
6 minute read
MEET DAVID GREENHILL WITH GOOD WOOD DECONSTRUCTION

2x4s are salvaged from the framing of existing structures. Larger timbers are found less frequently. However, heavy timbers that were previously graded can be “grandfathered in”, meaning they do not need to be regraded before use in a second-life structural application.
David Greenhill established Good Wood Deconstruction & Salvage soon after the city of Portland implemented a deconstruction ordinance in 2016. According to a report from 2018, in the first year that the ordinance was implemented, approximately 70% of the material from deconstructed homes was salvaged (Wood, n.d.).
The ordinance sharply increased demand for deconstruction services, drawing newcomers to the market. Greenhill says, “Before the ordinance, there were only two deconstruction companies in all of Portland. Since the ordinance, there are now twelve companies competing for business.” While demand for deconstruction services has increased since the ordinance was implemented, revenue is primarily created by selling the collected salvage materials, with wood holding the greatest value. “Selling salvaged wood is the only way to actually make money in this business,” Greenhill explains.
There are many challenges to extracting wood from old homes. Greenhill’s team often finds wood boards covered in lead paint or residual adhesive from insulation. Removing these coatings requires more time and effort to remove than the wood is worth, making the wood unsalvageable. However,
Deconstruction ordinances provide unique insight into the development of a wood salvage material market that parallels that which will likely come for the mass timber deconstruction industry. It is plausible to expect that many of the same challenges and opportunities encountered through this process would also apply to a salvage mass timber market.
Efforts in Support of a Circular Economy
Parallel to these efforts, many are working to address concerns surrounding adaptability and deconstructability during the design process. These efforts are collectively termed Design for Deconstruction and Reuse (DfDR). This concept acknowledges that buildings are not static objects. Rather, they are dynamic structures that should be designed to undergo repair, renovation, replacement, and ultimately deconstruction.
To facilitate deconstruction and reuse, tools are being developed to track material composition, value, origination, and history throughout a product’s lifetime. The most well-known of these is the material passport. Material passports contain levels of data to identify product types, materials, structural properties, and specific components. A serial number or other identifier is physically attached or embedded in the component and can be used to lookup additional product information. Collectively, this information provides a basis of value and capability for present use, recovery, and reuse that will support the development of salvage material markets (Heinrich & Lang, 2019).
In several countries, policy changes are being implemented to promote circularity by shifting responsibility for reuse to manufacturers. Extended Producer Responsibility (EPR) is a policy approach where a producer’s responsibility for a product is extended to the post-consumer stage of the product’s life cycle (Love, 2007). For example, the United States has mandated takeback programs for household batteries, electronics, items containing mercury, packaging, and pharmaceuticals. Similar take-back programs have been implemented for timber in several countries in Europe, but have excluded treated timber (Love, 2007).
Further development of material passports and EPR policies will be critical to make salvage mass timber markets possible in the future. Given the existing momentum behind the DfDR movement, the hope is that by the time that many mass timber buildings are approaching the end of their first life, precedent for salvage markets and policies will already be well established.
Manufacturer’s name/details
Manufacturer’s article number
Temporal information
Product name/brand
Unique Product Identifiers
Product’s main function
GTIN or EAN number CAS number
Definitions And Abbreviations
Circular Economy: Aims to keep materials, components, products and assets at their highest utility and value always. In contrast to the ‘take, make, use, dispose’ linear model of production and consumption, material goods are designed and produced to be more durable, and to be repaired, refurbished, disassembled, and reused in perpetuity – thereby minimizing resource use, eliminating waste, and reducing pollution (The Delphi Group, 2021).
Upcycling: Reuse in such a way as to create a product of higher quality or value than the original (Heinrich & Lang, 2019). Upcycling avoids the need for raw material inputs, energy required for processing, and minimizes the embodied carbon inputs.
Downcycling: Reduces the value and quality of a material in contrast to upcycling procedures (Heinrich & Lang, 2019).
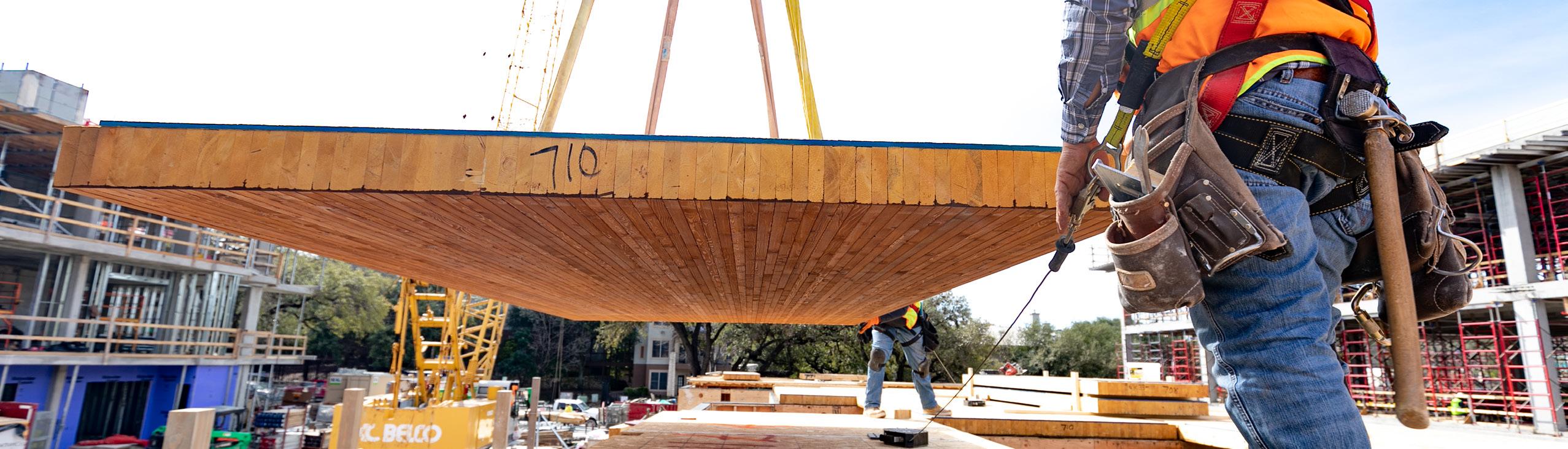
Cascading: Promotes the use of the waste material in its highest value alternative for as long as possible, and only resorts to energy recovery after its alternative value has diminished (Holgmeier et al., 2013).
Design for Deconstruction and Reuse (DfDR): The design of buildings to facilitate future changes and dismantlement (in part or whole) for recovery of systems, components, and materials, thus ensuring the building can be recycled as efficiently as possible at the end of its lifespan (Critescu et al., 2020).
Material Passports: Data sets describing defined characteristics of materials in products that give them value for recovery and reuse (Heinrich & Lang, 2019).
Extended Producer Responsibility (EPR): An environmental policy approach in which a producer’s responsibility for a product is extended to the post-consumer stage of the product’s life cycle. This approach provides incentives for producers to take responsibility for the environmental impact of their products throughout their entire life cycle (Love, 2007).
Takeback Programs: Programs that mandate that producer’s takeback or recycle products at the end of their useful lives (EPA, 1998).
A Historic Record Of Wood Reuse
While there is a limited amount of data available on mass timber’s potential for deconstruction and reuse, there is plenty of historical data available to demonstrate the reuse potential and durability of its core substance -- wood.
Serial Reuse of Ship Timber in Ancient Egypt
The earliest recorded example of wood deconstruction and reuse was in seafaring ships in ancient Egypt (Creasman, 2013). The Egyptians relied upon imports for timber for the construction of seafaring ships used to transport supplies. During the New Kingdom, the Egyptians’ faced challenges importing virgin timber, and it became common for timber from retired ships to be reused in new ships (Creasman, 2013). These ship timbers were joined using mortise and tenon joints and lashed together with rope. Markings were used to facilitate correct placement during the reassembly process. Recovered hull and deck planks have numerous and sometimes overlapping mortises, indicating serial reuse (Creasman, 2013). Creasman suggests that in ancient Egypt, the “Proclivity for repurposing ship timber was a matter of practicality…reuse was the rule rather than the exception (Creasman, 2013).” This historical evidence demonstrates the immense durability and versatility of modular wood elements.
Early Glue-Laminated Timber
Glue-laminated timber is the earliest form of mass timber known to be used in building construction and many of the earliest glue-laminated timber structures are still in use today. These structures demonstrate the durability and versatility of mass timber construction.
The oldest of these examples preceded any formal patents and was built in 1866 by architect Josiah George Poole. The building was designed to serve as an assembly room for King Edward VI College in Southampton, England. The project required speedy construction on a tight budget, which is ultimately why glue-laminated timber was used (Leonard, 2008). The building is still in good condition and continues to be used as a ceremony venue (Figure E.)
In 1934, the first two glue-laminated timber structures were built in Wisconsin. The first was a high school gym in Peshtigo and the second was a storage building, known as “Building Two” for the Forest Products Laboratory in Madison (Figure F.) The high school gym was converted to a library in the 1980s and is still in use today (Lehman, 2018). “Building Two” served as storage building, a laboratory, and as a lecture hall over the years, but was ultimately decommissioned in 2010. After decommissioning, recovered glue-laminated timber arches were tested to evaluate the loss of structural performance. Minimal loss of structural performance was found in all arches except one, which was exposed to a significant amount of water from extinguishing a fire many years earlier (Spartz, 2014).
Thirty-five years earlier in 1901, the first patent for gluelaminated timber was issued in Switzerland to Otto Karl Friedrich Hetzer, soon followed by a patent for curved glulam. The use of glue-laminated timber soon spread throughout Europe, and became especially useful for temporary structures (Lehman, 2018). At this time, glulam was more affordable than steel, quicker to assemble/disassemble due to its light weight and standard connections, and offered a more elegant, finished aesthetic than steel construction
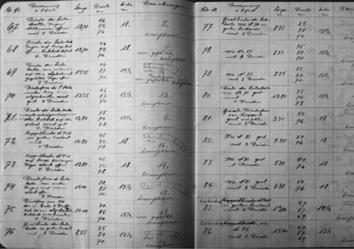

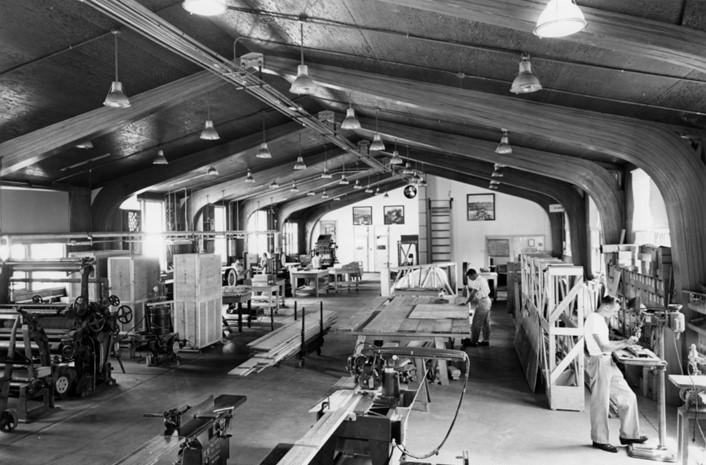
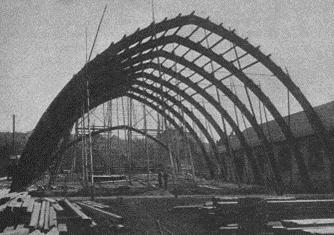
(Haddadi & Rinke, 2020). Many of these temporary glulam structures were large in scale, in use for only weeks at a time, and intended to be made available to a secondary market following its disassembly. For this reason, these structures used simple, repetitive, and reversible steel connections. Glulam elements were kept light weight, modular, and easy to transport (Haddadi & Rinke, 2020). One example of this was a temporary hall for the Swiss singing festival near Zurich, which was constructed in 1911 and used for one week before disassembly (Figure G.). It was common for secondhand glulam components to be sold either as a full-building package or as singular components. There are even examples of components from multiple buildings being combined within a new structure (Haddadi & Rinke, 2020). Figure H. shows an inventory of glulam pieces from a pavilion at the National Swiss Exhibition that was used to facilitate resale.
The Evolution of Adhesives
Since the earliest glue-laminated structures were built, several breakthroughs have been made in the development of wood adhesives and lamination techniques to make mass timber components significantly more durable and waterresistant.
The earliest glue-laminated beams were bonded using casein glues. Casein glues are derived from animal milk and were used as far back as ancient Egyptian times (Saleh Pascha, 2014). Casein glues are hardly waterproof, have low shear strength, and require long setting times. For this reason, casein glues limited the application of glulam construction until 1928, when the first cold-curing synthetic resin glues were introduced (Saleh Pascha, 2014). Referred to as “Kaurit,”