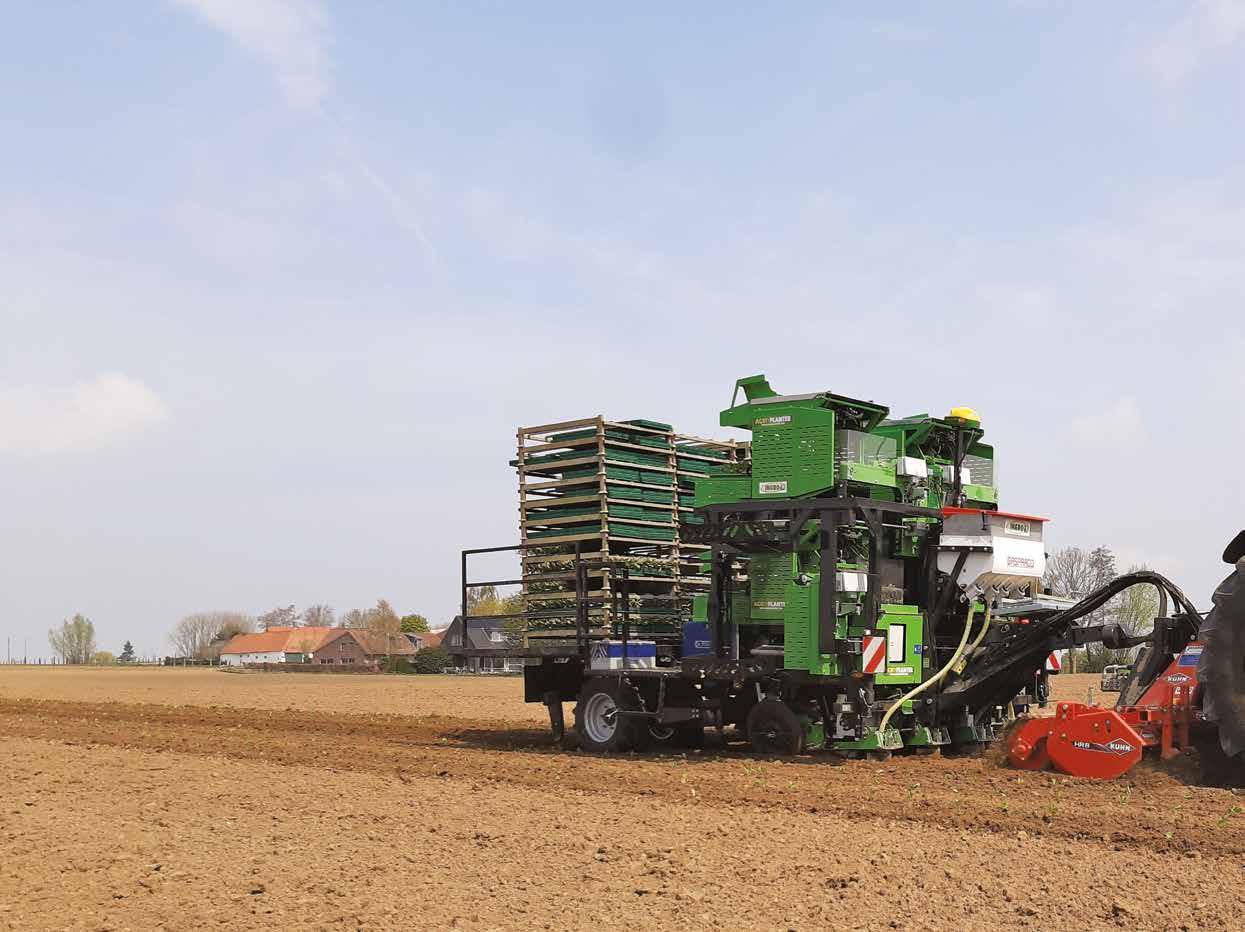
47 minute read
DOSSIER L’automatisation industrielle dans
L’INNOVATION EST CRUCIALE POUR LES DÉFIS DANS LE SECTEUR AGRICOLE
Dans notre pays, les entreprises sont confrontés aux factures énergétiques élevées, aux hausses des coûts salariaux, aux inquiétudes concernant l’impact sur l’environnement et à une grave pénurie de personnel. Dans le secteur agricole, ces problèmes sont aussi présents mais les défis et les obstacles sont bien plus grands. De plus, la recherche d’un rendement supérieur à l’hectare et les exigences des clients créent une pression supplémentaire. Comment la technologie peut-elle offrir une réponse à cela ?
Advertisement
Oubliez d’emblée les réflexions romantiques et les clichés sur ‘le monde paysan’ car les exploitations agricoles sont aujourd’hui à la pointe de l’innovation. L’utilisation de drones, de machines et de tracteurs autonomes, de capteurs et de la robotique ne sont que quelques exemples qui étayent cette affirmation. Travailler de manière rentable est une réelle nécessité.
Un exemple illustre bien les risques potentiels: dans la culture de la pomme de terre, le coût de production total par an et par hectare s’élève à environ 4.800 euros. Pour la ferme qui exploite 100 ha, cela signifie 480.000 euros qu’il faut récupérer à la vente. Mieux vaut donc ne rien gaspiller !
Notre secteur agricole est à la pointe de l’innovation. L’agriculture intelligente assure une croissance la plus efficace possible des plantations et des animaux. Découvrez dans ce dossier comment la technologie facilite la vie dans les fermes et s’avère économiquement rentable.
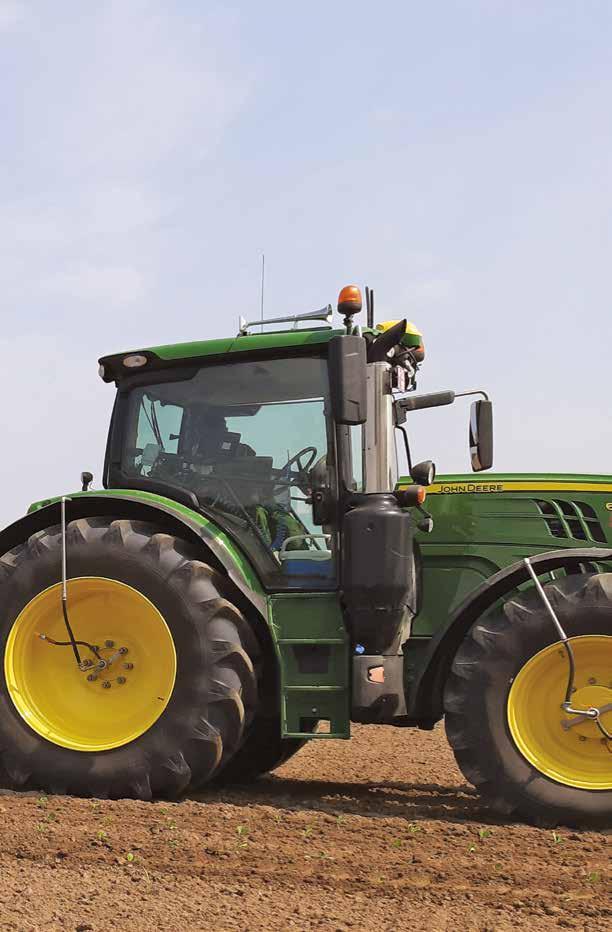
LA SOCIÉTÉ LDA PROPOSE QUELQUES SOLUTIONS
Mustafa Mourou de LDA à Zemst nous en dit plus sur les petites solutions – pertinentes – pouvant aider les entreprises agricoles.
« Je pense par exemple à nos vannes électriques de MAC valves pour le dosage de liquides. Elles sont largement utilisées dans les secteurs industriels classiques pour notamment le dosage d’additifs dans les boissons rafraîchissantes et le remplissage d’ampoules dans le secteur pharmaceutique. Ces vannes sont aussi très populaires dans l’agriculture et sont adaptées au produit et à ses caractéristiques. La membrane d’étanchéité qui protège la partie électrique du liquide est ainsi disponible dans divers matériaux comme le téflon ou le viton. Cela permet de traiter pratiquement tous les liquides sans problème. Le grand avantage de ces vannes est leur haute précision de dosage car dans le passé, on avait tendance à travailler selon la devise ‘plutôt-trop-que-trop-peu’, certainement lorsqu’il s’agissait d’engrais. En garantissant la quantité optimale, l’environnement est préservé et du produit est économisé, ce qui revient moins cher à l’agriculteur. »
Racleur
« L’adaptation de la vanne n’est pas uniquement liée au liquide, l’application joue aussi un rôle. Dans l’agriculture, la durée de vie est un point d’attention critique. Par rapport à une vanne à membrane standard, le nombre de cycles doit être plus élevé. Nous supposons une durée de vie de 100 millions de cycles voire plus, et nous atteignons cela de plusieurs manières. On peut par exemple utiliser plusieurs matériaux pour le boîtier comme de l’aluminium, l’inox 304 ou 316. Par ailleurs, les vannes sont équipées d’un système autonettoyant. Chaque fois que la vanne commute, un racleur élimine l’encrassement pour le maintenir hors de la vanne. Pour étendre le domaine d’utilisation, nous pouvons aussi adapter l’alimentation de 12 à 220V. Cela permet d’utiliser le système sur une machine mobile ou ailleurs dans un bâtiment. En cas de besoin, la consommation etant tres limitee, le fonctionnement est assure par une batterie. Enfin, je veux encore spécifier que les vannes doivent résister aux vibrations qui sont assez courantes dans les applications mobiles. »
Soufflets à air
« Les soufflets à air sont un autre groupe de produits utilisés dans l’agriculture. Ils sont mis en œuvre dans deux applications. Nous les retrouvons d’une part sous le siège conducteur des engins agricoles. Ils offrent tout le confort utile au conducteur lors de son labeur dans les champs. Dans certains cas, ils absorbent 99,9% des vibrations. ”
« La seconde application des soufflets à air se situe dans les systèmes de pulvérisation où ils font office de cylindre dans les bras gicleurs. Travailler dans les champs, c’est être secoué dans tous les sens en permanence parce que le terrain n’est jamais égal. En prévoyant des soufflets à air, il est possible d’obtenir une plus grande stabilité dans les bras. Qui peuvent mesurer 6 mètres, voire plus, et les vibrations et mouvements de la machine peuvent donc avoir un impact majeur. La structure mécanique est donc mieux protégée et la qualité du travail est meilleure grâce à l’amortissement. »
www.lda.be
DES ROBOTS CUEILLEURS DE CHICONS DANS UNE ENTREPRISE HORTICOLE DU FUTUR
Dans notre pays, les entreprises sont aux prises avec des factures énergétiques élevées, une hausse des coûts salariaux, des inquiétudes quant à l’impact sur le cadre de vie et une grave pénurie de personnel. Dans le secteur de l’agriculture, ces problèmes sont aussi présents mais les défis et les obstacles sont exacerbés au possible. De plus, la recherche d’un rendement supérieur à l’hectare et les exigences des clients créent une pression supplémentaire. Comment la technologie peut-elle offrir une réponse à cela ?
Dans le secteur de l’agriculture et de l’horticulture, les exploitations sont souvent dépendantes de facteurs externes. Si les conditions météorologiques déterminent en grande partie la qualité et la quantité des récoltes, la demande fluctuante du marché est un autre grand défi pour nombre d’exploitants. Lorsque Stefaan Gheeraert reprend l’exploitation familiale à Poperinge en 1991, en tant que quatrième génération, il est confronté à une baisse de la demande en houblon, une culture autrefois omniprésente dans cette belle région. Les grands brasseurs préfèrent acheter leurs cônes de houblon à l’étranger. C’est une incitation pour beaucoup de se tourner vers d’autres cultures, et Frachibel passe progressivement à la culture du chicon et de la fraise. Stefaan Gheeraert: « Les fraises sont principalement cultivées au printemps et en été. On recherchait donc un légume que l’on pouvait cultiver et récolter à l’automne et en hiver. Nous avons choisi le chicon. »
Un intérêt précoce pour l’automatisation
L’agriculteur avait automatisé la culture du chicon bien avant l’incendie de 2019, pour une bonne raison. Stefaan Gheeraert: « Notre premier robot date de 2015, nous avions alors installé un modèle Fanuc pour laver les bacs de forçage – dans lesquels les racines deviennent des souches – après la récolte, avant de les réutiliser. Trois ans plus tard, un second robot était installé pour le déplacement des bacs. Dans le secteur, on utilise des robots parce que nous sommes nous aussi confrontés à une pénurie de main d’œuvre. Il s’agit d’une activité où le travail manuel est prépondérant et surmonter cet obstacle n’avait rien d’évident. »
La solution robotisée fonctionnait à merveille jusqu’à ce que la catastrophe se produise. Outre les bâtiments, l’incendie a réduit toutes les machines en cendres. « Nous étions alors face à un croisement: soit tout arrêter, soit tout reconstruire. Comme notre fils nous avait indiqué vouloir reprendre l’activité, nous avons choisi la seconde option. Aujourd’hui, cela fait six mois que nous cultivons et traitons le chicon. »
« Si l’incendie et les conséquences ont été terribles, cela nous a donné aussi l’opportunité de redéfinir le processus de production avec l’aide de partenaires spécialisés en automatisation. Nous avions entretemps plus de 25 ans d’expérience dans la culture du chicon et nous connaissions exactement les points d’attention et les difficultés. Nous voulions absolument automatiser le processus de coupe des racines de souches. Les souches, cultivées dans les bacs de forçage, devaient être extraites une par une pour couper la racine avant la poursuite du traitement. Nous recherchions une solution mécanique pour réaliser cela. »
La variation du produit, un défi de taille
L’intégrateur DD Automation s’est chargé d’automatiser le processus de traitement des chicons. Il était représenté par Dominiek Deboosere, qui nous a expliqué le déroulement de la production : « Tout commence dans d’immenses cellules de culture. Plusieurs centaines de bacs y sont placés, chaque bac
8
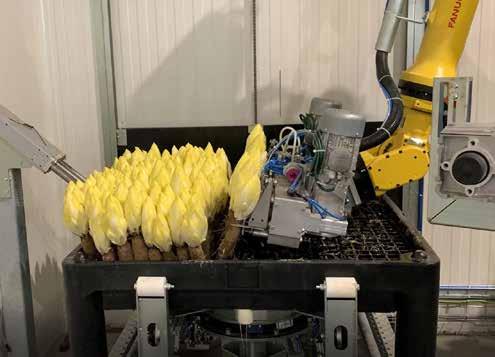
Frachibel à Poperinge ne produit plus de houblon mais des fraises et des chicons. L’installation automatisée représente une solution face à la pénurie de main d’œuvre dans le secteur.

contenant environ 70 kilos de chicons. Lorsque la croissance est terminée, les bacs sont amenés via un chariot élévateur vers la position d’attente. Le processus de traitement qui suit est entièrement automatisé : via deux manipulateurs, les bacs sont transférés par un convoyeur à chaîne vers les deux robots cueilleurs. Jusqu’ici, l’installation est relativement simple, mais elle devient plus complexe lors de la cueillette à cause d’une spécificité du chicon : c’est un produit naturellement fragile, qui varie dans sa longueur et son épaisseur. La manipulation des souches doit avoir lieu avec le plus grand soin. »
« Pour ce type d’applications, il n’existe pas de préhenseurs standard sur le marché et nous avons donc développé un système adapté. Nous avons choisi un concept où le préhenseur est constitué de vis entraînées qui s’enfoncent dans la racine du chicon. En une passe, une rangée complète de chicons et leurs racines est extraite des bacs de forçage et déposée sur un convoyeur à bande. A l’étape suivante, les chicons sont prélevés du convoyeur et débarrassés de leurs racines. Dans des conditions optimales, chaque robot traite dix à onze bacs à l’heure. Comme nous ne manipulons que la racine sans toucher la souche, nous ne sommes pas liés aux normes de sécurité alimentaires. Cependant, pour des raisons de sécurité, nous utilisons une lubrification de qualité alimentaire dans les robots, et le préhenseur en acier inoxydable pour un nettoyage optimale. »
Un automate central et 3 interfaces graphiques
Dominiek Deboosere: « Pendant le traitement, les bacs vides sont retirés de la cellule et envoyés à la cellule adjacente où se trouve le robot de lavage. Après le nettoyage, les bacs retournent à leur position tampon avant d’être finalement redirigés vers la zone où de nouvelles racines sont plantées. L’unité centrale Simatic 1515 pilote toute la ligne. La communication avec les robots cueilleurs et le robot de lavage de Fanuc passe par Profinet. Les trois robots Fanuc sont de type R 2000 iC. Les dispositifs de sécurité – comme les barrières immatérielles de sécurité et les contacts de portes – sont également gérés par l’automate. Le choix s’est porté pour le niveau de sécurité PL e, l’option la plus stricte. La commande a lieu via 3 écrans graphiques. En principe, l’exploitant n’a pas à programmer le robot, mais c’est parfaitement faisable avec la console “ Teach Pendant “. Il peut adapter manuellement le robot en cas de nécessité. »
D’après Dominiek Deboosere, les ajustements sont simples à réaliser. « L’installation fonctionne très bien, mais nous procèderons bientôt à une légère adaptation imposée par la diversité du produit. Nous constatons en effet que les racines ne sont pas toujours positionnées dans le même sens. Comme les robots cueilleurs prélèvent les racines rangée par rangée, il arrive parfois qu’un élément ne soit pas extrait, ou pas correctement. « En adaptant légèrement le processus de plantation, c’est-a-dire, le placement des racines dans les bacs, nous pourrons résoudre le problème. » Stefaan Gheeraert poursuit: « Le choix des racines de chicons a un impact sur le fonctionnement. Nous les achetons en partie en France. Elles sont plus courtes et ont une forme plus ovale sur le dessus, à l’inverse des racines belges ou néerlandaises qui sont plus rondes mais aussi plus chères. Nous cultivons aussi nos propres racines, mais leur forme et taille dépendent du climat. Compte tenu de la sécheresse, c’est toujours un peu l’inconnu. Nous voulons donc une installation qui puisse traiter tous les types de racines, quel que soit leur provenance. »
« La combinaison de notre expérience en culture du chicon et l’expertise en automatisation de DD Automation a conduit à ce beau résultat. Je pense que l’on peut dire à juste titre qu’il s’agit là d’une installation pionnière dans la culture du chicon. Il est difficiled’estimer les économies réalisées, mais si nous devrions tout faire manuellement, nous aurions besoin, au moins, de 3 personnes et d’un second chariot élévateur. »
www.koket.be www.ddautomation.be www.fanuc.eu
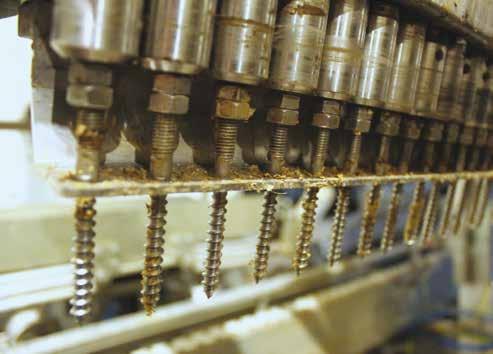
Le préhenseur possède des vis motorisées qui s’enfoncent dans la racine des chicons. Les robots Fanuc de type R 2000 iC utilisés pour les 2 applications
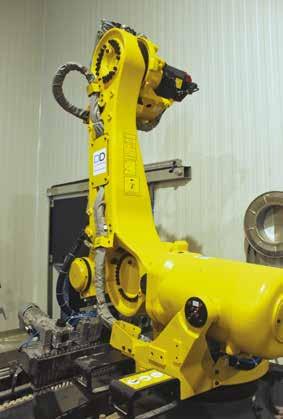
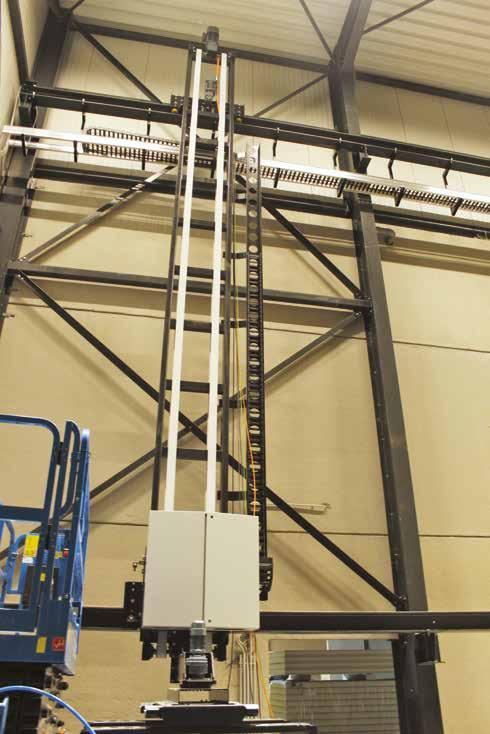
Deux axes X de 40 mètres et 1 axe Z de 9 mètres assurent le déplacement du préhenseur à travers l’entrepôt et les cellules de culture. Le coffret de commande se déplace avec l’installation de préhension.
Le concept a été développé par l’agriculteur Simon Deceuninck. Les servomoteurs pilotent la courroie qui alimente le mouvement vertical.
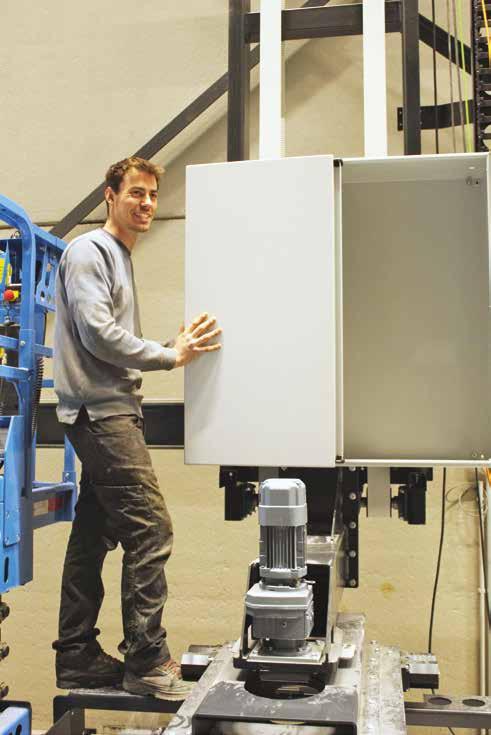
UN RAIL LINÉAIRE LONG DE 40 MÈTRES SUPPORTE UN PRÉHENSEUR SUR PORTIQUE
Outre leurs connaissances des légumes et des animaux, de nombreux agriculteurs possèdent une expertise en mécanisation qui leur permet de réaliser des projets d’automatisation d’un très haut niveau. Nous avons trouvé un bel exemple chez le producteur de chicons Ardolof : un système ingénieux, basé sur un rail linéaire, positionne les bacs de forçage pour le traitement ultérieur.
Au milieu des champs aux alentours d’Ardooie se trouve un bâtiment imposant au sein duquel les souches de chicon d’Ardolof sont cultivées. Les bacs de forçage sont empilés jusqu’à une hauteur de 18 bacs dans les cellules de culture. « Ardolof est connu depuis de nombreuses années pour sa culture de chicon », déclare l’exploitant Simon Deceuninck. « La ferme de mes parents a été récemment transformée en une exploitation biologique de 30 hectares, mais nous poursuivons la culture traditionnelle du chicon à grande échelle. La récolte de 230 hectares est traitée dans notre bâtiment. Une fois que les bacs de forçage avec les racines sont transférés vers les cellules de culture, ils y séjournent 3 semaines avant le traitement ultérieur. Le processus de croissance est étroitement surveillé. L’incidence de la lumière, le degré d’humidité et l’irrigation sont d’une importance capitale pour cultiver le chicon selon les souhaits des clients, toute l’année. »
L’innovation continue permet l’optimisation du processus de croissance
« Nous continuons d’innover pour répondre aux demandes des clients. Les grandes chaînes de distribution veulent par exemple des poids et des formats identiques. Nous essayons donc d’influencer positivement le processus de croissance et la qualité. Nous travaillons notamment avec des conduits de ventilation perforés et commandés qui répartissent l’air idéalement. L’incidence de la lumière est pilotée par le système de commande d’éclairage DALI (Digital Addressable Lighting Interface). Elle est donc adaptée automatiquement pour éviter
les dommages, car une demi-heure de lumière suffit déjà à rendre un plant de chicon invendable. Grâce au système de commande, chaque armature a son adresse numérique et est réglée séparément. Nous travaillons aussi avec un refroidissement au CO2 et une récupération de chaleur, et les gouttières des cellules de culture sont adaptées pour obtenir un drainage optimal. De tels détails nous permettent de faire la différence, même si le chicon reste un produit naturel. Il y aura toujours des petites différences au niveau de la forme et du poids. Voilà pourquoi je réfléchis à un système robotisé, basé sur une technologie de caméra, pour effectuer le tri. Mais ceci est un projet d’avenir car la priorité actuelle est l’automatisation du système d’approvisionnement et d’évacuation des bacs de forçage. »
« Le processus de transfert des bacs vers les cellules de culture et l’enlèvement des produits finis et leur empilement prend du temps avec un chariot élévateur. J’ai donc voulu automatiser cet aspect et le choix s’est porté sur un système avec un empileur automatique. J’ai entièrement dessiné le principe de fonctionnement car je voulais maitriser moimême le processus. J’ai toujours été intéressé par l’électricité et l’automatisation, c’est un sujet populaire dans mon cercle d’amis. Certains parlent de football et de cyclisme, moi de servocommandes », explique Simon Deceuninck.
« L’objectif est d’avoir une détection automatique des bacs pleins ou vides pour, via les codes QR sur les bacs et un lecteur sur le préhenseur, savoir où se trouve chaque bac. Le préhenseur prépare les bacs pour le traitement ultérieur. 90% de ce processus peut être automatisé, mais pour atteindre les 100%, il faut prévoir un chariot élévateur automatique ou un trolley pour le transport vers et depuis les cellules de culture. Je ne sais pas encore trop comment appréhender cela. »
Un empilement de neuf mètres de haut
Le bâtiment abrite plusieurs cellules de culture les unes à côté des autres et les bacs sont empilés par 16, ce qui représente une hauteur de 8 mètres. La construction sur laquelle se déplace le préhenseur a été livré par Vansichen Lineairtechniek. L’ingénieur de vente, Francis Lannoy nous explique: « La construction mesure 40 mètres de long sur 9 mètres de haut et comporte 2 axes X et un axe Z. Avec de tels rails, et les rails de robot, il n’y a finalement aucune limitation en longueur. Certes, il faut veiller à respecter la portée maximale et des transferts parfaitement droits. Nous calculons les poids, les vitesses, les accélérations d’autres paramètres pour le client. L’ensemble a été conçu et fabriqué en interne chez nous et installé chez le client avant la finition. Le toit du batiment a été posé une fois les portiques en place. »
Simon Deceuninck: « J’ai choisi de travailler avec un servomoteur pour le mouvement vertical et deux moteurs fonctionnant selon la configuration maître/esclave et entraînant les courroies. Le positionnement exact a lieu via des codeurs et des capteurs de distance. Le double système offre une certitude absolue sur la position. J’ai moi-même programmé la commande de l’automate et réalisé les calculs de sécurité nécessaires. Comme j’ai tout dessiné moi-même, cela nous coûte moins cher et je connais parfaitement l’installation. Quand vous travaillez avec des partenaires externes, vous êtes toujours dépendant et vous perdez en autonomie. D’autre part, il faut travailler avec de bons partenaires, qui vous donnent de l’information utile et un back-up. »
www.vansichen.be

Vue du mécanisme pour le mouvement du portique.
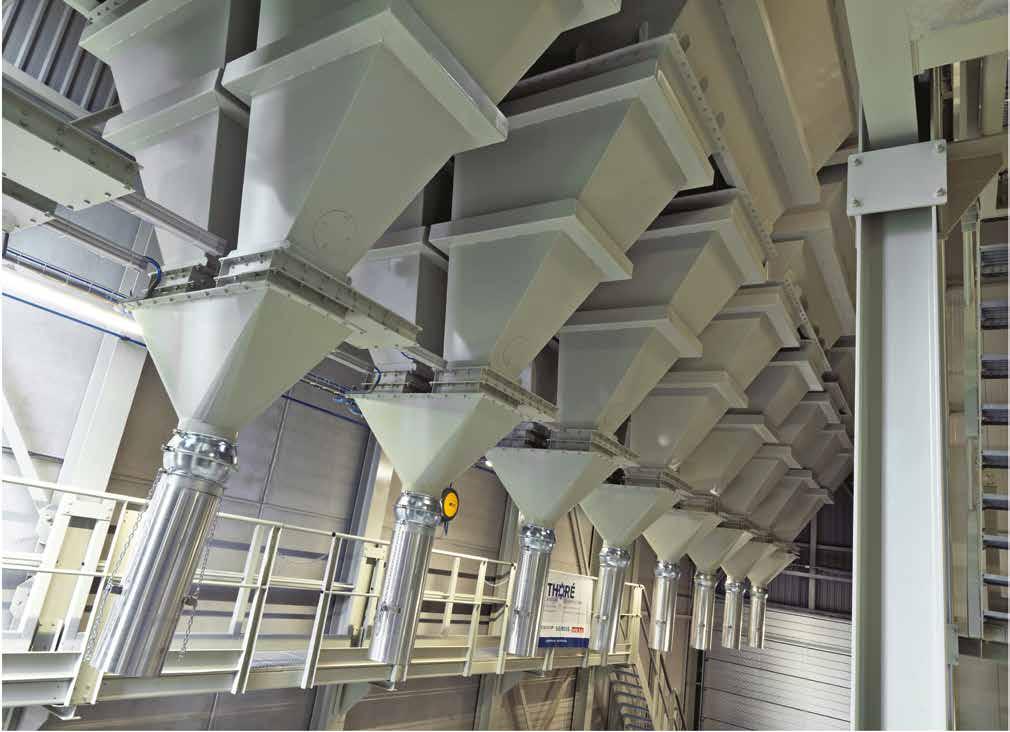
Chez Marvaco, le système d’alimentation optimisé garantit un élevage porcin optimal.
L’AUTOMATISATION COMME BASE INNOVANTE D’UNE TECHNOLOGIE D’ALIMENTATION ET D’UNE FERME CONTENEUR
L’automatisation est présente dans le secteur agricole sous des formes très diverses. Nous étayons ce constat avec 2 cas remarquables que nous vous présentons ci-dessous. L’approche commune est l’innovation. A la ferme porcine Marvaco d’Aarsele, un système automatique de mélange d’aliments aide les porcs à atteindre leur poids idéal. De son côté, Urban Crop Solutions à Beveren-Leie a développé une ‘plant factory’, un mélange entre une ‘indoor plant technologie’ et une ‘factory engineering’.
L’élevage porcin est omniprésent en Flandre occidentale. On dit parfois en plaisantant qu’il y a plus de porcs que d’habitants dans cette belle province. Après enquête, il s’avère que ce cliché est une grossière… sous-estimation. La Flandre occidentale comptabilise 3,3 millions de porcs, soit environ 3 bêtes par habitant. Une telle concentration fait de la Flandre occidentale le Walhalla en matière d’innovation dans cette branche du secteur agricole. A Aarsele, l’exploitation Marvaco de David Martain et Inge Van der Steene en est un bel exemple et fait office d’initiateur d’idées innovantes depuis plusieurs années. Fin mars 2019, la presse nationale en faisait même écho avec cette histoire étonnante : pour diminuer le stress et augmenter la qualité de la viande, de la musique est diffusée deux fois par jour durant trois heures pour stimuler le bien-être des bêtes. Une approche développée en concertation avec Breydel, le producteur de produits artisanaux à base de porc.
Marvaco était le partenaire idéal : « Nous sommes pleinement engagés dans le développement durable, la chaîne courte, la récupération de l’eau et le bien-être animal. Grâce à la collaboration avec Breydel, nous faisons aujourd’hui un pas de plus », explique David Martain. « Nos bêtes écoutent de la musique et bénéficient de plus d’espace, elles reçoivent une alimentation spécifique pour répondre aux exigences de qualité de Breydel. Nous devons livrer des bêtes qui entrent
parfaitement dans un certaine catégorie de poids, ce qui nécessite une alimentation équilibrée par type de porc. Au total, nous avons élaboré 12 recettes qui sont évaluées et adaptées régulièrement par des experts alimentaires.
L’alimentation comme facteur crucial
Le concept d’alimentation des porcs ne s’arrête pas là. Pour répondre aux exigences de qualité, David a repris la production de l’alimentation en mains. Une décision qui a un impact considérable. « L’alimentation est d’une importance cruciale pour la santé générale des porcs et la stimulation ou le ralentissement de leur croissance », explique-t-il. « Pour pouvoir organiser correctement ce processus, nous avons recherché une solution automatisée. »
David et Inge ont contacté le constructeur Quintyn Gebr. de Zulte qui a imaginé le concept mécanique du système d’alimentation. Thoré I&C, l’intégrateur de Poperinge, s’est chargé de l’installation électrique, de l’automatisation et du logiciel de traçage. Siemens a fourni les composants. Tom De Wilde nous détaille le concept de l’installation : « L’opérateur sélectionne une des 12 recettes et la quantité souhaitée via le système de visualisation WinCC Advanced. L’automate Simatic calcule ensuite automatiquement la quantité correcte de matières premières. Le pesage précis a lieu à l’aide de nos cartes de pesage Siwarex. Après avoir mélangé la recette, l’aliment est transféré aux animaux. L’ensemble est tracé afin de savoir exactement quel lot a été donné à quel moment. Ceci permet à Marvaco de satisfaire avec précision à la demande du client. »
L’agriculture dans des conteneurs
Nous retrouvons Urban Crop Solution à Beveren-Leie. La solution agricole que nous découvrons ici n’est pas traditionnelle mais consiste en un système sophistiqué pour la culture de légumes en intérieur. Le CTO Maarten Vandecruys nous explique son objectif: « Cette solution nous permet de cultiver des petites cultures toute l’année et n’importe où, dans des villes animées ou le désert. La culture a lieu dans un conteneur fermé avec un éclairage led spécialement développé, un contrôle climatique optimal et une irrigation avec de l’eau récupérée pour une consommation minimale. Le résultat ? Des légumes dont la croissance est bien plus rapide et plus nutritifs. La culture a lieu dans des bacs superposés pour maximiser le rendement par unité de surface. »
L’installation, à la pointe de la technologie, a été construite à partir de la technologie d’automatisation numérique de Siemens. Nick Vanden Broecke de Siemens nous explique: « Le client avait des souhaits spécifiques pour divers facteurs de l’installation. Il voulait notamment le moins d’intervention humaine possible, ce qui explique l’automatisation poussée, tant pour le réglage des cultures, le suivi de la croissance et la maintenance des équipements. De plus, l’aspect sécurité était prioritaire. Les ascenseurs amenant les bacs à l’opérateur lorsque les légumes sont arrivés à maturité s’arrêtent automatiquement lorsque quelqu’un pénètre dans la zone de culture. Il fallait aussi intégrer la plant factory dans l’ensemble de l’entreprise. Les processus peuvent donc être suivis tout au long de la chaine d’exploitation: de la production juqu’à l’administration. Enfin, la traçabilité des produits est essentielle. Si le client sait comment les légumes sont précisément traités, selon quelle quantité d’eau et de fertilisant par exemple, les processus peuvent alors être affinés en vue d’une croissance optimale. »
Prêt pour Industrie 4.0 via le standard ouvert OPC
Nick Vanden Broecke: « L’automatisation globale et la surveillance à distance sont rendues possibles grâce à la plateforme Totally Integrated Automation qui intègre les variateurs de vitesse, les panneaux de commande (HMI), les points d’accès et les commutateurs. Pour l’aspect sécurité, un contrôleur SIMATIC S7-1500 prévu pour chaque ascenseur suit le protocole de sécurité programmé. Ce composant comprend un automate et un relais de sécurité, et peut être connecté sans fil aux variateurs SINAMICS S120 qui pilotent les moteurs, via le standard PROFINET. L’installation est prête pour Industrie 4.0 car les composants machines sont connectés au logiciel OPC sur un pc par le protocole ouvert OPC. Ceci permet le trafic de données de et vers l’installation. Pour la traçabilité, un système RFID est intégré à l’installation. Chaque légume conditionné reçoit un tag reprenant, par exemple, le contenu, l’opérateur, la durée de croissance et le traitement. »
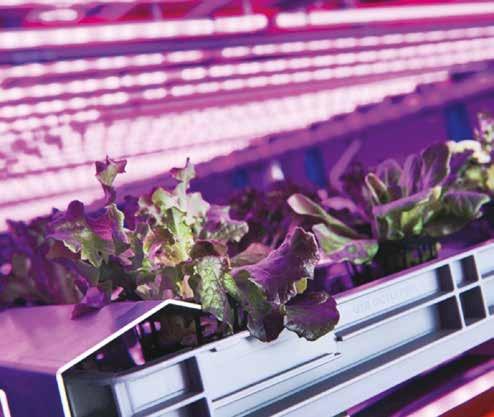
Urban Crop Solutions a développé un système de culture en intérieur entièrement automatisé.
www.icthore.be www.marvaco.be www.quintyn.be www.siemens.be www.urbancropsolutions.com
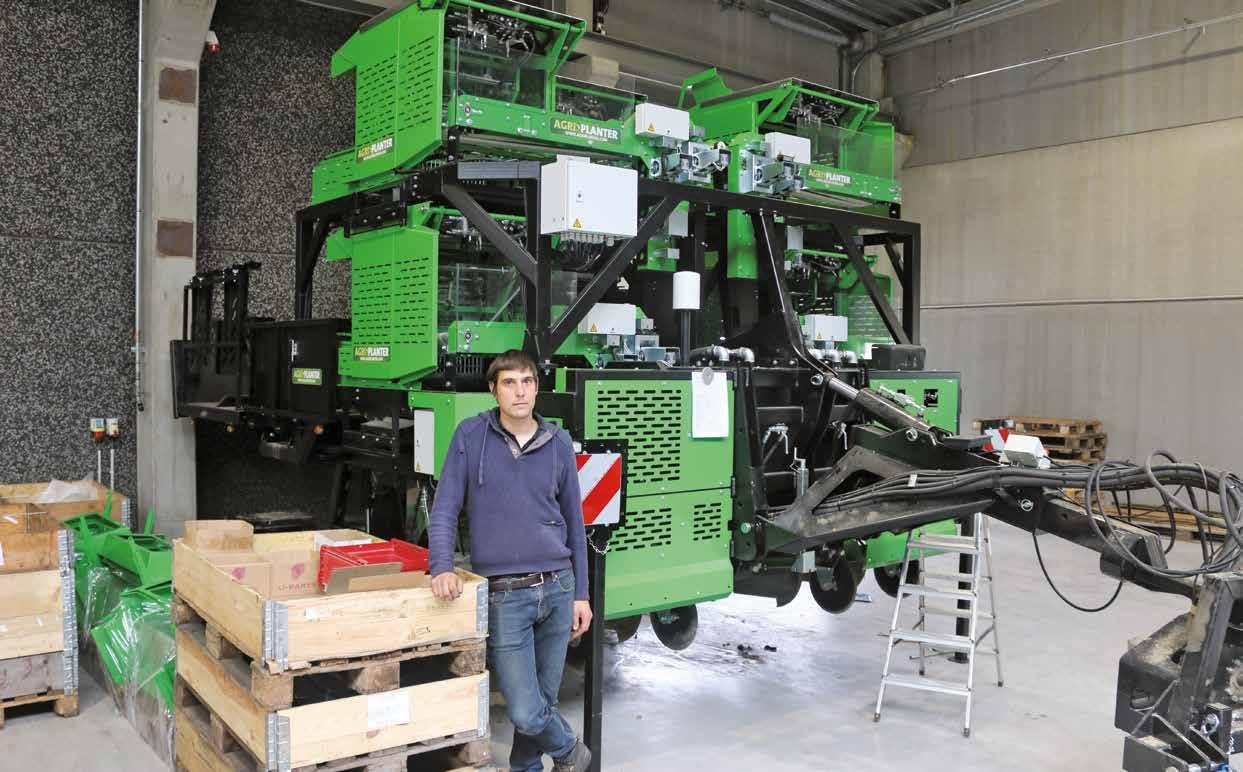
AGRIPLANT EST PRÊT POUR UNE CROISSANCE INTERNATIONALE AVEC SES PLANTEUSES DE LÉGUMES DE HAUTE TECHNOLOGIE
L’entreprise familiale belge Agriplant de LangemarkPoelkapelle est active dans la conception, la fabrication et la vente de planteuses de légumes automatiques. « Le travail manuel n’est plus abordable pour nos agriculteurs » déclare Tom De Rudder. Il nous raconte la croissance internationale de cette entreprise innovante.
L’entreprise de Flandre occidentale conquiert le monde avec la fabrication de planteuses de légumes automatiques. A la Brugseweg à Langemark-Poelkapelle, on remarque tout de suite que l’on construit ici des machines agricoles innovantes. Un nouveau bâtiment en béton a été érigé et mis en service à l’été 2020. Il ne reste plus qu’à placer le logo Agriplant sur la façade extérieure.
A l’origine, la famille Parrein assurait la distribution de tracteurs agricoles de marques comme Massey Ferguson et Kubota. Plus tard, elle a distribué des planteuses de légumes japonaises et commencé à les adapter aux exigences des clients belges. « A partir des années septante, Agriplant a acquis une solide expérience en repiquage de légumes dans les champs », explique le chef de projet Tom De Rudder. « Nous nous trouvons au cœur de la plus grande région maraîchère de Belgique. Le sol fertile des polders permet de cultiver une multitude de légumes : des choux de Bruxelles, des choux, des oignons, des tomates et même du céleri. Ce fut une bonne école d’apprentissage. Au fil des ans, nous avons acquis du savoir-faire et nous avons progressivement optimisé nos modèles. »
Au départ, les betteraves sucrières, la chicorée et les légumes verts étaient repiqués en pots de papier. En 1998, Agriplant lance alors l’Agriplanter, la première planteuse automatique de plants en barquettes et en mottes. Le repiquage automatique de légumes fait gagner du temps, offre un meilleur contrôle des mauvaises herbes et un taux de germination plus élevé. Tom De Rudder: « Nous utilisons des barquettes de jeunes plants cultivés en serres que l’on met en pleine terre. Nos modèles Agriplanter assurent le repiquage automatique de nombreux légumes comme tous les types de choux (choux
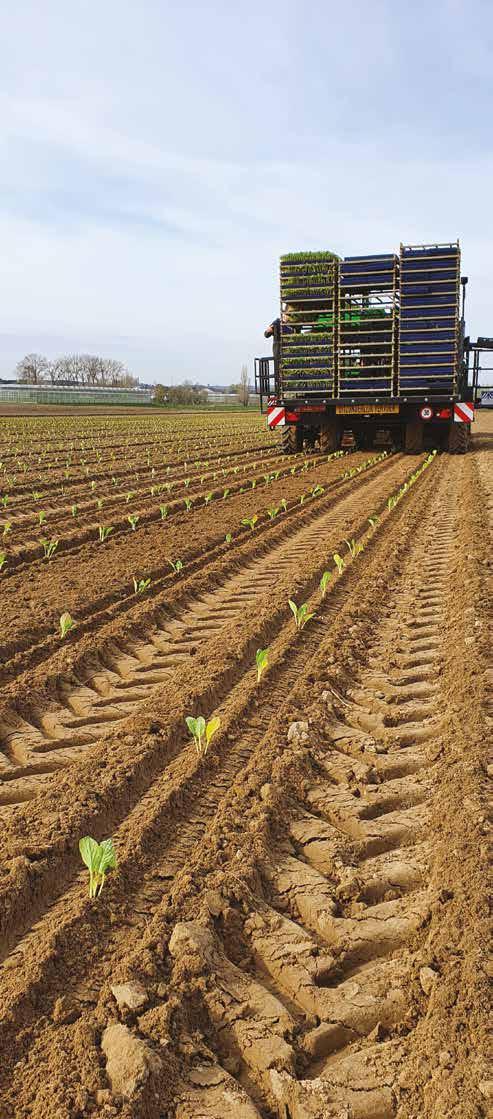
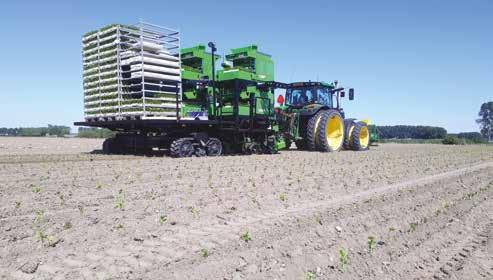
de Bruxelles, chou blanc, chou rouge, chou-fleur, chou vert, chou-rave, …) mais aussi du céleri, des tomates, des oignons, du fenouil… »
L’entreprise possède son propre département R&D qui conçoit, construit et adapte les machines. Elle travaille avec un logiciel et une ingénierie interne pour dessiner chaque pièce en 3D. Après 20 ans, les techniques brevetées intégrées dans les machines Agriplant sont perfectionnées dans les moindres détails. « Notre département ingénierie gère le concept et le développement et est impliqué dans le montage et la livraison finale des planteuses. Il en résulte une approche orientée vers la pratique. La qualité, l’expérience et une innovation poussée sont nos valeurs fondamentales. L’assemblage et le contrôle qualité ont toujours lieu par notre équipe de spécialistes. Agriplant possède aussi un vaste réseau de distributeurs dans de nombreux pays. »
La pièce maîtresse - l’Agriplanter – est capable de planter jusqu’à six rangs de légumes simultanément. Cette planteuse automatique est un monstre agricole dont la capacité de repiquage de plants en barquettes et en mottes peut atteindre 66.000 plants à l’heure, un record ! « Nous aidons à réduire les coûts de main d’œuvre et à augmenter le rendement des champs. L’agriculture moderne est une histoire de calculs. L’agriculteur doit constamment calculer pour produire le plus efficacement possible. Le travail manuel n’est plus abordable pour nos agriculteurs. »
La large gamme de modèles permet à Agriplant de répondre à la demande et aux exigences du marché. Grâce à l’innovation continue et aux performances élevées, le robot qui prélève les plants est adapté aux diverses barquettes. « L’Agriplanter peut traiter des barquettes en plastique et en mousse de polystyrène (EPS). Les barquettes varient en fonction des plants à repiquer et de la région où ils sont plantés. L’Agriplanter a prouvé son utilité dans de nombreuses régions du monde. Voyez les immenses champs en Californie et la culture industrielle de tomates pour produire du ketchup. Au vu de la taille des producteurs de tomates industriels, qui peuvent gérer plusieurs centaines d’hectares, nos machines ont d’abord été exportées en Italie, en Espagne, au Portugal et dans le sud de la France. La Belgique, les Pays-Bas et la France ont suivi pour d’autres cultures. Nous avons aussi des demandes du Japon jusqu’au Canada, notamment pour des applications dans la culture biologique de betteraves sucrières. »
« Au niveau mondial, il y a quelques concurrents mais nos machines sont techniquement meilleures et nous avons plus de capacité », poursuit Tom De Rudder. « Les avantages de l’Agriplanter sont la détection de mottes vides (sans le plant), le réglage automatique de la profondeur, une faible pression au sol, la distance de plantation réglable, une grande variété de cultures à planter et une grande variété de barquettes. Nos machines s’adaptent aux besoins du client. »
« La planteuse assure une circulation constante des plantes. Le robot sort les plantes de la barquette et les place sur la ‘sensorhead’ composée d’un convoyeur et d’un sélecteur. Le sélecteur fait tomber les mottes vides, seules les mottes avec les plants sont emmenées vers les bandes hérisson. Ces bandes verticales transportent les plantes depuis la sensorhead jusqu’à la partie planteuse. Des disques en caoutchouc orientent les plantes dans la bonne direction. Les plants sont alors placés dans le sillon à la bonne profondeur. Le sillon est refermé avec des roues de pression. La pression est réglable en continu, même lorsque la machine est en action. Tout cela assure une croissance rapide et optimale des jeunes pousses.
« Nous travaillons avec des partenaires de qualité qui nous fournissent rapidement les pièces adéquates pour nos modèles Agriplanter », poursuit Tom De Rudder. Une de ces entreprises est le spécialiste japonais en automatisation SMC. Christophe van Muylem de SMC nous en dit plus sur les vérins utilisés dans l’Agriplanter. « Il y a quatre types de vérins hydrauliques: CHMC25-50, CHMC25-200, CHDMC20-50 et CHQB20-5DM. Les trois premiers sont des vérins ronds, le dernier est un modèle compact (avec un boîtier carré). Les deux types ont une pression de service maximale de 3,5MPa. »
SMC, dont le centre de distribution européen est établi à Wommelgem, ne construit pas de vérins hydrauliques pour des ponts ou des écluses. Le travail est plus fin. Christophe van Muylem: « Notre expertise (Takumi) et notre attention (Omoiyari) résident dans la construction mécanique, là où la pneumatique manque de puissance et de précision au positionnement. L’hydraulique est meilleure parce qu’elle n’est pas compressible, notamment. Notre gamme atteint des diamètres de 160 mm et une pression de service maximale de 16MPa. Par ailleurs, le concept des vérins hydrauliques de SMC est souvent comparable à l’homologue pneumatique, ce qui s’en ressent sur la planche à dessin pour l’assemblage, le montage et les accessoires. »
« Pour les modèles Agriplanter, le choix des vérins hydrauliques a été déterminé par la puissance supérieure qu’un vérin hydraulique compact peut fournir et le fait que l’hydraulique est bien connue dans les machines agricoles », poursuit Christophe van Muylem. « En tant que SMC, il est de notre devoir (Hokori) de garantir au client final la continuité de fonctionnement de la machine lors de la saison des plantations (Keizokuzei), et les connaissances sur l’Agriplanter. »
Pour Tom De Rudder, les vérins hydrauliques de SMC sont idéaux car il ne faut pas exercer trop de pression sur les barquettes. « Les vérins dans le robot fonctionnent à une pression basse, de 32 bars. Les barquettes doivent être manipulées avec précaution par le robot pour éviter qu’elles n’éclatent. Pour Agriplant, il est crucial que les éléments commandés puissent être fournis rapidement afin que la construction des machines agricoles ne soit pas retardée. Même en période de corona, l’approvisionnement des pièces ne s’est pas arrêtée.
Tom De Rudder nous montre dans le nouvel entrepôt la construction d’un Agriplanter 5SP-A, pouvant gérer cinq rangs. Le colosse mesure 3,30 mètres de haut et pèse 7,2 tonnes. L’ensemble est posé sur des chenilles qui assurent une répartition uniforme du poids pour ne pas abimer les champs. « Tout est commandé et ajusté via un écran tactile. La construction d’un modèle 5SP-A dure deux semaines. Un modèle plus petit, comme une planteuse de 2 ou 3 rangs, prend une semaine. En 2020, nous avons conçu 25 planteuses, de 1 à 6 rangs », conclut Tom De Rudder.
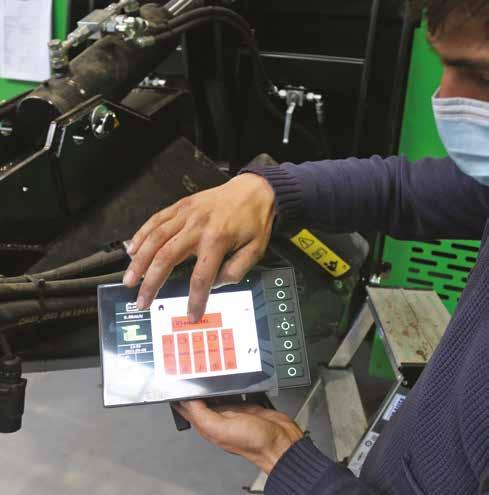
www.agriplanter.com www.smc.be

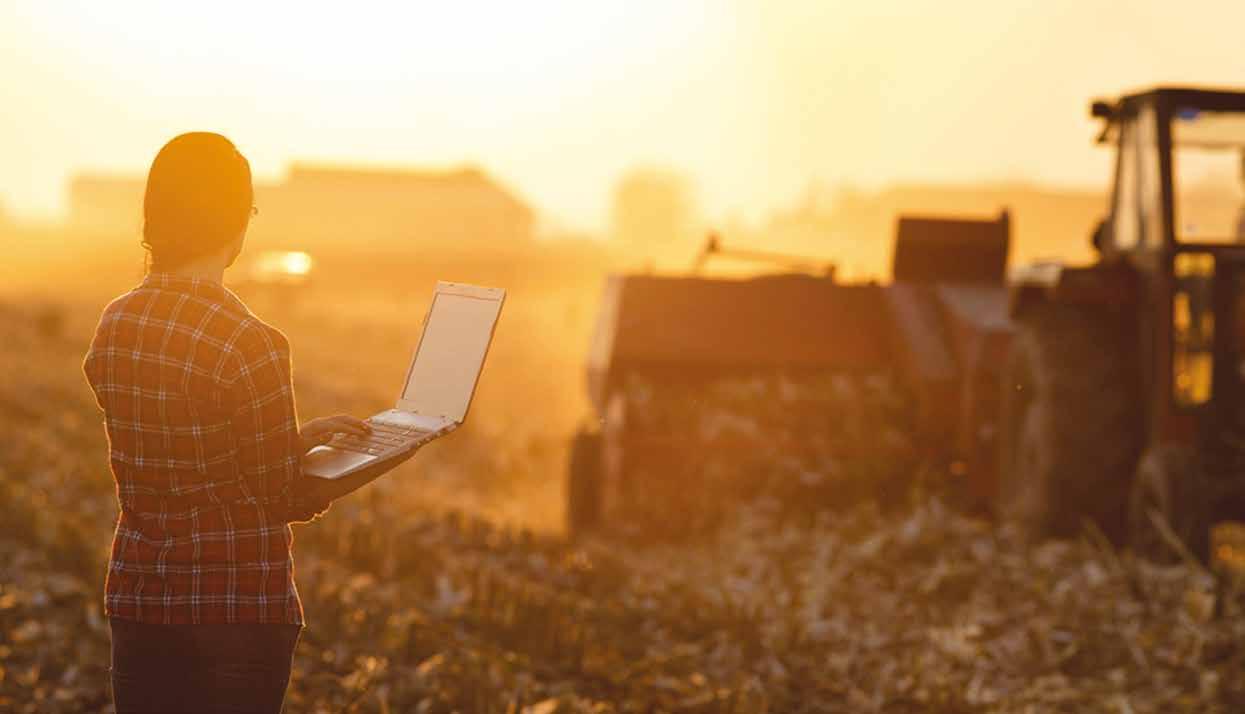
SOLUTIONS DE TRANSMISSION DE PUISSANCE POUR VEHICULES AGRICOLES AUTONOMES
La promesse d’une augmentation de la productivité agraire grâce aux véhicules agricoles autonomes stimule le développement rapide de cette technologie. Alors que de nombreux OEM testent ou mettent sur le marché des véhicules autonomes, de nouvelles solutions de transmission sont nécessaires pour optimiser la performance de ces nouveaux véhicules.
Grâce au guidage par laser ou par GPS, les véhicules agricoles sont maintenant capables d’effectuer des tâches de culture et de récolte de façon autonome. La technologie de robotique en essaim, qui permet à plusieurs robots de fonctionner collectivement et par le biais, assure le fonctionnement efficace de véhicules autonomes, même dans les plus grandes exploitations agricoles. Cependant, avec l’émergence de la technologie autonome, de multiples transmissions sont nécessaires pour couvrir la gamme de véhicules proposés par chaque OEM. Ces OEM utilisent des composants de transmission de puissance spécialisés, afin de répondre aux nouvelles exigences résultant de la complexité de ces véhicules du futur.
Petits véhicules électriques autonomes
Une tendance qui s’accentue dans le secteur agricole est celle du recours à de petits véhicules électriques standardisés sur lesquels peuvent être embarqués une variété d’outils. Cela permet à un seul robot d’effectuer efficacement de multiples tâches. Selon les batteries, ces véhicules peuvent généralement travailler sur le terrain jusqu’à 6 heures. Le rendement énergétique est un critère clé de la viabilité du véhicule, aussi il est extrêmement important de réduire la consommation des systèmes embarqués. Généralement, pour rester ouvert, un frein électromagnétique a besoin d’être constamment sous tension. En optimisant le fonctionnement du système de freinage, il est donc possible de réaliser d’importantes économies d’énergie.
Warner Electric, une marque d’Altra Industrial Motion Corp., a développé une solution répondre aux exigences de puissance des freins électromagnétiques avec son frein par impulsion SSPB. Ce frein est idéal en conditions sévères d’arrêt, que ce soit pour éviter des obstacles ou changer l’outil embarqué. Fournisseur mondial de freins électromagnétiques, Warner Electric a intégré une efficacité énergétique accrue dans le SSPB.
Le SSPB diffère des autres freins électromagnétiques parce qu’il s’ouvre et se ferme chaque fois qu’il reçoit une impulsion de courant. Cela se traduit par une importante réduction de l’énergie consommée par le système de freinage, permettant aux véhicules électriques ayant une capacité limitée de stockage des batteries de maximiser leur autonomie sur le terrain.
Véhicules Diesel automones
Étant donné les limitations de la capacité des batteries, au-delà d’une certaine taille et de puissance utile, son électrification complète est contre-productive. Pour faire rouler sur le terrain un tracteur de 250 ch pendant 8 heures, il faudrait une batterie pesant environ 15 tonnes – ce qui annulerait tout avantage d’efficacité ou de fonctionnalité que l’électrification complète pourrait éventuellement apporter.
Cela signifie que les moteurs à combustion resteront dans les engins agricoles des plus grandes exploitations pendant encore un bon bout de temps. Pour un véhicule autonome, cela fait ressortir l’importance de sa capacité à gérer la performance du moteur. La puissance fournie par le moteur doit être constamment gérée afin de s’adapter aux changements de terrain, de flux de récolte et des conditions de sol, tout en veillant au rendement énergétique global. Pour rationaliser ces données provenant d’un vaste réseau de capteurs, la puissance embarquée de traitement des informations à envoyer au système de gestion du moteur doit être considérable. Des solutions techniques sont nécessaires pour assurer le fonctionnement prévisible du moteur et réduire la puissanc requise pour exploiter le véhicule.
La gestion des moteurs est une spécialité de Jacobs Vehicle Systems, une autre marque d’Altra Industrial Motion Corp. Déjà bien établie dans les véhicules commerciaux routiers, Jacobs Vehicle Systems travaille directement avec les constructeurs des moteurs afin d’incorporer sans difficulté des technologies de frein moteur, d’actionnement variable de soupapes et de désactivation des cylindres dès la conception des moteurs.
L’actionnement variable des soupapes autorise le contrôle précis de leur mouvement et permet une mise au point optimale du moteur. Cela réduit la consommation de carburant, optimise les taux de compression, améliore la réponse transitoire, réduit les émissions et fondamentalement, assure le comportement prévisible du moteur, essentiel pour les véhicules autonomes mus par un moteur à combustion. En envisageant de telles technologies à l’étape de conception du moteur, les constructeurs de moteurs assurent la répétabilité et la prévisibilité du comportement du moteur, deux critères requispar les véhicules autonomes les plus recents
Véhicules autonomes hybrides Diesel / électriques
La transmission hybride constitue le juste milieu entre l’électrification complète et l’énergie fossile. Les entreprises agricoles cherchent à renforcer la protection de l’environnement dans les cas où l’hybridation convient aux exigences de taille et de puissance utile du véhicule.
En revanche, les pièces capables de répondre aux exigences des deux transmissions doivent faire preuve de souplesse. Stromag, marque d’Altra Industrial Motion Corp., offre sa gamme de combinaisons d’embrayages hydrauliques ou électromagnétiques « deux-en-un », d’accouplements flexibles ou d’accouplements élastiques. Offert prêt pour un assemblage immédiat (« plug and play ») : pour les chaînes de transmission hybride, le « deux-en-un » est monté entre le moteur à combustion et le moteur électrique. En embrayant ou en débrayant, le véhicule peut fonctionner selon les besoins sous propulsion diesel ou électrique.
Comme les véhicules autonomes hybrides contiennent des batteries, la limitation de la consommation énergétique globale est un autre facteur important. En réduisant les besoins énergétiques des systèmes auxiliaires tels que le climatiseur et les pompes hydrauliques, des gains d’efficacité peuvent être réalisés. Warner Electric offre un large éventail d’embrayages électromagnétiques qui offrent précisément cette fonctionnalité d’activation / de désactivation – garantissant l’utilisation la plus efficace possible de la puissance disponible.
www.altramotion.com

La technologie des machines agricoles autonomes étant encore à ses débuts, son potentiel mondial signifie que les produits sont en phase avec l’évolution des différentes approches en matière de transmission, approches indissociables de l’introduction de cette nouvelle technologie hydrauliques ou électromagnétiques « deux-en-un », d’accouplements flexibles ou d’accouplements élastiques
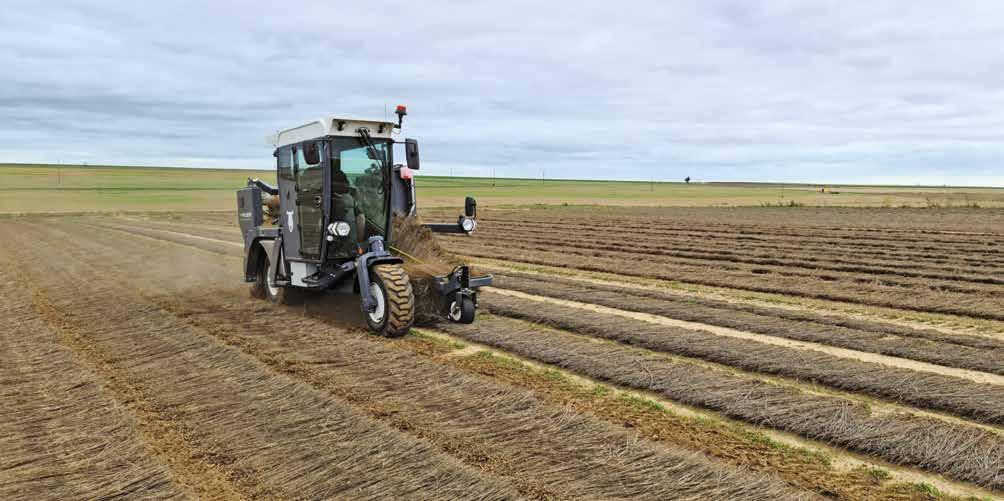
L’Easy-Turn 113A retourne les cultures récoltées sur le champ.
HYLER ET BOSCH REXROTH RÉCOLTENT LE CHANVRE ENSEMBLE
La culture du chanvre est en plein essor ces dernières années, c’est un marché porteur par excellence au sein des cultures agricoles. Une bonne nouvelle donc pour les producteurs de lin et de chanvre mais aussi les fournisseurs de moissonneuses et de machines de transformation des fibres. Le fabricant qui parvient à développer la première moissonneuse industrielle pour le chanvre industriel et le traitement de la fibre longue et à la commercialiser avec succès a un bel avenir devant lui. L’entreprise Hyler de Wielsbeke l’a bien compris et vise l’innovation pour faire la différence. Elle a trouvé en Bosch Rexroth le partenaire idéal.
« Le lin et le chanvre sont souvent mentionnés comme des cultures fournissant une contribution significative à l’obtention de l’European Green Deal », explique Niels Baert, le fondateur et administrateur de l’entreprise Hyler en Flandre occidentale, qui conçoit des machines pour la récolte et la transformation des fibres textiles. « Ils sont cultivés localement, sont négatifs en CO2 et contribuent à la biodiversité. De plus, les produits extraits du lin et du chanvre sont populaires. La culture du chanvre est intéressante aujourd’hui parce que notre climat est de plus en plus sec et l’usage de produits phytopharmaceutiques n’est pas nécessaire. »
Hyler a développé une machine capable de récolter et de transformer le lin mais aussi le chanvre. L’entreprise augmente significativement l’offre actuelle dédiée à la technique de récolte du lin et sa transformation. Niels Baert: « Les agriculteurs qui cultivent le lin sont intéressés par le chanvre comme culture supplémentaire. Cependant, il n’existe pas de machines pour récolter le chanvre efficacement, le déposer parallèlement en andains (rangées de culture, ndlr) sur le champ comme le lin, en utilisant les mêmes machines que celles du lin pour les traitements ultérieurs. Nous avons donc décidé de combler cette lacune sur le marché avec un produit qui se démarque dans tous les domaines. »
L’innovation est dans l’ADN
Pour réaliser cela, il fallait un partenaire fiable qui, à l’instar de Hyler, allie la solidité et la volonté d’innovation. « Vers qui d’autre se tourner que Rexroth avec qui nous avons déjà construit des machines ensemble », poursuit Niels Baert. « Nous avons découvert et apprécié l’approche personnalisée et le soutien actif de cette entreprise, et nous étions convaincus de pouvoir réaliser ce projet innovant ensemble. »
« L’innovation est ancrée dans notre ADN », confirme Maarten Van Houtte, account development manager mobile applications chez Bosch Rexroth Belgium. « Nous proposons notre savoir-faire de plusieurs décennies pour aider les clients à concevoir une solution qui correspond à leurs besoins. Nous n’hésitons pas à leur proposer des alternatives si nous pensons que les résultats seront meilleurs que les spécifications qu’ils nous demandent. Et le fait de développer une nouvelle catégorie de produits rend le défi encore plus intéressant. »
Sur le marché des engins mobiles tout-terrain, Rexroth propose une large gamme de produits et assume pleinement le rôle de partenaire en matière de pilotage des machines. Rexroth n’est pas qu’un fournisseur de systèmes hydrauliques mobiles ou stationnaires, mais propose également l’automatisation des machines tant au niveau composant que logiciel. Elle se focalise sur un support local pouvant répondre efficacement aux besoins des clients.
Un concept novateur dans tous les domaines
Développée par Hyler avec le soutien de Rexroth, cette machine est innovante à bien des égards. Tout d’abord, elle est multifonctionnelle : baptisée Sativa 200, elle peut être mise en œuvre tant pour la culture du lin que d’autres plantes textiles grâce au développement de deux systèmes de récolte spécifiques. Pour la récolte du chanvre, la machine est conçue de manière telle que les tiges de chanvre, naturellement longues, sont déposées en parallèle au sol.
La machine est entraînée par la combinaison d’une pompe à haute pression A4VG et quatre moteurs de roue A6VE montés sur les réducteurs de roue GFT8120 qui forment la base du train de transport. Les composants extrêmement solides font partie de l’offre standard de Rexroth, mais l’expérience de transport ultime a lieu par la création d’une symbiose parfaite dans le logiciel de conduite où la pompe et les moteurs ainsi que le frein dynamique dans les réducteurs de roue réagissent et interagissent au bon moment. Ce logiciel de conduite, supporté par Rexroth, évolue en permanence et intègre tant des expériences mondiales que locales, chaque machine étant différente. Le logiciel est aussi essentiel dans l’application des fonctions de sécurité pertinentes qui évoluent aussi en permanence.
La commande et l’exécution du logiciel de conduite a lieu via la gamme d’électronique mobile de BODAS qui comprend notamment des contrôleurs, des capteurs et des joysticks. Thomas Van Mossevelde, application engineer et responsable de l’élaboration du logiciel, nous explique que faire avancer la machine et la rendre opérationnelle représente 80 pourcents du travail. « C’est aussi la partie la plus simple. Les 20 derniers pourcents d’optimisation font la différence et sont généralement la clé du succès. »
Rexroth travaille toujours en fonction des commentaires du client. Pour l’hydraulique de fonctionnement, la meilleure adéquation a été recherchée entre ce que devait réaliser la commande et les composants les plus efficaces capable de le permettre
Analyse dans le cloud
La grande innovation se trouve dans les plus petits composants de la machine, comme les capteurs qui collectent de l’information pendant la conduite et l’envoient au cloud pour une analyse approfondie. Le choix s’est porté sur BODAS Connect qui, outre les hardware et software, forme le troisième pilier de l’application BODAS. BODAS Connect est la solution IoT (Internet of Things) et Telematics de Rexroth.
Les données sur la consommation, la distance et autres paramètres pertinents sont envoyées à Hyler qui soutient idéalement le client par la planification d’une maintenance

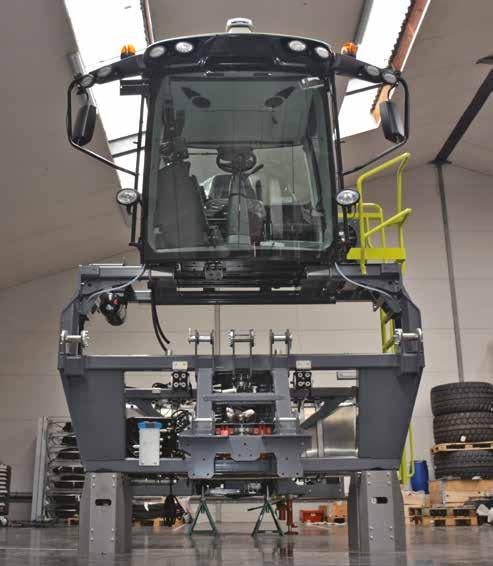
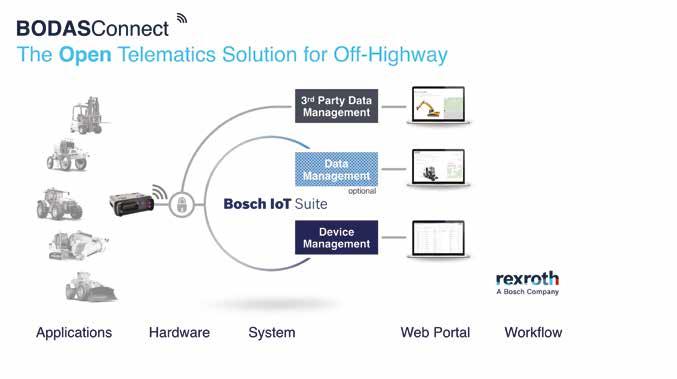
BODASConnect, la solution télématique ouverte pour le tout-terrain.
Rendu de la Sativa 200 intégrant les composants de Bosch Rexroth
lorsqu’elle s’avère vraiment utile, et non une maintenance annuelle classique qui a généralement lieu trop tôt ou trop tard, et par le remplacement en temps opportun de composants usés ou défectueux. Les mises à jour logicielles sont téléchargeables via BODAS Connect pour que le client soit automatiquement à jour sans devoir faire venir un technicien sur place. « Cela fait une belle différence pour le client : si des problèmes techniques surgissent sur la machine, nous pouvons l’assister immédiatement », fait remarquer Niels Baert.
Un élément plus intéressant pour Hyler est l’utilisation des capteurs pour collecter des données sur la récolte, souligne Niels Baert: « Ces données signifient une grande valeur ajoutée. Nous disposons d’une mine d’informations sur le processus de récolte et les paramètres idéaux pour une récolte optimale. »
Ces informations sont précieuses pour l’agriculteur qui peut ajuster le processus de récolte et poser d’autres choix. Les données et analyses sont aussi pertinentes pour Hyler. Niels Baert: « Avec une machine révolutionnaire et innovante comme celle-ci, il y a peu de données historiques qui indiquent à quoi doit ressembler la machine idéale. Les données en temps réel sur certains paramètres, charges, conditions de conduite selon une zone géographique sont capitales pour les prochaines machines. Elles offrent des perspectives qui nécessiteraient sinon plusieurs années. Vous découvrez comment la machine se comporte et vous comparez cela aux attentes que vous aviez définies. Ces perspectives nous aident à ajuster la machine actuelle et à construire des machines encore meilleures dans un proche avenir. Nous restons ainsi fidèles à notre réputation d’acteur innovant. »
Dans cette histoire complexe, BODAS Connect s’avère être un bon facteur de support et d’accompagnement. Grâce au système ouvert, il est possible d’obtenir une solution complète et des interactions sont possibles avec d’autres plateformes ayant leur propre cloud ou développements. Par cet environnement ouvert, BODAS Connect l offre une réponse à des questions souvent très complexes.
Succès commercial
Cette combinaison d’éléments innovants et de composants fiables éprouvés est une douce musique pour de nombreux agriculteurs. Des machines ont été commandées avant le lancement de la production. Au fur et à mesure que les engins prennent forme, l’intérêt augmente. Hyler a déjà prévendu toutes les machines dont la production est planifiée cette année. « Les clients sont dans une file d’attente (rires), et l’intérêt va encore croître lorsque les premières récoltes auront été réalisées avec ces machines », assure Niels Baert avec confiance. « Cela représente une véritable percée pour Hyler. Cette ligne de production est promise à un bel avenir et d’autres machines suivront pour d’autres applications mais toujours avec la même combinaison gagnante d’un hardware fiable et d’un software et d’une connectivité innovantes. »
Hyler a idéalement utilisé le marché en croissance des fibres naturelles comme tremplin pour son propre marché de croissance, un marché de machines pour la récolte et la transformation de lin, de chanvre, de jute et de kénaf avec des équipements hautement fiables et qui deviennent plus intelligents récolte après récolte, mètre après mètre. « Avec Rexroth, nous promettons un avenir brillant au lin et au chanvre », conclut Niels Baert.
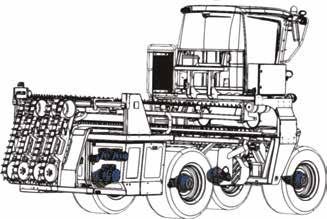
www.boschrexroth.com www.hyler.be
LE TRI AUTOMATISÉ DES CERISES A LA COTE
Produire un bon produit est une chose, le proposer au marché en est une autre, toute aussi importante. Dans le cas de la culture de la cerise, le diamètre du fruit est une caractéristique essentielle car il détermine son prix en grande partie. En outre, le processus de triage joue un rôle important car il permet au producteur de comprimer les coûts. Une machine conçue spécifiquement pour le pré-triage des cerises accélère le processus et le rend plus précis et fiable.
Les producteurs qui mettent leurs cerises en vente peuvent apporter leur production fraîchement récoltée à la criée. Les cerises sont alors triées pour déterminer leur calibre et la classe de prix, les plus charnues recevant un meilleur prix au kilo. Pour cette méthode de tri cependant, le producteur doit payer 50 cents par kilogramme fourni. Réaliser un pré-triage permet de neutraliser ce surcoût. Jadis, le processus de tri était mécanique et consistait notamment en un système de courroies trapézoïdales que l’on plaçait côte à côte. En les écartant légèrement, on obtenait un tri car les plus petites cerises passaient à travers les courroies. Mais la méthode était peu précise et nécessitait un traitement et un ajustement manuels supplémentaires. De plus, la capacité de traitement d’environ 200 kg à l’heure était insuffisante.
L’entreprise limbourgeoise Agrosoft a donc développé une machine de triage automatique. Son dirigeant, Willy Vanderlinden, nous explique comment il a abordé ce projet : « Nous avons développé un système de tri qui fonctionne sur base d’une mesure optique du diamètre du fruit. Nous avons dû surmonter plusieurs obstacles avant d’optimiser le processus. Tout commence par l’acheminement correct des cerises. Elles sont d’abord séparées et étalées manuellement sur un large convoyeur entraîné par des tambours moteurs asynchrones de LAT Himmel, un choix fondé sur leur montage parfaitement hygiénique. Il y a ensuite les convoyeurs à bande en forme de V entraînés par des moteurs compacts BLDC (Brushless DC) IP66 d’Orientalmotor. Nous les avons choisis pour la régulation de vitesse synchrone et facilement paramétrable. Le côté gauche du convoyeur est plus rapide que le côté droit, ce qui force les cerises à s’aligner sur une rangée. Après cette première action, les cerises arrivent sur un second convoyeur en forme de V plus rapide que le précédent afin de créer un espace entre deux cerises et les présenter avec leur pédoncule vers l’arrière. Elles sont alors parfaitement positionnées pour la mesure proprement dite. Les cerises arrivent sur un plateau circulaire rotatif dont l’extrémité comprend 100 broches sur lesquelles sont montés des rouleaux évidés en leur centre pour accueillir une cerise. Les rouleaux avec la cerise effectuent une rotation sous la caméra qui mesure la cerise sous plusieurs positions. Quatre diamètres et deux fois la surface sont calculés pour chaque cerise. »
« Lors de la prise de mesure, la qualité de la lumière est essentielle, et ce fut la partie la plus difficile à optimiser. Si la
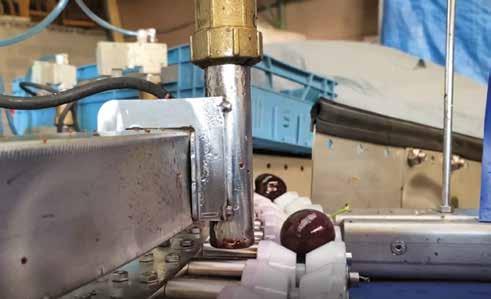
Le pré-triage automatique des cerises évite des coûts au producteur.
Les moteurs BLDC ont été choisis pour la régulation de vitesse synchrone et facilement paramétrable.
sélection avait lieu selon une image en couleur familière, la précision serait moins bonne. Nous avons donc opté pour une image en noir et blanc et une lumière halogène. Cela donne une image plus claire qui facilite la mesure. »
« Après le processus de mesure, les cerises passent par des poussoirs d’éjection, chaque poussoir représentant une classe spécifique. Via l’automate, chaque poussoir sait les cerises qu’il doit souffler vers le bac de collecte ou le convoyeur. Le temps de soufflage et la pression sont réglés avec précision pour éviter l’endommagement les cerises. Dans une configuration standard, on parle de 3 centièmes de seconde. »
Grâce aux évolutions dans le domaine du traitement de l’image et la puissance de calcul, la caméra est capable de calculer le diamètre et la couleur de 15 cerises à la seconde. Sachant que le poids moyen d’une cerise est de 11 grammes, cela donne une capacité de traitement théorique de 594 kg à l’heure. Dans la pratique, on ne peut remplir qu’une bonne moitié des rouleaux, ce qui porte la capacité réelle à environ 300 kg à l’heure. Une quantité qui coûterait 150 euros au producteur à la criée. Le délai d’amortissement est donc très court.
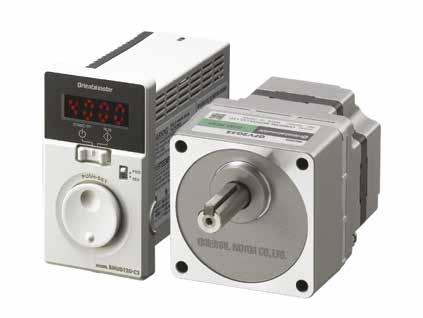
UNE EFFICIENCE AMÉLIORÉE POUR LES REMORQUES DES ENGINS AGRICOLES
Les engins agricoles nécessitent une attention particulière. Ils doivent être opérationnels par tous les temps, sont confrontés à des impacts majeurs et doivent effectuer diverses tâches nécessitant à la fois de la précision et de la rapidité. Par ailleurs, anno 2021, ils doivent être économes en énergie et durer toute une vie, pour ainsi dire.
Ces exigences s’appliquent aux nombreux composants mis en œuvre. Nous avons choisi de nous attarder sur les vannes hydrauliques. Ces dernières années, de sérieux efforts ont été fournis en matière d’efficacité énergétique, de poids et de flexibilité dans les installations hydrauliques mobiles. Chez VB Parts à Roeselare, nous avons trouvé un beau résultat de ces efforts avec le bloc de vannes LVS. Les vannes de commande proportionnelles, avec leur débit de 180 l/min et une plage de pression jusqu’à 350 bars, sont mises en œuvre tant dans les véhicules entraînés qu’à traction. Comment ces composants sont-ils adaptés à la dure vie agricole ? Une première caractéristique est leur structure compacte, offrant de la place tant aux vannes à commande électrohydraulique à deux étages qu’aux vannes magnétiques. La double fonction permet de réaliser diverses tâches simultanément, ce qui accélère le travail. Cette fonctionnalité étendue n’est pas un luxe superflu.
Une commande multiple
Si on prend une tonne à lisier comme exemple, on peut voir que les versions modernes disposent de plusieurs fonctions allant de l’accouplement automatique lors du chargement du lisier, à l’entraînement de la pompe réalisant cela, au mélange permanent pendant le travail, l’adaptation de la hauteur de châssis et l’épandage proprement sur les champs jusqu’au nettoyage automatique par après. Ces fonctions nécessitent à chaque fois des propriétés de commande adaptées, certaines étant proportionnelles et d’autres fonctionnant via un actionneur on/off classique qui requiert moins de débit. Si l’ensemble est commandé via un seul bloc de vannes modulaires, cela signifie un gain d’énergie et de place, ce qui profite à la fois au producteur et à l’utilisateur final. Dans le cas présent, des vannes en version à siège ou réglables sont prévues. Elles se commandent comme des actionneurs on/off en les combinant à des vannes bidirectionnelles SVH04 et des sièges de soupape à commande hydraulique ou régulation électronique.
Engins entraînés
Pour les engins entraînés, la qualité de la PTO (prise de force) hydraulique est mise en avant, l’utilisateur pouvant basculer entre la commande de l’engin et les fonctions à commande hydraulique. Aujourd’hui, on remarque un entraînement direct via le moteur de l’engin et une pompe hydraulique. Lorsque l’engin est en mode conduite, un bypass désactive la pompe. Si une action est requise à partir d’une fonction hydraulique, une pression sur le bouton suffit à désactiver le bypass et les fonctions hydrauliques sont à nouveau disponibles. Comme la pression n’est pas constamment requise, une belle économie peut être réalisée sur le diesel. Dans certains systèmes, on parle de commande pneumatique via Canbus, où les cylindres sont couplés aux vannes de commande hydrauliques et à une protection via les capteurs électroniques. On peut parler à juste titre d’un secteur multitechnologique.
Un autre système intéressant pour exécuter plusieurs fonctions simultanément se trouve chez Bucher Hydraulic et concerne la technologie split-tool LVS12 (photo) où une vanne de régulation est scindée. Dans le boîtier se trouve 2 vannes de régulation. Deux commandes peuvent donc fonctionner simultanément et indépendamment l’une de l’autre à un débit de 180 l/min et 350 bars. Les applications dans le secteur agricole sont légion comme le levage/l’abaissement ou la commande simultanée de 2 moteurs. La fonction d’alimentation et de retour de cette solution est identique à un support de pression réglable, en ce sens que les vannes d’alimentation et de retour peuvent être commandées et positionnées indépendamment l’une de l’autre. En faisant varier le rapport des ouvertures d’alimentation et de retour, chaque pression souhaitée peut être dirigée vers la sortie de l’actionneur.
www.hydrauliek-vbparts.be

VB Parts : le LVS12