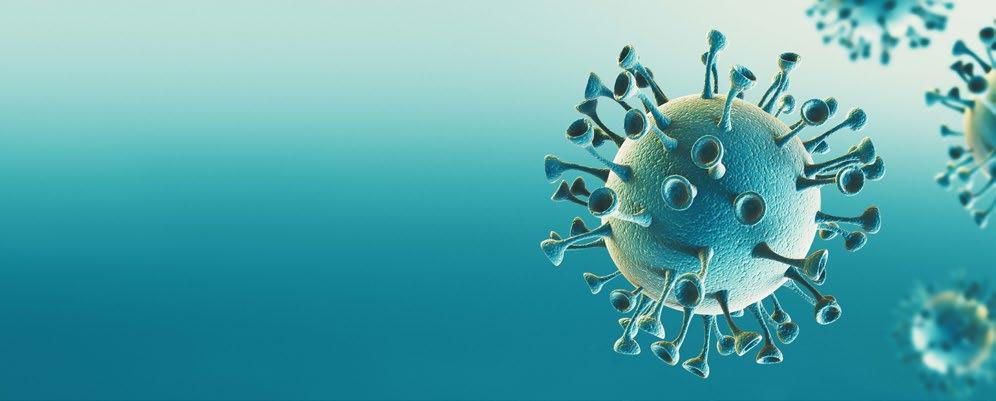
14 minute read
Corona and its impacts
Everything that is currently doing the rounds about estimates of the coronavirus pandemic’s impacts is still derived from past global crises, and is not very specific or relates only to individual sectors. baking+biscuit asked around and heard assessments of the crisis by suppliers to the industry, and how they are responding to it.
+S ignals from the baking sector differ as much as the structure of the businesses themselves. News reports day after day carried photos showing empty bread shelves. While trade suppliers activated all their spare production ca pacities, the situation among artisans, catering and chain stores looked quite different.
By using to-go concepts and deliveries, companies with a large proportion of catering were forced to attempt almost overnight to prevent the turnover collapse becoming life-threatening. Moreover, all the artisans suffered from consumers reducing their shopping trips and visiting as few businesses as possible, which tended to favor the food retail and prepacked goods on bread shelves.
“Please maintain social distancing” is the order of the day in shops. All those that have them use drive-in counters. In double-quick time, others open a pop-up drive-in at a former filling station. Opportunities to cushion losses are also available on the web. It’s the age of online stores and delivery services.
How Bakery Machine Constructors Are Dealing With The Crisis
acquisitions will certainly be delayed as a result. We have reconciled ourselves to a difficult period of at least six months, but we assume we can withstand a period of this kind without any crisis-related lay-offs.
Are there any impacts on supplies and installations?
We have put all outstanding deliveries, installations and service/maintenance contract fulfillments on hold until further notice. Third-party companies’ service technicians are allowed into production facilities only in an emergency (breakdown service) - and subject to very strict guidelines. As we already said, we have plants that were ordered in storage in our warehouse, fully assembled, and are in a position to install them promptly when called for by our customers.
How are coronavirus measures affecting service?
We guarantee the customary reliable service (24 hours / 7 days/ week) even in the current difficult situation. In conjunction with a modem for remote diagnostics, we still guarantee a maximum two-hour response time.
What is the current situation for your raw materials supplies?
The supply of raw materials (in our case, components for final plant completion) also has long-term security, perhaps to some extent with slight delays.
Have you announced short-time working/have you needed to lay off staff?
How is the coronavirus crisis affecting your company?
Currently, not yet so dramatically. We had a fantastic inflow of orders in the three months before the crisis, but were no longer able to execute deliveries planned for February to April, and these plants are standing in the warehouse ready for dispatch. So we have enough to do as soon as restrictions are eased and our customers accept external companies into their premises again. We were also no longer able to carry out a whole series of trial installations (mobile vacuum plants accompanied by our applications specialists to demonstrate the financial and product-specific operating benefits in the potential customer’s business). These test operations are the precursor to the conclusion of a successful sale, and future
Like all other businesses, we immediately set up a cost management strategy to secure the company’s future. Registering short-time working is also a component of this measure. Our principal aim is not only to safeguard the company’s liquidity, but also and most particularly the active retention of our employees, since that is the only way we can continue to offer our clients the customary high standard of quality after the crisis has been overcome.
Do you have special offers for your customers in view of the coronavirus crisis?
We are convinced that a high degree of solidarity is necessary, especially in crisis situations. Since solidarity strengthens us all, we are making our contribution in the form of a 20% discount on all service work and existing service/maintenance contracts, with immediate effect and until 31.12.2020.
What are your plans for the period after coronavirus?
We are contacting our existing and potential customers to find a suitable time to resume discussions that were interrupted, to gradually work through all trial installations that were booked and are still outstanding and, together with our customers, to develop strategies regarding how costs that have arisen due to the coronavirus crisis can be earned back and thus compensated by the targeted use of Cetravac’s vacuum conditioning and the considerable wage, process & energy cost savings and state subsidies associated with it. Then, preparations for the Südback trade fair, which hopefully will still take place and at which we want to present some pioneering new developments, are also coming to the fore again. Unfortunately, we had to cancel our workshop planned for mid-May, which had aroused an unexpectedly high level of interest. However, we will attempt to fix a substitute date in the fall or in the spring of 2021.
How is the coronavirus crisis affecting your company?
Meaningful forecasts are currently almost impossible due to the dynamic nature of developments. Like any manufacturing company in Germany, we also notice uncertainty among our customers and employees. We take very seriously our responsibility as one of the baking industry’s most important partners. Since we have depended on “Made in Germany” for more than 135 years, we are largely independent here. However, even we are beginning to notice transport options and rising delivery costs. Happily, we can continue
The situation at Harry-Brot
For several weeks, Harry-Brot in Germany has recorded a large demand for bread in self-service packs. The company says it responded to this with all available baking capacities, including special shifts. Harry-Brot is now again delivering the entire range of toast-bread, sandwich bread, wholegrain and mixed breads. It says “bake-off” is the only range in which the sustained high demand can still only be met by omitting a few articles. In contrast, the company notes a marked downturn for self-service sales of bread and frozen bread rolls in baking stations.
our day-to-day operations in the production area almost without restriction.
Because we and our high-quality mixers and systems for baked products serve a market representing one of the most important staple foods, we even see a rise in industrially manufactured and packed products in this crisis. Our task now is to ensure that we also do everything in our power to ensure this demand is met. Whether we succeed in doing that in the short and medium term depends on many factors.
Are there any impacts on supplies and installations?
Our customers can depend on us 100% here, because the organization of our in-house workshops is optimum. Orders already confirmed will, of course, also be processed and delivered. We will inform our customers promptly if delays due to illness or suppliers occur here. Reliable processes to keep the level of information up to date have been developed for this purpose. Insofar as these production chains function, we will also be able to deliver on time in the future as well. Of course, limitations arise due to restrictions on the freedom to travel. This affects mainly our experts who work at customers’ premises, i.e. sales staff, technical installers, technologists, programmers and commissioning staff. However, the DIOSNA Group has a large network of competent sales/marketing and service staff that allows us to access the respective specialist personnel on the spot, and to offer a well-structured customer service organization.
How are coronavirus measures affecting service?
The fact that we constantly optimize our processes, and already have “remote monitoring” access to many of our modern production plants, has proved useful in the current situation. Some of our service technicians use videoconferencing to provide fast, uncomplicated support. Furthermore, we also have a global network of selected partners who also provide the company. Employee health and risk minimization always have top priority in this respect. Staff returning from vacation, for example, stay away from the company for 14 days if they come back from risk areas. Our definition extends even further than the one issued by the Robert Koch Institute.
Harry-Brot gives a further report on the situation: “Since the coronavirus topic first emerged, a Harry strategy team at the highest level has assessed the current position on a daily basis, and has initiated appropriate measures for
Departure times of fresh delivery rounds and thus the simultaneous presence of employees were also separated. For office staff, systematic home office working enabled individual offices for employees present on site. Disinfection stations were installed everywhere. Hygiene standards in the production facility have always been strict and high, so there is no infection risk during a shift. Precautions to minimize contact were taken for all rest areas.” +++ local support to our customers insofar as possible and permissible. The different versions of our maintenance kits are especially popular. For example, they give customers the option to arrange for replacement wearing parts to be exchanged by their company’s own technicians.
What is the current situation for your raw materials supplies?
We have sourced our raw materials up to now. However, even we are beginning to notice transport options and rising delivery costs.
Have you announced short-time working/have you needed to lay off staff?
No.
Do you have special offers for your customers in view of the coronavirus crisis?
We utilize digitalization as an opportunity to develop new pathways. You can look forward to all the things we have in store for you.
Discussions with our customers and business partners take place online. This also includes the remote access mentioned above. It’s how we continue to assist our customers with active help and practical advice, and support them with our process know-how and as dough experts. Maintenance kits help our customers at their site. Moreover, we continue to offer more advice through our technologists, because sourdough can be prepared by using starter cultures such as our DIOStart. This in turn increases the shelf life and freshness of bakery products, and enables an increased input of water and a reduction in raw materials usage (e.g. sugar and fat). This can be hugely financially beneficial to our customers. In addition, our teams do further research into the means by which we can support our customers. For example, we currently provide information via online platforms such as LinkedIn about the fact that DIOSNA customers who own a wheat fermenter (W Series) can produce hand disinfection agents according to the WHO recipe.
The situation at Aryzta
The Irish-Swiss baking group Aryzta is putting a brake on costs due to the Covid-19 crisis. As the Group reports, eight production sites were temporarily closed in the past week, three of them in Europa and five in North America. The Group also reports possible temporary closures of other production lines in bakery facilities to “actively reduce capacity in line with demand”. About 30% of the staff are said to have been furloughed. It also says management salaries will be reduced by 30% for the coming three months, and government support measures are being utilized.
What are your plans for the period after coronavirus?
We will continue to give our customers high quality support in the usual way. The current global crisis is actually bringing us digitally a long way forward. The task in the future will be to utilize this opportunity and to develop it further for ourselves and for our customers.
How is the coronavirus crisis affecting your company?
In the first place, of course the coronavirus crisis is affecting our internal organization, i.e. we must protect our employees in the best possible way, which is why we have adopted a whole series of measures: mobile working, increased safety distancing, videoconferences instead of face-to-face meetings, and new models of working may be mentioned as just a few examples.
As far as the market is concerned, we currently see a further trend towards large plants. “One-stop shopping” in big supermarket chains is also spurring on the need for large industrial plants. On the other hand, unfortunately, smaller businesses are facing a very tough battle with the current situation, because they often rely on individual sales outlets such as cafés or street vendors, which are closed due to the current pandemic.
Are there any impacts on supplies and installations?
We are currently still in the fortunate position in which we can say that our business processes and supply chains still function very well. Internally, we are very well positioned as a result of organizational adjustments. Externally, i.e. in relation to supplies of materials, we currently also have no difficulties and continue to be supplied properly and with the appropriate numbers of items, which is why up to now we see no significant impacts here either. Thus at the present time there is no danger to any customer projects, and we continue to make deliveries. That can change at any time, however, which is why we are currently very vigilant in this respect. We also take into consideration the risk countries according to the RKI (Robert Koch Institute).
A spokesperson told Backspiegel’s editorial office that the three European factories mentioned above do not include any German ARYZTA production facilities. As the ARYZTA Bakeries Deutschland GmbH spokesperson also reported: “We responded to changed demand by rearranging production, reducing production volumes and developing new products to match the changed requirements. In agreement with the Works Council, we also introduced short-time working in a few areas to preserve all jobs in ARYZTA Germany as far as possible. To some extent this definitely affects whole production lines.” +++ production operations are continuing, while maintaining safety precautions. We have also arranged a large number of home office workplaces to give our employees the best possible protection.
How are coronavirus measures affecting service?
Here again, there are no significant limitations. We rely mainly on remote services in risk regions according to the RKI. In this context, for example, we use an augmented reality headset to give the best possible support to customers at the plant on site. Initial deployments were already highly successful. Via local subsidiary companies, we also still have the MULTIVAC service network on the spot, which has already undertaken FRITSCH’s service activities since 1.1.2020. Thus it allows us to provide very good service to our customers even despite the current challenging situation.
What is the current situation for your raw materials supplies?
Currently, there are no restrictions here either. Moreover, as a food machinery manufacture, the BMEL (German Federal Food & Agriculture Ministry) classifies us as system-critical, and our suppliers know that and accordingly give us very good support.
Have you announced short-time working/have you needed to lay off staff?
No, quite the contrary. As already stated, we currently see a high demand for industrial bakery machinery, and are a long way from short-time working at present.
Do you have special offers for your customers in view of the coronavirus crisis?
As already mentioned, the coronavirus crisis is having a big impact on small and medium-sized bakers at present. To support them, we created the #saveourbakers campaign on our social media channels. The campaign aims to draw attention to the situation of small and medium-sized bakers, and to show that the favorite local baker is also there for his customers even during this crisis. Bakers are also developing really fantastic initiatives for this, about which we will gladly report in the context of the campaign.
What are your plans for the period after coronavirus?
Corona “compelled” us to use new ways to collaborate. Wherever this functions, we will also enable it in the future as well. It has become apparent that it is not always necessary to come together at a single point to achieve very good results. For example, our company will continue to offer machine acceptances in the factory by video, and will also focus further on remote services. We are currently able to extensively test and optimize the latter.
At this point, we owe a big thank you to our employees, who are supporting us with great optimism and understanding in maintaining the operation of the business.
Are there any impacts on supplies and installations?
At the present time, taking additional legal and safety aspects into account, carrying out installations is possible to only a limited extent. We are experiencing very open, understanding communication with customers here, because of course bakeries also give top priority to employee health.
How are coronavirus measures affecting service?
Our global 24/7 service hotline and our service team are available as usual. Spare parts can be ordered and supplied/ delivered as before. Service deployments will be undertaken to only a limited extent for the time being. We are, therefore, doing our best to support our customers by using remote maintenance.
What is the current situation for your raw materials supplies?
As a production operation, security of supply is one of our very important aspects. Our raw material supply remains guaranteed due to our widespread network of suppliers and our purchasing department’s long-term planning.
Have you announced short-time working/have you needed to lay off staff?
In times of uncertainty, it is very important that we stress we have not laid off any employees. By using the “Corona Shorttime Working” model, the Austrian federal government has found a way to temporarily reduce normal working hours and thus reduce companies’ labor costs. After exhaustive evaluation, we have also adopted this option. Our aim in using it is to retain all employees as far as possible.
Do you have special offers for your customers in view of the coronavirus crisis?
Our offer consists of continuing to support our customers by all the means available to us, to ensure the security of their production operation. This support consists of the supply/ delivery of spare parts, our global service hotline, and the provision of advice by telephone and/or via remote service. In these challenging times, we should like to thank all the bakeries that are maintaining the supply chain and are providing people throughout the world with one of the most important foods - BREAD.
How is the coronavirus crisis affecting your company?
Because our status as a production operation means we make an essential contribution to maintaining supply chains, certain areas of our business remain unaffected by possible curfews and travel restrictions for the time being. Thus our
What are your plans for the period after coronavirus?
We observed a very positive development and willingness to invest in the bakery sector at the start of this year. We hope this trend will be continued in the time “after coronavirus”. The Südback trade fair in October will be an important indicator of this. We look forward to this trade fair with optimism, and are currently planning trade fair innovations. Our main focus in this respect is on the topics of hygiene and efficiency, to ensure our plants can be cleaned even better and quicker, thus giving customers maximum plant availability.
How is the coronavirus crisis affecting your company?
The Netherlands government has communicated general measures to the population and to companies. We must all take responsibility and act accordingly. We do not want to run the risk that Rademaker employees will become infected with the Covid-19 coronavirus and bring it back home as a result of travel and international field service deployments. However, Rademaker remains fully functional across all disciplines, which involves staff working under the recommended conditions, e.g. the rules for social distancing and meeting, either from home or in the headquarters. Here, we also benefit from the expansion of administration and production areas carried out in 2019, which allows more freedom of movement. We are now using modern telecommunications systems to a greater extent than previously for both internal and external discussions. For local activities, the use of our own sales/marketing subsidiaries and the international representatives network makes us less dependent on travel out of the Netherlands.
Are there any impacts on supplies and installations?
It may be impossible to adhere to stated and planned transport, installation and commissioning dates/times as a consequence of the great diversity of measures against the Covid-19 coronavirus among our customers in various countries worldwide. There are various different kinds of influencing factors, and for this reason we cannot assess the extent to which the consequences will have an impact. For this reason, we must keep legally open any possible delivery time postponements caused by countermeasures against the coronavirus. We have already communicated this very openly to our customers.
How are coronavirus measures affecting service?
Rademaker’s 24/7 service department still remains available to customers round the clock. In most cases, help can be supplied via telephone, E-mail, online access or shipment of replacement parts. The Rademaker Academy can give good support, e.g. with quick-guide instructions, for which the new media with visualization and remote guidance also play a big role. In the most urgent emergencies, Rademaker can respond by using local service technicians without breaching