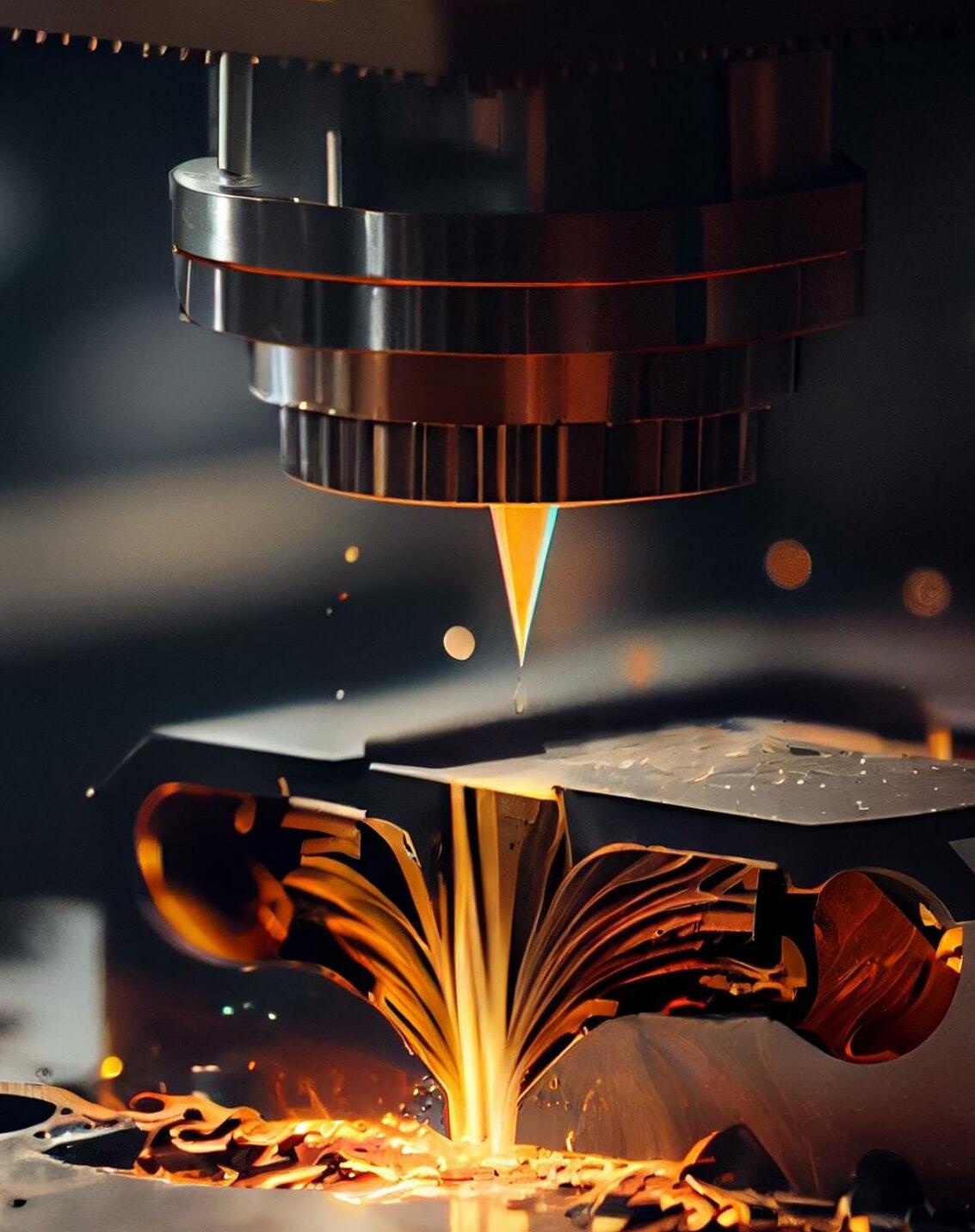


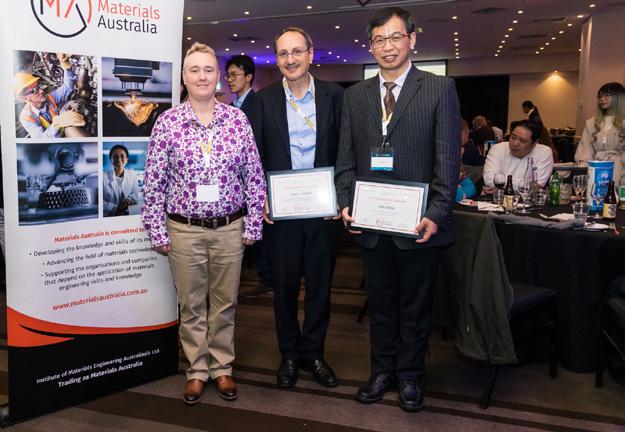
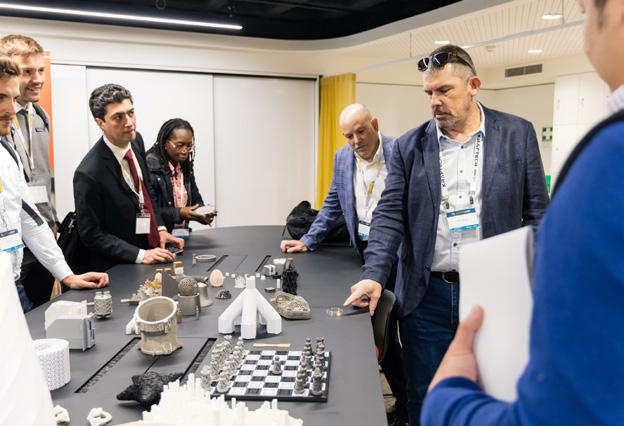
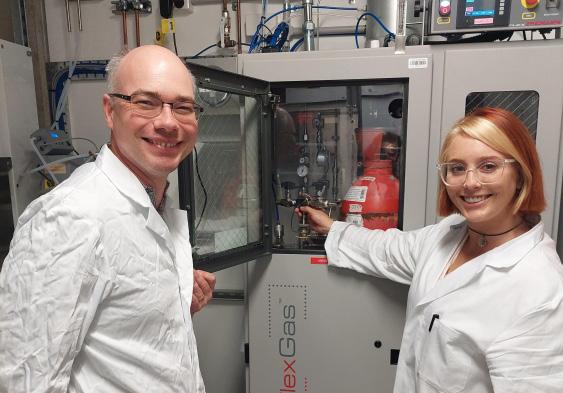
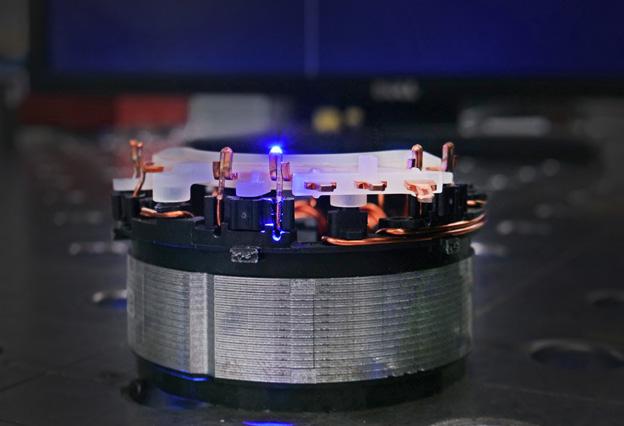
for special processes. As this has consumed thousands of hours of my time I thought it would be a good topic to share as I rank the achievement as a highlight of my career as a Materials Scientist and Engineer.
Nadcap stands for the National Aerospace and Defense Contractors Accreditation Program. It is a global cooperative program managed by the Performance Review Institute (PRI) that aims to ensure the quality and reliability of special processes used in aerospace and defence industries.
Welcome to the June 2023 edition of Materials Australia Magazine. For this month’s presidents message I thought I would share some recent experiences I have been involved with in my role as the Responsible Level 3 for nondestructive testing with my employer, AWBell, and our recent success in gaining Nadcap accreditation for Fluorescent Penetrant Inspection (FPI) and Digital Radiography (using a Digital Detector Array). This a particularly special achievement for our company and for me personally. Passing a Nadcap audit is an uncommon feature of Australian manufacturing industry and this achievement is the culmination of an initiative begun in about 2014 when we first completed special process audits with an aerospace customer, that were necessary because AWBell did not already have Nadcap accreditation
MANAGING EDITOR
EDITORIAL COMMITTEE
Prof. Ma Qian
RMIT University
Dr. Jonathan Tran
RMIT University
Tanya Smith
MATERIALS AUSTRALIA
Nadcap provides a standardized accreditation process for suppliers, known as "special process" suppliers, who perform critical manufacturing and testing activities. These processes include heat treating, non-destructive testing, chemical processing, welding, and many others.
The program involves a thorough audit of a supplier's operations, focusing on process controls, equipment calibration, personnel qualifications, and adherence to industry standards. Accreditation demonstrates a supplier's commitment to quality and compliance with stringent requirements. Typically, an audit will involve one day to review paperwork, then one day for each area requiring compliance audits.
In Australia, the number of companies who have achieved Nadcap accreditation for Flourescent Penetrant inspection is extremely low. The number achieving accreditation for
Rod Kelloway (02) 8539 7893
PUBLISHER
radiography is even lower. To the best of my knowledge, AWBell are the first Australian company to achieve Nadcap accreditation for aerospace Digital radiography. The participation rate is low in Australia because aerospace manufacturing within SME’s is a smaller focus of the manufacturing landscape. The importance of ISO9712 in accrediting personnel, administered by the Australian Institute of NonDestructive Testing (AINDT) also cannot be overlooked, since the system for aerospace is different (following standard NAS410), but hopefully will become more homogenous in future as the US adopts ASNT9712 for qualification of personnel and Australian Standards come into effect that are equivalent to NAS410.
Although I had been involved with various aspects of NDT for some years, the pathway to achieving this accreditation was torturous, even though I did have quite a bit of experience in NDT both from my time at CSIRO and in the period from 2012 onwards at AWBell. Formally, in 2015 I begun the journey by gaining an industrial radiography licence, followed by Level 2 film radiography (of welds) accreditation in early 2017 in accordance with ISO 9712. Later, I gained Level 2 accreditation for radiography of castings. In early 2019, I gained Level 2 accreditation for penetrant testing. In late 2019, I began my ISO 9712 Level 3 accreditation, a process that takes many months to complete fully meaning I (fortunately) passed all examinations and finished in March 2020.
In 2021 AWBell began the process of initiating upgrades to their penetrant testing line, and I began designing the general layout of our digital radiography facility. In early 2022, I also completed my Level 2 accreditation in Digital Radiography of welds. Equipment was later researched and procured and finally the system was commissioned in March 2023. Meanwhile, I completed additional Level 3 examinations (Coordinated by MA Corporate member, ATTAR to whom I owe enormous thanks) then followed by conducting examinations for our own Level 2 staff in accordance with the standard NAS410. The Nadcap auditor flew out from the United States in late April 2023 to conduct our onsite audits and I’m really pleased to say that we passed the two audits with a total number of four minor nonconformances. We have one more audit to go in July and hopefully it will go as well as the first two.
As you might appreciate, achieving Nadcap accreditation as a business is a huge achievement, a significant investment, and an enormous opportunity for business growth. Once completed suppliers become eligible to bid on contracts and projects that are exclusively available to accredited organisations. Supplier approval is recognized universally and globally by multiple aerospace and defense companies. This opens up new business opportunities and facilitates access a larger customer base, enhances credibility, instils confidence, and distinguishes companies from nonaccredited competitors.
Being a part of the Nadcap community also provides opportunities for networking and collaboration. Suppliers can connect with industry leaders, and participate in working groups, which
leads to partnerships, knowledge sharing, and business-to-business collaborations. Through engagement with the program, suppliers gain insights into the latest industry trends, technological advancements, and quality requirements. This knowledge enables them to enhance their processes, stay competitive, and seize new business opportunities.
As may be appreciated, nondestructive testing is not the only area of opportunity for gaining Nadcap accreditation. Having been through this process, I can really appreciate how there are such enormous opportunities for Australian advanced manufacturing by pursuing accreditation across all manufacturing industries who wish to supply products and services into aerospace.
Best Regards
Roger Lumley National President Materials Australiawelcomes editorial contributions from interested parties, however it does not accept responsibility for the content of those contributions, and the views contained therein are not necessarily those of Materials Australia. Materials Australia does not accept responsibility for any claims made by advertisers. All communication should be directed to Materials Australia.
Materials
GLOBAL STEEL HEAT TREATMENT
Source: Sally Wood
The 2023 Asia-Pacific International Conference on Additive Manufacturing (APICAM)—the third of its kind to be held in the Asia Pacific region—was held in Sydney in late June.
APICAM was created to provide an opportunity for industry professionals and thought-leaders to come together, share knowledge and engage in the type of networking that is vital to furthering the additive manufacturing industry.
Attendees heard from some of the leading minds in the industry, who presented highly informative and engaging presentations on pressing issues, as well as the ways in which innovations can navigate challenges. Important areas such as 3D printing and additive manufacturing in the clean energy, sustainability, biomedical, defence and aerospace industries were covered by experts from each respective field.
Just some of the keynote presentations included: 3D Bioprinting: Making Stuff that Makes Stuff using Biology by Distinguished Professor Gordon Wallace (University of Wollongong); 3D Printing Hierarchical Porous Ceramics by Professor George Franks (University of Melbourne); Addressing AM Sustainability of Polymer Use by Professor Ian Gibson (University of Twente); Burn the Boats: A Strategy to Accelerate Adoption of Advanced Manufacturing by Dr Lonnie Love (Sandia); and Crystallographic
Texture Control by Metal Powder Bed Fusion by Professor Takuya Ishimoto (University of Toyama).
The keynote addresses were complemented by countless other presentations, across a variety of subject areas, including metal, polymer, ceramic and concrete additive manufacturing, bioprinting and biomaterials, digital manufacturing, modelling and simulations, and emerging additive manufacturing technologies.
Asia-Pacific
Conference Chairs Lto R: Professor Sophie Primig and Professor Gwénaëlle
21st - 23rd June 2023
The University of Sydney
The
The Poster Session gave attendees the chance to become better acquainted with the significant volume of technical and academic research being undertaken in Australia’s additive manufacturing industry.
Each technical poster was accompanied by the academic who created it, giving attendees the opportunity to discuss the research and have all their questions answered. Our congratulations go to Andre Hatem, UniSA who won the award for best poster.
Sponsored by the CSIRO, the Conference Dinner at Rydges World Square was a highlight of APICAM. The Dinner was an opportunity for industry professionals to get together in a more relaxed setting and to forge friendships that might otherwise be impossible.
www.apicam2023.com.au
Speakers at the Dinner included Kathie McGregor (Research Director - Advanced Materials and Processing at the CSIRO) and Professor Nikki Stanford (Materials Australia Vice President, and Dean of Programs for Engineering and Aviation at the University of South Australia).
The Dinner also saw the presentation of the Materials Australia Silver Medal to Simon Ringer and Ma Qian. The Silver Medal is presented for outstanding contributions to the advancement of materials science and engineering through management, teaching, innovation, development or research. Our congratulations go to both Simon and Ma for their valuable contributions to our industry.
Of course, none of this would have been possible without our conference sponsors. Materials Australia would like to extend our gratitude to Trumpf, our Platinum Sponsor; Quintus Technologies and Nano Dimension, our Gold Sponsors; the CSIRO, our Dinner Sponsor; American Elements, our Lanyard Sponsors; Zeiss, our Notepad Sponsors; AML3D, our USB Sponsors; and Struers, our Pen Sponsors.
Materials Australia would also like to thank all our exhibitors, including 3D Ceram, AXT, ATA Scientific, Bruker, Cameca, Emona Instruments, Evident, Hexagon, Objective3D, Merck, and Warsash Scientific.
Whether your projects use traditional 3D printing methods or dynamic 4D techniques with time-dependent, self-assembly capabilities, our wide range of product formats will provide maximum design versatility, while maintaining energy efficiency. Using advanced printing techniques such as material jetting, vat polymerisation, and material extrusion, you will experience incomparable performance and economic productivity while reducing your environmental impact.
Our portfolio includes:
• Liquid crystal elastomers (4D printing enablers)
• UV-curable resins
• Polymeric & composite filaments
• Inorganic-based inks
Browse our collection today and see how 3D printing can benefit your business.
SigmaAldrich.com/3dprinting
This year’s APCIAM Program featured several engaging tours of the University of Sydney’s Core Research Facilities. Delegates had the opportunity to meet the University’s experts and discover the capabilities and services offered to researchers and industry. The facilities included the Sydney Manufacturing Hub, which offers world-class capability in additive manufacturing using advanced metals, ceramics and polymers, with a research focus, as well as Sydney Microscopy and Microanalysis, the University of Sydney's dedicated facility for analysis at a micro scale.
Delegates also visited the: Research and Prototype Foundry, the University of Sydney's state-of-the-art facility for micro and nano fabrication; the stress engineering arm of Sydney Analytical, the University of Sydney's facility for analysing material structure and composition; and the x-ray and spectroscopy arm of Sydney Analytical, the University of Sydney's facility for analysing material structure and composition; and an information session on the comprehensive research data services offered by Sydney Informatics Hub, home to the University of Sydney’s data experts.
• a unified crack-wake bridging model for strengthening and toughening of coarse-grained ceramics, cementitious materials and stitched/z-pinned composite laminates, which revolutionises the microstructure design of these materials;
• new fracture mechanics models for evaluation of fibre/matrix interface properties from single fibre pullout, push-in and fragmentation tests leading to the design of high toughness composites;
Materials Australia is pleased to announce that Professor YiuWing Mai has been awarded the institute’s prestigious Silver Medal. The Materials Australia Silver Medal is presented for outstanding contributions to the advancement of materials science and engineering through management, teaching, innovation, development or research. According to Materials Australia President, Dr Roger Lumley, CMatP, “Over the course of his career, Professor Mai has devoted his life to the study of materials. He has made significant contributions in the fields of advanced fibre composites, fracture research, superhard nanocomposites coatings, strengthening and toughening of ceramics, and electromagnetic materials.”
“Materials Australia would like to congratulate Professor Mai on his outstanding achievements and acknowledge him as a most deserving recipient of Materials Australia’s highest honour: the Silver Medal,” said Dr Lumley.
Professor Yiu-Wing Mai is distinguished for seminal work on fracture mechanics and materials science of advanced engineering materials. Through his many publications in the past four decades, Mai has made outstanding and lasting contributions to scientific and engineering knowledge in several research areas, including:
• a theoretical framework for the essential work of fracture method to measure toughness of ductile materials, especially polymer thin films and papers/newsprints;
• development of superhard (>40 GPa) multi-layered nanocomposites coatings on forming tools for green manufacturing through control of deposition processing parameters, microstructures and residual stresses; and
• nonlinear fracture mechanics of electromagnetic materials involving the development of theoretical models and their applications to fracture characterization in the presence of magneto-electrothermo-mechanical coupling and dissipative effects.
In recent years, Mai has focused his research efforts on polymer nanocomposites in which nano-sized particles (<100 nm) are incorporated into polymer matrices. He is making important continuing contributions on:
• basic understanding of the deformation, failure and toughening mechanisms of polymer nanocomposites;
• new syntheses and fabrication methods of multi-scale hierarchical reinforcements; and
• multifunctional applications such as fire retardancy, permeability, optical transparency, electrical and thermal conductivities, and cathodes/anodes in Li-ion batteries.
Mai's research results have also
influenced engineering practice with global impact. Some examples are the developments of (a) asbestosfree cements using cellulose fibres for building products (James Hardie & Coy Pty Ltd); (b) superhard layered nanocomposites coatings on machining tools for green manufacturing, and moulds & dies for wear resistance (General Motors, USA; Hong Kong Mould & Die Council); (c) improved composites manufacturing processes, such as pultrusion, thermoforming and stitching/zpinning (Cooperative Research Centre for Advanced Composite Structures, Australia); and (d) the essential work of fracture concept leading to an ISO International Standard (ISO 23524:2022 Plastics — Determination offracturetoughnessoffilmsandthin sheets — Essential work of fracture (EWF)method).
About Professor Yiu-Wing Mai Professor Mai built his entire academic and research career at the University of Sydney. He holds a University Chair and Personal Chair in Mechanical Engineering in the School of Aerospace, Mechanical and Mechatronic Engineering in which he has worked for nearly 46 years. He has held various positions over the course of his career at the University of Sydney, including Associate Dean –Research and Development (1990-93; and 1995-98) and Pro-Dean (19982004) of Engineering. He was the Founding Director of the Centre for Advanced Materials Technology (19892010). He was also the Director of the Sydney University Graduate School of Engineering (1995-98), the first of its kind in Australia.
In 2022, Professor Mai ranked 1st in Australia and 53rd in the world among 267,149 materials researchers in the world (Stanford University study: Mendeley Data, V5, doi: 10.17632/ btchxktzyw.5). He was also ranked 1st in Australia and 10th in the world in Mechanical and Aerospace Engineering by Research.com.
In 2010, Professor Mai was appointed AM of the Order of Australia for service to engineering, particularly in the fields of advanced fibre composites and fracture research. And in 2013, he was conferred a Doctor of Science (honoris causa) degree by the University of Hong Kong in recognition of his contributions to scientific research and society.
He was awarded an inaugural Federation Fellowship in 2001 (one of only three in engineering in that round). Through his elections to the fellowships of, and subsequent committee services to, the Royal Society of London, the UK Royal Academy of Engineering, the Australian Academy of Science, the Australian Academy of Technological Sciences and Engineering, and the Chinese Academy of Engineering, he has furthered enhanced the reputation and recognition of materials science and engineering at Sydney on the world stage.
Professor Mai has supervised or cosupervised nearly 60 PhD students to completion; and he advised over 60 postdoctoral and research fellows and visiting academics. Many of them are now successful leaders in their chosen fields in academia, industry and business.
Professor Mai was elected FRS (2008), FREng (2011), FAA (2001), FTSE (1992), and Foreign Member of the Chinese Academy of Engineering (2017). He has won some of the most prestigious research medals in his field. These include the RILEM Award and Robert L'Hermite Medal in 1981, Australian Fracture Group Achievement Award in 2000, and Takeo Yokobori Gold Medal of the International Congress on Fracture (ICF) in 2013. He was also awarded the Scala Award of the International Committee on Composites Materials (ICCM) in 2015, the AGM Michell Medal by the Mechanical College, Engineers Australia and the AA Griffith Medal by the UK Institute of Materials, Minerals and Mining (IOM3) in 2016. He has just been awarded the 2023 ASME Warner T Koiter Medal for pioneering research on fracture mechanics of fibre composites, ceramics and polymers.
Source: Sally Wood
Simon Ringer and Ma Qian were presented with their prestigious Materials Australia Silver Medal (awarded in 2020 and 2022 respectively) at APICAM 2023. The Silver Medal is presented for outstanding contributions to the advancement of materials science and engineering through management, teaching, innovation, development or research.
Simon is the Academic Director of the Core Research Facilities at the University of Sydney. He was the foundational executive director of Microscopy Australia and a founding director of Sydney Nano. Simon received the Medal for outstanding contributions to the advancement of materials science and engineering through research scholarship in microstructure-property-processing
relationships, research leadership in establishing world-class infrastructure for materials research, and service in the promotion and dissemination of materials issues to the wider community.
With a career that spans over 40 years, Ma is a Distinguished Professor of the School of Engineering at RMIT University in Melbourne. His research has made major contributions to industry, impacting on manufacturing processes such as casting, powder sintering, metal injection moulding and additive manufacturing. Ma received the Medal for outstanding scholarship and service to the materials community.
Materials Australia would like to congratulate both Simon and Ma, and thank them for their valuable contributions to our industry.
The Western Australia branch recently hosted a technical meeting, with Gilles Dour (Principal Asset Integrity Engineer, Worley) delivering a highly engaging presentation.
Gilles is a qualified mechanical engineer, who completed his undergraduate degree in France, followed by a Masters and PhD in Materials Science. He has been a Principal Integrity Engineer with the Worley group since 2013 when he joined the Transfield Worley Alliance. He has been part of the Advisian advisory group within Worley since 2015. Prior to this, he held roles with NOPSEMA and Applus RTD.
The pursuit of green steel (and iron) is now an important component of the world energy transition and the emerging move to hydrogen as an energy source. Several key steelmaking technologies that have been in development for the last several decades are now seeing a new focus on their ability to make economic use of hydrogen as their fuel source for the reduction of iron ores to iron.
One of the key aspects Gilles
acknowledged is that the industrial use of hydrogen has had a chequered past and was largely abandoned after the Hindenburg airship disaster in 1937. The explosive and highly flammable nature of hydrogen creates a very high risk for most industrial settings.
The traditional approach to iron ore reduction has been the pyrometallurgical use of blast furnaces (rather than leaching, which is common for base metals), or electrical processes, as with aluminium. Gilles then used the Ellingham diagram to show the attractions of using carbon in the iron reduction process. The Gibbs Energy curve versus temperature for carbon trends in the opposite direction to all the metal curves, allowing the reduction to take place at lower temperatures making it very economical (energy efficient).
The benefits of adopting this within a blast furnace environment is that this is a continuous solid-gas counter-current shaft reactor: solids pass top-down and the gas travels bottom up through the porous bed of coke and iron ore. Air injection at the base of the furnace
reacts with the solid coke to produce the CO, which reacts with the iron ore to produce iron metal. Then, in its molten form, this then reacts with the coke at the bottom to produce the carbon rich pig or cast iron (which is later converted or refined into steel). The additional benefit is that the rising high temperature gases (at circa 1,300°C) preheat the incoming solids. Ultimately, reduction of the ore by the CO produces CO2, which has always been vented to the atmosphere. This CO2 will now need to be captured or mitigated.
The question Gilles posed for the audience was whether we can also use hydrogen to reduce iron ore? The hydrogen curve on the Ellingham diagram shows that this in indeed possible, and in practice it has always been part of the ore reduction process. More recently, iron and steel makers have used pulverised coal injection (pci) to add more hydrogen. Other facilities will inject steam typically into the hottest part of the furnace.
Established steelmakers with operating blast furnaces are currently looking at converting them to new generation
designs that incorporate direct H2 injection (positioned above the current air injection points).
Current technologies looking to adopt hydrogen as a reductant, replacing some or all carbon include the following:
• The Midrex Reactor (developed in conjunction with Kobe in Japan)
• Direct Reduced Iron – also Midrex and HiSmelt
• Hybrit in Sweden (inclined rotary kiln)
• Fluidised Bed Reactors, such as the FinMet Reactor, that can use finer crushed ores
• Flash Reactors (currently being pilot tested)
• Moving Grate Technology
Many of these technologies will use a syngas (a mixture of CO and H2) as fuel and chemical reductant. The feed will often be iron ore pellets (to ensure gas permeability) and as a result they are temperature limited to 1,000°C, to prevent breakdown of the pellets (which would result in clogging and bridging of the furnace). Some of the technologies have utilised pellets with a CaO coating
to allow some higher temperatures to be achieved. These technologies operate with an excess of hydrogen is needed and this is recycled with the syngas fuel.
In terms of their current development status:
• Midrex seems to be the closest to full commercialisation, utilising syngas, which means it is defined as ‘blue hydrogen’. There are 14 DRI projects in Europe looking at this technology.
• The Hybrit process in Sweden looks to be the closest to using true hydrogen and will create ‘green steel’ (or iron). The storage and safe management of the large volumes of hydrogen required is still seen to be an issue.
• The Finmet process, which was the basis of the DRI/HBI project in Port Hedland is now being reconsidered for green steel production and Siemens and Posco have two live and active developments in play.
Gilles noted that many of these technologies are batch style processes, which creates production limitations (typically 2.5 Mtpa). In contrast, blast
furnaces can produce up to 10MTpa. However, moving grate technology seems promising in that it is continuous and can use any solids and allows easy variation in the gas feed, high reactivities and also allows easy options for recycling.
Gilles pointed out that all these projects will have additional complexities and costs for:
• Additional iron ore preparation stages (such as sintering of iron ore pellets)
• Accounting for the green energy supply to power electrolysis reactors to produce hydrogen
• Additional equipment to recycle (and possibly store) the unconsumed hydrogen gas
The presentation was well received by the audience and prompted many questions from the audience covering the use of magnetite, alternative gas production technologies (Hazer technology, which produces H2 and graphite) and the opportunity to bring these iron and steel making technologies closer to the iron ore source (as in the Whyalla model).
Source: Prof. Tim Sercombe (UWA) and Mike Brameld (Woodside)
Western Australia members were treated to a site visit of Woodside FutureLab TEchworks at University of Western Australia in late April.
This visit provided an opportunity for our long-standing National Honorary Secretary, Mike Brameld, to describe some aspects of his ‘day job’ at Woodside Energy. Mike has been responsible for establishing the FutureLab collaboration between Woodside and the University of Western Australia (UWA).
FutureLab is founded on many years of major research collaborations between the two organisations but takes these to a new level that enables what Mike referred to as ’effortless collaboration’. Established two years ago, with its own building on the UWA campus, and based on standing legal
agreements, FutureLab is designed to lower the overheads of establishing research agreements, and to encourage university academics and researchers to participate in commercially focused research and development.
While the overall FutureLab agreement encompasses both offshore and onshore research and development, the focus of the visit was on the TechWorks unit chaired by Professor Tim Sercombe, who is also Dean and Head of the School of Engineering at UWA. The major current project area for TechWorks is Additive Manufacturing. The overall aim of this work is to develop 3D printing as a business-as-usual activity for Woodside.
As Mike explained, the driver for this development is the recurring, and increasing, need for replacement parts
and components that are subject to corrosion and wear, both offshore and in Woodside’s onshore oil and gas processing plants. After more than 30 years’ operation, many replacement parts are no longer available off-theshelf or, indeed, at all. There are huge cost benefits both in having timely access to replacement parts, and in not requiring duplication using original production methods that were designed for high-volume production.
The challenge placed on Mike and Tim was to get a solution to this problem within two years. This was a ‘stretch target’ by any definition of the term. The way forward was to extend collaboration in the FutureTech program to Curtin and Monash universities, so that it is now a four-way collaboration, based on the same ideal of effortless collaboration. The team also secured the support of
the EOS Group, a leading manufacturer of industrial 3D metal printing equipment, who supplied an EOS M290 unit for research and prototyping.
The first task that TechWorks undertook was to select a single alloy that would satisfy all Woodside’s 3D printing requirements.
The explanation is that a single approved alloy reduces, and ideally eliminates, the risk that the wrong alloy can be specified. This is a constant concern as the consequences of wrong choices can be disastrous. This goal is economically feasible because the cost of the metal in 3D printing is typically only around 25% of the total.
The first campaign was to identify a set of candidate nickel-based alloys that are commercially available in powder form, make 3D printed test pieces and test their mechanical and corrosion properties. Tim showed a number of microstructures from these tests,
pointing out the typical extremely fine ‘nano-grains’ within the columnar grain structures.
Tim also showed some which differed in having ‘black dots’ of around 50 μm diameter. These were oxides, which had originated in the manufacture of the powder. It might have been an interesting research project to track down the cause in more detail, but the goal of the research was to find a suitable available powder, and indeed, this was found. The alloy, and its supplier, selected for further development is Inconel 625.
Testing showed that when 3D printed this alloy produces parts with adequate yield (above 600 MPa), ductility (around 30% elongation), corrosion resistance and Charpy energy above 300 J at liquid nitrogen temperature. With the alloy selected, the work then moved to manufacture of parts. The current research covers design, prototyping and monitoring build quality during printing,
as well as education and training.
The example Tim used was design of a replacement deluge nozzle. Corrosion is taking its toll on the hundreds of these safety-critical items which are installed across Woodsides’ operations. They are no longer available from the original manufacturer and the quoted cost for each of these domestic-scale nozzles is around $4,000 apiece.
Tim showed the progression of 3D printed prototypes, starting with a direct copy, to a similar version optimised for 3D printing, to what he described as the result of ‘generative design’. This used the capabilities of 3D printing to retain the functionality of the nozzle but with a different form and reduced material requirement. However, TechWorks does not make parts for Woodside to use. Instead, it establishes designs that Woodside issues to commercial 3D printing businesses for production.
The EOS M290 machine has facilities for melt pool monitoring and optical tomography as the part is built-up. Another project is using these to develop “signatures” for defects. Parts are formed with variously sized and shaped internal voids that simulate defects. The idea is to use these rather like calibration blocks that can be used as manufacturing quality checks.
This led to a discussion on how to qualify parts in the absence of established standards. Mikes’ response is that what matters is performance; when parts are seen to perform well, the codes and standards will follow. He explained that standards are formed when people get comfortable with the level of risk involved. This is essentially a social rather than an engineering issue.
The talk concluded with Mike’s comment that what TechWorks is doing represents a change in mindset. It’s no longer about using 3D printing for rapid prototyping; it’s about production.
Tim then conducted at tour of the facility where the machine could be seen in operation and a selection of intricate components could be handled and admired, with the members of the research and development team available to explain the fascinating details of their design and production features.
palladium catalysts
thin lm
nickel foam
buckyballs
MOFs
Nd:YAG
alternative energy
99.9999% aluminum oxide
glassy carbon
III-IV semiconductors
europium phosphors
diamond micropowder
additive manufacturing
organometallics
nanogels surface functionalized nanoparticles
YBCO
MOCVD
AuNPs
EuFOD
InAs wafers
nanodispersions
isotopes
ultralight aerospace alloys
metamaterials
borophene
osmium
h-BN
3D graphene foam
titanium aluminum carbide
niobium C103
quantum dots
transparent ceramics
radiation shielding
sputtering targets
endohedral fullerenes
gold nanocubes
tungsten carbide
tantaloy 60
photovoltaics
graphene oxide
UHP uorides
silver nanoparticles
scandium powder
rare earth optical ber dopants
OLED lighting
laser crystals
biosynthetics
exible electronics
GDC
perovskite crystals CIGS
ultra high purity materials
metallic glass
NMC
ITO
zircaloy -4
mischmetal
chalcogenides
carbon nanotubes
CVD precursors
deposition slugs
platinum ink
superconductors
Over 35,000 certi ed high purity laboratory chemicals, metals, & advanced materials and a state-of-the-art Research Center. Printable GHS-compliant Safety Data Sheets. Thousands of new products. And much more. All on a secure multi-language "Mobile Responsive” platform.
pyrolitic graphite
American Elements Opens a World of Possibilities..... Now Invent!
rare earth metals
mesoporus silica
www.americanelements.com
99.99999% mercury
Invar InGaAs
zeolites
Ti-6Al-4V
metallocenes
li-ion battery materials
SOFC powder
In early May, the Western Australia branch hosted a technical meeting, which saw Jeremy Reuben (Materials Engineer, LMATS) deliver a highly informative talk.
Jeremy obtained his Materials Engineering degree from the University of Western Australia in 1999. He started his career at the Perth Mint, where he developed his expertise in heat treatment of stamping dies. He then spent 15 years with Hoffmann Engineering, as their Heat Treatment Manager, before moving to a specialist role with LMATS. His work at LMATS covers materials engineering consulting, materials testing, failure analysis, corrosion and welding assessments, materials selection, and procedure development.
Many years of experience has taught Jeremy that investigating fractures and corrosion is only looking at the last stage of a failure process. Pinpointing their root cause is more complicated, and when the cause is found, whether anyone is really interested in doing anything about it can be a moot point.
Jeremy ruefully provided an example of root cause analysis by showing a photograph of his car, which had been hit by another vehicle when parked outside his house that morning. Whatever the reasons why the other driver had come to collide with his car, the root cause was that he had not parked his car in his carport.
Jeremy noted that it is very common for failure analysis reports to lack appropriate feedback that clients can use to avoid recurrence. He has seen how recurring failures lead to a cycle of
the ‘blame game’, or ‘spin the wheel to choose a cause’. The eventual result can be disaster.
He illustrated this observation with a case study of the collapse of a gantry over a tank, an incident that had resulted in a fatality. The ultimate failure was due to corrosion. However, this corrosion arose because the designer’s material recommendation had been overridden and a cheaper, inappropriate material had been substituted. At an even deeper level, the cause could said to be cultural: cost ahead of safety, or lack of knowledge of potential consequences, summarised as poor risk management. Jeremy singled out NDT as an area where misplaced confidence ’thinking you know how to interpret the observations’ can lead to poor assessment of risk.
Jeremy then went through the analysis of a sheave bolt failure. The failure was due to fatigue, with multiple initiation points originating in corrosion pits. However, the loading had a bending component. On further investigation of the sheave, the bending was found to have arisen because the face was not square to the bolt hole. Failure analysis involves more than just looking at the failure surface; it is essential to understand the loading.
He then gave a couple of examples of failures that were traced to faulty heat treatment. The root causes were pressure to take short cuts with heat treatment, especially with normalising, which is slow, expensive and to people who don’t understand materials, doesn’t seem to be doing much.
Another heat treatment example involved a ball mill liner retaining bolt that had cracked before being put into
service. Detailed SEM investigation showed that the crack was oxidised internally. Eventually the cause was traced to thermal shock when the room temperature bolt had been put into a furnace at 900°C for austenitising. The cure was to preheat to 500°C.
Jeremy then outlined his thoughts on prevention of unexpected materials failures, starting with top-down culture. Better training and procedures for materials selection, certification and testing and NDT needs to be combined with improved planning, design and review, and understanding of manufacturing methods. He noted that having more people involved in quality systems often seems to be accompanied by a decline in quality. The number of ‘boxes ticked’ can become the measure of quality, rather than fitness for purpose.
Jeremy had raised the question of who might want to act on advice as to root causes of failure. For example, OEMs are not necessarily interested in how profitable replacement parts might be improved. In other cases, failure analysis can be the basis for damages claims. This topic was taken up during question time. Sometimes there may be a sense that failure analysis is conducted to ‘keep up appearances’ of taking action, when in the end, nothing is changed. Often, this is something that materials people engaged in failure analysis have to accept, and just stick to the brief of describing the immediate cause of failure. In other cases, there is opportunity to take the extra step of identifying the (or a) root cause, as long as this can be done within budget!
10 TH INTERNATIONAL LIGHT METALS TECHNOLOGY CONFERENCE
9-12 JULY 2023 RMIT UNIVERSITY, MELBOURNE, AUSTRALIA
The Light Metals Technology (LMT) Conference is a biennial event that focuses on recent advances in science and technologies associated with the development and manufacture of aluminium, magnesium and titanium alloys and their translation into commercial products. The conference presents an opportunity for academic researchers, students and industry to discuss cutting edge developments and to facilitate new collaborations.
You are invited to submit abstracts on topics within the themes of Net Shape Manufacturing, Solid State Transformations and Mechanical Performance, and Translation to Applications. For example, but not limited to:
Opportunities for sponsorships and exhibitions are available, see below for contact details.
▶ Alloy development
▶ Solidification and casting
▶ Thermomechanical processing and forming
▶ Machining and subtractive processes
▶ Mechanical behaviour of light metal alloys
▶ Corrosion and surface modification
▶ Advanced characterisation techniques
▶ Joining
▶ Applications in bio-medical, automotive, aerospace, and energy industries
▶ Simulation and modelling
▶ Integrated computational materials engineering
For over 10 years, the Materials Australia’s End of Year function in Victoria has been a free event opened to members of sister professional societies such as the Australasian Corrosion Association Inc., Australian Ceramics Society, Australian Foundry Institute of Victoria, Alternative Technology Association, and Contract Heat Treatment Association of Australia.
This has been possible with the generous sponsorship of Phillips Ormonde and Fitzpatrick (Patent Attorneys) who first hosted this event in 2011. Since then, Phillips Ormonde and Fitzpatrick (pof) have continued to host the annual end of year (EOY) function which has become a highlight of the combined technical calendar for each of the participating professional bodies (a couple of events were necessarily missed during Covid).
The EOY evenings are an informal mix of networking, social conversation, and technical presentations conducted over some first class refreshments provided by the hosts, while enjoying a spectacular view over the north-eastern end of Melbourne afforded from the pof premises at 333 Collins St.
The event provides an opportunity for members from several professional bodies to listen to their colleagues give presentations related to new technologies or new challenges in technical areas, and also hear informative presentations by pof staff on IP aspects of such new technologies and challenges.
In keeping with the key interests of the audience, the technical presentations have included talks on new anticorrosive systems (both discovery and sensing), challenges in NDT, IP aspects of sensors and their applications, new carbon composite power line conductors for bushfire prone areas, processing of ultra-high temperature ceramic materials, successful commercialisation strategies, materials technologies for
Future Manufacturing, ceramic tiles and unintended mishaps, 3D printing of titanium and IP aspects of 3D printing. Sometimes the presentations can also be quite humorous, such as that from Jim Arthur (of CAST CRC) who talked of the pitfalls that can arise when competing interests recognize the value of IP that has been generated as part of a previously ‘friendly’ endeavour.
The 2022 event saw a presentation on the “Battery Electric Vehicle Fire Safety Challenge” from The Basic Group. The presenters for the evening were Jonathan Duler (Managing Director), Oscar Salt (Engineering Manager) and Jonathan Barnett (Technical Expert).
The presenters discussed the widespread engineering challenge that is associated with battery electric vehicles (BEV’s). One for which there is virtually no data, guidance, time, or money to solve the problem.
The speakers covered the historical context of the new risk presented by BEVs, some case studies of fires around the world and how our regulators and our engineers are responding. We heard that the challenge is current, for example, in September 2022, China reported seven BEV fires a day. The talk challenged those present to understand
the key issues and identified how we, as professionals, are needed to find a way forward.
The EOY event is scheduled again for late 2023, information will be forthcoming on the Materials Australia website and through all sister societies.
FUNDAMENTALS OF TITANIUM
CONTINUING EDUCATION WORKSHOP
The ITA is offering the Fundamentals of Titanium / Titanium the Ultimate Choice workshops in an in person format.
This comprehensive workshop will provide attendees with detailed information on the types, uses, and properties of common titanium alloys. Attendees will leave with an understanding of applied titanium metallurgy fundamentals.
Objectives & Content
Fundamentals of Titanium will prepare you to work effectively with job related functions that involve titanium. You will receive a complete overview of the titanium industry and a thorough grounding in its metallurgy, characteristics, properties and uses.
This workshop is brought to you by LMT2023 (Light Metals Technology 10-12 July 2023) www.lmt2023.com.au and sponsored by DMTC Ltd.
SESSION 1
• History
• Titanium from Ore to Metal
• Titanium Alloys and Heat Treatment
• Titanium Characteristics
• Corrosion
• Forming
SESSION 2
• Joining
• Finishing
• Properties & Design
• Comparisons with other Metals
• Applications
• Safety
• Recent Technology Advances
Donald E. Larsen
Donald E. Larsen is currently President of KineTic Engineering a consulting firm that provides expertise across the Titanium industry. Prior to this he spent over 30 years at Howmet Aerospace/Arconic retiring in 2018 as Vice President, R&D, General Manager Advanced Manufacturing for Arconic. In this role, he was responsible for leading R&D and production teams working on priority titanium technology projects, including 3D printing and advanced manufacturing activities. He also served as a liaison to the Arconic Technical Center (ATC) and Arconic’s Whitehall Technology Center. Don retired in Q3 of 2018 and temporarily took on the role of Interim Plant Manager Ti-Ingot Operation and Director of Special Projects.
Don joined Howmet Aerospace in 1988 and served in a number of roles focused on the research, development and production of titanium products. He has also held operational and sales and marketing roles with the company. Don has a master’s degree in metallurgical engineering from The Ohio State University, and is the holder of 11 U.S. patents. He has published more than 30 technical articles in the field of titanium.
$450+GST MA MEMBER
$500+GST NON MEMBER
$250+GST STUDENT
NOW
Enquiries: Tanya Smith Materials Australia +61 3 9326 7266
imea@materialsaustralia.com.au
Her work has been trialled on the Plasma Giken PCS 1000 fullscale industrial cold spray system (at CSIRO Lab 22) to great success. The outcomes of Tzu-Ying's research have shown effective control over biointerfacial interactions, showcasing the potential for improved biomedical devices for in vitro and in vivo applications.
Tzu-Ying has published seven research papers in prestigious journals and has presented her work at the renowned international conferences of 64th TwIChE Annual Meeting (Taiwan in 2017), MISE (Melbourne in 2020), ACSSSC (Adelaide in 2022), ASBTE (Melbourne in 2022), and Steven’s conference (USA in 2023).
(L to R): Dr Helmut Thissen (Team Leader for Biomaterial Surfaces and Devices, Director of Biomedical Materials Translational Facility, CSIRO); Tzu-Ying Liao (PhD student, SEAM, Swinburne University of Technology); Dr Peter King (Team Leader for Deposition and Additive Structures, CSIRO); and Professor Peter Kingshott (Deputy Director of SEAM, Swinburne University of Technology).
Tzu-Ying is a PhD candidate with the Surface Engineering for Advanced Materials (SEAM) Australian Research Council (ARC) Industrial Transformation Training Centre at Swinburne University of Technology.
Tzu-Ying completed her Bachelor of Chemical Engineering (2016) and Master of Chemical Engineering (2019) at National Taiwan University. Throughout the course of her career, Tzu-Ying has gained skills in coating manufacture, polymer synthesis, and chemical and mechanical characterisation methods. She has specialised in combining these skills with biological research and development, using eukaryotic cells, bacterial cultures, and animal studies.
Tzu-Ying commenced her career as an interns at the Chinese Petroleum Corporation (CPC) Training Centre in Taiwan where she first experienced industrial-scale science. This internship sparked her interest in industrial-scale problem solving and inspired Tzu-Ying to move to Melbourne for a six month internship with CSIRO for the final year of her Masters to work on coatings for biosensors. Combining functional engineering with biological science for a real-world application was a game-changer. Tzu-Ying wanted to peruse this type of R&D and so began her PhD journey at Swinburne University and SEAM in November 2019.
Tzu-Ying’s current PhD research is in collaboration with CSIRO (Lab 22)—renowned as Australia's leading centre for innovation in metallic additive manufacturing. Her PhD is focused on the development of antimicrobial thin films using cold spray to control infections in polymer-based biomaterials. Cold spray is a solid-state coating process that deposits particles onto a substrate at supersonic speeds to achieve surface functionalization.
At CSIRO, she has been involved in several commercial projects and collaborated with team leaders, senior research scientists, and postdoctoral researchers. The real-world problems Tzu-Ying works on at CSIRO aren’t confined to a single discipline. As such, Tzu-Ying uses her strong technical expertise in biology, engineering, chemistry and manufacturing to work within multi-disciplinary teams on these multi-discipline problems.
To build on her technical expertise, Tzu-Ying has learned to coordinate multiple projects, engage in strategic planning and adhere to strict timelines to ensure the timely delivery of highquality outcomes, particularly during the challenging times of the COVID-19 pandemic.
Tzu-Ying's academic journey and experiences reflect her passion for advancing the field of materials science, specifically in the development of functional coatings for antimicrobial applications. As a female scientist and engineer, Tzu-Ying is paving the way for greater diversity and encouraging future generations of women to pursue a successful career in STEM. Tzu-Ying's involvement in International Women's Day reflects her commitment to creating a more diverse scientific community. With her expertise and ongoing research efforts, she is ready to make significant contributions to the field by addressing critical issues in the biomedical sector and furthering our understanding of surface engineering with the use of advanced materials.
Acknowledgement: This work has been supported by the Australian Research Council (ARC). The ARC Training Centre in Surface Engineering for Advanced Materials, SEAM, has been funded under Award IC180100005. The additional support from industrial, university and other partners is critical for our success.
For more information about SEAM, please visit www.arcseam.com.au/ or email seam@swinburne.edu.au
The fifth International Materials Innovations in Surface Engineering (MISE) conference will be convened in Brisbane, Australia. The conference will be located at the state-of-the-art St Lucia Campus of the University of Queensland: twenty minutes from the centre of Brisbane.
MISE2023 features eminent academic and industrial plenary, keynote and invited speakers who encompass the engineering modification of a material’s surface to improve its performance.
The conference will cover topics such as:
> Coatings and Thin Films for Extreme Industrial Environments
> Surface Modification for Industrial Applications
> Surface Modification for Biomedical Applications
> Modelling and Simulation related to Surface Engineering
> Vacuum Deposition Coatings and Technologies: PVD and CVD
> Thermal Spray Coatings and Technologies
> Weld Overlays and Technologies
> Laser Processing and Technologies
> Characterisation of Surfaces, Coatings and Films
> New Horizons in Coatings and Thin Films
> Educational and Training of Early Career Researchers in Surface Engineering
> Case Histories for Surface Engineering, including Failure Analysis
> Corrosion, Bio-corrosion and Coatings for Corrosion Protection
> Wear of Materials
> Surface modification for Wear and Corrosion Resistance
Abstracts
Abstracts open 1 December 2022 and can be submitted online through the MISE website - www.mise2023.com.au
• Guidelines and an abstract template can be downloaded
Sponsorship and Sponsorship and Industry Displays
A number of limited sponsorship packages will be available. There will also be opportunities for sponsors to reserve space to exhibit their products and technologies. Please see the MISE2023 website for details.
Why should you participate in MISE?
Enquiries
Tanya Smith
Materials Australia
+61 3 9326 7266
imea@materialsaustralia.com.au
SPONSOR
•Networking opportunities to kick-off and maintain your research profile
•Interacting with leading, global industrialists to promote future activities
•Contribute to your Continuing Professional Development (CPD) portfolio Learn of the emerging manufacturing technologies that are on the near-term horizon
The following members of Materials Australia have been certified by the Certification Panel of Materials Australia as Certified Materials Professionals.
They can now use the post nominal ‘CMatP‘ after their name. These individuals have demonstrated the required level of qualification and experience to obtain this status. They are also required to regularly maintain their professional standing through ongoing education and commitment to the materials community.
We now have nearly 200 Certified Materials Professionals, who are being called upon to lead activities within Materials Australia. These activities include heading special interest group networks, representation on Standards Australia Committees, and representing Materials Australia at international conferences and society meetings.
A/Prof Alexey Glushenkov ACT
Dr Syed Islam ACT
Prof Yun Liu ACT
Dr Karthika Prasad ACT
Dr Takuya Tsuzuki ACT
Dr Olga Zinovieva ACT
Prof Klaus-Dieter Liss CHINA
Mr Debdutta Mallik MALAYSIA
Prof Valerie Linton NEW ZEALAND
Prof. Jamie Quinton NEW ZEALAND Dr Rumana
Edgar Mendez
Sam Moricca
Anna Paradowska
Elena Pereloma
Sophie Primig
Gwenaelle Proust
Zhijun Qiu
Waldemar Radomski
Ehsan
Nima
Miss Ana Celine Del Rosario VIC
Dr Yvonne Durandet VIC
Dr Mark Easton VIC
Dr Rajiv Edavan VIC
Dr Peter Ford VIC
Mr Bruce Ham VIC
Ms Edith Hamilton VIC
Dr Shu Huang VIC
Mr Long Huynh VIC
Mr Russell Kennedy VIC
Mr Daniel Lim VIC
Dr Amita Iyer VIC
Mr Robert Le Hunt VIC
Dr Michael Lo VIC
Dr Thomas Ludwig VIC
Dr Roger Lumley VIC
Mr Michael Mansfield VIC
Dr Gary Martin VIC
Dr Siao Ming (Andrew) Ang VIC
Mr Glen Morrissey VIC
Dr Eustathios Petinakis VIC
Dr Leon Prentice VIC
Dr Dong Qiu VIC
Mr John Rea VIC
Miss Reyhaneh Sahraeian VIC
Dr Christine Scala VIC
Mr Khan Sharp VIC
Dr Vadim Shterner VIC
Dr Antonella Sola VIC
Mr Mark Stephens VIC
Dr Graham Sussex VIC
Dr Kishore Venkatesan VIC
Mr John Edgley
Dr Jayantha Epaarachchi
Jeff Gates
Mr Payam Ghafoori
David Harrison
Dr Damon Kent
Miss Mozhgan Kermajani
Mr Jeezreel Malacad
Dr Jason Nairn
Mr Sadiq Nawaz
Mr Bhavin Panchal
Mr Bob Samuels
Dr Mathias Aakyiir
Mr Ashley Bell
Ms Ingrid Brundin
Mr Neville Cornish
A/Prof Colin Hall
Mr Nikolas Hildebrand SA
Mr Mikael Johansson SA
Mr Rahim Kurji SA
Mr Andrew Sales SA
Dr Thomas Schläfer SA
Dr Christiane Schulz SA
Prof Nikki Stanford SA
Prof Youhong Tang SA
Mr Kok Toong Leong SINGAPORE
Mr Madhusudhanan Jambunathan UK
Mr Devadoss Suresh Kumar UAE
Dr Shahabuddin Ahmmad VIC
Dr Ossama Badr VIC
Dr Qi Chao VIC
Dr Ivan Cole VIC
Dr John Cookson VIC
Mr Pranay Wadyalkar VIC
Dr Wei Xu VIC
Dr Ramdayal Yadav VIC
Dr Sam Yang VIC
Dr. Matthew Young VIC
Mr. Mohsen Sabbagh Alvani WA
Mr Graeme Brown WA
Mr Graham Carlisle WA
Mr John Carroll WA
Mr Sridharan Chandran WA
Mr Conrad Classen WA
Mr Chris Cobain WA
Mr Adam Dunning WA
Mr Jeff Dunning WA
Dr Olubayode Ero-Phillips WA
Mr Stuart Folkard WA
Mr Toby Garrod WA
Prof Vladimir Golovanevskiy WA
Mr Chris Grant WA
Mr Paul Howard WA
Dr Paul Huggett WA
Mr Ivo Kalcic WA
Mr Ehsan Karaji WA
Mr Biju Kurian Pottayil WA
Mr Mathieu Lancien WA
Mr Michael Lison-Pick WA
Dr Evelyn Ng WA
Mr Deny Nugraha WA
Mrs Mary Louise Petrick WA
Mr Johann Petrick WA
Mr Stephen Rennie WA
Dr Mobin Salasi WA
Mr James Travers WA
Source: Materials Australia
Accreditation as a Certified Materials Professional (CMatP) gives you recognition, not only amongst your peers, but within the materials engineering industry at large. You will be recognised as a materials scientist who maintains professional integrity, keeps up to date with developments in technology, and strives for continued personal development.
The CMatP, like a Certified Practicing Accountant or CPA, is promoted globally as the recognised standard for professionals working in the field of materials science.
There are now well over one hundred CMatPs who lead activities within Materials Australia. These activities include heading special interest group networks, representation on Standards Australia Committees, and representing Materials Australia at international conferences and society meetings.
Benefits of Becoming a CMatP
• A Certificate of Membership, often presented by the State Chapter, together with a unique Materials Australia badge.
• Access to exclusive CMatP resources and website content.
• The opportunity to attend CMatP only
networking meetings.
• Promotion through Materials Australia magazine, website, social media and other public channels.
• A Certified Materials Professional can use the post nominal CMatP.
• Materials Australia will actively promote the CMatP status to the community and employers and internationally, through our partner organisations.
• A CMatP may be requested to represent Materials Australia throughout Australia and overseas, with Government, media and other important activities.
• A CMatP may be offered an opportunity as a mentor for student members.
• Networking directly with other CMatPs who have recognised levels of qualifications and experience.
• The opportunity to assume leadership roles in Special Interest Networks, to assist in the facilitation of new knowledge amongst peers and members.
What is a Certified Materials Professional?
A Certified Materials Professional is a person to whom Materials Australia has issued a certificate declaring they have attained all required professional
standards. They are recognised as demonstrating excellence, and possessing special knowledge in the practice of materials science and engineering, through their profession or workplace. A CMatP is prepared to share their knowledge and skills in the interest of others, and promote excellence and innovation in all their professional endeavours.
The criteria for recognition as a CMatP are structured around the applicant demonstrating substantial and sustained practice in a field of materials science and engineering. The criteria are measured by qualifications, years of employment and relevant experience, as evidenced by the applicant’s CV or submitted documentation.
Certification will be retained as long as there is evidence of continuing professional development and adherence to the Code of Ethics and Professional behaviour.
Contact Materials Australia today: on +61 3 9326 7266 or imea@materialsaustralia.com.au or visit our website: www.materialsaustralia.com.au
ANSTO is celebrating 70 years since Australia began developing nuclear capabilities. Today, Australia is considered a highly sophisticated and complex nuclear nation.
ANSTO sits at the heart of the nation's nuclear capabilities and is the knowledge centre for nuclear science and technology. ANSTO also operates the nation’s leading nuclear facilities including the OPAL multipurpose research reactor; the Australian Synchrotron; nuclear medicine production facilities and many other significant landmark facilities. Other Government agencies including ARPANSA, ASNO and now ARWA also play important roles in Australia’s overall nuclear capabilities.
ANSTO’s mission is to provide knowledge, value and trust to the Australian Government and the people of Australia—delivering the social and economic benefits from the application of nuclear science and technology to benefit everyone.
Today, the accumulated learning of the last 70 years has formed the ANSTO of 2023 based on the development of knowledge, skills and capabilities over that time.
The nuclear infrastructure that has been developed is world leading—but it is only part of the story.
In addition to the talented people at ANSTO, young emerging scientists and engineers; collaborations with valued partners around the world means the picture is more complete. These elements form the foundation of ANSTO’s current nuclear capability and has paved the way for a future where Australia is an intelligent nuclear nation, ready to employ the different ways of using nuclear science and technology to continue to serve Australians well into the future. ANSTO is advancing science through modern nuclear and accelerator research techniques at world-leading facilities.
These include the Australian Centre
for Neutron Scattering, OPAL—a global centre for research enabled by our multipurpose reactor.
The Centre uses neutrons as a powerful tool to determine the atomic structure and properties of materials. Other national landmark infrastructure includes the Australian Synchrotron, the Centre for Accelerator Science and National Deuteration Facility.
Thousands of academics, representatives from other organisations, and industry access these facilities every year.
For many decades, ANSTO has undertaken research on the environment, human health (particularly the beneficial uses of radiation) as well as nuclear fuel, waste and nuclear technologies.
Through ANSTO, Australia is an established producer of nuclear medicine.
For example, molybdenum-99 (Mo99) Manufacturing Facility is among the most advanced manufacturing facilities for the supply of this critical Isotope in the world today.
It has the capacity to manufacture bulk Mo-99, supporting both the
domestic market and the global demand for technetium—99m generators (used in nuclear imaging).
ANSTO is also the global leader in the supply of neutron transmutation doped (NTD) silicon.
ANSTO also drives innovation in waste treatment technologies through the development of Synroc® , and the Synroc-Molybdenum (SYMO) Waste Treatment Facility.
This ‘first of a kind’ plant is progressing towards commissioning. Through ANSTO, Australia is also a leader in the development if radiation detection technologies with the launch of CORIS 360® the world’s most advanced radiation imaging system. It uses compressed imaging technologies to provide fast, accurate information in places where radiation is present.
CORIS 360® was the technology behind the successful and fast retrieval of the recent radioactive source in Western Australia.
ANSTO is a strong supporter for the Nuclear-Powered Submarine Taskforce and has played an important role in sharing expertise across key areas.
A new study that will help nuclearpropelled submarines to remain underwater—and undetected— for much longer, has put Monash University researchers in the global spotlight.
Professor Michael Preuss, a world expert in nuclear materials research, recently identified a critical corrosion mechanism of nuclear fuel cladding material that is affected by how the material is processed.
In nuclear submarines, the ultra-thin material, zirconium alloy, provides a barrier between the nuclear fuel and the water surrounding it. Until now, it’s been difficult to accurately predict the lifespan of the cladding. This wastes time, resources and potentially, millions of dollars.
“Nuclear submarines are expected to run for 25 years without refuelling, which contributes to them being highly undetectable,” Professor Preuss said. “In order to achieve this it is important to ensure that the life of the material encapsulating the nuclear fuel can be predicted.”
The research developments come as discussions heat up over AUKUS, the trilateral security pact between
Australia, the United Kingdom and the United States announced in 2021.
It will be the first time Australia has operated nuclear submarines, having used diesel-driven submarines—which unlike their more modern counterparts, require regular refuelling—until now.
Professor Preuss said the submarines would keep Australian waters open and safe. “The pandemic has demonstrated how vulnerable Australia is because the supply chain can be very easily interrupted. The submarines would increase the chances that the supply chain will not be interrupted because they’re a deterrent.”
Professor Preuss said the study findings are a timely reminder that Australia must do all it can to begin growing the skills needed to maintain, and eventually build, nuclear submarines.
“Australia is facing an unprecedented challenge in developing a skill base in nuclear within 15 years in which Australian universities will have to play a key role,” he said. “And it won't just be in one or two universities because the challenge is massive.”
To date, Professor Preuss said there
was very little research in Australia related to nuclear engineering, and more specifically, nuclear materials. However, Monash intends to lead the charge. Its latest research was mostly funded by the United Kingdom’s Engineering and Physical Research Council, with Rolls-Royce and Westinghouse also closely involved. Rolls-Royce, which powers Britain’s nuclear submarines, has also committed to funding two PhD students at Monash, in the area of nuclear materials.
Materials experts within Defence Science and Technology have also commissioned Monash to develop a report on the knowledge and skill base required in the field of nuclear materials.
Professor Preuss said Australia needs a strategy to develop its expertise. It comes as corrosion remains a huge financial burden globally, costing an estimated $US2.5 trillion each year. As part of the report, Monash will consult academics from various Australian universities, along with research organisations and industry in the United Kingdom and the United States.
Simufact and its technology partner toolcraft shows in a best practice case how additive manufacturing helps to save time and money in the production of prototypes.
MBFZ toolcraft GmbH from Georgensgmünd in Middle Franconia has optimized together with its software partner Simufact Engineering from Hamburg the additive production of a turbine wheel from ABB Turbo Systems AG. Typically, these components can be found in drive units of heavy machines and vehicles, such as diesel locomotives, off-highway trucks or dump trucks. Depending on the application, manufacturers
require the component to have a long service life and high wear resistance so that it can withstand mechanical and thermal loads.
Filigree blade geometries are typically produced by casting processes as an economical and robust production
process suitable for series production. However, before a new blade geometry can be used with the required properties, many tests are required for which prototypes or small batches of blades are required. In exceptional cases - depending on the number of parts required - the turbine blades required for testing can also be produced by casting in very small series. In general, these processes are very time-consuming and cost-intensive and therefore not much more than two prototypes are available to develop the
CHALLENGE: Transfer prototyping into serial manufacturing. Using the example of a ligree blade geometry we consider the challenges of traditional manufacturing.
SOLUTION: Generate variant diversity with the help of additive manufacturing. This technique helps you save time and money. Reach the rst-time-right approach through simulation.
USER: MBFZ toolcraft GmbH
nal product for use in series turbines. At this point, additive manufacturing has become a key technology that saves time and money. Furthermore, the technology offers a maximum exibility, one of the most important requirements in the eld of prototyping. W ith the help of this innovative manufacturing process, a variety of turbine blades can be produced in a very short time, which ultimately leads to a better product. This is where MBFZ toolcraft‘s high manufacturing competence throughout the entire valueadded chain in turbine blade production proves its worth. W ithin the framework of the cooperation between MBFZ toolcraft and ABB Turbo Systems AG, the products can be designed and implemented as 3D printing right from the start.
For MBFZ toolcraft, the greatest challenge in manufacturing prototypes is maintaining the required tolerances and dimensional accuracy. The decisive factor here is the component distortion caused by the AM process. In order to keep the distortions as low as possible, MBFZ toolcraft relies on Simufact Additive. By using the user-friendly and process-oriented simulation solution, MBFZ toolcraft makes it possible to signi cantly minimize distortions by means of suitable process parameters and to compensate where they cannot be avoided. In this way, MBFZ toolcraft can meet all required tolerances, thus eliminating the need for time-consuming reworking.
A closer look at the building process clearly reveals the challenges and problems.
Due to component geometry and thermal stress, high stresses occur during the building process. This is due to the special features of the geometry, which on the one hand has a solid core with a lot of material and volume, while on the other hand the blades are very ligree. As a result, there are large cross-sectional changes in the component, which favour the residual stresses during the manufacturing process. These in turn result in a high susceptibility to distortion.
MBFZ toolcraft solves this problem with a careful simulation-based as-is analysis in which critical areas are identi ed. From this, the necessary measures can then be derived to counteract the distortion problem. This includes the development of suitable support structures that generally minimize distortion and thus ensure a safe construction process. But the ideal alignment of the components to be printed on the base plate can also be very helpful in individual cases. The last step is an automated compensation of the remaining distortion based on a quantitative distortion analysis, with which the remaining distortion is determined. The results obtained in this way can be used to derive the print preparation. Thanks to the simulation, MBFZ toolcraft achieves a low-distortion component structure and can thus remain to its “ rst-time-right“ approach - to ful l all requirements on the component with the rst print. The use of additive manufacturing enables MBFZ toolcraft to react exibly and quickly to customer requests, such as design changes, and thus to signi cantly reduce project lead times. The virtual engineering offered by the powerful simulation solution enables signi cantly tighter processes in the process development of 3D printing projects. This approach can be realized through the reliable software Simufact Additive.
Source: ATA Scientific Pty Ltd
As the energy sector and transport industry seek to mitigate their environmental impact, green hydrogen will likely play a major role in achieving carbon neutrality, particularly in Australia as we decarbonise key industries such as steel making.
Green hydrogen is produced by the electrolysis of water using renewable energy sources, such as solar or wind power. Electrolysers based on polymer electrolyte membrane (PEM) technology provide an efficient pathway for producing green hydrogen through water electrolysis. By inverting the process, PEM fuel cells (PEMFCs) can be used to generate electricity using hydrogen as fuel. Fuel cells have the potential to make hydrogen a viable replacement for fossil fuels in energy, transport, and other industrial sectors. However, to achieve this on a large scale, their performance and cost must be optimised.
The catalytic material used to produce PEMFC electrodes, usually platinum-on-carbon (Pt/C), is the
main component in determining both the performance and the cost of fuel cells. Catalytic activity is governed by the size, dispersion, and morphology of the Pt-metal group nanoparticles. Equally important are the structural, textural, and surface chemistry properties. Catalytic activity and stability can be optimised in several ways: by controlling the particle size for maximum mass activity, ensuring uniform dispersion of Pt nanoparticles on the carbon support matrix or by developing novel Pt-alloy cathode materials.
Laser diffraction is a fast, nondestructive method suited for both laboratory and continuous in-line measurements and gives insights into the particle size distribution of the carbon-support particles. The wide measurement range of laser diffraction, from 10 nm to 3500 µm, is well suited to cover the coarse and fine agglomerates that may be present in a catalytic powder. While measurement of powder particles in a dry dispersion is possible, it is more common to measure them dispersed in a solvent such as isopropyl alcohol (IPA).
Figure 1 shows the particle size of Pt/C catalytic powders dispersed in IPA as determined using the Mastersizer 3000. Samples loaded with 60 % and 40 % Pt had similar size distributions. The powder containing 20 % Pt was different, with a significant population of smaller particles in the 1 µm size range.
The laser diffraction data reveals the most potentially significant difference between the three catalytic powders with different Pt loading levels. Differences in the initial particle size of Carbon could change the way the catalytic powder disperses in the ink, which is known to have a significant effect on the deposition process and thus the performance. It is unlikely that differences in Pt loading would affect the particle size distribution of Carbon support particles, suggesting that another process parameter may be changing during the production of the catalytic powders.
Automated morphological image analysis can also be used to analyse agglomerates of the C-support particles. Systems such as the Morphologi 4 image individual particles and produce a particle size distribution based on discrete particle counting. Particle imaging with the Morphologi 4 is advantageous because images of individual agglomerates can be retrieved, compared, and evaluated by parameters such as circularity, convexity, and roughness. Figure 2 shows a snapshot of particles imaged in 40 % Pt loaded catalytic powder. The agglomerates are nearly spherical not exhibiting any significant anisotropy to affect the ink processability. However, the roughness of the agglomerates could affect the ease of dispersion in the ink and the formation of porosity during deposition and drying.
Some alloys, such as platinum-cobalt (PtCo), are being studied with the aim
of reducing their costs by lowering the amount of precious metal required to produce PEMFCs. Other alloys such as platinum-ruthenium (PtRu) are being investigated with the aim of enabling reversible PEMFCs that can be used as electrolysers for H2 production and as fuel cells to generate electricity from H2. In Figure 3, laser diffraction analysis revealed that the C-support particle agglomerates had similar sizes for catalytic powders made with all three alloys.
Conclusion
Laser diffraction and automated image analysis can be effective techniques for analysing various properties of pure and alloyed Pt nanoparticles supported on a C matrix. Laser diffraction is ideal for analysing the particle size of C-support that influences the Pt dispersion and porosity in the catalytic active compound. Morphological imaging is valuable in providing images of individual agglomerates
to enable shape analysis. Together, these techniques can help optimise both the cost and performance of systems based on PEM technology by maximising catalyst efficiency, reducing the amount of Pt required or developing Pt-based alloy nanoparticles.
Contact us for more information today!
ATA Scientific Pty Ltd
+61 2 9541 3500 enquiries@ atascientific.com.au www.atascientific. com.au
ATA Scientific is a leading supplier of advanced scientific instruments and analytical services. They provide the tools and know-how needed to obtain meaningful and reliable analytical results. They do this by listening to their clients’ requirements and taking care to supply the most suitable technology and ongoing support.
ATA Scientific represents a group of highly regarded international companies, from Malvern Panaytical, Micromeritics and Avestin through to Thermo Fisher Scientific (Phenom desktop SEM), Micropore Technologies and Hauschild Speedmixer, to name a few. ATA's range of innovative instruments are applicable across the particle, surface, life and material sciences.
Established over 30 years ago, ATA Scientific has built an extensive customer base throughout Australia and New Zealand. This includes universities, the CSIRO and a diverse range of companies in the pharmaceutical, polymer, chemical and mining industries.
SPECIALIST ADVICE & TRAINING
Reference:
https://www.malvernpanalytical.com/en/ learn/knowledge-center/application-notes/ AN220419-Catalytic-Powders-PEM-Fuel-Cells
ATA’s people have an extensive range of skills and experience in analytical technologies, especially particle and biomaterial characterisation. Their team delivers ongoing applications assistance and advice regarding instrument operation and optimisation of data quality.
To help you get the best from your instrument, ATA Scientific also offers a range of events throughout the year including training courses, workshops and seminars. Training courses cover the fundamentals of the measurement technique, instrument operation, familiarity with software and data interpretation. Practical demonstrations form an important part of the training. A full range of technical services are provided by our engineers including operator training, preventative maintenance, repair and upgrades. ATA prides itself on long term support, so that you can enjoy the maximum benefit from their products and services.
Source: Sally Wood
Mobile phone batteries with a lifetime up to three times longer than today’s technology could be a reality thanks to an innovation led by engineers at RMIT University. Rather than disposing of batteries after two or three years, recyclable batteries could last for up to nine years. The researchers used high-frequency sound waves to remove rust that inhibits battery performance.
Only 10% of used handheld batteries, including for mobile phones, are collected for recycling in Australia, which is low by international standards. The remaining 90% of batteries go to landfill or are disposed of incorrectly, which causes considerable damage to the environment.
The high cost of recycling lithium and other materials from batteries is a major barrier to these items being reused, but the team’s innovation could help to address this challenge. The team is working with a nanomaterial called MXene, a class of materials they say promises to be an exciting alternative to lithium for batteries in the future.
Distinguished Professor of Chemical Engineering Leslie Yeo said MXene was similar to graphene with high electrical conductivity. “Unlike graphene, MXenes are highly tailorable and open up a whole range of possible technological applications in the future,” said Yeo from RMIT’s School of Engineering.
The big challenge with using MXene was that it rusted easily, thereby inhibiting electrical conductivity and rendering it unusable.
“To overcome this challenge, we discovered that sound waves at a certain frequency remove rust from MXene, restoring it to close to its original state,” Yeo said. The team’s innovation could one day help to revitalise
MXene batteries every few years, extending their lifetime by up to three times, he said.
“The ability to prolong the shelf life of MXene is critical to ensuring its potential to be used for commercially viable electronic parts,” Yeo said.
Co-lead author Mr Hossein Alijani, a PhD candidate, said the greatest challenge with using MXene was the rust that formed on its surface in a humid environment or when suspended in watery solutions. “Surface oxide, which is rust, is difficult to remove especially on this material, which is much, much thinner than a human hair. Current methods used to reduce oxidation rely on the chemical coating of the material, which limits the use of the MXene in its native form.”
The team says their work to remove rust from MXene opens the door for the nanomaterial to be used in a wide range of applications in energy storage, sensors, wireless transmission and environmental remediation.
Associate Professor Amgad Rezk, one of the lead senior researchers, said the ability to quickly restore oxidised materials to an almost pristine state represented a gamechanger in terms of the circular economy.
“Materials used in electronics, including batteries, generally suffer deterioration after two or three years of use due to rust forming,” said Associate Professor Rezk.
While the innovation is promising, the team needs to work with industry to integrate its acoustics device into existing manufacturing systems and processes.
The team is also exploring the use of their invention to remove oxide layers from other materials for applications in sensing and renewable energy.
Ease of use is what the Phenom
Pharos name has come to mean. All the capabilities of a floor-standing FEG-SEM have been housed in a tabletop model with the simplicity that Phenom desktop SEMs are known for.
Ease of use is what the Phenom Pharos name has come to mean. All the capabilities of a floor-standing FEG-SEM have been housed in a tabletop model with the simplicity that Phenom desktop SEMs are known for.
1. Super fast, sharp, high contrast images
Speeds up project work and provides high -end imaging and analysis critical for many fields from materials, forensics to industrial manufacturing and even life sciences.
2. Unsurpassed user experience
2. Unsurpassed user experience
2. Unsurpassed user experience
Easy to use without extensive training or SEM experience means the Phenom is accessible to everyone.
Easy to use without extensive training or SEM experience means the Phenom is accessible to everyone.
Easy to use without extensive training or SEM experience means the Phenom is accessible to everyone.
3. Multiple detectors reveal finer details
3. Multiple detectors reveal finer details
3. Multiple detectors reveal finer details
Fully integrated EDS and SE detector together with a low -kV beam (1 kV) allows thin contamination layers on the surface can be observed (Phenom Pharos).
Fully integrated EDS and SE detector together with a low -kV beam (1 kV) allows thin contamination layers on the surface can be observed (Phenom Pharos).
Fully integrated EDS and SE detector together with a low -kV beam (1 kV) allows thin contamination layers on the surface can be observed (Phenom Pharos).
4. Intuitive software with advanced automation
4. Intuitive software with advanced automation
4. Intuitive software with advanced automation
Simply click and go to work or use automated recipes with elemental mapping and line scan functionality.
Simply click and go to work or use automated recipes with elemental mapping and line scan functionality.
Simply click and go to work or use automated recipes with elemental mapping and line scan functionality.
5. Huge time and money saver
5. Huge time and money saver
5. Huge time and money saver
Provides rapid, multi -scale information in-house for process monitoring and improvement.
Provides rapid, multi -scale information in-house for process monitoring and improvement.
Provides rapid, multi -scale information in-house for process monitoring and improvement.
Phenom Perception GSR
Phenom Particle X SEM
• Field Emission Gun (FEG) SEM with 1 - 20 kV range
• Field Emission Gun (FEG) SEM with 1 - 20 kV range
• <2.0 nm (SE) resolution
• <2.0 nm (SE) resolution
• For large samples (100x100 mm)
• For large samples (100x100 mm)
• ideal for automation
• ideal for automation
• High performance desktop SEM
• High performance desktop SEM
• Fully integrated EDS
• Fully integrated EDS
• Automated GSR SEM
• Automated GSR SEM
• Dedicated for gunshot residue analysis
• Dedicated for gunshot residue analysis
• Automation software for Additive Manufacturing, Steel, Technical cleanliness and more
• Automation software for Additive Manufacturing, Steel, Technical cleanliness and more
✓
✓ COMPLETELY AUTOMATED
✓ COMPLETELY AUTOMATED
✓ UNIQUE A² TECHNOLOGY
✓ UNIQUE A² TECHNOLOGY
✓ COATING 1 to 100nm THICKNESS
✓ COATING 1 to 100nm THICKNESS
✓
✓ UPSIDE DOWN DESIGN
✓ UPSIDE DOWN DESIGN
✓
✓ TRIPLE FUNCTIONALITY
✓ TRIPLE FUNCTIONALITY
✓
✓ ROBUST DESIGN, MADE IN GERMANY
✓ ROBUST DESIGN, MADE IN GERMANY
ANSTO, in collaboration with BAE Systems Maritime Australia and the University of Wollongong, is working under the auspices of DMTC Limited to enhance advanced manufacturing techniques, such as robotic welding of large, stiffened ship panels for Hunter class frigates (Figure 1) and other maritime vessels through multi-physics high-fidelity and high-efficiency numerical simulations, supported by dedicated experimental work.
Although weldments are commonly associated with component failures, welding remains the most widely used joining technique in the manufacturing of engineering structures and assemblies. The welding process can, for example, introduce non-uniform microstructure, distortion, and residual stresses that can adversely affect manufacturing process as well as the performance of individual weldments, and ultimately the overall engineering structure. Welding-induced distortion is particularly significant in the manufacturing stage, as it can result in components that do not meet tolerances requiring costly rework. Additionally, if left unmitigated, welding-induced residual stresses can add to operational stresses, and thus exacerbate degradation mechanisms such as crack initiation and growth. Similarly, an unoptimized welding-induced microstructure can lead to premature failure, affecting the operational cost of the overall engineering system.
It is, thus, technologically important to mitigate the level of welding-induced distortion and assess the magnitude of residual stresses and the state of the microstructure when undertaking life and structural integrity assessments of welded structures. It is, however, not feasible to experimentally examine all weldments in a structure individually. Furthermore, it is prohibitively costly to experimentally optimize the welding procedures such as weld sequencing when manufacturing large panels
containing hundreds of individual welds. Numerical simulations are therefore an only vital tool in mitigating issues related to weldinginduced distortion, residual stresses, and microstructure affecting manufacturing and performance of welded structures.
ANSTO together with its industrial and university partners developed highfidelity and high-efficiency numerical simulation workflow outlined in Figure 2. The developed workflow allows to predict welding-induced microstructure, distortion, and residual stresses in T-joints while enabling weld sequencing optimisation for automated manufacturing of large, stiffened ship panels. As highlighted in Figure 2, the process begins with the manufacturing of small, instrumented T-joint benchmark specimens, followed by the development of high-fidelity and high-efficiency local welding simulations before moving on to the development of high-efficiency global welding simulations of large, stiffened panels and performing the weld sequencing optimization. After an optimized weld sequence has been identified, it can be translated into a robotic path program that can be used
for manufacturing on the factory floor.
To illustrate the impact of weld sequencing on welding-induced distortion, residual stresses, and microstructure, the developed highfidelity weld simulations of the small T-joint benchmark specimen shown in Figure 2 (top) were used to examine four different welding sequences. The examined sequences are outlined in Figure 3, along with resulting angular distortions. The results indicate that the weld sequencing has a noticeable effect on the final distortion, even when considering a small (200 x 300 mm) T-joint weldment.
Among the examined sequences, Sequence 1 ("sequential welding with interpass cooling"), in which the second weld is applied only after the cooling of the first weld, leads to the largest distortion (~2.3 mm). In contrast, Sequence 4 ("same direction tandem welding"), which applies both welds simultaneously in the single direction, leads to the lowest distortion (~1.5 mm). Sequence 2 ("sequential welding without interpass cooling"), which applies the second weld immediately after the first weld, and Sequence 3, which applies reversed direction tandem welding, lead to approximately
the same level of distortion (~1.8 mm). Overall, these findings demonstrate the importance of optimizing the weld sequencing to minimize weldinginduced distortion, particularly when manufacturing large, stiffened ship panels containing many welds. This example illustrates that by using numerical simulations to identify the optimal weld sequencing, we can enable the automated, low-distortion manufacturing of large, stiffened panels for maritime applications. However, while minimizing distortion which is essential for efficient manufacturing, it is also crucial to consider that different weld sequences lead to varying levels and distributions of residual stresses, as depicted in Figure 4 (top). These residual stresses can have adverse effects on the performance and durability of ship panels under operating in-service loading conditions. Additionally, altering the weld sequencing leads to modifications in the microstructure of the weld and the heat-affected zone, which impacts their mechanical properties, such as strength, hardness, and ductility. Figure 4 (bottom) highlights the effect of the employed welding sequences on the resulting
hardness, which is directly connected to the varying amounts of constitutive phases (i.e., martensite, bainite, ferrite, and perlite). Since not all constitutive phases have the same level of strength and performance (e.g., fatigue), one needs to make sure that the weld sequence optimisation does not lead to undesired post-welding microstructures.
To assess the effect of weld residual stresses on fatigue crack growth (i.e., fatigue life endurance), we conducted a fatigue crack growth analysis on T-joints produced using Sequence 1 leading to the worst distortion (Figure 3), and Sequence 4 leading to the smallest distortion. For comparison, an ideal T-joint without any pre-existing residual stresses was also considered. The results of the performed crack growth analysis, presented in Figure 5, demonstrates the impact of weldinginduced residual stresses on the kinetics of crack growth during fatigue loading. Specifically, the surface crack in an ideal T-joint without preexisting residual stresses requires approximately 3x105 cycles to grow to a depth of 3 mm. However, in the T-joint produced using Sequence 1, this occurs in approximately 1.5x105 cycles,
while in the T-joint produced using Sequence 4, it occurs in about 1x105 cycles.
It is worth noting that although Sequence 4 results in the smallest distortion, it also leads to the highest residual stresses and thus the fastest crack growth. This emphasizes the importance of considering multiple objectives when optimizing welding sequences. Focusing solely on reducing distortion may compromise other critical characteristics of the welded panel, such as fatigue life due to higher residual stresses and/or less fatigueresistant microstructure. To address this challenge, ANSTO and its partners are exploring the use of multiobjective optimization algorithms for weld sequencing. This approach will enable the manufacturing of lowdistortion ship panels with minimized levels of residual stresses and desired microstructure.
In conclusion, ANSTO, in collaboration with BAE Systems Maritime Australia and the University of Wollongong, is developing a high-fidelity and high-efficiency numerical simulation workflow to optimize welding sequences for automated, low-
distortion manufacturing of large, stiffened ship panels for Hunter class frigates and other maritime vessels. Through the use of numerical simulations, we been able to predict welding-induced microstructure, distortion, and residual stresses in T-joints and optimize the weld sequencing to minimize distortion while considering other critical characteristics of the welded panel such as fatigue life, residual stresses, and post-welding microstructure.
This research has significant implications for the maritime industry, where the efficient and reliable manufacturing of large, complex structures such as ship panels is essential. By using numerical simulations to optimize welding sequences, manufacturers can reduce the time and cost of producing these structures while ensuring their performance and durability under service loading conditions. Moreover, this research can be extended to other industries that rely on welding and additive manufacturing, such as aerospace and automotive, where distortions, residual stresses and unoptimized microstructures can also be significant challenges.
Researchers have developed an innovative technique for creating nanoscale materials with unique chemical and physical properties.
Scientists from UNSW Sydney have demonstrated a novel technique for creating tiny 3D materials that could eventually make fuel cells like hydrogen batteries cheaper and more sustainable. Researchers from the School of Chemistry at UNSW Science show it is possible to sequentially ‘grow’ interconnected hierarchical structures in 3D at the nanoscale, which have unique chemical and physical properties to support energy conversion reactions.
In chemistry, hierarchical structures are configurations of units like molecules within an organisation of other units that themselves may be ordered. Similar phenomena can be seen in the natural world, like in flower petals and tree branches. But where these structures have extraordinary potential is at a level beyond the visibility of the human eye— at the nanoscale.
Using conventional methods, scientists have found it challenging to replicate these 3D structures with metal components on the nanoscale. To understand just how small these tiny 3D materials need to be—in one centimetre, there are 10 millimetres. If you were to count one million tiny segments in just one of those millimetres, each of those would be one nanometre or nm.
“To date, scientists have been able to assemble hierarchicaltype structures on the micrometre or molecular scale,” said Professor Richard Tilley, who is the Director of the Electron Microscope Unit at UNSW and senior author of the study.
“But to get the level of precision needed to assemble on the nanoscale, we needed to develop an entirely new bottom-up methodology.”
The researchers used chemical synthesis, an approach that constructs complex chemical compounds from simpler
ones. They were able to carefully grow hexagonal crystal–structured nickel branches on cubic crystal—structured cores to create 3D hierarchical structures with dimensions of around 10-20 nanometres.
The resulting interconnected 3D nanostructure has a high surface area and high conductivity due to the direct connection of a metallic core and branches. These properties make it an ideal electrocatalyst support—a substance that helps speed up the rate of reactions—in the oxygen evolution reaction, a crucial process in energy conversion. The nanostructure’s properties were examined using electrochemical analysis from state-of-the-art electron microscopes provided by the Electron Microscope Unit.
“Growing the material step by step is a contrast to what we do assembling structures at the micrometre level, which is starting with bulk material and etching it down,” said Dr Lucy Gloag, who is the lead author of the study.
“This new method allows us to have excellent control over the conditions, which lets us keep all of the components ultra-small—on the nanoscale—where the unique catalytic properties exist.”
Nanocatalysts in fuel cells In conventional catalysts, which are often spherical, most atoms are stuck in the middle of the sphere.
In the next research stage, the scientists will look to modify the surface of the material with platinum, which is a superior catalytic metal though more expensive.
About a sixth of the cost of an electric car alone is the platinum powering the fuel cell.
“These exceptionally high surface areas would support a material like platinum to be layered on in individual atoms, so we have the absolute best use of these expensive metals in a reaction environment,” Professor Tilley said.
Bruker Nano Surfaces provides industry-leading surface analysus instruments for research and production. Bruker’s AFMs are enabling scientists around the world to make discoveries and advance their understanding of material and biological systems. Their tribometers and mechanical tests deliver practical data used to help improve development of materials and tribolocial systems.
Industry-leading quantitative nanomechanical and nanotribological test instruments are specifically designed to enable new frontiers in nanoscale materials characterisation, materials development, and process monitoring.
Whatever your surface measurement and surface analysis needs, materials or scale of investigation, Bruker has a specialised high-performance solution for you.
Tribology
Universal tribology platforms
Fast and cost-effective in-lab rapid screening of new friction materials
Nanoindentation
In-situ TEM/SEM nanomechanical instruments
Stand alone nanomechanical test systems
Wide range of environmental measurement options
Optical Profiling Next generation ContourX platforms
Improved optical resolution
Unmatched precision and repeatability
High-resolution AFM Microscopes
New NanoScope 6 platforms, improved speed and data capability
High resolution for all applications, all environments
AXT are excited to strengthen ties with the growing additive manufacturing sector by partnering with AMAZEMET. Founded in 2019, AMAZEMET design and manufacture systems for those involved with metal additive manufacturing, with products supporting everything from R&D to small-scale industrial scale production.
AMAZEMET is a spin-off of the Warsaw University of Technology. They successfully transferred ultrasonic atomisation technology, along with expertise in automated support removal and post 3D printing heat treatment, into state-of-the-art devices that are part of its portfolio, with systems now in action at institutions all over the world [[perhaps we could quantify this e.g. 300 instruments in 50 different countries]].
Their flagship system, rePowder is a fully customisable, modular designed system optimised to economically produce small quantities of highly spherical metal powders with narrow size distributions and free flowing characteristics, perfect for metal additive manufacturing. Using a unique process called ultrasonic atomisation, rePowder can produce powders
3D printing post-processing. safeEtch is a system that uses a patented chemical solution to remove supports from metal prints quickly and easily, producing a high-quality polished surface. inFurner is a compact vacuum furnace suited to the postheat treatment of 3D printed metal parts as well as the heat treatment of other materials requiring a controlled atmosphere.
Richard Trett, AXT’s Managing Director said, “3D printing is an extremely dynamic sector and we are excited by the prospect of becoming more involved by partnering with AMAZEMET to assist Australian researchers and companies to accelerate their development projects.”
Łukasz Żrodowski, AMAZEMET CEO responded, “We are currently experiencing rapid growth with systems being installed all around the world. It made sense for us to look at the Australian market and we are proud to partner with AXT on this journey which I am sure will yield results in the short term.”
For more details, please visit axt.com.au, where AMAZEMET’s products will augment AXT’s other 3D printing systems and related microscopy, metrology and computed tomography (CT) products lines.
The Rigaku CT Lab HX represents a large step forward in technology, with this benchtop system replacing a much larger Xradia system that AXT had also installed many years ago. The industrial client is well-versed in the use of microCT and selected the Rigaku system based on preliminary testing where they found the more compact system satisfied their requirements.
The CT Lab HX offers high-resolution 1.3 µm voxel resolution and wide 200 mm field of view. The highly versatile design also provides for adjustable
SOD (source-to-object distance) and SDD (source-to-detector distance), while X-ray sources up to 130kV and various filters enable users to adjust the system to cater for a various sample compositions and sizes. Furthermore, with scan speeds as fast as 18 seconds and auto sample loader the CT Lab HX is ideal for QC applications requiring rapid data and feedback.
A spokesman for the client commented, “microCT has become a crucial part of our workflow, helping us maintain and develop packaging solutions and maintaining product quality. We are extremely happy that we have been able to replace our old Xradia system with this much more compact Rigaku system that has slotted seamlessly into our environment.”
Richard Trett, Managing Director at AXT replied, “we are extremely happy that we been able to continue our long association with this customer who were an early adopter of microCT technology. The use of microCT is rapidly gaining momentum as both researchers and industrial companies better understand the benefits of non-destructive 3D imaging in product development and quality control.”
AXT have a broad portfolio of microCT solutions that suit everything from high-throughput industrial application to high-end academic research in life science, materials science and geological science. With system that cater for samples from the millimetre to meter size ranges, with subnanometre resolution, high temporal resolution and even spectral CT, click here.
UNIVERSITY SPOTLIGHT
Source: Sally Wood
Charles Darwin University (CDU) is a truly unique institution.
With its home and heart in the Northern Territory (NT), CDU embraces the inclusive, resilient, and courageous spirit of the NT. It provides globally recognised education to 21,000 students across campuses and delivery sites that reach a diverse footprint—from the capital cities of Darwin, Brisbane, Melbourne, Perth and Sydney, through to the regional hubs of Alice Springs, Palmerston and Katherine, and remote locations like Nhulunbuy and Tennant Creek.
Recognised worldwide for its outstanding commitment to research, CDU is also a global leader in their work towards the United Nation’s Sustainable Development Goals for Quality Education. The ranking has been welcomed by the educators of CDU, who work hard to ensure a wellrounded and excellent education for their students.
As a cross-sectoral institution, CDU assists students from around Australia and the world to become ‘futureready’ workers. Students develop the knowledge, skills and resilience to meet the challenges of an everchanging world and become lifelong learners who are equipped to find success in any sector.
The culture of CDU is deeply committed to sustainability, social justice, and collectively held values. They deeply respect the history and culture of Indigenous Australians, central to the Northern Territory locations of their campuses. CDU’s vision is to bring people together to collectively strive for excellence, integrity, accountability and equality of opportunity for all.
Named after one of the great observers and researchers of history, Charles Darwin University encourages curiosity, creativity, and the constant pursuit of knowledge.
CDU is a leader in research and innovation, making significant
advances in materials, manufacturing and engineering. Through collaboration with industry, CDU students are given the opportunity to gain real world experience and work with leaders within the sector.
The Faculty of Science and Technology provides students and researchers with state-of-the-art technology and an inspiring learning environment through several research organisations, including:
The Energy and Resources Institute provides high quality research and consultancy for all aspects of energy and resources, including engineering, scientific, economic, environmental, social, community, legal, policy and digital considerations.
The North Australia Centre for Autonomous Systems conducts integrated industry-focused research into the application of Autonomous Systems across industries, businesses, and other sectors in northern Australia and the Asia Pacific regions.
The Research Institute for the Environment and Livelihoods is a leader in tropical savanna and coastal research in north Australia. Research strengths include biodiversity conservation, savanna and arid adaptation and environments, water and catchments, and communities and livelihoods.
Advanced Manufacturing Alliance
CDU partnered with SPEE3D to form the Advanced Manufacturing Alliance, a joint initiative that utilises a worldfirst 3D metal printing technology. The Alliance aims to engage with industry partners, trades and academics.
SPEE3D printers are the world’s first metal 3D printing production cell, enabling the most affordable metal additive manufacturing process in the world. They make metal parts the fastest way possible, leveraging metal cold spray technology to produce industrial quality metal parts in just minutes, rather than days or weeks. The process harnesses the power of kinetic energy, rather than relying on high-power lasers and expensive gasses. It allows the flexibility of metal 3D printing at normal production costs.
To demonstrate the capability of SPEE3D technology to produce metal parts on demand for the Royal Australian Navy. These parts also need to meet military specifications however the process of 3D printing parts is fundamentally different than conventional manufacturing. Conventional methods already have established pathways for achieving these certifications. The challenge was to establish a pathway for 3D printed parts to also achieve the certification. This was a collaborative project with Charles Darwin University (CDU).
The research team consulted with the Royal Australian Navy to identify a part that is commonly in need of replacement on Navy ships. The part selected was a 50-mm type C aluminium camlock hose fitting. This type of hose fitting is commonly used on the Armidale class patrol boats for attaching hoses together and connecting hoses to other equipment, such as pumps. These fittings are used for the transfer of fresh, waste and sea water while at port and for on-board applications, such as firefighting.
The marine environment accelerates deterioration of these hose fittings through corrosion, often leading to their failure in service. Given the range of sizes and configurations of these fittings,
the ability to print suitable replacements parts, both as required and without the delays that are associated with the traditional procurement processes, is quite attractive.
The camlock hose fittings are specified according to standard MilC-27487/A-A-59326, which describes the required critical dimensions and tolerances, approved materials and functional requirements.
Following the specifications of the standard, a 3D model was developed for the final part’s geometry. The
process of printing, heat treating and post-machining to achieve this geometry was considered through the design phase, and the part’s geometry was adapted to meet the constraints of the print process and the postprocessing stages.
The parts were printed using the LightSPEE3D printer in 6061 aluminium, followed by testing per the requirements of the identified standards. Certificates that detailed the dimensional testing results, source material properties and supplier, functional test requirements and pressure testing results were produced. The pressure testing was conducted by an external NATA accredited test laboratory.
Following an internal risk assessment by the Royal Australian Navy, the parts were tested on site by Navy personnel to determine their functional effectiveness. The 3D printed fitting was tested as part of the operation of an engine-driven portable fire pump.
All testing showed that the part performed either equally well or better than the conventional cast and machined part. It met all requirements of the relevant specifications and was deemed fit for its purpose by the personnel of the HMAS Broome. The NATA-approved pressure test demonstrated the ability of the printing technology to achieve functional strengths in ‘real-world’ parts with complex geometries.
The then CDU Vice-Chancellor
Professor Simon Maddocks said the university had been working with the Navy for about two years and that the Minister’s announcement was recognition of the ground-breaking work the partnership had produced.
“This 3D printing technology has the potential to change the way many industries, including defence and defences industries, design, manufacture and supply parts. CDU has become a centre of excellence in developing this new technology,” Professor Maddocks said.
SPEE3D and the AMA at CDU worked
with the Patrol Boat System Program Office in Darwin to develop and qualify real-world parts using SPEE3D metal printing technology.
Professor Maddocks said the new project would provide Navy and CDU with expertise in deploying the technology into a sophisticated realworld environment.
“Taking the technology from the research context to being used by the Navy is a great example of the realworld impact of SPEE3D and CDU’s partnership in innovation. To be able to say the Navy will deploy the technology gives 3D metal printing a very high level of validation,” he said.
“The ability to integrate training of a new skills workforce, including apprentices, in partnership with the development and refinement of the technology through research is something CDU is particularly well positioned to deliver. By helping train Navy staff to operate the technology, we are better positioned to understand the role we can play in ensuring our graduates are equipped for the jobs of the future,” Professor Maddocks said.
Researchers have developed a cheaper and more energyefficient way to make hydrogen directly from seawater.
RMIT University researchers split the seawater directly into hydrogen and oxygen. This skips the need for desalination and its associated cost, energy consumption and carbon emissions.
Almost all the world’s hydrogen currently comes from fossil fuels and its production is responsible for around 830 million tonnes of carbon dioxide a year, which is equivalent to the annual emissions of the United Kingdom and Indonesia combined.
But emissions-free ‘green’ hydrogen, made by splitting water, is so expensive that it is largely commercially unviable and accounts for just 1 per cent of total hydrogen production globally.
Lead researcher Dr Nasir Mahmood said green hydrogen production processes were both costly and relied on fresh or desalinated water.
“We know hydrogen has immense potential as a clean energy source, particularly for the many industries that can’t easily switch over to be powered by renewables. But to be truly sustainable, the hydrogen we use must be 100% carbon-free across the entire production life cycle and must not cut into the world’s precious freshwater reserves,” Dr Mahmood said.
To make green hydrogen, an electrolyser is used to send an electric current through water to split it into its component elements of hydrogen and oxygen. These electrolysers currently use expensive catalysts and consume a lot of energy and water.
A team across three universities has developed new 'metasurface’ technology, which can offer significant benefits over current liquid crystal displays (LCDs).
The metasurfaces are 100-times thinner than liquid crystal cells, which offers a tenfold greater resolution and could consume less energy.
Today’s screen display market offers a large range of choices, each with its pros and cons. However, factors including production costs, lifespan and energy consumption have kept LCD technology the most dominant and popular technology for screens such as TV sets and monitors.
Liquid crystal cells are responsible for switching the transmitted light on and off and are constantly lit by a backlight, with polarising filters in the front and behind the pixels, forming a cross-polarised setup.
“Our pixels are made of silicon, which offers a long life span in contrast with organic materials required for other existing alternatives. Moreover, silicon is widely available, CMOS compatible with mature technology, and cheap to produce,” said Professor Andrey Miroshnichenko at UNSW Canberra.
“We hope this development could generate a frontier technology in new flat screen displays, which had a global market value of about $117 billion in 2020.”
The next phase of research will be building a large-scale prototype and generating images, which is hoped to be achieved within the next five years. It is expected the technology will then be integrated into flat screens and available to the public within the next 10 years.
This research was conducted by Nottingham Trent University in the United Kingdom, UNSW Canberra, and the Australian National University.
New technology is being developed to recycle used personal protective equipment (PPE) and turn it into raw materials for 3D printing.
Scientists and engineers extracted materials from discarded and out- of-date masks, gowns, sterile wraps and other hospital equipment to use as the feed stock in the 3D printing process.
This new PPE recycling technology and approach is being established thanks to a collaboration between innovative printing company 3RD Axis and ANSTO.
3rd Axis CEO Andrew Cooper said people are becoming increasingly concerned about the large amounts of PPE waste resulting from the pandemic.
“Wearing PPE is now part of our everyday lives, whether we pop on a mask to jump on the bus or to visit the doctor, it’s part of living with Covid. But of course, it also creates the problem of increased landfill and waste,” Cooper said.
“What we’re developing, along with collaborators at ANSTO, is a useful solution to this ever-growing problem.
3rd Axis is a member of nandin, ANSTO’s Innovation Centre, and a recent winner of a NSW Small Business and Innovation Research Grant.
ANSTO’s leader in Materials Development and Characterisation, Gerry Triani said ANSTO has an experienced team of researchers and engineers with expertise in solving technical challenges posed with developing and validating the performance of these recycled materials.
“The challenge is to re-use materials from the single use economy and transform them into durable manufactured articles that have a longer life cycle as the next product,” Triani said.
Australia’s national science agency, CSIRO, has signed a fiveyear agreement with US-based company SpaceX to support their future space missions.
Under the agreement CSIRO’s iconic Parkes radio telescope, Murriyang, as well as other telescopes owned and operated by the agency, will provide ground station downlink services to select SpaceX missions. This and other similar commercial agreements tap into CSIRO’s expertise and proven track record.
The Parkes telescope has a long history of providing spacecraft tracking services for NASA and other international space agencies.
Dr Douglas Bock, CSIRO’s Director of Space and Astronomy, said the agreement with SpaceX recognises CSIRO’s experience operating large, complex spacecraft tracking and radio astronomy infrastructure.
“Our Parkes radio telescope began supporting NASA space missions in 1962, when it tracked the first interplanetary space mission, Mariner 2, as it flew by the planet Venus,” Dr Bock said.
“The telescope, along with NASA’s Honeysuckle Creek tracking station, famously received the television signals from the Apollo 11 Moon landing watched by more than 600 million people around the world.”
The telescope recently received data from Voyager 2 as it entered interstellar space in conjunction with the Canberra Deep Space Communication Complex.
“Providing ground station services for space missions complements the astronomy research conducted with our telescopes and helps to maintain their capabilities as worldclass research instruments,” Dr Bock said.
Deakin University recently completed its expansion of the $20 million ManuFutures hub.
The hub is working in partnership with 14 successful and emerging businesses to grow advanced manufacturing capability in regional Victoria and Australia.
The new-look ManuFutures building at Deakin's Waurn Ponds campus has doubled in size to deliver an increased number of tenancy opportunities, new manufacturing incubator programs, training, and product engineering services.
Mark Curnow, the Research Innovations Regional Manufacturing Director at Deakin, said the completion of ManuFutures2 is crucial for manufacturing innovation.
"Our new ManuFutures2 building includes collaborative working spaces, further rental tenancy bays for manufacturing businesses, and an Innoveering Centre that includes product engineering and development capability, and opportunities for research collaboration and integration.”
"Four new manufacturing businesses have already moved into the new spaces as tenants, with room for two more. A total of 14 successful and emerging global manufacturing businesses now call Deakin's ManuFutures home,” Mr Curnow said.
Since opening in 2018, ManuFutures has a successful track record of helping entrepreneurs and start-ups take ideas from paper, to prototype, to emerging global businesses.
It has created over $1 billion in company value, incubated more than 17 advanced manufacturing start-ups, and created more than 120 advanced manufacturing jobs.
Houses made from hemp grown in South Australia could be the next sustainable solution to the nation’s building supplies crisis.
Hemp is emerging as a greener alternative to more traditional materials, such as bricks and concrete, for building more energy efficient buildings.
“It has massive potential and there’s lots of interest in being able to build houses now from hemp,” said the University of Adelaide’s Professor Rachel Burton, who is a researcher in the School of Agriculture, Food and Wine.
“Hemp is an extremely good insulator. It has been recognised that it controls humidity and it provides a lovely living environment for humans,” Professor Burton said.
Industrial hemp is a type of cannabis that doesn’t have high levels of THC, which is the chemical that triggers the ‘high’ associated with marijuana.
Fibres from inside the plant’s stem can be mixed with water and lime to produce a concrete-like mixture, which can be used to create bricks or the fibres can be used in pre-cast panels for sound-proofing or insulation.
“There are still many barriers to producing hempcrete but hemp houses and other plant-based products have huge potential to change how we build. People are looking for more environmentally friendly ways to reduce reliance on scarce resources,” Professor Burton said.
This is one of the topics in the University’s latest podcast series, The Discovery Pod. The series covers diverse subjects from hemp homes to using dogs to sniff out diseases, and how computers may be used to help treat mental illness.
Edith Cowan University (ECU) has partnered with Australia’s first lithium manufacturer, Tianqi Lithium Energy Australia (TLEA), and world-leading chemical engineering researchers, to drive a greener, more sustainable future for Australian lithium products.
The three-way collaboration is focussed on exploring ways to maximise the use of Australia’s finite lithium resources, which accounted for more than 55 per cent of the annual global lithium supply in 2021. Lithium hydroxide is a critical chemical enabling the decarbonisation of the transport and energy sectors by powering battery electric vehicles and energy storage systems.
Professor Hongqi Sun’s work on lithium and renewable energy is recognised globally.
“This partnership on lithium with TLEA is another big leap forward for Australia’s renewable energies future, and together we are excited to deliver research outcomes in years to come,” Professor Sun said.
TLEA produced Australia’s first battery grade lithium at its plant in Kwinana. The lithium hydroxide monohydrate produced is preferred by battery manufacturers like Tesla, and the Kwinana refinery has the capacity to produce 24,000 tonnes of per year.
“By producing materials from our lithium resources with beneficial uses, we can significantly reduce our carbon footprint and contribute to Australia’s decarbonisation efforts as well as those of our off-take customers,” CEO Raj Surendran said.
“We are very pleased to be part of this collaboration and to be able to tap into the University’s research expertise to investigate how the aluminosilicate’s properties can be enhanced to expand these existing market uses,” he added.
Researchers from UNSW Sydney have developed a national reference guide to help Australia hit its net zero targets.
The free online resource provides a pathway to achieving ‘whole of life’ net zero carbon for Australian buildings by 2040.
Race to Net Zero Carbon: A Climate Emergency Guide for New and Existing Buildings in Australia is a 40-page guide, which details critical information about materials and construction best practices to help architects, engineers and planners transform the building industry towards net zero carbon buildings.
“Our guide draws on Australian climate data but has global applicability,” said Professor Deo Prasad, who is lead researcher.
The guide is the first to detail a holistic approach to achieving net zero and fills knowledge gaps on net zero carbon buildings. Net zero means balancing greenhouse gas emissions produced by humans with emissions taken out of the atmosphere.
“This guide provides a deeper level of knowledge on how this sector can rapidly move towards net zero carbon buildings in the short term. Using science-based evidence and analytics, the guide maps a clear roadmap to achieving net zero by 2040 in the building industry. It goes beyond the aspirational and into the achievable,” Professor Prasad said.
The best way to minimise the embodied carbon footprint is by retrofitting and reducing materials in use.
“While the global community is aiming for net zero by 2050, the building sector has much greater potential and opportunity to reach net zero operational emissions by 2030 and a 60 per cent reduction in embodied carbon by 2030,” Professor Prasad said.
The University of Sydney recently announced a $7.4 million investment to expand its quantum technology facilities to establish the Future Qubit Foundry at the Sydney Nanoscience Hub.
The foundry will be a national-leading facility to invent the technology of tomorrow’s quantum computers, enabling them to operate at scale and be of use to society.
“The Future Qubit Foundry will leverage the University of Sydney’s research leadership in advanced quantum technologies and put us at the forefront of nextgeneration design of qubits, the heart of quantum computers,” said Deputy Vice-Chancellor (Research) Professor Emma Johnston.
“Crucially, it will also help ensure Australia can train the quantum workforce needed to operate tomorrow’s quantum tech,” she explained.
Quantum computers operating at scale promise to solve intractable problems in drug design, cryptography and engineering outside the reach of classical computing.
CSIRO predicts that quantum technology will be a $6 billion industry in Australia by 2045, employing 19,400 people.
The University's impressive quantum infrastructure already acts as a beacon to attract world-class researchers to Sydney.
“Australians like Dr John Bartholomew, who was at Caltech, and Dr Xanthe Croot, who was at Princeton, have come home to establish research teams at Sydney to develop future quantum tech,” Professor Stephen Bartlett, Associate Dean (Research) of the Faculty of Science, said.
A 2D metal-organic framework (MOF) on a substrate. Strong electronic interactions in the MOF allow local magnetic moments (arrows) to form in the molecules.
The University of Sydney Future Qubit Foundry will bring together Sydney’s existing strengths in quantum computing research to focus on the fundamental science, engineering and industry partnerships needed to invent the next generation of qubits.
Inside the cleanroom at the Sydney Nanoscience Hub.Industrial lasers have become indispensable tools in the manufacturing sector, particularly in materials processing. Their integration into various production lines has revolutionised throughput, quality and versatility, and has opened avenues for innovation.
When an airborne vehicle travels at hypersonic speed, it is moving at more than five times the speed of sound, otherwise known as Mach 5. For context, a trans-atlantic plane typically flies below Mach 1, while an F35 Joint Strike Fighter flies at Mach 1.6.
The types of lasers employed for materials processing vary widely, from CO2 and fibre lasers, through to Nd:YAG, and ultrashort pulse lasers, each with unique properties tailored for specific applications. CO2 lasers, for example, are often used for cutting, welding, and marking a variety of materials due to their high-power capabilities and efficiency. Fibre lasers, being solid-state, are known for their exceptional beam quality, and are extensively used in precision cutting, welding, and microfabrication.
Nd:YAG lasers find applications in processes that require a good balance between penetration depth and precision, such as drilling and spot welding. Ultrashort pulse lasers, on the other hand, are used in highprecision micro-machining and surface structuring, where minimal heataffected zones are critical.
One of the most noteworthy benefits of using industrial lasers in materials processing is precision. Lasers allow for highly accurate cuts and joints, essential in industries like electronics and aerospace. Another major benefit is speed; lasers can significantly expedite production rates without compromising quality. The non-contact nature of lasers minimises wear and tear, reducing maintenance costs and downtime.
Additionally, the flexibility that lasers provide allows for complex geometric configurations that would be otherwise unachievable using traditional machining methods. Furthermore, lasers are eco-friendly compared to conventional methods as they produce fewer pollutants and consume less energy.
In Australia, the academic research field related to industrial lasers in materials processing is burgeoning. Universities and research institutions such as the University of Sydney, RMIT University, and the Commonwealth Scientific and Industrial Research Organisation (CSIRO) are at the forefront. The focus spans from the development of new laser sources to optimising process parameters and developing applications in burgeoning industries.
One notable research area is in developing high-power, high-beamquality diode lasers. These lasers can potentially provide similar
performance to fibre lasers but at a fraction of the cost, which can be revolutionary in bringing down operational costs. Another area of active research is in ultrashort pulse lasers, where Australian researchers are working on improving the pulse duration and peak power to enable novel materials processing applications, particularly in the medical device manufacturing sector.
Australian researchers are also focusing on integrating additive manufacturing techniques like selective laser melting (SLM) and laser metal deposition (LMD) into the production pipeline. This includes researching novel materials and alloys and optimizing process parameters for better mechanical properties and surface finish.
Industrial lasers are a quintessential component in the manufacturing industry for materials processing, contributing to enhanced precision, speed, versatility, and environmental sustainability. The Australian academic landscape is vibrant in this domain, with research encompassing new laser sources, optimization of processing parameters, and development of innovative applications in emerging industries. The continuous evolution of laser technology promises to keep propelling the manufacturing sector into new realms of possibilities.
Industrial lasers are now well established as manufacturing tools in Australia, and their number and the number of applications has been evolving and growing steadily over the last forty years.
Australia in the late 1970s and 1980s was seen as a modern, industrialised society with significant potential for growth, stable government, good education and research infrastructure, but whose main economic activity was in primary production and not the manufacturing sector. Realising the significance of manufacturing in a world in which commodity prices for most of Australia’s exports at the time (coal, iron ore, wheat and wool) were not only declining but were influenced and controlled by overseas factors, the Australian community, particularly at the Federal Government level, were considering actions aimed at revitalising and strengthening manufacturing. Laser technology was identified as one of twenty technologies to be a “sunrise” industry capable of rejuvenating the Australian manufacturing industries. A number of government reports at the time informed favourably on the opportunities available for lasers in many industrial sectors [1,2].
In the 1980s the number of lasers employed in manufacturing increased from just a few to few hundred used in a range of industries at the time such as the automotive, electronics, metal fabrication and general manufacturing. This was despite the upheaval in Asia's industrialised countries in the late 1980s and the period of little or no growth in early 1990s during which several local laser manufacturers and users went into liquidation. The steady growth in the number of industrial lasers and new applications can be linked to a range of factors. These include Australia's growing economy over the period, the maturing of laser technology and some applications, the increased awareness of the technology's capability by engineers and middle
level managers through technology diffusion programs, the arrival of the internet, the government’s R&D policy and the policy of lowering Australia's trade barriers in order to increase efficiency and productivity. This last factor exposed local manufacturers to overseas competitors, who introduced lasers into their production lines early, and therefore forced Australian companies to examine and adopt similar manufacturing strategies in order to remain competitive. This situation was somewhat moderated from 2000 with the development and growth of the Chinese economy and globalisation in general. Since 2020 and the arrival of COVID-19 virus the focus has shifted to sovereign capability both at the laser industrial and research applications levels. Along with developments on the industrial front over this period the universities and CSIRO played their part in laser education at the undergraduate level, and various industry seminars on the subject were held [3]. However, in the early laser years the main “laser learning curve” for industry was dictated by the interchange of people working with lasers at various levels, and targeted fact-finding tours overseas and over the last 10 to 15 years through the proliferation of the internet and various social media platforms [4].
In line with overseas trends, the dominant laser materials processing application in Australia has been and continues to be laser cutting, mainly two dimensional cutting of sheet steels and plastics. Multiaxis processing was introduced in the late 1980, in particular the cutting of 3D parts such as plastic mouldings for the automotive industry and the cutting of complex parts from tubular steels. The lasers used for cutting applications were predominantly CO2
lasers. In the early to late 1980s they ranged in power up to 1300 W. The laser manufacturers were SpectraPhysics, Ferranti, Coherent, MesserGreishem and Photon Sources. The motion systems that these lasers were integrated with were typically 1 m by 1.5 m in size and were in most cases developed and manufactured in Australia. The demand for greater productivity and processing of thicker materials over the years has seen growth in source power with laser sources used for cutting being in the power range 3500 W to 10000 W and the motion systems typically 3m by 5 m in size. These motion systems in the early days were also being developed locally and illustrated the considerable capability which existed in Australia in the area on CNC. The lasers were all imported from companies such as Rofin-Sinar, PRC, Trumpf, AMADA and Bystronics. The laser sources were high power CO2 however the advances in solid state technology in late 1990s and early 2000s have seen these lasers replaced by solid state fibre and disk lasers from IPG and TRUMPF predominantly.
By far the largest number of these systems is found in job shops, which have increased steadily in number from a few in 1980 to some 50 today. Job shops are typically small companies with five to ten employees and an annual turnover these days of $2 to $5 million. A typical job shop operates one to three laser systems covering the medium to high power levels in two or three shifts a day. A number of these job-shops also offer plasma cutting and MIG and TIG welding facilities to complement their laser services.
Other commercial laser applications, such as laser drilling and laser welding are established in Australia but at a relatively low level. Laser marking was the fastest growing application in the 1980s and 1990s with an installed base of some two hundred units. Laser
drilling on a pre-production basis was first trialed in the General MotorsHolden engine plant in Melbourne in 1981. The system comprised a multiple-head Nd:glass laser for drilling one-millimeter diameter oil holes in camshafts. The laser units were supplied by Coherent and the system designed and manufactured by Laser Lab and Lasermatics. Today laser drilling is dominated by Actionlaser, a Sydney based company established in 1989 to manufacture micron size filtration screens for the sugar industry. This technology is a direct result of the research effort conducted by CSIRO [5] in the area of laser processing and is described in more details in a subsequent section. Another company, Laserexperts, performs lasers drilling as a job shop service.
Laser welding, although common overseas in particular in the automotive industry, has experienced very low uptake locally. In mid 1980s, Cochlear, a company involved in the manufacture of bionic ear, was using low power, 100 W, Nd:YAG lasers to weld the titanium case containing all the sensors. Another company, Telectronics, operating in the early 1990s was using a high average power (500 W) Nd:YAG laser to weld titanium heart pacemaker cases. Due to financial constraints the company closed down its plant in Sydney in mid 1990 and moved its operation to the US. This lack of significant welding activities in similar market areas to those overseas appears to be due to the small size of the domestic market and the relatively high cost of laser welding technology at the time. In addition, as most of the large companies operating in Australia today are subsidiaries of foreign multinationals there is a tendency to carry out their research and development of new laser applications at home. The dominant welding application was tailor welded blanks for the automotive industry established around 2001 and closed down in the late 2000 following the exit of the automotive companies from Australia.
Laser surfacing and in particular cladding, has seen a significant interest and growth over the last 20 years. In 2000, Jarvie Engineering,
based in Newcastle, acquired first two laser cladding systems in Australia manufactured by Balliue from Belgium. Both systems were based around the Rofin-Sinar's high power, 5000 W and 6000 W, CO2 laser sources and a large CNC motion system. Another company, HVOF in Sydney, set up another cladding system in 2001 based around a 5000 W PRC CO2 laser source. Both companies saw tremendous potential for laser cladding in Australia because of the nature of the domestic markets and benefits the technology offered compared to more traditional surfacing technologies in the mining, powergen and general manufacturing industries in particular. Today there are a number of laser cladding companies including Laserbond, with roots in HVOF, Hardchrome Engineering, D&T Engineering and Rosebank Engineering with fibre delivered diode cladding systems up to 25000 W in laser power.
Late 2000 and early 2010 has seen the arrival of laser additive manufacture in Australia both commercially and at the R&D level. This technology was seen to offer many benefits and opportunities compared to more
traditional manufacturing approaches. Companies such as Aurora in Western Australia started manufacturing laser powder bed systems while others such as, Amaero, a spinout from Monash University, Amiga Engineering, Romar Engineering, Objective 3D and others are service providers. They have the capability to design and print components in a range of metal alloys.
The number of local laser and system manufacturers has oscillated between one and five between 1980 and mid 2000s. Today there are no system or laser manufacturers. In the 1980s there were two CO2 laser manufacturers, Laser Dynamics and Laser Electronics. The lasers were of the slow flow type with output power typically in the range 200W to 400W. The companies also were developing fast axial flow lasers up to 750W in power. Their fate however was affected by the downturn in local and global economy in the early 1990s and they closed their laser development activities. During the same period another company, Quentron
Electronics, based in Adelaide, South Australia, was involved in the design and manufacture of Nd:YAG lasers up to 50W average power for drilling and welding applications. This company also closed its laser development activities in the early 1990s due to economic pressures.
Of the two prominent system manufacturers, HG Farley Laser Lab and Bristow Laser Systems, HG Farley Laser Lab was the oldest with its origin dating back to the 1970s. Over its lifetime Laser Lab had built considerable reputation in the design, development and construction of laser cutting systems and had achieved recognition as a world competitive supplier of quality laser machine tools. At a point in its history Laser Lab commanded 70% of the domestic market and export markets accounted for 70% of all systems manufactured at its the Melbourne facility. Some 350 Laser Lab systems were installed throughout the world. The company was very innovative in its system design and had developed a number of technical inventions. One of the technical achievements was the “Pentacon” five-axis laser cutting machine developed in mid 1980s (see Fig. 1). Laser Lab considered the “Pentacon” to be a true five –axis machine. As shown in Figure. 2, the “Pentacon” unlike traditional cutting heads of the time did not have an offset between the vertical Z axis centre line and the cutting nozzle
because of its double-jointed “B” axis. In the conventional design, the offset required that the linear axis must be capable of achieving very high acceleration in order to maintain a constant cutting speed at the surface of the workpiece.
Other inventions include a cantilever cutting head in 1991, a twin cutting head system in 1998 and a fully integrated flexible manufacturing system in 1997.
Bristow Laser Systems specialised in the design and construction of laser cutting systems. It developed a cutting system capable of cutting 30 mm thick mild steel plate using a 7000 W PRC CO2. While these two companies were the only local manufacturers of laser processing systems other international laser and laser system manufacturers were represented through local agencies or branches of overseas companies operating in Australia.
There are no local manufacturers of micromachining systems using UV lasers. Macquarie University's Centre for Lasers and Applications had been active in the research area since 1990 and had established together with the Applied Laser Technology Group a job shop facility in Sydney in 1996 for processing of polymers and thin metal films. The machining system was based around a copper vapour laser source. However the company is no longer trading.
R&D infrastructure also fluctuated over the last forty years. Until about 2010 there were four research groups engaged full-time in the research and development of both new applications and laser materials processing in general, CSIRO's laser group, Macquarie University's Centre for Lasers and Applications, the group at the Industrial Research Institute Swinburne (IRIS), at Swinburne University of Technology and University of Wollongong. Some applications development work was also conducted by the laser job shops but this was usually of short duration. With the rise of additive manufacturing since 2010 new R&D groups focusing on laser additive manufacture have been established, including large Centres at Monash, RMIT, Sydney University, CSIRO Lab 22 and smaller groups at other Universities. These groups complement each other in terms of their research interests and have formal and informal links.
The Centre for Lasers and Applications at Macquarie University was one of the oldest laser laboratories in Australia. Started in 1975 its primary role was the development of new laser sources predominantly based on metal vapour as the active medium and operating in the visible and near infra-red spectrum. It expanded rapidly in mid to late 1980s into the largest laser laboratory in Australia. In early 1990s
it started to broaden its research base to include laser micro-machining using copper vapour based sources which where developed at the Centre. The Centre conducted a significant amount of research into the processing of plastics, polymers and thin metallic films using doubled copper vapour laser. It was also involved in the establishment in 1995 of the first commercial UV micromachining facility in Australia. The Centre morphed into a Photonics Research Centre in early 2000s.
The CSIRO's industrial laser group was established in 1980 to conduct R&D in the use of lasers in manufacturing. In 1990 CSIRO formed an Industrial Laser Centre in Sydney to further develop new laser applications and promote the benefits of laser technology in manufacturing. The Centre conducted many short and long term studies with Australian industry and developed a number of new products and processes. The most significant was a new type of filter screen for reprocessing of sugar. The screens, typically one metre square in size, comprise of high number density (up to three million perforations per square meter), high quality slots (60 micrometers by 1000 micrometers) distributed uniformly in 250 micrometer thick stainless steel. Figure 3 shows the
relevant details. Note that the taper commonly produced in laser drilling is in this application a prerequisite as it prevents hole blockage. This technology was transferred to Actionlaser, a company established to commercialise it. The company is still enjoining growth and exports screens to some twenty countries overseas. In 1998 laser activities at CSIRO moved from Sydney to Adelaide and in late 2000 from Adelaide to Melbourne.
In addition to laser drilling the CSIRO in early 1990s were the first in Australia to conduct R&D in laser cladding using their 500 W average power fibre coupled Nd:YAG laser. In 1996 the group worked with PBR on the laser cladding repair of their P90 front caliper gravity diecasting die using robotic laser cladding. PBR were experiencing significant wear on their H13 die and were interested in exploring the use of laser cladding for the repair of the friction pad rattle spring window and possible die life extension. CSIRO investigated the use of metal matrix composite (WC particles in a nickel) and deposited a 1 mm thick layer on the die surface [6]. Illustrated in Figure 4 are the die and laser deposited clad layer.
The diecasting trials were conducted at PBR Automotive Pty Ltd. The results indicated a 300% improvement in wear resistance of the clad layer compared to the heat-treated die surface under similar production conditions.
a) above
b) below
The group at IRIS was conducting research and assisting industry in the areas of lasers cladding and welding in particular. The group was equipped with a 2.8 kW Nd:YAG laser from Rofin-Sinar and a 3kW diode laser from Laserline. Both lasers were integrated with robots and 4 axis CNC stations. In 2006 the group acquired a DMD machine from POM for conducting research into the manufacture and repair of tools and dies and 3D printing. A notable research success story for the group was its development of technology for the in-situ repair of eroded leading edge of low-pressure turbine blades used in the power generation industry in collaboration with the Cooperative Research Centre for Welded Structures, 11 power utilities and CSIRO [7]. The technology was commercialised in 2006 through
Hardwear, a company established by the Cooperative Research Centre with Swinburne as a shareholder. In 2009 the company was sold to Hardchrome Engineering. Illustrated in Figure 5 is the robotic laser repair process developed by IRIS laser researchers. IRIS closed in early 2010s however laser research activities are continuing under the ARC SEAM umbrella.
Laser additive research however continues to grow with some notable firsts produced by researchers at Monash University, first 3D printed jet engine, CSIRO first 3D printed human heel and chest plate and
RMIT University Centre for Additive Manufacture, first 3D printed spinal disc, shown in Figure 6, that was implanted into a patient in 2015 [8]. Despite a number of attempts at establishing a high-power (up to 25000 W) laser facility in Australia via various government and other R&D initiatives [9-12] in the 1980s and 1990s, no high power laser application facility was ever established. The establishment of relatively high laser power research activities at Universities since 2000 has to a large extend reduced the need for such a facility.
Commercial laser activity in Australia has been growing and evolving steadily since 1980 and this trend is likely to continue. This trend appears to be driven by several factors such as the expanding local economy, better industry awareness of the laser’s capabilities, lower technology costs and increased competition from overseas manufacturers using laser technology. The local R&D base in the area is also growing and evolving as the applications mature and are commercialised and new applications in particular in the additive manufacturing arena are researched and developed.
[1] Jones, A. J.: Lasers in Australia: A Compedium, 1984/85/86: Published by the Commonwealth Dept. of Industry, Technology and Commerce, Canberra, Australia (1986).
[2] Scott W. D. and Co.: Business Opportunities in Advanced Technology: Lasers: Published by the NSW Dept of Industrial Development and Decentralisation, Sydney, Australia, (1985).
[3] Arndt, G.; Kaebernick, H.; Brandt, M.: Manufacturing with Lasers: An awareness Seminar on Developments in and the Potential of Laser Processing in Australian Industry. CAMIA Report No PC14 November 1989.
[4] Arndt, G.: Report on Laser Activities During Study Leave 1994. Internal report CRC IMST/CAMIA, January 1995.
[5] Brandt M and Crane K.C.A: The manufacture of finely perforated sheet material: PCT/AU/89/00336.
[6] M. Brandt and K. Hooper: Wear performance of laser deposited WC/Ni clad layer on P90 front calliper gravity diecasting die. Materials Australia, Tooling 1999 conference, Melbourne, Australia.
[7] M. Brandt, S. Sun, N. Alam, P. Bendeich and A. Bishop, “Laser cladding repair of turbine blades in power plants: from research to commercialisation”. International Heat Treatment and Surface Engineering Vol 3 No 3 105 –114, 2009.
[8] https://www.rmit.edu.au/content/rmit/ au/en/news/all-news/2019/jul/3d-printspine.html
[9] Arndt, G.: Proposal for the Establishment of a Jet, Power beam and Electromagnetic (JBE) Manufacturing research Centre. Uni. Wollongong ARC Special Research Centre Application, January 1990.
[10] Arndt, G.: Consortium Application for a Cooperative Research Centre (CRC) in Advanced Joining and Cutting of Materials, CRC Program, October 1990.
[11] Brandt, M.: Proposal for a National Laser Manufacturing Technology Facility, Major National Research Facilities Program, January 1995.
[12] Norrish, J.; High Power Laser Facility for Advanced Material Processing. Application for a Research Infrastructure Equipment and facilities (RIEFP) Grant, ARC September 1997.
Source of information and images:
The blue diode laser by Laserline GmbH, revolutionizes the processing of copper, gold, and other highly reflective metals. The direct generation of up to 4 kW continuous wave laser power in the 450 nm wavelength range avoids the need for complex and inefficient wavelength conversion devices. At the same time, the absorption and process efficiency, is increased by a factor of more than 10, compared to lasers in the 1-micron range. With advances in beam quality and smaller focus diameter extremely thin and highly filigreed copper contacts can be processed using this blue diode laser. The diode laser’s energy deposition can be precisely controlled, enabling copper to be melted without evaporation, leading to a stable melt pool. This opens up new application opportunities in buildup processes such as cladding and additive manufacturing.
Additive manufacturing (AM) processes enable three-dimensional components to be constructed through the application of complex geometries. Laser based technology
provides a build-up process or layerby-layer construction suitable for individualization products or fit for purpose parts. Although AM was developed for the rapid creation of one or more prototypes, the generative manufacturing method using lasers has long since been adapted to produce full-scale molds and small series. The process has also found its way into repair welding – whether it be in the repair of break-offs or for the restoration of surface structures. Based on classic build-up welding, additive manufacturing with diode lasers has proved highly successful, whereas the LPBF (Laser Powder Bed Fusion) process - in which the component is generated by selective beam melting in a powder bed - has so far proven slow and costly, with part size and production volumes constrained by available space in the build chamber. Laserline systems use a process of Laser Metal Deposition (LMD) using powder to produce near net shape structures. High power diode lasers ensure a calm process – homogeneous, low porosity and free from cracks, as layers of material build-up a part in a single production step. While comparable to build-up welding, the setup for AM is quite
different. The system consists of a laser with a flexible 3D print head suitable for powder or wire feeding. During the process, the print head moves across the working platform referred by the three-dimensional design plan and melts the workpiece surface and the layering material. The layering material may be stainless steel, copper, aluminium and titanium alloys and even nickel-based and cobalt-based superalloys such as those used in aircraft construction. During the manufacturing process, it is possible to switch between different materials. This means that different requirements, such as wear resistance, thermal conductivity and ductility, can be combined in one component. Components made of two different materials can include copper to enable efficient cooling inside the component while the outer shell is built up using tool steels suitable for rough industrial usage. Here the blue laser can process both materials well, with significantly higher deposition rates achieved in copper-based materials with a blue 4 kW diode laser. The build-up is continuous, layer by layer, with no cooling time necessary. Shapes and structures are achieved with almost no material loss, reworking or tool wear.
The top-hat profile of the diode laser provides an homogeneous energy deposition for a smoother process, calmer melt pool and crack-free material.
The advantages of blue lasers: Laserlines’ blue diode laser, is a new performance class of blue industrial lasers, generating 4,000 W cw blue laser radiation straight out of the laser diodes. The technology avoids complex and inefficient wavelength conversions. The available laser power significantly broadens its application, and is particularly suited to welding, cladding and additive manufacturing with copper and other highly reflective metals. This is important, as copper, a material known for its excellent thermal and electrical properties, is becoming increasingly valued due to its outstanding electrical conductivity in the production of electric motors in the growing automotive sector. In addition, numerous advantages can also be achieved with other metals such as steel or nickel.
Blue diode lasers now available with an output power of 4 kW, with a short wavelength of around 450 ±20 nm, are ideal for attaining a high absorption rate. In addition is a beam quality of 33 mm·mrad and typical spot sizes of 0.45 to 0.6 mm. An efficiency of approximately 25 % is currently the highest for a laser in the visible wavelength spectrum. A selection of process optics is available for various laser processes, with the recent addition of industrial round and rectangular zoom optics – varying the size of round or rectangular laser spots at a fixed working distance, and a laser scanner system for the blue diode laser. Different powder nozzles can be combined with the modular optics systems for laser cladding and laser metal deposition (LMD). Because of the various configuration possibilities, flexibility is available with the process optics as they can be adjusted to different process requirements and onsite needs. Controlling the geometry of deposited material during the AM process remains a challenge hence controlling optics is essential. With all AM technologies where parts are created layer by layer, metallurgical bonding can be a problem. By attaining
calm melt pools by controlling the LMD process, due to the absorption rate of the blue laser when processing copper, the outcome is significantly improved.
Laserline’s concept of modular systems facilitates the stagewise scaling of the blue laser’s maximum power. At the same time, the beam quality can be adapted to suit the process requirements by means of different diode stack configurations. This unique technology provides flexibility, modularity and scalability, a hallmark of Laserline products.
The main benefits of LMD with blue diode lasers:
• First, the nozzle with optics can be attached to a robot arm meaning working on any size item is possible!
• Second, importantly is the ability to add a new feature to an already produced part be it a flat or curved surface to improve or add to functionality.
• Third, using this blue diode laser an improved melt pool stability for copper (alloys) is achieved with
powder efficiency of >80 % and deposition rate 5.4 times IR laser.
• A fourth benefit is found where several materials can be combined. Components made of two different materials are no longer a challenge. The blue laser can process both materials with exceptional metallurgical bonding.
Extending usage options:
Laserline’s concept of modular systems facilitates the stagewise scaling of the blue laser’s maximum power. At the same time, the beam quality can be adapted to suit the process requirements by means of different diode stack configurations. This flexible technology has extended the blue laser capability through a unique hybrid combination. Combining the blue laser radiation with a laser in the infrared wavelength range leads to highly stable, almost spatter-free keyhole welding processes. The blue laser stabilizes the process, even when welding in deep penetration mode, while the NIR laser provides the additional energy. Laserline has developed special hybrid optics that combine the blue and NIR laser beams providing:
• Direct emission of 445±20 nm with high efficiency
• 10-15 % higher absorption on copper than green lasers
• 10 times higher absorption on copper than IR lasers
• Top hat intensity profile
• High process stability and spatter free
• Compact design with up to 4kW
The future of blue lasers:
In the field of maritime surfaces and e-vehicles there is potential opportunity for blue laser processes. Around eight kilograms more copper is required for the manufacture of electric vehicles than for cars with combustion engines. The high seam quality of welding is also suited to electrical engineering such as the manufacture of components for power electronics where joints must be temperature resistant. Furthermore, the blue laser has proven itself in the removal of fouling on marine surfaces. In the past, fouling was mainly treated with coatings and mechanical cleaning -environmental and surface damage often had to be accepted. The laser method was tested with Laserline blue lasers as part of the FaulLas project, offers a more economical
and environmentally friendly option that does not damage the coating. In addition, the blue wavelength allows gold to be processed, for example, in the field of medical devices.
Raymax Applications Pty Ltd in Sydney, has been the Australian and NZ distributor for more than two decades working in close cooperation with Laserline. We are excited about the continuing technological innovation of high power diode lasers for industrial production in this new wavelength, as numerous other applications are expected to be tapped into in the future. Laserline GmbH’s 4 kW blue laser is already exceeding expectations, so even more efficient additive manufacturing of large and high-volume copper components will be possible in the future.
Electrical mobility is changing the worldwide vehicle industry. The trend has not only hit the major automotive brands. Also, truck, ships, constructions machines and even aviation is transforming towards electrical drives and battery technology.
Multi-national companies, their suppliers but also SME and startup companies developing new production methods and technologies for the new demand in e-mobility component in consistently high standard. And the laser has already become a standard for joining and welding of copper electrical components in the battery, motor and powertrain. But getting the welding process started with a conventional IR laser source (e.g. fiber lasers) require significant energy input. The material heats up and, as soon as the melting temperature is reached, the rate of radiation absorption suddenly increases, producing a spike in energy that is difficult to control.
Choose Green for Welding Copper! Copper – and to a lesser degree aluminum – is an ideal choice for electrical connectors due to its high electrical and thermal conductivity. It conducts electricity and heat better than any other commonly used industrial metals. Unfortunately, however, copper absorbs very little light in the infrared wavelength, which is exactly the wavelength region in which most industrial lasers operate. Working at a wavelength of around one micrometer, these lasers have a tough time processing copper: at room temperature, copper reflects 95 percent of infrared light and only absorbs between 3 and 5 percent. As well as being very inefficient, this also poses a hazard, since the reflected laser light can adversely affect or even damage its surroundings. The risk increases further if the chamber is narrow and confined or if temperature-sensitive components are located close to the weld point. As the temperature of the copper increases, so does the rate at which it absorbs infrared laser light, climbing as high as 20 percent. In addition, the excess energy leads to erratic processes with spatter along the entire weld path – something that is completely unacceptable in a confined environment full of sensitive
With green laser light, all these problems disappear. Scientists have long known that copper absorbs shortwavelength laser light significantly better than long-wavelength light.
At room temperature, copper absorbs 40 percent of this green laser light – a rate of absorption that is eight times higher than for near-infrared wavelengths.
And numerous tests have demonstrated that the copper’s surface properties have no effect on welding results with green light. In other words, it makes no difference whether the copper is polished, sanded, untreated, or heavily oxidized. The process is not affected by the degree of oxidation, superficial scratches or highly reflective, mirrorfinish surfaces. In an industrial setting, this means that, in many
aperture of 0.1. Therefore, scanner optics and fix beam welding optics with a long focal length can be used for laser welding processes. The
optic can be positioned above the workpiece at a distance to allow easier access to narrow work areas, reduce contamination and extend their service life. The significantly longer Rayleigh length (i.e. larger depth of focus) paves the way for less precision in in fixture design as well as part accuracy (tolerances).
Moreover, when you are comparing green and blue lasers, you should remember that blue lasers are direct diode lasers while as the green laser is based on the disk laser concept which is industrial proven by many thousand lasers sources operating in industrial environment for 2 decades.
With the unique beam quality of a green disk laser, it can be also used for Additive Manufacturing. The TruPrint 5000 Green Edition is the right tool for printing highly reflective materials such as copper. The machine is equipped with a TruDisk1020 with maximum 1kW output power in green wavelength and a beam quality of 2 mm mrad. The focus diameter in a TruPrint 5000 with the green laser is 0.2 mm.
This opens new opportunities for manufacturing induction coils, components for complex cooling applications, and for products such as high-performance heat exchangers for
TRUMPF 5 Axis laser machine which is able to do laser welding and Laser metal deposition with the green
The green LMD can be used for building 3D parts, modifying the shape of machines Cu parts or just us a high speed cladding process to add a thin laser of Copper onto the surfaces of machined parts.
With the e-mobility trend in the industry, the green laser has found his way already into the industrial advantages are obvious for thin cooper welding. This can be thin Cu foils but also powder surfaces. Blue and green wavelength have a signification higher absorption in Cu surfaces at RT compared with IR Laser sources. The blue Diode Laser has the highest absorption rate of industrial laser sources in Cu. But the higher beam quality and the higher available laser source makes the green Disklaser as the leading laser source at this moment for Cu Welding and AM for Cu parts. Green lasers are available for powder depositions heads (LMD) and powder spraying machines (LMD).
For thicker Cu materials - where the in-coupling of the laser beam into a Cu surface at Room Temperature is not so critical - the IR might be still a good alternative since higher power laser sources are available in IR wavelength.
As the world's industries scramble to find solutions to the growing problems posed by climate change, the construction industry has made significant strides thanks to the development of 3D concrete printing. This cutting-edge innovation not only helps mitigate our impact on the planet, but it also makes it possible to build reasonably priced homes out of recycled materials.
The release of glasshouse gases during the traditional concrete production process significantly increases carbon emissions. Traditional concrete production process is responsible for approximately 8% of global carbon dioxide (CO2) emissions. Furthermore, construction also creates an estimated third of the world's overall waste at least 40% of the world's carbon dioxide emissions. However, a greener option is available with 3D concrete printing. This technology helps cut down on waste and energy consumption up to 50% compared to conventional building practises by precisely layering concrete in a controlled manner. The carbon footprint of 3D-printed structures can be reduced over their lifetimes with the help of modern additives and binders that increase their durability and energy efficiency. As a result, 3D concrete printing is crucial to fighting climate change because it drastically cuts down on carbon dioxide emissions from the building sector.
The construction and demolition debris contribute to a significant portion of the waste generated worldwide, with estimates ranging from 25% to 40% of the total waste generated. The exciting feature of 3D concrete printing is its ability to incorporate recycled materials, thereby decreasing reliance on virgin resources and redirecting waste away from landfills, thereby contributing to sustainable construction. Engineers and scientists are always looking for new ways to ensure the structural integrity of buildings made from
recycled materials like construction and demolition debris, recycled concrete aggregates, and even plastic waste by blending them with binders and additives. A recent study at RMIT University demonstrated the efficient use of recycled materials in 3D concrete printing, providing a practical answer to waste management issues and opening the door to a more environmentally friendly building sector.
An urgent problem in many parts of Australia, especially in urban areas, is the high cost of housing. 3D concrete printing offers a promising solution. In this case, 3D concrete printing offers a possible answer. This technology drastically cuts down on time and money spent on building by allowing for the rapid construction of complex shapes and designs. Recycled materials are often more cost-effective than conventional building materials, adding to affordability. In addition to providing versatility and adaptability, 3D-printed homes can be tailored to meet individual housing needs. The advent of 3D concrete printing has revolutionised the construction industry, opening the door to more cost-effective housing options across Australia.
Incorporating 3D concrete printing into the construction industry offers
a game-changing chance to address climate change, waste management issues, and Australia's housing affordability crisis, among other things. This technology demonstrates its potential to make a positive and lasting impact on sustainability by lowering carbon emissions through optimised construction methods, employing recycled materials, and redirecting waste from landfills. Researchers, engineers, and policymakers in Australia are making great strides towards perfecting 3D concrete printing techniques, which bodes well for the country's construction industry in the future. The research conducted at RMIT University has made significant strides in expanding the capabilities of 3D concrete printing. RMIT’s scientists have successfully developed a new eco-friendly 3D-printable concrete made from recycled glass. They obtained fine particles that can replace traditional sand in the concrete mixture by crushing and processing waste glass. This novel approach not only keeps glass waste out of landfills, but it also reduces the environmental impact of sand extraction. The recycled glass-based concrete has better mechanical properties and can be used for a variety of purposes, including construction. This advancement advances the use of recycled materials in construction processes and contributes to the advancement of sustainable 3D concrete printing. Using recycled plastics in 3D concrete
printing is another major innovation developed at RMIT. Concrete mixtures can now be enhanced with recycled plastics like high-density polyethene (HDPE) and polypropylene (PP) for 3D printing, thanks to a technique developed by scientists. These plastics, which come from a variety of recycling streams, are converted into filaments that function optimally in 3D printers. This combination improves the printed structures' mechanical properties and functionality while simultaneously decreasing plastic waste.
The issues of climate change, waste management, and the rising cost of housing are all being addressed by the advent of 3D concrete printing in Australia. A more sustainable and equitable future is made possible by this technology, which makes use of recycled materials, reduces carbon emissions, and employs cost-effective building techniques. Australia is prepared to adopt environmentally conscious, resource-efficient, and affordable housing solutions thanks to ongoing research and refinement of 3D concrete printing techniques. Australia can lead in promoting environmentally friendly and socially just building practises by taking advantage of the revolutionary potential of 3D concrete printing.
Standards are critical in establishing best practises, defining quality requirements, and promoting consistency across various projects and stakeholders. The need for comprehensive standards becomes even more critical in the context of construction, where structural integrity and safety are paramount. Standards can boost confidence in AM technologies, facilitate regulatory compliance, and foster industry-wide collaboration by providing guidelines for material properties, manufacturing processes, and quality control.
Creating standards for Additive Construction involves a number of unique requirements and challenges. These are some examples:
a. Material Considerations: AM technologies in construction use various materials, including cement, compounds, adobe-based materials, metals, and polymers. Each material type has unique properties, performance demands, and manufacturing considerations. Creating standards that address material diversity while ensuring consistent quality and compatibility is difficult.
b. Manufacturing Techniques: AM includes a variety of manufacturing techniques, including extrusion, powder bed fusion, and binder jetting, each with its own set of parameters and considerations. To ensure repeatability, accuracy, and reliability, standards must define process parameters, equipment requirements, and quality control measures for various AM processes.
c. Building Structural and Infrastructure Elements: Additive Construction incorporates a wide range of applications from structural to non-structural elements. Building structural and infrastructure elements have unique requirements when compared to other industries. To ensure the safety and reliability of printed structures, standards should address factors such as load-bearing capacity, durability, fire resistance, and long-term performance.
d. Interoperability and Compatibility: Architects, engineers, contractors, and material suppliers are among the many stakeholders involved in Additive Construction. Standards should enable seamless collaboration and integration throughout the project lifecycle by facilitating interoperability and compatibility among various software, hardware, and materials.
e. Safety and Sustainability: Standards must address safety concerns such as structural stability, fire resistance, and health hazards associated with materials and processes. Furthermore, to promote responsible AM practises in construction, sustainability aspects such as material efficiency, waste reduction, and environmental impact should be incorporated into the standards.
Work Scope:
ISO/TC 261/JG 80 (Joint ISO/TC 261-ASTM F 42 Group) and ASTM F42.07.07 subsection on Construction is extensively at work developing a proposed standard that addresses the quality requirements for additive construction, with a focus on structural and infrastructure elements. Standard ISO/ASTM 52939 (ASTM WK77614) - Additive manufacturing for construction — Qualification principles — Structural and infrastructure elements, aims to provide guidance on AM processes, quality-relevant characteristics, and factors along the process chain. The standard, which is in its final approval stage, further aims to bridge the gap between traditional construction standards and Additive Construction approaches.
The standard will address cement, compounds, and adobe-based materials that are commonly used in construction AM projects. It will, however, exclude metal materials. The standard will define activities and sequences within an AM site or project, providing a systematic approach to building and construction manufacturing processes.
The ASTM committee's creation of this standard demonstrates the industry's recognition of the importance of having specific guidelines and requirements for AM in construction. The proposed standard will greatly benefit architects, engineers, 3D printing technology and service providers, material suppliers, and general contractors by promoting quality, safety, and interoperability in adopting AM technologies in the construction industry.
The committee also emphasises the importance of broadening participation in the development process, especially in areas such as 3D and architectural design, safety, and sustainability. This inclusive approach ensures that the resulting standard reflects stakeholders' collective expertise and perspectives, resulting in a strong standard that addresses sector critical needs. It is worth noting that further ISO/ASTM efforts are underway to develop specific standards for Printed Element Testing and Evaluation as well as Element Design Conversion.
These short courses provide you with an engaging learning experience. Courses may include flash animations, video of instructors teaching the course in a classroom, video segments from ASM’s DVD series relevant to the learning material, and PDFs of instructor Power Points used in the instructor led training. All online courses require internet access for reading and viewing course content. Both HTML pages and PDF files for each lesson are downloadable and printable for easy offline access. www.materialsaustralia.com.au/training/online-training
Steel is the most common and the most important structural material. In order to properly select and apply this basic engineering material, it is necessary to have a fundamental understanding of the structure of steel and how it can be modified to suit its application. The course is designed as a basic introduction to the fundamentals of steel heat treatment and metallurgical processing. Read More
Have you ever been handed a failure investigation and have not been quite sure of all the steps required to complete the investigation? Or perhaps you had to review a failure investigation and wondered if all the aspects had been properly covered? Or perhaps you read a failure investigation and wondered what to do next? Here is a chance to learn the steps to organise a failure investigation Read More
This course provides students with a fundamental understanding of the design process necessary to make robust medical devices. Fracture, fatigue, stress analysis, and corrosion design validation approaches are examined, and real-world medical device design validations are reviewed. Further, since failures often provide us with important information about any design, mechanical and materials failure analysis techniques are covered. Several medical device failure analysis case studies are provided Read More
This course provides essential knowledge to those who do not have a technical background in metallurgical engineering, but have a need to understand more about the technical aspects of steel manufacturing, properties and applications.
Read More
Profit from failure analysis techniques, understand general failure analysis procedures, learn fundamental sources of failures. This course is designed to bridge the gap between theory and practice of failure analysis.
Read More
This course is designed as an extension of the Introduction to Heat Treatment course. It discusses advanced concepts in thermal and thermo-chemical surface treatments, such as case hardening, as well as the principles of thermal engineering (furnace design) Read More
Composites are a specialty material, used at increasing levels throughout our engineered environment, from high-performance aircraft and ground vehicles, to relatively low-tech applications in our daily lives. This course, designed for technical and non-technical professionals alike, provides an overarching introduction to composite materials. The course content is organised in a manner that guides the student from design to raw materials to manufacturing, assembly, quality assurance, testing, use, and life-cycle support Read More
An ideal first course for anyone who needs a working understanding of metals and their applications. It has been designed for those with no previous training in metallurgy, such as technical, laboratory, and sales personnel; engineers from other disciplines; management and administrative staff; and non-technical support staff, such as purchasing and receiving agents who order and inspect incoming material.
Read More
Taking a fundamentals approach, this course is presented as an introduction to the world of induction heat treating. The course will cover the role of induction heating in producing reliable products, as well as the considerable savings in energy, labor, space, and time. You will gain in-depth knowledge on topics such as selecting equipment, designs of multiple systems, current application, and sources and solutions of induction heat treating problems Read More
Titanium occupies an important position in the family of metals because of its light weight and corrosion resistance. Its unique combination of physical, chemical and mechanical properties, make titanium alloys attractive for aerospace and industrial applications. Read More
www.materialsaustralia.com.au
Materials Australia members are involved in all aspects of materials science, technology and engineering. Members include manufacturing technical officers, professional engineers, academics, research scientists, technical staff and students. Our members are experts in polymers, nano and biomaterials, ceramics, metals, composites and all of their engineering applications.
There are two types of Materials Australia membership available: Individual and Corporate.
Individual members can join Materials Australia as a Student Member, Graduate Member, Standard Member, Retired Member or a Certified Materials Professional (CMatP).
Corporate members can opt for a Standard, Premium, or Premium Plus membership package.
• Accreditation as a Certified Materials Professional (CMatP) if eligible.
• Discounts on all Materials Australia conferences and training courses, including the CAMS and APICAM Conferences.
• Digital subscription to Materials Australia Magazine, our quarterly publication that is jam-packed with industry, product, technical and research news.
• Discounts on advertising in Materials Australia Magazine.
• Conferences, training courses, workshops and regular branch meetings, designed to facilitate continued professional development.
• Outstanding networking opportunities through regular branch meetings, conferences and training courses.
• Regular branch newsletters full of information on local activities.
• Discounts on advertising in Materials Australia Magazine.
• Editorial support for articles in Materials Australia Magazine.
• Digital subscription to Materials Australia Magazine.
• Free employment listings on the Materials Australia website.
• Free company listing on the Materials Australia website.
• Free company listing in the Materials Australia Magazine.