LIFTING MATTERS
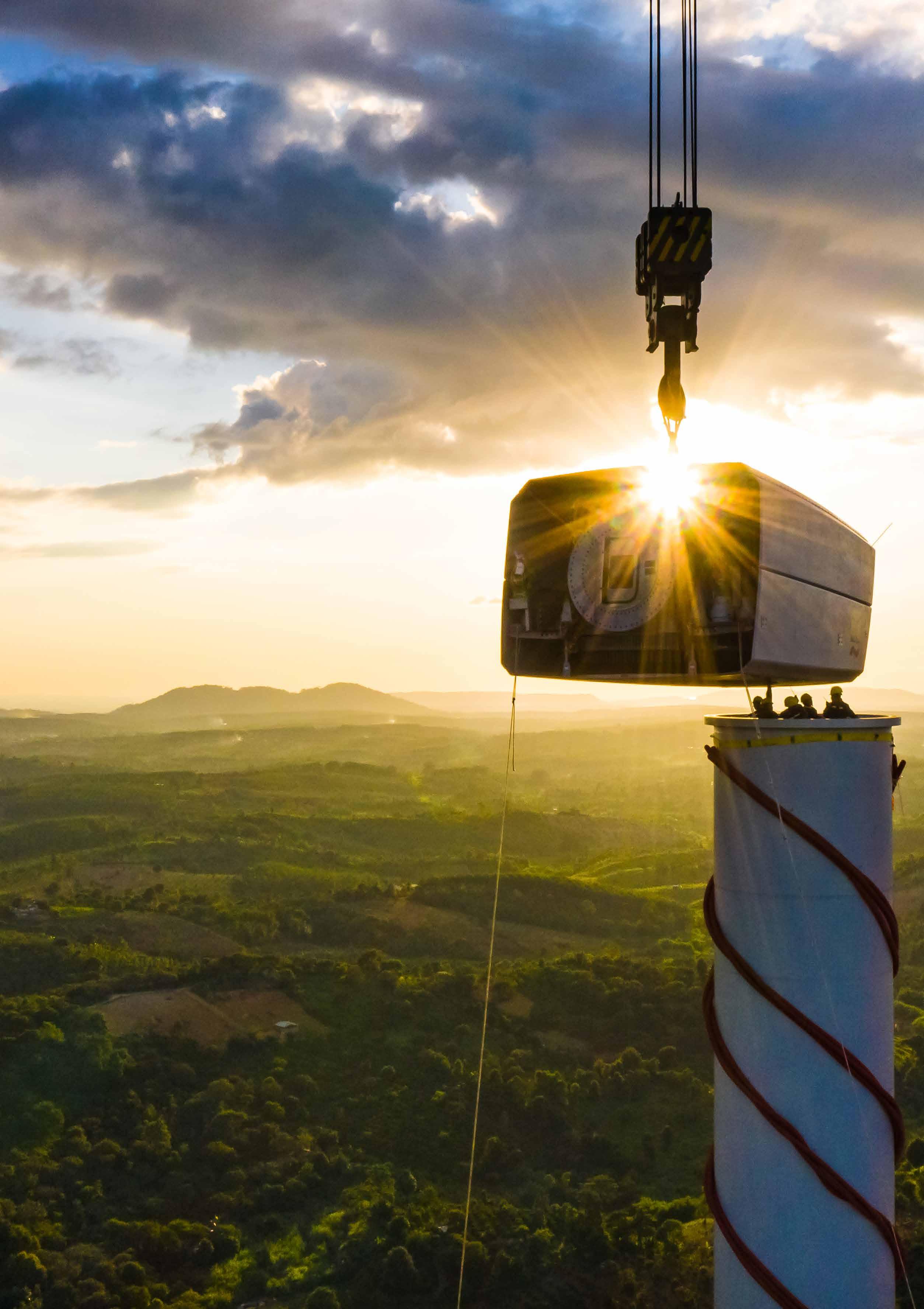
Thanks to this edition’s contributors
Thanks to this edition’s contributors
We want to hear from you.
Are you an aspiring author? Are you passionate about the safety of your workmates? Do you have an idea for improving safety or efficiency in your workplace? We want to hear from you.
Contribute to Lifting Matters’ vision of a safer industry by submitting your ideas and articles to editor@liftingmatters.com
We are seeking stories about recurring or significant incidents, any prevalent issues, ideas about safer and more efficient ways of working, important reminders, or anything else relating to safety in the industry.
You can either submit a full article (from 200 to 1000 words) or let us know what you would like to read about in future issues of Lifting Matters. If you’re from a business, we will mention you as a supporter and publish your logo at no cost.
We can’t wait to hear from you!
EDITION 22
Welcome to Edition 22 2022 of Lifting Matters.
It’s been an eventful couple of years for Australia’s renewable energy sector. Despite the country falling a spot in Ernst and Young’s (EY) latest Renewable Energy Country Attractiveness Index (RECAI), we are now seeing evidence that investment is picking up—and 2022 may mark an important turning point for clean energy development within the country with more Power Purchase Agreements (PPAs) and long overdue investment of our transmission infrastructure on the horizon.
There are currently 117 projects that are under construction (or due to start construction soon) around Australia. This is based on projects that have reached financial close and are not yet commissioned.
QLD 17 NSW 23 ACT 0 VIC 16 SA 10 NT 2 WA 8 TAS 0
Wind power remains the largest renewable energy source in Australia, generating enough energy to meet 35.9 percent of the country’s electricity demands and 9.9 percent of Australia’s overall electricity supply.
By 2030, the wind industry is planning to have 50 percent of the share of electricity generation in Australia. This is an ambitious goal that is likely to present a massive opportunity to players that are involved in the Wind Energy sector or those who are planning to be involved in the future.
In Australia, there have been more wind farm projects in 2021 than ever before. These include four mega projects with
energy systems between 180 – 228 turbines. There are 60 wind projects planned for the next 5 years that will be a total value of $33 billion. The Australian renewable energy industry powered on in 2021, generating more clean energy than ever before and adding a record amount of new capacity.
Cranes are critical to the construction of wind turbines, and the availability, efficiency and safety of cranage on these renewable energy projects will underpin the growth and success of this industry.
Read on to get more information on these innovations, plus insights into other advances making an everyday difference in the safety of our people.
If you would prefer printed glossy copies for your crane cabs, cribs, mess hall, or reception, please send your postal address and the number of copies you require to editor@liftingmatters. com. Lifting Matters is available at liftingmatters.com, or you can subscribe to receive an email copy each quarter.
Stay safe and see you next edition!
Dashelle Bailey, Editor editor@liftingmatters.com
There are 60 wind projects planned for the next 5 years that will be a total value of $33 billion.
As the projects that cranes construct continue to evolve, so must the cranes themselves. These days, the rapidly growing renewable energy sector is creating demand for a new breed of crane. At the heart of that industry is wind power. With demand for cheap, clean energy only set to rise, modern cranes are developing to meet the demand and become safer, more portable, and more adaptable than ever before.
Around the world, countries are waking up to the dangers of global warming and are putting the wheels in motion to prevent it. Australia has committed to achieving net zero emissions by 2050, in line with our Paris Climate Agreement obligations, and more recently, the new Federal Labour government has increased our 2030 goal to reduce emissions by 43% from their peak in 2005.
In support of that goal, an additional focus has been placed on reducing our reliance on fossil fuels in favour of renewable energy. Australia’s abundance of renewable energy sources, namely sun and wind, means we are perfectly positioned to become a global leader in the production of clean energy. Wind, in particular, is seeing tremendous growth, becoming the country’s cheapest and most popular source of clean energy, accounting for 35.9% of Australia’s renewable energy and 9.9% of our total energy used in 2020.
And all that growth is seeing huge demand for new wind generation projects. In 2020 alone, 10 new wind projects were signed off around the country. Currently, there are 21 additional projects in construction or soon to begin construction.
Not only are more and more wind generation farms popping up around the
country, but the turbines themselves are growing in size to capture the stronger winds that exist at greater heights. The average hub height (the distance from the ground to the middle of the rotor) has increased 66% since the 1990s to an average elevation of 100m. And this is only the beginning, with wind turbines set to get larger still as demand for cheap renewable energy continues to increase.
Crane technologies have always been shaped by the projects that require their use, with innovation and design advancement directly linked to increasingly complex project visions. Like the buildings and skyscrapers before them, the sheer scale of wind generation projects has meant cranes must adapt to enable their construction. The first hurdle to conquer? Size.
Dutch company Mammoet has been one of the first to respond to this growing need, developing cranes specifically designed for wind farms. The Wind Turbine Assembly Crane (WTA 250), for example, does away with traditional supports and is instead installed on a guardrail attached to the turbine itself. This guardrail can be moved up and down the turbine’s tower to facilitate new construction, meaning there is virtually no upper limit to the crane’s lifting height.
Unlike a building that typically only requires the use of a crane once during construction, the constant momentum of wind turbines means they require maintenance at least once a year and sometimes more as the turbine ages.
The Wind Turbine Maintenance Crane (WTM 100), also from Mammoet, is built to serve this purpose. With a reduced lifting capacity, the crane is designed to carry out maintenance, rather than construction, using a combination of hoisting eyes and claws that wrap around the tower to pull itself—and its cargo—up to the top of the turbine.
Another notable benefit of the modern crane developed for wind projects is portability. Because these cranes can clamp onto turbines for support, they are lighter and need far fewer components than traditional cranes. While a traditional crane may need 50 individual truckloads to move, a model like the WTA 250 needs as little as 9.
While a traditional crane may need 50 individual truckloads to move, a model like the WTA 250 needs as little as 9.
With demand for cheap, renewable energy tipped to increase even further, construction of wind farms is on the rise both across Australia and globally. In some ways, the future of this industry is already here, with new models of purposebuilt cranes making the construction of turbines of any size possible.
As new wind generation projects are fast-tracked in more remote
and treacherous areas, like the proposed Star of the South wind farm off the coast of Victoria, cranes will continue to innovate with safety and efficiency in mind.
With the global crane market hitting $19.3 billion in 2021 and predicted to grow 4.8% in the decade to 2031, one thing is for sure—the next decade will see tremendous transformation in the crane industry.
In some ways, the future of this industry is already here, with new models of purpose-built cranes making the construction of turbines of any size possible.Image sourced from Mammoet, the WTA system is now design-ready and can be ready to enter the market during Q2 2023.
Palfinger (PF) has redesigned its fixed boom crane range to meet the latest safety requirements of the global offshore wind industry. The new PF range aims to improve the safety and efficiency of lifting operations during regular maintenance of offshore wind turbines. The new line was launched at WindEnergy in Hamburg September 2022, with a full-size PF120-4 model displayed on the company’s stand.
The new range has been designed in accordance with the latest technical requirements of European standard EN13852-3 for light offshore cranes for lifting spare parts and equipment from the delivery craft to the turbine’s transition piece (TP) platform. Built with a modular design, the cranes have a radius/reach of three to seven metres.
Franz Schnöll, Head of Global Marine Product Management, said: “Because access to offshore wind farms is limited and every working hour must be efficiently used, we’ve made the new PF cranes highly resistant to the harsh environmental conditions. Furthermore, we reduced the maintenance effort to lower the life cycle costs for the wind park owner. The new crane range was designed based on more than 15 years of installed base experience and feedback from service teams and our clients. It is therefore well positioned for the future requirements of the global offshore wind industry.”
Palfinger says it has already received orders for more than 250 new fixed boom cranes units. With deliveries scheduled for the UK, Taiwan, USA and Japan starting immediately and running through to the first half of 2024. They will be installed on jacket and monopile bottom fixed structures and used for servicing offshore wind turbines and other equipment installed on substations.
Article sourced from: vertikal.net/en/news/ story/40493/new-palfin ger-offshore-cranes
The new PF range aims to improve the safety and efficiency of lifting operations during regular maintenance of offshore wind turbines.
21.10.2021
Offshore wind vessel Alfa Lift Liebherr HLC 150000
A 3,000-tonne crane being installed aboard the new offshore wind vessel Alfa Lift was involved in a serious incident last week that may delay the vessel’s planned commissioning date. Details are minimal, but it seems to be associated with the crane’s folding A-frame.
www.seaway7.com/vessels/seaway-alfa-lift/
Offshore wind installation specialist
Seaway 7 ordered the semi-submersible heavy lift crane vessel for installing offshore wind tower foundations and transition pieces. The crane, a Liebherr HLC 150000, can handle 3,000 tonnes at a 30 metres radius or 1,000 tonnes at 76 metres. It was built and tested at the manufacturer’s maritime plant in Rostock, Germany, then shipped to China, where China Merchants Heavy Industry is building the vessel and where the ‘incident’ took place.
The crane is unusual in that it features a foldable A-frame, which reduces the height of the crane and vessel to pass under bridges, such as the Great Belt bridge in Denmark, between the North Sea and the Baltic. The 51,000-tonne
vessel has a 148-metre long/10,000square metre smart deck, which can transport up to 10 XL monopiles or eight jackets at one time. It has accommodation on board for 100 people. Seaway 7, part of the Subway 7 group, was recently merged with OHT ASA to become ‘Seaway 7 ASA’. The company said: “We have been informed of an incident involving the folding A-frame on the main crane of Alfa Lift, currently under construction in China. No personnel have been injured, and the unplanned movement of the folding A-frame is currently being investigated. The incident is a matter between the shipyard and crane vendor, and it is too early to indicate if this will have an impact on the delivery schedule of the vessel.”
The crane is contracted to install new turbines for the Dogger Bank offshore wind farm next year, with is expected to run through 2024.
A statement from Liebherr added: “We can confirm that during the installation of an offshore crane at a shipyard in Jiangsu (China), an incident with the crane’s A-frame occurred. Investigations into the exact circumstances and causes of the incident are currently underway. We can confirm that no one was injured. A team of Liebherr engineers is on site. Our colleagues are in close contact with all persons and support the investigation.”
Since the incident, Seaway 7 said that Seaway Alfa Lift was now expected to be delivered in the second half of 2023 and, due to this delivery delay, Seaway Strashnov would be deployed on the Dogger Bank Wind Farm project in the UK for a full 2023 campaign.
Fortunately no one was injured however this incident has had a flow on effect. Many projects that were contracted based on the successful delivery of the Alfa Lift in 2022 have either being cancelled, pushed back or put on hold.
When planning for these large scale builds offshore, it’s important to factor in weather delays and breakdowns as well as developing a realistic timeline with a solid contingency plan.
When planning for these large scale builds offshore, it’s important to factor in weather delays and breakdowns as well as developing a realistic timeline with a solid contingency plan.
17.2.2021
Björkvattnet wind farm Demag CC 3800
A 650-tonne crawler crane overturned on a wind farm in Sweden last month and is now being recovered.
The incident occurred on the Björkvattnet wind farm in a remote location north-west of Sundsvall450km north of Stockholm - in central Sweden. GE Renewables is installing 33 of its 5.3 MW 5.3-158 Cypress turbines on the site for wind power company Treblade Björkvattnet –owned by Infravia Capital Partners. It was using a Demag CC 3800 owned by Austrian crane and access rental company Prangl which had been on site since last June.
The crane overturned to the rear, dropping its Superlift ballast onto the deck. The crane was left fully rigged on the evening of January 11th, and unfortunately, a bad snow storm with high winds whipped up overnight. When the snow ploughs came by the site in the morning, they spotted the crane had gone over
backwards, with the boom coming down on a larger generator. No one was hurt in the incident, although there was a minor oil and diesel leakage. The recovery of the crane was due to get underway last week. It seems that the two main casualties from the incident are the crane itself and the deadline for completion of the project, which will be delayed by around a month.
We have seen the official reports from the incident, which have failed to identify anything yet regarding the precise cause, apart from the weather. Although it seems that the out-of-service positioning/ configuration could have been a factor.
This is not the first such crane to come down in conditions like this while working on wind farms. It may well be worth operators, owners and project managers checking and familiarising themselves with the manufacturer’s out-of-service instructions and recommendations in order to avoid such disruption.
Heavy snow initially hampered the investigation and the recovery work, but we understand that it has been completed along with an environmental assessment.
GE has said that it is working closely with its client to continue to install turbines at the site as quickly and safely as possible.
It may well be worth operators, owners and project managers checking and familiarising themselves with the manufacturer's out-of-service instructions and recommendations in order to avoid such disruption.Photos courtesy of the initial accident reports
Image sourced: www.sarens.com/services/wind.htm
For years, the world has been immersed in a major paradigm shift in energy demand and consumption. In part due to geopolitical factors, which define how important energy sources will be in the immediate future, but also due to various international regulations seeking to reduce greenhouse gas emissions to achieve better living conditions for citizens worldwide.
During the COP26 in November 2021, it was clear that governments worldwide have to redouble their efforts to achieve the goals set by the Paris Agreement to reduce global warming by 1.5 degrees compared to the pre-industrial era. And at the next COP, the trend will continue in the same vein.
Australia is not an exception. During the COVID-19 pandemic, energy demand slowed down significantly, but this didn’t slow down the transition to cleaner energy sources. It’s important to raise that our region continues to rely, for the most part, on coal-fired electricity generation: up to 51% of the electricity produced across our continent comes from this source, which is the most damaging to the environment and, therefore, to the health of our citizens.
In contrast to this worrying figure, 29% of all energy produced came from renewable sources in 2021, according to the Australian Energy Statistics 2022 prepared by the Department of Climate Change, Energy, The Environment and Water. In addition, 19.1% of the energy consumed in Australia already comes from wind power.
Our region must become a world leader in this type of energy generation. Approximately 1% of all wind power installations in the world are located in our territory, with 75 wind farms already in operation. The contribution of these installations goes beyond the energy sector, as they generate employment in the areas where they are installed, both in their installation and later in their maintenance, and in the form of taxes and rents for the landlords on which they are installed.
This, of course, is also a significant boost to the construction industry. Each of these wind farms requires the
installation of foundations, the transport of the wind turbines from where they are manufactured to their final location and, once there, their hoisting. This overcomes all kinds of technological challenges, as these are infrastructures weighing hundreds of tonnes and are installed in areas that are usually difficult to access. A task, in short that requires great precision, which is why it’s important to turn to companies like Sarens, which have participated in hundreds of similar installations all over the world, and also have the capacity to advise and collaborate throughout the process and to choose the necessary machinery at all times.
As a complement to traditional wind farms, a new type of wind energy exploitation is becoming increasingly common all over the world: offshore wind power. Unlike traditional wind farms, each wind turbine is installed at sea, sometimes dozens of kilometres from the coast, to take advantage of the greater power of the wind currents produced there. Australia has not wanted to lag behind in exploiting this modality, and at the beginning of August 2022 announced the approval of the first wind farm of this type on the coast of Gippsland, in the southwest of Victoria. This project will soon be joined by projects in the Hunter Valley and Illawarra in New South Wales, in Portland, Victoria; northern Tasmania; Perth; and Bunbury in Western Australia.
Approximately 1% of all wind power installations in the world are located in our territory, with 75 wind farms already in operation. The contribution of these installations goes beyond the energy sector, as they generate employment in the areas where they are installed, both in their installation and later in their maintenance, and in the form of taxes and rents for the landlords on which they are installed.
These installations are also full of challenges. The first, and perhaps the most complicated, is connecting the entire infrastructure to the grid, which is usually located far from the coastal area. The actual transport and installation of each wind turbine also require specialised work such as that carried out by Sarens, as it is necessary to load each structure onto barges, usually semi-submersible. Each piece must then be anchored, either directly to the seabed or installed on floating structures, which are more respectful of the seabed and the natural ecosystem and allow for faster and more efficient installation and dismantling.
Regardless of the type of installation, it is necessary to carry out maintenance on each unit throughout its useful life to avoid downtime. Having the machinery and specialised personnel for this can end up being an important competitive advantage to ensure the success of any new or existing project. Sarens assure our commitment to wind energy to secure
Australia’s electricity supply in a much cleaner and more sustainable way.
It’s important to raise that Sarens owns extensive international experience in the assembly and maintenance of wind farms. The company is currently participating in some of the most critical projects in the world, such as SaintNazaire in France, Provence Grand Large or, more recently, in the lifting and transport of the foundation bases of the new offshore wind farm in Saint Brieuc, off the Brittany coast, where it has been able to transport loads of more than 1,150 tons. Those works demonstrate how important it is to have specialists who can ensure the project’s viability and maximise cost reduction and efficiency throughout the implementation phase.
The future will be full of significant challenges, but only with the commitment of all stakeholders, companies, institutions and individuals will Australia be able to meet them all successfully.
Cheaper to install.
As it is not necessary to use barges to move the wind turbines several kilometres offshore, the transport logistics are considerably cheaper. Similarly, it is not necessary to carry out marine excavation work to prepare the foundations for each wind turbine using specialised machinery.
Shorter cabling is required for operation.
It is possible to install the substation that converts the energy produced by the wind turbines to high voltage just a few metres from them, which reduces the need for long cable runs, sometimes tens of kilometres long, while at the same time reducing their impact on the land. Connection to the grid is also easier.
Low environmental impact.
Wind energy does not produce any type of waste in its generation, and wind turbines do not cause pollution in their environment so that the land on which they are installed can be exploited both for agriculture and livestock with no risks.
Easier and faster maintenance.
As they are more accessible installations, any maintenance manoeuvre, both predictive and corrective, only requires the participation of a crane and the necessary technical equipment.
Smaller wind turbines with low visual impact on the environment. Although they tend to have heights that sometimes reach 100 metres to benefit from the wind currents produced at higher altitudes, the blades and turbine module size are smaller.
Lower power generation capacity.
Due to the smaller size of its blades and the low power of the wind gusts produced on land, this modality generates less energy, with an average of approximately 2.5 MW per year.
Variable wind speeds.
As wind gusts and wind speed change direction on land, it is not always possible to maximise the use of wind turbines, although, in their installation, the optimal orientation is studied to minimise this effect.
Noise pollution.
As the blades are in motion, their aerodynamic noise can become unpleasant if exposure to this sound increases over time.
Increased power generation capacity.
Marine winds are more intense and frequent, which maximises the performance of each wind turbine, up to a capacity of more than 3.5 MW per year.
Greater wind consistency.
As no obstacles can deflect the gusts of wind (mountains, towns, etc.), the wind that reaches the wind turbines is more stable.
Less visual impact.
Wind turbines can be installed dozens of kilometres from the coast, so they can be larger and have less visual impact than those installed on land.
Low environmental impact.
Especially in the case of the new floating type (FLOW), in which damage to the seabed is reduced depending on the type of anchoring used.
Easier and faster dismantling.
In the case of floating wind farms, the dismantling time is exponentially reduced while minimising the impact on the seabed once unanchored. All of this also reduces costs.
More expensive installation.
Unlike onshore wind farms, this type of installation requires construction infrastructure in a nearby port, specialised dredging machinery and barges to move the wind turbines on multiple trips.
More expensive maintenance.
Benefiting from stronger and more intense winds, rotor maintenance is higher and more frequent. Likewise, the continued impact of waves increases the wear and tear on the poles, which increases the need for regular servicing of the installations.
Longer cable runs.
As the entire installation is carried out kilometres from the coast, kilometres of cable must be laid on the seabed, a more complicated, delicate and expensive task.
When the world is turning to renewable energy as a more environmentally friendly energy source, it is important to remember that wind energy comes from an inexhaustible source, and its generation does not produce any waste, making it one of the cleanest sources of energy.
Although the first steps are already being taken around the world to extend this type of energy, there is still a long way to go. The future, in this sense, will be bright for wind energy if the kilometres of coastline present in Australia are used to extend the offshore mode and if the onshore projects already in operation are consolidated and properly maintained.
From Sarens, we offer all our support and international experience to both public institutions and construction companies involved in developing wind energy facilities so that the future of this energy is bright and contributes to reducing the impact of the current energy crisis and dependence on unsustainable sources.
it is important to remember that wind energy comes from an inexhaustible source, and its generation does not produce any waste, making it one of the cleanest sources of energy.
Wind farming is part of the Australian Government’s renewable energy plan to reduce the country’s dependence on fossil fuels. Wind energy is one of Australia’s primary renewable energy sources, generating enough electricity to meet 7.1 per cent of the nation’s total electricity demand .
Cranes are crucial to renewable energy targets, as the weight of current turbine designs require large mobile cranes. As well as the suitability of crane size, serious consideration must also be given to wind speeds and location when planning the lift.
Wind farms are typically erected on hilltops and sea cliffs, which can be difficult to access and pose challenges by wind speeds and ground conditions. The locations are selected to harness wind power, which is excellent for meeting energy objectives but is not without issues regarding lifting objectives.
1 2022. ARENA: Australian Government Renewable Energy Agency.
Mobile crane operations are subject to excessive wind forces that pose risks during lifting, erection, servicing, and dismantling of wind turbines as parts to be lifted are usually heavy and have a large surface area. The mass and shape of the load plays a major role in how much influence the wind will have on the lifting operation.
Calculating the wind effect on lifting the wind turbine parts:
⊲ Suppose the wind surface area (multiplying the load surface area by the drag coefficient) of the load is less than the total allowable wind surface area (equals to load weight multiplied by the wind surface area to load ratio specified by the crane manufacturer). In that case, no further calculations need to be made.
⊲ (More likely) if the wind surface area of a load is greater than the total allowable wind surface area, further calculations need to be made to determine the permissible wind speed.
The Permissible Wind Speed can be determined by calculating allowable wind surface area, dynamic wind pressure, wind surface area, wind speed and air density. This resultant permissible wind speed should be compared against the maximum operable wind speed nominated by the manufacturer for the required crane configuration. The manufacturer’s nominated maximum wind speed limit should not be exceeded.
Before starting lift operations, the crane operator should determine the expected maximum wind speed on site (for example, by checking a trusted weather website (http://www.bom.gov. au/vic/observations/melbourne.shtml), if the forecasted maximum wind speed exceeds the permissible wind speed for the lift, the load should not be lifted, and the crane may not be able to be erected. Wind speed on site should be measured and compared with the operator manual’s load chart wind speed or the calculated permissible wind speed to see if it’s safe to operate the crane under the site condition. (It should be noted that the wind speed can vary between ground level and the boom tip or load height.
Calculating wind load impact on crane operation is complex, and for exceptional cases, the lift designer should seek the crane manufacturer’s instruction on wind load calculation as the crane manufacturers have better knowledge of the static/dynamic stability and the specific crane’s limits.
Using anemometers attached on a boom tip can be an excellent way to assess the conditions.)
Calculating wind load impact on crane operation is complex, and for exceptional cases, the lift designer should seek the crane manufacturer’s instruction on wind load calculation as the crane manufacturers have better knowledge of the static/dynamic stability and the specific crane’s limits.
Other than the calculations, when it comes to wind effect, another area worth noting is freely suspended loads (especially loads with large wind surface areas like wind turbines), as they can swing or rotate in the direction of the wind during the lift. This swing or rotation must be managed or controlled to reduce the lateral load against the crane or the boom.
Riggers/doggers on-site usually use tag lines to control/manage the swing/rotating action caused by the wind. A tagline is a rope attached to a load during a lifting operation to allow the riggers/doggers to control the swinging and/or rotation of a suspended load. They should not be used to pull a load out of its natural suspended line, inducing in-haul or out-haul of the load lines or hold a load against wind forces trying to push it out of line.
Working with wind turbines also requires working at heights, and as always, planning is key to understanding how the risk of falls will be controlled and what to do if a fall does occur. Planning should include:
⊲ Minimising the time and number of persons working at heights ⊲ Ensuring the person/s working at heights are height safety trained ⊲ Using anchorages that are rated to AS/NZS1891.4 or equivalent
⊲ Ensuring compliant full-body harnesses (with trauma relief straps) are used and fitted correctly
⊲ Preventing falls with short or adjustable lanyards and minimising the distance to fall with a retractable lanyard ⊲ Using an energy absorber that will limit shock loads to <6kN ⊲ Having a rescue plan
Transport of odd-shaped and overdimensional components is common with the construction of wind farms. Securing the load in a way that both holds the load in position and doesn’t damage the components requires careful planning and route assessment. The load
0.2W
0.5W
Half the weight of the load sideways (cornering) 0.8W 80% of the weight of the load forwards (braking)
(W = weight of the load)
• 0.8 g deceleration in a forward direction
• 0.5 g deceleration in a rearward direction
• 0.5 g acceleration in a lateral direction
If relying on friction to withstand the force in other directions 0.5W Half the weight of the load rearwards (accelerating, braking in reverse)
0.5W
Half the weight of the load sideways (cornering)
Graphic used with permission from the National Transport Commission
• 0.2 g acceleration in a vertical direction if relying on friction to withstand forces in other directions. g means gravitational acceleration or 9.81 m/s2
restraint guide as outlined in the image extracted specifies the transverse, lateral and vertical load restraint requirements.
Once on site, the access roads and construction areas need sufficient area and ground bearing capacity to manoeuvre and unload. Recent weather conditions in South East QLD, Australia serve as a reminder that the suitability
of an access road or the hardstand needs to continue to be monitored as excessive rain can cause deterioration.
Specialised rigging is used nowadays to position the various components, removing the need to select correct slings and sling arrangements. The lifting sequence needs to be followed according to the lift procedure.
Comprehensive planning is vital to ensure the safe lifting of turbines to protect people, equipment, and the environment.
The CICA Guidance Note: Crane Stability and Ground Pressure and the ICSA: Mobile Crane Ground Preparation for Wind Farm Construction are useful reference documents when considering ground conditions for wind turbine lift planning. Both documents are available from the CICA website.
Concerning ground conditions, the ICSA (International Crane Stakeholder Assembly) Guidance Note focuses on both:
⊲ Access roads - ground bearing pressure for crane weight on the road - route path (e.g., swept path analysis to assist the determination of dimensional and clearance requirements for the crane path).
⊲ Crane working areas - suggestions on hardstand constructionground bearing pressure for different lifting configurations - ground level requirements for crane working areas
Ground condition inspection should provide permissible ground pressure, and during the planning stage, a geotechnical engineer should conduct this inspection. This inspection should assess the bearing capacity of the ground, including surface conditions, as well as the layers of the ground underneath the surface that could influence ground bearing capacity.
Any ground, particularly coastal ground, can have weak layers below the surface, and these underlying layers of weak or soft ground can possibly collapse. The inspection should also outline the estimated settlement due to the load and whether the settlement would cause any instability of the crane during the lift.
If the ground is found to be not suitable, additional measures must be taken before proceeding with the task. These may include, but are not limited to:
⊲ Design measures to reduce imposed loads, i.e. re-sizing the crane mat used, repositioning the crane, reducing task loads (e.g. splitting of loads), and re-selecting the crane.
⊲ Design measures to ensure ground suitability, i.e. soil stabilisation, grouting, and dynamic compaction.
The Federal Labor Government has updated Australia’s emissions reduction obligations under the Paris Agreement to a 43% emissions reduction by 2030, based on 2005 levels, so the renewable energy transition will rely on cranes for many years. Comprehensive planning is vital to ensure the safe lifting of turbines to protect people, equipment, and the environment.
Note: Documents, guides and information provided may vary in your country.
NAME: Ben Gerkin
EMPLOYER: Industrial Training International
NUMBER OF YEARS IN THE INDUSTRY: 20
I began working in the lifting and hoisting industry as a truck driver hauling counterweights for mobile cranes. I worked my way up and began my career operating three years later. After a 10-year stint as an operator, I was offered a job as a salesman for a crane and rigging company in Shreveport, Louisiana and my family and I relocated to the south. I was fortunate to receive excellent training on the company’s equipment, and I quickly learned how to provide lifting solutions to clients and customers.
In 2012 I worked as a district manager for a crane company from Louisiana that added operations in Pennsylvania and eventually worked myself into a position as a lifting and hoisting consultant for a major oil and gas company. In that role, I was able to audit and provide training to numerous contractors who were performing lifting and hoisting operations in North and South America. It was in this role that I was introduced to my current employer, ITI. I began work as a crane and rigging instructor for ITI in the summer of 2021.
Without question, the most common issue I have seen in this situation is the operator and the riggers not having the proper specific rigging to perform the job safely and successfully. This is not always due to the operators not planning the lift properly, it is typically due to others involved in the lift who may be less informed about what the scope of work will be. These issues tend to happen on the front end of the work process, and they are more prevalent to happen when there are new crane contractors hired to perform the work. These kinds of mishaps will create hazards that, at best, lead to unnecessary downtime in the field with the cranes and personnel.
My best piece of advice would be to check the wind and weather reports and be sure to plan the work around these items. Never exceed wind speed allowances for the
WHAT IS THE MOST COMMON ACTION OR BEHAVIOUR YOU WITNESS IN THE FIELD WHEN OPERATORS DON’T PLAN FOR LIFTS, OR MOVEMENT OF OVERSIZE WIND TURBINE PARTS, APPROPRIATELY? HOW DO YOU THINK WE CAN FIX IT?
HAVE YOU ANY THOUGHTS OR IDEAS ON AN INNOVATION OR PROCESS THAT MAY HELP TO PREVENT OR ALERT WORKERS WHEN LIFTS ON WIND FARMS ARE POTENTIALLY UNSAFE?Image of Crane Operator Training from ITI website
The most common issue I have seen in this situation is the operator and the riggers not having the proper specific rigging to perform the job safely and successfully.
crane and if there is lightning in the area, always follow the manufacturer guidelines to ensure the safety of the equipment and personnel in the area.
Wind is typically the main hindrance to proper crane operation, and since these job sites have been selected due to their high exposure to wind and the loads to be lifted have very large sail areas, the necessary deductions in maximum permissible wind speeds must be calculated. There are resources available to personnel to help aid them in performing these calculations, and proper training can be vital to ensuring these are performed for the equipment.
Lightning can also be a critical issue. There are various lightning detection apps operators have available to them, and they should take advantage of their availability. It is necessary that crane owners, site supervisors and lift directors have strong policies and procedures to manage these known hazards that can arise quickly and without warning on wind farm locations during lifting activities.
In my current role, I am exposed to many crane operators and riggers working in this industry. A future challenge that I’ve seen which will affect the crane and rigging industry is the need to hire qualified employees. The best way to fill this need is to expose these new employees to proper training in order to promote their competency. Once they have been exposed to this training, it is essential to get them working in their role quickly and with proper supervision.
WHAT
DO YOU HAVE ANY SUGGESTIONS FOR MEASURES OR DEVELOPMENTS YOU WOULD LIKE TO SEE IN THE WIND INDUSTRY AND CRANES, ESPECIALLY IN REGARD TO STANDARD PROTOCOLS AND TRAINING, THAT WOULD IMPROVE INDUSTRY STANDARDS AND SAFETY?
In recent years, there have been massive advances in the capability to train
My best piece of advice would be to check the wind and weather reports and be sure to plan the work around these items
employees on operating equipment that have no physical consequences. Virtual Reality (VR) training has become available to trainees with minimal cost to employers. Utilising this type of training can be valuable to qualifying operators with no real-world risk. This immensely benefits employers, employees, and primary contractors, as employee competency can be tested on various machine types and environments. Also, these VR machines can be set to expose the operators to specific conditions they may encounter while working on different job sites, which allows employers to assess the operator’s reactions to the different challenges they encounter. These assessments can also be very helpful in verifying the operator’s level of competency.
An incredible push towards clean, renewable energy is occurring in the global market right now. With the geography of Australia and the need for more sustainable energy sources, I believe the wind industry will be extremely busy for Australia in the next 5 to 10 years. The need for larger and more capable cranes and unique and viable rigging solutions will be ever more necessary to accommodate these demands. Along with these demands, the greatest challenge
facing the industry is the need for qualified and competent operators to be available to perform these functions.
I believe the future of this industry is very bright. Business leaders who have the foresight to ensure the qualifications of their personnel will be the companies that rise above and succeed in the current environment. I believe a potential labour shortage is forthcoming and qualified personnel will be in short supply. As an industry, we must realise this and address it.
NAME: Rusty Rhodes
EMPLOYER: Contractor to Smith Cranes
NUMBER OF YEARS IN THE INDUSTRY: 20+
ROLE: Technical Support
GIVE US A SUMMARY OF YOUR PROFESSIONAL JOURNEY SO FAR… WHAT IS YOUR CURRENT ROLE AND HOW DID COME TO BE IN THIS ROLE? WHAT ARE YOUR CURRENT SAFETY RESPONSIBILITIES AND ACCOUNTABILITIES?
I’ve been in the crane and construction industry for over 20 years. Growing up on a rural farm in New Zealand made me who I am today. From an early age I learned how to get my hands dirty and work hard, from shearing sheep, to driving tractors and trucks, to hay making or cropping. As soon as I could open the gate to the farm and wide world, it was off to work.
I started out doing my apprenticeship in Wanganui as a welder and specialised in welding and heavy fabrication. I then crossed the ocean to Australia where I worked in Western Australia for 8 years in the mining industry. I worked on various projects that specialised in a variety of metals (such as gold, nickel, copper and iron ore). I was looking after mechanical and structural builds and upgrades before returning to New Zealand to work with cranes and structural steel in Auckland.
I started working for Smith Cranes and Construction after the earthquakes in 2011, helping with the decommissioned Clarendon towers and QEII buildings. After that I helped with multiple projects, including the Mill Creek Wind Farm, the Waterview Tunnel construction, New Zealand refinery project and the Pūhoi bridge lifts. While working with Smiths, I have developed my knowledge and understanding of cranes and their capability.
I am working at Ohakea building air hangers as the Site Manager, and am currently getting ready to head back to Turitea Wind Farm to complete South 27 turbines at the end of this year.
What I’m seeing is that working in the crane industry is no longer recognised as a specialist trained job. There is no longer a clear pathway for the younger generation to be attracted to work in the industry. We need to promote the opportunities available, working your way up from dogman to rigger to crane operator.
I am not a safety professional, I am a practical worker on the ground. I do try to champion safety in all that I do. My motto: I wouldn’t ask anyone to undertake a task that I wouldn’t do.
In terms of safety, it’s more about getting the crew you work with to accept and respect the policies and procedures that are in place. Try to incorporate those into your daily tasks and understand that health and safety is part of everything we do.
What makes me proud is when I get a crew and we create an atmosphere of helping each other. This culture allows them to be themselves as they improve their own skills and understanding. Teamwork and collaboration will result in a safer working environment and the right attitude towards safety and policies.
We need to promote the opportunities available, working your way up from dogman to rigger to crane operator.
First
PLEASE PROVIDE A
OVERVIEW OF THE TURITEA WIND FARM PROJECT. WHAT DID IT INVOLVE? WHAT WAS YOUR ROLE? WHAT WERE THE KEY OUTCOMES OR ACHIEVEMENTS? WHAT WAS THE AWARD THAT THE PROJECT WON?
Working on a wind farm has been challenging but rewarding.
We faced many challenges such as a tough environment to deliver items to and install, and limited skilled workers available due to travel restrictions with Covid.
My role for this project was Crane Supervisor. We started the project with one main crane then added another one to hit the tight timeline. Having two cranes on the job meant we had to ensure crane movements were safe and efficient to avoid any incidents.
We also had to plan the lifts during optimal weather windows, and monitor and test all the equipment so we didn’t have any break downs or lifting delays.
The biggest achievement for me was being able to withstand the continuous pressure and not let it affect the guys on the ground. We had to keep pushing, day after day and keep improving our techniques and learnings. I strive to be the best role model to lead and build from the front. I tried to keep positive and deliver a quality product to the client in the Smith name.
My motto:
I wouldn’t ask anyone to undertake a task that I wouldn’t do.lift with Smith Cranes new LTR11200, NZ’s largest crane at Kopaki near Te Kuiti. Rusty and the team secured the job and mobilised the crane.
Workplace Health and Safety Queensland (WHSQ) has recently identified several issues around the lifting of loads over workers in the wind farm construction sector. WHSQ is concerned about the use of mobile cranes to lift tower sections on wind turbines while riggers are standing under the load. The lifting of loads over people creates exposure to serious injury or death and should only be done when it’s safe to do so, and other systems of work that eliminate the need for workers to be situated under suspended loads are not reasonably practicable to implement.
Section 219 of the Work Health & Safety Regulation in relation to suspending loads over persons states:
(1) This section applies in relation to plant that is used to lift or suspend persons or things.
(2) The person with management or control of plant at a workplace must ensure, so far as is reasonably practicable, that the plant used is specifically designed to lift or suspend the load.
(3) If it is not reasonably practicable to use plant that is specifically designed to lift or suspend the load, the person must ensure that—
(a) the plant does not cause a greater risk to health and safety than if specifically designed plant were used; and (b) if the plant is lifting or suspending persons, the use of the plant complies with section 220.
(4) The person must ensure that the lifting and suspending is carried out—
(a) with lifting attachments that are suitable for the load being lifted or suspended; and (b) within the safe working limits of the plant.
(5) The person must ensure, so far as is reasonably practicable, that no loads are suspended or travel over a person unless the plant is specifically designed for that purpose.
(6) The person must ensure, so far as is reasonably practicable, that loads are lifted or suspended in a way that ensures that the load remains under control during the activity.
(7) The person must ensure, so far as is reasonably practicable, that no load is lifted simultaneously by more than 1 piece of plant unless each piece of plant used to lift the load is specifically designed to lift a load.
When it is not reasonably practicable to perform a lifting operation at wind farm construction sites other than for a worker to be positioned under a suspended load, the following matters apply:
⊲ Plan the lift:
• Select the right crane for the job (more than adequate capacity for the working radius, sufficient boom length etc.)
• Ensure lifted loads are well within the working load limit of the selected crane at identified operating radii, develop procedures for multiple crane lifts
• Ensure any process involving work under a suspended load is
only carried out where all other options are exhausted, and workers are positioned under the load at the last possible moment (for joining of tower sections where the tower section is close to its final position a short distance above the existing tower. Workers must remain in a safe location, for example, underneath a tower access platform, until it is safe to be positioned under the load).
• A system must be in place to ensure worker’s safety in case of a failure (load is positioned 100mm over a structure that, should the load fail, it would come to rest on the structure and not place the worker at risk).
⊲ Develop effective emergency procedures – consideration should be given to the location of the closest emergency services (including consultation with the nearest branch prior to work commencing to ensure an effective response), the possible need for an on-site rescue team and trained medical staff
(paramedics), method of the rescue of workers (particularly workers at height), the method of communication given the work location (UHF vs VHF radios), the ability of emergency rescue teams to access the location;
⊲ Ensure all required documentation is prepared before starting work (WHS management plan, safe work method statements, plant inspection and maintenance documentation etc.)
⊲ Use appropriately trained and qualified workers - training and experience in the task, high-risk work licences, competency (including where multiple crane lifting operations are being performed)
⊲ Lifting equipment must be in good condition and maintained (consider the ability of lifting equipment to maintain security of the load in case of a failure)
⊲ Cranes should be in good condition and maintained in accordance with the manufacturer’s instructions
The lifting of loads over people creates exposure to serious injury or death and should only be done when it’s safe to do so
If the lift is going to take a long time, it’s important to check the forecast to ensure the wind does not pick up and exceed the maximum wind speed during the lift.
⊲ Use effective communication between workers involved in the task (crane operator and riggers) - consideration should also be given to the communication method given the work location (type of radio)
⊲ Check that weather conditions are adequate for the task and monitor conditions to ensure that a change in weather does not adversely affect the lifting operations. This includes ensuring the maximum wind speed for the lift is not exceeded (including wind gusts) and ensuring good visibility can be maintained (during rain or fog). Also, anemometers on all cranes in this sector are important so the crane operator can ensure the maximum wind speed is not exceeded. If the lift is going to take a long time, it’s important to check the forecast to ensure the wind does not pick up and exceed the maximum wind speed during the lift.
⊲ Crane stability – set up the crane in accordance with the manufacturer’s instructions, and ensure adequate ground conditions (a crane operating pad certified for the actual working pressures of the crane outriggers/tracks for the loads being lifted, including where any changes due to weather could affect the integrity of a certified crane operating pad), adequate
lifting capacity of the crane at identified working radii, level ground due to the typically high centre of gravity of loads lifted for wind turbine construction
⊲ Conduct a prestart assessment of the work area and conditions, including consultation with the workgroup in relation to the task
⊲ Only workers involved in the activity should be allowed in the lift zone
⊲ Ensure adequate controls for falling objects - for example, tool and equipment lanyards and clearly identified exclusion zones
⊲ Always ensure safety latch on crane hooks and lifting slings are used and are in good condition.