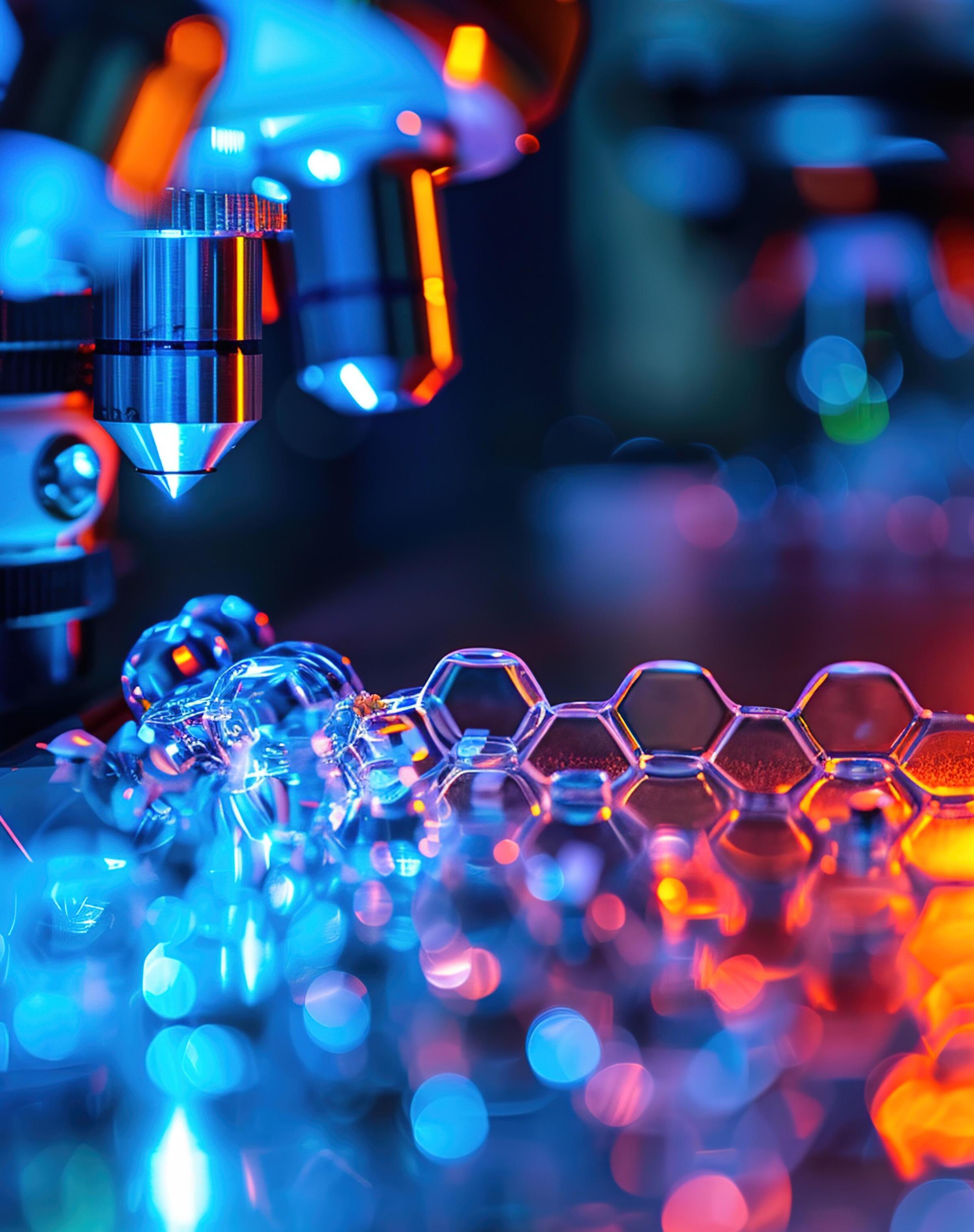
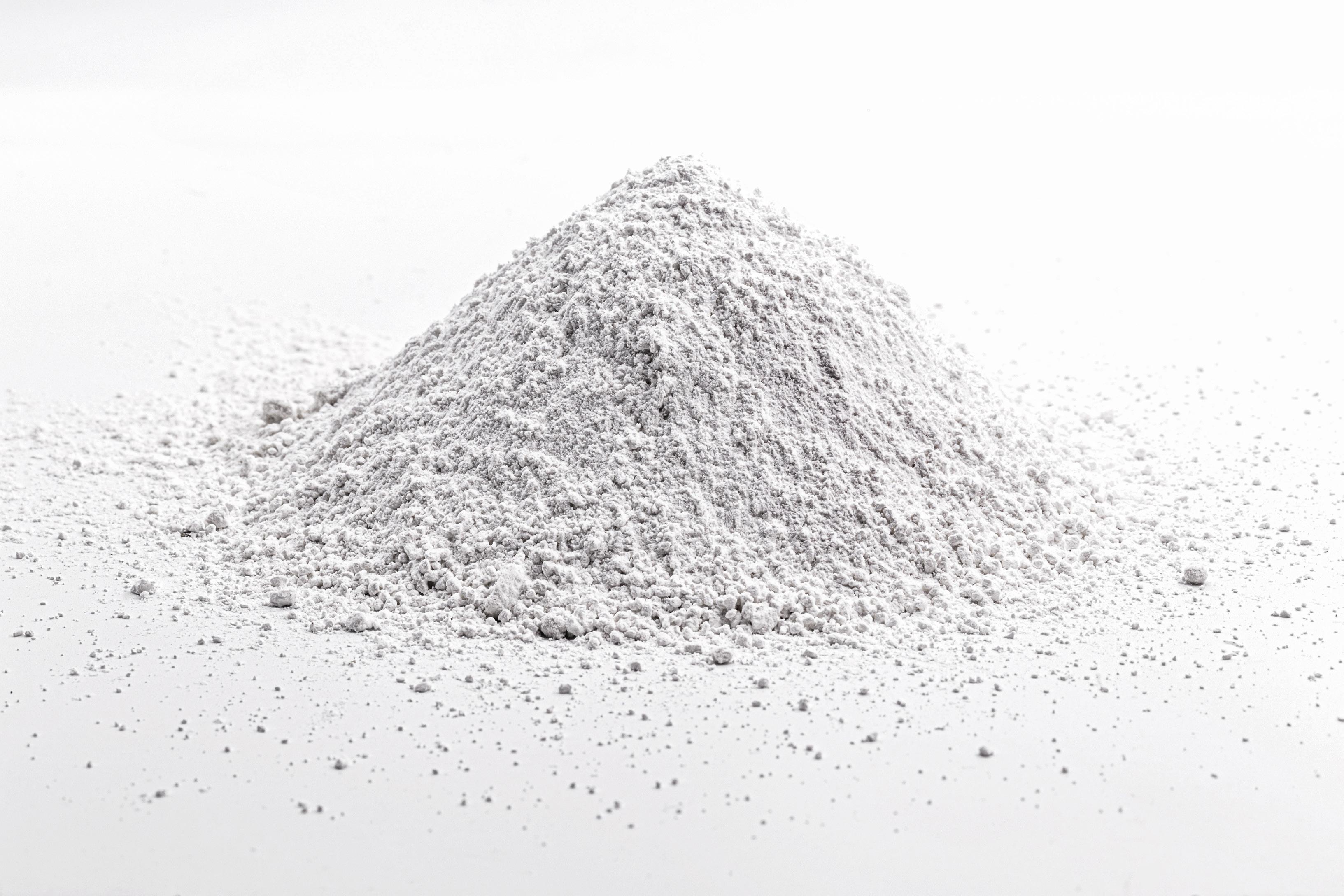
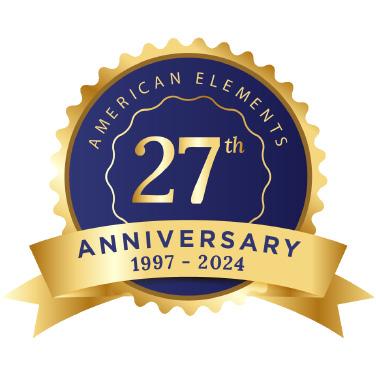
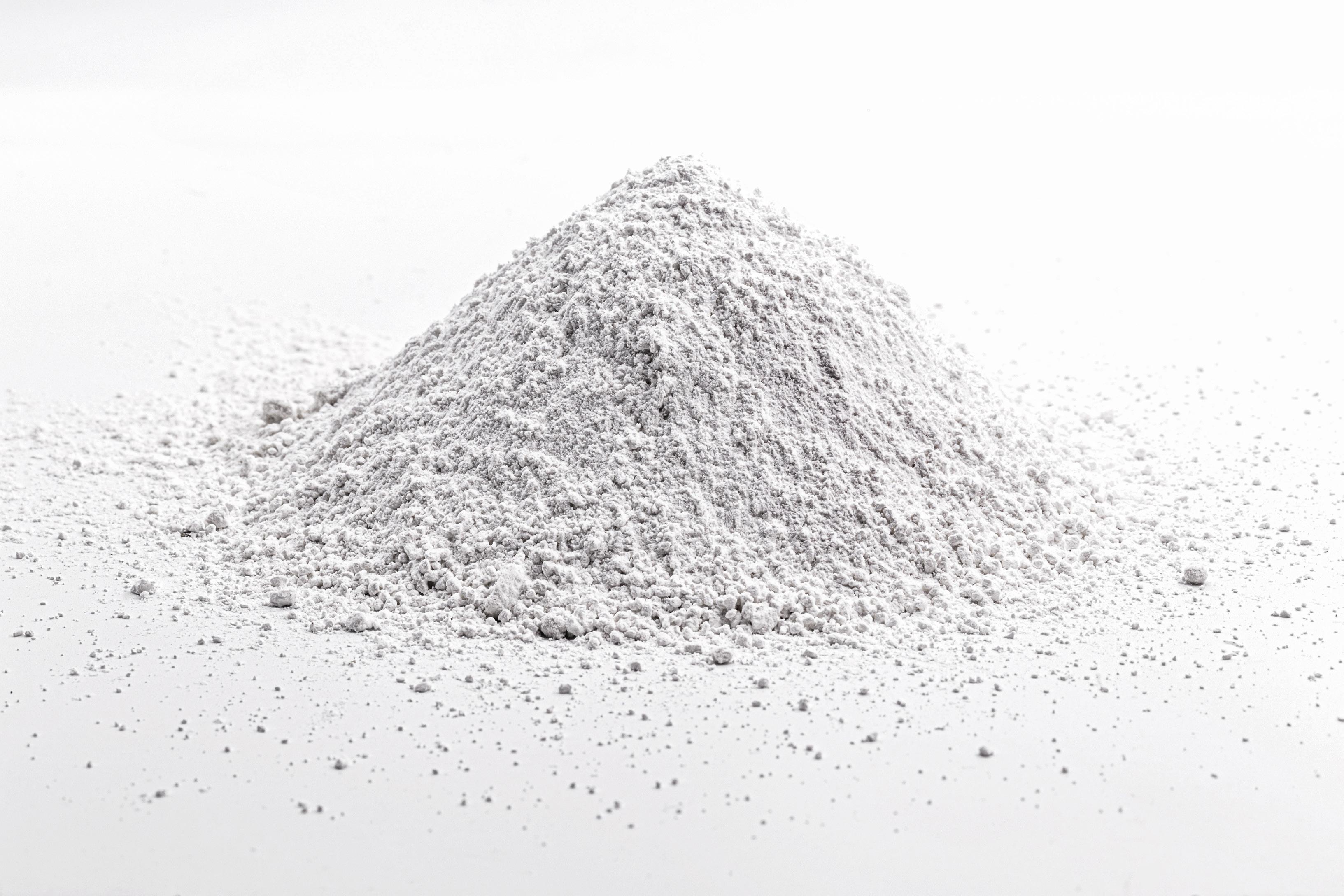
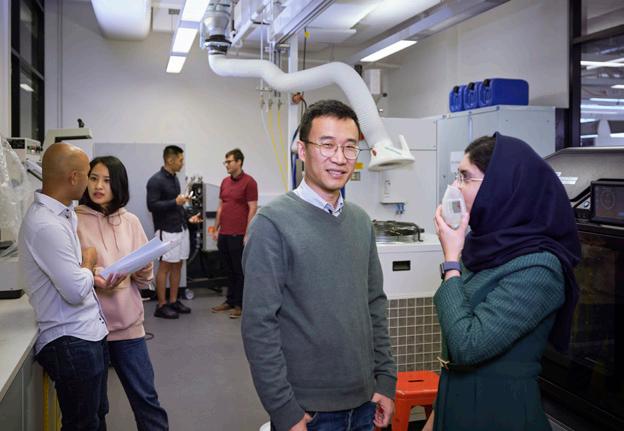
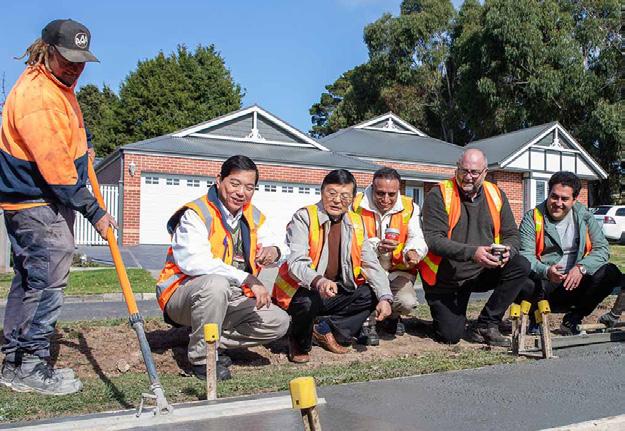
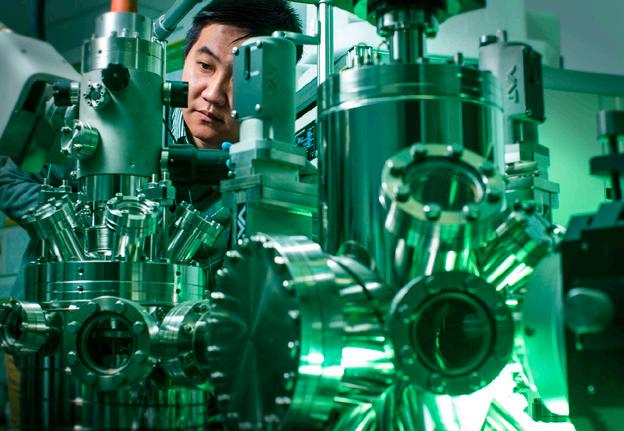
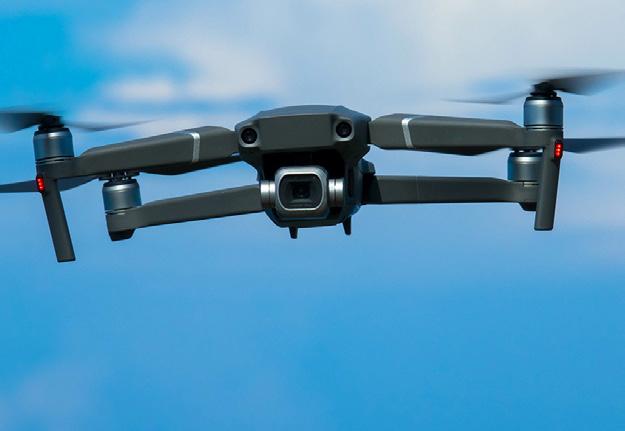
Materials engineering in Australia is a vibrant community, characterized by cuttingedge research, industry collaboration, and a growing focus on sustainability. As a country, we really do punch above our weight in materials science and engineering. Australia represents only 0.3% of the worlds population, yet Australia publishes about 5% of the worlds scientific literature on materials science. Although the United States and Europe still dominate the list of the worlds best research centres, the QS rankings show that Australia has two universities (UNSW and Monash) in the world top 50 for Materials Science and Engineering. We also have amazing materials research organisations such as CSIRO and ANSTO.
Most of our success in materials comes from our historical investment in mining and metallurgy. The mining industry remains a cornerstone of Australia’s economy, and is
a significant driver of materials engineering research and innovation. Innovations such as more efficient separation technologies and the development of advanced materials for ore processing are hot topics. Researchers are also exploring ways to recycle and repurpose mining waste, aligning with broader goals of sustainability and circular economy.
The materials field is broad reaching, our community is one of the most diverse. We have people studying macroscopic problems such as environmentally sustainable concrete, all the way to microscopic research such as atom probe tomography. Research is becoming increasingly computational, with some materials scientists living completely in the theoretical worlds of atomistic simulations. We’re blessed in Australia
Materials Australia National Office PO Box 19
Parkville Victoria 3052 Australia
T: +61 3 9326 7266
E: imea@materialsaustralia.com.au W: www.materialsaustralia.com.au
NATIONAL PRESIDENT Nikki Stanford
MANAGING EDITOR
Gloss Creative Media Pty Ltd
EDITORIAL COMMITTEE
Prof. Ma Qian
RMIT University
Dr. Jonathan Tran
RMIT University
Tanya Smith
MATERIALS AUSTRALIA
ADVERTISING & DESIGN MANAGER
Gloss Creative Media Pty Ltd Rod Kelloway 0418 114 624
PUBLISHER
Materials Australia Technical articles are reviewed on the Editor’s behalf
PUBLISHED BY Institute of Materials Engineering Australasia Ltd.
B.Eng(Hons) Ph.D. CMatP
to have access to a vast network of open access research facilities such microscopy and mechanical test labs throughout the country. For a country of such a modest population, we really have everything a materials enthusiast could need. Our biggest challenge is distance, its not easy to transport a specimen from Perth to Sydney, but we do manage to find a way. If your not yet convinced about how exceptional materials science and engineering is in Australia, I invite you have a look through the names on the Materials Australia Silver Medal winners list. Power houses like Ian Polmear, Max Hatherly and Simon Ringer all appear as famous Australians that have made their mark on the global materials community.
At Materials Australia, our goal is to bring our amazing community together. If you’d like to celebrate our breadth, excellence and achievements, you still have time to register for CAMS 2024. And don’t forget APICAM in July 2025!
Best Regards
Nikki Stanford
National President Materials Australia
This magazine is the official journal of Materials Australia and is distributed to members and interested parties throughout Australia and internationally.
Materials Australia welcomes editorial contributions from interested parties, however it does not accept responsibility for the content of those contributions, and the views contained therein are not necessarily those of Materials Australia.
Materials Australia does not accept responsibility for any claims made by advertisers.
All communication should be directed to Materials Australia.
Advertisers - September 2024
Source: Dr Laura Machuca, TECHT
Dr Laura Machuca Suarez holds a degree in microbiology and gained her PhD in Chemistry at Curtin University. There, she went on to play a leading role in research collaborations with the petroleum industry aimed at dealing with microbiologically induced corrosion (MIC). Subsequently Laura has become a co-founder and director of TECHT, a Western Australia company that provides technology and services to the energy and resources sector in the areas of corrosion and asset integrity management. She leads BioTECHT, the division of TECHT that focuses on biocorrosion, biodeterioration and biodegradation. Microbial life processes can lead to undesirable effects, including material decay and premature industrial equipment failure. This had been the topic of a previous presentation Laura
had made to this branch of MA, in which she had described the nature of MIC and the critical role of biofilms, as well as describing ways of mitigating MIC. However, as Laura stressed, microbes also hold the key to healthier living, clean energy solutions, efficient waste management, and numerous sustainable applications.
For this presentation, Laura placed the focus on the extraordinary bioelectrochemical machinery of microbes, such as bacteria, and on their profound impact on materials and sustainable development. She stressed that understanding the microbial world is not only crucial for averting harm but also for harnessing their potential.
To set the scene, Laura pointed out that there is no getting away from microbes. They make up the bulk of all
biomass on Earth and there are more of them in a gram of garden soil than there are human beings on this planet. They originated 3.8 billion years ago, and species have evolved to thrive in a wide, and quite extreme, range of environments. Their main structural features are a cell wall, separating the organism from the environment, and containing ribosomes (for protein synthesis) and a nucleoid (holding their DNA); the cell wall may also have external appendages (such as flagellae) allowing movement.
Like all life forms, microbes require energy to function. From a bioelectrochemical point of view, all life involves a flow of electrons down an energy gradient. Thus, a microbe needs a source of electrons to take in, and a sink to which electrons can be expelled at a lower energy.
The 8th conference of the Combined Australian Materials Societies, incorporating Materials Australia and the Australian Ceramic Society.
Our technical program will cover a range of themes identified by researchers and industry as issues of topical interest.
Symposia Themes
> Additive manufacturing
> Advances in materials characterisation
> Metals, alloys, casting & thermomechanical processing
> Biomaterials & nanomaterials for medicine
> Ceramics, glass and refractories
> Corrosion & wear
> Materials for energy generation, conversion and storage
> Computational materials science - simulation & modelling
> Nanostructured/nanoscale materials and interfaces
> Progress in cements, geopolymers and innovative building materials
> Surfaces, thin films & coatings
> Polymer technology
> Composite technology
> Waste materials and environmental remediation/recycling
> Semiconductors and electronic materials
> Materials for nuclear and extreme environments
> Advances in Science and Technology of Ceramics (AOCF)
In the case of metallic MIC, a metal is the source of electrons. For aerobic bacteria, oxygen acts as the electron sink. Thus overall, the metal is converted to its metallic oxide, just as in electrochemical corrosion. The difference is that the microbe uses the energy difference to operate its own life processes, which in additional to the fundamental process of reproduction, typically include excreting extracellular polymeric substances that bind to the surface, forming biofilms. These typically grow into multi-species self-supporting colonies maintaining and accelerating the corrosion for the benefit of the microbial community and making the biofilm increasingly difficult to remove.
However, oxygen is not the only sink for electrons. Anaerobic bacteria can expel lower energy electrons to reduce dissolved molecules such as nitrates and sulphates. Other microbes can expel electrons directly to insoluble materials, such as mineral surfaces.
Consequently, depending on the species, MIC need not require oxygen. It is a major problem in the petroleum industry, where it is reckoned to account for around 20% of the cost of corrosion. Furthermore, metals are not the only source of electrons. Polymers and composites are also subject to MIC
In practice, low flow velocities, crevices, temperature, etc., can combine to facilitate establishment of biofilms, and the microbial communities within them. These communities are distinct from their individual members and exhibit complex behaviours. For example, the community can establish defensive barriers against chemical treatments. At the individual level, some bacteria are able to supply electrons directly to other bacteria that are not in direct contact with the source. Laura showed a video of one species forming conductive filaments (nano wires) to ‘feed hungry neighbours’.
With such well adapted, tenacious and ubiquitous life forms, the first objective
for MIC control is to make it difficult for them to attach to a metallic surface in the first place, with clean surfaces, flow velocity and biocides.
Laura then turned to other aspects of microbial life processes, pointing out that in nature there is ‘no waste, only a resource to be transformed’. Pointing out the promise of a ‘circular bioeconomy’, she gave examples including degradation of pollutants together with production of electricity in microbial fuel cells. She also referred to the CSIRO ‘Carbon Lock’ research program aimed at removing atmospheric carbon dioxide biologically, and to the local biotech company Uluu, which has developed a microbiological process to produce biodegradable PHA (biological polyester) from seaweed.
Laura’s presentation was enlightening to the many in the audience who had been unsure of how MIC related to ordinary corrosion and why it is so challenging to manage.
Source: Ivan Cole
The Victoria and Tasmania Branch hosted two great outreach events in the last few months, and is looking forward to some of our favourite events of the year.
At the end of April, we hosted an event titled Steel Industry –Changing of the Guard. Professor Geoffrey Brooks (Professor of Sustainable Mineral Processing at Swinburne University) outlined the changes in steel making as the industry looks forward to a greener future, based on circular economy principles. Professor Brooks touched on the push towards decarbonisation of steel production, the major options to achieving decarbonisation and exciting developments in Australia in this area.
In June, we ran a forum on the Directions of Materials Research in Europe. The forum featured prominent experts from across Europe, including:
• Javier Gravalos (Senior Manager Innovation Partnership, RMIT University, Barcelona Campus)
• Tomáš Prošek (President, European Federation of Corrosion)
• Dr Mira Todorova (Head of Group, Electrochemistry and Corrosion, Max Planck Institute for Sustainable Materials)
• Dr Taner Tunç (Associate Professor, Sabanci University)
The panel outlined changes in materials research and industry from machining to metal alloy coatings, computational modelling for materials design, and partnerships and engagement. The strong synergies between Australian and European research and technical directions were evident, as were the opportunities for Australian companies and organisations in Europe.
In July, we had the privilege of being the first Materials Australia Branch to host the SEAM Roadshow. Professor Chris Berndt (Swinburne University) outlined the great work that the Australian Research Council Training centre for Surface Engineering for Advanced Materials (SEAM) has carried out over the last five years. This work spans a wide range of surface technologies including additive manufacturing, laser and thermal spray, cold spray and nano scale surface modification and thin films.
Over the next few months we will host some of our favourite events for the year, including the Technologists Picnic, the Boreland Forum, the Gifkins Lecture and, of course, our cross society Christmas Party. If you haven’t already registered for these exciting events, now is the time to do so. Simply visit the Materials Australia website for futhter details: https://www.materialsaustralia.com.au/events
Our prefabricated electronic components and substrates greatly reduce processing time for semiconductor material characterisation and FET-based sensor construction. Quickly build field-effect transistors with pre-patterned, back-gated, interdigitated electrodes featuring reliable ohmic contacts and large channel width-to-length ratios. Our back-gated LOFET circuits simplify material characterisation, and we offer unique substrates and prefab electronic components for micro/ nanoelectronic applications.
SigmaAldrich.com/materials
Source: Alan Todhunter - NSW President.
The currently has a number of engaging events on the calendar, and in the works.
The 2024 CMatP mini-conference will be hosted online on Wednesday 25 September. A Zoom link will be sent out to members approaching the date. This annual event always proves popular, and is a wonderful opportunity to hear the research areas of our fellow materials experts.
The Australian Research Council Training Centre in Surface Engineering for Advanced Materials (SEAM) roadshow will be held on Monday 21 October followed by a presentation at University of Wollongong the next day on Tuesday 22 October. More details will be posted closer to the event date. Distinguished Professor Christopher C. Berndt (Director ARC Industrial Transformation Training Centre, SEAM) will give a presentation on the background for the establishment of SEAM, the professional model by which SEAM interacts with industry, universities and national labs, as well as case histories that document SEAM’s successes.
Some examples of SEAM and industrial interactions include:
• Refurbishment and Enhancement of Mining Equipment: Over the past four years, SEAM has supported D&T to develop a high-quality laser cladding process. This has enabled D&T to refurbish a wider range of heavy-industry parts, in a range of materials. Each part is optimised for different end-use applications, with performance often exceeding OEM specifications.
• Coating and Repair of Manufactured Components:
LaserBond partnered with SEAM to develop advanced process sensing enabling on-line defect detection. Unlocking a deeper understanding of product and process enabled better control, improving product quality, while adding capabilities that open the door to new products and services.
• Surface Optimisation of Components Using an Additive/ Subtractive Machine: Rosebank brought a need for a highspeed thin-film surface engineering capability to SEAM. These developments in additive manufacturing will increase the production efficiency and decrease costs, as well as provide lab-measured confidence in the performance of these new coatings.
A Steelworks Tour at Bluescope in Wollongong is under discussion. These tours offer great insights into the inner workings of the steelworks. At the Basic Oxygen Steelmaking (BOS) plant, attendees can climb to the furnace floor for the best vantage point. Inside the BOS control room, you’ll see the 1600-degree Celsius process to transform molten iron into steel.
The high steel gantries of the BOS and the Continuous Slab Caster offer a birds eye view of the fascinating process of pouring molten steel into casting machines. In the tour’s final stage, you can see the Hot Strip Mill or Plate Mill. Further details will be made available as soon as possible.
1-3 July 2025 RMIT UNIVE RSIT Y, ME LBOURNE
CALL FOR
The 4th Asia-Pacific International Conference
on Additive Manufacturing (APICAM) is the not-to-be-missed industr y conference of 2025.
The 4th Asia-Pacific International Conference on Additive Manufacturing (APICAM) is the not-to-be-missed industry conference of 2025.
APICAM was created to provide an oppor tunit y for industr y professionals and thinkers to come together, share knowledge and
engage in the t ype of net working that is vital to the fur thering of the additive manufacturing industr y
Some of the leading minds in the industr y will give presentations on pressing issues and the ways in which innovations can navigate
challenges Impor tant areas such as 3D printing and additive
manufacturing in the automotive, biomedical, defence and aerospace
industries will be covered by exper ts from each respective field
The purpose of this conference is to provide a focused forum for the presentation of advanced research and improved understanding of
various aspects of additive manufacturing
The APICAM2025 organizing commit tee is seeking abstracts for
either an oral or poster presentation
CLOSES: 1 March 2025
Abstracts are able to be submit ted
in the following areas:
Additive Manufacturing Defence Application
Additive Manufacturing Green/Clean Energy
Additive Manufacturing Space Application
Additive Manufacturing Post- Processing
Bioprinting and Biomaterials
Ce rami
M
M
Po
Sustainabilit y
Dr. Shareen Chan (postdoctoral fellow) working on the microstructural analysis of laser-clad coatings.
Shareen Chan is a Postdoctoral Fellow with the Australian Research Council (ARC) Industrial Transformation Training Centre on Surface Engineering for Advanced Materials (SEAM) at Swinburne.
Shareen is a multi-disciplinary engineer by training, with a PhD in chemical and biomedical engineering (2024) from the University of Melbourne, and an Honours in mechanical engineering (2009) from the National University of Singapore. Between degrees, she worked as an engineer then assistant laboratory manager in a quality assurance (QA) testing multi-national company. Having completed her PhD in 2024, her previous experiences working across both industry and academia made her ideally placed to take on her current role as a postdoctoral researcher at the SEAM ARC training centre.
For Shareen, the attractions of the new role included the opportunity to conduct innovative research across a range of projects, while remaining firmly grounded in areas of industrial relevance. From a technical aspect, Shareen was able to apply her robust knowledge of materials engineering, processing and characterisation immediately to the projects, while growing her knowledge in other areas such as metallurgy. At SEAM, Shareen primarily supports industrial R&D projects with industrial partners D&T Hydraulics and Engineering in Mackay, Queensland, and Titomic in Mount Waverley, Victoria. In addition to her technical skills, these projects offered Shareen to put apply her project management skills to work, taking over leadership of research activities with the D&T Hydraulics
project. Furthermore, having the opportunity to work across the interface of academia and industry provides Shareen with opportunities to continuously hone her skills in communicating and translating research findings to stakeholders at all levels.
While all the industrial projects Shareen supports share a common base in materials engineering, each also has a different area of specialisation. The project with D&T Hydraulics and Engineering works to optimise laser cladding processes, to repair and refurbish damaged or compromised components. The project with Titomic focuses on refinement and validation of cold spray additive manufacturing processes, including novel developments with machine learning for process optimisation. Meanwhile, another project collaborating with industry involves developing effective antibacterial coatings to service the food industry.
In addition to project management and conducting handson testing and analysis of results, Shareen also actively applies her own experiences and knowledge to assist with mentoring and training of other early career researchers (ECRs), and the supervision of higher degree research students (HDRs).
Shareen recognises the advantages of being a part of an ARC training centre like SEAM. Such centres equip ECRs and HDRs with crucial skills for working in both academic and industrial environments. The wide variety of SEAM projects fosters innovation and the ability to work seamlessly within multidisciplinary teams. This in turn prepares graduates to become leaders in academia and industry alike, offering far-reaching benefits to the Australian economy. R&D solutions developed at the university have been applied to commercial products, and the feedback from industry partners has been extremely positive. The work done by Shareen and the team at SEAM all help to foster growth of local research talent, as well as support Australia to stay at the cutting-edge in STEM innovation.
As a woman in science and engineering, Shareen is appreciative of the opportunity to promote her research and to inspire young girls that women can also excel in the STEM fields. The ARC and SEAM are thanked for providing equal opportunities to women of merit, such as Shareen, and are praised for their strong vision for diversity and inclusion.
For more information about SEAM, please visit www.arcseam.com.au/ or email seam@swinburne.edu.au
Founded in 2019 as a partnership between three universities, SEAM’s mission is to help solve critical surface engineering problems faced by industry, while training up talented industry-ready graduates for our future.
Cutting tools are essential across many industries, such as aerospace, construction, and electronics
Founded in 2019 as a partnership between three universities, SEAM’s mission is to help solve critical surface engineering problems faced by industry, while training up talented industry-ready graduates for our future.
national science and research priorities by providing nuclear-based analytical techniques and world-class Australian Centre for Neutron Scattering and the Australian cutting-edge research including surface engineering
Sutton Tools, an Australian company based in Melbourne, is recognized globally as a market leader in the
ANSTO supports the national science and research priorities by providing access to advanced nuclear-based analytical techniques and world-class facilities, such as Australian Centre for Neutron Scattering and the Australian Synchrotron, to conduct cutting-edge research including surface engineering carried out by SEAM
ROMAR engineering is working with SEAM to use the full flexibility of direct energy deposition additive and subtractive manufacturing unit to improve the quality of their built components The focus of the project is on reducing residual stress, voids and maximizing surface properties
Working with industry partner LaserBond during his PhD studies at ARC ITTC SEAM, (now) Dr Andre Hatem compared the characteristics of commercial water-atomised (WA) and gas-atomised (GA) AISI 431 stainless steel powders and their influence on the tribological and corrosion performance of laser metal deposition (LMD - also known as laser cladding) elements
Working with DMTC, LaserBond and McTaggart Scott Australia, (now) Dr Alexander Osi designed, manufactured, assembled, and tested a functional hydraulic piston rod prototype, made of polymer-matrix composite, and successfully coated with WC-10Ni-5Cr
used in cutting tool production for both HSS (High Speed Steel) and Tungsten Carbide substrates Dr Minh Nhat Dang achieved this during his PhD at SEAM by developing a custommade electrochemical apparatus and carefully selected electrolytes and process conditions This innovation brings significant commercial benefits to the cutting tool industry, enhancing manufacturing efficiency and tool quality.
ROMAR engineering is working with SEAM to use the full flexibility of direct energy deposition additive and subtractive manufacturing unit to improve the quality of their built components The focus of the project is on residual stress, voids and maximizing surface
Dr Dang has since transitioned to his current role as an Application Engineer at ANCA, where he continues to advance the field
It was found that WA powders absorb more laser energy than GA powders and this led to a large difference in cladding properties Previously, most studies involving LMD correlated properties using the Global Energy Density function However, such an analysis excluded important factors, such as energy absorption of the powder, that have since been found to significantly influence the cladding properties A key recommendation by Dr Hatem was that proper reporting of deposition conditions be made, so that inter-study relationships can be more meaningfully compared The findings from the study enabled LaserBond to provide claddings with improved quality and performance to their customers
Achieving a reduction in weight of up to 63% compared to conventional nickel aluminium bronze alloy piston rods, there are immediate implications for numerous industries with increased efficiency, reduced fuel consumption, increased payload capacity and overall operational performance.
Superior Shot Peening has partnered with SEAM, focusing on developing peening and protective coating technologies for application inside internal diameters of pipelines commonly used in oil and gas industries The collaboration aims to deliver a solution for addressing corrosion and durability issues in the field
Dr Hatem is currently a Mechanical Engineer in Submarine Systems at ASC Pty Ltd
According to LaserBond’s Hugo Howse, “this project has not only academic quality but also a working prototype which in academic research, is very rare ” While Ryan Yeates of McTaggart Scott Australia added that this project has created “not just a theory, but a piece of hardware we can take to industry”.
Dr Osi is now employed in a supervisory role with Nexans
Founded in 2019 as a partnership between three universities, SEAM’s mission is to help solve critical surface engineering problems faced by industry, while training up talented industry-ready graduates for our future See more: https://arcseam.com.au
Dr Xiaopeng Li is currently an Associate Professor in the School Mechanical and Manufacturing Engineering at UNSW Sydney, leading a research group working on additive manufacturing and advanced materials research.
Xiaopeng received his PhD degree in Materials Engineering from The University of Queensland, Australia in 2013, where his PhD thesis won the Best Thesis Award by Australian Research Council Centre of Excellence for Design in Light Metals in 2013. After his PhD, he joined The University of Western Australia as an Assistant Professor, working on additive manufacturing of metallic glasses, light alloys and their composites till 2016. Following this, he joined one of the world-famous additive manufacturing groups led by Prof JeanPierre Kruth in KU Leuven, Belgium as a Research Fellow till 2017. In 2020, Dr Li was awarded Australian Research Council DECRA Fellow. Since 2020, Dr Li is listed as World’s Top 2% Scientists in Materials & Applied Physics & Enabling Strategic Technologies in the database of the most-cited scientists developed at Stanford University.
Where do you work?
Describe your job.
I work at the University of New South Wales (UNSW) Sydney, where I hold the position of Associate Professor in the School of Mechanical and
Manufacturing Engineering. In my role, I lead a dynamic research group focusing on additive manufacturing and advanced materials. My responsibilities encompass a wide range of activities, including teaching undergraduate and graduate courses on additive manufacturing, supervising PhD and postdoctoral researchers, and conducting pioneering research projects. I also engage in extensive collaboration with national and international institutions, and work closely with industry partners to translate research findings into practical applications. Additionally, I am involved in community engagement initiatives and contribute to the development of innovative technologies that advance the field of additive manufacturing.
What inspired you to choose a career in materials science and engineering?
My journey into materials science and engineering was fueled by a deep-seated curiosity about the fundamental building blocks of the world around us. During my undergraduate studies in materials science and engineering, I became fascinated by the potential of materials to revolutionize various technologies. The idea that we can design and engineer materials with specific properties to address realworld challenges captivated me. This fascination was further nurtured by the exposure to cutting-edge research and the realization of the vast impact that advancements in materials science can have on industries such as healthcare, aerospace, and manufacturing. This combination of curiosity and the desire to make a tangible difference in the world inspired me to pursue a career in this exciting and impactful field.
Who or what has influenced you most professionally?
My professional journey has been shaped by several influential mentors and collaborative experiences. Distinguished Professor Ma Qian, who supervised my PhD, played
a pivotal role in developing my research skills and instilling a rigorous scientific approach. His guidance and encouragement were instrumental in shaping my early career. Additionally, my time as a Research Fellow at KU Leuven under the mentorship of Professor Jean-Pierre Kruth provided invaluable insights into advanced additive manufacturing techniques. Collaborative experiences with leading institutions such as Stanford, MIT, and EPFL have also enriched my professional development, exposing me to diverse perspectives and cutting-edge research. These experiences, combined with the support of my colleagues and the inspiration drawn from the collective pursuit of innovation, have significantly influenced my professional growth.
What has been the most challenging job or project you've worked on to date and why?
The most challenging project I've undertaken was the rapid development of an on-demand manufacturing capability for personal protective equipment (PPE) and critical medical device components during the COVID-19 pandemic. This project required us to swiftly innovate and adapt our existing additive manufacturing technologies to address urgent public health needs. The technical challenges were formidable, involving the design and production of reliable and scalable manufacturing processes under unprecedented time constraints. Coordinating efforts with a diverse team of academics, government officials, and industry partners added another layer of complexity. Despite these challenges, the project's success in delivering vital supplies during a critical period was immensely rewarding and highlighted the transformative potential of additive manufacturing in emergency response scenarios.
What does being a CMatP mean to you?
Being a Chartered Materials Professional (CMatP) represents
a significant milestone in my career, reflecting a recognition of my expertise and commitment to the field of materials science and engineering. It signifies adherence to the highest standards of professional excellence and integrity, and connects me with a community of like-minded professionals dedicated to advancing the discipline. The designation serves as a testament to my continuous pursuit of knowledge and innovation, and it underscores my commitment to contributing to the advancement of materials science through research, teaching, and community engagement. It is both an honour and a responsibility that I take very seriously.
What gives you the most satisfaction at work?
The most satisfying aspect of my work is witnessing the tangible impact of our research on society. Whether it's through the development of innovative medical implants that enhance patient outcomes or the creation of advanced manufacturing techniques that drive industry advancements, knowing that our efforts make a real difference is incredibly fulfilling. Additionally, mentoring students and seeing them grow into confident, capable professionals is a source of great pride. The collaborative nature of our work, the excitement of discovering new knowledge, and the opportunity to contribute to solving real-world problems all contribute to my sense of satisfaction and purpose in my career.
What is the best piece of advice you have ever received?
The best piece of advice I've ever received is to stay curious and never stop learning. The field of materials science and engineering is constantly evolving, and maintaining a sense of curiosity drives innovation and discovery. This advice has kept me open to new ideas and technologies, allowing me to continuously advance my research and teaching. Additionally, I've learned the importance of perseverance and resilience—pursuing ambitious goals often involves overcoming obstacles,
and staying determined and adaptable is key to achieving success.
What are you optimistic about?
I am optimistic about the future of additive manufacturing and its potential to revolutionize various industries. The advancements we are making in materials design and manufacturing processes will lead to more sustainable, efficient, and innovative solutions. I am particularly excited about the potential for additive manufacturing to address complex challenges in healthcare, such as personalized medical implants and on-demand production of critical components. Additionally, the growing emphasis on interdisciplinary collaboration and the increasing integration of artificial intelligence and machine learning into our field are promising developments that will accelerate progress and unlock new possibilities.
What have been your greatest professional and personal achievements?
Professionally, one of my greatest achievements is leading a successful research group at UNSW and contributing to significant advancements in additive manufacturing. Securing substantial funding, publishing influential research papers, and receiving prestigious awards such as the ARC DECRA Fellowship have been major
milestones in my career. Personally, co-founding a spin-out company focused on orthopaedic implants and making a meaningful impact during the COVID-19 pandemic are achievements I am particularly proud of. These accomplishments reflect my dedication to both advancing scientific knowledge and applying it to solve real-world problems.
What are the top three things on your “bucket list”?
Develop a Breakthrough Medical Implant: I aspire to create a nextgeneration medical implant that significantly improves patient recovery and quality of life. This goal reflects my passion for applying materials science to address critical healthcare challenges.
Global Research Collaboration: Establishing a global research network that brings together leading experts to tackle major challenges in materials science and engineering is a key ambition. I believe that interdisciplinary and international collaboration is essential for driving innovation and making significant scientific advancements.
Adventure Travel: Exploring some of the most remote and beautiful places on Earth is a personal dream. Combining my love for adventure with a deeper understanding of different cultures and environments will enrich my life and provide new perspectives that can inspire my work.
The following members of Materials Australia have been certified by the Certification Panel of Materials Australia as Certified Materials Professionals.
They can now use the post nominal ‘CMatP‘ after their name. These individuals have demonstrated the required level of qualification and experience to obtain this status. They are also required to regularly maintain their professional standing through ongoing education and commitment to the materials community.
We now have nearly 200 Certified Materials Professionals, who are being called upon to lead activities within Materials Australia. These activities include heading special interest group networks, representation on Standards Australia Committees, and representing Materials Australia at international conferences and society meetings.
A/Prof Alexey Glushenkov ACT
Dr Syed Islam ACT
Prof Yun Liu ACT
Dr Avik Sarker ACT
Dr Olga Zinovieva ACT
Prof Klaus-Dieter Liss CHINA
Mr Debdutta Mallik MALAYSIA
Prof. Jamie Quinton NEW ZEALAND
Dr Amir Abdolazizi NSW
Ms Maree Anast NSW
Dr Edohamen Awannegbe NSW
Ms Megan Blamires NSW
Prof John Canning NSW
Dr Phillip Carter NSW
A/Prof Igor Chaves NSW
Dr Evan Copland NSW
Mr Peter Crick NSW
Mr Seigmund Jacob Dollolasa NSW
Prof Madeleine Du Toit NSW
Dr Ehsan Farabi NSW
Prof Michael Ferry NSW
Dr Yixiang Gan NSW
Mr Michele Gimona NSW
Dr Bernd Gludovatz NSW
Dr Andrew Gregory NSW
Mr Buluc Guner NSW
Dr Ali Hadigheh NSW
Dr Alan Hellier NSW
Prof Mark Hoffman NSW
Mr Simon Krismer
Prof Jamie Kruzic
Prof Huijun Li
Dr Yanan Li
A/Prof Xiaopeng Li
Dr Hong Lu
NSW
NSW
NSW
NSW
NSW
NSW
Mr Rodney Mackay-Sim NSW
Dr Matthew Mansell
Dr Warren McKenzie
Mr Edgar Mendez
Mr Sam Moricca
NSW
NSW
NSW
NSW
Dr Ranming Niu NSW
Dr Anna Paradowska NSW
Prof Elena Pereloma
A/Prof Sophie Primig
Dr Gwenaelle Proust
Miss Zhijun Qiu
Dr Blake Regan
Mr Ehsan Rahafrouz
Dr Mark Reid
Prof Simon Ringer
Dr Richard Roest
Mr Sameer Sameen
Dr Bernd Schulz
Dr Luming Shen
Mr Sasanka Sinha
Mr Frank Soto
Mr Michael Stefulj
Mr Carl Strautins
Mr Alan Todhunter
Ms Judy Turnbull
Mr Jeremy Unsworth
Dr Philip Walls
Dr Alan Whittle
Dr Richard Wuhrer
Dr Vladislav Yakubov
Mr Deniz Yalniz
NSW
NSW
NSW
NSW
NSW
NSW
NSW
NSW
NSW
NSW
NSW
NSW
NSW
NSW
NSW
NSW
NSW
NSW
NSW
NSW
NSW
NSW
NSW
NSW
Dr Michael Bermingham QLD
Mr Michael Chan QLD
Prof Richard Clegg QLD
Mr Andrew Dark QLD
Dr Ian Dover QLD
Mr Oscar Duyvestyn QLD
Mr John Edgley QLD
Dr Jayantha Epaarachchi QLD
Dr Jeff Gates QLD
Mr Payam Ghafoori QLD
Mr Mo Golbahar QLD
Dr David Harrison QLD
Dr Janitha Jeewantha QLD
Dr Damon Kent QLD
Mr Jaewon Lee QLD
Mr Jeezreel Malacad QLD
Mr Sadiq Nawaz QLD
Dr Saeed Nemati QLD
Mr Bhavin Panchal QLD
Mr Bob Samuels QLD
Mr Ashley Bell SA
Ms Ingrid Brundin SA
Mr Neville Cornish SA
A/Prof Colin Hall SA
Mr Brendan Dunstall SA
Mr Nikolas Hildebrand SA
Mr Mikael Johansson SA
Mr Rahim Kurji SA
Mr Andrew Sales SA
Dr Thomas Schläfer SA
Dr Christiane Schulz SA
Prof Nikki Stanford SA
Prof Youhong Tang SA
Mr Kok Toong Leong SINGAPORE
Dr Muhammad Awais Javed VIC
Dr Ossama Badr VIC
Dr Christian Brandl VIC
Dr Qi Chao VIC
Dr Ivan Cole VIC
Dr John Cookson VIC
Miss Ana Celine Del Rosario VIC
Dr Yvonne Durandet VIC
Dr Mark Easton VIC
Dr Rajiv Edavan VIC
Dr Reza Emdad VIC
Dr Peter Ford VIC
Mr Bruce Ham VIC
Ms Edith Hamilton VIC
Dr Shu Huang VIC
Mr Long Huynh VIC
Dr Jithin Joseph VIC
Mr. Akesh Babu Kakarla VIC
Mr Russell Kennedy VIC
Mr Daniel Lim VIC
Dr Amita Iyer VIC
Mr Robert Le Hunt VIC
Dr Thomas Ludwig VIC
Dr Roger Lumley VIC
Mr Michael Mansfield VIC
Dr Gary Martin VIC
Dr Siao Ming (Andrew) Ang VIC
Mr Glen Morrissey VIC
Dr Khurram Munir VIC
Dr Mostafa Nikzad VIC
Dr Eustathios Petinakis VIC
Dr Leon Prentice
Dr. Muhammad Mehran Qadir VIC
Dr Dong Qiu
Mr John Rea VIC
Miss Reyhaneh Sahraeian VIC
Dr Christine Scala VIC
Mr Khan Sharp VIC
Dr Vadim Shterner VIC
Mr Mark Stephens VIC
Dr Graham Sussex VIC
Dr Kishore Venkatesan VIC
Mr Pranay Wadyalkar VIC
Dr Wei Xu VIC
Dr Ramdayal Yadav VIC
Dr Sam Yang VIC
Dr Matthew Young VIC
Mr Angelo Zaccari VIC
Dr Yuman Zhu VIC
Mr Mohsen Sabbagh Alvani WA
Dr Murugesan Annasamy WA
Mr Graeme Brown WA
Mr John Carroll WA
Mr Sridharan Chandran WA
Mr Conrad Classen WA
Mr Chris Cobain WA
Mr Adam Dunning WA
Mr Stuart Folkard WA
Mr Toby Garrod WA
Prof Vladimir Golovanevskiy WA
Mr Chris Grant WA
Dr Paul Huggett WA
Mr Ivo Kalcic WA
Mr Srikanth Kambhampati WA
Mr Ehsan Karaji WA
Mr Ka-Seng Leung WA
Mr Mathieu Lancien WA
Dr Evelyn Ng WA
Mr Deny Nugraha WA
Mrs Mary Louise Petrick WA
Mr Johann Petrick WA
Mr Biju Kurian Pottayil WA
Dr Mobin Salasi WA
Mr Daniel Swanepoel WA
Mr James Travers WA
Source: Materials Australia
Accreditation as a Certified Materials Professional (CMatP) gives you recognition, not only amongst your peers, but within the materials engineering industry at large. You will be recognised as a materials scientist who maintains professional integrity, keeps up to date with developments in technology, and strives for continued personal development.
The CMatP, like a Certified Practicing Accountant or CPA, is promoted globally as the recognised standard for professionals working in the field of materials science.
There are now well over one hundred CMatPs who lead activities within Materials Australia. These activities include heading special interest group networks, representation on Standards Australia Committees, and representing Materials Australia at international conferences and society meetings.
Benefits of Becoming a CMatP
• A Certificate of Membership, often presented by the State Chapter, together with a unique Materials Australia badge.
• Access to exclusive CMatP resources and website content.
• The opportunity to attend CMatP only networking meetings.
• Promotion through Materials Australia magazine, website, social media and other public channels.
• A Certified Materials Professional can use the post nominal CMatP.
• Materials Australia will actively promote the CMatP status to the community and employers and internationally, through our partner organisations.
• A CMatP may be requested to represent Materials Australia throughout Australia and overseas, with Government, media and other important activities.
• A CMatP may be offered an opportunity as a mentor for student members.
• Networking directly with other CMatPs who have recognised levels of qualifications and experience.
• The opportunity to assume leadership roles in Special Interest Networks, to assist in the facilitation of new knowledge amongst peers and members.
A Certified Materials Professional is a person to whom Materials Australia has issued a certificate declaring they have attained all required professional standards. They are recognised as demonstrating excellence, and
possessing special knowledge in the practice of materials science and engineering, through their profession or workplace. A CMatP is prepared to share their knowledge and skills in the interest of others, and promote excellence and innovation in all their professional endeavours.
The criteria for recognition as a CMatP are structured around the applicant demonstrating substantial and sustained practice in a field of materials science and engineering. The criteria are measured by qualifications, years of employment and relevant experience, as evidenced by the applicant’s CV or submitted documentation.
Certification will be retained as long as there is evidence of continuing professional development and adherence to the Code of Ethics and Professional behaviour.
Contact Materials Australia today: on +61 3 9326 7266 or imea@materialsaustralia.com.au or visit our website: www.materialsaustralia.com.au
Source: Sally Wood
The Australian National Fabrication Facility (ANFF) Materials Node, housed at the University of Wollongong’s (UOW) Innovation Campus, has been awarded $800K as part of the NSW Government’s National Collaborative Research Infrastructure Strategy (NCRIS) Support Program 2024-2025.
This co-funding underpins an existing $1.094 million per annum in National Collaborative Research Infrastructure Strategy (NCRIS) funding provided to the UOW’s Materials Node over five years from 2024-2028.
The Materials Node, which includes UOW and the University of Newcastle, applied as a part of a NSW Consortium of ANFF Nodes, which includes ANFF-NSW (University of Sydney, University of New South Wales and University of Technology Sydney), ANFF OptoFab (UMQ) Nodes, to share in the multi-million-dollar funding targeted at open access New South Wales strategic research infrastructure.
A total of $15.2 million over two years from the NSW Government’s NCRIS Support Program has been invested in research and development facilities, including the $3.2 million to ANFF’s facility Nodes in NSW.
“Once again, the NSW Office of the Chief Scientist and Engineer (OCSE) has recognised the incredible return on investment that state-of-the-art infrastructure can bring. This latest round of funding will see a continuation of the amazing services on offer at the six ANFF locations across
New South Wales,” said ANFFCEO Jane Fitzpatrick.
“The continued support of the NSW Government, via the OCSE, is pivotal as it underpins the Materials Nodes staffing,” said ANFF Materials Node Director Peter Innis.
“This funding also ensures that the Materials Nodes infrastructure continues to support UOW’s research efforts through its role within UOW’s research platforms. This investment underpins research efforts in materials and biomaterials development as well as ensuring the Node’s capabilities in advanced polymer, metal, ceramic and bio additive fabrication and 3D printing remains at the stateof-the-art and openly accessible to all users.”
“We recognise the vital role NCRIS facilities play in supporting the state’s research and development sector,” said NSW Chief Scientist & Engineer Hugh Durrant-Whyte.
“These facilities enable the most advanced research and commercialisation opportunities to happen right here in NSW. These activities are a critical driver for innovation in the state’s economy.”
The Commonwealth Government announced $650 million over four years to fund 80 projects across 15 facilities under the NCRIS. All projects align to the Commonwealth Government’s $15 billion National Reconstruction Fund. Eight of these facilities will also receive funding from the NSW Government under the NCRIS Support Program to support 10 projects. Together, this increases the scale of infrastructure investment and capability in NSW.
Since the Commonwealth Government established the NCRIS Program in 2006-2007, the NSW Government has now provided more than $65 million to NSW-based NCRIS facilities through the Office of the Chief Scientist & Engineer.
A recent return-oninvestment analysis by Lateral Economics estimated the benefits derived from NCRIS at $7.50 for every dollar of investment.
NETZSCH’s latest innovation, the STA 509 Jupiter® Series, is redefining the landscape of thermal analysis. This cutting-edge instrument series, comprising the Classic, Select, and Supreme models, is meticulously designed to cater to the diverse needs of quality control and materials development laboratories.
The STA 509 Jupiter® Series boasts several new features that elevate its performance. An optional piercing device for the 20-sample-position ASC empowers researchers to handle moisture-sensitive materials with precision. The new gas switch valve system facilitates seamless transitions between humid and dry atmospheres, delivering unmatched control over experimental conditions.
For the demanding realm of
hydrogen-based materials testing, the H₂Secure system ensures unparalleled safety while enabling research in pure hydrogen or controlled hydrogeninert gas mixtures. This modular system allows for dedicated hydrogen analysis without compromising the instrument’s versatility for other applications.
The STA Series harnesses the power of Proteus ® 9 software, featuring customizable menus, workspaces, and a robust search engine for streamlined analysis. The groundbreaking AutoEvaluation function automates the detection of critical thermal events, including mass changes, exothermic/endothermic effects, and glass transitions, saving time and enhancing objectivity. Identify, a revolutionary software
component, performs automatic curve recognition and material identification by comparing results against a comprehensive database of over 1,300 entries. This unparalleled capability accelerates material characterization and identification processes.
The STA 509 Jupiter® Series, coupled with advanced software solutions and a wide range of accessories, empowers researchers to explore the thermal behavior of diverse materials, including polymers, composites, ceramics, metals, pharmaceuticals, and environmental samples. With its exceptional flexibility, precision, and reliability, this instrument is poised to become the gold standard in thermal analysis.
For more information, please contact at.au@netzsch.com
Source: By Arora, Sonakshi, ThermoFisher and ATA Scientific
From the early warning signs of workplace exposure to asbestos in the 1930s [1] to today's advanced detection technologies, the journey of asbestos awareness is marked by significant scientific and regulatory milestones. The use of asbestos in building materials, notably for thermal and acoustic insulation and structural reinforcement, peaked in the mid-20th century. Thereafter, the health hazards associated with asbestos exposure prompted technological advancements and regulatory changes that have transformed how we detect and manage this dangerous material.
Asbestos fibres are notorious for their resilience and hazardous nature. When inhaled, these microscopic fibres can cause serious health issues, including asbestosis, lung cancer, and mesothelioma [2]. The latency period for these diseases can be decades long, making early detection and prevention critical. This danger, coupled with the widespread use of asbestos, necessitated robust methods for detecting and identifying asbestos fibres.
Asbestos is a naturally occurring silicate mineral, often used in construction, where it is mixed with cement or woven into fabric. Asbestos is known to be hazardous to human health, causing serious and fatal illnesses, including lung cancer and asbestosis. In more than 50 countries, asbestos has been banned since the early 1970s, with strict regulations in place concerning its use.
Since the mid-20th century, technologies for asbestos testing worldwide are limited to primary methods such as optical microscopy (OM) and polarized light microscopy (PLM) to identify asbestos fibres. These techniques relied on the visual examination, which push the optical systems’ capabilities to detect as small as 200nm fibres. Additionally, optical microscopy lacks the material analysis capability to distinguish between the six different asbestos silicates, making it difficult to accurately identify all types of asbestos fibres. The resolution limitation and labour-intensive nature of these techniques have driven the search for more advanced, automated and efficient systems.
As the limitations of OM and PLM became apparent, the field of asbestos detection saw a significant shift towards electron microscopy (EM). Specifically scanning
electron microscopy is employed for asbestos testing, tailored to different sample types such as air filters used in environmental monitoring, bulk building materials, soil samples, and even water samples where asbestos fibres might be present.
In Europe, stringent regulations mandate the use of EM for asbestos analysis, ensuring higher accuracy and safety in asbestos detection and management [3]. Despite the EU's ban on asbestos nearly two decades ago, it remains a threat due to its presence in older buildings. The new regulations further reduce the maximum permissible exposure limit to 0.01 fibres of asbestos per cubic centimetre, which is ten times lower than the earlier limit. Following a maximum transition period of six years, member states will have to implement electron microscopy (EM) as the standard method for measuring asbestos levels, eventually replacing optical techniques and can measure thinner asbestos fibres, enhancing detection accuracy and worker safety.
In Australia, the situation is equally dire. More than 4,000 Australians die each year from asbestos-related diseases. An estimated 6,000,000 tonnes of asbestos material remains in the built environment, present in one in three homes across the country. Research indicates that initiative-taking asbestos removal from buildings could prevent up to 28,000 deaths by 2100 [4]. The Australian government has responded with updated regulations, including the AS 5370:2024 standard, which adopts and changes ISO 22262-1:2012. This standard specifies methods for sampling and identifying asbestos in bulk materials, ensuring comprehensive and effective management of asbestos in the built environment.
To this end, The Thermo Fisher Scientific, Inc. Phenom XL G2 Desktop SEM has recognised the need for advanced asbestos testing and has been consistently delivering.
Not only does it follow the requirements of the standards but also provides added benefits:
• High Resolution – With a resolution capability down to 10 nanometres, it can accurately identify 200-nanometer asbestos fibres.
• Large Sample area - Its large sample area 100mm x 100mm allows for extensive multiple sample analysis in a single session, enhancing efficiency.
• High speed – High quality imaging in just 40 seconds facilitates quick analysis.
• Small footprint - Its compact design makes it suitable for small labs and larger facilities alike. Only a power connection is needed to operate the system, making it ideal for on- and off-site inspections, crucial for timely quality.
• Automated Workflows: Automated fibre analysis workflows reduce operator intervention and increase consistency [5].
• Comprehensive Reporting: The one-click report feature provides immediate, actionable results.
In addition, Thermo Fisher Scientific offers the Asbestos Scan solution as a specialised tool for inspecting
filters for asbestos presence. It systematically moves through consecutive fields with no overlap, inspecting a defined region of interest and incorporates SEM and EDS capabilities. This process is fully compliant with ISO standard 14966, offering significant support to operators and alleviating their workload.
Conclusion
The integration of high-resolution imaging, large sample capacity, time efficiency, footprint, and automation in modern SEMs of the Phenom XL G2 represents a new era in asbestos detection. These advancements not only comply with stringent regulatory standards but also provide practical benefits that enhance the safety and efficiency of asbestos management practices. Thereby making the future of asbestos detection promising and vital for continued public health and safety.
DON’T WAIT - BOOK YOUR PERSONAL DEMO & START USING THE PHENOM XL G2 DESKTOP SEM TODAY!
For more information contact us
ATA Scientific Pty Ltd +61 2 9541 3500 enquiries@atascientific.com.au www.atascientific.com.au
References:
[1] Järvholm B, Burdorf A. Asbestos and disease - a public health success story? Scand J Work Environ Health. 2024 Mar 1;50(2):53-60. doi: 10.5271/sjweh.4146. Epub 2024 Feb 7. PMID: 38323897; PMCID: PMC10924740.
[2] https://www.asbestos.com/exposure/
[3] Directive (EU) 2023/2668 amending Directive 2009/148/EC on the protection of workers from the risks related to exposure to asbestos at work.
[4] Phase Three Asbestos National Strategic Plan 2024-2030 - https:// www.asbestossafety.gov.au/what-we-do/asbestos-and-silica-safety-and-eradication-agency
[5] Advancing Asbestos Analysis in Bulk Samples with Artificial Intelligence - https://www.sgs.com/en/whitepapers/advancing-asbestos-analysis-in-bulk-samples-with-artificial-intelligence-form
Source: Sally Wood
Freshly brewed coffee concrete may be coming to a street near you after RMIT University teamed up with Macedon Ranges Shire Council to conduct a world-first coffee concrete footpath trial.
Several other upcoming infrastructure projects around Victoria, Australia, will also turn spent coffee grounds into biochar and transform this waste into a valuable resource for the construction industry.
The RMIT team will partner with Australian-owned BildGroup – a civil infrastructure, asphalt paving and road profiling company – to deliver these other circular-economy projects.
Organic waste going to landfill, including spent coffee grounds, contributes 3% of greenhouse gas emissions, but Dr Rajeev Roychand and his colleagues at RMIT are set on transforming this waste into a valuable resource for the construction industry.
Organic waste cannot be added directly to concrete because it would decompose over time and weaken the building material. To overcome this challenge, the team has developed a technique to make concrete 30% stronger by using coffee biochar made with a low-energy process without oxygen at 350 degrees Celsius, to give the drink-additive a “double shot” at life and reduce waste going to landfill.
Australia generates 75 million kilograms of ground coffee waste every year – most of it goes to landfills, but it could replace up to 655 million kilograms of sand in concrete because it is a denser material. Globally, 10 billion kilograms of spent coffee is generated annually, which could replace up to 90 billion kilograms of sand in concrete.
“It's very exciting to see this worldfirst trial of our coffee and woodbased biochar in these footpaths collaboration with Macedon Ranges
Shire Council,” said Roychand from the School of Engineering.
“It's really important for Council to be involved in projects such as this and to be working closely hand in hand with universities such as RMIT.
The researchers will evaluate the performance of the concrete in these trial footpaths in Gisborne, with the aim of supporting the further roll out of this innovation.
“We are currently working in the supply chain sector so that we can make this research into a mainstream product for commercial applications, and we’re not only looking into coffee – we're expanding this into all forms of different organic waste,” Roychand said.
The trial with Macedon Ranges Shire Council did not reduce the amount of cement normally used to make concrete for footpath projects, but the RMIT team plans to experiment with using less cement.
Ease of use is what the Phenom Pharos name has come to mean. All the capabilities of a floor-standing FEG-SEM have been housed in a tabletop model with the simplicity that Phenom desktop SEMs are known for.
Ease of use is what the Phenom Pharos name has come to mean. All the capabilities of a floor-standing FEG-SEM have been housed in a tabletop model with the simplicity that Phenom desktop SEMs are known for.
1. Super fast, sharp, high contrast images
Speeds up project work and provides high -end imaging and analysis critical for many fields from materials, forensics to industrial manufacturing and even life sciences.
2. Unsurpassed user experience
2. Unsurpassed user experience
2. Unsurpassed user experience
Easy to use without extensive training or SEM experience means the Phenom is accessible to everyone.
Easy to use without extensive training or SEM experience means the Phenom is accessible to everyone.
Easy to use without extensive training or SEM experience means the Phenom is accessible to everyone.
3. Multiple detectors reveal finer details
3. Multiple detectors reveal finer details
3. Multiple detectors reveal finer details
Fully integrated EDS and SE detector together with a low -kV beam (1 kV) allows thin contamination layers on the surface can be observed (Phenom Pharos).
Fully integrated EDS and SE detector together with a low -kV beam (1 kV) allows thin contamination layers on the surface can be observed (Phenom Pharos).
Fully integrated EDS and SE detector together with a low -kV beam (1 kV) allows thin contamination layers on the surface can be observed (Phenom Pharos).
4. Intuitive software with advanced automation
4. Intuitive software with advanced automation
4. Intuitive software with advanced automation
Simply click and go to work or use automated recipes with elemental mapping and line scan functionality.
Simply click and go to work or use automated recipes with elemental mapping and line scan functionality.
Simply click and go to work or use automated recipes with elemental mapping and line scan functionality.
5. Huge time and money saver
5. Huge time and money saver
5. Huge time and money saver
Provides rapid, multi -scale information in-house for process monitoring and improvement.
Provides rapid, multi -scale information in-house for process monitoring and improvement.
Provides rapid, multi -scale information in-house for process monitoring and improvement.
• Field Emission Gun (FEG) SEM with 1 - 20 kV range
• NEW STEM Sample Holder
• For
✓
MADE IN GERMANY
Source: Sally Wood
Geotextile lining systems are essential components of composite lining systems in modern landfills to contain waste and leachates seeping into soil and waterways, but new research has revealed they may be part of the problem – instead, spreading potentially harmful ultra short-chain PFASs into the environment.
PFASs, or per- and poly fluoroalkyl substances, are chemicals used in various textile manufacturing and fabric treatment applications for stain and water protection. They are also notorious as ingredients in firefighting foams.
Although the full extent of the risks of PFAS to humans is unknown, the chemicals can remain in humans and the environment for years and as a precaution exposure should be minimised.
Researchers, including the Institute for Frontier Materials’ Associate Professor Will Gates, analysed perand poly fluoroalkyl substances (PFAS) in geotextiles commonly used in geosynthetic composite lining systems for waste containment facilities.
The research revealed that the geotextiles do contain the ultrashort chain PFAS compound pentafluoropropionic acid (PFPrA)
– usually considered a breakdown product of other PFAS. Although smaller PFAS are considered less toxic and used in many consumer products, they also appear to disperse further and are present everywhere they have been looked for.
“This body of research has revealed the fact that materials used for mitigation may form part of the problem,” said Associate Professor Gates.
“PFPrA was detected in 100% of all samples from polypropylene geotextiles and at least 70% of all polyester geotextiles at concentration that potentially pose environmental risks – from products used to contain contaminants themselves.”
“All geotextiles tested had been locally manufactured in Australia between 2020 and 2022 from imported virgin plastics. These results lead to questions as to whether PFPrA is as much breakdown product as believed.”
In landfill, geotextiles are used together with other materials and products to stabilise the subsoil and side slopes; serve as filters, root barriers and protective layers for critical components, such as leach collection pumps; and are an integral part of composite liners, for example, geosynthetic clay liners.
“Normally geotextiles are used in conjunction with geomembranes, or high-density polyethylene sheets,”
Associate Professor Gates said.
Associate Professor Will Gates contributed to the paper, “Are Geotextiles Silent Contributors of Ultrashort Chain PFASs to the Environment”, which analysed per- and poly fluoroalkyl substances (PFAS) in geotextiles commonly used in geosynthetic composite lining systems for waste containment facilities. Image credit: Deakin University.
“However, the recent explosion of research into the presence and quantification of all sorts of PFAS in various environments (natural and anthropic) and in various manufactured products has shown that they are everywhere. Basically, wherever one searches, one finds them.”
Associate Professor Gates, who specialises in sustainable and durable infrastructure materials, previously showed that PFAS contaminated soil, after being remediated through a novel heat treatment process, could be used as fine aggregate for concrete and mortar.
Now, he hopes to continue his research on improving PFAS containment with modern engineered lining systems.
“Landfill lining systems are an important part of critical infrastructure. The EU has recently instigated legislation to eliminate the use of any PFAS in the manufacture of geomembranes, or high-density polyethylene products used in landfill lining. I expect other jurisdictions will follow suit.”
Source: Sally Wood
More than almost any other substance on Earth, lithium (Li) is valued as a 21st century treasure. But Australia's race to unlock its lithium is challenged by political and economic headwinds both global and domestic.
Why Lithium?
Lithium is a critical mineral and is vital to modern technology. It has become synonymous with the future of energy storage, already powering electric vehicles and renewable grids. Thanks to its lightweight, high energy density properties, lithium is ideal for rechargeable batteries.
As more countries transition to cleaner energy and zero emissions, the demand for lithium has skyrocketed. But securing a stable supply of lithium is hard, especially finding it and extracting it efficiently.
Finding Lithium can be Tricky and Processing it Harder
Dr Ryan Manton is a Research Scientist in our Hydrothermal Footprints team. He is no stranger to the barriers of lithium exploration,
such as finding deposits buried under cover, and the task of characterising complex pegmatite mineralogy.
"Most, if not all, hard rock lithium deposits in Australia have been found in outcrops. This is where portions of the deposits, which are known as pegmatites, stick up above the ground. And many of them have been found by accident or from historical mining of other metals, such as tin oxides or nickel sulphides," Ryan said.
"Many recent world-class lithium hardrock deposits have been found this way in Western Australia. World-class roughly means more than 100 million tonnes of resources per deposit, with ore grades of 1.5 per cent lithium oxide (Li2O). This begs the question: how many large deposits are buried under cover, that are yet to be discovered?"
Meanwhile, petrophysical studies, looking at how the properties of rocks interact with fluids, examine the density, magnetic susceptibility and seismic properties needed to guide geophysical exploration.
Characterisation techniques for
regolith, the loose ground that covers solid rock, can shed light on what sits above the mineralised lithium pegmatites. It's an arsenal that equips researchers to identify hidden deposits beneath the Earth's surface, potentially unlocking vast, untapped swathes of lithium.
We have a potential gamechanger in LithSonic, a patented metal production process that uses supersonic flow dynamics to enhance the dissolution of lithium from ores.
Our patented technology activates a carbothermic reduction of lithium oxide to generate lithium metal vapor. A carbothermic reduction is a chemical reaction involving the reduction of substances using carbon as the reducing agent.
Dr Nick Wilson is our Team Leader for Electron Microscopy and Analysis. He thinks that ICP-OES is actually one of the more straightforward techniques for bulk characterisation of lithium.
"But it's also important to be able to characterise lithium spatially within a sample, so you can see which mineral phases it sits in. There are many techniques that can characterise lithium at different length scales," Nick says.
More broadly, our initiatives in lithium-ion battery recycling point to our commitment to using the critical mineral sustainably. Emerging recycling technologies both reduce the environmental impact and recover valuable lithium resources. The circular economic approach echoes the current global spirit of sustainable resource management. Along with nickel and cobalt, lithium is precious to a world electrifying transport and cutting emissions, an existential step towards global climate targets.
By Dr. Cameron Chai, AXT PTY LTD
Australia continues to occupy a leading position in the global research community. AXT continue to identify and source the latest technologies to assist the Australian research community with maintaining their position at the cutting edge. Consequently, they have teamed up with Exum Instruments and now offer their unique MassboxTM, Laser Ablation, Laser Ionisation Time of Flight Mass Spectrometry (LALI-TOF-MS) Instrument.
Exum Instruments was founded in 2017 by Jeff Williams. Disillusioned with shortcomings of existing analytical techniques, he developed
LALI-TOF-MS technology. LALI-TOFMS can take any solid material and rapidly identify the full periodic table of its constituents. Packaged into a compact, desktop instrument, the MassboxTM delivers:
1. Quantitative analysis – down to trace level for all elements in the periodic table
2. Elemental mapping – on areas up to 83x83mm down to 5µm resolution
3. Depth profiling – ideal for analysis of surface modifications, the systems’ laser typically removes 10’s of nanometers per shot
4. Rapid screening – Ultrafast analysis allows users to identify unknown materials or detect trace elements in just seconds
AXT’s Managing Director, Richard Trett said, “when I first learned about the MassboxTM I was extremely excited about its potential to disrupt existing technologies. My expectations have been confirmed by high-profile researchers who I have spoken to about the MassboxTM and its capabilities. This instrument could very well shake up several fields such as materials science, battery research, chemistry, environmental and earth science. In fact, we are looking at installing one in our Automated Mineralogy Incubator facility in Perth due to its potential in the mining and minerals sector.”
Exum’s CEO and CTO, Jeff Williams said, “from my background in cosmochemistry, I got to use nearly every analytical instrument in the field. This experience inspired me to start a company focused on transforming the way solid samples are analysed. I am thrilled and proud to have AXT represent our MassboxTM and help us grow across different market segments. We are especially excited to leverage their expertise in the mining and mineral sector and we look forward to working in partnership with AXT.”
The MassboxTM from Exum Instruments is now available from AXT.
For more information on the MassboxTM, please visit https://www.axt.com.au/products/ massbox-lali-tof-ms/
By Dr. Cameron Chai and Peter Airey
Laser Powder Bed Fusion (LPBF) is the technique of choice when it comes to metal 3D printing, providing greater levels of flexibility and speed compared to machining and casting, especially when dealing with complex shapes. LPBF becomes an even more attractive option when dealing with more exotic materials, where material expense becomes a serious consideration.
Two common issues encountered when 3D printing metal parts are cracking and distortion which can occur during the printing process. While it is possible to overcome these problems by optimising printing parameters, it can take several iterations before arriving at the optimal processing procedure. While time required goes up, the increased number of iterations may become
an issue if material is in short supply and/or expensive.
Cracking and distortions are normally a result of thermal stresses brought about by thermal gradients and rapid cooling. The problem can be exacerbated when dealing with brittle materials e.g. cermets and hightemperatures alloys. And while there are many off the shelf materials, your application may also require an alloy that isn’t readily available in powder form, or you may need a powder with different properties e.g. particle size. In such cases you can tailor make your own alloy powders using systems like the Amazemet rePowder which uses ultrasonic atomisation.
To prevent cracking and distortion, preheating is the solution. Aconity3D’s metal 3D printers (with the exception
of their small benchtop system) offer heated build plates which help to reduce thermal stresses. While this certainly helps, the effectiveness is reduced as the build height increases and the distance from the build plate increases.
Higher end systems like the AconityTWO, have multiple lasers and allow lasers to be configured for preheating. In this case, the laser/s can be configured to preheat and/or post heat the region where the metal powder is being fused, again reducing thermal stresses and minimising the likelihood of cracking and distortion. For more details, visit axt.com.au
Source: Damien Yiyuan Khoo Senior Applications Scientist, Bruker Nano Surfaces and Metrology Division
Over the years, modern machining technologies have driven an enormous increase in cutting-tool development. Such development notably adds value to the machining of mechanical components that require threaded parts for accurate and fast assemblies. Typically, these threads are produced using either cutting or forming tap during the last stage of component manufacturing. The internal threading is a highly complex operation where characteristics of threaded material, metalworking fluid, and the tapping tool all need to be optimised to ensure product quality. This application note discusses how the Bruker UMT TriboLab™ tapping torque test rig is specifically designed to provide both fast monitoring of tapping process conditions and precise analysis of the process performances.
The tapping torque test rig shown in Figure 1 consists of a UMT TriboLab configured with a high-speed rotary drive, a torque sensor, and a tapping torque kit. In a typical test, an uncoated high-speed, size 10 steel tapping tool is inserted into the rig’s chuck holder while a workpiece pre-drilled with an 8.5 mm hole is placed in to the sample holder. Approximately 5 mL of metalworking fluid (MWF) is then added to fill up the hole of the workpiece as coolant and lubricant. In this study, the tapping accuracy and precision were enhanced with the synchronism feature between the machine rotation and feed motion. For the purpose of demonstrating the rig performance, three different types of pre-drilled hex blanks (6061-T6 aluminium, C360 brass, and 1215 steel) were tapped (see Figure 2). A commercially available heavy-duty MWF was used, without any further dilution, to lubricate the tapping process. The test parameters are presented in Table 1. Each tapping
process was repeated five times using a new workpiece for each test. The system’s software provided realtime torque, friction coefficient, tap depth, and multi-channel acquisition of important data to enable easy determination of the tapping torque efficiency.
The test methodology and evaluation approach in this study were adapted from two normative tapping torque test standards: ASTM D5619 00 (2011)1 and ASTM D8288 19.2 Briefly, an M10 cutting tap is fed into a nut blank while the machine rotates in the opposite direction as the nut blank interior is threaded. Simultaneously, resulting torque values are acquired by the system’s torque sensor. Figure 3 shows the torque profiles for three metals exhibiting large differences of shear modulus (80 to 26 GPa) and hardness (Brinell hardness 95 to 167). This covers most common manufacturing applications where 1) brass is used for roll threading and knurling; 2) T6 aluminium is used for aircraft or marine fittings; and 3) 1215 steel is used for rod rolling or wiring. To compile statistics and ensure consistency of collected data, each material was screened five times
Description Values
Spindle speed (rpm)
Feed rate (mm/sec)
Hole depth (mm) 17.5 (through hole)
Hole diameter (mm) 8.5
Tapping tool
M10x1.5, HSS, chip clearing
Lubricant volume (ml) 5
Workpiece material (nut blank)
C360 brass
6061-T6 aluminium 1215 steel
Workpiece dimension (mm x mm) 8.5 x 17.50
(a) Aluminum: (5.41+/-0.03) N.m.;
(b) Brass: (7.40+/-0.05) N.m.;
(c) Steel: (9.48+/-0.06) N.m.
The torque values varied from 5.4 Nm to 9.48 Nm for the three types of threaded nuts. From these values, it can be deduced that the 6061-T6 aluminium, which produced the lowest torque value among the three alloys, has the best machinability. On the other hand, the 1215 steel with the highest torque value demonstrated poorer machinability due to its 50% higher hardness and three-fold higher shear modulus than brass or aluminium. Overall,
(a) Aluminium: (5.41+/-0.03)
(b) Brass: (7.40+/-0.05) N.m.
(c) Steel: (9.48+/-0.06) N.m.
best matching components. Due to the modularity of UMT TriboLab, lubricant performance can be easily assessed through the 4-ball setup,3 and coating on tapping tools can be characterized via scratch test.4
Bruker’s UMT TriboLab tapping torque test rig provides flexible and practical tapping torque evaluation of tool materials, metalworking fluids, and workpiece material combinations. Different sizes of tapping tools, ranging from M2 to M10, and their respective pre-drilled counterparts can be used for evaluating both cutting tap and forming tap performance efficiencies. By complementing the tapping torque test rig with multiple sensors, automated test procedures, and data presentation, UMT TriboLab offers unprecedented modularity and performance that is ideal for various types of ASTM, DIN, SAE, and other customized tests.
the tapping torque test rig on UMT TriboLab proved to be highly repeatable with dispersion well under 1%, which fully complies with acceptance criterion defined by ASTM D5619. Besides evaluating the performance of cutting tap as described in this study, a similar test approach could be utilised to assess forming tap. With such accuracy and the short time to result, this setup is ideal for wide screening over tapping tools, lubricant/cooling fluids, and machined materials. Threading conditions can also be seamlessly varied to quickly converge toward best machining conditions with best matching components. Due to the modularity of UMT TriboLab, lubricant performance can be easily assessed through the 4-ball setup,3 and coating on tapping tools can be characterised via scratch test4 .
Bruker’s UMT TriboLab tapping torque test rig provides flexible and practical tapping torque evaluation of tool materials, metalworking fluids, and workpiece material combinations. Different sizes of tapping tools, ranging from M2 to M10, and their respective pre-
drilled counterparts can be used for evaluating both cutting tap and forming tap performance efficiencies. By complementing the tapping torque test rig with multiple sensors, automated test procedures, and data presentation, UMT TriboLab offers unprecedented modularity and performance that is ideal for various types of ASTM, DIN, SAE, and other customised tests
References:
1. ASTM D5619-00(2011), Standard Test Method for Comparing Metal Removal Fluids Using the Tapping Torque Test Machine (Withdrawn 2016), ASTM International, West Conshohocken, PA, 2011.
2. ASTM D8288-19, Standard Test Method for Comparison of Metalworking Fluids Using a Tapping Torque Test Machine, ASTM International, West Conshohocken, PA, 2019.
3. G. Ramirez and I. Miller, “Simulating the Friction of Lubricants and Materials with a High-Frequency Reciprocating Rig,” Bruker Application Note 1016 (2019).
3
4. S. Shaffer and S. Lesko, “Evaluating Cutting Tool Coatings with Scratch Testing,” Bruker Application Brief 1014 (2019).
American Elements is a global manufacturer of numerous nanoscale materials including nanoparticles, nanopowder, nanotubes, nanowire, quantum dots, as well as submicron, -325 mesh, and high surface area metal powders with particle distribution and size controlled and certified. We also produce larger -40 mesh, -100 mesh, -200 mesh range sizes and <0.5 mm, 2 mm, 5 mm and other mm sizes of shot, granules, lump, flake and pieces. Our technical teams are experts in not only the chemical properties of advanced materials, but also their physical properties and morphology. American Elements is capable of producing most compounds, metals, and alloys in the submicron and nanopowder range and atomized metallic powders in sizes as low as -325 mesh to ultrafine particle. Surface areas as high as 140 m2 /g have been achieved. If a customer requires a particular material in the submicron or nanoparticle range that is not in our catalog, we can probably produce it.
The Pacific Rim International Conference on Advanced Materials and Processing is held every three years, jointly sponsored by the Chinese Society for Metals (CSM), The Japan Institute of Metals and Materials (JIMM), The Korean Institute of Metals and Materials (KIM), Materials Australia (MA), and The Minerals, Metals and Materials Society (TMS). The purpose of PRICM is to provide an attractive forum for the exchange of scientific and technological information on materials and processing. PRICM-12 will be held in Gold Coast on August 9-13, 2026, hosted by Materials Australia.
PRICM-12 aims to bring together leading scientists, technologists and engineers from the Asia-Pacific region and around the world to discuss contemporary discoveries and innovations in the rapidly evolving field of materials and processing. This event is also intended to foster stronger and closer interactions between materials practitioners and their international counterparts.
Gold Coast Convention & Exhibition Centre
ORGANIZING SOCIETY
Materials Australia
Tanya Smith +61 3 9326 7266 pricm12@materialsaustralia.com.au
This conference will cover most aspects of advanced materials and their manufacturing processes. It has 15 symposia:
Symposium A: Advanced Steels and Properties
Symposium B: Advanced Processing of Materials
Symposium C: Structural Materials for High Temperature
Symposium D: Light Metals and Alloys
Symposium E: Additive Manufacturing
Symposium F: Thin Films and Surface Engineering
Symposium G: Materials for Energy Storage and Generation
Symposium H: Electronic and Magnetic Materials
Symposium I: Biomaterials and Soft Materials and their Application
Symposium J: Materials Characterization and in situ/3D/4D Analysis
Symposium K: High-Entropy Materials and Amorphous Materials
Symposium L: Composite, Coating and HeteroMaterials
Symposium M: Nano Materials and Nano Severe Plastic Deformation
Symposium N: Computational Materials and Artificial Intelligence
Symposium O: Materials for Sustainability (Green Steel, Recycling, and Corrosion)
On behalf of the organising committee, it is our great pleasure to cordially invite you to PRICM-12.
Professor Jianfeng Nie
Organizing Chair of PRICM12
Source: Sally Wood
In just under 50 years, the University of Wollongong (UOW) has emerged as one of Australia’s leading young universities.
In the post-war era of development and innovation, the then New South Wales University of Technology established a division in Wollongong to train the engineers and metallurgists of the local steel industry. That institution grew and evolved and, in 1975, legislation was passed in the parliament of New South Wales, establishing the University of Wollongong as an independent institution.
In 1982, the University amalgamated with the Wollongong Institute of Higher Education, which had begun life in 1962 as the Wollongong Teachers' College. The merger sparked a period of rapid growth for the University, and the emergence of a distinctive identity based on a personalised style and a reputation for excellence in teaching and research.
Originally established as a provider of technical education for engineers and metallurgists required for the region's steel industry, the University now offers a wide range of courses across four faculties:
• Arts, Social Sciences and Humanities
• Business and Law
• Engineering and Information Sciences
• Science, Medicine and Health
UOW's excellence in teaching and research has earned it a place among the top one per cent of universities worldwide.
Central to UOW’s success is its strategic vision, which is driven by a commitment to creating positive change locally and globally. UOW's vision for 2030 and beyond emphasises a global outlook, trust through partnerships, and making a difference through impactful research and education.
As UOW approaches its 50th anniversary, the university reflects on decades of impactful contributions to education and research, particularly through its School of Mechanical, Materials, Mechatronic, and Biomedical Engineering (MMMB).
MMMB is at the forefront of fields like 3D printing, green energy, and robotics, offering unique study areas that ensure graduates are equipped and industry ready.
From pioneering new materials and manufacturing processes to designing intelligent systems and biomedical devices, the school plays a crucial role in driving technological progress.
MMMB’s strong industry connections ensure that its programs are aligned with the latest trends and needs, providing students with practical experience and a competitive edge in the job market.
UOW is dedicated to encouraging innovation and critical thinking, preparing the next generation of engineers to lead and excel in a rapidly evolving world.
The School of Mechanical, Materials, Mechatronic and Biomedical
Engineering is involved in the Engineering Materials Institute (including the BlueScope Steel Metallurgy Centre); the Intelligent Polymer Research Institute (and associated ARC Centre of Excellence in Electromaterials Science); the Institute for Superconducting and Electronic Materials; the SMART Infrastructure Research Facility; the Energy Pipelines Cooperative Research Centre; Sustainable Buildings Research Centre; CRC Railway; the Defence Materials Research Centre; and other multidisciplinary research centres.
One of the strengths of the School is its high number of collaborative links with industries within the local region and with leading national and international universities and institutes. As a result, UOW has an extremely strong track record in developing collaborative research programs with industry and in attracting competitive grant funding from governmental sources.
There are many aspects to UOW’s wide range of fundamental and applied research programs, with highlights include:
• Advanced manufacturing and robotics
• Advanced materials for nanoscale actuators and sensors for cutting edge applications including
biomechanical and biomedical technologies
• Bulk materials handling technologies
• Innovative fabrication technologies
• Intelligent nano, micro and macro mechatronic systems
• Renewable and sustainable energy systems
• Smart materials and structures
• Steel production
• Tribology
• Welding systems
A pair of researchers from the University of Wollongong (UOW) have been given the green light to explore a new manufacturing process for bipolar plates that will advance the clean energy industry and work towards Australia’s goal of net zero by 2050.
The Australian Research Council (ARC) announced the recipients of the Linkage Project Scheme Round 2, with the UOW project sharing in $43 million worth of funding.
Distinguished Professor Zhengyi Jiang, from the School of Mechanical, Materials, Mechatronic and Biomedical Engineering, and Dr Hui Wu, an Honorary Fellow at UOW, will work alongside industry partners Baosteel and SNS Unicorp on the Linkage Project, which received $565,193 over three years.
The researchers will develop a new austenitic stainless steel bipolar plate for hydrogen fuel cells. Austenitic stainless steel contains a crystalline structure, which creates a higher resistance to corrosion. This type of stainless steel is nonmagnetic and is not hardened by heat treatment.
Bipolar plates play a crucial role in generating electricity and physically strengthening a fuel cell stack. Usually made of steel or graphite, they have two sides – the bipolar - that help to manage the flow of electrical charges to the fuel cell.
The project aims to develop a green, efficient, and cost-effective manufacturing process to produce a new stainless steel bipolar plate for fuel cells that are powered by hydrogen.
It will work to solve long-standing issues in traditional materials used for bipolar plates, which are either brittle, costly, or susceptible to corrosion in acidic, high-humidity, and temperate environments.
Professor Jiang said the researchers, along with the industry partners, were thrilled to have been awarded the funding and to be able to have a positive impact on the future of clean manufacturing and hydrogen fuel cell vehicles in Australia.
“The project will lead to a breakthrough in steelmaking by significantly reducing industrial pollution and operation costs and enhancing the overall performance of Hydrogen Fuel Cells,” Professor Jiang said.
“Research like this, undertaken with industry partners, will be essential in
developing clean energy in Australia and helping to achieve the goal of cutting carbon emissions.”
UOW Deputy Vice-Chancellor and VicePresident (Research and Sustainable Futures) Professor David Currow congratulated Professor Jiang and Dr Wu on their success in the ARC Linkage Projects.
“Manufacturing and industry have such an integral role to play in the nation’s move towards clean energy, and projects like this show that we are heading in the right direction towards achieving a sustainable future,” Professor Currow said.
“Congratulations to Distinguished Professor Jiang and Dr Wu, alongside the teams at BaoSteel and SNS Unicorp, on this interesting and worthy ARC project.”
Innovation Promises to Prevent Power Pole-Top Fires
Engineers in Australia have found a new way to make power-pole insulators resistant to fire and electrical sparking, promising to prevent dangerous poletop fires and reduce blackouts.
Pole-top fires pose significant challenges to power providers and communities worldwide. In March, pole-top fires cut power from 40,000 homes and businesses in Perth.
The 2020 Royal Commission into National Natural Disaster Arrangements found that power outages experienced by 280,000 customers from various energy providers during Black Summer fires were mainly triggered by events involving insulators and poles.
RMIT University Vice-Chancellor’s Postdoctoral Fellow Dr Tariq Nazir said these fires can occur when consecutive hot, dry and windy days are followed by damp and misty conditions.
“Dust and pollution builds up on power-line insulators, which enables electricity to spark and heat metal fixtures that can cause wooden power poles to catch fire,” Dr Nazir said.
In collaboration with researchers at the University of New South Wales, Nazir has improved the performance and safety of insulation materials for power poles at the lab scale.
“Power utilities wash insulators on overhead power lines as a vital maintenance procedure to prevent problems like contamination and electrical sparking, which can cause pole-top fires and power outages.”
The composite material comprises chopped fiberglass, aluminium hydroxide and a type of clay derived from volcanic ash as additives. Nazir and his colleagues are behind another fire-protection innovation co-developed with the company Flame Security International – a fire-retardant paint that is already commercially available in Australia.
A pair of researchers from the University of Wollongong (UOW) have been awarded more than $500,000 to solve long-standing problems with traditional materials. The researchers have been given the green light to explore a new manufacturing process for bipolar plates that will advance the clean energy industry and work towards Australia’s goal of net-zero by 2050.
The Australian Research Council (ARC) announced the recipients of the Linkage Project Scheme Round 2, with the UOW project sharing in $43 million worth of funding.
Distinguished Professor Zhengyi Jiang, from the School of Mechanical, Materials, Mechatronic and Biomedical Engineering, and Dr Hui Wu, an Honorary Fellow at UOW, will work alongside industry partners Baosteel and SNS Unicorp on the Linkage Project, which received $565,193 over three years.
The researchers will develop a new austenitic stainless steel bipolar plate for hydrogen fuel cells.
The project aims to develop a green, efficient, and cost-effective manufacturing process to produce a new stainless steel bipolar plate for fuel cells that are powered by hydrogen.
Professor Jiang said the researchers, along with the industry partners, were thrilled to have been awarded the funding and to be able to have a positive impact on the future of clean manufacturing and hydrogen fuel cell vehicles in Australia.
“The project will lead to a breakthrough in steelmaking by significantly reducing industrial pollution and operation costs and enhancing the overall performance of Hydrogen Fuel Cells,” Professor Jiang said.
UOW Deputy Vice-Chancellor and VicePresident (Research and Sustainable Futures) Professor David Currow congratulated Professor Jiang and Dr Wu on their success in the ARC Linkage Projects.
A collaborative project between Deakin, Colac Otway Shire, Formflow and Urbis that addresses the need for housing in regional Australia will receive more than $2 million in Federal funding as part of the regional Precincts and Partnerships Program (rPPP).
The Colac Otway Adaptable Precincts project, a collaboration between the Colac Otway Shire, FormFlow, Urbis, and Deakin’s Institute for Frontier Materials and the School of Engineering and Built Environment (SEBE), will take a share of the $207 million in Australian Government funding that aims to support the delivery of capital works projects in regional and rural Australia that support community socio-economic outcomes and regional priorities.
According to the Regional Australia Institute, there is dire need to increase availability and affordability for regional housing stock, with Australia’s regional population growing at an average of about 89,000 people each year over the period of 2012 to 2022, while the number of homes approved for construction declined in four out of these 10 years.
IFM’s project lead Associate Professor Matthias Weiss said their project aimed to develop a living community laboratory.
“FormFlow has been developing prefabricated and modular building solutions to address Australia’s need for low-cost housing and rapid disaster relief,” Professor Weiss said. “For the living community laboratory, FormFlow will further optimise the housing solution.”
The SEBE architecture team will help FormFlow perform a live cycle analysis to determine the environmental impact of the building solution. IFM will investigate manufacturability – aiming to have a holistic approach towards design, materials and manufacturability.
A new project by University of Wollongong (UOW) researchers to develop battery systems that can withstand extremely cold temperatures, including in outer Space, has been awarded a prestigious national grant.
Professor Jung Ho Kim and Professor Konstantin Konstantinov, both based in the Faculty of Engineering and Information Sciences at UOW, received a National Intelligence and Security Discovery Research Grant from the Australian Government’s Office of National Intelligence. UOW is among only 10 teams nationwide to receive the funding.
It is the first time a UOW project has secured these highly competitive grants, underlining the researchers’ exceptional capabilities in battery technology.
The project will see the design and advancement of an innovative battery device able to operate in temperatures below -40℃.
The goal is to explore new battery configurations using solid electrolytes, as opposed to the liquids or pastes used in existing batteries, and eliminates carbon-based graphite used in traditional anodes.
Professor Kim said, if successful, the battery systems would align with the increased focus on space utilisation and exploration.
“Batteries are crucial for extended space research due to their energy storage and high-power output. However, they face challenges like limited energy capacity and weight constraints. As space exploration progresses, developing compact, lightweight batteries with high-energy output for cold environments remains a key challenge,” Professor Kim said. “Through our efforts, we aim to revolutionise exploration in uncharted realms.”
The project focus on using advanced technology to create battery systems that can operate in extremely cold environments will also go a long way towards increasing Australia’s technological advantages.
FLEET researchers from the University of Wollongong have revisited the concept of spin gapless semiconductors (SGSs), one of the most fascinating materials classes in quantum condensedmatter physics, originally proposed by Xiaolin Wang in 2008.
The FLEET research team reviewed theoretical and experimental progress in the SGSs and provided a new perspective to uncover underlying physics and the utilisation of SGSs in quantum technologies. This study sheds light on various quantum materials hosting spin gapless behaviour, symmetry constraints leading to spin gapless features, theoretical models characterising SGSs, and device structures and mechanisms for quantum technologies made of SGSs.
Such inherently present Chern magnetism in SGSs could solve a long-awaited problem: achieving the QAH effect at room temperature, explains Dr. Muhammad Nadeem (University of Wollongong), who is a Research Fellow at FLEET.
The emergent quantum technologies aim to achieve three critical attributes: ultra-fast speed, ultra-high sensitivity, and ultra-low power consumption.
Physical realisations of contemporary quantum technologies are held back because a of gap between fundamental science and its implementation is not fully understood yet. The exotic electronic, magnetic, and thermal properties of SGSs render them an ideal platform for developing quantum technologies that can meet the three ‘ultra’ criteria, says Prof Xiaolin Wang (University of Wollongong), who is a Chief Investigator of FLEET.
Device structures and mechanisms for various quantum technologies making use of SGSs and the associated QAH phase promise enhanced functionalities and capabilities.
Energy-momentum dispersion of Dirac spin gapless semiconductors (i-iv) and parabolic spin gapless semiconductors (v-viii). Dashed bands represent flat-band spin gapless semiconductors.
Schematic representation for QAH effect in SGSs. QAH effect in a) Dirac type-I SGSs, b) Dresselhaus type-I SGSs (i) and Rashba type-II SGSs (ii), c) SU(3) SGSs of type-III (i), and type-IV (ii), and d) Rashba type-I SGSs.
L-R: University of Melbourne Professor David Jamieson and University of Manchester Dr Maddison Coke inspect the focused ion beam system used to purify silicon at the University of Manchester
Researchers at the Universities of Melbourne and Manchester have invented a breakthrough technique for manufacturing highly purified silicon that brings powerful quantum computers a big step closer.
The new technique to engineer ultra-pure silicon makes it the perfect material to make quantum computers at scale and with high accuracy, the researchers say.
Project co-supervisor Professor David Jamieson, from the University of Melbourne, said the innovation in Communications Materials, a Nature journal uses qubits of phosphorous atoms implanted into crystals of pure stable silicon and could overcome a critical barrier to quantum computing by extending the duration of notoriously fragile quantum coherence.
University of Manchester co-supervisor Professor Richard Curry said ultra-pure silicon allowed construction of high-performance qubit devices, a critical component required to pave the way towards scalable quantum computers.
“What we’ve been able to do is effectively create a critical ‘brick’ needed to construct a siliconbased quantum computer. It’s a crucial step to making a technology that has the potential to be transformative for humankind,” Professor Curry said.
This latest work was supported by research grants from the Australian and UK governments. Professor Jamieson’s collaboration with the University of Manchester is supported by a Royal Society Wolfson Visiting Fellowship.
A 2020 report from Australia’s CSIRO estimated that quantum computing in Australia has potential to create 10,000 jobs and $2.5 billion in annual revenue by 2040.
“Our research takes us significantly closer to realising this potential,” Professor Jamieson said.
One of the Australian Research Council's (ARC) six new Industrial Transformation Training Centres will be headquartered at Deakin University, spearheading the development of more efficient and sustainable materials in the pathway to net zero.
The ARC Training Centre for Resource Efficient Alloys in a Circular Economy 'circAlloy' will be supported by $4,988,139 in ARC funding and will be led by Professor Matthew Barnett, Chair in Metallurgy at Deakin’s Institute for Frontier Materials.
Professor Barnett is an ARC Laureate whose world-leading research team unlocks the potential of metals to develop longer-lasting, energy-saving alloys, for critical industries such as mining and construction.
Deakin's Deputy Vice Chancellor Research and Innovation Professor Matthew Clarke said the new training centre was a fantastic coup for Deakin in its mission to deliver education and research that builds a better future for all.
'circAlloy will help us train the next generation in alloy science and manufacturing for resource efficiency in a circular economy, creating a muchneeded workforce of the future,' Professor Clarke said.
Research groups supporting the centre include Deakin's Institute for Frontier Materials and Applied Artificial Intelligence Institute, plus the Institute for Sustainable Futures at the University of Technology Sydney. Professor Barnett will be joined by centre deputy directors Professor Daniel Fabijanic (Deakin) and Professor Damien Giurco (University of Technology Sydney).
The centre will also make use of Deakin's extensive pilot scale facilities, including the new fastAlloy Lab.
The High Voltage Pulse technology being used to break mineralised ores.
Zapping rocks with a high-voltage pulse, similar to a lightning strike could be the answer to decarbonising the mining industry according to researchers from the University of Queensland (UQ).
Researchers from UQ’s Sustainable Minerals Institute have developed High Voltage Pulse (HVP) technology, which uses a short-pulsed discharge similar to a lightning strike, to selectively break mineralised ores while keeping barren rocks intact.
Project leader Dr Christian Antonio said their HVP technology, in the process of being commercialised, could significantly reduce energy consumption and essentially help decarbonise the mining industry.
“Mineral processing is the most energy intensive part of mining and is a significant consumer of energy globally,” Dr Antonio said.
Dr Antonio said the concept behind HVP technology was similar to lightning attractors – or how lightning was more likely to strike someone holding a metallic umbrella.
“This is a more efficient way to deliver the energy while achieving the over one hundred tonne per hour throughputs required by the mining industry.”
Group Leader Associate Professor Kym Runge said there was wide industry interest in how the technology could decarbonise operations.
“A key part of this project is showing our partners that the technology can feasibly be added to their plants,” Associate Professor Runge said.
This research is funded through the Resources Technology and Critical Minerals Trailblazer program, which also has the support of several mining industry partners, including Newmont and JKTech.
Researchers have developed a 'blood vessel-on-a-chip' for heart disease with the potential to change the future of drug testing and development. The technology could also reduce our reliance on animal testing.
A University of Sydney team have successfully created a transparent microchip with the potential to reduce the testing of new drugs to treat heart disease on animals before proceeding to clinical trials.
“This is an incredible development because we took advantage of these microchips being made from a transparent material, and we mimicked the conditions of the coronary artery, that supplies blood to the heart muscle, and imaged them with a microscope to map the areas of cell damage which were similar to the locations of blockages in patients with heart disease,” says Associate Professor Anna Waterhouse from the Charles Perkins Centre and the University of Sydney Nano Institute.
Although mice and other animals have similarities to human biology, the vessel-on-a-chip utilises real human cells and offers more manageable and cost-effective control in the lab.
This study, co-led by Professor Marcela Bilek and Professor Anna Waterhouse, developed a new more effective surface modification approach that improves the materials current microchips are made from, making them better for protein and cells to attach to compared to the traditional materials.
The teams are now working to incorporate additional types of vascular cells to better mimic human vessels and add in fats to mimic the build-up of cholesterol in blood vessel cells, which is the next stage of heart disease.
Image
Clever bio-inks that sit inside the human body and restore damaged neurons could cure a whole swathe of diseases in the next 20 years: conditions that have baffled scientists and clinicians for centuries.
Think blindness, deafness, chronic pain, epilepsy, motor neurone disease, and Parkinson’s disease.
According to University of South Australia materials engineer Associate Professor Matthew Griffith, these ‘incurable’ diseases are all linked to misfiring neurons that humans have not been able to control.
However, new technology being developed by Dr Griffith and his team at UniSA’s Future Industries Institute could overcome these obstacles, offering hope to billions of people around the world.
The researchers are creating carbon-based biocompatible inks printed into soft flexible devices that can be surgically implanted, electronically communicating with the neural network on demand.
“The aim is to reprogram injury and diseases out of existence by printing cheap, electronic devices that can talk to our bodies in a language it understands,” Dr Griffith says.
“We believe we can change this by developing clever, organic electronic inks, which we can 3D print into flexible devices that are able to talk to neurons, grow new nerve cells and create artificial neural interfaces.”
Around three billion people suffer from neurological conditions worldwide; another 200 million are blind; and one in five people live with chronic pain. All are related to neurons misfiring, resulting in undesirable changes to the brain, senses, and behaviour.
Monash University spinout company ElectraLith has proven its Direct Lithium Extraction and Refining (DLE-R) technology can produce battery grade lithium hydroxide using no water, no chemicals and minimal energy.
Backed by Rio Tinto, IP Group and Monash Investment Holdings, ElectraLith’s DLE-RTM technology is unlocking a green future and emerging as the cleanest, most versatile and cost-efficient method for extracting and refining lithium, the fundamental element driving a sustainable future.
The DLE-R technology can produce battery grade lithium hydroxide from a range of lithium sources including salar brines, geothermal oilfield brines and spodumene leach in locations across the US, Argentina and Australia.
Lithium is an essential element in ‘clean energy’. It is used to make batteries for electric vehicles and wind and solar power storage. Most processes to extract lithium are costly and have negative impacts on the environment such as carbon dioxide emissions, mineral waste, chemical pollution, and the subsequent alteration of the hydrological cycle from the use of vast quantities of water.
DLE-R uses electro-membrane and electrodialysis technology to extract and produce battery-grade lithium hydroxide in a single, scalable and modular step. Other DLE technologies generally require further processing and energy to produce a usable lithium chloride product.
ElectraLith’s patented DLE-stage membranes are based on revolutionary work conducted by Professor Huanting Wang, Sir John Monash Distinguished Professor and Australian Laureate Fellow within the Faculty of Engineering.
Monash University Chief Commercialisation Officer Dr Alastair Hick congratulated the team on the breakthrough.
ElectraLith’s DLE-RTM technology is unlocking a green future
Engineers have invented energy-efficient bricks with scrap materials, including glass, that are normally destined for landfill.
RMIT University engineers collaborated with Visy –Australia’s largest recycling company – to make bricks with a minimum of 15% waste glass and 20% combusted solid waste (ash), as substitutes for clay.
Test results indicate that using these bricks in the construction of a single-storey building could reduce household energy bills by up to 5% compared to regular bricks, due to improved insulation.
Replacing clay with waste materials in the brick production helped reduce the firing temperature by up to 20% compared with standard brick mixtures, offering potential cost savings to manufacturers.
Team leader Associate Professor Dilan Robert said about 1.4 trillion bricks were used in construction projects globally every year.
“Business-as-usual brick production produces harmful emissions – including carbon dioxide, sulphur dioxide and chlorine – and puts a serious strain on our natural resources, particularly clay,” said Professor Robert.
The team’s research showed the new bricks have enhanced energy efficiency through improved thermal performance, and met stringent structural, durability and environmental sustainability standards. The technology has met the key compliance requirement of fired clay bricks set by Standards Australia (AS 3700).
“Bricks play a key role in preventing energy loss from buildings,” Professor Robert said. “We can also produce lightweight bricks in a range of colours from white to dark red by changing our formulations.”
In the ever-evolving landscape of materials science and engineering, sensor materials have emerged as a critical field of study, driving innovations across industries and revolutionising our ability to interact with the physical world. This article explores the fascinating realm of sensor materials, tracing their history, key developments, and the cutting-edge research being conducted in Australia.
CSensor materials are the foundational elements that enable devices to detect and respond to changes in their environment. These materials convert physical, chemical, or biological stimuli into measurable electrical signals, forming the basis of modern sensing technology.
The history of sensor materials dates back to the early 20th century, with the development of rudimentary devices capable of detecting basic parameters such as temperature and pressure. However, it was the advent of semiconductor technology in the mid-20th century that truly revolutionised the field.
The invention of the transistor in 1947 marked a pivotal moment in sensor technology. Transistors allowed for the creation of compact, power-efficient electronic components, paving the way for more sophisticated sensing devices. This was followed by the development of microcontrollers in the 1970s, which enabled on-board data processing and programmability in sensors.
The 1980s saw the rise of Radio-Frequency Identification (RFID) technology, introducing new capabilities in object tracking and identification. The subsequent introduction of Wi-Fi in 1997 and Bluetooth in 1998 further expanded the potential of wireless sensor networks, enabling seamless data transmission and integration.
As sensing technology progressed, so did the materials used in their construction. The late 20th century witnessed significant advancements in printed electronics, particularly with the development of flexible and wearable electronics. The exploration of conductive inks and flexible substrates in the 1980s opened up new possibilities for integrating electronics into everyday objects. A major breakthrough came in the early 2000s with the development of organic electronics. These devices, made from organic-based materials, could be printed
onto flexible substrates using techniques like inkjet printing and screen printing. This innovation led to the creation of organic lightemitting diodes (OLEDs) and organic photovoltaics (OPVs), expanding the range of possible sensor applications.
Micro-Electro-Mechanical Systems (MEMS) technology has played a crucial role in the miniaturisation and improved performance of sensors. MEMS devices integrate mechanical elements, sensors, actuators, and electronics on a common silicon substrate through microfabrication technology. This integration has led to the development of highly sensitive, low-power, and cost-effective sensors for various applications.
The advent of nanotechnology has further revolutionised sensor materials. Nanomaterials, such as carbon nanotubes, graphene, and quantum dots, have unique properties
that make them ideal for sensing applications. These materials offer high surface-to-volume ratios, enhanced sensitivity, and the ability to detect minute changes in their environment. Recent years have seen the emergence of smart materials and metamaterials in sensor technology. These engineered materials can change their properties in response to external stimuli, opening up new possibilities for adaptive and self-healing sensors.
Today, sensor materials are at the forefront of technological innovation. The integration of artificial intelligence and machine learning with advanced sensor materials is enabling the development of intelligent sensing systems capable of real-time data analysis and decision-making. The future of sensor materials looks promising, with ongoing research in areas such as biomimetic materials, self-powered sensors, and quantum sensing. These advancements are
expected to drive the development of more sensitive, efficient, and versatile sensing technologies, with applications ranging from healthcare and environmental monitoring to industrial automation and smart cities.
As we look to the future, the field of sensor materials continues to evolve, promising exciting developments that will shape our interaction with the world around us. The ongoing research in Australia, which we will explore in the next section, is playing a crucial role in pushing the boundaries of what's possible in sensor technology.
Australia has established itself as a significant contributor to the global research landscape in sensor materials. With world-class universities and research organisations, the country is at the forefront of developing innovative sensor technologies. This section highlights some of the key institutions and projects driving sensor materials research in Australia.
University of New South Wales (UNSW)
UNSW is a leader in sensor materials research, particularly in the field of quantum sensing. The UNSW Quantum Computing Research Group, led by Professor Michelle Simmons, is working on developing atomic-scale quantum sensors using silicon. These sensors have potential applications in medical imaging, navigation, and mineral exploration.
The University of Melbourne
At the University of Melbourne, the Centre for Neural Engineering is pioneering the development of biocompatible materials for neural interfaces. Professor Stan Skafidas and his team are working on flexible, high-density electrode arrays made from novel materials that can interface directly with the brain, opening up new possibilities for neural prosthetics and brain-computer interfaces.
Australian National University (ANU)
The ANU Research School of Physics and Engineering is at the forefront of developing advanced optical sensors. Professor Yuri Kivshar's team is working on metasurfaces—engineered surfaces with unique optical properties—that can be used to create ultra-thin, highly sensitive optical sensors.
Monash University
Monash University's Department of Materials Science and Engineering is making significant strides in the development of wearable sensors. The group is working on graphene-based flexible sensors that can be integrated into clothing for continuous health monitoring.
Commonwealth Scientific and Industrial Research Organisation (CSIRO)
CSIRO, Australia's national science agency, is heavily involved in sensor materials research. Their Sensor Systems Group is developing a range of advanced sensors for applications in agriculture, environmental monitoring, and industrial processes. One notable project is the development of a novel sensor material for detecting methane leaks in natural gas pipelines. This sensor, based on a nanocomposite material, can detect methane at very low concentrations, potentially revolutionising leak detection in the gas industry.
Defence Science and Technology Group (DSTG)
The DSTG, part of the Australian Department of Defence, is conducting research into advanced sensor materials for defence applications. Their work includes the development of infrared sensor materials for night vision technology and chemical sensors for detecting explosive materials.
ARC Centre of Excellence for Transformative Meta-Optical Systems
This centre, led by the Australian National University, brings together researchers from multiple institutions to develop next-generation optical systems. Their work includes the development of novel meta-materials for sensing applications, such as ultrathin, highly sensitive gas sensors.
CRC for Contamination Assessment and Remediation of the Environment (CRC CARE)
CRC CARE is working on developing innovative sensor materials for environmental monitoring. One of their projects involves the creation of a novel biosensor using genetically modified bacteria to detect and measure heavy metal contamination in soil and water.
Graphene-Based Sensors for Food Safety
Researchers at the University of Adelaide, led by Professor Dusan Losic, are developing graphenebased sensors for detecting food contaminants. These sensors can detect trace amounts of pesticides and other harmful chemicals on the surface of fruits and vegetables, potentially revolutionising food safety testing.
A team at the University of Melbourne, led by Professor Lloyd Hollenberg, is working on developing quantum sensors using nitrogen-vacancy centers in diamond. These sensors have unprecedented sensitivity and could be used for a range of applications, from detecting brain activity to exploring for minerals.
3D Printed Sensors for Prosthetics
Researchers at the University of Wollongong's ARC Centre of Excellence for Electromaterials Science are using 3D printing technology to create customised pressure sensors for prosthetic limbs. These sensors, made from novel conductive hydrogel materials, can provide real-time feedback to improve the comfort and functionality of prosthetics.
Nanostructured Materials for Gas Sensing
At RMIT University, Professor Kourosh Kalantar-Zadeh's team is developing nanostructured materials for highly sensitive and selective gas sensors. Their work includes the creation of twodimensional metal oxide nanosheets that can detect specific gases at very low concentrations.
Piezoelectric Nanogenerators for SelfPowered Sensors
Researchers at the University of Adelaide are working on developing piezoelectric nanogenerators that can harvest mechanical energy from the environment to power small sensors. This technology could lead to self-powered sensor networks for applications in structural health monitoring and wearable devices.
Biomimetic Sensor Materials
Australian researchers are increasingly looking to nature for inspiration in developing new sensor materials. For example, a team at the University of New South Wales is developing artificial skin sensors inspired by the structure of human skin. These sensors could provide more natural tactile feedback in prosthetics and robotics.
Machine Learning-Enhanced Sensors
The integration of machine learning with sensor technology is a growing trend in Australian research. At the University of Technology Sydney, researchers are developing smart sensor systems that use machine learning algorithms to improve sensor accuracy and enable real-time data analysis.
Quantum sensing is an area where Australia is making significant contributions. The ARC Centre of Excellence for Engineered Quantum Systems, which involves multiple Australian universities, is at the forefront of developing quantum sensors for applications ranging from medical imaging to mineral exploration.
With Australia's unique environmental challenges, there's a strong focus on developing sensors for environmental
monitoring. For instance, researchers at James Cook University are working on advanced coral reef sensors to monitor the health of the Great Barrier Reef.
While Australian research in sensor materials is thriving, there are challenges to overcome. Funding constraints and the need for better industry-academia collaboration are often cited as hurdles. However, these challenges also present opportunities for innovation and cross-disciplinary research.
The Australian Government's focus on innovation, particularly through initiatives like the National Innovation and Science Agenda, provides a supportive environment for sensor materials research. Furthermore, Australia's strong mining and agricultural sectors offer unique opportunities for the application and commercialisation of new sensor technologies.
As global demand for advanced sensing technologies continues to grow, Australia is well-positioned to play a leading role in shaping the future of sensor materials. From quantum sensors to biomimetic materials, Australian researchers are pushing the boundaries of what's possible, promising exciting developments in the years to come.
In a world first, a new wearable device developed by Monash University researchers will help to record the impact of artificial light on our bodies for sound sleep, improved mental wellbeing and treating chronic health conditions.
The ‘MiEye’ sensor is the brainchild of circadian biology experts Professor Sean Cain (Adjunct) and Associate Professor Andrew Phillips (Adjunct) from the Faculty of Medicine, Nursing and Health Sciences.
Professor Jon McCormack, Elliott Wilson and Dr Rowan Page from SensiLab – a joint lab between the Faculty of Information Technology and the Faculty of Art, Design and Architecture – worked on making the MiEye device wearable and adapted it for commercial production.
When worn, the device, which senses light over 11 channels and is about as big as a 20-cent piece, records the impact of any light source, such as fluorescent light, overhead LED, sunsets, phone light and device light on the wearer. It then sends feedback to a smartphone application, which calculates the impact of ambient light on our body clock.
Research lead Professor Sean Cain said our light behaviour is fundamental to all aspects of our health.
“By providing feedback on light environments, we are trying to make people more conscious of their exposure to different types of light and guide them towards healthier light exposure patterns,” Professor Cain said.
“By helping to manage circadian rhythms, MiEye will be a powerful clinical tool that can aid in the treatment of type 2 diabetes, mental health issues, cardiovascular disease and hypertension, and generally improve health and longevity.”
The MiEye sensor has been developed for public use by Circadian Health Innovations – a spin-off company founded
by the lead researchers of the project.
Circadian Health Innovations Co-Founder and Chief Technology Officer Associate Professor Andrew Phillips said the device is currently available to select researchers and will be more widely available to clinicians and researchers in 2025.
“Ultimately we aim to have the device available to the public where people can use it to get real-time feedback and understand as well as manage their exposure to different types of light. This can be especially useful for travellers suffering from jet lag and shift workers,” Associate Professor Phillips said.
In its development stage, the MiEye sensor won a prestigious Australian Good Design award in 2022 under the ‘Design Research’ category.
“For it to be a feasible wearable device, we designed MiEye to be as compact and light as possible while still incorporating the required sensors from the technological point of view,” SensiLab Engineer, Elliott Wilson said.
Research for the MiEye project was funded by the Monash Institute of Medical Engineering and commercialisation was made possible through Monash Innovation.
“This new device is a shining example of synergy between quality research and enterprise to produce tangible health outcomes and positively impact communities,” Monash Innovation Chief Commercialisation Officer Dr Alastair Hick said.
MiEye Project Lead and Monash University Adjunct Professor Sean Cain and Professor Jon McCormack from the Faculty of Information Technology are available for interviews.
To learn more about MiEye and submit expressions of interest for purchasing the device, please visit: https://www. circadianhealth.com.au/mieye
Industrial design expert
Dr Rowan Page wearing the MiEye device. Image courtesy of Monash University.
A compact, lightweight sensor system with infrared imaging capabilities developed by an international team of engineers could be easily fitted to a drone for remote crop monitoring.
This flat-optics technology has the potential to replace traditional optical lens applications for environmental sensing in a range of industries.
The innovation could result in cheaper groceries as farmers would be able to pinpoint which crops require irrigation, fertilisation and pest control, instead of taking a one-sizefits-all approach, thereby potentially boosting their harvests.
The sensor system can rapidly switch between edge detection – imaging the outline of an object, such as a fruit – and extracting detailed infrared
information, without the need for creating large volumes of data and using bulky external processors.
The capability to switch to a detailed infrared image is a new development in the field and could allow farmers to collect more information when the remote sensor identifies areas of potential pest infestations.
This research by engineers at the City University of New York (CUNY), the University of Melbourne, RMIT University and the ARC Centre of Excellence for Transformative MetaOptical Systems (TMOS) is published in Nature Communications
How Does the Sensor System Work?
The prototype sensor system, which comprises a filter made with a thin layer
of a material called vanadium dioxide that can switch between edge detection and detailed infrared imaging, was engineered by TMOS Chief Investigator Professor Madhu Bhaskaran and her team at RMIT in Melbourne.
“Materials such as vanadium dioxide add a fantastic tuning capability to render devices ‘smart’”, she said.
“When the temperature of the filter is changed, the vanadium dioxide transforms from an insulating state to a metallic one, which is how the processed image shifts from a filtered outline to an unfiltered infrared image.”
“These materials could go a long way in futuristic flat-optics devices that can replace technologies with traditional lenses for environmental sensing applications – making them ideal for use in drones and satellites,
which require low size, weight and power capacity.
RMIT holds a granted US patent and has a pending Australian patent application for its method of producing vanadium dioxide films, which may be suitable for a broad range of applications.
Lead author Dr Michele Cotrufo said the system’s ability to switch between processing operations, from edge detection to capturing detailed infrared images, was significant.
“While a few recent demonstrations have achieved analogue edge detection using metasurfaces, most of the devices demonstrated so far are static. Their functionality is fixed in time and cannot be dynamically altered or controlled,” said Cotrufo, who conducted his research at CUNY.
“Yet, the ability to dynamically reconfigure processing operations is key for metasurfaces to be able to compete with digital image processing systems. This is what we have developed.”
Co-author PhD scholar Shaban Sulejman from the University of Melbourne said the design and materials used make the filter
amenable to mass-manufacturing.
“It also operates at temperatures compatible with standard manufacturing techniques, making it well-placed to integrate with commercially available systems and therefore move from research to realworld usage rapidly.”
TMOS Chief Investigator
of Melbourne, said flat optics technologies had the potential to transform countless industries.
“Traditional optical elements have long been the bottleneck preventing the further miniaturisation of devices. The ability to replace or complement traditional optical elements with thin-film optics breaks through that bottleneck.”
Source: Guanyi Gong, Huajun Shen, Chenglong Xu, Xiangyang Guo, Yongxiang Li
Wearable electronic devices are flexible, stretchable and considered to be human-friendly[1]. Therefore, wearable electronic devices have a wide range of applications in the fields of medical care and health[2]. Sensors are an important component of wearable electronic devices because they can be used to collect and monitor information such as vibration, temperature and humidity. Flexible piezoelectric sensors are widely used in wearable electronic devices because of their self-powered advantages[3].
Piezoelectric materials are simple, low-cost, lightweight, and easily controllable smart materials for structureactuated applications. Piezoelectric materials generate electricity under mechanical stress. As shown in Fig. 1, direct piezoelectric materials generate charges when deformed (Fig. 1a), or conversely, inverse piezoelectric materials deform when an electric potential is applied (Fig. 1b).
Fig 1. Schematic of the piezoelectricity principle: (a) direct and;(b) Inverse piezoelectric effect.[4]
For linear piezoelectric materials (Fig. 1), the constituent equations of the direct and inverse piezoelectric effects are as follows[5]:
Direct effect: D=dT+εE (1)
Inverse effect: X=sT+dE (2)
Where, D is electrical displacement, d piezoelectric coefficient, T stress, ε permittivity of the material, E electric field, X Strain, s mechanical compliance. The piezoelectric coefficient (d33) is an important parameter for piezoelectric materials.
As one of the most common electronic materials, piezoelectric materials continue to evolve with the needs of the market. Single ferroelectric crystals such as lithium niobate (LiNbO3) and lithium tantalate (LiTaO3) have been widely used in piezoelectric sensors and other fields[6]. The multibillion-dollar piezoelectric market spans the telematics, automation, automotive, and defense industries. Many commercial piezoelectric devices have been used in these applications, such as gas and fuel igniters, sensors, microphones and speakers, high-power transducers, mechanical frequency filters, etc. [7-11]. Piezoelectric materials can be divided into piezoelectric ceramics, polymers, and ceramic-polymer composites[7]. Piezoelectric ceramics have high piezoelectric properties, but they are hard and brittle, with poor mechanical impact resistance, and it is difficult to meet the requirements of efficient
power-to-electricity conversion under complex stress conditions such as bending and stretching. Compared with piezoelectric ceramics, piezoelectric polymers have lower piezoelectric coefficients, but their advantages such as good flexibility, easy molding, and low cost make them have broad application prospects.
PVDF, as the most studied piezoelectric polymer, is a polycrystalline polymer that can be prepared into α, β, γ, δ and ε crystal phases associated with different chain conformations[7, 12, 13]. Currently, the reported PVDF piezoelectric devices are mainly two-dimensional (2D) films[13]. Compared with 2D planar structures, 3D structures have the following advantages: (1) The porous structure can greatly reduce the material Yang’s modulus, amplify the deformation under the same stress, and effectively improve the piezoelectric effect. (2) The porous structure makes the compressive stress uniformly distributed, suppresses the strain in the direction perpendicular to the stress, and significantly alleviates the clamping effect[3]. 3D printing is an additive technology for part manufacturing which can additively transform digital graphics into 3D objects[4]. 3D printing technology has many advantages: low cost, flexible design, ability to manufacture complex 3D structures, multi-material manufacturing, reduced labor costs, reduced material waste, and customizable parts. Many studies have shown that 3D printing is suitable for fabricating complex structures, such as commonly used pore structures[14].
In this study, a printable PVDF-TrFE ink was prepared, and the reliability of the process was verified by a 3D inkjet printer (Ceradrop). The morphology, crystal phase and piezoelectric response of the PVDF-TrFE film were studied using advanced XRD and PFM and correlated with the piezoelectric coefficient and mechanical response.
Literature Review
3D Printing Technologies
This section discusses 3D printing methods. The types of 3D printing are divided into four categories: extrusion-based, jet-based, liquid resin-based and powder-based. Table 1 lists the commonly used 3D printing methods, including fused deposition modelling (FDM)[15, 16], direct ink writing (DIW)[16, 17], inkjet[18], aerosol jet printing (AJP)[19, 20], binder jetting[17], stereolithography (SLA)[17], direct light processing (DLP)[18], mask stereolithography (MSLA/LCD), two-photon lithography, selective laser sintering (SLS) [21], direct metal laser sintering (DMLS) and direct energy deposition (DED)[22].
3D inkjet printing is a relatively new printing technology that allows for additive manufacturing of design-based devices. The significant difference between 3D inkjet and traditional inkjet printing is that the printing process is repeated layer
Jetting-based
Aerosol jet printing (AJP)
Binder jetting (BJT)
Stereolithography (SLA)
Direct light processing (DLP)
Liquid resin-based
Extrusion-based
Power-based
Mask stereolithography (MSLA/LCD)
Two-photon lithography
Fused deposition modeling (FDM)
Direct ink writing (DIW)
Selective laser sintering (SLS)
Direct metal laser sintering (DMLS)
Direct energy deposition (DED)
Ultraviolet (UV) curable and low viscous materials
Micro/nanoparticle solutions, conductive pastes Ceramics and metals
Light (UV, LEDs, or laser) curable polymers
Thermoplastics, e.g., PLA, ABS, nylon Elastomers, thermosets, metals and ceramics in micro/ nanoparticle solutions, and biomaterials
Metals and alloys, ceramics, polymers, and semiconductors
by layer until the 3D structure is achieved[23]. The principle of this process (Fig. 2) is that tiny droplets of ink are directly and accurately deposited on the substrate by the nozzle. The performance of the ink itself is critical, and the ink parameters must meet the recommended specifications of the nozzle and substrate[24]. Generally, good ink drop ejection requires ink with extremely low viscosity (about 8-20 cp), good surface tension, suitable particle size and very high resolution (down 20 μm)[18]. There are many types of inks;
Flexible electronics and sensors, layered structures, energy harvesting devices.
High resolution prototyping, architected materials, microfluid devices.
Rapid prototyping, composites, functional materials, lightweight materials, soft robotics, sensors and actuators, biomedical devices.
Aerospace and automotive, dental parts, construction.
the more common ones are dielectric polymers, conductive nanoparticles, and organic conductors[25]. After printing, the ink is usually cured by UV light to obtain a solid structure. Because the image processed by this process is digital, the product can be easily changed according to the needs of the design[18]. Furthermore, inkjet printing can be fabricated on 3D surfaces and cavities, which can be applied to more complex printing situations[26]. Since non-contact printing does not exert additional pressure on the substrate, the method can be used on any substrate of any material[27]. Therefore, 3D inkjet printing is the preferred technology for preparing flexible piezoelectric materials.
The principle of the piezoelectric effect is to use the piezoelectric effect to convert physical quantities such as pressure, force, and strain into measurable electric fields and vice versa. Piezoelectric materials have been widely used in actuation[29], sensing, biomedicine, energy storage[30], wearable electronics and electronic skin, acoustics, aerospace, and other fields[4, 7].
Commonly known piezoelectric polymers are polyvinylidene fluoride (PVDF) and its copolymers[7, 31]. The molecular formula of PVDF is [C2H2F 2] N . PVDF polymers exist in four different phases: α, β, γ, and δ phases[31]. α-phase PVDF films are commonly used as insulating materials due to their low thermal conductivity, low density, and high chemical
and thermal resistance. PVDF films with a highly polar β-phase are widely used in 3D printing. As shown in Table 2, PVDF and its copolymers are known for their relatively high piezoelectric coefficient, high flexibility, lightweight, easy processing, and stability and become a promising piezoelectric polymer[8, 32].
PVDF films are produced from melt or solution. Typically, PVDF powder is stirred in N, N-dimethylformamide (DMF) or dimethylacetamide (DMA) with a magnetic stirrer and combined with a photopolymer resin[7, 33]. The mixed paste was then photocured using an SLA 3D printer to produce PVDF polymers (Fig. 3)[33]. The PVDF film is polarized by applying a high electric field on an order of 3 MV/m under tension[7].
The piezoelectric coefficient of PVDF film is 20-30 pC/N, which is ten times lower than that of PZT[7]. Therefore, to improve the production process and the quality of materials, researchers have developed copolymers of PVDF, trifluoro- ethylene and tetrafluoroethylene. For example, the copolymer PVDF-TrFE piezoelectric coefficient is greater than 100 pC/N[7]. The piezoelectric properties of 3D printing PVDF still need to be improved to achieve the performance of traditional piezoelectric ceramics.
Inkjet printing offers cost-effectiveness, simple production, typically high resolution, highly precise deposition, and high material diversity[34, 35]. One of the research focuses is to
improve the piezoelectric properties of polymers by adding other nanoparticles (metallic nanoparticles, inorganic nanoparticles, conductive polymers, and their composites) to the ink. By varying the composition of the materials, the nanocomposites can be printed simultaneously after preparing customized multiple inks. Another advantage of this technology is the increased β-phase content, this has been revealed in different reports. The extrusion pressure applied when inkjet printing films resulted in consistent polymer changes and increased β-phase content according to FTIR results compared to spin coating films[36]. However, for inkjet printing, both the preparation and application of the ink are challenging issues. Ink and printhead compatibility and the changes in the ink droplet during the dripping process are critical aspects. In addition, the stability of organic inks is also a challenge. For example, polymer powders are well suspended in DMF, once MEK is added to the system gels and it is more difficult to dilute[37]. Therefore, ink flocculation must be avoided during the printing process, resulting in low dispersion that would clog the nozzle. In addition, the rheology, surface tension, and droplet size of the ink should be characterized before inkjet printing to obtain good droplets and high resolution, thereby obtaining more uniform printed devices[8, 18]. Inkjet printing can only use low-viscosity inks, and the printable viscosity range of inkjet printheads is usually 1-20 cp.
Thuau et al. prepared a PVDF-TrFE sensor and actuator by inkjet printing. The PVDF-TrFE films they produced exhibit piezoelectric and ferroelectric properties comparable to spin-coated films. A remanent polarization of μC/cm-2 and a d31 piezoelectric coefficient of 10.4 pm/V were obtained. Facilitating the development of printed electroactive polymers for various flexible electronic applications[38].
In addition, polylactic acid (PLA) and polyhydroxybutyrate (PHB) are also common piezoelectric polymers. All of the above polymers are biocompatible, and therefore, many studies have used them as biomaterials[39]. The most
attractive applications of piezoelectric polymers are flexible sensors, piezoelectric nanogenerators (PENGs), flexible keypads, hydrophones, piezoelectric ignition systems, selfpowered electronics and artificial muscles [40-42].
This section discusses the challenges faced by piezoelectric devices in the 3D printing process. These challenges come from the selection of piezoelectric materials and the preparation of inks, as well as from the production and postprocessing of devices. 3D printing technology is also facing many challenges, mainly in the following aspects in terms of technology.
In 3D inkjet printing, Ink compatibility is very important. Organic inks with too high a solid content can clog the nozzle due to their high viscosity. Conversely, if inks are designed with too low solid content, it is challenging to support subsequently deposited layers during printing, resulting in insufficient mechanical properties[43]. In addition, when solid powders (such as piezoelectric ceramics) are added, binders and dispersants must be added to the ink to improve the performance of the ink during processing, after debonding, the density of the device tends to decrease. During atomization, low boiling point solvents evaporate in flight, when employed alone resulting in the deposition of discrete, dry particles with high surface roughness and porosity. Evaporation can result in droplets with inadequate inertia for impaction, preventing patterning and emitting more particles into the atmosphere than onto the substrate. Therefore, the improvement of 3D printing piezoelectric ink performance is achieved through more uniform dispersion, more suitable additives and more reasonable storage process[44, 45].
For 3D printed piezoelectric materials, there are mainly two poling methods, contact polarization or corona polarization[4]. Depending on the material and polarization technology, the coercive and breakdown field of the material are different, and the piezoelectric coefficient of 3D printing piezoelectric materials is different[4]. Ducrot et al. demonstrated that the required poling electric field at room temperature is 100 V/μm; below this value, PVDF-TrFE is poorly polarized, and beyond this value, the piezoelectric performance does not improve significantly. It is also shown that the poling time required to achieve a sufficiently strong electric field is very short (5 min). The results show that the annealing time required for 4 μm film at 140℃ is also very short (3 min). After stabilizing the piezoelectric properties, average piezoelectric coefficient d31 = 11 pm/V. The finding shows that the piezoelectric effect of the material can be effectively improved through appropriate annealing and polarization, which is very attractive from the perspective of industrial applications[46].
In order to conduct research on piezoelectric devices of different materials and analyze their performance to cope
with the requirements of miniaturization and portability. It is highly desirable to systematically investigate how changes in structures and mechanical properties affect the piezoelectric properties and acoustic impedance of the polymers. There are many factors that affect the performance of piezoelectric materials. First, the porosity and shape of the voids will significantly affect the structure and Young's modulus of the piezoelectric material, which in turn affects the device's mechanical properties and piezoelectric coefficient[47, 48]. Next, the device's design is also critical, and the structure of the device will also have a particular impact on the piezoelectric coefficient, dielectric coefficient, and acoustic impedance. It is important to calculate the formulas of Young's modulus and piezoelectric coefficient, dielectric constant and acoustic impedance of the materials through experiments.
This study is determined to investigate the PVDF piezoelectric materials based on the CeraPrint 3D printer. The printer is shown in Fig. 4. The printer has three inkjet printheads (DMC_SAMBA, Dimatix Q Class-Sapphire 10 and Dimatix Q Class-Sapphire 80) and one aerosol inkjet printhead. PVDF and silver-based circuits were made based on Q Class-Sapphire 10 (QS-10).
3D inkjet-based PVDF-TrFE solution was prepared. Dissolved PVDF-TrFE (Piezotech FC30, Arkema, France) in the solvent and then stirred it with a magnetic stirrer to obtain a clear solution. Usually, the optional solvents for PVDFTrFE solution are methyl-ethyl-ketone (MEK), dimethyl sulfoxide (DMSO), N, N-dimethylformamide (DMF) acetone or N-Methyl-2-pyrrolidone (NMP). Because inkjet printing has stringent requirements on the viscosity of the ink and the particle size of the particles in the solution, this study tried all the above types of solvents and mixed solutions. Find a PVDF ink with a suitable viscosity (8-20 cp) and usable particle size (less than 100 nm).
First, PVDF-TrFE inks of different solvents were prepared,
and the viscosity of the solutions was tested respectively. Then, a layer of PVDF film was designed on the 14 μm×14 μm silicon wafer by inkjet printing, dried and then annealed. Finally, profilometer, XRD and FTIR were used to characterize the PVDF-TrFE film and test its performance. The viscosity and β-phase content of these inks were compared, and the ink with the best performance was retained for the next experiment.
Then, the viscosity of the ink was adjusted by continuously changing the PVDF-TrFE content in the ink, the type of solvent, and the mixing process of the solution. Since the viscosity range allowed by the QS-10 inkjet print head does not exceed 20 cp, according to literature review and multiple tests, the viscosity of 1wt% PVDF-TrFE/MEK-DMSO ink is 5-10 cp, which is very suitable for inkjet printing. However, the ink of this concentration caused nozzle clogging as the temperature increased during the printing process, and this situation did not improve after priming. Therefore, after gradually reducing the solid content in the ink, 0.3wt% PVDF was prepared, which is a good choice for the QS-10 inkjet printhead.
Processing of PVDF Inkjet Printing
PVDF-TrFE film was prepared on a silicon wafer with a lower electrode, and E-beam was used to generate a layer of 200 nm gold and 20 nm titanium lower electrode on the silicon wafer. The ink with better performance in the first process was selected, and the PVDF sensor was prepared by 3D printing. Then the solution was annealed at 140°C for 3 min. The properties of the annealed film were characterized by profilometer and XRD. The contact area was then protected by photoresist, and the upper electrodes of gold and titanium were deposited on the PVDF by the electron beam. Then it was polarized in room temperature silicone oil under a 100 V/μm DC electric field for 5 min to obtain a polarized PVDF-TrFE piezoelectric sensor. The β -phase content in the polarized piezoelectric film was tested. Its piezoelectric properties were measured by an oscilloscope and PFM. And the β-phase content in the PVDF-TrFE film was increased by improving the annealing process and polarization conditions.
First, use an optical microscope to observe the surface of the film as shown in Fig. 5.
It can be seen that there are some defects on the film surface, which are caused by the rheological properties of the ink. When the ink was sprayed onto the substrate surface, it was affected by the surface tension, resulting in the ink not forming a complete plane. In addition, the uneven heating during the thermal curing of the ink also aggravated the generation of defects.
Then, XRD was used to characterize the crystallinity of the PVDF-TrFE, and D2 Phaser-Bruker was used to characterize the film, as shown in Fig. 6. In the range of 2θ = 15°~70°, the X-ray diffraction pattern of all annealed samples have only one prominent peak. This peak is assigned to the (110) and (200) plane reflections of the crystal[49]. Then, analyze the β crystal phase composition of the sample, and the percentage of crystal content can be calculated using the following formula.
(3)
where AC is the peak area of the crystalline phase and A A corresponds to the amorphous phase. Calculated ferroelectric crystallinity corresponds to the total crystallinity.
The peak of each film can be found using the peak search
function. It can be seen that the peak 2θ is 19.72° from Fig. 6. According to the XRD standard Data, this peak is the β-phase of PVDF-TrFE. According to formula (3), the β-phase content is calculated to be 84.74%.
PFM investigation was carried out on the 3D printing PVDFTrFE (0.10 wt%) films to measure the amplitude variation with a bias voltage. An AFM equipped with a high voltage accessory was used for this experiment.
The PFM of PVDF was performed in Dual AC Resonance Tracking (DART) mode (Fig. 7). The applied voltage was between 0 V and 5 V with a 1 V increment, and an area of 5 μm2 was imaged at a scan rate of 2 Hz.
The A and φ data were processed using dedicated PFM software. Fix zero after removing the Q factor (Q f) of
the biased cantilever. Record the data and calculate the piezoelectric coefficient d33 of the PVDF at each voltage. The formula is as follows:
(4)
where A is the amplitude, φ is the phase, and V is the applied bias.
After calculation, the relationship between the amplitude and voltage of PVDF is shown in Fig. 8. Calculation can get d33 = -2.00 pm/V, which is much higher than that of the spincoated PVDF-TrFE co-polymer (d33 = –0.50 pm/V)[50].
Conclusion
In summary, this review introduces materials and technology for 3D printing of piezoelectric polymer sensors and focuses on the challenges in printing and conditions for successful printing. For 3D inkjet printing, suitable ink viscosity and uniform dispersion are crucial. This determines the density of the product and whether the ink can pass through the nozzle. Another limitation is the structure and size of piezoelectric devices, limiting their use in specific applications.
In this study, the feasibility of using a Ceraprint printer to
prepare piezoelectric film sensors was studied. The MEK/ DMSO-based PVDF ink and piezoelectric films was prepared. Although the piezoelectric coefficient reaches d33=-2.00 pm v-1, the content of the β-phase and the uniformity of the film still need to be improved.
This study will continue to focus on the preparation of flexible piezoelectric sensors and inks to find out the best weight ratio by optimizing the doping materials. Additionally, the study will contribute to the commercial application of PVDF-based piezoelectric materials through process and material optimization. By conducting closed-loop research, we aim to continuously improve the structure and materials of products, reduce costs, and improve production quality.
This work used the RMIT Micro Nano Research Facility (MNRF) in the Victorian Node of the NCRIS-enabled Australian National Fabrication Facility (ANFF-Vic).
[1] D. Yin et al., "Mechanically robust stretchable organic optoelectronic devices built using a simple and universal stencil-pattern transferring technology," Light: Science & Applications, vol. 7, no. 1, p. 35, 2018.
[2] G. Wang et al., "Flexible pressure sensor based on PVDF nanofiber," Sensors and Actuators A: Physical, vol. 280, pp. 319-325, 2018.
[3] X. Liu, Y. Shang, J. Zhang, and C. Zhang, "Ionic liquid-assisted 3D printing of self-polarized β-PVDF for flexible piezoelectric energy harvesting," ACS Applied Materials & Interfaces, vol. 13, no. 12, pp. 14334-14341, 2021.
[4] S. Bodkhe and P. Ermanni, "Challenges in 3D printing of piezoelectric materials," Multifunctional Materials, vol. 2, no. 2, p. 022001, 2019.
[5] G. H. Haertling, "Ferroelectric ceramics: history and technology," Journal of the American Ceramic Society, vol. 82, no. 4, pp. 797-818, 1999.
[6] R. E. Newnham, L. Bowen, K. Klicker, and L. Cross, "Composite piezoelectric transducers," Materials & Design, vol. 2, no. 2, pp. 93-106, 1980.
[7] E. R. Cholleti, "A Review on 3D printing of piezoelectric materials," in IOP Conference Series: Materials Science and Engineering, 2018, vol. 455, no. 1: IOP Publishing, p. 012046.
[8] L. Koroglu, E. Ayas, and N. Ay, "3D Printing of Polyvinylidene Fluoride Based Piezoelectric Nanocomposites: An Overview," Macromolecular Materials and Engineering, vol. 306, no. 10, p. 2100277, 2021.
[9] F. Mokhtari, G. M. Spinks, S. Sayyar, and J. Foroughi, "Dynamic mechanical and creep behaviour of meltspun pvdf nanocomposite fibers," Nanomaterials, vol. 11, no. 8, p. 2153, 2021.
[10] R. A. Surmenev et al., "Hybrid lead-free polymer-based nanocomposites with improved piezoelectric response for biomedical energy-harvesting applications: A review," Nano Energy, vol. 62, pp. 475-506, 2019.
[11] F. Mokhtari, J. Foroughi, T. Zheng, Z. Cheng, and G. M. Spinks, "Triaxial braided piezo fiber energy harvesters for self-powered wearable technologies," Journal of materials chemistry A, vol. 7, no. 14, pp. 8245-8257, 2019.
[12] M. N. Islam et al., "Boosting Piezoelectricity by 3D Printing PVDF‐MoS2 Composite as a Conformal and High‐Sensitivity Piezoelectric Sensor," Advanced Functional Materials, vol. 33, no. 42, p. 2302946, 2023.
[13] H. Liu, J. Zhong, C. Lee, S.-W. Lee, and L. Lin, "A comprehensive review on piezoelectric energy harvesting technology: Materials, mechanisms, and applications," Applied physics reviews, vol. 5, no. 4, 2018.
[14] J. Bonilla-Cruz, M. A. Ávila-López, F. E. L. Rodríguez, A. AguilarElguezabal, and T. E. Lara-Ceniceros, "3D Printable Ceramic Pastes Design: Correlating Rheology & Printability," Journal of the European Ceramic Society, 2022
[15] Z. Liu, Y. Wang, B. Wu, C. Cui, Y. Guo, and C. Yan, "A critical review of fused deposition modeling 3D printing technology in manufacturing polylactic acid parts," The International Journal of Advanced Manufacturing Technolog y, vol. 102, no. 9, pp. 2877-2889, 2019.
[16] R. L. Truby and J. A. Lewis, "Printing soft matter in three dimensions," Nature, vol. 540, no. 7633, pp. 371-378, 2016.
[17] Y. Jiang et al., "Recent Advances in 3D Printed Sensors: Materials, Design, and Manufacturing," Advanced Materials Technologies, p. 2200492, 2022.
[18] A. C. Fischer, M. Mäntysalo, and F. Niklaus, "Inkjet printing, laserbased micromachining, and micro–3D printing technologies for MEMS," in Handbook of silicon based MEMS materials and technologies: Elsevier, 2020, pp. 531-545.
[19] S. Agarwala, G. L. Goh, G. D. Goh, V. Dikshit, and W. Y. Yeong, "3D and 4D printing of polymer/CNTs-based conductive composites," 3D and 4D Printing of Polymer Nanocomposite Materials, pp. 297-324, 2020.
[20] E. B. Secor, "Principles of aerosol jet printing," Flexible and Printed Electronics, vol. 3, no. 3, p. 035002, 2018.
[21] T. D. Ngo, A. Kashani, G. Imbalzano, K. T. Nguyen, and D. Hui, "Additive manufacturing (3D printing): A review of materials, methods, applications and challenges," Composites Part B: Engineering, vol. 143, pp. 172-196, 2018.
[22] S. Kumar, "Selective laser sintering: a qualitative and objective approach," Jom, vol. 55, no. 10, pp. 43-47, 2003.
[23] X. Zhou and P. S. Lee, "Three dimensional printed nanogenerators," EcoMat, vol. 3, no. 3, p. e12098, 2021.
[24] X. Shen and H. E. Naguib, "A robust ink deposition system for binder jetting and material jetting," Additive Manufacturing, vol. 29, p. 100820, 2019.
[25] K. Y. Shin, J. Y. Hong, and J. Jang, "Micropatterning of graphene sheets by inkjet printing and its wideband dipole‐antenna application," Advanced materials, vol. 23, no. 18, pp. 2113-2118, 2011.
[26] M. Mäntysalo, K. Kaija, S. Koskinen, and J. Niittynen, "Inkjetted 3D interconnections for electronic applications," in IMAPS Advanced Technology Workshop and Tabletop Exhibition on Printed Devices and Applications, Orlando, Florida, USA, February 25-27, 2009, 2009, p. 4.
[27] C. Ru, J. Luo, S. Xie, and Y. Sun, "A review of non-contact microand nano-printing technologies," Journal of Micromechanics and Microengineering, vol. 24, no. 5, p. 053001, 2014.
[28] R. Magazine, B. van Bochove, S. Borandeh, and J. Seppälä, "3D inkjetprinting of photo-crosslinkable resins for microlens fabrication," Additive Manufacturing, vol. 50, p. 102534, 2022.
[29] Y. She, C. Li, J. Cleary, and H.-J. Su, "Design and fabrication of a soft robotic hand with embedded actuators and sensors," Journal of Mechanisms and Robotics, vol. 7, no. 2, 2015.
[30] C. Ribeiro, D. Costa, and J. Correia, "Nunes-Pereira, J," Oliveira, P. Martins, R. Gonçalves, VF Cardoso, and S. Lanceros-Méndez, Nat. Protocols, vol. 13, p. 681, 2018.
[31] Y. Zeng et al., "Recent progress in 3D printing piezoelectric materials for biomedical applications," Journal of Physics D: Applied Physics, 2021
[32] W. Heywang, K. Lubitz, and W. Wersing, Piezoelectricity: evolution and future of a technology. Springer Science & Business Media, 2008.
[33] H. Kim et al., "3D printing of polyvinylidene fluoride/photopolymer resin blends for piezoelectric pressure sensing application using the stereolithography technique," MRS Communications, vol. 9, no. 3, pp. 1115-1123, 2019.
[34] M. Tilli, M. Paulasto-Krockel, M. Petzold, H. Theuss, T. Motooka, and V. Lindroos, Handbook of silicon based MEMS materials and technologies Elsevier, 2020.
[35] S. Vadodaria and T. Mills, "Jetting-based 3D printing of edible materials," Food Hydrocolloids, vol. 106, p. 105857, 2020.
[36] H. Zhu, Z. Liu, and F. Wang, "Improved dielectric properties and energy storage density of poly (vinylidene fluoride-cotrifluoroethylene-co-chlorotrifluoroethylene) composite films with aromatic polythiourea," Journal of Materials Science, vol. 52, pp. 50485059, 2017.
[37] C. K. McGinn et al., "Formulation, printing, and poling method for piezoelectric films based on PVDF–TrFE," Journal of Applied Physics, vol. 128, no. 22, p. 225304, 2020.
[38] D. Thuau, K. Kallitsis, F. D. Dos Santos, and G. Hadziioannou, "All inkjet-printed piezoelectric electronic devices: energy generators, sensors and actuators," Journal of Materials Chemistry C, vol. 5, no. 38, pp. 9963-9966, 2017.
[39] C. Ribeiro, V. Sencadas, D. M. Correia, and S. Lanceros-Méndez, "Piezoelectric polymers as biomaterials for tissue engineering applications," Colloids and Surfaces B: Biointerfaces, vol. 136, pp. 4655, 2015.
[40] X. Chen, X. Han, and Q. D. Shen, "PVDF‐based ferroelectric polymers in modern flexible electronics," Advanced Electronic Materials, vol. 3, no. 5, p. 1600460, 2017.
[41] R. Sahoo, S. Mishra, A. Ramadoss, S. Mohanty, S. Mahapatra, and S. K. Nayak, "An approach towards the fabrication of energy harvesting device using Ca-doped ZnO/PVDF-TrFE composite film," Polymer, vol. 205, p. 122869, 2020.
[42] J. Nunes-Pereira, P. Martins, V. Cardoso, C. Costa, and S. LancerosMéndez, "A green solvent strategy for the development of piezoelectric poly (vinylidene fluoride–trifluoroethylene) films for sensors and actuators applications," Materials & Design, vol. 104, pp. 183-189, 2016.
[43] I. Buj-Corral, A. Domínguez-Fernández, and A. Gómez-Gejo, "Effect of printing parameters on dimensional error and surface roughness obtained in direct ink writing (DIW) processes," Materials, vol. 13, no. 9, p. 2157, 2020.
[44] T. Rosental and S. Magdassi, "A new approach to 3D printing dense ceramics by ceramic precursor binders," Advanced Engineering Materials, vol. 21, no. 10, p. 1900604, 2019.
[45] Z. Chen et al., "Dense ceramics with complex shape fabricated by 3D printing: A review," Journal of Advanced Ceramics, vol. 10, no. 2, pp. 195-218, 2021.
[46] P.-H. Ducrot, I. Dufour, and C. Ayela, "Optimization of PVDFTrFE processing conditions for the fabrication of organic MEMS resonators," Scientific reports, vol. 6, no. 1, pp. 1-7, 2016.
[47] M. T. Craton, X. Konstantinou, J. D. Albrecht, P. Chahal, and J. Papapolymerou, "A chip-first microwave package using multimaterial aerosol jet printing," IEEE Transactions on Microwave Theory and Techniques, vol. 68, no. 8, pp. 3418-3427, 2020.
[48] J. Kloster, M. Danley, T. Struntz, V. Lai, and P. Zhao, "Simulating the Effects of Porosity on the D31 Piezoelectric Coefficient of Polyvinylidene Fluoride," in Smart Materials, Adaptive Structures and Intelligent Systems, 2022, vol. 86274: American Society of Mechanical Engineers, p. V001T01A005.
[49] Y. J. Park et al., "Ordered ferroelectric PVDF– TrFE thin films by high throughput epitaxy for nonvolatile polymer memory," Macromolecules, vol. 41, no. 22, pp. 8648-8654, 2008.
[50] N. A. Shepelin et al., "Interfacial piezoelectric polarization locking in printable Ti3C2T x MXene-fluoropolymer composites," Nature communications, vol. 12, no. 1, p. 3171, 2021.
The inventors of nano-isolators – the optical equivalent of a diode – say the device could start a technology revolution.
In the 1950s, a technological revolution in electronics began, spurred by the miniaturisation of diodes and transistors. The first electronic devices, simple radios and TVs, soon evolved into today’s smartphones, tablets and laptops, containing billions of diodes and transistors.
ANU Scientists Aditya Tripathi and Dr Sergey Kruk from the Nonlinear Physics Centre, believe a similar revolution could be imminent in the field of optics. Their team has developed an optical counterpart of the diode, called an isolator, that is only nanometres in size - millions of times smaller than existing technology.
Such radical miniaturization was what allowed diodes and transistors to end up installed in smartphones by the billion, when only a handful of the original vacuum-tube units could be fitted inside a fifties radio or TV.
The new optical technology offers the same potential, said Dr Kruk.
"While we can fit billions of electronic diodes and transistors inside a smartphone, we cannot do the same with conventional optical isolators. With current technology, a billion optical isolators would occupy at least an area of a football stadium and would cost the total annual earnings of all Australians.”
"Small and affordable optical isolators can open up a new era of optical engineering," said Dr Kruk.
Optical isolators allow light to pass through in only one direction, just as diodes permit electrical current to flow in only one direction. But light is highly reciprocal: if it can travel in one direction it can almost always retrace its path. To avoid this, current optical isolators use crystals and magnets which makes them bulky and expensive.
But with the new nanoscale isolators, many components could be fitted in consumer devices, which unleashes
their true power, said Dr Kruk, pointing out that in electronics the effectiveness of diodes is far greater when combined than as individual components.
“In the past, by including more and more electrical diodes and transistors into systems, we could progress from creating memory cells to performing mathematical operations, to developing computers and smartphones, to artificial intelligence.”
"The ability to integrate large quantities of small optical isolators into systems could lead to incredible innovations. We might see advancements in optical signal processing, machine vision, or perhaps entirely new technologies we haven't even imagined yet."
To break reciprocity in the propagation of light, the team’s optical isolator, which is reported in an article published in Nature Communications, incorporates vanadium dioxide, which has a key property. When heated, it undergoes a phase change which turns the material from a transparent dielectric-like phase to a non-transparent metal-like phase, in less than a billionth of a second.
The challenge the team had to solve was how to make this transition happen for light passing through in one direction, but not the other.
To do this they leveraged their skill in designing optical components with state-of-the-art nanotechnology. Such components, often termed metasurfaces, are made of arrays of structures much smaller than the wavelength of light, thousands of times smaller than the width of a human hair. The choice of the size and shape of these structures allows the unlocking of new properties of the interaction between the light and the material.
The team introduced asymmetry into the design, which they reasoned they could make one direction of travel favour the light absorption. In this direction the vanadium dioxide would be heated, triggering its phase change, and cut out transmission for that direction.
Choosing a light wavelength commonly
used for fast internet communications (around 1.5 microns), the team ran tens of thousands of computer simulations to find an optimal design that also was possible for modern nanofabrication. The modelling settled on an array of cylinders of silicon with radius and height both of 540 nanometres, arranged in a square lattice 820 nanometres apart, sitting on a layer vanadium dioxide 35 nanometres thick.
To make a prototype, the team turned to colleagues in Tennessee, United States, at Vanderbilt University and Oak Ridge National Laboratory. On delivery back to ANU, the prototype successfully allowed light to pass through from one side, while the reverse direction was indeed opaque.
The simplicity of the device could enable its widespread adoption, said lead author, PhD student Aditya Tripathi.
“Besides vanadium dioxide, this work uses some of the most basic elements in nanophotonic structures: silicon nanoresonators, which are convenient elements for modern nanofabrication.”
“The underpinning concepts are also relatively straightforward to implement in contemporary nanophotonics. Other researchers can tailor the design of an optical nano-isolator based on our methodology,” Mr Tripathi said.
“We believe that this work will lead to the development of all-optical steering and routing of light as well as multiplexing optical devices at the nanoscale.”
“The development of such devices will ultimately be a huge leap in the field of integrated photonics feeding further into quantum photonics.”
It opens the door for a low cost alternative, in which photovoltaics are recycled.
These short courses provide you with an engaging learning experience. Courses may include flash animations, video of instructors teaching the course in a classroom, video segments from ASM’s DVD series relevant to the learning material, and PDFs of instructor Power Points used in the instructor led training. All online courses require internet access for reading and viewing course content. Both HTML pages and PDF files for each lesson are downloadable and printable for easy offline access. https://www.materialsaustralia.com.au/training-courses-and-workshops/online-training
Steel is the most common and the most important structural material. In order to properly select and apply this basic engineering material, it is necessary to have a fundamental understanding of the structure of steel and how it can be modified to suit its application. The course is designed as a basic introduction to the fundamentals of steel heat treatment and metallurgical processing. Read More
Have you ever been handed a failure investigation and have not been quite sure of all the steps required to complete the investigation? Or perhaps you had to review a failure investigation and wondered if all the aspects had been properly covered? Or perhaps you read a failure investigation and wondered what to do next? Here is a chance to learn the steps to organise a failure investigation Read More
This course provides students with a fundamental understanding of the design process necessary to make robust medical devices. Fracture, fatigue, stress analysis, and corrosion design validation approaches are examined, and real-world medical device design validations are reviewed. Further, since failures often provide us with important information about any design, mechanical and materials failure analysis techniques are covered. Several medical device failure analysis case studies are provided Read More
This course provides essential knowledge to those who do not have a technical background in metallurgical engineering, but have a need to understand more about the technical aspects of steel manufacturing, properties and applications.
Read More
Profit from failure analysis techniques, understand general failure analysis procedures, learn fundamental sources of failures. This course is designed to bridge the gap between theory and practice of failure analysis.
Read More
This course is designed as an extension of the Introduction to Heat Treatment course. It discusses advanced concepts in thermal and thermo-chemical surface treatments, such as case hardening, as well as the principles of thermal engineering (furnace design) Read More
Composites are a specialty material, used at increasing levels throughout our engineered environment, from high-performance aircraft and ground vehicles, to relatively low-tech applications in our daily lives. This course, designed for technical and non-technical professionals alike, provides an overarching introduction to composite materials. The course content is organised in a manner that guides the student from design to raw materials to manufacturing, assembly, quality assurance, testing, use, and life-cycle support Read More
An ideal first course for anyone who needs a working understanding of metals and their applications. It has been designed for those with no previous training in metallurgy, such as technical, laboratory, and sales personnel; engineers from other disciplines; management and administrative staff; and non-technical support staff, such as purchasing and receiving agents who order and inspect incoming material.
Read More
Taking a fundamentals approach, this course is presented as an introduction to the world of induction heat treating. The course will cover the role of induction heating in producing reliable products, as well as the considerable savings in energy, labor, space, and time. You will gain in-depth knowledge on topics such as selecting equipment, designs of multiple systems, current application, and sources and solutions of induction heat treating problems Read More
Titanium occupies an important position in the family of metals because of its light weight and corrosion resistance. Its unique combination of physical, chemical and mechanical properties, make titanium alloys attractive for aerospace and industrial applications. Read More
Bruker Nano Surfaces provides industry-leading surface analysus instruments for research and production.
Bruker’s AFMs are enabling scientists around the world to make discoveries and advance their understanding of material and biological systems. Their tribometers and mechanical tests deliver practical data used to help improve development of materials and tribolocial systems.
Industry-leading quantitative nanomechanical and nanotribological test instruments are specifically designed to enable new frontiers in nanoscale materials characterisation, materials development, and process monitoring.
Whatever your surface measurement and surface analysis needs, materials or scale of investigation, Bruker has a specialised high-performance solution for you.
Universal tribology platforms
Fast and cost-effective in-lab rapid screening of new friction materials
Optical Profiling
Next generation
ContourX platforms
Improved optical resolution
Unmatched precision and repeatability
In-situ TEM/SEM nanomechanical instruments
Stand alone nanomechanical test systems
Wide range of environmental measurement options
High-resolution AFM Microscopes
New NanoScope 6 platforms, improved speed and data capability
High resolution for all applications, all environments
Materials Australia members are involved in all aspects of materials science, technology and engineering. Members include manufacturing technical officers, professional engineers, academics, research scientists, technical staff and students.
Our members are experts in polymers, nano and biomaterials, ceramics, metals, composites and all of their engineering applications.
There are two types of Materials Australia membership available: Individual and Corporate.
Individual members can join Materials Australia as a Student Member, Graduate Member, Standard Member, Retired Member or a Certified Materials Professional (CMatP).
Corporate members can opt for a Standard, Premium, or Premium Plus membership package.
• Accreditation as a Certified Materials Professional (CMatP) if eligible.
• Discounts on all Materials Australia conferences and training courses, including the CAMS and APICAM Conferences.
• Digital subscription to Materials Australia Magazine, our quarterly publication that is jam-packed with industry, product, technical and research news.
• Discounts on advertising in Materials Australia Magazine.
• Conferences, training courses, workshops and regular branch meetings, designed to facilitate continued professional development.
• Outstanding networking opportunities through regular branch meetings, conferences and training courses.
• Regular branch newsletters full of information on local activities.
• Discounts on advertising in Materials Australia Magazine.
• Editorial support for articles in Materials Australia Magazine.
• Digital subscription to Materials Australia Magazine.
• Free employment listings on the Materials Australia website.
• Free company listing on the Materials Australia website.
• Free company listing in the Materials Australia Magazine.