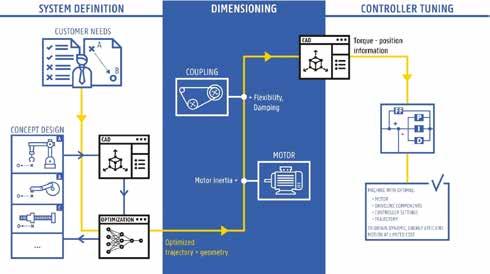
7 minute read
CASE STUDY Tetra OptiMotion : Optimisation
OPTIMISATION D’UN RESPIRATEUR POUR PATIENTS COVID 19 AU LIEU DE VENTILATEUR CORONA
Les constructeurs de machines subissent une pression croissante pour optimiser la productivité, les coûts et la qualité des machines. Les tentatives visant à minimiser les coûts et à maximiser la qualité et la productivité reflètent la nécessité de trouver un optimum. Pour optimiser les ressources et les composants à l’extrême, la conception ne peut plus reposer sur l’instinct ou l’expérience. Il faut une méthodologie qui puisse garantir un fonctionnement optimal.
Advertisement
Deux tendances permettent d’optimiser la conception de machines. La première concerne les opportunités de conception virtuelle, avec les diverses options de simulation au sein des outils de CAO. La plupart des constructeurs de machines travaillent déjà avec un logiciel CAO, mais de nombreuses PME ne l’utilisent que pour la modélisation 3D de machines. Ce logiciel CAO permet aussi de simuler immédiatement l’effet des modifications apportées dans le concept machine (ingénierie virtuelle). Une étude antérieure de Tetra (AmoCAD) a montré dans six cas industriels que le couple d’entraînement d’une machine existante peut être réduit de 50%, représentant une économie de 20% sur le prix d’achat du moteur, en utilisant des outils de simulation CAO.
La seconde tendance se situe dans le potentiel des routines d’optimisation mathématiques. L’objectif global du projet Tetra OptiMotion est de convertir des algorithmes complexes en outils aisément applicables pour la PME - le constructeur de machines.
La combinaison de ces deux tendances - des algorithmes utilisant des modèles de machines virtuels dans un environnement de CAO pour l’optimisation du concept machine – offre un potentiel énorme.
Tetra OptiMotion
Le projet Tetra est une collaboration entre l’Université de Gand campus Courtrai, l’Université d’Anvers et Flanders Make. Un projet TETRA (TEchnology TRAnsfer) vise à étudier des nouvelles technologies industrielles et à les déployer de manière claire et rapide au groupe cible.
Pendant le projet, un flux de travail compréhensible (figure 1) est établi en tant que fil conducteur pour la conception virtuelle et l’optimisation d’un système mécatronique. Il est divisé en trois grands piliers : System Definition, Dimensioning et Controller tuning.
Pendant le projet, ce flux de travail a été appliqué sur plusieurs cas industriels afin de démontrer la plus-value dans la pratique. Un de ces cas est l’optimisation d’un concept de respirateur Covid 19, développé par Gear Up Medical vzw.
Figure 1: Flux de travail d’un projet Tetra OptiMotion
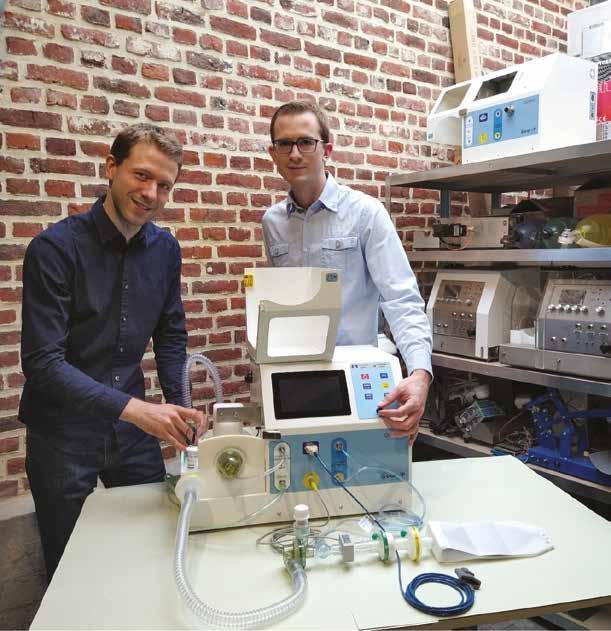
Stijn et Jan Herregodts
ressort / soufflet
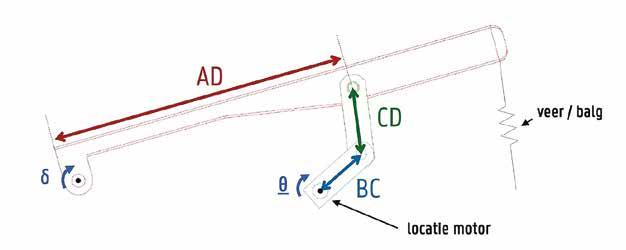
résilience à l’indentation
emplacement du moteur
Figure 3: Le mécanisme des tiges du respirateur Covid 19
Le respirateur COVID 19
Lorsque la pandémie de corona a éclaté début 2020, le monde entier a connu une pénurie de respirateurs dans les unités de soins intensifs pour le traitement des patients souffrant du virus.
L’entraînement du respirateur Covid 19 repose sur un mécanisme à tiges, entraîné centralement par un moteur DC. Une représentation simplifiée de cet entraînement est illustré à la figure 3. Ce mécanisme effectue un mouvement répétitif de haut en bas qui comprime le soufflet à air (représenté comme un ressort) pour créer un débit d’air spécifique qui est envoyé dans les poumons du patient.
Dans le cas du respirateur Covid 19, le défi à relever se situait au niveau de la définition des dimensions optimales des tiges d’entraînement (AD, CD et BC) pour obtenir un couple d’entraînement le plus bas possible. Pour cette question d’optimisation, l’équipe TETRA a suivi et appliqué la ‘Optimisation’.
En réduisant le couple d’entraînement, il est possible de sélectionner un moteur d’entraînement plus petit/moins cher, ce qui diminue la consommation énergétique de la machine.
Optimisation du concept
Après avoir défini les objectifs de la machine à développer et à optimiser, l’étude du concept a suivi. Plusieurs solutions potentielles ont été comparées les unes aux autres pour obtenir finalement le concept optimal. Il n’est pas évident pour l’utilisateur de comparer ce concept objectivement et de déterminer les dimensions optimales des composants de l’entraînement. L’aspect innovant du flux de travail OptiMotion est qu’il utilise des simulations de mouvement CAO associées à des algorithmes d’optimisation.
La tâche supérieure de l’algorithme d’optimisation est de générer des combinaisons de dimensions (dans une plage imposée), de les proposer au logiciel CAO afin de convertir automatiquement les nouvelles dimensions en un modèle 3D adapté, pour finalement définir le couple d’entraînement correspondant au nouveau concept. Sur base du résultat, l’algorithme prend des décisions intelligentes pour générer un nouvel ensemble de dimensions et relancer le cycle. Après la mise en place du cycle d’optimisation (figure 4), des recherches efficaces et automatiques peuvent avoir lieu entre des centaines de combinaisons de dimensions possibles. Un concept optimal peut alors être obtenu dont le couple d’entraînement est fortement réduit.
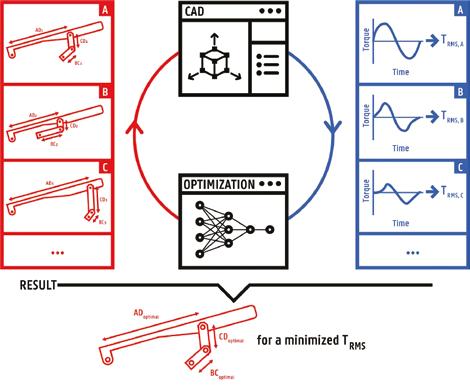
Figure 4 : Concept du cycle d’optimisation
CONCEPT
Concept initial Concept optimisé
TRMS [Nm] Tmax [Nm]
11,29 6,37 - 43,61 16,03 8,48 - 47,13
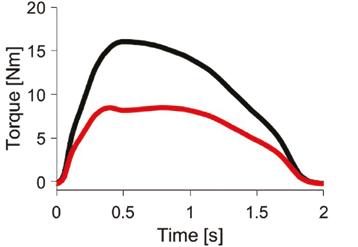
Tableau 1 : Résultats liés au respirateur Covid 19

Le team Tetra OptiMotion (de gauche à droite): Abdelmajid Ben Yahja, Stijn Derammelaere, Santiago Ramos Garces, Nick Van Oosterwyck, Simon Houwen et Bart Vanwalleghem.
Résultats
En appliquant le flux de travail OptiMotion sur le respirateur Covid 19, des réductions significatives allant jusqu’à 43.61% du couple d’entraînement RMS sont réalisées par rapport au concept initial (tableau 1). Le résultat de la routine d’optimisation est un concept optimisé avec un profil de vitesse et de couple correspondant. Sur base de cela, les composants d’entraînement peuvent être idéalement adaptés à l’application (pilier 2 du flux de travail, figure 1), permettant notamment la sélection d’un moteur plus petit/meilleur marché.
Lorsque le couple d’entraînement diminue, la vitesse du moteur va augmenter pour respecter l’équilibre de puissance. Mais étant donné que les pertes dépendent principalement du couple d’entraînement requis, la réduction du couple résultera en une consommation d’énergie réduite. Les mesures d’énergie effectives entre un concept optimisé et un concept initial ont confirmé la diminution drastique (33,2%) de l’énergie consommée.
Conclusion
Le projet Tetra OptiMotion étudie les possibilités d’optimisation d’un concept machine au moyen de l’ingénierie virtuelle. Cette approche peut être appliquée pour l’optimisation d’un concept, comme celui du respirateur Covid 19, mais d’un trajet d’entraînement. Les essais sur des cas industriels ont montré que par l’optimisation de la géométrie ou du trajet d’entraînement, il était possible de réduire le couple d’entraînement jusqu’à 40%! L’optimisation d’un composant ou d’une combinaison de composants offre de nombreux avantages. Les principaux sont:
• Par la minimalisation du couple d’entraînement et l’adaptation optimale des composants d’entraînement, il ne faut plus surdimensionner les composants et un moteur plus petit peut être sélectionné. • La diminution du couple d’entraînement va de pair avec une réduction de la consommation d’énergie de la machine! • Le cycle de conception est plus rapide et donc meilleur marché : les différents concepts/prototypes peuvent être testés virtuellement (dynamiquement).
Une journée d’étude pour présenter les résultats d’un projet de deux ans
Le mercredi 22 septembre 2021, une journée d’étude sera organisée pour présenter les résultats/méthodes du projet. Si les résultats de ce projet ou la journée d’étude vous intéresse, n’hésitez pas à contacter bart.vanwalleghem@ugent.be ou stijn.derammelaere@uantwerpen.be.
Réalisez rapidement et simplement une machine totalement flexible : avec XTS
www.beckhoff.be/xts
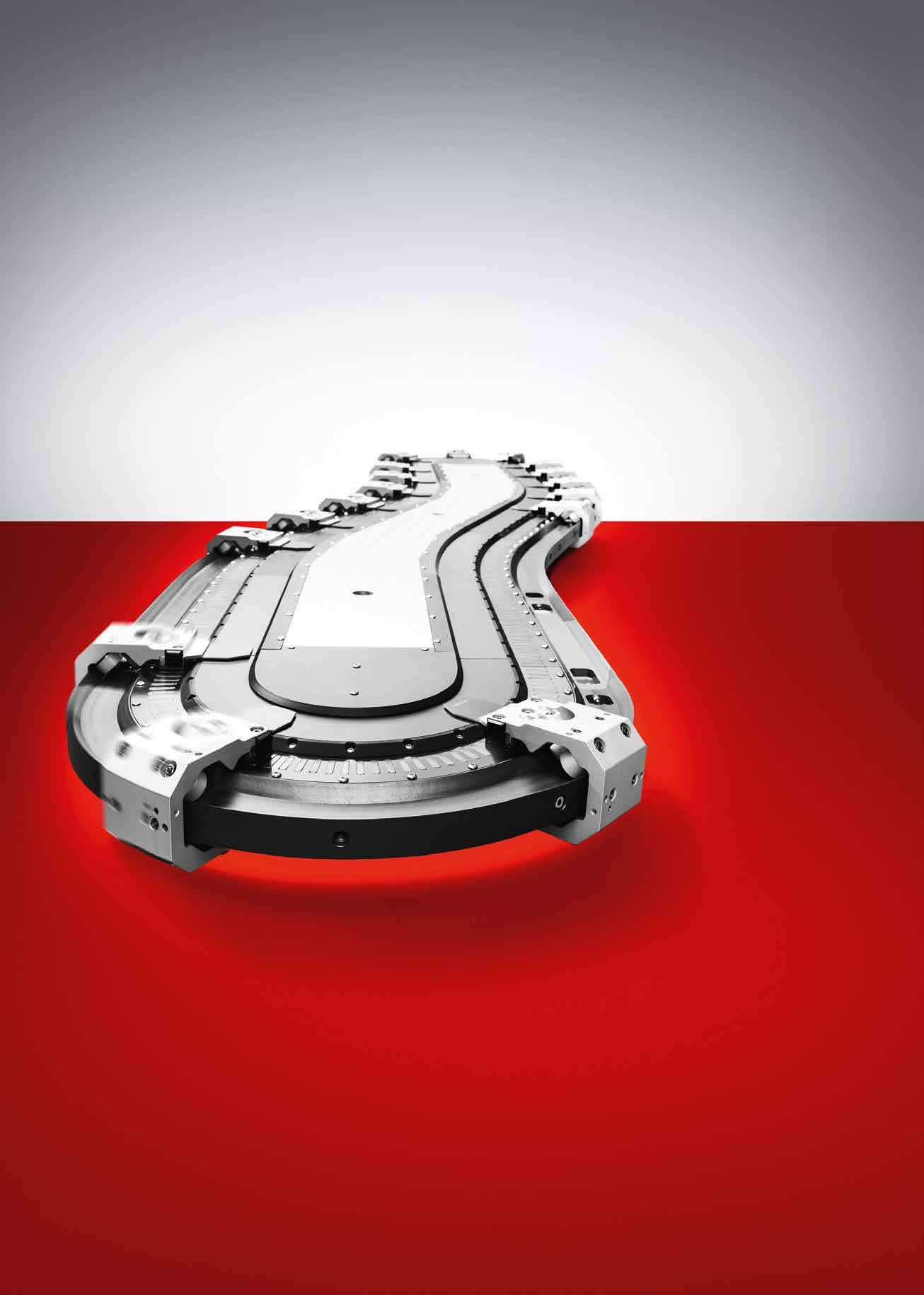
Les industriels du monde entier doivent proposer des produits de plus en plus personnalisés – avec des machines de moins en moins encombrantes tout en améliorant la productivité. Le système de transport linéaire XTS offre ces précieux atouts, en association le contrôle commande sur base PC et l’EthernetCAT. Flexible, il permet de réaliser de nouveaux concepts de machine, adapté aussi bien pour le transport, la manutention que le montage. Dans sa version en acier inoxydable Hygienic, XTS est le système idéal pour une utilisation dans l’industrie Alimentaire et Pharmaceutique.
Positionnement de montage totalement flexible
Construction compacte et optimisé
Géométrie librement sélectionnable
Peu d’éléments et composants mécaniques
Les avantages de l’XTS
Mouvement circulaire Système modulaire et flexible Mover à mobilité individuelle
Les bénéfices pour les utilisateurs
Plusieurs étapes de fabrication en une seule machine Gain de place des installations Changement de format contrôlé par un logiciel sur base PC Amélioration de la disponibilité Augmentation de la production Réduction des délais de mise sur le marché