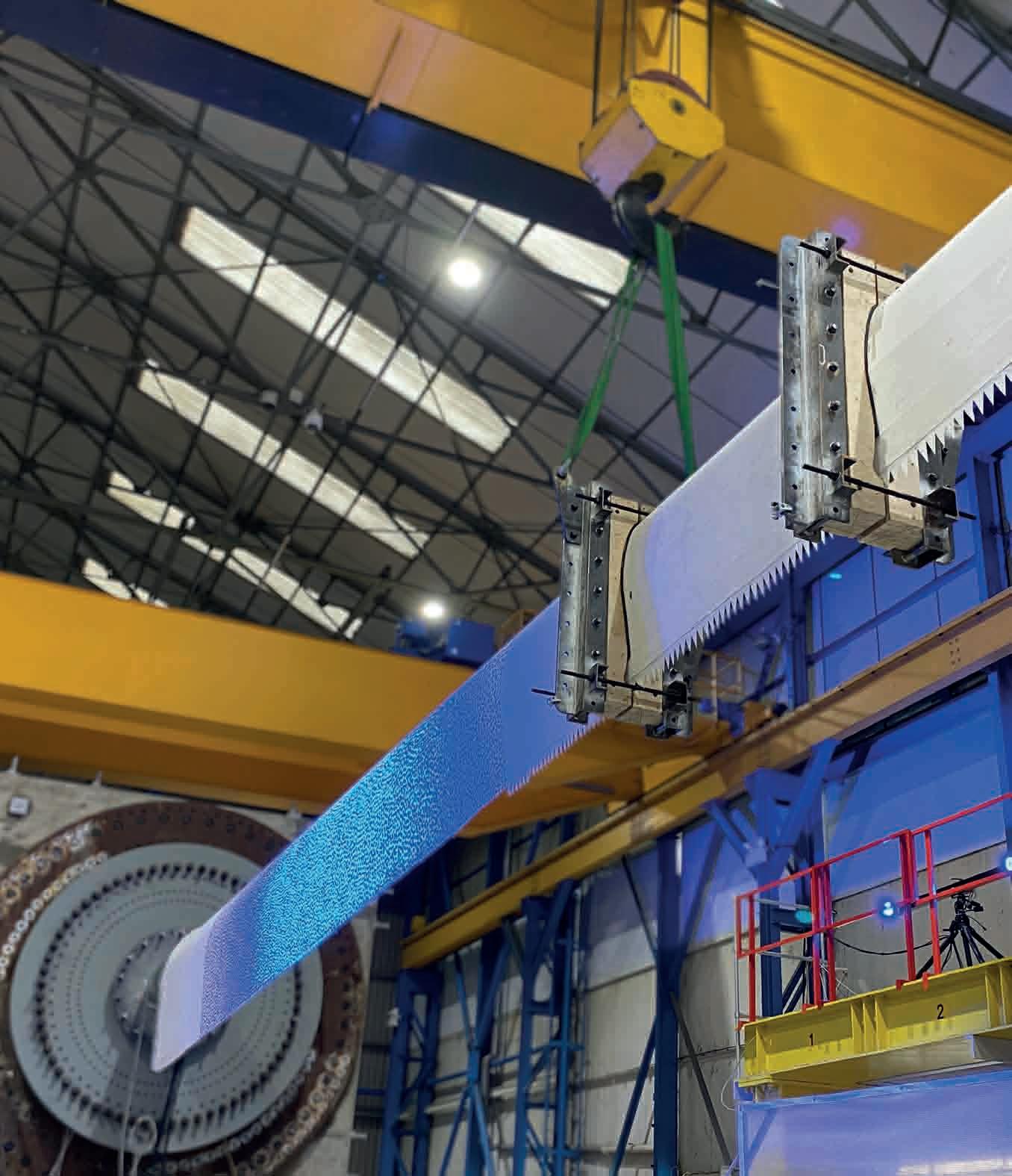
4 minute read
Lightweight and resilient
TEXTILE TURBINE BLADES
INNOVATION IS OFTEN BROUGHT ABOUT BY ADAPTING TECHNOLOGY FROM ONE INDUSTRY TO IMPROVE A CERTAIN ASPECT IN ANOTHER. WHEN OFFSHORE RENEWABLE ENERGY (ORE) CATAPULT ISSUED A BLADE INNOVATION CHALLENGE BACK IN 2015, THE RESPONSE CAME FROM AN UNEXPECTED SECTOR: THE YACHT-RACING WORLD.
ORE Catapult, a technology innovation and research centre for offshore renewable energy based in the UK, has set out several innovation challenges in recent years. One of these challenges was directed at wind turbines blades, tasking companies to improve blade performance.
Same race One response to the challenge immediately caught ORE Catapult’s attention: that of Dr Sabrina Malpede, founder of UK-based SMAR Azure. Dr Malpede and her team have been designing some of the fastest sails in the world for more than a decade. Their innovative technology and design have helped yachts travel up to three times the speed of wind. Dr Malpede identified an opportunity to adapt her team’s sailing technology to improve the performance of wind turbines for the energy sector. She commented: “I realised that the offshore wind industry was engaged in the same race as we were in the yacht-racing world: we need to reduce loads and capture more wind power without compromising on durability.” As Dr Malpede didn’t have enough knowledge of the renewable energy sector and needed to qualify her theory with sector experts, she entered ORE Catapult’s Blade Innovation Challenge. The result was a spin out company, ACT Blade, that designed the world’s first textile blade.
ACT Blade Following the completion of a feasibility study conducted in collaboration with DNVGL and ORE Catapult, ACT Blade was founded in November 2015 and its namesake blade was created. Made up of an internal composite structure and high-tech textiles, as opposed to the prevailing fibreglass, ACT’s blades are 24% lighter. A lower weight means blades can be made 10% longer than the standard 55m blade >>
Dr Sabrina Malpede, Founder of SMAR Azure and Execute Director of ACT Blade.
The ACT Blade is made of an internal composite structure and high-tech textiles, as opposed to the prevailing fibreglass.
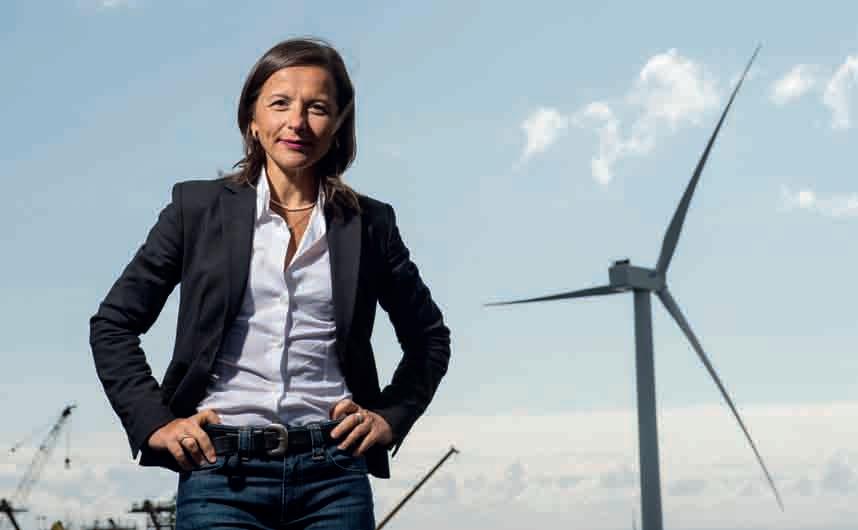
Testing of the ACT Blade prototype at ORE Catapult’s blade test and validation facility at the National Renewable Energy Centre in Blyth, Northumberland.
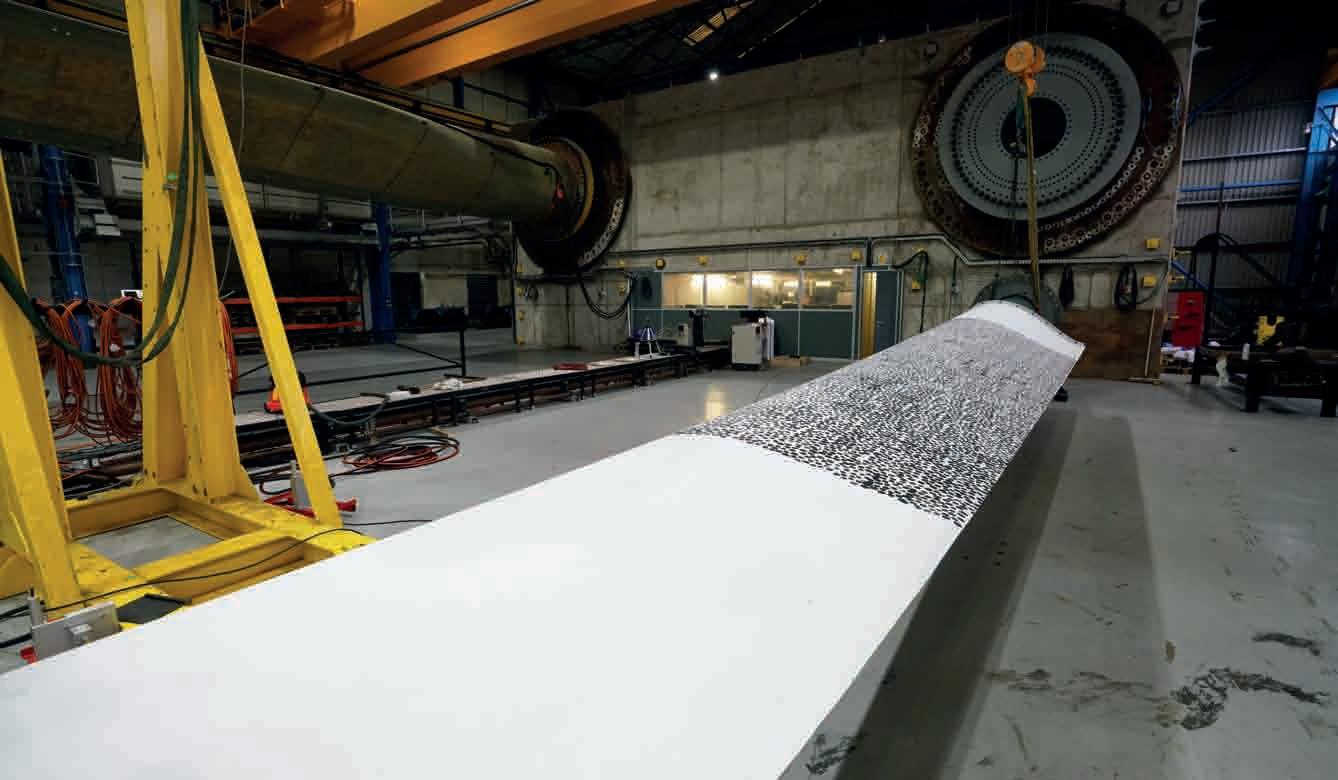
Photo courtesy of ORE Catapult.
around today. By covering a larger swept area, the longer blade captures more wind, thus increasing the energy production, which lowers the levelised cost of energy (LCoE). In April 2020, ACT Blade announced that it had successfully completed the first of two tests of its novel lightweight blade at ORE Catapult’s blade test and validation facility at the National Renewable Energy Centre in Blyth, Northumberland. Over a period of three weeks, a full-length prototype blade withstood the world’s toughest simulation of offshore wind conditions, aimed at testing its structural integrity and durability to the limit.
Production gains According to the test, the textile ACT Blade could achieve a 9% production gain and a reduction in the LCoE of 6.7%, making it one of the most promising innovations in the history of renewable energy. Post-test inspections showed the ACT Blade prototype to have held its shape with no damage. The test results indicated that the blade could withstand extreme loads and every type of direction and twist, going beyond those predicted for an in-service turbine. The test data – including optically measured strain and deflection results from within the blade textile – are now being analysed to gain a fuller understanding of the blade’s behaviour.
Commercial installation Over the next six months, ACT Blade will work with the Energy Technology Centre to prepare for installation of three blades on a working wind turbine at the Myres Hill Wind Farm in Scotland, as a further step towards commercialisation of the blade concept. The development of modular blades could prove promising for developing countries, where poorer infrastructure means fulllength blades are all but impossible to transport. Moreover, since the ACT Blade weighs 24% less than a conventional blade, less material is needed, reducing production waste as well. To produce an eight-ton blade, this saves nearly two tonnes in production materials, and an estimated 1.5t in production waste. The ACT blade is made of smaller components and end-of-life (EoL) design
Act Blade and SMAR Azure
ACT Blade was founded in November 2015. The founders are Dr Sabrina Malpede (Executive Director), Dr Alessandro Rosiello (Finance and NonExecutive Director) and Dr Donald MacVicar (Technical Director). The team’s first successful venture, SMAR Azure, is the market leader in tailored computerised design and analytical software for the marine industry. Their products are used by more than 200 users, including two certification agencies in 30 countries. The R&D team comprises specialists in aerodynamics, structures mechanical and composite engineering.
principles are considered, making it easier to dismantle and separate materials for recycling. The use of textile also allows for monitoring sensors to be embedded and to be re-used at its end-of-life, just as is done in sailing.