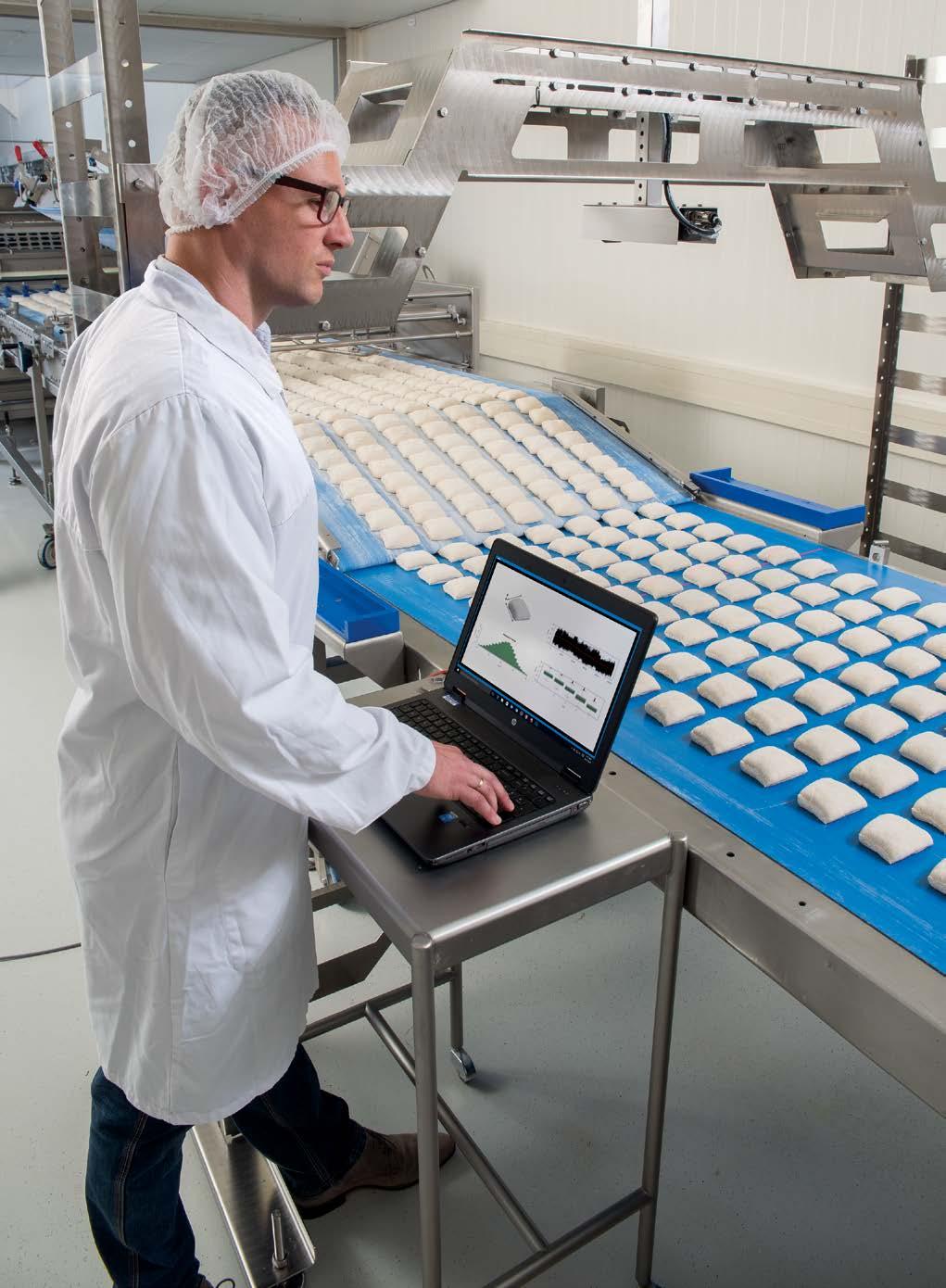
3 minute read
Experts in dough technology
Customers demand the highest quality bakery products delivered on time and at the right price. Rademaker understands these challenges. We provide efficient bakery equipment for every possible production environment, based on your specific dough processes and product requirements. Resulting in the lowest cost of ownership in the market yielding maximal results in terms of product quality and return on investment.
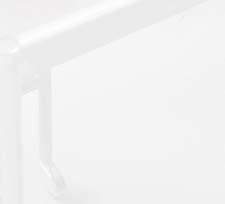
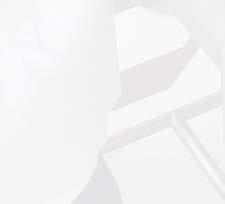
and also for it to be transferrable to other production sites without any problems.
When searching for a suitable solution, Lieken’s attention was drawn to the Membrain GmbH software house in Munich. After intensive discussions and thorough examination of the proposed solutions, Lieken’s Purchasing, Quality Assurance and IT specialist departments decided in favor of a solution comprising a Membrain PAS (Primary Application Server) in conjunction with the Membrain RTC (Real-Time Communications) server. Commenting on the decision, Lieken’s Jürgen Middelbeck says “We chose Membrain because we found the solution strategy to be convincing.” The baked products manufacturer now uses a solution consisting of a Membrain PAS combined with a Membrain RTC, which acts as a data hub and offers applications (Apps) for various platforms.
Data collection solutions
The practical implementation and integration of mobile data collection solutions are very complex and cost-intensive, because generic SAP interfaces are often non-existent. Moreover, many conventional solutions operate using a point-to-point approach that does not offer the required depth of integration and flexible connectivity options. Data storage in the Membrain solution takes place consistently in the SAP system, and the availability of data in accordance with the company’s specifications is guaranteed at all times. This enables uninterrupted operation even during short-term system failures or during maintenance windows. The standard software has an SAP-certified interface and guarantees the real-time availability of all data – stationary and mobile. The “Hybrid Mode” functionality also offers uninterrupted working, entirely irrespective of whether an employee has a “live” connection to the system. Thus it is also possible to work in offline mode. Data is automatically synchronized in the background as soon as the mobile device regains an active connection to the master system. The native application keeps the data available at the same time. This is also said to enable maximum flexibility and unrestricted intuitive work, even if the employees do not have an in-depth knowledge of IT.
Implementation
Lieken implemented the solution in close collaboration with Membrain. The first action after installation was to define the applications and screen templates for the handheld devices. This took place in a three-day workshop together with Membrain’s developers, during which the functionalities, forms layout and interfaces to SAP were defined and then programmed. Jürgen Middelbeck comments that “Implementation was quick and well-structured, and we were already able to test the first of the forms and processes after two to three weeks.” Further development then took place in an iterative process between the two companies, in which the entire development cycle lasted approximately eight to ten weeks. “One specific challenge was to create an application on the MDE devices that required the fewest possible number of manual inputs.” The requirement was for data-gathering to take place by scanning barcodes or simply confirming pre-defined values, thus allowing an on-site employee to complete his/her tasks more easily and faster.
The Membrain solution is now in use in three of Lieken’s factories, and is being used in combination with SAP MM in the merchandise planning and incoming goods areas for raw materials and packaging. Warehouse administration functions are also being used. The old solution was largely a manual process and thus also error-prone because goods were received by hand, using paper delivery notes. Faster processing of incoming goods reduced costs, and the precise display of material stocks in SAP increased data quality. This also led to more accurate scheduling and to higher capacity utilization of available storage areas in the respective production works.
Plans for expansion
Based on their experience in using the Membrain, Lieken already has plans to extend it to all the other production facilities. An expansion of the system is also already at the planning stage. According to Jürgen Middelbeck: “In parallel with its use in materials management processes, we have already started a new project based on Membrain technology. This new project involves using mobile devices or terminals to collect and record key production indicators and key quality indicators so as to make these data available to central locations more quickly.” Due to the solution’s scalability, mobile data collection can also be transferred step by step to other areas such as outgoing goods, order-picking, dispatch, maintenance etc., since these are based on the same platform from the technology point of view. +++
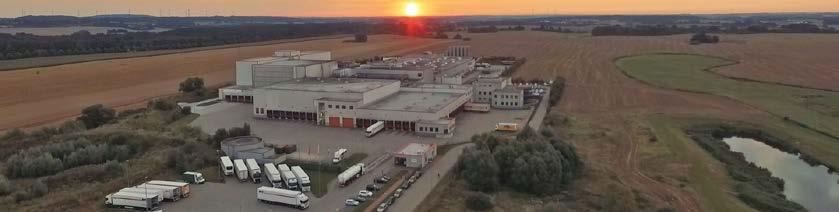