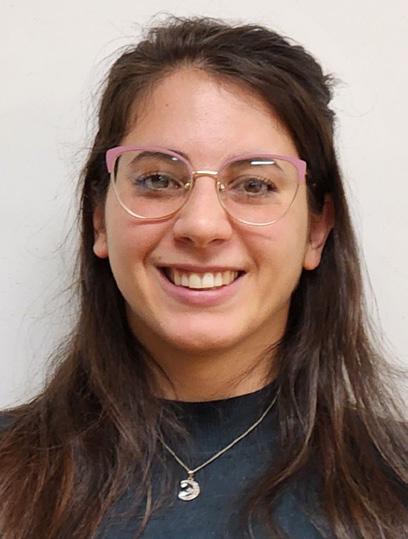
3 minute read
WA Branch Technical Meeting - 10 June 2024 Catching the Green Wave: Opportunities in Nickel Processing
Source: Dr Sofia Hazarabedian, DNV
Sofia started her presentation with a short description of how DNV had developed from its beginnings 160 years ago, in marine insurance and standards, to its current position as globally leading quality assurance and risk management company operating in more than 100 countries across the maritime, energy, food and healthcare industries, as well as a range of other sectors. Sofia’s presentation was based on a recent analysis that DNV had undertaken on nickel production.
Sofia graduated as a materials engineer from the Sabato Institute, Argentina and holds a PhD from Curtin University for her research focused on mitigating hydrogen embrittlement within the oil and gas sector. Her current role as a Hydrogen Engineer in the ANZ Hydrogen and Carbon Capture Utilisation and Storage (CCUS) team at DNV reflects DNV’s strategic positioning to cover the emerging hydrogen value chain. Sofia’s current work involves strategic studies for hard-to-abate industries including large-scale green hydrogen and ammonia production, hydrogen pipelines, and decarbonisation roadmaps for critical metals and green steel.
Nickel is a crucial material for stainless steel and electric vehicle (EV) batteries, with a rapid growth in demand for high-grade nickel, driven by the burgeoning EV industry. The market for nickel metal is divided into Class 1 (>99.8% Ni), used for non-ferrous alloys and batteries, and the less pure Class 2, used for making stainless steels. Batteries currently make up around 7% of demand, but this is forecast to grow to 35% by 2030. The demand for nickel to enable a ‘greener’ economy has led to questioning of the ‘green credentials’ of nickel production. This has become particularly acute with the recent expansion of the Indonesian nickel industry. Sofia described how, in response, DNV has undertaken a desktop study for a white paper on the environmental costs of producing nickel for the three major ore types, through their typical processing routes.
The major division between nickel ores is into sulphides (produced by segregation in cooling magma) or laterites (produced by weathering of ancient rocks). Laterites are either saprolites (silicates) or limonites (oxides). These three ore types are processed in different ways. The first consideration is that while sulphide ores can be concentrated to produce high-grade nickel sulphide, laterites have low nickel content, and the nickel is chemically combined and cannot be concentrated.
Sulphide concentrates are suitable for the production of highgrade nickel, by either pyro- or hydrometallurgical process routes. The main environmental consideration is dealing with the sulphur content, which is typically used to produce sulphuric acid. Saprolitic laterites are typically processed through the rotary kiln, electric arc furnace route to produce ferro-nickel used for stainless steel. Limonitic nickel laterites are typically processed by high-pressure acid leaching (HPAL) followed by hydrometallurgical purification, making them a suitable source of Class 1 nickel.
The environmental impact of processing laterites arises mainly through the high energy cost of having to process all the ore to extract the low nickel content. With HPAL, there is an additional environmental impact from the release of carbon dioxide from the decomposition of limestone needed for the neutralisation of acid from the leaching stage. Overall, the carbon footprint of HPAL processing is approximately twice that of processing sulphide ores.
The DNV desktop study has been used to investigate the environmental costs associated with the emerging Indonesian nickel industry, which is based on lateritic ores. There is clearly a “net-zero paradox” as these operations have a high carbon footprint, while Indonesia has a goal of becoming carbon-neutral by 2050.
There are potential ways of reducing the carbon impact of processing in Indonesia. For example, there are large potential geothermal power resources, though these are not necessarily close to the nickel operations. Moreover, Indonesia is an archipelago and transmission of power over long distances between islands would involve large infrastructure costs.
Sofia engaged with the audience in expanding on these topics. The low direct cost of Indonesian nickel introduces high environmental costs from the use of coal as the main energy source for processing and the additional emissions from acid neutralisation. Change would require a “green wave” of regulatory pressure or a market preference for “greener” nickel. In the absence of such forces, Australian nickel production is at a long-term cost disadvantage.
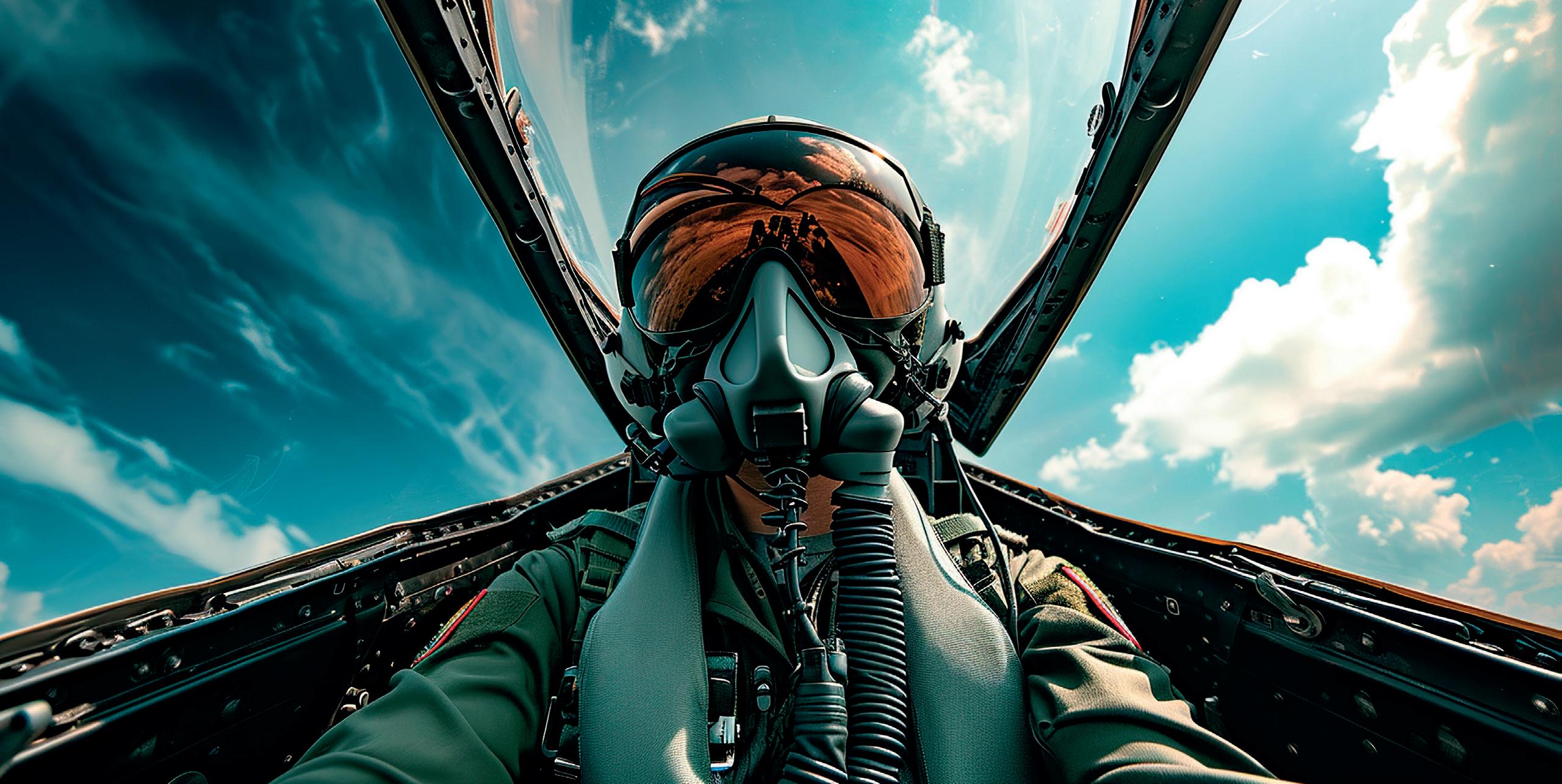
Making Sure They Have a Safe Ride
HYPERSONIC MATERIALS CHARACTERISATION UP TO 2000°C AND BEYOND
∙ Thermal conductivity determination for temperatures up to 2800°C using laser flash analysis
∙ Determination of specific heat and degradation behaviour up to 2400°C and beyond
∙ Analyzing thermal expansion up to 2800°C with dilatometry
∙ Characterizing dynamic mechanical properties with forces up to 500N and 1500°C using DMA

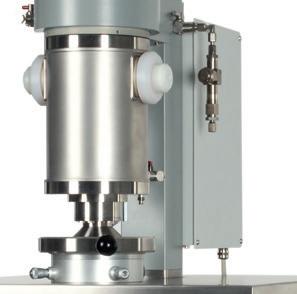
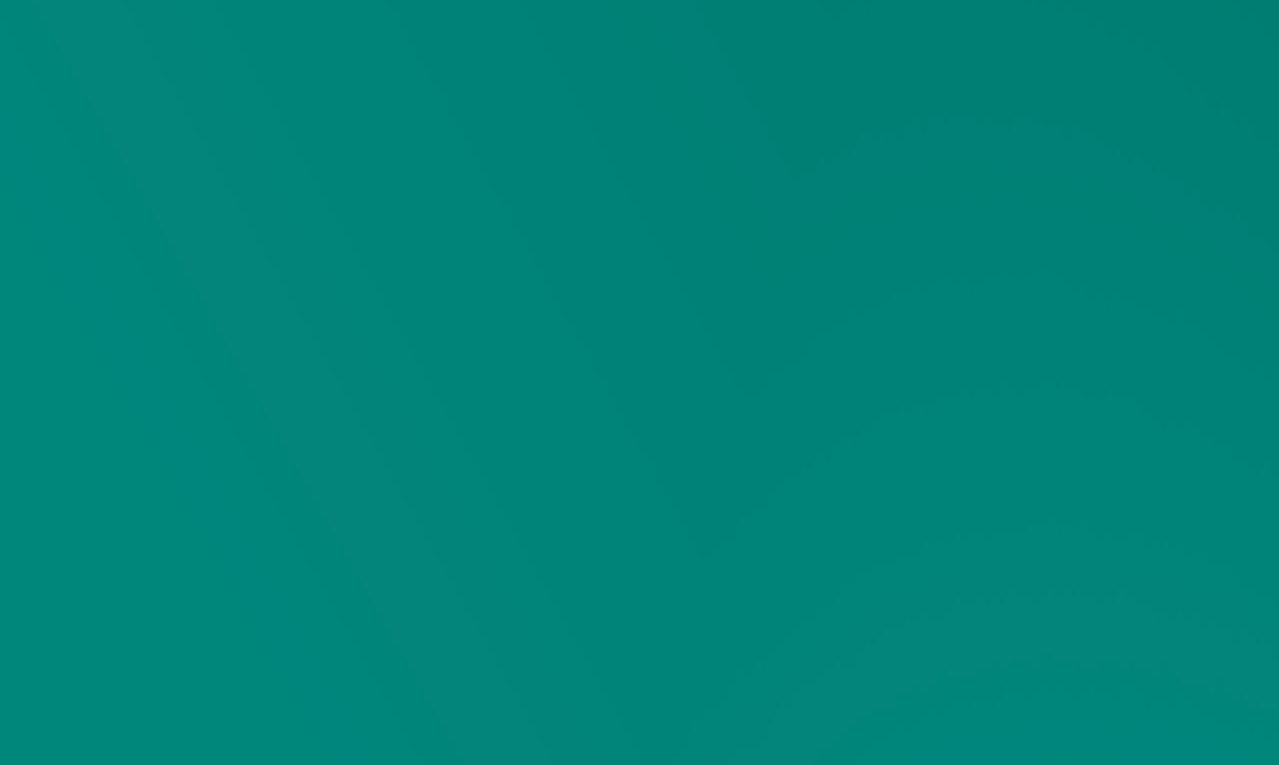
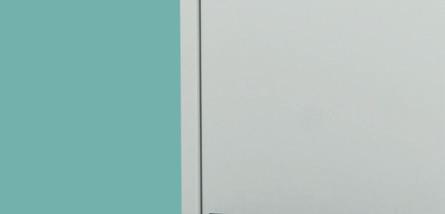
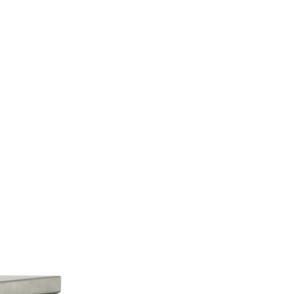
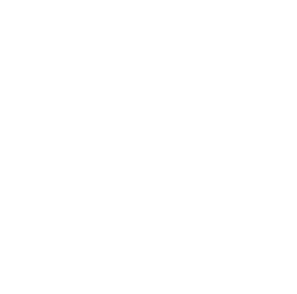
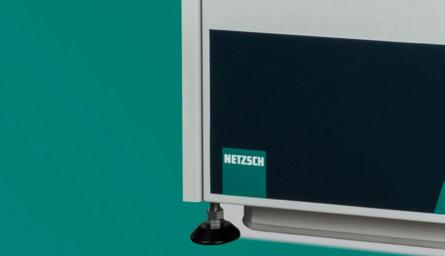

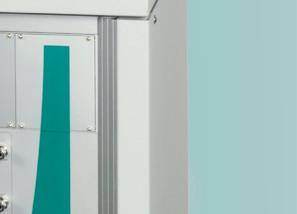

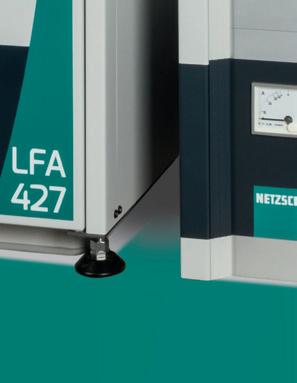

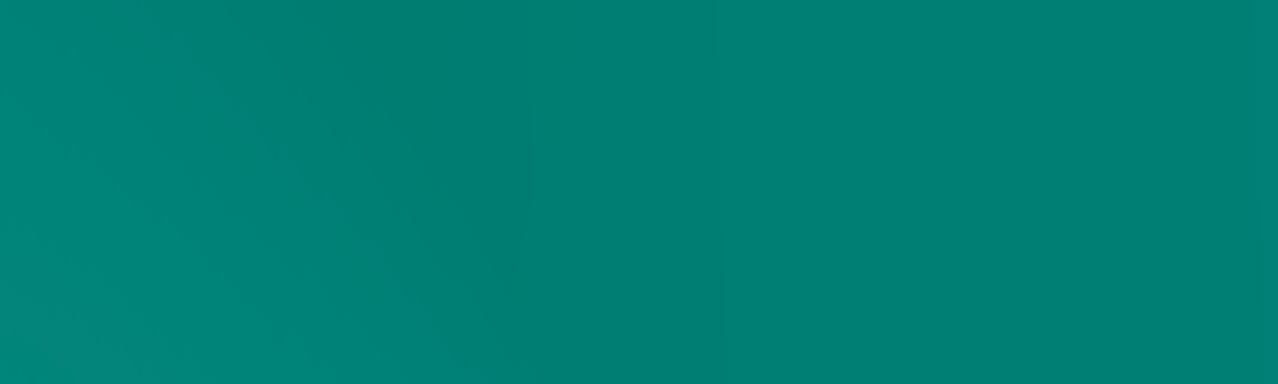