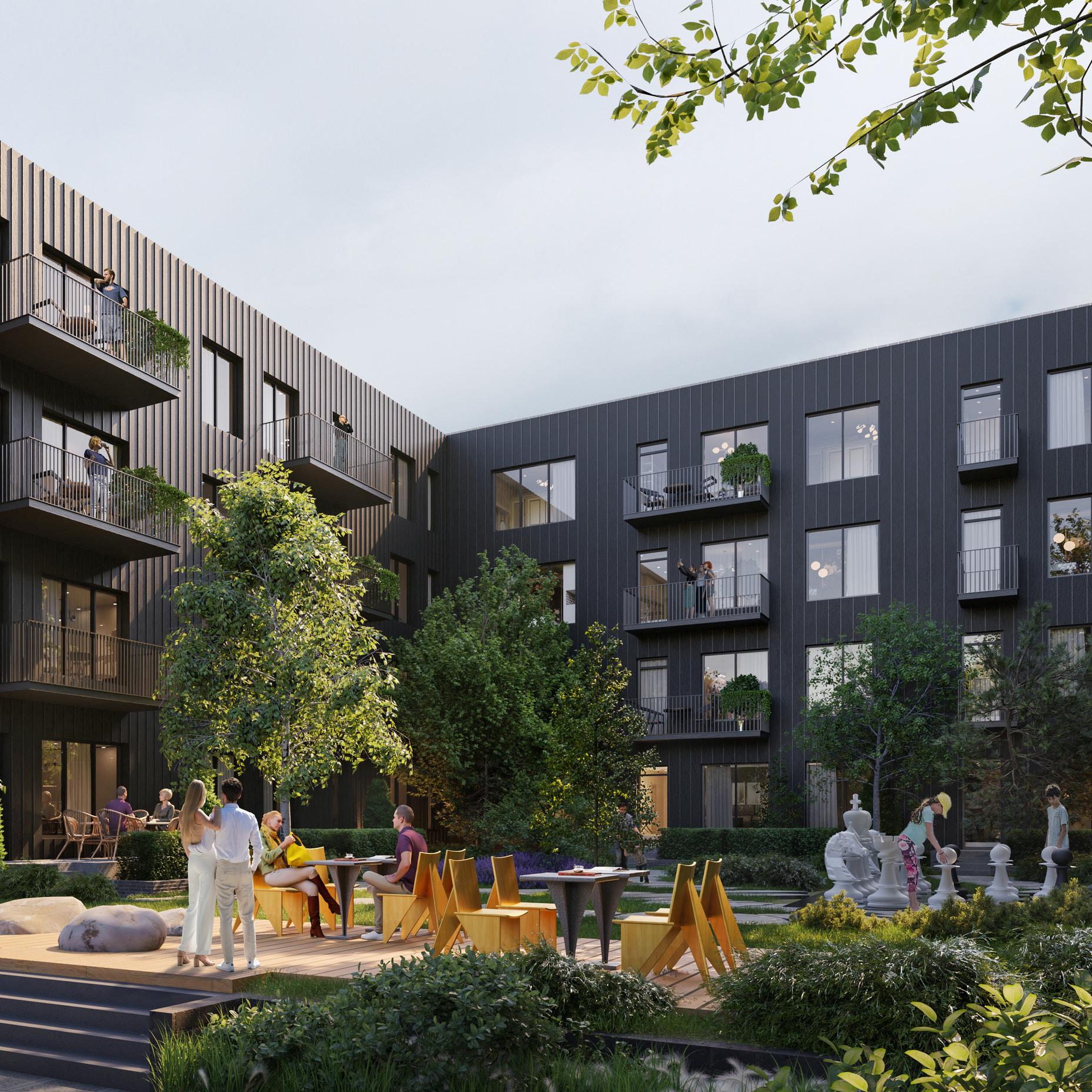
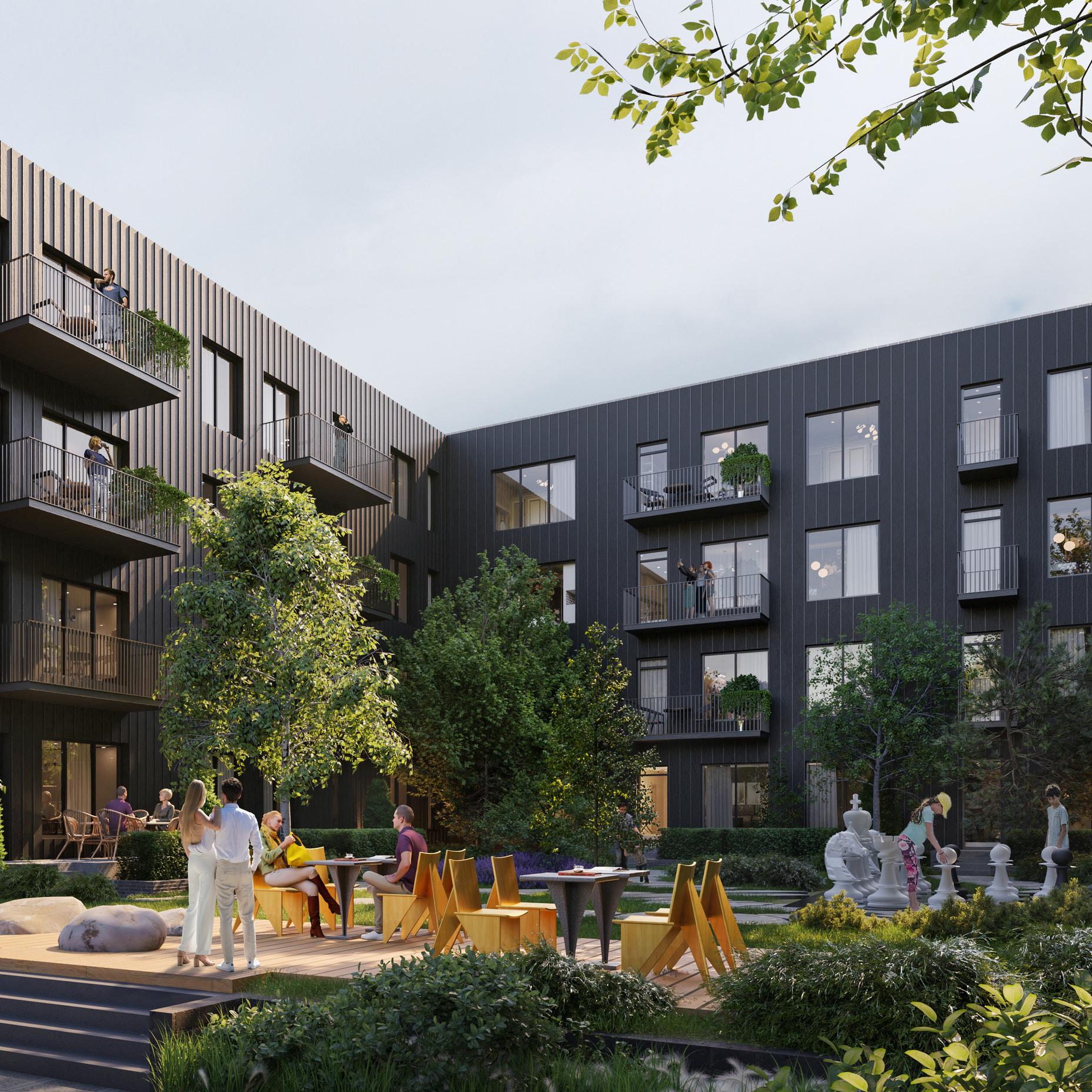
Designing for Deconstruction
DESIGN INVESTIGATIONS
a new way of thinking about materials
Re-thinking the Process
Construction has long been thought of as a linear process. We extract raw materials from the earth, transport them to factories, and transform them into building components through the manufacturing process. We then ship them to a building site, install them, and discard them when the building reaches the end of its useful life. Carbon is emitted at every stage of the process. Demolished buildings – and all of the materials and embodied carbon they entail – typically end up in landfills, even as the extraction process begins anew for the next building. With over eight billion people sharing the planet, and an understanding of the urgent need to curtail carbon emissions as quickly as possible, this model is no longer working.
What if we thought about our materials, and our buildings, differently? What if the process were more of a circle than a line? Proponents of Designing for Deconstruction (DfD, also referred to as Designing for Disassembly) believe that we can transform our buildings into “materials banks” by designing components to be reused multiple times in multiple buildings. In Beyond Zero, authors Bruce King and Chris Magwood argue that “currently, we design and build in a way that leaves us no choice but to ruin materials in order to remove them…this isn’t inevitable. Buildings are designed this way. They can be designed differently in order to achieve different outcomes.”i
In terms of carbon reduction, the most effective strategies include increasing building life spans, reducing the need for new materials, and integrating materials which can be reused ii Adaptive reuse of existing buildings is a highly effective strategy for harnessing embodied carbon. The greenest building is the one which doesn’t have to be built, so taking advantage of existing building stock which can be retrofitted for new purposes is an ideal place to start. Even a renovation project, however, is likely to involve a change of building components for finishes, partitions, facades, and other requirements that could benefit from a DfD mindset. Where new construction is required, the stakes are even higher, and the DfD opportunities are even greater.
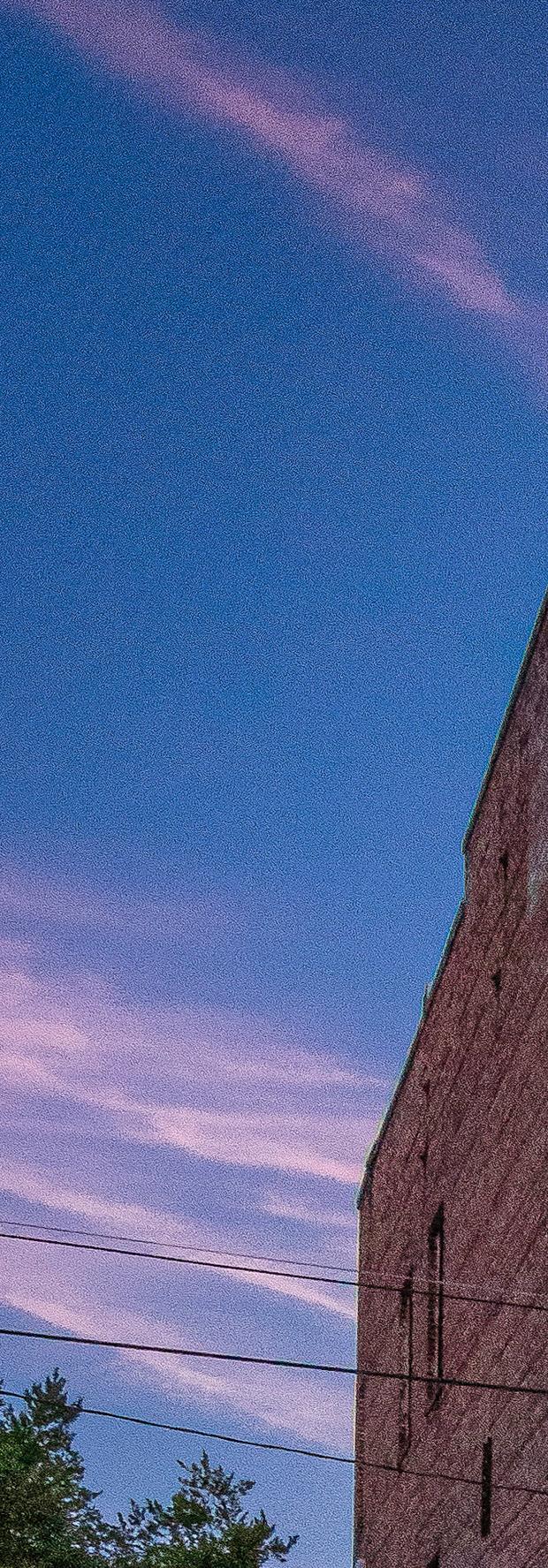
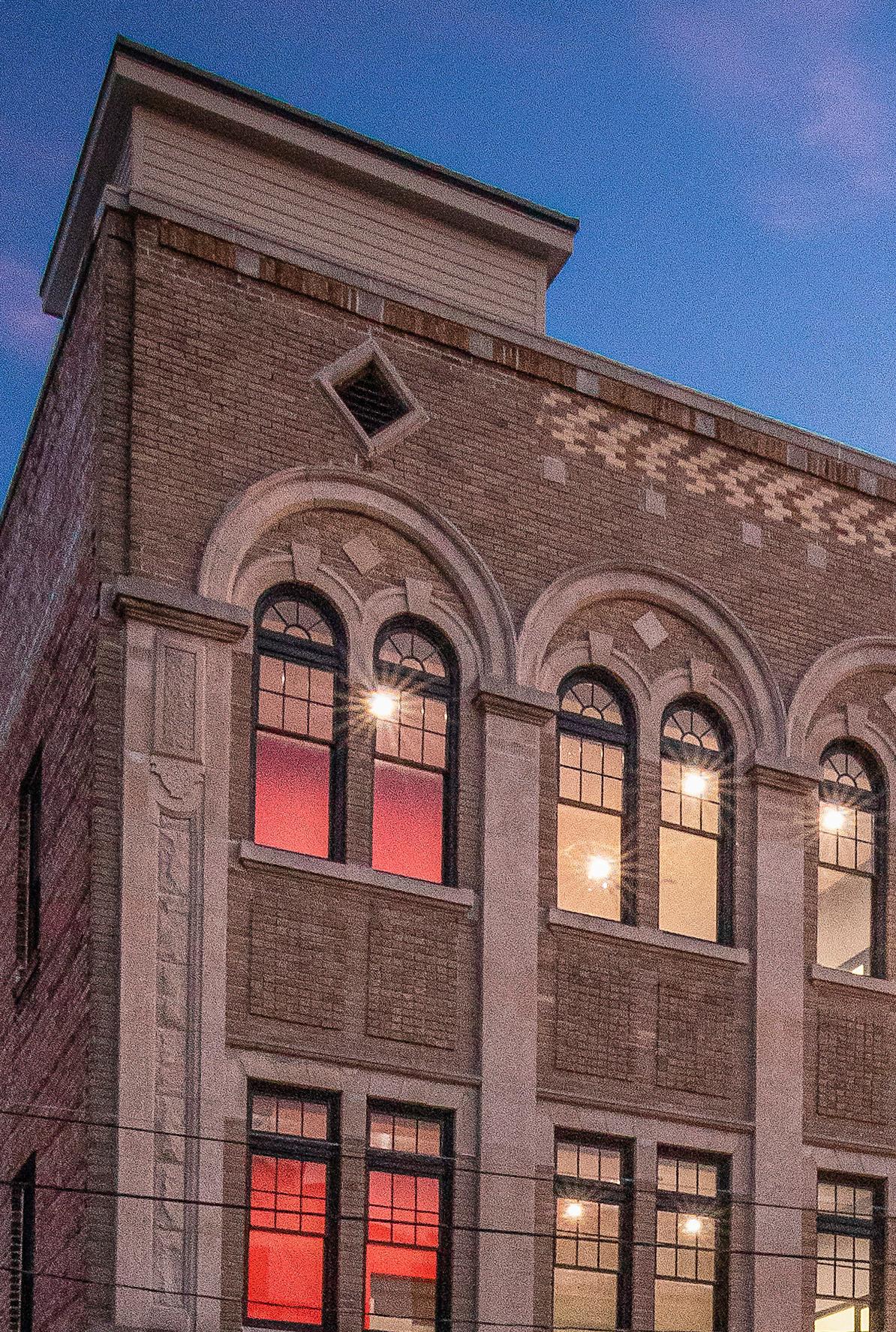
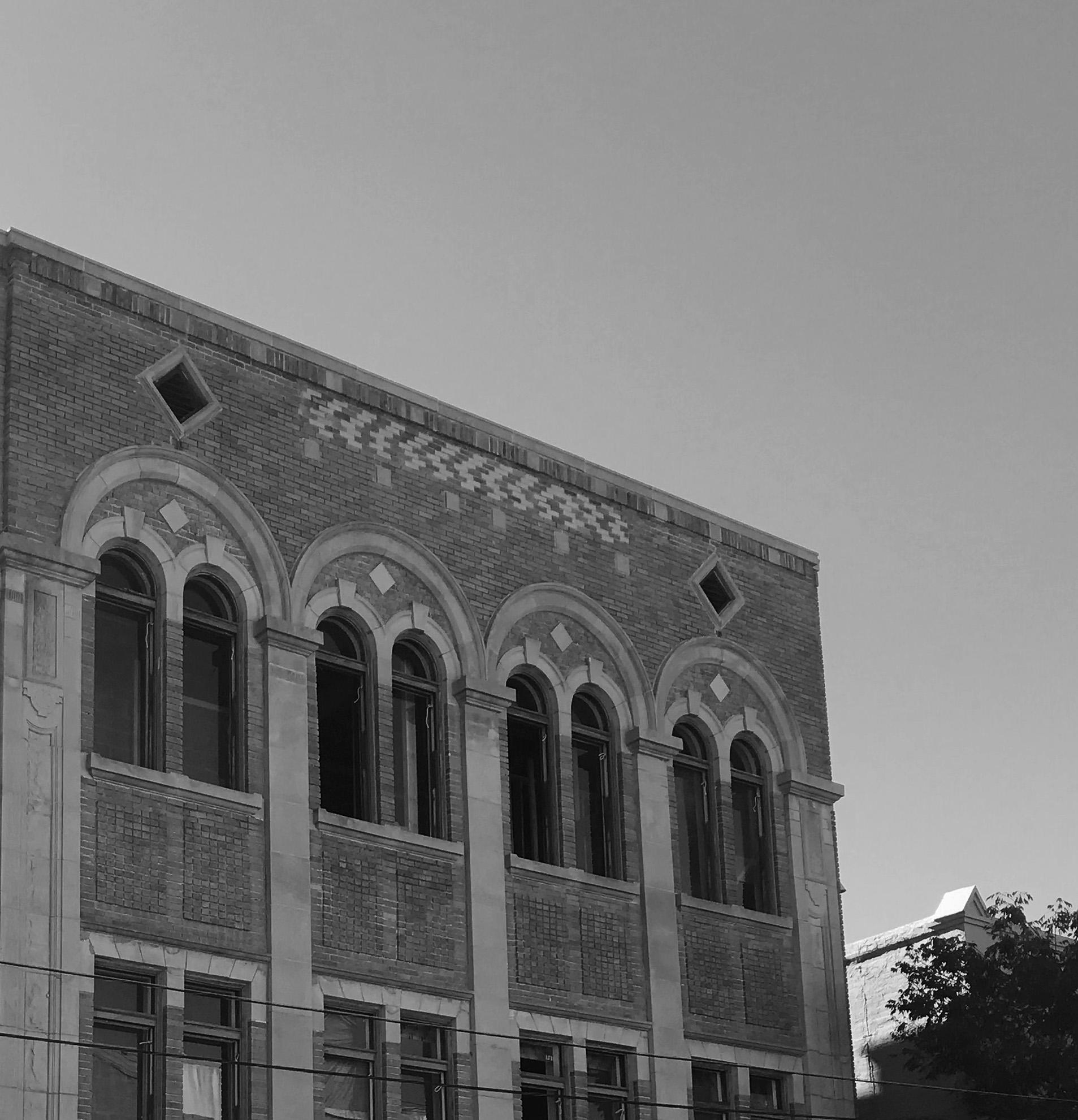
The concept of designing buildings to be taken apart, moved, and reassembled is an old one. Nomadic tribes move their village structures seasonally, military deployments are designed for rapid assembly and disassembly, and World’s Fair installations such as the Barcelona Pavilion have showcased cutting-edge design for their eras. Both vernacular and architectural designers have explored DfD in many contexts.
Translating this concept to today’s urgent needs opens the door to circularity in our
built environment, beginning with the earliest stages of design. The circular approach reduces materials impacts in two directions: first by minimizing the need for mining and extraction to create new construction materials, and second by reducing construction waste that ends up in landfills. DfD keeps building components in rotation across multiple building cycles; instead of being composed of singleuse items, DfD buildings can be thought of as “materials banks” that can be dismantled efficiently for future projects.
it’s time for innovative
thinking
How does it work?
Remembering that the greenest building is one that’s already built, the first question for a new project should be, “do we have to build a new building, or is there an existing building we can salvage?” The longer a building stays in use, the better. Adaptive reuse also provides an opportunity to showcase the history of timeless architectural elements as part of the design aesthetic. Another important question to ask, whether renovating or building new, is, “are we building something worth keeping?” Buildings that are beautiful, flexible, durable, and efficient can provide lasting value to their communities and are likely to endure.
When DfD is a priority, it should be addressed at all design phases.iii In predesign, the team should focus on aligning expectations, identifying key metrics, setting achievable goals, and conducting due diligence on DfD opportunities. During schematic design, the team should conduct a life cycle cost analysis and be sure that goals and project aesthetics are aligned. In design development and the construction documents phase, the details, specs, and MEP systems will need to be designed and coordinated to achieve DfD goals. In the construction administration and closeout phases, the team should create full as-builts and a detailed DfD manual to facilitate repairs, renovations, and eventual deconstruction.
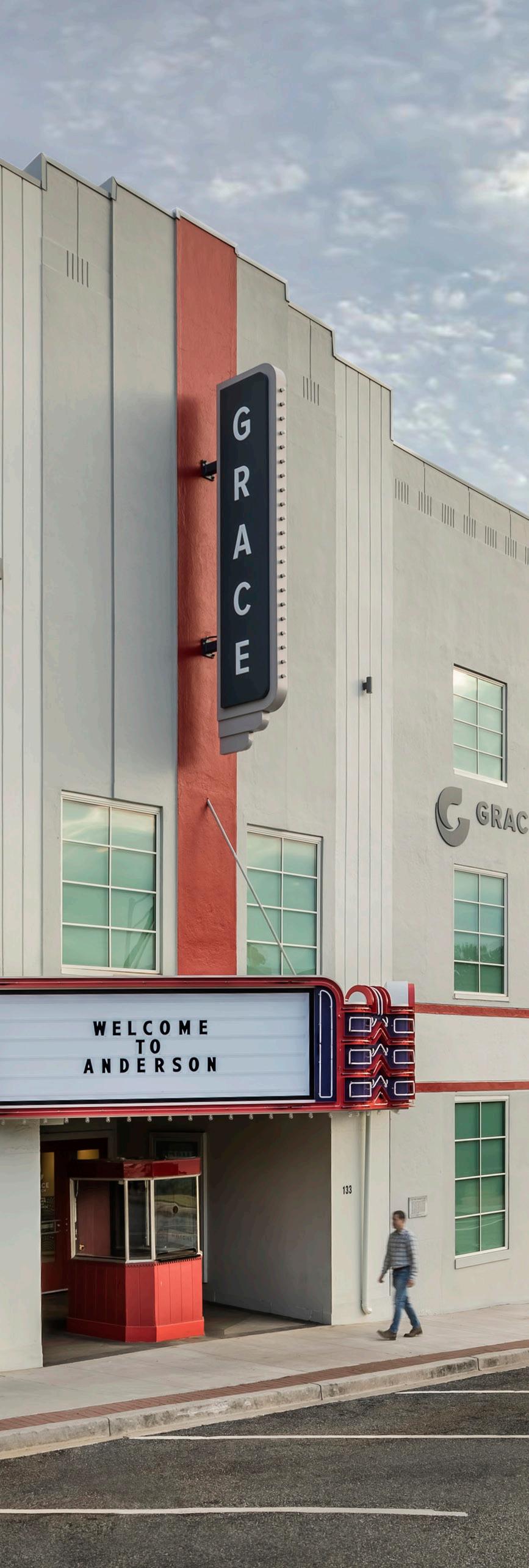
Separation of Systems
Intertwined systems are difficult to access for maintenance, repair, replacement, or removal. Careful design of structural, envelope, and MEP systems can prevent materials from becoming entangled. Systems such as plumbing and vertical circulation which are difficult to alter should be placed in centralized locations to allow for maximum flexibility for the rest of the floor plate. Designers should provide strategic access panels, or leave systems exposed, so that one component can be changed without damaging others. To the greatest extent possible, the envelope should be separate from the structure. If rooftop equipment or PVs are present, these should be mounted strategically to allow for roof repair and replacement. Noncomposite floors are preferable for DfD, but where concrete topping slabs are used over timber flooring, a slipsheet should be installed between layers for ease of separation.
a set of common design principles will make disassembly
easier
Materials
Some materials lend themselves better to DfD than others.
The general rule of thumb is to specify durable, high-quality materials, beginning with a foundation which will outlive the building. A foundation contains a significant portion of a building’s embodied carbon, so reusing it for future projects can greatly reduce carbon emissions. Structure is another key consideration.
Steel can be designed for disassembly without damaging individual structural members, particularly when bolted instead of welded. Though it is easy to disassemble and reuse, steel is often recycled and refabricated instead, which requires significant energy to melt and remanufacture. Where possible, reuse of steel members is a better choice.
Bricks are a popular choice for reuse due to the aesthetics of reclaimed brick and the convenient scale of the material. Historic bricks, typically assembled with lime-based mortar, are much easier to reuse than those assembled with Portland cementbased mortar and rebar.
Timber can easily be designed for disassembly and re-use. Nails can be challenging to remove, so components assembled with screws and bolts are preferable. Reuse of intact pieces of timber is preferable to downcycling into flooring or smaller components, which are harder to salvage for future projects and require energy to process. Designers should specify that wood products are not incinerated at end of life.
Insulated Metal Panels (IMPs) can typically be reused. Even if the joints and finish fail, the panel can be cut to a new size and reinstalled in a different application.
Concrete is inexpensive to reclaim, but cast-in-place concrete is typically downcycled as aggregate or landfilled. Precast panels, however, can be reused if installed with mechanical connections. Standard sizes and reinforcement make panels easier to reuse in future projects.
Resins, adhesives, and coatings should be avoided wherever possible. Instead, designers can select materials which minimize the need for additional finishes. Low-toxicity materials will provide better Indoor Environmental Quality (IEQ) and be safer for workers to disassemble.
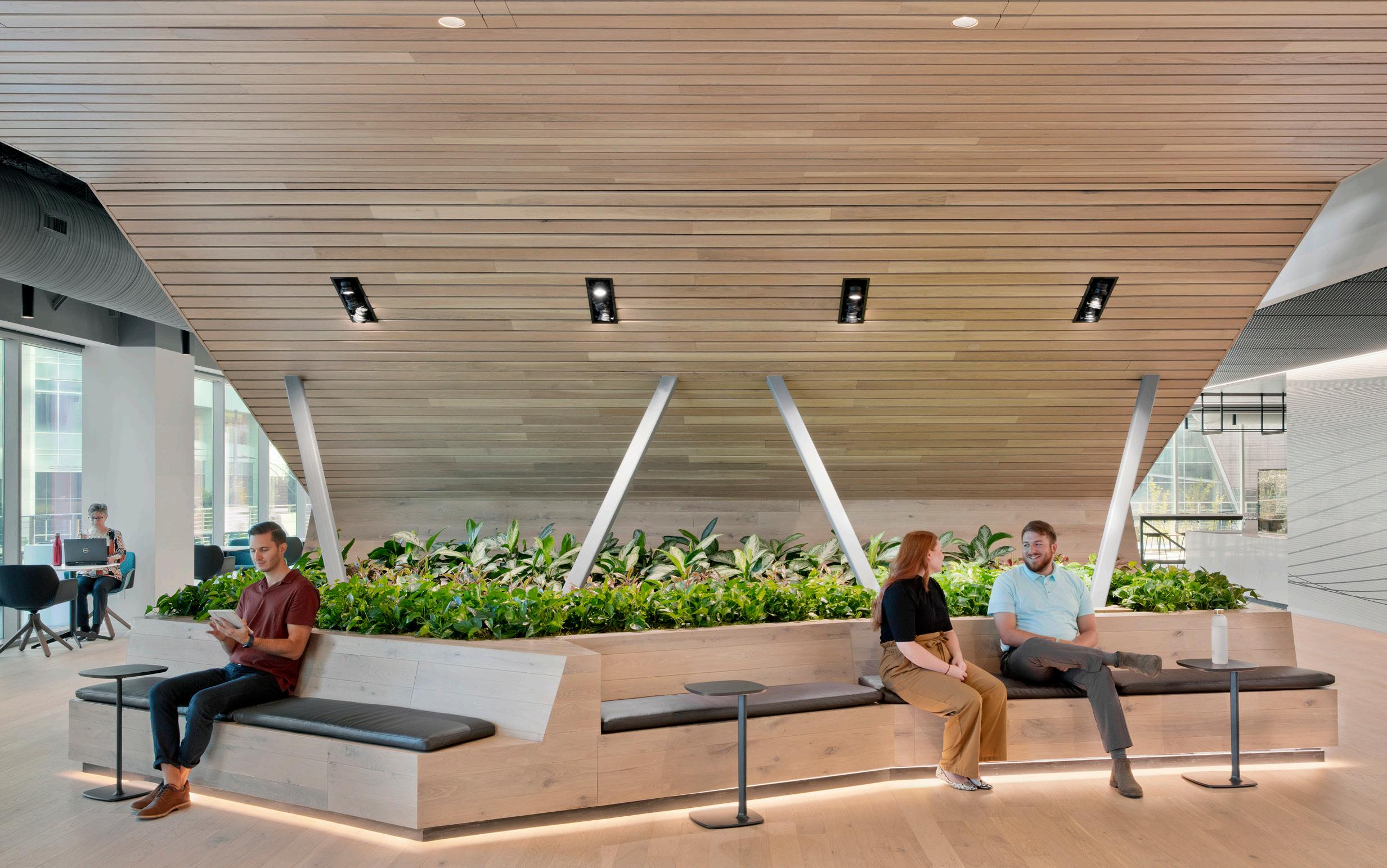
Long-term thinking at the beginning of the project can pave the way for DfD far into the future. Designers should integrate timeless materials with long lifespans rather than looking at short-lived trends which will quickly become dated. When materials are co-located, the lifespan of each material becomes even more important, and detailing must allow for one material to be repaired or replaced without damaging another. Building components which are reusable and recyclable should be permanently labeled.
Detailing and Assembly
In DfD, the type, quality, and number of connections are critical. The design should target fewer, stronger connections, and these connections should be exposed for easy access. With careful planning, these connections can become an attractive design feature. Mechanical connections are preferable, and highquality hardware makes for easier disassembly by minimizing stripped screws and other damage. Finishes and coatings should be minimized – especially those that cover connections. Where finishes are needed, choose installation options with minimal or no adhesives such as carpet tiles installed with tape rather than glues, or floating resilient flooring which typically requires less adhesive than standard installations.
Buildings are layered, and DfD requires careful consideration of the order of operations required to install, repair/replace, and eventually disassemble each layer. Components should be layered according to lifespan, iv and strategies such as exposed systems, crawl spaces, or plenum flooring can provide easy access to reduce the cost and collateral damage of maintenance, repairs, and renovations. Providing spare parts and dedicated storage will make required repairs easier.v
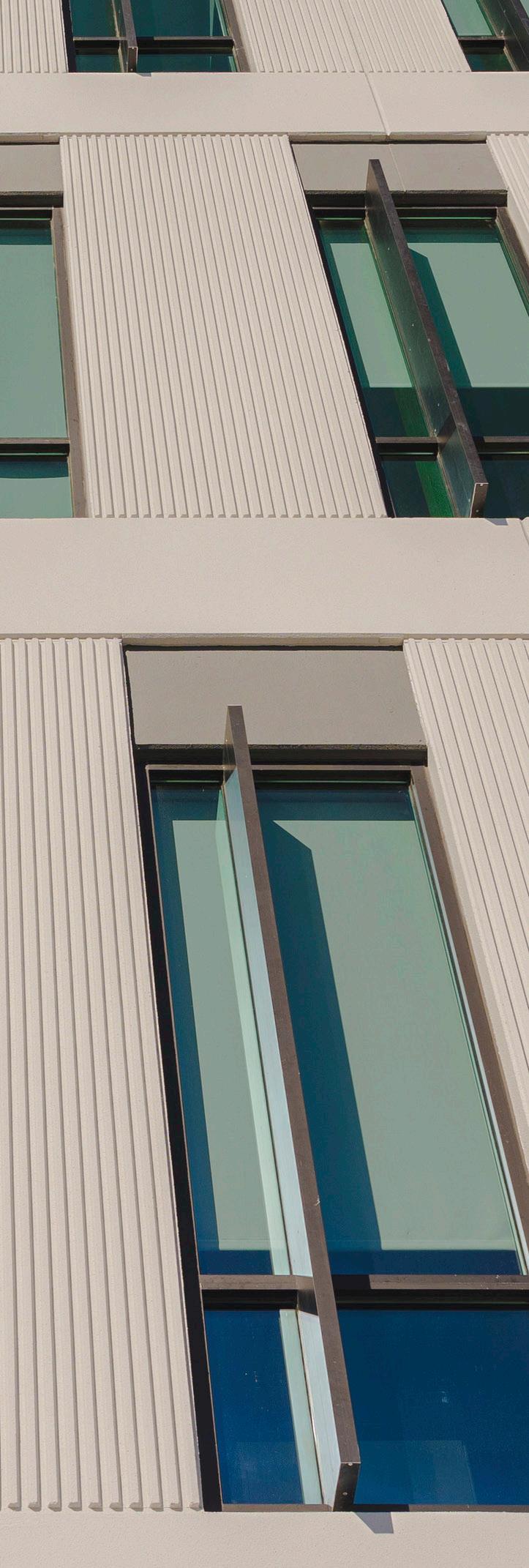
Design for Simplicity
Repeatable, standardized components with repetitive connections will make the building easier to assemble, easier to modify, and easier to deconstruct. Adaptability and flexibility of the building over time are key, and minimizing custom assemblies is also helpful. Materials should ideally be sized for manual handling and low skill. Modular and prefab elements may provide efficiency and flexibility. Minimizing the number of materials and components will also speed both assembly and disassembly.
Education, Communication, and Buy-in
DfD requires a high degree of coordination, so it’s important to align expectations with the whole team at the beginning of the process. The design team, owner, contractor, and consultants should all agree on the project’s DfD goals, which may require education to achieve full buy-in. Structural, architectural, interiors, and MEP designers will all work hand in hand to create a design and an effective order of operations for installation. The owner, design team, and contractor will need to collaborate closely on goals and parameters for detailed construction and deconstruction manuals which will stay with the building through changes of ownership. (Construction
means and methods which are beyond the scope of the architect, but the design team will provide general guidance while the contractor provides a clear methodology.) The deconstruction manual should include all as-built drawings and instructions for disassembly.
Options for Materials Reuse
Realistically, opportunities for reusing building components will vary according to local market conditions, and designating a material for reuse does not guarantee easy transfer into a new project nearby. To boost the likelihood that components can be reused once removed from the building, designers should prioritize materials which are easiest to recycle, and seek out vendors who offer take-back programs for their products. Some organizations such as Rheaply provide resources for cataloging, sourcing, and decommissioning materials and furnishings.vi Because storage of disassembled materials is a challenge, reclaimed materials warehouses are both a current need and future opportunity. Designers also increase the percentage of materials which get reused when they think about new ways to reimagine old materials, adding history and texture to their projects in the process. Another option: designers and contractors can collaborate on quick ways to separate building components using existing equipment to speed the process.
Waste Hierarchy
vii
These guidelines for reducing waste have been in use in the UK since the 1990s, and offer clear priorities for handling construction waste:
Prevention: Eliminate or reduce waste at the source to the greatest extent possible
Reuse: If waste cannot be prevented, products should be reused
Recycling: Where reuse is not possible, materials should be recovered for use as a secondary raw material
Recovery: If recycling is not possible, energy from the material should be recovered and used in place of other nonrenewable energy sources
Disposal: As a last resort, materials should be discarded according to regulations
benefits of designing for deconstruction
DfD yields benefits throughout a building’s lifecycle. During the construction phase, DfD can be safer for workers due to the simplicity of connections and the reduced need for adhesives and finishes. A flexible, adaptable structure makes design changes easier at any stage of a project. While a building is operational, DfD creates adaptability, making the building easier to repair, reconfigure, and renovate due to flexibility and ease of access for individual building components. When the building components (or the whole building) have reached the end of their service life, DfD means that most materials can be removed and reused elsewhere.
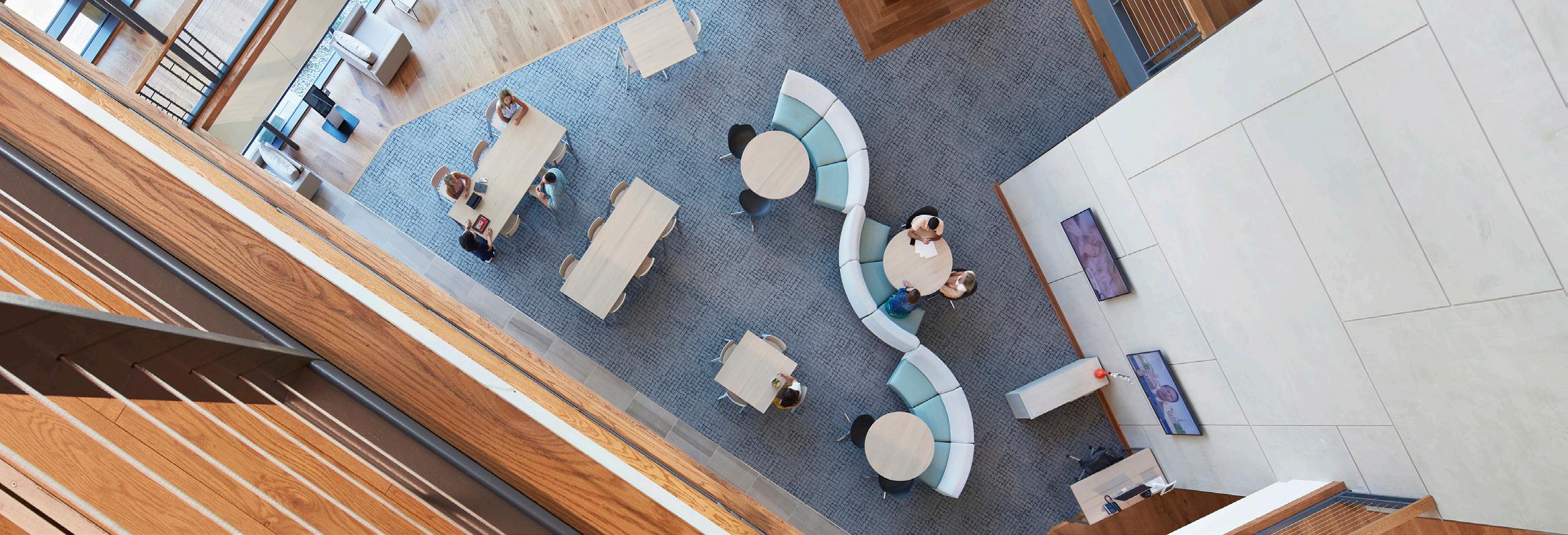
Disassembly rather than demolition avoids landfill tipping fees and landfill impacts, while a growing market for reusable components means materials retain some value after the building is dismantled. The disassembly site is less toxic than a typical demo site for workers, and the evolving salvage economy has the potential to create desirable jobs for unskilled workers.viii
When the disassembled components are eventually reused in another building, DfD can significantly reduce
carbon emissions by reducing the need for extraction, transport, and manufacturing of new materials and the associated environmental and human impacts. Furthermore, a growing market means increasing options: items such as furniture and tech equipment are already available for lease rather than purchase, and manufacturers of other goods such as carpeting are following suit. Taking advantage of these options may be beneficial to a projects’ life cycle assessment (LCA) and may assist with achieving a Building Life Cycle
Impact Reduction credit for LEED certification.
As interest in circular projects grows, so will the resources to support circular and lower embodied carbon product options. The Inflation Reduction Act, for example, is already incentivizing research through federal grants supporting data and tools, including support for Environmental Product Declarations (EPDs) for both salvaged and new materials.ix
challenges of designing for deconstruction
DfD comes with real challenges as well as benefits. New ways of thinking and working will require education and training, and the complexities of designing for a building’s end of life before it’s built requires time to research and coordinate. The palette of appropriate materials will be more limited than with traditional linear construction, and designers wishing to source salvaged materials at the beginning of a new project may have to deal with hazardous materials such as lead paint or polyvinyl chloride which are durable, long lasting, and harmful to human health. Other salvaged materials may be damaged by adhesives or the demolition process.
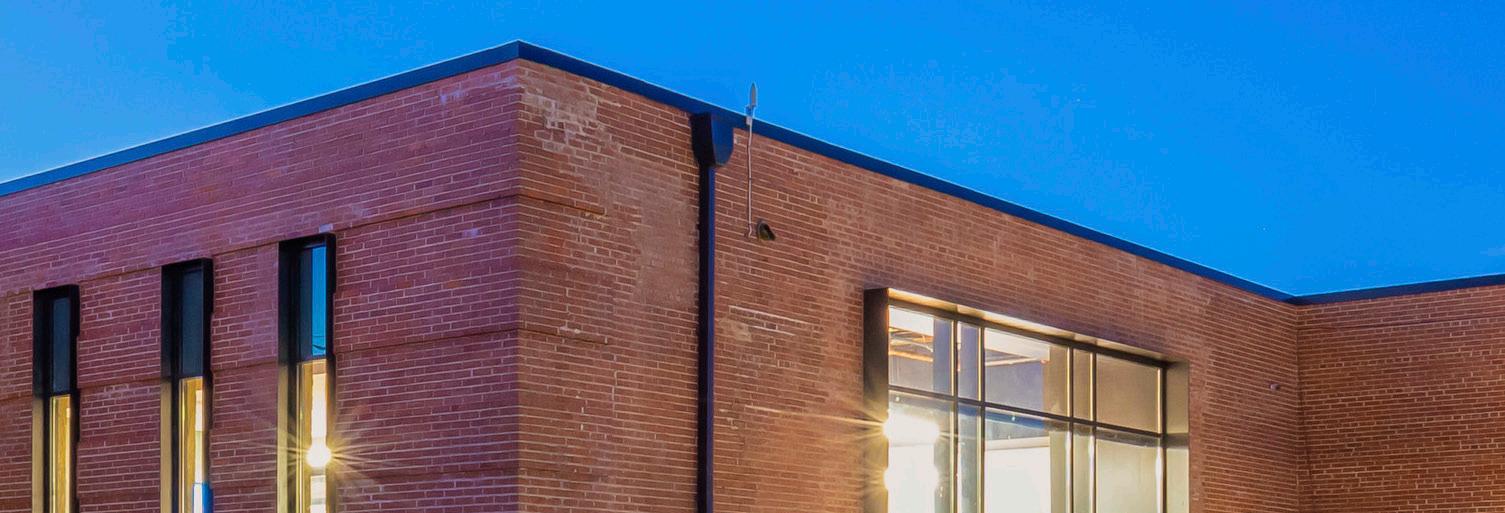
Designing and constructing exposed connections requires time and skill. At the end of a building’s lifecycle, disassembly takes more time than demolition. Both value and ease of recovery matter at this stage; for example, cast-in-place concrete may be easy to reclaim and crush for future aggregate, but is bulky and has low economic value. Other materials such as wood paneling may require more time and precision to salvage, but have much higher value.x In planning for future reuse, designers and owners must weigh the value of
salvaged materials (economic, environmental, and cultural) against the cost of labor
The reusability of materials is not guaranteed. The salvage economy currently varies widely by market (for example, brick is frequently reused in Chicago due to the number of old brick buildings constructed with lime mortar, but it may be less available in other cities). Also, when materials are removed from a disassembled building, they must be handled, transferred, stored, and then reinstalled, which potentially adds time and cost. xi The
market for reclaimed materials is growing, but currently lacks a unified infrastructure and is unpredictable across the decades of a building’s anticipated lifespan.
drawing conclusions
Adopting a Circular Mindset
Whether as part of an adaptive reuse, renovation, or new construction project, adopting a circular mindset can have substantial positive impacts for current and future buildings. Every component that can be removed intact and reused recaptures embodied carbon and lowers environmental impacts for the next project. When we begin to shift our mindset to think of our buildings as material banks for the future, we create exciting possibilities to drive positive change in the industry.
case study: confidential industrial client

This factory and office building client prioritized a circular mindset from the inception of the project. The European client’s design guidelines specify building components to be assessed (at a minimum) for eventual disassembly and reuse. The design team, owner, and contractor collaborated on DfD goals and parameters; the DfD plan ultimately relies on the contractor’s waste management professional to help inform the process of disassembly for reuse, as means and methods are outside the scope of the architect.
The design included a simplified structure and connections, and MEP systems are separated wherever possible. The insulated metal panel (IMP) walls can be disassembled and re-cut to desired size for future projects. A slip sheet separates timber flooring from the concrete topping slab for eventual disassembly. Mechanical fasteners are used instead of adhesives for ease of deconstruction. The steel structure is welded, and the steel is likely to be remelted when the building is demolished.
The design also balanced optimization of the structure with the desire for uniformity of structural members. Some areas of the building prioritized cost and material through smaller beam span depths and smaller structural members. In these areas, CLT panels and steel structural members could be more difficult to reuse due to size variation.
The client is pursuing LEED and WELL certification for the projects; both programs incorporate strategies to reduce material toxicity within the building. The
design is also informed by European protocols including Registration, Evaluation, Authorisation and Restriction of Chemicals (REACH) and Substances of Very High Concern (SVHC).
The client plans to retain construction and deconstruction information on its digital platforms to help future salvagers understand the opportunities of the building as a material bank 60100 years after construction.
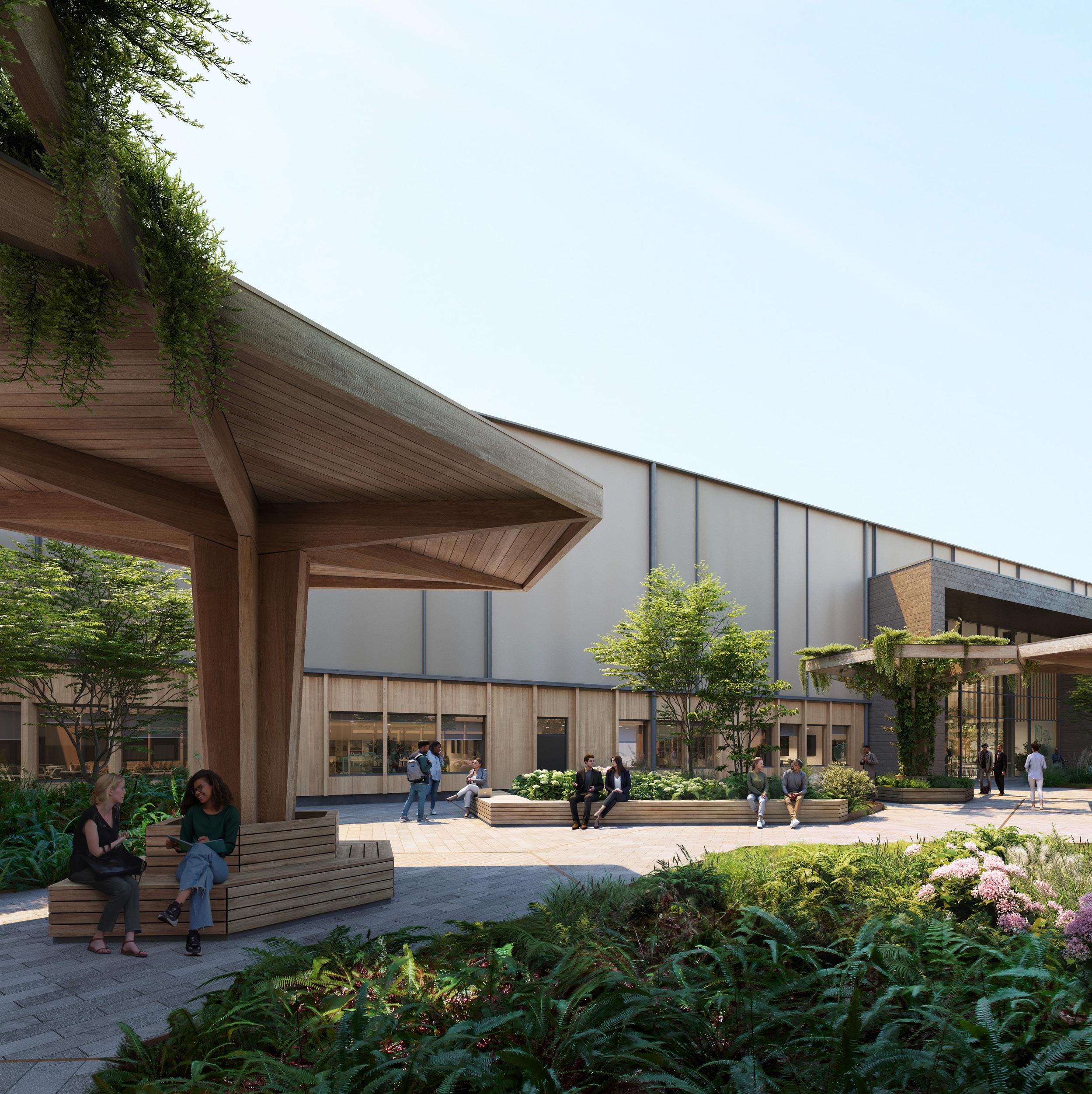
Adaptability “the ability of a space to be modified for uses beyond its original purpose.” xii
Adaptatationxiii “the adjustment in natural or human systems in response to actual or expected climatic stimuli or their effects, which moderates harm or exploits beneficial opportunities.” xiv
Adaptive Reuse the “redesign and alteration of a building to support a new function it was not originally intended to serve.” xv
Circular Economy “an economic model supporting a closed-loop system of material reuse through market-based means.” xvi
Closed Loop the process of designing with materials that can be reused repeatedly.
Cradle to Cradle a phrase coined by environmentalist William McDonough to describe a theoretically endless cycle of material reuse.
Deconstruction “the careful removal of building materials to retain their integrity and value at the end of a building’s service life.” xvii
Demolition the process of dismantling a building, often by heavy equipment; materials are typically destroyed and landfilled as part of the process
Downcycling the process of reassembling materials into lowervalue items, typically beotecause they can not be recycled as items of a similar strength or quality (for example, plastic grocery bags being collected and melted into grocery checkout dividers because the material is too degraded to be used as new bags).
Embodied Environmental Impacts the environmental costs of creating materials.xviii These include the impacts of raw materials extraction, transportation, manufacturing, installation, operation, and disposal.
Lice Cycle Assessment (LCA) calculates the environmental impact of an item across its entire lifecycle.
Life Cycle Building the concept of designing a building for many iterations, including deconstruction and eventual reuse of material.
Life Cycle Cost Analysis (LCCA) a cost calculation which accounts for the entire life of a product, including cost of purchase, installation, operation, maintenance, repair, and eventual disposal.
Life Cycle Cost Effectiveness (LCCE or LCC-Effectiveness) measures all economic costs and benefits of an item including research and development, operations and maintenance, and disposal. xix
Material Bank concept of a building being designed to use and store materials which are intended to be harvested for future construction.xx
Material Reuse “use of materials salvaged during construction, deconstruction, or renovation for either the same or different purposes.” xxi
Recycling reusing a material for the same purpose for which it was manufactured (for example, aluminum cans being reclaimed and turned back into aluminum cans).
Reusing using an item for the same purpose multiple times (for example, washing and reusing Ziplock bags to prolong their use).
Salvaging reclaiming a material that would otherwise have been discarded (for example, removing a fireplace mantel from a building planned for demolition).
Upcycling repurposing a material for a higher value purpose than its original use (for example, making haute couture fabrics from plastic bags).
Additional Resources
US EPA’s Deconstruction Manuals for Construction and Demolition (C&D) Projects
Rheaply’s Materials Marketplace
AIA’s Buildings that Last: Designing for Adaptability, Deconstruction, and Reuse
Works Cited
King, Bruce and Magwood, Chris. “Beyond Zero.”
ii European Environment Agency. Modified March 25, 2024. “Buildings and Construction.” https://www.eea.europa.eu/en/topics/in-depth/buildings-andconstruction .
iii Guy, Brand and Ciarimboli, Nicholas. Hamer Center for Community Design: University of Pennsylvania. DfD: Design for Disassembly in the Built Environment
iv Kanters, Jouri. Design for Deconstruction in the Design Process: State of the Art. November 6, 2018
v Guy, Brand and Ciarimboli, Nicholas. Hamer Center for Community Design: University of Pennsylvania. DfD: Design for Disassembly in the Built Environment
vi Materials Marketplace - Rheaply. Accessed August 20, 2024.
vii Morgan, Chris and Stevenson, Fionn. 2005. “Design for Deconstruction: SEDA Design Guides for Scotland.”
viii Kanters, Jouri. Design for Deconstruction in the Design Process: State of the Art. November 6, 2018
ix US EPA. July 16, 2024. “ Biden-Harris Administration Announces Nearly $160 Million in Grants to Support Clean U.S. Manufacturing of Steel and Other Construction Materials .” https://www.epa.gov/newsreleases/biden-harris-administrationannounces-nearly-160-million-grants-support-clean-us#:~:text=WASHINGTON%20 %E2%80%93%20Today%2C%20July%2016%2C,of%20construction%20materials%20 and%20products.
x American Institute of Architects. N.d. “Buildings that Last: Design for Adaptability, Deconstruction, and Reuse. Accessed July 30, 2024. https://www.aia.org/ resource-center/design-adaptability-deconstruction-reuse
xi Morgan, Chris and Stevenson, Fionn. 2005. “Design for Deconstruction – A SEDA Design Guide for Scotland.” chrome-extension://efaidnbmnnnibpcajpcglclefindmkaj/ https://static1.squarespace.com/static/5978a800bf629a80c569eef0/t/5aa999f7652deaa43 0532afd/1530223259684/Design+%26+Detailing+for+Deconstruction.pdf
xii American Institute of Architects. N.d. “Buildings that Last: Design for Adaptability, Deconstruction, and Reuse. Accessed July 30, 2024. https://www.aia.org/ resource-center/design-adaptability-deconstruction-reuse
xiii American Institute of Architects. N.d. “Buildings that Last: Design for Adaptability, Deconstruction, and Reuse. Accessed July 30, 2024. https://www.aia.org/ resource-center/design-adaptability-deconstruction-reuse
xiv UN Intergovernmental Panel on Climate Change. N.d. “Introduction.” Accessed July 8, 2024. https://unfccc.int/topics/adaptation-and-resilience/the-big-picture/ introduction#:~:text=Adaptation%20refers%20to%20adjustments%20in,climatic%20 stimuli%20and%20their%20effects.
xv American Institute of Architects. N.d. “Buildings that Last: Design for Adaptability, Deconstruction, and Reuse. Accessed July 30, 2024. https://www.aia.org/ resource-center/design-adaptability-deconstruction-reuse
xvi American Institute of Architects. N.d. “Buildings that Last: Design for Adaptability, Deconstruction, and Reuse. Accessed July 30, 2024. https://www.aia.org/ resource-center/design-adaptability-deconstruction-reuse
xvii American Institute of Architects. N.d. “Buildings that Last: Design for Adaptability, Deconstruction, and Reuse. Accessed July 30, 2024. https://www.aia.org/ resource-center/design-adaptability-deconstruction-reuse
xviii American Institute of Architects. N.d. “Buildings that Last: Design for Adaptability, Deconstruction, and Reuse. Accessed July 30, 2024. https://www.aia.org/ resource-center/design-adaptability-deconstruction-reuse
xix Mckillop, Riley. May 6, 2021. “ Life Cycle Cost-effectiveness (LCC-effectiveness) – The New Federal Standard for Climate Resilient Projects.” https://autocase.com/life-cyclecost-effectiveness-lcc-effectiveness-the-new-federal-standard-for-climate-resilientprojects/
xx BAMB: Buildings as Material Banks. N.d. “Enabling a Circular Building Industry.” Accessed July 8, 2024. BAMB - Buildings As Material Banks (BAMB2020) - BAMB
xxi American Institute of Architects. N.d. “Buildings that Last: Design for Adaptability, Deconstruction, and Reuse. Accessed July 30, 2024. https://www.aia.org/ resource-center/design-adaptability-deconstruction-reuse