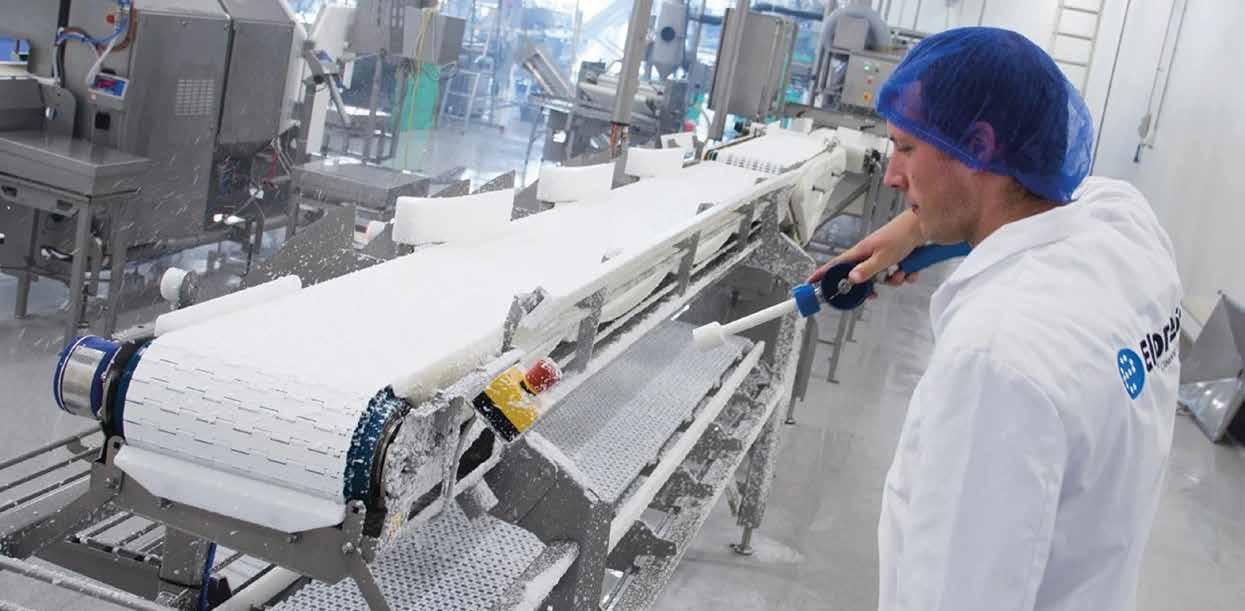
14 minute read
DOSSIER Hydraulica, pneumatica en elektromechanica in de drankenindustrie
Frequente reiniging met chemicaliën, hoge druk, contact met vet, vocht en warmte… de lijst met negatieve invloeden is ellenlang in de voedingssector. Dat heeft repercussies voor de machinebouw.
TUSSEN VOEDSELVEILIGHEID EN PRODUCTIVITEIT: DE DAGELIJKSE EVENWICHTSOEFENING VAN DE VOEDINGSINDUSTRIE
Advertisement
De voedingssector is een zeer belangrijke pijler van onze Belgische economie. Een omzet van 54,4 miljard euro, bijna 100.000 FTE-jobs en meer dan 4.000 actieve bedrijven, de cijfers zijn op zijn minst impressionant te noemen. Ook de technologische investeringen zijn niet minnetjes. In 2020 - omwille van evidente redenen nochtans een uitdagend jaar - klokten die af op 1,8 miljard euro. De speerpunten van de investeringen richten zich naast de betere infrastructuur vooral op digitalisering en automatisering.
Voor dit centrale dossier in Automation Magazine leggen we de focus vooral op de automatisering in de voedings- en drankensector. Iedereen die actief is of was in deze sector, zal het ongetwijfeld beamen: werken voor de voedingsnijverheid is niet altijd even evident. De vaak moeilijke omstandigheden waarin componenten en installaties moeten blijven opereren vormen een belangrijk obstakel. Vet, vocht, warmte, reiniging onder hoge druk, contact met bijtende producten en koude zijn maar enkele van de mogelijke extra hordes die moeten genomen worden. Dat zal ook later in dit dossier blijken, met bijvoorbeeld een case waar de loutere aanwezigheid van suiker al voldoende was om een installatie in de war te sturen. Ook de specificiteit van elk product is een hinderpaal. Het opnemen en verplaatsen van dozen is bijvoorbeeld relatief eenvoudig door de herhaalbaarheid maar bij de nietvormvaste producten die in de voedingsindustrie schering en inslag zijn is dit een compleet ander verhaal. De inherente verschillen in producten dwingen systeembouwers om deze diversiteit ook op te nemen in hun installaties. In deze sector wordt daarom met heel veel belangstelling uitgekeken naar pakweg de prestaties van camerasystemen met beeldanalyse via artificiële intelligentie, of naar evoluties in robot- en grijpertechnologie.
Er zijn daarnaast nog bijkomende restricties en speciale regels van kracht, die een extra uitdaging vormen bovenop de uitdagingen van ‘standaard’ automatiseringsprojecten. Specifiek denken we dan in eerste instantie aan voedselveiligheid. Elk voedingsbedrijf is als de dood voor een besmetting of contaminatie van hun product met een voedselvreemd item. Dat heeft vaak ook grote gevolgen voor de machines, installaties en technieken die er ingezet worden.
Om dat te staven volstaat het te wijzen naar de bekende HACCP methode, die vandaag officieel evenwel niet meer van toepassing is, maar wel nog frequent gebruikt wordt. Daarin worden meerdere potentiële risicobronnen voor contaminatie aangeduid:
• Medewerkers: Hoesten, niezen, vuile handen, haarverlies, ontstoken huidwonden, … • Voedingsmiddelen: Besmette rauwe grondstoffen zoals verse groenten, vlees en gevogelte, eieren, productbereidingen, toxines in schaal- en schelpdieren, … • Werkmethodes: Slecht uitgevoerde handelingen zoals het onvoldoende wassen van de handen, het gebrekkig schoonmaken van de lokalen, een verkeerde manipulatie van de producten, ongunstige opslagomstandigheden, foutieve verpakking, gebrekkig afvalbeheer, … • Omgeving: Besmette lucht, verkeerde inrichting van de lokalen, aanwezigheid van insecten of ongedierte, … • Uitrusting: Besmette of slecht schoongemaakte oppervlakken, materiaal, machines, werktafels, verpakkingen, …
Hoe kan technologie hierbij helpen?
De rol van technologie wordt - in tegenstelling tot wat men zou kunnen denken - niet beperkt tot de laatste pijler. Uiteraard ligt het zwaartepunt op zaken als makkelijk afwasbare materialen, het vermijden van vuilophoping in hoeken en randen en de inzet van voedselveilige producten en vloeistoffen. Alle mogelijke onderdelen moeten daarbij onder de spreekwoordelijke loep genomen worden: de bekabeling, machinebesturing, drukknoppen, verdeelkasten, vloeren, wanden, hekwerken en noem maar op.
Een mooi voorbeeld van dit soort voedselveilige uitrusting vinden we bijvoorbeeld bij de aandrijvingen. Hun opgewekte warmte is een doorn in het oog van de voedselveiligheid, want wie via ventilatie de hitte wil afvoeren wordt willens nillens een verspreider van potentiële contaminanten vanuit de aandrijving, zoals roest. Dat voorkomen kan via diverse pistes. Een eerste oplossing voor het vermijden van roestdeeltjes en ander vuil is werken met RVS/Inox. Daarvoor zijn er opnieuw enkele gradaties: - Een tandwielkast met uitgaande as, met het huis en de uitgaande as standaard uit RVS - Een tandwielkast met uitgaande as, met de gehele tandwielkast met motorflens uit RVS - Een tandwielkast met uitgaande flens, met het huis en de uitgaande flens standaard uit RVS - Een tandwielkast met holle uitgaande as, met het huis en de holle as standaard uit RVS
Andere oplossingen zijn onder meer het weghalen van de aandrijving uit de productieruimte of het groter dimensioneren van de motor, zodat er minder warmte geproduceerd wordt. Maar hoe bepaal je nu voor elk onderdeel van de installatie welke optie het best is? Want de keuze voor de aandrijving is slechts één van de vele
De veelheid aan normen en regels maakt het niet evident om een consensus te bereiken over de opbouw van een installatie.


Roestvast staal is zeer geschikt voor de voedselverwerkende industrie.
facetten in de opbouw van een voedselveilige installatie. Het gebeurt soms dat een installatie volledig conform de regels is opgebouwd - daar komen we meteen op terug - maar dat details toch leiden tot problemen. De kwaliteit van rubber afdichtingen is bijvoorbeeld een punt dat vaak over het hoofd gezien wordt. Het is voor machinebouwers niet duidelijk welk type rubber ze daarvoor moeten inzetten, want er is geen specifieke en duidelijke wetgeving. Er zijn bovendien enorm veel verschillende compounds of samenstellingen, die zich anders gedragen. Bovendien is het ook belangrijk om op de hoogte te zijn van productcombinaties die ingezet worden bij de eindklant, plus de eventuele chemische reacties die mengelingen kunnen veroorzaken. Daar komt nog bovenop dat ze in vele gevallen ook zullen moeten weerstaan aan frequente reiniging via SIP of CIP.
Welke normen van toepassing?
We haalden het al kort aan: wie werkt voor de voedingsnijverheid zal het ongetwijfeld beamen: in slechts weinig sectoren zijn er zoveel normerende instanties en wetgevingen van kracht als in de voeding. Naast de bekende HACCP regels, gaat het bijvoorbeeld om BRC, FDA EC1935/2004, ISO 14159:2002, EU 10/2011, GMP2023/2006, EHEDG (doc 44), IFS, ISO 22000 en FSSC 22000. Deze staan zeker niet op dezelfde hiërarchische schaal, noch hebben ze compleet hetzelfde actiegebied. Bovendien hebben ze niet allemaal wetgevende kracht. De BRC en IFS zijn bijvoorbeeld 2 sets van regels die opgelegd worden door retailers. Deze sets moeten dus volgens de letter van wet niet opgevolgd worden, maar in de praktijk gebeurt het wel om een verkoopskanaal open te houden. Daar komt nog bovenop dat een voedingsbedrijf meestal een kruisbestuiving is van procestechnologie, chemie en machinebouw. Binnen de voedingsbedrijven hangt de keuze rond normen met andere woorden ook vaak af van de afdeling die ermee geconfronteerd wordt. De veelheid aan regels maakt het uiteraard niet makkelijk werken, want in elke norm of wet komen dezelfde onderwerpen min of meer terug. Als we perslucht als voorbeeld nemen dan lezen we in de BRC regelgeving het volgende: Lucht, andere gassen en stoom die tijdens hun gebruik rechtstreeks in contact komen met producten, moeten bewaakt worden om te verzekeren dat dit geen risico van contaminatie inhoudt. Gebruikte perslucht die rechtstreeks in aanraking komt met het product moet worden gefilterd.
Bedrijven gaan vervolgens met deze summiere info aan de slag en doen daarvoor beroep op regels van organisaties met een andere achtergrond, zoals BCAS (British Compressed Air Society) of de ISO 8573-1:2010. Die laatste deelt het gebruik van perslucht in 3 categorieën, afhankelijk van het contact met het product:
• Direct contact: De perslucht komt direct en/of langdurig in aanraking met de voedingsmiddelen als onderdeel van de receptuur of tijdens productieproces (bijv. bij beluchten, spuiten of vernevelen van ingrediënten) of wordt tijdens opslag, transport en/of verpakken gebruikt om voedingsmiddel te verplaatsen of transporteren (bijv. laden of lossen tanks, pneumatisch transport). • Non-contact: De perslucht komt nooit in contact met voeding waaronder ingrediënten, eindproducten, verpakkingsmaterialen, opslagvaten, transport of de productie- en verpakkingsmachines. • Indirect contact: Perslucht wordt uitgestoten in de omgevingslucht waar open voedingsmiddel of open primaire verpakking aanwezig is of wordt bijv. gebruikt voor het drogen of schoonspuiten van productcontactoppervlakken. Volgens de HACCP regels zijn dit de ruimtes waar potentieel besmettingsgevaar bestaat aangeduid met Hygiëne zoneclassificatie M (Medium) of H (High) of een overgangs- of bufferzone. De omgevings- of perslucht komt of kan in contact komen met ingrediënten, eindproducten,
verpakkingsmaterialen, opslagtanks, verpakking of de productie- / verpakkingsmachines. Denk bijvoorbeeld ook aan perslucht die via pneumatische cylinders atmosferisch wordt afgeblazen of een verpakking die wordt geproduceerd met lucht (bijv. PET flessen).
Technologie
Naast perslucht en elektrische aandrijving is ook pneumatica alomtegenwoordig. Pneumatica was altijd al een populaire technologie voor applicaties op het vlak van voedingsmiddelen en drank. De reden daarvoor is niet ver te zoeken: pneumaticatechnologie is schoon, betrouwbaar, veilig en makkelijk te onderhouden. De opkomst van het Industrial Internet of Things (IIoT), maakt van pneumatica nog meer een prima keuze voor applicaties op het vlak van voedingsmiddelen en drank. Met IIoT connectiviteit kan proces apparatuur veiliger worden bediend en kan preventief onderhoud uitgebreid worden. Daarnaast kan energiegebruik nauwkeuriger worden bewaakt en bestuurd. Daar leest u verderop in dit nummer meer over.
IIoT connectiviteit
We vertellen u weinig nieuws als we zeggen dat apparatuur kan worden uitgerust met sensoren die essentiële bedrijfsparameters meten, zoals temperatuur, druk, debietwaarden, cyclustijden en ventielreactiesnelheid. Machinebouwers kunnen via deze data de prestaties van de machines nauwkeurig in het oog houden. OEM kunnen op hun beurt gebruik maken van deze mogelijkheden, bijvoorbeeld voor het in de gaten houden van parameters en de klanten desgevallend een waarschuwing te sturen over de staat van cilinders, ventielen en andere apparaten.
De toevloed aan nieuwe data is vaak een hinderpaal voor gebruikers die aan het begin staan van hun IIoT traject. Dat geldt ook voor voorzieningen waarbij het centrale besturingssysteem (bijvoorbeeld een PLC) nu zwaarder wordt belast. Een aantal fabrikanten heeft edge gateways ontworpen die data uit machinecomponenten registreren en analyseren op het lokale fabrieksniveau om prestaties te vergelijken met ontwerpparameters. Dit vindt plaats zonder dat de informatie naar de machinebesturing of de cloud wordt verzonden. Als de sensorgegevens aangeven dat de machine zich buiten de grenzen bevindt, verzend het randapparaat waarschuwingen naar de juiste personen. Alleen eventuele uitschieters in de data worden doorgestuurd naar de centrale besturing of de cloud.
Deze randapparaten kunnen overal in de installatie ingezet worden en kunnen tot 250 inputs afhandelen. Dit is waarschijnlijk niet genoeg voor een complete installatie. Maar dit kan echter zeker toereikend zijn voor het bewaken van essentiële functies die nodig zijn voor een proces lijn of -gebied binnen de installatie. Het verbinden van sensoren met pneumaticacomponenten via een gateway opent de deur voor belangrijke verbeteringen op het vlak van onderhoud, veiligheid en energieverbruik.
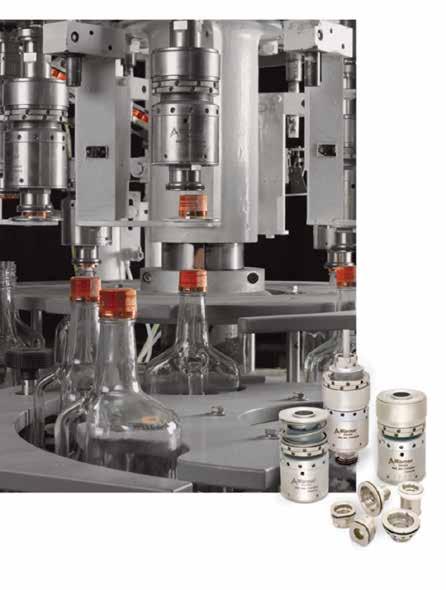
MAGNETISCHE KOP VOOR HET PLAATSEN VAN DOPPEN
Warner Electric voorzag een grote frisdrankbottelarij van soepele koppen voor de geautomatiseerde plaatsing van doppen op de flessen. Dat gebeurde op twee bottellijnen: één met 16 headsets die tussen 300 en 700 flessen per minuut verwerkt, en een tweede met 20 koppen die tot 1.000 flessen per minuut van een dop voorziet. Omdat er een roestprobleem was met de oude headset, moesten die om de 8-10 weken vervangen worden. De keuze viel op de componenten van Warner. Na bijna twee jaar in bedrijf, meldde de bottelarij geen enkele uitvaltijd meer. Het aanhaalmoment bleef ook consistent gedurende de hele periode. De eerder gebruikte headsets begonnen na slechts 10 weken koppel te verliezen en moesten om de drie maanden vervangen worden. Het smeerinterval kon teruggebracht worden van wekelijks naar maandelijks, en het onderhoudsinterval werd gereduceerd tot 1/4 van het vorige niveau. Ook voor de lijnoperator is het eenvoudiger werken. Hij schat de benodigde tijd om een headset te vervangen op 1/3 van die van vroegere componenten, dankzij het vereenvoudigde ontwerp en het gemak waarmee ze gedemonteerd en gemonteerd kunnen worden. De snelle productondersteuning door Warner Electric was ook belangrijk voor deze klant. Voor deze klant ontwierpen de technici enkele modificaties om beter te voldoen aan de vereisten van de lijn, wat zeer op prijs werd gesteld.
Componenten in de voedingsindustrie moeten tegen meer dan één stootje kunnen.
Uitgebreid onderhoud
Slijtage is onvermijdelijk, in welke industriële omgeving dan ook. Via IIoT kan een geheel nieuw niveau van preventief onderhoud geïmplementeerd worden. Het systeem kan door de machineprestaties te vergelijken met vastgestelde instelpunten, de juiste beheerder waarschuwen als het systeem niet voldoet aan de vastgestelde normen. Onderhoudstechnici kunnen bijvoorbeeld vaststellen dat een schokdemper op het einde van een cilinder achteruitgaat door het detecteren van een toename van de cyclussnelheid. Dit kan zelfs als deze toename slechts enkele milliseconden betreft. Machinebouwers kunnen genieten van de diagnostische functies van met IIoT uitgebreide pneumatica voor het meten van essentiële parameters, zoals cilindersnelheid. In beide situaties kunnen technici doordat ze weten welke apparatuur onderhoud nodig heeft, ongeplande stilstand voorkomen en componenten vervangen op basis van kortere en beter geplande machinestops.
Een veiligere werkplek
IIoT breidt verder de pneumatica technologie uit via nieuwe tracking- en meetopties. Deze nieuwe functies bieden operatoren nog meer inzicht in de prestaties van een machine en de bijbehorende componenten en subsystemen. Een goed voorbeeld is een snijmachine met een veiligheidslichtgordijn en de bijhorende aansturing van een veiligheidsventiel. Als de ventielreactieduur wijzigt van 30 milliseconden richting de 50 of zelfs 70 milliseconden, kan een operator veel verder doordringen in de gevaarlijke zone van een machine voordat de veiligheidsreactie wordt geactiveerd. Normaal gesproken zou een dergelijke situatie niet opgemerkt of aangepakt worden voordat het apparaat het vervangingsinterval voor het desbetreffende product had bereikt. Met IIoT mogelijkheden kan deze achteruitgang in de ventielreactietijd (en de corresponderende waarschuwingsreactietijd) tijdig geregistreerd, geanalyseerd en gerapporteerd worden, zodat er corrigerende maatregelen kunnen getroffen worden voordat de functionaliteit terugloopt en de machineoperator effectief risico loopt.
Pneumaticatechnologie biedt naast IIoT connectiviteit een breed scala aan andere voordelen voor producenten op het vlak van voedingsmiddelen en drank zoals hygiëne. Pneumatica is ideaal voor werkzaamheden waarbij regelmatig reiniging is vereist. Er zijn ventielen voor deze omstandigheden die bestand zijn tegen agressieve oplosmiddelen en chemicaliën. Ook betrouwbaarheid is zeker een pro. Pneumatica componenten zijn relatief gesproken weinig complex en dat draagt bij aan de betrouwbaarheid. De ventielen zijn specifiek gemaakt met het oog op hoge schakelsnelheden en zijn dus geschikt voor productie aan hoge snelheid of zeer snelle bewegingen.

www.altramotion.com www.emerson.com www.se.com
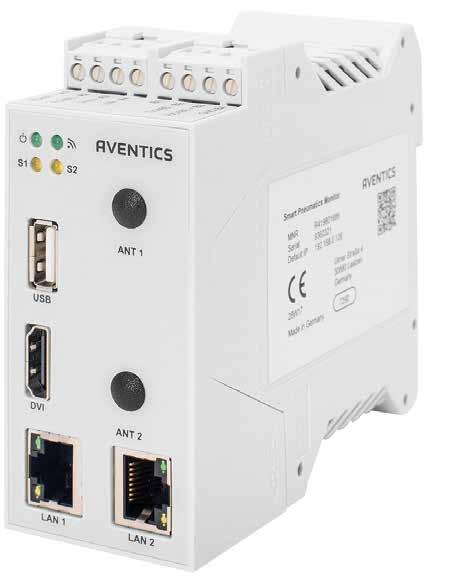
Deze Smart Pneumatics Monitor module van Aventics biedt de gebruiker betrouwbare informatie over de slijtagestaat van pneumatische cilinders, ventielen en andere apparaten, en over de energiezuinigheid van pneumaticasystemen.
Dit ASCO™ 290 multifunctionele pneumatisch bediende ventiel van Emerson is een direct werkend ventiel waarbij de interne natte componenten voldoen aan de normen Food Safe (EC-1935/2004) en FDA (CFR 21).
RVS TANDWIELKAST VAN APEX DYNAMICS
In de drankenindustrie is er veel vraag naar elektromechanische aandrijvingen, met op de eerste plaats aandacht voor toenemende capaciteiten, prijsdruk en innovatie. Daardoor wordt de traditionele draaistroommotor meer en meer vervangen door een servomotor met een spelingsarme tandwielkast. Maar waar worden die producten dan precies toegepast in deze keten?
Hier een aantal toepassingen, die wellicht niet zo voor de hand liggen:
• Bij de productie van glazen flessen en potten is het van belang de wanddikte van het glas zo dun mogelijk te houden. Met een lineaire unit wordt de druppel glas precies in het midden van de mal gedeponeerd, zodat de wanddikte overal even dik is en er minder glas nodig is bij de productie.
• Voor pasteuze vloeistoffen worden de spuitmonden servo-mechanisch aangedreven. • Flesjes worden afgevuld in een carrousel of afvuller. De aanvoer gebeurt middels wormwielen welke de flesjes van een stuwband precies in de nokken van de carrousel schuiven. De besturing van de wormwielen en het draaiplateau zijn zo op elkaar gekoppeld, dat de flesjes naadloos in de pockets vallen. Dit alles is mogelijk bij capaciteiten tot 36.000 flesjes per uur, en is niet meer mogelijk zonder servomotoren en spelingsarme tandwielkasten. • Als er op de flesjes een draai-dop komt, worden deze middels een electromechanische aandrijving erop gedraaid met het juiste koppel. • Wordt het flesje niet bedrukt, maar wordt er een “sleeve” omheen gekrompen dan zitten in de aandrijving servoaandrijvingen om de timing van het schieten van de “sleeve” goed te krijgen.
In de drankenindustrie zijn er speciale eisen aan de aandrijvingen: RVS of Inox producten verdienen de sterke voorkeur, en daarvoor heeft Apex Dynamics een hele reeks aangepaste tandwielkasten (series AE, AES, AD en AT). De tandwielkasten zijn schuinvertand voor een laag geluidsniveau, hebben hoge koppels en zijn zeer schokbestendig.
www.apexdyna.be
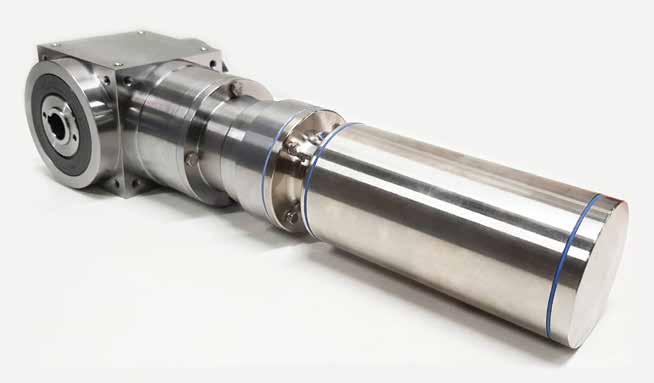
TRX zorgt voor een revolutie in 3D-beweging
Telescopisch triflex® TRX - ruimtebesparende installatie met een uittreklengte tot 40%
l Minimalisatie van de loop formatie l Ruimtebesparend ontwerp l Compatibel met het triflex® R-portfolio van het TRE-assortiment l Gemakkelijk achteraf te monteren l Minimalisatie van ingekochte onderdelen l Kortere kabellengtes l Alle componenten zijn afzonderlijk vervangbaar l Minimalisatie van installatietijden dankzij het "easy" ontwerp motion plastics® /trx

Tel. 03-330 13 60 info@igus.be