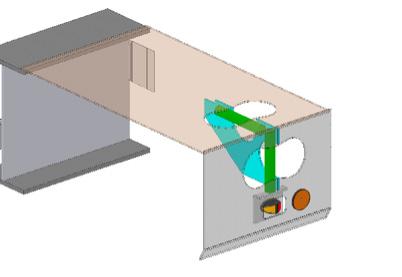
6 minute read
INDUSTRY INNOVATION
TRT manufactures innovative load connection device to increase efficiency of Modular Platform Trailers
TRT is a New Zealand manufacturer of specialist trailers for the crane and heavy haulage industries. Having sold our first trailer into Australia back in 1992 we learnt that whilst the Australian Road Transport Industry had codes and standards that covered trailer lighting and brakes, at that time it had no standard that load restraints were required to be engineered too.
Advertisement
In NZ, all vehicles over 3.5 tonne are required to have their various tie down (load restraints) points certified by a registered Transport Engineer. They are engineered to NZS 5444:2005, which covers rope rails through to the more complex restraints engineered into the deck of a low loader. For these to be rated correctly, TRT manufacture a weldment section of the trailer (see image Fig 1).
Fig 1 – Certified load restraint system This duplicates the section of the deck and coaming rail to be tested. We then take it to a test facility and have it pull tested. The structure (load restraint) must retain its structural integrity to a minimum of 1.5 times its given load rating without permanent deformation. Typical load ratings in low loaders is 10,000 kg per deck or coaming rail load restraint.
Whilst there was no load restraint standard that was a requirement to get a trailer registered back in 1992, TRT used the NZ standard 5444, for designing and engineering in the load restraint points in all trailers sold into the Australian market.
As Bruce Carden, Manufacturing Director for TRT says, “It’s all very well having a requirement to use rated chain securing the load, but if the points that some chain are secured to are not engineered to the same code as the dogs and chains, then the weak point may well be the attachment at the trailer.”
Knowing a load restraint requirement within the trailer may come one day, TRT ensured all trailers sold in Australia from those early days onwards have all been built to a code which gives the operator and company owner piece of mind.
With our ongoing focus on load security, safety and providing workable solutions for the owner/operator of trailers, TRT then developed a unique system for Crane Support Trailers. These trailers are specially designed for the payload they are intended to transport. The goal is to reduce the number of standard dogs and chains, and in most cases TRT completely eliminates these. Instead, the trailer is designed around the payload. Counterweights, jib sections, hook blocks, spreader bars, outrigger pads and the rigging box are all placed on the trailer in positions that allow the combination to weigh out correctly, making it legal for axle mass (see image Fig 2).
Fig 2 – GMK5150 Equipment Semi Trailer with specifically designed mounting system In doing this, the design takes into consideration how all these items will be secured. This might be a combination of; The use of these to secure the various items to be transported takes the decision away from the operator and ensures all items are placed in the correct position, to both weigh out legally and have everything secure. This provides for a safe vehicle on the road as well as peace of mind for the company, knowing their duty of care to others on the road hasn’t been
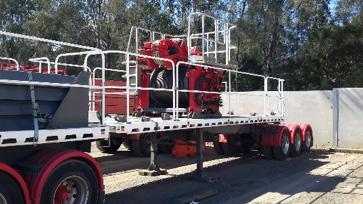
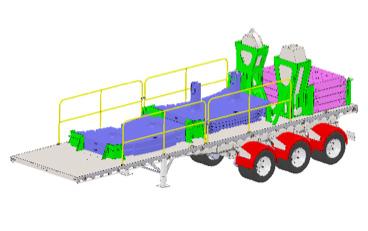
compromised.
Headboards and corner fabrications
Pinning systems
Soft sling type straps, pre-set for length
Image – B-double set up for GMK6400 showing auxiliary winch pinned in place and ground pads on the lead trailer module attachment
TRT has recently developed a unique load connection device to enable large Modular Platform Trailers to be interconnected. Typically, Platform Trailers that are used to carry loads in excess of 80 tonne take hours to “build” when the configuration needs to be altered. Going from a trailer that is 6 Rows of 8 out to 10 lines long, can take the operator up to half a day with 3 personnel to add in 4 axle lines and reconfigure the steering to have it operate safely on the road.
A long-time client threw down a challenge to TRT: “this reconfiguring cannot take any longer than 20 minutes to complete to be ready for the road”.
This drove TRT down a path to develop a joint (see Fig 3) between each modular axle group that: • Is quick to operate for the user.
Is safer with less chance of harm to the operator as there is no need to climb under the trailer or use large hammers and drifts to extract the various securing pins.
Figure 3 - TRT’s Electronic Steering System (ESS)
Modular Platform System with Quick Connect joint When the load is applied to the trailer, the top plates take all the compression, whilst the bottom point takes all the tension (shown in coloured blue and purple in Fig 3). This lower pin is hydraulically engaged/ disengaged by a double acting cylinder. No longer does the operator need to lie on his back to drive out pins manually. Instead, he or she simply turns a switch at the outside edge of the coaming rail, stands clear for safety and watches the cylinder engage itself as the lower pin (See Fig 3).
Has a stronger joint and allows for camber as more axle lines are attached. TRT’s unique Electronic Steering System (Aust. Innovation Patent Pending number 201802100) allows “the geometry to be reconfigured for the addition of axle lines at the touch of a button”. This ensures a safe and efficient trailer is put back on the road. This new concept does away with the need for the operator to climb under the trailer at each wheel group to remove tie rods, reposition them to different hole centres, which is required to ensure the trailer steers correctly. This is done via the truck producing the steering angle
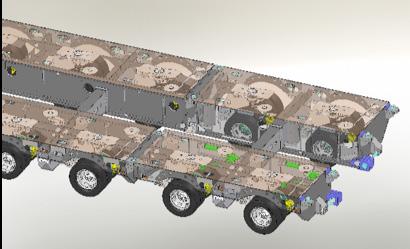
required to turn (see Fig 4).
Fig 4 – Encoder sends a signal to the electronic steering controller when the Prime Mover turns

The slew ring moves and indicates to the individual rams at each wheel group what angle they are designed to steer to. Refer to Fig 4 which shows the skid plate and slew ring set up. Figure 3 has the steer rams coloured green.
Efficiency has been the main driver for this innovation to secure various modules together. TRT has developed a much safer unique load connection device for large Modular Platform Trailers.
For more information about TRT’s Load Connection Device visit www.trt.co.nz
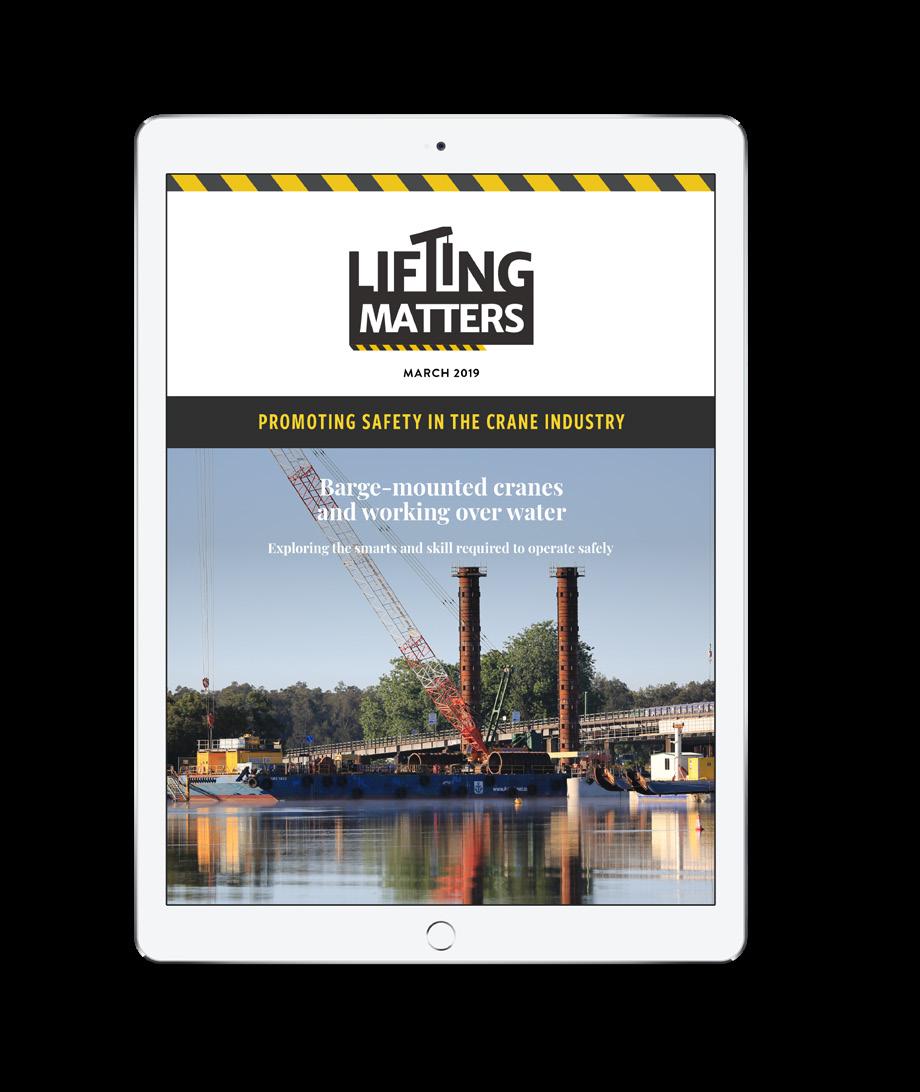
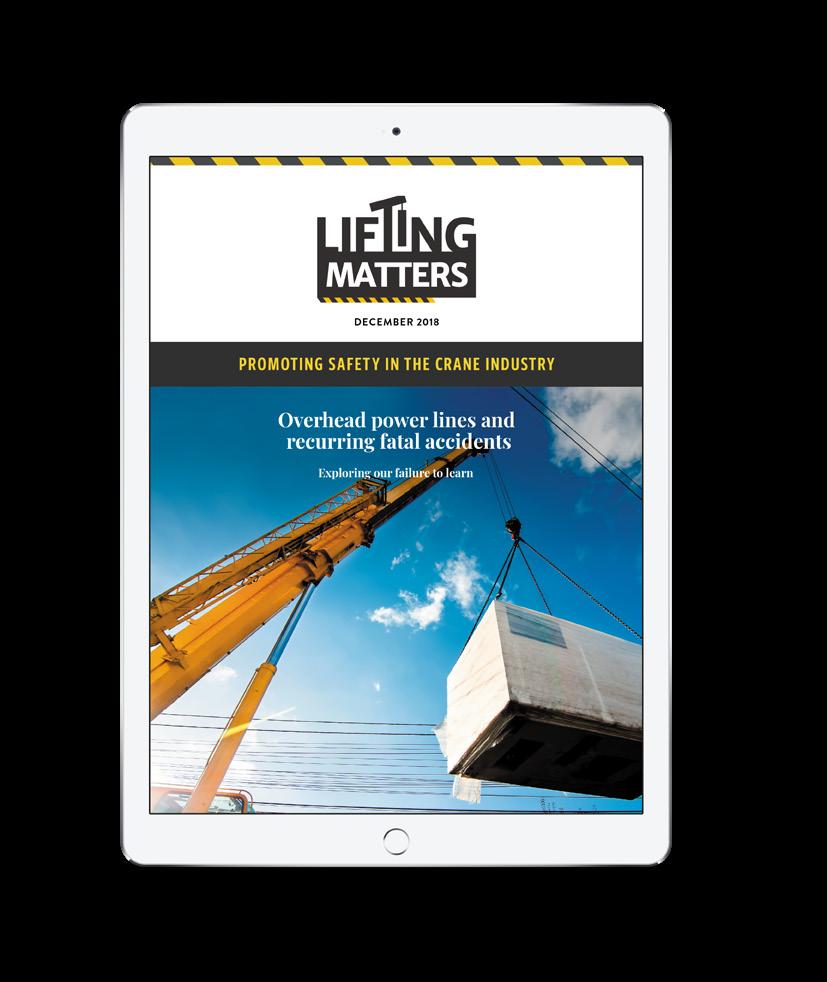
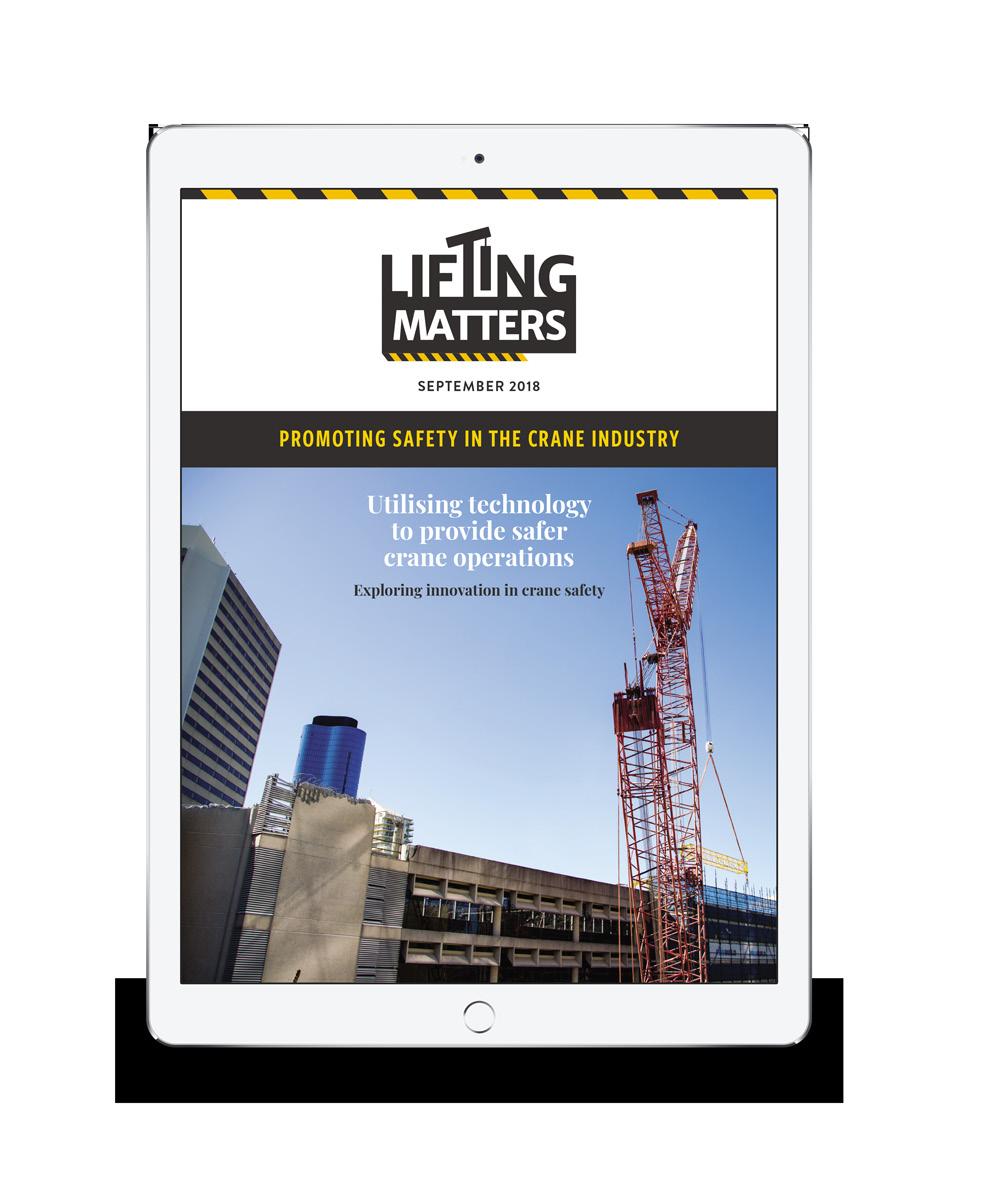
CALL FOR CONTENT


Contribute to Lifting Matters’ vision of a safer industry by submitting your ideas and articles to: liftingmatters@writestrategy.com.au

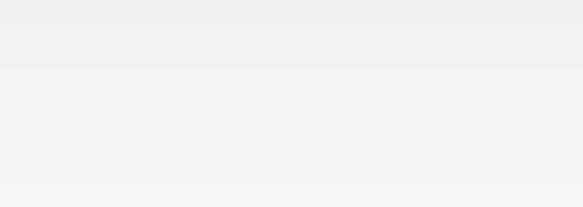
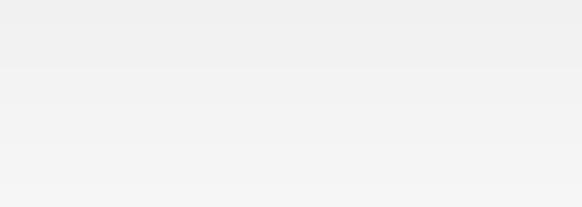




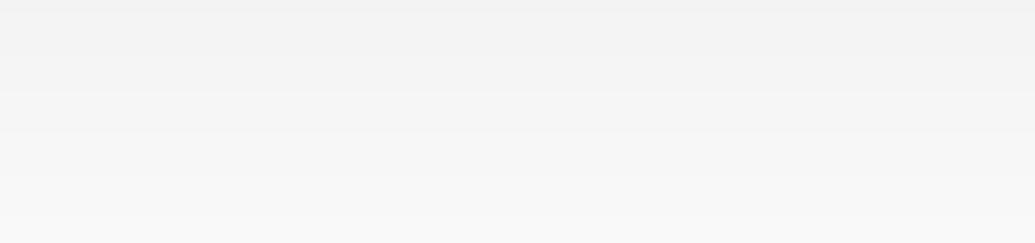




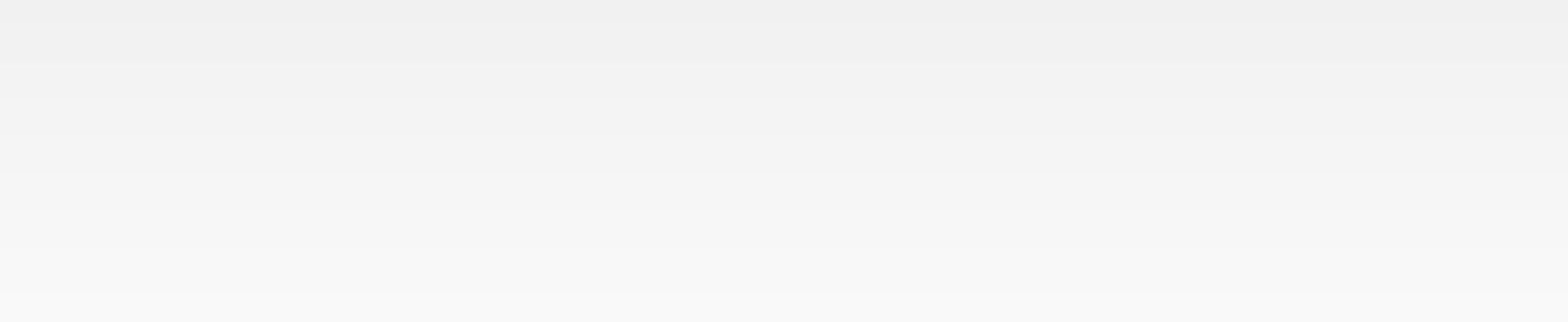

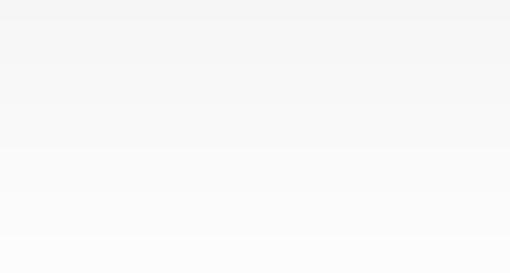
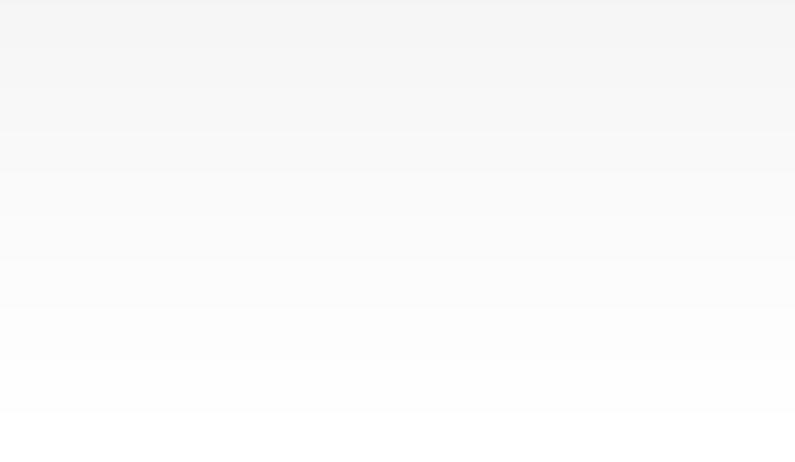
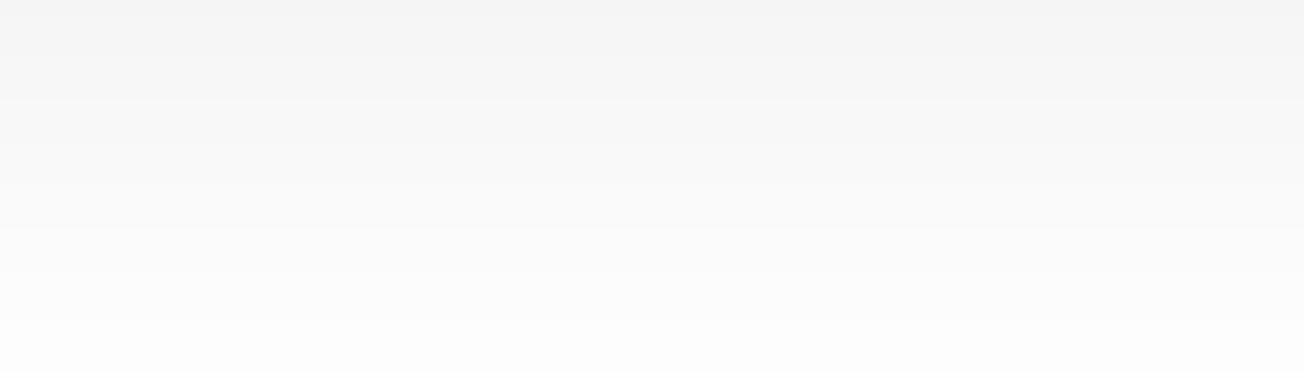