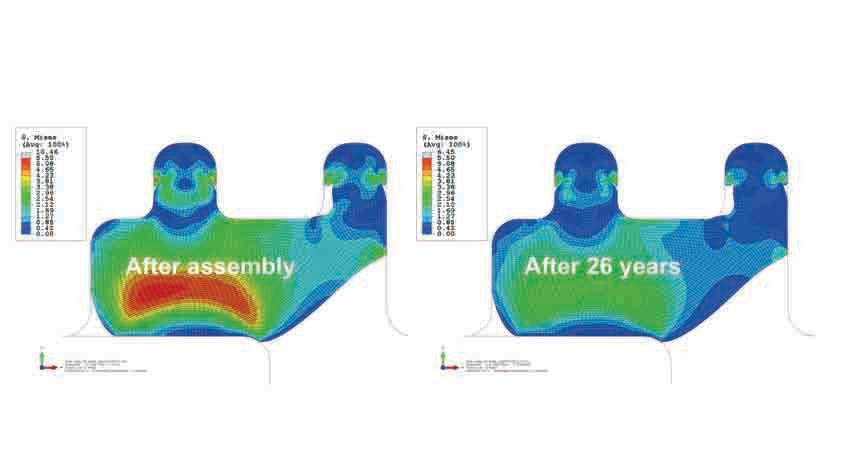
5 minute read
The search for the holy grail
MAINTENANCE-FREE SEALING
WITH AMBITIOUS TARGETS SET BY THE GOVERNMENT OF MANY COUNTRIES ALL OVER THE WORLD, OFFSHORE WIND IS GOING TO BE ONE OF THE MOST IMPORTANT SOURCES OF RENEWABLE ENERGY. CONSTRUCTED AT SEA, THE INSTALLATIONS MUST DEAL WITH HARSH CIRCUMSTANCES THAT AFFECT OPERATIONAL COSTS.
ALL IMAGES COURTESY OF FREUDENBERG SEALING TECHNOLOGIES, UNLESS STATED OTHERWISE.
Once they provide energy, offshore turbines require maintenance and technicians hence need to go offshore. This is expensive and not without risk, which is why ample companies are looking for components that are long-lasting. In the best case, they are completely maintenance-free and need no replacement during a turbine’s technical lifetime. International steel construction company Smulders, for example, asked Freudenberg Sealing Technologies to think along to find a maintenance-free sealing solution for the protection of the bolted connection of monopiles (MPs), transition pieces (TPs), and turbine towers. We learn more about this from Jelle Timmers, Project Manager at Smulders, and Patrick De Schryver, Sales Engineer at Freudenberg Sealing Technologies.
Valued partner “As more and more offshore windfarms are non-subsidised projects, operators are seeking ways to cut down costs”, Mr Timmers says. “Limiting the need of maintenance contributes to this goal. As producer of MPs and TPs, one of our challenges in this matter is to improve the protection of bolts that are used for connecting the MPs, TPs, and towers. The protection is important as the impact of water will lead to corrosion of the connections and this will subsequently undermine the turbine’s safe and stable construction. Freudenberg has been a valued partner for us in lots of projects and we contacted them to look for a sealing solution for the Triton Knoll project that will last at least as long as the predicted technical life of the turbines, which is approximately 27 years.” Early stage “Most seals used in the offshore wind industry are more or less universal”, Mr De Schryver explains. “This means that they are a compromise to fit various sizes of bearings. For many, searching for zero maintenance is like searching for the holy grail as this will considerably reduce costs. Throughout the years, we have built a lot of knowledge about sealing solutions in many different industries and our research recently resulted in a maintenance-free seal that we first used in a previous offshore windfarm project. This seal formed the basis for the development of the seal for the Smulders project.” “For us,” Mr De Schryver continues, “it was a big advantage that Smulders contacted us in the beginning of the project at an early stage. We usually join a project much later and must then deal with fixed specifications that leave us little room, but we were now able to give advice even before the design phase.”
DNV GL approved simulations The search for a seal that will last for more than 25 years was a real challenge, according to Mr De Schryver. The biggest issue was that it is impossible to really test the seal’s lifespan, as this would take more than 25 years. Freudenberg thus had to find a proper way of simulation that was found in FEM (finite element method) calculations. “With the FEM calculations, we were able to simulate the lifetime of the seals, which finally resulted in the best compound. To guarantee our customers that the tests are reliable and representative, they have been >>
Simulation of a seal (cross sectional view) at installation, demonstrating that the seal is still highly effective after 26 years of use.
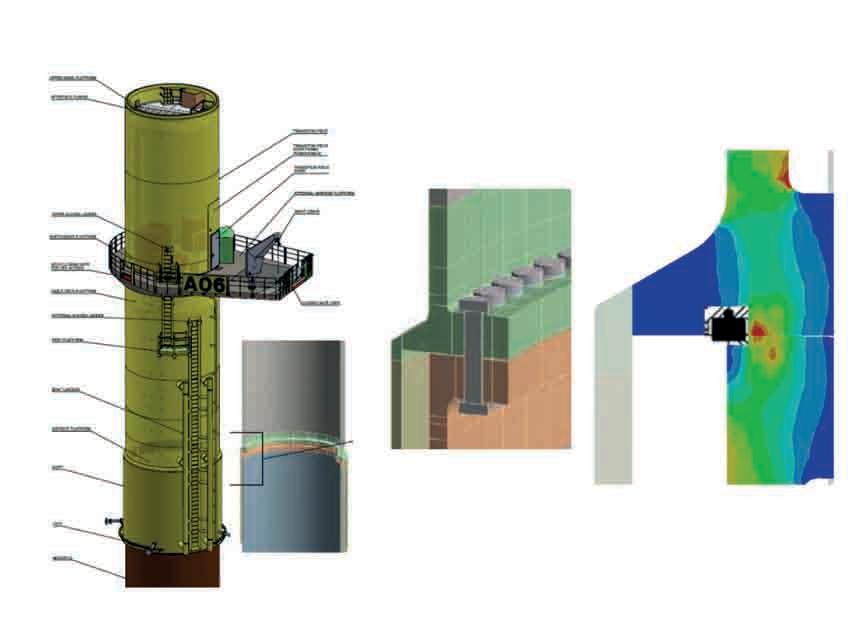
To obtain the best result from the seal, the depth of the bearing should accurately match the size of the seal.
Once they provide energy, offshore turbines require maintenance and technicians hence need to go offshore. This is expensive and not without risk.

Photo courtesy of Ørsted.
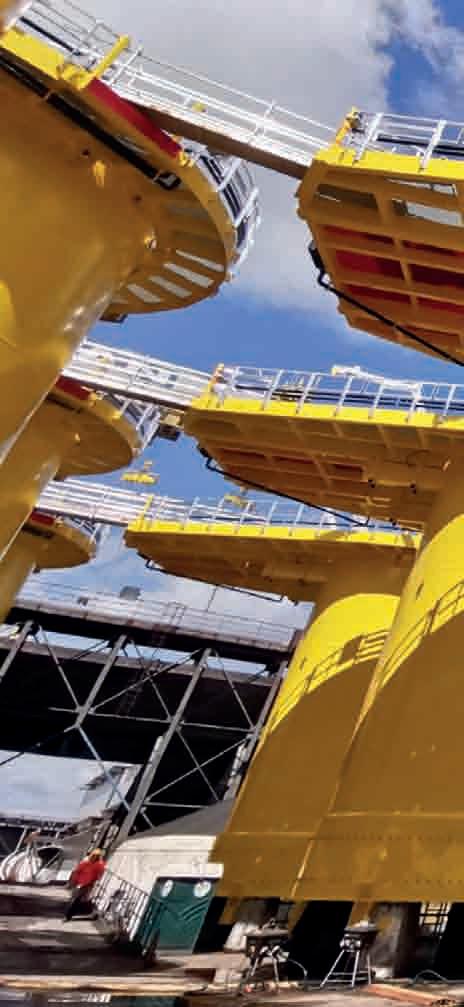
checked and approved by DNV GL. In other words, our simulations represent the seal’s behaviour in real-time use.”
Little tolerance A more generic challenge in the development of the rubber seal to be used in steel construction is that the design characteristics of rubber and steel are in a way contradictory. “In order to get the best protection for bolted connections, the type of rubber used is relatively hard. This leaves little tolerance in dimensions. Even the smallest deviation can result in a bad sealing”, Mr De Schrijver explains. “For steel, on the other hand, the engineers prefer more tolerance. We always have to find some kind of compromise, without loss of the protection quality. Take the bearing, for example. To obtain the best
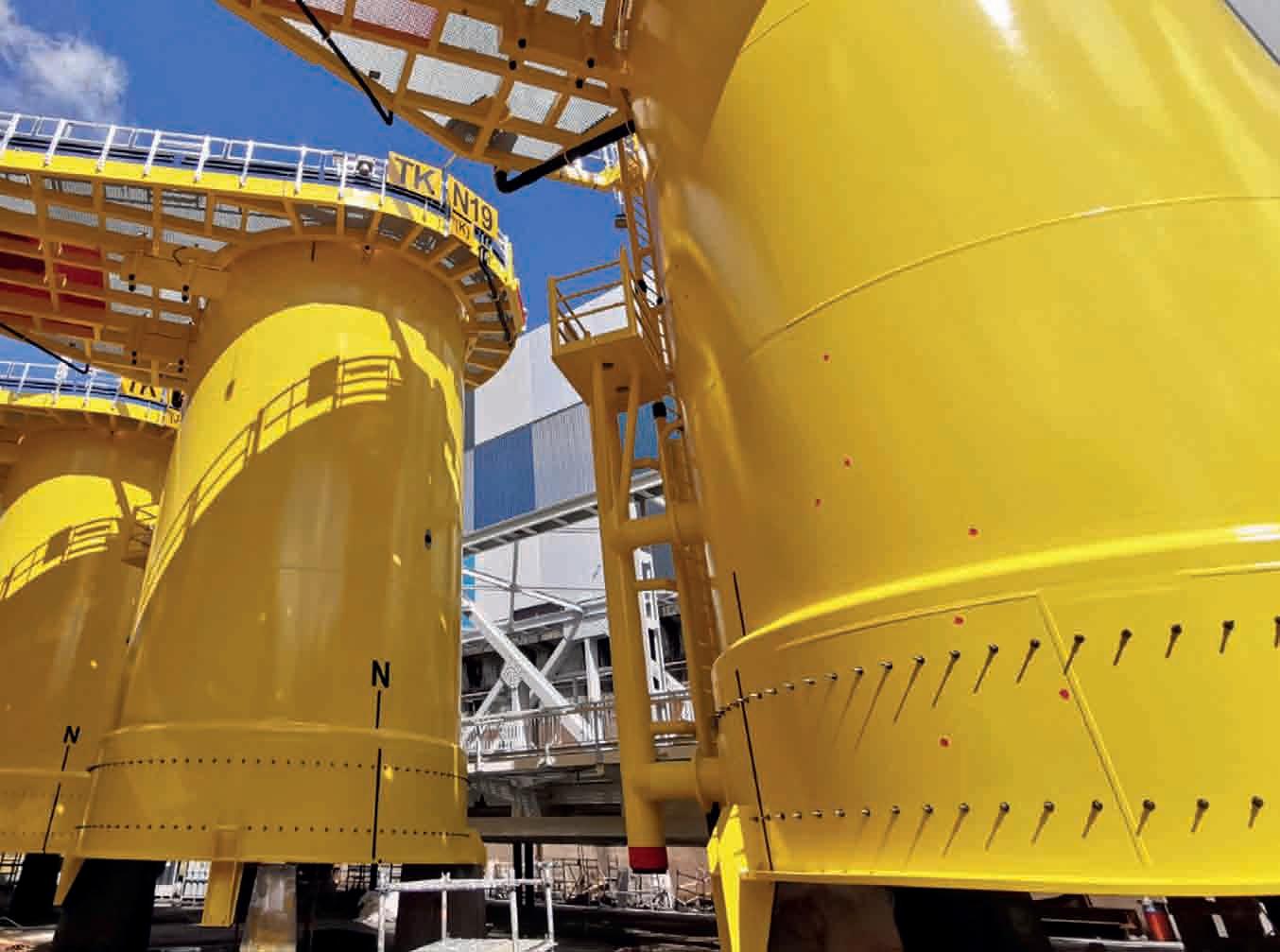
One of Smulders’ challenges is to improve the protection of bolts that are used for connecting the MPs, TPs, and towers. Freudenberg has been a valued partner for them in lots of projects.
result from the seal, the depth of the bearing should accurately match the size of the seal. Steel manufacturers prefer a bearing with as little depth as possible, as this makes the construction stronger.” Mr De Schyver continues, “Being involved in the design of the monopiles at an early stage helped us to find the right compound for the Triton Knoll windfarm. In one single windfarm, almost each monopile foundation differs in dimensions. But the good thing was that once we had found the proper compound, we could use it for the various sizes of structures, not only for wind turbines but for the substation, too.”
Solving issues Over the years, the companies involved have always searched for improvements in the field of construction and O&M. A point of interest in this issue is the size increase of offshore wind turbines that demand more from the materials used. “Apart from the use of bolts,” says Mr Timmers, “other connection solutions are also developed, such as the slip joint connection. But as construction and maintenance at sea is very expensive, the market is relatively conservative. This is why most operators and contractors opt for existing solutions that are constantly improved, instead of going for something totally new.” The growing size of turbines is certainly challenging for the sealing experts at Freudenberg. “The seal must increase along with the growth of the turbine”, elaborates Mr De Schryver. “However, that is not the only issue. The larger the turbines become,
Photo courtesy of Smulders.
the more they will be affected by forces such as wind and waves, and a lot is required from our seals in absorbing these movements.” According to Mr De Schryver, solving exactly these types of issues truly distinguishes Freudenberg from any competition. “Our company was founded in 1849. Since the development of our Simmerring Radial Shaft Seal in 1929, we have been working constantly on improving our sealing solutions. Like Smulders, plenty of renowned companies know this and value our collaboration for making their products even better. We have thus become a reliable sealing partner for the offshore industry”, Mr De Schryver concludes.