
4 minute read
Cranemec
the rope construction. The CPU can be directly connected to a laptop during the inspection or downloaded to a laptop after the inspection and the result will be displayed as a graphical trace.
The trace delivers three primary sets of information: • Extent of the occurrence of broken wires. • Amount of steel loss due to wear (cross-sectional area) • Corrosion, damage and abrasion.
A trained MRT operator can use the signal (graphic trace) to detect the location of the degradation and assess the severity of the wire rope using visual and MRT evidence. The approximate reduction in rope strength can be accurately estimated. The entire length of the wire rope has to be tested and the complete cross section of the rope can be examined.
MRT detects broken wires or corrosion damage on the inside of the rope not visible to an external visual inspection.
Wire ropes deteriorate in three distinct stages: STAGE 1: During this stage large numbers of core wire usually in clusters will fail due to fatigue breaks
STAGE 2: Eventually, the internal wire rope core (IWRC) will break. This hazardous condition is rarely detected by visual inspection. In contrast, it is glaringly obvious to the MRT technician (LMI).
STAGE 3: As the IWRC fails, the outer strands lose their support which causes secondary fatigue breaks in the wires of the outer strands called “valley breaks”.
Detectable only by exceedingly meticulous visual inspection, this is the terminal deterioration phase frequently followed by catastrophic and fatal rope failures.
Summary There is an inexplicable lack of knowledge by some Lifting Machine Inspectors/Competent Persons on the uses and benefits of MRT testing.
Operational safety depends not only on your equipment, but also on the awareness, skill and performance of the people who
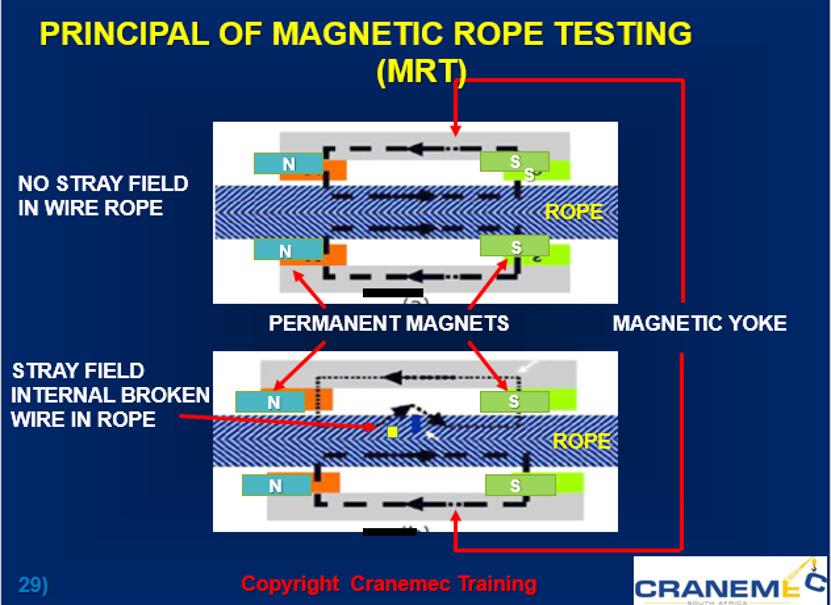
manage and use it. It is often difficult to quantify the cost benefits of training the right people but very easy to count the cost of a disaster, you do not need a wire rope to fail in order to learn. So, become ISO 4309-2017 compliance.
For more information regarding the usage, supply and training on Magnetic Rope Testers, do not hesitate to contact Cranemec Group to discuss your needs.
Cranemec can offer Engineering Council approved CPD training courses. Cranemec are one of only a few entity’s in Southern Africa offering a complete package when it comes to testing your lifting equipment. Cranemec Group SA, +27 (0) 16 366 1393, +27 (0) 83 268 4857, info@cranemec.co.za, www.cranemec.co.za
The Department of Labour is increasingly encouraging industry to opt for mobile elevated work platforms (MEWPs) rather than man cages
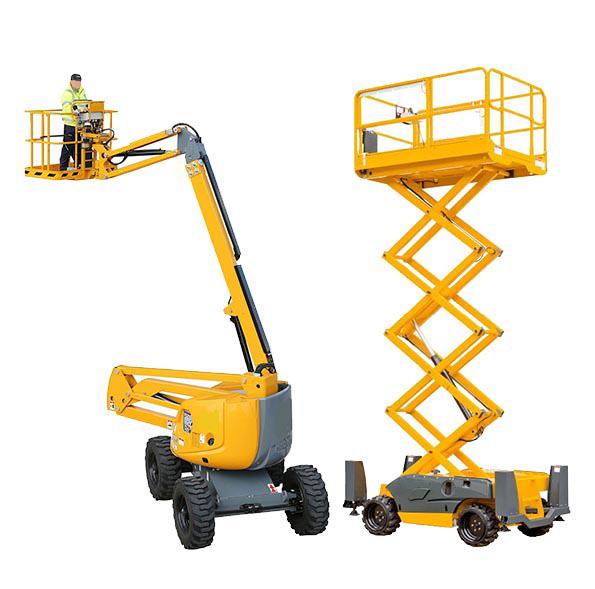
Steve Harper of Alpha Load Testing and Services spoke at the annual LEEASA/Lifting Africa conference about these aerial platforms.
With a range of applications from construction to warehousing and a host of others in between, MEWPs are considered one of the safest means to provide temporary access to work at height.
Also known as aerial work platforms they are considered extremely useful, says Harper, but are complex pieces of equipment that require operators to be well-trained.
“The applications for this product is very wide. From using it in a garden to cut trees to load testing overhead cranes or stock-taking,” he said. “It is an incredibly versatile piece of equipment.”
According to Harper, there is, however, still a tendency in South Africa to use man cages instead of MEWPS. “It is very common to use a man cage on a forklift for things like stocktaking and many other jobs, but a MEWP is, in fact, the right product for these tasks. M
an cages on forklifts should only ever be for occasional use and not be in operation as regularly as is the case.” The DoL has more recently introduced far more stringent requirements for the use of man cages that includes a letter of approval from the DoL for its use. These approvals are depending on what the job requirement is and could also include a site inspection.
12 Lifting Africa - Jan/Feb 2020 This is, however, not the case with MEWPs that are slowly starting to gain traction in the market. Available for hire
Types of MEWPs Whilst there are more than 13 categories of different MEWPS, they are usually categorised into four main groups, says Harper.
Scissor lifts Named for the crisscrossing metal supports that elongate as the platform is raised (known as known as a pantograph or scissor mechanism), this motorized vehicle with a railed platform is raised vertically and often used in hard to reach areas.
According to Harper these machines vary in size and allow workers to work at areas high above ground level without any concern for balance that they would have to exercise if they were using a ladder for example. says Harper.
They are run either on electric power or diesel. They can also be multi-powered, although not very common.
“Articulated booms application allows the operator to go up and over and under,” says Harper. “the biggest competitor for this machine is scaffolding, but you can hire this machine, do some driver familiarization, get a license for a year and have it on sight immediately. It replaces scaffolding
“They are also available as rough terrain versions and can work very well on uneven surfaces. We have three of the biggest diesel scissor lifts operating in South Africa in the Southern hemisphere,” said Harper.
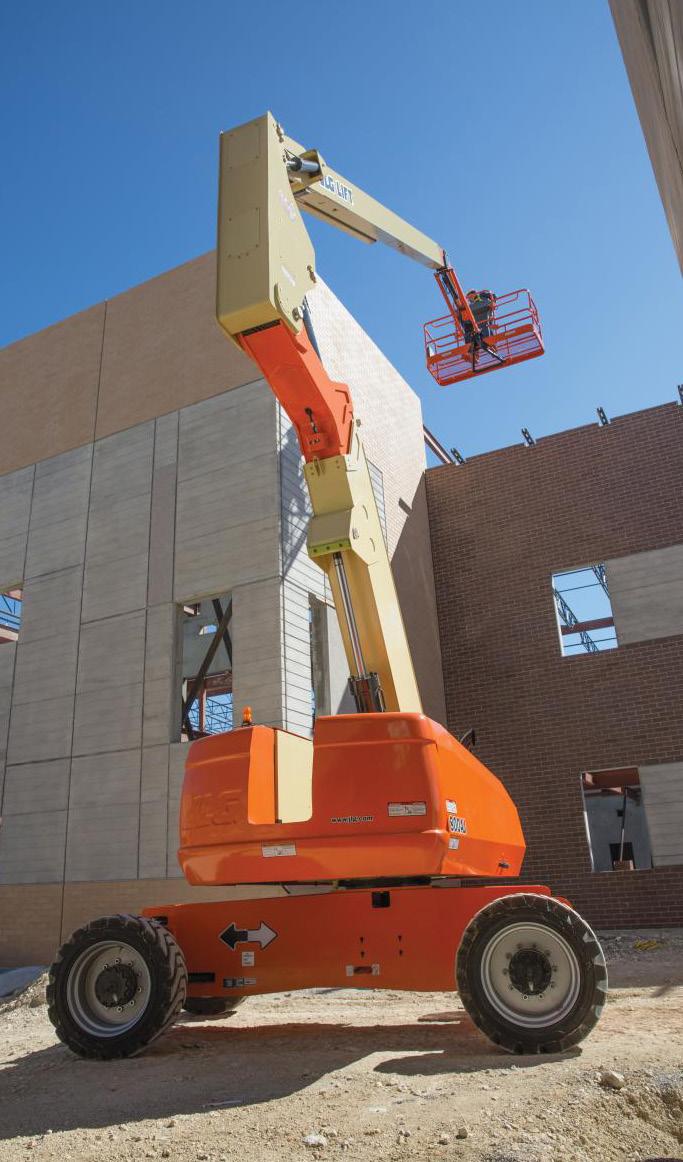
Boom lifts Also known as cherry pickers, man lifts, basket cranes or hydraladders boom lifts have a variety of uses,