
6 minute read
Beyond Reality: : How Australia's Manufacturing Industry is Embracing VR
Augmented reality and virtual reality are among the emerging digital tools turning manufacturing on its head.
Virtual reality (VR) puts real people into virtual spaces, while augmented reality (AR) puts digital objects in real spaces.
Recent research by PwC revealed that the use of VR and AR in product and service development could add $1.5 trillion to the global economy by 2030, and deliver a $360 billion GDP boost to Australia by 2030. Not surprisingly then, Meta reports it has more than 10,000 people working in the space, while Apple has more than 2,000.
Virtual reality (VR) has surged as a transformative force in manufacturing, reshaping how industries conceptualise, train, and execute production processes.
In Australia, VR has been integrated into various manufacturing sectors, showcasing a commitment to innovation and efficiency.
For instance, virtual prototyping allows manufacturers to create and iterate designs without the material and time costs associated with physical prototypes. Collaboration in VR offers stakeholders across different locations a shared space for co-working, ensuring alignment and speeding up the design process.
Spatial visualisation through VR aids in acclimating new employees to complex industrial settings, minimising risks and enhancing operational understanding. Real-world applications have demonstrated VR’s utility, such as using VR models of oil rigs for safety training, employing digital twins for optimising machinery like turbines, and training aircraft technicians with 3D models to understand complex engines.
Several companies are using virtual reality to ensure particular components are assembled properly. For example, Lockheed Martin, the defence and aerospace company, has an entire virtual reality lab dedicated to product design and manufacturing. After using VR to build the F-35, Lockheed Martin found that engineers could not only work faster, but with an accuracy of approximately 96%. The lab, which is one of the largest of its kind, allows engineers to evaluate the efficacy, cost and risk of designs and models in a lowstakes environment.
Similarly, Boeing technicians use VR smart glasses that provide the necessary instructions for each wiring repair, reducing the necessary work time by 25%.
Joining automakers such as Ford, who has been using virtual technology since 1999, Hyundai now implements VR and 3D digital tools when designing new vehicles and parts. VR allows the designers to test models in specific contexts that mimic real-world scenarios — something that was impossible with the clay models of the past. Hyundai currently has a VR design review system, allowing team members around the world to thoroughly look at every step of the design and modelling process.
Learning Online Through Virtual Reality
Deakin University has partnered with HYDAC Australia – a world leader in motion control and fluid technology – to train operators on their machines by use of sophisticated VR software.
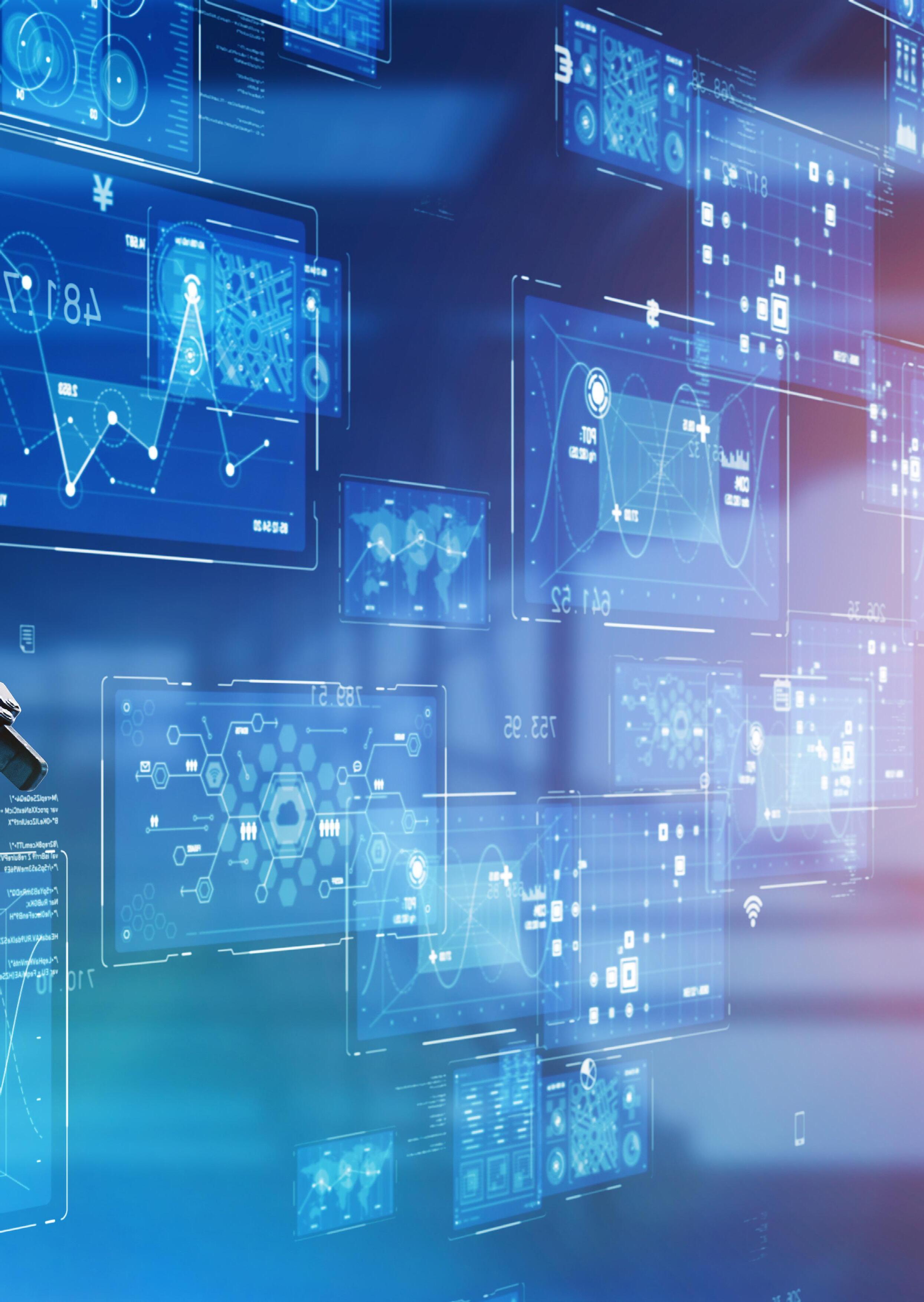
The training is unique in that it simulates hazardous events that would be impossible to demonstrate safely in real life. Students are able to virtually interact with equipment and receive real-time instructions and feedback from a professional, qualified technical trainer in the use of complex hydraulic machinery.
Deakin is one of the leading Victorian universities providing virtual reality training solutions to industry and has a strong track record of successful collaborations. Virtual reality experts from Deakin’s Motion Lab virtually recreated one of HYDAC’s most sophisticated machines – the wheel lock hydraulics pressure unit – allowing user interaction within a virtual environment.
The HYDAC Wheel Lock Hydraulics Pressure Unit virtual reality model and user experience design went through an iterative six-month development cycle, involving Deakin Motion Lab staff, HYDAC engineers and end users. The virtual reality model directly translates the real-world Hydraulics Pressure Unit device’s engineering plans, down to its minute details. Through the software, users communicate via voice, use natural hand gestures, and assemble and disassemble complex machinery with tools and hand movements that mimic real processes, whilst being guided by instructors and task panels. Hydraulics training requires expensive and heavy equipment. Hands-on training on complicated hydraulics machines is limited to specific locations and specific times. HYDAC’s virtual reality training provides an unprecedented opportunity for physically-distanced students to gain access to an expanded training program in the use of complex hydraulics machinery. For economic reasons, this level of training has not previously been possible on a broad scale. The VR technology removes the need for travel and provides training to staff located in remote areas, such as the mining sites in the Pilbara, where this type of machine is located.
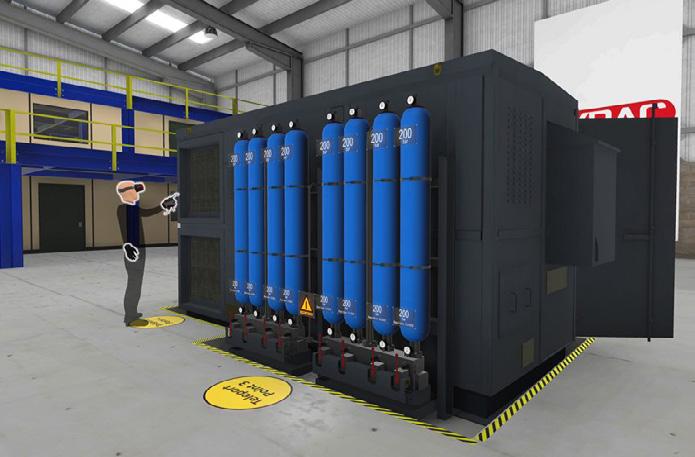
By removing the need to transport several tones of equipment around training centres throughout the country, the VR training also plays a role in reducing greenhouse gas emissions.
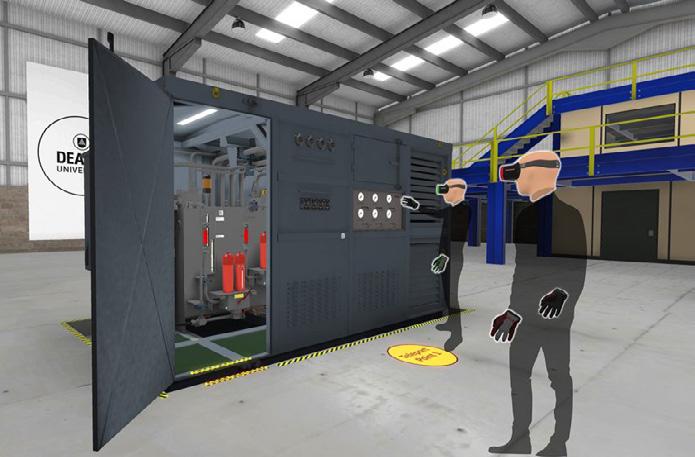
Australian Research Centre for Interactive and Virtual Environments
The University of South Australia’s Australian Research Centre for Interactive and Virtual Environments is a unique alignment of computer science, art and design, brought together to transform industry and society and solve contemporary challenges.
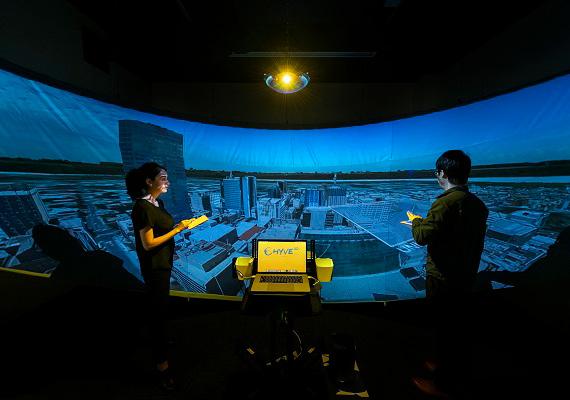
The Centre is a focal point for interdisciplinary AR and VR research into wearable computing, human-computer interactions (HCI), 3D visualisations and telepresence.

In partnership with BAE, ASC Shipbuilding and IMCRC, the Centre worked on a project to innovate the Hunter Class Frigate Program by harnessing data visualisation to improve shipyard planning and problem-solving capacity.
A first-of-its-kind digital environment of the entire ship design and construction process will be created to improve productivity, quality and safety outcomes in Australia’s naval shipbuilding industry. Research focused on how narrative visualisation and big data processing can deliver, reshape and refine the highly complex manufacturing environment. The outcomes will be extended beyond the Hunter program, assisting critical local supply chains and future projects across the manufacturing landscape.
In collaboration with Jumbo Vision International (JVI), the Centre has developed and commercialised smart manufacturing technologies. This partnership leveraged our researchers unique capabilities in AR visualisation of large system design and JVI’s expertise in the design and delivery of audiovisual solutions and command and control rooms.
Current design processes for manufactured high-end instrumented facilities, such as command centres and control panels, are flawed; the traditional process requires significant time, significant associated costs and can still result in a sub-optimal client experience.
The Centre’s researchers, led by Professor Bruce Thomas, developed VR simulations that provide fly-through animations and guided tours, as well as AR solutions that offer the ability to physically walk around and touch objects; allowing for the modification of a design concept in real time. This AR technology can significantly assist a client’s appreciation of the design and the effects of any changes; resulting in a better, more efficient and cost-effective end result.
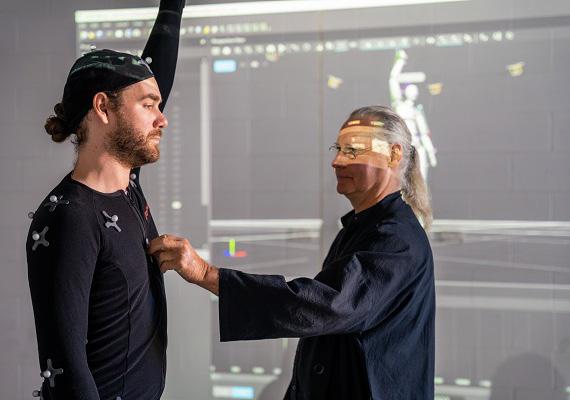
These instances are mere snippets of VR's burgeoning role in Australian manufacturing, indicating a future where virtual and physical realities coalesce to drive industry advancements.
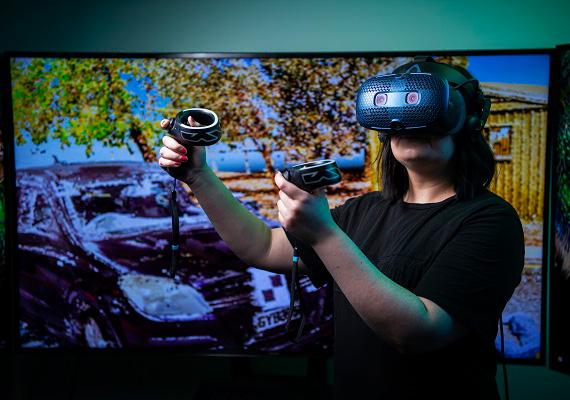