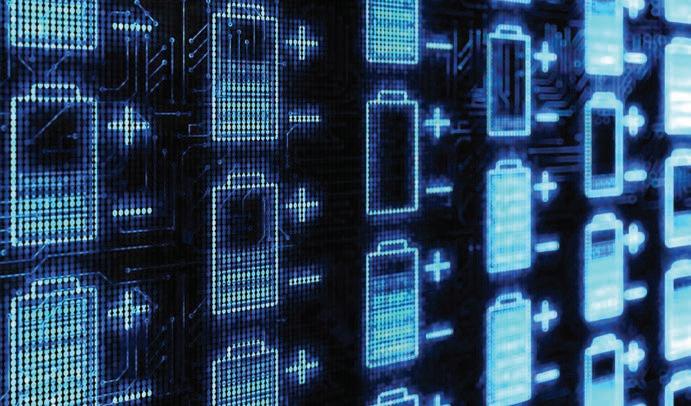
6 minute read
SAFETY
Risks Associated with ESS are Preventable
Battery technology and energy storage solutions (ESS) are set to play a vital role in shipping’s journey towards decarbonization. The technology not only reduces GHG emissions, but can help enhance performance in both hybrid and electric vessels by reducing the need for maintenance, providing additional functionalities like backup power, and reducing the need to rely on other emissions abatement technology.
Advertisement
This expansion of battery use in marine energy has however seen the emergence of ESS-related incidents and dangers. This is unacceptable, and importantly, avoidable— and it indicates that competition on cost is potentially risking a race to that threatens the safety of batteries.
Despite this, the risks and dangers surrounding ESS use are preventable, with the right measures and information in place. That is, if they are properly and consistently deployed.
Understanding the Risks
Given the relative novelty of ESS technology, there is a greater need for thorough and consistent safety measures and more so, increased transparency of testing and testing standards from battery manufacturers.
One of the most serious risks for ESS is thermal runaway. Thermal runaway can occur when battery cells are subjected to mechanical damage, internal short, operating over or under the correct voltage or internal temperature. In these situations, heat may be generated within the lithiumion cells, which results in the temperature increasing until the cell vents toxic and flammable gasses.
If ignition occurs, these gases can create an unpredictable fire that can be very difficult to extinguish. In high enough concentrations, and in an unvented room, gases are also capable of creating very large explosions as the fire spreads from one cell to another. The propagation of fires in cells is, importantly, entirely preventable if battery manufacturers exercise the correct precautions.
Thermal runaway can incur serious, even fatal risks. Put into context, a fire on board a battery-powered vessel in October 2019 saw an explosion lead to a dangerous battery fire, due to thermal runaway. Adding to the complication, the vessel was out at sea at the time of the fire. This, combined with the fact that many battery-fueled vessels are passenger vessels, makes controlling the situation all the more challenging — and the need for built-in, pre-existing measures all the more necessary.
Universal Solution, Universal Challenge
One of the benefits of energy storage solutions is that they can be deployed in a wide range of energy and vessel types. Implemented to optimize or replace diesel in marine, grid and heavy industrial applications—and depending on the vessel size, type and ultimate purpose—battery technology can be utilized as a part or full solution.
Of course, this universality and convenience presents the challenge of how to ensure that safety in battery technology remains a priority throughout development, implementation, and ongoing use?
For one, safety systems in marine batteries should be designed holistically. This ensures that every aspect of the battery is as safe as possible, and more so that safety systems are designed into the core of the ESS, rather than as an add-on or an extra. Battery safety is maximized if all systems on board are designed to work together from inception—not as an after-thought.
Systems such as integrated water-cooling provides an effective way of stopping a damaged cell from entering thermal runaway. Simply put, it cools the cell faster than it can heat up. When this water-cooling is embedded in the heart of the design and manufacture of the cell, it can cool a cell or bank of cells faster than they heat up in a thermal runaway situation. And, as with the Arizona 2019 fire, metal barriers between cells can help prevent overheated, overcharged, or damaged cells from propagating the next cell. Otherwise known as ‘cascading thermal runaway.’
With the exposure of toxic and flammable gases detrimental to crew health, effective ventilation systems are those that vent all gases to the exterior of the battery room, reducing the risk of explosion, consequently helping to protect the crew, vessel, and of course, first responders.
What is the Key to Enhanced Safety?
The introduction of new and stringent safety standards—such as DNV’s new 2020 class rules for commercial vessel batteries— indicates growing awareness of the need to prioritize safety and mitigate the risk of ESS. However, there is a significant proportion of enhancing safety that relies on manufacturers’ accountability in terms of transparency towards customers, integrating preventative measures, and establishing the need for greater safety in the first place.
Battery power is ready to unlock a range of efficiencies in a lower carbon future—but this cannot come at the cost of safety. Both in terms of implementation and maintenance, high standards of ESS safety are entirely achievable for owners and operators.
IAN ROBINSON Director of Engineering ZeroNorth
45th ANNUAL INTERFERRY CONFERENCE
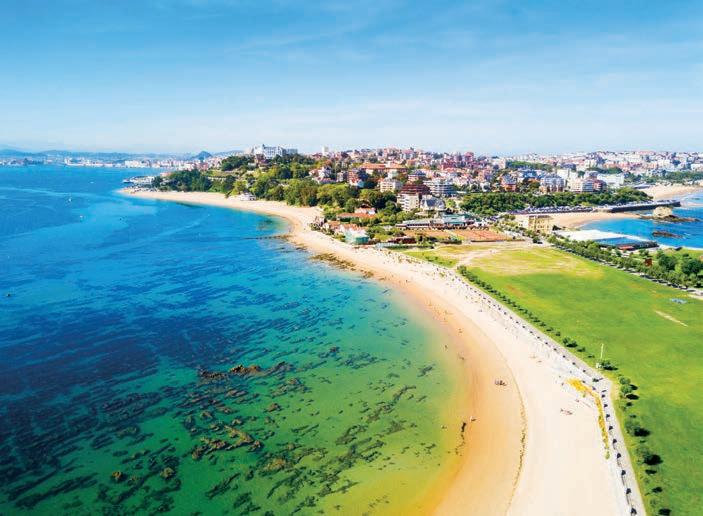
PLATINUM SPONSORS
SANTANDER, SPAIN • OCTOBER 2-6, 2021 • REGISTRATION IS OPEN!
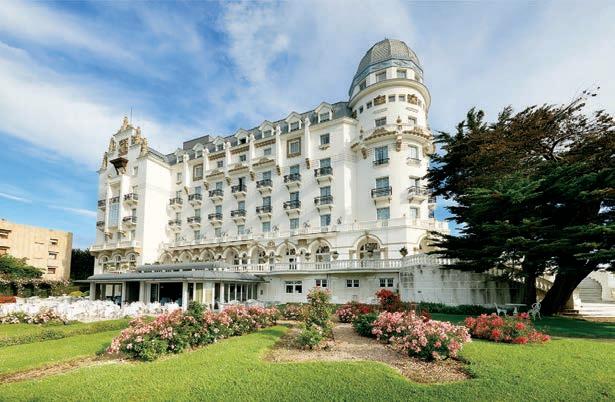
Eurostars Real Hotel
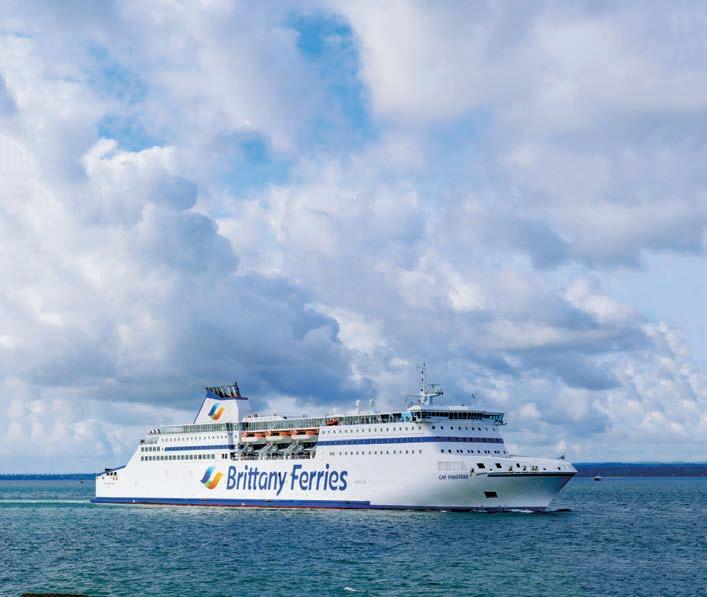
PLATINUM PRESIDENT’S
THE FUTURE IS FERRIES
Registration is open for the 45th Annual Interferry Conference in Santander, Spain. In addition to the popular CEO roundtables, the conference will feature sessions on: solutions for GHG emissions reductions; innovative ship and shore design technologies; ferry safety and safety systems; attracting tomorrow’s customers; and supply chain logistics. Our program of networking and social events includes a Welcome Reception at the Palacio de la Magdalena, a Networking Reception aboard Brittany Ferries’ Pont-Aven, and the Farewell Dinner at the Hotel Real. The Technical Tour features visits to Astander Shipyard and ERZIA Santander Teleport. The conference website has all the information you’ll need about this year’s conference including: registration; accommodations; speakers and sessions; networking and social events; activities; and sponsorship. Check the website often and watch our social media accounts for updates.
SPEAKERS PROGRAM
OUR SPONSORS
Interferry’s Global Ferry Market Study Seagliders – Battery Powered Flying Ferries Spanish Ferry Market & Shortsea Shipping NYC Ferry Project The EU Ferry Market & Prospects for Recovery Sustainable Ferries & High Speed Ferries Customers Acquisition & Experience IP/Data Protection Issues & Cybercrime Mitigation GHG Regulatory Update Zero Emission Solutions – Terminals & Ships Responsible Cabin Designs Ferry Connectivity Study Human Factors Integration in Systems Design CEO Panels – Operators
SILVER GOLD
We take the heat, so you don’t have to.
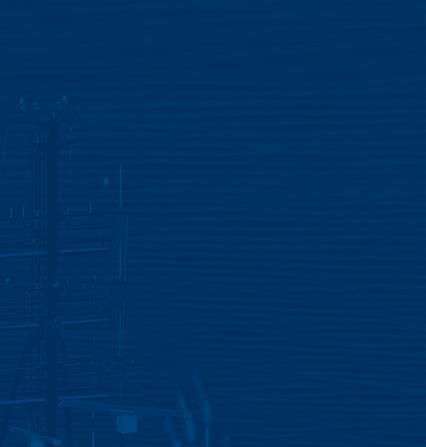
Cool. Because you need it.
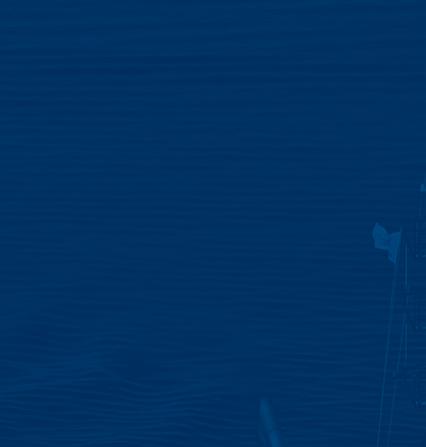
We deliver cool based on your reality. So no matter where you operate, hot days and heavy loads will never slow you down.
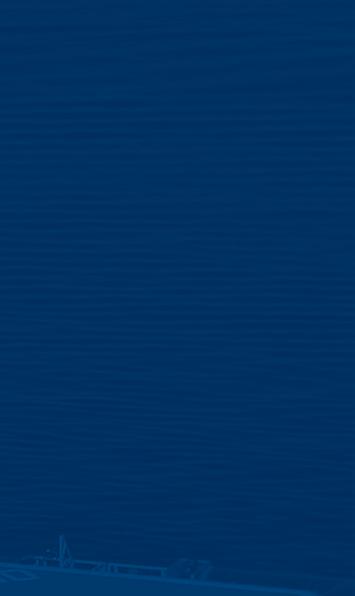
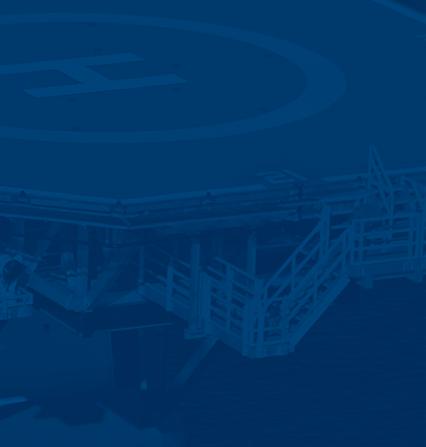
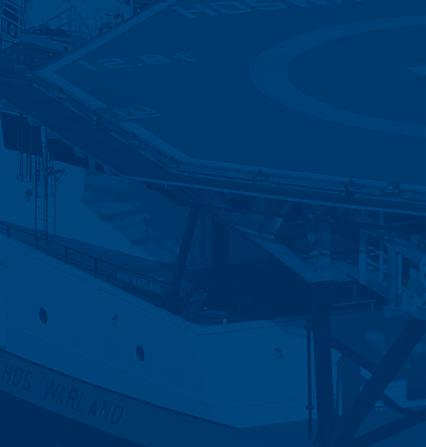
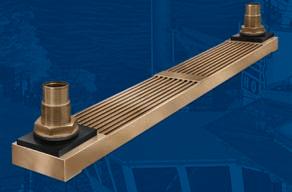

GRIDCOOLER® Keel Cooler
• One Piece Head Design maintains greater structural integrity. • Higher Silver Content Braze Joints resist fatigue and maintain the strength of surrounding material. • Better Penetration at Braze Joints places more braze material with less heat, making joints stronger. • 2-Year Warranty on Copper Nickel GRIDCOOLER Keel Coolers: Industry-leading design, craftsmanship and materials create industry-leading products. • 70 Years of Experience with Fully Assembled
Packaged Keel Coolers: Our focus is and always has been heat exchangers.
WEKA Boxcooler®
• Over 20 Years of Experience with Copper Nickel Boxcoolers o ering longer product life cycle than standard coated tube units. • Manufactured in the USA and The Netherlands: provides the greatest product availability. • Weka Guard and Protector eliminate the need for bulky and costly copper sacrificial anodes.
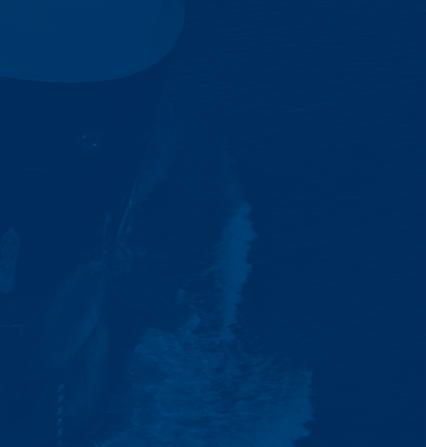
fernstrum.com | 1.906.863.5553 | sales@fernstrum.com | ISO 9001:2015
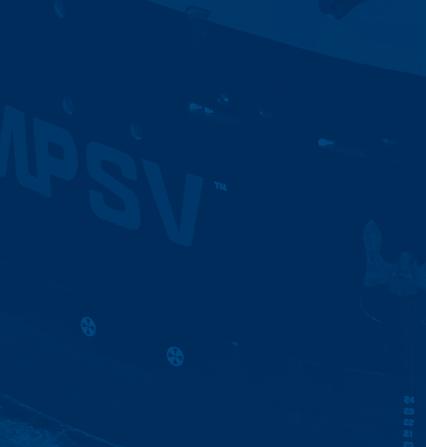
