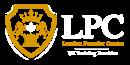
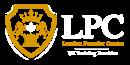

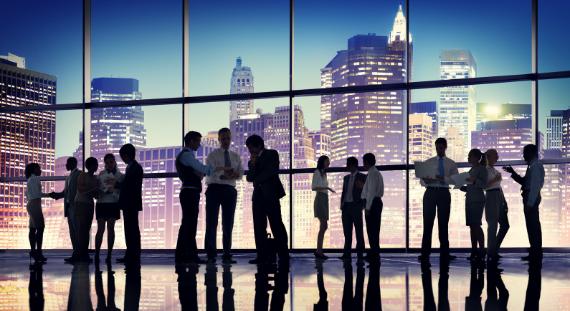

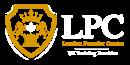
INTRODUCTION
High levels of quality are essential to achieve the Company business objectives. Quality, a source of competitive advantage, should remain a hallmark of Company products and services.
High quality is not an added value; it is an essential basic requirement. Quality does not only relate solely to the end products and services a Company provides but also relates to the way the Company employees do their job and the work processes they follow to produce products or services.
The work processes should be as efficient as possible and continually improving. Company employees constitute the most important resource for improving quality. Each employee in all organizational units is responsible for ensuring that their work processes are efficient and continually improving.
By attending this course , participants will have a clear understanding of the principles of quality The ability to set quality standards in their area of work An identification of methods which can be used to improve quality Skills in motivating staff to achieve high standards Throughout the day delegates will be encouraged to develop methodologies pertinent to their place of work through practical activities
This course designed to enable supervisors and managers to set and achieve high standards and to improve quality in their area of work.
OBJECTIVES
By the end of the Best Practices In Quality Control And Assurance Course you will be able to:
Understand the fundamentals of quality management
Understanding the relationship of quality engineer with a quality system
Understanding the problem solving techniques
Basic concepts of statistics and method for using technical quality
Creating accepted sampling plans
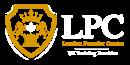
WHO SHOULD ATTEND ?
This training Best Practices In Quality Control And Assurance Course is suitable for:
Operations directors
Heads maintenance and operations management.
Senior executives, managers, advisors and officers who wish to develop a thorough knowledge of quality management.
COURSE OUTLINE
Day 1
Fundamentals of Quality Management
Understanding the quality management system
Planning the strategies for quality management
Concept of Quality Information system
Importance of customer relations and supplier management
Understanding the strategies for Application Deployment
Day 2
Components of the Quality System
Components of a quality system
Required documentation for a quality system
Concepts of Quality Auditing and Cost of Quality
Understanding the rules and standards of quality
Training on Quality
Day 3
Process for Product Design
www.lpcentre.com
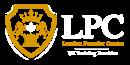
Understanding the characteristics of quality
Methods of material control
Accepted sampling plans
Reviewing design inputs
Reliable and maintainable designs
Concepts of Measurement System Analysis and Metrology
Day 4
Methods of Quality Control
Quality management and control tools
Methods / tips on continuous improvement of quality
Concept of CAPA Corrective and Preventive action
Training on Quality Control
Day 5
Quantitative Methods and Techniques
Method 1: Collecting and analysing data
Method 2: Decision making and statistics
Method 3: Variable relationship
Method 4: Statistical Process Control(SPC)
Method 5: Capability of processing and performance
Method 6: DOE (Design of Experiment) and analysing
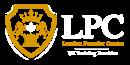
