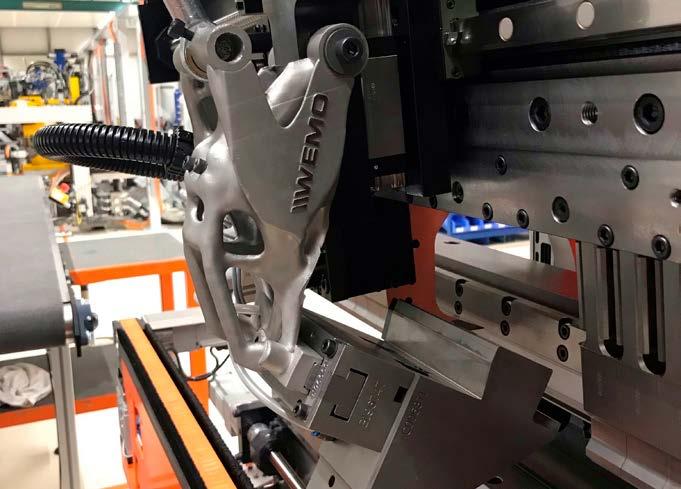
5 minute read
WEMO 3D print zwenkarm plaatwerkproductielijn
WEMO heeft samen met Additive Center een zwenkarm voor de automatische productielijn voor plaatwerk herontworpen voor additive manufacturing. Het resultaat is een veel lichtere zwenkarm, waardoor een kleinere cilinder volstaat. Daarnaast wordt het machine-onderdeel nu als één geheel geprint in plaats van samengesteld uit vier losse onderdelen. Voor de machinebouwer in Den Bosch is dit een pilot, die zeker een vervolg gaat krijgen.
Duurder onderdeel levert onder de streep lagere kosten en meer kwaliteit
Advertisement
Innovatie aanjagen
CEO Jeff Hagelen staat 3D printen quasi gelijk aan het aanjagen van innovatie. De technologie zet aan om anders over onderdelen en systemen te gaan denken. Daarom heeft hij het initiatief genomen om samen met Additive Center de mogelijkheden van 3D printen bij de machinebouwer te verkennen. Nogal een uitdaging, zegt Ardie van Oudheusden, engineer bij de producent van automatische productielijnen voor plaatwerk. “In grote machines zijn de toepassingen lastiger te vinden dan in consumentenproducten. Bovendien werken wij vooral met metaal.” Toch hebben ze de uitdaging opgepakt in een multidisciplinair team, waarin alle afdelingen meededen. Na een eerste workshop over de mogelijkheden van additive manufacturing heeft het team naar toepassingen in de WEMOmachines gezocht. Het prijskaartje dat aan een 3D geprint onderdeel hangt, is daarbij in eerste instantie weggelaten. Terecht, vindt Maarten van Dijk, die vanuit Additive Center het project begeleid heeft. “De grootste uitdaging is om de nieuwe technologie te gaan bekijken vanuit de mogelijkheden. Daarvoor moet je elke mogelijke blokkering in je hoofd weghalen. De kosten zijn een van de grootste blokkeringen. Een idee kost echter niks.” In de workshop is in eerste instantie met name gezocht naar onderdelen waar gewicht bespaard of functies geïntegreerd kunnen worden.

Na een redesign is de nieuwe zwenkarm als één geheel geprint. Dat levert onder aan de streep een kostenbesparing op, ondanks dat de prijs van het geprinte onderdeel hoger is dan die van de losse onderdelen.
Totale kostenplaatje valt gunstiger uit
Uiteindelijk is de zwenkarm in de buiglijn van WEMO als pilotcase gekozen. Dit onderdeel zit dus in het hart van de buigmachine. Conventioneel bestaat het onderdeel uit vier losse frees- en draaidelen, met elk hun eigen toleranties én de tolerantie van de zwenkarm als geheel. Ardie van Opheusden: “Het is een mooi compact stuk in de machine, maar wel heel complex met een behoorlijke nauwkeurigheid.” Als eerste stap heeft het engineeringteam van WEMO een eerste ontwerp gemaakt voor een geïntegreerde zwenkarm. Samen met Rein van der Mast, een van de adviseurs van Additive Center, is het ontwerp vervolgens in meerdere iteraties qua topologie geoptimaliseerd. De optimalisatie is in samenwerking met Altair Inspire verzorgd. Het resultaat is dat de zwenkarm in plaats van 3,8 kilo in de geprinte vorm nog slechts 1,6 kilo weegt. “Het voordeel hiervan is dat we kunnen volstaan met een lichtere cilinder voor de aandrijving van de arm”, licht Ardie van Opheusden toe. “Dat bespaart kosten.” Precies hiervoor is het belangrijk, vult Maarten van Dijk aan, om dit soort projecten multidisciplinair aan te pakken. Het 3D printen van de zwenkarm in 316L is namelijk duurder dan de kostprijs van de vier losse onderdelen. “Maar op het totale plaatje besparen we kosten.” De inkoop- en logistieke kosten voor de vier onderdelen vervallen immers. Er is minder assemblage nodig. Er kan een lichtere cilinder worden ingezet. “En de kwaliteit verbetert doordat er geen speling meer kan ontstaan”, zegt Ardie. Ook in de productie is er een besparing omdat bij de vroegere zwenkarm het onderdeel altijd nog licht nageslepen moest worden om precies aan de maat te zijn. Nu de zwenkarm als een geheel wordt geprint, is de totale tolerantie beter zodat er minder nageslepen hoeft te worden.
Software sluit nog niet aan
De WEMO engineers zijn tijdens het project ook tegen de moeilijkheden in de AM-workflow aangelopen. De designspace - de fysieke ruimte inclusief de krachten die op de zwenkarm komen - is in PTC Creo 3 gemodelleerd, waarna met de generative design software van Altair het ontwerp voor additive manufacturing is gemaakt en geoptimaliseerd om zo min mogelijk materiaal nodig te hebben. Vervolgens wilden de engineers een simulatie doen met het geoptimaliseerde design. Dan blijkt dat je zaken opnieuw moet gaan tekenen omdat de modellen lastig in te laden zijn in CAD-software. Ardie van Opheusden zegt ook bepaalde specifieke features voor additive manufacturing in de designsoftware te missen, bijvoorbeeld het invullen van een ruimte met een honingraadstructuur. “De nieuwste versie van Creo heeft al veel meer features voor 3D printen. Misschien moeten we nu sneller gaan overstappen.”

Zo ziet de huidige zwenkarm in de automatische productielijnen voor plaatwerk van WEMO eruit, een samenstelling van draai- en freesdelen.
Additive Center heeft het project bij WEMO begeleid, gecoördineerd en de ontwikkeling van de zwenkarm verzorgd, maar er zijn meerdere partijen betrokken geweest bij de uiteindelijke realisatie van de 3D geprinte zwenkarm. De topologie optimalisatie is samen met Altair gedaan. Machinefabriek De Valk heeft het onderdeel geprint op de Metalfab1 metaalprinter en daarna machinaal een aantal passingsvlakken nabewerkt.
Vooroplopen met technologie
De zwenkarm is inmiddels in de buigmachine gemonteerd en de eerste serie producten is ermee geproduceerd. De komende tijd wordt nog verder getest. Als de resultaten goed zijn, verwacht Ardie van Opheusden dat 3D printen snel de standaard techniek voor dit onderdeel zal worden. “De zwenkarm is een zichtdeel in de machine. Het 3D geprinte onderdeel straalt uit dat we als WEMO op technologiegebied vooroplopen.” Ondertussen zijn de betrokken medewerkers enthousiast geworden over de nieuwe technologie. Hij merkt dat men eerder aan 3D printen denkt, zelfs bij zoiets eenvoudigs als kalibratieblokjes. Die print WEMO zelf op de Ultimaker 3D printer. “Iedereen omarmt de mogelijkheid om snel dingen te maken.”
Gereedschapkist voor engineer
De engineer ziet 3D printen als een uitbreiding van de gereedschappenkist waaruit de engineers kunnen kiezen. “Het is een aanvulling, geen vervanging.” Het vraagt wel een heel ander denkproces in de organisatie. Meer vanuit een probleem de oplossing gaan zoeken waarbij je breder moet kijken dan enkel het onderdeel waar het om gaat. Inmiddels 3D print WEMO dan ook al eenvoudige onderdelen, zoals een beschermkap voor kabels. Daar zullen nog de nodige draai- en freesdelen aan toegevoegd worden, verwacht Maarten van Dijk. “WEMO heeft veel complexe frees- en draaidelen nodig voor de machines, maar vaak slechts enkele tientallen stuks per jaar. Dat maakt additive manufacturing zowel technisch als economisch interessant.” Overstappen naar 3D printen als productietechniek vergt nu nog een redesign. Ardie van Opheusden denkt dat WEMO bij de ontwikkeling van nieuwe machines of nieuwe onderdelen 3D printen vanaf het begin als productietechniek gaat meenemen. En dan wordt er direct voor AM ontworpen.