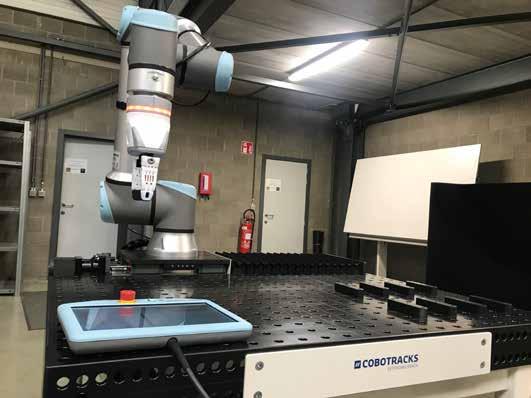
22 minute read
Extension de la zone de travail du cobot avec un axe linéaire
Le cobot connaît sa position exacte grâce au servomoteur et à l’encodeur. Lors d’un montage vertical, une vis à billes est utilisée pour des raisons de sécurité.

Vous avez pu lire dans ce dossier que les cobots sont en train de conquérir des parts de marché. La technologie dédiée aux cobots évolue, et les fabricants d’équipements périphériques rendent l’implémentation possible. L’entreprise Cobotracks de Hasselt fournit par exemple des rails linéaires, un ‘septième axe’ au cobot.
Le directeur Pieter Vansichen nous en dit plus sur les activités de Cobotracks : « Notre société-sœur Vansichen Lineairtechniek a une longue expérience dans la fabrication de rails pour les robots industriels classiques. Via ces rails, nous proposons un septième axe au cobot qui étend considérablement sa portée. A un moment donné, les cobots ont été exposés dans des salons professionnels et les médias. Nous avons donc travaillé une solution pour ce segment, et comme le marché est spécifique, nous l’avons hébergée dans une société distincte. »
« A l’époque, le marché se limitait à un seul grand acteur - Universal Robots (UR) – qui occupait donc une position prédominante. Dans un premier temps, nous avons voulu développer une solution pour le cobot de cette entreprise. Mais pour développer un rail pour UR, votre solution doit être certifiée UR+. Cette certification UR+ peut être considérée comme un app store, mais alors spécifiquement pour les cobots de l’entreprise. Tout fabricant peut en principe développer une solution pour Universal Robots mais il doit se conformer à des exigences de qualité sévères. Nous avons dû construire un prototype qui a été testé dans les moindres détails par les ingénieurs d’UR. Il s’agissait d’un développement pour leurs cobots qui devait aussi être compatible avec d’autres composants et accessoires UR+ développés par d’autres entreprises pour Universal Robots. A côté de cela, on attend de sociétés comme les nôtres des exigences de qualité envers l’approche client, comme la mise à disposition de manuels et de catalogues de qualité. En échange, notre solution de septième axe est répertoriée sur la plateforme UR+, ce qui donne plus de visibilité à nos produits.»
Le plug & play facilite l’utilisation
« Un autre acteur propose un septième axe à Universal Robot mais notre solution va plus loin. Le logiciel dispose par exemple de plus de fonctionnalités pour faciliter l’intégration du robot. Le système fonctionne selon le principe plug & play pour abaisser le seuil, et le cobot est contrôlé de manière plus ciblée, grâce à la possibilité de réaliser des arrêts et des variations de vitesse. L’argument de vente d’un cobot est sa convivialité. Nous voulions véhiculer cette philosophie dans notre solution. »
Large palette d’applications
« Les applications potentielles sont très diverses. Nous pensons principalement à des applications de soudage et de palettisation en logistique, mais nous avons aussi des projets de collage de grandes pièces. Un cobot sans septième axe a une portée limitée. Il y a aussi des demandes pour des tâches de montage comme le serrage de boulons. Nous avons entretemps vendu des modèles dans pratiquement tous les pays voisins : l’Allemagne, le Danemark, l’Espagne, le Royaume-Uni, la Suisse, l’Italie et le Luxembourg. Il y a clairement un grand marché et notre solution est demandée ; et pourtant, nous ne l’avons jamais exposée à des salons suite à la pandémie du COVID-19. »
Structure
Pieter Vansichen: « Via notre société-soeur, nous bénéficions
d’une grande expérience dans la conception d’un septième axe pour les robots industriels. La grande différence dans l’approche est qu’il ne s’agit pas d’une solution purement mécatronique. Il a fallu développer le logiciel et la communication inhérents au cobot. Ce processus nécessite une grande compréhension du fonctionnement d’un cobot. »
« Nous avons opté pour une construction en acier, mais nous pouvons proposer une solution en aluminium sur demande. La version en acier couvre des distances plus longues que l’aluminium. En principe, on peut aller jusqu’à 50 mètres et la rigidité est meilleure. Le mouvement linéaire est standard avec une transmission par courroie crantée, et pour les longueurs plus importantes, nous passons à une crémaillère. Une transmission par courroie crantée est moins précise lors de longueurs importantes, un inconvénient que nous n’avons pas avec les systèmes à crémaillère. Si le mouvement a lieu dans le sens vertical, nous utilisons une vis à billes parce qu’elle est plus sûre. »
L’entraînement du mouvement linéaire a lieu en standard avec un servomoteur et le variateur correspondant de SEW. En théorie, on pourrait aussi travailler avec des moteurs pas à pas, mais nous l’évitons parce que le fonctionnement d’un servomoteur est plus précis et plus compact. Le module de commande d’un moteur pas à pas compte le nombre de pas pour définir sa position, il n’y a pas de rétroaction de la position exacte du moteur. A des vitesses élevées, des pas peuvent se perdre et l’installation perd l’acquis sur la position correcte. A des vitesses très basses, un comportement oscillant peut se produire. Notre servomoteur fonctionne avec un résolveur, ce qui permet d’obtenir une plus grande précision, tant en matière de précision du positionnement que de répétabilité.
De plus, le servomoteur possède une plage de vitesses plus large, ce qui nous permet d’implémenter ce système d’entraînement dans de multiples solutions. Nous limitons ainsi le nombre de pièces de rechange utiles et nous pouvons garantir un haut niveau de service.
Aussi pour d’autres cobots
« Le fait que nous ayons d’abord élaboré une solution pour Universal Robots était logique puisque c’est un leader de marché dans le monde des cobots. Aujourd’hui, nous développons des solutions avec un septième axe pour d’autres fabricants. Nous travaillons actuellement sur une solution pour Techman – un autre grand acteur de marché – et nous avons des contacts avec Doosan et FANUC. C’est un marché passionnant qui ne cesse de croître et d’évoluer. L’expérience acquise avec Universal Robots nous permet de proposer un niveau élevé dans l’élaboration d’une solution qui correspond au fabricant. Cela exige aussi de l’ouverture de la part des fabricants de cobot. Nous avons besoin des dimensions mécaniques et nous devons aussi pouvoir interagir avec le fonctionnement du cobot : quels sont les signaux qui sont communiqués, via quels ports, qu’en est-il des commandes ? »
Sécurité?
« En principe, Universal Robots ne nous impose pas de vitesses ou d’accélérations maximales. Nous pouvons construire les installations sans restrictions. Le cobot fonctionne normalement, comme il le ferait sans rail. Cependant, il revient au client final d’évaluer la sécurité de son installation, comme il doit le faire pour toutes ses machines, et cela dépend de son application. Les clients nous demandent parfois si un cobot équipé d’un septième axe peut encore effectuer un travail collaboratif : ici aussi, la réponse dépend de l’application : quels sont les risques qui ont été ajoutés, qu’en est-il de la vitesse, quelles sont les mesures de sécurité qui ont été prises, … Parfois, il faut prévoir des scrutateurs laser de sécurité, dans d’autres cas, un grillage s’impose. »
« Aucune maintenance n’est nécessaire, à l’exception d’une lubrification si on travaille avec des versions à crémaillère ou une vis à billes. Nos solutions exigent peu d’entretien », conclut Pieter Vansichen.
www.cobotracks.com

Un axe linéaire étend sérieusement la portée du cobot. Une exécution verticale est aussi possible.
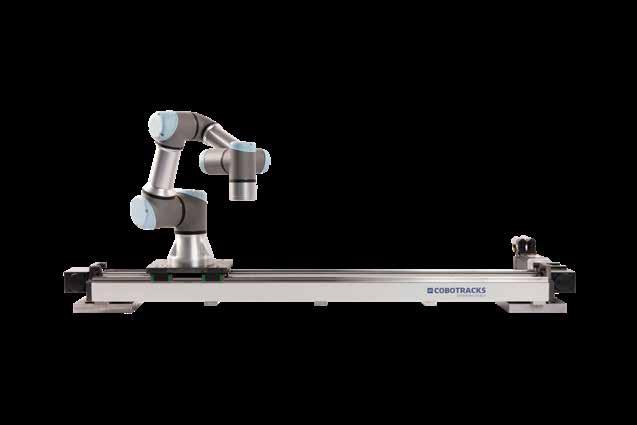
ESCO DÉMÉNAGE ET LANCE UN COBOT
De bonnes perspectives attendent Esco en cette fin d’année 2020. L’entreprise emménagera bientôt dans un nouveau bâtiment à Ghislenghien, et Mitsubishi vient de lancer son premier cobot. Autant de bonnes raisons de rencontrer Koen D’Haese, sales manager.
« Mitsubishi est connue depuis longtemps pour sa gamme de robots industriels pour moyennes et petites charges. Au Japon, l’entreprise fabrique des robots à quatre et six axes depuis 1980. Aujourd’hui, plus 120 000 robots fonctionnent dans le monde entier. », explique Koen D’Haese d’Esco. « Nous suivons les évolutions du secteur des cobots depuis un certain temps car ce secteur se développe rapidement. Avec les robots classiques, nous sommes surtout actifs dans le segment des charges utiles de 1 à 12 kg. Les cobots travaillent principalement dans ce segment. Voilà pourquoi cette extension de gamme est importante pour Mitsubishi. »
La sécurité via Safe Torque Range (STR)
« Mitsubishi attache une grande importance à la sécurité et à la précision, et cela se retrouve dans le développement du nouveau cobot baptisé Melfa Assista. Le fonctionnement du cobot dans des zones avec une présence humaine est assuré par la fonction de sécurité safe torque range (STR) ou plage sûre de couple. Le cobot sait quel couple mesurer dans une zone spécifique. Au moindre contact ou blocage, le couple n’est plus dans les limites définies et le cobot s’arrête automatiquement. Cette détection de force est rendue possible par une très grande précision de mesure du couple développé par le servo-moteur, domaine où Mitsubishi possède également une très grande expertise.
Une deuxième fonction de sécurité est une indication visuelle de l’état du cobot via une led : le vert signifie ‘en fonctionnement’, l’orange ‘en mode apprentissage’ et le rouge ‘alarme’. Les personnes à proximité du cobot sont donc clairement informées de l’état de celui-ci. »
Une troisième fonction de sécurité est la possibilité de prévoir plusieurs modes de vitesse. En évaluant le risque, le cobot règle sa vitesse selon diverses zones de vitesse préétablies et la présence ou non d’être humain proche.. Il peut alors travailler plus rapidement en l’absence d’opérateurs, ce qui contribue grandement à la productivité. Trois zones sont programmables : Highspeed Mode (1000 mm/s), Standard Mode (250 mm/s) et Low Speed Mode (50 mm/s).
Programmation
Pour les tâches simples, nous avons conçu un outil de programmation graphique intuitif et tactile « RT Visual Ox ». Sa facilité d’utilisation permet de construire vos programmes avec des blocs simples, sans connaissances préalable en programmation. L’utilisation d’un assistant graphique étape par étape vous permet de définir tous les paramètres nécessaires. Pour des tâches plus complexes, vous pouvez programmer Assista à l’aide de « RT ToolBox3 » exactement de la même manière que nos autres robots.
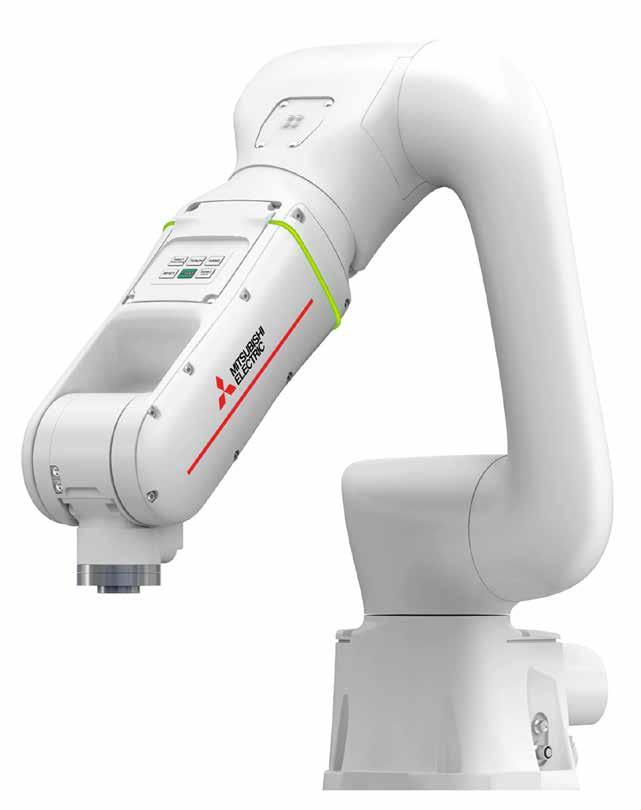
Nouvelle génération de moteurs
Les servo-moteurs de la série J5 assurent une collaboration homme-robot en toute sécurité sans capteur de force ou de couple supplémentaire tout est géré dans le drive grâce à la gestion en temps réel du courant admis au moteur. Cette gamme de moteurs est également disponible pour des projets d’automation spécifiques de nos clients.
Collaborations
« Les clients sont demandeurs de solutions complètes. Voilà pourquoi Mitsubishi a conclu des collaborations avec des fournisseurs de préhenseurs, de capteurs de forces et de systèmes de vision. Il y a plusieurs noms connus. Pour les
Melfa Assista le nouveau cobot de Mitsubishi
La sécurité est notamment assurée par le Safe Torque Range, diverses zones de vitesse et une indication visuelle de l’état du cobot.
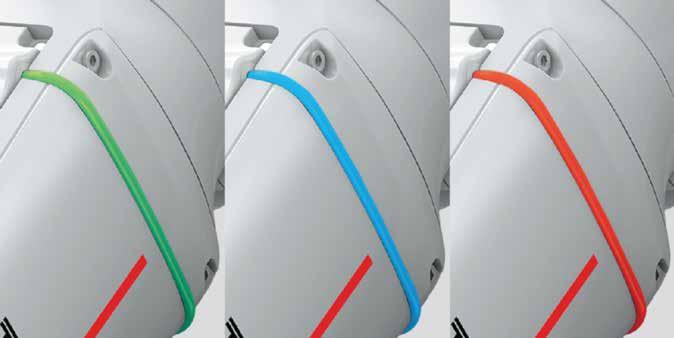
préhenseurs, Schunk, Zimmer, Schmalz et SMC offrent une gamme étendue et de qualité irréprochable. Pour les systèmes de vision, nous travaillons avec Cognex, expert en la matière. Leurs produits sont implémentés dans le package logiciel standard, ce qui facilite la configuration. La caméra est calibrée automatiquement via le logiciel de programmation du robot, ce qui représente un gain de temps pour le paramètrages des différents composants. »
Précision avec la dernière technologie d’encodeur
Koen D’Haese: « Mitsubishi est reconnu pour sa haute precision que l’on retrouve dans cet appareil. Les servomoteurs sont, par exemple, équipés de la dernière technologie d’encodeur. Ils affichent une résolution de 26 bits, ce qui signifie l’émission de 67 millions d’impulsions par révolution. La mesure de position est extrêmement précise, tout comme le contrôle du moteur. La précision de répétitivité est de 0,02 mm. Avec ce cobot, il n’est pas nécessaire d’avoir des batteries pour garder la position absolue, même lors de coupure d’alimentation de longue durée. Enfin, la construction du cobot est robuste pour travailler dans un environnement industriel. Une version est disponible pour l’industrie alimentaire, avec une lubrification de qualité alimentaire. »
Nouveaux développements dans les robots 6 axes:
Mitsubishi a élargi sa gamme de robots 4 axes et 6 axes, actuellement disponibles jusqu’à une charge de 3 kg à 20 kg, pour répondre aux demandes du marché de charge plus large avec un positionnement rapide et précis.
Des modèles de 35 kg, 50 kg et 70 kg en version 6 axes sont disponibles avec une portée de 2050 mm, une vitesse jusqu’à 13 m/s et une répétabilité de +/- 0,07 mm, en version IP40 ou IP67, ceci complète le programme de robot Mitsubishi.
Entre-temps, le robot RV-8CRL 6 axes a également été mis sur le marché, une solution plus abordable avec une portée de 931 mm pour des charges jusqu’à 8 kg, une vitesse jusqu’à 10,5 m / s et une répétabilité de +/- 0,02 mm, le tout dans un Version IP65.
Déménagement vers le site de Ghislenghien
Esco quittera le site de Diegem d’ici fin 2020 pour emménager dans un nouveau bâtiment à Ghislenghien. L’entreprise sera établie à la Rue des Foudriers 14 à 7822 Ath (Ghislenghien).
www.esco.be
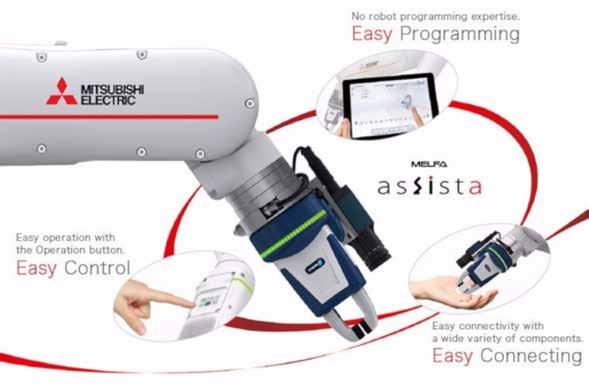
La conclusion de partenariats avec des fabricants de préhenseurs et de systèmes vision facilite l’implémentation.

Distributeur DAVID BROWN® réducteurs
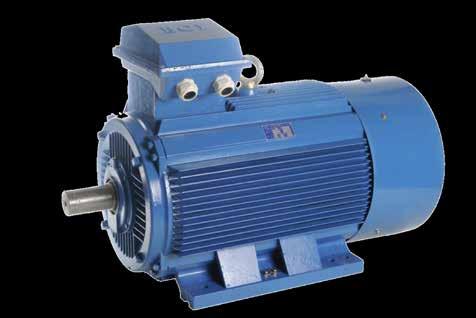


þ Tous moteurs - réducteurs - ven�lateurs þ OMRON® Servomoteurs - Drivers þ OMRON® Variateurs de fréquence þ Toutes répara�ons þ Changement spéciaux dans notre propre atelier þ Grand stock, service rapide þ Analyse moteur - équilibrage - alignement
Gentstraat 187 B-8770 INGELMUNSTER www.bci.be Tel: +32 (0) 51 30 49 73 +32 (0) 51 30 98 63 info@bci.be
NOUVELLES DATES POUR INE XL ET MACHINEERING
L’équipe d’Industrialfairs a adapté le calendrier d’INE XL (Indumation Network Event) et de MACHINEERING en vue de meilleures conditions de marché et une plus grande confiance des visiteurs et des exposants après la période de mesures strictes liées au coronavirus. L’organisateur des événements fait savoir qu’INE XL 2021 se déroulera le 27 mai 2021 (Courtrai Xpo) et MACHINEERING du 8 au 10 septembre 2021 (Brussels Expo).
Les deux événements auront lieu selon une formule hybride: les salons ‘on-site’ seront complétés par une plateforme en ligne interactive. De cette manière, chacun pourra réseauter ‘en direct’, agréablement et efficacement, déclarent les organisateurs. Ils espèrent aussi que le coronavirus sera d’ici là plus sous contrôle.
Comme annoncé précédemment, INDUMATION.BE n’aura pas lieu en 2021. Les organisateurs Industrialfairs, InduMotion vzw et Agoria ont décidé de reporter cette édition du plus grand salon industriel du pays à février 2022.
www.industrialfairs.com
Rapide. Compact. AMCAP.

L’AMCAP est un système haute performance permettant de générer automatiquement des palettes de produits mixtes, afin de répondre aux exigences les plus récentes du secteur du commerce de détail. La solution AMCAP optimise l’emprise au sol et l’espace nécessaire de 50% par rapport aux systèmes conçus antérieurement grâce à la combinaison des principaux modules fonctionnels. Cela signifie pour vous : l’optimisation de votre espace, une productivité élevée et par conséquent une augmentation de votre compétitivité. www.dematic.com
Power the Future of Commere

Via la tête magnétique, le robot TX200 peut mieux diriger les particules actives sur la tumeur cancéreuse. Le résultat est un traitement plus efficient.
LE ROBOT EST A L’AVANT-GARDE DE LA LUTTE CONTRE LE CANCER
L’implication de robots dans le traitement de patients n’est pas évidente. Les exigences sévères en matière de sécurité, d’hygiène et de précision catégorisent le secteur médical parmi les applications les plus exigeantes. Néanmoins, Stäubli est parvenu à affiner un traitement révolutionnaire contre le cancer à l’aide de son robot TX200. Les conséquences sont énormes pour les patients.
Soyons clairs: les robots ne sont pas nouveaux dans le secteur médical mais leur apport est souvent limité à l’automatisation de tâches de laboratoires ou à la production sécurisée de médicaments dans les grandes entreprises. Ils sont assez rares dans les hôpitaux et les blocs opératoires. Si la robotique n’est utilisée que dans certaines interventions chirurgicales spécifiques, le secteur s’intéresse progressivement à d’autres applications médicales. Le traitement du cancer en est un exemple.
Quiconque a été confronté à cette maladie connaît l’impact qu’elle peut avoir sur le corps et l’entourage. Pour traiter les tumeurs, deux grandes options sont généralement avancées : les retirer chirurgicalement ou essayer de les neutraliser via un traitement chimiothérapeutique. Dans le second cas, les problèmes sont connus : il est très difficile de cibler les tumeurs cancéreuses, et les cellules saines dans le corps sont affectées. Le patient doit souvent subir les effets secondaires des doses élevées de chimiothérapie.
Projet de recherche SEON
Les centres de recherche et les hôpitaux sont engagés depuis longtemps dans la recherche d’un traitement permettant de cibler les tumeurs sans toucher aux cellules saines. Le projet SEON de l’hôpital universitaire d’Erlangen est une de ces études prometteuses. Les chercheurs ont mis au point des nanoparticules magnétiques à partir d’oxyde de fer qui transportent les substances actives. Leur déplacement via une tête magnétique vers les tumeurs solides (métastases) permet d’obtenir un traitement plus effectif, plus rapide et moins douloureux. Cette méthode a été baptisée Magnetic Drug Targeting. Dans une première phase, la tête magnétique est placée manuellement dans les bonnes positions par le praticien et déplacée sur les tumeurs. Mais cette méthode a rapidement montré ses limites. Christoph Alexiou, chercheur: « En soi, cette méthode fonctionnait bien mais il y a des limites à la motricité humaine. Il va de soi qu’un robot à six axes peut mieux remplir cette tâche car il peut saisir l’ensemble du champ magnétique et aborder les zones à problèmes sous tous les angles possibles. »
Positionnement via la rétroaction IRM
« Ce qui est important dans notre approche, c’est le comportement des particules magnétiques. Via la technologie IRM (imagerie par résonance magnétique), nous pouvons découvrir quel a été l’impact du traitement car les particules d’oxyde de fer provoquent une différence dans le signal renvoyé. Nous pouvons donc savoir combien de particules ont atteint la tumeur et avec quelle efficacité cela s’est produit. En couplant cette information au contrôleur du robot, de nouvelles opportunités font leur apparition. Le robot, via la rétroaction, est informé en permanence de l’emplacement exact et de la taille de la tumeur. Il est donc possible de calculer précisément sa trajectoire et de mieux diriger la tête magnétique. Les nanoparticules pourront atteindre leur cible via un itinéraire le plus court possible. Le corps du patient sera moins sollicité et le traitement sera plus supportable. Par ailleurs, le taux d’erreurs est sensiblement moins élevé. »
Le TX200 de Stäubli
Le choix s’est porté sur le robot TX200 de Stäubli, également disponible dans une version clean room de classe 5 pour les applications médicales. La répétitivité du robot est de 0,06 mm et la portée de 2194 mm, ce qui est plus que suffisant pour cette application. Comme il n’est pas question ici de prévoir un grillage autour du robot, les mesures utiles ont été prises pour garantir la sécurité du patient. Le bâtiment a lui aussi connu quelques ajustements pour pouvoir supporter la charge de 2 tonnes.
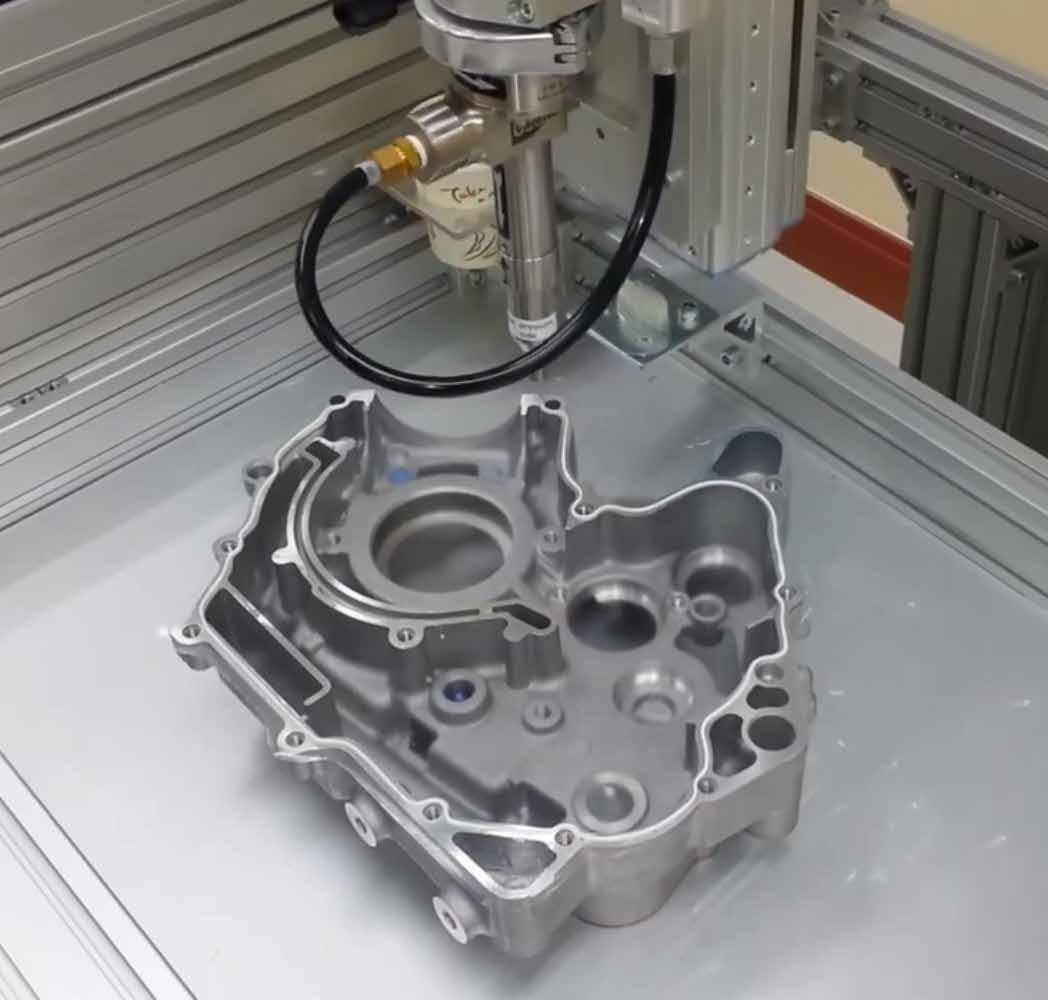
La fonction de distribution servocommandée améliorée de Yamaha avec le contrôleur RCX340.
UNE FABRICATION PLUS PRODUCTIVE GRÂCE À UN DOSAGE À HAUTE VITESSE
L’utilisation d’un robot pour doser les revêtements peut améliorer sensiblement la productivité, d’autant plus si la servocommande et la commande de distribution sont reliées, afin de garantir une vitesse optimale et une épaisseur de revêtement régulière
Dans le monde entier, les fabricants se tournent de plus en plus vers l’automatisation à grande vitesse pour relever les défis actuels en matière de productivité. Il est toutefois de plus en plus difficile d’augmenter le rendement tout en préservant la qualité en faisant appel à l’automatisation classique.
L’augmentation de la vitesse d’un processus tel que le dosage ou la distribution peut compromettre la précision et la répétabilité, et nécessiter des réglages des plus complexes pour obtenir la qualité souhaitée en fin de ligne. Généralement, seul un petit nombre de techniciens qualifiés et expérimentés sont capables de paramétrer et de superviser de tels processus, ce qui ralentit parfois l’introduction de nouveaux produits et entraîne des arrêts sur les lignes de production.
Allier productivité élevée et dosage de précision
L’expérience de Yamaha Robotics auprès de clients issus de secteurs aussi divers que l’automobile, l’électronique et la médecine, entre autres, est un gage de réussite. La dépose de joints sur les bords de composants métalliques moulés ou en plastique, tels que les couvercles et les boîtiers à assembler, est souvent réalisée à l’aide d’entraînements conventionnels pour coordonner le mouvement linéaire et la dépose du joint.
Pour déposer une ligne continue de joint, le système de contrôle des mouvements doit suivre précisément un trajet prédéterminé le long des bords droits et dans les angles. La vitesse doit généralement être réduite dans les coins pour que le trait soit précis à cet endroit. À l’inverse, il est préférable d’augmenter la vitesse de déplacement le long des bords droits de façon à réduire la durée totale du processus.
Pour garantir qu’un volume constant de joint soit déposé à chaque endroit, le mécanisme de distribution doit être contrôlé de manière à réduire le flux de pâte dans les angles, où la vitesse est faible, et à l’augmenter lorsque le moteur se déplace plus rapidement. Cette régulation est difficile à effectuer et les entreprises sont souvent dépendantes d’un petit nombre d’employés dotés du savoir-faire nécessaire.
En cas de mauvaise configuration, des défauts comme un excès de volume de joint dans les angles peuvent se produire, conduisant au final à un plus grand nombre de pièces rejetées en bout de ligne. Autrement, le choix d’une vitesse d’entraînement et de distribution lente et constante peut simplifier le contrôle du processus, mais avec un temps de cycle plus long et un rendement global plus faible.
En général, l’objectif des fabricants est d’allier haute qualité et grande vitesse sans devoir faire appel à des compétences spécialisées, ce qui passe par une solution capable d’ajuster automatiquement la vitesse de distribution des joints en fonction des variations de vitesse du mouvement, afin que le volume de produit souhaité soit appliqué à la vitesse maximale possible pour chaque position
L’automatisation et les robots
Plusieurs industries adoptent aujourd’hui l’automatisation robotique pour améliorer leur productivité et gagner en
flexibilité afin de faire face à l’avenir. Yamaha Robotics a en outre travaillé sur la facilité d’utilisation des contrôleurs de robots de la série RCX et de leurs outils de programmation graphique, afin d’aider les utilisateurs à tirer tous les avantages de cette technologie.
Le contrôleur RCX340 de Yamaha possède des capacités de mouvement améliorées et simplifie la configuration du système de distribution robotique. En particulier, la fonction de commande de la distribution peut être reliée à la servocommande, ce qui permet au RCX340 de contrôler le débit de distribution en fonction de la vitesse de déplacement pour garantir une grande précision, une vitesse élevée et une épaisseur de revêtement régulière. Cette « distribution servocommandée » (Photo 1) est applicable aux robots SCARA et aux robots cartésiens de Yamaha.
En outre, le contrôleur permet de relier facilement plusieurs robots à commander simultanément et est compatible avec un jeu d’instructions étendu, comprenant des instructions de vision dédiées qui simplifient la programmation et contribuent à minimiser le temps de démarrage des équipements. L’environnement de programmation RCX STUDIO 2020 contient des fonctions de débogage qui regroupent de nombreuses tâches, ainsi que des fonctionnalités qui accélèrent la saisie des programmes et la configuration.
Enfin, l’utilisation d’interfaces de communication couramment utilisées dans l’automatisation industrielle permet une intégration facile dans l’environnement existant d’une usine. En plus des ports RS-232C et Ethernet, le RCX340 accepte les bus de terrain courants : CC-Link, EtherNet/IP™, DeviceNet™, PROFIBUS, PROFINET et EtherCAT. Les connexions avec des servoamplificateurs d’usage général ou des systèmes de vision tiers sont également faciles à établir et simplifient l’introduction de la technologie robotique au sein des processus de fabrication existants.
Le dosage haute vitesse en pratique
Récemment, Yamaha Robotics a aidé un client du secteur automobile à accélérer la dépose de précision de joints liquides sur des pièces moulées en aluminium au moyen du contrôleur RCX340 et des robots Yamaha. Ce fabricant n’avait pas réussi à augmenter son rendement en accélérant la vitesse d’entraînement de son automate de distribution existant. Le simple fait d’augmenter la vitesse avait fait perdre le contrôle de la distribution de joints, d’où la formation d’importants amas de liquide aux endroits où la vitesse d’entraînement était plus lente. L’entreprise avait donc été contrainte de faire fonctionner l’équipement à une vitesse constante, allongeant de ce fait le temps de cycle.
Le responsable d’équipe du projet, qui cherchait une solution plus rapide et facile à mettre en place, sans avoir recours à des techniciens qualifiés, s’est tourné vers Yamaha pour savoir si la technologie robotique pourrait constituer une solution pratique. Après avoir vu la démonstration de la distribution servocommandée de Yamaha, il a rapidement installé un système pilote au sein de son usine pour en explorer le potentiel.
« Au-delà de l’augmentation de la vitesse de production, nos analyses ont montré que la qualité du revêtement était également parfaite, commente-t-il. Nous avons également interrogé Yamaha sur le processus de distribution que nous avions préalablement mis en place grâce à notre expérience en interne. Leur expertise supplémentaire nous a permis de calculer très rapidement les meilleurs réglages, d’où une réduction drastique de la charge de travail de nos ingénieurs. »
Après avoir atteint la vitesse souhaitée ainsi qu’une qualité stable, l’équipe du projet a procédé aux dernières vérifications puis a introduit ce processus sur la ligne de production. Une fois cette tâche terminée, elle a tout de suite commencé à explorer les possibilités d’utiliser des robots Yamaha pour améliorer d’autres processus au sein de l’usine.
Conclusion
Les fabricants, dans l’automobile comme dans d’autres secteurs, doivent renforcer l’automatisation pour accroître leur productivité en raccourcissant les temps de cycle tout en maintenant la qualité. (Photo 2)
Les robots peuvent répondre à cette problématique en étant associés aux dernières techniques de contrôle des mouvements ainsi qu’à des outils pratiques d’aide à la programmation et à la configuration. En effet, la facilité d’utilisation est essentielle pour aider les utilisateurs à introduire rapidement les nouveaux processus au sein de leur environnement industriel.
www.yamaha-motor-im.eu
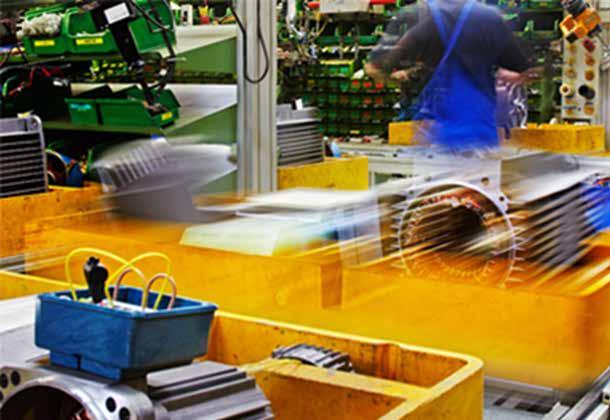
Les fabricants automobiles doivent concilier une productivité soutenue et une excellente qualité.