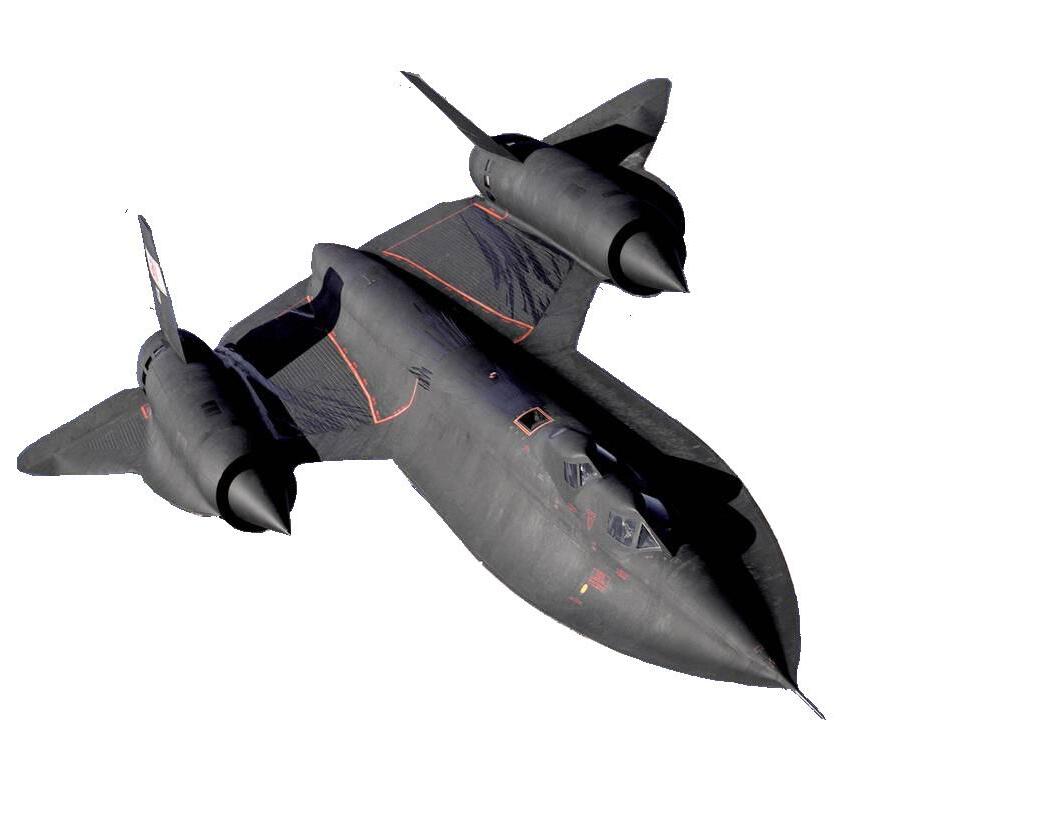
5 minute read
Pioneers of Aerospace
By Daniel Canache
say that the successors of these pioneers are not preparing to make their mark at this very moment?
Advertisement
Ever since the early 20th century, transportation above the Earth’s surface has been such organizations, the 21st has seen an increase in private and commercial aerospace companies, allowing rapid development across a variety of sectors. Indeed, dozens of companies have begun to branch out into hypersonics, small space, Venus Aerospace has different plans. With so much untapped potential in the commercial aviation industry, the company based in Houston, Texas has decided to bring to fruition the dreams of many airlines: the ability to transport passengers at hypersonic speeds. As implied by its name, the term “hypersonic” refers to speeds greater than or equal to five times the speed of sound, which is often referred to as Mach. The only vehicles that have laid claim to reaching/ passing Mach 5 are space capsules returning to Earth and highly specific test vehicles, such as NASA’s X-15 rocket-powered plane. From the view of the public, at least, the only aircraft which has been able to transport passengers supersonically (at Mach 1 or greater) was the Concorde, an exclusive passenger jet which could reach speeds just past Mach 2. However, due to mechanical problems and a lack of practicality, the Concorde saw a relatively short service life. Hannah McCallum, a senior propulsion engineer at Venus, says that in a current commercial aircraft, a flight from Los Angeles to Tokyo will take “10, 12 hours …. in plush, comfort and everything, but oftentimes time is money. So in [Venus’] case, we hypersonics for military institutions. These and many more are all possible applications of such a vehicle.
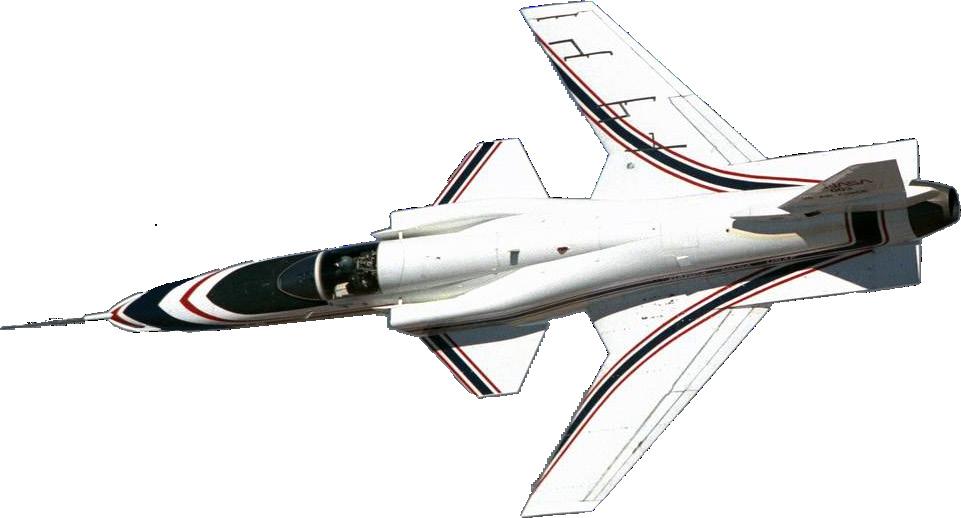
Of course, the act of flying at Mach 5 requires extensive planning and refinement. Perhaps the most unique of the various innovations that Venus is incorporating into its aircraft is the propulsion system, starring a Rotating Detonation rotating pattern. These substances are then ignited, causing a continuous wave of detonation in a rotating motion. The key detail here is the detonation. Most, if not all, rockets being used to propel flying vehicles as of this writing are considered deflagration engines, in which a flame passes through a mixture of fuel and oxidizer below the speed of sound. An example of deflagration would be a bonfire. Detonation engines, on the other hand, entails a supersonic (faster than sound) combustion and the consequent shock wave. According to McCallum, the latter form of combustion “has a much higher peak energy level, so the goal with the detonation engine is to capture that peak in that performance.” At this point, even without endless lectures regarding thermodynamics, you may be wondering why these marvelously efficient engines haven’t made their way into the aerospace industry. “The problem with detonation engines is that they’re pretty new,” says McCallum. Indeed, the difficulty in maintaining a constant detonation has staved off many efforts to make
RDREs practical. While some have been use as experimental payloads or run in labs, a motor of this type has never been the main source of thrust for any vehicle prior to this writing.
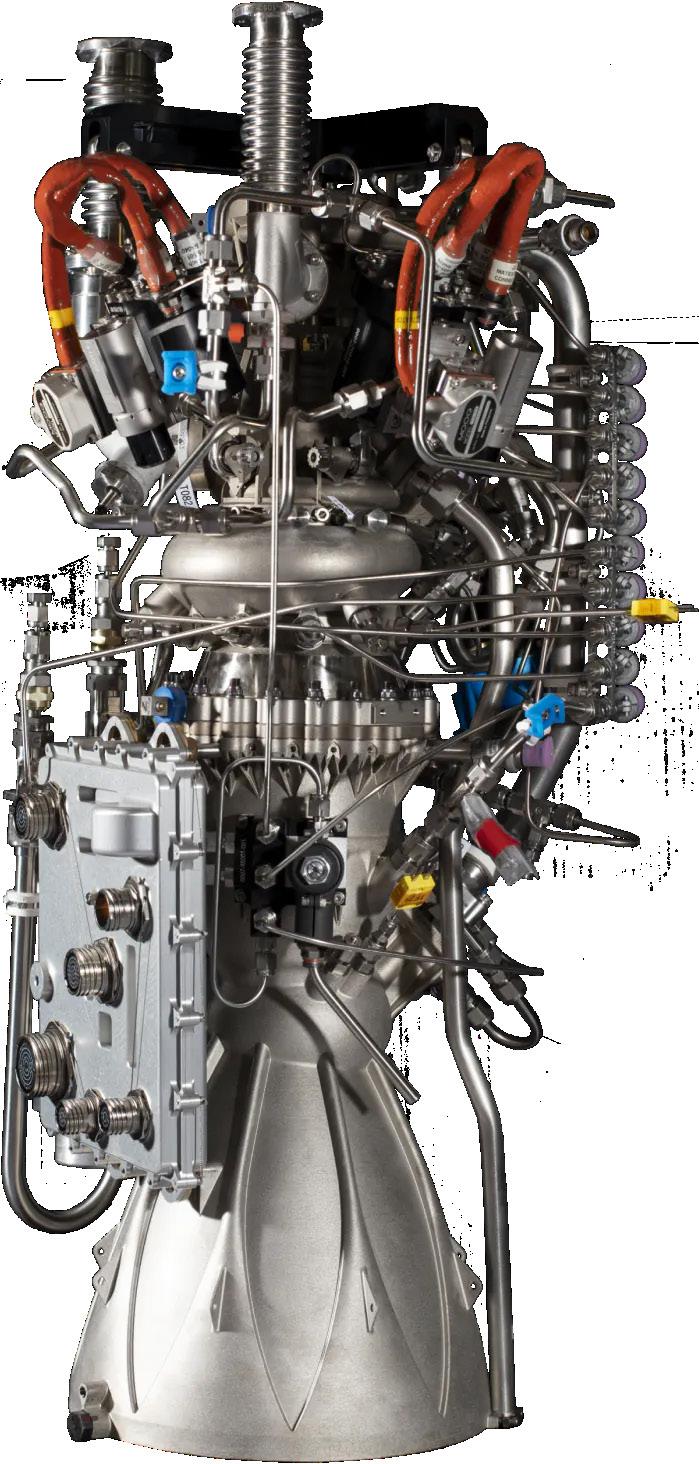
While RDREs have many advantages over their deflagration counterparts, the latter has one key asset at the time of this writing: unanimity. Because of the widespread use of these motors, they have been thoroughly researched and therefore refined. Ursa Major Technologies from Berthoud, Colorado is expanding the availability of these rocket engines to small private launch organizations. According to Sabrina Ames, a mission program manager at Ursa Major, “There are a lot of really interesting markets opening up for small rocket engines.” In other words, there are many companies seeking to develop air and space vehicles that lack the resources to develop an engine simultaneously. Case in point, Ames states that Ursa Major already has engine agreements with Stratolaunch, a hypersonics company, and Phantom Space Corporation, a vertical launch rocket company.
Ursa Major’s innovations don’t end at the privatization of spaceflight. Ames states that “85% of [Ursa Major’s] rocket engine is 3D printed out of metal.” While 3D printing is becoming more widespread in the hobbyist/ consumer market, this has profound implications in rocket science. One reason for this is that certain parts of rocket engines undergo extreme conditions during operation, and the ability to 3D print parts which can withstand these conditions is remarkable. Most notably, however, the design cycle of the engines is much shorter. While building a rocket motor usually entails bending, cutting, and welding small tubes and fabricating large nozzles/combustion chambers via costlier, more time-consuming conventional methods, 3D printing brings the fabrication of the bulk of the engine “down to three days.” Not only does this greatly increase the rate of development by allowing rapid iteration, it also allows for a much higher production rate of rockets and parts. The most fascinating part of this additive manufacturing spectacle is that at this point in time, nongovernmental organizations are the ones implementing this technology.
Last, but not least, is Radian Aerospace out of Renton, Washington, which is developing a reusable low earth orbit spacecraft, or in other words, a modernized space shuttle. As stated by Esther Deena, an aerospace technology development engineer at Radian, “It is very, very similar [to the shuttle] in terms of the environment that it goes through.” However, there is a serious emphasis on the “modernized” aspect of this vehicle. First off, Radian One, as this spacecraft is called, is single stage to orbit, meaning that all sources of thrust and fuel are on board the vehicle itself, without the detachable boosters and fuel tanks seen on space shuttles and many rockets. This greatly simplifies missions by requiring only fuel and maintenance to regain flight readiness, analogous to a conventional aircraft, instead of attaching new/recovered fuel tanks and external boosters. Another important detail is that space shuttle launched vertically, requiring more specialized infrastructure. On the other hand, Radian One is able (in theory) to take off horizontally, much as a plane would, using a rocket-powered “sled”. While not necessarily usable at conventional airports, this feature once again increases the vehicle’s practicality and is an improvement over NASA’s space shuttle.
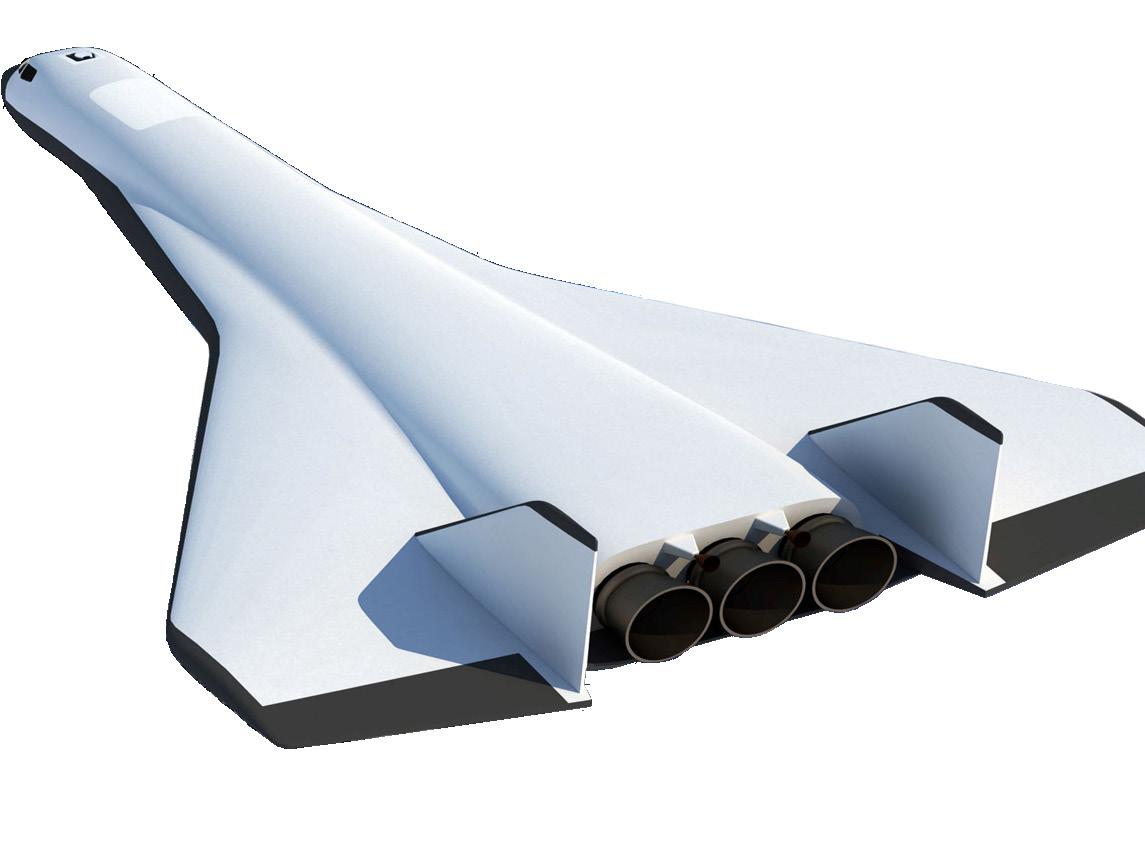
“the aircraft would be next to impossible. Unfortunately, the cancellation of the space shuttle program has virtually eliminated demand for these tiles, therefore causing the supply to disappear with it. Because of this, Radian is must to revive old supply chains in order to create their improved, more practical space shuttle.

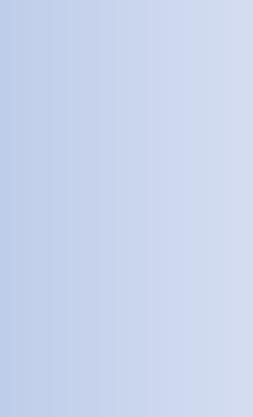
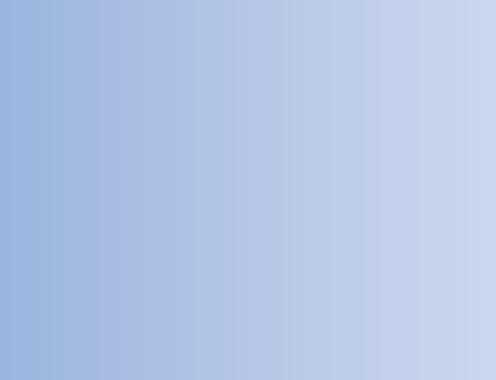
Augmented reality (AR) is a technology that overlays digital information, such as images, sounds, or text, onto the real world in real-time. It enhances the user’s perception of reality by combining computer-generated sensory inputs with the real world environment.
So the question will be whether the benefit will justify the cost and whether you actually see it. It gives you some, some real life quality of life improvement because now most examples you see, they are very toyish.
- Michael Nebeling


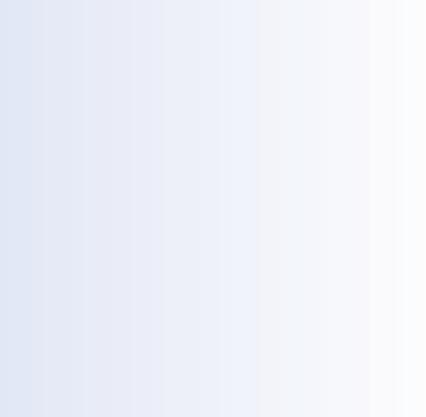
AR can be experienced through various devices, such as smartphones, tablets, smart glasses, or headsets, which use cameras and sensors to detect the physical environment and superimpose virtual elements onto it. The virtual elements can be interactive and respond to the user’s actions or movements, creating an immersive and engaging experience.
Currently, benefits of Augmented Reality glasses are dwarfed by the numerous problems that consumers dislike when looking at affordability and reliability along with everyday use. Function: