
35 minute read
Through The Looking Glass A Transparent Look at Glass Science
Through The Looking Glass:
A Transparent Look at Glass Science
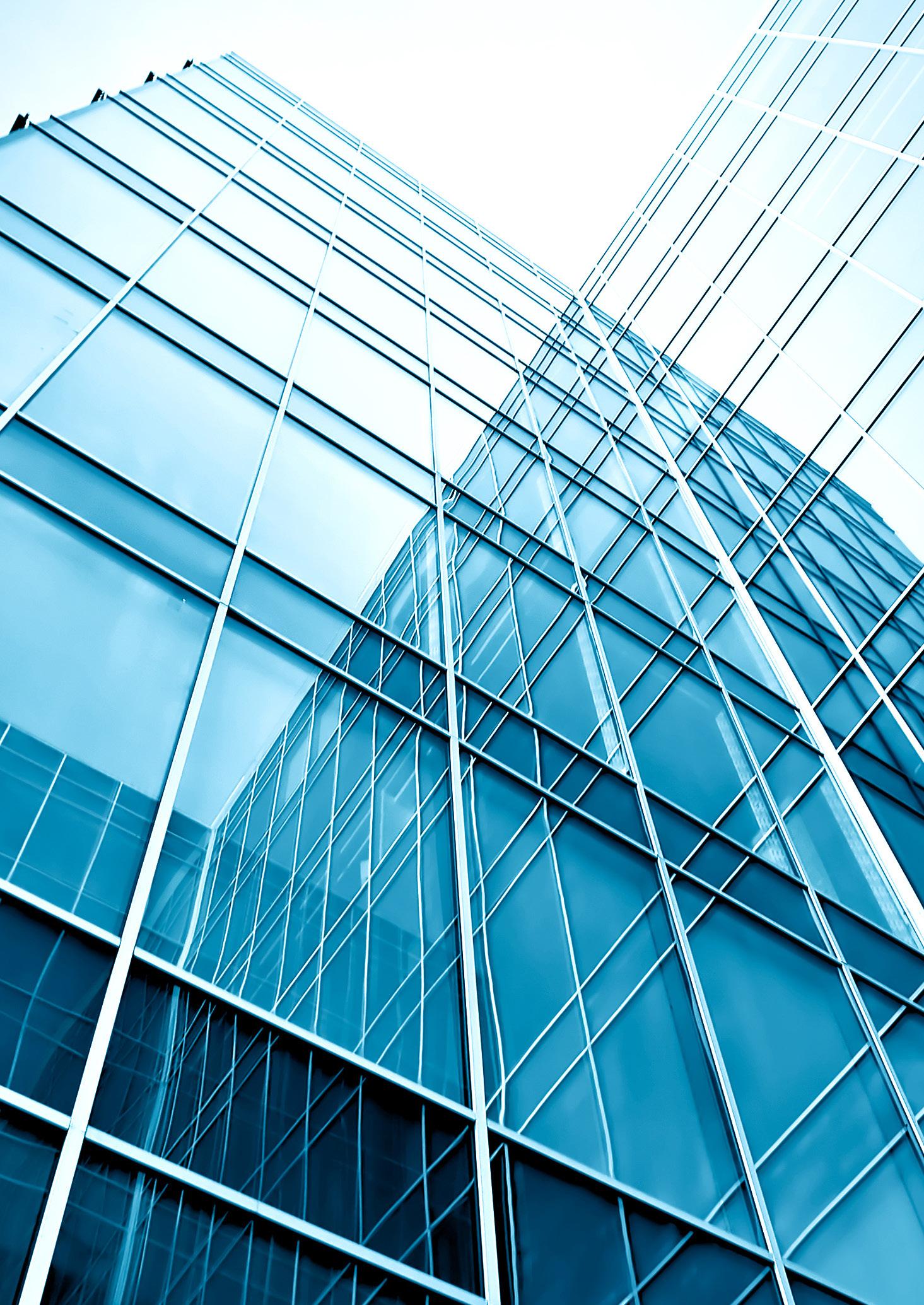

From food storage, and windshields in motor vehicles, through to test tubes in laboratories – glass is one of the world’s oldest, and most known synthetic materials.
Glass is highly versatile and durable. It can be spun finer than a spider’s web or even moulded into a disk for use in mirrors or telescope lenses. In addition, glass has the capacity to be stronger than steel, or more fragile than a single sheet of paper. Glass also comes in an array of shapes, sizes and colours. From historical uses in the middle of the desert, to contemporary usage in computing and technology – glass has changed the way that humans work, interact, and socialise. Glass has a wide variety of applications. For instance, in healthcare, bioactive glasses and ceramics are typically used in the dentistry community. They can also be used in bone regeneration. In fact, borate glass fibres, which are oxygen-born compounds, can heal soft tissues. In addition, researchers have found that radioactive glass microspheres have practical applications in the fight against cancer. Other uses of glass in the health sector include an anti-microbial cover glass that can suppress the spread of serious and deadly infectious diseases. Similarly, some glass materials can activate a certain type of gene within a living cell, which is crucial for stem cell engineering. Glass also plays a pivotal role in technology. For example, fibre optic cables that have been extensively used for the rollout of Australia’s National Broadband Connection, have accelerated internet speeds across the nation. In addition, optical interconnects that are made from glass and other glass-based devices will continue to play a fundamental role for the flow of data in the future of information technology. The environment is also a key winner. In the field of solar energy, researchers have found that glass is a key component in photovoltaics and other conversion processes where solar is turned into energy. Researchers have also discovered the importance of glass to ensure equal access to water and clean air. Glass is even able to securely hold and store radioactive waste materials from nuclear power generation. While the use of glass is far and wide, these innovations rely on continuous research and advances in glass science.
What is Glass Science?
Glass science is the stream of research that questions and analyses the scope for new glass compositions and manufacturing capabilities. In this stream of research, scientists seek to utilise previously unknown or unavailable functionalities for glass. Together, glass science focuses on the cutting-edge research available across physics, chemistry, engineering, geology, and mathematics. For centuries, researchers have been fascinated with glass’ ability to reflect, refract, and transmit light that follows geometrical optics entirely without any scattering effects. As such, contemporary glass science seeks to address the challenges of tomorrow. It focuses on three core areas: glass physics, glass chemistry, and glass engineering technology.
Glass Physics
Glass is in a constant state of thermodynamic disequilibrium, which is a continuous relaxing towards a more stable liquid phase. Researchers consider this to be one of the most intriguing phenomena in modern glass physics. While there has been significant progress in understanding the transition and relaxation of glass, its structural relaxation remains a key focus area. In addition, glass physicians are perplexed by the origins of thermal properties like heat capacity, thermal expansion and conductivity, and the acoustic properties of glass.
Glass Chemistry
Like glass physicists, glass chemistry continues to raise a series of new challenges and research areas. However, the chemistry of glass also opens a new world for researchers, who have access to nearly the entire periodic table to feature as palettes for possible ingredients. Glass boasts chemical durability, which provides a platform for vast applications like pharmaceutical labware, nuclear storage, architecture, and the automotive industry. As such, chemists remain focused on understanding the chemical compounds, structures, and kinetics in relation to glass and its durability.
Glass Technology
Finally, glass forming and processing technologies are at the cutting-edge of the globe’s future. Glass technology brings expertise in glass physics and chemistry to lead the development of precise and speciality glass products for mass consumption. For example, the Pilkington float process has allowed the production of a range of glass sheets for contemporary homes and high-rise skyscrapers. Similarly, the fusion draw process aids to the development of high-precision and ultra-thin glass for panel displays.
The History of Glass Science
A Roman historian, Pliny, wrote about his discovery of glass before 79 A.D. In his version of events, he believed that the discovery of glass was accidental. In fact, the discovery occurred after several Phoenician merchants mixed nitre, or a bicarbonate of soda, with sand and heated it up on the coast near Palestine. Pliny reported that “they together produced transparent streams of an unknown fluid, and such was the origin of glass”.
In 1607, the first glass furnace was constructed in Jamestown, Virginia. A second plant was erected a short time later, in 1620 to produce glass beads. These beads were a key source of trade between locals and the Indigenous population at the time. However, both glasshouses were destroyed in 1622. Other ancient uses of glass included bottles and vases. In 1609, Gasper Lehmann invented glass engraving, which changed the industry dramatically. Spanish glass, venetian, German glass and French glasses were all conceptualised and sold during the 1600s. In addition, glass manufacturing accelerated when gas was substituted for coal, and after the invention of the glass-blowing machine. As time went on, glass became more prominent in the built environment. Lamp chimneys, lantern globes, laboratory glassware, globes for street lighting, and tumblers were all crucial items that accelerated glass manufacturing. Advances in technology have prompted the departure from traditional glassmaking practices to contemporary and more sustainable approaches. Today, there are many unique types of glass, including: • Flat glass: used primarily in windows • Glass containers: used for food packaging and medicines • Optical glass: used for microscopes, glasses and telescopes • Fibreglass: tightly packed and combined with plastics for technological purposes • Bullet-resisting glass: a thick multi-layer that can absorb the energy of a single bullet. The use of glass has expanded and grown for a range of different purposes. Today, glass is a crucial material in everyday life. But despite its purpose, the process for glass-making is relatively similar: melting source materials, forming a structure, and allowing it to cool. As physicians and chemists learn more about glass and its properties, the societal impacts of glass remain strong.
Research Developments Over the Years
Some of the world’s most integral objects and systems – windows, computer screens and smart phones – are made from glass. These materials are made when sand, rock and gravel are crushed and melted. While materials science has evolved to incorporate new manufacturing processes, the natural environment remains a key player in the formation of glass. Glass is primarily made from silica sand, which is a more precise material than asphalt gravels and concrete. After water, sand is the world’s most consumed raw material. But there is a global shortage of sand. In fact, researchers and scientists believe that the global sand shortage is a challenge to the world’s overall sustainability. The United Nations believes that around 4.1 billion tonnes of cement are produced per annum, which is made up of 58 per cent of the contemporary sand-fuelled construction. But the global demand of sand and gravel is estimated to be around ten per cent higher than cement, which has cascading effects for glass science. For example, the global production of silicon chips relies on sand. However, global shutdowns prompted by the COVID-19 pandemic, Chinese trade disputes, and severe weather in Texas caused delays to the production of silicon chips. Estimates show that it can take up to half a year to create a chip. When making some products, the entire process involves over 1,000 steps. Similarly, Australia’s National Broadband Network has been impacted by the global chip shortage. These silicon chips are integral for powering smartphones, computers, video game consoles, automobiles, and home Wi-Fi networks. Analysts believe that production may take up to a year to bounce back, as organisations and governments alike negotiate new deals and seek alternative sources of production. Urbanisation has changed the world. However, a surge in people living in major cities and built environments has challenged traditional norms and processes in materials science. Sand is a crucial material for glass science. But the global rate of sand consumption has tripled in the last 20 years, which has prompted new research developments and innovations. Given the scarcity of sand, materials scientists are also seeking new avenues for glass production into the future. As history shows, it is likely that renewed glass science approaches will be required to prevent further damage.
2022 Year of Glass
Since 1959, the United Nations (UN) General Assembly has allocated specific subject areas as themes for that year. In previous years, UN member states propose a theme, or an occasion to be marked. Similarly, a specialised agency of the United Nations like UNESCO and UNICEF may put forward a proposal. Unlike previous years, ACerS member David Pye proposed the ‘Year of Glass’. On 18 May 2021, the UN General Assembly approved the idea, which will be celebrated in 2022. Alicia Durán is the president of the International Commission on Glass and chair of the International Year of Glass 2022. She said the year will underline the “scientific, economic and cultural roles and celebrate several anniversaries”. “Glass supports many vital technologies, facilitates sustainability and a green world and enriches our lives, yet often goes unnoticed,” she explained. Planning is already underway for the international event. An opening congress will take place in Geneva and an International Commission on Glass conference will feature in Berlin. Meanwhile, an interactive Glass Expo with additional satellite events will be held in China. Also, art and history congresses with a key focus on glass will take place across Egypt, Europe and the United States. Over 1,500 universities and research groups supported the decision and 79 countries across five continents approved the Year of Glass. The event will pave the way for dedicated international journals, exhibitions, and planned events in museums, where public and private glass collections and materials will be showcased. It will also promote glass science and finding renewed manufacturing processes for the future. “Heartfelt thanks go to the Spanish Mission at the UN, particularly the Spanish ambassador Agustín Santos Maraver and Ana Alonso, who led this process through the difficult twists and turns of diplomacy in stressful times,” Ms Durán said.
Glass Science at the University of Adelaide
Source: Dr Heike Ebendorff-Heidepriem
Research in inorganic non-metallic glasses was brought to The University of Adelaide (UoA) in 2005 when Dr Heike EbendorffHeidepriem joined UoA.
Heike has been passionate about glass since 1985 when she took up the offer of a summer project at the end of her first year at university. The project saw her assist in the development of novel optical glasses at the Otto-Schott-Institute for Glass Chemistry at the University of Jena, Germany. This project sparked her enthusiasm about glass as a material—it allows an unprecedented broad range of shapes and properties, while each glass piece is itself a work of art. Glass has been made for thousands of years but still holds a lot of mystery that waits to be uncovered. This is what has driven Heike’s research on glasses over the past 25 years. Working at the Otto-Schott-Institute was instrumental in helping Heike—as a young researcher—learn to work beyond disciplines, particularly with physicists, for example to test the glasses’ lasing ability. She also took the opportunity to work in collaboration with industry partners—a very different and equally rewarding learning curve—to develop new glasses for specific applications. Heike’s experience is a testament to a strong cultural heritage in Jena, when in the 19th century, three pioneers worked together to develop the optical microscope we know and still use today. These pioneers included: Otto Schott, a glass chemist and entrepreneur who developed new glasses suitable for microscope objectives; Ernst Abbe, a physicist who uncovered the optical imaging principles and invented the microscope lens; and Carl Zeiss, an entrepreneur that took the risk to manufacture the optical microscope. Another key experience that shaped Heike’s research journey was her hands-on training and then research on specialty glass optical fibre fabrication at the Optical Research Centre (ORC) at the University of Southampton in the United Kingdom. The ORC is the world-leading research institution in the development of novel optical fibres. In 2005, Heike joined Professor Tanya Monro (now Australia’s Chief Defence Scientist) to build the Centre of Expertise in Photonics (CoEP) at UoA. This was a once-in-a lifetime offer for Heike to build a world-class laboratory for the fabrication and characterisation of glasses and glass fibres for photonics applications including light-based sensing, novel light sources and delivery of light at new wavelengths. Even more, working with Tanya offered the perfect environment to establish an optical glass and fibre capability that is integrated in an interdisciplinary research culture. In 2009, the CoEP transformed into the Institute for Photonics and Advanced Sensing (IPAS), with Heike as one of the co-founders. IPAS was created on the strong belief that many of the challenges we face as a society can only be solved by pursuing a transdisciplinary approach to science. IPAS brings together experimental physicists, chemists, material scientists, biologists, experimentally driven theoretical scientists and medical researchers to create new sensing and measurement devices, primarily using glass technology.
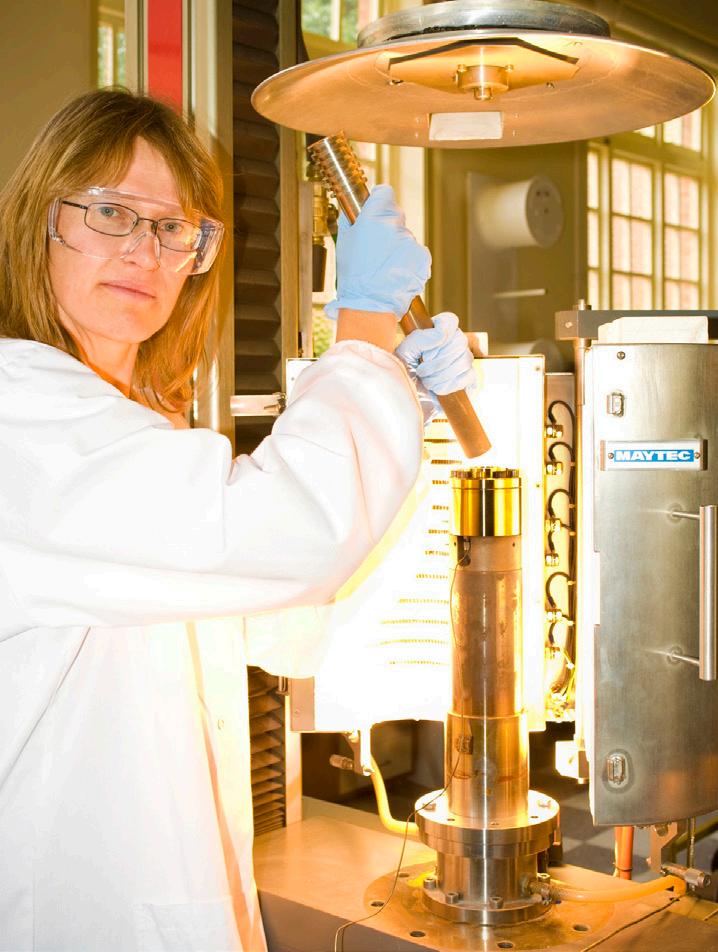
Glass extrusion to create glass preforms - Prof Heike Ebendorff-Heidepriem
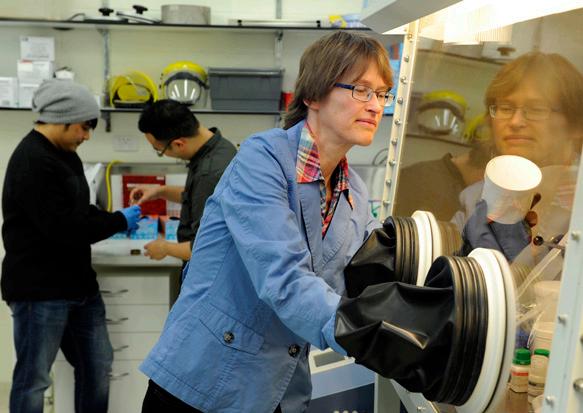
Controlled atmosphere glovebox - Prof Heike Ebendorff-Heidepriem Electron Miroscope Images of Microstructured Optical fibres. Prof Andre Luiten and Prof Heike Ebendorff-Heidepriem.

A Fascinating Material
Glass is a fascinating material that only exists due to kinetic hindrance. When a liquid glass melt is cooled down sufficiently fast, the transformation into a solid state with regular crystalline structure is inhibited, resulting eventually in a solid with a frozen-in amorphous structure that is similar to the liquid melt. This feature makes the properties of glasses highly dependent on the process conditions, which is why it is essential to consider both chemical composition and fabrication parameters (i.e. science and technology) in the development of new glasses and fibres. The everyday glasses around us are made of silicate glasses with SiO2 (i.e. sand) as the main component. Such glasses have a large resistance to crystallisation (also called devitrification) and have a large working range at elevated temperature, meaning that these glasses have a wide time window for being shaped at elevated temperature (e.g. via blowing and moulding) in an unlimited range of geometries. By contrast, glasses with exotic compositions, such as fluoride glasses, need extensive fine-tuning of the glass melting and shaping process to prevent crystallisation of the end-product. Therefore, the research aims of Heike’s team have been focussed beyond the traditional small sample glass chemistry needed to develop new glass compositions. The team is working to develop advanced and new glass technology, including understanding the glass flow during glass processing, a critical factor in creating the desired structures and achieving step-change functionalities.
Real World Applications
Heike is passionate about connecting glass research with real world applications. This has motivated her to help to create the world-class facilities at IPAS, including the National Collaborative Research Infrastructure Strategy (NCRIS) funded Optofab Adelaide node of the Australian National Fabrication Facility (ANFF), which houses over $20 million in advanced manufacturing equipment. As Director of Optofab Adelaide, Heike has shaped the facilities over the years to ensure researchers and industry worldwide have access to state-of-the-art fabrication facilities: the key to achieving specialised optical glass and fibre production. Glass research at UoA covers a broad range of glass types, ranging from traditional optical glasses in the silicate system to exotic glass compositions such as glasses composed entirely of fluoride components. This breadth of glass types is motivated by the diverse range of glass science and technology topics tackled by the glass research at UoA in close collaboration with huge numbers of researchers from academia and industry. A few examples illustrating the breadth in fundamental and application driven research are described in the following.
Fundamental Glass Science
One example of fundamental glass research in Heike’s group is the understanding of dissolution and dispersion of nanocrystals in glass. Her team has been investigating how to best embed nanoparticles in glass, instilling the glass with the properties of the nanoparticles it contains. In collaboration with Macquarie University and the University of Melbourne, five years ago, the team developed a method for embedding light-emitting nanoparticles into glass without losing any of their unique properties. This research has opened up exciting possibilities for new hybrid materials and devices that can take advantage of the properties of nanoparticles in ways we haven’t been able to do before – a major step towards ‘smart glass’ applications such as 3D display screens or remote radiation sensors.
Glass Art Collaboration
A key source of inspiration for the glass research at UoA is the ongoing collaboration with the thriving glass art community in Adelaide. In 2011, Heike collaborated with the community in Adelaide through a joint exhibition ‘A fine line – glass science meets art’. The collaborative exhibition with artists at Jam Factory’s Glass Studio incorporating video footage and examples of the works created by both artists and scientists, showcasing the technique and process behind the making of both glass art and the glass that underpins new science and technologies. As a result of the exhibition, strong interactions were established between the glass art and glass science communities.
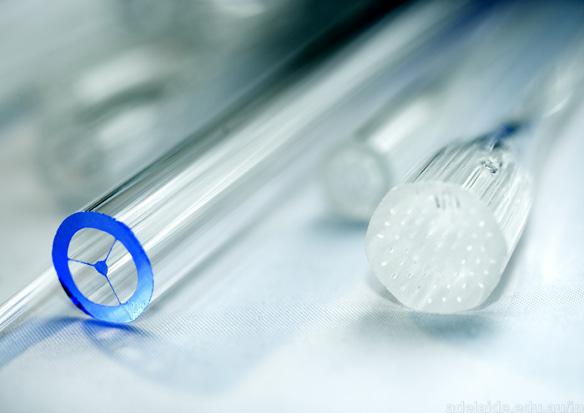
Glass Preforms. Soft Glass Optical Fibre Draw Tower - Prof Heike Ebendorff-Heidepriem.
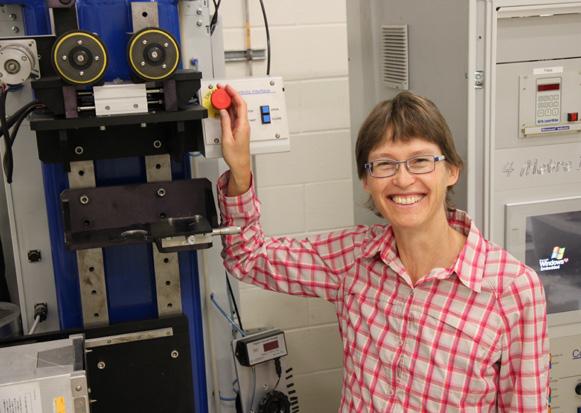
This relationship inspired the creation of a new diamond-glass fibre for quantum sensing. Artist Karen Cunningham’s work on embedding diamonds in glass inspired Heike to apply the technology to make a new class of diamond-glass fibre, which has been used by her collaborating research fellows to develop quantum sensors to monitor changes in magnetic fields – with implications for mining and underwater monitoring. In 2020, the team of researchers (from the University of Adelaide, RMIT, University of Melbourne, DSTG and UniSA) was awarded a Global-X Challenge Award of $1.5 million to develop an optical fibre-based network, like the National Broadband Network, capable of underwater operation.
Glass Flow Models to Advance Production
Another part of the transdisciplinary puzzle in this area is Heike’s collaboration with mathematicians at UoA, which has contributed to the development of mathematical and computational models for the glass flow during fibre drawing and led to the experimental validation of these models. All of these models have resulted in more complex preform and fibre geometries with a significantly higher first-time success rate. This collaboration together with the world-class facilities in glass and fibre manufacture at UoA underpins industry research with the global medical instrument manufacturer Trajan Scientific and Medical. The longstanding collaboration of Trajan with UoA’s fibre manufacture and mathematical modelling team has enabled the realisation of research, development and commercialisation of new generation specialty glass products for the global science and medical equipment market. Another example of commercial impact of the glass development and manufacture capabilities and expertise at UoA is the reproducible fabrication of fluoride glass with excellent optical quality, enabling the development of a new class of waveguide laser by the start-up company Red Chip Photonics. Glass-based fibres developed at UoA have also generated real world impact in the mining sector via an ultra-high temperature optical fibre sensor allowing local companies to monitor processes for the first time within a smelter environment, enabling significant reductions in energy use.
Ecofriendly Coloured Glass
A few years ago, one of Heike’s PhD student (now a postdoctoral researcher in her group) in collaboration with the PhD supervisors invented a new technology to create gold and silver nanoparticles in a highly controlled way in any oxide glass type. As these nanoparticles impart colour, this invention opens up the development of coloured glasses from non-toxic raw materials with unlimited colour choices and unique dichroic colour effects. The team realised that this new technology offers a path to the manufacture of ecofriendly coloured glass that can be made compatible to any type of clear oxide glass. The coloured glasses produced have been successfully employed by local glass artists at the Jam Factory to make glass sculptures. In 2020, the team established EZY-GLAS Technology Pty Ltd to commercialise their eco-friendly and compatible coloured glass manufacturing technology. The company’s vision is to provide coloured glass products for use in glass art, printing and other high-value applications where product identity, safety and quality are prerequisites.
3D Glass Printing
There are many future opportunities in the glass materials space for innovation. One area that Heike’s team have been working towards is how to 3D print glass with optical qualities. This potentially overcomes conventional manufacturing challenges that limit the design of traditional optical systems. This work builds on the extensive metal and plastics printing experience in the ANFF team at Adelaide and on the recently established collaboration with 3D glass printer manufacturing start-up company Maple Glass Printing. The team at Adelaide University works with a wide range of industry and government customers from around the world and are always keen to explore how their skills, expertise and technology can assist making the world a healthier, safer and wealthier place.
Prof Heike Ebendorff-Heidepriem
School of Physical Sciences The University of Adelaide tel: +61 8 8313 1136 email: heike.ebendorff@adelaide.edu.au www.adelaide.edu.au/ipas
Characterising Glasses using Thermal Analysis
Source: Andrew Gillen, NETZSCH Analyzing and Testing
Glass is a uniform amorphous solid material (at ambient temperatures), usually produced when the viscous molten material cools very rapidly to below its glass transition temperature, without sufficient time for a regular crystal lattice to form. The most common glasses are silicate based, especially soda-lime, lead and borosilicate types used for windows, containers and decorative objects. Non-silicate glasses including amorphous metals, polymers and supercooled molecular liquids and molten salts are also used in various applications. The insulation industry utilises the excellent thermal properties of glass wool in roof and wall insulation products.
In its pure form, glass is a transparent, strong, hard-wearing and essentially inert material, which can be formed with very smooth and impervious surfaces. Below glass transition temperature, glasses are brittle and will break into sharp shards. These properties can be modified or changed with the addition of other compounds or heat treatment. Common glass contains about 70% amorphous silicon dioxide, which is the same chemical compound found in quartz.
Thermal Expansion and Shrinkage Steps using Dilatometry
Coefficients of thermal expansion (CTE), glass transition temperatures and softening points are crucial parameters for the characterisation of glass formulations. Using pushrod dilatometry (DIL), all of these parameters can be measured precisely utilising the high resolution of the inbuilt displacement sensor. If the sample maintains a constant mass, then temperature dependent density can be calculated utilising dilatometer data, sample mass and cross sectional area. Presented in the plot (Figure 1) is a dilatometry measurement of a soda-lime glass. The mean thermal expansion coefficient was calculated as 9.35ppm/K in the temperature range 50…500ºC. The glass transition temperature was evaluated to be 556ºC and softening point detected at 614ºC. In a manufacturing environment, shifts in the glass transition temperature and softening point from sample to sample are indicative of slight variations in composition. Glass technologists and researchers often need to characterise the sintering behaviour of glasses in powder form. In such cases, dilatometers can be employed for measuring sintering temperatures and shinkage steps. Optimisation of sintering temperature programs used in production are possible using dilatometer data and thermokinetic modelling software. The NETZSCH DIL402 Expedis® Series offers state-of-the-art dilatometer technology for a wide range of research and development and industrial applications. The instrument covers a temperature range of -180…2800ºC and is the first horizontal dilatometer series on the market allowing force modulation, bridging the gap between dilatometry and thermomechanical analysis (TMA).

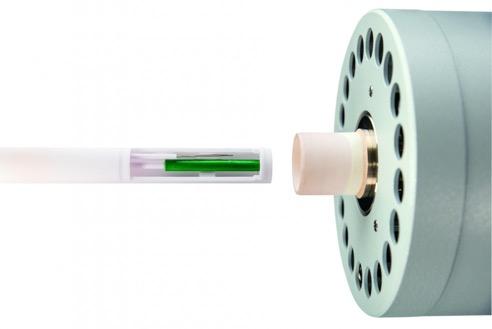
Figure 2: Typical sample setup in a high temperature pushrod dilatometer. Specimen (green) is placed inside furnace (pictured) for the desired heating cycle.
Debindering and Crystallisation Behaviour Using Simultaneous Thermal Analysis
Organic binders are often employed to maintain the integrity of glass powder green bodies prior to heat treatment. These binders typically decompose well below the sintering temperature. Simultaneous Thermogravimetry (TGA) and Differential Scanning Calorimetry (DSC) are commonly used for measuring debindering/ calcination temperatures and recrystallisation in glass formulations. In Figure 3, below, the graph shows a simultaneous TGA and DSC measurement (NETZSCH STA449 F1 Jupiter®) of a glass green body heated in synthetic air at 10K/min. The green plot (TGA) shows a minimum 2-step mass loss coming from the decomposition of the organic binder with characteristic DTG peaks at 301 and 438ºC, respectively. The blue plot (DSC) first shows the 3-step exothermic combustion of the organic binder, glass transition temperature at 704ºC, and finally recrystallisation peaks at 818ºC and 897ºC, respectively. The endothermic peaks at 946ºC and 962ºC are indicative of the melting of the recrystallised material. Crystallisation and sintering processes can be further investigated
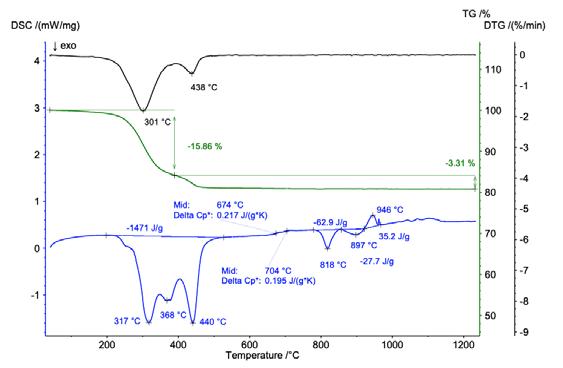
Figure 3: Simultaneous TGA/DSC measurement of a glass green body with a NETZSCH STA449 F1 Jupiter® .
using thermokinetic modelling via model-free methods (eg. Friedman, Vyazovkin), and model-based methods where knowledge about the chemistry of the process is required. NETZSCH Kinetics Neo software offers a powerful all-in-one thermokinetic modelling solution with a user-friendly interface suitable for all user levels. The Analyzing & Testing business unit of the NETZSCH Group (est. 1873, Germany) develops and manufactures a complete highprecision instrument line for thermal analysis and thermophysical properties measurement, as well as offering world class commercial testing services in our laboratories. Their instrumentation is employed for research and quality control in the glass and ceramics sector, polymer sector, the chemical industry, and many more. Their instruments accommodate various testing needs including: thermal expansion, thermal conductivity, glass transition temperature, specific heat capacity, rheology and more.
Contact at.au@netzsch.com or visit www.netzsch.com.au/at for more information
KEEPING YOUR GLASS IN SHAPE
by Combining Simultaneous Thermal Analysis, Dilatometry and Kinetic Analysis for Process Opimization
∙ ∙ ∙ ∙ Characterise thermal expansion Determine sintering steps Measure debindering and crystallisation behaviour Use NETZSCH Kinetics Neo for simulation of sintering processes
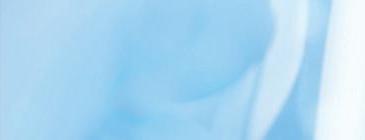
STA 449 F1STA 449 F1 Jupiter®Jupiter® DIL 402 Expedis Select Expedis Select
Contact us for more information or visit www.netzsch.com.au/at NETZSCH Australia Pty Ltd ∙ Unit 3/591 Withers Rd, Rouse Hill NSW 2155 ∙ Tel.: 02 96412846
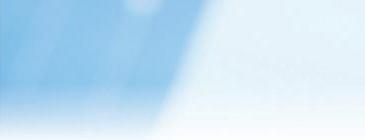

Glass – More than Meets the Eye
Source: James Riley (GTS Glass) and Dr. Cameron Chai
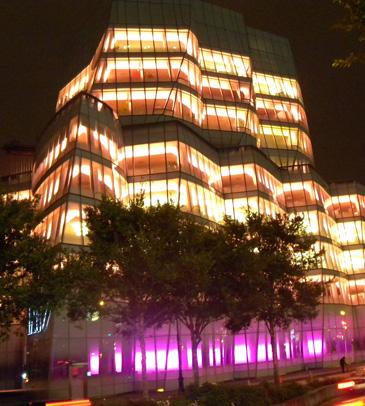
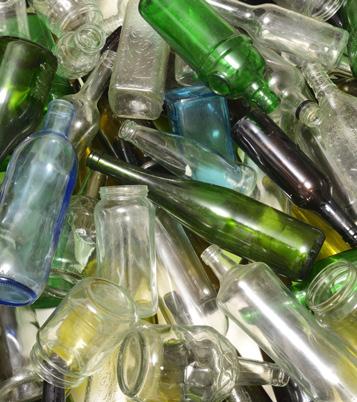
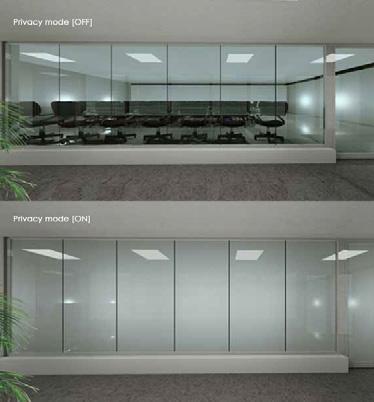
Glass Recycling Switchable-glass
We are all familiar with glass, as an amorphous material that allows us to bring the outside in, but at the same time protecting us from the elements. With the sleek and clean lines it offers, glass is becoming a material of choice in architecture and engineering. Various grades and types of glass are available that can provide specialised properties suited to a wide range of applications offering designers choices they may have never considered using glass for.
What is Glass?
SiO2 72.5 Na2O 15 CaO 9 MgO 2.5 Al2O3 1 Others Balance According to a report generated by the United Nations International Year of Glass 2022 (a recently ratified event celebrating the role of glass in society), global production of flat glass rose sharply to 84.0 million tonnes worth US$90.2b per annum in 2020, up from 59.2 million tonnes and US$ 48.3b per annum in 2016. Two-thirds of this production is consumed in architecture, and the bulk of the rest is used in automotive applications. Driven by explosive growth over the last decade of touchscreen and smart devices, production of smart and display glass has also seen rapid growth. Needing to be very thin, this glass has greater durability thanks to ion exchange strengthening.
Common glass or soda lime glass is made primarily from silica (sand) with additions of soda ash and limestone, and makes up over 90% of all glass produced. This composition is used for many different types of glass including float glass. Float glass is so named, as the molten mixture of raw materials is floated on a bed of molten tin, above which thin sheets of glass can be produced and used for windows as well a precursor for other applications that we will discuss herein. Nominal float glass composition
Composition wt. %
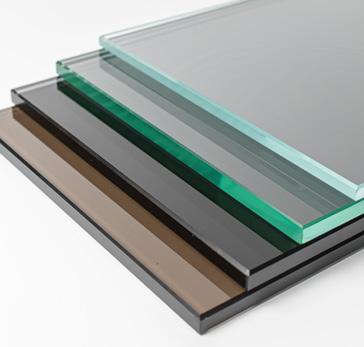
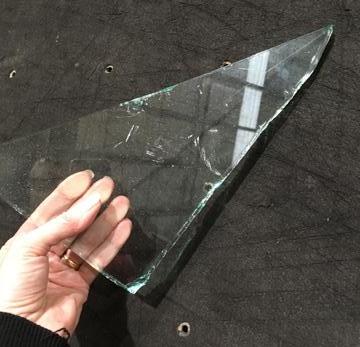
Glass Recycling
Glass lends itself to recycling. Secondary glass processors have turned waste and offcuts into cullet which can be fed back into glass production. Similarly, glass bottles and packaging can be recycled.
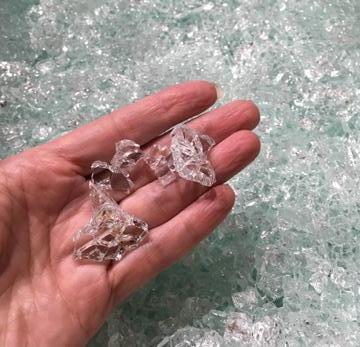
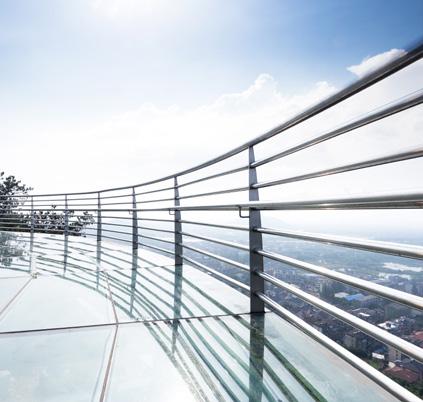
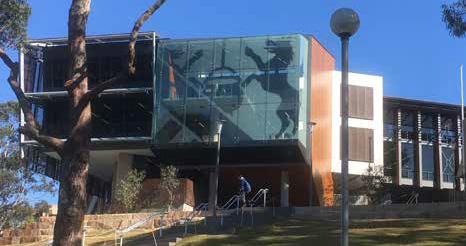
Above: Glass-walkway. Top: Multi-panel-printed-facade.
However, more emphasis needs to be put into recycling of architectural glass. Use of recycled glass reduces the strain on environmental resources, reduces the energy required to melt feedstocks, thereby reducing energy consumption and hence CO2 emissions as well as saving money.
Machining Glass
Gone are the days where complex glass shapes are nigh on impossible to produce. Now, if you can draw it, it can be made. Drawings can now be imported into CAD-based systems and complicated geometries can be generated by waterjet cutters and CNC machining centres. Final machining processes such as arrising and polishing ensure machined surfaces are finished to the same standard as the flat float glass faces.
Toughened Glass
Float glass is a precursor for a range of architectural and engineering glass products. It is annealed after coming off the float line to remove residual stresses so it is easy to cut and machine. Toughening or tempering results in an increase in strength of between 4 to 6 times making it suitable for engineering applications, most commonly in building. In Australia, this is carried out in accordance with Australian Standard AS 2208 – Safety Glazing Materials in Building which is stamped on all toughened glass. The process involves heating the glass to 620°C and then rapidly cooling it using jets of air. This induces compressive stresses of more than 69MPa (typically 80MPa) in the surface which significantly reduces the ability of cracks to form, resulting in higher strength. When float glass fails, it commonly forms large shards which we have all seen used as lethal weapons in movies. Toughened glass on the other hand, shatters into small, almost cubic granules when it fails, which is another advantage of toughened glass. Toughened glass is now commonplace in pool fencing, balustrading, shower screens and glass furniture, with different thicknesses available to suit the required engineering specifications.
Laminated Glass
Laminated glass is another form of safety glass in which glass sheets sandwich a polymer interlayer. Typically PVB or polyvinyl butyral has been used, however, other interlayer materials such as EVA or ethylvinyl acetate and Kuraray’s ionoplast structural interlayer SGP are increasingly popular choices for specific applications. Different grades of PVB are available, which can be combined with various thicknesses of glass sheets (both toughened and non-toughened) to provide a range of properties tailored to specific applications such as: • Safety glazing – awnings, curtain walls, windows, doors, splashbacks, fins etc. • Structural and security glazing – where maximum strength is required including glass flooring, stairs, facades and roofing, areas prone to extreme weather conditions (cyclones), intrusion protection and ballistic and bomb protection • Sound control glazing – enhanced acoustic insulation, ideal for high traffic areas, hotels, airports etc. • UV control glazing – can block almost all UV-A and UV-B radiation providing protection for artwork, furniture and even people • Decorative glazing – available in a range of colours and opacities suitable for indoor and outdoor use, designers are afforded even further design freedom. • Switchable glass – allows privacy control at the touch of a button Similar to toughened glass, different thickness glass sheets can be combined to provide the required strength. Furthermore, multiple interlayers can be combined to provide multiple properties or enhanced protection.
Printed Glass
Large area glass installations lend themselves to blank canvasses for designers to create visual impact or even simply to create brand awareness. Many options are available for this purpose. Starting at the budget end are vinyl graphics which can potentially be applied and removed if necessary. Painted glass is also possible, but longevity is an issue. Sandblasted designs offer a permanent solution and can be very effective for applications not requiring colour. Where designs can be repeated many times over, screen printing using ceramic pigments offers a suitable solution. Using ceramic pigments that are fused to the glass during the tempering process. Screen printed designs are permanent and colours will not fade over time. For the ultimate in design freedom, full digital ceramic printing services are offered. Using systems akin to inkjet printers, ceramic pigments can be laid out using fully custom designs. Again, the ceramic pigments provide permanence of colour, even under long-term UV exposure. While the maximum size of glass panels might be limited, the size of a glass installation such as building façades is almost infinite using well understood fixing systems. These installations are also at the mercy of graphic designers with digital printing and ceramic pigments offering total design freedom and ultimate durability.
The Future of Flat Glass
Flat glass will continue to play a significant role in architecture in aesthetic, structural and engineering applications as well as in and the automotive industry. The push for more energy efficient buildings will see the continued development and use of low emissivity glasses which reflect heat in the summer and trap warmth in the winter. As part of an overall strategy, more energy efficient designs will better control internal climates and reduce the need for HVAC and artificial lighting. Electrochromic glass shows potential for the future to further improve energy efficient designs as well as photovoltaic coatings with high visible light transmission.
No Cracks: Maple Glass’ 3D Printing Is Seamless
Source: Sally Wood
The world of 3D printing has grown significantly in recent years. Today, the practice can create crucial body parts and even houses. But when it comes to glass, 3D printing has not been explored because of the vast challenges that it poses. In fact, 3D glass printing has only been practiced by a select group of researchers and companies around the world.
However, Maple Glass Printing (MGP) have been bringing their expertise and skills to the world of 3D glass printing since 2017. The company has a simple mission: to reduce glass waste by 3D printing it. The Melbourne-based company enables broken and unused glass to be reused as part of their additive manufacturing processes. Unlike other companies and researchers that have used extreme temperatures and heat-resistant facilities to print molten glass, MGP uses advanced manufacturing capabilities to ensure a point of difference and a more sustainable approach to glass production. The company focuses on the three core pillars of a more sustainable environment: reduce waste, reuse materials, and recycle. MGP’s Chief Executive Officer, Dareen Feenstra and Chief Technology Officer, Nick Birbilis believed there was a gap in the market for more a sustainable and affordable glass manufacturing process. The innovation started when Birbilis was working with Feenstra, who was a PhD candidate at Monash University’s Woodside Innovation Centre at the time. They noted that glass was a popular material, but additive manufacturing had not penetrated it for greater use among industry. Four years later, the company is challenging traditional thinking in materials science.
“Our prolific use of materials is so entrenched in the norm of our thinking, and that’s largely because there is nobody alive on the planet today that hasn’t lived in a period where materials are just thought of as coming from a factory. That has created a mindset where it is often thought that there is an infinite supply of materials in a factory, and that’s not the case,” Birbilis explained. Birbilis said 3D printing of glass is a disruptive technology that raises a suite of new possibilities for manufacturers and companies alike. “3D printing has allowed us to start to think very different about the way in which we use materials and the type of materials that we use.” Unlike traditional glass-making technologies, MGP only heats the glass in a focused manner and momentarily at a high temperature. The company uses 100 percent recycled glass in a favourable environment. “Glass is one of these materials that has been used for centuries but I think we know very little about it. “When glass is very thin, around a fifth of the thickness of your hair, it can become infinitely flexible. Glass can also be very tough in large dimensions and resist cracking,” Birbilis said. Other universities have made attempts at producing 3D printed glass, but there were various concerns among industry groups and bodies about its wider use. “It’s no secret that Australia, like other countries, is having a waste and landfill crisis. Our systems of a circular economy are not yet up to the task.” “However, 3D printing of glass has remained at the bleeding edge. Fortunately, there are some companies giving it a red hot go,” Birbilis said.
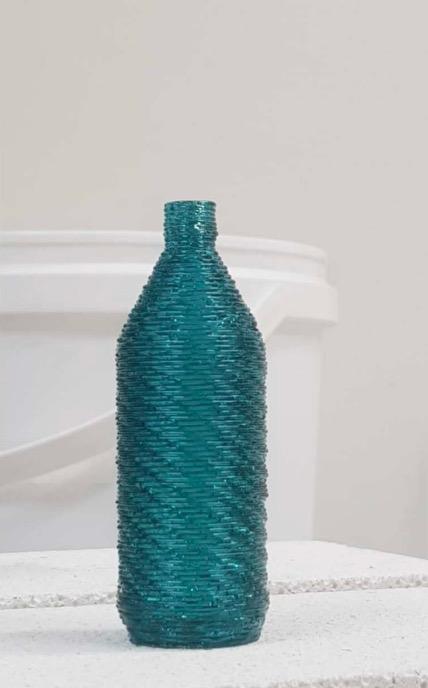
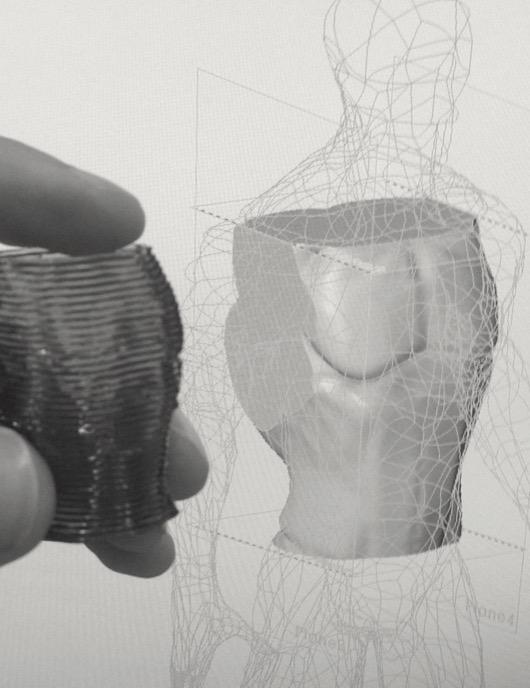
MGP Launches World-First 3D Glass Printers
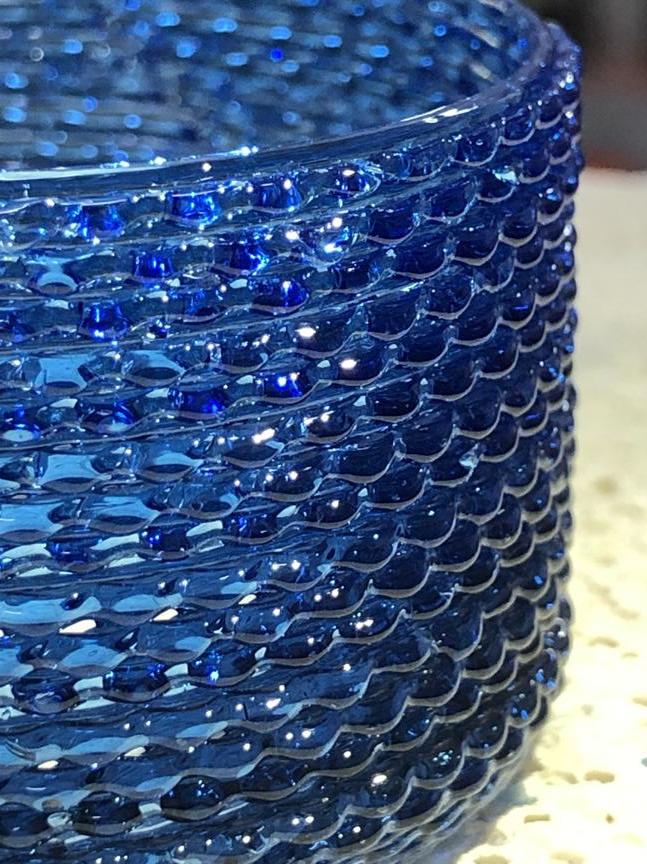
manufacturing game with the development of one of the world’s most affordable 3D glass printers. The The Maple 2™ printer allow users to create a series of complex digital designs with glass. It uses a unique technology to remove any shortfalls and inconveniences that are usually linked with glass manufacturing. The innovation follows two years of research by Maple Glass Printing (which has drawn upon local engineering talent), developing a prototype, and finalising a patent. Together, they were among ten projects selected from more than 200 applicants for the Monash Generator Accelerator Program – before fully spinning off to their Northcote (Victoria) premises. The program engages start-ups and individuals to produce inspiring and innovative ideas. It supports a full range of services, including a one-on-one seminar with an entrepreneur about launching an idea. “Universities sit on such a hot bed of talent when it comes to knowledge and innovation and we’re seeing that reflected in the incredible founders from our student, staff and alumni communities who are engaging with the Generator,” said Julie Stevens, who is the Program Manager of the Generator program. “The nine to five is becoming a thing of the past so it’s important for universities to prepare our graduates to shape their own world of work,” she said Maple Glass Printing were also part of the CSIRO-sponsored program, OnPrime, which assists researchers to gain critical skills and knowledge-sharing to innovate in a more efficient and faster way. The The Maple 2™ printer allows MGP’s customers to create rapid prototypes and designs that meet high repeatability – a crucial concern and challenge for industry. It also provides a series of environmental and economic benefits for clients. The innovation is poised to be the “world’s affordable 3D glass printer”. The 3D printing technology is currently in production and sales. MGP believes it will allow users to create “complex digital designs” with glass in a sustainable manner. This will reduce the time of glass prototypes from weeks or days, to minutes. Unlike polymers and metals, additive manufacturing has not expanded into the world of glass. This is because of the challenging process associated with glass production. But MGP guarantee that their 3D printers will ensure a point of difference. “Customers can create rapid prototypes with unique designs and iterate with high repeatability. “By using recycled glass, our printers can print detailed glass pieces with an economically viable process.”
Sustainability is at MGP’s Heart
Unlike previous models and innovation, the Maple 2™ printer provides a more sustainable approach to glass-making. Feenstra said the technology will play a critical role in the world’s sustainable future. “I see being able to print glass as another step towards creating a more sustainable world. It’s more efficient in terms of the recyclable materials it can use and less energy intensive than other recyclable processes currently on the market,” he said. Feenstra also explained that the Maple 2™ printer have been thoroughly trailed and tested with a range of glass materials, colours, and even multi-colours. “We’ve spent a lot of time and energy ensuring that our printer can use all kinds of recyclable glass materials because, at the moment, there are tonnes of waste being put in landfill and it’s not all necessarily waste – we just need the right tools to process it, to make new products and reduce our footprint.” “This is where glass printing could be part of the movement towards a fully sustainable society,” he explained. “We are proud to be manufacturers, and manufacturing, in Australia”. The printers currently eject glass with a layer height of around 0.25mm. However, the company plans to further reduce that figure to allow to produce pieces with flatter surfaces. The Maple 2™ printer can produce objects with dimensions of 250mm. But MGP can scale this for production versions that are not ‘benchtop’ oriented – traversing the needs of prototypers, artists and researchers, through to dedicated producers.