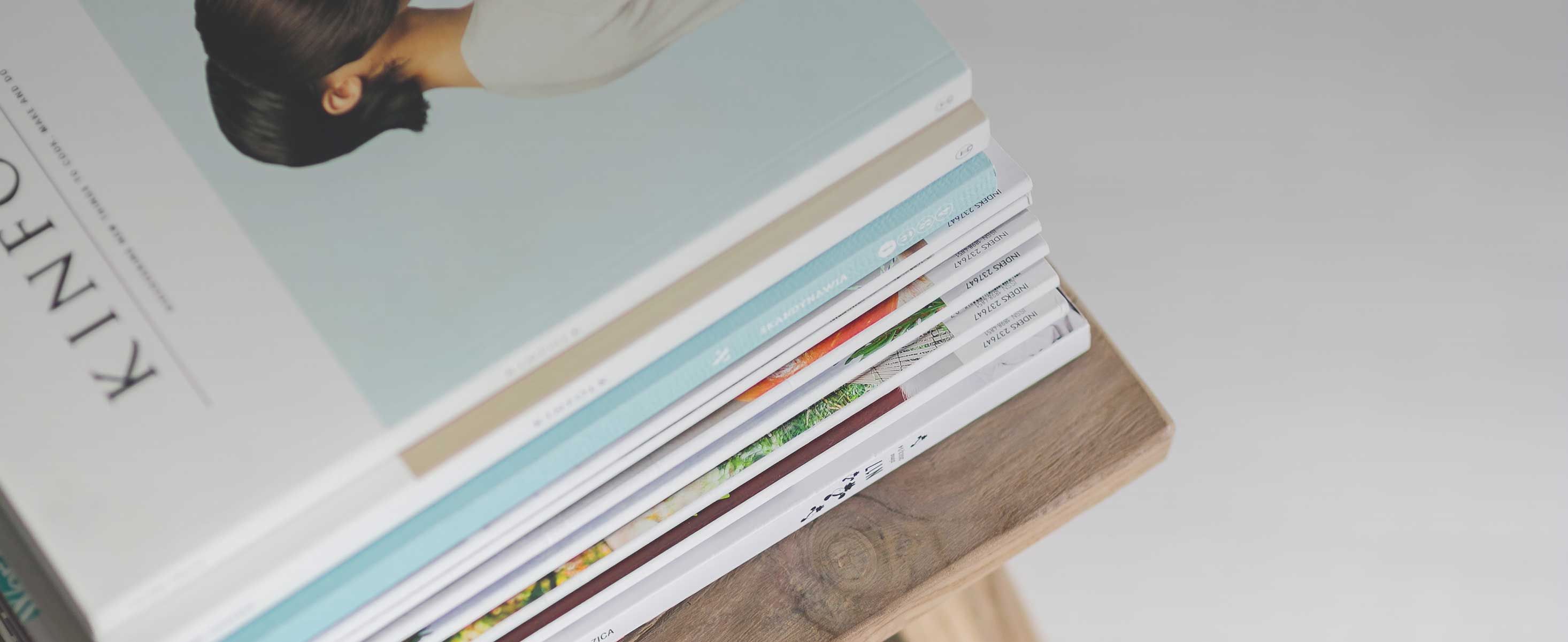
2 minute read
PROCESSES
Building Information Modelling (BIM):
The use of BIM – 3D modelling of the design – can potentially provide IPD project teams with the opportunity to pursue a truly collaborative approach to design, construction and ongoing management of an asset.
Pull planning works by identifying and isolating project phases adding detail in reverse order. The backward process will eventually add more detailed than a look ahead schedule when it is worked out in a reverse process when details and scopes are clearly defined and analysed. The pull planning process is derived from the actual project schedule when steps are analyzed, and details are added based on collaborative input from all responsible manager and superintendents.
The Big Room According to the Lean Construction Institute, “An effective Big Room supports cross-functional team collaboration by advancing work and bringing the larger team up to speed on the activities of other groups or individuals. It allows teams to understand their impact across clusters or work groups. The Big Room also provides teams with the time to discuss project-wide concerns like budgets, hot topics, or global changes. The term Big Room refers more to the behaviours and actions of the team than the physical space. The Big Room is more than co-location of people; it is about collaborative behaviour and the work they are producing.”
The communication and coordination strategy between the design consultants was defined in early design stage.
The project’s BIM execution plan defined the way of Revit models and CAD files would be exchanged within the project team. Consistent file naming conventions were established to keep track of various models and their versions. For example, each Revit file had to be named by project number, name, consultant discipline, and version (i.e. 10000_MC4_ARCH_v14).
The architects provided the base Revit model with grids, levels, orientation, and shared internal coordinates set in place. The levels and grids were copied/monitored from architect’s model and placed on consultants’ designated work set for increased control of grids and levels visibility in each consultants’ model.
During design coordination meetings, the consultants had to note meeting minutes of any changes needed in the model for future update. The consultants had to exchange their models every week by Friday noon and run coordination and interference checks to address any clashes of linked model elements.
Outside IPD and lean experts were brought in to facilitate intensive 2-day IPD and lean training for the project team
The project team participated in lean pull pl anning and lean scheduling training workshops starting early in the project process. IPD “boot camp” training was provided by Hanson Bridgett (author of the construction contract) and DPR Construction, a US-based contractor with IPD expertise that had been providing advice to Chandos. Project team members could also voluntarily attend a weekly or bi-weekly webinar for extra coaching. Chandos continued to offer regular informal coaching to team members after the initial training program and to trades as part of the onboarding process to help them get up to speed quickly.
Regular “Big Room“ meetings brought every player of the team to the table and everybody had access to anybody.
The Big Room meetings were very helpful in making the team gel as a collaborative group. In particular, the Big Room culture enabled the team to collaborate on finding cost efficiencies to the design. The “open book” approach allowed for a detailed review of labour and materials costs from the trades which generated opportunities to discuss how to decrease them. The first Big Room meeting was held over two days in Fall 2013 once the whole team was selected.