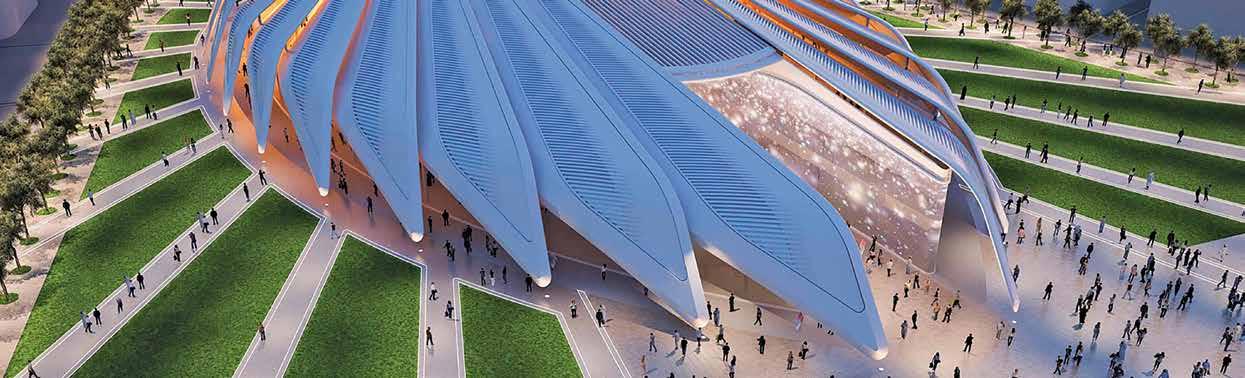
8 minute read
EXPO 2020 DUBAI
Une Technologie Hydraulique De Pointe Pour Un Toit Mobile
Le pavillon du pays hôte, les Emirats Arabes Unis (EAU), fut l’une des principales attractions de l’Expo 2020 à Dubaï. L’aspect technique du toit du bâtiment a attiré tous les regards. Les 28 ailes mobiles en fibre de carbone et de verre, d’un poids de 5 à 18 tonnes et des longueurs totales de 30 à 65 m, sont actionnées via un système hydraulique.
Advertisement
Quelques chiffres-clés montrent l’ampleur du projet : le système se compose d’une unité d’entraînement hydraulique d’environ 1 MW. Un réseau de 2 km de conduites a été posé, la pression nominale est de 210 bars, et 46 vérins hydrauliques d’une masse de 1,5 tonne chacun assurent un mouvement automatique via 9 automates distincts. Ils sont assistés par un logiciel spécifique, 2.000 capteurs et plus de 20 km de faisceaux de câble.
La commande des ailes est un défi majeur. Suite aux dimensions et au poids correspondant, certaines d’entre elles sont actionnées par plusieurs (deux ou trois) vérins hydrauliques synchronisés. Ce n’est qu’à cette condition que les contraintes exercées à la structure mécanique sont acceptables et que les dommages sont évités.
À ce fonctionnement synchrone s’ajoute une longue liste d’exigences à respecter, qui vont au-delà des exigences habituelles des applications industrielles. Dans le contexte de l’Expo à Dubaï, il était essentiel de réaliser quelque chose qui puisse surprendre, un aperçu de la perfection en quelque sorte. Le maître d’ouvrage recherchait un produit fonctionnel mais aussi quelque chose d'exceptionnel. Cette idée a été le fil conducteur lors du processus de développement où la précision absolue, l’esthétique et le concept de durabilité de l’Expo 2020 devaient former une combinaison fluide.
Pour ce projet, toutes les ailes doivent s’ouvrir et se fermer en parfaite synchronisation, de manière silencieuse et avec le plus faible impact visuel possible. En outre, le processus doit se dérouler avec la plus grande fiabilité, sécurité et efficacité énergétique possible.
La solution : l’Hydraulic Power Unit de 1MW
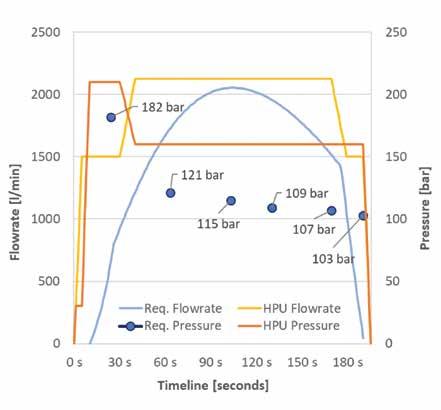
Le coeur du système est une installation hydraulique, une HPU de 1MW, installée au sous-sol du bâtiment. 46 vannes pilotes et des capteurs de pression règlent indépendamment le mouvement de chaque vérin hydraulique (46 également), lesquels sont équipés de capteurs de course et de proximité. L’idée de base du concept est de réguler le débit et la pression du système indépendamment et de les adapter à chaque condition de fonctionnement. Pour ce faire, des pompes fixes sont utilisées et commandées via des électromoteurs et des variateurs de fréquence. Cela permet un ajustement presque instantané de la pression du système sur base de la charge spécifique.
Représentation graphique (points bleus) de la pression résultante utile pour permettre le mouvement du système.
Pour minimiser la consommation d’énergie, le débit et la pression du système sont régulés selon le cycle de travail. Par le mouvement avec ses accélérations et décélerations associées, et la l'absorption de puissance liée à la position angulaire de l’aile, la demande en pression est maximale au début du mouvement d’ouverture, où la vitesse d’écoulement est minime. Après l’accélération, celle-ci diminue tandis que la demande de débit augmente. Il y a donc une interaction constante entre la pression et le débit, ce qui permet d’optimiser la consommation d’énergie. Le débit généré par la HPU et la pression appliquée à la conduite de pression sont respectivement indiqués par les courbes orange et jaune et correspondent aux valeurs demandées.
L’exigence du fonctionnement le plus silencieux possible a conduit au choix d’une pompe à engrenages à denture interne. Des éléments d'amortissement sont placés dans les conduites et la séquence de démarrage a été choisie pour minimiser les vibrations. Pour les pompes à haute pression, le choix s’est porté sur des modèles aux émissions sonores les plus faibles. De plus, deux pompes sont prévues à chaque unité de pompage. Elles sont installées de manière à ce que la pulsation soit en contre-phase, ce qui limite l’ondulation de la pression sur la conduite de pression et donc les émissions sonores.
L’importance
du réseau de conduites
Le déploiement du système de conduites a joué un rôle déterminant dans la réussite du projet. Le réseau de conduites du système est conçu pour garantir une vitesse d’écoulement élevée du fluide hydraulique, même à une grande distance de la HPU. C’est important en raison de la déformation potentielle de la structure du bâtiment, du climat désertique et ses températures extrêmes, ses tempêtes de sable et ses fortes pluies.

Techniquement, il fallait tenir compte des différentes hauteurs des vérins et des entraînements. L’acier inoxydable 316L non peint a été choisi comme matériau pour les conduites. Il est considéré comme le matériau le plus fiable pour garantir la fonctionnalité pendant la durée de vie du pavillon, limitant les besoins en maintenance.
La HPU est conçue pour fournir une pression de service constante maximale de 210 bars et un débit de plus de 2000 l/min.
Entraînements hydrauliques et mouvement
Le mouvement de chaque vérin hydraulique est réglé indépendamment par un manodétenteur proportionnel spécial. Des vannes supplémentaires sont prévues pour gérer la position de verrouillage, la fermeture d’urgence et le sens de mouvement. Elles sont installées sur un bloc à l’arrière de chaque vérin, ce qui réduit la distance et le temps de réponse de la commande. Les soupapes de surpression et vannes de fermeture sont montées sur le vérin pour des raisons de sécurité.
Présentation schématique de l’emplacement de la HPU et des conduites du système dans le pavillon.
La solution de contrôle de mouvement est conçue en fonction de cette architecture hydraulique spécifique et des composants. La régulation de la vitesse de chaque vérin hydraulique s’effectue via une vanne proportionnelle à commande pilotée et compensée, avec le signal d’un capteur de position comme élément de contrôle.
Deux systèmes ont été développés pour la commande des ailes : l’un est basé sur un axe et l’autre sur plusieurs axes. Chaque axe possède une carte de contrôle de mouvement spéciale. Dans le cas d’une aile multiaxe, une carte de contrôle de mouvement supplémentaire sert de gardien au fonctionnement synchrone. Les cartes communiquent en interne via un bus CAN. La connexion au sous-système d’automatisation et de commande s’effectue via une interface PROFINET.
Le profil standard d’une course complète consiste en un mouvement d’ouverture/fermeture à effectuer en 180 s avec une marge de +/-2s. Une fermeture rapide à une vitesse maximale est possible en 120 s en cas de conditions critiques. Comme il ne s’agit pas de conditions de travail nominales, un générateur de profil permet un mouvement de récupération à partir d’une position intermédiaire.
Une synchronisation est nécessaire pour les ailes à deux ou trois axes. Dans ce cas, la commande est reprise par un autre algorithme (SSC au lieu de SAC). C’est nécessaire car la cinématique des axes appartenant à la même aile est différente, un profil normalisé est donc utile. On l’obtient via une régulation PI en boucle fermée (fréquence = 1 kHz) basée sur une approche maître-esclave. L’objectif est de minimiser les erreurs de synchronisation sous la limite maximale acceptable de +/-10 mm autour de la position linéaire normalisée.
Pour chaque actionneur, la commande de l’aile doit gérer les sous-systèmes suivants : -> régulation de l’écoulement directionnel et proportionnel des vannes pour la commande de vérins, -> Transducteurs de pression, -> Capteurs de course, -> Capteurs de température. En plus des exigences mentionnées plus haut, chaque aile dispose de vannes supplémentaires pour régler le mécanisme de verrouillage à des fins de maintenance.
De plus, des modules entrée/sortie sont utilisés sur chaque position de vérin. Ils résistent aux températures élevées du toit et possèdent une classe de protection IP67. Chaque raccordement est connecté au réseau de communication PROFINET et fonctionne selon une alimentation 24V.
Calculer les pertes de charge
Une simulation a permis d’analyser deux paramètres importants. Le premier concerne la perte de charge du système sous diverses conditions de travail, qui dépendent de la demande des vérins à chaque moment du mouvement. La simulation répond à la question de savoir si les vérins peuvent effectivement accomplir leur tâche sous n’importe quelle charge.
Un second paramètre important consiste à déterminer la réserve de pression disponible lors d’un fonctionnement dans des conditions les plus défavorables.
Outre la HPU, le premier modèle comprend les soupapes de surpression (PRV = Pressure Relief Valve) pour le réglage de la pression et du réseau de conduites.
Le modèle HPU est basé sur des signaux. Les rendements hydromécaniques et volumétriques sont cartographiés. Tous deux dépendent de la pression système appliquée et du régime moteur. Cela permet de cartographier le couple effectif de l’axe moteur et la perte de débit volumique le long de sa courbe caractéristique, du démarrage au point de fonctionnement. Le paramétrage et la validation ont lieu à l’aide de fiches techniques et de mesures de caractérisation de la pompe. Le modèle ne tient pas compte du comportement dynamique et des pulsations de la pompe, et ignore le comportement au démarrage des électromoteurs.
Le second pilier – la soupape PRV – comprend plusieurs vannes et filtres uniquement décrits par leurs caractéristiques d’écoulement. Une cartographie fonctionnelle n’est pas nécessaire car elles ne fonctionnent que lorsque le système n’est pas actif. Le modèle PRV (Soupape de sécurité proportionnelle) est basé sur la description fonctionnelle de la vanne sur base des profils pression-temps, du comportement dynamique et des données de débit volumique.
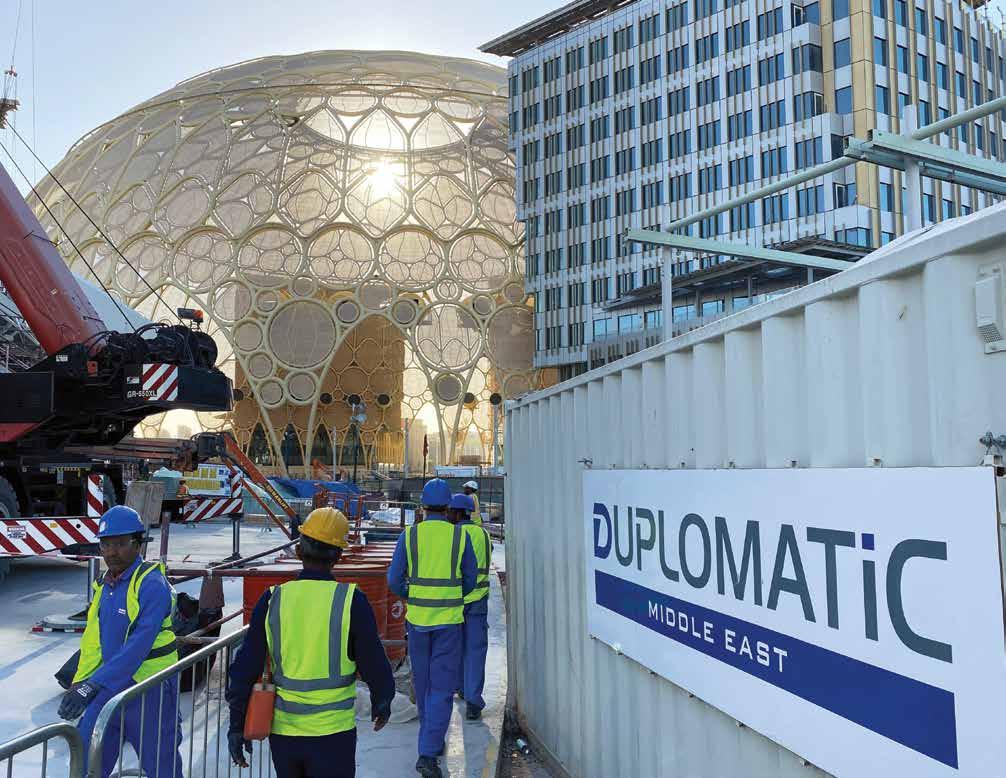
Le troisième pilier – le concept de conduites – englobe les données de conception comme les longueurs, les diamètres et les différences de hauteur des éléments de conduite individuels. Chaque élément prend en compte : la puissance hydraulique et l’induction/les pertes hydrostatiques/les pertes hydrodynamiques/la friction de conduite selon Haaland/la résistance à l’écoulement.
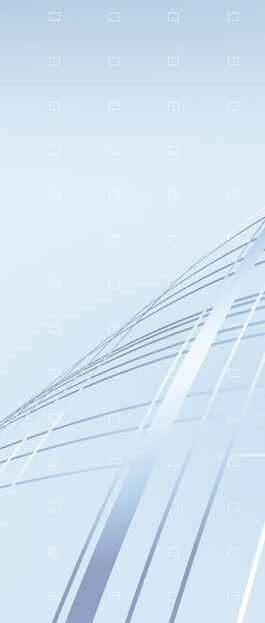
Evaluation de la réserve de pression
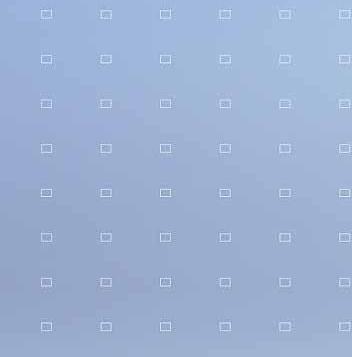
L’évaluation de la réserve de pression du système nécessite la modélisation de la commande du vérin hydraulique, dont la vanne de régulation de débit (FCV = Flow Control Valve) et les composants supplémentaires. Le comportement du système est principalement déterminé par les caractéristiques de la FCV. Selon la taille du vérin, deux types de vannes aux débits volumiques nominaux de 60 l/min ou 110 l/min sont déployés. Les autres composants sont modélisés sur base de leurs propriétés d’écoulement. La FCV comprend une bobine de vanne proportionnelle, un compensateur de pression et une vanne pilote. Le débit volumique est maintenu constant lors de conditions de charge changeantes, à un débit de consigne constant. Ce résultat est obtenu grâce au compensateur de pression qui veille à une perte de charge constante dans le limiteur de débit.
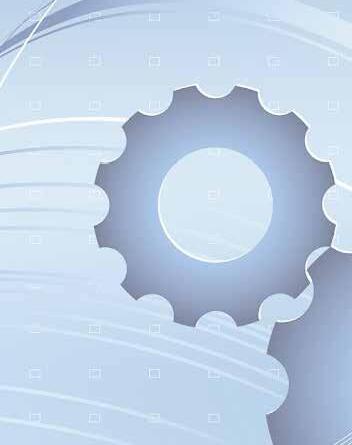
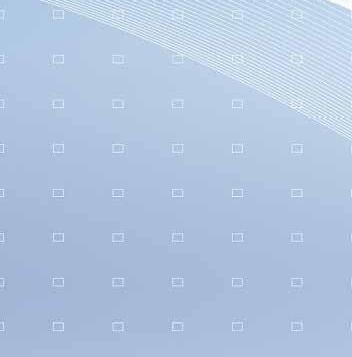
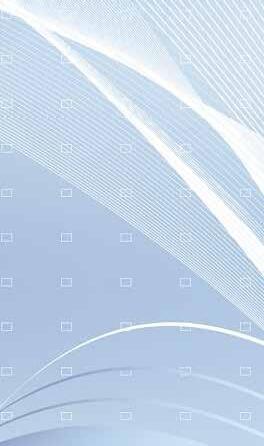
Une vanne FCV présente généralement un comportement non idéal, avec des caractéristiques d’écoulement dépendant du débit et de la pression, ainsi qu’une hystérésis. La plage de régulation de la vanne commence à une chute de pression de 8 bars. Le modèle comprend les éléments suivants : -> Une représentation des points caractéristiques des vannes ; -> Une hystérésis dépendant du débit; -> Le comportement de la vanne en dehors de la plage de régulation.
Une cartographie basée sur le signal a été utilisée pour la détermination de la carte FCV caractéristique. À cette fin, des mesures de la vanne ont été enregistrées dans quatre configurations différentes, elles ont été utilisées et analysées pour dériver les caractéristiques de base et les caractéristiques des composants impliqués.
Cette figure montre la configuration de mesure de la vanne. Pendant le test, une pompe fournit un débit volumique constant. Deux PRV différents génèrent une différence de pression pratiquement constante à travers la vanne de régulation. Les scénarios de test suivants sont suivis: 1. Accumulation croissante du débit sans contre-pression, 2. Accumulation croissante du débit avec une contre-pression constante de 180 bars, 3. Accumulation croissante de la contre-pression avec un débit d’ouverture constant à 1900 mA, 4. Accumulation croissante de la contre-pression avec un débit d’ouverture constant à 1260 mA.
Sur base de l’analyse des données de mesure, les composants de modèle suivants ont été générés avec un niveau de précision acceptable :
• Carte de vanne caractéristique
• Hystérésis en fonction du changement du débit de consigne
• Etranglement idéal en dehors de la plage de régulation
L’hystérésis dépendant de la pression est négligée