
6 minute read
Harnessing aerospace technology
A MODERN WIND SOLUTION FOR SHIPPING
AT THE TIME OF WRITING, THE GLOBAL COVID-19 PANDEMIC HAS THE WORLD’S PEOPLE AND ECONOMY IN ITS GRIP. WITH THE SHORT-TERM IMPACT CAUSING A SIGNIFICANT UPSET IN THE GLOBAL SHIPPING MARKETS, THERE IS A CONSIDERABLE AMOUNT OF SPECULATION AS TO HOW THE GREEN ECONOMY WILL FARE ONCE WE EMERGE AT THE OTHER END OF THIS CRISIS.
ALL IMAGES COURTESY OF AIRSEAS. WORDS BY VINCENT BERNATETS, CEO AND FOUNDER OF AIRSEAS.
However, bearing in mind the long-term implications of a slowdown in managing carbon emissions, the shipping industry shouldn’t take its eye off the 2050 IMO decarbonisation reduction target against the backdrop of COVID-19. Indeed, many commentators are arguing that the recovery from the current crisis must be green. The American Morgan Stanley bank, for example, has stated in a recent report that “there may be some short-term delays in climate policy. But decarbonisation remains an attractive investment theme for the decade ahead, with a green recovery likely.”
Growing potential As the 2050 target looms, many technologies and innovations are coming to the fore to help fleets manage their carbon emissions, spurred on by the broadly successful implementation of the IMO 2020 sulphur cap. Emerging through the debate of future zero-carbon technologies, wind is becoming more and more visible as a viable option to be deployed alongside a future zero-GHG fuel. According to a recent study from the UCL-based commercial advisory service and the Getting to Zero Coalition, a future zero-GHG fuel could be as much as USD 800 per ton, given the level of investment. This means that any fuel saving percentage generated by wind power is going to present a significant return on investment to any future owner.
To indicate the growth in the potential of wind, the International Windship Association has increased its membership
When deployed, the Seawing kite will fly at height of up to 400m above the vessel and generate up to 100t of traction.
nearly tenfold since 2014. Translating this growth into a physical presence, the EU estimates that by 2030, there will be 10,700 wind propulsion installations. Furthermore, the UK Clean Maritime Plan estimates the wind market for shipping will grow to 2.3 billion euros a year by the 2050s.
As wind solutions continue to gather pace and scale, much like other zero-carbon research, innovation will accelerate. This is a vital step to establish wind power as a key element of shipping’s decarbonisation strategy, as the technology to which it leads fulfils certain criteria for viable wind solutions. Firstly, it will need to ensure solutions are safe, working seamlessly alongside the crew to ensure reliability. Secondly, it will need to ensure that wind solutions and hardware are easy to retrofit and work around existing vessel design. Finally, it must ensure that the fuel savings are maximised, therefore generating the return on investment that owners will need.
This is where wind propulsion can learn from other industries. It was this inspiration from other industries, specifically aviation, that contributed to the founding of Airseas, an organisation backed by Airbus to harness advanced aerospace technology to develop a modern wind solution for shipping.
Learning from the flight deck Taking learnings from aviation is nothing new to shipping; for instance, there has

A Seawing kite system installed on an Airbus.
been significant knowledge transfer in terms of safety protocols, as both industries are safety-critical. The importance of safety has also made the aviation industry develop some of the most advanced automation and safety technology. Could it be possible to bring the lessons learned from the flight deck and avionics systems to a wind solution for ships? The reality is closer than most people think.
This reality of aviation-inspired wind solutions is unfolding through the Seawing product developed by Airseas. The Seawing is a 1,000m 2 kite sail system supported by advanced flight control programmes, that when deployed will fly at heights of up to 400m above the vessel and generate up to 100t of traction. The design of the Seawing includes many learnings from aviation. While there are some differences; for example, the parafoil is a flexible material compared to a rigid wing, there are no passengers and slower operating speeds – many principles of aeronautical engineering are at play in the solution’s design. However, the real innovation exchange between aerospace and maritime occurs through digital twinning - the merging of the physical hardware with automation systems underpinned by multiple data streams.
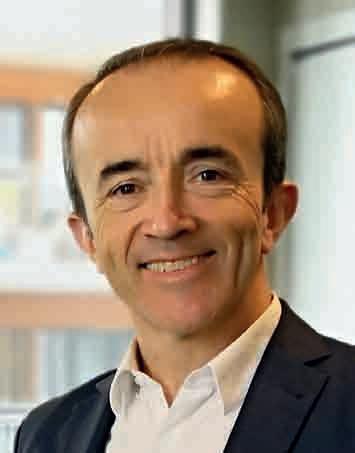
Digital twinning Through digital twinning, the challenge of creating an automated wind solution that maximises wind-generated fuel savings while taking account and reacting to the conditions can be tackled. Changes in sea state, waveform and direction, for example, impact the pitch and roll of the vessel, along with (minor) changes in the wind speed and direction that will need to be accounted for. The sources of these data streams reveal that there are two distinct digital twin applications with the Seawing. The first takes account of inbound meteorological, navigational and seascape data from existing >>
Vincent Bernatets, CEO and founder of Airseas.
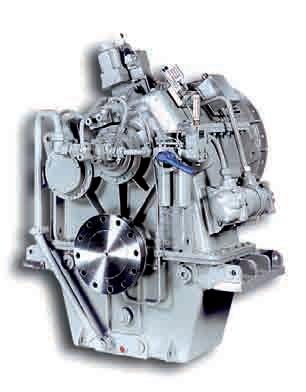
WAF 665 1386 kW at 1800 rpm
REINTJES Gearboxes - the best choice for your vessel!
For over 75 years already, REINTJES Benelux – based in Antwerp – handles sales and services of REINTJES gearboxes and reversing gears for Dutch shipping for short-sea, sea going, dredging, fi shery, inland vessels and luxurious yachts … Our service department is available for all spare parts as well as repairs. Whether it is an inspection or repair, our team of experienced service engineers is always there for you and assures you the reliability and quality REINTJES represents.
REINTJES Benelux BVBA | Luithagen Haven 2 | Unit F | 2030 Antwerpen Phone +32 (0) 3 541 92 33 | info@reintjes.be | www.reintjes-gears.com
To indicate the growth in the potential of wind, the International Windship Association has increased its membership nearly tenfold since 2014.
bridge systems along with sensor data. From analysing this data, informed recommendations can be made to the crew about the optimum time to deploy the Seawing, with the final decision being made by the bridge crew and captain. After the kite has been deployed, sensors contained in a pod mounted on the kite detect minute changes in air pressure, wind speed or direction, resulting in the Seawing automatically making microadjustments in its profile within a 300-millisecond response time. As well as optimising the operation of the kite to maximise fuel-saving, this increases safety. Through its autonomous operation, human input is minimised, reducing the risk of damage caused by human error. This digital twinning model also supports system safety by validating the data gathered in real-time use against virtual models and simulations of the system. If there is no synchronisation between the data in the virtual and real-time model, then something is potentially wrong, and the crew is alerted.
The second digital twin concept within the Seawing is based on the coupling of the ship and the kite and considers all aspects of the operation between the two. By integrating the automation software with routing and navigation software, a route is recommended to the captain that optimises use of the Seawing and maximises fuel savings. Although this is highly dependent on ship type and load, the algorithm will allow it to work well with a wide variety of ships and cargos.
The digital twin concepts found on the Seawing go a long way in facing the expectations that the shipping industry will have for modern and future wind solutions. We believe that automation technology will be a core pillar in the future of wind, through its role in the optimisation of fuel saving and in ensuring safe and reliable operation alongside the crew.
To help develop wind solutions further, an approach could be to look at the technology used in other sectors, as we have demonstrated with the Seawing and the aviation industry. Through this shared learning, wind propulsion can be developed and perfected further to help shipping on the road to decarbonisation.