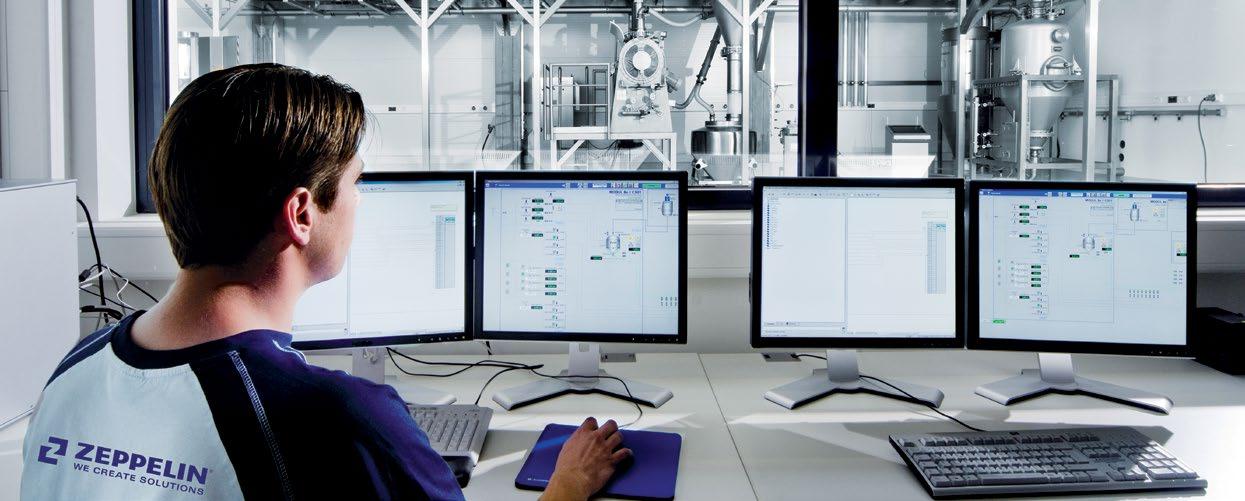
2 minute read
Equipment thinks for itself
Zeppelin Anlagenbau is working on a transition from the previous controller to a new system called “MIRA” whose capabilities are designed to equal the functionality of an MES (Manufacturing Execution System).
The device on the table in Rödermark looks almost inconspicuous, but it’s the first representative of a new generation. Measuring approx. 50 x 30 x 20 cm, the grey box contains a computer-controlled water mixing and metering system developed by Zeppelin w hich no longer needs a PLC (programmable logic controller) as u sed in the past. The computer is programmed in a high-level programming language and is therefore capable of platform-independent communication with any device or control system.
It is currently integrated into the Prisma Web2, a batch management system which supplies the controller with a recipe, process, batch traceability and stock management, even when using a multi-stage production process, and involves the operator via an HMI (Human-Machine Interface). Up to now, Prisma Web2 has communicated with the respective equipments` PLC via Ethernet for control purposes, and provides visualization on the operator’s PC via a bus system.
The new water mixing and metering system can be integrated into this world, but is also usable for a future in which process control is no longer based on PLCs but on industrial computers instead. A computer of this kind is not only more efficient than any PLC, but can also be individually adapted, re-programmed, expanded or exchanged at any time, and for example it can thus also replace any other control computer. These computers can be used as intelligent decentralized controllers. The feature that clearly distinguishes them from previous controller installations is their ability to interlink and to analyze data.
At the iba trade fair, Zeppelin presented a process automation product that analyzes an optimum end-product to create derivatives from it for product optimization. Described in simple terms, this is designed to reveal the points at which adjustments should be made to achieve this production optimum, even in the presence of numerous mutually interacting input and output parameters.
The water mixing unit is the first practical application of Zeppelin’s new MIRA automation concept. MIRA communicates both with control computers and with PLC plants, and is therefore able to map Prisma Web2’s basic functions in the future. In addition, it will combine data streams from controllers with sensor data and analyze them, will create
Zeppelin Automation
The Zeppelin Group which operates worldwide, is working in various fields, one of which is plant engineering. This in turn supplies raw material handling components and plants to the food industry, the chemicals & plastics industry and the rubber and tire industry. The plant engineering head office is in Friedrichshafen, whereas the “Food” business unit is based in Rödermark near Frankfurt. Automation, including control cabinet construction for the plant engineering. Is also based in Rödermark. With a total of 75 employees, plant design concepts are realized in the business units.
integrates your automation and digitalization

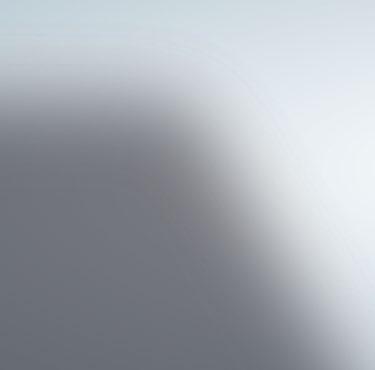
++ quality-relevant relationships based on empirical values or chemical/physical theories, and will suggest solutions. Thus the equipment will no longer just be controlled and regulated, but will also “think” for itself.
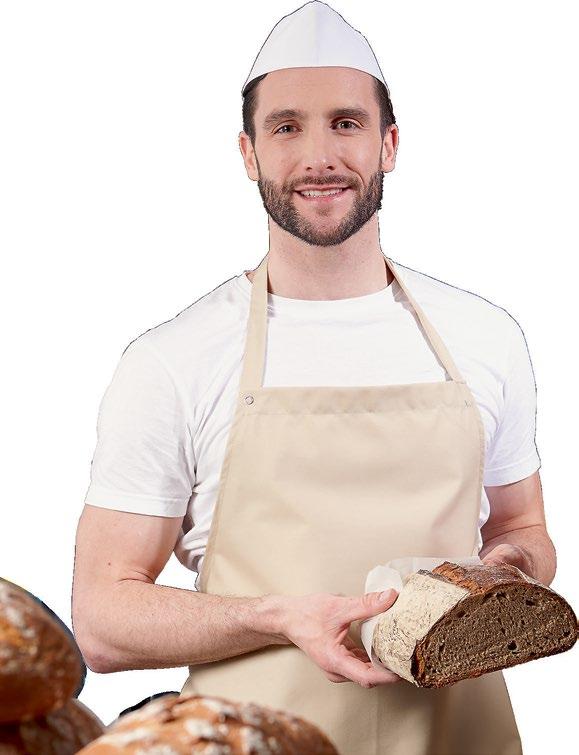
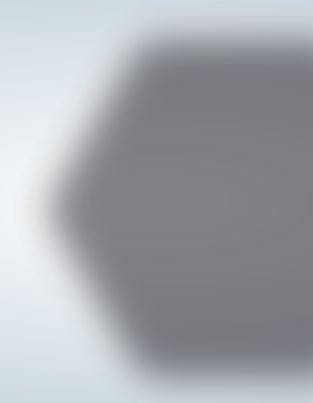
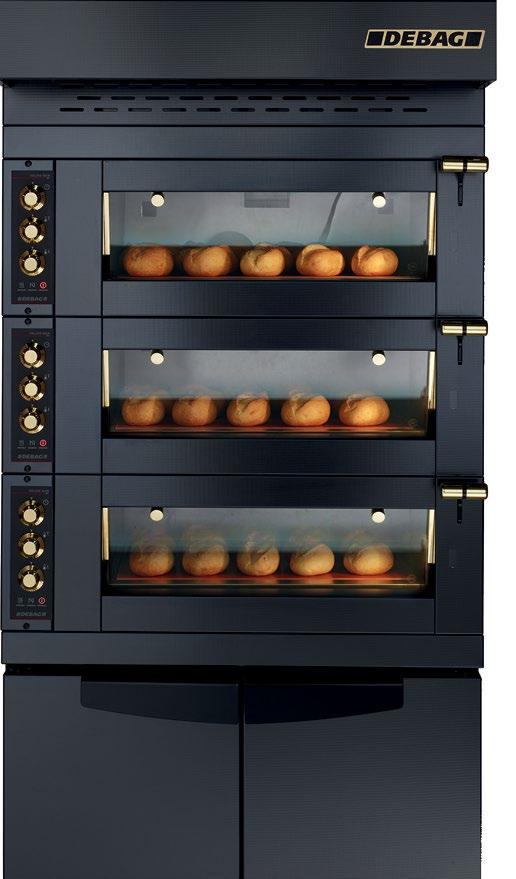
The application of MIRA in food production is on the agendas of the development departments in Rödermark and Friedrichshafen for the coming months and years. Currently, a search is ongoing for a partner that is interested in implementing a pilot project with Zeppelin Systems. +++
++ MIRA Control, implemented for a water mixing unit (WMU) using an industrial PC instead of a PLC
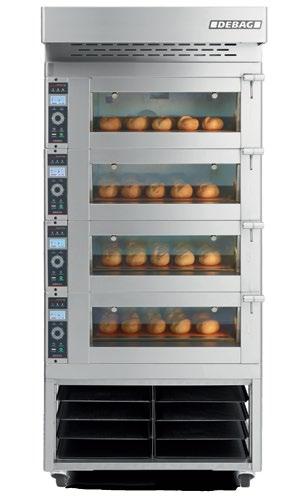
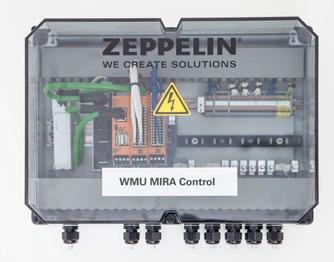