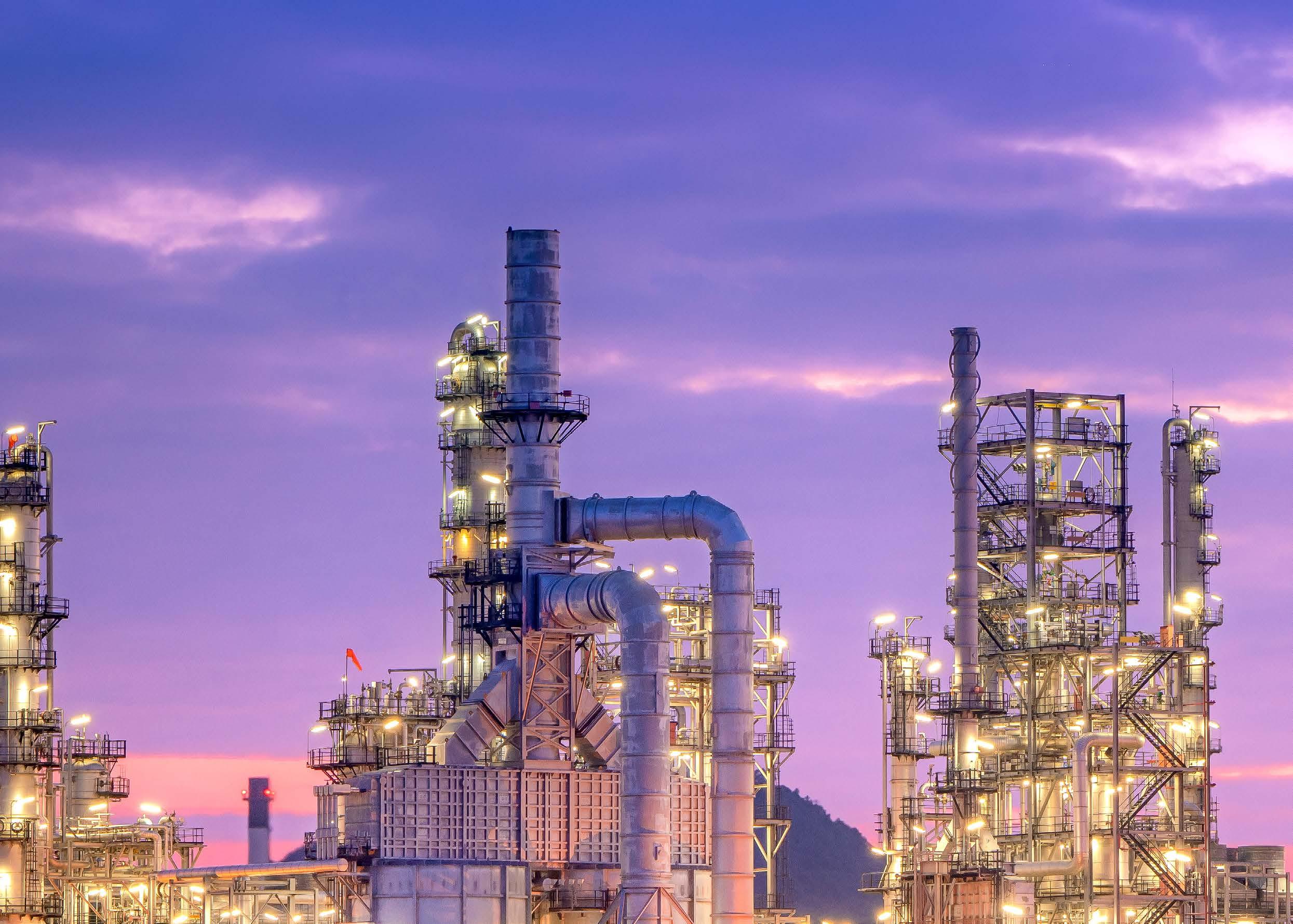
29 minute read
Feature - Materials Engineering for Australia’s Mining, Oil and Gas Sector
Mining is Australia’s largest sector. According to the Australia Bureau of Statistics, it accounts for more than 10% of the nation’s economy. It is particularly crucial for securing Australia’s economic future and prosperity. Together, mining, oil and gas production reached $221.2 billion over the 2019–2020 reporting period, which positions Australia as a strong domestic and international economy. Minerals have been crucial to Australia’s long-term economic future for some time. From the early gold rushes to the mining boom—the sector is underpinned by high demand for commodities in industrialising economies like India and China.
In fact, Australia is the world’s largest exporter of black coal, iron ore, lead, zinc, and alumina. It is also the world’s second largest exporter of uranium. This positions Australia as one of the globe’s top five producers of minerals commodities overall.
Western Australia and Queensland are the cornerstones of Australia’s mining sector, as the most resource-rich states. The sector employs nearly over 240,000 Australians—led by coal, iron ore, and gold mining personnel. In fact, the sector is on an upwards trend. Workers grew by 4.9% at the 2019–2020 Australian Census reporting period. This was driven by increased demand and ongoing supply chain issues. The Chief Executive of the Minerals Council of Australia, Tania Constable said Australia’s gross value add from mining was 11.1% in 2019–2020, when compared to just 4.6% between 1999–2000.
“The Australian minerals industry is a major contributor to investment, highwage jobs, exports and government revenues in Australia,” she said. Even throughout the ongoing COVID-19 pandemic, the sector has pivoted towards a stable and profitable future. The sector was identified as an ‘essential service’ in March 2020, which allowed it to continue working relatively unscathed in light of nationwide lockdowns. Australia’s mines are relatively isolated away from the major capital cities, and ongoing exploration allowed the sector to guarantee confidence in its long-term ambitions. “The mining industry has been a pillar
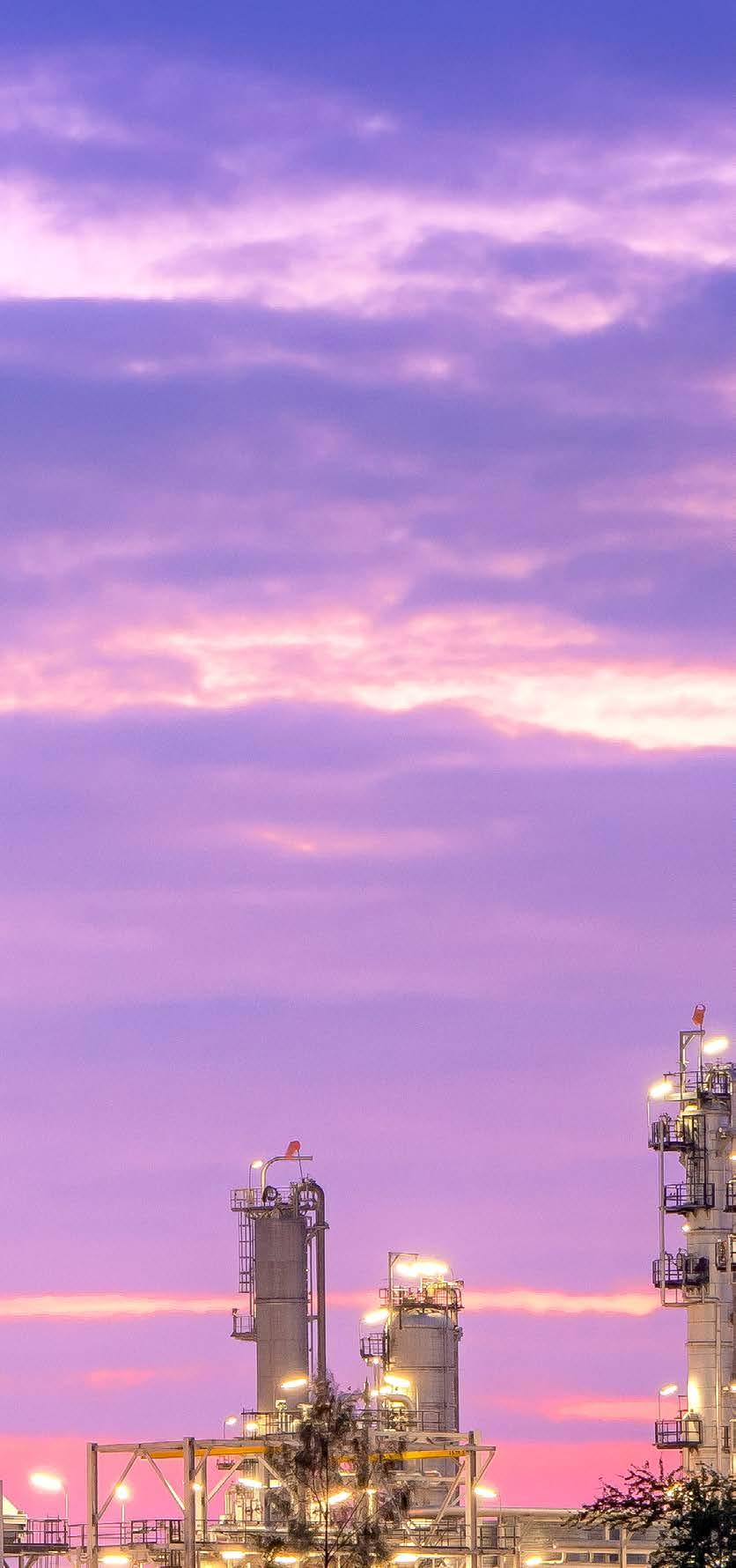
of stability,” Constable said. “Growth in mining industry GDP has allowed it to hire new workers while adhering to strict health and safety protocols that have protected people in their workplaces and communities around Australia,” she explained. However, the sector continues to face an unprecedented level of challenges. From cost-effective production, technology developments, and environmental and sustainable challenges. Ms Constable said the sector requires a strong pipeline and cross-sector support to ensure its ongoing prosperity. “To ensure mining continues to drive Australia’s post-COVID economic recovery governments should support the industry with faster project approvals, competitive tax rates, coinvestment in modern skills programs and more flexible workplaces,” she said. The Minerals Council of Australia has a balanced list of projects and policy objectives, including a commitment to reliable and affordable energy, and putting Australia on a pathway to a net-zero emissions future by 2050. The company’s members have previously endorsed the Climate Action Plan, which relies on research in materials science to better understand technologies and practices that will drive decarbonisation across the sector.
The plan recognises the major technological, economic and social challenges of reducing emissions, and believes Australia’s minerals sector must play its part. “The technology-led transformation required cannot occur without the minerals and raw materials provided by the Australian minerals sector,” Constable said.
However, these developments are not possible without the dedicated support and investment in technology from member companies and research partners.
Australia’s mining sector extracts and explores minerals that are linked to a variety of services, which are crucial to Australia’s day-to-day life. These services crucially include electricity and gas supply. However, the sector is also well-positioned to become a core player in modern technologies, like the production of electric vehicles.
Materials scientists are collaborating with industry personnel to gain a better picture of the sector, and identify opportunities to transition to a greener future.
Sustainable Materials Institute
Researchers are the University of Queensland’s Sustainable Minerals Institute (SMI) recently developed bioengineering technology that could rehabilitate mine waste back to useful soil. trials at two Queensland refineries in partnership with Rio Tinto and Queensland Alumina Limited (QAL). Professor Longbin Huang works within SMI, and said the process would transform the bauxite residue, which is commonly known as ‘red mud’ into a soil-like material that is capable of hosting plant life. “The team has secured more than $3 million in funding from Rio Tinto and QAL that will allow us to trial the technology at an operational scale at two red mud sites.”
“This project demonstrates how transformative industry-academia partnerships can be—Rio Tinto and QAL have supported the research for the past eight years, from proof of concept to full field trials,” Professor Huang said. There are more than four billion tonnes of red mud stored in dams around the world. However, Australia is the second largest producer of the mineral waste by-product of alumina refining, which create a research gap for the sector.
“The process we have developed is gamechanging as it involves ecoengineering the mineral and organic constituents of the red mud into material that is more hospitable to plant life.” “It is a more sustainable and costeffective way of managing red mud compared to traditional methods, which require companies to excavate and transport metres of topsoil from other locations to cover thousands of hectares of waste,” Professor Huang explained. The University of Queensland is a trailblazer in materials science and innovation. Together, it has partnered with several end-users to minimise their environmental footprint. The university boasts a $440 million environmental strategy, which runs across five years. The strategy aligns with the United Nations’ Sustainable Development Goals and performance measurement systems to meet its objectives.
Institute for Frontier Materials
Deakin University’s Institute for Frontier Materials (IFM) is a multicultural, vibrant and world-class
research facility. IFM’s role is to bridge the gap between materials scientists and end-users in the mining, oil and gas space. Professor Matthew Barnett is the Director of IFM, who believes in the importance of materials science.
“Technological advance springs often from a breakthrough in materials science,” he said. At IFM, researchers work through complex challenges, and develop solutions based on profitability, energy efficiency, competitiveness and extended product life. For example, IFM recently established a $3.9 million partnership with CSIRO, Callidus, and several mining companies to cut costs and emissions based on extending component life. The project links theory to practice by developing a novel technique to double component life, improve the efficiency of machinery, and save millions of dollars in lost production time. In addition, four of Deakin University’s research institutes, including IFM, recently joined Science and Technology Australia (STA). The partnership strengthens IFM’s research networks and shares its knowledge and expertise with a broader range of key stakeholders. “This partnership will enable us to build on our ongoing successes in STEM that have contributed to Australia’s science and technology capabilities,” said Professor Julie Owens, who is the Deputy ViceChancellor Research Alfred Deakin.
“From pioneering space and defence technologies to innovative mental health solutions, we look forward to sharing our expertise across STA’s networks,” she explained. The partnership opens the door for 90,000 STEM professionals to work together through STA. “We are excited to partner with STA who also will provide key opportunities to train and upskill Deakin researchers in policy engagement and communication, and to help us continue to forge valuable research networks and collaborations across the sector,” Professor Owens said. IFM also supports the next generation of students and research trailblazers. Over 30 PhD students graduate from IFM annually, and over 80 postdoctoral researchers are gainingrealworld knowledge at any given time. Together, IFM generates $16.5 million in research outcomes annually.
Surface Engineering for Advanced Materials
The Australian Research Council’s (ARC) Industrial Transformation Training Centre in Surface Engineering for Advanced Materials (SEAM) is the nation’s leading research and development hub. SEAM’s key focus is on applied research with real-world outcomes. The hub seeks to inspire and nurture the next generation of industrial innovation leaders.
The centre aspires to provide an excellent environment for carrying out research, and exploring projects with industry, government and other likeminded organisations. Specifically, the centre’s key research theme of thick coatings manufactured by laser and thermal spray technologies are crucial for wider use in heavy industries, mining and transportation. This research undertaking is a gamechanger for the repair and remanufacturing of components that drive the mining, oil and gas sectors.
Thermal spray coatings are widely known for their strength in the face of corrosion, conductivity and performance. But SEAM researchers are investigating the coating process from a holistic perspective to gather information about its materials and applications. A range of new coatings will be developed for partners within the sector and trialled to determine the best performance in a range of operational environments. In addition, SEAM targets early career researchers to offer highstandards of training in an industrial context to undertake ambitious research outcomes.
This research is tied to industry needs, which contributes to commercial benefits for industry.
Efficient Beneficiation of Materials
Similarly, the ARC boasts a Centre of Excellence for the recovery and concentration of high metallurgical particles. The process is known as beneficiation, where researchers are focussing on new engineered forms of synthetic polymers and engineered biopolymers. This process of using polymers to collect minerals is relatively new. However, researchers are designing a series of mineral processing chemical that will enhance the recovery and performance of valuable materials. In all, this will grant industry with a new method of treating waste materials, increase performance, and allow for the production of costeffective chemicals in mining.
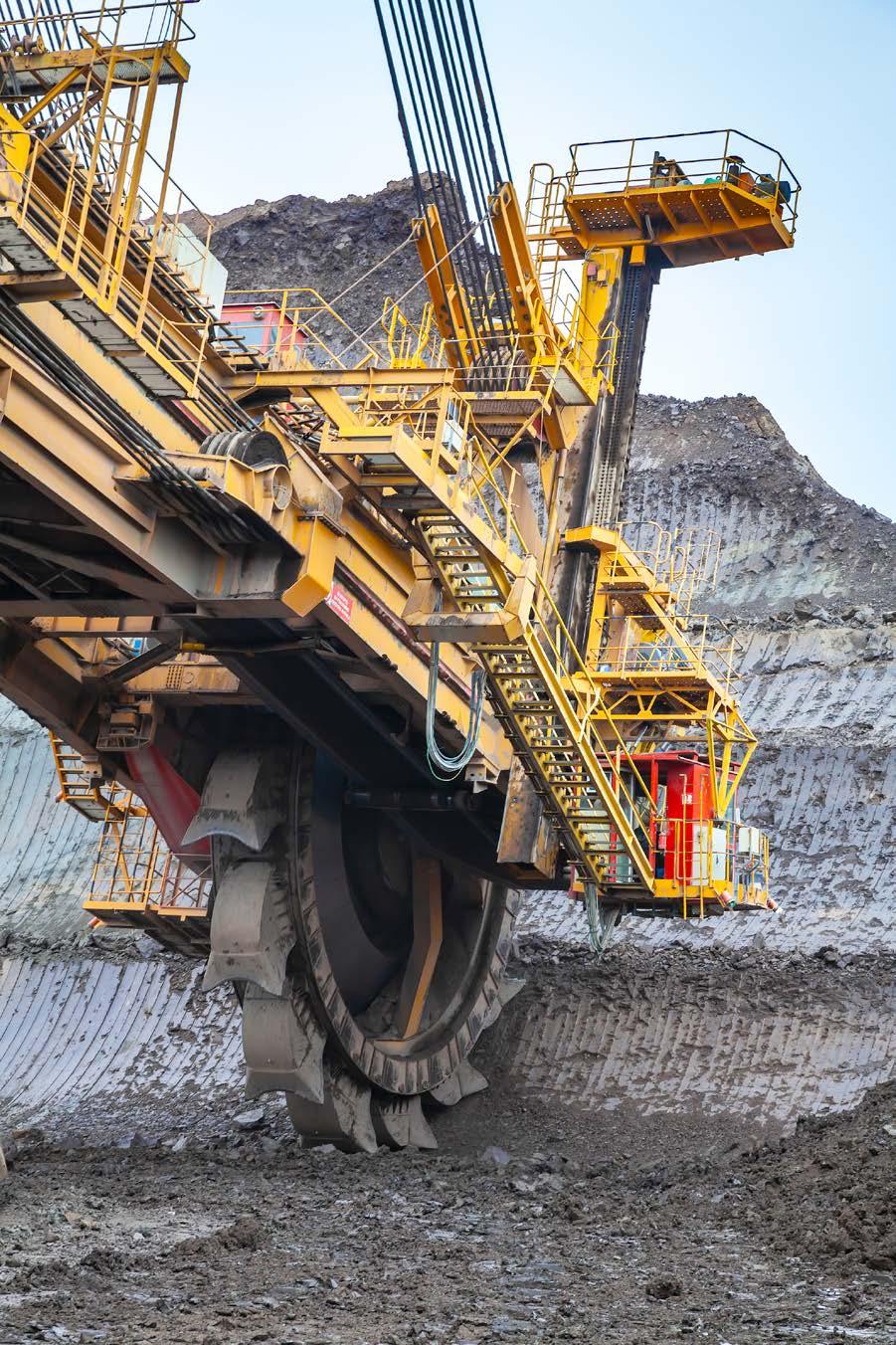
The ARC Enabling Eco-Efficient Beneficiation of Mineral has its eyes on 2050 and beyond, where the demand for minerals will outstrip supply. The research consists of two subprograms: • improving selectivity of valuable mineral recovery • producing easily dewatered waste mineral streams.
Together, the work will focus on macromolecules for targeted adsorption.
Materials Australia Members at The Forefront of Innovation
Industry is at the forefront of Australia’s mining, oil and gas sector. Materials Australia members are leading the way in heat treatment and laser cladding services that help to protect heavy duty industrial equipment. Mining equipment faces a variety of pressures and environments, these include high and low temperatures; wet and dry environments; and corrosive and abrasive hydrocarbons. As such, Materials Australia members work to extend their service life, and incorporate innovative technologies in their daily operations for a sustainable future.
RCR Mining Technologies
RCR Mining Technologies is a market leader in the manufacture and design of materials handling solutions, which are tailored for rail and ore wagons. The company was founded in 1979, and acquired by NRW Holdings 2019. Since then, the company has successfully navigated through the COVID-19 pandemic to deliver highend mining technologies to local and international markets.
RCR Mining Technologies offers advanced heat treatment solutions, including interactive workshop and site services. It boasts furnace facilities in Western Australia and Victoria to cover large industrial heat treatments, including dry outs; stress relief; normalising; and solutionising. The company’s Welshpool facility in Western Australia, is one of the most advanced heat treatment plants in Australia. It boasts controlled an atmosphere and quenching furnace, which are used for hardening processes. It also houses the largest permanent stress relieving furnace in Australia. Together, this allows the company to take on complex projects, and meet challenges across the broader sector.
Westate Mining Supplies
Likewise, Westate Mining Supplies was born in 2004, when Mike Ledger sought to fill a gap in the marketplace. Mr Ledger brings 35 years’ experience in the mining industry to offer unique design and manufacturing solutions to site specific challenges. The company specialises in earthmover rim technologies, which should be crack tested after 10,000 hours. Mr Ledger’s team offers wheel rim tracking and management, nondestructive testing, and replacements and repairs. The repairs meet strict Australian Standards, and use high-quality products to avoid future catastrophic failures and production shutdown. In addition, the company meets clients’ strict time constraints and offers prompt service delivery. It also delivers industry-specific products that are uniquely designed to lower workplace injury rates.
Enduraclad
Enduraclad International is another example of an Australian company that understands the extremities that face the mining, oil and gas sector. The company offers an impressive feat of services including metallic lining products, advanced ceramic products, and hard facing. For example, the wear plate technologies offer unmatched results for large mining corporations like BHP and Rio Tinto. This makes Enduraclad International one of the largest suppliers for metallic wear products to Australia’s mining sector. The company also has a keen focus on sustainable practices for the future. As such, the company invests 10% of all funds into research and development, which paves the way for ongoing improvements on existing products.
Soto
Soto is another Australian company that is a pioneer in the mining sector, with automated processes for increased energy efficiency. The company is positioning itself as a gamechanger in the renewable energy space, which accounts for around 24% of Australia’s electricity. In 2019, $4.3 billion was invested in renewable energy projects across the nation. But these solutions require advanced engineering and equipment. Therefore, Soto engineers use their creative flare and expertise to design, manufacture and refine critical infrastructure and technology for a new era of energy generation. For example, the Soto method of company extensive analysis and modelling was used for an inspection of Illawarra Coal’s rill tower and conveyor at its Dendrobium site. The 128m high tower had limited access, but Soto used virtual reality systems and a video drone to unlock a close-up inspection from the safety of the ground. The Soto AeroCam allowed the team to conduct the audit in one day, which saved time and a complete shutdown of the plant.
HMG
HMG’s manufacturing capabilities in Brisbane are providing increased capacity for Australia’s mining, oil and gas sector. The company has a vast network of industry partners—like BHP; Caterpillar; Hitachi; Glencore; and Komatsu—who operate in challenging environments, and connects them with engineering solutions. HMG offers full fabrication and welding services; deep hole boring and drilling; milling machinery; blasting; stripping; inspection; and surface finishing. These services are operated from HMG’s state-of-the-art 4,000m2 operating shop in Queensland. The company is best known for its hydraulic cylinder remanufacturing, which delivers enhanced operations for the sector.
Improving Component Life for Minerals Processing
Source: Sally Wood
Australia’s mining sector is crucial for powering the nation’s economy. The sector comprises coal and iron ore mining; oil and gas extraction; metal ore operations; non-metallic minerals; and exploration of other mining services.
In all, the sector generated around $221.2 billion over 2019–2020 reporting period. In fact, iron ore, goal and natural gas are Australia’s top three exports—with rapid growth for securing the nation’s economic future. The sector is responsible for powering the lives of all Australians. From busy city offices to rural and regional properties—mining, oil and gas remains Australia’s single largest sector. But the sector relies on ongoing advancements in technology and research to ensure that it meets local demand, and remains internationally competitive. As such, researchers and industry alike are working together to propel Australia’s mining, oil and gas sector into the future. These developments include cost-effective technologies that avoid complete network shutdowns; are weather and corrosion resistant, and maintain a strong environmental focus.
Linking Theory to Practice with Global Partnerships
The Institute for Frontier Materials (IFM), based at Deakin University in Melbourne, is a trailblazer in this space. The research body delivered $15.4 million in research income during 2020, and was featured in over 420 international research papers. This is in stark contrast to other university-based research institutes, which have been battered by the ongoing pandemic. IFM has two fundamental goals, which form part of its mission: • Re-design materials for a circular economy • Impart materials with extraordinary functionality It seeks to create and translate knowledge at the frontier of materials science. IFM links world-leading materials science research with industry partners. For example, IFM recently partnered with Callidus Welding Solutions to extend the life of metal components that are used in mineral processing. Callidus Welding Solutions is an innovative company based in the heart of Australia’s mining industry in West Australia.
Researchers at IFM are collaboratively working with Callidus Welding Solutions to bridge the gaps between theory and practice. They are developing a novel surface engineering solution that will avoid severe erosion and corrosion issues.
Australia’s mining sector is consistently exposed to hot and dry conditions, which leads to increased maintenance demands.
As such, the IFM and Callidus Welding Solutions partnership is working to avoid these impacts in critical metal reactor components. These components are typically used when nickel, cobalt and gold are processed. These are complex techniques with limited space for error. The novel technique seeks to minimise erosion and high-temperature acid corrosion in hydrometallugical reactors, which are often pushed to their limits.
The partnership forms part of the Federal Government’s Cooperate Research Centre program, which links end-users with research trailblazers to deliver sustainable industry outcomes. Gary Lantzke is the Chief Executive Officer of Callidus Welding Solutions, who said the partnership is already delivering tangible outcomes for his business.
“The partnership we have developed with Deakin is a true win, I hope for both teams. Innovation although a bit overused today is at the core of our DNA as a company.” “What happened when Deakin became a resource has been truly magic. Almost every trial we have placed has performed exceptionally well and to date two new products have been born,” Lantzke explained. Professor Matthew Barnett, Associate Professor Daniel Fabijanic, and Dr Santiago Corujeira Gallo, make up the research team.
The IFM team draws its expertise from other researchers at CSIRO— Australia’s leading science agency— and other companies involved in the mining space, like Murrin Murrin Operations and Newcrest. The novel component design and surface modification technologies will enable the project team to double component life. In addition it will improve the efficiency of existing processes and potentially save the industry millions of dollars in lost production time. Associate Professor Fabijanic said these impacts are a gamechanger for the sector.
“This is a great example of letting a partnership naturally develop.” “First, we assisted Callidus with insight into a process they had been independently developing over a few years.” “Next, I introduced a new surface modification concept, which they could immediately adopt using their current capabilities,” he explained. Associate Professor Fabijanic is an expert in the development of such techniques for ferrous metals. He has previously placed a strong emphasis on the commercialisation of a patented low temperature duplex surface treatment option, which can be used for aluminium metal forming tooling. But his most recent partnership is leading to strong industry outcomes, through his colleagues at Callidus Welding Solutions. “It was a real highlight to see Gary Lantzke’s eyes light up at the possibilities of this new technology angle,” he said.
The Benefits for Australians
Australia’s mining, oil and gas sector is a major contributor to the way that Australians live. In addition, it relies on fresh ideas to maintain its international competitive advantage. Without such crucial research partnerships, like IFM and Callidus Welding Solutions, the daily lives of Australians would be vastly different. In fact, the sector is responsible for over 10 per cent of the nation’s economy, and provides jobs for nearly 240,000 people. Associate Professor Fabijanic said these partnerships close the research knowledge gap: research to operations, and operations to research. “Callidus is very open to new ideas, and so far these new concepts are working well. The benefits and learning have been two-way, which is how a partnerships should be,” he said. Callidus Welding Solutions is also undertaking crucial work in the robotic welding space, where the company’s versatile GTAW and GMAW systems work with a wide range of materials. Together, these systems are reducing the cost and turnaround of ongoing repair and manufacturing requirements. Together, the IFM and Callidus Welding Solutions partnership is a strong example bridging the gap between science, policy and practice.
Environmental Focus for The Future
Callidus Welding Solutions also has Australia’s environmental future at its heart, by tailoring its operations in line with the United Nation’s Sustainable Development Goals. In fact, Callidus Welding Solutions’ parent company, Pon, has launched its own Corporate Social Responsibility program. The new program focuses on eight of the global sustainable development goals, which are considered to align with the company’s business objectives and values. In addition to reducing carbon emissions, the company is also seeking to meet social responsibility goals in terms of diversity and inclusion. Callidus Welding Solutions has been selected to be one of two operating companies in the industrial mobility group to drive this environment and sustainability strategy creation. The company has taken on additional staff to ensure the best strategy outcomes. Together, these impacts are expected to be felt across the wider company and operations team.
Laser-Focussed Approach to Mining Equipment Longevity
Source: Sally Wood
Australia’s manufacturing sector is based on a multi-stage approach. This means that industry personnel must undertake several processes to refine and export products. However, this method leads to increased wear and tear for equipment—like corrosion, erosion, adhesion and abrasion—which is detrimental for the sector’s long-term future. Australia’s mining, oil and gas sector is the backbone of the nation’s economy—accounting for over 10 per cent of gross domestic product. As such, the sector relies on strong equipment and technology to power the lives of all Australians.
Shutdowns for repairs and maintenance of equipment can cost upwards of $100,000 for every hour of downtime. Therefore, it is crucial that equipment maintenance costs and production downtime are minimised.
Australian researchers and industry are working together to develop innovative solutions that reduce ongoing maintenance requirements. For example, coatings that protect certain machinery components can be implemented in multi-stage manufacturing to meet global supply and demand.
LaserBond is an Australian company that is at the forefront of this research. Since the company was founded in 1992, it has focussed its operations on the development of advanced surfaceengineering techniques that reduce the wear and tear, maintenance and operating costs of production. The company uses a unique thermal spray coating and laser cladding, which are underpinned by state-of-the-art welding, heat treatment, surface finishing and metallurgy lab processing. Laser cladding is a widely-used additive manufacturing process. It has a suite of benefits, including: • Improving the performance and longevity of equipment • Enhanced protection against wear and corrosion • Cost-effectiveness • Reclaiming life in fatigued components • Precision and accuracy LaserBond’s in-house services offer some of Australia’s greatest corrosion protection for manufacturers.
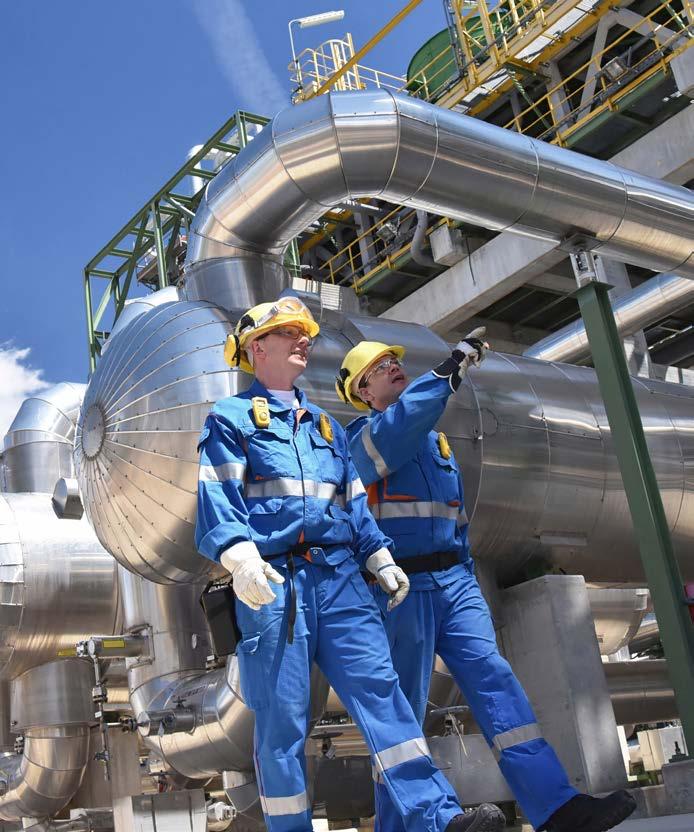
Fixing Industry Problems with Innovative Solutions
Thermal spraying technologies are not new to the mining, oil and gas sector. In fact, this process has been used for over 90 years across a range of applications. It can protect playground equipment, buildings, and wind turbines from excessive corrosion or damage. The process is also the most recommended protective coating for structural steelwork. It is strongly supported by international standards, which underpin the safety and precision of work conducted in the sector.
In all, the process provides more than 20 years to the next round of maintenance in overly aggressive environments, which are common in some Australian contexts.
LaserBond uses thermal spraying across a variety of settings, including on the CAT 777 dump truck. Large dump trucks are used across the Australian mining environment. These trucks experience wear damage to their drive splines and ongoing contamination, which can lead to drive spindle failures. When a truck experiences down time, it impacts the entire site’ production. The process of remanufacturing these critical components can be complex and requires a strong attention to detail. Even some welding or thermal spraying can lead to increased risk and downtime.
However, LaserBond’s laser cladding technique saves considerable time and money, rather than waiting for new parts. The company employs a metallurgical bond, which unlocks the potential for applied layers to be used in high impact settings. The remanufacturing process involves an inspection, pre-machining to remove damaged surface, cladding and some finishing touches to meet industry specifications. This technique minimises undesirable thermal decomposition and leads to a faster turnaround of components. Similarly, road headers are rock cutting machines that help with tunnelling and civil applications. They are made up of a rotating head, which thrusts through rock faces. But damage to this hard chrome can occur through abrasion, corrosion, and contamination.
Hard chrome finishes may struggle in certain environments in which there are fine abrasive particles. Wet environments can also lead to internal rusting, substantial delamination, and overall equipment failures. LaserBond have pioneered a technique that uses cladding material to offer greater protection and longevity against these parts. LaserBond’s internal bearing surfaces of road heads are clad with a range of different metallurgy to suit the application’s primary failure mechanisms.
After a stringent laser cladding process, high-capacity lathes and borer machines are used for increased protection. LaserBond have also used similar techniques on underground mining cutter drums by cleaning the surface, a rigorous inspection, and laser cladding. Together, this brings the machinery back to original equipment manufacturer specifications. In some cases, like base frames, LaserBond has successfully extended equipment’s lifespan from 20,000 to over 40,000 hours. It also leads to increased availability of machinery and less downtime.
Linking Australian Research with Practice
LaserBond actively draws on the support of Australia’s world-leading researchers to fill any gaps in the industry. This research loop ensures that researchers and industry alike are working together to develop modern technologies, and change any existing ways of thinking. For example, LaserBond has a $2.4 million research partnership with the University of South Australia and the Innovative Manufacturing Cooperative Research Centre (IMCRC). The partnership unlocks the potential for experts and scientists to develop some of the world’s most resilient minerals processing equipment. Professor Peter Murphy is the lead researcher from the University of South Australia, who said he is pleased to grow the advanced manufacturing sector within Australia.
“This comes at a time where we need to nurture our manufacturing capability and this project has the capacity to grow, employ and lead Australia through the challenging economic times,” Professor Murphy said. The team is focussed on increasing the longevity of mineral processing equipment through composite coatings. The improved cladding process seeks to reduce facility maintenance shutdown schedules and other operational requirements. By matching the machinery life to service schedules, unforeseen shutdowns can be avoided or minimised entirely. The Chief Executive Officer and Managing Director of IMCRC David Chuter said the research collaboration builds on a long-standing and collaborative partnership. “Together, wear and corrosion, continues to be a costly and disruptive challenge across many industries and developing advanced materials and technologies for wear and corrosion protection will help both Australian and global manufacturers combat these challenges,” he said. IMCRC leads the way for change in transforming the future of Australian manufacturing. It seeks to position the sector as a competitive leader in the global manufacturing space. It is funded under the Federal Government’s Cooperative Research Centre program, which links researchers with end-users based on gaps within the overall market. “It is great to see, that through engagement with the University of South Australia’s researchers, LaserBond, in collaboration with local manufacturers can develop its solution locally and then take it globally,” Chuter explained. The Centre works with over 85 industry and research organisations. Together, it has invested $34 million in collaborative research and innovation.
Swinburne Start-Up Receives $1.5 Million Investment to Help Make Mining Environmentally Safer
Source: Sally Wood
An Australian start-up company is using particles from space to help mining companies detect weaknesses in dams that secure highly toxic mining waste by-products. mDetect is a spin-out company from Swinburne University of Technology, which is using ‘muons’ from space to make mining waste environmentally safer. The ground-breaking hazardous waste early warning system, using muon technology will revolutionise how mining companies monitor the stability of tailings dams. The Federal Government has invested $1.5 million in the initiative under the Advanced Manufacturing Growth Centre (AMGC) Commercialisation Fund to fast track its commercial production. Global mining companies use tailings dams to manage potentially dangerous by-products. It is estimated that around three tailings dams fail worldwide every two years, which potentially leads to damaging environmental outcomes. However, there have traditionally been no detectable early warning signs from deep within the walls to prevent failure.
Creating Positive Impact
According to Swinburne University of Technology’s Vice-Chancellor, Professor Pascale Quester, research and education into space technologies and their terrestrial applications have extraordinary potential. “Swinburne is focused on ensuring that the vital research we do has significant positive impact. The important work of mDetect, led by Swinburne’s Professor Alan Duffy, is emblematic of Swinburne’s cutting-edge research and our ability to market innovative ideas.” The research seeks to bridge positive economic and social impact for the next generation of materials production. “This is paving the way for successful research commercialisation that provides real solutions for industries. It is projects like this that best exemplify our vision of bringing people and technology together to build a better world. We thank the AMGC for their support and commitment to this important initiative,” Professor Quester said. The researchers have linked with key industry partner, OZ Minerals, who will deploy the device at their tailings dam at the Carrapateena Province. Myles Johnston, General Manager of OZ Minerals Carrapateena Province, said the company has acted on its responsibility to meaningfully contribute to regional economic and social wellbeing. “By ethically and responsibly exploring for and mining copper, we contribute to a low carbon future and economic wellbeing, which helps us achieve our purpose and contribute to a better future.”
“We congratulate mDetect on being awarded the AMGC grant, and the team at Carrapateena is excited to be collaborating with mDetect on the development of a fully supported, flexible 3D muon monitoring system,” Johnston said. The mDetect team pulls together the deep technical expertise and research of Professor Alan Duffy, Dr Shanti Krishnan and Craig Webster, along with the start-up experience of Dr Eryadi Masli and Dr Jerome Donovan. “Muons are heavier versions of electrons, that are made when cosmic rays slam into atoms in Earth's atmosphere. We have patented new detectors, that combined with powerful AI techniques, take an X-ray style scan through solid rock revealing different density structures,” Professor Duffy said. Muon technology can look through rocks to create underground images and detect abnormalities that will provide the early warning signs needed to prevent potential structural failures.
mDetect will work with Elgee Industries and Swinburne’s Factory of the Future to produce the muon devices at scale.
The patented technology can provide intelligence on the internal structures and substances of buildings, infrastructure, and subterranean and aquatic features. It is expected to open up a range of commercial opportunities for the construction and mining industries.
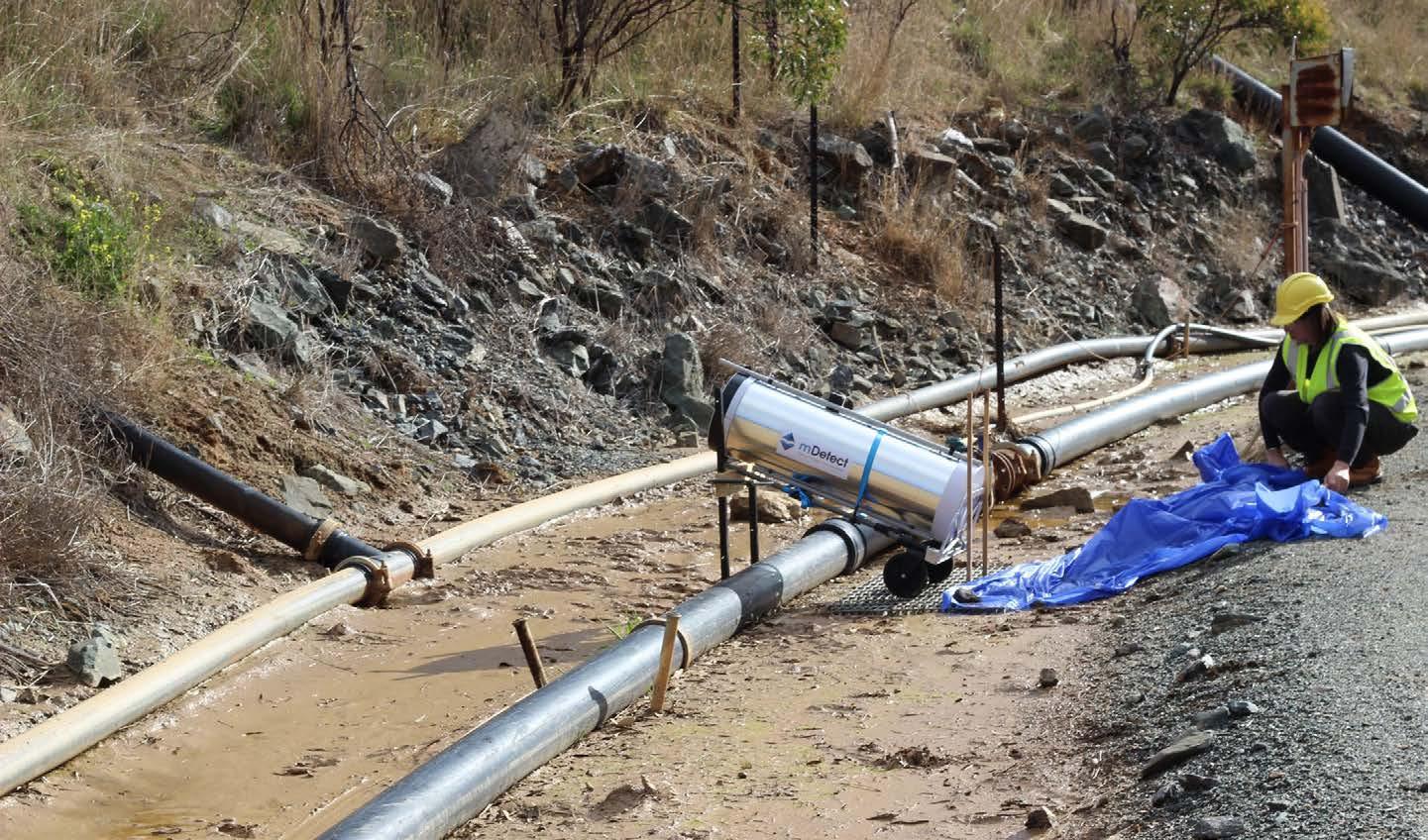
mDetect's ground-breaking early warning system will help mining companies detect weaknesses in dams that secure highly toxic mining waste by-products. Image credit: Swinburne University.
Plants That Absorb Metal Could Help Provide a Sustainable Future for Mining
Researchers from the University of Queensland have recently discovered that harvesting plants, which can absorb metal from the ground, may offer a sustainable solution for mining and rehabilitation. The Sustainable Minerals Institute has teamed up with the Queensland Government to investigate whether plants can reliably produce metals such as cobalt and zinc. The process is known as phytomining, where the plants absorb metals from the ground. Associate Professor Peter Erskine said the study is investigating if this process, once implemented at a large scale, could be a sustainable option for mining rare metals and the transition from carbon-fuelled mining. “We’re currently growing plants using metal-rich soil and tailings from around Queensland,” Professor Erskine said. Queensland is home to native plants that have an ability to absorb metal, which are known as hyperaccumulators. “Further phytomining research has the potential to unlock a sustainable stream of critical metals, including from mine wastes and tailings, that still hold residual metals of interest. So, in effect, phytomining could turn waste into new resources,” Professor Erskine said. The researchers are confident that the phytomining of nickel could quickly proceed to full-scale production and that the phytomining of cobalt, thallium and selenium are on the horizon. Queensland’s Minister for Resources, the Hon Scott Stewart MP, said the joint study had the potential to shape the state’s mining future. “Rare earth metals are vital to the global economy with the popularity of renewable technology and electric vehicles continuing to grow,” Minister Stewart said. The research capitalises on Queensland’s rich deposits of minerals like cobalt, copper and vanadium. “Research like this will help Queensland emerge as a worldleader in extracting and processing these metals, meaning more jobs and investment for all Queenslanders,” Minister Stewart said. It builds on the Sustainable Minerals Institute’s vision of finding solutions to other complex problems, which are facing the environment, humanity and the economy. It supports initiatives that address population growth, food and water security, energy, poverty reduction and escalating inequity. Professor Rick Valenta said phytomining had the potential to help the mining industry address the expected drop in critical metals supply. “Lithium, cobalt, copper and nickel are going to be increasingly important for society as renewable energy technologies and electric vehicles become more prevalent.” “But these critical metals are becoming increasingly difficult for the mining industry to access due to environmental, social, governance and technical factors.” “Without supporting alternative methods of extracting these critical metals, the mining industry may find that is unable to keep up with the growing demand for them,” Professor Valenta explained. The origins of phytomining date back to nearly 500 years ago, where the father of modern mineral smelting, Georgius Agricola, smelted plants in his free time. He believed in uncovering what metals lay in the ground below, just by looking at certain elements in a leaf. However, the term was coined in 1983 when Rufus Chaney, an agronomist with the US Department of Agriculture invented the word. The phenomenon was extensively tested in the Borneo highlands in the heart of Malaysia’s farmland. Professor Valenta said the process offers unique advantages that are not matched by other technologies or processes. “Phytomining is uniquely suited for that role because it both introduces an abundance of new resources that can be unlocked with less invasive methods and it allows the sourcing of metals from mine waste,” Professor Valenta said.
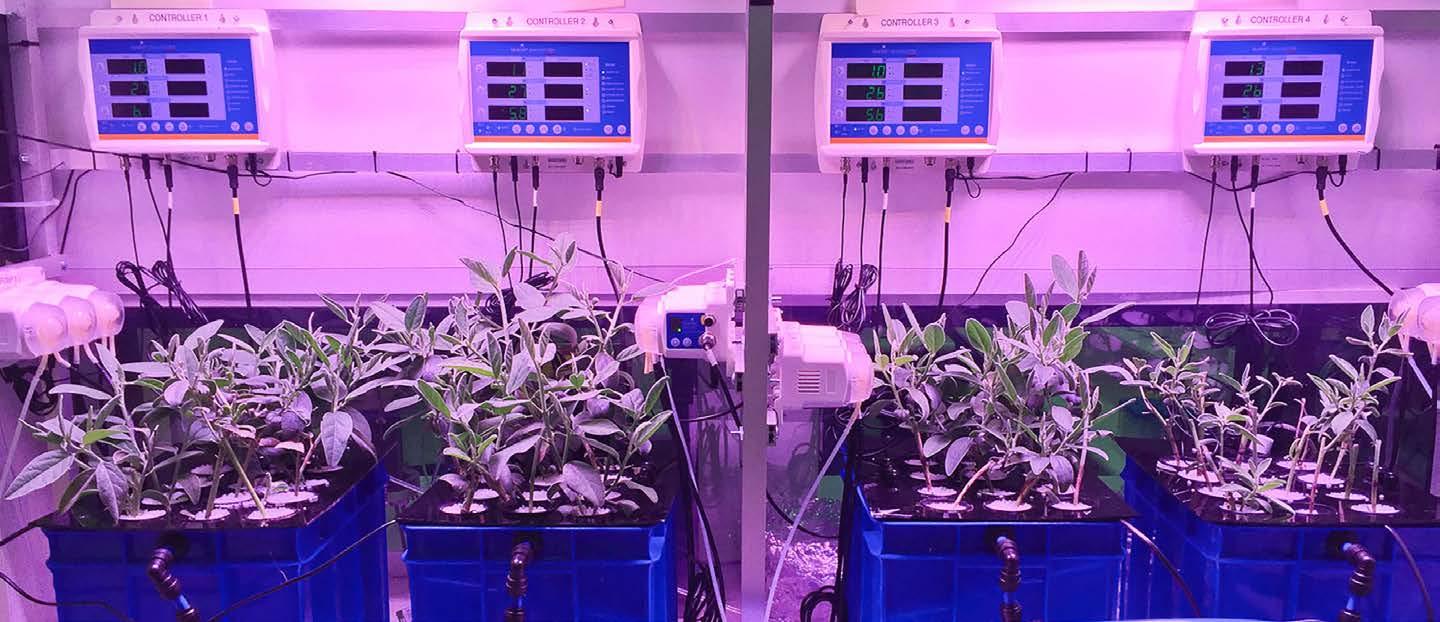
Laboratory hydroponics dosing experiment with the zinc hyperaccumulator Crotalaria novo-hollandiae. Image Credit: Antony van der Ent, UQ.
Queensland Minister for Resources Scott Stewart looking at a plant in the SMI laboratory.
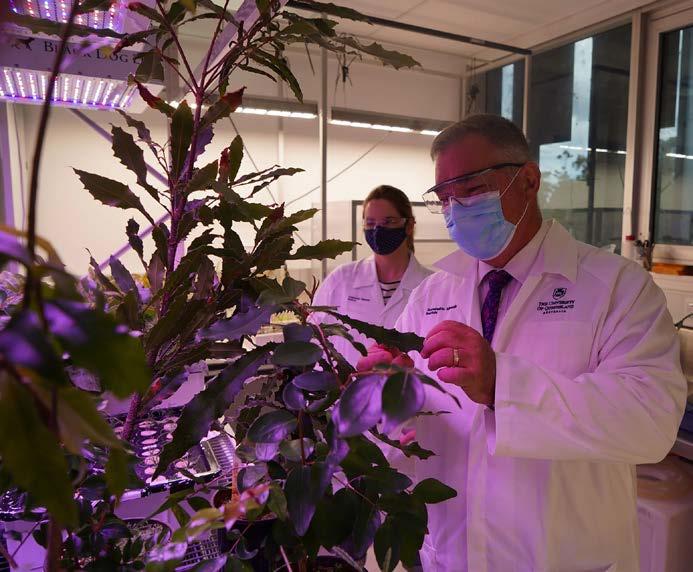