Life Size Legos
As designers, we are charged with a complex multitude of decisions to best serve our clients, communities, and artistic conscience. While most of our time is spent drawing and coordinating, the act of building is the central core of why we do what we do.
Matt Barnett, AIA, USGBC // Architect ©LS3P 2023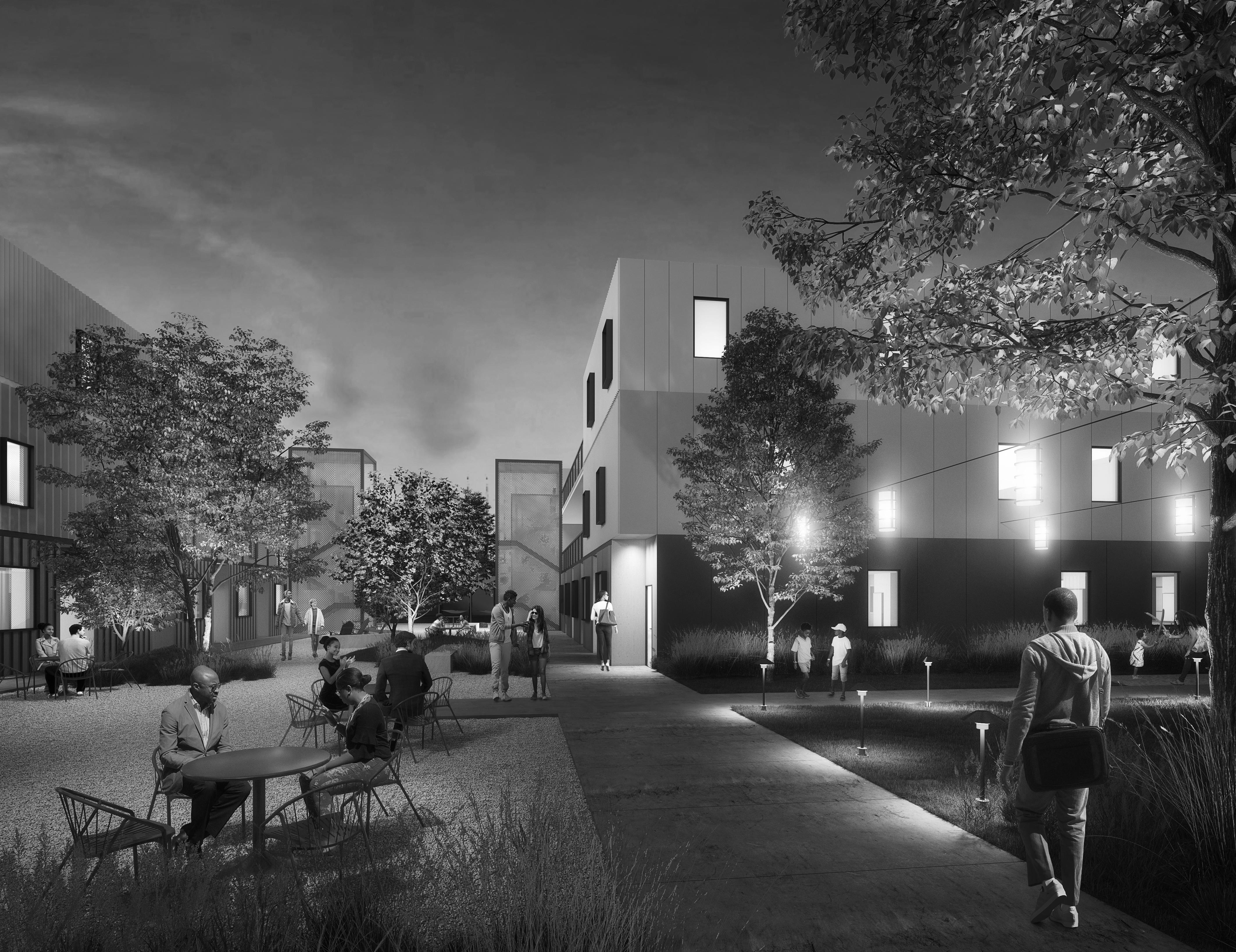
As designers, we are charged with a complex multitude of decisions to best serve our clients, communities, and artistic conscience. While most of our time is spent drawing and coordinating, the act of building is the central core of why we do what we do.
Currently we are in a construction crisis of labor cost inflation, lack of access to skilled tradesmen, and immense pressure to deliver projects quickly. This crisis can be attributed to many reasons, including the hot AEC economy, which creates opportunities for success as well as challenges to overcome. Our Herculean goal is to create buildings which embody design excellence and elite quality of detailing and deliver them on budget and on schedule.
Construction systems are slow to evolve and are heavily influenced by market forces, trade talent, and technology. Rarely do we have to chance to truly celebrate and accentuate construction systems, means and methods, and market constraints. When we embrace these elements and constraints, prefabricated modular construction is the perfect recipe to bridge many of the forces at play.
Designers are often raised with an appetite for art and creation. One of my favorite memories is the endless hours I spent as a child using LEGO® bricks to create dream worlds by stacking the colored bricks in unlimited configurations. So, it is no surprise that I eagerly embraced my inner nerd while designing modules that would be stacked and configured as real life sized building blocks while also allowing the general public to enjoy visually reminiscing about childhood hobbies.
Here are some of the lessons learned from my experience working on one of the first contemporary examples of prefabricated modular housing in the United States:
Cost Efficiencies to Mitigate the Hot Economy
Due to the sheer amount of work available, the market is being defined by unfettered subcontractor pricing, dependent on the amount of competition within a specific area. Currently we are seeing a yearly 5-10% cost inflation based almost purely on labor costs. Modular construction is created turn-key, off-site in factories usually set up in rural places that desperately need employment opportunities. This strategy results in the best labor talent available at reasonable prices, eliminating the local labor inflation in larger market areas. Large modular companies have longstanding relationships with material suppliers based on their immense buying potential from decades of modular home creation. When applied to commercial construction in multifamily and hotel sectors, buyers can potentially procure a higher level of finish quality for lower prices.
Superior Quality of Construction
Modular construction can achieve higher levels of construction quality by taking cues from the automobile industry. The construction of the modular units happens on an assembly line where each worker has a controlled environment with everything needed to complete each specific repetitive task. Inspection and oversight are easily accomplished along the production line. Workers are completely removed from inclement weather and work in a climate-controlled space. Factory conditions remove the variables of temperature and precipitation. The nature of the modules themselves results in a superior level of acoustical separation and, in turn, occupant satisfaction. Once assembled into a project, apartment and hotel units have double walls, floors, and ceilings, creating a structural separation for impact and airborne noise. Units are finished completely on the inside before they are shipped to the site and onsite contractors do not even need to enter the units once they are assembled vertically. Corridors are left unfinished to allow for electrical and plumbing connections.
Speed of Schedule
Time is money, and modular construction can shorten the construction schedule by up to 50%. Materials are 100% procured and stored before the building process in the factory to allow for continual construction without delivery delays. Tradesmen can work on all phases of the modules at one time and do not need to wait for each other to finish or coordinate schedules. All the site work, foundations, and podiums can be completed at the same time, allowing for the seamless trade-off from groundwork to having a crane stack the modules. Stacking is a very quick process and a building can seemingly take shape overnight.
Low Fab Performance
The biggest areas of sustainability which benefit from modular construction are waste reduction and energy efficiency. Waste on a conventional jobsite is typically around 10%, which can weigh heavily on the final budget price and creates more waste in our landfills. Waste on a prefabricated modular site is around 3%, nearly all of which occurs in the factory setting and not on the actual job site. The superior quality of construction increases energy efficiency by as much as 25-40% through very tight building construction and reduced infiltration in the finished units. A rainscreen façade installed can create further energy savings.
Collaboration & Constraints
Early collaboration between the designers, general contractor, MEP, and the modular contractor is critical to success in modular building. Teams are required to do extensive collaboration very early in the design process and front-load most of the work that is typically spread out over design development and construction documents. One successful model is to create a design-build structure from the beginning, and bid out the modular construction at the schematic level. The construction bid should include all the architects and engineers who are employed by the modular company and who will provide very large complete building shop drawings. The designers will have significantly less work to do in terms of construction drawings, but that will be made up in the coordination of all the MEP systems on the front end. Changes to the project are not possible after certain cut-off dates, so all decisions must be made early and stuck to throughout the process. The way we design must be tailored to the structural constraints of a module and the shipping constraints of a semi-trailer truck.
Celebrating Construction with Design
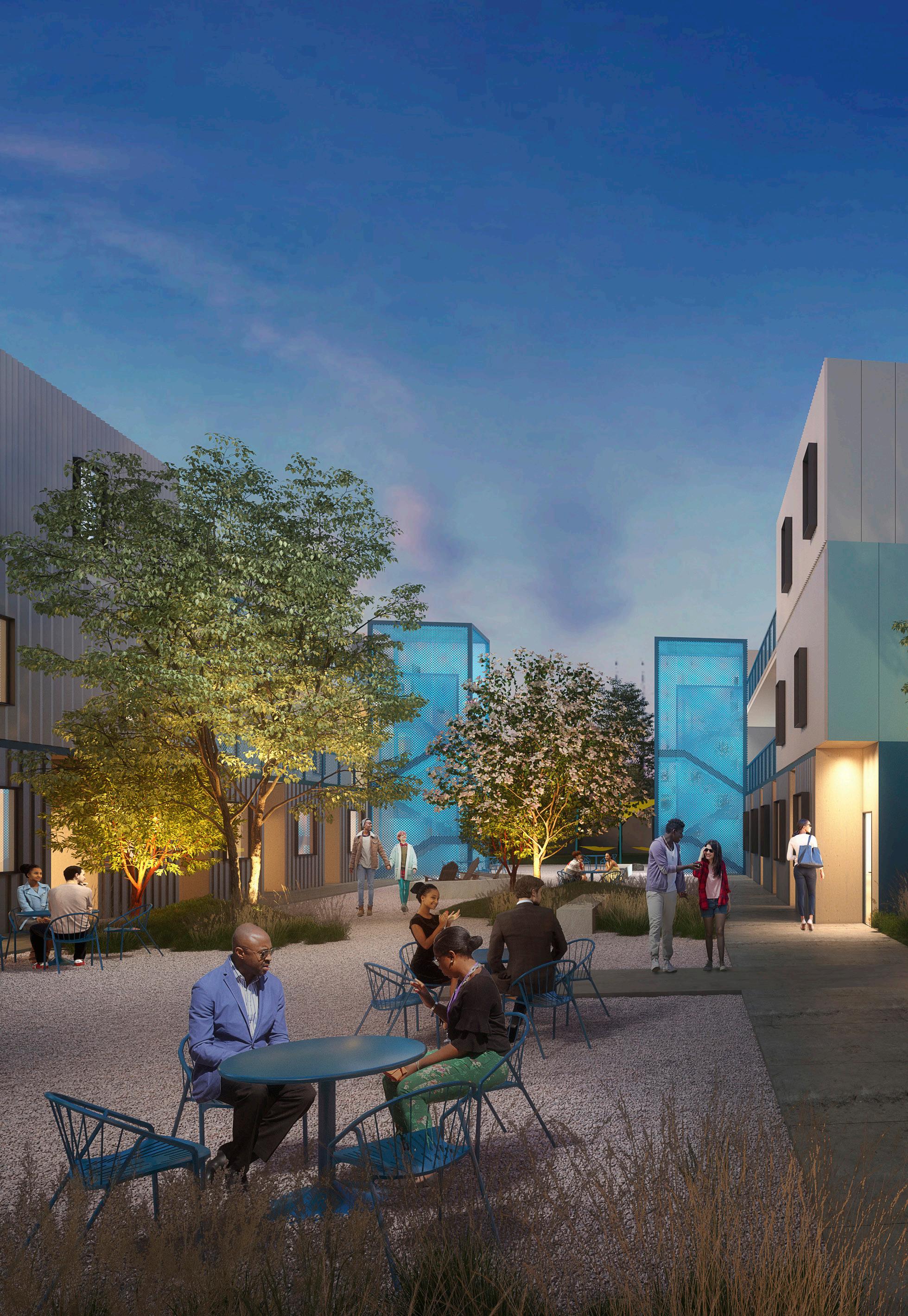
Modular construction can be made to look like conventional construction, but I believe in embracing the opportunity to accentuate the nature of how the building is made. The boxy form of singular units making up a collection offers endless possibilities in pixelated form-making. By choosing designs that highlight the units, we can engage the public through art and education of how the building was made and create a playful juxtaposition between design and making. This idea can be taken from a largescale form making down to the smallest details.
Meet the Author
Matt Barnett is a Senior Associate in LS3P’s Wilmington office focusing on community-oriented projects, design excellence through rigorous research, and narrative-based conceptual frameworks. His work has been recognized with over 70 design awards, including a Progressive Architecture Award, AIA COTE Top 10 Awards, an AIA National Institute Honor Award, and Chicago Atheneum American Architecture Awards.
Matt was named an AIA Young Architect awardee at the national level in 2022 and an AIA NC Young Architect awardee in 2021, and became a member of the inaugural “40 Under 40” class at the University of Tennessee in 2020. He is currently serving as Director of Environmental Stewardship and Chair of the Committee on the Environment for AIA NC.
