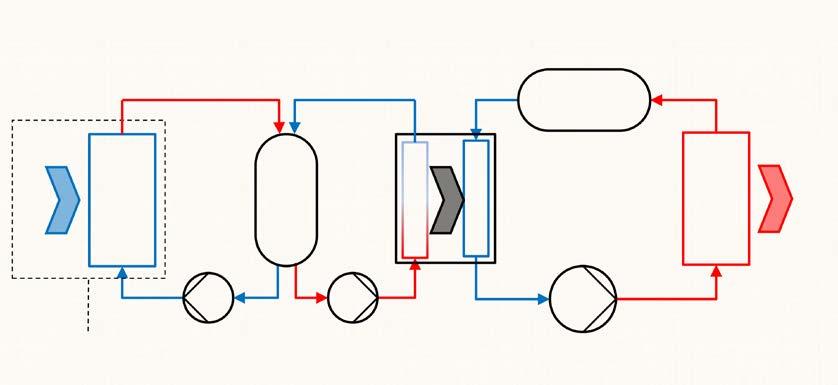
3 minute read
Natural refrigerant
The European Union has enacted an F-Gases Regulation (fluorinated greenhouse gases) that will slowly but surely have clear impacts on the baked goods sector, because nowadays the cooling and freezing area is markedly larger than the baking area, even in many artisan businesses.
Most refrigerants were and are partially fluorinated hydrocarbons, HFCs. The F-Gases Regulation is aimed at reducing their use by 80 to 95% by 2050. This has only a limited impact on industrial frozen baked products manufacturers, since as a rule they use ammonia as the refrigerant.
There are four significant dates for industrial cooling and freezing equipment, stationary refrigeration devices and central refrigeration plants with a refrigeration capacity of more the 40 kW.
Since 1. 1. 2015, the Global Warming Potential, GWP, must be stated for the refrigerant that is used. The GWP is also called the CO 2 equivalent. The figure states how much a greenhouse gas contributes to the Earth’s global warming.
From 1. 1. 2020 onwards, only refrigerants whose GWP value is below 2500 will remain permitted for use in new refrigeration or freezer plants. Continued use of synthetic refrigerants used up to that time will remain permissible only if they were recycled or reprocessed. If a plant contains more than 40 tons CO 2 equivalent of a previously existing refrigerant, it will no longer be permissible for refrigerants with a GWP greater than 2500 to be used even for servicing and maintenance/repairs.
From 01.01.2022 onwards, a GWP of less than 1500 will apply to industrial cooling and freezing equipment, stationary refrigeration devices and central refrigeration plants with a refrigeration capacity of more the 40 kW.
From 1. 1. 2030 onwards, recycled and reprocessed refrigerants whose GWP value greater than 2500 will be prohibited, even for servicing and maintenance/repairs. Whatever breaks down then, is forever broken.
The EU has clear ideas about the increments with which the disappearance of partly fluorinated hydro carbons from the market is to take place. Of the average 2015 consumption, only 63% should remain in use by the end of 2020. There is a stick and carrot policy to achieve this. Subsidy payments of up to 5% of the total investment are designed to make the switchover to other refrigerants palatable to businesses, while on the other hand manufacturers and importers marketing refrigerants with a GWP above 2500 must obtain quotas for them, which will probably restrict availability and force up prices.
Anyone investing in new refrigeration plants and freezers today can operate in an entirely legally permissible framework for the time being by using combinations of synthetic frigens and CO 2. There are a couple of unknown quantities, however, that could lead to problems, e.g. the suitability of such refrigerant blends throughout the whole spectrum of applications from chilling to shock-freezing. The specific characteristic properties of the individual components might possibly lead to a situation in which the Δ t is too great, which can damage sensitive dough pieces. Another imponderable is the development of prices, and not least the cost and effort required for the newly enacted leak-tightness requirements and monitoring obligations.
Of course, a more ecological and probably also more futureproof solution is to use natural refrigerants such as propane, CO 2 and ammonia.
Propane-R 290 – has low toxicity but is flammable. Plants in which more than 50 kg of propane is used need a special license. Propane is often used for ready-to-plug-in devices whose requirement is considerably less than 50 kg. Propane is frequently used as the first cooling stage in combined systems with brine chilling or CO 2. In rare cases, both the lower and upper stages are operated using propane. To eliminate the risk of a fire in the bakery if there is a leak, manufacturers offer compact propane-operated plants entirely housed in a container set up outside of the bakery. The connection to the brine circulation in the bakery can be isolated at any time. Moreover, the container option has the attractive feature that it can be included in the move or sold if the production operation is relocated.
ammonia circulating within the refrigeration plant, ammonia is normally used in combined plants in which the second stage is operated using brine or CO 2. Thus ammonia is present “only” in the machine room.
Ammonia is a very pungent-smelling gas that can be fatal if inhaled. Therefore its use is subject to stringent safety requirements that are economically justifiable only in the case of very large installations. The advantage of ammonia is its very favorable COP value (Coefficient of Performance), which defines the ratio between available cooling and the consumption of electricity. To avoid the danger due to the ++ CO2 unit
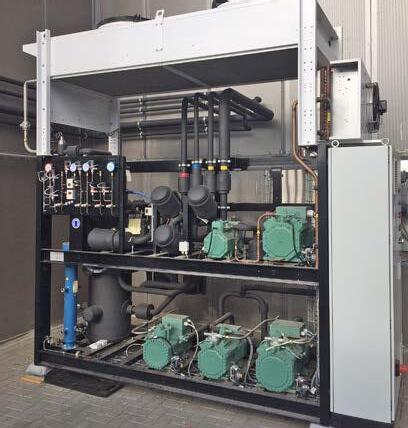
The operating principle of a propane/brine refrigeration circuit
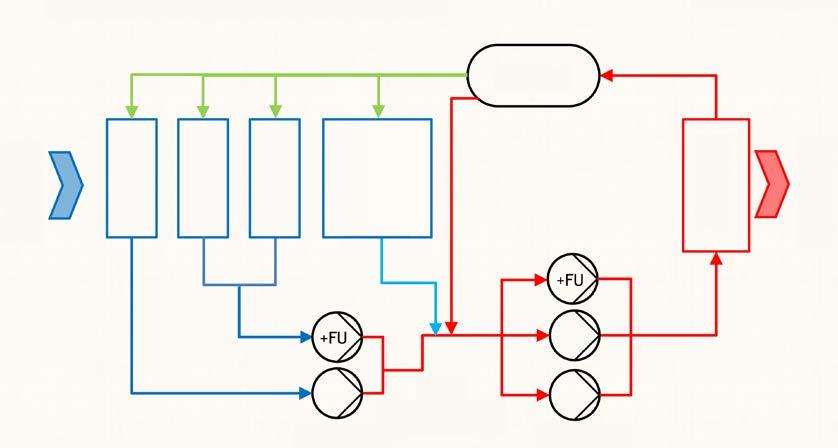
CO2 Refrigerants
CO 2 is the third natural refrigerant that comes into consideration for newly-installed plants. If one wanted to retrofit existing plants to use it, the entire refrigeration engineering would have to be replaced, and only the shell would remain. It is neither flammable nor toxic, and is colorless and tasteless. However, high pressures occur when CO 2 is used. If a leak occurs, however, there is no resulting climate damage, and the plant simply needs to be fixed and refilled. Another point that must be taken into account with CO 2 plants is the interference caused by sub-critical or trans-critical outdoor temperatures. If temperatures at the gas cooler drop far below 31°C, the gas completely liquefies in the gas cooler. If outdoor temperatures lie too close to the so-called triple point of 31°C, the gas no longer liquefies. Thus it depends on how the plant is designed and where the gas cooler is