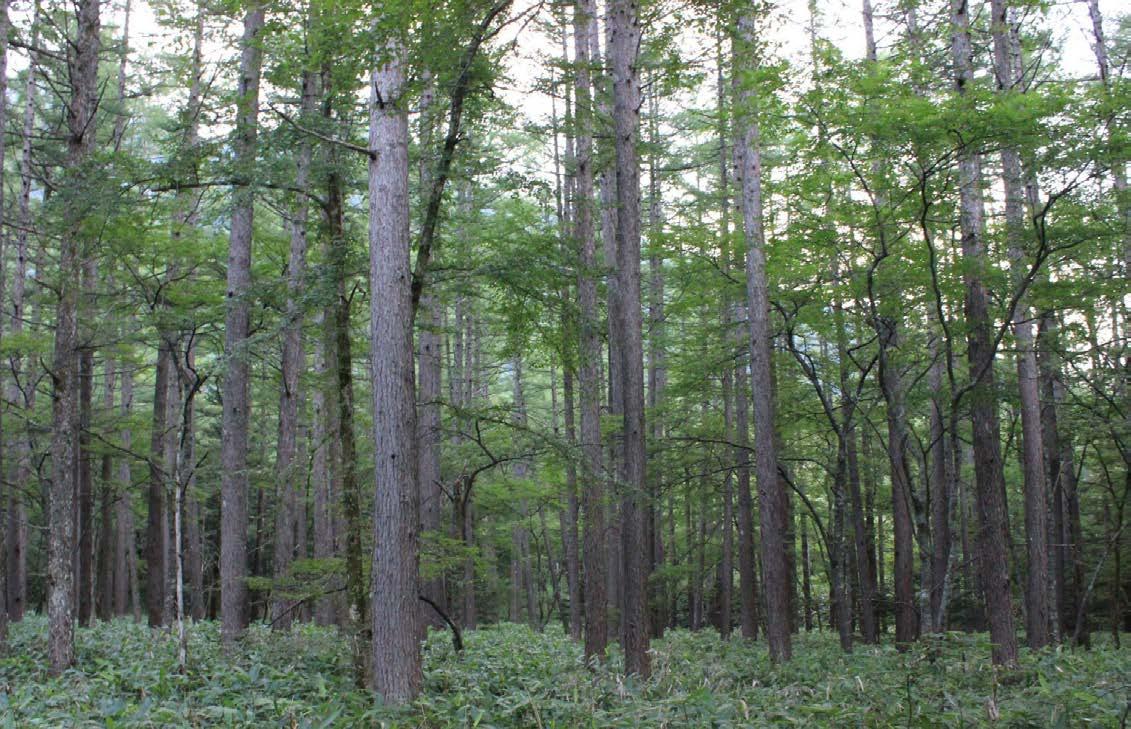
6 minute read
INTRODUCTION
from Research by Design
History: Japanese Joinery
Throughout Japan you can utter the word kodama and all around you will know it. “The spirit of a tree.” It remains a term still relevant today, undoubtedly a product of the country’s rich history deeply entrenched in a reverence for all things natural.1 Japan is dominated by volcanic soil that hostorically provided little for masons but an endless veriety of trees for carpenters. To no surprise, the vernacular architecture leans heavily timber. Japanese joinery was born of circumstance.1 Iron fasteners were rendered ineffective by Japan’s high humidity, paving the way for the development of tsugite and shiguchi — splicing and connecting joints that do not rely on glue, nails, or screws.1
Advertisement
The first examples of Japanese joinery can be found dating back to 3000 BCE with the construction of simple timber stuctures framed over pits and covered in thatching, though it was not until the advent of iron tools in the Yayoi period (250 BCE-200 CE) that Japanese joinery, as we know it today, began to take form. Over the next millenium, family guilds organized with each specializing in different typologies, and the unification of the country under a single banner fostered the spread of information and techniques throughout. Consequently, the varied design and engineering requirements of the many types of structures resulted in hundreds of distintcly different joints, many of which remained largely out of reach of the public domain.2 The guild system was fiercly competitive and perpetuated a culture of guild trade secrets, the effects of which can still be seen today. Though, at the core of these guilds still remained the craft, one of which its craftsmen showed immense respect.
The Japanese carpenter did not enter an apprenticeship, he entered a way of life. From the moment a tree was felled, a strict and disciplined process began that echoed the care and beauty clearly visible in a completed joint. This same reverence can also be found in the tools used to fashion the wood. Historically, a carpenter’s instruments were refered to as dogu, or “instruments of the Way”. The word tool did not show adequate respect to the means of the craft, but rather demoted it.2
Traditional joinery would continue to dominate the architectural landscape in Japan up until the Second Industrial Revolution.
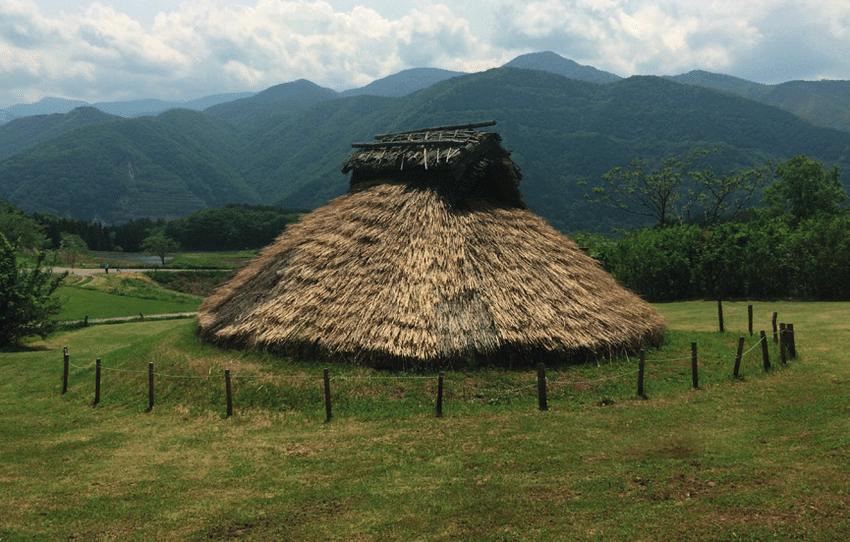


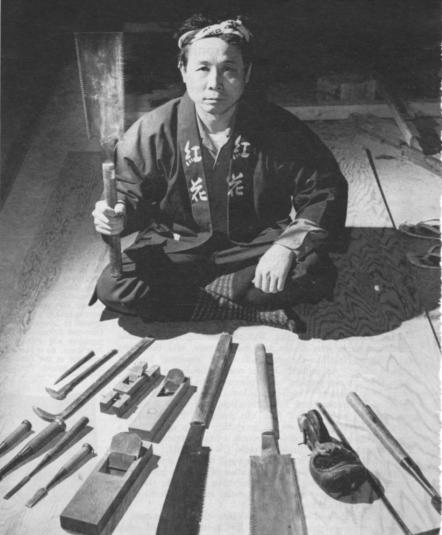
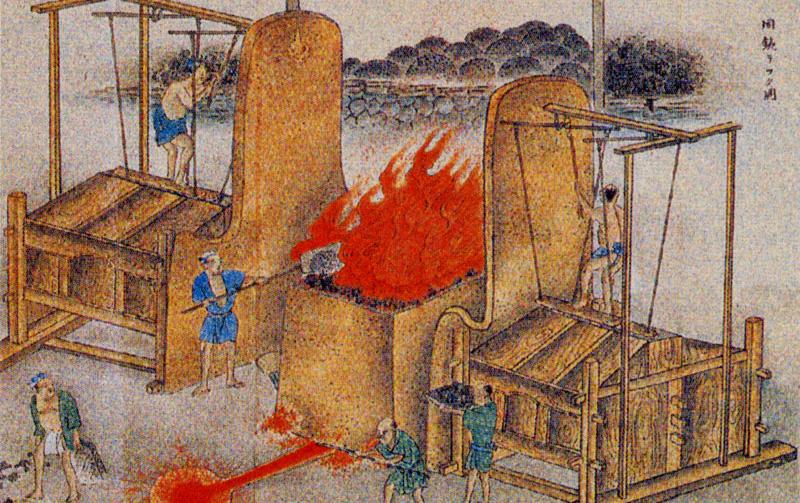
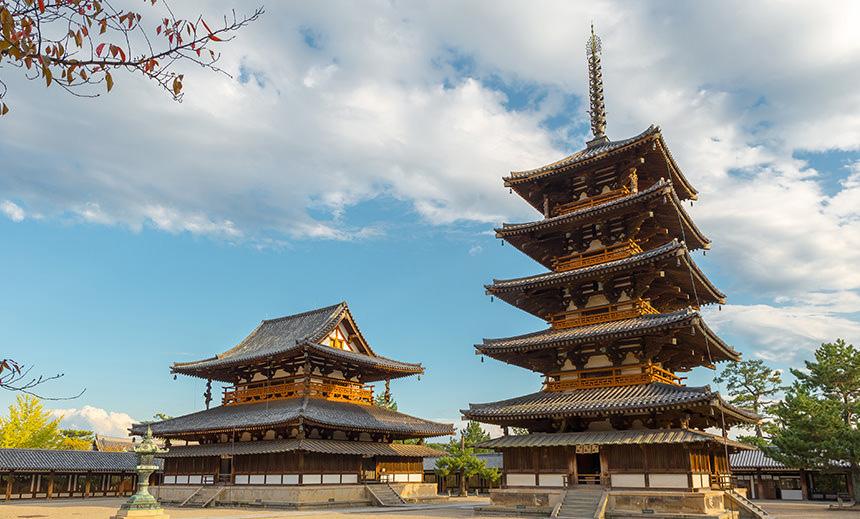

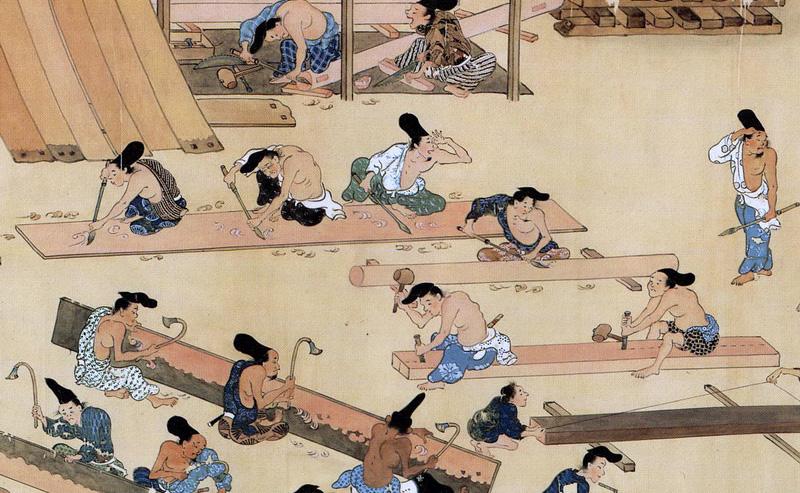
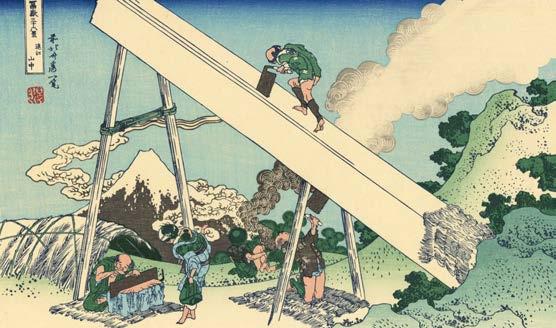
History: CNC Routing
The history of computer numerical control can be traced back to 1775 when John Wilkinson invented the first machine tool. A simple design, by today’s standards, that bore cylinders for steam engines set off a cascade of innovation. Contemperaneously, Joseph Jacquard was laying the foundations for modern computing by revolutionizing the loom industry. He found a way to control looms by encoding data on paper cards through a series of punched holes.1 Analog systems would continue to develop over the next two centuries, but it was not until 1952 that the real revolution began behind the innovation of the father of numerical control himself, John T. Parsons.
Parsons, in conjunction with the Massachusetts Institute of Technology (MIT), would for the first time ever wire a digital computer to a milling machine. This, by definition, created the first numerically controlled machine tool. By replacing a machinist with a computer program, the team was able to produce aircraft components more complex than by any means otherwise.2 By 1972, the development of Computer Aided Design (CAD) and Computer Aided Machining (CAM) pushed the fabrication method further, though it wasn’t until 1976 when 3D computer-aided design were incorporated into CNC machining. Further still, the technology continued to grow with the launch of the Enhanced Machine Controller project, or LinuxCNC, that enabled general purpose computers to run personal CNC machines.3
Today, CNC machines can work in up to 6 axes and can cut a plethora of materials. It can be assumed with great certainty that almost every commercial product on the market has been directly or indirectly touched by CNC machining.
1 Mohammadi, Goli. “History of CNC Machining.” Medium, April 12, 2019. https://medium.com/cnc-life/history-of-cnc-machining-part-12a4b290d994d
2 Gershenfeld, Neil. “How to Make Almost Anything: The Digital Fabrication Revolution.” Foreign Affairs 91, no. 6 (November 1, 2012): 43–57. https://search.ebscohost.com/login.aspx?direct=true&AuthType=ip,shib&db=edshol&AN=edshol.hein.journals. fora91.114&site=eds-live&scope=site.
3 Bethany. “How CAD Has Evolved Since 1982.” Scan2CAD, June 28, 2019. https://www.scan2cad.com/blog/cad/cad-evolvedsince-1982/
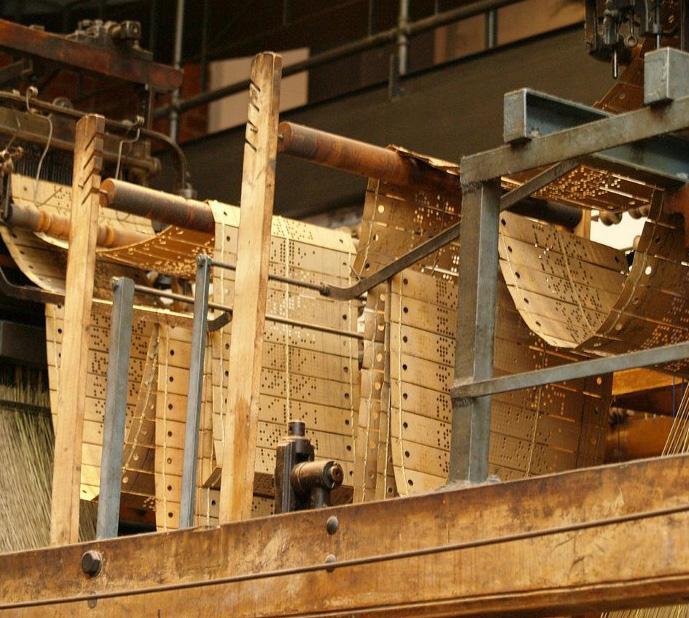
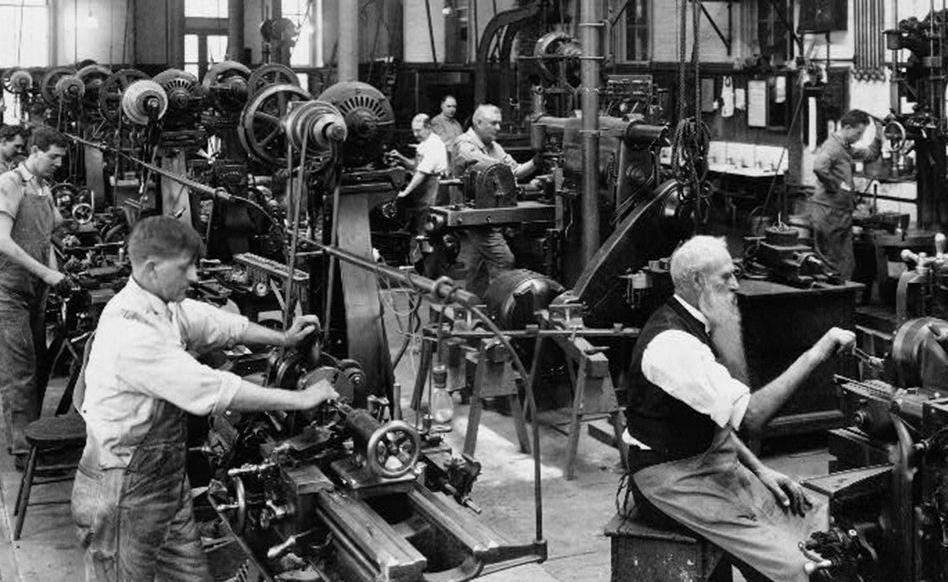
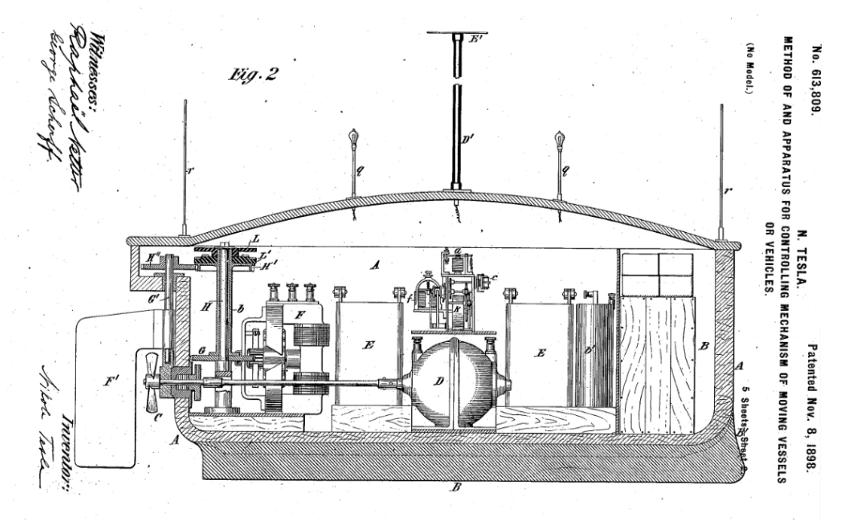
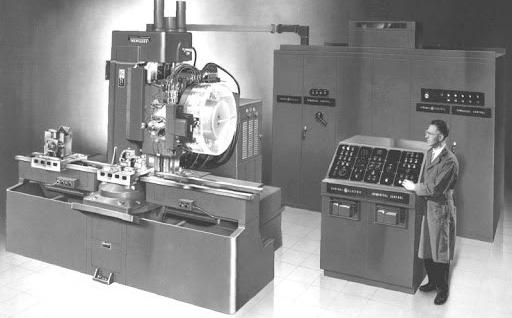

Current Status: Japanese Joinery
Although beautiful and resilient, Japanese joinery has become less common in the modern architectural landscape. The advent of mass prodution and the industrial revolution rendered many time consuming crafts obsolete in a society now concerned with economic growth and efficiency at scale. Nevertheless, the craft is still practiced sparingly as a construction method, but remains more common in furniture and small craft design. Some modern works take inspiration from the traditonal craft, though the heavy lifiting of structure is now typically left to concrete and steel.1 Most notably, Kengo Kuma used tsugite as a central element in the design of the Prostho Museum Research Center in Kasugai-shi, Japan.
Current Status: CNC Routing
Whether you know it or not, almost every commercial product that you own has been directly or indirectly fabricated by a numerically controlled machine. Everything from laptop cases to tools that mold mass produced goods are touched by fabrication method.2 Today, CNC machines have advanced far beyond the machines of old. 5-axis machines are at the cutting edge, fabricating extremely detailed geometries at incredible speeds. The increasing intuitiveness of CAD and CAM softwares has increased efficiency and accuracy, while also seamlessly integrating into the machine platform that run them. This has lowered the barrier of entry to understand and operate what used to be much more technical machinery.3
2 Gershenfeld, Neil. “How to Make Almost Anything: The Digital Fabrication Revolution.” Foreign Affairs 91, no. 6 (November 1, 2012): 43–57. https://search.ebscohost. com/login.aspx?direct=true&AuthType=ip,shib&db=edshol&AN=edshol.hein.journals. fora91.114&site=eds-live&scope=site.
3 Fast Radius. “5 CNC Machining Trends to Watch Out for in 2021.” Fast Radius. November 30, 2020. https://www.fastradius.com/resources/cnc-machining-trends-2021/

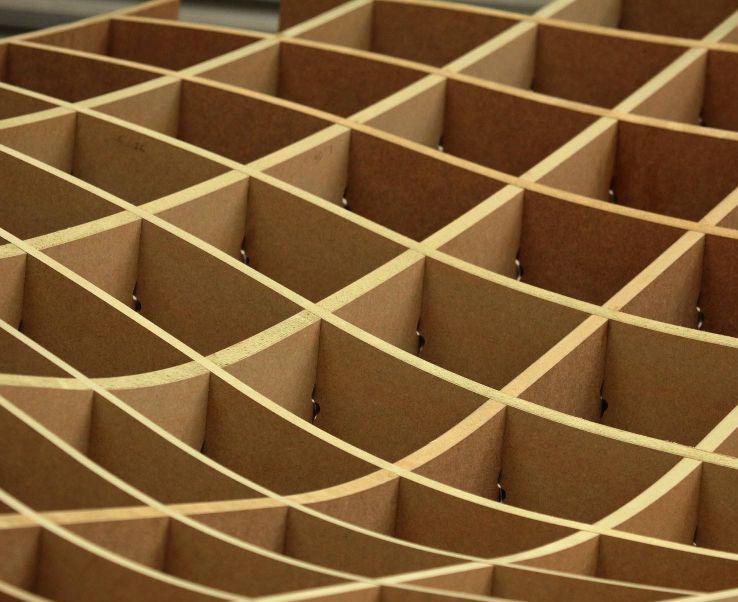
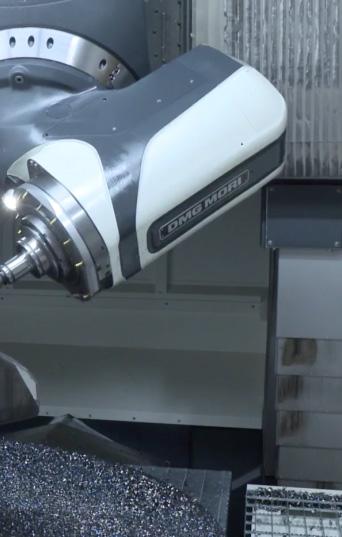
Methods
Process: Japanese Joinery
From selecting the wood to hammering in the final tenon, the Japanese carpenter follows a detailed process that focuses less on the end result and more on the process itself. In The Complete Japanese Joinery, Hideo Sato tells us:
“
...one should truly enjoy one’s work. It is also important to remember that wood is a living thing — one must understand its properties and not oppose them. Whenever work is forced, it either ruins the piece, damages the tools, or injures the worker, so work must always be done with the utmost care.”1
Despite the immense amount of training and technique required to construct even one joint, Japanese joinery can be viewed as a philosphy just as quickly as it can a technical craft. This is an important distinction to note. For the purposes of this brief, the following will outline the construction of one joint and will exclude much of the early steps involved in processing the lumber, as this research is more narrowly focused on the joinery crafts of tsugite and saguchi.
Kanawa Tsugi Blind dadoed, rabbetted and keyed scarf joint. This is a common end joint for girders and the base of columns.
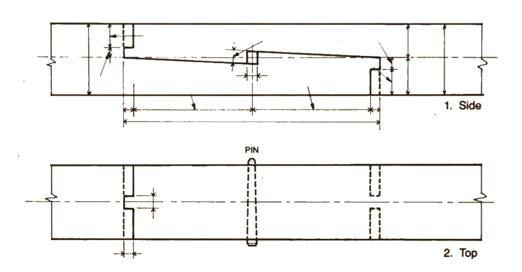
2. Procedure
i. Draw cut lines ii. Ripsaw kerf along A to intersect B iii. Cut along B and C to intersect D with a crosscut saw
Scarf joint step 1 (Sato 1995)
Scarf joint step 2 (Sato 1995) iv. Chisel out from C to B. Then make a rip saw kerf at E v. Finish chiselling the notch to line F vi. Slope kerf with rip saw on both sides vii. Chisel diagonally where marked
Scarf joint step 3(Sato 1995) vi. Rip saw kerf along J to intersect F vii. Chisel diagonally where marked viii. Assemble
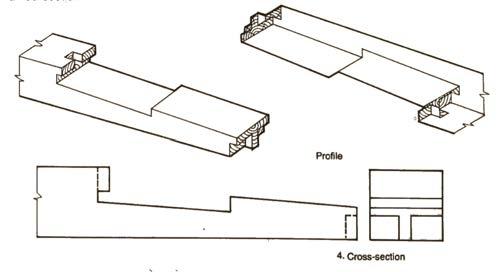
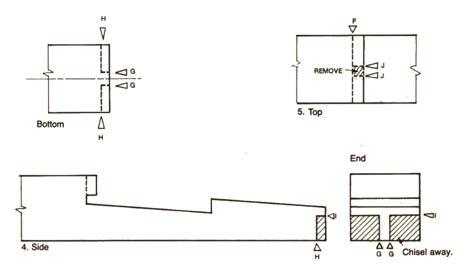
Scarf joint step 4 (Sato 1995)
Process: CNC Routing
Although the process is vastly more advance, computer numberical control design can be broken down into 3 basic parts — input, process, and output. A computer, the input, is used to design what is to be routed using CAD or CAM softwares. Next, an interface, or the process, connecting the software to the CNC machine is used to break down the input into a set of coordinates that the CNC mahcine can use to cut materials. The CNC machine, or the output, uses the signals generated by the interface to move in the X, Y, and Z directions to cut the materials placed on the machine.1 Of course, as it is with all things, the actual process is not so simple. The following pages of this section will demonstrate the process used to generate the first joint as part of this research.
1. Input — Rhino 7
i. Generate a 3d model within the parameters of the CNC machine ii. Break the model into the individual parts required for the output
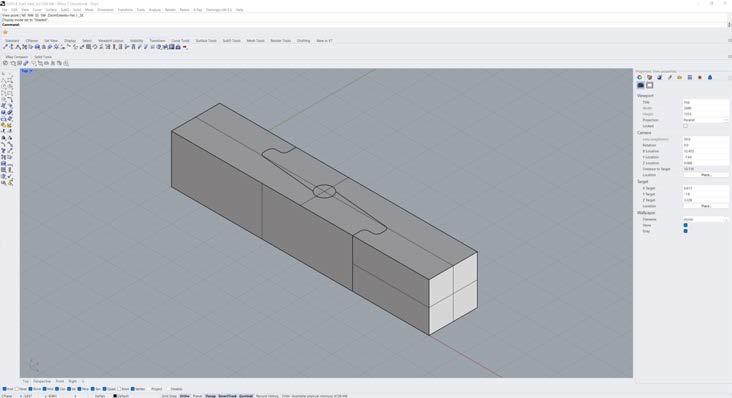
2. Process i. Calibrate interface to to desired specifications — drill speed, offset, dogbone, etc... ii. Set 0 point for drill path iii. Convert 3d model to data set to generate drill path
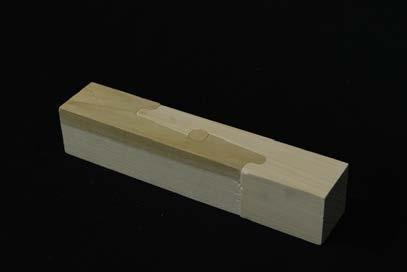
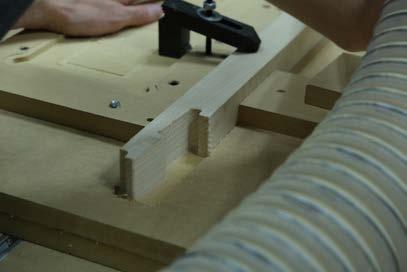

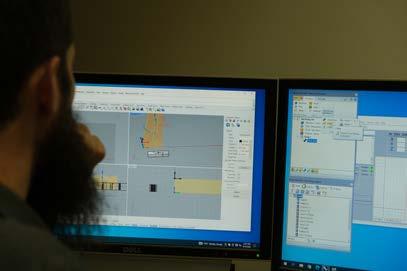
3. Output i. Set up vice to desired specifications ii. Achor material in place iii. Run drill path, all members iv. Sand output v. Assemble