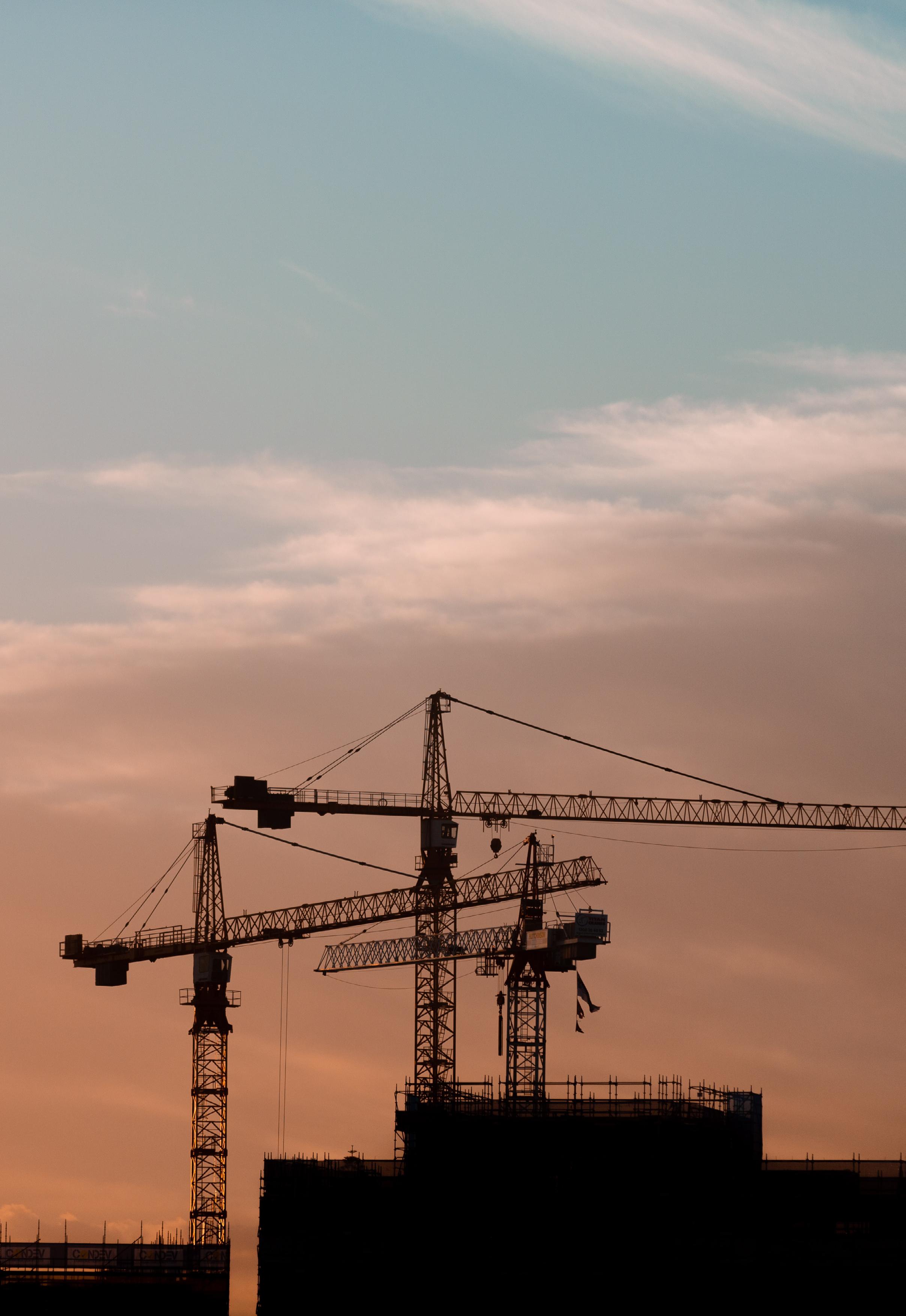
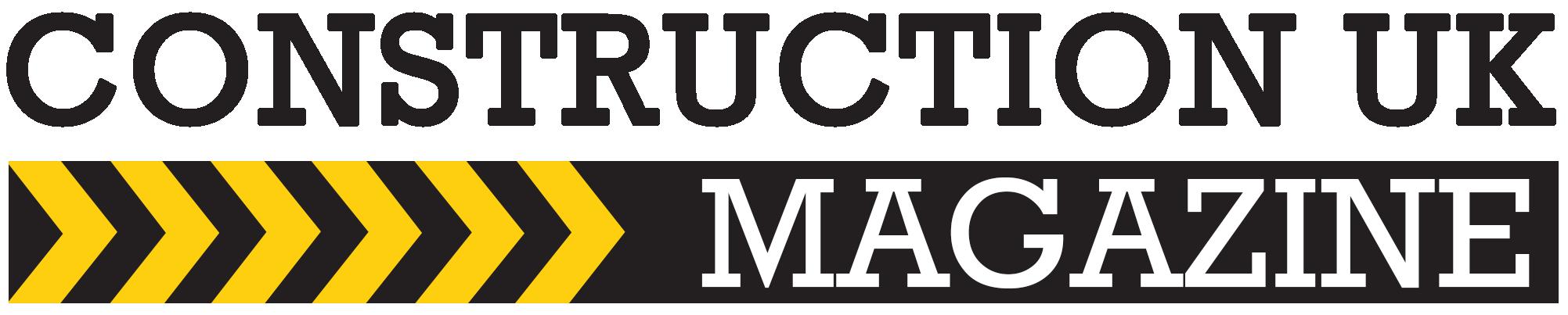
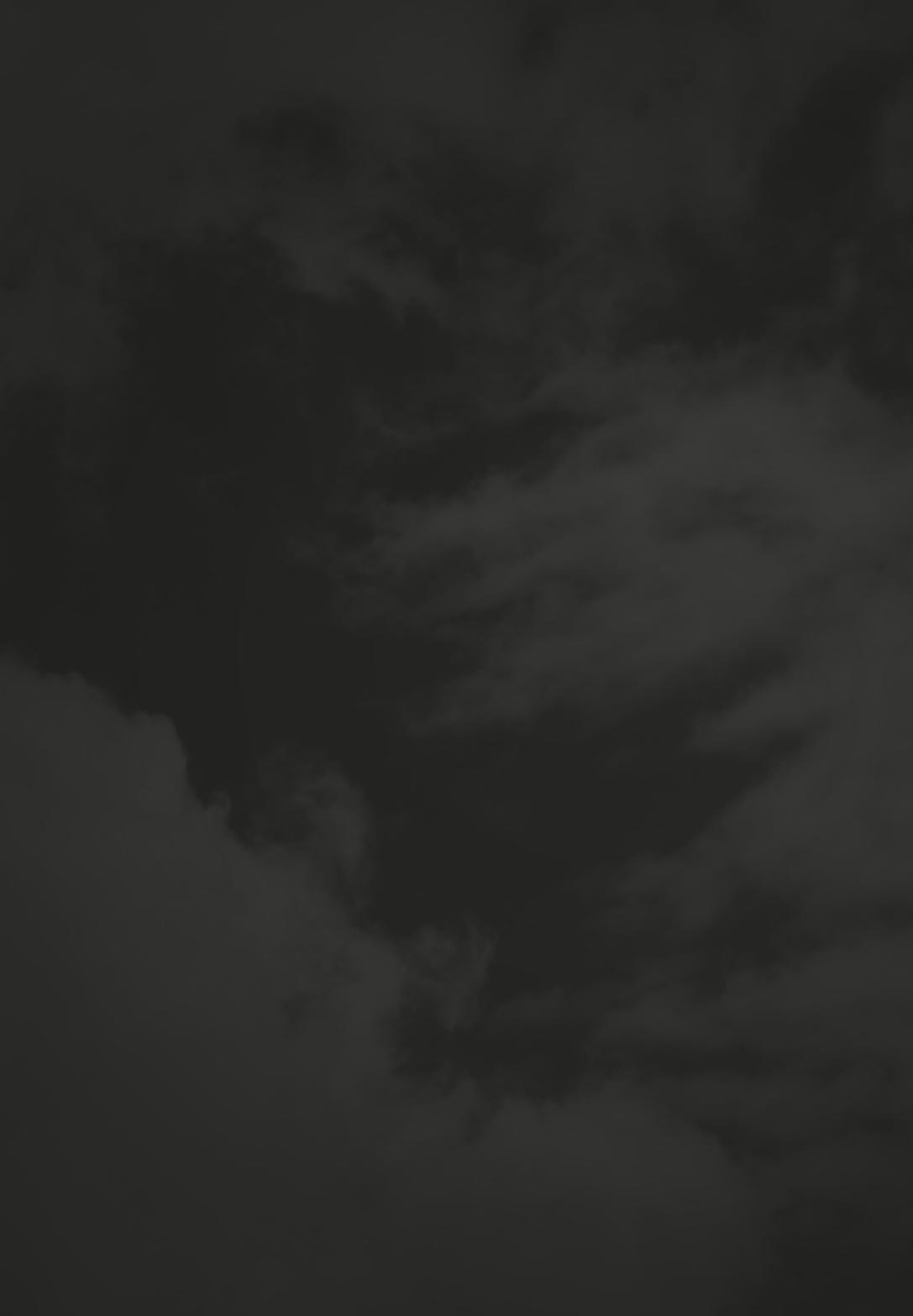
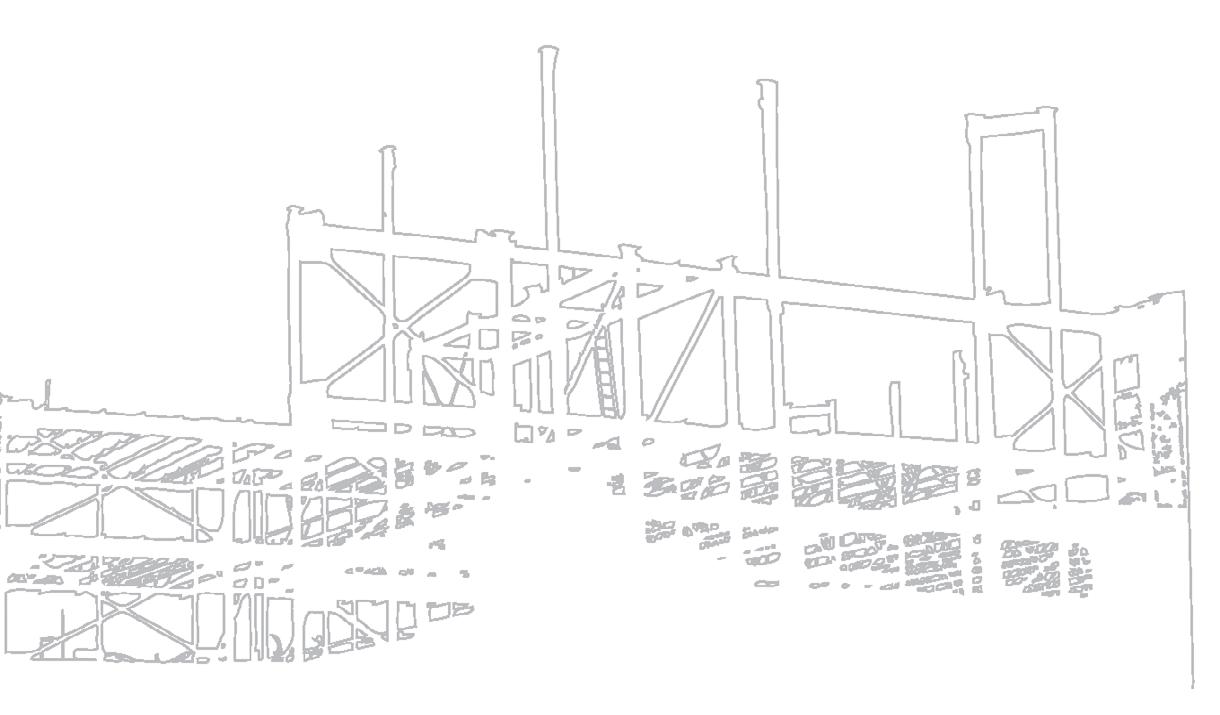

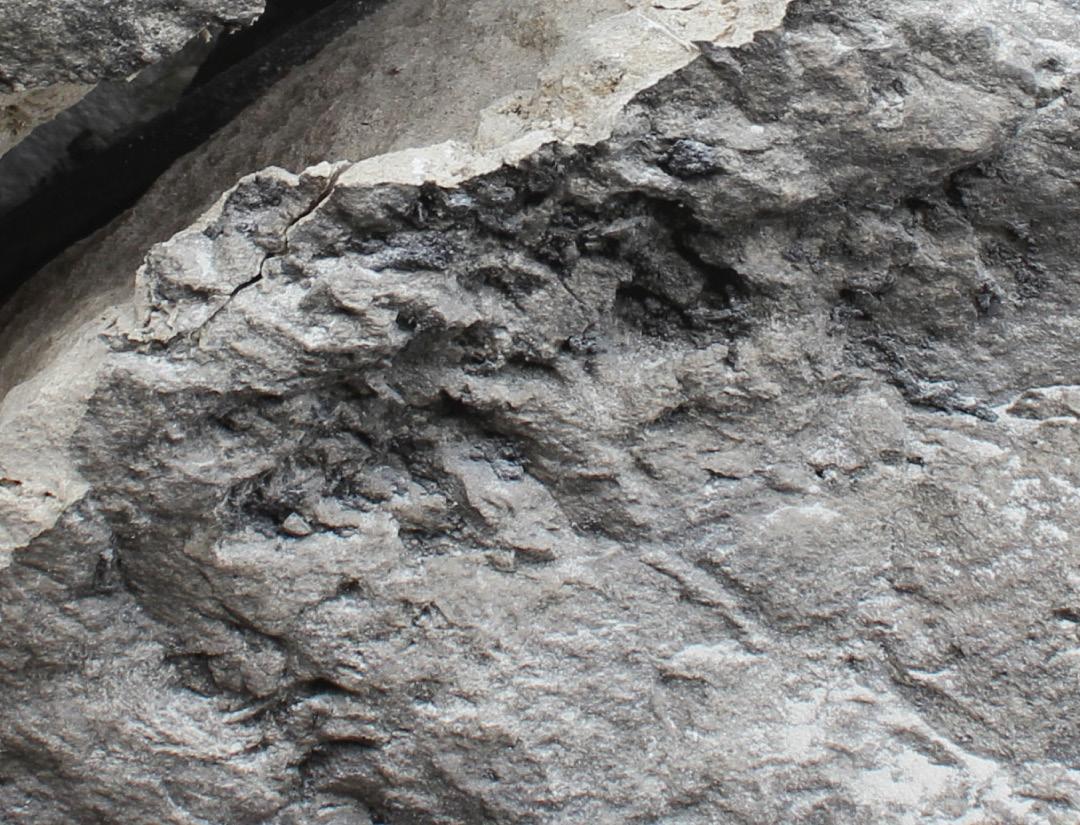

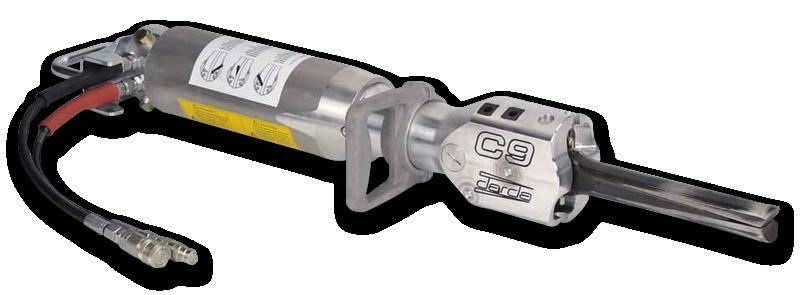

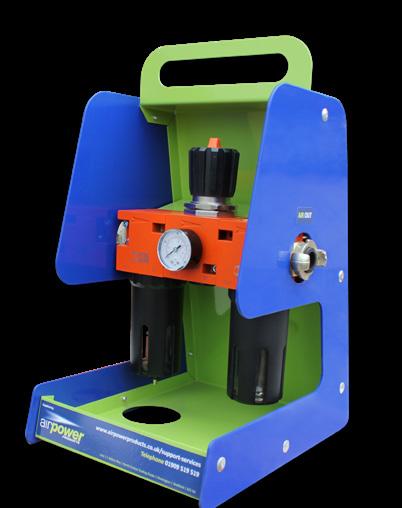
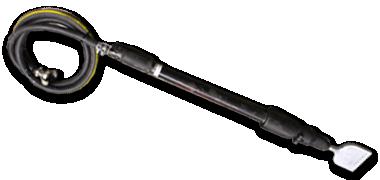

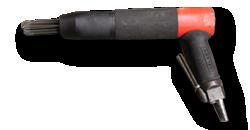

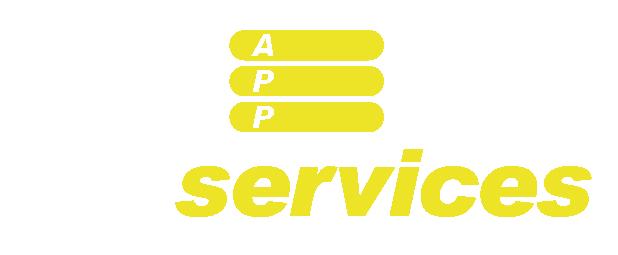
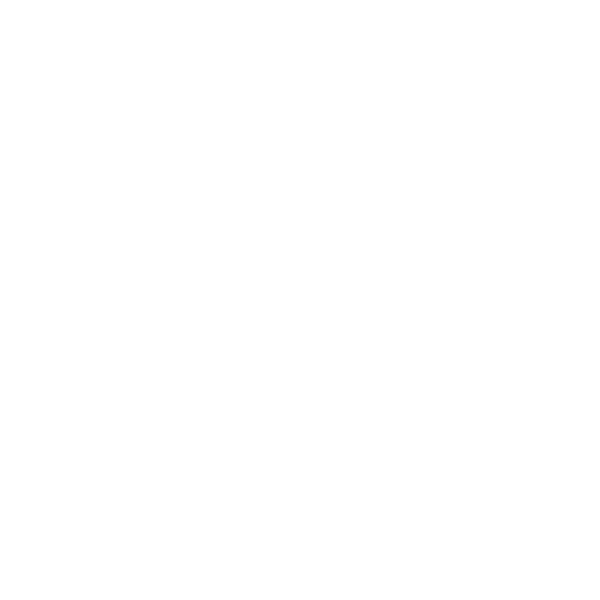
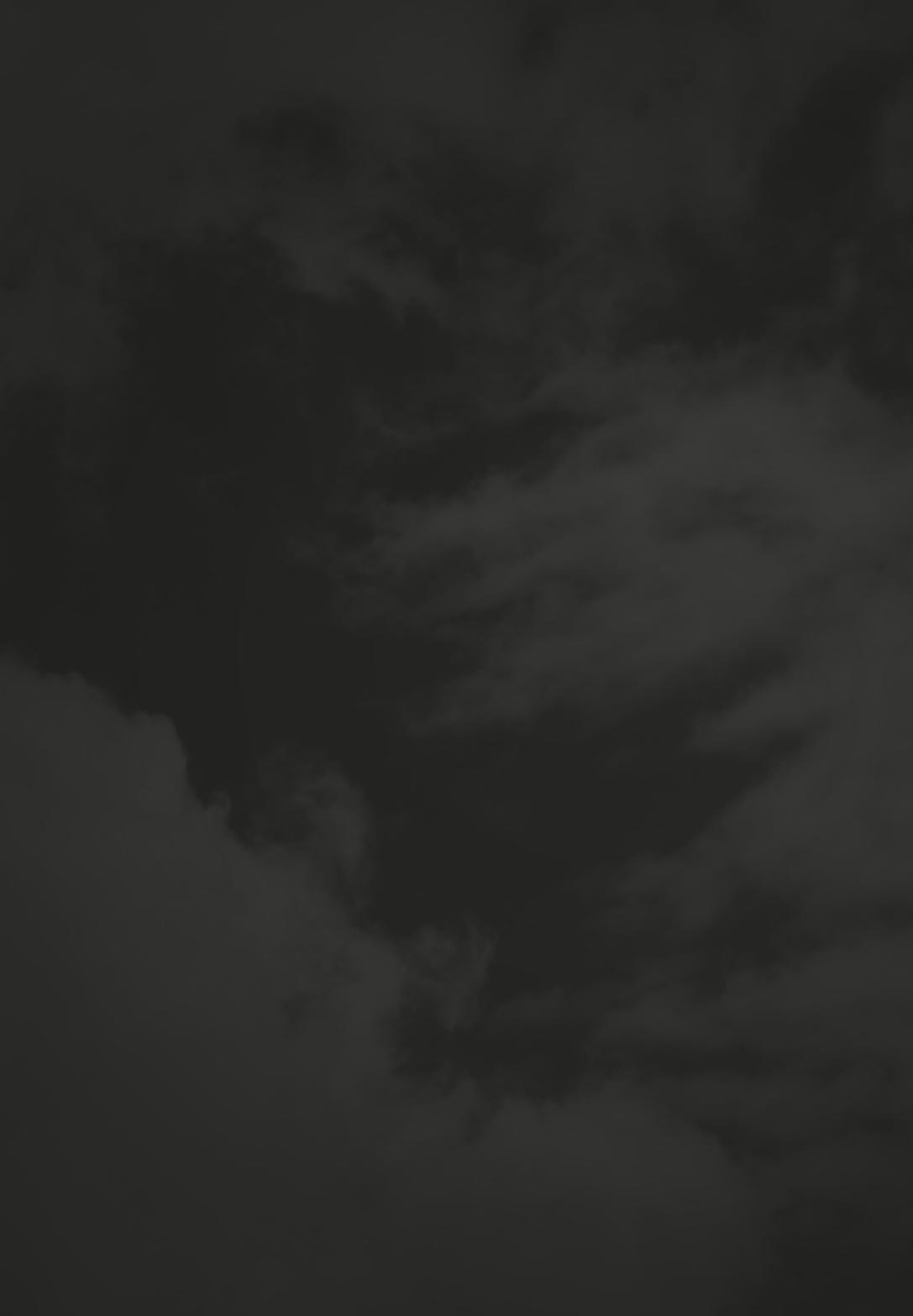
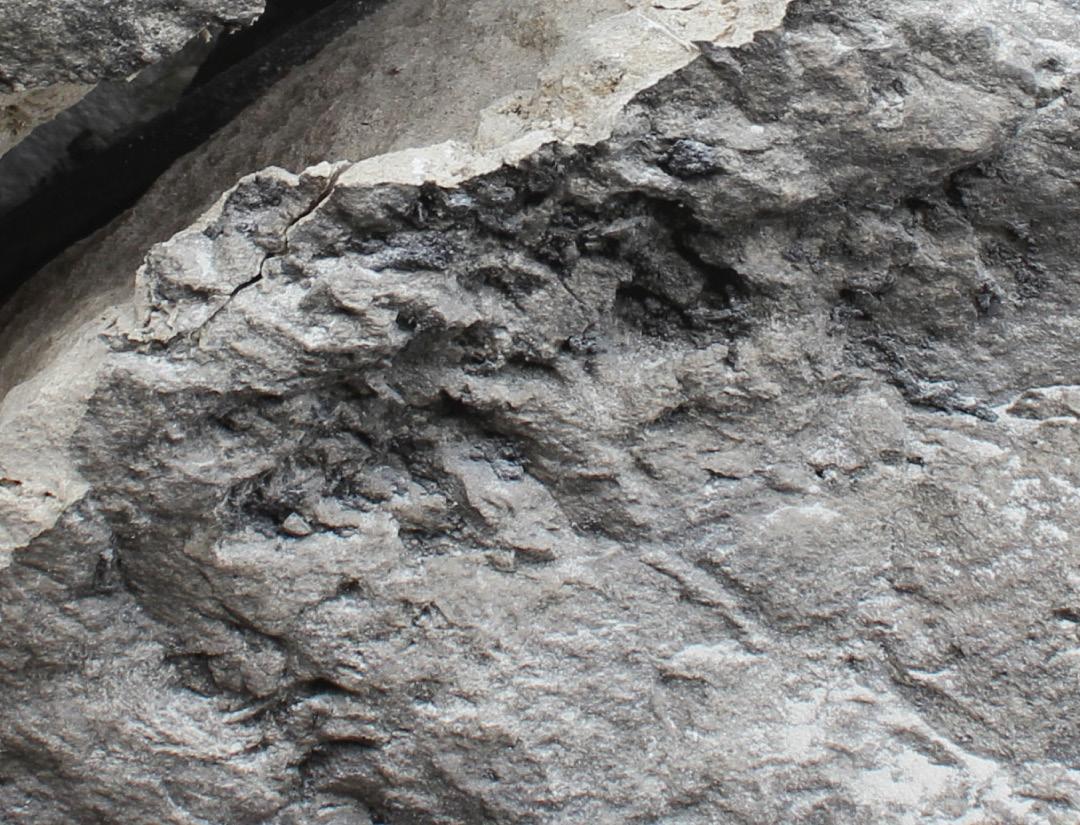

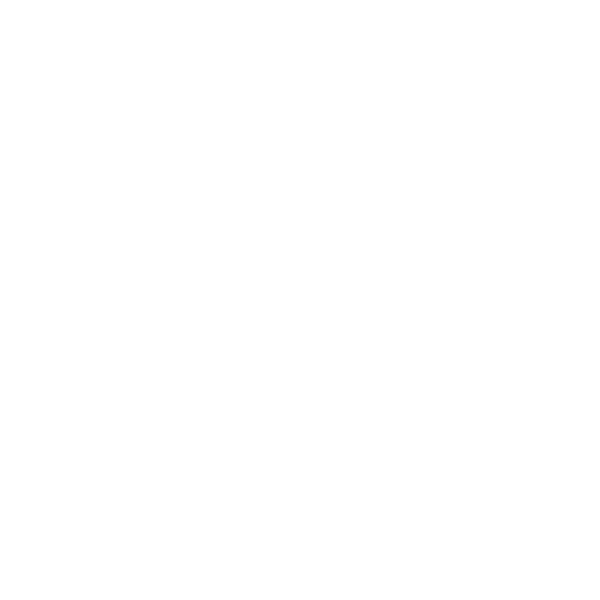
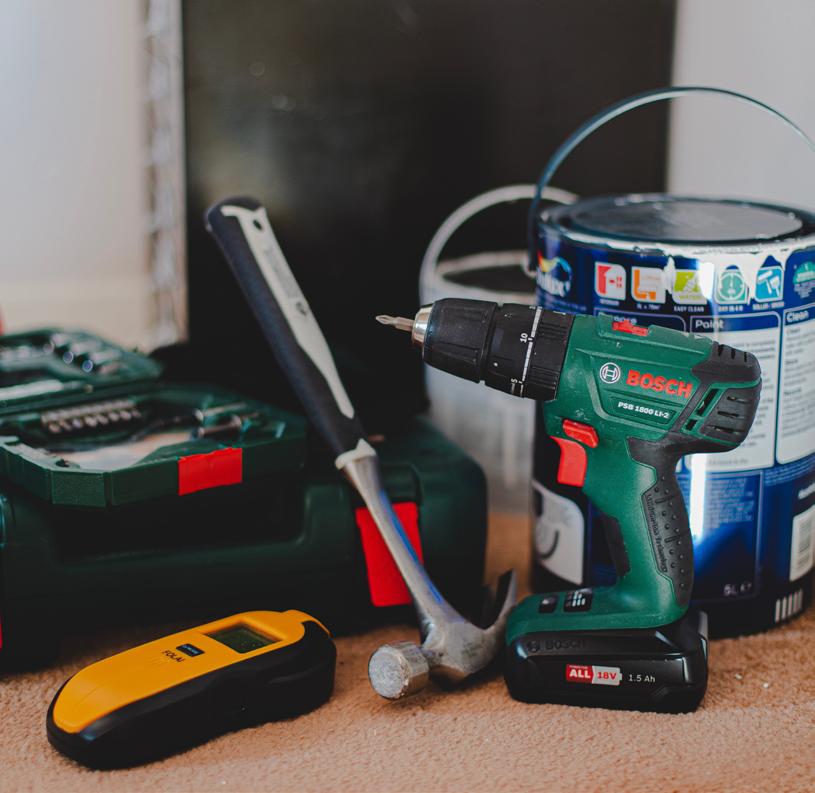
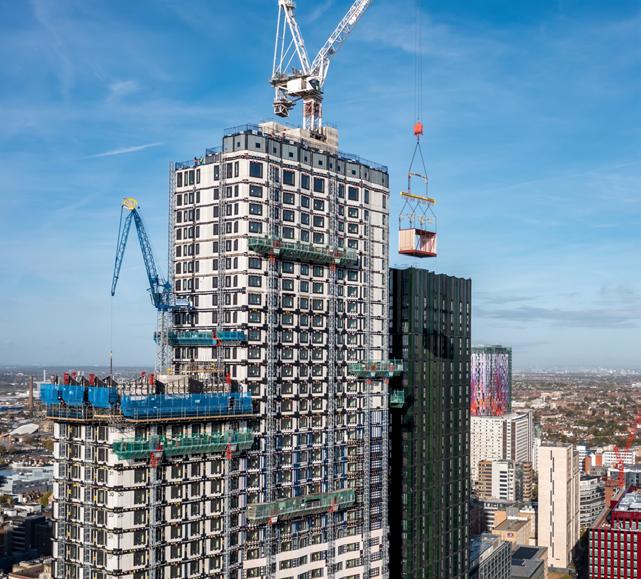
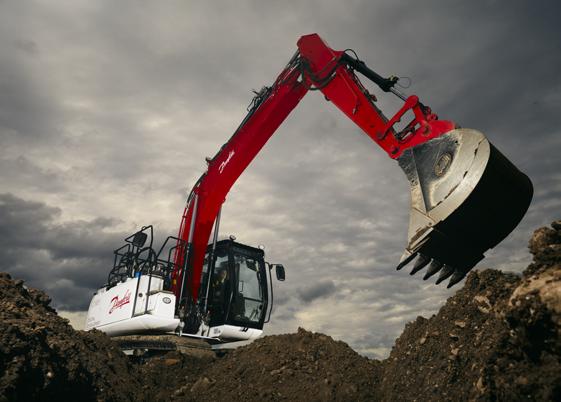
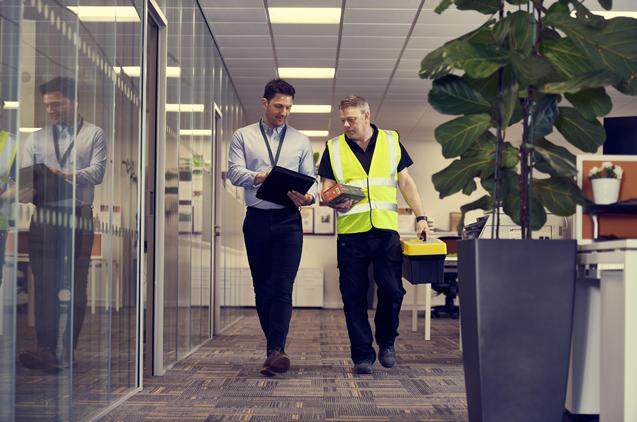
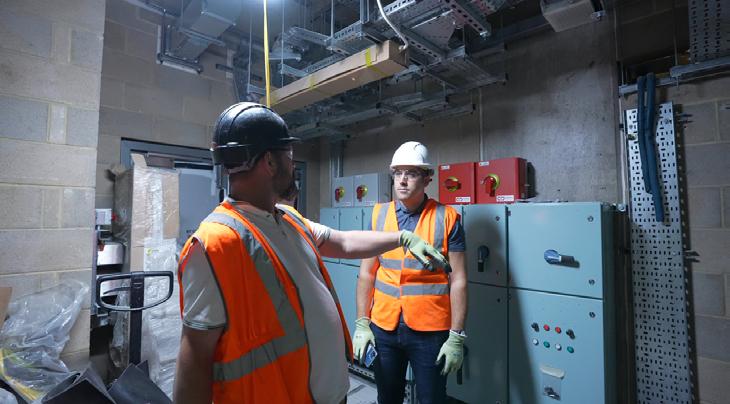




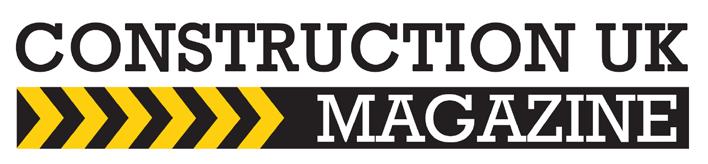
British Gypsum has made further progress towards its goal of being carbon neutral by 2050, thanks to the introduction of Hydrotreated Vegetable Oil (HVO) fuelled vehicles to its UK fleet.
This additional investment in low-emission vehicles reflects British Gypsum’s ongoing commitment to significantly reducing its impact on the environment, putting it on course to achieving its pledge of net zero carbon emissions by 2050.
British Gypsum has started to convert its HGV fleet from diesel to HVO and is expected to use approximately 75000 litres of fuel per week. This means that around 40% of the company’s UK fleet will now operate on HVO fuel, with a further 10% using Liquefied Natural Gas (LNG). The use of multi-fuelled vehicles at this scale is expected to reduce British Gypsum’s carbon emissions by approximately 70%, year on year.
To support the implementation of HVO vehicles, British Gypsum has made several upgrades to
site infrastructure, including an HVO refuelling point in Robertsbridge and a new fuel island capable of delivering 110,000 litres a week at its Distribution Centre in Gotham.
HVO is an emerging ‘drop-in’ fuel replacement for diesel, and is manufactured at refineries from waste materials such as cooking oils and other waste streams that are not fit for human consumption. The British Gypsum vehicles are using Green D+ HVO, which is an EN15940 fuel - recognised by almost all major engine manufacturers as it leaves no carbon deposits, and also has a cleaning effect on engines. It’s becoming more ubiquitous due to its wealth of environmentally-friendly benefits, including reducing greenhouse gas emissions by up to 90%.
To reach net zero in 2050, global net human-caused emissions of carbon dioxide need to fall by about 45% from 2010 levels by 2030. In October 2021, more than a third of businesses across all industries reported taking at least one action to reduce emissions.
Contractor and developer Real has been appointed to construct 92 quality & affordable homes in the London Borough of Sutton Town Centre.
The new homes at Beech Tree Place will be delivered as part of the broader revitalisation of the Town Centre and will respond to Sutton residents’ desire to deliver sustainable, quality led projects which protect heritage & promote sustainability in a changing commercial environment. Real will dedicate its work to support the broader ambitions of Sutton council and residents, by working
sympathetically and proactively to ensure the successful delivery of these affordable homes.
Attention to sustainable energy will be at the heart of the project, including modern installations, like air source heat pumps to provide heating and hot water. The development will be gas free and follow exemplar design methodology.
Beech Tree Place residents will benefit from a new communal rear garden, an open green roof-top and internal communal spaces to socialise and meet.
Sutton Council, along with its construction partners have paid particular attention to the heritage of the neighbouring Grade II listed, St. Nicholas Church and have begun the much anticipated process of opening up the gyratory to a more welcoming and accessible public realm design.
Mark Unsworth, Regional Director of Real LSE, said: “We are pleased to be working with the London Borough of Sutton on this project to deliver modern, spacious & affordable housing for Sutton residents. We are proud to be supporting the borough’s
York Against Cancer are pleased to announce that Lodestone Projects have been appointed to construct the brandnew Leveson Centre, a support centre for people living with cancer, at the York Community Stadium, with work commencing this week.
Project Management company Turner & Townsend have been managing the contractor tender process which was sent out in the summer. Two companies were shortlisted with Lodestone Projects coming out on top after careful assessment. The tender criteria was based on Quality, time management & Cost which were all successfully met through Lodestone Projects detailed proposal.
James Gilyead, Director at Turner & Townsend commented; ‘‘Turner & Townsend are delighted to be working with York Against Cancer to help to produce an outstanding cancer support centre, we are proud to be involved in such a meaningful scheme that will see true benefit to its users. Having appointed Lodestone Projects as the principal contractor, we are confident that their experience, innovative thinking and attention to detail will bring exactly what York Against Cancer are looking for’.
Lodestone Projects experience of fitting-out similar sized units includes the University of Leeds Clothworkers Central, Skipton Building Society branches across the UK and Fibre Extrusion Technology CAT A & B refurbishment.
Josh Donnelly, Managing Director at Lodestone Projects says “I am very proud and appreciative that Lodestone Projects have
been trusted with the delivery of the new Leveson Centre.
York Against Cancer is an important and life changing organisation which is truly making a difference to people’s lives. This will be a game changer for the region, with amazing people providing world class support and care for those who need it. We are absolutely delighted to be part of a fantastic team delivering this much needed facility.
wider regeneration goals, particularly at a time when affordable housing is needed due to the cost of living crisis and increasing rental prices.”
Cllr David Bartolucci, Lead Member for Housing, London Borough of Sutton, said: “The London Borough of Sutton is committed to maintaining and improving its council estates, so we can continue providing quality homes for our existing residents and the broader community. We are therefore pleased to have selected Real LSE to deliver the Beech Tree Place scheme.
“Real LSE are vigilant to the present challenges in the construction industry and are engaging with residents and Sutton Council on how we ensure the resident co-design scheme is fulfilled to the highest standard.
“We look forward to working with them and Beech Tree Place residents, in order to deliver and provide 92 ‘exemplar’ homes for local people.”
The Leveson Centre has been designed by Award Winning Leeds Architect and Interior Design firm, Fuse Studios. Fuse’s design concept fits the brief supplied by the charity which was ‘…to implement a design that can be a force for good. To create a space where anyone will feel at home a retreat, a sanctuary, an area to escape to where you can tackle one of life’s toughest challenges.’
CEO of York Against Cancer, Julie Russell, said; ‘With the contractors now on site, we are looking forward to having the development complete so we can welcome everyone into the new Centre, this really is a huge milestone for both the charity and the region, and we can’t wait to open the doors.”
If you would like to support York Against Cancer in the work they do to help cancer patients and their families across Yorkshire, you can do so by donating to them here: https://www.justgiving.com/ campaign/YorkAgainstCancer
Willmott Dixon Interiors has been appointed to deliver a new biomedical research and development facility in central Oxford.
The fit-out and refurbishment specialist contractor will redevelop two former retail warehouse assets on Botley Road into c.65,000 sq. ft of world-class laboratory and creative office space.
Known as Inventa, the redevelopment is being delivered on behalf of a joint venture between property developer, Mission Street, and BentallGreenOak, a global real estate investment management advisor, which acquired the property in 2021.
Willmott Dixon Interiors will reuse and extend the existing structure of the two warehouse buildings, adding a new internal floor and a colonnade to the north elevation.
The additional floorspace will enable the creation of a new reception area and a combination of sustainable new spaces for market-leading life science companies. They include enhanced common areas and meeting rooms, new collaboration and circulation spaces, breakout areas and café provision, as well as a new cycle centre and shower facilities.
The building fabric will also be substantially upgraded, including a new façade, while new mechanical and electrical services will also be installed.
Externally a cycle and pedestrian route and a newly landscaped car park will create a revitalised visitor experience, with landscaping at the rear of the building doubling as an area for flood mitigation.
Inventa is expected to be complete in summer 2023.
Morrison Data Services (MDS), part of M Group Services’ Energy Division, is proud to announce it has secured a contract extension with EDF. The relationship between MDS and EDF ensures the continued rollout of EDF’s smart meters across the UK.
This rollout is part of the government’s Smart Meter Implementation Programme (SIMP) which helps consumers in the UK manage their energy consumption leading to a more efficient service across the grid as dependency and demand increases.
The initial contract was first signed in 2015 and to date, MDS has installed hundreds of thousands of smart meters
for their client. The two-year extension will see these installations continue until the end of 2024 with the opportunity to extend the contract again.
David Dale, Director of Installation Services at MDS, said: “This contract extension, with one of M Group Services’ key strategic partners, is testament to our people’s hard work across the contract. The trust shown in MDS by EDF shows our reliability and dedication as a business.”
M Group Services’ Energy Division provides a range of services including, metering services, regulated data management, national meter reading, energy theft detection & resolution and smart metering support services.
A CGI of Inventa, a new biomedical research and development facility that is being created in central Oxford.The latest market report from international property and construction consultancy Gleeds reveals that rising labour and materials prices continue to threaten growth in the construction sector. Over three quarters of contractors questioned said they had seen further increases to labour rates in the preceding quarter, and nearly 70% reported continuing volatility in materials prices.
The ongoing escalation of costs was cited as the biggest threat to the industry, with 77% of contractors believing that growth is suffering as a result and around a third of all respondents warning that recession will do further damage going into 2023. Issues around availability of labour also persist, with 60% of contractor respondents experiencing problems, however almost half of all of those quizzed were optimistic
that concerns around the availability of materials were beginning to settle.
Gleeds CEO Graham Harle said of the survey, “Our report reveals that spiralling costs of materials and labour show no signs of abating, although there is some hope that availability of both is stabilising compared to the previous quarter. It seems inevitable that the turbulent political backdrop will impact investor confidence, and the prospect of a recession has led to predictions of a decrease in tender opportunities going into Q4.
HM Revenue and Customs (HMRC) is urging contractors in a wide range of roles across the construction sector not to get caught out by unscrupulous promoters of tax avoidance schemes.
Tax avoidance is when people bend the rules of the tax system to try to pay less than they should. But those who join avoidance schemes then end up having to pay the tax due in the first place – as well as interest and potentially penalties. That is on top of the fees or margin they have already paid for joining the scheme.
HMRC wants to stop people being drawn into such schemes and also to help them leave tax avoidance schemes if they believe they might be caught up in one. HMRC is working with construction firms to give them the tools to educate the contractors who work for them on the risks of using tax avoidance schemes.
This is because each of us is responsible under UK law for paying the correct amount of tax.
This still applies if contractors have appointed someone else to deal with their tax affairs or have been given bad advice – the ultimate responsibility and risk rests with the individual.
HMRC is urging contractors, agency workers or those who work through an umbrella company to check how they are paid to make sure they’re not caught out. They can use the interactive risk checker to see whether their current contract could involve tax avoidance.
To find out how to spot the signs, report avoidance, or get help leaving or reporting a tax avoidance scheme, HMRC wants contractors to:
Recognise...tax avoidance. Learn how to spot the signs, understand how these schemes operate, and know the risks.
Understand...how umbrella companies work. If you work through an ‘umbrella company’ - here’s what you need to know about how they should operate.
The consultancy’s report also found that a massive 91% of respondents believe the government should be doing more to support retrofitting measures and energy performance, with 64% of noncontractors and 47% of contractors reporting that clients themselves are giving greater consideration to both on projects. Meanwhile, 82% and 69% respectively said that projects are also increasingly incorporating futureproofing measures such as flexibility for change of use or easy renewal of components.
Check...your pay and contract arrangements. Looking at your payslip is a useful way to check for signs that you may be involved in a tax avoidance scheme.
Get help...if you think you’re already in a tax avoidance scheme and don’t know how to get out.
For further information read Tax avoidance: getting out of an avoidance scheme.
HMRC publishes Spotlights about tax avoidance schemes on GOV.UK that warn people about what they should look out for. Spotlight 60 published in August 2022 specifically warns about noncompliant umbrella companies and what to look out for.
Productivity remains high, though and the teamwork we’ve seen on projects to combat these challenges has continued to increase, with over 80% of those we surveyed experiencing greater collaboration on schemes.
Local suppliers have been involved in two Linden Homes launch events for the forthcoming Langham Meadows location in Langham.
Vistry Group held an information day for prospective purchasers on Saturday 3 September at Langham Community Centre, with refreshments provided by Frinton Golf Club.
A second event, when the first homes were released for sale, was also held at the centre on Saturday 24 September, and also involved the golf club’s catering team.
Golf club catering manager James Oxley said: “It was nice to be involved in a community event.
“I live close to Langham and have a good relationship with those in the village.
“It is a lovely area, and we took our children to school here.
“We work at the community centre a lot to provide catering for events like this.
“We provided tea, coffee and fresh juices as well as homemade cakes and cookies.
We had also been looking forward to catering for the launch of the first homes for sale in phase one of Langham Meadows later in the month which was equally successful.
Vistry is building 20 new properties under the Linden Homes brand in phase one at Langham Meadows, including a choice of threebedroom houses which will be completed in time to meet the Help to Buy construction deadline at the end of December this year.
Welcome to our Editor’s Products of the Year, where you will find carefully selected companies, chosen for their product innovations and quality. Throughout the feature you will find information on these companies. Please also visit their websites for further information and enquiries.
At Door Controls Direct we are continually applying our expert knowledge, quality products, and exceptional value to provide product solutions to the FM and building industry to keep people safe and secure. We have been trading for 25 years but our history of supplying architectural ironmongery dates back over 100 years. Our recently published product catalogue makes the procurement of our door hardware even easier.
Providing our customers with access to trusted and reliable branded products and information, supported by guidance from our technical team of industry experts is the foundation which Door Controls Direct has built itself upon and to this day is our passion. Being able to engage with our customers directly allows us to offer a premium service and quality products at a competitive price.
Our company has gone from strength to strength, and we would especially like to thank you, our customers, for your continued loyalty and for allowing us to keep you at the heart of all our decisions.
For more information on our products and services, you can visit our website: https://doorcontrolsdirect.co.uk/ or contact our sales team on 01305 263300 sales@doorcontrolsdirect.co.uk
UK welfare manufacturer, Boss Cabins is delighted that its sustainable solarpowered Deep Green range of site welfare has been recognised by Construction UK Magazine in their round-up of the year’s best products.
Deep Green has had a phenomenal 2022 with the welfare cabins’ solar performance outstripping all expectations. With over 500 Deep Green units now in the field, extensive data gathered from the units’ on-board remote access telemetry system has demonstrated that almost all these units have functioned almost entirely without the generators running at all. With no generator usage, fuel consumption and costs for Deep Green users have plummeted. And more importantly, zero generator run-time means zero CO2 emissions at the point of use meaning these cabins can be a largescale contributor to helping construction companies and other welfare users achieving Net Zero targets on site.
As well as being proven in practice on worksites all over the country, the fuel cand carbon saving properties of the Deep Green range have been analysed and verified by independent industry assessors Carbon Footprint Ltd. Their in-use Energy Saving Assessment concluded using that a Deep Green welfare unit in place of a standard one
could save up to 3400 litres of fuel each year on operation and servicing and reduce CO2 emissions by 8.4 tonnes.
In addition, Deep Green was recognised by judges at this year’s Showman’s Show winning Boss Cabins a Highly Commended Award in the Green Suppliers and Innovations category.
As well as solar technology, Deep Green units incorporate a unique patented rain harvesting and grey water recycling system which sees sterilised rainwater used for hand-washing and then re-used to flush the toilets. They are also fitted with a patented Infinity generator that needs servicing 10x less than the industry standard. In addition, the telemetry system monitors water, waste and fuel levels remotely meaning service visits can be planned precisely when they are needed with no wasted trips. Together, these innovations significantly reduce the need for service visits and their associated environmental and financial costs.
Deep Green cabins are built from stainless steel with a guaranteed lifetime of 25 years and are 97.2% recyclable at end of life.
Boss Cabins’ Managing Director, James Kearsey, says: “We’ve had a fantastic response from the major players in the construction and infrastructure sectors. They recognise how our Deep Green 2030 range gives the welfare industry a product that truly reduces environmental impact while not sacrificing any of the performance you need or expect from a high-spec welfare cabin.
Even better, this success in removing carbon from the cabins’ operations can easily be monitored and reported for the purpose of ESG scoring, investor reports etc. using the SolarTrack remote telemetry system. Users get 24 hour remote access to transparent information showing exactly what their energy usage is and what source it derives from.
The Deep Green 2030 range includes mobile and static welfare units plus portable toilet solutions. For information contact Boss Cabins Sustainable Welfare Team 01778 300475, sales@bosscabins.co.uk, www.bosscabins.co.uk
and Remediation Tax Relief is one of the best kept secrets in the UK construction and building industries.
It is available to recover costs of carrying out remediation work prior to receiving planning permission to render the land useable for new developments.
Qualifying criteria are few. You must be a registered UK corporate entity and the owner of the land. You cannot claim if you own the land and caused the contamination. From this point most costs associated with the clean-up measures, disposal of waste and making good the finished projects form the basis for cost evaluation and submission of the claim.
Known contaminated land can be claimed for. Derelict land that
has remained unused from the earlier of 1st April 1998 or date of acquisition can also form the basis of a claim, especially if it has suffered tipping and illegal waste disposal over the years.
Since Land Remediation must
construction works begin, it is advised to consider remediation
All contributory costs should be identified and recorded. These are wide and include your own company costs of
contractors, suppliers, travel and subsistence costs, surveys, tests, disposal and replacement
Generally, brown field sites and land that has existing buildings will be contaminated, especially where older buildings
are suspected of containing asbestos in any form. Used land can contain old foundations, utility services, hydrocarbon and chemicals whatever. If remediation surveys discover radon gas emissions, Japanese Knotweed and any other invasive plant species and contaminants deposited through earlier occupier activities, these too can be included in remediation costs. Where buildings contain asbestos, costs of removal and either demolition or insitu encapsulation and sealing of the asbestos elements is a claimable cost.
The definition of what is contaminated land is peculiar to land remediation relief legislation and is broader than for planning purposes as in Environmental Protection Act 1990. It is beneficial to know land remediation relief is available before purchase of land. This reduces possible uncertainty and risk.
MCS Corporate urges its clients to consider all possible sites for development and planning. We can give early assurance of a likely claim and work with you to identify, prepare and submit claims as the remediation proceeds. Contact T: +44 (0)1926 512475 E: charlotte@mcs-corporate.com W: www.mcs-corporate.com
To qualify for Land Remediation Tax Relief your company must have incurred costs on cleaning up land or buildings considered to be in a contaminated state. The scope of costs allowed is generous.
You must be registered as a limited company in the UK and be the owner of the land or building at the time of the remediation work. In addition, the land or building must be owned either as a freehold or longer-term leasehold.
Common examples of qualifying contamination:
• Asbestos
• Ground and landfill gases
• Japanese Knotweed
• Sulphate contamination in soil and concrete
• Arsenic
• Removal of redundant utility services and concrete foundations
Qualifying costs can include surveys, excavations, soil and groundwater treatments, staff costs, materials and subcontractor costs. Claims can be made for categories of derelict land. This can be advised with relevance to time periods when land could be considered for derelict status.
Regardless of the industry you operate within, if you’ve acquired land or buildings in a contaminated or derelict state for intended commercial use, you could claim.
Astra Lumos is an exclusive and bespoke lighting and electrical solutions company. They have been installing high-end lighting designs integrated with control systems since 2014 and although they have been doing lighting design alongside this, until their rebrand, they haven’t advertised this fact. With their new name and branding they are making waves and their existing clients have really got behind them.
Do you know how lighting can affect colours, mood or even energy of a room? Have you thought about a bespoke lighting design for your next project or are you just assuming the architect or M&E company will take care of it? Are you tired of looking into your garden at night and seeing nothing but abyss?
Based in the Cotswolds but serving clients nationally, Astra Lumos offer bespoke lighting and electrical designs with the huge benefit of being able to install the designs. Historically Astra Lumos would be given a design which would have quite a few “flaws,” due to the lack of installation experience by the designer. David Ritchie (one of the directors at Astra Lumos) is now chief designer, having worked on-site since the age of 18. With nearly two decades of on the tools experience, Astra Lumos are confident their designs are able to overcome the “usual pitfalls” of a traditional lighting and electrical design.
Lighting can completely change the ambience of a room and affect all aspects of the space. From altering the colours of the soft furnishings, to changing the energy of the room, lighting is a hugely important aspect of interior and exterior design.
Light added to your garden is a great way to ‘extend’ the space from your home to the outside, creating an additional ‘room.’
As Astra Lumos put it, “The right lighting can illuminate your garden, adding a soft glow which brings to life an almost ethereal and magical space you can enjoy well into the night. From creating a safe path through the garden to highlighting textures and features, lighting can add both beauty and function to your outdoor space.”
• Design led installations – we have the capabilities to consult and advise on design, whilst also completing the installation. This means you will not be left with a design that can’t be installed, and we help to engineer designs that have installation in mind, whether this be sympathy to the architecture, or designing for install time or minimal damage.
• Consultants able to diagnose issues with installations by others – often we are called in to help clients where previous installers have failed.
• Research & Development – unlike other installers, we have an R&D department where we are able to bring custom designed solutions for unique problems.
Astra Lumos is Latin for star light, hence the name choice. Just as starlight beautifies the night sky, our stunning lighting solutions can really amplify the beauty of your garden and home.
With over 50 years of experience, ELA Container is one of the leading suppliers of high-quality and flexible room modules. The German family-owned company with over 1,200 employees and 20 locations worldwide has also become an important player in the UK since market entry in 2018.
The ELA UK office and production facility is located in Scunthorpe. Due to the well-established distribution network, the containers are quickly delivered to customers in all areas of the UK. A comprehensive stock of fully equipped containers and on-site assembly ensures fast and ready-to-occupancy delivery.
The ELA UK sales team on the stand at UK Construction Week 2022 in Birmingham.
ELA Container is represented in Scunthorpe with a twostorey office building.
With a wide product range of multifunctional rooms, ELA containers create optimal conditions. Whether as an office, changing room, recreation room, accommodation, storage container, workshop or sanitary area. Thanks to the modular design and stackability of the units, any project can be built on a small footprint. For example, a large container building suitable for 400 individuals was installed in Central London with over 80 containers across four floors.
At this year’s UK Construction Week in Birmingham, the UK team was represented with its own exhibition stand and as event sponsor. It was shown that there is a massive change in the building industry increasingly towards large and open spaces. ELA creates those spaces where people like to stay, improving the overall wellbeing.
More information at www.ela-container.co.uk
GEZE UK has demonstrated its commitment to supporting customers with technical advice and product guidance with the recent appointment of Ian Prince, who joins the renowned manufacturer of door and window control systems as Area Sales Manager for supply and fit of automatic doors covering the East Midlands and East of England.
Ian will be focusing on building strong business relationships with customers supporting them by analysing their requirements and proposing technical solutions from the company’s extensive range of automatic operators.
With a strong track record of B2B sales and over 20 years’ experience in account management and business development across 5 different industries Ian brings with him a wealth of knowledge to assist customers make the right choices for their projects.
Ian has a BA (Hons) Degree in Marketing, is ADSA accredited and has won the Yellow Pages award for performance several times.
Said Ian ‘I am delighted to join GEZE UK, they are an industry-leading company that offer a complete service of design, supply and fit of automatic doors.
Andy Iredale, National Sales Manager for Automatic Doors and Window Technology added ‘It’s great to have Ian join the team; he has vast experience across several sectors and will be a great asset to the company. He will be an important part of the company’s continued growth.’
For more information about GEZE UK’s comprehensive range of automatic and manual door and window control products visit www.geze.co.uk
As the construction industry gets ready to welcome a new year with a fresh set of challenges and opportunities, 2023 heralds the dawn of changing trends and possibilities in the world of interior timber doors and door sets. Ever one to embrace innovation and seen as a true manufacturing trailblazer, Vicaima bring design, performance and quality solutions to the interiors arena. With this in mind, the launch their latest incarnation of the perennially popular Interior Door Selector (IDS) has been much anticipated.
In recognition of changing specifier preferences, Vicaima is largely moving away from conventional paper-based brochures, towards digital catalogues.
This is not only environmentally friendly, but also enables a more dynamic user experience. New products and useful information can be updated instantly and at the same time enabling links to other resources such as technical data, so that specifiers can be fully equipped to make an informed decision about their next project.
Bigger than ever! This latest brochure contains over 150 pages to inspire professionals who are looking to transform modern living space. From economy options which are ideal for affordable homes in the current cost of living crises, to ground-braking quality designs that create an instant wow factor and set the standard for twenty twenties living!
Although best known for fresh ideas in veneer, foil, laminates and paint lacquered finishes, Vicaima are also opening a window to the future with their new Infinity Range, where digital and precision imagery can re-imagine stone, metal and other surface features, in a way that hitherto was the stuff of dreams!
Of course, innovative doors from Vicaima are not confined to aesthetics alone. With fire safety, security, acoustics, and thermal efficiency very much in the minds of specifiers and regulators. Vicaima Door kit and set solutions build on a framework of rigorous testing and superior constructional cores. Among recent additions to what is already a comprehensive performance range, comes VCP 60 from Vicaima. This in-house developed core, which is thirdparty accredited under the BM TRADA Q-Mark scheme; provides a one-hour FD60S rated door, but with a considerable cost saving over conventional products, thereby improving safety while keeping budgets on track.
What to look out for in the latest Vicaima IDS
There are a great many new products to be found in this latest issue, among which look out for:
• Naturdor Vision – A new range where real wood veneers are taken to new heights, with tones such as Rich Mocha and Fresh Bamboo
• New Economy Veneer Range – Cost effective options such as Red Oak and Walnut Crown EV give that luxury look for less
• Dekordor 3D - Two new colour tones are added to this highly tactile and durable finish range, with Cloud White and Pale Oak
• Visual Sensations - A touch of Scotland comes to this popular foil collection, with the introduction of Highland.
• Vicaima Wardrobes – Flexible configurations to match Vicaima’ s many door finish options.
• Infinity – Endless Possibilities to be explored. Pushing the boundaries of interior design
To download a copy of the Vicaima Interior Door Selector or for further inspiration, Visit www.vicaima.com, contact info@vicaima.com, or Tel: +44 (0) 1793 532333
In the search for the most cost-effective materials in the building, construction, and infrastructure sectors, the fire, smoke, and toxicity (FST) properties of materials are often considered too late. Here, Eric Moussiaux, VP technology at Exel Composites, explains why it’s important to understand the standards, select the right tests, and choose composites that deliver the best FST performance.
Whether it’s windows, doors or curtainwall profiles, interior or exterior cladding, or even railway cable trays, the fire, smoke and toxicity properties of materials should be considered early in the journey of any new project. Fail to do this and by the time you come to consider the FST properties, you’ll already be on the backfoot, potentially having to overspend to acquire a material that meets all your needs. In extreme cases, not considering the FST properties of a material early on could result in businesses having to discard or offload materials they’ve already purchased or make costly adjustments to tooling investments.
Part of the problem stems from the historic discrepancy in fire standards across Europe, which weren’t unified until about two decades ago. Whether it was Germany’s Musterbauordnung (national model building code), France’s safety commissions, Spain’s onus on local authorities, or the UK’s devolved enforcement, there was little harmony in fire safety. Some of these rules were prescriptive — requiring structures to meet specific fire tests — others were
based on performance testing, where the regulation only set out how a building or structure is expected to perform, not how it should be designed. Ultimately, it was clear that fragmentation was creating trade barriers, and hampering business.
In 2000, the European Union introduced the Euroclass system, or EN135011. This system classifies the reaction to fire of construction and building materials, based on three main factors: combustibility, smoke production and the production of flaming droplets or particles. Combustibility achieves a classification from A1-F with A1 being the least combustible; smoke production ranges from S1 to S3, with S1 producing the least smoke emissions; and flaming droplet production ranges from D0 to D2, with D0 demonstrating no dripping. So, for example a material classified as B-s2,d0 would be one with limited combustibility, that produces smoke at a quantity and speed that is of an average intensity, and produces no flaming droplets during combustion.
However, the use of defined tests can be a limiting factor. In a recent project, Exel Composites worked with a customer in Germany to develop a composite cabletray for use on embankments at the side of German railroad tracks. Hot summers can cause the desiccated grass to catch fire from sparks generated by the brakes of a passing train. The resulting bush fire can expose the underside of the elevated cable trays to fire, so it’s essential that the tray can continue to protect the cables inside it.
There is a danger that choosing a simple, well-known test in such specifications, can be less relevant to the real-world application and add unnecessary difficulty. One such test is the UL 94 vertical test in which a small sample — 25 mm wide by 100 mm in length — is lit at the bottom with a 20 mm flame. Picture it like holding a matchstick from the top and lighting it from the bottom; the flame will quickly reach and burn your fingers.
In this scenario, the specified bushfire test is much more appropriate. Here, a normalized quantity of hay is lit under the tray. The tray must then withstand the fire until it stops, without causing structural damage or allowing the internal temperature to rise high enough to damage the cables inside. The difference is that one material composition might fail the UL 94 test dramatically, while surviving the bushfire test with flying colors.
As well as selecting appropriate FST tests, specifying engineers must ensure that the composites they choose are not hazardous to health.
Many composites contain flame retardant additives, which reduce or delay the combustion process using substances such as aluminum trihydrate (ATH), which give off far less toxic smoke when burned compared to traditional halogenated additives.
However, the associated filler material leaves less room for reinforcing fibers, which can affect structural performance. The answer is to work with a composites partner that understands the complex manufacturing and pultrusion techniques to produce composites that deliver both structural and FST performance.
The takeaway here for anyone working in the building, construction, or infrastructure sector is to consider FST requirements early, understand the standards, select the right tests, and choose composites that deliver consistent, high-quality results.
To find out more about composites for building, construction, and infrastructure applications, visit exelcomposites.com
Established in 1979 by MD Derek Ward, the Envirograf® brand quickly evolved to become a leading force in passive fire products. Having developed fire retardant and fire stopping products for numerous scenarios, the company’s reputation as an innovator and developer is widely recognised with many products unique to Envorgraf®.
From Intumescent paints that provide over 60 minutes protection on timber, steel and plasterboard, to intumescent seals and electrical fire protection, the vast range of products enjoys widespread international demand.
Mr Ward says that, when it comes to passive fire protection, every risk must be considered to ensure that loss of life and property are kept to a minimum. While many people are aware of the importance of fire barriers in preventing or delaying the spread of fire, they do not always consider the implications when breaching the fire barrier, for example, to allow electrical wires or other services to pass through a wall, floor or ceiling. That is why a range of Envirograf® intumescent products has been designed, to safeguard the integrity of fire barriers by swelling to seal such gaps should the worst happen and fire break out.
One of Envirograf’s strengths is the ability to adapt to the constantly evolving needs of their customers. Following a number of enquiries, they recently introduced of a new variant to the versatile and popular FIROBLOK® range of fire sleeves; a new version designed to be inserted into hollow plasterboard or lath and plaster ceilings and walls, that sits flush with the surface.
Another common enquiry relates to the use of metal back boxes in hollow plasterboard walls. In recent months the company has received an increasing number of calls asking how they can maintain fire separation capabilities when installing metal back boxes in plasterboard walls. Fortunately, Envirograf® have an extensive range of tried and tested expanding intumescent gaskets and linings that are ideal for a wide range of standard electrical boxes. They are lightweight, flexible and can be trimmed to size to fit most socket boxes.
Sister company, EnviroEcoWall Panels has been established to manufacture one of Mr Ward’s latest innovations, a pre-engineered, insulated, load bearing panel system designed to form a fireproof building envelope. This unique system combines structure and insulation into one prefabricated, thermally efficient component. Not only are EnviroEcoWall Panels protected from fire by Envirograf’s intumescent coatings, the buildings are also designed to cope with flooding as they are constructed on a unique metal sub-frame that can carry the structure from 150mm to any height off the ground and can be raised to a new level at a later date in 300mm intervals.
Additionally, the system reduces build time, minimises waste on site and doesn’t require the significant amount of water consumption associated with more traditional construction methods.
Using the same high-spec system, the company recently introduced a range of smaller garden office buildings as a unique and cost-effective way to gain extra work or leisure space at home. In addition to standard models, the company offers a bespoke design service.
For more details you can call 01304 842555 or email sales@envirograf.com
Because pipes, cables, ventilation ducts and other services sometimes need to pass through a hollow plasterboard or lath & plaster ceiling we have introduced new variants of our successful FIROBLOK® range of fire protection sleeves.
Designed specifically for plasterboard or lath & plaster ceilings, these new products have a metal encasement under the reinforced foiled cloth which also serves as a hinge, enabling the sleeve to open up for fitting around existing services. Once, fitted, the adhesive tag is peeled off to seal the two halves together.
Fixing tabs are used to secure the sleeve with screws or toggle bolts as appropriate.
Following the growth in popularity of using metal back boxes in hollow plasterboard walls, we fire tested various combinations of metal boxes, extenders and gaskets in a hollow plasterboard partition wall to ensure that fire integrity of the wall was maintained. Some boxes were mounted flush with the face of the plasterboard and others were set back.
Kirk Smith of Allegion UK discusses fire door neglect and how to spot the potential faults that could be compromising your fire safety procedures.
Purpose built to compartmentalise fire and smoke, fire doors are recognised as a critical element of passive fire protection and exist in practically every building where we work, sleep and live. Such is their importance; they are acknowledged by several professional bodies and are a legal requirement in non-domestic premises and houses in multiple occupation (HMOs).
Day to day we use them without a thought, yet fire doors consist of much more than a simple piece of furniture. A fire door is a complete door assembly, comprising of a doorset fit with a door frame, leaf, essential hardware, edge seals and integral panels. In the event of a fire, not one of these elements can fail, and so to meet the necessary standards, a fire doorset must pass one or more of a series of standardised tests, confirming its certification and FD ratings.
So why can fire doors experience failure in critical moments? Between neglect, misspecification and a misunderstanding
of their significance, 75% of fire doors fail to meet the required standard, as has been revealed by the Fire Door Inspection Scheme (FDIS). To combat this, a conscious effort is needed, with more attention given to fire doors and their components. Once installed, simple checks can help ensure a fire door is safe to fulfil its role, but where should you start when spotting a door’s potential faults?
Upon operation, a fire door calls upon its many elements - all of which must function in tandem to ensure the door is effective in a fire situation. Generally, there are eight core areas to consider when conducting regular risk assessments and spotting potential faults. Kirk Smith of Allegion UK explains more:
“When opening or closing a door, our hands instinctively reach out for the handle. Should it be absent, or even loose, it could affect whether a door can be opened in an emergency. Because of this, a handle should always remain installed on a fire door and its screws tight. Bolt-through fixings pass right
through the door and the lock or latch case and will strengthen the installation of handles by preventing the screws from moving or becoming loose. Check whether the handle operates smoothly and returns freely to a horizontal position after use, too. Finally, if the fire door in question is on an escape route, it must open in the direction of travel, without the use of a key. Keep it simple, but effective.”
“Hinges are a necessary pivot action fixing that provides the movement to a door. A standard height fire door requires the installation of three hinges minimum, with intumescent pads fitted. A door standing over 2.2 metres will require four hinges. This will prevent the door from warping in a fire due to its weight, and so should you see a fire door only hung on two hinges, it must be changed. Again, screws must be fitted securely, and the hinges themselves must be free of metal fragments and oil leakage as this could indicate signs of wear. When it comes to certification, check for CE or BS EN 1935 marks. Hinges may be hidden somewhat, but they can never be overlooked.”
“To form an effective barrier against fire, a fire door must close fully. Locks and latches help to keep doors held shut and so must be fixed firmly and working correctly. Upon inspection, it’s important to check whether the latch engages fully into the strike plate and whether the door can be held firmly in place without rattling. Failure to do so may indicate faulty or damaged hardware. Like hinges, check for metal dust deposits - typically located on the latch bolt or strike plate - as this could also show wear or damage.”
“Door closers facilitate the operation of a fire door and must be UKCA and CE marked and tested to EN 1154. When opened, a fire door should fully engage into the door frame every time, shutting tight by use of its own selfclosing device. When conducting checks, the trick is to open a door to 5° or 75mm, and upon letting it go, it should close and engage the latch successfully. Failing to do so could indicate the door closer has been incorrectly installed or damaged and, therefore, needs adjustments or replacing. Adjustments can be made to the closing power and speed of door closers, and in busy environments such as schools and hospitals, a prolonged closing action is useful, giving people extra time to pass through the doorway.”
“Buildings with high footfall may benefit from approved, electromagnetic hold-open devices tested to BS EN 1155, which permit open fire doors that automatically release to close in the event of a fire. Naturally, these systems are more complex and regular maintenance is mandatory, so it’s vital to spot any potential faults, such as the door straining against its self-closing device upon operation.
an electromagnetic hold-open device not release the door when a fire alarm is activated, a problem has occurred and must be resolved immediately.”
“Exit devices are designed to provide safe and effective escape through a doorway with minimum effort. All panic and emergency exit devices must be functioning correctly, with fixings on the operating device, bolts and strikes tightly fit. Emergency exit devices and panic exit devices should be tested to BS EN 179 and BS EN 1125 respectively, as well as UKCA and CE marked. Aside from their mechanical operation, it’s critical to keep emergency exits clear and without obstruction - assisting a quick escape when called upon.”
“When rated FD30 or FD60, a fire door is certified to resist smoke and fire for 30 or 60 minutes, respectively. For this to remain true, a doorset must be fitted with intumescent seals which, in the event of a fire, expand significantly to close the gap between the door and its frame. Intumescent seals should track continuously around the frame or door leaf and must remain in good condition, intact and undamaged.
If you can see excessive gaps between the side of the door and the frame, a fire door may be ineffective. A maximum gap of 3mm is recommended around all fire doors and can be assessed with simple gap tester tools.
“Although not a mechanical element of a fire door, signage plays an important role in fire door safety and must be considered when checking for faults. Providing quick and key information in an emergency, ‘Fire Door Keep Shut’ signage must be fitted to both sides of a fire door. Additionally, ‘Automatic Fire Door Keep Clear’ signs must appear on fire doors with hold open devices and ‘Fire Door Keep Locked’ signs must be fitted to doors without self-closing devices – which can commonly be found in storerooms and cupboards.”
A complete and functional fire door is a prerequisite for fire safety and regular maintenance periods are required to ensure they retain their standard while in operation. The first step is to understand the various components of a fire doorset and the potential faults to look out for when evaluating its condition. Should any doubt linger, it’s crucial to seek out professional advice immediately. Checks can save lives but where action is an obligation, knowing what to look out for is only half of the responsibility.
“Should
Sales Director sees 300% increase in fuel security enquiries following the red diesel ban.
MHM Group, the UK-wide distributor of leading hireto-hire solar and diesel equipment, has launched a range of high security fuel storage and management systems in line with a 300% increase in security enquiries this year.
Concern around the security of fuel storage tanks has risen dramatically following the red diesel ban in April 2022, which means that the white fuel now found in storage containers can be stolen and decantated directly into cars.
In addition, the rising fuel cost crisis affecting the UK has led to a proportion of drivers turning to theft, with forecourts reporting a 39% increase in stolen fuel since January.
To that end, the MHM Group’s multipurpose, fuel storage containers that can be paired with generators or heaters, have been launched as a new product offering in response to the crisis.
To combat fuel theft, the tanks consist of a two-part locking system which can also be monitored virtually with the latest telematics solution so that customers can track their fuel level remotely. Users can set phone or email alerts when the tank is being used.
MHM Sales Director Brad Ireland, who has nearly a decade of experience in the storage container industry said, “We believe this increase in queries is due to the recent
rise in fuel costs, as well as the red diesel ban in April. Red dye allowed law enforcement to identify and quickly prosecute illegal usage, but with the construction, demolition and other industries making the change to white diesel, there is no way of differentiating or spotting the stolen diesel.
“We are delighted to launch our latest product range of fuel storage tanks to the hireto-hire industry.
“To meaningfully address the fuel theft crisis, we have included a range of products in our secure fuel storage fleet, including the SteelCube tanks that can be paired with generators or heaters.
“Our ready-to-rent tanks have the option of an all-new tracking solution which sets us apart from others in the market.
“We can provide our customers with innovative and integrated solutions that monitor their fuel safely, as well as increase business efficiencies by producing less waste.”
The MHM Group has grown from a small family business into an industry-leading enterprise with a total of nine depots across the UK and Ireland.
Brad added, “The team have worked hard to ensure that our specialist tanks are robust and reliable and readily available across the UK, so our customers have peace of mind that they are receiving the best product possible.
We look forward to seeing where this initiative will take us and will continue to develop products that meet the needs of our clients.”
Red dye allowed law enforcement to identify and quickly prosecute illegal usage, but with the construction, demolition and other industries making the change to white diesel, there is no way of differentiating or spotting the stolen diesel.
Construction is one of many contributors to particulate pollution. A result of operating diesel-powered machinery, demolition and construction, research suggests that building works are responsible for 18% of the UK’s PM10 emissions, and this has been found to be a staggering 30% in London (Impact on Urban Health). To protect the neighbourhoods surrounding construction sites, operators must comply with strict environmental permits and choose the right air quality monitor that both satisfies their permit requirements, but also works flexibly and in line with construction activities.
This is where the Monitoring Certification Scheme (MCERTS) becomes an important factor. MCERTS certifies the data quality coming from monitoring equipment of emissions into air, land, and water. Certified pollution monitors are a non-negotiable for regulatory and safety purposes, like EarthSense’s Zephyr® air quality monitor, which has been approved as compliant with MCERTS performance standards for indicative monitoring of particulate matter (PM2.5 and PM10).
Taking this into account, EarthSense has taken an alternative approach to monitoring dust emissions as its new construction suite covers all angles of air quality monitoring. The suite starts with the Zephyr® monitor, offering MCERTS data quality for simultaneous PM2.5 and PM10 monitoring to meet local permit requirements. With live measurements of NO, NO2, O3, SO2, CO, H2S, CO2, TVOC (key gaseous pollutants) together with wind speed and direction, the Zephyr® can help provide a detailed understanding of air quality across sites, delivering the data needed to protect the local community and on-site staff from exposure to harmful pollutants.
To ensure all dust monitoring locations are covered, including those where monitoring dust emissions may be challenging, the suite offers a level of flexibility due to the various power options for the Zephyr®. Choose from using a solar panel, connect to mains power, or run for up to three months on an external battery source – no longer do monitoring locations become compromised due to a lack of power. The flexibility also provides a range of options
as sites transition through different stages of development. Walk-away confidence is another important consideration during equipment installation, and EarthSense’s Companion App provides an intuitive way to check the status of instruments. Using a phone or tablet, professionals can now connect to Zephyr® monitors via Bluetooth and check functional statuses, making it quick and easy to check operation, even if units are out of reach.
Once Zephyr® networks are up and running, air quality data is automatically transmitted to EarthSense’s data application, MyAir®. Within the app, configurable air pollution alerts can be set up and sent via email or SMS, enabling onsite managers to know where and when to act immediately.
EarthSense’s air quality service is providing the basis for safer practices across the world. It might be for the simplicity of connecting to a Zephyr® network, or for its MCERTS certified data quality, EarthSense have trusted solutions for construction, consultants, local authorities and more.
Find out more by signing up to EarthSense’s webinar: www. earthsense.co.uk/mcerts-webinar.
Construction professionals can now quickly and easily access the web app and use dust data for regulatory reasons, be it for traceability to evidence compliance with local policies, responding to local complaints, impact assessments or reporting compliance with dust management plans.
So, the first thing I do when I wake up is get some caffeine into the system to get my brain working and then check my phone to see if there have been any late-night messages come in. This mainly comes from working in a rail environment where lots happens at night so it’s indoctrinated in me to see if there is anything urgent that needs attending as soon as I wake up, this could be lost shifts, an HSE incident or simply to see the nights’ progress reports.
I head to work early so I can get through my emails before people start coming in as typically my day is meeting-heavy. The main day-to-day tasks of my role, however, is to serve our team and be there to do whatever they need in terms of support, direction, or guidance.
I spend a lot of time talking to everyone about what’s happening in their world, where we are doing things right, where we could be doing things better, and then working on improving them.
I like to move quickly on everything I do and being good at communicating the pertinent information to the relevant people quickly is key to being successful in this role as it keeps momentum.
The best part about my role is having the opportunity to build a team the way I believe it should be built; on honesty, integrity, and a strong delivery ethic. If you say you’re going to do something then do it! I love developing people and giving them autonomy, enabling them to grow in a safe environment and the real reward comes from seeing people succeed in their roles and be totally self-sufficient.
When I was young, I actually started out wanting to be an architect, I loved drawing and creating things, taking my ideas and imagination and putting them on paper.
As I grew older, I realised I wanted more than just to create the idea I wanted to build it too. So, I found interest in civil and structural engineering. I completed my Masters in this field and went into a graduate scheme with a Rail company (Tube Lines), a very successful JV between Amey and Bechtel.
The graduate scheme taught me so much about the rail construction industry, and just how vast it was in terms of different roles, disciplines, systems, and history. You can have a whole career in rail and not cover everything.
I developed my engineering skill set with London Underground and quickly realised how my real fulfilment came from managing people, fixing problems and making decisions, and owning them too, whether they are right or wrong.
Once I knew this is what made me happy, I moved around different disciplines such as signalling, communications, and now mechanical and electrical to test myself in different arenas and still see if I can achieve the same outcomes.
Have you always aspired to become a Director in this industry?
I suppose the short answer to this question is yes. The reason is that I love autonomy in a job, I like to be the person where the buck stops. I enjoy the responsibility and the challenge that comes from making big decisions based on lots of complexity and quite often a lot of moving parts. That’s the challenge and is what makes my job fun.
We are currently working on several projects for London Underground through various clients, bringing the knowledge of our vastly experienced rail team to a more Commercial Environment. One of the particular projects we are working on is Paddington Square.
This is a four-level extension to the Bakerloo Line including all mechanical and electrical fit-out and HV Transformer Room installation.
However, our focus for the future is within the HS2 space. We believe that as a company we have a considerable offering to this major infrastructure organisation, we want to bring our well-established delivery reputation to the private sector and apply that drive to the rail environment spearheaded by our experienced rail delivery team.
There are lots of opportunities out there but we are being selective about the projects we are targeting as we want to be considerate of project suitability to ensure we are the right choice for the client.
Why is it important to ensure that there are more equal opportunities in the rail and engineering industry provided for all?
This importance stems from the benefits that diversity provides. Rail and construction has typically been a maledominated industry for a long time. It is getting better but slowly and we need to move this on quicker to ensure the industry survives.
best part about
is having the opportunity to build a team the way I believe it should be built; on honesty, integrity, and a strong delivery ethic. If you say you’re going to do something then do it! I love developing people and giving them autonomy, enabling them to grow in a safe environment and the real reward comes from seeing people succeed in their roles and be totally selfsufficient.
The perception of rail and construction is half of the problem, I don’t believe that young students at school understand just how vast the industry is and you can pretty much do every profession out there within the environment. We need to provide that education of available opportunity back to the next generation so they can harvest that excitement and grow a want for a career in rail.
I have three daughters and I desperately want to see them succeed in a career in rail because there are so many routes and
paths, they can take to a career that makes them happy. However, I recognise there isn’t an abundance of women in rail so how do we change this? I feel (and I may be wrong here) there is a misconception that there are no opportunities for young women in the industry, I think the problem is the opposite, I think there are lots of companies looking to offer these opportunities but the number of young women who want to come into the industry is low.
So, the important question for me is how do we convince these young women to want a career in rail?
What one piece of advice would you give to anyone out there that wants to get into this industry?
The advice I would give is to not be put off by any perception of rail or construction but to make your own judgement by speaking to different people in different organisations and at all levels to understand how broad the spectrum of career opportunities there are available to everyone.
Or even better try a job in rail, you may just find your calling...
- Stacy Benson, Director at Lonsdale RailThe
my role
Sustainability has become one of the construction sector’s main concerns.
Architects and designers are increasingly looking for eco-efficient materials and solutions that ensure quality and comfort, without harming the environment. Cork - which combines sustainability and performance – meets these requirements since it offers tremendous potential for construction, urban rehabilitation and large-scale public works.
An increasing proportion of the world’s population lives in cities. Big or small, old or new, cities have become our natural environment. According to the United Nations, around 55% of the world's population currently live in urban areas, and this percentage is estimated to increase to 68% over the coming decades*.
Cork - as a natural renewable raw material that reduces greenhouse gases - is increasingly used in the field of sustainable and eco-efficient construction, primarily due to its thermal insulation properties and capacity to control acoustics and vibrations. Studies indicate that for every ton of cork produced, the cork oak forest can sequester up to 73 tons of CO2, thereby helping reduce the Global Warming Potential**.
But nature is just the starting point. In order to protect the future we also need to rethink the way that we look at waste. Amorim Cork Composites is helping build a circular future, by transforming materials that were previously considered to be waste into new business opportunities.
The combination of cork granules with surplus production from other industries
has made it possible to create a diversified portfolio of acoustic insulation and vibration control solutions, thereby enhancing the natural characteristics of this raw material.
Cork-based acoustic blanket in the new premises of the eMedia group
A diversified portfolio of sound insulation and vibration control solutions is based on a mixture of cork granules and various polymers. The cork-based material, Acousticork by Amorim, ensures longlasting performance with stable material properties, throughout the product's lifetime.
These were the principal reasons for choosing the cork-based Acousticork underscreed, for eMedia Investments’ new headquarters. The solution ensures impact noise insulation, while offering maximum comfort to users.
Located in the city of Johannesburg, South Africa, the building houses the offices and studios of the various radio and television channels of the media group - which owns the eNCA news channel.
Applied during the construction process in the floor between the structural slab and the screed, an underscreed significantly reduces the propagation of impact noise through the building’s structural elements
© eMedia Investments, all rights reserved © Asia Alliance International,
and improves its sound insulation – an essential characteristic for a television studio. In addition to limiting heat loss, it also improves the building’s overall thermal performance, offering journalists and other employees the best working conditions and comfort.
Designed to fill the spaces between the concrete slabs, Amorim Expandacork expansion joints absorb expansions and contractions caused by temperature variations in different construction materials. These joint-filling products enable the structures to move without causing damage. They guarantee longterm sustainability and high technical performance for buildings and large public works.
Taoyuan International Airport in Taipei City, Taiwan is being expanded through the construction of a new passenger terminal, which is expected to open to the public in 2026.
Amorim Expandacork was chosen for the expansion joints of Terminal 3’s buildings and other infrastructures. It is a corkbased solution for expansion joints that guarantees excellent performance and low maintenance.
Use of Amorim Expandacork expansion joints makes a positive contribution to the contraction and expansion of the construction elements, preventing cracks and reducing the preventive maintenance ratio.
For further information visit: www.amorimcorkcomposites.com
*Source: https://unhabitat.org/sites/ default/files/2020/10/wcr_2020_ report.pdf
**Source: https://www.apcor.pt/wpcontent/uploads/2015/10/Brochura_ Ambiente__EN.pdf
Kier has been appointed by NHS Ayrshire & Arran to deliver Foxgrove, a mental health facility at Ayrshire Central Hospital in Irvine. It will be the first medium secure adolescent inpatient service for young people in Scotland and has been procured through The Health Facilities Scotland Framework.
Foxgrove will be an inpatient unit for children aged 12-18 years who have
complex difficulties and need a high level of care. This means that young people in the facility will be cared for nearer to home and will receive appropriate care, treatment, therapies, security and on-going education.
The new unit will comprise of 12 en-suite bedrooms, a dining area, recreational areas including a gym and sports barn, external relaxation and horticultural areas, therapy and education space, as well as staff areas
including accommodation. Externally, there are numerous areas for patient therapies. The building is a timber frame with rendered insulation panels and facing brick forming the envelope with a Kalzip roof.
Phil McDowell, regional director at Kier Construction North & Scotland said: “This is such an important project, and the first of its kind in Scotland. We’re proud to be working with NHS Ayrshire & Arran to deliver a key
A major scheme to replace the A533 Expressway bridge has reached a key milestone after the new bridge was lifted into position.
The 67m steel structure was built off-site at a compound close to the side of the M56 and was moved into place over the weekend.
Using a self-propelled modular transporter (SPMT), the bridge was slowly transported down the embankment, along the carriageway of the motorway and into position.
The M56 between junctions 11 and 12 was closed over the weekend to allow for the work to be carried out.
Stewart Jones, National Highways’ Regional Delivery Director, said: “Installing a bridge of this size in a single weekend was hugely ambitious. Our team worked around the clock to make sure it was a success, and I’m pleased to say the motorway was reopened for traffic ahead of schedule, late on Sunday night. I’d like to thank everyone who planned ahead for their journeys over the weekend. Reduced traffic volumes on the M56 meant delays were significantly lower than forecast.”
The existing A533 Expressway bridge was also closed while the bridge was installed.
Chris Buckley, AmeySRM Project Manager, said: “It was an absolute priority for us to minimise disruption to the local
community over the weekend. Our team ensured a safe crossing point for any pedestrians or cyclists who were passing through. We’re extremely grateful for local support over the last 10 months.
“To celebrate this important milestone, we teamed up with SRM’s Strong Foundations grant to donate £25,000 to charities and community groups. We were honoured to have some of these join us at our recent ‘topping out’ ceremony.”
Phoenix Community Archery Club in Runcorn was awarded £3,000 to build a new platform providing all-weather access for wheelchair users.
First Knutsford Scout Group also received £3,000 to help build their new scout hut and Huyton Asphalt received £3,000 on behalf of the Bobby Colleran Trust.
National Highways made use of the weekend closures to also carry out additional work – reducing the need for more closures in the future.
As well as removing narrow lanes from the M56, they also installed three new manholes and a 4m deep drain. They also carried out structural surveys, installed infrastructure for new power and phone cables, and completed general maintenance work.
The next project milestone will be removing the old bridge which is expected to happen spring 2023.
strand of the Scottish Government’s Mental Health Strategy (2017-2027). During the construction of the building, we’ll also be focusing on leaving a lasting legacy in the local community, working with local supply chain partners and providing employment and apprenticeship opportunities.”
Caroline Cameron, Director for North Ayrshire Health and Social Care Partnership, said: “This is fantastic news and is a real milestone in this national project which is being taken forward in Ayrshire and will benefit young people around the country.
“Currently, there are no facilities in Scotland to care for this most challenging and vulnerable group of patients. This means that children are referred to secure adolescent mental health facilities in England, or in some cases, the child may be cared for in an adult inpatient setting. This places significant additional pressure and stress on the child, as well as their families.
Foxgrove will without doubt improve the outcomes for young people who are seriously unwell and pose a risk to themselves. Scottish adolescents with complex mental health needs will be able to access the health care, education and support services they need in an appropriate, modern environment bespoke to their needs and aspirations. It is great news for young people throughout Scotland, as well as their families and carers.
Mental Wellbeing Minister Kevin Stewart said: “I am pleased that the Scottish Government has been able to provide funding of over £16 million to allow this national facility to be built for young people with complex needs and mental health conditions.
“This will help ensure children and teenagers are being given care in the most appropriate setting for their needs. I look forward to seeing how the build progresses and develops.”
Building work on 33 units at the iconic Botany Bay site in Chorley will deliver 405,000 sq ft of industrial and commercial space.
Construction work on a new £26m industrial and commercial park at the historic 21-acre Botany Bay site in Chorley will start this month.
When complete, the scheme will deliver 33 units for light industrial and commercial use across 405,000 sq ft and a drive-thru food outlet.
FI Real Estate Management (FIREM) received planning permission for the development from Chorley Borough Council in July and the development will be the largest ever built by its construction arm, FI Construction.
FIREM manages assets totalling more than £1bn and founder and managing director, Tim Knowles said the Botany Bay development was one of the most important in the company’s 40-year history.
Tim said: “We want to create the highest quality industrial and commercial space for local businesses and those from further afield looking to make Lancashire their home.
“Botany Bay is an iconic location and the development will be built in two phases. The construction costs for phase one will be £26m and the fit out costs will add an estimated 10 per cent to the total bill. We’ve already significantly grown our FI Construction arm to deliver it. We’re also fully committed to provided further training and employment opportunities to local people as well as seeking new supply chain partners from across Lancashire to ensure FIREM’s investment benefits the local economy.”
The company employs 300 people across the Group and plans to add another 100 as part of its growth strategy.
Once complete, the new development will provide units specifically designed for light industrial use. Unit sizes will range from 1,000 sq ft reaching 164,000 sq ft.
FIREM’s Botany Bay development forms part of its growing pipeline of new build projects across the UK, totalling 5m sq ft over the next four years. It sits within FIREM’s already extensive UK portfolio of commercial property which now exceeds 10m sq ft.
Work has begun on a substantial housing development in Carterton in Oxfordshire that will see 200 homes provided for people to live in the area.
Platform Housing Group have begun work at the site at Milestone Road which has been provided by West Oxfordshire District Council and will be developed by United Living. It represents the group’s largest site in the area to date and the continuation of their strong start of their strategic partnership with Homes England.
Over the next four years, the new homes will be made available through Platform’s different affordable options. 105 of the homes will be available to rent, 12 as rent to buy and 83 through the increasingly popular shared ownership scheme. This allows people to purchase a share of their home and then pay a rent on the rest
with the option to increase that share up to 100%.
Amongst those visiting the site was MP for Witney and West Oxford Robert Courts who said, “It was a pleasure to visit the site in Carterton which will provide much needed affordable homes for local people. It was encouraging to see work getting underway and useful to learn more about how this development will benefit local people and the wider area in Carterton. I look forward to following progress closely.”
Group Chief Executive of Platform Elizabeth Froude said, “It’s been fantastic to see the site today where we’ll be able to provide much needed affordable housing for the area. We look forward to offering people real opportunities to live in the area and even buy a home that is quality and
Outpost Management announced that its latest build to rent development, Enclave: Croydon, has reached its maximum height. Standing at 158m, the development is Europe’s tallest modular building and now becomes the tallest building in Croydon, and one of the tallest buildings in London.
Due to open in late 2023, Enclave: Croydon will feature 817 rental homes across a 50-storey tower in the heart of Croydon.
Employing the latest modular construction techniques, the development, being delivered by developer and contractor Tide Construction and its volumetric modular company Vision Modular Systems, is set to complete with an estimated construction time of only 30 months - using the Vision Modular Systems construction methodology typically saves 40% - 50% on construction programmes compared to traditional methods.
affordable. With 200 different homes, we are delighted to be offering such a large site for our partners at West Oxfordshire District Council who have been fully committed to these options to help with the growth of the area. I’d also like to thank our developers United Living and Homes England for their help in delivering this development.”
Carl Rylett Cabinet Member for Planning and Sustainable Development at West Oxfordshire District Council said, “It’s good to see this site come forward for development; affordable housing is greatly needed in West Oxfordshire. We identified the site through the Council’s Local Plan, and granted planning permission in 2020. We are fully committed as a council to bringing forward sites for affordable housing development, and this development will make a real difference to the community.”
Neil Farmery, Construction Director, United Living New Homes, said: “We are delighted to have started building work at Milestone Road. Working collaboratively with Platform Housing Group, we look forward to delivering high-quality, affordable new homes that will provide a welcome housing boost to the local community.”
Celebrating the topping out onsite, Troy Tomasik, Outpost Management founder and CEO, said: “We’re excited to have reached this important construction milestone on Europe’s tallest modular building. The speed and precision of its construction is testament to the hard-work and dedication of our construction and development teams. Enclave: Croydon will offer one of the highest amenity provisions in the U.K., equipping residents to be more productive, healthy, and social, and we can’t wait to welcome them to their new homes next year.”
Fibrelite provided a lightweight retrofit replacement for failing heavy concrete trench access covers over an existing oxygen pipework trench at this UK hospital.
The previously installed concrete trench access covers over an oxygen pipework trench at this hospital were causing a number of issues due to both their weight and deterioration.
• The sheer weight of the previously installed concrete covers made them timeconsuming and costly to remove and replace, as well as causing health and safety risks.
• The concrete covers were located on a public walkway and were causing a trip hazard for pedestrians because they had begun to degrade and crack.
• Potential to decelerate essential maintenance and repair works due to the time required to remove and replace the covers.
The Fibrelite technical team attended the site to conduct a full survey, following which they custom designed and manufactured a bespoke retrofit covering solution which fit directly into the existing frames.
• All Fibrelite trench access covers can be safely removed and replaced manually by two people, saving time and cost.
• Quick and painless to install, no need for concrete break out: Fibrelite’s custom manufactured trench access covers were retrofitted directly into the existing frames.
• Corrosion resistant: Fibrelite’s access covers are unaffected by water, underground gasses and most chemicals.
• Fibrelite’s anti-slip tread pattern provides a safe walking surface for pedestrians.
This hospital now has a trench access covering solution which can be removed and replaced quickly and safely manually by two people and will provide many years of trouble-free service.
Key Fibrelite benefits at a glance:
• Easy access to trench services using Fibrelite’s ergonomically designed lifting handles.
• Successful application of the bespoke design solution.
• Fast installation.
• Corrosion resistant.
• Anti-slip/skid surface.
Visit the Fibrelite website for more case studies
Fibrelite’s lightweight trench covers can safely be removed and replaced manually by two people (Image used for illustration purposes and shows a different installation) Fibrelite designed and engineered bespoke covers to fit existing apertures Fibrelite’s anti-slip tread pattern, provides a safe walking surface Fibrelite’s lightweight retrofit GRP trench access coversIn a market saturated with products claiming to be eco-friendly, it can be very hard to sort the wheat from the chaff. With confusing and conflicting information at every turn, it would be reassuring to know that the product you are buying or hiring actually does what it says on the tin.
For this reason, UK manufacturer Boss Cabins decided it was important that the fuel and carbon savings of their flagship solarpowered Deep Green welfare range were verified by independent internationallyrecognised assessor, Carbon Footprint Ltd.
We turned to Carbon Footprint Ltd because we wanted independent confirmation that our Deep Green cabins really do offer the welfare market a best-in-class site accommodation solution that cuts our customers’ carbon emissions and carbon footprint as well as dramatically reducing their spend on fuel and servicing.
After thorough analysis, Carbon Footprint concluded that using a Deep Green Canteen Office welfare unit in place of a standard one, would save a total of 3400 litres of fuel each year on operation and servicing and reduce CO2 emissions by 8.4 tonnes.
At current market prices, the financial savings on the fuel used and service visits avoided by replacing a standard ‘eco’ 24ft Canteen Office with the Deep Green alternative, would equate to an annual operational cost reduction of £10,641.
Carbon Footprint carried out an in-use Energy Saving Assessment, looking at data contrasting the performance of a 24ft Deep Green Canteen Office to that of a standard Canteen Office of the same size with some ’eco’ features such as LED lighting. The solar performance, energy consumption and generator runtime of the cabins while in normal on-site operation mode were all calculated and compared.
Carbon Footprint’s analysts concluded that replacing one standard ‘eco’ Canteen Office cabin on site with an equivalent solarpowered Deep Green model will save on average circa 3,260 ltrs of fuel per annum which equates to 8.1t CO2e/year. Deep Green cabins annual operations have 9.3% of the in-use emissions of a standard ‘eco’ cabin, a 90.7% overall reduction.
Carbon Footprint also looked at the impact of reduced service visits on Deep Green’s fuel and carbon savings. Assessors considered the reduction in toilet service visits and water deliveries produced by the Waste Management ProTM system and assessed that the water saving and reduced waste production benefit from the embedded technology cuts the requirement for toilet servicing by circa 2/3, reducing the fuel consumption and associated CO2 emissions by the same percentage.
They also looked at the reduction in generator service visits effected by the patented InfinityTM generator fitted in Deep Green cabins. The Infinity incorporates a unique automatic oil change function that increases the service interval to once every 2000 hours. Compared to a standard generator that needs servicing approx. 6 times a year (every 200-250 hours of runtime), this is a reduction in generator service requirements of circa 99.4%. With generator runtimes in the Deep Green so low, users would expect to service the generator roughly every 19 years.
By cutting the number of service vehicles visiting site, it was calculated that the reduced service attendance requirements will save approx. 140 litres of fuel per annum and a further 352kg of CO2 emissions per cabin.
For more information contact Boss Cabins on 01778 300475 or email sales@bosscabins.co.uk
To find out more about Carbon Footprint Ltd.: https://www.carbonfootprint.com/
Boss Cabins Managing Director James Kearsey states:Deep Green cabins run almost entirely from solar power for most of the year. Huge fuel and carbon savings verified by Carbon Footprint Ltd. Track savings with 24/7 remote reporting of energy production and consumption plus location and tank levels for precise service planning. High performance low-impact eco welfare solutions. Saving you cash while saving the planet.
National construction charity Band of Builders and its community of volunteers and supporters has delivered a milestone £1m worth of projects to help tradespeople battling illness or injury, making a life-changing difference to them and their families.
The organisation, affectionately known as BoB to its near 50,000-strong community of volunteers and supporters, was founded in 2016 and has just completed its 27th project.
The latest project takes the equivalent cost of labour and materials in total to over
£1m - with the estimated delivery value of an average project at more than £37,200.
Reaching the £1m milestone has involved 772 volunteers giving up their time for free on projects that took a total of 203 days and involved 18,087 hours of labour. Materials and support are provided by organisations and businesses across the sector who support the charity on individual projects or through ongoing partnerships.
BoB’s projects, which include renovations, adaptations or repairs to the homes of tradespeople affected by illness or injury,
range in scale. The biggest to date was a complete reconfiguration of the ground floor of the home of plasterer Mark’s partner Cher Little in North Wales, who was left relying on a wheelchair after having her legs amputated. More than 75 volunteers answered the call for help over a 31-day period, with a delivery value of more than £102,000.
The smallest involved six volunteers in a two-day project over a weekend in Stokeon-Trent just before Christmas 2021 to fix the leaking roof of the bungalow that 93-year-old former brickie Tom Knapper built in the 1970s for his family. This project had a delivery value of £2,250.
The project that saw BoB pass the £1m delivery value landmark was for Martin Wilks from Herefordshire, who was left paralysed from the chest down after falling off a stepladder in June 2018 and hitting his head on a concrete planter, causing a severe traumatic brain injury. This was the second in three project phases to help level flooring on the ground floor of the family’s home, as well as to widen doorways to make it easier for Martin to move around in his wheelchair.
Reflecting on the landmark total, the charity’s CEO Gavin Crane paid tribute to
all the volunteers who have given up their time to help fellow members of the UK construction industry, their families and their dependents.
“It’s a very proud moment for everyone connected to Band of Builders to have reached such a significant milestone in the history of a charity that only started six years ago,” said Gavin.
“Through the kindness and generosity of our community, who keep volunteering their time to work on projects, we have helped make a life-changing difference to 27 beneficiaries and their families across the UK.”
Gavin also paid tribute to the wider construction industry for its support and praised the generosity of companies such as builders’ merchants, which often supply materials free of charge.
He added: “It’s also important that we say thank you to all the businesses that continue to support the charity with the supply of materials free of charge, plant hire and anything else that we need for projects – such as portable toilets for each site. And then there are the unsung heroes of each project, such as local businesses that generously feed our volunteers and even give them free or much-reduced rates on accommodation.”
The charity has come a long way since it was founded in 2016 when, upon hearing that his friend Keith Ellick was diagnosed with terminal cancer, Lincolnshire landscaper Addam Smith wanted to do something to make his mate’s life a little bit easier. A plan to landscape his garden won the support of his fellow tradespeople and saw the project grow into a full-scale
renovation of Keith’s house, carried out by volunteers from across the country.
Gavin summed up by saying: “We have come such a long way in such a short space of time. We only became a registered charity in 2019. In that time, we have seen our community of supporters grow and thrive, and we have built relationships with a raft of businesses that have made us their chosen charity or become part of our programme of patrons.
But, above all else, Band of Builders and those who support us have not only made a life-changing difference to 27 people and their families but will continue to complete practical projects to help members of the UK construction industry who are battling illness or injury.
SPATEX 2023: The UK’s only dedicated water leisure exhibition will return to the Coventry Building Society Arena from Tuesday January 31st to Thursday February 2nd. Awash with an impressive line-up of exhibitors and unique networking opportunities, it is a must-attend event for every construction professional in the UK.
Now in its 27th year, the annual exhibition is bursting with the very latest innovations in swimming pools, wellness facilities, water features and all their ancillary equipment. It offers architects, surveyors, specifiers, developers, and all those involved in the construction of facilities incorporating water, whether leisure or ornamental, to meet over a thousand people from the industry in one day.
Many of the one hundred plus exhibitors, drawn from all four corners of the globe, will feature generous show discounts, competitions and prize-giveaways.
With the price of energy and fuel inexorably rising, SPATEX’s focus is on sustainability and showcasing the latest innovations designed to reduce energy consumption and bills.
“We aim to bring the topic of energy saving into sharp focus and make it a forum for discussion and finding solutions,” says SPATEX Organiser, Michele Bridle.
With education, the latest technological advances and careful management, there are effective ways to significantly reduce energy consumption and bills. It’s this positive message that, with the help of our exhibitors and experts, we aim to communicate to our visitors.
SPATEX is the first opportunity to view 2023’s most box-fresh, technologically advanced products. This is the place to pick up the latest labour-saving products to make installation and operation speedier. Viewing the latest trends will ensure your projects reflect the very best in the marketplace.
Pick up free impartial advice from leading industry representatives and associations, such as BISHTA (British & Irish Spa & Hot Tub Association) and SPATA (Swimming Pool & Allied Trades Association). Please call in at the SPATEX Technical Help Desk, at the entrance to the exhibition hall, and the team will be happy to point you in the right direction.
Visitors have the opportunity to build their training and education. Be sure to check out the double seminar arena featuring forty talks and taking place over the course of the three days of the show – all free-to-attend.
In Arena 1, the ISPE (Institute of Swimming Pool Engineers) is staging the ever-popular workshop programme. CPD accredited, the workshops offer all the latest insights and tools the industry has to offer plus the latest standards and guidance affecting all working in wet leisure facilities.
Register now for FREE https://spatex-2023.reg.buzz/
SPATEX 2023 Tuesday January 31st to Thursday February 2nd 2023. The Coventry Building Society Arena, Coventry CV6 6GE is easy to get to - just 500 yards off the M6 and within two hours commuting time of 75 per cent of the population, with 2,000 free on-site car parking spaces.
For more info: helen@spatex.co.uk Tel: +44 (0) 1264 358558.
Engineering specialist, SES Engineering Services (SES), has completed £25m worth of engineering services at The JJ Mack Building, commercial developer Helical’s flagship scheme for sustainability.
Working closely and collaboratively with Principal Contractor Mace, SES has delivered full mechanical, electrical and plumbing (MEP) services for the 200,450 sq ft, ten-storey block in the heart of Farringdon, London – originally referred to as 33 Charterhouse Street. This includes a Category A office fit-out with the latest in integrated building services to make the building ‘smart’ and ultimately, more energy efficient.
Smart technology includes making variables like heating, lighting and security accessible on one network, giving the end user real-time updates of usage and allows them to control the entire building using just one platform.
This innovation has meant that the JJ Mack Building is on track to achieve a BREEAM rating of ‘Outstanding’ –Helical’s first commercial offering to do so - as well as a NABERS five-star rating. It has been designed with sustainability as a priority from its conception, to support the developer’s ambitions of having all new builds Net Zero Carbon in operation by 2025.
The scheme prioritises end-user operation. SES worked closely with all delivery partners and stakeholders –including facilities management company, Ashdown Philipps – to ensure all services were integrated correctly, while an extensive digital twin model was used to ensure seamless assimilation.
Offsite construction was vital to construction with the company’s bespoke offsite manufacturing facility, PRISM being utilised to help design, build and deliver pumps skids, floor service modules, duct work riser modules and the largest and most complex mechanical risers that the facility has built to date.
SES MEP Installation commenced in July 2021, with handover achieved on
30th September 2022 – finishing on Programme.
Steve Joyce, Managing Director at SES Engineering Services, said: “Smart buildings are revolutionising the commercial sector as the potential to reduce energy costs and personally manage usage becomes an incredibly attractive option to end tenants. Providing this service seamlessly is a true test of engineering ingenuity and we pride ourselves in being able to deliver this capability to clients to such a high standard.
“As well as our technical expertise, our prior working relationship with both Helical and Mace has been invaluable. Integrating complex building systems relies on early stakeholder collaboration. Already being onboarded with their teams, fully aligned with their goals and ways of working helped streamline delivery and, alongside our offsite capability, has played a large part in successfully handing over this scheme ahead of schedule.”
Frank Connolly, Operations Director at Mace, said: “The success of this project is directly attributed to the teamwork and understanding of both Mace and SES project teams.
The positive attitude set by senior SES management has influenced the SES site team and their supply chain, setting a constructive and supportive attitude on site. It has been a pleasure to work and deliver this fantastic project with SES and Prism.
Pavlos Clifton at Helical, said: “Working with trusted companies like SES has allowed us to explore our aspirations to challenge construction methodologies to find better solutions to deliverability. The team understood what we were trying to achieve and had the in-house support and capability to deliver what we wanted. In that way it was mutually beneficial to both our businesses, which is the best working relationship”.
The JJ Mack Building is the latest build to demonstrate SES’ capabilities in delivering smart buildings, with the company currently delivering other smart projects including 4 Angel Square, at the NOMA development in Manchester.
New from CHAS, the trusted expert in supply chain compliance, is Verified Supplier, a compliance verification service which enables construction material suppliers to showcase their commitment to operating credibly, safely and ethically.
While contractors are well-versed in providing evidence of their working practices, materials suppliers have traditionally managed to escape the same level of scrutiny.
Yet with supply chains still reeling from the pandemic, rising inflation, global shortages and the high-profile impact that the poor choice of materials can have on performance and safety, selecting the least risky products and supplier is now more important than ever. Gone are the days when just choosing the cheaper materials or supplier was an easy option to take.
Evidence of proactivity around the environment and workplace diversity are now just as likely to feature highly in any decision-making. And with added
pressure on companies to ensure their supply chains and builds meet the most stringent of standards, the onus is on suppliers to stay ahead of the curve and ensure they stand out as a reliable and trustworthy choice.
Specifying CHAS Verified Supplier gives buyers confidence that their suppliers operate to a consistently high standard. This helps protect buyers from the disruption and reputational harm that can arise from non-compliant supply chains and helps to streamline their supply chain risk management processes.
Becoming a CHAS Verified Supplier is a convenient way to demonstrate compliance across a range of risk management areas via a single verification, reducing duplication of prequalification questionnaires (PQQs) and making it faster and easier to prequalify for contracts across the UK.
As well as demonstrating a supplier’s commitment to quality practices and processes, achieving CHAS Verified Supplier helps suppliers highlight compliance with the following laws and regulations:
• Health and Safety at Work etc. Act 1974
• Modern Slavery Act 2015
• Environment Act 2021
• UK GDPR
• Equality Act 2010
Verified Suppliers also get access to an easy-to-use dashboard with a complete overview of their compliance records and renewal and expiration dates, as well as benefiting from a growing bank of exclusive benefits, including discounted training courses, free legal advice and special offers and discounts from the likes of TradePoint, Checkatrade.com and Speedy Hire.
Alex Minett, Head of Products and Markets, CHAS comments, “CHAS’s new Verified Supplier service makes it easier for responsible materials suppliers to highlight their credentials to potential customers. CHAS Verified Supplier underlines CHAS’s commitment to simplifying prequalification in the construction industry while raising risk management standards and ensuring that responsible businesses thrive.”
To find out more about becoming a CHAS Verified Supplier, visit www.chas.co.uk or call 0345 521 9111
Easily demonstrate compliance with Verified Supplier
For housebuilders, all new housing by 2025 will be expected to produce 75-80% less carbon emissions compared to current standards. Faced with these ambitious targets under the Future Homes Standard, it is clear that improving the building fabric will be key to meeting these new regulations. Smartroof’s offsite modular roof system meets these ambitious targets and can go a long way to lowering carbon emissions and addressing heat loss.
Tom Wright, Design and Technical Director at Smartroof, explains how the company’s offsite manufactured modular roof system is already 2025 compliant, and one of the most cost-effective and efficient ways for housebuilders to address thermal bridging at junction details within the roof build-up.
While the Smartroof system meets the industry’s demand for solutions that enable the construction of better quality homes, it can also help the housebuilder meet the latest energy efficiency targets. It does this in a number of ways including:
• Wide range of U-values
• Junction details
• Vaulted ceiling option
• Dedicated design team
• In-house production facility
The Smartroof solution offers a wide range of U-values. This offers significant increases in design flexibility as its insulation levels can be adjusted to suit the customer’s requirements. Not only does this allow the client to ‘futureproof’ their roof, it can potentially offer significant cost savings as the SAP assessor can trade off gains from one area to another. Achieving higher Fabric Energy Efficiency Standards (FEES) in house types specification’s will be crucial for housebuilders in order to pass SAP and comply with Part L.
Smartroof has recently carried out an independent assessment of its junction details to assess the psi value. All details have outperformed the psi values given as default in table K1 for 2020 regs. Smartroof will happily make these details available so that your SAP assessor can take these into account.
The “loft zone” above the ceiling in a room-in-roof system will have a negative effect on SAP calculations and likely result in a higher U-value specification for roof components. The result will be more expensive materials and/or more follow-on trades. The majority of Smartroof systems have no structural beams, thus allowing the housebuilder flexibility to adjust their ceiling height. A system with structural beams is likely to be more restrictive when adjusting ceiling height and will result in costly compromises.
Smartroof’s design department has a wealth of panelised roofing experience.
This experience allows the designers to offer various options to its customers when exploring their thermal options.
Smartroof has always worked closely with leading SAP assessors and its ‘room in roof’ panel system is already meeting the standards required. Computer modelling enables the company to produce bespoke roofs that are tailored to a client’s needs.
Production of the Smartroof system in a factory environment ensures no cold spots in the panels or spandrels that may arise from more traditional methods onsite. The system’s design makes it inherently airtight and an ideal roof solution for those developers adopting a fabric first approach. Smartroof’s in-house production facility enables it to stock a wide range of materials and insulations to ensure it meets every customer’s thermal requirements.
The new SAP 10 methodology is around the corner which means that thermal bridging and junction details will go hand-in-hand. In the past you could apply a set value to it, but now the regulators will want a great deal more information about the actual product and what those values are. With default thermal bridging figures set to increase by about a third, the Smartroof system is ready to meet those requirements and will go some way to helping our homes become more energy efficient and cut carbon emissions.
To find out more download the Smartroof brochure or contact info@smartroof.co.uk
At DJS Metal & Lead Roofing Ltd we complete both main contractor and sub-contractor works to both new and historic buildings across the UK such as churches and cathedral through to new housing. With over 30 years of experience within the construction and restoration industry you can be assured that with a great level of knowledge, skill and a great deal of passion and pride in what we do your projects are in safe hands.
DJS Metal & Lead Roofing Ltd had the pleasure of being the main contractor on this beautiful 1960’s chapel in Cambridge. Works that were completed where that of new timber works, insulation & Felt roof coverings, new skylights to the five openings and new milled lead works. This has then a pleasure to work on and with the finished detailing this beautiful structure will stand proud for many years to come.
With new code 5 milled lead sheeting, fascia, capping’s, and flashings supplied by CEL Lead & Hard Metals and Installed by DJS Metal & Lead Roofing Ltd this has now brought the building back to life and also reduced running costs due to the insulation and products installed.
DJS Metal & Lead Roofing Ltd Progress House, 256 Station Road, Whittlesey, PE7 2HA
This 1980’s traditional building was showing signs of age with a number of leaks which had begun to deteriorate the timber roof structure. Following a thorough inspection of the roof area and structure DJS Metal & Lead Roofing Ltd was awarded to project which was to be completed in ZM Zinc Quartz with various timber repairs and warm roof 110mm insulation board installed.
Following the completion of various timber repairs, 110mm insulation boarding and the installation of new VM Zinc Quartz standing seam roof and new Quartz gutters the building can again stand proud. Installation of all works completed by DJS Metal & Lead Roofing Ltd with the supply of VM Zinc from CEL Lead & Hard Metals Ltd.
Tel: 01733 206633 (Option 2)
Europe’s leading provider of low carbon solutions for the cement and construction industries, Ecocem, has announced the appointment of Mark Brown as Regional Sales Manager for Northern UK.
Mark brings 15 years of construction and logistics industry experience to his new role. Prior to joining Ecocem Mark worked in the admixture sector where he gained extensive knowledge of the UK concrete and cement markets.
As Regional Manager for Northern UK, Mark will continue to promote innovation, deepen existing customer connections, continue to build the company’s success with Engineer and Architect specifications, and develop high-quality leads in new areas.
For more than 20 years, Ecocem has led the development of technology that reduces the carbon footprint of the traditional cement manufacturing process by half. It’s pipeline of technology continues to be industry leading, and the company was recently backed by Breakthrough Energy Ventures, a coalition of private investors led by Bill Gates, supporting innovations that will lead the world to net-zero emissions.
Ecocem GB is currently specified on the high-speed railway HS2 in the United Kingdom, with the first leg scheduled to be completed between 2029 and 2033.
John Sisk & Son today announces a senior management appointment in its UK business. Ger Hayes has been appointed Managing Director UK South, taking on the role previously held by Ajaz Shafi. Ajaz was appointed Chief Operating Officer for Sisk’s entire UK business earlier this year.
Speaking on his appointment Ger said: “I am honoured and excited to be stepping into the role of Managing Director of the UK South Division of John Sisk & Son, following Ajaz’s successful time in the role. The quality of our people, their commitment to getting the job done and the range of projects and clients in UK South mean it is a really an exciting time to be working for Sisk.
“We want to expand on our experience in high rise residential and in the commercial sector on the back of projects such as Unity Place in Milton Keynes. We also see further opportunities in the healthcare sector building on the back recent projects,” he added.
Ger joined Sisk as a graduate recruit in Ireland in 2003 and worked across a range of projects in Sligo and Belfast before moving to the UK in 2010 to work on the redevelopment of Wembley Park. Sisk has worked with Quintain at Wembley for the last 18 years and Ger has been part of the team delivering this unique regeneration.
Commenting on the appointment, Ajaz Shafi, Chief Operating Officer Sisk in the UK said: “Ger Hayes has worked his way up at Sisk from graduate level to now being MD of the UK South and this is testament to his skill, hard work and commitment as well as Sisk’s approach to supporting and developing our people. I wish Ger all the best in his new role and I know the team in UK South will continue to deliver under his leadership.”
One of the UK’s leading multidisciplinary property consultancy firms, EDGE, has welcomed its 100th employee with the appointment of Simon Spencer. Simon joins as director in the EDGE Leeds office, representing a significant milestone in the continued growth of the business.
Simon brings a wealth of project management experience in the construction industry, through both the public and private sectors. He has extensive experience within the
education sector specifically for the delivery of schools, Further Education colleges and Higher Education campuses across the north of England. Within the private sector, Simon has project managed large-scale infrastructure, commercial and mixeduse schemes.
Based in the fast-growing Leeds office, Simon will support the continued growth of the business, while providing high-quality project management expertise to EDGE’s ongoing education, infrastructure and commercial offering within Leeds and the wider northern regions.
Simon’s appointment builds on the company’s continued business growth in its established offices in Leeds, Nottingham, Sheffield, Birmingham and London, resulting in a 40% year-on-year increase in turnover from 2021 to 2022.
Soho Housing Association, one of Central London’s key social housing providers, has appointed Andrew Billany as Chair of the Board.
Alongside Barbara Brownlee, CEO of Soho Housing, he will be an ambassador for the organisation as it embarks on its next phase of development, with plans to create at least thirty new homes in the next five years.
Andrew brings a wealth of experience to the position, having worked in the housing, local authority and voluntary sector in senior roles for over 20 years. Andrew is currently Corporate Director of Housing and Community Safety at Dorset Council and a trustee of Nacro, the Social Justice charity.
Andrew has also worked in roles that include Managing Director at Homes for Haringey, in which he led the Executive Team in the management of housing services across the area, the Director of Housing at Newham Council and senior Housing Association roles such as the Director of Home Ownership at The Guinness Partnership, and Chief Executive of Hornsey Housing Trust.
The Finnish Contech company Aiforsite announced key appointments to its UK organisation. Aiforsite offers a gamechanging productivity management solution to construction industry leaders.
Construction technology company Aiforsite has appointed Vassos Chrysostomou as the Chief Operating Officer (COO) and Tom Woodhead as the Chief Experience Officer (CXO) of Aiforsite UK Ltd.
The new appointments will have a significant role in the growth of Aiforsite’s business in the UK market. Vassos will oversee the implementation of the company’s strategy to achieve business expansion and profitable growth, while Tom will contribute to developing and strengthening the customer experience.
Vassos Chrysostomou, COO UK
The new Chief Operating Officer, Vassos Chrysostomou, joins Aiforsite with over 20 years of experience in lean construction and integrated project management.
In his previous leadership role as a founder and managing partner of IBE Partnership LLP, he has acquired a powerful combination of knowledge
and expertise in collaborative working, supply chain management, lean construction techniques, sustainability and continuous improvement tools.
At Aiforsite UK, Vassos will be responsible for setting the overall direction of the country’s operations as well as the day-to-day operational management. He will establish and grow sales of Aiforsite solutions and build long-lasting relationships with customers and partners.
Tom Woodhead, CXO
Tom Woodhead, the new Chief Experience Officer, brings to the company over 20 years of experience from both the public and private sectors and the construction industry.
Over the last ten years, Tom has been responsible for the development of business services at Woodhead Group as a member of the Board of Directors with strategic oversight and accountability for continuous improvement, customer care, marketing, HSEQ, CSR, and ICT.
Technology, people, and methodology are the foundations of Aiforsite’s approach, and Tom’s expertise will enable the company to have a sharper, insight-based user experience for customers.
Construction firm, Helix, has appointed a new Head of Design to lead its design team and continue its expansion into the future.
Andrew Gullett brings more than 25 years of experience to the Newbury-based construction business, where he will continue to build on Helix’s growth and achievements to date.
Andrew, who is based in West Oxfordshire, started his career in London with Taylor Woodrow Construction and went on to work with housing contractors, including Willmott Dixon Housing and Hill Group.
Joining the Helix team as Head of Design, where he will head up the technical and design department, Andrew brings a wealth of knowledge to the fast-growing construction firm.
One area Andrew wants to focus on is continuing Helix’s strong relationship with partners and building a network of design consultants to work alongside: “Helix is a young company but has experienced huge growth already.
Andrew added: “There are several large projects that Helix is working on right now, which is exciting to see. I’m looking forward to seeing the business grow, and to playing my own part in that.”
I want to see us continuing to work with great companies, building trust and communication, and expanding the business while continuing to provide a fantastic service to clients.
Senior leaders from the UK construction industry and data experts came together to discuss how the sector could be radically reformed through improved collaboration – and sharing of company and industry data.
Hosted by framework provider Pagabo, roundtable attendees discussed key shifts in the construction industry that are needed to transform and improve hot topics such as health and safety, productivity, SMEs, skills and training, and the green agenda.
Attendees included Ann Bentley, global board director at Rider Levett Bucknall; Dave Newitt, CEO of data centre giant Yondr; Gareth Parkes, head of data and analytics at Sir Robert McAlpine and board member of Construction Data Trust; James Butler, managing director at Faithful+Gould; John Waterman, COO at Willmott Dixon; Jon James, managing director UK Construction at ISG; Martin Ward, co-founder at Construct.ID; Paul Tremble, chief strategy officer at WSP; Quam Adewale, industry strategy lead – built environment at Microsoft; Rab Scott, director of industrial digitalisation at The University of Sheffield Advanced Manufacturing Research Centre; Rob Byrnes, business support director and head of frameworks at VINCI Building; Steffan Speer, technical director at Morgan Sindall and Charley Wainwright, the future of construction lead at Pagabo.
Gerard Toplass, group CEO The 55 Group and Pagabo, organised the session – and
From L-R, Steffan Speer, Dave Newitt, Paul Tremble & Rob Byrnestalked about the need for a ‘black box’ moment for the construction industry.
He said: “Technology has democratised a lot of things and gives us a huge opportunity. Lots of other industries and businesses have experienced massive booms because of their willingness to share data.
“Just think about e-commerce and the amount of information businesses like Amazon holds on its customers, combining with AI to create the best experiences and value for consumers.
Construction businesses are often quick to try and gatekeep - and protect - their data. They predominantly make decisions based on only their own information, fostering a one-dimensional approach and ultimately slowing everything down significantly. This combines with slow-to-change attitudes and an industry full of more archaic industry bodies.
Toplass talked about a need to encourage leading contractors and consultants to put competition to one side, and instead really collaborate – sharing data across organisations in order to understand
what is happening in the industry, and how a real step change could radically improve the way things are currently done.
John Waterman said: “I have been a COO for several years and every year for me is about driving change, understanding how we can improve company services, alter our culture for the good of our people. What we are talking about today is among the things I am trying to do at Willmott Dixon.
“I absolutely agree that data sharing among the industry is vital for change. Every organisation needs to scrutinise the data for our own business and see what it is telling us – but then this data should be shared. We can then learn how productive we are as an industry, what the movement is in our businesses.
“I don’t think there is even an argument against for this. You have to start the journey – and we are now at the beginning of that journey. I think we need to decide which data we start with.
“Let’s start experimenting and health and safety is a great starting point. For me, it’s about ‘bite size’ pieces – dealing with data in chunks and starting small. Let’s not try and tackle everything at once.”
Rob Byrnes, business support director at VINCI Building, said: “Data drives change and publishing data about our industry is vital to transform the construction sector.
“Health and safety for example is an area that would benefit hugely if all contractors shared and analysed their data. It’s for the greater good of the industry and we should all support it.”
Toplass added: “We at Pagabo want to bring organisations together to discuss these topics – and come up with a collaborative plan where we can all work across the industry, sharing data and getting the best outcomes for our people and our projects.”
Performance improvement company, STC INSISO, has announced the launch of its latest product, Vendorse, which enables organisations to manage and risk assess their supply chain effectively.
STC INSISO has a deep-rooted heritage of working in the construction industry, providing software solutions for businesses globally. The latest software achieves supply chain compliance by ensuring suppliers complete the designated actions, always abide by the latest policies and procedures, and keep their respective profiles up to date. Some of the key features include:
• Supplier Onboarding – A simple and effective process that sends a request to the designated supplier to complete their profile.
• Supplier Review – Upon completion of the initial supplier request details, users can review supplier details, certifications and documentation provided in a concise format.
• Supplier Risk Assessment - Using a custom scoring system, assessors can conduct an effective assessment of the supplier, grading them on key metrics such as expenditure, environmental impact, safety, and security.
• Supplier Action Tracking – Users can define actions for suppliers to complete as part of their ongoing compliance. The built-in notification and reminder system ensures suppliers complete actions when required, with minimal intervention from the company.
• Company Branding and Configuration – System administrators can configure the platform to suit the needs of their organisation, as well as customising the portal with the company branding.
• Supplier Categorisation – Based on the risk assessment conducted, Vendorse can automatically identify the supplier with the appropriate categorisation level.
Two-factor authentication makes Vendorse one of the most secure tools of its kind; it is hosted in Microsoft Azure, adding an extra layer of cyber protection, and is fully autonomous. Overall, Vendorse is a dynamic, clean, cloud-based system which can be swiftly implemented into any construction business.
To find out how Vendorse can help you, visit: https://www.vendorse.io
Base Structures are proud to be a key part of this ground-breaking project to design and construct a dedicated drone airport in Coventry – the first ever in the UK.
The project sees multiple partners working together to create ‘Air One,’ an ambitious fabric structure that hosts a moveable hydraulic FATO platform (final approach and take-off area) in the structure’s centre. The 45m diameter structures was clad with PVC coated polyester fabric and included a fabric lining incorporating clear visual panels to the internal drum wall.
Andy Traynor, Director of Base Structures, said: “As a blueprint for the first of many urban drone airports, there’s an ambitious target to roll out as many as 200 Vertiports out around the world in the next five years. We’re proud to be to provide and apply our fabric knowledge and skills in a totally unique way.”
Although we’re at the forefront of such technology, it’s widely believed that drones will play an increasing transportation roll across the world and may be a more familiar sight in the skies above us. UK company Urban Air Port look to grow such an industry, with one day hosting electric and Vertical Take-off and Landing (VTOL) aircraft from their Vertiports that could be used to transport paying passengers.
For more information about Base Structures, visit www.basestructures.com and have a look at their extensive portfolio of tensile fabric solutions and canopies for outdoor areas. For any questions or to chat through some options with the team, ring +44 (0) 1179 115250 or email sales@basestructures.com
For more information about this project, visit: https://www.urbanairport.com/ or contact sales@basestructures.com
From initial design through to construction, technology can help the construction sector move away from its heavy contribution to carbon emissions by providing the data and understanding needed to enable better decision making.
The industry has to move to Net Zero. Enshrined in law, part of government guidance and increasingly influencing procurement, finance and insurance, it is a question of when, not if. The industry has until 2050 to eliminate emissions in domestic and commercial buildings so we must design with that in mind.
With clients and end users also pushing for more sustainable solutions, now is the time for organisations to act.
Many organisations are testing new technologies to improve building performance and reduce carbon emissions in construction and operation. But, there are lots of innovations out there and it can be difficult for people to compare options and choose the right route forward.
That is why the first step should be to invest in software tools that bring the whole supply chain together and allow easier collaboration, from the moment the project objectives are set. Early engagement at design stage makes the likelihood of a more sustainable project greater, by having access to the full range of experts who will be responsible for the project.
With organisations moving to reduce their environmental impacts in the wake of rapidly rising costs and increasing climate related events, technology holds the key.
This can drive early decision making about key aspects of the project. What passive measures will the building utilise, such as shading or ventilation? What technological inputs will the building have to better manage energy or heat? What materials will be selected and what will be the construction methodology?
Get the right things in place at project inception, including agreement on realistic performance expectations, and you’ll be a good step along the journey.
Working in this way is more efficient too, increasing the opportunities to remove wastage from the process. Even at its most basic level, collaborative software removes a significant amount of paper and gets everyone using the latest plans, avoiding unnecessary work and creating a helpful audit trail for the project.
There remains a challenge with retrofitting existing buildings, however. While there are tools that can be used to measure existing buildings, there is currently a lack of capacity and skills within the sector to deliver change at volume.
Manufacturing also lends itself to continuous improvement, with more effective processes or materials being switched in as and when appropriate. It means that as new, more energy efficient or eco-friendly products become available, the production can easily follow suit.
Tracking life-cycle information via operational dashboards and regular reporting, which compares the original brief, design approach and “in-use” performance, provides building operators with a greater understanding of their assets. This should lead to better decisions about our built environment when planning new projects, reducing both the financial and carbon cost, and see more innovation in materials and processes. This data should be made centrally available and fed back into the design process so that good initiatives can be repeated elsewhere.
In practice, it would mean that we would start to see accurate, updated digital records of buildings from design stage through to construction, operation and maintenance. Software is perfectly placed to make this happen, by building audit trails, spotting and manage risks, ensuring compliance and ultimately driving project learnings to make projects more efficient, better quality and achieve better value.
Of course, it’s not just in traditional construction methods that we need to look at sustainable options. Modern Methods of Construction (MMC) promise a more efficient, low carbon future too.
Greater use of offsite manufacturing can embed sustainability from the start. Constructing buildings in a factory-based environment means that the most efficient and accurate production methods can be used, improving quality and removing waste from the process. That even includes the use of standardised components, allowing more accurate forecasting and use of materials and allowing excess parts to be used elsewhere.
So, for organisations, understanding how technology can help address these issues is more important than ever. It is for this reason that we have worked on a guide with the Chartered Institute of Building (CIOB) to outline where technology can be introduced so that the benefits described above can be realised.
The guide is divided into three sections: planning and design, construction and occupation and ongoing management, to help people along every step of the way. Our aim is to give clients the understanding of how technology can be effectively harnessed so that they can achieve the outcomes that they desire.
Download your copy of the guide.
Founded in 1847, Radley College is one of the country’s most esteemed independent public schools. The college’s Grade-II listed chapel is the site’s spiritual centre, being it’s the only place where the whole school can congregate for daily services. As part of an elaborate expansion, the chapel recently underwent a refurbishment that included the building of a sanctuary. To augment this stunning new architectural feature, an octagonal plan form and roof lantern created from self-supporting curved structural glass featured as part of the design. The expanded chapel delivered an additional 207 seats to increase its total seating capacity to 807.
The approach to the new sanctuary’s octagonal plan form features a series of stone and rubbed brock arches. For these elegant structures, which lead from openings specifically created from within the chapel’s nave, IG Masonry Support provided six, sectional brick slip masonry support arches. These bespoke designed solutions not only facilitated the inclusion of some intricate brick detailing to meet the architect’s imaginative design, they ensured a time and cost-efficient installation beyond the capability of traditional brickwork techniques.
Selected for the project on account of the company’s expertise in the supply of prefabricated sectional arches, IG Masonry Support was nonetheless confronted with a number of conundrums due to the programme’s size and complexity. The sectional brick slip masonry support arches were required for two elements of the college chapel refurbishment: four new apse openings, and two ante sanctuary brick arches where an end wall intersected the existing chapel walls.
Products Used: Sectional Brick Slip
Masonry Support Arches (x6)
Architect: Purcell Architects
Main Contractor: Beard Construction
Subcontractor: OG Stonemasonry
Images: Dan Paton Photography
For IG Masonry Support, the four apse openings presented a challenge due to the varied wall thicknesses. Each apse arch had to fit between two kicker stones which differed in height, resulting in IG Masonry Support’s design team having to work to tight tolerances and size variations in two planes. All four arches were a variety of widths, with different wall thicknesses on each side also needing to be taken into account. Challenges also came in the form of the arches’ elevation, which needed to match the small radius vertically and the join that intersected them. Furthermore, the apex of each arch had to be the same size and level despite the variance of surrounding components.
To meet the application’s requirements, which needed to be unerringly precise due to the tight tolerances and size variances of the arches and surrounding structure, IG Masonry Support bespoke designed and manufactured each sectional brick slip masonry support arch. The process was complex and due to its non-standard nature, required a methodical, yet innovative approach. The support arches needed to blend seamlessly with the existing chapel and extension in a form that was beyond traditional bricklaying techniques. IG Masonry Support’s success in meeting its intricate brief is testament to its experience and expertise in delivering brick slip solutions for projects of all size and purpose. The expanded college chapel has not only enhanced the historic building’s grandeur and capacity, the refurbishment has been nominated for three industry awards: the Construction Excellence SECBE Awards (Conservation and Regeneration category), the Brick Development Association Brick Awards (Education category) and the OxPropFest Awards (Project of the Year category).
Karl Devlin FIOC, Site Manager at Beard Construction, said:
This was a truly magnificent project. It was a one-off build in a superb location – we felt privileged to help bring it to fruition. Andy Sharlot, Chief Designer at IG Masonry Support, had a great influence on the project’s success. His technical knowledge and expertise made for an enjoyable working experience, which for such a challenging project, proved to be a real bonus.
Have you ever toiled with the prospect of becoming a teacher? Are you passionate about passing your knowledge to younger generations? If the answer is YES, it could be time to consider the available teaching options.
Further education colleges and commercial training companies are always looking for vocational lecturers, trainers, and assessors across bricklaying, the built environment, civils, engineering, plumbing & gas, carpentry/joinery, electrical, and machining world who can pass on their knowledge to the next generation.
There are many reasons why more and more tradespeople look to teach for their next career move. Many want to supplement their income from their main businesses, some have had enough of the wear and tear on their bodies, and others are looking to retire from the trade but are not quite ready for retirement.
In 2021, the IET’s report revealed an estimated shortfall of over 173,000 workers in the STEM sector, with an average of 10 unfilled roles per business in the UK. The IET’s latest ‘Skills Survey’ (based on research conducted by YouGov) identifies that almost half (49%) of engineering businesses are experiencing
difficulties in the skills available when recruiting. (IET.org). If you were looking to get into teaching, now would be a perfect time.
Don’t have any qualifications… That’s ok; there are still opportunities.
Experience goes a long way. Many further education colleges take tradespeople on without the necessary teaching qualifications.
Temporary positions are always available and offer excellent flexibility as well as highly competitive hourly rates of pay.
Suppose you are passionate about passing on your knowledge to younger generations and enjoy working with adolescents. In that case, you could join a college as a technician to work alongside a lecturer or, in some cases, straight into a lecturing or assessing role. We have seen experienced technicians become lecturers at the same college and colleges, supporting temporary and permanent employees with the relevant qualifications and experience to forge a career in the sector. All you need is
an enhanced DBS and complete necessary vetting checks to work with under 18’s.
The average starting salary for a fulltime teacher is £28k, and for science, technology, engineering, and mathematics (STEM) related subjects, in specific areas of the country, an extra £9k incentives (spread over three years). Temporary positions are always available and offer excellent flexibility as well as highly competitive hourly rates of pay.
• Communication skills
• Interpersonal skills
• Technical skill and subject knowledge
• Good time management / Organisational skills
Interested in what to do next? Call us today on 0333 0326 333, or visit our website ironbridgepartners.co.uk and we can start looking for a role for you.
Kier has started work on the country’s first net zero carbon prison in operation, for the Ministry of Justice (MoJ).
Damian Hinds, Minister for Prisons and Probation, along with Councillor Jonathan Owen yesterday attended a ground-breaking ceremony at the site in the East Riding of Yorkshire to mark the commencement of the project.
The nearly 1,500-bed Category C prison will be the first to be zero-carbon in operation, and once built will run fully on electricity. Other sustainable design features include solar panels, heat pumps and more efficient lighting systems to reduce energy demand.
In a further drive to reduce embodied carbon, Kier will use elements of modern methods of construction (MMC) as well as cement replacement for the build, along with bio fuel and renewable sources, including solar panels.
The new jail follows Kier’s successful build of HMP Five Wells in Wellingborough and supports the MoJ’s drive for platform design (PDfMA); the new prison is based on the blueprint of Kier’s design for HMP Five Wells, and part of the houseblock design used in the Accelerated Houseblock Delivery Programme.
Opening up employment opportunities in the local area, hundreds of jobs will be created during construction, and once built, 600 jobs in a range of fields will be created. Social value will be a key element of the project, with Kier committing to 50
sustainable employment opportunities for prison leavers, 50 apprenticeships, and upskilling 1,000 workers within its supply chain.
Additionally, Kier and the MoJ’s commitment to supporting rehabilitation will provide employment opportunities for serving prisoners and prison leavers through Kier’s industry-leading Making Ground initiative; including work opportunities for Release on Temporary Licence (ROTL) prisoners.
Completion is due in 2025.
Liam Cummins, Group managing director of Kier Construction said: “Breaking ground at Full Sutton yesterday was a major milestone for this new prison. It builds on our successful partnership with the MoJ, where we have been operating successfully in close collaboration for the past decade.
“We will deliver this new prison as a cuttingedge facility, built on engineering excellence that we have utilised on other projects, and using innovative sustainable methods which will achieve net zero in operation. Alongside this, we’ll create hundreds of jobs throughout the lifecycle of the project, supporting local people and the supply chain, as well as providing opportunities for prisoners on release.”
Minister for Prisons and Probation Damian Hinds said: “The new prison at Full Sutton is a best-in-class example of how energy-efficient technology can cut costs for taxpayers and deliver state-of-the-art, modern prisons. The project will boost
jobs in East Yorkshire and offer invaluable employment opportunities for up to 50 exoffenders during construction – helping to cut reoffending and keep communities safe.”
Mace, the global consultancy and construction company, is the MoJ’s delivery partner and alliance manager for the HMP Full Sutton project since 2019.
Jason Millett, CEO for Consult at Mace, said: “Mace has worked closely with the MoJ to deliver the New Prisons Programme, completing at HMP Five Wells earlier this year and bringing practical delivery experience to the entirety of the programme.
The new prison at HMP Full Sutton is a world-leading example of how a focus on net zero development can create positive, sustainable change. This milestone is a fantastic achievement for our teams and demonstrates our strength in delivering against the decarbonisation agenda.
“We are excited to drive further innovation on the programme for the MoJ, creating social value and opportunities for local communities.”
Kier was recently named as a contractor on the £500m Accelerated Houseblocks Development Programme for the Ministry of Justice and last year completed the multi-award winning HMP Five Wells.
Leading construction company, Henry Brothers, has been named winner of the GB & Republic of Ireland Construction Project of the Year Over £2.5million category at this year’s Construction Employers Federation (CEF) Excellence Awards.
Launched in 1999, the Construction Excellence Awards are considered the most prestigious event in the Northern Ireland construction calendar and are designed to reward the achievements of the industry whilst highlighting the contribution it makes to the local economy.
Henry Brothers received the Construction Project of the Year Award for its completion of a £4.4m woodland day nursery and forest school at Staffordshire University.
Ian Taylor, Managing Director of Henry Brothers Midlands, said: “We are pleased to have received industry recognition for our very first carbon neutral project, representing a significant milestone in Henry Brothers’ strategy to reach net zero carbon emissions by 2050.
Congratulations must go to our exceptional staff which have delivered an outstanding modern nursery and forest school on campus, with sustainability at its core.
“Henry Brothers is privileged to provide Staffordshire University with a truly futureproof facility which will provide significant benefit to staff, students, and their families.
“We look forward to constructing many more carbon-neutral projects for our valued clients in the years to come.”
The Woodlands Day Nursery and Forest School is a single-storey timber frame building located close to the University’s nature reserve at the heart of its Leek Road site in Stoke-on-Trent. The facilities were designed to meet high demand from both students and staff nursery places and to provide additional places for the wider local community.
Sustainability, digital technology, and nature are at the forefront of the build, which features REHAU earth tubes and air source heat pumps which use passive cooling/heating rather than mechanical ventilation; along with roof mounted solar photovoltaic panels to offset carbon emissions.
In addition to Henry Brothers, the project team consisted of Mace as project and cost managers, Feilden Clegg Bradley Studios as lead designer and architect, Max Fordham as building services engineers, Civic Engineers as structural engineers and transport consultants, and Re-form Landscape as landscape designers.
The Henry Brothers’ design team included CPMG Architects, structural and civil engineer Hexa and Couch, Perry, Wilkes for M&E services.
Henry Brothers is part of The Henry Group, which comprises a number of manufacturing and construction sector companies, ranging from external construction through to interiors fit-out.
Eight plumbing apprentices are battling it out for the chance to be crowned the best in the UK.
The UK National SkillPLUMB 2022 Final, which is taking place between 16-18 November, is a competition promoting standards and skills across the plumbing industry, developing competence into excellence.
BPEC organises the competition on behalf of WorldSkills UK and it is being supported by WaterSafe, the national register of qualified, approved plumbers, supported by all UK water companies and the drinking water regulators.
All SkillPLUMB candidates had to complete a practical task at their local college or training centre before reaching the regional heats. Record numbers of competitors took part in the seven regional heats. The top highest scoring competitors were then invited to take part at the UK final being held over three days at Middlesbrough College.
Finalists will be tested on a complex installation task and judged against a strict marking criteria. Those that perform well could then be invited to compete against other young plumbers across the globe at the WorldSkills 2024 event in France.
Finning, exclusive dealer of Cat® machines and equipment in the UK & Ireland, are celebrating after their apprentices graduated with distinction, having overcome Covid restrictions to complete their four-year programme.
The high-flying Class of 2018 enjoyed a graduation ceremony together with family and friends at the Clayton Hotel in Birmingham earlier this month, with 13 apprentices officially becoming fully qualified and accredited engineers and eight of them achieving distinctions.
Marsha Myles, learning and organisational development manager, explained that the company has achieved a 91.7% Qualification Achievement Rate which represents one of the highest qualification rates across the whole of England where the national average is 58.4%.
All the apprentices have now secured permanent roles within Finning. Among them was Joe Cross who won the Apprentice of the Year Award, achieving the highest mark for his assessment, and Sam Elphick who has dyslexia, who was also delighted to achieve a distinction having got
to grips with a combination of online and hands-on training.
Sam is now based at the Finning UK site in Ashford in Kent, working within the workshop helping to prepare and rebuild machines from dozers to loading shovels.
This graduation was particularly special as it was the first Finning has been able to hold in-person over the last two years and gives the apprenticeships a pivotal point to mark the start of their career
journeys. Finning has a successful career pathway development programme that’s open to everyone and enables them to access funded courses up to master’s level together with professional memberships.
Many previous apprentice graduates have gone on to take up senior roles within the service and product specialist teams, including Director of Service Operations, Iain Carpenter, who began his career as an apprentice with the company over 20 years ago.
The National House Building Council (NHBC) has recognised Andy Martin (43) for his site management capabilities with a Seal of Excellence Award, marking him as among the best in the UK.
Andy is overseeing the construction of new homes at Woodland Heath, off Salhouse Road in Rackheath.
Originally from Attleborough, the site manager has worked for Barratt and David Wilson Homes for 24 years and has now secured his second consecutive Seal of Excellence award.
Andy said: “It’s a great feeling to have won this prestigious award for the second year in a row, and I feel a huge sense of achievement to be considered as a winner amongst some of the best site managers in the country. The award is a reflection of what a great team effort can achieve.
“The Seal of Excellence reflects the quality in each home at Woodland Heath at every build stage from foundation to finish.”
These accolades rate Site Managers against key criteria such as technical expertise, health and safety, consistency, leadership and attention to detail. The awards celebrate the vital role Site Managers play in ensuring new homes are delivered on-time, on safe sites and to the highest quality standards.
Having won a Pride in the Job Quality Award earlier in the year, the Seal of Excellence achievement marks an excellent year of achievements for Andy and his team at the development.
Simon Wood, Managing Director at Barratt and David Wilson Homes Anglia, said: “Our site managers are on the ground each and every day making sure our housing developments are operating smoothly and to the high standards we set. We’d like to congratulate all of our award-winners for their continued hard work. With our employees winning Seal of Excellence awards, it demonstrates the long-term commitment we’ve made to providing our customers with the best possible service.”
A Barratt and David Wilson Homes site manager has won a top national award for the quality of homes being built at new housing development near Norwich.JM Clark is an established mechanical road sweeping and surfacing support company, with over 10 years’ experience in the industry. Combining their extensive range of services and a reputation for providing a superior level of service, they have become a driving force in the plant hire business.
We are widely recognised as specialist suppliers and work alongside some of the biggest construction companies in the UK. Our ongoing programme of investment ensures that you hire the latest fully operated vehicles, all equipped with the most advanced technology.
There will often be vehicles preventing road construction from going ahead, our ultra-modern machines are fully equipped to handle the movement of most vehicles weighing up to 7.5 tonnes. Using a crane and the sturdy aid of wheel cradles this method enables a damage free solution for relocating your obstructive vehicles. Our fleet of Volvo vehicle lifters provide quick and easy clearances.
Mechanical Road Sweepers - We have a large fleet of the latest Bucher Municipal sweepers, designed to perform even on the most demanding work sites. Our truck mounted mechanical sweepers collect, compact and remove virtually all forms of debris in wet or dry conditions. The fleet is fully equipped with pressure jet washers,
heavy-duty overhead gully suckers and a microtrap dust suppression system.
Bitumen Emulsion Spraying and Joint Sealant - Using the rear spray bar or a handheld lance our state-of-the-art schäfer-technic and secmair fayat bitumen sprayers deliver the highest precision of dosing quantities and spraying results. With tank capacities of up to 5,000 litres and spray widths up to 5m, we can cover large surface areas while satisfying the very highest quality standards. Our sprayers are equipped with the latest technology, left and right side vertical joint spraying arms and a quick dry dope spraying system, to provide you with fastdrying bitumen emulsion.
Road Marking - Using the highest quality materials our expertise covers road and highway markings, car park markings, EV charging bays, disabled bays, school playgrounds, safety walkways, workshop markings and bespoke custom markings. Our operators are passionate about road markings, with every job carried out to the highest standard.
JM Clark takes the well-being of our clients and operators very seriously. We strongly believe in safety-first and will continuously enhance our overall fleet safety wherever possible. A handful of our current fleet safety additions include:
• FORS GOLD accreditation
• Proximity lighting system
• Automatic braking systems
• Fully chapter 8 with night working lights
• Highway maintenance signage
• 360 camera system
• Audible right hand turn alert
• Cyclist proximity sensors
• Fully insured and qualified operators
• LOLER tested annually
With tailored machines in your chosen field and a choice of hiring options available, our fleet has the flexibility to provide you with all the specialist solutions you require.
JM Clark takes the well-being of our clients and operators very seriously. We strongly believe in safety-first and will continuously enhance our overall fleet safety wherever possible.
Find us on:
Twitter: jmclarksweepers
Facebook: Jmclarkltd
LinkedIn: jmclarkltd
Instagram: jm_clark_ltd
YouTube: JmclarksweeperhireUk
Accreditations: FORS GOLD, Avetta, Constructionline, CHAS, MQPC and RSTA
Get in touch -
Telephone: 0800 014 6241
Email: info@jmclarkltd.co.uk
Website: https://jmclarkltd.co.uk/
Following its launch last week, the first 105kVA Tecnogen/PUNCH HydrogenFlywheel Generator has been purchased by John F Hunt Power.
Sharing the common commitment to be market leaders, the 20-year relationship between BGG Tecnogen and John F Hunt was strengthened earlier this year when Hunt invested £12 million in the largest single purchase of Stage V Generators in the UK.
Now, an innovative collaboration between Tecnogen and the PUNCH Group has resulted in a ‘World First’, by combining a Hydrogen Engine with Flywheel Power System technology, integrated into a generator.
PUNCH Hydrocells developed the hydrogen engine, which is based on a robust diesel engine design, already being produced in high volumes for other applications.
The integrated Flywheel Power System, developed by PUNCH Flybrid, rapidly injects high powered energy, increasing the dynamic load response and peak power of the generator for demanding applications as required.
The unit itself has been created by Tecnogen, part of the Bruno Group based in Italy, whose generators are characterised by incredibly low noise, high efficiency and outstanding reliability.
The John F Hunt Group, who are openly committed to achieving Net Zero emissions, have closely monitored the revolutionary developments in the hydrogen sector for some time and have seen this as the right moment in time to invest in the technology via their Power Rental business.
With an internal commitment to becoming carbon net zero by 2030, leading wet civil engineering firm Land & Water has become the first company in the UK to invest in brand new Kobelco SK210 Hybrid 15m Long Reach Tracked Excavators. This specialist plant will add to the firms existing sustainable fleet which aims to reduce the carbon footprint of the projects it undertakes.
The new excavators use innovative hybrid technology alongside lithium-ion batteries to power the swing motor. This, coupled with the newest and cleanest engines, brings a fuel saving quality to the end user of up to 17% in comparison to conventional ICE excavators.
Land & Water’s specialist long reach and amphibious marine equipment,
which can be hired through its Plant division, has been carefully chosen to ensure it has environmental capabilities, including:
• Paddle designs on the track of amphibious excavators to reoxygenate the water
• The ability to use HVO fuel which is up to 90+% carbon neutral
• Machine features including eco mode and machine idle cut offs reducing emissions
• Clean engines (Stage five)
• Onboard telemetry that reports carbon saving and fuel usage
• Machine control to ensure task accuracy, avoiding over digging and revisiting, therefore reducing the use of the machine
Dan Jackson, Strategic Account Manager at Land & Water Plant Hire, said: “We are extremely excited to receive these machines and lead the way when it comes to implementing sustainable solutions. At Land & Water, we strive to offer our clients a range of excellent services that keep cost and environmental protection at the forefront of our minds. Being the first company in the UK to invest in this new machinery is extremely poignant and we urge our industry to follow and consider ways in which it can meet the current net zero target.”
The construction and civil engineering industry makes up almost 40% of the world’s CO2 emissions. Land & Water is committed towards reducing its carbon footprint and becoming Carbon Net Zero by 2030, this is making them one of the industries key pioneers.
JPS, a leading supplier of tool hire, plant, powered access and tower solutions, has recently been acquired by UK Hire Group as part of new plans for the company which will see it continue to grow and implement new innovative products under its two divisions JPS Group Services and JPS Platforms.
Founded in 2014 by John Young and Sandra Clarke who saw a gap in the market, JPS works across London and the South East to deliver equipment hire solutions, environmental services and working at height training including IPAF and PASMA courses. It has also recently been named one of the top 30 powered access companies in the UK by Cranes and Access as part of its annual survey.
Adam Hems, Chief Executive of UK Hire Group, says: “Our plan is to maintain the strong customer service that has enabled the impressive growth to date, whilst progressing with a strong technical focus.
“New innovative products will be introduced soon in order to offer products and services that make the jobs of our customers safer, more productive and more efficient. We also want to continue growing our team. The people within JPS are who make the company what it is today. We want to maintain our strong culture but also continue to attract the best people. We are currently in the process of creating training programmes for those
at every level and every role to ensure that progression and career opportunities are front and centre. The acquisition has presented a brand new and exciting opportunity for JPS as it continues to solidify its place as the leading plant and tool hire company within the UK.”
Within the past couple of months UK Hire Group has already invested in new equipment including its largest scissor lift to date and hired new employees including Shane Walker who will act as General Manager of JPS Group Services. The acquisition will see the company continue to evolve, creating more employment
opportunities, and develop its sustainable offering which includes a 70% electric fleet.
John Young, Founder and Director of JPS, comments: “Myself and Adam both shared ambitions to build a modern, technically focussed hire business and after the Coronavirus pandemic shifted the way in which large projects are undertaken, the acquisition felt right. JPS is in a strong position to supply our contractors across Essex, London and the South East and continue its expansion. I am very much looking forward to being part of JPS’ new journey and remaining as Director to support its growth.”
Global hydraulics and electric powertrain systems supplier Danfoss Power Solutions has secured a grant worth £407,112 from the U.K. government to accelerate the electrification of construction machinery. The U.K. Department for Business Energy and Skills awarded the grant through its Red Diesel Replacement competition, which seeks to accelerate the transition to electric off-road vehicles such as excavators and wheel loaders.
Danfoss plans to combine electrification with its Digital Displacement® technology to significantly improve machine efficiency. Reducing energy consumption by as much as 50%, the technology can dramatically decrease the size of batteries needed to power the machines and the amount of energy needed to charge them.
Danfoss is already constructing a £25 million state-of-the-art manufacturing, research, and development facility in Edinburgh, Scotland, to commercialize its Digital Displacement technology and Editron electric drivetrains, which it believes will transform the construction machinery sector.
Dubbed the Decarbonization Hub, the facility will become operational next year.
Danfoss research has shown that as much as 70% of an excavator’s energy is wasted in the hydraulic system between the engine and the working functions.
Significantly reducing this energy loss enables future machines to use much smaller, and therefore cheaper, batteries.
Danfoss’ computer-controlled Digital Displacement technology can significantly improve system efficiency and reduce energy use.
A paper Danfoss submitted to the International Fluid Power Conference (IFK), one of the world’s largest scientific conferences on fluid power, shows that Digital Displacement technology can already deliver a 24.8% lower capacity battery to complete eight hours of typical operation.
Volvo Construction Equipment (Volvo CE) is investing into the future of its facility in Braås, Sweden, the home of its leading range of articulated haulers, as a clear signal of its commitment to lead the transformation across all products toward a more sustainable construction future.
The A30G articulated hauler made from fossil-free steel was built at Braås
• An investment of SEK 360 million –approximately $32.7million – will accelerate the phased shift towards electromobility for its articulated haulers
• The factory will be adapted to enable it to produce a larger range of articulated haulers with different types of powertrains
• This forms part of Volvo CE’s longterm focus on environmental care and driving industry transformation to combat climate change
Volvo Construction Equipment (Volvo CE) has announced its intention to invest SEK 360 million, approximately $32.7million, into its production facility in Braås, Sweden between now and 2027.
The facility in Braås, long recognized for its environmental credentials, specializes in the design and manufacture of articulated haulers for the global market. It produced a fossil-free construction machine that was the first in the world to be delivered to a customer - an A30G which is now in use on customer NCC’s worksite.
The decision to invest in Braås was made by AB Volvo’s board of directors and means that the factory will be adapted over the coming years to enable it to produce a larger range of articulated haulers with different types of powertrain to reflect the shift in demand towards equipment with more sustainable power sources.
The investment will be used to extend production capacity at the 45,000 m² site in southern Sweden to broaden the product range going forwards, with the addition of new buildings and production equipment. Setting its sights firmly on the future and in line with its purpose to build the world we want to live in – and workplaces we want to work in - Volvo
CE will also invest in automation and ergonomics to both reduce the need for employees to engage in repetitive tasks and create a safer work environment.
Sustainable innovation in its DNA
Pioneering manufacturing techniques is nothing new for Braås. Since producing the world’s first series manufactured articulated hauler, the “Gravel Charlie”, a 10-ton hauler, in 1966, the facility has been at the forefront of innovation. The site is most famous for producing the largest articulated hauler in the world, the 60-ton class A60H, a real feat of engineering.
It is important for us to continue to be at the forefront and make clear decisions to meet our Science Based Target commitment to achieve net zero value chain emissions by 2040.
By adapting our production for electric machines, we are progressing along our electrification roadmap.
As well as constructing the world’s first articulated hauler made from fossilfree steel, the engineering talent based
here has also been instrumental in the building of the world’s first prototype articulated hauler powered by hydrogen fuel cells – the concept Volvo HX04 –which is currently the focus of testing to develop future hydrogen solutions.
Braås is also leading the way in environmental protection and was the first in the construction industry to achieve a carbon neutral operation powered entirely by renewable energy. In 2018, the site also became a zero-landfill facility.
“The transport and construction industry is undergoing a transformation with, among other things, an increasing number of electrified vehicles,” says Jonas Lakhall, site manager at Volvo CE in Braås. “This investment will enable us to adapt and extend our production facility so that we can offer a broader range of machines – with different powertrains – to our customers and help them meet their emission reduction ambitions.
“It is important for us to continue to be at the forefront and make clear decisions to meet our Science Based Target commitment to achieve net zero value chain emissions by 2040. By adapting our production for electric machines, we are progressing along our electrification roadmap.”
• Over half (58%) of tradespeople predict the cost-ofliving crisis will exacerbate the rates of tool theft in the country
• Tradespeople already losing an average of £4,470 due to their tools being stolen
• 59% of tradespeople report having their tools stolen in the last year vs 17% 1-2 years ago. Overall, 4 in 5 (78%) tradespeople have experienced tool theft
• More than one in six (15%) experiencing increased anxiety and as many as one in five feeling less safe to trust others and wider society.
Levels of tool theft in the UK – a crime which already impacts 4 in 5 tradespeople – are predicted to increase as a result of the cost of living crisis, according to a new report.
As the economic squeeze continues, over half (58%) of tradespeople believe that a rise in tool theft is inevitable. Tool theft is already having a significant impact on tradespeople across the UK, with a staggering four in five (78%) being directly affected by the crime – totalling an estimated £2.8bn worth of tools stolen across the UK.
Three in five (59%) have experienced tool theft in the past year alone, compared to only 17% 1-2 years ago. With tool theft costing tradespeople an eye-watering £4,470 each on average, it is having a profound impact on construction workers across the country.
Alarmingly, 39% of tradespeople reported having their tools stolen from their van whilst it was parked directly outside their home.
A further one in five (20%) say they’ve had tools stolen from their place of work. Over half (52%) did not have tool insurance at the time of taking the survey, leaving many with little choice but to take time off work while they replace their stolen equipment..
On Tuesday 27 April 2021, a motion for leave to bring in a Bill was presented in the House of Commons. The Bill proposed a requirement for persons selling second-hand
tools online to show the serial numbers of those tools in searchable advertisement text, and for connected purposes. As it stands, the Bill has not become legislation, leaving tradespeople of the UK feeling unsupported against the crime of tool theft.
Consumer awareness around the crime is high, with 71% of consumers believing that the average tradesperson has had their tools stolen once or more during the past year. Yet, according to the study, over a fifth (23%) of consumers purchased second-hand and/or refurbished tools. Out of which 19% consumers purchased without making any checks.
Introducing ground-breaking technology available to all hospitals, clinics, aged care homes and beyond.
Now Available in Wickes stores nationwide.
BT1 (Bathroom Technology Number 1) was developed from the creators of CT1, the number 1 sealant and adhesive on the market, that itself replaces several products in just one tube ( “All you need is one”.) CT1 is widely used by all trades, industries and DIY users alike. It is now specified onto most new builds, unsurprising giving that it has over 25 accreditations and is the most eco-friendly sealant available on the market today.
CT1, which leads the way in research and development, realised the industry was lacking extra advancements. At a time when we as a global community faced a global pandemic, all polymeric sealants were failing to provide clinically clean environments.
Creating a healthier and a cleaner environment seems in many cases a deciding factor when using a product. We now look at workspaces and living spaces differently. How can we prevent future risks from disease? How can we keep our surrounding environments free from bacteria? Of course we all play our part, and everyone has changed habits and considered options, but prevention is better than cure…
BT1, which uses CT1’s TRIBRID® Technology - the latest revolutionary technology in the world of sealants and adhesives - has also grabbed the attention of the healthcare industry. BT1 has been developed specifically for bathrooms and kitchens. This unique TRIBRID® technology is scientifically created to fight bacteria and fungus. Tested under MOD IOS 22196:2011, BT1 has been proven to reduce bacteria by up to 99.99%. As laboratory tests have proven, this unique formulation creates a barrier around itself, providing protection from foreign bodies and maintaining its clinical white colour. Leaving a clinically clean environment.
BUT - that was not all. BT1 was created at first purely for the bathroom area, eliminating fungal, pesticides and bacteria growth, whilst remaining flexible so no cracks or leaks would ensue. BT1 showed - after vigorous testing - that the actual real scientific breakthrough was that it reduces the risk of MRSA, E. COLI and Campylobacter. Hospitals and clinics are now widely using this not only for repair, but for new kitchen installations, for new bathrooms and for new laboratories.
BT1 comes with a guarantee of colour retention for up to 25 years. It is scientifically formulated in a way that bacteria/microbes cannot survive, making it easier to maintain a more hygienic surface, free from solvents and isocyanates. This makes it the ideal sanitaryware product, ideal for all public health institutions and clinics.
Hospitals such as Solihull Hospital in Birmingham, Good Hope Hospital in Sutton are amongst institutions that are now using BT1 for facility repair and maintenance work - thus creating a healthier environment. Many factories involved in food processing and handling are also now using this ground-breaking product.
Hospitals need the highest standard of cleanliness – yet want each department to be more sustainable. Of course, when hospitals are faced with a choice that puts hygiene up against sustainability, hygiene always wins. Hospitals now more than ever demand the highest level of hygiene, but they also want to be greener.
BT1 is EC1 awarded for lowest emissions, A+ Green, which is awarded for lowest indoor emissions green rated, Green ISO standard. The most unique is The Norwegian Asthma and Allergy association. The NAAF logo is highly sought after and one of the hardest accreditations to receive. This association test and award products based on their ability to reduce asthma and allergy attacks in the home. CT1 and BT1 have been awarded this. They are the only sealant and adhesives globally to achieve this.
BT1, with it’s unique TRIBRID® formula has also been awarded ETAG 022 approval for bonding shower panels. BT1 can be used to bond and seal. It can work in unison with CT1, which can be used for additional applications and also outdoors. Both are Made in Britain, and stocked in Wickes branches nationwide. Two leading brands supplying the nation’s leading building contractors.
Lignacrete