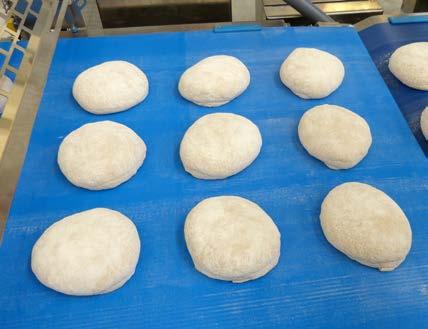
3 minute read
Industrial bread line for artisan products
The Swiss company RONDO Burgdorf AG presented a new universal bread line to visitors at an open-house event in Schio, Italy. The plant can produce sliced/cut, long-molded and round-molded artisan breads and bread rolls.
R ONDO Industrial solutions, RONDO Burgdorf AG’s industrial division, organized an open-door day in Schio, Italy, for European production managers. The company presented the newly-developed ARTISANA bread line to the expert audience. The plant can produce sliced/cut, long-molded and round-molded artisan breads and bread rolls. As explained by CEO Dr. Michael Witzak during the practical demonstration of the plant: “The RONDObot is also the only system worldwide that can round-mold doughs with a dough yield of 180 or more.”
Mode of operation
The plant begins by forming a dough sheet, for which RONDO uses the ASTec design of the universal MIDOS dough sheeter (Multiple Industrial Dough System) supplied with dough via a bowl tipper. A roller system developed specifically for soft to firm doughs creates a homogeneous dough sheet without using process flour or process oil. This is followed by a satellite head, cross-roller and calibrating station to produce the required dough sheet thickness and width. A built-in automatic weighing device ensures that the weights of the made-up pieces are as accurate as possible. After cutting and spreading apart the dough sheet, and separating the dough pieces, the RONDObot comes into operation. This is the basic technology for a novel round- molding system for dough sheeters, and its task is to prepare round-molded artisan and “ordinary” rolls and breads in a wide range of weights. The round-molding system consists of the RONDObot, an industrial robot with an IP67 design, novel interchangeable tools (these tools are changed automatically), and a special round-molding table. The RONDObot’s six degrees of freedom enable optimum matching of the round- molding process to the dough and end-product, and replicates round molding with 100% repetition accuracy.
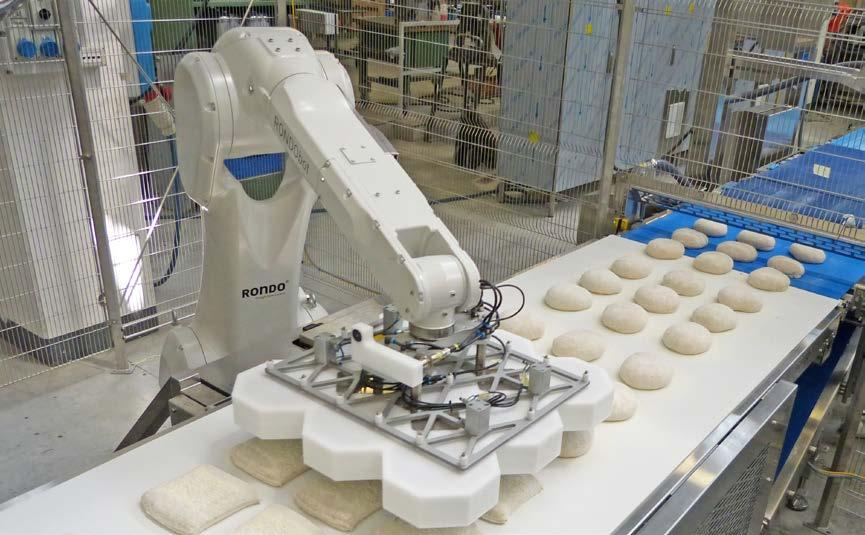
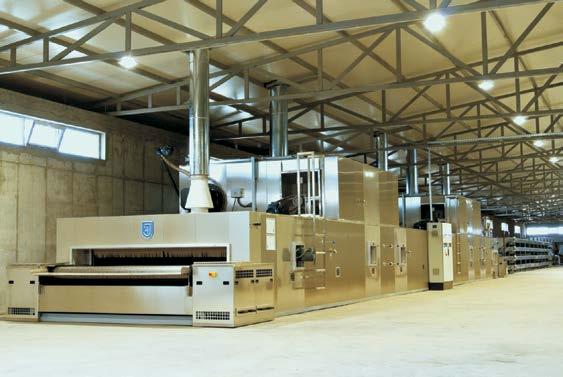
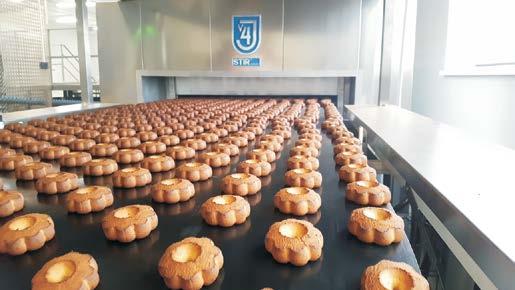
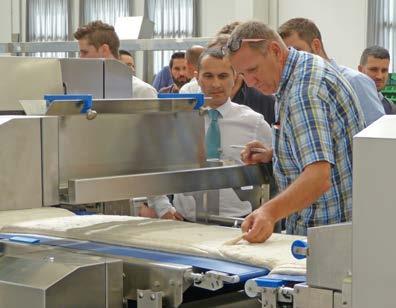
Round-molding in the multi-phase rounding process is divided into individual phases, in each of which the molding movements are carried out in the same way as a baker would perform them manually. The plant enables not only the adjustment of the molding speed but also a definition of the changes in the eccentric movements and the pressure on the dough piece. All the parameters of the multi-phase rounding process are stored in the plant’s controller and can be called up again.
The plant can process artisan rolls and breads in a weight range from 40 to 1,000 g. It can also process wheat doughs and doughs with a proportion of rye or seeds. In particular, doughs with a long dough rest time can be made up through the plant. Thus, as was explained to participants during the event, the RONDObot is the only currently available rounding system that can achieve good molding results with doughs containing large amounts of water and with a prolonged pre-proofing time. Basically, the RONDObot can be integrated
ASTec lines
RONDO ASTec lines are designed to meet the highest hygiene requirements. Fast, safe plant cleaning is ensured by the hygiene-friendly design and construction, and by the use of high-quality materials. ASTec lines are cleaned according to a computer-assisted program individually defined for the respective production facility. The cleaning steps are logged and recorded for possible audits. ASTec lines are available in two versions: one for dry cleaning and one for wet cleaning. An advantage of ASTec lines is a reduction in cleaning times by up to 30% compared to other plants. On the one hand this leads to reduced costs, and on the other to increased production time. +++ into existing or new bread and roll baking lines. This round-molding system is the RONDObot’s first application. Dr. Witzak explained that RONDO is currently considering automating additional dough processing steps. The RONDObot can also be bypassed to manufacture long-molded and cut/sliced products on the ARTISANA.
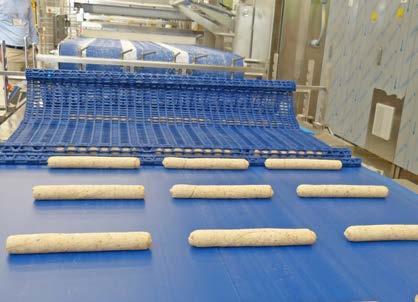

Industry 4.0
However, the new plant’s practical application was not the only thing that was presented during the event. The role played by the topic of Industry 4.0 in the RONDO company was also explained to the visitors. Dr. Witzak presented the RONDOnet, in which production and plant data are collected in a cloud. Users receive an overview, e.g. about system alarms, the operator or the plant’s capacity utilization. All the events are recorded online and stored in the cloud. Machine incidents, e.g. a plant start or stop, have a date/timestamp and a value. All the components can send warning or fault states at the same time. These messages can be forwarded to the internal service or directly to RONDO’s service team. According to Dr. Witzak: “If the system has an ERP connection available, these messages can also trigger an order for spare parts.” In this respect, RONDO supplies a servicing plan for each component, which should be complied with to guarantee faultless functioning. Moreover, the plant can be equipped with up to four webcams to monitor the progress of the production operation. An analysis tool currently being developed should, in the near future, allow the number of products and their dimensions and color to be established. As Dr. Witzak explained: “Preventive maintenance with proactive alarms and online event recognition is the first step towards the target of nil downtimes for our customers.”
The open-house event in Schio allowed participants to take a look at the company’s new developments. More information about the industrial bread line for artisan products will also be available at the iba trade fair in Munich. +++
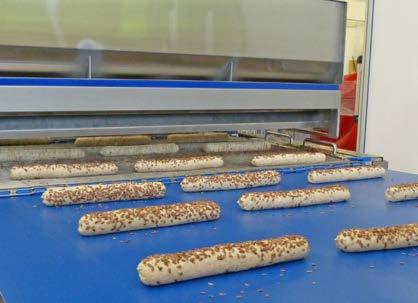
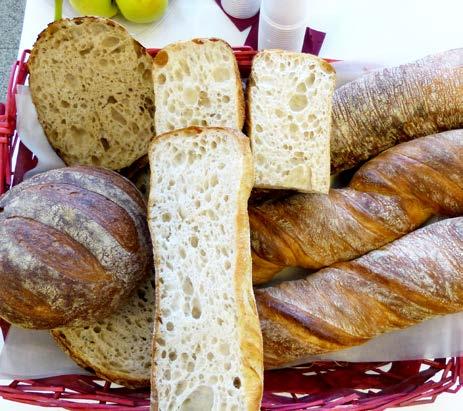
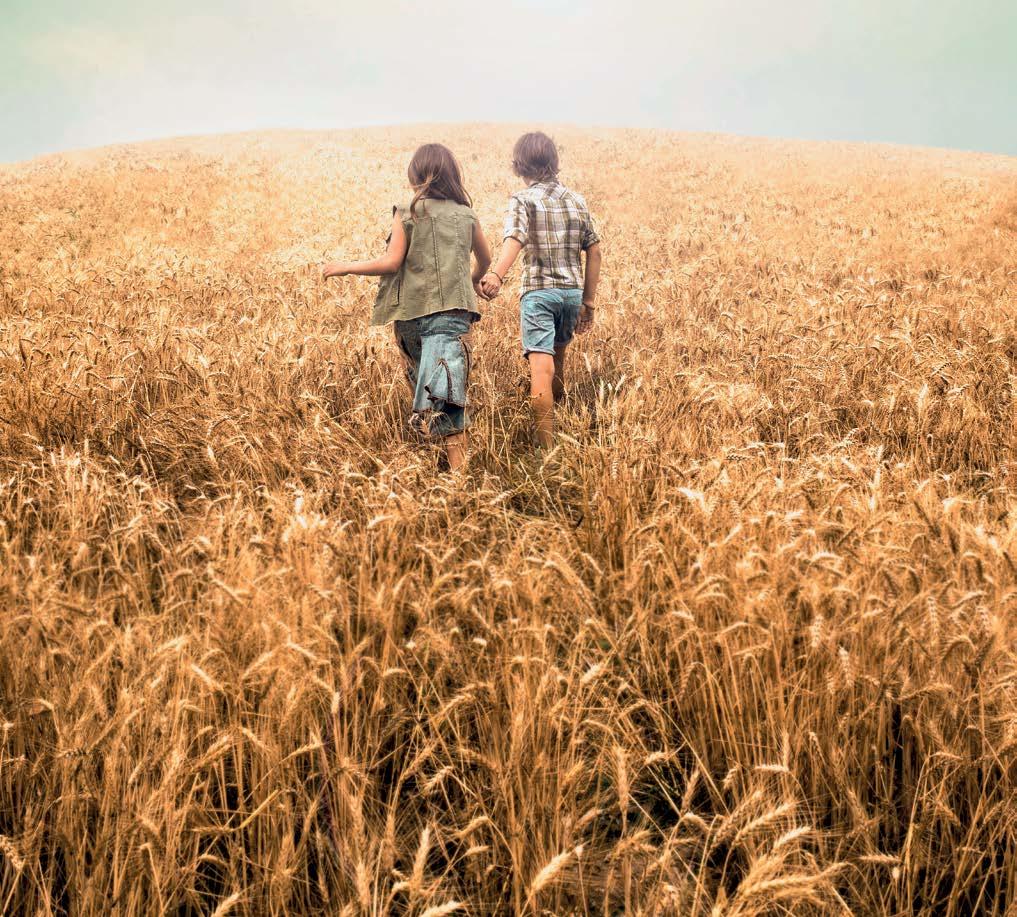
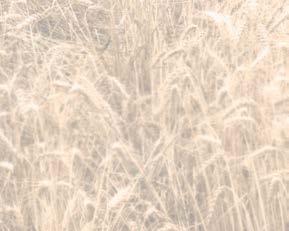