
3 minute read
Flooring Horror Stories — Don’t Let Them Happen to You
WAGNER METERS
Jason Spangler Wagner Meters’ Flooring Sales Manager Jason Spangler has more than 25 years’ experience in sales and sales management across a broad spectrum of industries. He has successfully launched a variety of products to the market, including the original Rapid RH® concrete moisture test. Jason, who received an MBA from West Texas A&M University in November 2018, has extensive industry involvement, including the National Wood Flooring Association (NWFA), the International Certified Flooring Installers Association (CFI), and is Vice Chairman of Associations for The Flooring Contractors Association (FCICA). Call Wagner Meters today at (844) 533-9100 and ask for Jason or visit www.wagnermeters.com
Advertisement
Flooring Horror Stories — Don’t Let Them Happen to You
Stop me if you’ve heard this one before — a flooring crew installs a gorgeous nail-down hardwood floor and within a short amount of time… nearly every plank shows signs of cupping.
How could it all go wrong so quickly? The crew built up a plywood subfloor system on the concrete slab utilizing industry-recommended methods and then installed the hardwood flooring.
Well, the first mistake was that the crew didn’t evaluate the moisture condition of the subfloor. After they started ripping up the newly installed hardwood floor, they learned the concrete and plywood had moisture levels that were way too high!
Perhaps the crew also forgot to let the hardwood acclimate to the environment before installing it. If they did forget, they hit a double-whammy that guarantees moisture-related flooring failure!
Don’t Be That Flooring Crew
Everyone swaps jobsite stories, but you don’t want to be the one telling this kind of flooring horror story. You want to be the flooring professional who tells stories about how smoothly you handled a client pushing to install the hardwood flooring quickly when you knew the moisture condition of the concrete subfloor wasn’t conducive for a successful flooring installation.
Let’s face it — most hardwood flooring horror stories come down to moisture.
Hardwood flooring moisture issues might become apparent quickly, or they may take months. But in most cases, the underlying cause of the moisture failure was present during the installation. Typically, one of a few mistakes leads to moisture-related problems:
1. The wood didn’t get enough time to acclimate to the installation location. 2. Nobody checked the subfloor for moisture issues or addressed any moisture issues that were found. 3. The design of the installation didn’t account for the risks of water coming from external sources.
Quantifying the Costs of Each Moisture Horror Story
A hardwood floor can get deformed from both too much or too little moisture. Cupping and swelling show up when the floor absorbs too much moisture. On the other hand, the boards will crack and shrink if dry air sucks too much moisture out of them because the boards were wetter than the target moisture content for the area.
The moisture damage also affects your schedule and your bottom line. When moisture damage appears in the hardwood floor, you now have to invest time and team effort to investigate and come up with a solution. That’s unpaid time. And if you scheduled another job during that time, you’ll have a waiting, frustrated customer.
If you take the steps necessary to manage moisture at the start of the project, before installing the hardwood floor, your project plan can account for the possibility that extra drying or acclimation time might be needed. When you know that going in, you can better plan for contingencies, like using that time to start on the next job.
When you wait until moisture damage appears, you not only have to wait for extra drying time—which wasn’t on your schedule—but you might also have the additional time and costs of ripping up the hardwood floor and reinstalling it.
That’s a costly hit on your wallet, your time management, and your reputation.
Make Moisture Measurement a Part of Your Standard Worklist
One thing that’s so frustrating about moisture horror stories is how easily they could be avoided. Build time into your standard work plan to evaluate the moisture condition of the subfloor and underlayment (assuming it’s a material that holds moisture). Schedule delivery of the hardwood with enough time for it to acclimate to its service surroundings. Continued on page 28 If you take the steps necessary to manage moisture at the start of the project, before installing the hardwood floor, your project plan can account for the possibility that extra drying or acclimation time might be needed.
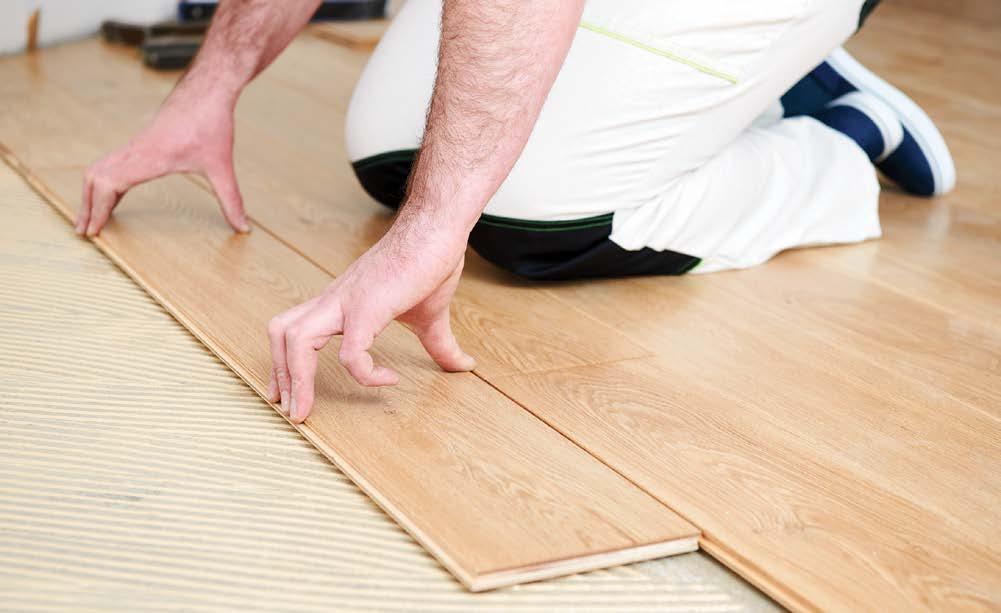
Don’t let your beautiful hardwood flooring project become a horror story! Always pay attention to moisture.