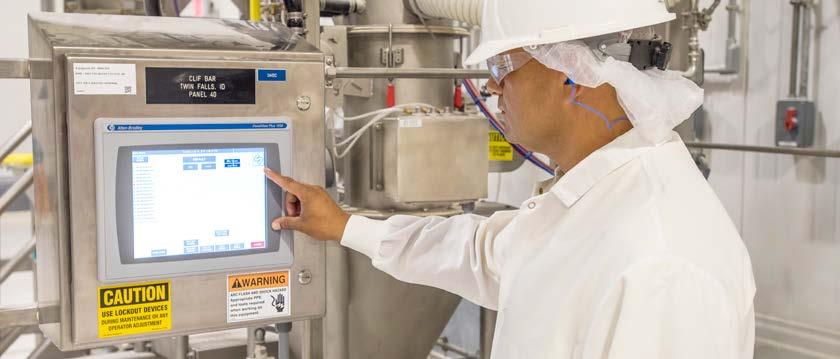
8 minute read
Shick Esteve: Traceability and recipe management
Traceability levels
1. Automation level (ES-PLC) 2. SCADA level (Clarity/Es-Track) 3. MES level: MY-PLANT 4. ERP level: customer’s ERP
Traceability and recipe management
It takes a great deal of synchronization to consistently follow recipes and dose ingredients with maximum accuracy. Automation not only guarantees precision and efficiency in weighing and dosing, but also brings the benefits of achieving complete traceability of the materials processed, in as much detail as each manufacturer wants.
+In recipe management, Shick Esteve’s silo and dosing systems, developed with expertise from staff at facilities in Kansas City, Missouri, USA and Rians, France and delivered worldwide, comprise the automation and PLC level, in production, and the monitoring and traceability level supported by its Clarity Process Management. The PLC acts like a local, safe data storage location as well, even if the network connection is temporarily lost for any reasons. “In this way, we can ensure that the customer will not lose any data, as it will upload what the system missed as soon as the connection is re-established,” explains Yann Weissgerber, director of International Sales & Marketing, Shick Esteve Rians. On top of this, the SCADA system within the Clarity Software Suite collects data and makes user-friendly information available for the user. From this database, information can be shared with other software used in the facility, as needed - even with multiple systems simultaneously (i.e., MES, ERP). The Clarity Software Suite converts the PLC data to a software database, which makes it ready for sharing with virtually any software on the market.
Data accessing is streamlined
The ERP will feed SCADA production orders (including order numbers), and the SCADA will prepare the production plan. Once the batch is produced, the SCADA updates the ERP: it will then upload recipes, production orders, as well as traceability, and ingredient information into the ERP. It should be noted that the SCADA will share real data from production (for example, if the recipe for a certain batch called for 200kg of flour, it will accurately report that 201kg were used if this is what actually happened). In addition to the recipe details, the ERP will add information for each batch the number, names, production lines, and delivery information.
This communication between the two systems cross-referencing programmed data with real data begins from the moment flour arrives into the silo: the SCADA will measure and report to the ERP if the 20t of flour programmed to fill a silo were in fact 21.5t, for example. This is valuable information for inventory management, which is why the ERP should always be updated with real data regarding production.
Managing dosing errors
If dosing is fully automated, there are no mistakes regarding accuracy; the system is able to control its own operations to the extent that it will stop dosing if there is no incoming material in the buffer for the scale, for example – and an alarm will alert operators. The process is monitored at each step, to ensure the precise quantity of each ingredient in the
About Shick Esteve
Shick Esteve is a complete ingredient automation provider. It designs, manufactures, installs and services ingredient automation systems for customers worldwide. For more information, visit www.shickesteve.com/fr.

© Shick Esteve
About Linxis Group
LINXIS group’s purpose is to leverage our collective expertise to develop and implement specialized equipment solutions, enabling our customers to be best-in-class industrial players wherever they operate. www.linxisgroup.com
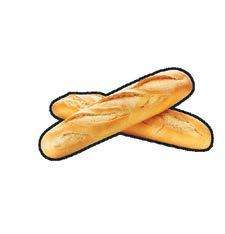
recipe has left its silo and automated scale and has also arrived at the dosing station in the production area. This combination virtually eliminates mistakes. Common errors are human-made, so the PLC tracks all events that occur during operation, for each of the system users. For manual feeding, predefined tolerances will allow processes to be performed and the sequence of ingredients to be dosed; if these values are exceeded, the system will not proceed to the next step, as a fail-safe measure. Moreover, if the wrong ingredient reaches the scale, it is set to not show any values and subsequently interrupt the process.
Gathering, analyzing and storing data drive traceability
Shick Esteve’s Clarity Process Management stores the manufacturer’s PID (control mechanism that automatically applies an accurate and responsive correction to a control function, eds.) with all the physical ingredients in production. The level of ingredients available in silos or bags is monitored; every time a bag is changed, the system is also informed about the lot number of the newly added ingredient, either by inputting such data manually or with the help of a bar code reader. In this way, all production data where a certain ingredient was used becomes available, the quantities received and used, the specific type of ingredient, including that ingredient’s delivery information (actual weight, truck plate numbers, driver’s name, etc.).
“We always compare what we are using on the line and what remains in the silo, to make sure that flour isn’t lost somewhere. If weight variations are detected, compared to what the container should have, this indicates a potential leakage (which should be looked into), for example,”
ADVERTISEMENT
TECHNOLOGY MEETS BAKER‘S CRAFT.
FOR YOUR PERFECT BUNS.
GENTLE DOUGH PROCESSING Menes-H dough sheeting line
Fluffy ciabatta, tasty artisan bread or crusty baguette. Produce high-quality products with the Menes-H dough sheeting line. The line combines high weight accuracy with perfect handcraft quality.
GENTLE DOUGH SHEET FORMING “Twin Sat” satellite head
Two satellite rollers positioned one above the other produce a virtually tension-free dough sheet. The Twin Sat module reduces high mechanical load to a minimum while gently forming the dough sheet.
“H“
HYGIENIC DESIGN
Scan here & follow us
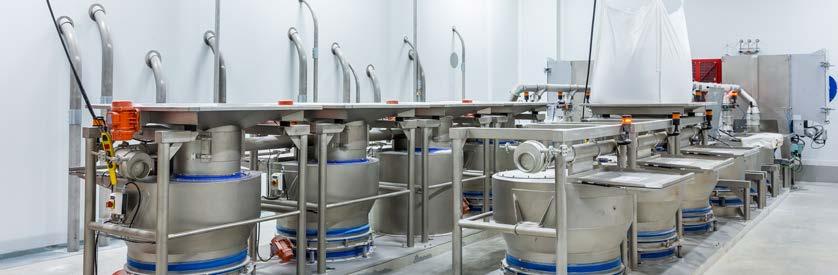
Weissgerber explains. There are different ways to detecting a flour leakage. Shick Esteve recommends monitoring the vacuum/pressure curve of the pneumatic transfer in the traceability system in real-time; if there is a drop, respectively a loss of vacuum or pressure, the operator should inspect the line for the cause, which can be a door that was opened for maintenance and not closed correctly, or a broken gasket allowing flour to escape. To monitor the process accuracy, capability is used. This is “a set of indicators that verify whether the measurement results for all produced parts are within the specified tolerances,” the specialist from Shick Esteve adds. This concept is an estimate of the risk of nonconformity of a characteristic of the product. The measurement unit Σ shows the accuracy of the weighing cells. Values under +/- 3Σ for this measurement are within variations of actual ingredient compared to values defined in the recipe that would not prompt reasons for alarm; values higher than that mean the system should be checked. Industry statistics show that 68% of the dosing falls into +/-1Σ variations; 95% are in +/-2Σ, 99.7% are within +/-3Σ; Shick Esteve’s systems calculate this curve to ensure minimum deviations occur, according to these statistics. For example, on a dosing station of 200kg, the weighing cells have an accuracy of 200g, the specialist illustrates.
Accuracy in dosing
From an automation standpoint, the physical state of the ingredient (solid, powder, liquid) does not bring any challenges to the dosing process. The PLC does not consider this aspect, but only the parameters that will correctly describe the flowing characteristics of the specific ingredients the manufacturer is using. Ensuring accuracy in the dosing process relies on the correct assessment of this trait instead. Shick Esteve manufactures dosing screws dedicated to each ingredient, with unique profiles and shapes to match materials with very different flowing behavior, such as flour and sugar, for example. To optimize accuracy, as soon as the quantity for dosing is in the screw at the desired material density, a valve closes the infeed; at the end, the pitch of the screw is extended to guarantee the density will be a stable 0.6 and increase accuracy, respectively. The company can provide specialized screws in around 25 different lengths and diameters; plus, Shick Esteve can recommend the best fit for each ingredient from over 100 possible combinations of pitch configurations that it has developed.
Generally, the variations between types of flour are minor, by extension, each type of solid ingredient will behave similarly.
For liquids, anything from water, oils, sweeteners, cream yeast, chocolate, etc., Shick Esteve’s portfolio includes dedicated systems and bulk tanks or intermediate bulk container (IBC) storage solutions, indoor or outdoor installations. Pumps and flow meters are chosen according to the type of liquid, and a buffer ensures that the pump never works dry and allows the operator time to change the IBC. The size of the buffer is directly proportional to the time it allows. “For example, if the IBC is empty, if we use a 20l buffer tank, the customer will have 20 minutes to change the IBC,” illustrates Weissgerber. Choosing the right size for the buffer depends on the workflow and on the overall organization. To combine different pieces of standard equipment for the optimum line-up, the company requests liquid samples and analyzes them (this process is similar for solids, too).
To the future
To manage all these operations, software will be key, not just in itself, but also in the way it will work. “The kind of data exchanged has remained mostly the same over the past 10 years, but the way in which we are going to support this data will be different,” the specialist highlights. In the coming years, all data, which is now stored via the software in a network on a local server, will be transferred to the cloud. The software will also be located on a web server and will collect the data from the sea of information stored in the cloud, following general software trends towards transferring computational power online so that I would not be needed in local devices. This will also be beneficial in terms of maintenance, anticipates Weissgerber. An access interface will be the only necessary tool to connect to these data capabilities – physically, this will mean any device, even a mobile phone, located anywhere in the world. +++