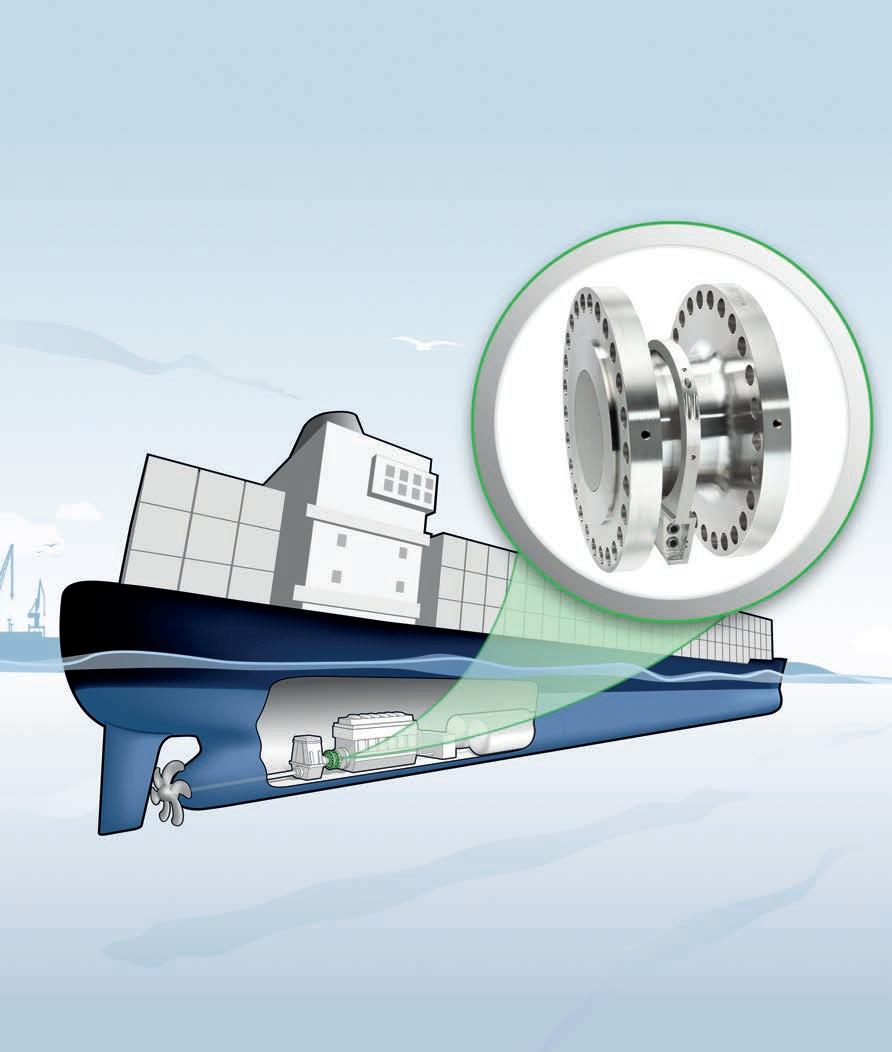
4 minute read
Electric motor testing in marine propulsion systems
The implementation of advanced electric motor testing can enable a huge increase in effciency and smaller drivetrain designs for a range of marine applications.
IN THESE TIMES OF RISING FUEL PRICES AND STRICTER GUIDELINES FOR EMISSION REDUCTION, ELECTRIC DRIVETRAINS ARE BECOMING THE FUTURE IN MARINE APPLICATIONS.
WORDS BY RENE BASTIAANSSEN, BUSINESS DEVELOPMENT MANAGER AT HBK.
As a result of this, a variety of electric drives and drive variants are coming onto the market. Increasing quanttes and high demands in quality and reliability call for advanced testng methods, monitoring systems and test bench technology. Questons that arise include: How can motor testng be simplifed? How can system propertes such as torque ripple and NVH be measured appropriately? And how can dynamic power measurement provide satsfying results to improve efciency?
The implementaton of advanced electric motor testng will enable a huge increase in efciency and smaller drivetrain designs for a range of marine applicatons. Contnuous development of electric motor technologies is helping the marine industry’s transiton to new alternatve energy solutons. Electric motor testng is not new, but can be quite complicated, especially when testng marine propulsion systems that combine high system complexity, multple drives, and voltages over 1,000V.
Testing
Traditonal testng methods and equipment were primarily designed for statc (steadystate) testng of straightorward three-phase drivelines. Testng complex drive train systems in the marine industry with a high voltage requires a lot more than this. Not only a huge amount of data must be synchronously and contnuously recorded with a high resoluton and at high sample rates, but the datainverter voltage, current, torque, speed, vibraton, and noise - must also be analysed in real tme to be able to use the results to monitor and control the test itself.
NVH in electric drivetrains
In the drivetrain, the inverter creates AC power with high switching frequencies. The resultng currents create switching magnetc felds, which not only creates the desired torque, but also cyclic torque fuctuatons where frequency and amplitude are proportonal to the number of phases and RPM. These fuctuatons have various causes, depending on the motor structure and control strategy. ln a permanent magnet motor, the magnets interact with the stator, causing what is called cogging torque. ln the switched reluctance-type motors it is the pulsed current that induces the hard torque pulses, while in the inducton-type machine magnetsm is induced in the rotor interactng with the stator magnets. The motor itself acts like a flter due to its inerta and so it removes some of this content, but current ripple and torque ripple will stll result in noise and vibraton, which is not desirable for end users.
Actions required
Torque fuctuatons or even torque reversals, can cause efects like gear chater in gearboxes, which may lead to damage or reduce the life of gearboxes connected in the drivetrain. Torsional vibratons can also cause fatgue in driveshafs and other drive >>
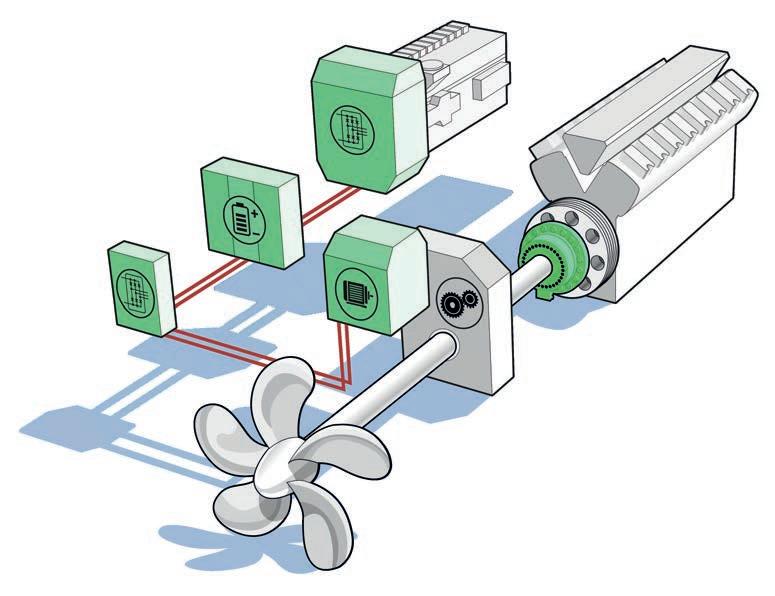
The eDrive Technology is a solution that meets the testing demands for today’s complex electric and hybrid powertrains.
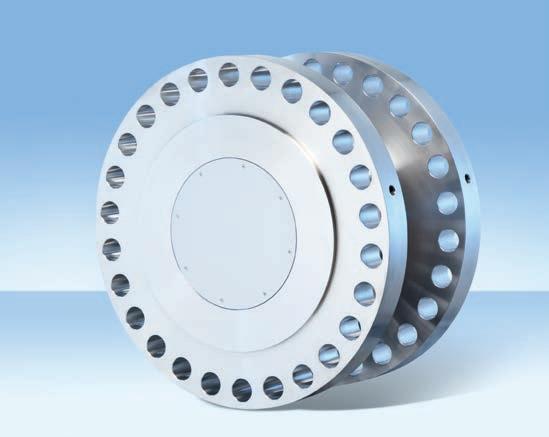
The T40MAR torque fange has been especially developed for use in ship drives. The equipment is certifed according to international shipping standards.
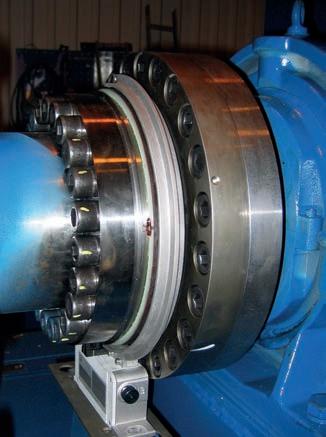
The eDrive system
The eDrive system measures the mechanical parameters (torque, engine speed, temperature) and electrical parameters (current and voltage) of an electric engine. With the associated sofware, the soluton consttutes a powerful test and analysis system for electric and hybrid drive systems. components. If not on a level where the vibratons cause damage or wear, they can stll cause issues regarding the comfort of passengers. To analyse and improve this negatve behaviour, actons are required. The ideal soluton designed to efciently undertake all these tasks is the eDrive system of HBM, which is a HBK company.
Complete analysis solution
With the eDrive system, HBM is a single source supplier for sensors, the data acquisiton system, and the sofware. The data acquisiton system is equipped with the real-tme computng functons of a power analyser. All recorded raw data can later be analysed in the integral system or be shared with third-party solutons or systems. Designed for electrifcaton, unlike other power analysers, HBM’s eDrive system not only ofers measured data, but also in-depth analysis. For machines with more than three phases, the data are available in seconds. The eDrive test equipment shows all relevant data in high resoluton during the testng process, such as mechanical and electrical power. It enables the user to achieve the best setng for the motor, which means beter efciency, higher maximum power, and optmised handling.
i. hbkworld.com
HBM’s eDrive system not only offers measured data, but also in-depth analysis.
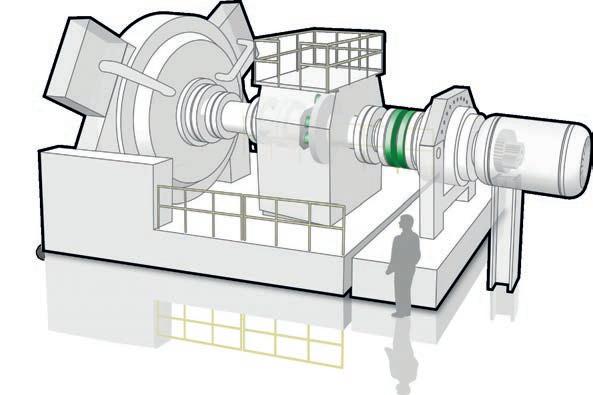