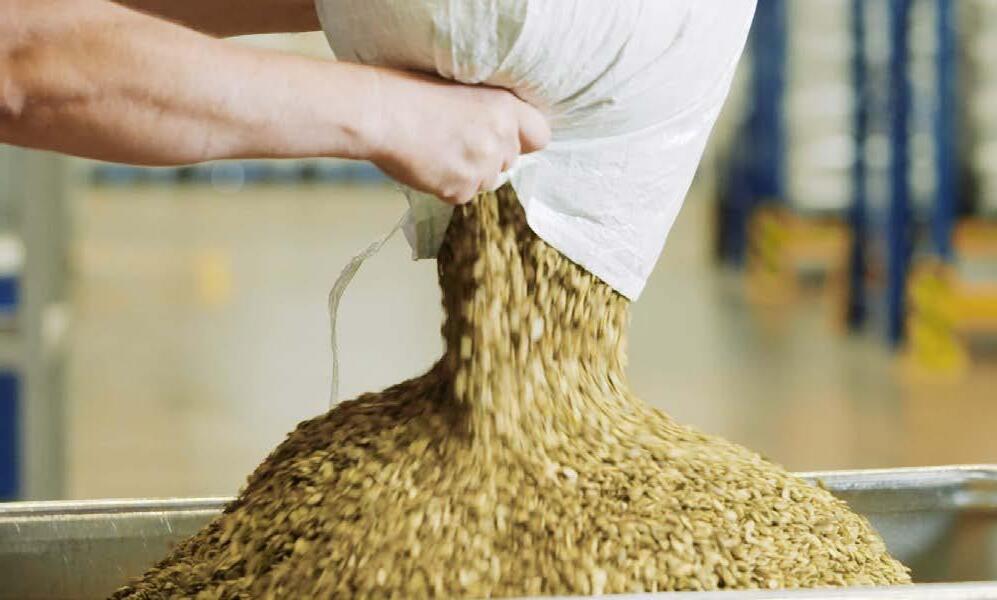
2 minute read
Optimized materials management
+As in all production areas, the baking sector also focuses on efficient workflows, i.e. optimum control and utilization of production capacity. However, an imperative precondition for this involves making production-relevant data available in real time, together with a paper-free procedure and executing all processes from the master ERP (Enterprise Resource Planning) system. As one of Germany’s leading bread and baked goods producers, this strategic approach is especially important to the Lieken Group.
By digitizing in the materials management area, the company achieves time and cost savings as well as other positive effects such as efficient warehouse space utilization or improved data recording for quality control purposes. To attain this, Lieken GmbH relies on intensified mobile data gathering in its production processes. A software solution from the Münchner Membrain GmbH is currently in use in three of its works. Real-time data availability as mentioned above is centrally important for optimum control. The MembrainRTC (RealTime Communicator) communications server is the heart of the application in this respect. It “handles” all the necessary data in an optimum way between the master ERP system (SAP), the (mobile) front-ends, and the materials management system SAP MM (SAP Materials Management).
Lieken’s materials management processes comprise central purchasing of raw materials and packaging materials at optimum conditions, call-off of these materials by planners, acceptance, inspection and storage of raw materials and packaging on delivery, and forwarding these materials to the production operation in a way that is optimum for fabrication. For these processes, Lieken’s experts looked for an IT solution that simplifies, standardizes, optimizes and digitally visually displays all these materials management processes.
Tough requirements
One of Lieken’s most important requirements was full integration into the master ERP system to enable materials management data to enter the central SAP, to be viewed and to undergo further processing directly in real time via mobile terminal devices. This was designed to ensure synchronization of materials and information flow, to increase data quality and to achieve faster availability of information for scheduling and warehouse management. However, further demands were imposed on the new solution at Lieken. Another requirement was for incoming goods data recording to take place using GS1-128 barcodes via MDE (Mobile Data Entry) devices, and standardized recording of incoming goods by auto-ID technology. Further requirements included digital recording of quality inspections and pallet movements. Jürgen Middelbeck, Manager Business Competence Center IT, explains that “Although this catalogue of requirements was extremely ambitious, ultimately we were also using it to pursue clear objectives. By visually displaying all the processes, our aim was to achieve higher capacity utilization of all the existing storage areas in the respective production works, while at the same time checking and optimizing the tools to supply the production operation.” Another factor that was important to those responsible in Lieken was for the solution to be scalable for further applications and areas of the company,