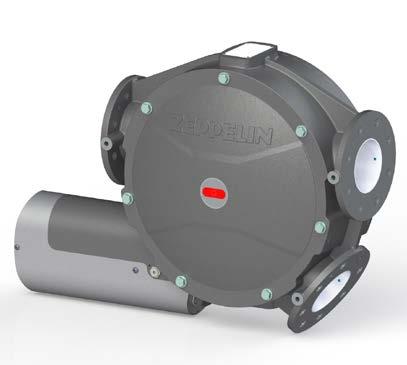
2 minute read
A new CODOS and more
Zeppelin-Systems GmbH is an international market leader with regard to continuous dough mixing. The Rödermark-based company will present a new CODOS generation at the iba trade fair.
New drive technology, new cooling, Washing in Place, a nd of course also a new control system that communicates with Zeppelin’s higher-level automation and digitization software. Zeppelin Systems has granted the Codo a complete makeover, after more than 100 n ow, have been in service in baked goods production worldwide.
The previous asynchronous geared motor has been swapped for a water-cooled servo drive with a single gear reduction, which means not only a 40% weight saving but also a reduced installed length, i.e. space is saved and on top of that, energy consumption is reduced. Furthermore, with immediate effect there is an emergency stop function on all plants, which instantly brings it to a standstill.
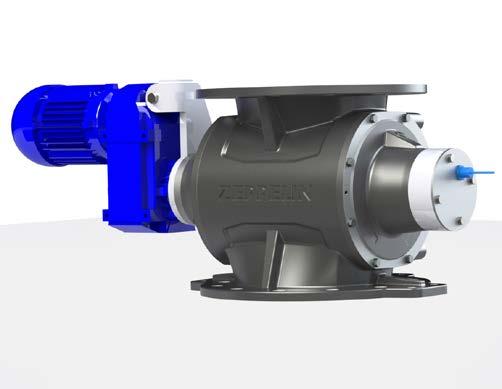
The cooling system of the CODOS NT has also been fully redesigned. The efficiency level of the trough cooling has been improved considerably, which ensures better heat transfer. All the trough cooling assemblies will be positioned outside of the CODOS in future.
Moreover, with assistance of research at the Cereals Research Institute in Rehbrücke, the geometry and spacing distances of the mixing tools themselves have been optimized again.
According to Michael Piepenbrock, Zeppelin’s Business Unit Manager, Food Processing Plants: “That provides more power and performance with less energy consumption, and makes the CODOS scalable.” There will be a CODOS NT 160 with a dough production capacity of approx. 3 tons/hour, the
CODOS NT 200 with 4 – 5 tons/hour and the CODOS NT 230 with up to 8 tons/hour of dough. In 80% of all cases, a CODOS stage will be combined with a DymoMix that supplies pre-mixed, uniformly wetted raw materials to the CODOS. A two-stage CODOS solution is usually used when processing flours containing extremely high gluten levels.
Of course, Zeppelin is also moving towards digitization in its control technology. The very closely interrelated topics of automation and digitization will be combined under the MIRA brand name in future.
This means for the CODOS NT is that control will still take place via the existing Prisma Web system. However, the Prisma Web system will be incorporated into the MIRA concept in the near future. Topics, such as data analytics and cloud capability are already being developed. Whether it’s Cloud in the Web or a local solution can be chosen freely. The development focuses on the future solution’s easy applicability and scalability. Another important element are MES functionalities, which play an important role in MIRA. In concrete terms, that means input, output, energy consumption, process times, etc. are documented and can be called up and analyzed at any time. Moreover, a mobile terminal device can be used to view the documentation belonging to the Zeppelin modules, and spare parts can be ordered, if necessary. A remarkable aspect of all of this is that the Zeppelin landscape has no problems incorporating even components that do not originate from Zeppelin. In order to be able to use this technology also in already existing plants, it is sufficient to retrofit the plant positions in question with a “beacon” which records the corresponding data and feeds it into the system.
In future, the CODOS NT will be installed on load cells in order to carry out some measurements. On the Zeppelin both you can already experience “hands on” the entire MIRA system consisting of the MIRA Control and MIRA Connect.
“Simple” hardware improvements sometimes find it hard to gain a hearing with so much IT around, but looking into that area is also worthwhile, because they directly improve reality. For example, Zeppelin will show a new series of models of water mixing and metering devices, a new manual weighing station, a new diverter valve and a new rotary valve in Munich.
The new generation of rotary valves and diverter valves for the medium-pressure impressively show Zeppelin’s new design language, clearly and powerfully drawn, with lighter weights and more powerful performance than ever before, and EHEDG has not been forgotten either. In this respect, Zeppelin is consistently going down the road of digitally networking every component, and thus MIRA Connect (formerly: PLANT.GATE) is also on board as standard.