

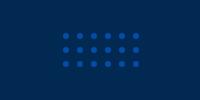



INTRODUCTION
Lean Six Sigma is a business approach to continual improvement which focuses on stripping out areas of waste from processes and minimizing product reduction. Lean refers to maximizing customer value and minimizing waste; creating more value for customers with less wasted resources. Six Sigma is the on-going effort to continually reduce process and product variation through a defined project approach. Lean Six Sigma represents a business philosophy leading to the elimination of waste and the reduction of variation. With Lean Six Sigma, costs are reduced, productivity is raised and customer satisfaction is enhanced. The effort starts with understanding value through the eyes of the customer. Anything that does not add value is waste. Any variation from the target or ideal state is a potential source of added cost. Lean Six Sigma efforts tackle both waste and variation with a focus on customers and their needs. Lean and Six Sigma are part of a continuum in which efficiency (Six Sigma) is coupled with effectiveness (Lean) to create a robust improvement environment. This course will give you an understanding of what Lean Six Sigma is and how it can benefit your organization. You will be able to put in place your own Six Sigma framework to achieve reduced costs through streamlined processes, increased time and performance management as well as increased customer satisfaction levels
The Introduction to Lean Six Sigma course will provide you with an understanding of the background and application of Lean Six Sigma. You will learn how to apply Six Sigma principles to different business areas, how the DMAIC process works, and how it can improve your business. Our tutors will also guide you through the belt system, and the roles and responsibilities of Green and Black Belts
OBJECTIVES
Upon completion of this Introduction to Lean Six Sigma course, participants should be able to: Understand the scope and breadth of a Lean Six Sigma initiative.
Gain an understanding of what waste is and how to identify it so that it can be reduced.
Become aware of variation and techniques to reduce it.
Become familiar with the DMAIC team project model.
Be aware of the infrastructure needed to support a Lean Six Sigma effort
Comprehend the critical elements of the Six Sigma approach
Recognize how poor quality harms business in a service environment
Identify the new roles and responsibilities employees play in this approach
Identify those processes that need improvement

WHO SHOULD ATTEND ?
Introduction to Lean Six Sigma training course is of interest to:
All those working in improving their organizations. In particular, to executives, managers, and improvement team leaders and members, seeking to learn how to implement business improvement through Lean-Six Sigma concepts and processes.
COURSE OUTLINE
Day 1
What is Lean Six Sigma
Lean Six Sigma Philosophy
Lean Six Sigma Methodologies
Quality defined: types and relationships
Quality issues in the Service Sector
The Cost of Poor Quality in Services
Quality Organization, Culture and Roles
Day 2
Improvement Methodologies
Value Stream Mapping
Elimination of Waste
The 5S's
The DMAIC Project Cycle
Lean Manufacturing philosophy: the "5 S"
The Seven Basic Quality Tools
Value Stream and State Maps: Improvement Id.
Case example of Lean in Service Sector
Phase by Phase implementation & tools
The House of Quality: QFD

Day 3
Supporting Infrastructure
Components in the Supporting Infrastructure:
Leadership team
Champions
Black Belts
Green Belts
Project Teams
Subject Matter Experts
DMAIC Project Management
Day 4
Application and Outcomes
Lean Six Sigma in: Manufacturing
The "Office"
Order Entry
Warehousing and Distribution
Combining Lean-Six Sigma Advantages of Combining Lean-Six Sigma
Basic statistics used in Lean-Six Sigma
Quality Process: Analyze, Improve and Control
Day 5
Case Studies and Simulations.
Where Lean meets Six Sigma: concepts
Case Study: Lean-Six Sigma; a fusion
Case examples of Lean-Six Sigma in Service
Simulation of data analysis in Lean-Six Sigma Simulation of Lean-Six Sigma implementation
www.lpcentre.com

