message on personal mobile devices. For more personalized communication, several ERP systems are furnish with an in-built messaging system that allows staff, students, and non-teaching staff to share confidential information privately and instantly. Parents and non-teaching staff can immediately apply this information to enhance communication between all parties.
Fewmodulesnotablyenhancecommunicationineducationalsettingslikecollegesanduniversities. The main module is SMS integration, which uses messaging on personal mobile devices to provide updates to stakeholders. Several ERP systems have an integrated messaging system that enables instructors, students, and non-teaching staff to rapidly and privately share sensitive information for more individualized communication.
Conclusion
ERP software has enormous advantages for organizations to carry out daily tasks. This software helps educational institutions to perform academic and non-academic activities. The advantages and benefits are mentioned in the above context. ERP software has changed how educational institutions aremanaged. Everyone involved in the educational process can connect to the data they require and gain more awareness.
Ms. Kasaraneni Jeevitha MBA,
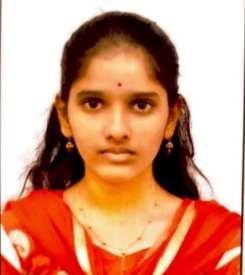
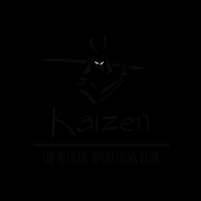
2022-2024 IBS Hyderabad
Reducing Risk in Your Supply Chain: How to Implement Effective Risk Management Strategies
Risk management is essential to a successful supply chain strategy and can help businesses protect themselves from potential losses, increase efficiency, and improve customer satisfaction. Unfortunately, many companies don't have the resources or knowledge to implement effective risk management strategies. This guide will provide an overview of the key risk management strategies businesses should consider implementing to reduce the risks associated with their supply chain. We'll look at identifying potential threats, creating a risk management plan, and developing processes and procedures to minimize potential losses. With the right risk management strategies, businesses can ensure that their supply chain runs smoothly and avoid costly failures.
Reducing Risk in Your Supply Chain: How to Implement Effective Risk Management Strategies
Risk management is essential to a successful supply chain strategy and can help businesses protect themselves from potential losses, increase efficiency, and improve customer satisfaction. Unfortunately, many companies don't have the resources or knowledge to implement effective risk management strategies. This guide will provide an overview of the key risk management strategies businesses should consider implementing to reduce the risks associated with their supply chain. We'll look at identifying potential threats, creating a risk management plan, and developing processes and procedures to minimize potential losses. With the right risk management strategies, businesses can ensure that their supply chain runs smoothly and avoid costly failures.
Identifying and Analyzing Risk in the Supply Chain
Before any risk management strategies can be implemented, businesses must identify and analyze the risks associated with their supply chain. The risks can be divided into two broad categories: internal and external. Internal hazards include those caused by the organization, such as poor inventory management, inadequate staffing, or inefficient processes. External risks are caused by factors outside the organization, such as natural disasters, economic conditions, or supplier issues. Businessesshoulddevelopacomprehensivelistofallpotentialrisksandevaluateeachtodetermine the likelihood of it occurring, the potential financial impact, and the risk mitigation strategies that could be implemented. This will help the organization understand the potential risks and the steps needed to minimize them.
How to Create a Risk Management Plan
Once the risks have been identified and analyzed, the next step is to create a risk management plan. The plan should include a detailed description of the processes and procedures that will be implemented to mitigate the risks. It should also include assessing the resources needed to implement the plan and the timelines for each step.
The plan should be regularly reviewed and updated to remain relevant and practical. Businesses should also consider conducting regular risk assessments to identify new potential risks or changes in existing risks. This will help the organization avoid potential issues and ensure an effective risk management plan.
Developing Processes and Procedures to Minimize Risk
Once the risk management plan has been created, the next step is to develop processes and procedures to minimize the risks. This can include implementing quality control measures, improving inventory management systems, and investing in new technology. Ensuring that all employees understand the processes and procedures and know the potential risks is also essential. This will help ensure that the risk management plan is adequate and the chances are managed effectively.
Key Risk Management Strategies to Consider
When developing a risk management strategy, businesses should consider the following key strategies: a. Establish clear roles and responsibilities: Defining clear roles and responsibilities for each team member will help ensure everyone knows their duties and is accountable for their actions. b. Implement effective communication: Developing effective communication channels will help ensure that everyone is aware of potential risks and can act quickly to address them. Create a culture of risk management: Promoting a culture of risk management throughout the organization will help to ensure that everyone is aware of the potential risks and is taking steps to minimize them. c. Investin technology: Investing in technology can help to reduce the risk oferrors and improve the efficiency and accuracy of processes. d. Use data to identify trends: Using data to identify trends and patterns can help to identify potential risks and enable businesses to take the necessary steps to reduce them. e. Monitor and review regularly: Monitoring and reviewing processes and procedures regularly will help ensure that the risk management strategy is effective and that any potential risks are managed effectively. f. Outsourcing Risk Management Services: Businesses may also consider outsourcing risk management services. This can benefit companies needing moreresources orexpertiseto manage the risks. Outsourcing risk management services can reduce costs and improve efficiency, as a team of experienced experts will handle the services. g. Implementing Automation to Reduce Risk: Automation can be a powerful tool for reducing risk. Automating processes and procedures can reduce the risk of errors, improve accuracy, and speed up processes. Automation can also help to reduce the risk of fraud or unauthorized access to sensitive data. Businesses should consider implementing automation solutions tailored to their specific needs and designed to reduce the risk of errors and improve accuracy. Automating processes and procedures can help companies to reduce costs and ensure effective risk management strategies. h. Monitoring Risk in Real Time: Monitoring risk in real-time can help businesses to identify potential risks quickly and take the necessary steps to address them. Real-time monitoring includes using data analytics to identify trends, tracking changes in market conditions, and monitoring customer feedback. Real-time monitoring can also help businesses to detect potential fraud and unauthorized access to sensitive data. Implementing real-time monitoring solutions can help companies identify and address potential risks quickly, minimizing possible losses.
The Benefits of Effective Risk Management
Effective risk management can help businesses to reduce costs, improve efficiency, and ensure that their supply chain runs smoothly. Implementing the right risk management strategies can help companies to protect themselves from potential losses and ensure that their supply chain runs smoothly.
Risk management can also help businesses to improve customer satisfaction. Companies can ensure their customers receive the best possible service by implementing processes and procedures to minimize risk. This can improve customer loyalty and retention and help businesses gain a competitive edge.
Conclusion
Risk management is an essential part of a successful supply chain strategy. By implementing effective risk management strategies, businesses can protect themselves from potential losses, increase efficiency, and improve customer satisfaction. This guide has provided an overview of the key risk management strategies companies should consider implementing to reduce the risks associated with their supply chain. With the right risk management strategies in place, businesses can ensure that their supply chain runs smoothly and avoid costly losses.
Ms. Rutuja R. Jangale
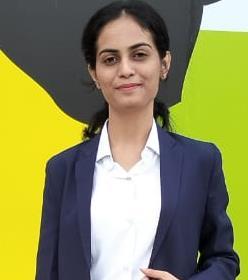
MBA, 2022-2024
IBS Hyderabad
Capacity Planning: Investigating How Companies
Can Use Capacity Planning to Optimize Their Operations and Maximize Their Financial Returns
Capacity planning is a critical process that companies use to manage the number of resources, including equipment, facilities, and labor, needed to meet their production demands. It involves forecasting future demand, identifying the available resources, and creating plans to optimize the utilization of these resources. Capacity planning is a complex process that requires a deep understanding of the business, market trends, and available resources. Companies can improve efficiency, reduce costs, and maximize their financial returns by optimizing capacity. This article will investigate how companies can use ability planning to optimize their operations and maximize their financial returns.
Understanding Capacity Planning
Capacity planning involves evaluating the demand for a company's products or services and determining the resources required to meet that demand. It is a crucial process for any organization that wants to remain competitive, maximize profits, and grow sustainably. Capacity planning is a continuous process that requires ongoing monitoring and adjustment to ensuretheresources remain aligned with the demand.
The primary goal of capacity planning is to ensure that a company has the right resources at the right time and quantity to meet customer demand. The process involves forecasting future demand and then creating plans to optimize the utilization of available resources. The projects should consider the current capacity, potential bottlenecks, and the availability of additional resources, including labor, equipment, and facilities.
This involves several steps, including: a. Forecasting demand: Companies must forecast demand accurately to ensure they have enough capacity to meet customer needs. They can use historical data, market trends, customer feedback, and other factors to make these forecasts. b. Identifying available resources: Once the demand has been forecasted, companies must determine the available resources to meet that demand. This includes identifying the equipment, facilities, labor, and other resources needed to meet the demand. c. Creating plans: Companies must create strategies to optimize the utilization of available resources. This may involve shifting production schedules, outsourcing specific tasks, or investing in new equipment or facilities. d. Monitoring and adjusting: Capacity planning is an ongoing process that requires monitoring and adjustment as demand and resources change. Companies must continually evaluate their plans and adapt to align with the direction.
Benefits of Capacity Planning: Capacity planning offers several benefits to companies that use it effectively. These benefits include: a. Improved efficiency: Companies can improve efficiency and reduce waste by optimizing capacity. They can produce more goods or services with the same resources, increasing profitability. b. Reduced costs: Capacity planning can help companies reduce costs by ensuring they have the right resources at the right time. This can reduce idle time, minimize downtime, and avoid overproduction. c. Maximized profitability:By optimizing capacity, companies can maximizetheirprofitability. Theycanproducemoregoodsorserviceswiththesameresources,increasing revenueandprofits. d. Improved customer satisfaction: Capacity planning can help companies meet customer demand more efficiently, leading to higher customer satisfaction.
Capacity Planning Strategies: Companies can use several capacity planning strategies to optimize their operations and maximize their financial returns. Some of these strategies include: a. Demand forecasting: Accurately forecasting demand is a crucial capacity planning component. Companies can use historical data, market trends, customer feedback, and other factors to make these forecasts. b. Resource optimization: Once demand has been forecasted, companies must determine the available resources to meet that demand. They can optimize the utilization of these resources by shifting production schedules, outsourcing specific tasks, or investing in new equipment or facilities. c. Inventory management: Managing inventory is a critical capacity planning component. Capacity planning is critical for companies that want to optimize their operations and maximize their financial returns. Companies can improve efficiency, reduce costs, and increase profitability by effectively managing their capacity. a. Improved Efficiency: Capacity planning helps companies optimize their operations by ensuring they have the right resources at the right time. By accurately forecasting demand and identifying available resources, companies can create plans to maximize the utilization of these resources. This helps to reduce idle time, minimize downtime, and avoid overproduction. b. Reduced Costs: Capacity planning can help companies reduce costs by ensuring they have the right resources at the right time. By optimizing the utilization of available resources, companiescanminimizedowntime,reducewaste,andavoidoverproduction.Thishelpstoreduce costs and improve profitability.
In this section, we will explore how capacity planning helps to optimize financial returns.
For example, a manufacturing company may use capacity planning to optimize the utilization of its production line. By accurately forecasting demand and identifying available resources, the company can create a production schedule that maximizes the utilization of its equipment and labor.
For example, a service company may use capacity planning to optimize the utilization of its staff. By accurately forecasting demand and identifying available teams, the company can create a schedule that minimizes idle time and maximizes productivity. This helps to reduce labor costs and improve profitability. c.MaximizedProfitability:Byoptimizingcapacity,companiescanmaximizetheirprofitability. By accurately forecasting demand and identifying available resources, companies can create plans to maximize the utilization of these resources. This helps to increase revenue and reduce costs, which improves profitability. d. Improved Customer Satisfaction: Capacity planning can help companies meet customer demand more efficiently, leading to higher customer satisfaction. By accurately forecasting demand and identifying available resources, companies can create plans to optimize the utilization of these resources. This helps to reduce wait times, improve quality, and increase reliability, which improves customer satisfaction.
For example, a retail company may use capacity planning to optimize the utilization of its stores. By accurately forecasting demand and identifying available resources, the company can create a store layout that maximizes its space and staff utilization. This helps to increase revenue by improving the shopping experience for customers and reducing costs by minimizing idle time and maximizing productivity.
For example, a healthcare facility may use capacity planning to optimize the utilization of its resources. By accurately forecasting demand and identifying available staff and equipment, the facility can create a schedule that minimizes wait times and maximizes the quality of care. This helps to improve patient satisfaction and increase loyalty.
Conclusion
Capacity planning is a critical process that companies use to manage the number of resources needed to meet their production demands. It involves forecasting future demand, identifying available resources, and creating plans to optimize the utilization of these resources. Companies can improve efficiency, reduce costs, and increase profitability by effectively managing their capacity. Companies that want to remain competitive and maximize their financial returns should invest in capacity planning and make it an ongoing process that is continuously monitored and adjusted to ensure that it remains aligned with demand.
Mr. Sanjay. K MBA, 2022-2024 IBS Hyderabad
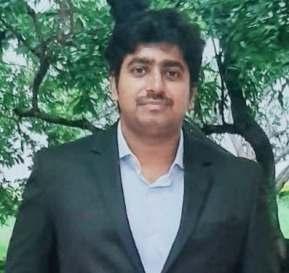
Online Grocery Business
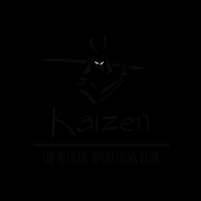
Operations play a prominent role irrespective of any organization, from manufacturing the product to delivering it to the customers. From reaching the product to the warehouse to retail shelves everywhere, operations play a dominant role, especially in cost-cutting strategies. In one of the organizations where functions work like blood, the relevance of processes at each stage will be explained in detail. It's crucial to consider competitive criteria while developing a grocery store, such as on-time delivery, quick delivery, partnership flexibility, and high quality. The attainment of on-time, swift delivery in relationships with partners and suppliers, including grocery shops, and relationships with customers are essential to process capabilities that must be developed. Additionally, it's crucial to have flexible relationships and channels of communication with consumers, partners, and suppliers.
There are quite a few challenges that many organizations face while setting up grocery stores, whether online or offline. A seven-step methodology creates a road map to set up the proper online grocery store.
Step – 1: business model: In this business model, we calculate the capital investments, operating expenses, break-even sales, and the return on investment on this particular business and sale forecasting and projecting the sales for the upcoming years. With this, one can understand how much they can spend on marketing and other related expenses. Without a proper business model, if anyone commences the business, it's like playing a game in the dark.
Step – 2: Product category Finalization: Product category plays a prominent role in an online or offline grocery store. One should make a list of classes that one wants to sell. It is essential to design the products based on the location, the margins, and the demand in that particular geographical region.
Step – 3: Layout planning: For a proper store layout, the position of the entry and the exit, the flow of goods inside and outside and the flow of people, the store size, and racks that fit within the store should be aligned with the product category finalization. The layout should be designed to be theft-free, and all the corners should be accessible to the cameras. In the case of ecommerce, one should be very careful of inverting the goods, macro checking and micro checking, packaging, barcoding, and others. The layout size should be designed to be easy to operate, and the turnaround time for each order should be minimized.
Step – 4: organization structure: Designing the organization structure is hiring people. Plan the human resource for each department and for what position we are hiring them, along with their job profiles in the reporting structures.
Step – 5: standard operating procedures: SOPs are the standard operating procedures for ecommerce supermarkets. One should develop very strong SOPs for the complete order management cycle, right from receiving the order to processing the order to fulfill the other order when it comes to the physical store. The complete SOPs need to be defined. The complete purchase accounts, warehouse, sales, marketing, HR, IT, inventory management, hygiene department, and security areonlineorofflinestores. Foreverydepartment, thestandardoperating procedures need to be defined clearly so that everyone within the organization, from top to bottom, should have a clear idea about the actual process that takes place within the organization. This acts as a bible for the smooth performance of the operational activities within the organization.
Step – 6: software evaluation: The most significant step is because the organization's vision is aligned with it. If we want to expand our stores or are running an e-commerce and want to set up a physical store, the software should be capable enough to adapt to both modes. The software should manage multiple chain operations and be competent in handling e–commerce operations in the warehouse, customer relationships, and inventory management. These are the basic modules that one requires.
Step – 7: recruitment and training: Make sure that we hire the right people for the correct position. Train the people in their respective work. They should be capable enough to run the store even in the manager's absence.
Specific stages of grocery retail supply chain planning
a. Procurement: Technology will impact sourcing strategy, making it simpler to monitor a supplier's performance based on factors including cost, quality, availability, inventiveness, and environmental impact. To choose a supplier based on previous and projected performance as well as market data, big data analytics will be extremely important. It will be more efficient to segregate products and allocate them in accordance with order trends. Technology will give suppliers access to information about inventory status and Point of Sale (POS) data, allowing for better promotion planning.
b. Warehousing: Increased decision support provided by technologies will impact the quantity, location, kind, and function of warehouses.
c. IoT, CPS, AR, and RFID will operationally enable visualization of indoor placement for all goods, machines, and people. For inbound and outbound order picking, mobile robots and people will be given the best routes and other directions to enhance product handling. Capacity planning is more effective by precisely estimating the needs for workers, machinery, and even shifts based on utilization and efficiency statistics.
d. Distribution: The distribution structure will be changed by technology, which will optimize delivery schedules, frequency, and delivery volumes. RFID and wireless sensor networks with temperature control would be used in tandem to monitor the quality of perishables throughout distribution. Automating inbound logistics, which will enable seamless information flow about entering goods, will alleviate the load on inbound logistics.
Conclusion
The grocery industry is changing primarily due to shifting consumer expectations and tastes. The supply chain, a crucial aspect of the grocery industry, is viewed as a field with enormous potential for technological intervention. Thankfully, technology is keeping up with the changing customer demands. IoT, RFID, CPS, big data analytics, and machine learning are becoming increasingly integrated into the supply chain strategy that directs the food industry. It brings about transparency, monitoring opportunities, waste reduction, automation, and optimization. These technologies have the potential to increase automated decision-making and decision support.
Ms. Gauri Sharma
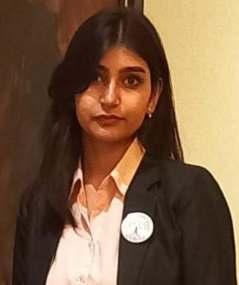
MBA, 2022-2024 IBS Hyderabad
ERP: Is it a boon to the supply chain strategy?
Supply chain management is crucial to a company's overall success, particularly in the manufacturing sector. To keep production on schedule, manufacturers rely on their suppliers and partnersto providethem with theappropriatekind and quantity ofresources at theappropriatetime. Nonetheless, "97% of respondents indicate supply chain management occupies a substantial amount of employee's time," according to a recent 2021 State of Manufacturing Survey. If not handled effectively, supply chain management may be a laborious and time-consuming process that can hinder productivity, cause delays, impair quality, incur extra costs, and lose money.
Supply chain management may become a crucial part of a wise business strategy as manufacturers grow. For easier and more successful outcomes, organizations can substantially benefit from streamlining and optimizing their supply chain management processes using enterprise resource planning (ERP) software.
What Is the Role of an ERP System in Supply Chain Management?
One cannot overstate how important ERP is to supply chain management. ERP software has significantly changed how organizations can operate, and it is directly related to corporate expansion. Successful ERP and supply chain management are essential components of business growth. These technologies, which may be obtained from supply chain specialists like QAD, combine supply chain operations under a single dashboard, enhancing visibility and streamlining cooperation between vendors and suppliers. Software for manufacturing ERP can automate supply chain procedures to increase employee productivity in other areas.
Benefits of Using ERP in a Supply Chain Management Strategy
a. Efficient Managing Demand & Procurement: Demand planning is automated by ERP, which generates demand when orders are received. The scheduling is carried out by the program when an order is received. Team members may more effectively plan production tasks and product delivery because they have access to real-time information on how resources are being used in production. Managing warehouse resources, material transportation, and other supply chain processes can all be automated or streamlined to increase efficiency.
b. Reliable Processing & Documentation: Invoices can be generated by an ERP system and sent directly to the customer once the products have been delivered. Alternately, make and send the necessary import and export papers for cross-border shipments. Additionally, it automatically compiles a history of shipments and deliveries to assure on-time delivery and better customer service while minimizing errors.
c. Enhanced Collaboration: ERP and supply chain management procedures are particularly useful for streamlining vendor and business coordination. When suppliers have access to your ERP system, they can collaborate with you more successfully to achieve your goals and eliminate bottlenecks. For example, they may identify when specific supply inventories are low and guarantee resource availability.
d. Increased Visibility: Businesses may develop smarter plans for using their resources, from parts to employees, with greater visibility and transparency. ERP software may give your team a thorough, real-time view of company operations, enabling you to pinpoint particular inefficiencies for better results and determine where things are going well and where they are not.
e. Cloud Capabilities: Although there are on-premise ERP system options, cloud ERP software has grown in popularity recently. Mobile access and dedicated data security are two of cloud ERP's main advantages. Ifyou usean ERP solutionhosted in thecloud, you can access thesystem from any location at any time using a mobile device as long as you have an internet connection. Due to the fast-moving nature of supply chains, this enables rapid action without necessitating the presence of the entire team.
Factors to Consider when Choosing an ERP System
a. Ease of use: ERPs support all aspects of your manufacturing firm, including coordinating your supply chain with your operations. The ideal ERP has user-friendly features for all users, from manufacturing and accounting to shipping and receiving.
b. Cost: Olderhosted ERP systems were expensiveto purchase and maintain, and they frequently failed to provide the return on investment they promised (ROI). You get more predictable expenses and a quicker time to value with subscription-based, cloud ERP solutions since they cover all running costs, including upgrades and storage.
c. Ease of Integration: Your ERP can be integrated with a variety of SCM solutions, but manual, custom interfaces can be expensive and difficult to manage. The same data model underlies unified SCM and ERP solutions on a similar platform, enabling native collaboration.
d. Common Data Model: ERPs and SCMs that operate from a single source of truth, a shared data model, guarantee data accuracy. Your team will save a lot of time integrating information and data points by implementing a consistent data model from the beginning.
e. Cloud-Based ERP: With all of your manufacturing business operations and data accessible at any time, from anywhere in the globe, and from any connected device, cloud-based solutions connect every link in your supply chain. This offers you the best visibility possible, enabling you to exert instant control and support where it is most required.
In conclusion, it depends on how an ERP system is chosen, which further defines how well it will benefit Supply Chain Management.
How Does ERP Improve Supply Chain Management & Efficiency?
ERP plays a crucial role in the efficiency of the supply chain in another area, namely business disruption, in addition to facilitating better forecasting, planning, and collaboration. Almost every industry may see market disruptors at some point, and if yours does, you must be prepared to successfully and swiftly adjust to continue doing business.
The COVID-19 epidemic has demonstrated how crucial effective planning and reaction are to maintaining enterprises. In order to create flexible sourcing and more integrated supply chain networks to respond to consumer needs, manufacturers are now putting less emphasis on cost reductions and more on supply chain adaptability, risk management, and speed. To boost supply chain operations and avoid significant losses when business disruptions occur, performance improvements such as more visibility, quicker decision-making, quick response times, and others are required.
How an ERP system can affect supply chain management functions?
a. Supply Chain Planning: In order to make sure that manufacturing can keep up with demand from customers, supply chain planning entails choosing the right marketing channels, managing promotions, and controlling the stock quantities and inventory needed. Hence, ERP systems provide a simple and flexible means of establishing and altering the parameters within which the supply chain functions.
b. Global Visibility: The ability to see SCM data with role-based or permission-based access has long been a hallmark of ERP software. Manufacturing companies can use the ERP to understand how and where their inventory is placed across the supply chain. As a result, management will be able to draught a well-planned production.
c. Evaluate Vendor Performance: ERP systems make it simpler for a company to evaluate both quantitative and qualitative aspects of different vendors. This aids management in improving performancein thepresent market and making betterjudgments. It facilitates ongoing monitoring and assists the purchasing department in choosing the vendor or supplier. Such information can aid in better negotiating when moving vendors.
d.AutomatedCustomerServiceProcess:Manybusinessesrely on enterpriseresourceplanning to streamline their customer service operations. Employees can ensure that their clients receive consistent care and that the back-office process is not hampered thanks to ERP's streamlined customer service experience. Automating all other resources enables businesses to foresee new items and respond to clients swiftly.
Ms. Kalyani Bhatt
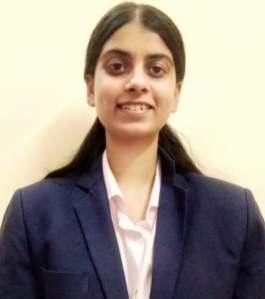
MBA, 2022-2024 IBS Hyderabad
Metal Manufacturing Energy Efficiency
As the world's demand for metals grows, the metal manufacturing industry is under increasing pressure to produce more while reducing its environmental impact. One way to achieve this is by improving energy efficiency in metal manufacturing. In this article, I will discuss the advantages of energy efficiency in metal manufacturing, common energy wastage, strategies for improving energy efficiency, case studies of successful energy efficiency projects, tools and technologies for measuring energy consumption, best practices for implementing energy efficiency projects, regulatory incentives and programs, and future trends.
Advantages of Energy Efficiency in Metal Manufacturing
Improving energy efficiency in metal manufacturing has several advantages. First, it can reduce energy costs significantly. Energy is a significant expense for metal manufacturers, and improving energy efficiency can lead to substantial cost savings. Second, it can reduce greenhouse gas emissions and other pollutants that contribute to climate change and air pollution. This can help metal manufacturers comply with regulations and improve their environmental credentials. Third, it can improve the reliability and resilience of the energy supply by reducing the reliance on external energy sources. Finally, it can enhance metal manufacturers' competitiveness by lowering operating costs and improving their reputation.
Common Energy Wastage in the Metal Manufacturing Industry
There are several familiar sources of energy wastage in the metal manufacturing industry. One is inefficient equipment, such as outdated furnaces or motors. These can consume more energy than necessary to produce the same output. Another is poor maintenance practices, such as failing to clean or lubricate equipment regularly. This can reduce the efficiency of the equipment and increase energy consumption. A third source of energy wastage is process inefficiencies, such as overproduction, idle time, or excessive scrap. These can lead to optional energy consumption to produce the desired output.
Strategies for Improving Energy Efficiency in Metal Manufacturing
There are several strategies for improving energy efficiency in metal manufacturing. One is to conduct an energy audit to identify areas of energy wastage and prioritize energy-saving opportunities. Another is to invest in energy-efficient equipment, such as high-efficiency motors or furnaces. A third is to improve maintenance practices, such as implementing a preventive maintenance program ortraining staff on best practices. A fourth is to optimizeprocesses to reduce energy consumption, such as adjusting production schedules or reducing idle time. A fifth is implementing energy management systems to monitor and control energy use in real time.
Case Studies of Successful Energy Efficiency Projects in Metal Manufacturing
In recent years, there has been a growing awareness of the need for industries to reduce their environmental impact, particularly concerningenergy consumption and greenhousegas emissions. In response to this challenge, many metal manufacturers have implemented successful energy efficiency projects, significantly reducing energy consumption and emissions.
One notable example of this trend is ArcelorMittal, the world's largest steel producer. To improve the energy efficiency of its electric arc furnaces, the company implemented various measures, including upgrading the furnaces with more efficient electrodes and waste heat recovery systems. These changes resulted in a 5% reduction in energy consumption and a corresponding decrease in greenhouse gas emissions. This project is a testament to the potential benefits of investing in energy-efficient technology, which can reduceacompany'senvironmental impact, loweroperating costs, and increase overall efficiency.
Another example of successful energy efficiency in metal manufacturing is Novelis, a global aluminium manufacturer. To reduce energy consumption and emissions, the company implemented a project to improve the energy efficiency of its rolling mills. This project included installing new motors and drives and optimizing the speed and tension of the rolling process. As a result, Novelis achieved a 10% reduction in energy consumption and a corresponding decrease in greenhouse gas emissions. This project is a prime example of how implementing energy-efficient practices can significantly benefit the environment and a company's bottom line.
Overall, the success of these energy efficiency projects in the metal manufacturing industry highlights the potential for other sectors to follow suit and reduce their environmental impact. By investing in energy-efficient technology and implementing best practices, companies can lower their emissions and improve their efficiency and profitability.
Tools and Technologies for Measuring Energy Consumption and Identifying Energy-Saving Opportunities in Metal Manufacturing
Several tools and technologies are available for measuring energy consumption and identifying energy-saving opportunitiesin metal manufacturing.Oneis energymonitoring systems, which can track energy use in real-time and identify areas of energy wastage. Another is energy modeling software, which can simulate different scenarios and identify the most effective energy-saving opportunities. A third is energy audits, which can provide a detailed analysis of energy use and identify specific areas for improvement. A fourth is energy-efficient equipment, which can reduce energy consumption without sacrificing performance.
Future Trends in Metal Manufacturing Energy Efficiency
Several trends will likely drive the future of energy efficiency in metal manufacturing. One is the increasing use of renewable energy sources, such as solar and wind power, to replace fossil fuels. Another is the development of new materials and processes that require less energy to produce. A third is adopting digital technologies, such as artificial intelligence and the Internet of Things, to optimize energy use and reduce waste. These trends will likely result in further energy efficiency improvements and reduced environmental impact.
Conclusion
Improving energy efficiency in metal manufacturing is essential for reducing costs, improving environmental performance, and maintaining competitiveness. By identifying areas of energy wastage, investing in energy-efficient equipment, optimizing processes, and implementing energy management systems, metal manufacturers can achievesignificant energysavings and reducetheir environmental impact. With the support of regulatory incentives and programs, manufacturers can further accelerate their progress toward a more sustainable future.
Ms. Twinkle Mehta MBA,
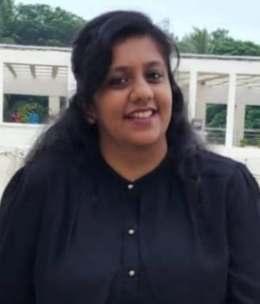
2022-2024
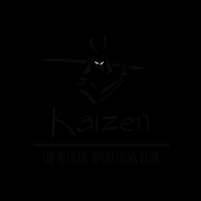
IBS Hyderabad
The Art of Process Analysis: A Blueprint for Streamlining Business Operations
As businesses grow and evolve, it becomes increasingly important to have efficient processes in place to ensure smooth operations. Process analysis is a powerful tool that can help enterprises to streamline their operations, identify inefficiencies, and optimize their processes. In this article, I will discuss the importance of process analysis in business operations, the steps for conducting a process analysis, tools and techniques, and case studies of successful process analysis implementations.
Process analysis is the systematic examination of a business process to identify areas for improvement. It involves breaking down a cycle into individual steps, analyzing each step, and identifying opportunitiesforimprovement. Process analysis aims to streamlineoperations, increase efficiency, and reduce costs.
Process analysis is an essential part of any business operation. It helps businesses identify inefficiencies and bottlenecks in their processes, leading to increased productivity, better customer satisfaction, and higher profits. By understanding and optimizing the processes, companies can ensure that they operate at maximum efficiency and provide the best possible service to their customers.
The Importance of Process Analysis in Business Operations
Process analysis is essential in business operations for several reasons. First, it helps businesses identify inefficiencies in their processes. This can lead to cost savings, increased productivity, and improved customer satisfaction. Second, it helps companies optimize their operations to ensure that they operate at maximum efficiency. This can lead to improved profitability and a competitive advantage in the marketplace.
Process analysis also helps businesses identify areas for improvement in their processes. By analyzing the process, companies can identify bottlenecks and places where the process can be streamlined. This can lead to faster cycle times, reduced lead times, and improved quality.
Steps for Conducting a Process Analysis
The process of conducting a process analysis can be broken down into several steps:
Mapping out the Current Process
The first step in conducting a process analysis is to map out the current process. This involves identifying all the steps in the process, the inputs and outputs of each step, and the people or departments responsible for each step. This helps businesses understand the current process and identify areas for improvement.
Identifying Bottlenecks and Areas for Improvement
Once the current process has been mapped out, the next step is to identify bottlenecks and areas for improvement. This involves analyzing each step in the process to identify areas where the process can be streamlined or improved. Bottlenecks are areas in the process where work is piling up or where there is a backlog of work. Businesses can optimize their operations to ensure maximum efficiency by identifying bottlenecks and areas for improvement.
Creating a New and Improved Process
The next step in conducting a process analysis is to create a new and improved process. This involves taking the findings from the previous step and developing a unique approach that is more efficient and effective. The new method should be designed to eliminate bottlenecks, reduce lead times, and improve quality.
Implementing the New Process
Once the new process has been developed, the next step is implementing the new strategy. This involves training employees on the new process and ensuring they have the resources and tools to effectively implement the new method. It is essential to monitor the implementation process to ensure that the new approach is followed and that any issues are addressed promptly.
Monitoring and Measuring the Effectiveness of the New Process
The final step in conducting a process analysis is to monitor and measure the effectiveness of the newprocess.Thisinvolvescollectingdataonthenewprocessandcomparingittothedatacollected on the old method. This helps businesses identify areas where the new approach must be fixed and adjusted.
Tools and Techniques for Process Analysis
There are several tools and techniques that can be used for process analysis:
Process Mapping
Process mapping is a visual representation of a process that shows the flow of work and the people and departments involved in each step. It is a useful tool for identifying bottlenecks and areas for improvement in a process.
Value Stream Mapping
Value stream mapping is a process analysis tool that shows the flow of work through a process and identifies areas where value is added and where waste occurs. It is a valuable tool for identifying areas where the process can be streamlined and improved.
Root Cause Analysis
Root cause analysis is a process analysis tool used to identify a problem's underlying cause. It involves asking a series of questions to identify the root cause of the problem and developing a plan to address the root cause.
Case Studies of Successful Process Analysis Implementations
Several examples of businesses have successfully implemented process analysis to improve their operations. One example is Toyota, known for its "lean" manufacturing processes. Toyota uses process analysis to identifyareas wherewaste can beeliminatedand techniquescan bestreamlined, resulting in increased efficiency and profitability.
Another example is Amazon, which uses process analysis to optimize its supply chain operations. Amazon employs a combination of process mapping and value stream mapping to identify bottlenecks and areas for improvement in its supply chain processes, resulting in faster delivery times and improved customer satisfaction.
Conclusion
In conclusion, process analysis is a powerful tool to help businesses streamline their operations, identify inefficiencies, and optimize their processes. Companies can successfully implement process analysis and improve their operations by following the steps outlined in this article and using the tools and techniques discussed. The next step is implementing process analysis in your organization and reaping the benefits of improved efficiency and profitability.
About Us
The word “Kaizen”, where “Kai” = change, “Zen” = good, signifies change for the better. In its birthplace Japan, the word Kaizen is imbibed as a process that many small continuous changes in systems and policies bring effective results than few major changes. This methodology applies to every department across different sectors.
Kaizen–TheOfficialOperationsClubofIBSHyderabadhasalwaysbeenaspiring“ConstantChange ad Evolvement”. We, as an organization work to inspire and aspire to the student community for the betterment of the future.
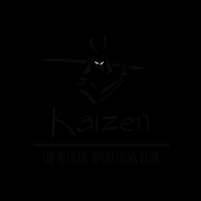
KORE – Kaizen’s Operations and Research Entity, one of our primary wings provide the students with a platform to improve and hone their technical competencies to meet the changing demands of the organizations. KORE’s sphere of influence includes Case-Based Research, Consultancy, Live Projects, and Workshops.LAKSHYA, an initiativeofKOREfocuses on improvingthereader's knowledgeabout Operations Management by providing insights in the form of articles on various operation techniques followed by different companies and also updating the emerging trends in the communities.
Diksha Jain EDITOR IN CHIEF - KORE
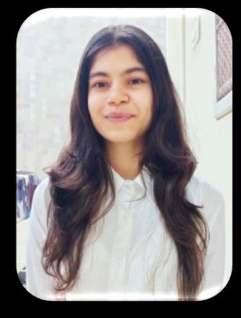
Club Kaizen – IBS Hyderabad
Batch 2022-2024
LAKSHYA is an academic print and is not for any commercial sale. Reliability and Responsibility, for sources of data for the article vests with the respective authors. Please feel free to drop in your suggestions at kaizenclub.ibs@gmail.com
KORE: Kaizen’s Operations & Research Entity. Kaizen – The Official Operations Club of IBS Hyderabad
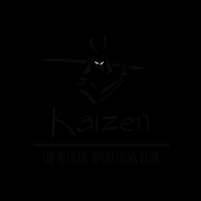
All Rights Reserved
Designed by