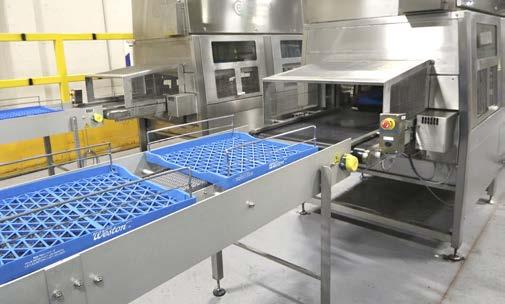
2 minute read
The de-luxe class from Northern Italy
Colussi Ermes is considered to be a supplier of de-luxe class washing plants. Word of this has spread around, not just in industrial businesses but also in the baked products sector.
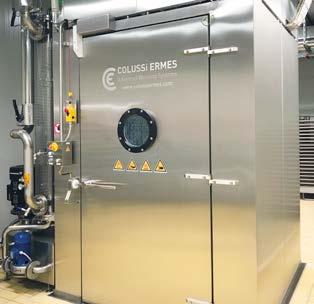
The whole washing plant business that began in Casarsa della Delizia, North-eastern Italy, was for the high-class San Daniele ham made quite nearby in the Italian region of Friaul. The ham was followed by dairy processors, who asked Colussi Ermes to build washing plants for their cheeses, and finally pharmaceutical companies and all kinds of food manufacturers came knocking on the door. The baked products industry now appreciates Colussi’s hygiene standard, and does so worldwide.
There are several reasons for this. Colussi always builds its washing plants individually, according to the needs and space circumstances of the respective operation. The product range has expanded over the years, and now includes washing plants for everything that needs washing in a bakery: trays, pans, crates, rack trolleys, bread trolleys, thermoroll trolleys and transport crates of all kinds. Cleaning in industrial operations is increasingly understood as part of the whole process chain, and is integrated into lines. That’s why Colussi built a plant equipped with 14 blowers to clean 130 x 130 cm peelboards for a frozen baked products manufacturer, which ensures a level of dryness so high that the peelboards can be loaded again immediately.
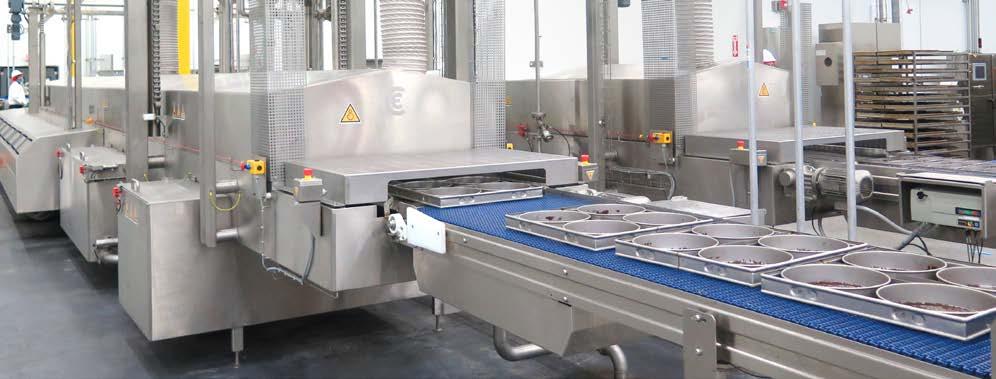
Although Colussi itself says it produces plants whose daily period of use is not finished in two or three hours but more
++ A four-row folding crate plant with an hourly throughout of up to 10,000 crates like one or two shifts, that does not in any way limit its customer base to industry alone. The company also makes combination plants for chain-store businesses that can wash trays, pans, crates and even rack trolleys or other transport trolleys.
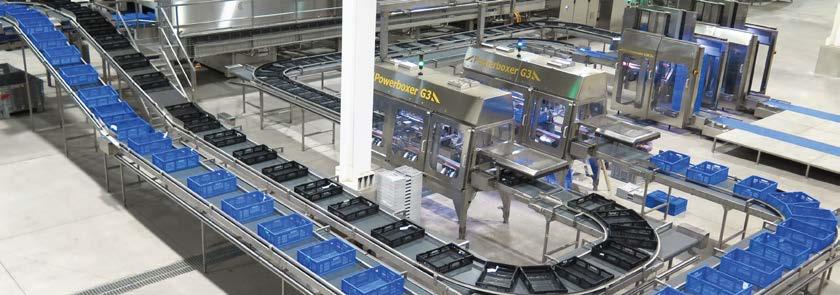
The fact that the plants are consistently fabricated from stainless steel, and not just pushed or screwed together but fully welded, is all part of Colussi’s standards, just like the special water sealing of the upper covers on tunnel oven washing plants. The hot steam condenses on the cover and runs into a channel carrying the seal. The channel is sealed watertight by the water, and only after the shift has ended is the channel emptied by the operator.
There are many details that boost efficiency. Thus many trolley washing plants are happily recessed into the floor, because in this way the water from the washroom can drain away quickly and efficiently, while at the same time there is no need for a ramp to wheel in the trolley. Another example is the externally mounted drum filter fitted with a scraper that removes coarse dirt from the water circulation. It extends into the water only far enough to trap the residues, and doesn’t repeatedly drag them through the water again but removes them with the scraper as quickly as possible after they have been collected. Cleaning the plant itself is assisted by the fact that all the parts are accessible without effort, and/or can be opened or dismantled even without using tools.
New: 2000 crates uses 10 kW-hours
Based on experience from the fruit and vegetable industry, which operates plants that need to clean more than 8000 crates/hour in an energy-efficient way, Colussi recently built a plant for the baking industry that cleans 2,000 crates per hour, which it does with an average of 10 kW-hours of energy. A plant with only one centrifuge, which copes with 1,200 crates per hour, even makes do with an energy consumption of 5 kW-hours. Centrifuge drying reduces the residual water on the crates to 2 grams/m 2, on top of which it remains not in the form of droplets on the surface but as a fine film that quickly evaporates. To keep the energy consumption low, the braking energy released during centrifuging is fed directly back into the electricity network again. +++