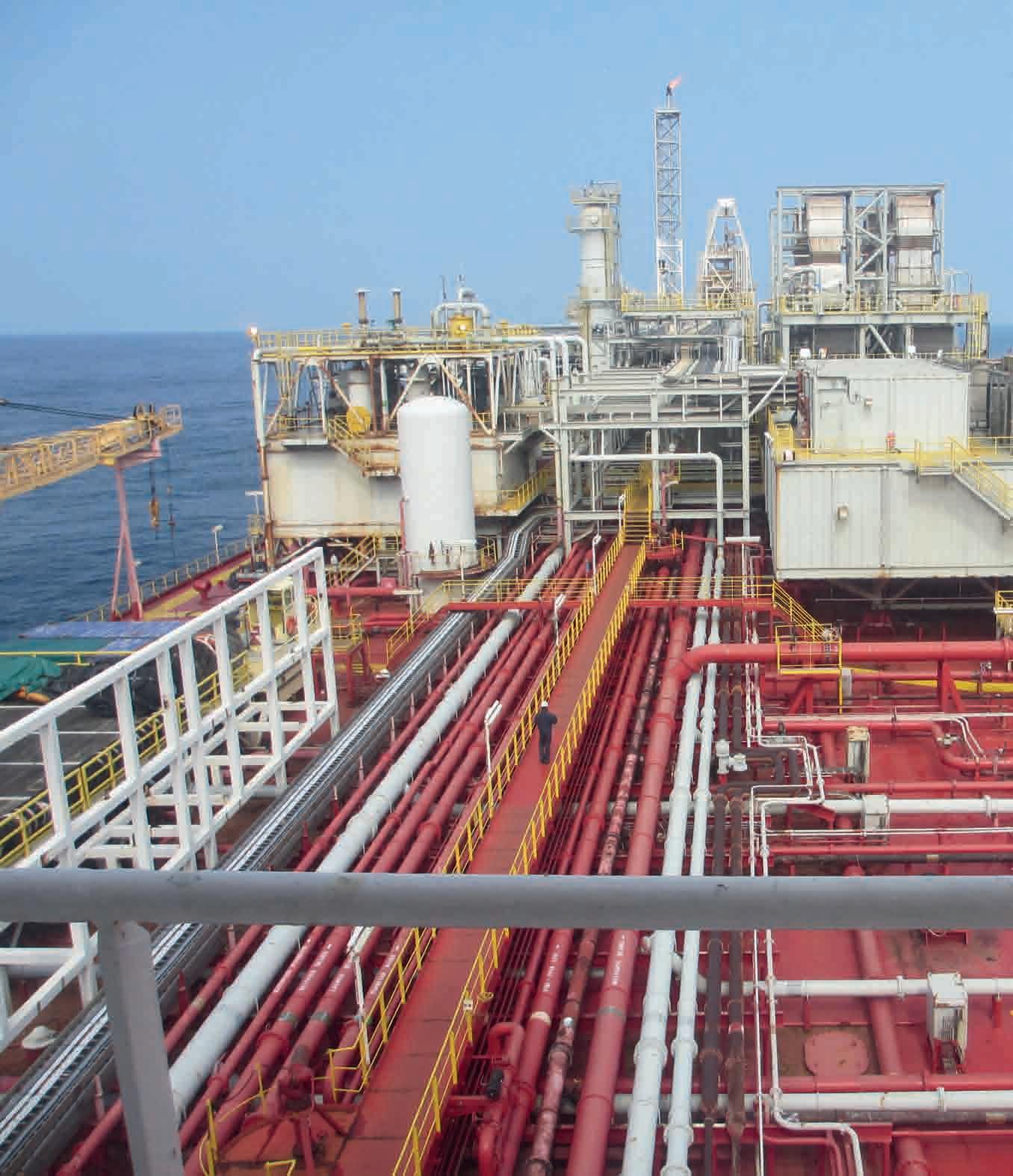
7 minute read
SPS Technology offers answer to unnecessarily costly repairs
No hot work repairs
SPS TECHNOLOGY OFFERS AN ANSWER TO UNNECESSARILY COSTLY REPAIRS
In these uncertain times, it is important that companies look at smart solutions for repair and maintenance of FPSOs.
A KNOWLEDGE GAP AND LACK OF COMMUNICATION IN THE OFFSHORE MARKET IS CAUSING REPAIR PROJECTS ON FPSOS TO COST MILLIONS OF EUROS MORE THAN NECESSARY.
ALL IMAGES COURTESY OF SPS TECHNOLOGY.
The already low oil prices are currently being driven down further by the COVID-19 pandemic. Oil producers have the choice of either closing wells or storing their oil until prices go up again. As a direct result of the latter, it is likely that Floating Production, Storage and Offloading (FPSO) vessels will be more in demand than ever. That means these vessels will need more maintenance and repairs, especially when companies are re-activating older or retired assets. In these uncertain times, it is especially important that companies look at smart solutions for repair and maintenance, says SPS Technology Business Manager Ian Nash. And according to him, that has long been one of the industry’s biggest challenges. “FPSO units have become the go-to asset, reflecting the market sentiment for maximising output with minimal spend. Offering lower CAPEX, more flexibility, and cheaper abandonment costs than fixed platforms, the FPSO market is expected to be worth EUR 49 billion by 2023, up by more than 50% against 2016 levels.” In order to capture the FPSO retrofit opportunity with lifecycle extension solutions, reviving ageing FPSOs requires considerable maintenance and repair work. “This is typically a time-consuming and expensive undertaking when choosing traditional repair methods, with costly downtime and potentially hazardous operations”, adds Mr Nash. “A more holistic view of maintenance projects combined with a broader understanding of available and proven repair methods could generate millions of dollars in time and cost savings. However, there are obstacles intrinsic to the industry which are keeping these potential savings out of reach of repair and maintenance managers.”
Growing knowledge gap Referencing the industry survey ‘FPSO 2019: The State of the Market’, Mr Nash observes that decision makers at all key stages of an
asset’s lifecycle are recognised as possessing less industry knowledge than would have been typical ten years ago. “There is a brain drain, because people who have been working in the industry for 20 to 30 years are retiring. At the same time, there is an escalating shortage of skills entering the market and an increasing competition for talent. The resulting brain drain is a hindering factor.” There is huge opportunity for asset owners to educate themselves and their teams to review and reconsider their historic understanding of the cost and capability of the numerous repair techniques available in today’s market. “Generally, operators in the offshore industry can spend more than half a year preparing for planned maintenance periods, during which remedial work can be undertaken in what is normally a hazardous environment”, states Mr Nash. “Furthermore, the true costs of a repair can be difficult to ascertain, as the budgets for these repairs are often spread across a myriad of departments, each managed by different personnel with their own budget and goals. With this fragmented approach, senior managers are unable to take an overarching view of procedures and identify areas of overspend or excess downtime.”
>> Thinking outside the box In order to make the most of the available budgets, it is imperative that there is a closer collaboration across departments to facilitate knowledge sharing. It is also vital that the industry looks at all the available solutions for lifecycle extension. “The oil & gas industry has done things a certain way for a long time and that way has worked when the profit margins were healthy. That is no longer the case, so we need to focus on ways to control costs”, urges Mr Nash. “The answer lies in looking at technological improvements for their potential to reduce the spend. There are other options available, that have been around for a long time, but they are not industry practice.
WWW.DEHOOP.NET

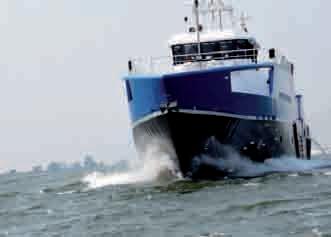
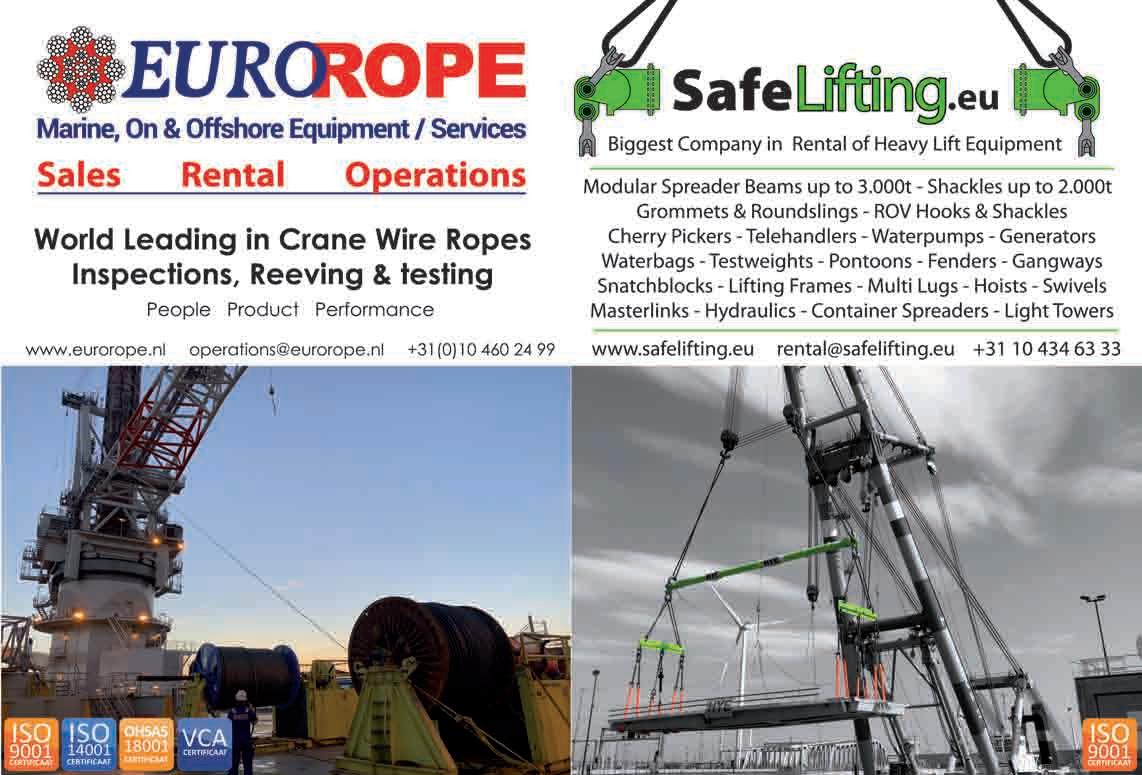
CREATIVITY
130 YEARS OF EXPERIENCE

Shipyard De Hoop concentrates on designing, engineering and building custom vessels, for both the inland and seagoing markets. The yard has all the core disciplines in house to provide clients with creative and innovative solutions, both in design and production. De Hoop is committed to a customer-oriented, goal-based approach in which quality and flexibility are paramount.
INNOVATION
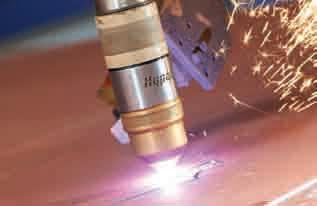

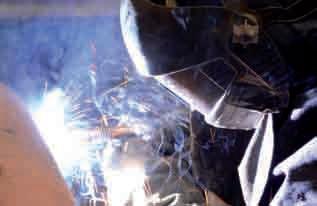
CRAFTMANSHIP
The industry needs people who think outside the box.” Structural steel repairs are one such area where alternative solutions are available. “Traditional methods include cutting away the affected steel and replacing it with a new section. However, there is an alternative method that offers both improved cost control and reduced downtime and comes with a ream of safety and environmental benefits”, states Mr Nash. “Our repair technique is one of the industry’s best kept secrets. It is time that changes.”
Permanent class approved repair SPS Technology offers ‘SPS no hot work’ (NHW) repairs, a patented composite steel repair solution. The affected section of the hull is left in place, but a new steel top plate is fitted over it on the inside of the vessel. It is then bonded to the original section by a solid polyurethane elastomer core. “The no hot work solution reduces the down time of the asset massively,” reveals Mr Nash. “There is no risk of oil leaks and there is no need for divers or special equipment, so you eliminate those health and safety risk factors as well.” According to Mr Nash, another major advantage is the fact that the NHW repairs do not affect day-to-day operations of an FPSO. “With traditional main deck repairs, the tanks may need to be emptied or operations halted while the repair is in progress. With NHW, there is no need for that. Our solution can be up to eleven times cheaper and three times faster than traditional crop and renewal. And it is a permanent class approved structural repair.”
Massive money and disruption SPS Technology has carried out NHW repairs since 2003 and has worked on a wide range of projects on all sorts of vessels, including cruise vessels, LNG tankers, ROROs, and bulk carriers. “We can work on anything that floats”, declares Mr Nash. To illustrate, he recalls an FPSO where the side shell hull below the waterline had reduced down to 50% of the original thickness. “In this instance, the options were to either replace the section or add to it from the inside of the vessel. The first option would have required a cofferdam to cut out the section from the inside and bring in the new plate section. That takes massive money and disruption, and you require more people”, explains Mr Nash. “For the second option, you need to prepare the inner surface of the hull and clean it up,
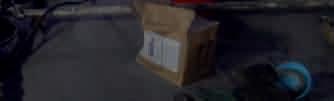
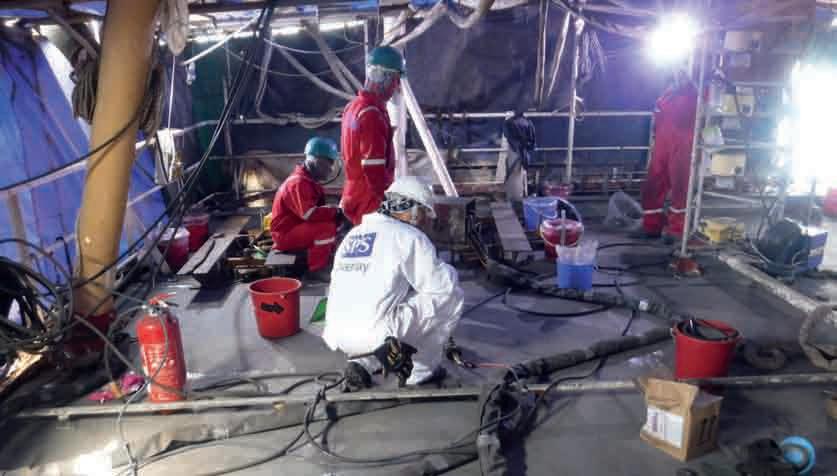
According to SPS Technology a broader understanding of available and proven repair methods could generate millions of dollars in time and cost savings.
SPS Technology offers ‘SPS no hot work’ repairs, which do not affect day-to-day operations of an FPSO.
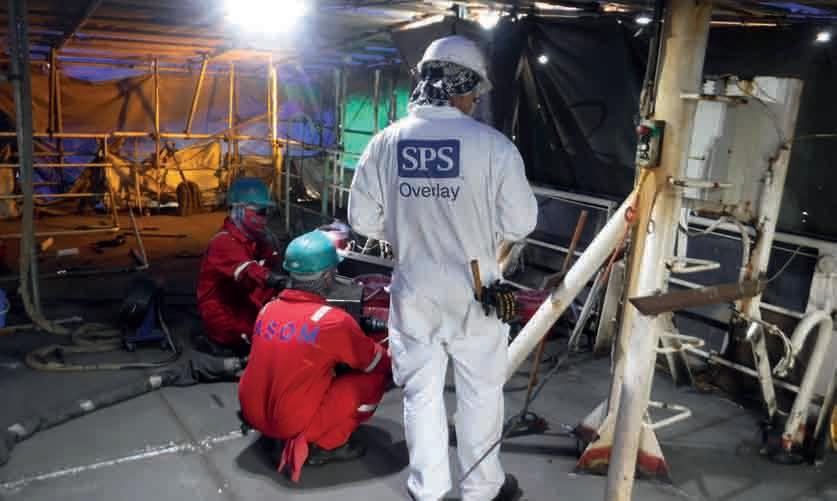
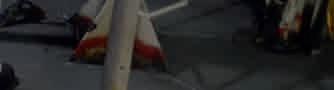
so you can attach a new top plate. The 25mm gap between the new plate and the steel hull is then injected with a polyurethane resin that bonds the new plate to the hull. The new section is now protected by the old hull, by the polyurethane, which is impervious to most substances including sea water and oil, and by the new steel plate. There is no need for the added expense of divers or of shutting down the FPSO completely.” In another instance, SPS Technology’s NHW solution received approval from classification society ABS to carry out repairs on the main deck of an FPSO. Using traditional methods, the cargo tanks with oil would have had to be emptied before any welding or hot work could be done. “With our technology, there was no need to do so. We attached bars to the steel deck with industrial strength adhesive and the new plates were bolted to the bars. The polyurethane was injected. There was no hot work, so the cargo well could remain full and the tanks could stay in operation during the work. That is a massive advantage.”
Best kept secret In these uncertain times, companies need to embrace any solution that can save them time and money, concludes Mr Nash. “Our repairs have prolonged the lifetime of the vessel and have cost considerably less. It really is a game changer. Don’t waste money, especially when there is an equivalent that is as good, if not better.”