
5 minute read
Case Study
Case Study:
Robotic Field Painting
By Brendon Connor, Superintendent of Grounds, College of the Holy Cross, Worcester, MA
Introduction
Holy Cross is a D1 liberal arts school in Worcester, Massachusetts. Our athletic field crew is expected to deliver high quality fields that are safe and top quality for all game, practice, and intramural activities. With increased field use, budget constraints, a reduced skilled labor pool, and increased responsibility on our campus property, demands on our daily maintenance tasks have grown steadily.
We invested in a robotic field painter as a means to both save on labor costs and improve the quality of our lines. We now use the robot on all our fields and have seen a massive time and labor cost savings.
Site Conditions
• Seven- and one-half acres of varsity game fields.
• Seven acres of practice fields.
Problems
• Continual increase in the costs of labor and materials to maintain the athletic fields.
• Steady expansion of responsibilities; employees’ time is limited.
• Prior to painting a field, the time dedicated for the initial layout on any of our game or practice fields has been one of our biggest labor costs, requiring 2–3 employees. Expectations for perfectly painted lines are very high; it takes time to make sure we get it right.
Goals
• Reduce labor related to lining out and painting fields.
• Increase time available for other maintenance tasks.
• Achieve consistent precision in field quality and appearance.
Steps Taken
• First, I completed an audit of total inputs for the layout and painting of a field. This analysis helped us prove to administration that a robotic painter was worth the investment. We considered several autonomous-type paint machines and selected the model that best met our needs.
• We have a four-year lease, which costs about $10,000. Buying the machine was cost-prohibitive (about $40,000), and we expect the technology to improve over time, so it was more practical to lease. The lease comes with an excellent service program.
• Once we received the machine, we spent some time on each field becoming familiar with programming and completed the initial set ups. The program is very user-friendly and easy to use. Once the machine is programmed with the correct dimensions, the same set up can be reused in subsequent years.
• While the robot is painting, one person is required to be onsite to oversee the machine. Although the employee cannot walk away from the machine while it is in operation, it is possible to multi-task small jobs in and around the field.
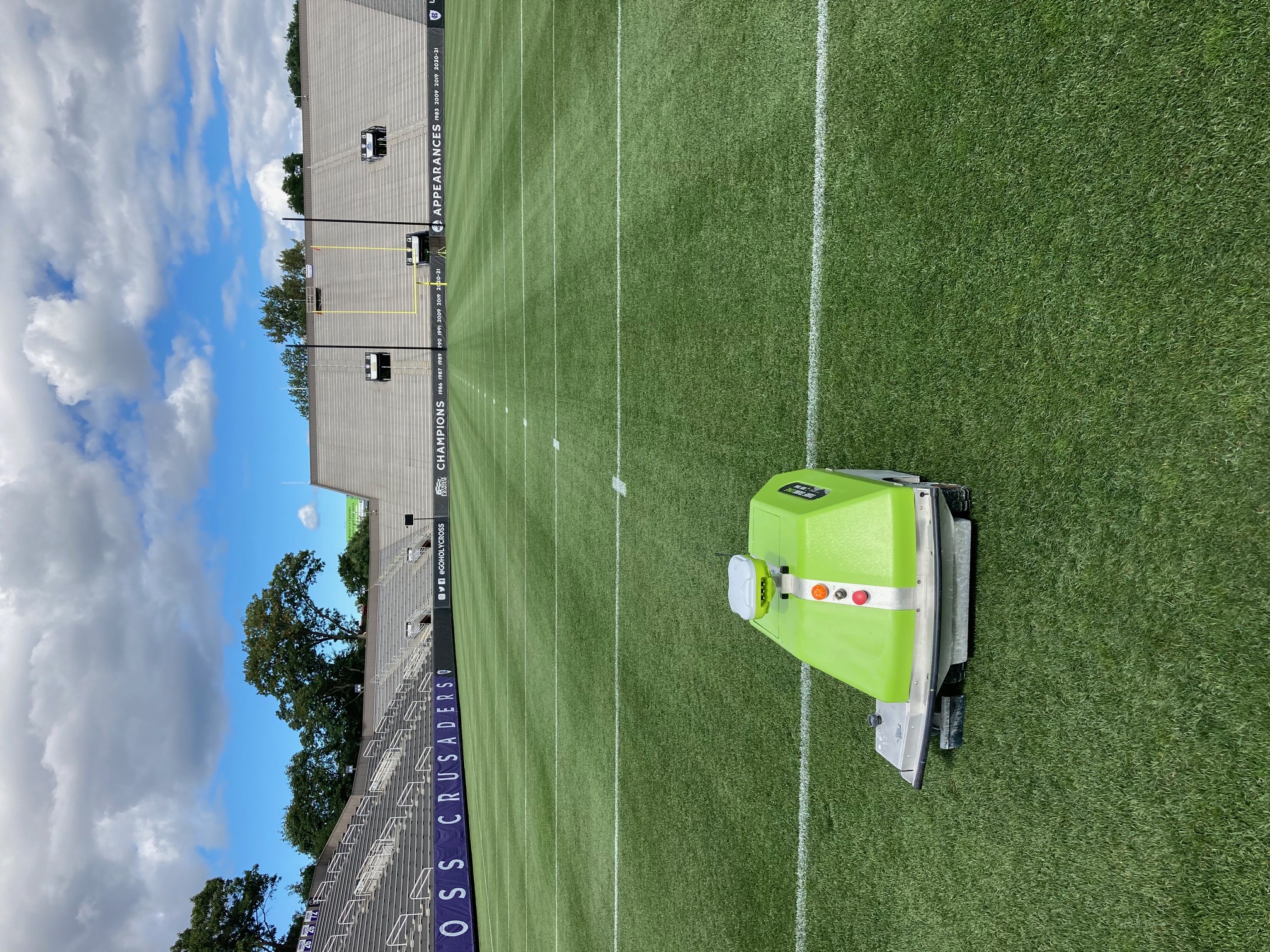
Results
• During the first full year of using the paint machine, we saved about 100–200-man hours. For example, it takes roughly half the time to paint the soccer field, with only one employee needed to oversee the machine. Paint use is about the same.
• We saw the greatest time-savings on the football field because there are so many different lines to paint. The return on that field was extensive—about 40-man hours, over the course of the first initial set up and complete painting of the field.
• With the time saved, we now have employees available to do other tasks, which has been of enormous benefit to our crew.
• The quality of the lines has significantly improved. The robot paints perfect lines each and every time without any human error.
• We have also found other ways that the machine helps us complete responsibilities. We can locate irrigation heads, mark out edges of baseball and softball fields for accurate infield skin and warning track dimensions, as well as efficiently line the football stadium for graduation and baccalaureate mass seating and stage setup. Labor for graduation setup used to require 100- man hours; the robot can complete that setup in four hours.
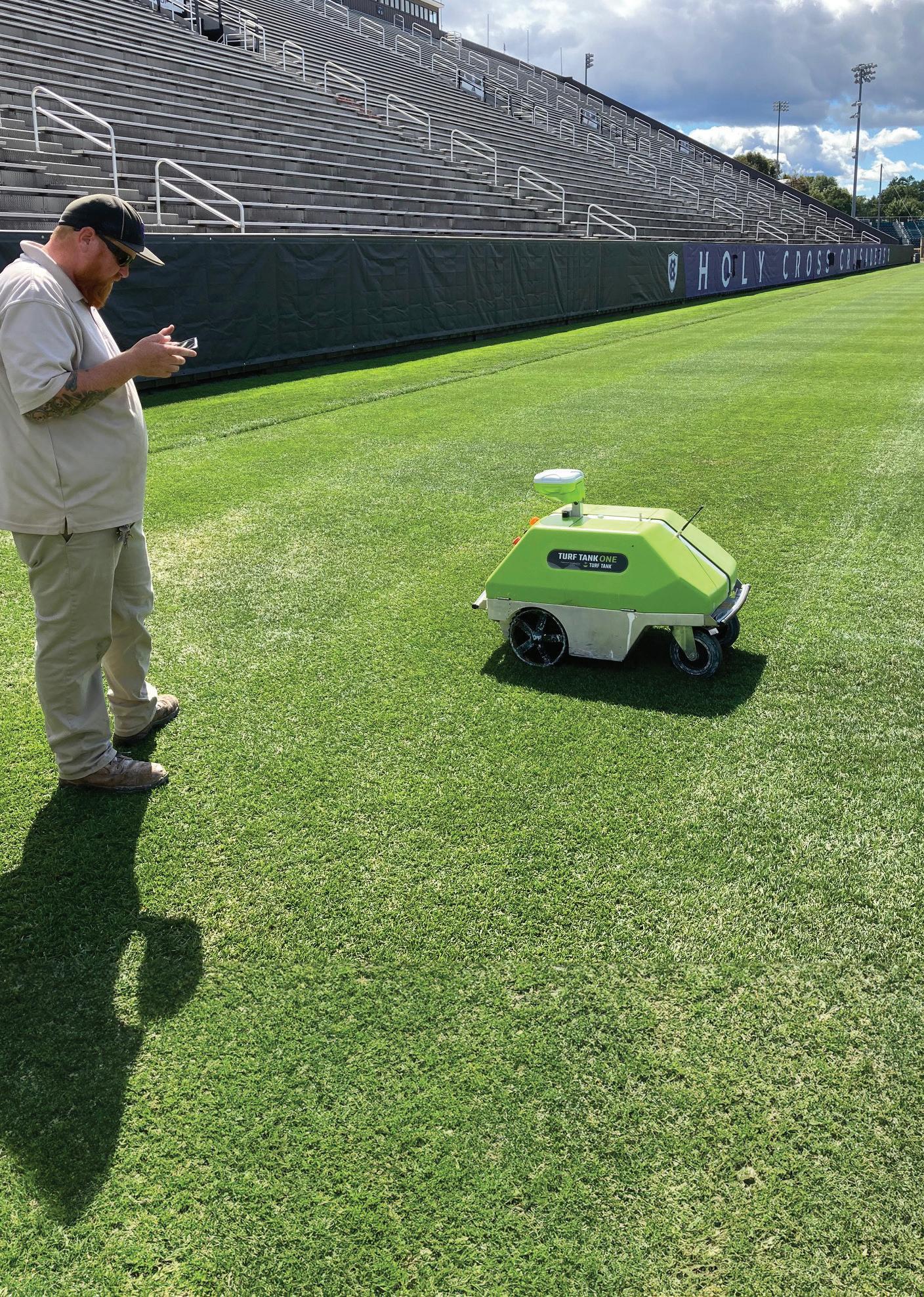
What We Learned
• The machine is limited to an 8–10 hour day of painting; the transponder battery cannot be swapped out.
• If the battery in the robot or transponder is exhausted, the machine will paint erratic lines or stop completely. If the machine has a clogged nozzle, it will continue to try to paint, which requires the operator to manually stop the machine, unclog the nozzle, and restart the line.
• The machine also does not seem to function properly in cold temperatures (near freezing). When cold, it has difficulty painting straight lines, which may be due to the type of oil in the drive motors. Keeping the machine warm is important.


Conclusion
Over the course of the first full year with the robotic paint machine, we have dramatically reduced our labor costs related to field layout and painting. We increased our efficiency as a crew and improved the quality of the product we present for our student athletes and campus community. •
Funds to support the creation of NESTMA’s Best Management Practices for the New England Sports Field Manager, including this case study, were provided by the New England Regional Turfgrass Foundation. All photos courtesy of the author.