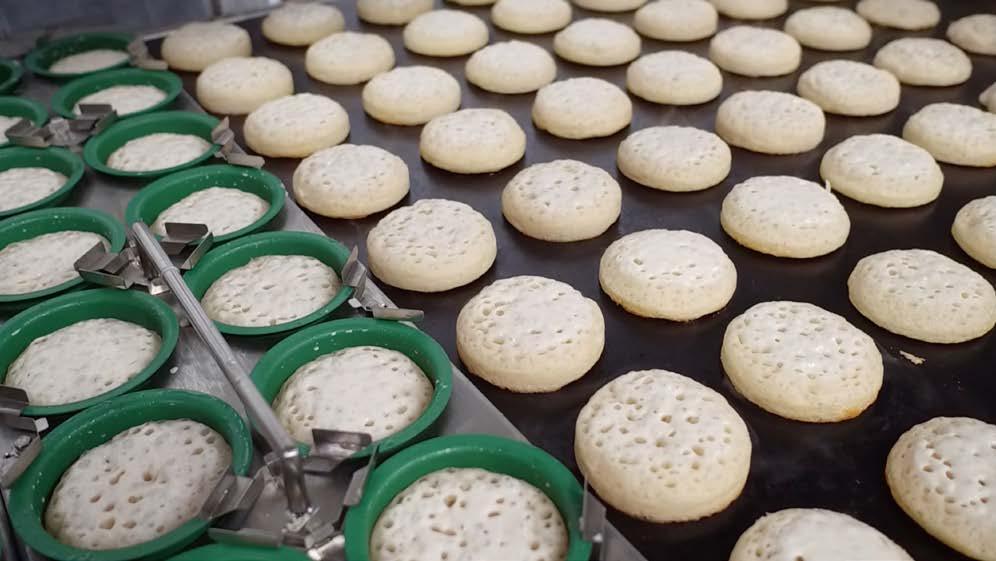
8 minute read
Sugden: Solid engineering supports expansion, new business
Solid engineering
Sugden Ltd is a leading designer and manufacturer of hotplate systems. Less than one month into the year, the UK-based company had made two major business announcements: the launch of a Mini Hotplate system for SMEs, and the acquisition of AMF’s VanderPol Waffle Systems, a fitting addition to its portfolio of Stroop waffle, Funcake, Belgian and Soft waffle production lines.
+Against a backdrop of preservation, a sentiment that defined business in 2020 including bakeries, this UK-based company marched on. It settled into a new facility that greatly expanded its capabilities, developed and launched a new solution with a smaller footprint, and added an entire range to its portfolio with the purchase of the waffle specialist. How did it manage to do all of this, while navigating the same volatile 2020 as the entire industry? Chris Baldwin, managing director, granted baking+biscuit international an interview, just as the news of the acquisition was breaking, and shared the company’s strategy, and what it plans going forward. The VanderPol deal had been two years in the making, we learned. Initially, Sugden was not in a position to make the acquisition, as at the time it was still running operations from the old factory – a smaller facility with room only for the manufacturing of one or two lines at the most. At the same time, the new 35,000sqf facility was under construction, which would be home to the production of up to six lines simultaneously. Sugden moved to the new factory in
September 2019, just before the COVID-19 measures took hold. By February 2020, two brand new lines had left the factory, for Germany and the UK.
Thriving in survival mode
A project was signed for three lines in Australia in March 2020, in addition to © Sugden Ltd other projects in the UK; four lines in total were slated to be made in the new facility over the 12 months from the start
Chris Baldwin, managing director of the pandemic (down from the initial Sugden Ltd six, potentially eight). “We can even survive with three-four lines a year; we are lean enough to do that without losses. We are in a good position to manufacture higher volume (but that is not needed at the moment) and I think that is critical for any business. But we could do more,” he tells us. As a light at the end of the tunnel was starting to flicker midway through the year, the decision was taken to proceed with the VanderPol acquisition as well. The timing may not have been ideal under the circumstances, “But it was a great opportunity that wouldn’t come around again,” Baldwin adds. The deal was closed in December and it has proved to be to Sugden’s advantage to complete the company’s portfolio in this way, and potentially
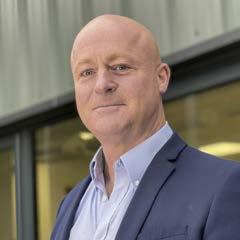
Sugden Ltd
Founded in 1972, Sugden Ltd is based in Nelson, Lancashire, and employs 38 people. Its solutions, made exclusively in Britain, go to customers worldwide, from Europe through to Australia.
The company recently acquired the intellectual property of VanderPol Waffle Systems, meaning it can now manufacture, supply, and install a wide range of industry-leading Stroop waffle, Funcake, Belgian waffles and Soft waffle systems, further widening its solution capabilities.

© Sugden Ltd
double its overall capacity with products complementing each other. The move had been in the pipeline for months ahead of the public announcement; for Sugden, it entailed intensive preparations prior to the winter holidays, before the transfer was given the green light.
“We work generally on a 40-50-week delivery schedule; manufacturing we can safely predict, but the problems start with shipping and installing; 50 weeks from December 2020, we should be in a place where we can travel safely [and avoid such issues, for the most part],” Baldwin details his calculations for putting these plans in motion. “When markets open fully, we’ll be in a great place to install and capitalize on our acquisition,” he concludes. In this sense, it was the perfect timing to expand.
A transition
Sugden has worked very closely with AMF globally. At this stage, the technical departments are finalizing the file transfers for seamless integration of VanderPol’s systems, which is already listed on the company’s website. The process is further helped by the similarities between Sugden’s existing lines and the new waffle systems (and related processes). Besides, AMF will provide support on projects going forward to help with the transition. At the end of the day, to get up-to-speed with the new lines, “We are very good engineers; we understand drawings,” the specialist summarizes the company’s expertise. In the beginning, 3-4 additional weeks are scheduled, to ensure the new lines perfectly match the blueprints.
As it masters the development of the VanderPol portfolio, Sugden will also look into improvements in all aspects. For example, all its existing equipment is insulated, which helps reach up to 50% in energy savings – such efficiency features will also be analyzed for the new technology. The expanded production means two specialists are joining the projects team, a design engineer and a production supervisor. Also, “We have another design engineer joining the team, and more personnel on the fabrication side, and the installation side; we are going to expand even more in the service and spares department,” he highlights an area in high demand. Solid engineering is at the base of perfecting the systems and related services, underlines Sugden’s MD.
Since the announcement, inquiries have been pouring in from all over the world, for the entire range of newly-added products. Overall, English muffins and crumpets are among the products that will remain popular this year, Sugden anticipates. Emerging markets worldwide are requesting lines for crumpets and pancakes – which is why the Mini Hotplate was introduced.
The strategy on overseas installations is to consider the installation itself as a separate contract, which could partially be outsourced locally to work around traveling and/or quarantine restrictions. “We have to work smarter and for the expansion of the range, we need to look into local markets anyway,” Baldwin explains. It would be difficult to put together a team to work overseas for weeks at a time, compared with engaging local engineering companies. Since the new facility allows for the lines to be fully commissioned in-house, the installation on-site can be reduced by at least 30%.
Care for the equipment
The semi-automatic Mini Hotplates are another recentlyfinalized project, featuring massive upgrades to support emerging markets and smaller, craft, or niche businesses. It is designed for flexibility to support anything from bunny
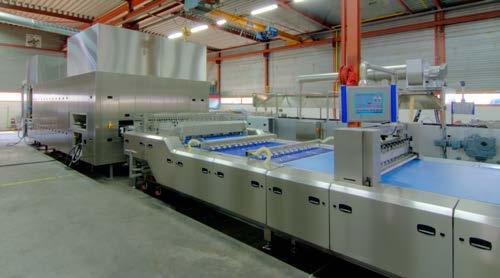
© Sugden Ltd

rabbit crumpets, pancakes, to seasonal-themed products, with a capacity of 800-1,200 pieces an hour and the expertise gained from full-scale lines. On an 8-hour daily up-time, the ROI for such a system can be as little as 12 months. “The strategy behind developing this is to not only fulfill a requirement but also to introduce products into an area that isn’t aware of specialties such as crumpets,” he highlights. In five years, these markets would then be requesting larger-scale lines.
The Mini Hotplate incorporates all the technology features used in the company's larger systems. Any batter-based product can be made with this equipment; crumpets in various shapes are also supported, as well as pancakes. It can also be used for sheeted products such as potato scones and Welsh cakes. Gluten-free is also a well-fitting segment for this equipment. The depositing process is automated – 12 x 8 rows are deposited at the touch of a button, which are then timed according to the recipes and are turned manually when the alarm prompts it, then removed at the next signal. Custom-made solutions can be engineered for any specific requirements; challenges arising from the layout of the factory, in most cases. “Anything is possible in engineering, it just has to be cost-effective,” he stresses.
For training, the bakery’s engineering team is involved as early as possible – to get familiar with the line, and even assist with its building and installation. Operation training follows. For the VanderPol systems, where there are individual controls for each burner, Sugden trains staff to set and save recipes and make changes to the product on the fly. Within a week, all the necessary training is covered. The partnership with clients also includes regular visits after commissioning, to ensure the equipment works within parameters and to provide service and maintenance advice – in short, to look after the equipment and make sure it’s not neglected, which can happen when a trained member of the engineering staff leaves, for example. Improvements and retrofits are also offered as they are developed. The lines are easy to maintain, “The importance of oiling the chain cannot be overstated, as well as using the correct oil, ” Baldwin illustrates. “If you maintain hygiene on a line, you can see everything clearly and maintain it easily; it means taking care and ownership of the line, which is critical,” he summarizes.
Big improvements are featured in the high-capacity lines that are currently being commissioned as well, regarding functionality, access, cleaning, and the overall process flow (and they can be retrofitted on existing systems as well). The Multi Plant line (a bespoke solution for each manufacturer, according to the range of products they manufacture) can now dock into a sheeting line, for another example of recent developments, to add products such as potato and Welsh cakes into production.
As the production of VanderPol lines is incorporated, Sugden aims to provide its solutions worldwide going forward, while building dependable relationships with its customers for the duration of the equipment’s operation. Brexit may bring unknowns in deliveries, but they will be handled as they are encountered and are not a cause for worry, Baldwin thinks. The message the MD has for his team remains “Do whatever it takes.” +++