
5 minute read
AutomationX: Effectiveness and quality measurements
How effective is your production?
Effectiveness and quality measurements in piece goods production have been commonplace in the automotive industry for decades. In the bakery industry, the demand for corresponding software solutions is increasing for more efficient production and with higher quality corresponding products.
© AutomationX
+MES, OEE, BDE ... terms, terms, terms Manufacturing Execution Systems (MES) are ‘software solutions that guide, direct, control, and monitor a production process.’1 An MES system can map the entire production process from planning to quality assurance as well as giving an effectiveness measurement and much more – from goods receipt to goods issue. Alternatively, individual modules of an MES software package can also be used as stand-alone solutions for monitoring sub-processes.
Overall Equipment Effectiveness (OEE) is a module of an MES system for measuring and evaluating effectiveness.
Production Data Acquisition (PDA) is necessary to automatically transfer data from the machines to the system, e.g. the number of pieces, malfunctions, set recipe, and also to record information by manual input. The recorded operating data is linked to production data in the MES system.
How does data get from the machine to the software?
Modern machine controls offer the possibility of exchanging data via a standardized interface (OPC UA). Attention! A standard interface is a means to an end. The content of the interface must be defined. Not every machine can transmit the same data. For example, in the case of a spiral freezer, the temperature setpoint and actual value are primarily relevant; in the case of a dough divider, it is the number of pieces. The data to be exchanged must be provided by the equipment manufacturer. In the case of older systems, it is sometimes necessary to install additional sensors if it is not possible to tap the data automatically. In particular, if spare parts are no longer available for the existing control system, consideration should be given to upgrading the system to collect additional data when the control system is replaced (Data acquisition is mainly an interaction of automatically acquired data, which is then fed manually).
Essentially, the following information is important: Performance data: How many pieces are currently being produced on the machine? If more pieces are produced than specified, the performance factor can also be over 100%. If the machine does not supply this data, it can be realized by installing additional sensors. Quality data: On some machines, temperature, relative humidity, or other measured parameters influence product quality. In any case, such data should also be transmitted and recorded. This data is displayed in trends related to a product and allows conclusions to be drawn about quality deviations simply. Fault messages: Ideally, all faults are transmitted to the MES system. Their priority can be defined in the MES system. Many small disruptions do not affect production and are therefore not interesting for an effectiveness analysis.
Is it possible to record staff time?
Yes, and it's very simple. The employee logs on to an order that is displayed on a touch panel, e.g. via RFID or barcode. The personnel times are calculated for an order according to its current status. If the status ‘Setup’ is selected, the personnel times are booked to ‘Setup’.
Does data acquisition function fully automatically?
No. Machines provide only partial information. As an example, information as to whether a machine is ‘ready for operation’, ‘switched off’ or ‘in operation’ is usually supplied by the machine. Information about rejects or whether maintenance
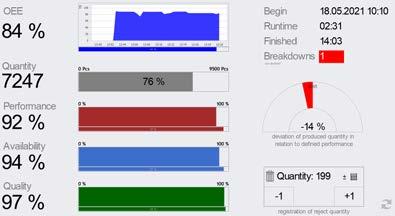
Real-time display of production progress with deviations
© AutomationX
AutomationX GmbH
With its 90 employees, the company specializes in the development and implementation of production software, especially in the baked goods industry. Recipe management, silo control, or the conversion of old control systems are just as much a part of the daily bread as the introduction of MES systems for mapping the entire manufacturing process from goods receipt through warehouse management, production planning, and production data acquisition to shipping.
is currently being carried out is very important for evaluations but must be entered manually or recorded semi-automatically. Above all, scrap recording must happen simply. After all, no one counts the individual pieces that are selected from a conveyor. Usually, the best way to do this is to collect the scraps in bins and weigh them. If the scrap is added back to a batch of dough (rework), the batch traceability can also be mapped in the system.
Isn't manual input too complicated for a line operator?
Ease of operation is a key requirement in bakery operations. Here, suppliers of MES systems differ significantly, as different industries also have different requirements. Experience has shown that in the food industry, less is more. The input screen must be clearly designed and easy to use. The screens on the line can also be used for multiple purposes, such as quality data collection or weighing.
Who benefits from the software?
The data is useful for the user on the line, right up to the company manager. They are shown the progress of the order and its effectiveness via a large display. For example, they can see whether the planned order will be completed earlier or later than scheduled. The technician can see via an evaluation summary which faults have occurred and how often, and the duration of the interruptions to the operation that they have caused. The analysis facilitates prioritization in the elimination of defects. All events, including their causes, are documented. A shift book can also be used to record all the activities of the respective technicians in their shifts. The production manager receives an overall view of the manufacturing process. In the event of changes to machine settings or the production process, it can be very clearly displayed whether this has resulted in an improvement in performance or quality.
The evaluations can be easily adapted to the needs of the respective company. Not everyone needs the same information. By assigning rights, the respective user sees only the information that is important to them. +++
1 Source: Wikipedia ADVERTISEMENT
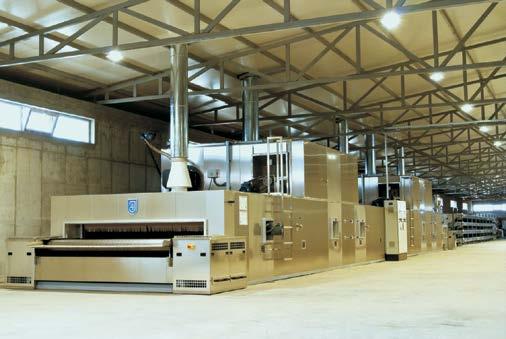
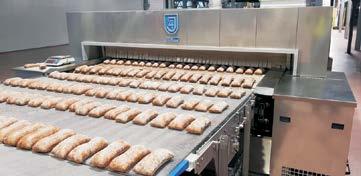
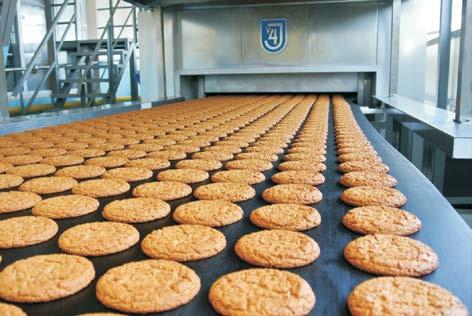
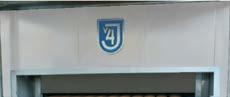


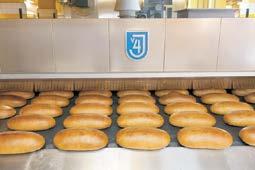
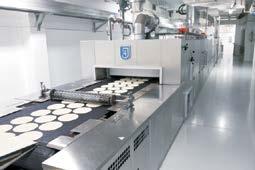