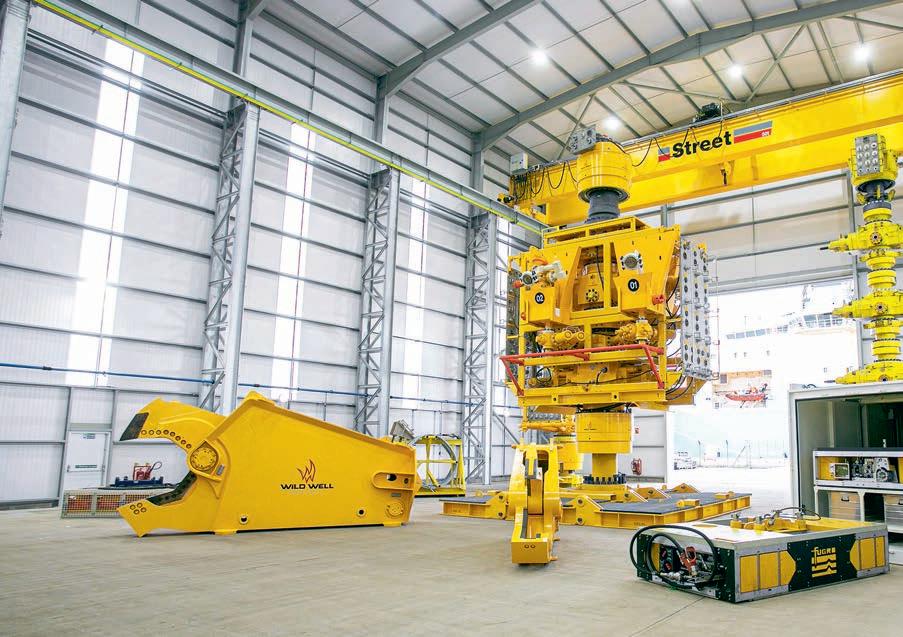
5 minute read
Ensuring you are ready for the unexpected
Wild Well subsea response package. The capping stack is the centrepiece of any response package.
Since the 2010 Macondo disaster in the US Gulf Of Mexico, detailed emergency response planning and access to purpose-built subsea response equipment became the norm to ensure industry readiness in case another deepwater drilling incident should occur.
WORDS BY CHRIS LECOMPTE, GENERAL MANAGER, WELLCONTAINED SERVICES GROUP, WILD WELL CONTROL. ALL PHOTOS COURTESY OF WILD WELL CONTROL.
With the majority of the equipment aging since it has been manufactured, maintenance and preservation to a high standard are imperative to ensure its readiness. Maintenance programs should include detailed record keeping, fuid sampling and testing, function and pressure testing, and elastomer changes in line with original equipment manufacturer (OEM) recommendations. Ofshore operators should conduct regular audits to ensure that subsea emergency response equipment providers are maintaining the equipment
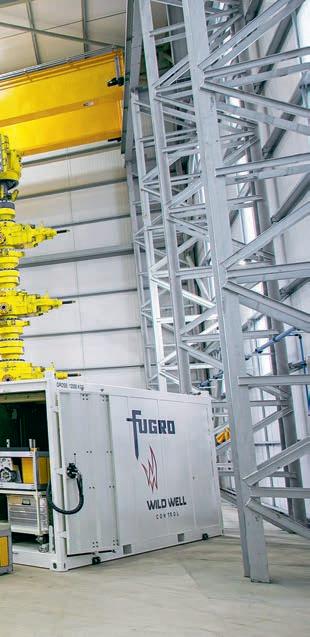
to these high standards. This article discusses key components of an efective equipment maintenance program. Since this equipment is safety critical but seldom feld used, it’s crucial that the maintenance program addresses consistency and thoroughness so no efectiveness is lost due to complacency, process failure, or human error. The article also discusses predictive maintenance and fuid sample analysis through technology.
Subsea response solutions
The Macondo disaster launched a review of subsea safety processes and procedures globally and initiated the development of dedicated subsea well control prevention, planning, and response equipment. Subsea response packages vary depending on the
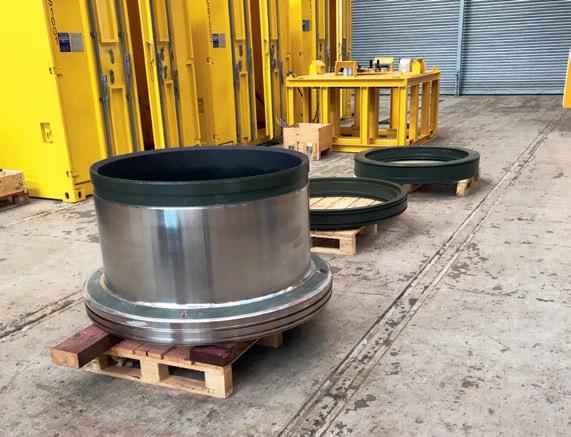
Connector disassembled for inspection and recertifcation.
provider. However, they typically include cutting equipment for the removal of subsea debris, a capping stack, and subsea dispersant application equipment such as hoses, ROV wands, and manifolds. The capping stack is the centrepiece of any response package. It is lowered over the incident well to stop or redirect the fow of hydrocarbons to minimise hydrocarbon release into the environment while control of the well is re-established. Wild Well Control, one of the leading providers of well control emergency response, has developed a range of subsea capping solutions via its WellContained division: services include prevention and contingency planning, system and equipment maintenance and testing, and event response to feld deployment of a capping stack onto an uncontrolled well.
Essential maintenance
Key considerations for maintenance of subsea response equipment are ensuring it is ready to be deployed promptly and ensuring all equipment tracking, testing, and certifcation documents are valid and up to date. Thankfully, no large-scale deepwater disasters occurred since Macondo. Because of this, complacency becomes a large risk. Equipment providers must undergo a comprehensive program of maintenance outlined in the second edition of API Recommended Practice 17W. However, OEM maintenance recommendations are developed for equipment that is in use every day, or for preservation of equipment in long-term storage. Neither is wholly appropriate for subsea response equipment, so bespoke maintenance programs must be developed and agreed upon with >>
Media Kit 2023 Available Now!
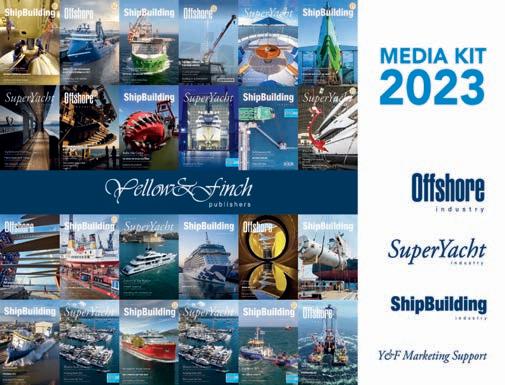
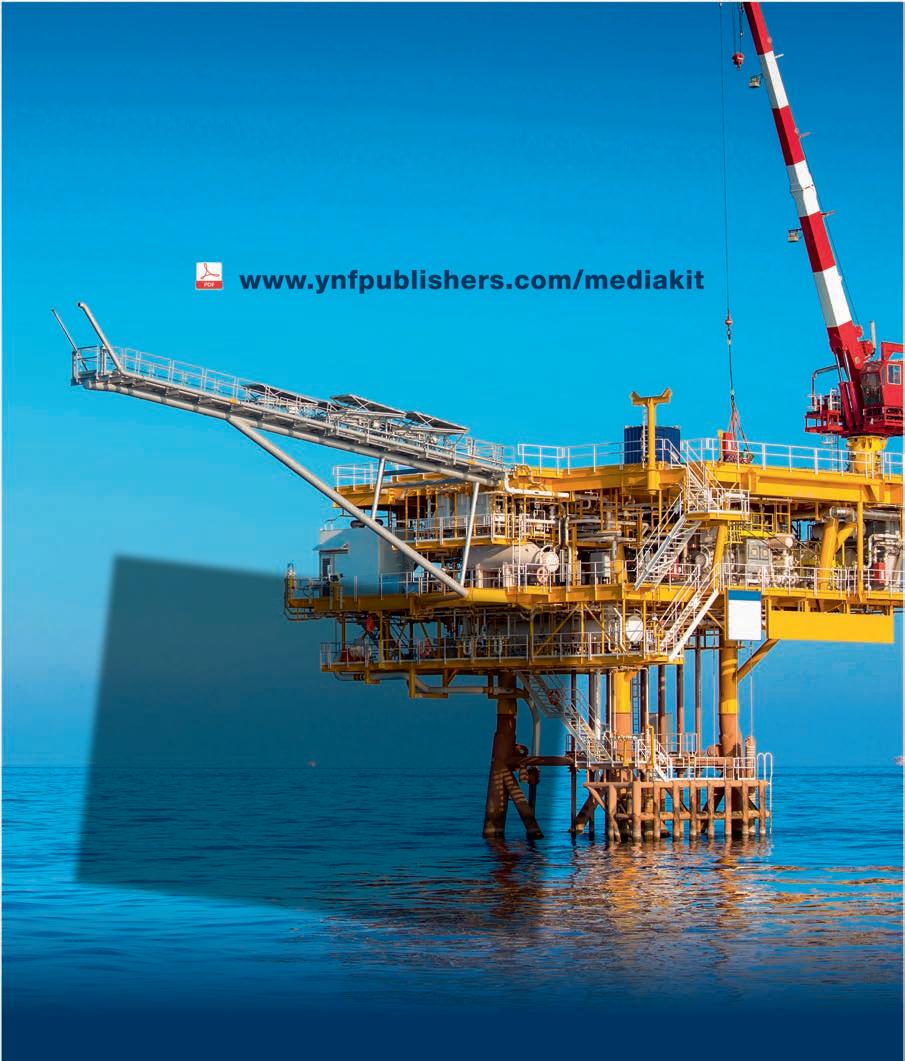
the equipment OEM. Wild Well Control worked with OEMs over several years to develop maintenance programs that support both the OEM and Wild Well Control’s standards and policies for maintenance of the company’s subsea response equipment.
Fluid and pressure testing
Sample analysation of equipment operating fuid can reveal much about the internal condition of the equipment. Fluid samples should be taken and sent for laboratory inspection every time the equipment is operated. Lab tests can reveal fuid acidity and determine cleanliness level. Lab analysis of any particles or colouring found in the fuid can also indicate elastomeric seal and internal coating condition. Pressure testing is another clear indicator of equipment performance. In addition to providing pass/fail information on the pressure control equipment, pressure testing the functional circuits of the equipment provides data on elastomeric seal condition and other internal conditions. Monitoring and recording running pressures during functioning of the equipment can signal the need for further investigation if the pressures are out of OEM specifcations and can be used simultaneously with predictive maintenance programs to reveal problems proactively.
Detailed records
Detailed record keeping incorporating full traceability of parts is critical and should include up to date OEM COCs. COCs are valid for a period of fve to twenty years depending on equipment type and API certifcation, so it is important to stay up to date current on COC expiration dates. Subsea response package providers internal records should include: OEM COCs, material data books, periodic testing records, rigging certifcation records, details of any non-conformance fndings and their resolutions along with data logs of operating parameters of the equipment. Elastomer changes should be carried out per OEM recommendations, but at minimum at each COC renewal. OEMs issue engineering bulletins or equipment notices when there are required upgrades or recommended improvements due to lessons learned from equipment in use in the feld that should be incorporated into maintenance activities.
Predictive consistency through digitalisation
The increased use of digital technology enables consistent results and record keeping by identifying trends and test anomalies. Wild Well Control’s maintenance software system creates work orders with detailed instructions for technicians to follow, mitigating any missteps. The industry’s commitment to exploration and pushing boundaries of existing technology means subsea response providers must continually adapt. In addition, the introduction of carbon capture projects will require analysis of operational risks in order to determine suitability of existing capping equipment or to develop new requirements for additional purpose-built equipment.
Conclusion
The subsea industry made signifcant improvements to ensure that major subsea incidents don’t happen again. Major investments in personnel training, planning, and equipment have been made to certify that the industry is better prepared should events occur. However, it is critical that complacency doesn’t hurt the continued investment in properly maintained equipment.
i. wildwell.com
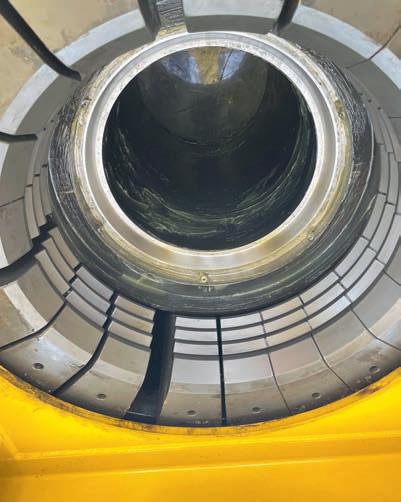
Inspection inside the connector.
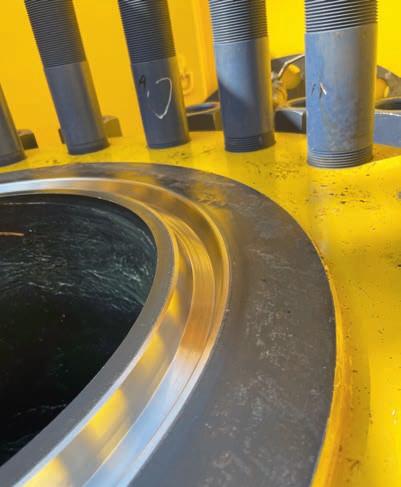