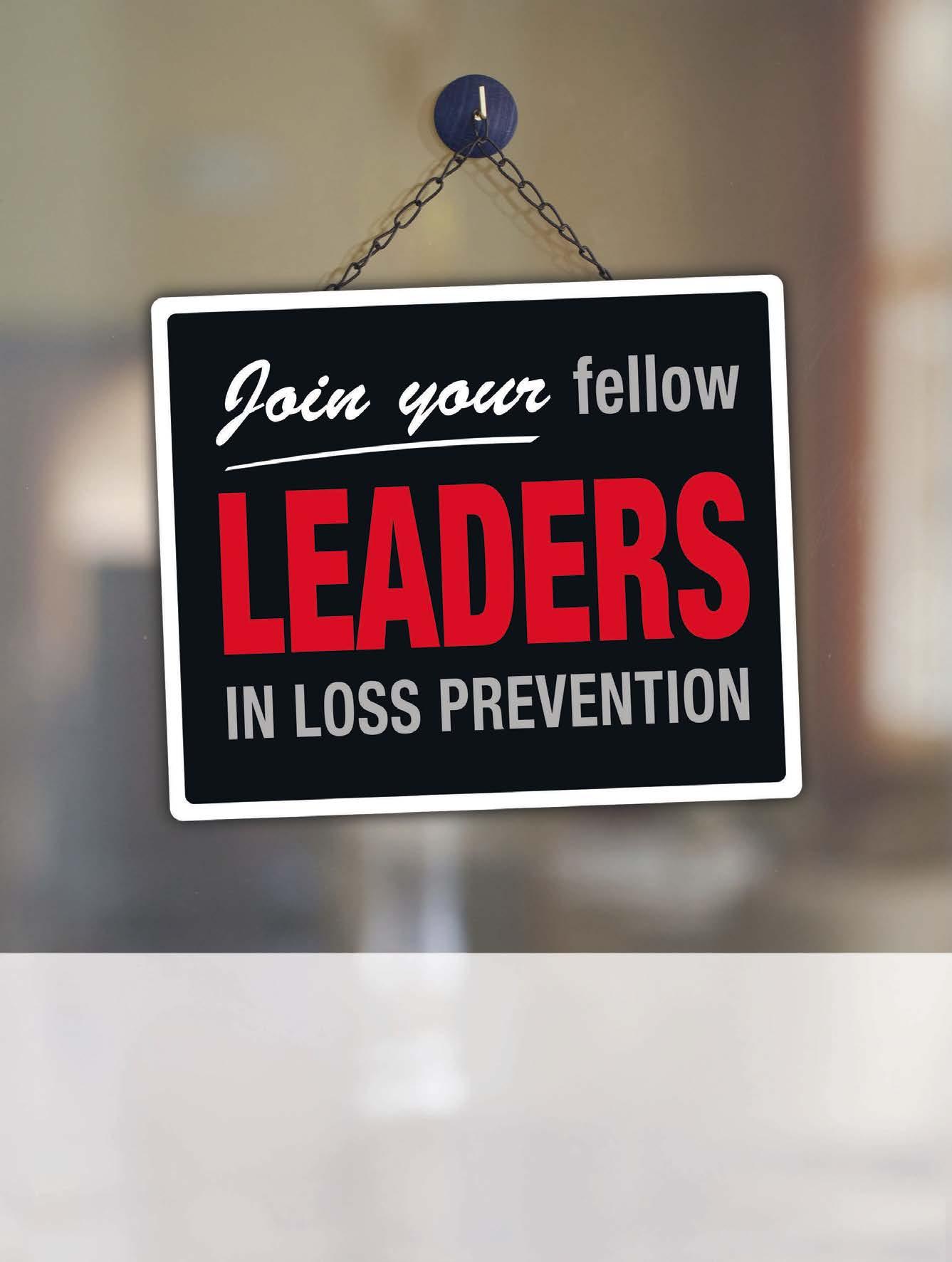
23 minute read
DIGITAL DIALOGUE
Something Given, Something Earned, Something Lost
Respect is a word that carries powerful messages. It is something that we look for and expect from others. It is something that is both given and received. Depending on our frame of reference, we may see this as something that is established over time. Respect can be viewed as something that has to be earned. It is also something that can be lost.
As professionals there are many different ways that respect can become part of our discussions. There is the respect that we share with our coworkers and counterparts. There is the respect that we share with our supervisors and subordinates. There is the respect that we share with our business partners and solution providers. There is the respect that we have for our companies, our departments, and all of the many resources that help us to perform our jobs. But because respect has so many different ways that it can be applied in our lives, occasionally lines are crossed, messages are blurred, and meanings are lost.
For example, we’ve all heard the introduction “with all due respect” as a prelude to a conversation. Most often it is a sincere and reverent means to address a difficult or delicate subject or discussion. But occasionally we will still come across those that will attempt to hide behind “with all due respect” in a poorly veiled attempt to mask the true implication: “With little or no respect whatsoever, I’m going to share with you this message or insult.” Most of the time it’s easy to distinguish one from the other—often due to the character of the specific individual using the words—but as a result, there are other circumstances when we are left questioning the true motive.
Another important distinction may occur between an individual and a job or role. For example, we may respect a particular position, but not hold much respect for a particular individual holding that position due to a specific or general flaw in their attitude or character.
However, a particularly difficult differentiation of respect for many loss prevention professionals can occur when attempting to separate individuals’ actions from the individuals themselves. Many learn to separate one from the next, especially with time and experience. But for others, the distinction is much more challenging.
By Jacque Brittain, LPC
Brittain is editorial director, digital, for LP Magazine. Formerly a director of learning design and certification, Brittain managed the development of the LPC and LPQ certification programs in collaboration with the Loss Prevention Foundation. Prior to that he was vice president of operations for the industry’s largest executive search and consulting firm. In his thirty-plus years in the LP industry, he has helped build and enhance many learning initiatives and provided career counseling for thousands of industry professionals. Brittain can be reached at jacb@lpportal.com or by phone at 704-246-3143.
The Dilemma
For those of us who deal with theft and crime on a consistent basis, we regularly experience the bad decisions and poor behavior of the criminal element. We are often in close contact with individuals who have shameless attitudes and corrupt intentions. We occasionally see those who will do whatever it takes to get what they want, even if it means hurting or even killing others in the process.
We see the outcomes that result from theft, fraud, and other criminal behavior, and it leaves an indelible impression on us. We despise these acts because of the consequences. We see the stupidity of the actions. We deal with the aftermath and emotional scars that follow a robbery or assault. We’ve seen how all of this can destroy lives and ruin companies.
We’ve seen people when they’re at their worst. They lie and yell and cry and fight and insult—whatever they think it might take to get out of the situation that they’ve put themselves in, and all of this is most often at our expense.
This has the potential to build heavy calluses. When we are dealing with theft, we see a thief. When we’re in the moment, it remains our priority. Our concern is taking appropriate action based on the incident at hand. We have a professional responsibility to deal with the situation and resolve the matter based on our company policies and practices. We follow the necessary guidelines and move toward resolution.
However, we must be especially careful when these behaviors threaten to stoke animosity. This can lead to bad judgment and poor decisions on our part and can ultimately bring about regretful outcomes.
Acknowledging the Separation
What we always have to keep in mind is the difference between the act and the individual. We have to keep in perspective that, in most cases, we are seeing individuals at their
As a member of The Loss Prevention Foundation, you join an association founded by and for loss prevention professionals. With access to an elite network of fellow industry professionals, development tools tailored specifically to our industry to help you advance your career and other great member benefits such as exclusive access to elite savings and discounts on thousands of products and services nationwide. Your membership is not only a demonstration of industry leadership; it’s a commitment to the profession and to your own professional development. Elevating the Industry, One Leader at a Time. For more information, visit losspreventionfoundation.org or call (866)433-5545
continued from page 52 very worst. Most aren’t criminal masterminds; they’re simply people who have made extremely poor decisions. That’s not to excuse what they’ve done or minimize the event, but it’s an important distinction that can help us manage and navigate the situation, and even mitigate potential incidents.
Even the most hardened individuals should be managed with every reasonable effort made to leave their dignity intact. It’s not our place to impart our personal moral character upon others. It’s not our responsibility to pass judgment or pass sentences.
This isn’t intended to be a message of clemency or leniency. We absolutely do have a professional responsibility to deal with the situation and resolve the matter based on our company policies and practices. Those policies are constructed by our leadership to provide objective standards and appropriate measures to guide our decisions in the best interests of the company and all others concerned. But a critical aspect of our professional conduct is dignity and respect, and typically that is written directly into our policies and codes of conduct.
When Dignity Is Lost
Recent news stories have been reported and discussed through our digital channels that provide us with vivid and unfortunate examples of what can happen when we fail to make the appropriate distinction between respect for the act and respect for the individual.
One incident involved a young man with a developmental disability who was accused of theft and then was allegedly submitted to a “walk of shame” in which he was paraded through the store in handcuffs in front of his fellow employees—a practice that other employees claim happens on a regular basis. His employment was terminated, but he was never charged with a crime. According to reports, he was “shocked, confused, and mortified” at being handcuffed and paraded through the store and “had no idea why he was being arrested.” He later told his family, “This is the worst day of my life.” Three days later he jumped off a nearby building, taking his own life. Was he actually involved in a criminal event? Would that justify the way he was treated? The retailer is currently facing litigation for false imprisonment, intentional infliction of emotional distress, negligence, and wrongful death.
A second incident involved a young woman who was apprehended for switching price tags at a store in the United Kingdom and subsequently charged with fraud. According to reports, a TV production company that was filming for a reality show in the store captured the incident. According to reports, the young woman was repeatedly “hounded” with messages stating that the footage would appear on television for a national audience. Dreading the threat of being exposed on national television, she took her own life, hanging herself at her home.
It wasn’t simply theft or fraud that led to these tragic outcomes. The actions described and the way these incidents were handled won’t be found in any company policy or practice, nor will they have been condoned in any way by company leadership. If in fact these events occurred as described, they were much more likely the actions of a few individuals who took it upon themselves to “send a message” about their perceptions of just behavior based on their extremely limited views of theft and punishment. If this is truly what happened, these alleged criminals were bullied and humiliated for the sake of effect.
Somewhere along the way, those involved lost sight of an essential aspect of their responsibilities, and now two people are gone. We may attempt to view these incidents as extreme events, even while acknowledging that they aren’t isolated incidents and have happened before. We can look at other similar events that have occurred and cite different outcomes. While that doesn’t
make it right, it still might only mean that we were lucky similar events didn’t lead to tragic endings. Yet whatever our own answers may be, it should still lead each of us to pause and reflect on ourselves, our people, and our programs—even if it’s simply out of respect for the possibilities and the memories of those lost.
We all have our own opinions of right and wrong. We may not like or personally accept the reasons put forward by those involved in theft and related criminal acts. Yet we have a professional obligation to treat everyone with a degree of dignity and respect. We have a responsibility to protect the profits of our companies thoughtfully, sensibly, respectfully, and with appropriate discretion.
What Judgment Means in LP
Every year shoplifting incidents, employee theft, fraud, and other criminal acts wreak havoc on our businesses, costing retailers billions of dollars. They are serious problems that cost all of us in countless ways and have directly contributed to the demise of many companies. This legitimizes the need for a loss prevention program. It supports our policies, practices, and initiatives. However, it does not give anyone the right to deliberately and purposefully exploit or humiliate.
We all have our own opinions of right and wrong. We may not like or personally accept the reasons put forward by those involved in theft and related criminal acts. Yet we have a professional obligation to treat everyone with a degree of dignity and respect. We have a responsibility to protect the profits of our companies thoughtfully, sensibly, respectfully, and with appropriate discretion. Failing to follow our most basic principles can lead to tragic results.
Respect is indeed a word that carries powerful messages. But perhaps the most important is the message of responsibility. When that responsibility is neglected, self-respect is ultimately what is lost.
PRECIOUS CARGO
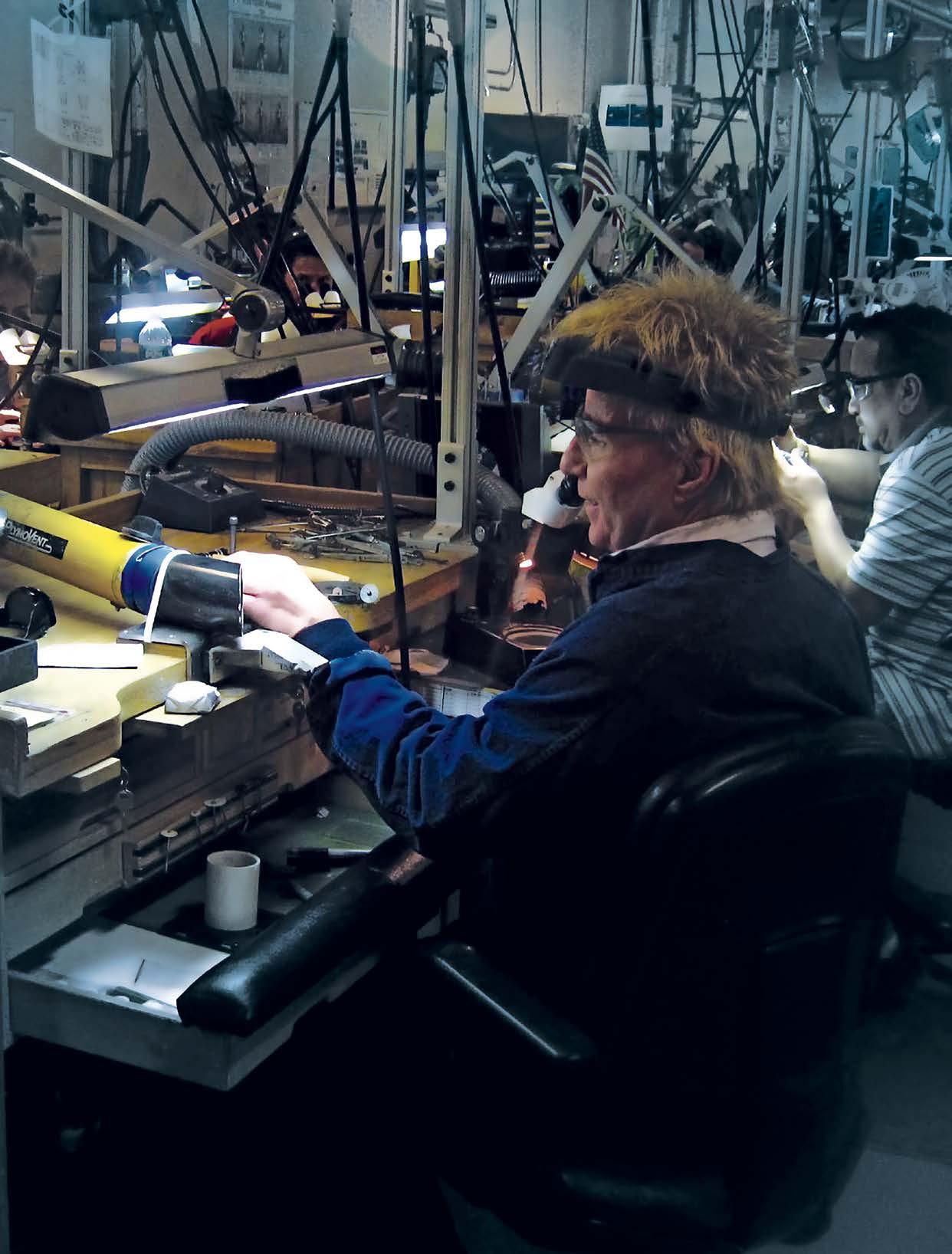
A CLOSER LOOK AT TIFFANY’S SUPPLY-CHAIN NETWORK

Every retail organization requires supply networks that are efficient, streamlined, and able to move quickly to meet consumer-driven demand. The competitive nature of the business requires resourceful and proficient channels that quench the customer’s desire for variety, availability, and immediacy. Every product that eventually ends up in the hands of a customer reaches this destination as a result of the cumulative efforts of a complex system of people and processes, all of which must be accomplished while balancing
price, quality, and service. This is the lifeblood of the retail enterprise, providing the pulse that makes everything else flow smoothly.
The comprehensive management of the supply-chain network is an essential aspect of the process, coordinating and synchronizing crucial activities within the business to reach desired outcomes. Depending on the organization, the exact configuration of the global supply network can vary greatly based on the needs of the business and the specific types of products sold. But for any product or service offered by any company, there are usually a number of different stages within the supply chain that must be managed, and security will play critical role in every aspect of the process.
Successful supply-chain management strategically and efficiently integrates suppliers, manufacturers, warehouses, and stores so that merchandise is produced and distributed at the right quantities, to the right locations, and at the right time. From the point of origination to the hands of the customer, products can pass through many locations and cross thousands of miles. Each stage of the process can present unique challenges for security and product protection efforts. When managed effectively, every product is considered precious cargo. As we continue to explore the details of the supply-chain network, let’s take the voyage with one of the gems of the retail world.
Considering the value and demand for Tiffany products, safety and protection is always a paramount concern. Security resources must be highly effective, well-contained, and rigorously managed. Security protocols must be well-conceived, meticulously followed, and strictly enforced. And while the company security program has been highly successful, there are always those looking for ways to steal the products.
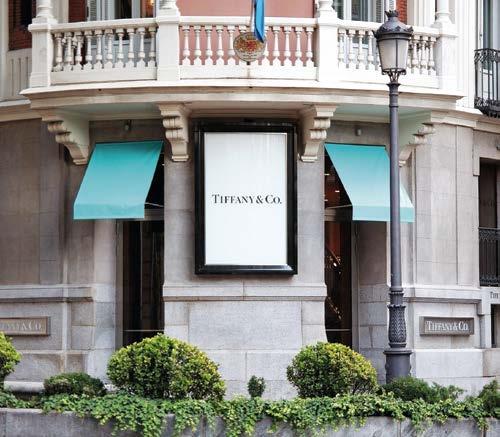
The Tiffany & Co. Supply Chain
Tiffany & Co. designs, manufactures, and retails jewelry worldwide. Headquartered in New York City, the company has been highly regarded as one of the world’s premier jewelers since 1837. The company currently operates stores throughout the Americas, Asia-Pacific, Japan, Europe, and other locations across the globe in addition to Internet and catalog sales, business-to-business sales, and wholesale distribution.
For more than 175 years, Tiffany has been synonymous with luxury and style, crafting jewelry and other high-quality creations of timeless beauty and superlative craftsmanship. Its products include fine, fashion, and statement jewelry; engagement rings and wedding bands; and non-gemstone, metal jewelry including sterling silver and gold. The company also sells timepieces, leather goods, sterling silverware, china, crystal, fragrances, and accessories. Tiffany designs and produces many of the world’s premier sports trophies, such as the Commissioner’s Trophy (baseball), the Larry O’Brien Championship Trophy (basketball), the Vince Lombardi Trophy (football), and many others.
But long before a knee is bent to offer a ring to a future bride, a family heirloom is passed to a grandson or granddaughter, or a trophy is raised in victory at a sporting event, these treasures must be sourced, crafted, and delivered through a worldwide network of facilities and transportation
services before ever reaching that final destination. That journey ventures both the details and distance of a sophisticated supply chain with strict controls, hardened facilities, and advanced security resources to protect the products as they make their way from the mines to the global marketplace.
Responsible Sourcing
Historically diamond, gemstone, and precious metal supply chains have been complex and often lacking in transparency. Today that is changing dramatically, with the jewelry industry committed to better understanding the social, economic, and environmental impacts of the mining and processing of precious materials, as well as working to better ensure that those activities are conducted responsibly.
The Kimberley Process Certification Scheme was a resolution intended to
strengthen the diamond industry’s ability to block sales of “conflict diamonds” or “blood diamonds” and prevent these gems from entering the mainstream rough diamond market. The resolution called for an international certification system on the export and import of diamonds and legislation in all countries to accept only officially sealed packages of diamonds. It imposed criminal charges on anyone trafficking in conflict diamonds and instituted a ban on any individual found trading in conflict diamonds. This resolution was intended to ensure that buyers of diamonds are not contributing to aggression around the globe and are not financing rebel movements and other violent acts.
Tiffany has been a leader in working toward a more responsible jewelry industry and championed efforts to seek congressional approval of US participation in the Kimberley Process. Traceability is key to ensuring that mines are operated in environmentally and socially responsible ways, and the company has developed direct sourcing relationships with mines around the world. In many cases the output of those mines is delivered directly to Tiffany’s own diamond cutting and polishing facilities.
By establishing rigorous standards for responsible mining, sourcing precious materials directly from mines that are committed to social and environmental stewardship, and working with industry colleagues and other organizations to establish more rigorous standards for responsible mining, business can be conducted in ways that are acceptable to all stakeholders in the process. Other jewelers in the US have also been passionately involved in this movement.
Diamond Procurement and Processing
African operations include facilities in Botswana, Namibia, and Mauritius that provide diamonds for manufacturing and are sourced directly from local mines. Company executives deal directly with mine operators, working off of prearranged agreements to source rough stones. Once the stones are purchased they are processed into manufactured diamonds through a series of steps that include: ■ Marking—the process that determines how the stone will be cut, to include size and shape, ■ Bruting—cutting the stones to give the diamond its round shape, ■ Cutting—cutting the stones by machine to give the diamond its shape, ■ Polishing—placing the stone above a rotating wheel that smoothes the stone to create the diamond’s finished look, and ■ Quality assuring—establishing the weight, quality, clarity, color, and other distinguishing features of the stone.
The European facility is located in Antwerp, Belgium, the world-renowned diamond capital of the world with 90 percent of the world’s diamonds passing through these facilities. It is home to the largest of the Tiffany diamond factories and processes the majority of the diamonds sold at Tiffany stores worldwide. Sourcing stones from Russia, Canada, and the United Kingdom, diamonds are purchased and processed as they are in the African facilities, but in much greater volume.
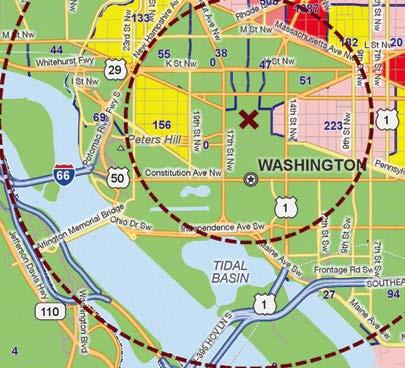
OUTSMART CRIME, EVERY TIME.
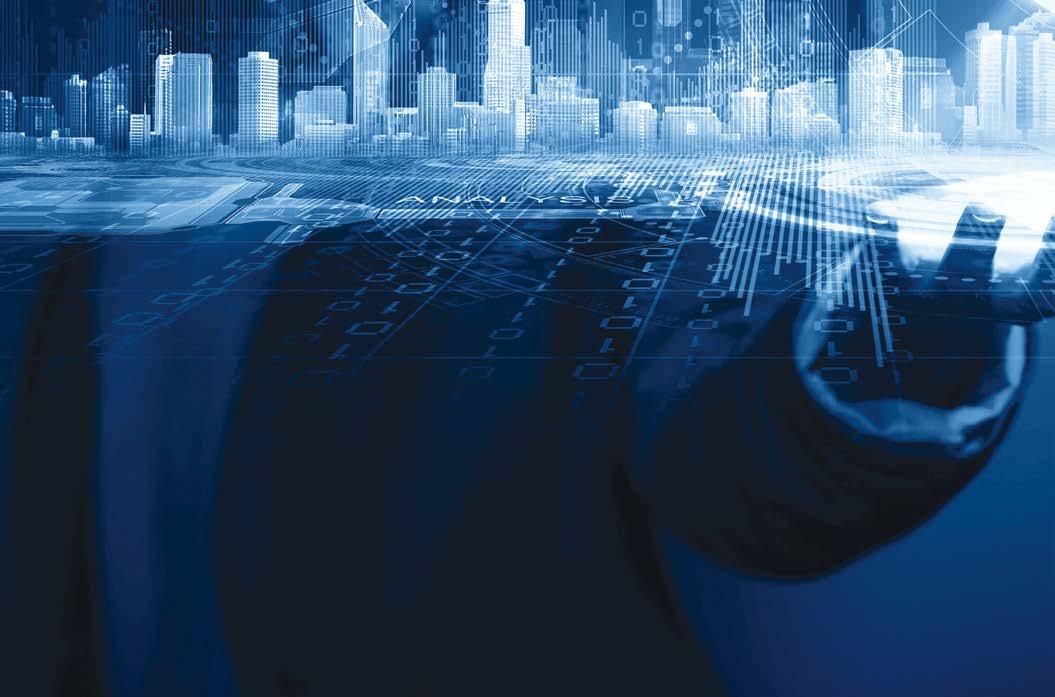
Read how CAP helps a major retailer OUTSMART CRIME® in our latest case study! Download now: capindex.com/outsmart
1-800-227-7475 I askcap@capindex.com
OUTSMART CRIME
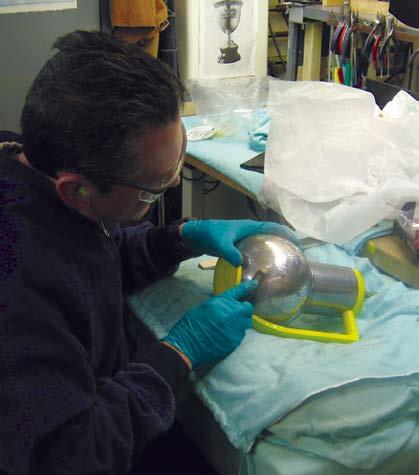
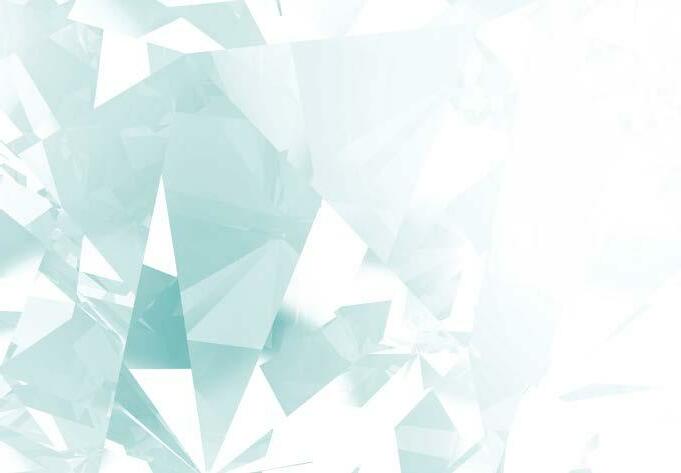
At Tiffany both employees and products are considered precious resources. Every professional has a responsibility to learn as much about the different functions within the company as they possibly can, and that clearly includes various aspects of the supply-chain network. This remains a critical need within the retail environment and an opportunity for professional growth as security continues to evolve.
Asian factories in Vietnam and Cambodia play an important role in diamond production within the supply chain. These sister facilities, known as “melee factories,” only work with diamonds that are 0.18 carat or smaller. Stones are sourced from the facility in Antwerp. They are also marked, bruted, cut, and polished at these sites. However, the process is extremely meticulous and much more delicate due to the size of the stones.
All of the processing facilities are meticulously hardened to include best-in-class equipment, strict access controls, and the latest in protection technologies to ensure the safety and protection of the workers and products. Stringent and detailed audit processes are in place to manage the inventory and accountability of the stones during processing. Special clothing and other requirements may also be in place to maintain the highest levels of security and protection.
Once the stones are processed, they are sealed in special containers and shipped via armed, armored carrier to the United States facilities.
Diamond Manufacturing
After receiving finished stones from company factories in Africa, Europe, and Asia, the US facilities located in New York and Kentucky produce over 70 percent of all Tiffany diamond jewelry sold in the world. The largest factory is located in Pelham, New York, and produces everything from solitaire diamond rings to diamond earrings, necklaces, and bracelets. Its satellite factory in Mt. Vernon, New York, handles overflow from Pelham and produces many of the same types of products. The facility in Lexington, Kentucky, is a relatively new venture and primarily produces solitaire diamond rings along with a small assortment of other jewelry.
Naturally, security is at a premium in these facilities with state-of-the-art alarm and surveillance systems, the latest in today’s technology, and stringent, detailed audit processes to manage the inventory and accountability of the products during processing. All merchandise, once completed, is shipped via armored carrier to the company distribution center in Parsippany, New Jersey.
Colored Gemstones
We are a world that treasures variety, and that is certainly no less true in our tastes in jewelry. Precious gems come in a kaleidoscope of colors, valued based on the type of stone, the internal clarity of the stone, the depth of color, size, shape, and many other variables.
Long known as the color gemstone capital of the world, Thailand is the newest addition to the Tiffany supply chain. A small factory newly opened, it is responsible for manufacturing colored gemstone jewelry for Tiffany. Stones are purchased precut from local vendors and manufactured into jewelry of all types that feature colored stones.
Metal Manufacturing
The largest factory in the supply chain, Tiffany’s facility in Cumberland, Rhode Island, is home to almost 800 employees. All metal jewelry is produced here, from silver bracelets and earrings to platinum and gold settings for diamond engagement rings.
Material resources are received here in manufactured forms (flat sheets, tubing, or chain) from precious metal vendors throughout the United States. Once received, the metal will travel to one of two facilities depending on the material. Finished goods, such as silver bracelets, are shipped directly to the company distribution center either by UPS or an armored carrier, depending on the product. Shanks for rings or necklaces that will hold diamonds are sent to one of the diamond manufacturing facilities. These pieces are typically shipped via armored carrier.
The Cumberland facility is also home to the hollowware shop, which produces silver platters and dinnerware and crafts most of the professional sports trophies awarded across the United States.
Silver merchandise, a small but important part of the supply chain, is produced in the Rhode Island factory and then shipped to a Dominican Republic factory, which provides the final polish for all silver jewelry sold at Tiffany & Co. Once the product has reached a level of polish that meets Tiffany standards, it is sent back to Rhode Island for final manufacturing.
This environment presents some of the greatest opportunities for losses in the supply-chain network, primarily as a result of scrap metal thefts and similar incidents. For example, many of the rings manufactured are created with multiple rings attached to a sprue, which is a common target for theft.
A sprue is a metal framing that holds the rings during manufacturing, very similar to the way plastic model pieces are attached to a plastic sprue, which is the plastic framing that holds all of the pieces together. The sprues are made out of the same precious metals as the rings they hold, which means that they will hold material value as a precious metal source that can be melted
continued from page 58 and re-used. As a result, they are often the targets of attempted theft. Posts, shavings, and even the dust gathered as part of the polishing process are all composed of the precious metals, making them attractive targets for theft.
In addition to hardened security requirements, strict controls, and metal detection equipment, special shoes and other clothing items are required in these facilities to help mitigate theft opportunities and other potential losses.
Distribution
Located in Parsippany, New Jersey, the Retail Service Center (RSC) is Tiffany’s primary distribution point, supplying all retail locations with final finished product. The facility is housed within a hardened and strictly protected corporate park and is home to over 500 employees. Shipments are received from internal manufacturing partners and select external vendors. Once received, products are stored in a designated secure area based on product value and other related variables. Depending on the specific products, orders are then shipped via UPS or armored carrier for sale in the Tiffany store locations worldwide.
The Hanover, New Jersey, Customer Fulfillment Center is located just five miles from the main distribution facility. Home to more than 200 employees, this facility fulfills orders for customers that use online services at Tiffany.com to shop. Products are primarily supplied through the RSC with fulfillment provided through a highly sophisticated and largely automated
While the Tiffany supply-chain network may offer some unique challenges for the security team, the need for strong controls, appropriate protection, investigative prowess, and well-managed training and awareness efforts strike a common chord in every retail operation. Every supply-chain network requires attention and protection, regardless of the retailer or the needs of that particular company.
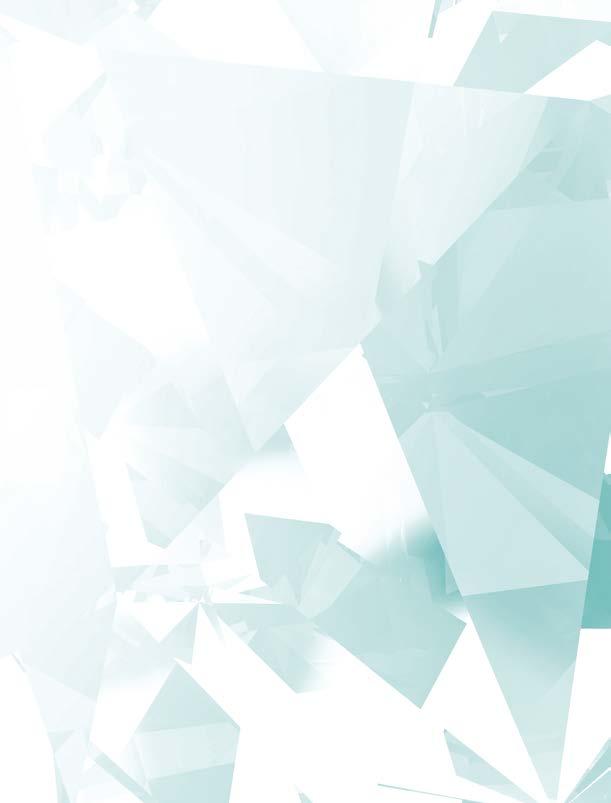

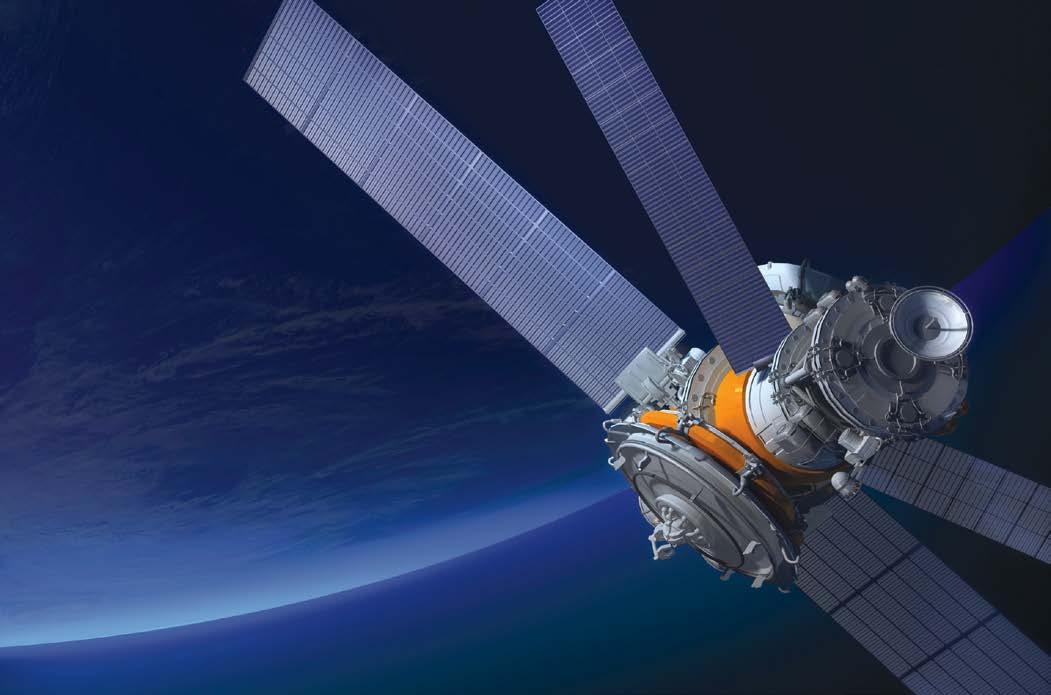
Innovative GPS Tracking Solutions
for Financial, Retail, Transport and Law Enforcement
●
Protects all types of valuable assets
Automatically and silently notifies law enforcement when a theft occurs
24/7 customer support center The ONLY tracking system partnered with over 5000 Law Enforcement Agencies
info@3siecurity.com | 3sisecurity.com
process within the facility. It is also home to many value-added services such as engraving, hand engraving, and etching.
The Tiffany Service Center (TSC) located in Queens, New York, is the main hub for repair and maintenance of all Tiffany customer products. If customers return merchandise to a store for repair or service, it is sent to the TSC. Orders are received via UPS or armored carrier and serviced by a team of over 100 jewelers and craftsman. Once the merchandise is repaired, it is then shipped directly to the store of origin.
Supply-Chain Protection
Considering the value and demand for Tiffany products, safety and protection is always a paramount concern. Security resources must be highly effective, well-contained, and rigorously managed. Security protocols must be well conceived, meticulously followed, and strictly enforced. And while the company security program has been highly successful, there are always those looking for ways to steal the products. Some will pursue creative and covert methods, while others may attempt force and more violent means to gain access. Some will attempt a combination of both. Either way, there’s little room for error.
This requires a well-trained and highly disciplined security team to keep the employees safe and the products protected. There must be leadership buy-in and employee ownership at every level of the organization. It is a process that must start from the point of origin and be maintained throughout the entire network to ensure maximum efficiency.
While the Tiffany supply-chain network may offer some unique challenges for the security team, the need for strong controls, appropriate protection, investigative prowess, and well-managed training and awareness efforts strike a common chord in every retail operation. Every supply-chain network requires attention and protection, regardless of the retailer or the needs of that particular company.
At Tiffany both employees and products are considered precious resources. Every professional has a responsibility to learn as much about the different functions within the company as they possibly can, and that clearly includes various aspects of the supply-chain network. This remains a critical need within the retail environment and an opportunity for professional growth as security continues to evolve. We don’t all need to work with precious metals to develop a gold-standard management program. But the right tools, strong partnerships, and the right approach can help us achieve that goal.
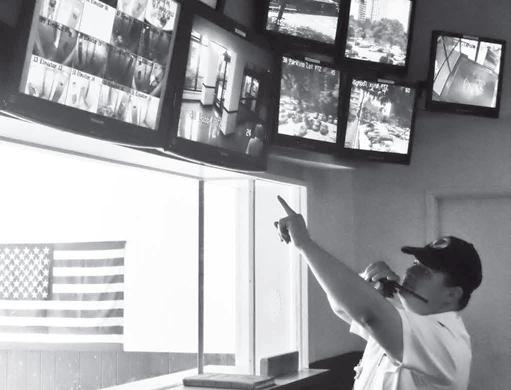
STEVEN PALUMBO, LPC, CFI is currently group director of security for distribution and manufacturing at Tiffany & Co. He has more than twenty-eight years of experience in loss prevention and retail security, having held leadership positions both internationally and domestically in retail and supply-chain security. He serves as the chairperson for the Northeast Chapter of CFI. Palumbo has a BA in criminal justice from Seton Hall University and a MS in protection management from John Jay College of Criminal Justice. He can be reached at 212-230-6855 or steven.palumbo@tiffany.com.